钢材表面预处理通用工艺
集装箱钢材表面处理及检验

Q/CIMC 中集集团企业标准Q/CIMC 40109—2008集装箱钢材表面处理及检验Preparations and Tests for Steel Surfaces of Freight Containers中国国际海运集装箱(集团)股份有限公司发布目 次前 言 (II)1 范围 (1)2 规范性引用文件 (1)3 集装箱钢材表面处理的一般要求 (1)4 钢材表面处理工艺 (1)5 表面处理的检验 (2)前 言为规范和统一集装箱钢材表面处理的工艺、要求、检验标准和方法,有利于箱厂进行生产和现场质量控制,提高和稳定产品质量,特制订本标准。
本标准为推荐性标准。
本标准起草单位:中集集团干箱技术中心。
本标准起草人:金菁、何思东本标准由中集集团技术管理部审核批准并归口管理,由集团及各企业体系主管部门进行实施监督。
集装箱钢材表面处理及检验1 范围本标准规定了通用集装箱常用钢材表面处理的工艺和要求,以及对表面处理质量进行检验的标准和方法。
2 规范性引用文件下列文件中的条款通过本标准的引用而成为本标准的条款。
凡是注日期的引用文件,其随后所有的修改单(不包括勘误的内容)或修订版均不适用于本标准,然而,鼓励根据本标准达成协议的各方研究是否可使用这些文件的最新版本。
凡是不注日期的引用文件,其最新版本适用于本标准。
IS0 8501-1 涂装前钢材表面处理一表面清洁度的目视评定,第1部分:未涂装钢材和全面清除原有涂层后的钢材的锈蚀等级和除锈等级IS0 8502-3 涂装前钢材表面处理一表面清洁度的评定试验,第3部分:涂装前钢材表面的灰尘评定(压敏胶带法)IS0 8503-1 涂装前钢材表面处理一喷射清理过的钢材表面粗糙度特征第1部分:喷砂处理表面的ISO表面轮廓比较仪的规范和定义IS0 8503-2 涂装前钢材表面处理一喷射清理过的钢材表面粗糙度特征第2部分:喷砂处理表面的定级方法比较方法IS0 8503-4 涂装前钢材表面处理一喷射清理过的钢材表面粗糙度特征第4部分:表面轮廓比较仪的校准方法和表面轮廓的测定方法、触针仪器的方法3 集装箱钢材表面处理的一般要求钢材表面处理质量直接影响到涂膜的寿命,表面杂质会导致涂膜过早失效,表面粗糙度影响油漆与钢材表面的粘着性。
钢铁热处理工艺流程

保温
在达到加热温度后,保持钢铁材料在一定温度范围内一段时间,使材料内部的原子和晶体发生再分布。
5
冷却
保温后,对钢铁材料进行冷却处理,冷却方式包括自然冷却、油冷却、水冷却等。
6
检验
对热处理后的钢铁材料进行质量检验,包括硬度测试、金相组织观察等。
7
包装与入库
合格产品经过包装后入库,等待进一步加工或使用。
钢铁热处理工艺流程
序号
工艺流程
描述1Leabharlann 预处理清洗钢铁材料,去除表面污垢或氧化层,包括化学清洗(酸洗、碱洗)和机械清洗(喷砂、抛光)。
2
切割与机加工
对预处理后的钢铁材料进行切割和机加工,获得所需的形状和尺寸。
3
加热
将钢铁材料加热至预定温度,根据材料种类和性能要求选择适当的加热方式(高频感应加热、盐浴炉加热、电阻加热等)。
涂装通用工艺
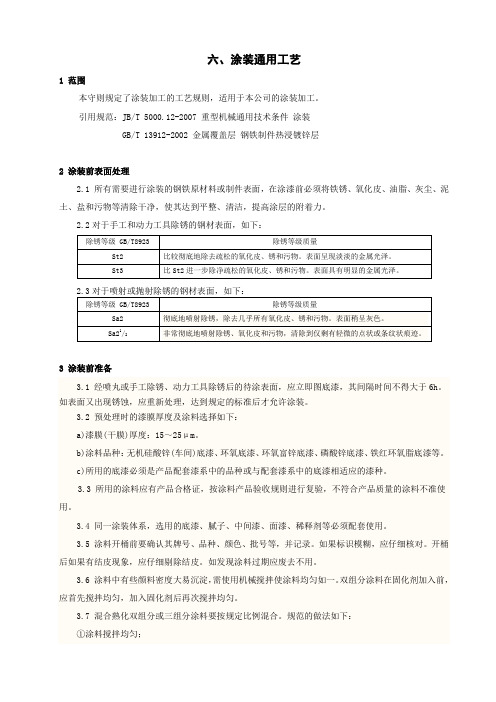
六、涂装通用工艺1 范围本守则规定了涂装加工的工艺规则,适用于本公司的涂装加工。
引用规范:JB/T 5000.12-2007 重型机械通用技术条件涂装GB/T 13912-2002 金属覆盖层钢铁制件热浸镀锌层2 涂装前表面处理2.1 所有需要进行涂装的钢铁原材料或制件表面,在涂漆前必须将铁锈、氧化皮、油脂、灰尘、泥土、盐和污物等清除干净,使其达到平整、清洁,提高涂层的附着力。
2.2对于手工和动力工具除锈的钢材表面,如下:3 涂装前准备3.1 经喷丸或手工除锈、动力工具除锈后的待涂表面,应立即图底漆,其间隔时间不得大于6h。
如表面又出现锈蚀,应重新处理,达到规定的标准后才允许涂装。
3.2 预处理时的漆膜厚度及涂料选择如下:a)漆膜(干膜)厚度:15~25μm。
b)涂料品种:无机硅酸锌(车间)底漆、环氧底漆、环氧富锌底漆、磷酸锌底漆、铁红环氧脂底漆等。
c)所用的底漆必须是产品配套漆系中的品种或与配套漆系中的底漆相适应的漆种。
3.3 所用的涂料应有产品合格证,按涂料产品验收规则进行复验,不符合产品质量的涂料不准使用。
3.4 同一涂装体系,选用的底漆、腻子、中间漆、面漆、稀释剂等必须配套使用。
3.5 涂料开桶前要确认其牌号、品种、颜色、批号等,并记录。
如果标识模糊,应仔细核对。
开桶后如果有结皮现象,应仔细剔除结皮。
如发现涂料过期应废去不用。
3.6 涂料中有些颜料密度大易沉淀,需使用机械搅拌使涂料均匀如一。
双组分涂料在固化剂加入前,应首先搅拌均匀,加入固化剂后再次搅拌均匀。
3.7 混合熟化双组分或三组分涂料要按规定比例混合。
规范的做法如下:①涂料搅拌均匀;②倒入一半固化剂搅匀;③再倒入剩下的固化剂搅匀;④然后必要时加入稀释剂搅匀;⑤按规定放置一定时间进行熟化预反应;注意使用时间不要超过规定。
熟化时间和混合使用时间随温度上升而缩短,须注意厂商说明。
高温季节须避免在太阳下施工。
3.8 稀释涂料通常开桶就可以使用,无需稀释,必须避免习惯性稀释。
钢材预处理0技术方案

一、设备用途本生产线主要用于钢板和各类型钢在加工前对其表面进行抛丸清理、喷漆和烘干。
钢材预处理的目的是为了清除钢材表面的锈蚀、氧化皮和污物,使钢材具有清洁和一定粗糙度的表面,以增强漆膜与钢材表面的附着力,从而提高产品的抗腐蚀能力和表面质量。
该设备一般用于工程机械、矿山机械、化工设备、压力容器、交通车辆、船舶制造及建筑型材等行业,用于提高产品的外观质量和其表面抗腐蚀能力。
二、设备主要技术规格1、处理工件规格:(1)处理钢板板厚:δ=5-60mm宽度: B≤3000mm长度: L=4000~12000mm(2)处理型材高度: H≤300mm长度: L=1600~12000mm2、输送辊道(1)辊道最大负荷: 2t/m(2)输送速度: 0.5-6.5m/min(变频无级调速)处理钢板速度: 1.5-5m/min处理型钢速度: 1-2m/min(3)驱动减速机: BWED2718-121-4(两台)(4)电机功率:4kw×2(5)滚轮直径: 180mm(6)滚轮有效宽度: 3500mm(7)辊道上平面高度:800mm(8)滚轮间距:抛丸室外635mm,抛丸室508mm3、抛丸清理机(1)抛丸器: 8台型号: Q035抛射速度: 72m/s抛丸量: 280kg/min电机功率: 18.5kw(2)纵向螺旋输送机:型号: GX300输送能力: 144t/h驱动装置: BWY22-29-7.5转速: 50rmp功率: 7.5kw(3)横向螺旋输送机:型号: GX300输送能力: 144t/h驱动装置: BWY22-29-5.5转速: 50rmp功率: 5.5kw(4)斗式提升机型号: D450提升能力: 144t/h料斗运行速度: 1.25m/s驱动装置: BWY22-17-11输出转速: 88rpm功率: 11kw(5)丸砂分离器分离能力: 120t/h分离区风速: 4-5m/s通风量: 10000m3/h驱动装置: BWY22-29-4功率: 4kw(6)清丸装置清扫滚直径: 900mm滚刷材质:四氟乙烯(进口刷丝)驱动装置: BLY18-23-3清丸风机: 9-19-6.3A风机功率: 15kw(7)清丸升降装置:提升高度: 500mm驱动电机: XWED63-289-3(电磁制动)电机功率: 3kw4、设备除尘系统(1)除尘通风量: 28000 m3/h(2)除尘器型号: MC-48(3)离心通引风机型号:4-72-8C(4)电机功率: 30kw(5)过滤风速: 0.4~0.8m/min5、自动喷漆装置:(1)喷漆形式:高压无气喷漆喷漆泵型号: 241-84R45:1高压喷涂机压力比: 45:1排量: 13L进气压力: 0.2~0.6MPa数量: 1(2)喷枪喷枪型号: 206-513自动喷枪喷枪到工件距离: 300mm(根据工件高度调整)喷枪数量: 4+1支(一把为手动喷枪,用于补漆或需要手动喷漆)(3)输送小车喷枪移动速度: 20m/min-50m/min(变频调速)数量: 2台(上下各一)(4)风动搅拌器: S-100型(5)G-01型油漆过滤器:25L6、烘干房(1)加热装置:采用燃油加热,30万大卡蒸汽加热器或电烘干加热风机功率: 15kw(2)通风机:结构:内置式耐热风机型号: GW-8C功率: 15kw(3)板链输送机:输送速度: 0.5~6m/min驱动装置: BWEY3322-121-5.5电机功率: 5.5kw7、漆物处理装置(1)风机:型号: B4-72 No8C左90º处理风量: 13000 m3/h风压: 1507Pa功率: 11kw(2)漆雾滤纸: 500×500×358、电气控制:采用控制面板集中控制,9、抛丸清理后的工件表面质量:Sa2.5级 GB8923-8810、喷漆漆膜厚度: 15-25µm(涂料为无机硅酸锌)11、烘干区温度: 40-70℃12、设备最大外形尺寸(长、宽、高):48000mm 、10000mm、10000mm13、年处理钢板量: 100000t14、设备最大功率:约280KW三、工作原理及工艺流程钢板被吊放至上料辊道,由上料辊道直接送到抛丸清理室进行清理,利用抛丸器高速抛射出的弹丸将工件表面进行清理;然后利用弹丸清扫装置(收丸刮板、清丸滚刷、高压吹管等)将工件表面的积丸和灰尘吹扫干净;除锈后的钢材直接进入喷漆室,通过装在上、下喷漆小车上的喷枪,将车间保养底漆涂在工件表面上,再进入烘干室,使钢材表面漆膜达到指干状态后由输出辊道输送出,进行下料。
