双流板坯连铸机漏钢率分析
板坯连铸机粘结漏钢的原因分析及预防 刘雷锋

板坯连铸机粘结漏钢的原因分析及预防刘雷锋摘要:随着连铸技术的发展和广泛应用,连铸坯的质量和品质受到了人们的广泛关注,提高连铸坯的质量成为连铸生产中重点关注的问题之一。
连铸过程开始广泛运用于有色金属行业,尤其是铜和铝。
连铸技术迅速发展起来。
本文对此进行了分析研究。
关键词:坯;连铸;连铸工艺连铸漏钢是个常见现象。
钢水在结晶器内形成坯壳,连铸坯出结晶器后,薄弱的坯壳抵抗不住钢水静压力,出现断裂而漏钢。
对于薄板坯连铸来说更易发生漏钢事故。
漏钢对连铸生产危害很大。
即影响了连铸车间的产量,又影响了连铸坯的质量,更危及操作者的安全。
因此,降低薄板坯连铸漏钢率是提高生产效率,提高产量,提高产品质量,降低成本的重要途径。
现对某厂自2008~2013年薄板坯漏钢率进行统计。
2008年漏钢率达0.56%;2009年漏钢率达0.19%;2010年漏钢率达0.19%;2011年漏钢率达0.19%;2012年漏钢率达0.15%;2013年漏钢率达0.07。
1 工艺流程某厂第一钢轧厂工艺流程为:鱼雷罐供应铁水/混铁炉供应铁水→铁水预处理→转炉炼钢→氩站→精炼→薄板坯连铸2 薄板坯漏钢类型某厂薄板坯连铸漏钢主要有:粘结漏钢、裂纹漏钢、卷渣漏钢、开浇漏钢、鼓肚漏钢五个类型。
3 薄板坯漏钢特征、原因及预防措施3.1 粘结漏钢粘结漏钢是指钢水直接与结晶器铜板接触形成粘结点,粘结点处坯壳与结晶器壁之间发生粘结,此处在结晶器振动和拉坯的双重作用下被撕裂,并向下和两侧扩展,形成倒“V”形破裂线,钢水补充后又形成新的粘结点,这一过程反复进行,粘结点随坯壳运动不断下移,此处坯壳较薄,出结晶器后,坯壳不能承受上部钢水的静压力,便会发生漏钢事故。
据统计,粘结漏钢发生率最高,高达50%以上。
(1)铸坯粘结漏钢后特征。
粘结漏钢后铸坯特征。
坯壳呈“V”字型或“倒三角”状,粘结点明显。
(2)粘结漏钢的原因:1)保护渣性能不好。
保护渣在结晶器铜板与凝固坯壳之间起润滑的效果。
板坯连铸机漏钢原因分析及控制措施

板坯连铸机漏钢原因分析及控制措施1.操作不当:操作人员操作不规范或经验不足,如操作时间过长、操作不准确等,容易导致板坯连铸机漏钢。
为了避免操作不当导致漏钢,应加强操作人员培训,提高他们的技术水平和操作经验,严格遵循操作规程,并进行必要的考核和监督。
2.连铸结晶器破损:连铸结晶器是冷却板坯的关键部件,如果结晶器破损,冷却水可能会直接进入铸坯中,导致漏钢。
为了避免这种情况,应定期对结晶器进行检查和维修,及时发现并更换破损的部件。
3.气孔:气孔是指铸坯内部存在的空隙,通常由于钢水中的氢气无法完全逸出而形成。
气孔会影响铸坯的质量,导致漏钢。
为了减少气孔,可以采取以下措施:(1)控制钢水的合金成分,控制钢水中的氢含量。
(2)在铸造过程中加入除氧剂,提高钢水中的溶解氧含量,减少气体生成。
(3)合理设计结晶器,使气泡易于从铸坯中升出。
4.结晶器堵塞:连铸结晶器内部可能会堵塞,导致冷却水无法均匀地冷却铸坯,造成漏钢。
为了避免结晶器堵塞,应定期对结晶器进行清洗和维修,保证结晶器内部的冷却水流通畅。
5.铸坯温度过高:铸坯温度过高会导致铸坯内部产生过多的气体,增加气孔的形成,从而引起漏钢。
为了控制铸坯温度,可以在连铸过程中控制冷却水的流量和温度,以达到合理的冷却效果;同时,在连铸过程中加强温度监控,及时调整连铸速度和冷却水的冷却效果。
6.铸模破损:铸模破损会导致铸坯内部形成孔洞和裂缝,导致漏钢。
为了避免铸模破损,应定期进行铸模的检查和维修,及时更换破损的部件。
7.其他原因:除了以上几点外,板坯连铸机漏钢还可能受到其他因素的影响,如连铸设备的老化、设备维护不当等。
