钢材预处理
钢材表面预处理

一、目的与适用范围1 范围1.1本工艺适用于钢材,包括钢板和型材的抛丸预处理流水线。
2 定义2.1钢材进厂后,在加工前对钢材的原材料进行处理,除去表面的氧化皮和锈蚀,涂上车间底漆以确保钢材在加工过程中不继续腐蚀,这一阶段的钢材表面处理,称之为钢材的表面预处理。
2.2钢材预处理的方式有抛射磨料处理、喷射磨料处理和酸洗处理三种方式。
其中要获得高效率的自动化流水作业,目前还只有抛射磨料处理方式。
抛射磨料处理亦称为抛丸处理。
二、工艺内容1 钢板校平造船用钢板,在运输过程中或经过长期的堆积后,会产生形变。
形变的钢板在分段落料加工时会影响加工精度,形变严重的钢板将影响船体的线型。
因此,钢板的预处理之前或之后,应对钢板作校平处理。
2 预热预热是为了在抛丸前将钢板升温,除去表面水分、部分油污,使钢板升温至一定的温度以利于喷漆后的干燥。
预热应使钢板升温至40左右。
升温太低,不利于除去水分、油污,不利于而后喷涂的车间底漆的干燥;升温过高,则多耗能量,又易使车间底漆在干燥过程中产生起泡的弊病。
3 抛丸及磨料抛丸用于清除钢材表面的氧化皮与锈蚀,并使钢材产生一定的粗糙度。
理想的抛丸处理磨料是钢丸加钢丝段或钢丸加钢砂,前后两者的比例为1:1到1:2范围之内。
4 喷漆抛丸处理后的钢材表面需立即涂覆车间底漆。
涂漆以自动化方式进行。
5 烘干钢材喷漆后应进入烘干炉,促使快速干燥以利迅速搬运。
烘干炉可以远红外辐射或蒸汽为热源,不能采用明火直接加热。
烘干炉应设排风装置,防止炉内溶剂气体积聚而引起燃爆事故。
6 抛丸预处理流水线工艺要求6.1车间底漆一般采用无机硅酸锌涂料。
6.2普通钢板及型材采用灰色的车间底漆,特殊强度的钢材则采用浅绿色车间底漆加以区分。
6.3钢材在进行预处理前必须采用清洁剂擦洗及高压淡水冲洗等方法去除钢材表面的油污等杂物(如有任何污物)。
6.4一般厚度介于6mm与40mm之间的钢板,需经钢板预处理流水线抛丸队锈,除锈标准为ISO8501-1:1988中规定的Sa2.5级(除锈标准均采用ISO标准),粗糙度必须控制在40—70微米范围,相当于ISO8503Medium Grade 至Course Grade的表面粗糙度。
1-1 钢材预处理.
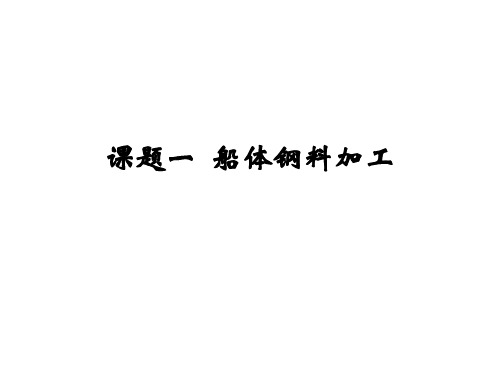
1、钢板的矫正 (1)钢板矫正的原理 钢板的任何一种变形,都是由于其中一部分纤维较另 一部分纤维缩得短或是伸得长所致。因此,钢板的矫正实际 上是将较长的纤维缩短或是将较短的纤维拉长,使它们和周 围的纤维有相同的长度,从而消除局部的不平。实际上,一 般是采用拉长纤维的方法,因为压缩纤维难以实现。 (2)钢板矫平工艺 ① 多轴辊式矫平机 工作部分: 由上下两列工作轴辊组成; 下列是主动轴辊,由轴承固定在机体上,不能作任何 调节,由电动机通过减速器带动它旋转; 上列为从动轴辊,可通过手动螺杆或电动调节装置来 调节上下辊列间的垂直间隙,以适应各种不同厚度钢板的矫 平作业。
二、钢材的表面清理
1、抛丸除锈法 利用专门的抛丸机将铁丸或其它磨料高速地抛射到钢材 表面上,以去除钢材表面的氧化皮、铁锈和污垢等。
抛丸除锈设备一般均设置有丸粒回收系统,并配置有 通风除尘设备。
2、钢材预处理流水线 由钢材的矫正、除锈、喷漆、烘干等工序形成的自动作 业流水线。
钢材预处理流水线的工艺流程 (1)先用电磁吊或自动装卸运输车将钢材吊放到输送辊 道上。 (2) 辊道以3-4m/min的速度将钢材送多辊矫平机,对 钢板进行矫平处理。 (3)矫平后的钢板由输送辊道送入加热炉,使钢材温度 达40~60℃。 (4)钢板进入抛丸除锈机,抛丸装置自动地向钢板两面 抛射丸粒,并用热风除去钢板表面的灰尘。 (5)钢材除锈并清洁后,进入喷涂室喷涂保养底漆。 (6)钢板离开喷涂室后,进入干燥室进行烘干。 (7)钢板烘干后从干燥室出来,进入高速辊道,以 20~30m/min的速度送出预处理流水线。经质量检验合格 后送入加工车间进行号料、加工。
第一节 钢材预处理
一、钢材的矫正 钢材变形的原因: 造船使用的钢板和型材,由于受轧制时压延不均、轧制后 冷却收缩不均以及运输、贮存过程中各种因素影响,常常产 生波浪形、局部凹凸和各种扭曲变形。 钢材变形的影响: (1)影响号料、气割及其他加工工序的正常进行,降低 加工精度; (2)在焊接时还会产生附加应力或构件失稳而影响构件 的强度。 钢材矫正的方法: 一般用多辊矫平机矫正钢板的变形,用型材矫直机矫正型 材的转动而啮入,并在上下辊列间承受方向相反的 多次交变的小曲率弯曲,因弯曲应力超过材料的屈服极限而产生 塑性变形,使那些较短的纤维伸长,使整张钢板矫平。 增加矫平机的轴辊数目,可以提高钢板的矫平质量。 钢板愈厚,矫正愈易;薄板容易产生变形,矫正比较困难。
钢材预处理工艺
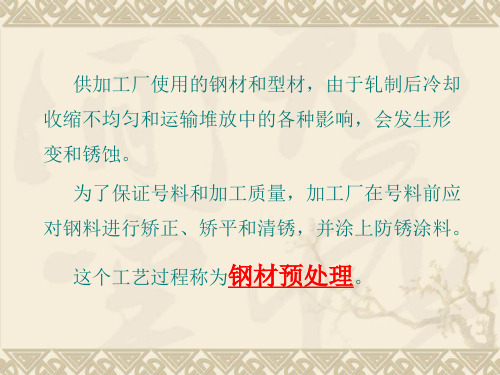
任务三:钢材预处理流水线
钢材预处理线简介:
二、表面清洁 表面清洁主要有升降刮板、吹扫机构、室体、除尘系统
等组成。 工作原理:钢板上料运行中,刮板可将钢板表面的块状
物及粉状废料分流至钢板两侧,从废料口进入废料桶收集, 钢板表面经刮扫后进入吹扫段,经喷吹后的钢板表面干净无 粉尘,达到钢板平前的清洁要求。喷吹过移产生的废气经除 尘器处理后达到环保排放标准要求。
覆盖层一般应满足下列基本要求:结构紧 密,完整无孔,不透电解质,附着力强,高强 度,耐磨,分布均匀。
任务三:钢材预处理流水线
任务三:钢材预处理流水线
任务三:钢材预处理流水线