表面处理工艺标准
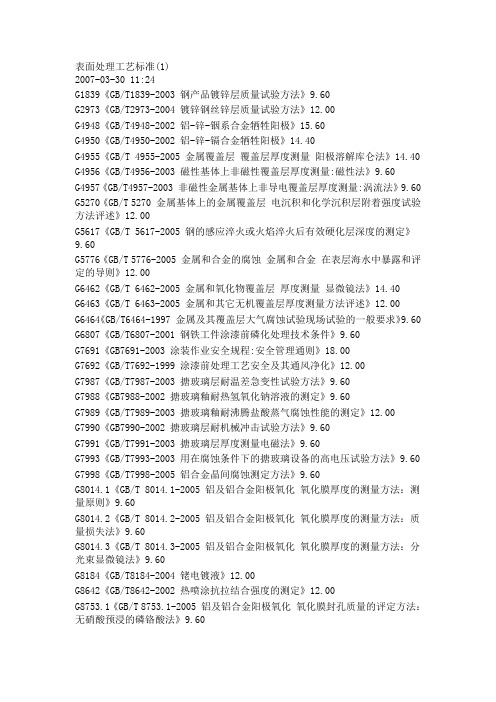
表面处理工艺标准(1)2007-03-30 11:24G1839《GB/T1839-2003 钢产品镀锌层质量试验方法》9.60G2973《GB/T2973-2004 镀锌钢丝锌层质量试验方法》12.00G4948《GB/T4948-2002 铝-锌-铟系合金牺牲阳极》15.60G4950《GB/T4950-2002 铝-锌-镉合金牺牲阳极》14.40G4955《GB/T 4955-2005 金属覆盖层覆盖层厚度测量阳极溶解库仑法》14.40 G4956《GB/T4956-2003 磁性基体上非磁性覆盖层厚度测量:磁性法》9.60G4957《GB/T4957-2003 非磁性金属基体上非导电覆盖层厚度测量:涡流法》9.60 G5270《GB/T 5270 金属基体上的金属覆盖层电沉积和化学沉积层附着强度试验方法评述》12.00G5617《GB/T 5617-2005 钢的感应淬火或火焰淬火后有效硬化层深度的测定》9.60G5776《GB/T 5776-2005 金属和合金的腐蚀金属和合金在表层海水中暴露和评定的导则》12.00G6462《GB/T 6462-2005 金属和氧化物覆盖层厚度测量显微镜法》14.40G6463《GB/T 6463-2005 金属和其它无机覆盖层厚度测量方法评述》12.00G6464《GB/T6464-1997 金属及其覆盖层大气腐蚀试验现场试验的一般要求》9.60 G6807《GB/T6807-2001 钢铁工件涂漆前磷化处理技术条件》9.60G7691《GB7691-2003 涂装作业安全规程:安全管理通则》18.00G7692《GB/T7692-1999 涂漆前处理工艺安全及其通风净化》12.00G7987《GB/T7987-2003 搪玻璃层耐温差急变性试验方法》9.60G7988《GB7988-2002 搪玻璃釉耐热氢氧化钠溶液的测定》9.60G7989《GB/T7989-2003 搪玻璃釉耐沸腾盐酸蒸气腐蚀性能的测定》12.00G7990《GB7990-2002 搪玻璃层耐机械冲击试验方法》9.60G7991《GB/T7991-2003 搪玻璃层厚度测量电磁法》9.60G7993《GB/T7993-2003 用在腐蚀条件下的搪玻璃设备的高电压试验方法》9.60 G7998《GB/T7998-2005 铝合金晶间腐蚀测定方法》9.60G8014.1《GB/T 8014.1-2005 铝及铝合金阳极氧化氧化膜厚度的测量方法:测量原则》9.60G8014.2《GB/T 8014.2-2005 铝及铝合金阳极氧化氧化膜厚度的测量方法:质量损失法》9.60G8014.3《GB/T 8014.3-2005 铝及铝合金阳极氧化氧化膜厚度的测量方法:分光束显微镜法》9.60G8184《GB/T8184-2004 铑电镀液》12.00G8642《GB/T8642-2002 热喷涂抗拉结合强度的测定》12.00G8753.1《GB/T 8753.1-2005 铝及铝合金阳极氧化氧化膜封孔质量的评定方法:无硝酸预浸的磷铬酸法》9.60G8753.2《GB/T 8753.2-2005 铝及铝合金阳极氧化氧化膜封孔质量的评定方法:硝酸预浸的磷铬酸法》9.60G8753.3《GB/T 8753.3-2005 铝及铝合金阳极氧化氧化膜封孔质量的评定方法:导纳法》9.60G8753.4《GB/T 8753.4-2005 铝及铝合金阳极氧化氧化膜封孔质量的评定方法:酸处理后的染色斑点法》9.60G8923《GB8923-1988 涂装前钢材表面锈蚀等级和除锈等级》18.00G9276《GB/T9276-1996 涂层自然气候嚗露试验方法》12.00G9791《GB/T9791-2003 锌、镉、铝-锌合金和锌-铝合金的铬酸盐转化膜试验方法》12.00G9792《GB/T9792-2003 金属材料上的转化膜:单位面积上膜层质量的测定》12.00G9793《GB/T9793-1997 金属和其它无机覆盖层热喷涂锌、铝及其它合金》9.60G9797《GB/T 9797-2005 金属覆盖层镍+铬和铜+镍+铬电镀层》15.60G9798《GB/T 9798-2005 金属覆盖层镍电沉积层》14.40G9799《GB/T9799-1997 金属覆盖层钢铁上的锌电镀层》9.60G9989《GB/T9989-2005 搪瓷耐室温柠檬酸性能试验方法》9.60G11164《GB/T11164-1999 真空镀膜设备通用技术条件》9.60G11375《GB11375-1999 金属和其它无机覆盖层热噴涂操作安全》14.40G11376《GB/T11376-1997 金属的磷酸盐转化膜》12.00G11378《GB/T 11378-2005 金属覆盖层覆盖层厚度测量轮廓仪法》12.00G12334《GB/T12334-2001 金属和其它非有机覆盖层关于厚度测量的定义和一般原则》9.60G12305.6《GB/T12305.6-1997 金属覆盖层金和金合金电镀层:残留盐的测定》7.20G12306《GB/T12306、12307.1~2-1990 金属覆盖层工程用银和银合金电镀层》14.40G12307.3《GB/T12307.3-1997 金属覆盖层银和银合金电镀层:残留盐的测定》7.20G12599《GB/T12599-2002 金属覆盖层锡电镀层技术规范和试验方法》14.40G12600《GB/T 12600-2005 金属覆盖层塑料上镍+铬电镀层》15.60G12607《GB/T12607-2003 热喷涂涂层命名方法》9.60G12608《GB/T12608-2003 热喷涂火焰和电弧喷涂用线材、棒材和芯材分类和供货技术条件》14.40G12609《GB/T 12609-2005 电沉积金属覆盖层和相关精饰计数检验抽样程序》14.40G12612《GB/T 12612-2005 多功能钢铁表面处理液通用技术条件》12.00G13912《GB/T13912-2002 金色覆盖层钢铁制品热镀锌层技术要求及试验方法》15.60G14907《GB/T14907-2002 钢结构防火涂料》14.40G15519《GB/T15519-2002 化学转化膜钢铁黑色氧化膜和试验方法》12.00G15970.2《GB/T15970.2-2000 金属和合金的腐蚀:弯梁试样的制备和应用》9.60G15970.4《GB/T15970.4-2000 金属和合金的腐蚀:单轴加载拉伸试样的制备》7.20G15970.5《GB/T15970.5-1998 金属和合金的腐蚀:C型环试样的制备和应用》12.00G15970.6《GB/T15970.6-1998 金属和合金的腐蚀:预裂纹试样的制备和应用》9.60G15970.7《GB/T15970.7-2000 金属和合金的腐蚀:慢应变速率试验》9.60G15970.8《GB/T 15970.8-2005 金属和合金的腐蚀应力腐蚀试验:焊接试样的制备和应用》15.60G16545《GB/T16545-1996 金属和合金腐蚀试样上腐蚀产物的清除》 7.20G16744《GB/T16744-1997 热喷涂自熔合金涂层》9.60G16744《GB/T16744-2002 热喷涂自熔合金喷涂与重熔》12.00G16745《GB/T16745-1997 金属覆盖层产品钎焊性的标准试验方法》7.20G16921《GB/T 16921-2005 金属覆盖层覆盖层厚度测量 X射线光谱法》15.60 G17460《GB/T17460-1998 化学转化膜铝及铝合金上漂洗和不漂洗铬酸盐转化膜》9.60G17461《GB/T17461-1998 金属覆盖层:锡-铅合金电镀层》9.60G17462《GB/T17462-1998 金属覆盖层:锡-镍合金电镀层》9.60G17720《GB/T17720-1999 金属覆盖层:孔隙率试验评述》19.20G17721《GB/T17721-1999 金属覆盖层:孔隙率试验铁试剂试验》7.20G17722《GB/T17722-1999 金属覆盖层厚度的扫描电镜测量方法》7.20G17723《GB/T17723-1999 黄金制品镀层成分的X射线能谱测量方法》7.20G17731《GB/T17731-1999 镁合金牺牲阳极》7.20G17750《GB17750-1999 涂装作业安全规程浸涂工艺安全》12.00G17754《GB/T17754-1999 