为了确保连铸机的正常运行和减少漏钢,应加强设备的维护保养,定期进行设备的检修和更换关键部件。
综上所述,要控制板坯连铸机漏钢,需要从操作规范、设备维护、冷却控制等多个方面着手,以保证连铸过程的正常进行和铸坯质量的提高。
只有在整个生产过程中严格按照操作规程进行操作,定期维护检修设备,并加强钢水质量控制,才能有效控制和减少板坯连铸机漏钢的发生。
降低板坯连铸漏钢率的措施
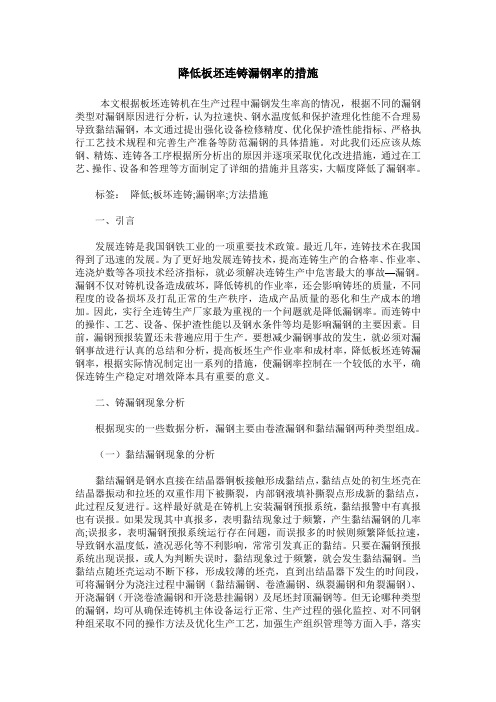
降低板坯连铸漏钢率的措施本文根据板坯连铸机在生产过程中漏钢发生率高的情况,根据不同的漏钢类型对漏钢原因进行分析,认为拉速快、钢水温度低和保护渣理化性能不合理易导致黏结漏钢,本文通过提出强化设备检修精度、优化保护渣性能指标、严格执行工艺技术规程和完善生产准备等防范漏钢的具体措施。
对此我们还应该从炼钢、精炼、连铸各工序根据所分析出的原因并逐项采取优化改进措施,通过在工艺、操作、设备和答理等方面制定了详细的措施并且落实,大幅度降低了漏钢率。
标签:降低;板坏连铸;漏钢率;方法措施一、引言发展连铸是我国钢铁工业的一项重要技术政策。
最近几年,连铸技术在我国得到了迅速的发展。
为了更好地发展连铸技术,提高连铸生产的合格率、作业率、连浇炉数等各项技术经济指标,就必须解决连铸生产中危害最大的事故—漏钢。
漏钢不仅对铸机设备造成破坏,降低铸机的作业率,还会影响铸坯的质量,不同程度的设备损坏及打乱正常的生产秩序,造成产品质量的恶化和生产成本的增加。
因此,实行全连铸生产厂家最为重视的一个问题就是降低漏钢率。
而连铸中的操作、工艺、设备、保护渣性能以及钢水条件等均是影响漏钢的主要因素。
目前,漏钢预报装置还未普遍应用于生产。
要想减少漏钢事故的发生,就必须对漏钢事故进行认真的总结和分析,提高板坯生产作业率和成材率,降低板坯连铸漏钢率,根据实际情况制定出一系列的措施,使漏钢率控制在一个较低的水平,确保连铸生产稳定对增效降本具有重要的意义。
二、铸漏钢现象分析根据现实的一些数据分析,漏钢主要由卷渣漏钢和黏结漏钢两种类型组成。
(一)黏结漏钢现象的分析黏结漏钢是钢水直接在结晶器铜板接触形成黏结点,黏结点处的初生坯壳在结晶器振动和拉坯的双重作用下被撕裂,内部钢液填补撕裂点形成新的黏结点,此过程反复进行。
这样最好就是在铸机上安装漏钢预报系统,黏结报警中有真报也有误报。
如果发现其中真报多,表明黏结现象过于频繁,产生黏结漏钢的几率高;误报多,表明漏钢预报系统运行存在问题,而误报多的时候则频繁降低拉速,导致钢水温度低,渣况恶化等不利影响,常常引发真正的黏结。
板坯连铸机粘结漏钢的原因分析及解决措施
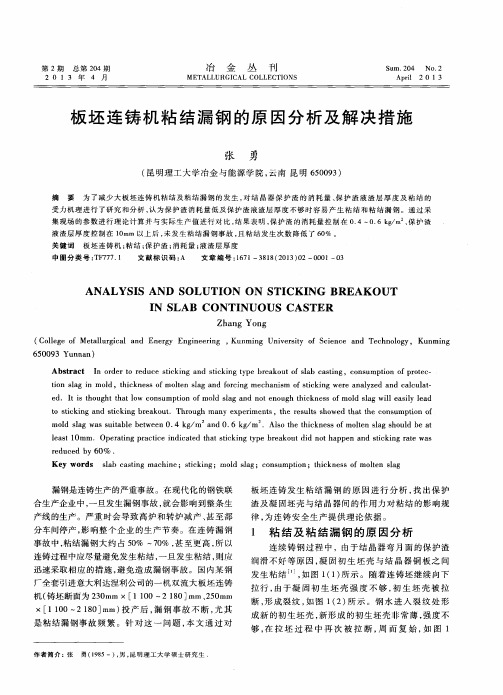
漏 钢是连铸生产的严重事故。在现代化 的钢铁联
板坯 连 铸发 生粘 结 漏 钢 的原 因进 行 分 析 , 找 出保 护 渣及 凝 固坯壳 与 结 晶器 间的作 用力 对粘 结 的影 响规 律, 为连 铸安 全生 产 提供理 论依 据 。
张 勇
( 昆明理 工大 学 冶金 与能 源学 院 , 云南 昆 明 6 5 0 0 9 3 )
摘 要 为 了减 少 大 板 坯 连 铸 机 粘 结 及 粘 结 漏 钢 的 发 生 , 对结 晶器保 护渣 的消耗 量 、 保 护 渣 液 渣 层 厚 度 及 粘 结 的
受 力 机 理 进 行 了研 究 和 分 析 , 认 为保 护 渣 消 耗 量 低 及 保 护 渣 液 渣 层 厚 度 不 够 时 容 易 产 生 粘 结 和 粘 结 漏 钢 。 通 过 采 集 现 场 的参 数 进 行 理 论计 算 并 与 实 际 生 产 值 进 行 对 比 , 结果表 明 , 保 护 渣 的消 耗 量 控 制 在 0 . 4~0 . 6 k g / m 、 保 护 渣
