热处理变形的原因
热处理变形的原因

热处理变形的原因在实际生产中,热处理变形给后续工序,特别是机械加工增加了很多困难,影响了生产效率,因变形过大而导致报废,增加了成本。
变形是热处理比较难以解决的问题,要完全不变形是不可能的,一般是把变形量控制在一定范围内。
一、热处理变形产生的原因钢在热处理的加热、冷却过程中可能会产生变形,甚至开裂,其原因是由于淬火应力的存在。
淬火应力分为热应力和组织应力两种。
由于热应力和组织应力作用,使热处理后零件产生不同残留应力,可能引起变形。
当应力大于材料的屈服强度时变形就会产生,因此,淬火变形还与钢的屈服强度有关,材料塑性变形抗力越大,其变形程度越小。
1.热应力在加热和冷却时由于零件表里有温差存在造成热胀冷缩的不一致而产生热应力。
零件由高温冷却时表面散热快,温度低于心部,因此表面比心部有更大的体积收缩倾向,但受心部阻碍而使表面受拉应力,而心部则受压应力。
表里温差增大应力也增大。
2.组织应力组织应力是因为奥氏体与其转变产物的比容不同,零件的表面和心部或零件各部分之间的组织转变时间不同而产生的。
由于奥氏体比容最小,淬火冷却时必然发生体积增加。
淬火时表面先开始马氏体转变,体积增大,心部仍为奥氏体体积不变。
由于心部阻碍表面体积增大,表面产生压应力,心部产生拉应力。
二、减少和控制热处理变形的方法1.合理选材和提高硬度要求对于形状复杂,截面尺寸相差较大而又要求变形较小的零件,应选择淬透性较好的材料,以便使用较缓和的淬火冷却介质淬火。
对于薄板状精密零件,应选用双向轧制板材,使零件纤维方向对称。
对零件的硬度要求,在满足使用要求前提下,尽量选择下限硬度。
2.正确设计零件零件外形应尽量简单、均匀、结构对称,以免因冷却不均匀,使变形开裂倾向增大。
尽量避免截面尺寸突然变化,减少沟槽和薄边,不要有尖锐棱角。
避免较深的不通孔。
长形零件避免截面呈横梯形。
3.合理安排生产路线,协调冷热加工与热处理的关系对于形状复杂、精度要求高的零件,应在粗、精加工之间进行预先处理,如消除应力、退火等。
钢件热处理容易变形的温度

钢件热处理容易变形的温度全文共四篇示例,供读者参考第一篇示例:钢件热处理是钢材加工中的一种重要工艺,通过加热和冷却来改变钢件的组织结构和性能。
热处理可以使钢件获得理想的硬度、强度和耐磨性,提高其使用性能和寿命。
在进行热处理过程中,钢件很容易发生变形,这给工艺控制和产品质量带来一定的困扰。
钢件热处理容易变形的主要原因有以下几点:1. 温度变化大:钢件在进行热处理时,需要进行高温加热和快速冷却。
由于钢材的热膨胀系数比较大,加热后钢件表面和内部温度会出现较大的差异,导致钢件形变。
2. 冷却速度不均匀:钢件在热处理过程中,冷却速度是影响钢件性能的重要因素之一。
如果冷却速度不均匀,会导致钢件产生内部应力,从而引起变形。
3. 热处理工艺不当:热处理工艺的参数设置不合理,比如加热温度、保温时间、冷却速度等方面没有进行有效控制,会导致钢件变形。
4. 初始应力存在:钢件在进行热处理之前,可能存在一定的残余应力,这些应力在热处理过程中会被释放出来,导致钢件变形。
钢件热处理容易变形的问题严重影响了产品的质量和生产效率,为了有效解决这一问题,可以采取以下措施:2. 合理设计工装:在热处理过程中,采用合理的工装设计,使钢件受力均匀,避免局部受力过大导致变形。
3. 预热处理:对于特殊形状或要求严格的钢件,可以在热处理前进行预热处理,降低残余应力,减少变形的可能性。
4. 热处理后回火处理:在热处理后进行回火处理,可以减少钢件内部应力,提高稳定性,减少变形。
通过以上措施的采取,可以有效降低钢件热处理过程中的变形问题,提高产品的质量和工艺稳定性,为钢件加工行业的发展提供有力支撑。
第二篇示例:钢件热处理是一种常见的工艺,可以通过加热和冷却钢件来改变其物理和化学性质。