摩擦学术语》72.00G17848《GB/T17848-1999 牺牲阳极电化学性能试验方法》9.60G17849《GB/T17849-1999 涂覆涂料前钢材表面处理喷射清理用非金属磨料的试验方法》9.60G17850.1《GB/T17850.1-2002 涂覆涂料前钢材表面处理喷射清理用非金属磨料的技术要求:导则和分类》9.60G17850.3《GB/T17850.3-1999 涂覆涂料前钢材表面处理喷射清理用非金属磨料技术要求:铜精炼渣》7.20G18179《GB/T18179-2000 金属覆盖层孔隙率试验:潮湿硫试验》9.60G18226《GB/T18226-2000 高速公路交通工程钢构件防腐技术条件》9.60G18570.2《GB/T18570.2-2001 涂覆涂料前钢材表面处理:清理过的表面上氯化物的实验室测定》9.60G18570.3《GB/T 18570.3-2005 涂覆涂料前钢材表面处理:涂覆涂料前钢材表面的灰尘评定(压敏粘带法)》12.00G18570.4《GB/T18570.4-2001 涂覆涂料前钢材表面处理:涂覆涂料前凝露可能性的评定导则》16.80G18570.5《GB/T 18570.5-2005 涂覆涂料前钢材表面处理:涂覆涂料前钢材表面的氯化物测定(离子探测管法)》9.60G18570.6《GB/T 18570.6-2005 涂覆涂料前钢材表面处理:可溶性杂质的取样Bresle法》12.00G18570.8《GB/T 18570.8-2005 涂覆涂料前钢材表面处理:湿气的现场折射测定法》12.00G18570.9《GB/T 18570.9-2005 涂覆涂料前钢材表面处理:水溶性盐的现场电导率测定法》9.60G18570.10《GB/T 18570.10-2005 涂覆涂料前钢材表面处理:水溶性氯化物的现场滴定测定法》9.60G18590《GB/T18590-2001 金属和合金的腐蚀点蚀评定方法》14.40G18592《GB/T18592-2001 金属覆盖层钢铁制品热浸镀铝技术条件》16.80G18593《GB/T18593-2001 熔融结合环氧粉末涂料的防腐蚀涂装》14.40G18681《GB/T18681-2002 热喷涂:低压等离子喷涂镍-钴-铬-铝-钇-钽合金涂层》12.00G18682《GB/T18682-2002 物理气相沉积TiN薄膜技术条件》18.00G18684《GB/T18684-2002 锌铬涂层技术要求》12.00G18719《GB/T18719-2002 热喷涂术语分类》15.60G18838.1《GB/T18838.1-2002 涂覆涂料前钢材表面处理:导则和分类》9.60G18839.1《GB/T18839.1-2002 涂覆涂料前钢材表面处理:表面处理方法总则》9.60G18839.2《GB/T18839.2-2002 涂覆涂料前钢材表面处理:磨料喷射清理》14.40G18839.3《GB/T18839.3-2002 涂覆涂料前钢材表面处理:手工和动力工具清理》9.60G18847《GB/T18847-2002 聚氯乙烯覆膜金属板》15.60G19291《GB/T19291-2003 金属和合金的腐蚀腐蚀试验一般原则》12.00G19292.1《GB/T19292.1-2003 金属和合金的腐蚀:大气腐蚀性分类》14.40G19292.2《GB/T19292.2-2003 金属和合金的腐蚀:大气腐蚀性腐蚀等级的指导值》9.60G19292.3《GB/T19292.3-2003 金属和合金的腐蚀:大气腐蚀性污染物的测量》14.40G19292.4《GB/T19292.4-2003 金属和合金的腐蚀:用于评估腐蚀性的标准试样的腐蚀速率的测定》9.60G19349《GB/T19349-2003 金属和其他无机覆盖层;为减少氢脆危险的钢铁预处理》9.60G19350《GB/T19350-2003 金属和其他无机覆盖层;为减少氢脆危险的涂覆后钢铁的处理》9.60G19351《GB/T19351-2003 金属基体覆盖层孔隙率的测定:硝酸蒸汽试验》12.00G19352.1《GB/T19352.1-2003 热喷涂热喷涂结构的质量要求第1部分:选择和使用指南》12.00 G19352.2《GB/T19352.2-2003 热喷涂热喷涂结构的质量要求第2部分:全面的质量要求》12.00G19352.3《GB/T19352.3-2003 热喷涂热喷涂结构的质量要求第2部分:标准的质量要求》12.00 G19352.4《GB/T19352.4-2003 热喷涂热喷涂结构的质量要求第2部分:基本的质量要求》12.00 G19353《GB/T19353-2003 搪玻璃釉密闭系统中的腐蚀试验》12.00G19354《GB/T19354-2003 铝搪瓷在电解液作用下铝上瓷层密着性的测定》9.60G19355《GB/T19355-2003 钢铁结构耐腐蚀防护:锌和铝覆盖层指南》20.40G19356《GB/T19356-2003 热喷涂:粉末成份和供货技术条件》15.60G19502《GB/T19502-2004 表面化学分析辉光放电发射光谱方法通则》12.00G19745《GB/T 19745-2005 人造低浓度污染气氛中的腐蚀试验》12.00G19746《GB/T 19746-2005 金属和合金的腐蚀盐溶液周浸试验》14.40G19747《GB/T 19747-2005 金属和合金的腐蚀双金属室外暴露腐蚀试验》14.40G19816.1《GB/T 19816.1-2005 涂覆涂料前钢材表面处理喷射清理用金属磨料的试验方法:抽样》12.00G19816.2《GB/T 19816.2-2005 涂覆涂料前钢材表面处理喷射清理用金属磨料:颗粒尺寸分布的测定》9.60G19816.3《GB/T 19816.3-2005 涂覆涂料前钢材表面处理喷射清理用金属磨料的试验方法:硬度的测定》9.60G19816.4《GB/T 19816.4-2005 涂覆涂料前钢材表面处理喷射清理用金属磨料的试验方法:表观密度的测定》9.60G19816.5《GB/T 19816.5-2005 涂覆涂料前钢材表面处理:缺陷颗粒百分比和微结构的测定》9.60 G199816.6《GB/T 19816.6-2005 涂覆涂料前钢材表面处理:外来杂质的测定》9.60G199816.7《GB/T 19816.7-2005 涂覆涂料前钢材表面处理:含水量的测定》9.60G19822《GB/T 19822-2005 铝及铝合金硬质阳极氧化膜规范》15.60G19823《GB/T 19823-2005 热喷涂工程零件热喷涂涂层的应用步骤》12.00G19824《GB/T 19824-2005 热喷涂热喷涂操作人员考核要求》16.80G20015《GB/T 20015-2005 电镀镍、自催化镀镍、电镀铬及最后精饰自动控制喷丸硬化前处理》20.40G20016《GB/T 20016-2005 金属和其它无机覆盖层不锈钢部件平整和钝化的电抛光法》12.00 G20017《GB/T 20017-2005 金属和其它无机覆盖层单位面积质量的测定重量法和化学分析法评述》15.60G20018《GB/T 20018-2005 金属与非金属覆盖层覆盖层厚度测量β射线背散射法》14.40G20019《GB/T 20019-2005 热喷涂热喷涂设备的验收检查》14.40GJ480A《GJB480A-1997 金属覆镀和化学覆盖工艺质量控制要求》9.60GJ594A《GJB594A-2000 金属覆盖层和化学覆盖层选择原则与厚度系列》30.00QJ450A《QJ 450A-1996 金属镀覆层厚度系列与选择原则》21.60QJ2842《QJ2842-1996 电解加工通用技术条件》7.20QJ2853《QJ2853-1996 钛合金阳极氧化膜层技术条件》7.20QJ2854《QJ2854-1996 钛合金阳极氧化工艺规范》9.60QJ2855《QJ2855-1996 锡锌合金镀层技术条件》7.20QJ2856《QJ2856-1996 锡锌合金镀层工艺规范》9.60QJ2857《QJ2857-1996 锡锌合金镀覆溶液分析方法》7.20QJ2907《QJ2907-1997 铝合金胶接前磷酸阳极氧化膜层技术条件》7.20 QJ2908《QJ2908-1997 铝合金胶接前磷酸阳极氧化膜层工艺规范》7.20 QJ2909《QJ2909-1997 铌合金化学酸洗技术条件》6.00QJ2910《QJ2910-1997 铌合金化学酸洗工艺规范》7.20QJ2921《QJ2921-1997 锌镀层、镉镀层抗腐蚀性技术要求》9.60QJ2973《QJ2973-1997 铝合金化学砂面处理工艺规范》9.60QJ3131《QJ 3131-2001 热处理常用槽液技术条件》10.80HB6-66《HB 6-66-2003 航空仪表涂层代号及选用》 14.40HB102《HB/Z 102-2000 机载设备“三防”涂层涂漆工艺》9.60H233《HB/Z233-1993 