板坯连铸机漏钢成因分析及预防措施

;: 常规板坯连铸机参数及漏钢情况
; 5 9: 常规板坯连铸机的主要工艺参数 酒钢第二炼钢常规板坯连铸机主要工艺参数见 表 8。
第 ! 期8 8 8 8 8 8 8 8 8 8 8 8 程子建: 板坯连铸机漏钢成因分析及预防措施8 8 8
表 !" !##$ % !##& 年逐月漏钢情况
项目 产量 ( +) 综合合格率 (, ) 漏钢次数 !""# 年 %月 )’ """ **- )) ’ !月 $* #’* **- ) % &月 )) %#" **- $ ! ’月 $$ ("" **- )# % (月 ** ’&# **- ) % #月 )# &!$ **- )’ % $月 )" ((’ **- *’ & )月 $% $&# **- *& " *月 #% *&* **- *& " %" 月 !* ($& **- *! " %% 月 ($ )&" **- *$ " %! 月 $$ !’) **- *) " !""$ 年 %月 #"#&) **- *) " !月 #"""" **- *( " 合计
(
% "%’ (*" **- )* %&
表 ’" 漏钢情况统计结果
次数 % ! & ’ ( # $ ) * %" %% %! %& 时间 !""#."%."! !""#."%.%" !""#."%.&" !""#."%.&" !""#."!.%! !""#."&.") !""#."&.%# !""#."’.%! !""#."(.%( !""#."#.!( !""#."$."$ !""#."$.%$ !""#."$.%) 钢种 //’"" //’"" //’"" //’"" //’"" //’"" 5!&(67 5!&(6 5!&(6 ( 改) 5!&(67 ( 改) 5!&(67 ( 改) 5!&(67 ( 改) 5!&(67 ( 改) 规格 %#" 0 (!" %#" 0 (!" !!" 0 (&" !!" 0 (&" !!" 0 (&" !!" 0 (&" !!" 0 (&" !!" 0 (&" !!" 0 (&" !!" 0 (&" !!" 0 (&" !!" 0 (&" !!" 0 (&" 炉次 换包第 ! 炉 换包第 ! 炉 换包第 ! 炉 第( 炉 第) 炉 第 %& 炉 第( 炉 第# 炉 第 %! 炉 第* 炉 第# 炉 第) 炉 第( 炉 拉速 %- ! 1 2 134 %- !& 1 2 134 %- "( 1 2 134 %- " 1 2 134 %- "( 1 2 134 %- "& 1 2 34 %- "( 1 2 134 "- $( 1 2 134 "- *( 1 2 134 %- ") 1 2 134 %- " 1 2 134 %- " 1 2 134 "- $( 1 2 134 漏钢位置 内弧距坯头 #(" 11, 中间位置 内弧出结晶器, 距坯头 )%" 11, 中间位置 内弧中部距坯头 *"" 11 处 内弧中部偏西距结晶器上口 *"" 11 处 漏钢部位位于窄右出结晶器足辊位置 内外弧距结晶器上口 % &)" 11 外弧正中部, 漏钢点距结晶器上口 )(" 11 外弧中部偏西距结晶器上口 )"" 11 处 内弧出结晶器, 距坯头 )%" 11, 中间位置 内弧出结晶器下口位置 外弧宽面下口处 漏钢位置在结晶器窄左距上口 % 1 处 外弧宽面结晶器下口中部 漏钢形式 粘结漏钢 粘结漏钢 粘结漏钢 粘结漏钢 粘结漏钢 卷渣漏钢 粘结漏钢 粘结漏钢 粘结漏钢 粘结漏钢 粘结漏钢 机械外力划破坯壳 粘结漏钢
连铸机典型漏钢的特征及成因分析
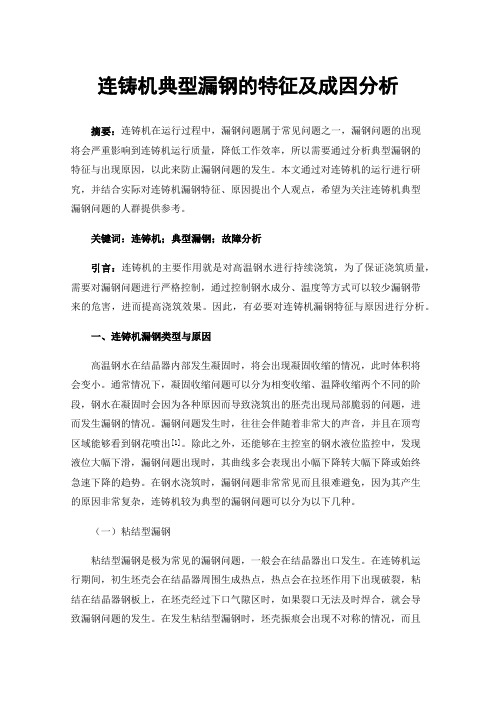