加工厂把钢材输送、矫正、除锈、涂车间 底漆和烘干等工序所使用的机械装置,按工艺 流程用传送道连接起来,组成钢材预处理自动 流水线。
旋输送器、弹丸吹扫系统、供丸系统等组成。
任务三:钢材预处理流水线
钢材预处理线简介:
四、抛丸清理机 1、抛丸器 抛丸器是关键部件,对钢材清理质量及使用寿命,维护
都有很大影响。该系列机采用多台世界上先进的单园盘曲线 叶片高效抛丸器,弹丸由导入管流入,经分丸轮、定向套、 叶片抛出射出的高速密集弹丸,打击在工件的表面上,使工 件表面上的锈蚀层及其污物迅速脱落,获得一定粗糙度的光 洁表面,提高了漆膜与材料表面的附着力,提高了材料的抗 疲劳强度和抗腐蚀能力。该部件主要由叶轮、主轴及主轴承 座、分丸轮、定向套、护板、传动机构等组成。
任务三:钢材预处理流水线
钢材预处理线简介:
六、烘干室 烘干室是薄板箱形结构,它与喷漆室连接贯通。喷漆后的
工件在烘干室室内由板链输送进行烘干,由于工件与板链输送 辊之间没有相对运动,从而保证了工件下表面漆膜的完好。
烘干室上方设有通风除尘系统,被加热到40-50℃的热空气 管道闸门调节风量后送入烘干室内部,使被处理的工件达到漆 膜指干的要求。
钢材的预处理

图3-4 钢材预处理生产线 1-滤气器;2-除尘器;3-进料辊道;4-横向上料机构;5-预热室; 6-抛丸机;7-喷漆机;8-烘干室;9-出料辊道
2. 化学除锈法
化学除锈法即用腐蚀性的化学溶液对钢材表面进行腐蚀清洗。此法效率高, 质量均匀而稳定,但成本高,并会对环境造成一定的污染。
化学处理法一般分为酸洗法和碱洗法。酸洗法主要用于除去钢材表面的氧化 皮、锈蚀物等污物;碱洗法主要用于去除钢材表面的油污。其工艺过程较为 简单,一般是将配制好的酸、碱溶液装入槽内,将工件放入浸泡一定时间, 然后取出用水冲洗干净,以防止余剂的腐蚀。
钢材的预处理
1. 机械除锈法
2. 化学除锈法 3. 火焰除锈法
1. 机械除锈法
机械除锈法常用的主要有喷砂(或抛丸),手动砂轮或钢丝刷,砂布打磨等。 采用手动砂轮、钢丝刷和砂布打磨方便灵活但劳动强度大、生产效率低。现 在工业批量生产时多用以喷砂(或抛丸)工艺为主的钢材预处理生产线。 常见的钢材预处理生产线由输入辊道、表面清洁、预热室、抛丸清理机、中 间轨道、中间过桥、喷漆室、烘干室、输出轨道、除尘系统、漆雾处理系统、 电气等组成、并设有模拟屏,可显全线工作状态。钢材上料后由辊道进行输 送,然后进行表面清洁和预热处理,然后干砂(或铁丸)从专门压缩空气装 置中急速喷出,轰击到钢材表面,将其表面的氧化物、污物打去,再经过除 尘、喷漆、烘干等处理。这种方法清理较彻底,效率也较高。但喷砂(或喷 丸)时粉尘大,需要在专用车间或封闭条件下进行,同时经喷砂(或抛丸) 处理的材料会产生一定的表面硬化,对零件后续的弯曲加工有不良影响。喷 砂(或抛丸)也常用在结构焊后涂装前的清理上。图3—4为钢材预处理生产 线。
3. 火焰除锈法
钢材预处理0技术方案

一、设备用途本生产线主要用于钢板和各类型钢在加工前对其表面进行抛丸清理、喷漆和烘干。
钢材预处理的目的是为了清除钢材表面的锈蚀、氧化皮和污物,使钢材具有清洁和一定粗糙度的表面,以增强漆膜与钢材表面的附着力,从而提高产品的抗腐蚀能力和表面质量。
该设备一般用于工程机械、矿山机械、化工设备、压力容器、交通车辆、船舶制造及建筑型材等行业,用于提高产品的外观质量和其表面抗腐蚀能力。
二、设备主要技术规格1、处理工件规格:(1)处理钢板板厚:δ=5-60mm宽度: B≤3000mm长度: L=4000~12000mm(2)处理型材高度: H≤300mm长度: L=1600~12000mm2、输送辊道(1)辊道最大负荷: 2t/m(2)输送速度: 0.5-6.5m/min(变频无级调速)处理钢板速度: 1.5-5m/min处理型钢速度: 1-2m/min(3)驱动减速机: BWED2718-121-4(两台)(4)电机功率:4kw×2(5)滚轮直径: 180mm(6)滚轮有效宽度: 3500mm(7)辊道上平面高度:800mm(8)滚轮间距:抛丸室外635mm,抛丸室508mm3、抛丸清理机(1)抛丸器: 8台型号: Q035抛射速度: 72m/s抛丸量: 280kg/min电机功率: 18.5kw(2)纵向螺旋输送机:型号: GX300输送能力: 144t/h驱动装置: BWY22-29-7.5转速: 50rmp功率: 7.5kw(3)横向螺旋输送机:型号: GX300输送能力: 144t/h驱动装置: BWY22-29-5.5转速: 50rmp功率: 5.5kw(4)斗式提升机型号: D450提升能力: 144t/h料斗运行速度: 1.25m/s驱动装置: BWY22-17-11输出转速: 88rpm功率: 11kw(5)丸砂分离器分离能力: 120t/h分离区风速: 4-5m/s通风量: 10000m3/h驱动装置: BWY22-29-4功率: 4kw(6)清丸装置清扫滚直径: 900mm滚刷材质:四氟乙烯(进口刷丝)驱动装置: BLY18-23-3清丸风机: 9-19-6.3A风机功率: 15kw(7)清丸升降装置:提升高度: 500mm驱动电机: XWED63-289-3(电磁制动)电机功率: 3kw4、设备除尘系统(1)除尘通风量: 28000 m3/h(2)除尘器型号: MC-48(3)离心通引风机型号:4-72-8C(4)电机功率: 30kw(5)过滤风速: 0.4~0.8m/min5、自动喷漆装置:(1)喷漆形式:高压无气喷漆喷漆泵型号: 241-84R45:1高压喷涂机压力比: 