铝及铝合金硫酸阳极氧化工艺》12.00HB236《HB/Z236-1993 电镀铅锡合金工艺》9.60H237《HB/Z237-1993 铝及铝合金硬质阳极氧化工艺》12.00H265《HB/Z265-1994 钛合金紧固件离子镀铝工艺》7.20H294《HB/Z294-1996 干膜润滑剂涂覆工艺》7.20H314《HB/Z314-1998 钛合金电解加工》12.00H318《HB/Z318-1998 镀覆前削除应力和镀覆后除氢处理规范》7.20H335《HB/Z335-1999 紧固件二硫化钼干膜润滑剂涂覆工艺》7.20H337《HB/Z337-1999 铝合金化学转化溶液分析方法》7.20H338《HB/Z338.1~2-1999 铝合金绝缘阳极氧化溶液分析方法》9.60H339《HB/Z339.1~2-1999 铝合金铬酸阳极氧化溶液分析方法》9.60H344《HB/Z344-2001 钛合金酸洗工艺及质量检验》9.60H347《HB/Z347-2002 钛及钛合金阳极氧化工艺及质量检验》9.60H5005《HB/Z 5005-2004 铝合金零、部件涂漆工艺》9.60H5034《HB5034-1995 零(组)件镀覆前质量要求》7.20H5036《HB5036-1992 镉镀层质量检验》 7.20H5037《HB5037-1992 铜镀层质量检验》7.20H5039《HB5039-1992 黑镍镀层质量检验》9.60H5041《HB5041-1992 铬镀层质量检验》7.20H5042《HB5042-1992 装饰铬镀层质量检验》7.20H5043《HB5043-1992 涨圈松孔铬镀层质量检验》9.60H5044《HB5044-1992 汽缸松孔铬镀层质量检验》9.60H5045《HB5045-1992 黑铬镀层质量检验》9.60H5046《HB5046-1992 锡镀层质量检验》7.20H5049《HB5049-1993 铅锡合金镀层质量检验》9.60H5051《HB5051-1992 银镀层质量检验》7.20H5055《HB5055-1992 铝及铝合金硫酸阳极氧化膜层质量检验》9.60H5057《HB5057-1992 铝及铝合金硬质阳极氧化膜层质量检验》7.20H5062《HB5062-1996 钢铁零件化学氧化膜层质量检验》7.20H5063《HB5063-1996 钢铁零件磷化膜层质量检验》9.60H5068《HB/Z5068-1992 电镀锌、电镀镉工艺》14.40H5069《HB/Z5069-1992 电镀铜工艺》9.60H5071《HB/Z 5071-2004 化学镀镍工艺及质量检验》14.40H5073《HG5073-1993 电镀锡工艺》12.00H5074《HG5074-1993 电镀银工艺》14.40H5076《HG5076-1993 铝及铝合金绝缘阳极氧化工艺》9.60H5079《HB/Z5079-1996 钢铁零件化学氧化工艺》9.60H5080《HG5080-1996 钢铁零件磷化工艺》9.60H5083《HB/Z5083-2001 金属镀覆和化学覆盖溶液分析用试剂》21.60H5084《HB/Z 5084.1~6-2000 氰化电镀锌溶液分析方法》12.00H5085《HG5085.1~8-1999 氰化电镀镉溶液分析方法》18.00H5086《HB/Z 5086.1~9-2000 氰化电镀铜溶液分析方法》18.00H5087《HB/Z 5087.1~7-2004 酸性电镀铜溶液分析方法》30.00H5088《HG5088.1~6-1999 电镀镍溶液分析方法》14.40H5090《HB/Z5090.1~.3-2001 化学镀镍溶液分析方法》9.60H5091《HG5091.1~6-1999 电镀铬溶液分析方法》14.40H5092《HB/Z5092.1~4-2001 电镀黑铬溶液分析方法》9.60H5093《HB/Z 5093.1~7-2000 碱性电镀锡溶液分析方法》14.40H5094《HB/Z 5094.1~4-2004 酸性电镀锡溶液分析方法》14.40H5095《HB/Z 5095.13-2004 氰化电镀黄铜溶液分析方法》12.00H5096《HB/Z 5096.1~2-2004 电镀铅溶液分析方法》9.60H5099《HB/Z 5099.1~8-2000 电镀银溶液分析方法》18.00H5104《HG5104.1~3-1999 铝合金硫酸阳极氧化溶液分析方法》9.60H5105《HB/Z 5105.1~3-2000 电化学抛光溶液分析方法》9.60H5108《HG5108.1~3-1999 磷化溶液分析方法》9.60H5109《HB/Z5109.1~16-2001 钝化溶液分析方法》30.00H5110《HB/Z 5110.1~4-2000 电化学除油及化学除油溶液分析方法》12.00 HB5258《HB5258-2000 钢及高温合金的抗氧化性测定试验方法》12.00H5453《HB5453-2004 铝合金化学铣切保护涂料》9.60H5335《HB5335-1994 金属镀覆盖和化学覆盖工艺质量控制》9.60H7054《HB7054-1994 钛合金紧固件离子镀铝层质量检验》7.20H7056《HB 7056.1~4-2004 干膜润滑剂试验方法》19.20H7269《HB7269-1996 热喷涂涂层质量检验》6.00H7236《HB7236-1995 热喷涂封严涂层质量检验》9.60H7479《HB7479-1996 铝合金表面缺陷的修复》6.00H7627《HB7627-1997 爆炸喷涂碳化钨、碳化铬耐磨涂层质量检验》9.60H7740《HB 7740-2004 燃气热腐蚀试验方法》9.60H7751《HB 7751-2004 爆炸喷涂涂层结合强度试验方法》9.60WJ2607《WJ 2607-2003 兵器产品表面化学处理与电化学氧化处理膜层通用规范》12.00 WJ2610《WJ 2610-2003 兵器产品表面涂漆层通用规范》9.60YB9231《YB/T9231-1998 钢筋阻锈剂使用技术规程》12.00J3206《JB/T3206-1999 防锈油脂加速凝露腐蚀试验方法》6.00J3998《JB/T3998-1999 涂料流平性涂刮测定法》12.00J4050《JB/T4050.1~2-1999 气相防锈油》12.00J4051《JB/T4051.1~2-1999 气相防锈纸》12.00J4108《JB/T4108-1999 热喷涂设备分类及型号编制方法》12.00J4216《JB/T4216-1999 防锈油膜抗热流失性试验方法》6.00J4323.1《JB/T4323.1-1999 水基金属清洗剂技术条件》6.00J4323.2《JB/T4323.2-1999 水基金属清洗剂试验方法》12.00J6922《JB/T6922-2004 真空蒸发镀膜设备》 12.00J7501《JB/T7501-1994 湿热环境典型机械产品有机涂层技术条件》 9.60J7502《JB/T7502-1994 离子镀前零件表面质量控制技术要求》7.20J7504《JB/T7504-1994 静电喷涂装备技术条件》12.00J7505《JB/T7505-1994 离子镀术语》7.20J7507《JB/T7507-1994 刷镀通用技术规范》12.00J7508《JB/T7508-1994 光亮镀添加剂技术条件》12.00J7509《JB/T7509-1994 热喷涂涂层孔隙率试验方法铁试剂法》7.20J7558《JB/T7558-1994 摩擦学术语》72.00J7702《JB/T7702-1995 金属基体上金属和非有机覆盖层盐水滴腐蚀试验》7.20J7703《JB/T7703-1995 热喷涂陶瓷涂层技术条件》12.00J7704《JB/T7704.1~6-1995 电镀溶液试验方法》24.00J7706《JB/T7706-1995 有机涂料涂刷通用技术规范》9.60J7707《JB/T7707-1995 离子镀硬膜厚度试验方法球磨法》6.00J7708《JB/T7708-1995 金属热变形用保护润滑剂技术条件》12.00J8424《JB/T8424-1996 金属覆盖层和有机涂层天然海水腐蚀试验方法》6.00J8425《JB/T8425-1996 铁基喷涂粉末中铬、镍钼和钒的X射线荧光光谱分析方法》6.00 J8426《JB/T8426-1996 金属覆盖层镍-磷合金镀层X射线衍射试验方法》12.00J8427《JB/T8427-1996 钢结构腐蚀防护热喷涂锌铝及其合金涂层》12.00J8554《JB/T8554-1997 气相沉积薄膜与基体附着力的划痕试验法》6.00J8595《JB/T8595-1997 机械产品表面防护层分等分级》38.40J8695《JB/T8695-1998 无气喷涂机》12.00J8926《JB/T8926-1999 火焰喷钼涂层的检验方法》6.00J8927《JB/T8927-1999 铝及铝合金等离子体有机涂层》6.00J8928《JB/T8928-1999 钢铁制件机械镀锌》12.00J8945《JB/T8945-1999 