连铸机典型漏钢的特征及成因分析摘要:连铸机在运行过程中,漏钢问题属于常见问题之一,漏钢问题的出现将会严重影响到连铸机运行质量,降低工作效率,所以需要通过分析典型漏钢的特征与出现原因,以此来防止漏钢问题的发生。
本文通过对连铸机的运行进行研究,并结合实际对连铸机漏钢特征、原因提出个人观点,希望为关注连铸机典型漏钢问题的人群提供参考。
关键词:连铸机;典型漏钢;故障分析引言:连铸机的主要作用就是对高温钢水进行持续浇筑,为了保证浇筑质量,需要对漏钢问题进行严格控制,通过控制钢水成分、温度等方式可以较少漏钢带来的危害,进而提高浇筑效果。
因此,有必要对连铸机漏钢特征与原因进行分析。
一、连铸机漏钢类型与原因高温钢水在结晶器内部发生凝固时,将会出现凝固收缩的情况,此时体积将会变小。
通常情况下,凝固收缩问题可以分为相变收缩、温降收缩两个不同的阶段,钢水在凝固时会因为各种原因而导致浇筑出的胚壳出现局部脆弱的问题,进而发生漏钢的情况。
漏钢问题发生时,往往会伴随着非常大的声音,并且在顶弯区域能够看到钢花喷出[1]。
除此之外,还能够在主控室的钢水液位监控中,发现液位大幅下滑,漏钢问题出现时,其曲线多会表现出小幅下降转大幅下降或始终急速下降的趋势。
在钢水浇筑时,漏钢问题非常常见而且很难避免,因为其产生的原因非常复杂,连铸机较为典型的漏钢问题可以分为以下几种。
(一)粘结型漏钢粘结型漏钢是极为常见的漏钢问题,一般会在结晶器出口发生。
在连铸机运行期间,初生坯壳会在结晶器周围生成热点,热点会在拉坯作用下出现破裂,粘结在结晶器钢板上,在坯壳经过下口气隙区时,如果裂口无法及时焊合,就会导致漏钢问题的发生。
在发生粘结型漏钢时,坯壳振痕会出现不对称的情况,而且在多数时间都会在结晶器的内部残留一截坯壳。
粘结型漏钢的出现原因大致可以分为以下几种。
1.保护渣当保护渣自身的理化性能无法与钢种、钢水温度等参数匹配时,就有可能出现粘结型漏钢的问题,因为保护渣的熔化速度、熔点等参数性能都将会影响到连铸机的浇筑质量。
连铸生产漏钢事故的分析

连铸生产漏钢事故分析摘要:通过对连铸漏钢时结晶器内坯壳的剖析和工艺分析,查明漏钢的分类、原因和解决办法和如何避免事故的发生,如何提前预报漏钢。
关键词:连铸漏钢保护渣预报漏钢一、漏钢的危害漏钢—影响铸机有效性连铸中遇到的主要操作故障之一是“漏钢”。
当铸流坯壳破裂时,坯壳内静止的熔融钢水溢出,堵塞机器,需要付出昂贵的停机代价。
为拉出漏钢坯壳,就要再延长漏钢引起的停机时间。
因为它可能会堵塞导辊或足辊,需要用气割清理堵塞,拉出坯壳。
当漏钢坯壳温度降低时,需要把它切成小块,用矫直机从机器中取出,而矫直机设计成能在稳定阶段逐步地矫直曲冷坯壳,上轧辊可提供足够的提升重力,弄出不太长的弯曲铸流。
因此,漏钢对铸机的有效性有重大影响——影响生产率和生产成本。
二、漏钢的分类根据漏钢坯壳的外观,大致把漏钢分成以下几类:悬挂或粘结引起漏钢--钢水粘结到结晶器上,因而称为粘结或悬挂。
这可能是由结晶器和坯壳之间润滑不适或者结晶器调节不当引起的,而润滑不适可能是由质量较差的保护渣、结晶器中坯壳夹渣、结晶器钢水溢流、结晶器角缝、方坯连铸机润滑不良、不均等原因造成的。
1、裂纹引起漏钢--坯壳角部纵裂和宽面纵向裂纹都会造成漏钢发生。
如果纵向裂纹引起漏钢,则保护渣流动不均,结晶器传热不均导致坯壳厚度不均,保护渣选择不当和结晶器冷却不均造成冷却时坯壳破裂。
对角部纵裂引起漏钢来说,沿结晶器窄面凝固厚度不够的坯壳因收缩时受到拉伸应力而破裂,拉伸应力是由结晶器窄面锥度减小和窄面传热不均造成的。
2、夹渣漏钢--坯壳夹带保护渣或大粒夹杂物导致传热减少,形成薄坯壳而漏钢。
方坯连铸时,二次氧化产物、低碳钢冶炼时高粘性渣中不当的脱氧产物,结晶器中三氧化二铝偏高,这些都促使坯壳夹渣,抑制坯壳生长,造成漏钢。