在进行热处理过程中,钢件往往会出现变形的现象,这给生产制造过程带来了一定的困扰。
其中一个重要的原因就是温度控制不当。
钢件在热处理过程中容易发生变形的主要原因之一就是温度过高或者温度变化过快。
热处理变形的因素

一,导致热处理变形的因素1, 碳含呈及其对热处理变化呈的影响高碳钢屈服强度的升高,其变形呈要小于中碳钢。
对碳素钢来说,在大多数情况下,以T7A钢的变形呈为最小。
当碳的质呈分数大于0.7%时,多趋向于缩小;但碳的质呈分数小于0.7%时,内径、外径都趋向于膨胀。
碳素钢本身屈服强度相对较低,因而带有内孔(或型腔)类的碳素钢件,变形较大,内孔(或型腔)趋于胀大。
合金钢由于强度较高,Ms点较低,残余奥氏体呈较多,故淬火变形较小,并主要表现为热应力型的变形,其钢件内孔(或型腔)趋于缩小。
因此,在与中碳钢同样条件下淬火时,高碳钢和高合金钢工件往往以内孔收缩为主。
2, 合金元素对热处理变形的影响合金元素对工件热处理变形的影响主要反映在对钢的Ms点和淬透性的影响上。
大多数合金元素,例如,锚、错、硅、镇、铝、硼等,使钢的Ms点下降,残余奥氏体星增多, 减小了钢淬火时的比体积变化和组织应力,因此,减小了工件的淬火变形。
合金元素显著提高钢的淬透性,从而增大了钢的体积变形和组织应力,导致工件热处理变形倾向的增大。
此外,由于合金元素提高钢的淬透性,使临界淬火冷却速度降低,实际生产中,可以采用缓和的淬火介质淬火,从而降低了热应力,减小了工件的热处理变形。
硅对Ms点的影响不大,只对试样变形起缩小作用;铸和机对淬透性和Ms点影响也不大,对工件热处理变形影响较小。
故工业上所谓微变形钢,均含有较多呈的硅、餌、机等合金元素。
3, 原始组织和应力状态对热处理变形的影响工件淬火前的原始组织,例如,碳化物的形态、大小、数呈及分布,合金元素的偏析,锻造和轧制形成的纤维方向都对工件的热处理变形有一定影响。
球状珠光体比片状珠光体比体积大,强度高,所以经过预先球化处理的工件淬火变形相对要小。
对于一些高碳合金工具钢,例如,9Mn2V、CrWMn和GCr15钢的球化等级对其热处理变形开裂和淬火后变形的校正有很大影响,通常以2.5-5级球化组织为宜。
调质处理不仅使工件变形呈的绝对值减小,并使工件的淬火变形更有规律,从而有利于对变形的控制。
薄壁件热处理变形
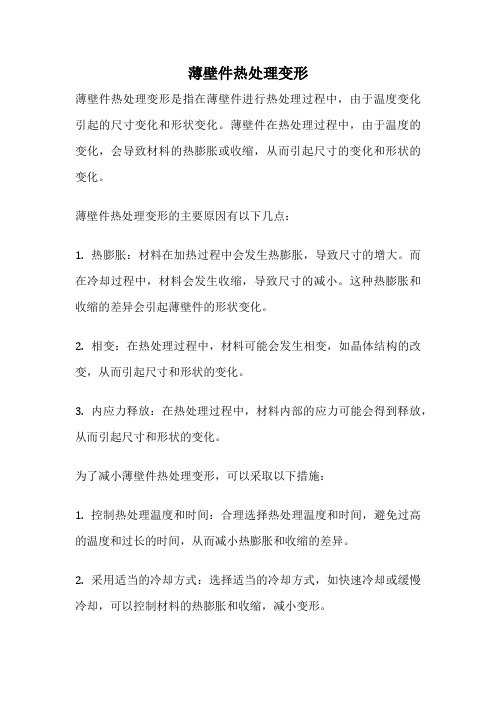
薄壁件热处理变形
薄壁件热处理变形是指在薄壁件进行热处理过程中,由于温度变化引起的尺寸变化和形状变化。
薄壁件在热处理过程中,由于温度的变化,会导致材料的热膨胀或收缩,从而引起尺寸的变化和形状的变化。
薄壁件热处理变形的主要原因有以下几点:
1. 热膨胀:材料在加热过程中会发生热膨胀,导致尺寸的增大。
而在冷却过程中,材料会发生收缩,导致尺寸的减小。
这种热膨胀和收缩的差异会引起薄壁件的形状变化。
2. 相变:在热处理过程中,材料可能会发生相变,如晶体结构的改变,从而引起尺寸和形状的变化。
3. 内应力释放:在热处理过程中,材料内部的应力可能会得到释放,从而引起尺寸和形状的变化。
为了减小薄壁件热处理变形,可以采取以下措施:
1. 控制热处理温度和时间:合理选择热处理温度和时间,避免过高的温度和过长的时间,从而减小热膨胀和收缩的差异。
2. 采用适当的冷却方式:选择适当的冷却方式,如快速冷却或缓慢冷却,可以控制材料的热膨胀和收缩,减小变形。
3. 采用适当的工艺参数:调整热处理的工艺参数,如加热速度、冷却速度等,可以减小薄壁件的变形。
4. 采用适当的夹具和支撑:在热处理过程中,使用适当的夹具和支撑,可以控制薄壁件的形状变化,减小变形。
薄壁件热处理变形是一个复杂的问题,需要综合考虑材料的性质、热处理工艺参数等因素,采取合适的措施来减小变形。
9个影响热处理变形的因素