45:1排量: 13L进气压力: 0.2~0.6MPa数量: 1(2)喷枪喷枪型号: 206-513自动喷枪喷枪到工件距离: 300mm(根据工件高度调整)喷枪数量: 4+1支(一把为手动喷枪,用于补漆或需要手动喷漆)(3)输送小车喷枪移动速度: 20m/min-50m/min(变频调速)数量: 2台(上下各一)(4)风动搅拌器: S-100型(5)G-01型油漆过滤器:25L6、烘干房(1)加热装置:采用燃油加热,30万大卡蒸汽加热器或电烘干加热风机功率: 15kw(2)通风机:结构:内置式耐热风机型号: GW-8C功率: 15kw(3)板链输送机:输送速度: 0.5~6m/min驱动装置: BWEY3322-121-5.5电机功率: 5.5kw7、漆物处理装置(1)风机:型号: B4-72 No8C左90º处理风量: 13000 m3/h风压: 1507Pa功率: 11kw(2)漆雾滤纸: 500×500×358、电气控制:采用控制面板集中控制,9、抛丸清理后的工件表面质量:Sa2.5级 GB8923-8810、喷漆漆膜厚度: 15-25µm(涂料为无机硅酸锌)11、烘干区温度: 40-70℃12、设备最大外形尺寸(长、宽、高):48000mm 、10000mm、10000mm13、年处理钢板量: 100000t14、设备最大功率:约280KW三、工作原理及工艺流程钢板被吊放至上料辊道,由上料辊道直接送到抛丸清理室进行清理,利用抛丸器高速抛射出的弹丸将工件表面进行清理;然后利用弹丸清扫装置(收丸刮板、清丸滚刷、高压吹管等)将工件表面的积丸和灰尘吹扫干净;除锈后的钢材直接进入喷漆室,通过装在上、下喷漆小车上的喷枪,将车间保养底漆涂在工件表面上,再进入烘干室,使钢材表面漆膜达到指干状态后由输出辊道输送出,进行下料。
钢材预处理安全操作规程
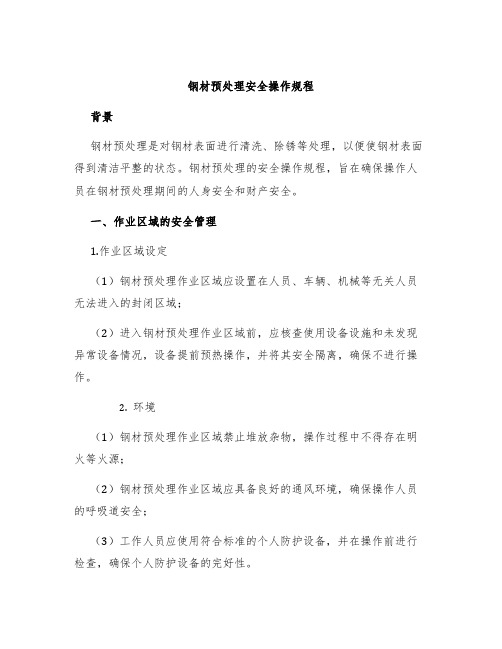
钢材预处理安全操作规程背景钢材预处理是对钢材表面进行清洗、除锈等处理,以便使钢材表面得到清洁平整的状态。
钢材预处理的安全操作规程,旨在确保操作人员在钢材预处理期间的人身安全和财产安全。
一、作业区域的安全管理1.作业区域设定(1)钢材预处理作业区域应设置在人员、车辆、机械等无关人员无法进入的封闭区域;(2)进入钢材预处理作业区域前,应核查使用设备设施和未发现异常设备情况,设备提前预热操作,并将其安全隔离,确保不进行操作。
2.环境(1)钢材预处理作业区域禁止堆放杂物,操作过程中不得存在明火等火源;(2)钢材预处理作业区域应具备良好的通风环境,确保操作人员的呼吸道安全;(3)工作人员应使用符合标准的个人防护设备,并在操作前进行检查,确保个人防护设备的完好性。
1.钢材预处理设备的安装(1)在设备安装前,应核查设备型号、尺寸、电气设备等质量相关要素,确保设备的安装满足要求;(2)设备安装后应进行调试,操作人员应当使用特制工具和安全绳,确保操作的稳定性。
2.钢材预处理液体的配制(1)钢材预处理液体的配制应严格按照工艺要求进行,配制前应按照标准调查设备运行状态,确保设备稳定运行;(2)操作人员应穿着符合要求的防护服和个人防护用品,确保无接触到钢材预处理液体;(3)如若操作不慎,如发现水不清或酸碱值异常,应及时采取措施。
3.钢材预处理液体的更换(1)发现钢材预处理液体的温度、酸碱值不符合要求时,应当停机排液并更换;(2)将液体更换后,应先进行清洗再安装,避免产生钢材损坏或需要重新处理情况的发生;(3)处理液体更换操作过程应确保预处理设备和周围设备完好无损。
1.钢材预处理的操作前准备(1)复查设备是否处于正常使用状态,机器开启前应检查是否齐全、摆放是否完好;(2)操作人员应穿戴符合标准的个人防护设备。
2.钢材预处理操作(1)钢板加工时,禁止使用锤击或任何力量敲打钢板,以免出现开裂、变形等不良后果;(2)钢板完整性原则:地面上禁止敲打或踩踏。
钢材堆放及预处理
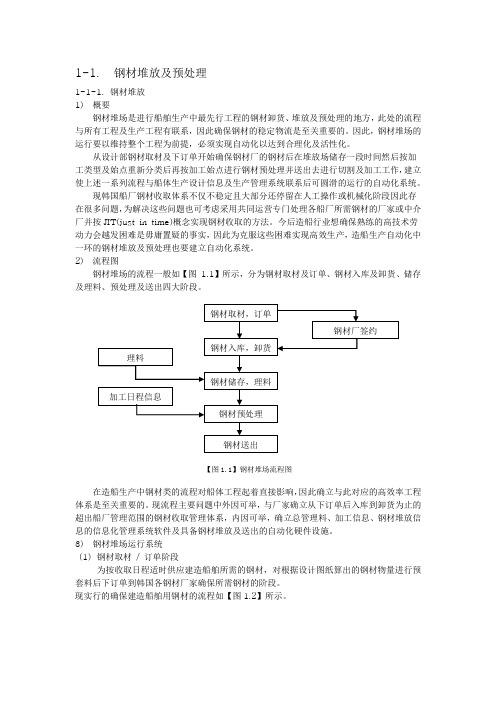
1-1.钢材堆放及预处理1-1-1.钢材堆放1)概要钢材堆场是进行船舶生产中最先行工程的钢材卸货、堆放及预处理的地方,此处的流程与所有工程及生产工程有联系,因此确保钢材的稳定物流是至关重要的。
因此,钢材堆场的运行要以维持整个工程为前提,必须实现自动化以达到合理化及活性化。
从设计部钢材取材及下订单开始确保钢材厂的钢材后在堆放场储存一段时间然后按加工类型及始点重新分类后再按加工始点进行钢材预处理并送出去进行切割及加工工作,建立使上述一系列流程与船体生产设计信息及生产管理系统联系后可圆滑的运行的自动化系统。
现韩国船厂钢材收取体系不仅不稳定且大部分还停留在人工操作或机械化阶段因此存在很多问题,为解决这些问题也可考虑采用共同运营专门处理各船厂所需钢材的厂家或中介厂并按JIT(just in time)概念实现钢材收取的方法。
今后造船行业想确保熟练的高技术劳动力会越发困难是毋庸置疑的事实,因此为克服这些困难实现高效生产,造船生产自动化中一环的钢材堆放及预处理也要建立自动化系统。
2)流程图钢材堆场的流程一般如【图 1.1】所示,分为钢材取材及订单、钢材入库及卸货、储存及理料、预处理及送出四大阶段。
【图1.1】钢材堆场流程图在造船生产中钢材类的流程对船体工程起着直接影响,因此确立与此对应的高效率工程体系是至关重要的。
现流程主要问题中外因可举,与厂家确立从下订单后入库到卸货为止的超出船厂管理范围的钢材收取管理体系,内因可举,确立总管理料、加工信息、钢材堆放信息的信息化管理系统软件及具备钢材堆放及送出的自动化硬件设施。