3、薄壳漏钢--观察方坯连铸机中这类漏钢是由结晶器中坯壳厚度不均造成的,原因可能是结晶器中浇注流偏心,或结晶器冷却管严重变形。
4、停止浇注引起漏钢--连铸过程中发生中断而未能断开停止浇注,如果衔接点不能承受重新浇铸施加的拉力,则整炉钢都会溢漏。
板坯连铸机漏钢原因分析及控制措施
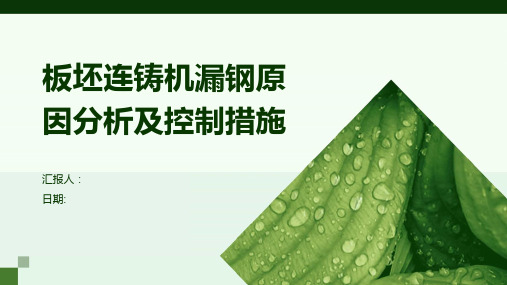
产品质量下降
漏钢会造成铸坯表面缺陷 ,严重影响板坯的质量和 后续加工性能。
生产效率降低
漏钢事故会中断连铸生产 ,导致生产效率降低,增 加生产成本。
漏钢现象的常见表现
铸坯表面出现裂纹、孔洞或凹陷。 钢水泄漏导致的烟雾、火花或燃烧现象。
拓展控制措施
在现有控制措施基础上,寻求更多创新手段,如 引入先进技术、优化设备结构等,进一步提高板 坯连铸机运行稳定性。
推动智能化发展
利用大数据、人工智能等技术手段,建立板坯连 铸机漏钢预警系统,实现事前预防和控制,提高 生产安全性。
THANK YOU
感谢观看
缺乏经验
对于新上岗的操作人员,由于缺乏经验,对于异常情况反 应不及时,也容易导致漏钢事故的发生。
监控不到位
在生产过程中,如果监控人员对于连铸机的运行状态监控 不到位,如未能及时发现设备异常、工艺参数偏离等情况 ,也会导致漏钢事故的发生。
03
控制措施
设备改进
提高设备精度
通过采用高精度设备,减少连铸 过程中的设备误差,确保钢水准
铸坯局部或整体形状变形。 设备异常声音或振动。
02
漏钢原因分析
设备因素
01
设备老化
连铸机设备长时间运行,关键部件磨损严重,未能及时更换或维修,容
易导致漏钢。
02
设备安装精度
设备在安装过程中,如果存在安装精度不达标或者关键部位的紧固不牢
固,会在运行过程中产生缝隙,进而导致漏钢。
03
冷却系统失效
连铸机的冷却系统对于防止漏钢起到关键作用,如果冷却系统发生故障
优化后的工艺参数使得铸坯内部组织更加 致密,减少了缺陷产生。
板坯粘结漏钢分析

5 结束语
1)降低保护渣熔化温度、粘度,提高熔速, 对减少粘结漏钢有利; 2)采用非正弦振动,对减少粘结漏钢有利; 3)提高钢水纯净度,对避免粘结漏钢有利; 4)稳定拉速和液面,“黑渣”操作,可减少粘 结漏钢; 5)温度过低,拉速不宜过高。
3.1 保护渣性能及耗量的影响 3.2 钢水纯净度的影响 3.3 结晶器液面波动的影响 当结晶器内钢液面上升到与渣圈相接触时,液 渣向下的通道将被堵住,当钢液面继续上升时, 会把渣圈向上推,将渣圈与固态渣膜分开,使钢 液直接和结晶器壁接触,并粘结在一起;正滑脱 时,坯壳强度大于粘结力,坯壳被拉走,如果坯 壳强度小于粘结力时,坯壳被拉断,在结晶器出 口产生漏钢。 3.4 拉速变化的影响 拉速发生变化后,温度变化滞后,液渣层厚度 变化、固态渣膜变化和恢复到最佳状态所需时间 推迟,在高拉速时,更易出现这种漏钢。
Nhomakorabea保护渣熔化速度低,单位时间内熔化的保护渣量小,进入铸坯与铜板缝隙的 液渣量就少。 保护渣熔化温度对钢液面上溶渣层厚度的影响如图1。 保护渣熔化温度h、钢液面温度t,、保护渣表面温度h。在钢液面上的熔渣层 与粉渣层间形成一个温度为t:的等温面,在稳定态传热的条件下,通过双层 平板的传热,在粉渣层内带走的热量应等于熔渣层所传导的热量。 即 通过粉渣层传热 q1= 1(t 2 t1); (1) S1 通过熔渣层传热 q2= 2(t 3 t 2 ) ; (2) S2 按稳定态传热条件,则ql=q2由此得出:
板坯粘结漏钢分析
1 2 3 4 5
前言 生产条件 影响粘结漏钢的因素及原因 粘结漏钢的预防措施 结束语
1 前言
漏钢是连铸生产中严重的生产事故, 影响铸机作业率,降低钢水收得率并 使设备严重损坏。 粘结漏钢在板坯连铸漏钢原因中所 占比例大,2000年我厂板坯连铸漏钢 25次,其中粘结漏钢13次,占漏钢次 数的52%。