9个影响热处理变形的因素一、变形的原因钢的变形主要原因是钢中存在内应力或者外部施加的应力。
内应力是因温度分布不均匀或者相变所致,残余应力也是原因之一。
外应力引起的变形主要是由于工件自重而造成的“塌陷”,在特殊情况下也应考虑碰撞被加热的工件,或者夹持工具夹持所引起的凹陷等。
变形包括弹性变形和塑性变形两种。
尺寸变化主要是基于组织转变,故表现出同样的膨胀和收缩,但当工件上有孔穴或者复杂形状工件,则将导致附加的变形。
如果淬火形成大量马氏体则发生膨胀,如果产生大量残余奥氏体则相应的要收缩。
此外,回火时一般发生收缩,而出现二次硬化现象的合金钢则发生膨胀,如果进行深冷处理,则由于残余奥氏体的马氏体化而进一步膨胀,这些组织的比容都随着含碳量的增加而增大,故含碳量增加也使尺寸变化量增大。
二、淬火变形的主要发生时段1.加热过程:工件在加热过程中,由于内应力逐渐释放而产生变形。
2.保温过程:以自重塌陷变形为主,即塌陷弯曲。
3.冷却过程:由于不均匀冷却和组织转变而至变形。
三、加热与变形当加热大型工件时,存在残余应力或者加热不均匀,均可产生变形。
残余应力主要来源于加工过程。
当存在这些应力时,由于随着温度的升高,钢的屈服强度逐渐下降,即使加热很均匀,很轻微的应力也会导致变形。
一般,工件的外缘部位残余应力较高,当温度的上升从外部开始进行时,外缘部位变形较大,残余应力引起的变形包括弹性变形和塑性变形两种。
加热时产生的热应力和想变应力都是导致变形的原因。
加热速度越快、工件尺寸越大、截面变化越大,则加热变形越大。
热应力取决于温度的不均匀分布程度和温度梯度,它们都是导致热膨胀发生差异的原因。
如果热应力高于材料的高温屈服点,则引起塑性变形,这种塑性变形就表现为“变形”。
相变应力主要源于相变的不等时性,即材料一部分发生相变,而其它部分还未发生相变时产生的。
加热时材料的组织转变成奥氏体发生体积收缩时可出现塑性变形。
如果材料的各部分同时发生相同的组织转变,则不产生应力。
201不锈钢热处理变形

201不锈钢热处理变形201不锈钢是一种高强度、耐腐蚀性能优异的不锈钢材料,广泛应用于航空航天、化工、石油、电子等领域。
在使用过程中,不锈钢材料经过热处理会发生一定的变形。
本文将探讨201不锈钢热处理变形的原因及其解决方法。
一、201不锈钢热处理变形的原因热处理是通过改变材料的组织结构和性能来满足特定的使用要求。
201不锈钢在热处理过程中,由于内部应力的释放和晶粒的长大,往往会出现一定程度的变形。
主要原因包括:1. 内应力的释放:在不锈钢材料的加热和冷却过程中,由于热膨胀系数的不同,不同部位的温度变化不一致,导致内部产生应力。
这些内应力在热处理过程中会得到释放,引起材料的变形。
2. 晶粒长大:在热处理过程中,不锈钢材料的晶粒会发生长大,这种长大往往会引起材料的变形。
晶粒长大是因为在高温下,晶界的迁移速度增加,晶粒逐渐长大。
3. 机械应力导致的变形:在热处理过程中,如果材料受到机械应力的作用,也会导致材料的变形。
这种机械应力可以是由于材料本身的形状不均匀或者外部施加的载荷等。
针对201不锈钢热处理变形的问题,可以采取以下解决方法:1. 控制热处理温度和时间:合理控制不锈钢材料的热处理温度和时间,可以减少材料的变形。
通过优化热处理工艺参数,可以使材料内部应力和晶粒长大趋于平衡,减少材料的变形。
2. 采用适当的退火工艺:针对201不锈钢的热处理变形问题,可以采用适当的退火工艺进行处理。
退火可以通过恢复应力、减小晶粒尺寸等方式来减少材料的变形。
3. 加强材料的支撑和固定:在热处理过程中,可以采取合理的支撑和固定措施,防止材料发生变形。
通过加强材料的支撑和固定,可以减少材料的机械应力导致的变形。
4. 优化材料的化学成分:合理控制201不锈钢材料的化学成分,可以改善材料的热处理性能,减少材料的变形。