3)钢材堆场运行系统(1)钢材取材/ 订单阶段为按收取日程适时供应建造船舶所需的钢材,对根据设计图纸算出的钢材物量进行预套料后下订单到韩国各钢材厂家确保所需钢材的阶段。
现实行的确保建造船舶用钢材的流程如【图1.2】所示。
【图1.2】确保建造船舶用钢材流程如【图1.3】所示,船厂与钢材厂间的钢材收取要在开工105~130天前下发POR,签合同后从开工60天前开始最初纳期到开工30天前的30天为纳期。
钢材表面预处理线应注意的问题

根据以上分 析 , 角垫 板位 移是 由窄 边与 宽边 铜板 之 间的巨大摩擦力 和热 膨胀 引起 , 针 对此 原因 采取 以下 措 施: 1) 增加联结 强度 : 角 垫板 用沉 头螺 钉紧 固于 窄边 铜 板上后 , 应再用铜铆钉进行了铆固 , 固 定效果会更好。 2) 减小宽边 铜板 对窄 边铜 板的 压紧 力 : 在调 整夹 紧 装置时 , 上部和下 部的 压紧 力不 能相 等。一 方面 由于 钢 水静压力上部小 而下 部大 , 所 以下 部压 紧力 相对 要大 一 些 ; 另一方面由于上部温度高 , 窄边铜 板上口 膨胀时导 致 压紧力增加 , 因此上部压紧力要适 当调得 小一些 , 以抵 消 上口膨胀而增加的压紧力。这 一条原 则在新 组装和使 用 现场调整时都要遵守。 3 结束语 由于连铸生 产现 场环 境恶 劣 , 结晶 器的 使用 寿命 还 受到水压、 水质和冷却强度等多方 面因素 的影响 , 遇到 类 似问题应首先分 析出 导致 问题 发生 的直 接原 因 , 再分 析 这个原因是由哪 些因 素的 变化 引起 的 , 这样 才能 有的 放 矢。采取措施后 , 连续在连铸生 产线上 使用了 6 台 , 均 没 有发生角垫板位移、 挂钢等现象 , 拉钢 炉数比 改进前提 高 了 220 炉左右 , 现场验证的效 果十分 理想 , 措施有 效。本 课题的研究成功也为结晶器 制造厂家 和炼钢 厂提供了 现 场经验。 参考文献 [ 1] 现代板坯连 铸 . 曹广 畴主 编 . 北京 : 冶 金工 业出 版社 , 1994. 11 [ 2] 中华人 民共 和国冶 金行 业标 准 : ! 板 坯结 晶器 技术 条 件∀ , 标准号 : YB/ T 078- 1995 ( 收稿日期 : 2002 # 10 # 14)
钢材预处理
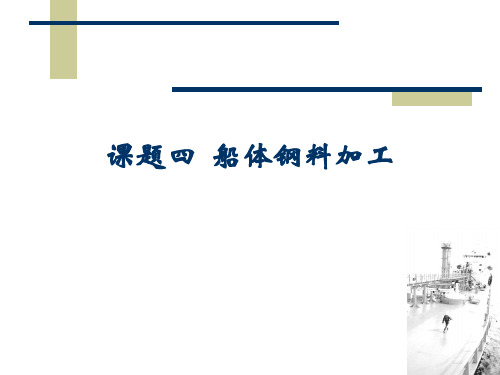
GL钢砂:尽管此类钢砂的硬度比GP钢砂要高一些,但在 喷砂过程中仍会失去棱角,特别适合于钢材表面去除氧 化皮预处理作业。 GH钢砂:此类钢砂硬度很高,在喷砂作业中会始终保持 棱角,对形成规则的,发毛的表面特别有效。GH钢砂 用于喷丸机作业时,应考虑施工要求优先于价格因素的 场合(如冷轧厂的轧辊处理)。此钢砂主要用于压缩空 气喷丸设备。
二、钢材的表面清理
1、抛丸除锈法 利用专门的抛丸机将铁丸或其它磨料高速地抛射到钢材 表面上,以去除钢材表面的氧化皮、铁锈和污垢等。
抛丸除锈设备一般均设置有丸粒回收系统,并配置有 通风除尘设备。
钢砂
GP钢砂:此种磨料新制成时,是尖棱状的,使用过程中 棱角很快就被磨圆,特别适合于钢材表面去除氧化皮预 处理作业
① 矫平设备:多轴辊式矫平机
工作部分:由上下两列工作轴辊组成; 下列是主动轴辊,由轴承固定在机体上,不 能作任何调节,由电动机通过减速器带动它 旋转; 上列为从动轴辊,可通过手动螺杆或电动调 节装置来调节上下辊列间的垂直间隙,以适 应各种不同厚度钢板的矫平作业。
② 矫平机的工作原理 钢板随轴辊的转动而啮入,并在上下辊列间承受方 向相反的多次交变的小曲率弯曲,因弯曲应力超过材料 的屈服极限而产生塑性变形,使那些较短的纤维伸长, 使整张钢板矫平。 增加矫平机的轴辊数目,可以提高钢板的矫平质量。 钢板愈厚,矫正愈易;薄板容易产生变形,矫正比 较困难。
2、化学除锈
主要是利用酸与金属氧化物发生化学反应, 从而除掉金属表面的锈蚀产物的一种除锈 方法,即通常所说的酸洗除锈,只能在车 间内操作 除锈后,还要有一层防护处理,常放入磷 化槽中进行 再吊入热水槽内清洗,自然干燥4~6h。
3、喷丸除锈
主要以颗粒喷射的冲蚀作用,构成的以达到表 面清洁和适宜的粗糙度,设备包括敞开式喷丸 (砂)除锈机、密闭式喷丸(砂室)、真空喷 丸(砂)机。敞开式喷丸(砂)机应用较为广 泛,能较为彻底地清除金属表面所有的杂质, 如氧化皮、锈蚀和旧漆膜,除锈效率高 4~5m2/h,机械程度高,除锈质量好。但对由 于磨料一般不能回收,对其他作业有影响,清 理现场麻烦。所以环境污染较重,近来逐渐被 限制使用。
钢材预处理生产线设备组成
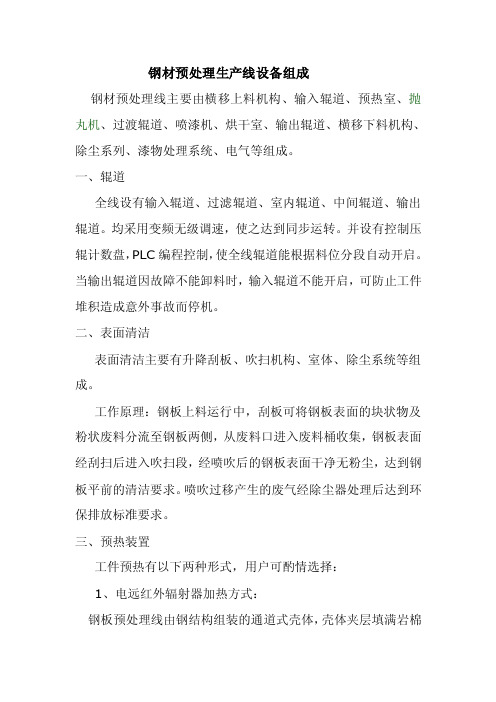
钢材预处理生产线设备组成钢材预处理线主要由横移上料机构、输入辊道、预热室、抛丸机、过渡辊道、喷漆机、烘干室、输出辊道、横移下料机构、除尘系列、漆物处理系统、电气等组成。
一、辊道全线设有输入辊道、过滤辊道、室内辊道、中间辊道、输出辊道。
均采用变频无级调速,使之达到同步运转。
并设有控制压辊计数盘,PLC编程控制,使全线辊道能根据料位分段自动开启。
当输出辊道因故障不能卸料时,输入辊道不能开启,可防止工件堆积造成意外事故而停机。
二、表面清洁表面清洁主要有升降刮板、吹扫机构、室体、除尘系统等组成。
工作原理:钢板上料运行中,刮板可将钢板表面的块状物及粉状废料分流至钢板两侧,从废料口进入废料桶收集,钢板表面经刮扫后进入吹扫段,经喷吹后的钢板表面干净无粉尘,达到钢板平前的清洁要求。