方坯连铸机漏钢的原因分析及改进措施Doc1

方坯连铸机漏钢的原因分析及改进措施毕业论文摘要:在连铸生产中,漏钢是危害很大的事故。
分析了夹渣漏钢,粘结漏钢和角部裂纹漏钢的特点及机理。
产生各类漏钢的主要原因是保护渣的性能.结晶器的精度.钢水的过热度.拉速及浸入式水口对中.操作等因素。
通过采取相应的措施,让铸机的漏钢率有明显的降低。
关键词:方坯连铸;夹渣;粘结;角部裂纹;漏钢在连铸生产中,漏钢是危害很大的事故,轻则影响铸坯质量造成废品,重则影响影响连铸机作业率,损坏设备危机操作人员安全。
近年来,随着连铸工艺技术的进步,漏钢事故得到了有效控制,但仍不能完全避免。
在连铸日趋高效化的今天要保障生产的顺利进行,提高连铸机作业率就必须减少和控制漏钢次数。
1.铸机参数及漏钢情况1.1连铸机主要参数唐钢二钢扎厂有两台四机四流.三台六机六流方坯连铸机,实际年生产力400万吨浇铸的断面有四种:150mm*150mm.165mm*165mm.165mm*225mm.165mm*280mm,所生产的钢种主要有建筑用钢.低合金钢.硬线钢.轴承钢.焊接钢等近百种。
铸机采用定径水口和塞棒控制两种,浸入式水口加保护渣进行保护浇铸。
1.2漏钢情况对该厂2008年全年的漏钢情况分类统计,以夹渣漏钢.粘结漏钢.角部裂纹漏钢为主要漏钢类型,分别占漏钢总数的33.2%..26.5%和22表一1.3 武钢一炼钢厂有两台5机5流弧型方坯连铸机,设计年生产能力为170万t,浇铸的断面有4种:200 mm × 200 mm、200 mm × 230 mm、230 mm × 250 mm、250 mm × 280 mm,所生产的钢种主要有建筑用钢、低合金钢、帘线钢、轴承钢等18个系列100多个品种。
铸机采取定径水口加塞棒自动控制结晶器液面,浸入式水口加保护渣进行保护浇铸。
该厂连铸机的主要工艺参数见表1。
1.4连铸机主要技术参数表1武钢集团昆钢股份炼钢厂7#铸机主要技术参数序号名称单位参数1 机型倾动存放式刚性引锭杆全弧形连铸机2 弧形半径m 9(连续矫直)1×5×53 台数×机数×流数4 流间距mm 12005 冶金长度m 16.46 铸坯断面mm×mm 150×1507 浇铸钢种碳素结构钢、低合金结构钢、优质碳素结构钢、标准件用钢、冷镦钢8 铸坯定尺长度m 6、9、129 拉坯速度m/min 1.9m/min10 最大拉速 3.5mm 95011 中间罐溢流液面12 振动侍服机械正弦13 引锭杆型式全刚性、可径向微调14 送引锭速度m/min ~3.515 铸坯定尺方式电视摄像+无动力自动火焰切割机16 出坯辊面标高m -2.01.2漏钢情况统计对该厂2006年全年的漏钢情况分类统计得知,以粘结漏钢和角部纵裂漏钢为主要漏钢类型分别占61.90%和21.43%,见表2。
连铸方坯漏钢原因分析以及预防措施

连铸方坯漏钢原因分析以及预防措施摘要:本文分析了新疆伊犁钢铁有限责任公司炼钢厂连铸小方坯漏钢的成因和影响因素,并在此基础上提出了在实际生产过程中解决连铸小方坯漏钢的基本思路以及解决措施,取得了良好的效果。
关键词:连铸小方坯漏钢分析措施1前言近年来,随着国内连铸工艺技术的进步,连铸漏钢事故得到了有效地抑制,但仍是一种不能完全避免的事故。
在连铸生产中,漏钢是危害性很大的事故。
它不仅产生废品、降低连铸机作业率和影响产量,而且损坏设备,极大地降低企业经济效益。
制约着铸机拉速、全流率等主要技术经济指标的提高,因此降低漏钢率是连铸工序历来十分重视的问题。
连铸日趋高效化的今天,要保障生产的顺利进行,就必须对漏钢原因进行分析,寻找防范措施,促进连铸高效化。
2漏钢原因2012年伊钢连铸车间漏钢共计58次。
以纵裂漏钢和角裂漏钢为主要漏钢类型,其中纵裂漏钢占41%,角裂漏钢占36%。