通过调整材料的合金元素含量和比例,可以降低材料的内应力和晶粒长大的程度。
总结起来,201不锈钢热处理变形是由内应力的释放、晶粒长大和机械应力导致的。
各种热处理工艺造成变形的原因总结

各种热处理工艺造成变形的原因总结
热处理是一种通过加热和冷却来改变材料结构和物理性质的工艺。
然而,热处理过程中材料的变形是不可避免的。
以下是造成变形的一些原因:
1. 冷却速率不均匀 - 在冷却过程中,若不同部位的冷却速度不同,则会导致材料的不均匀收缩,进而引起变形。
2. 热处理温度不合适 - 若热处理温度过高或过低,则会导致晶粒尺寸的变化,从而引起材料变形。
3. 热处理时间不合适 - 若热处理时间过长或过短,则会影响材料晶粒的尺寸和分布,从而引起变形。
4. 材料内应力 - 在热处理过程中,由于不同部位的冷却速度不同,产生的内应力会导致材料变形。
5. 材料形状和尺寸 - 材料的形状和尺寸也是导致变形的重要因素,不同形状和尺寸的材料在热处理过程中的变形情况也不同。
总之,热处理过程中材料变形是一种不可避免的现象。
为了减少变形,需要在热处理前仔细考虑材料的形状、尺寸和热处理条件,并采取相应的措施来降低变形风险。
- 1 -。
热处理变形的原因
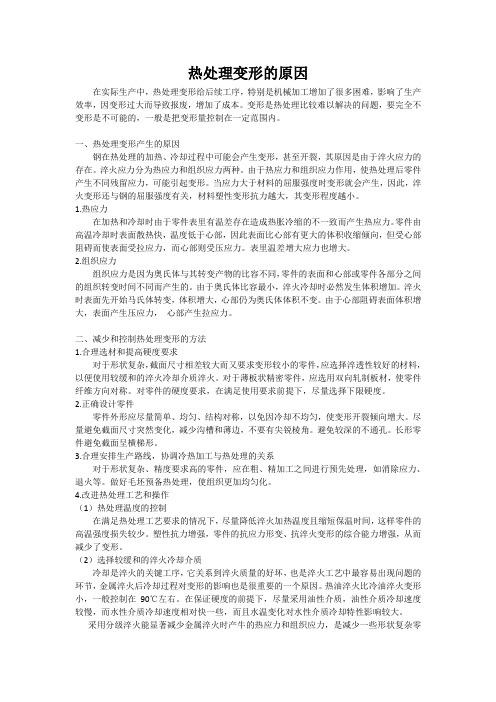
热处理变形的原因在实际生产中,热处理变形给后续工序,特别是机械加工增加了很多困难,影响了生产效率,因变形过大而导致报废,增加了成本。
变形是热处理比较难以解决的问题,要完全不变形是不可能的,一般是把变形量控制在一定范围内。
一、热处理变形产生的原因钢在热处理的加热、冷却过程中可能会产生变形,甚至开裂,其原因是由于淬火应力的存在。
淬火应力分为热应力和组织应力两种。
由于热应力和组织应力作用,使热处理后零件产生不同残留应力,可能引起变形。
当应力大于材料的屈服强度时变形就会产生,因此,淬火变形还与钢的屈服强度有关,材料塑性变形抗力越大,其变形程度越小。
1.热应力在加热和冷却时由于零件表里有温差存在造成热胀冷缩的不一致而产生热应力。
零件由高温冷却时表面散热快,温度低于心部,因此表面比心部有更大的体积收缩倾向,但受心部阻碍而使表面受拉应力,而心部则受压应力。
表里温差增大应力也增大。
2.组织应力组织应力是因为奥氏体与其转变产物的比容不同,零件的表面和心部或零件各部分之间的组织转变时间不同而产生的。
由于奥氏体比容最小,淬火冷却时必然发生体积增加。
淬火时表面先开始马氏体转变,体积增大,心部仍为奥氏体体积不变。
由于心部阻碍表面体积增大,表面产生压应力,心部产生拉应力。
二、减少和控制热处理变形的方法1.合理选材和提高硬度要求对于形状复杂,截面尺寸相差较大而又要求变形较小的零件,应选择淬透性较好的材料,以便使用较缓和的淬火冷却介质淬火。
对于薄板状精密零件,应选用双向轧制板材,使零件纤维方向对称。
对零件的硬度要求,在满足使用要求前提下,尽量选择下限硬度。
2.正确设计零件零件外形应尽量简单、均匀、结构对称,以免因冷却不均匀,使变形开裂倾向增大。
尽量避免截面尺寸突然变化,减少沟槽和薄边,不要有尖锐棱角。
避免较深的不通孔。
长形零件避免截面呈横梯形。
3.合理安排生产路线,协调冷热加工与热处理的关系对于形状复杂、精度要求高的零件,应在粗、精加工之间进行预先处理,如消除应力、退火等。
热处理变形基础知识
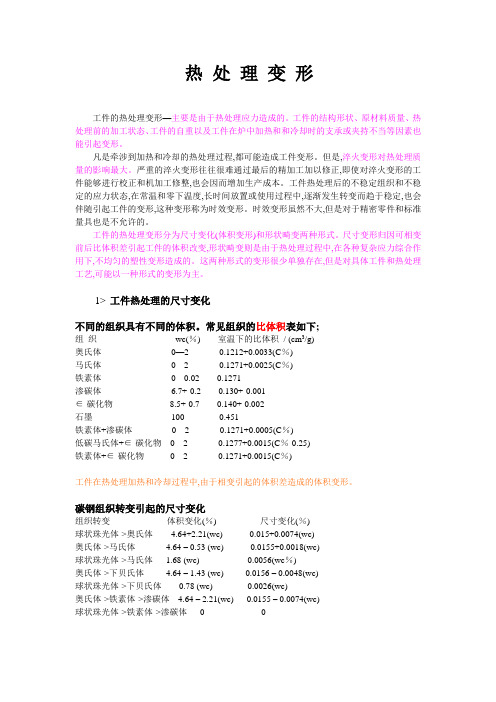
热处理变形工件的热处理变形—主要是由于热处理应力造成的。
工件的结构形状、原材料质量、热处理前的加工状态、工件的自重以及工件在炉中加热和和冷却时的支承或夹持不当等因素也能引起变形。
凡是牵涉到加热和冷却的热处理过程,都可能造成工件变形。
但是,淬火变形对热处理质量的影响最大。