真空溅射镀膜设备》6.00J8946《JB/T8946-1999 真空离子镀膜设备》6.00J9188《JB/T9188-1999 高压无气喷涂典型工艺》6.00J9480《JB/T9480-1999 铝及铝合金阳极氧化膜封闭质量的评定方法》9.60J10174《JB/T10174-1999 钢铁零件强化喷丸的质量检验方法》14.40J10240《JB/T10240-2001 静电粉末涂装设备》14.40J10241《JB/T10241-2001 金属覆盖层装饰性多色彩组合电镀层》12.00J10242《JB/T10242-2001 阴极电泳涂装通用技术规范》33.60J10339《JB/T10339-2002 光亮镀锌添加剂技术条件》14.40J10394.1《JB/T10394.1-2002 涂装设备通用技术条件第1部分:钣金件》14.40 J10394.2《JB/T10394.2-2002 涂装设备通用技术条件第2部分:焊接件》14.40 J10394.3《JB/T10394.3-2002 涂装设备通用技术条件第3部分:涂层》14.40J10394.4《JB/T10394.4-2002 涂装设备通用技术条件第4部分:安装》14.40J10413《JB/T 10413-2005 喷漆室》 12.00J10448《JB/T 10448-2005 钢铁构件固体渗铝工艺及质量检验》 18.00J10458《JB/T10458-2004 机械设备抗高温氧化涂层技术条件》 12.00J53021《JB/T53021-1999 真空镀膜设备产品质量分等》12.00SH3022《SH3022-1999 石油化工设备和管道涂料防腐蚀设计规范》48.00SJ10537《SJ/T10537-1994 涂料涂覆典型工艺》21.60SJ10674《SJ/T10674-1995 涂料涂覆通用技术条件》12.00SJ11131《SJ/T11131-1997 蒸发镀膜设备基本参数系列》7.20SJ11185《SJ/T11185-1998 蒸发镀膜设备通用规范》9.60SJ20129《SJ/T20129-1992 金属镀覆层厚度测量方法》24.00SJ20130《SJ/T20130-1992 金属镀覆层附着强度试验方法》9.60SJ20146《SJ/T20146-1992 银电镀层总规范》12.00SJ20147《SJ/T20147.1~2-1992 银和银合金镀覆层测试方法》12.00SJ20443《SJ/T20443-1994 铑电镀层规范》9.60SJ20515《SJ/T20515-1995 金电镀层薄层电阻测试方法》9.60SJ20516《SJ/T20516-1995 金电镀层纯度分析方法》9.60SJ20813《SJ20813-2002 铝和铝合金化学转化膜规范》14.40SJ20817《SJ20817-2002电子设备的涂饰》35.00SJ20818《SJ20818-2002电子设备的金属镀覆与化学处理》39.00SJ20846《SJ20846-2002 电镀用氰化亚金钾规范》12.00SJ20890《SJ 20890-2003 电子装备的处理与涂装》18.00SJ20891《SJ 20891-2003 化学镀镍磷合金层规范》12.00SJ20892《SJ 20892-2003 铝和铝合金阳极氧化膜规范》12.00SJ20893《SJ 20893-2003 不锈钢酸洗与钝化规范》12.00SJ20897《SJ 20897-2003 聚对二甲苯气相沉积涂敷工艺规范》12.00SJ20910《SJ20910-2004 粉末静电涂装通用规范》14.40SJ20912《SJ20912-2004 金属覆盖层低应力镍电镀层》12.00HG2471《HG/T2471、2951-2001 电解槽金属阳极涂层》19.20HG3679《HG/T3679-2000 电解槽金属阳极涂层用三氯化钌》9.60YS456《YS/T456-2003 铝电解槽用干式防渗料》12.00YS480《YS/T 480-2005 铝电解槽能量平衡测试与计算方法四点进电和两点进电预焙阳极铝电解槽》19.20YS481《YS/T 481-2005 铝电解槽能量平衡测试与计算方法五点进电和六点进电预焙阳极铝电解槽》18.00SY0319《SY/T0319-1998 钢制储罐液体环氧涂料内防腐层技术标准》14.40SY0320《SY/T0320-1998 钢质储罐氯磺代聚乙烯外防腐层技术标准》14.40CE01《CECS01:2004 呋喃树脂防腐蚀工程技术规程》18.00CE73《CECS73:1995 二甲苯型不饱和聚酯树脂防腐蚀工程技术规程》18.00Q1131《QB 1131-2005 首饰金覆盖层厚度的规定》12.00Q1132《QB 1132-2005 首饰银覆盖层厚度的规定》9.60A143《ASTM A143/A143M-2003 热浸镀锌结构钢制品防脆化的安全措施和探测脆化用的标准实用规程》(中文版)36.00G1《ASTM G1-2003 腐蚀试样的试样准备、清洁和评定用标准实用规程》(中文版)46.00AG48《ASTM G48-2003 使用三氯化铁溶液做不锈钢及其合金的耐麻点府蚀和抗裂口腐蚀性试验的标准方法》(中文版)57.50。
金属前处理工艺
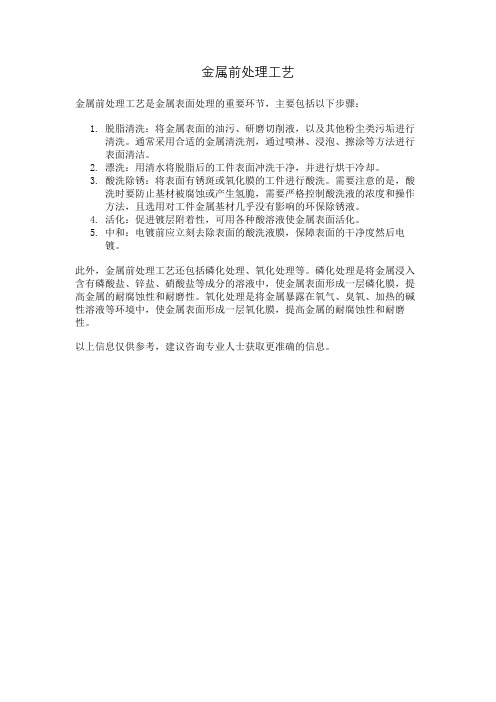
金属前处理工艺
金属前处理工艺是金属表面处理的重要环节,主要包括以下步骤:
1.脱脂清洗:将金属表面的油污、研磨切削液,以及其他粉尘类污垢进行
清洗。
通常采用合适的金属清洗剂,通过喷淋、浸泡、擦涂等方法进行表面清洁。
2.漂洗:用清水将脱脂后的工件表面冲洗干净,并进行烘干冷却。
3.酸洗除锈:将表面有锈斑或氧化膜的工件进行酸洗。
需要注意的是,酸
洗时要防止基材被腐蚀或产生氢脆,需要严格控制酸洗液的浓度和操作方法,且选用对工件金属基材几乎没有影响的环保除锈液。
4.活化:促进镀层附着性,可用各种酸溶液使金属表面活化。
5.中和:电镀前应立刻去除表面的酸洗液膜,保障表面的干净度然后电
镀。
此外,金属前处理工艺还包括磷化处理、氧化处理等。
磷化处理是将金属浸入含有磷酸盐、锌盐、硝酸盐等成分的溶液中,使金属表面形成一层磷化膜,提高金属的耐腐蚀性和耐磨性。
氧化处理是将金属暴露在氧气、臭氧、加热的碱性溶液等环境中,使金属表面形成一层氧化膜,提高金属的耐腐蚀性和耐磨性。
以上信息仅供参考,建议咨询专业人士获取更准确的信息。
散货船驳船船体建造原则工艺

散货船驳船船体建造原则工艺1 目的为了确保各项目建造质量,指导各项目的船体建造和施工,特制定本通用工艺。
2 适用范围本原则工艺规定了本船船体建造的工艺要求及过程,适用于公司内所有船舶产品的建造过程。
3 引用文件相关造船质量标准。
4 材料用于船体建造的钢材是要经过船级社认可的标准品质的普通钢和高强度钢,所有钢料包括铸钢件和锻钢件都要在质量上符合船级社的要求。
普通钢和高强度钢用于主船体的建造,高强度钢和普通钢又可清楚地识别。
没有经过船级社认定的钢材要符合船舶行业标准和建造方的标准。
所有船体构件的尺寸都要基于结构吃水进行计算,并得到船级社的认可。
船级社没有明确要求的构件,其尺寸要符合建造方的标准。
5 船体建造(通用工艺)5.1 钢材表面预处理本船满足PSPC规定,预处理及涂装要求必须符合本船涂装原则工艺;本船所有板材及型材均应进行钢材表面预处理,钢材经预处理后,材料的牌号、钢号及炉批号等应及时跟踪标注。
5.2 放样下料5.2.1 放样间地板应保持平整,其局部不平度,以3米平直尺在任何方向检查,不得超过5mm。
线条宽度不大于0.1mm~0.12mm,线条应光顺连续,粗细均匀,不应有间断和不清楚的地方;5.2.2 船体型线放样时,对型线图中型值的修改,一般不要超过型线图面比例;5.2.3 样板形状准确,边缘与零件展开面的曲线轮廓相符合,其结构牢固,防止变形,制作好的样板应根据其用途不同划上必要的线条与标记,如角尺线、检验线、外板或甲板接缝线、船体中心线、水平检验线、胎架中心线、所属产品名称及图号、零件名称、安装位置、材料规格、号料数量以及加工符号和余量数值等;5.2.4 样条和样杆截面均匀,边缘平直,变形小,各种标记清楚正确;5.2.5 船体理论线见《理论线图》及各分段结构图;5.2.6 下料前,应清除钢材表面的铁锈、油污、检查表面有无缺陷,边缘有无裂缝、分层,如发现钢板表面有大量麻点、氧化铁压入物等表面缺陷时,应及时与检验部门联系,并按《中国造船质量标准》(2005 版)有关规定进行处理,应做好拓印存档工作;5.2.7 零件号料应用记号笔,不得使用油漆及硬质号料工具;5.2.8 严禁不必要的随意切割,切割后产生的缺陷应自行修补完整,不计工时。
船舶涂装通用工艺
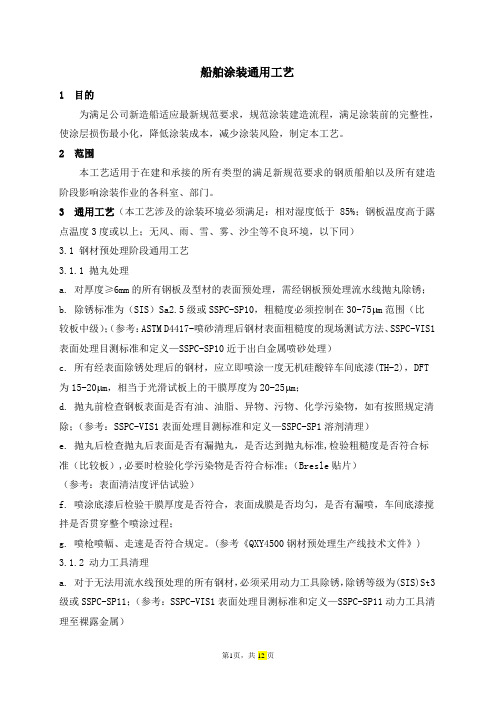
船舶涂装通用工艺1目的为满足公司新造船适应最新规范要求,规范涂装建造流程,满足涂装前的完整性,使涂层损伤最小化,降低涂装成本,减少涂装风险,制定本工艺。