喷吹过移产生的废气经除尘器处理后达到环保排放标准要求。
三、预热装置工件预热有以下两种形式,用户可酌情选择:1、电远红外辐射器加热方式:钢板预处理线由钢结构组装的通道式壳体,壳体夹层填满岩棉保温材料,通道两端有橡胶帘密封,使之组成封闭性较好的预热室。
钢材经过预热室时由辅射加热,钢材预热后温升约40-50℃。
.2、热水加热方式:该装置的结构是由C型槽板组装的大壳体,这个壳体支持两根槽钢上,槽钢为输送辊道球面调心轴承的支架,在这个壳体里由橡胶帘子组成封闭性较好的预热室。
钢材加热是通过电加热器将热水加热到70℃,再通过室内设有的上、下热水喷筒把热水喷被预热的钢板上、下表面进行加热,钢材预热后温升约40-50℃。
3、此外,尚有燃气、燃油等多种加热方式,可根据用户求设计。
四、抛丸清理机抛丸清理主要由抛丸器、清理室、提升机、分离器、螺旋输送器、弹丸吹扫系统、供丸系统等组成。
1、抛丸器抛丸器是关键部件,对钢材清理质量及使用寿命,维护都有很大影响。
该系列机采用多台世界上先进的单园盘曲线叶片抛丸器,弹丸由导入管流入,经分丸轮、定向套、叶片抛出射出的高速密集弹丸,打击在工件的表面上,使工件表面上的锈蚀层及其污物迅速脱落,获得一定粗糙度的光洁表面,提高了漆膜与材料表面的附着力,提高了材料的抗疲劳强度和抗腐蚀能力。
简述钢材预处理的一般步骤
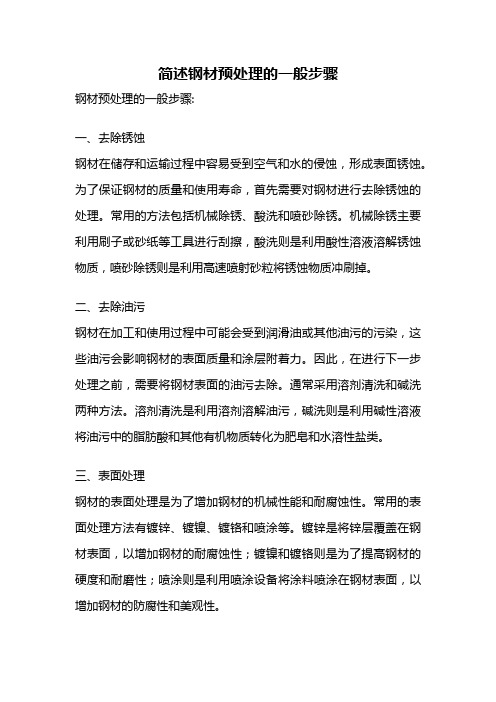
简述钢材预处理的一般步骤钢材预处理的一般步骤:一、去除锈蚀钢材在储存和运输过程中容易受到空气和水的侵蚀,形成表面锈蚀。
为了保证钢材的质量和使用寿命,首先需要对钢材进行去除锈蚀的处理。
常用的方法包括机械除锈、酸洗和喷砂除锈。
机械除锈主要利用刷子或砂纸等工具进行刮擦,酸洗则是利用酸性溶液溶解锈蚀物质,喷砂除锈则是利用高速喷射砂粒将锈蚀物质冲刷掉。
二、去除油污钢材在加工和使用过程中可能会受到润滑油或其他油污的污染,这些油污会影响钢材的表面质量和涂层附着力。
因此,在进行下一步处理之前,需要将钢材表面的油污去除。
通常采用溶剂清洗和碱洗两种方法。
溶剂清洗是利用溶剂溶解油污,碱洗则是利用碱性溶液将油污中的脂肪酸和其他有机物质转化为肥皂和水溶性盐类。
三、表面处理钢材的表面处理是为了增加钢材的机械性能和耐腐蚀性。
常用的表面处理方法有镀锌、镀镍、镀铬和喷涂等。
镀锌是将锌层覆盖在钢材表面,以增加钢材的耐腐蚀性;镀镍和镀铬则是为了提高钢材的硬度和耐磨性;喷涂则是利用喷涂设备将涂料喷涂在钢材表面,以增加钢材的防腐性和美观性。
四、调质处理调质处理是指通过对钢材进行加热和冷却处理,改变钢材的组织结构和性能。
常用的调质处理方法有正火、淬火和回火。
正火是将钢材加热至适当温度保持一段时间后冷却,以改善钢材的韧性和强度;淬火则是将钢材加热至临界温度后迅速冷却,以增加钢材的硬度和耐磨性;回火是在淬火后将钢材重新加热至较低温度,然后冷却,以减轻淬火过程中产生的内应力和提高钢材的韧性。
五、尺寸整理钢材在预处理过程中可能会出现一些尺寸误差,需要进行尺寸整理。
尺寸整理包括修整、切割和矫直等步骤。
修整是对钢材表面进行修整,使其符合规定的尺寸要求;切割则是将钢材切割成符合要求的长度或形状;矫直是对钢材进行拉伸或压缩,使其恢复到原来的形状和尺寸。
六、质量检验钢材预处理完成后,需要进行质量检验,以确保钢材的质量和性能符合要求。
常用的质量检验方法有外观检查、化学成分分析、物理性能测试和机械性能测试等。
钢材的表面预处理与矫正

钢材的矫正
钢材在使用前,其表面常存有不平、弯曲、扭曲、波浪形等缺陷,这 些缺陷使钢材在下料划线时,不可能获得所需要的下料精度,造成零件 尺寸的偏差,从而影响后续工序的顺利进行。
所以,钢材在下料和成形加工之前,必须对钢材进行矫正。
钢材变形的原因:
1.钢板轧制引起的变形 在轧制钢板时,当轧辊沿其长度方向受热不均匀,或者由于轧滚弯曲,轧辊调 整设备失常等各种原因,都将造成轧辊之间的间隙不一致,从而导致钢材在宽度 方向的压缩不均匀,于是钢材的每根纤维沿着长度方向的延伸就不相同。
(2)机械矫正
1)钢板的矫正 多辊矫正机是金属钢板、带材矫平的通用矫平设备。一般矫平辊数目
越多,矫平质量就越好。通常5 ~11辊用于矫中、厚板;11 ~21辊用于 矫平薄板。
矫平机的辊子直径、辊间距和数目是影响矫平效果的主要因素。 钢板矫平条件与被矫材料内的应力度系数有关,应力系数可按下式计 算:
喷丸除锈是利用风管中高速流动的压缩空气的压力使铁丸冲击 金属表明的绣层,依靠铁丸的机械冲击力,将氧化皮和锈斑剥离, 从而达到除锈的目的。一般在喷丸除锈后需立即喷底漆,否则易生 黄绣,影响除锈质量。
下图所示为GYX-nM型钢材预处理装置。它是一种大型喷丸除锈 设备,既可以用于钢板、型钢的表面处理,也可以用于结构部件的 表面处理。
2.运输、存放引起的变形 钢材在运输、存放过程中的不当也会产生局部皱曲。
变形的表现:表面凹凸不平、弯曲、扭曲、波浪形等
钢材的矫正原理: 矫正就是使钢板或工件在外力的作用下产生与原来变形相
反的塑性变形,以消除弯曲、扭曲、皱折、表面不平等变形, 从而获得正确形状的过程。
钢材的任何一种变形都是由于其中一部分纤维比另一部分纤维缩 得短些或是伸得长些所致。
钢材预处理
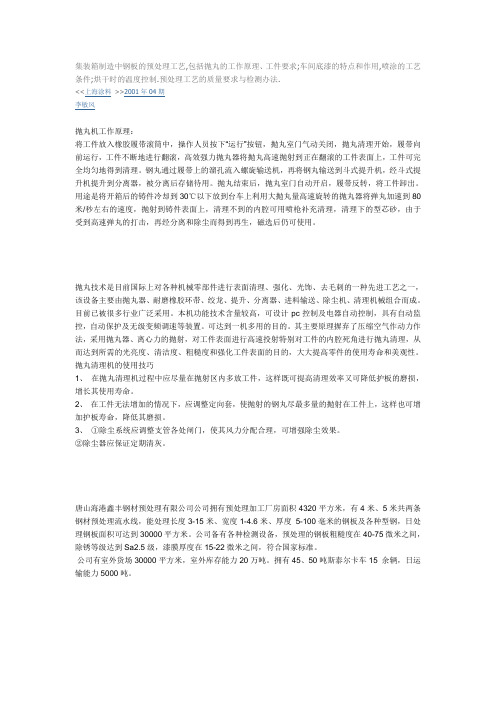