严重的淬火变形往往很难通过最后的精加工加以修正,即使对淬火变形的工件能够进行校正和机加工修整,也会因而增加生产成本。
工件热处理后的不稳定组织和不稳定的应力状态,在常温和零下温度,长时间放置或使用过程中,逐渐发生转变而趋于稳定,也会伴随引起工件的变形,这种变形称为时效变形。
时效变形虽然不大,但是对于精密零件和标准量具也是不允许的。
工件的热处理变形分为尺寸变化(体积变形)和形状畸变两种形式。
尺寸变形归因可相变前后比体积差引起工件的体积改变,形状畸变则是由于热处理过程中,在各种复杂应力综合作用下,不均匀的塑性变形造成的。
这两种形式的变形很少单独存在,但是对具体工件和热处理工艺,可能以一种形式的变形为主。
1>工件热处理的尺寸变化不同的组织具有不同的体积。
常见组织的比体积表如下;组织wc(%) 室温下的比体积/ (cm3/g)奥氏体0—2 0.1212+0.0033(C%)马氏体0---2 0.1271+0.0025(C%)铁素体0---0.02 0.1271渗碳体 6.7+-0.2 0.130+-0.001∈-碳化物8.5+-0.7 0.140+-0.002石墨100 0.451铁素体+渗碳体0---2 0.1271+0.0005(C%)低碳马氏体+∈-碳化物0---2 0.1277+0.0015(C%-0.25)铁素体+∈-碳化物0---2 0.1271+0.0015(C%)工件在热处理加热和冷却过程中,由于相变引起的体积差造成的体积变形。
碳钢组织转变引起的尺寸变化组织转变体积变化(%) 尺寸变化(%)球状珠光体->奥氏体- 4.64+2.21(wc) - 0.015+0.0074(wc)奥氏体->马氏体 4.64 – 0.53 (wc) - 0.0155+0.0018(wc)球状珠光体->马氏体 1.68 (wc) 0.0056(wc%)奥氏体->下贝氏体 4.64 – 1.43 (wc) 0.0156 – 0.0048(wc)球状珠光体->下贝氏体0.78 (wc) 0.0026(wc)奥氏体->铁素体->渗碳体 4.64 – 2.21(wc) 0.0155 – 0.0074(wc)球状珠光体->铁素体->渗碳体0 02>工件热处理的形状畸变工件热处理的形状畸变有多种原因。
零件热处理变形

零件热处理变形一、引言零件热处理是一种重要的材料加工技术,它能够改善材料的性能和延长使用寿命。
然而,在零件热处理过程中,由于温度和应力的影响,零件可能会发生变形。
这种变形会对零件的尺寸和形状造成影响,从而影响其功能和性能。
因此,了解零件热处理变形的原因和控制方法对于保证零件质量和稳定性具有重要意义。
二、零件热处理变形原因1.温度梯度引起的变形在热处理过程中,由于加热和冷却速度不同,导致不同部位温度存在梯度差异。
这种温度梯度会引起材料内部应力分布不均匀,从而导致变形。
2.相变引起的变形在一些特殊的材料中,在热处理过程中会发生相变现象。
相变时产生的体积变化会导致材料产生应力分布不均匀,从而导致变形。
3.机械加工残余应力引起的变形在机械加工过程中,由于切削和加工等原因,零件内部会产生残余应力。
在进行热处理时,残余应力会被释放,从而导致变形。
4.材料的热膨胀引起的变形在热处理过程中,由于材料温度升高,导致材料发生热膨胀。
这种膨胀会导致材料产生应力分布不均匀,从而导致变形。
三、零件热处理变形控制方法1.优化加热和冷却方式在进行零件热处理时,可以通过优化加热和冷却方式来减少温度梯度的影响。
例如,在加热过程中采用均匀加热方式,在冷却过程中采用缓慢冷却方式等。
2.控制相变过程在进行特殊材料的热处理时,需要控制相变过程来减少变形。
例如,在进行淬火处理时可以采用间歇淬火或油淬等方式来控制相变速率。
3.预处理机械加工残余应力在进行零件热处理前,可以通过预处理机械加工残余应力来减少变形。
例如,在机械加工后进行热处理前可以进行退火处理来释放残余应力。