2 范围本工艺适用于在建和承接的所有类型的满足新规范要求的钢质船舶以及所有建造阶段影响涂装作业的各科室、部门。
3 通用工艺(本工艺涉及的涂装环境必须满足:相对湿度低于85%;钢板温度高于露点温度3度或以上;无风、雨、雪、雾、沙尘等不良环境,以下同)3.1 钢材预处理阶段通用工艺3.1.1 抛丸处理a. 对厚度≥6mm的所有钢板及型材的表面预处理,需经钢板预处理流水线抛丸除锈;b. 除锈标准为(SIS)Sa2.5级或SSPC-SP10,粗糙度必须控制在30-75μm范围(比较板中级);(参考:ASTM D4417-喷砂清理后钢材表面粗糙度的现场测试方法、SSPC-VIS1表面处理目测标准和定义—SSPC-SP10近于出白金属喷砂处理)c.所有经表面除锈处理后的钢材,应立即喷涂一度无机硅酸锌车间底漆(TH-2),DFT 为15-20μm,相当于光滑试板上的干膜厚度为20-25μm;d. 抛丸前检查钢板表面是否有油、油脂、异物、污物、化学污染物,如有按照规定清除;(参考:SSPC-VIS1表面处理目测标准和定义—SSPC-SP1溶剂清理)e.抛丸后检查抛丸后表面是否有漏抛丸,是否达到抛丸标准,检验粗糙度是否符合标准(比较板),必要时检验化学污染物是否符合标准;(Bresle贴片)(参考:表面清洁度评估试验)f. 喷涂底漆后检验干膜厚度是否符合,表面成膜是否均匀,是否有漏喷,车间底漆搅拌是否贯穿整个喷涂过程;g.喷枪喷幅、走速是否符合规定。
(参考《QXY4500钢材预处理生产线技术文件》)3.1.2 动力工具清理a.对于无法用流水线预处理的所有钢材,必须采用动力工具除锈,除锈等级为(SIS)St3 级或SSPC-SP11;(参考:SSPC-VIS1表面处理目测标准和定义—SSPC-SP11动力工具清理至裸露金属)b. 动力工具处理前检查钢板表面是否有油、油脂、异物、污物、化学污染物,如有按照规定清除;(参考:SSPC-VIS1表面处理目测标准和定义—SSPC-SP1溶剂清理)c.动力工具处理后检查待涂表面是否达到动力工具处理标准,必要时检验化学污染物是否符合标准;(Bresle贴片)d.动力工具处理后的钢材,应立即喷涂一度无机硅酸锌车间底漆(TH-2),DFT为15-20μm,相当于光滑试板上的干膜厚度为20-25μm;e. 喷涂底漆后检验干膜厚度是否符合,表面成膜是否均匀,是否有漏喷,车间底漆搅拌是否贯穿整个喷涂过程。
cr12调质工艺

CR12调质工艺
CR12是一种通用的冷作模具钢,其调质工艺如下:
1、预备热处理:采用正火处理,将钢材的硬度控制在适当范围,以便于后续的淬火工艺。
正火温度通常在900-920℃,处理时间视具体钢材厚度而定。
2、淬火工艺:将正火后的钢材在850-900℃的高温下进行淬火处理,使钢材内部的碳化物充分溶解,提高钢材的硬度和强度。
3、回火工艺:淬火后的钢材需要进行回火处理,以消除淬火产生的内应力,防止钢材变形和开裂。
回火温度通常在200-300℃,处理时需保持足够的保温时间。
4、精磨:经过调质处理后的钢材需要经过精磨,以达到模具的精度要求。
精磨的精度要求较高,通常需要达到0.01mm的精度。
以上就是CR12模具钢的调质工艺,具体的工艺参数需要根据模具的具体要求和钢材的具体情况进行调整。
钢材的表面预处理与矫正

钢材的矫正
钢材在使用前,其表面常存有不平、弯曲、扭曲、波浪形等缺陷,这 些缺陷使钢材在下料划线时,不可能获得所需要的下料精度,造成零件 尺寸的偏差,从而影响后续工序的顺利进行。
所以,钢材在下料和成形加工之前,必须对钢材进行矫正。
钢材变形的原因:
1.钢板轧制引起的变形 在轧制钢板时,当轧辊沿其长度方向受热不均匀,或者由于轧滚弯曲,轧辊调 整设备失常等各种原因,都将造成轧辊之间的间隙不一致,从而导致钢材在宽度 方向的压缩不均匀,于是钢材的每根纤维沿着长度方向的延伸就不相同。
(2)机械矫正
1)钢板的矫正 多辊矫正机是金属钢板、带材矫平的通用矫平设备。一般矫平辊数目
越多,矫平质量就越好。通常5 ~11辊用于矫中、厚板;11 ~21辊用于 矫平薄板。
矫平机的辊子直径、辊间距和数目是影响矫平效果的主要因素。 钢板矫平条件与被矫材料内的应力度系数有关,应力系数可按下式计 算:
喷丸除锈是利用风管中高速流动的压缩空气的压力使铁丸冲击 金属表明的绣层,依靠铁丸的机械冲击力,将氧化皮和锈斑剥离, 从而达到除锈的目的。一般在喷丸除锈后需立即喷底漆,否则易生 黄绣,影响除锈质量。
下图所示为GYX-nM型钢材预处理装置。它是一种大型喷丸除锈 设备,既可以用于钢板、型钢的表面处理,也可以用于结构部件的 表面处理。
2.运输、存放引起的变形 钢材在运输、存放过程中的不当也会产生局部皱曲。
变形的表现:表面凹凸不平、弯曲、扭曲、波浪形等
钢材的矫正原理: 矫正就是使钢板或工件在外力的作用下产生与原来变形相
反的塑性变形,以消除弯曲、扭曲、皱折、表面不平等变形, 从而获得正确形状的过程。
钢材的任何一种变形都是由于其中一部分纤维比另一部分纤维缩 得短些或是伸得长些所致。
钢铁化学抛光配方

钢铁化学抛光配方钢铁化学抛光是一种常用的表面处理方法,它能够使钢铁表面变得光滑、亮泽,同时还能增强其防腐蚀性能。
化学抛光过程主要是通过化学试剂与钢铁表面的氧化物发生反应,将其去除,从而达到抛光效果。
二、配方成分 1. 主要成分:氢氧化钠(NaOH)、硝酸(HNO3)、硫酸(H2SO4)、磷酸(H3PO4)等。
2. 辅助成分:水(H2O)、硅酸钠(Na2SiO3)、硬脂酸(C17H35COOH)等。
三、配方比例 1. 氢氧化钠(NaOH):适量,用于去除钢铁表面的氧化物。
2. 硝酸(HNO3):适量,用于提高钢铁表面的清洁度。
3. 硫酸(H2SO4):适量,用于增加抛光效果。
4. 磷酸(H3PO4):适量,用于软化钢铁表面,使其更容易被抛光剂侵蚀。
5. 水(H2O):总体比例的70%-80%,用于调节溶液的浓度。
6.硅酸钠(Na2SiO3):适量,用于增加溶液的粘度,使抛光剂更容易附着在钢铁表面。
7. 硬脂酸(C17H35COOH):少量,用于改善抛光剂与钢铁表面的亲和力。
四、操作步骤 1. 将所需量的水加入容器中,加热至适宜温度。
2. 按照比例加入氢氧化钠、硝酸、硫酸和磷酸,搅拌均匀。
3. 加入硅酸钠和硬脂酸,继续搅拌均匀。
4. 将准备好的抛光剂加入溶液中,搅拌均匀。
5. 对钢铁表面进行喷涂或浸泡在溶液中,保持一定时间,直至表面达到理想的抛光效果。
6. 清洗钢铁表面,干燥。
五、注意事项 1. 操作时要佩戴手套和护目镜,防止溶液溅入眼睛或皮肤。
2. 溶液要现用现配,储存时要注意密封,避免与空气接触而变质。
3. 抛光时间不宜过长,以免造成钢铁表面过软,影响使用寿命。
4. 未用完的溶液要及时密封保存。
以上就是钢铁化学抛光的配方及操作步骤,希望对您有所帮助。
钢制压力容器热处理通用工艺规程

钢制压力容器热处理通用工艺规程
1. 预处理:在热处理之前,应对压力容器的表面进行清洗和除油处理,以确保表面的干净和无杂质。
2. 加热:将压力容器置于加热设备中,升温速率一般为200℃/h。
加热温度根据压力容器的材料和规格确定,通常在800℃到1200℃之间。
3. 保温:将压力容器保持在设定的加热温度下一定时间,以保证热处理的效果。
保温时间一般根据厚度和材料类型确定,通常为1到4小时。
4. 冷却:将保温结束的压力容器缓慢冷却至室温。
冷却速率一般为100℃/h,可通过空气冷却或水冷却等方法实现。
5. 温度检测:使用温度计或热处理仪器检测压力容器的冷却温度,确保其达到设定要求。
6. 检验:对热处理后的压力容器进行金相组织检验、硬度测试等,以评估其热处理效果和性能。
7. 完工:对经过热处理并合格的压力容器进行标记和存储,准备下一步的使用或出售。
注意事项:
1. 热处理过程中应确保冷却速率和温度控制的稳定性,以避免产生过多的应力和变形。
2. 不同类型的钢制压力容器可能需要采用不同的热处理工艺,具体工艺规程应根据材料和设计要求来确定。
3. 热处理前应对压力容器进行适当的预处理,以清除表面的污染物和杂质,避免对热处理结果产生影响。
4. 热处理结束后,应对热处理后的压力容器进行必要的检验和测试,确保其达到设计和安全要求。
5. 注意热处理设备和操作人员的安全,避免发生火灾、爆炸等事故。
钢板喷漆前预处理工序
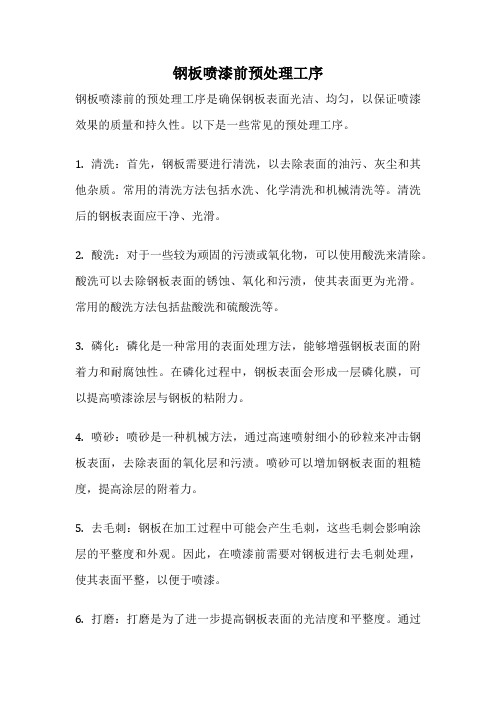
钢板喷漆前预处理工序钢板喷漆前的预处理工序是确保钢板表面光洁、均匀,以保证喷漆效果的质量和持久性。
以下是一些常见的预处理工序。
1. 清洗:首先,钢板需要进行清洗,以去除表面的油污、灰尘和其他杂质。
常用的清洗方法包括水洗、化学清洗和机械清洗等。
清洗后的钢板表面应干净、光滑。
2. 酸洗:对于一些较为顽固的污渍或氧化物,可以使用酸洗来清除。
酸洗可以去除钢板表面的锈蚀、氧化和污渍,使其表面更为光滑。
常用的酸洗方法包括盐酸洗和硫酸洗等。
3. 磷化:磷化是一种常用的表面处理方法,能够增强钢板表面的附着力和耐腐蚀性。
在磷化过程中,钢板表面会形成一层磷化膜,可以提高喷漆涂层与钢板的粘附力。