集装箱制造中钢板的预处理工艺,包括抛丸的工作原理、工件要求;车间底漆的特点和作用,喷涂的工艺条件;烘干时的温度控制.预处理工艺的质量要求与检测办法.<<上海涂料>>2001年04期李敏风抛丸机工作原理:将工件放入橡胶履带滚筒中,操作人员按下“运行”按钮,抛丸室门气动关闭,抛丸清理开始,履带向前运行,工件不断地进行翻滚,高效强力抛丸器将抛丸高速抛射到正在翻滚的工件表面上,工件可完全均匀地得到清理。
钢丸通过履带上的溜孔流入螺旋输送机,再将钢丸输送到斗式提升机,经斗式提升机提升到分离器,被分离后存储待用。
抛丸结束后,抛丸室门自动开启,履带反转,将工件卸出。
用途是将开箱后的铸件冷却到30℃以下放到台车上利用大抛丸量高速旋转的抛丸器将弹丸加速到80米/秒左右的速度,抛射到铸件表面上,清理不到的内腔可用喷枪补充清理,清理下的型芯砂,由于受到高速弹丸的打击,再经分离和除尘而得到再生,磁选后仍可使用。
抛丸技术是目前国际上对各种机械零部件进行表面清理、强化、光饰、去毛刺的一种先进工艺之一,该设备主要由抛丸器、耐磨橡胶环带、绞龙、提升、分离器、进料输送、除尘机、清理机械组合而成。
目前已被很多行业广泛采用。
本机功能技术含量较高,可设计pc控制及电器自动控制,具有自动监控,自动保护及无级变频调速等装置。
可达到一机多用的目的。
其主要原理摒弃了压缩空气作动力作法,采用抛丸器、离心力的抛射,对工件表面进行高速投射特别对工件的内腔死角进行抛丸清理,从而达到所需的光亮度、清洁度、粗糙度和强化工件表面的目的,大大提高零件的使用寿命和美观性。
抛丸清理机的使用技巧1、在抛丸清理机过程中应尽量在抛射区内多放工件,这样既可提高清理效率又可降低护板的磨损,增长其使用寿命。
2、在工件无法增加的情况下,应调整定向套,使抛射的钢丸尽最多量的抛射在工件上,这样也可增加护板寿命,降低其磨损。
3、①除尘系统应调整支管各处闸门,使其风力分配合理,可增强除尘效果。
桥梁钢材的处理方法

桥梁钢材的处理方法桥梁钢材的处理方法桥梁是连接两个地点的重要交通设施,而桥梁的强度和稳定性在很大程度上依赖于使用的钢材质量和处理方法。
桥梁钢材的处理方法对于桥梁的使用寿命和安全性有着关键的影响。
在本文中,我将深入探讨桥梁钢材的处理方法的不同方面,以及我的观点和理解。
1. 钢材预处理在桥梁建设之前,一系列的预处理步骤是必要的。
钢材需要经过表面清洁处理。
这可以通过腐蚀清除剂、喷砂或酸洗等方法完成,以去除表面的油脂、氧化物和其他杂质。
该材料需要进行除锈处理,以去除铁锈和腐蚀产物。
除锈可以通过机械手段,如钢丝刷除锈,或者化学手段,如采用酸性或碱性除锈剂来完成。
这些处理步骤有助于提高钢材的表面质量,从而使其更耐用和具有更好的耐蚀性。
2. 焊接技术桥梁钢材的连接通常采用焊接技术。
良好的焊接技术对于桥梁的结构强度至关重要。
在焊接之前,需要对钢材进行切割和准备工作,并确保准备表面的质量良好。
选择合适的焊接方法和焊接材料也是至关重要的。
常见的焊接方法包括电弧焊、气体保护焊和激光焊等。
我认为,选择适当的焊接技术和材料可以有效提高焊接接头的强度和耐久性。
3. 热处理桥梁钢材在使用过程中可能面临高温或低温环境,这就需要对钢材进行热处理以提高其性能和耐候性。
热处理可以通过淬火、正火、回火和退火等方式实现。
淬火可以提高钢材的硬度和强度,但也会增加脆性。
正火和回火可以消除残余应力和改善材料的韧性。
退火可以使钢材的晶粒细化,提高其韧性和延展性。
在选择热处理方法时,需要考虑桥梁的具体使用条件和要求。
4. 防腐处理桥梁钢材通常会接触到湿度、大气中的氧气和其他化学物质,容易生锈和腐蚀。
进行防腐处理是非常重要的。
常见的防腐方法包括喷涂防腐漆、热镀锌和冷镀锌等。
这些方法可以在钢材表面形成一层防护膜,以防止氧气和湿气进一步侵蚀钢材。
我认为,选择合适的防腐方法和材料可以大大延长桥梁钢材的使用寿命以及减少维护成本。
总结回顾:桥梁钢材的处理方法对于桥梁的性能、耐久性和安全性起着至关重要的作用。
船体加工-钢材预处理钢材的表面清理与防护

课程导入
表面清理
清除钢材表面的氧化皮和铁锈,俗称除锈
船用钢材在钢厂热轧时, 会跟空气中的氧气直接起 氧化反应,在表面形成一 层完整的、致密的氧化皮
课程导入
钢材表面会吸附空气中的水分 钢中含有一定比例的碳和其它元素 在钢材的表面会形成无数的微电池而 发生电化锈蚀,使钢材表面产生锈斑
钢表面清理与防护
覆盖层保护法
船体钢材所使用的覆盖 层除磷化处理后的磷酸
盐膜层外
主要是使用油漆
钢表面清理与防护
覆盖层保护法
船用油漆根据其用途不同分为
• 防锈漆 • 防污漆 • 水线漆
• 甲板漆 • 船壳漆 • 船舱漆
钢表面清理与防护
覆盖层保护法
防
富锌底漆
锈
底
漆
锌白色
环氧铁红底漆 紫红色
钢材预处理流水线
目前用于钢材预处理的最好方法
✓ 主要除去钢板表面的氧化皮和铁锈 ✓ 适合于组建钢材预处理的流水生产线
钢表面清理与防护
原材料抛丸法
利用离心式抛丸机的旋转叶轮将铁丸或其它磨料高速抛射到钢材的表面上,使氧 化皮和铁锈剥落的一种除绣工艺方法
立式抛丸机
卧式抛丸机
钢表面清理与防护
原材料抛丸法
20世纪60年代初出现了卧式抛丸机
钢表面清理与防护
原材料酸洗法
• 酸洗除锈法除用于薄板外
主要用于
处理
管子
舾装件
形状复杂的零件部件
可作为抛丸除锈法的补充手段
钢表面清理与防护
分段喷丸法
喷丸除锈多用于分段表面锈斑的清理,属于二次除锈
利用风管中高速流动的压缩空气将铁 丸喷射到钢板表面上,使锈层和氧化 皮剥离下来,从而达到除锈的目的
PSPC涂层标准对钢材预处理的要求(汇总)

CCS:
特性/参考标准 2 一次表面处理
喷射处理和粗糙 .1
度②③
水溶性盐限制
.2
(相当于氯化
钠)④
.3
车间底漆
要求