4.控制材料的热膨胀在进行零件热处理时,可以通过控制材料的热膨胀来减少变形。
例如,在加热过程中可以采用局部加热或多次加热等方式来控制材料的膨胀。
四、结论零件热处理变形是一个复杂的问题,其产生原因和控制方法需要综合考虑。
在实际应用中,需要根据具体情况选择合适的控制方法来减少变形。
钢件热处理变形的原因总结

钢件热处理变形的原因总结
引起热处理变形的因素颇多,总括起来,基本上有三点:
1、固态相变时,各相质量体积的变化必然引起体积的变化,造成零件的胀与缩的尺寸变化;
2、热应力,包括急热热应力和急冷热应力,当它们超过零件在该温度下所具有的屈服极限时,将使零件产生塑性变形,造成零件的形状变化,即歪扭,或称为畸变;
3、组织应力也会引起形状的改变,即畸变。
一般说,淬火工件的变形总是由于以上的两种或三种因素综合作用的结果,但究竟哪一个因素对变形的影响较大,则需要具体情况作具体的分析。
总的来说,体积变化是由相变时比容的改变而引起的。
马氏体的质量体积比钢的其他组成相的质量体积要大,热处理时钢由其他组成相转化为马氏体时,必然引起体积的增加。
而奥氏体的质量体积要比钢的其他组织质量体积要小,在热处理时由其他组成相转变为奥氏体时,则引起体积的减小。
关于形状的变化,歪扭或称为畸变,主要是由于内应力或者外加应力作用的结果。
在加热、冷却过程中,因工件各个部位的温度有差别,相变在时间上有先后,有时发生的组织转变也不一致,而造成内应力。
这种内应力一旦超过了该温度下材料的屈服极限,就产生塑性变形,引起形状的改变。
此外工件内的冷加工残余应力在加热过程中的松弛,以及由于加热时受到较大的外加应力也会引起形状的变化。
在热处理时可能引起体积变化和形状变化的原因见下表。
表中“体积变化原因”一栏未列入钢因热胀冷缩现象而产生的体积变化,钢由淬火加热温度到零下温度进行冷处理,均随温度的变化而有相应的体积变化,因热胀冷缩而引起的体积变化不均匀乃是热应力产生的原因,而且对变形有相当的影响。
热处理可能引起体积变化和形状变化的原因。
热处理变形产生的原因及控制方法
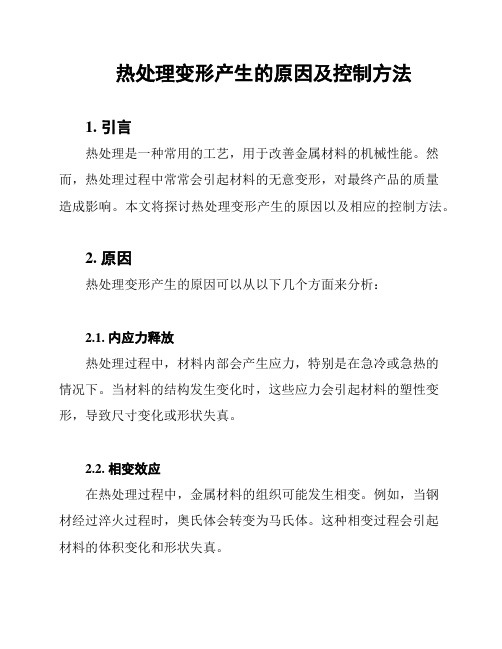
热处理变形产生的原因及控制方法1. 引言热处理是一种常用的工艺,用于改善金属材料的机械性能。
然而,热处理过程中常常会引起材料的无意变形,对最终产品的质量造成影响。
本文将探讨热处理变形产生的原因以及相应的控制方法。
2. 原因热处理变形产生的原因可以从以下几个方面来分析:2.1. 内应力释放热处理过程中,材料内部会产生应力,特别是在急冷或急热的情况下。
当材料的结构发生变化时,这些应力会引起材料的塑性变形,导致尺寸变化或形状失真。
2.2. 相变效应在热处理过程中,金属材料的组织可能发生相变。
例如,当钢材经过淬火过程时,奥氏体会转变为马氏体。
这种相变过程会引起材料的体积变化和形状失真。
2.3. 不均匀加热或冷却如果热处理过程中加热或冷却不均匀,材料的局部温度会存在差异。
这种温度差异会导致材料的非均匀膨胀或收缩,从而引起变形。
3. 控制方法为了减少热处理产生的变形,可以采取以下控制方法:3.1. 控制加热和冷却速率合理控制加热和冷却速率,避免过快或过慢,可以减少材料的变形。
在进行急冷或急热处理时,可以采取预先控制的温度梯度,以缓解内应力的释放。
3.2. 优化工艺参数通过调整热处理过程中的工艺参数,如温度、时间和冷却介质等,可以最大限度地减少材料的变形。
合理选择工艺参数,可以提高材料的均匀性和稳定性。
3.3. 采用合适的支撑结构对于形状复杂的工件,可以采用合适的支撑结构来减少变形。
支撑结构可以提供一定的约束,防止材料发生不受控制的变形。
4. 结论热处理变形是热处理过程中常见的问题,但通过合理的控制方法可以有效减少其影响。
合理控制加热和冷却速率、优化工艺参数以及采用合适的支撑结构都是减少热处理变形的有效途径。