4. 喷砂:喷砂是一种机械方法,通过高速喷射细小的砂粒来冲击钢板表面,去除表面的氧化层和污渍。
喷砂可以增加钢板表面的粗糙度,提高涂层的附着力。
5. 去毛刺:钢板在加工过程中可能会产生毛刺,这些毛刺会影响涂层的平整度和外观。
因此,在喷漆前需要对钢板进行去毛刺处理,使其表面平整,以便于喷漆。
6. 打磨:打磨是为了进一步提高钢板表面的光洁度和平整度。
通过打磨,可以去除钢板表面的凹凸不平和瑕疵,使其表面更加平滑。
7. 底漆涂覆:在进行喷漆前,通常需要先进行底漆涂覆。
底漆能够填补钢板表面的微小孔洞和不平整,提高涂层的附着力和光泽度。
8. 表面处理:根据具体要求,还可以对钢板进行其他表面处理工序,如防锈处理、防腐处理等。
这些处理方法可以提高钢板的耐腐蚀性和使用寿命。
以上是钢板喷漆前的一些常见预处理工序。
通过这些工序,可以确保钢板表面的光洁度和附着力,从而获得高质量的喷漆效果。
这些工序的严谨执行对于保证喷漆质量的稳定性和持久性非常重要。
查询前处理金属六合一的工艺流程

查询前处理金属六合一的工艺流程前处理金属的六合一工艺流程是指将金属材料进行预处理,以提高其表面质量、粘附性、防腐性和耐久性的工艺。
下面将详细介绍六合一工艺的流程。
第一步:清洗清洗是前处理的第一步,目的是去除金属表面的污垢和油脂,以提高金属的粘附性。
清洗方式包括机械清洗、化学清洗和溶剂清洗。
机械清洗使用刷洗、抛光或喷砂等方式进行;化学清洗采用酸碱等化学溶液进行;溶剂清洗则是利用溶解性较强的溶剂来清洗金属。
第二步:脱脂脱脂是将金属表面的油脂完全去除的过程。
油脂会影响后续工艺的粘附效果,因此脱脂是非常重要的一步。
脱脂方法一般有溶剂脱脂和热解脱脂两种方式。
溶剂脱脂通过将金属浸泡在溶剂中来溶解油脂;热解脱脂则是将金属加热至油脂挥发,然后通过排风系统将油脂排出。
第三步:酸洗酸洗是指用酸溶液将金属表面氧化物、锈蚀物和金属的氧化膜清除的过程。
常用的酸洗溶液有硫酸、盐酸和磷酸等。
酸洗能够改善金属表面的光洁度和净度,提高后续工艺的效果。
第四步:磷化磷化是将金属表面形成一层磷化层的过程。
磷化层能够提高金属的防腐性和涂层的粘附性。
常用的磷化方法有锌磷化和锰磷化。
锌磷化是将金属表面浸泡在含锌盐和磷酸盐的溶液中,通过化学反应形成磷化层;锰磷化则是在锌磷化的基础上添加适量的锰盐。
第五步:活化活化是指用酸或碱溶液将金属表面的磷化层溶解,以去除磷化层上的杂质,提高金属的表面质量。
常用的活化方法有酸活化和碱活化。
酸活化使用稀硫酸或稀盐酸溶液,碱活化则使用稀氢氧化钠或稀氢氧化钾溶液。
第六步:涂覆涂覆是将经过前面工艺处理的金属进行涂层处理的过程。
常用的涂层材料有喷涂、浸涂和电镀等。
涂层能够进一步提高金属的防腐、耐磨和抗氧化性能,同时也能够增加金属的装饰性。
涂覆方式根据不同的需求和金属材料的特性选择。
以上就是前处理金属六合一的工艺流程。
该流程能够提高金属材料的表面质量和耐用性,达到更好的使用效果。
不同的金属材料和工艺要求,可能会略有不同,需要根据具体情况进行调整和改进。
钢制压力容器热处理通用工艺规程范文(二篇)
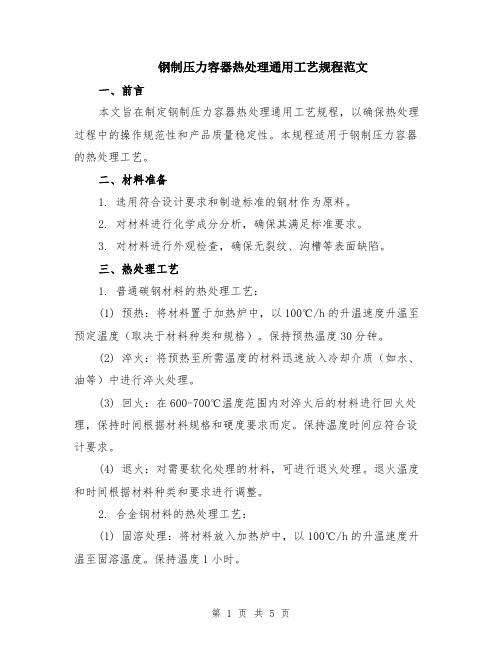
钢制压力容器热处理通用工艺规程范文一、前言本文旨在制定钢制压力容器热处理通用工艺规程,以确保热处理过程中的操作规范性和产品质量稳定性。
本规程适用于钢制压力容器的热处理工艺。
二、材料准备1. 选用符合设计要求和制造标准的钢材作为原料。
2. 对材料进行化学成分分析,确保其满足标准要求。
3. 对材料进行外观检查,确保无裂纹、沟槽等表面缺陷。
三、热处理工艺1. 普通碳钢材料的热处理工艺:(1) 预热:将材料置于加热炉中,以100℃/h的升温速度升温至预定温度(取决于材料种类和规格)。
保持预热温度30分钟。
(2) 淬火:将预热至所需温度的材料迅速放入冷却介质(如水、油等)中进行淬火处理。
(3) 回火:在600-700℃温度范围内对淬火后的材料进行回火处理,保持时间根据材料规格和硬度要求而定。
保持温度时间应符合设计要求。
(4) 退火:对需要软化处理的材料,可进行退火处理。
退火温度和时间根据材料种类和要求进行调整。
2. 合金钢材料的热处理工艺:(1) 固溶处理:将材料放入加热炉中,以100℃/h的升温速度升温至固溶温度。
保持温度1小时。
(2) 淬火:将固溶处理后的材料迅速放入冷却介质(如水、油等)中进行淬火处理。
(3) 回火:在450-600℃温度范围内对淬火后的材料进行回火处理,保持时间根据材料规格和硬度要求而定。
保持温度时间应符合设计要求。
四、操作注意事项1. 操作人员应经过相关培训,熟悉工艺要求和操作规程,严格按照规程进行操作。
2. 加热炉和冷却介质的温度应定期校准,确保温度准确性。
3. 热处理过程中,应定期检查冷却介质的质量,如有杂质应及时更换。
4. 淬火工艺中,应控制冷却介质的冷却速率,以避免材料出现裂纹等缺陷。
5. 温度控制器和计时器的准确性需要定期检查和校准。
五、质量控制1. 热处理后的材料应进行硬度测试和金相组织检查,确保满足标准要求。
2. 对热处理过程进行记录,包括材料种类、规格、加热炉温度、保温时间等重要参数。
JHT E02-2008 集装箱钢材表面处理及检验

JH 中国集装箱行业协会行规JH/T E02-2008集装箱钢材表面处理及检验 Preparation and Tests of Steel Surfaces for Freight Containers2008-8 实施中国集装箱行业协会JH/T E02-2008目次前言 ----------------------------------------------------------------------------------------------------------------------------Ⅰ1 范围 ------------------------------------------------------------------------------------------------------------------------12 规范性引用文件 ---------------------------------------------------------------------------------------------------------13 钢材表面处理的一般要求-----------------------------------------------------------------------------------------------14 表面处理工艺--------------------------------------------------------------------------------------------------------------15 表面处理的检验-----------------------------------------------------------------------------------------------------------2JH/T E02-2008前言根据中国集装箱行业协会工作计划和实际需要修制订本行规 — JH/T E02-2008。
钢结构表面处理及涂装作业

钢结构表面处理及涂装作业指导书编制部门:质量技术部钢结构制造有限公司二0一五年二月二十六日一、适用范围本作业指导书适用于建筑钢结构工程中钢结构的防腐蚀涂层涂装施工。
二、参考标准及规范1、《钢结构工程施工质量验收规范》50205-20012、《涂装前钢材表面锈蚀等级和除锈等级》89233、《钢结构防火涂料通用技术条件》14904、《钢结构防火涂料应用技术规程》24:90三、一般规定1、根据设计和施工图的要求,编制涂装工艺及技术交底等文件并进行技术交底。
技术资料应完整,操作人员经过技术培训。
2、构件成品或半成品,在涂装前表面预处理按设计和施工图规定的除锈等级进行,并达到规定的预处理等级。
3、各种底漆或防锈漆要求最低的除锈等级四、钢构件表面处理(抛丸)要求1、构件在进入抛丸机前应保持干燥且无油污。
抛丸机的抛丸直径为1.5~1.8。
构件的抛丸速度应在设备正常情况下控制在1.4m左右,摩擦试板及高强螺栓接触面的抛丸速度不应大于1.2m。
抛丸后的构件应色泽一致。
2、大型构件采用喷砂表面处理,砂采用石英砂或其它同等效果的材料,颗粒直径为1~4。
构件喷砂时空压机的工作压力应在62,喷砂速度应控制在42,对于摩擦试板及高强螺栓接触面喷砂速度应控制在53、涂装前的构件表面状态,应是在完全去切割边缘毛剌、焊渣和飞溅、不残留切割缺口、焊缝缺口、超标咬边、松散氧化皮、未包角焊和焊缝外形等缺陷,在除锈后若发现上述缺陷,必须在修补合格及表面预处理达到规定的等级并经专检确认合格后方可进行涂装。
4、构件的除锈等级、涂装漆膜厚度及涂装遍数应严格按照单项工程涂装工艺通知单进行。