由于发生漏钢事故主要表现在纵裂漏钢和角部纵裂漏钢。
因此下面主要分析这两种漏钢类型的特点和机理以及产生的原因。
2.1形成的原因铸坯的表面纵裂纹产生于结晶器[1.2],由于热流分布不均匀,造成坯壳厚度不均匀,在坯壳薄的地方产生应力集中,结晶器壁与坯壳表面间的摩擦力使坯壳承受较大的负荷,在牵引坯壳向下运动时产生纵向应力,这种应力与从结晶器窄面,到宽面中心线的距离呈直线增加,最大处在铸坯的中间,而钢水静压力随着坯壳往下移动呈直线增加,静压力使得坯壳向外鼓,表面裂纹得到进一步增大,当不能承受钢水静压力时出现纵裂漏钢。
在结晶器内,初生凝固坯壳由于角部为二维传热,凝固较其它部位快,气隙形成早,热阻增加,坯壳在结晶器中下部运行过程中生长慢,故坯壳较其它部位薄,在各种因素引起的拉应力作用下,便产生应力集中。
当坯壳薄弱处承受不住应力作用时,形成角部微小纵裂纹,出结晶器后失去支撑以及受二冷强冷影响,裂纹进一步扩大,出现漏钢。
2.2影响因素1结晶器的影响结晶器的锥度对纵裂纹形成具有决定性的作用[3]。
连铸板坯角裂和边裂漏钢原因的分析
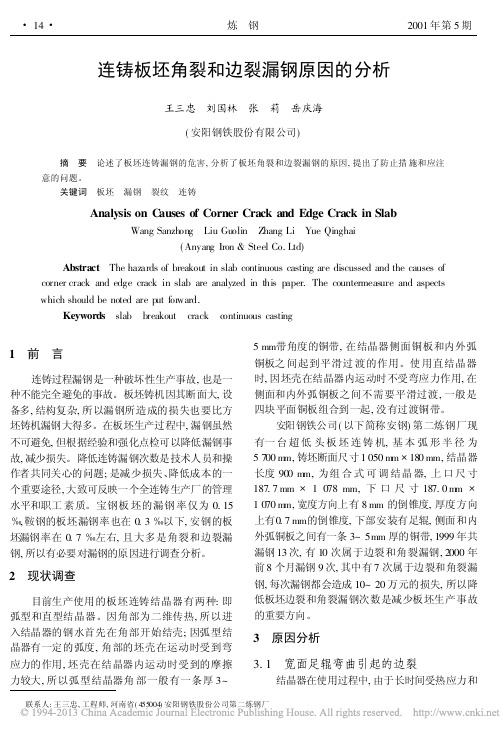
通过以上措施的实施, 从 2000 年 9 月以来, 板坯生产比较稳定, 共发生恶性漏钢事故 1 次, 且 属于操作上的失误, 很少发生板坯角裂和边裂漏 钢, 为稳定生产、降低成本、减少废品做出了积极 的贡献。
6结论
目前国内外建设的较先进的连铸机大多安装 有结晶器漏钢预报系统, 但由于目前安钢需要改 造的项目较 多, 而用于技术改造的 资金有限, 所 以, 只有从设备和操作上来尽可能避免漏钢, 其具 体措施为:
( 4) 结晶器液面翻钢卷渣危害较大, 其一, 引
起夹渣和角裂漏钢; 其二, 增加钢中夹杂物影响铸 坯质量。为了解决结晶器液面翻钢问题, 设计了 多种型号的水口进行试验, 根据试验效果, 总结出 符合我厂铸坯断面和生产需要的水口形状, 将浸 入式水口侧孔面积之 和与水口内孔 面积比定为 3. 2。另外, 在铸机开浇、更换水口和中间包时, 结 晶器内的钢液面不高出浸入式水口侧孔时, 不添 加保护渣, 防止保护渣进入钢液, 造成角裂或夹杂 漏钢。
5 mm带角度的铜带, 在结晶器侧面铜板和内外弧 铜板之 间起到平滑过 渡的作用。使 用直结晶器 时, 因坯壳在结晶器内运动时不受弯应力作用, 在 侧面和内外弧铜板之间不需要平滑过渡, 一般是 四块平面铜板组合到一起, 没有过渡铜带。
安阳钢铁公司( 以下简称安钢) 第二炼钢厂现 有一 台 超 低 头 板 坯 连 铸 机, 基 本 弧 形 半 径 为 5 700 mm, 铸坯断面尺寸 1 050 mm 180 mm, 结晶器 长度 900 mm, 为组 合 式 可 调 结晶 器, 上 口 尺 寸 187. 7 mm 1 078 mm, 下 口 尺 寸 187. 0 mm 1 070 mm, 宽度方向上有 8 mm 的倒锥度, 厚度方向 上有0. 7 mm的倒锥度, 下部安装有足辊, 侧面和内 外弧铜板之间有一条 3~ 5mm 厚的铜带, 1999 年共 漏钢 13 次, 有 10 次属于边裂和角裂漏钢, 2000 年 前 8 个月漏钢 9 次, 其中有 7 次属于边裂和角裂漏 钢, 每次漏钢都会造成 10~ 20 万元的损失, 所以降 低板坯边裂和角裂漏钢次数是减少板坯生产事故 的重要方向。
板坯连铸机漏钢原因分析及控制措施

钢种优化
钢种选择与优化
根据实际生产需求,选择合适的钢种,并进行优化,以降低因钢种问题导致的漏钢风险 。
钢种质量检测与控制
加强钢种的质量检测和控制,确保钢种的质量稳定,降低因钢种质量波动导致的漏钢风 险。
04
结论与展望
研究结论