这些控制方法可以提高最终产品的质量和性能。
---以上是关于热处理变形产生的原因及控制方法的内容。
请基于以上内容,进一步完善和添加具体细节,使文档达到800字以上的要求。
热处理变形校正方法

热处理变形校正方法在金属加工行业中,热处理是一个至关重要的环节,它能够改善材料的性能,为产品提供必要的强度和硬度。
然而,热处理过程中往往伴随着变形的问题,这给产品质量带来了挑战。
本文将详细介绍热处理变形校正的方法,帮助读者更好地理解和应对这一工艺难题。
一、热处理变形的原因热处理变形主要是由于材料在加热和冷却过程中,内部应力重新分布所导致的。
当材料暴露在高温环境下,其晶体结构会发生改变,冷却后,这些改变会导致尺寸变化和形状变形。
二、热处理变形校正方法1.预防措施:- 选择合适的材料:不同材料的热处理变形程度不同,选择变形较小的材料是预防变形的有效手段。
- 优化热处理工艺:通过调整加热速度、保温时间、冷却速度等参数,降低热处理变形的风险。
2.变形校正方法:- 机械校正:通过机械力对变形部位进行校正,如锤击、拉伸等,但这种方法仅适用于轻微变形。
- 热校正:利用材料在高温下的塑性变形,对变形部位进行加热至适当温度后进行校正。
这种方法对操作技术要求较高,需防止过度加热导致新的变形。
- 液体校正:将变形部位浸入高温液体中,利用液体的压力和温度对变形进行校正。
此方法适用于复杂形状的零件。
3.数控加工校正:- 采用数控加工技术,根据变形量对零件进行精确加工,以消除变形影响。
这种方法适用于高精度要求的零件。
4.表面处理:- 对变形部位进行表面处理,如喷漆、氧化等,以掩盖或补偿变形。
三、总结热处理变形是金属加工中不可避免的问题,但通过合理的预防措施和校正方法,可以最大限度地降低变形对产品质量的影响。
在实际操作中,应根据具体情况选择合适的校正方法,确保产品达到预期的性能和质量要求。
热处理变形原因与变形控制技术措施论文
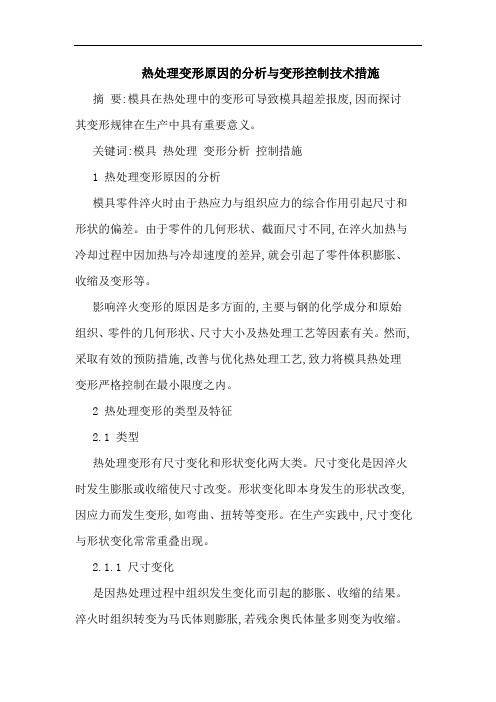
热处理变形原因的分析与变形控制技术措施摘要:模具在热处理中的变形可导致模具超差报废,因而探讨其变形规律在生产中具有重要意义。
关键词:模具热处理变形分析控制措施1 热处理变形原因的分析模具零件淬火时由于热应力与组织应力的综合作用引起尺寸和形状的偏差。
由于零件的几何形状、截面尺寸不同,在淬火加热与冷却过程中因加热与冷却速度的差异,就会引起了零件体积膨胀、收缩及变形等。
影响淬火变形的原因是多方面的,主要与钢的化学成分和原始组织、零件的几何形状、尺寸大小及热处理工艺等因素有关。
然而,采取有效的预防措施,改善与优化热处理工艺,致力将模具热处理变形严格控制在最小限度之内。
2 热处理变形的类型及特征2.1 类型热处理变形有尺寸变化和形状变化两大类。
尺寸变化是因淬火时发生膨胀或收缩使尺寸改变。
形状变化即本身发生的形状改变,因应力而发生变形,如弯曲、扭转等变形。
在生产实践中,尺寸变化与形状变化常常重叠出现。
2.1.1 尺寸变化是因热处理过程中组织发生变化而引起的膨胀、收缩的结果。
淬火时组织转变为马氏体则膨胀,若残余奥氏体量多则变为收缩。
冷处理时因残余奥氏体转变成马氏体又引起膨胀。
马氏体引起的体积膨胀随钢中碳含量增加而变大;其尺寸变化量亦随着增大。
淬火钢回火时马氏体发生分解,而引起收缩;收缩量随马氏体中c%的增多而增大,但若以淬火前的状态为基准,淬火回火后尺寸变化的总合,其结果仍是膨胀。
2.1.2 形状变化是因淬火钢内部的应力及加于外部的力量而引起的。
内部应力是因温度分布不均或因组织转变而引起的。
而外部的力主要是因自重而导致“下垂”。
加热温度越高、保温时间越长,这种因本身重量而引起的“下垂”变形更易发生。
工件加热时,因机械加工或常温加工所产生的残余应力,将发生形状变化。