Sa 2½ 级,粗糙度介于 30-75 μm。 在下列情况下不应进行喷砂: .1 相对湿度超过 85%;或 .2 钢板的表面温度高于露点温度少于 3℃。 在表面处理结束时,在进行底漆涂装前,应依据涂料商的建 议检查钢板表面的清洁 度和粗糙度。 CCS4.3 全面清理后钢板的制备等级评定可按 ISO8501-1 或 GB/T 8923-1988 进行。 CCS4.4 表面粗糙度应按 ISO 8503-1/2 进行测定。 ≤ 50 mg/m2 NaCl。 CCS4.5 水溶性盐的测量应按 ISO8502-9 或 GB/T18570.9-2005 标准进行,测定的电导 率应全部折算成钢板表面氯化纳的密度。
编页号
MEASURED TIME 测量时间 DRY BULB TEMP. 干球温度 WET BULB TEMP. 湿球温度 RELATIVE HUMIDITY 相对湿度 DEW POINT 露点 SURFACE TEMP. 表面温度
ORE
CHANGES
干球温度(℃)
WET BULB TEMP.
湿球温度(℃)
RELATIVE HUMIDITY
相对湿度(%)
DEW POINT
露点(℃)
SURFACE TEMP.
表面温度(℃)
WATER SOLUBLE SALTS
水溶性盐含量
PROFILES
粗糙度
DUST
灰尘
OIL CONTAMINATION
油污
船体加工-钢材预处理船体结构用钢材

奥氏体不锈钢和双相不锈钢
—— 不 锈 钢 ——
能够抵抗大气腐蚀的钢
耐酸钢
能抵抗某些酸性介质的腐蚀
耐热钢
在高温下具有良好的抗氧化性和高温强度
由于耐酸钢和耐热钢均能抵抗大气腐蚀,故习惯上包括在不锈钢内
奥氏体不锈钢和双相不锈钢
不锈钢
不一定耐酸 能够抵抗大气腐蚀
船体结构用其它钢材
复合钢板
定义
• 指由基体材料和在其单面或 双面上整体结合的薄层(覆层 金属)所组成的板材
• 适用于化学制品运输船的容器 和液货舱
船体结构用其它钢材
复合钢板
基体材料
• 凡适合采用轧制或爆炸复合方法结合的碳钢或碳锰钢均可作为 基体材料
• 若板材拟用作船体结构的一部分 (如液货舱)或拟用于受压容器, 则基体材料应符合CCS《材料与焊 接规范》(2012年)的规定
船体结构用其它钢材
复合钢板
覆层金属
• 凡适合于预定用途的材料,均可作为覆层金属
如: 奥氏体不锈钢 铬 钢 铝合金 铜镍合金
• 无论何种复合钢板,其覆层 金属的厚度均应经CCS认可
船体结构用其它钢材
复合钢板
粘合
基体材料和覆层金属 之间
• 应充分粘合 • 除另有协议外,粘合面积比例至少应达到95%
如复合钢板在以后的焊接过程中发现焊接 接头部位有未粘合的情况,应采取经CCS 同意的方法进行粘合
耐酸钢
—— 耐酸钢也会生锈 ——
铬镍 耐酸钢
• 在硝酸和有机酸中有较好的耐蚀性 • 在盐酸和硫酸中则容易被腐蚀
奥氏体不锈钢和双相不锈钢
不锈钢
不一定耐酸 能够抵抗大气பைடு நூலகம்蚀
- 1、下载文档前请自行甄别文档内容的完整性,平台不提供额外的编辑、内容补充、找答案等附加服务。
- 2、"仅部分预览"的文档,不可在线预览部分如存在完整性等问题,可反馈申请退款(可完整预览的文档不适用该条件!)。
- 3、如文档侵犯您的权益,请联系客服反馈,我们会尽快为您处理(人工客服工作时间:9:00-18:30)。
钢材表面的预处理
航行于海洋上的船舶或海洋结构,一直处于强腐蚀性介质之中,其腐蚀问题十分突出。
由此而引起的经济损失是相当严重的。
因此,必须采取有效的防腐措施,以减少这种腐蚀损失。
对于船舶和钢结构来说,涂刷防护涂层,仍然是当今防止其腐蚀的主要手段之一。
钢材表面所涂防腐涂层的有效保护寿命与许多因素有关,如涂装前钢材表面处理的质量,所采用的涂料种类、涂膜厚度、涂装的工艺条件等。
其中钢材表面处理质量的好坏对涂层有效保护影响程度大50%多。
因此,钢材表面处理的质量控制是确保防腐涂层性能最关键的环节。
涂装前钢材表面处理,俗称除锈,他不仅除去钢材表面的铁锈,而且还包括除去覆盖在钢材表面的氧化皮、旧涂层以及沾污的油脂、焊渣、灰尘等污物。
此外,除锈之后钢材表面还形成一定的粗糙度。
所谓钢材表面的质量主要是上述污物的清除程度,或称“清洁度”,以及除锈之后钢材表面形成的粗糙度的大小。
国家标准GB8923是等效采用国际标准ISO8501-1: 该标准将未涂装过的钢材表面原始锈蚀程度分为四个“锈蚀等级”,将未涂装过的钢材表面及全面清楚过原有涂层的钢材表面除锈后的质量分为若干各“除锈等级”。
除锈前,钢材表面原始锈蚀状态对除锈后的表面外观质量评定具有一定影响。
同时不同锈蚀程度钢材,欲达到同一除锈等级,所花费的清理费用也不同。
因此,该标准根据钢材表面氧化皮覆盖程度和锈
蚀状况将其分为四个等级,分别以A、B、C和D表示。
A 全面的覆盖着氧化皮而几乎没有铁锈的钢材表面;
B 已发生锈蚀,并且部分氧化皮已经剥落的钢材表面;
C 氧化皮已因锈蚀而剥落,或者可以刮除,并且有少量点蚀的钢材表面;
D 氧化皮已因锈蚀而全面剥离,而且已普遍发生点蚀的钢材表面。
除锈等级,该标准对喷丸(砂)或抛丸除锈、手工和动力工具除锈以及火焰除锈的钢材表面清洁度规定了除锈等级,并且分别以字母“Sa”、“St”、和“F1”表示。
字母后面的阿拉伯数字则表示清除氧化皮、铁锈和油脂涂层等附着物的程度等级。
喷射和抛射除锈该项国家标准设有四个除锈等级,每一等级的文字定义如下:
Sa1 轻度的抛射或喷射除锈,钢材表面应无可见的油脂和污垢,并且没有附着不老的氧化皮、铁锈和油漆涂层等附着物。