5、涂装施工的环境应符合如下要求:环境温度宜为5—38。
C。
环境相对湿度不宜大于85%,或者钢材表面不应有结露,涂装后4小时内应保持免受雨淋。
在有雨、雾雪、风沙和较大灰尘时,禁止在户外涂装施工。
6、涂料的确认和贮存涂装前应对涂料名称、型号、颜色进行检查,确认是否与设计规定相符,产品出厂日期是否超过贮存期限,与规定不相符或超过贮存期的涂料不得使用。
船舶涂装通用工艺
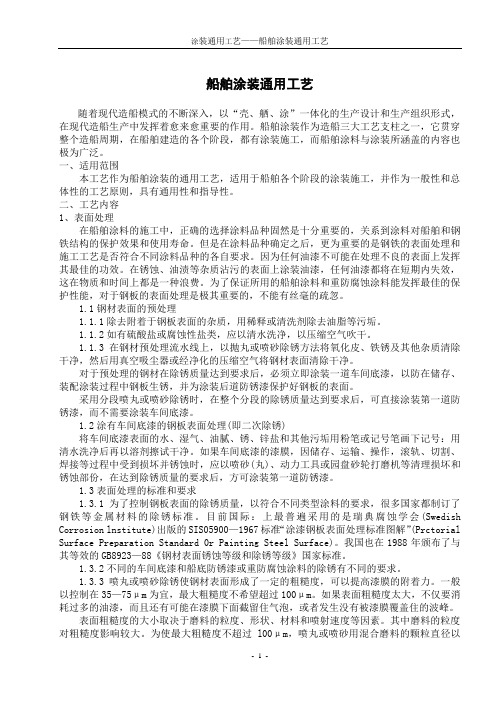
船舶涂装通用工艺随着现代造船模式的不断深入,以“壳、舾、涂”一体化的生产设计和生产组织形式,在现代造船生产中发挥着愈来愈重要的作用。
船舶涂装作为造船三大工艺支柱之一,它贯穿整个造船周期,在船舶建造的各个阶段,都有涂装施工,而船舶涂料与涂装所涵盖的内容也极为广泛。
一、适用范围本工艺作为船舶涂装的通用工艺,适用于船舶各个阶段的涂装施工,并作为一般性和总体性的工艺原则,具有通用性和指导性。
二、工艺内容1、表面处理在船舶涂料的施工中,正确的选择涂料品种固然是十分重要的,关系到涂料对船舶和钢铁结构的保护效果和使用寿命。
但是在涂料品种确定之后,更为重要的是钢铁的表面处理和施工工艺是否符合不同涂料品种的各自要求。
因为任何油漆不可能在处理不良的表面上发挥其最佳的功效。
在锈蚀、油渍等杂质沾污的表面上涂装油漆,任何油漆都将在短期内失效,这在物质和时间上都是一种浪费。
为了保证所用的船舶涂料和重防腐蚀涂料能发挥最佳的保护性能,对于钢板的表面处理是极其重要的,不能有丝毫的疏忽。
1.1钢材表面的预处理1.1.1除去附着于钢板表面的杂质,用稀释或清洗剂除去油脂等污垢。
1.1.2如有硫酸盐或腐蚀性盐类,应以清水洗净,以压缩空气吹干。
1.1.3在钢材预处理流水线上,以抛丸或喷砂除锈方法将氧化皮、铁锈及其他杂质清除干净,然后用真空吸尘器或经净化的压缩空气将钢材表面清除干净。
对于预处理的钢材在除锈质量达到要求后,必须立即涂装一道车间底漆,以防在储存、装配涂装过程中钢板生锈,并为涂装后道防锈漆保护好钢板的表面。
采用分段喷丸或喷砂除锈时,在整个分段的除锈质量达到要求后,可直接涂装第一道防锈漆,而不需要涂装车间底漆。
1.2涂有车间底漆的钢板表面处理(即二次除锈)将车间底漆表面的水、湿气、油腻、锈、锌盐和其他污垢用粉笔或记号笔画下记号:用清水洗净后再以溶剂擦试干净。
如果车间底漆的漆膜,因储存、运输、操作,滚轨、切割、焊接等过程中受到损坏并锈蚀时,应以喷砂(丸)、动力工具或园盘砂轮打磨机等清理损坏和锈蚀部份,在达到除锈质量的要求后,方可涂装第一道防锈漆。
t处理工艺流程

t处理工艺流程
《T处理工艺流程》
T处理工艺是一种广泛应用于金属加工行业的热处理工艺,它可以改善金属材料的物理性能和化学性能,从而提高其机械性能和耐腐蚀性。
T处理工艺流程包括多个步骤,每个步骤都对最终的工艺效果起着重要的作用。
首先,T处理工艺的第一步是预处理。
在这一步中,需要对金属材料进行清洗和去除表面氧化物,以确保后续的处理步骤能够得到良好的效果。
通常,预处理包括碱洗、酸洗和水洗等过程,以确保金属表面得到彻底清洁。
接下来,T处理工艺的第二步是加热。
在加热过程中,金属材料被加热到特定的温度,以改变其物理结构和化学性质。
这一步骤通常需要严格控制加热温度和时间,以确保金属材料能够达到所需的工艺效果。
然后,T处理工艺的第三步是冷却。
在冷却过程中,加热后的金属材料需要在空气或液体介质中快速冷却,以稳定其新的物理结构和化学性质。
这一步骤通常需要根据具体的金属材料和工艺要求来选择合适的冷却方法和速度。
最后,T处理工艺的最后一步是后处理。
在后处理过程中,需要对冷却后的金属材料进行表面处理或其他特殊处理,以进一步改善其性能和外观。
这一步骤通常包括清洗、退火、拉丝、阳极氧化等过程,以确保金属材料能够满足特定的工艺要求。
总的来说,T处理工艺流程是一个复杂而严谨的过程,需要经验丰富的工艺师和先进的设备来保证其成功实施。
通过精心设计和严格控制每个步骤,T处理工艺可以为金属材料带来显著的提升,使其更加适用于各种工程和应用领域。
- 1、下载文档前请自行甄别文档内容的完整性,平台不提供额外的编辑、内容补充、找答案等附加服务。
- 2、"仅部分预览"的文档,不可在线预览部分如存在完整性等问题,可反馈申请退款(可完整预览的文档不适用该条件!)。
- 3、如文档侵犯您的权益,请联系客服反馈,我们会尽快为您处理(人工客服工作时间:9:00-18:30)。
钢材车间预处理通用工艺
一、目的与适用范围
1 范围
1.1本工艺适用于钢材,包括钢板和型材的抛丸预处理流水线。
2 定义
2.1钢材进厂后,在加工前对钢材的原材料进行处理,除去表面的氧化皮和锈蚀,涂上车
间底漆以确保钢材在加工过程中不继续腐蚀,这一阶段的钢材表面处理,称之为钢材的表面预处理。
2.2造船用钢材预处理的方式有抛射磨料处理、喷射磨料处理和酸洗处理三种方式。
其中
要获得高效率的自动化流水作业,目前还只有抛射磨料处理方式。
抛射磨料处理亦称为抛丸处理。
二、工艺内容
1 钢板校平
造船用钢板,在运输过程中或经过长期的堆积后,会产生形变。
形变的钢板在分段落料加工时会影响加工精度,形变严重的钢板将影响船体的线型。
因此,钢板的预处理之前或之后,应对钢板作校平处理。
2 预热
预热是为了在抛丸前将钢板升温,除去表面水分、部分油污,使钢板升温至一定的温度以利于喷漆后的干燥。
预热应使钢板升温至40左右。
升温太低,不利于除去水分、油污,不利于而后喷涂的车间底漆的干燥;升温过高,则多耗能量,又易使车间底漆在干燥过程中产生起泡的弊病。
3 抛丸及磨料
抛丸用于清除钢材表面的氧化皮与锈蚀,并使钢材产生一定的粗糙度。
理想的抛丸处理磨料是钢丸加钢丝段或钢丸加钢砂,前后两者的比例为1:1到1:2范围之内。
4 喷漆
抛丸处理后的钢材表面需立即涂覆车间底漆。
涂漆以自动化方式进行。
5 烘干
钢材喷漆后应进入烘干炉,促使快速干燥以利迅速搬运。
烘干炉可以远红外辐射或蒸汽为热源,不能采用明火直接加热。
烘干炉应设排风装置,防止炉内溶剂气体积聚而引起燃爆事故。
6 抛丸预处理流水线工艺要求
6.1车间底漆一般采用无机硅酸锌涂料。
6.2普通钢板及型材采用灰色的车间底漆,特殊强度的钢材则采用浅绿色车间底漆加以区
分。
6.3钢材在进行预处理前必须采用清洁剂擦洗及高压淡水冲洗等方法去除钢材表面的油
污等杂物(如有任何污物)。
6.4一般厚度介于6mm与40mm之间的钢板,需经钢板预处理流水线抛丸队锈,除锈标
准为ISO8501-1:1988中规定的Sa2.5级(除锈标准均采用ISO标准),粗糙度必须控制在40—70微米范围,相当于ISO8503Medium Grade 至Course Grade的表面粗糙度。
厚度小于6mm或大于40mm的钢板和型材一般采用喷砂处理。
6.5抛丸过程中钢板的走速
在预处理时应根据钢板的不同锈蚀等级来调节钢板的走速。
A级大于3m/min
B级大于2.5m/min
C级大于2m/min
D级按实际要求而定
6.6由于在抛丸过程中,磨料磨擦和破损等原因,磨料会不断的消耗,所以要定期加入新
的磨料来补充,加入量应符合磨料的消耗量。
6.7为了与涂料的运输速度相配及防止过多的变叠层出现,在喷涂时需及时检查喷枪的扇
型面和喷枪速度,如需要应及时更换喷嘴。
6.8涂料的稀释和混合
6.8.1按不同的温度稀释涂料,如15℃时,约加入专用稀释剂8%(±5℃加入±1-2%
的稀释剂)。
6.8.2基料和固化剂必须彻底的分开搅拌,然后慢慢地把固化剂倒入锌粉里,并不断地
搅拌,不能反相进行。
6.8.3在喷涂过程或在停转过程中,涂料必须不断地搅拌,直到用完为止。
6.8.4涂料必须在下列情况下进行施工:
温度范围:0-40℃
相对湿度:必须超过50%(若低于50%,用水雾喷在室内,以增加相对湿度)
6.8.5涂料混合后必须在20小时内(25℃)用完,一旦超过使用时间,则此涂料不能使
用。
6.9加热装置的调节
6.9.1加热装置的调节是按照从加热区域出来的温度而定,钢板温度不能超过40℃(如
果温度过高,将会引起涂料的开裂)。
6.9.2钢板不能放在加热区域内超过4分钟,如果是进行修补,则需待钢板出来后进行
修补,但钢板温度不能超过40℃。
7 车间底漆的修补
7.1钢板或型钢车间底漆漏涂的地方,必须进行修补。
7.2修补前钢板表面必须无油脂,污物等,并且修补前是干燥的。
7.3修补用涂料也必须搅拌,防止锌粉可能沉积在漆桶的底部。
8 磁性铁盘
由于钢板从流水线中出来,涂料不能完全固化,因此必须检查磁性吸铁盘的清洁情况,确保其无油脂、油腻,以防污染已涂好的表面涂层。
9 车间底漆的检验方法
9.1检验车间底漆露底的方法
9.1.1用放大镜观察漆膜表面
9.1.2用100*400的玻璃片喷涂后,对光观察透明度
9.2测量车间底漆膜厚的方法
9.2.1用70*300平整光滑的铁片置于钢板上,喷涂干燥后,测量出其表面上的干燥厚度,
其数值即被认为是钢板表面的漆膜厚度。
9.2.2用干膜测厚仪直接测量干燥后的钢板表面的漆膜厚底,其数值应为真实膜厚的
60%左右。