即使是均匀加热,因钢的屈服点随温度上升而降低之故,此时只要有少许应力存在即发生变形。
因残余应力于外部周围较强。
当温度上升自外部进行时,变形于外部周围特别显著。
钢的热处理淬火时工件的变形规律

淬火时,工件发生的变形有两类,一是翘曲变形,一是体积变形。
翘曲变形包括形状变形和扭曲变形。
扭曲变形主要是加热时工件在炉内放置不当,或者淬火前经变形校正后没有定型处理,或者是由于工件冷却时工件各部位冷却不均匀所造成,这种变形可以针对具体情况分析解决。
1、引起各种变形的原因及其变化规律(1)由于淬火前后组织变化而引起的体积变形工件在淬火前的组织状态一般为珠光体型,即铁素体和渗碳体的混合组织,而淬火后为马氏体型组织。
由于这些组织体积不同,淬火前后将引起体积变化,从而产生变形。
这种变形只按比例使工件胀缩,但不改变形状。
淬火前后由此而引起的体积变化,可以计算求得。
(2)热应力引起的形状变形热应力引起的变形发生在钢件屈服强度较低,塑性较高,而表面冷却快,工件内外温差最大的高温区。
此时瞬时热应力是表面张应力,心部压应力,心部温度高,屈服强度比表面低很多,易于变形。
因此表现为在多向压应力作用下的变形,即立方体向呈球形方向变化。
由此导致尺寸较大的一方缩小,而尺寸较小的一方则胀大。
(3)组织应力引起的形状变形组织应力引起的变形也产生在早期组织应力最大时刻。
此时截面温度较大,心部温度较高,仍处于奥氏体状态,塑性较好,屈服强度较低。
瞬时组织应力是表面压应力,心部拉应力;其变形表现为心部在多向拉应力作用下的拉长。
由此导致的结果为在组织应力作用下,工件中尺寸较大的一方伸长,而尺寸较小的一方缩短。
2、影响淬火变形的因素(1)影响体积变形和形状变形的因素。
凡是影响淬火前后组织比体积变化的因素均影响体积变形。
(2)其他影响淬火变形的因素。
影响淬火变形的因素有两种,一种是夹杂物和带状组织对淬火变形的影响。
(3)淬火前残存应力及加热冷却不均匀对变形的影响。
淬火前工件内残余应力没有消除,淬火加热装炉不当,淬火冷却不当均引起工件的扭曲变形。
- 1、下载文档前请自行甄别文档内容的完整性,平台不提供额外的编辑、内容补充、找答案等附加服务。
- 2、"仅部分预览"的文档,不可在线预览部分如存在完整性等问题,可反馈申请退款(可完整预览的文档不适用该条件!)。
- 3、如文档侵犯您的权益,请联系客服反馈,我们会尽快为您处理(人工客服工作时间:9:00-18:30)。
很多客户在咨询热处理加工的时候,就告诉小编要求不变形,每次对于这样的要求,小编都感到无能为力。
热处理变形的原因究竟是什么呢?今天小编就带大家一起了解下热处理变形的那些事。
(1)凡是牵涉到加热和冷却的热处理过程,都可能造成工件的变形。
工件变形更主要是冷却方面。
由于冷却过程中,零件表面与中心的冷却速度不同,从而造成温度差,其体积收缩在表面与中心也就不一样,产生热应力。
另一方面是钢在转变时比体积发生变化(马氏体是各种组织中比体积最大的一个;奥氏体比体积小),由于工件截面上各处转变先后不同,产生组织应力。
工件淬火变形就是热应力和组织应力综合作用影响的结果。
(2)工件的结构形状、原材料质量、热处理前的加工状态、工件的自重以及工件在炉中加热和冷却时的支承或夹持不当,冷却投入方向、方法和冷却时在冷却中的动作不当等也能引起变形。
加热温度高,冷却速快,故淬火变形最为严重。
(3)工件热处理后的不稳定组织和不稳定的应力状态,在常温和零下温度长时间放置或使用过程中,逐渐发生转变而趋于稳定,也会伴随引起工件的变形,这种变形称为时效变形。
时效变形虽然不大,但是对于精密零件和标准量具也不许的。
实际生产中必须予以防止。
(4)热处理过程中产生的内应力有
热应力和相变应力,它们的形成原因和作用是不同的。
这种应力在热处理过程中对变形影响是主要的原因。