Sa2 彻底的喷射和抛射除锈,钢材表面应无可见的油脂和污垢,并且氧化皮铁锈和油漆涂层等附着物已基本清除,其残留物应是牢固附着的。
Sa2.5 非常彻底的喷射或抛射除锈,钢材表面应无可见的油脂、污垢、氧化皮、铁锈和油漆涂层等附着物,任何残留的痕迹应仅是点状或条纹状的轻微色斑。
Sa3 使钢材表面洁净的喷射或抛射除锈,钢材表面应无可见的油
脂、污垢、氧化皮、铁锈和油漆涂层等附着物,该表面应显示均匀的金属色泽。
手动和动力工具除锈,该项国家标准设有两个除锈等级,每一等级的文字定义如下:
St2 彻底的手动和动力工具除锈,钢材表面应无可见的油脂和污垢,并且没有附着不老的氧化皮、铁锈和油漆涂层等附着物。
St3 非常彻底的手动和动力工具除锈,钢材表面应无可见的油脂和污垢,并且没有附着不老的氧化皮、铁锈和油漆涂层等附着物。
除锈应比St2更为彻底,底材显露部分的表面应具有金属光泽。
火焰除锈,该项标准对于火焰除锈只设一个等级定义如下:
F1火焰除锈,钢材表面应无可见的油脂、污垢、氧化皮、铁锈和油漆涂层等附着物,任何残留的痕迹应仅为表面变色(不同颜色的暗影)。
经过时代的变迁和前辈们的不断研究,当今船舶钢材表面处理的方式主要为:原材料抛丸预处理并涂装车间底漆;喷丸处理;酸洗及磷化处理。
要获得高效率的自动化流水作业,目前还只有抛射磨料处理方式。
抛射磨料处理亦称为抛丸处理,是利用抛丸机的叶轮在高速旋转时所产生的离心力,将磨料(钢丸、钢丝段、棱角砂等)以很高的线速度射向被处理的钢材表面,产生打击和磨削作用,除去钢材表面的氧化皮与锈蚀,让钢材表面露出金属本色并呈现一定的粗糙度,以利于涂料的粘附。
抛丸处理的效率很高,可在密闭的条件下进行,配以粉尘吸收装置则不会污染环境,配以自动化涂装装置则可达到除锈---涂装临时保养用的车间底漆一体化于自动化流水作业。
我们称为钢材预处理流水线。
抛丸预处理流水线的工艺流程如下:
以上各工位控制信号信息反馈
总控制室
注:带“*”处均有手控与联动控制箱
预处理线工作流描述:
利用工厂起重机械或其他吊装方式,将钢板或型材摆放在横向输送上料装置上,根据工件的长度开启
相应的顶升台条。
通过横向移动摆放
到输入式辊道上。
传感器测量到工件
正确进入到输入辊道输送系统上后,
工件就可以向前输送进入下一道工
序。
工件通过辊道上的传感器和计数器,测出钢材的高度和宽度,通过信号转换成数据传送到主控制系统。
通过数据可以精确自动调整后续工序的工作高度和宽度。
待工件将到达高压水枪装置前开启高压水闸对钢板进行上下两面清洗(主要是控制盐分含量),同时用高耐磨硬橡皮刮板刮去钢板表面的积水和通过高压风机的吹扫,吹除钢板表面水分。
(厂房设有废水处理管道)
工件经过表面吹扫之后,进如预热室,其主要加热方式是红外线加热。
使钢材在通过预热室时快速蒸发钢材表面水分,钢材表面温度均匀。
出预热室在抛丸室入口前端有一工件传感器,可以检测工件的到来以及主要尺寸并将有关信息发送到中央控制柜。
工件到来时,中央控制柜启动抛丸机的丸料供应系统,仅向需要满足工件宽度的抛丸器供料。
并控制喷漆机的喷嘴运动系统的工作范围于工件宽度想匹配。
这样在获得最大生产效率的现时能量消耗、丸料消耗和油漆消耗量最少。
工件在通过抛丸室时,快速和均匀的去除了氧化皮和除锈,然后通过刮扫螺旋装置进行一级清扫,高强度的尼龙滚刷+收丸螺旋装置为二级清扫,高压风机在抛丸室内吹
灰+预留压缩空气补吹管路为三级清
扫。
将工件上残留的丸料清楚掉,同
时所有粉尘通过负压除尘系统抽走。
丸料清扫后通过在抛丸室下部的
两个纵向螺旋和一个横向螺旋,回收
至提升机再由提升机输送到分离螺旋,钢丸回到丸料箱内。
利用重力风选原理,过滤细小丸料、粉尘从废料口流出。
抛丸室内粉尘和细小颗粒的回收采用重力沉降+旋风体组+滤筒式除尘器的除尘方式。
粉尘通过
风机产生的负压作用将含尘气
流经管道收集到含尘室,通过滤
筒过滤分离经洁净室和风机排
出。
粉尘则被滤芯阻拦在其表面
上,当被阻留的粉尘在滤芯表面
不断沉积时,滤芯里外的压差也
同时不断加大,当压差达到预先
设定值时,控制压缩空气的电磁
阀被打开,压缩空气经管道喷入反吹清扫系统,通过清扫机构完成脉冲清灰动作,使沉积在滤芯上的粉尘颗粒在高压气流的作用下脱离滤芯表面掉落,使得整个滤芯表面都得到清扫。
净化后的空气由风道、经风机排出(也可通过脉冲控制仪延时顺次反吹)。
符合质量的工件然后进入到喷漆机进行喷漆。
喷汽机前侧设有光帘式传感系统,可以控制往复式喷漆系统的高度以及无气喷嘴。
根据传感器测的宽度控制喷嘴小车的运动和喷嘴的开闭,防止油漆重喷。
确保油漆的消耗量少,成本低,同时改善预处理后工件的焊接质量。
工件离开喷漆机后进入烘干室。
采用热风循环原理,使热量得意充分利用。
烘干室温度一般在30~70℃可调。
烘干室的输送系统为窄条是板链输送系统。
输送器为重型结构设计。
漆雾处理装置分为漆雾过滤装置和有害气体吸附装置两部分。
由喷漆室的含漆雾气体经过喷漆室管道被吸入漆雾过滤箱,在送风机的作用下,废气经过主进阀和旁通阀切换调节进入热交换器,通过热交换器的换热和加热器的加热,使冷废气加热到催化起然温度(250℃-300℃)。
然后进入催化反应床,在催化剂的催化作用下,有机物进行氧化反应生成无害的水和二氧化碳。
由于催化反应放热,使反应后
气体温度上升达到一定温度值,反应后的高温气体经过热交换换热,预热原废气使气体温度升高,并且反应后的高温气体降低一定的温度,最后经风机、通过回用调节阀的调节一部份进入烘箱,另一部份排入大气。
烘干后的工件随后输送到工件输出辊道式输送系统,通过横向卸料系统或行车进行卸料。
主要技术性能。