板坯连铸机漏钢的主要原因包括:钢 水成分、温度和浇注工艺控制不当, 结晶器设计、维护和操作不当,以及 保护渣性能和质量问题等。
设备老化
随着设备使用年限的增加,铸机 内部零件可能发生磨损、老化或 疲劳断裂,导致设备性能下降, 容易出现漏钢事故。
设备维护不当
缺乏定期的设备检查和维护,可 能导致铸机内部零件出现故障或 潜在的安全隐患,从而引发漏钢 事故。
操作因素
操作失误
操作工人在生产过程中出现失误,如 错误地调整铸机参数、操作顺序不当 等,可能导致铸机运行异常,引发漏 钢事故。
操作不规范
操作工人未按照规定的操作规程进行 操作,可能对铸机造成损伤或引发漏 钢事故。
钢种因素
钢种特性
某些特殊钢种可能具有较高的结晶温度和凝固温度范围,增加了铸机操作的难 度,容易引发漏钢事故。
钢水成分
钢水中含有杂质或有害元素,可能影响钢的流动性和铸机的正常操作,从而增 加漏钢的风险。
03
控制措施
02
在控制措施方面,虽然本文提出了一些具体的建议,但实 际应用效果还需要进一步验证和完善。
03
未来研究可以针对不同类型的板坯连铸机进行更深入的调 查和研究,以制定更加具体和针对性的控制措施,提高铸 机的生产效率和产品质量。同时,可以探索更加智能和自 动化的监测和控制系统,实现铸机生产的全面优化和升级 。
THANKS
谢谢您的观看
方坯连铸机漏钢原因分析及改进措施

方坯连铸机漏钢原因分析及改进措施摘要:近年来,随着社会经济的迅猛发展,钢铁工业中的连铸工艺技术也随之不断提升,漏钢事故的发生率虽日趋下降,但仍然还存在隐患。
本文就钢厂的方坯连铸机漏钢的各种原因进行详细分析,比如保护渣的性能情况、钢水过热、结晶器的精准度以及操作失误等。
并针对漏钢源头提供相应的解决措施,最大限度的降低连铸机的漏钢率。
关键词:方坯连铸机;漏钢;粘结;角部纵裂;夹渣1 前言在钢铁工业的连铸生产过程中,一旦发生漏钢事故,产生的影响是巨大的。
轻度的漏钢会导致铸坯质量受损从而无法投入使用,若是严重的漏钢,则会破坏设备,甚至危及工作人员的安全。
在当前连铸工艺技术日益高效的大背景下,只有最大限度的减轻和限制漏钢次数,才能够不断提升连铸机器的作业率,从而更好的保证一切生产操作的顺利运行。
2 连铸机的参数某一炼钢厂有两台4机4流全弧型单点矫直连铸机,年生产力在200万T,浇铸的断面有四种,所生产的主要钢种包括:建筑用钢、低合金钢以及焊接钢等。
连铸机是使用浸入式水口加保护渣的方式进行操作。
3 夹渣漏钢、粘结漏钢和角部裂纹的原因分析3.1 夹渣漏钢的特点和原因夹渣漏钢的主要特点是,坯壳是有一定的弯弧,给人撕裂的印象,但又与裂纹漏钢并不相似。
并且,在漏钢后,结晶器内一般没有残留的坯壳。
连铸坯壳在形成的时候夹杂着保护渣或是有极大颗粒的高熔点杂物,从而造成热的传递大大减少而形成了坯壳漏钢。
出现夹渣漏钢的主要因素有以下几点:第一,当结晶器发生震动的时候,平衡度不够而造成的左右摆度不均衡,结晶器内部的渣子因此被带入钢水中,当其临近坯壳的时候,就会导致传热过低的情况,从而造成坯壳根本不能够耐受钢水所产生的压力,就出现了漏钢事故。
第二,操作人员的操作不当,导致结晶器的钢水液面波过大,因此而产生卷渣漏钢情况。
第三,钢水不够纯净。
冶炼过程中,如果钢水的纯净度不够或者被二次氧化,导致杂质不断增多,当杂质积累到一定的数量,就会被卷入结晶器的钢水当中,于是就会产生与结晶器震动不平稳的时候相类似的漏钢情况。
板坯连铸机漏钢原因分析及控制措施

⑦液面不稳,波动较大,破坏了保护渣的正常流入和弯月面处初生坯壳的 形成条件。
⑧浇钢操作不规范:保护渣加入不均匀;挑渣条过深,破坏了初生坯壳; 给Ar气量不够或过大,造成液面死板或大翻等。
⑨钢水成分: 包晶钢及裂纹敏感钢,钢中S、P含量高等
三、漏钢的识别和控制
2、由设备原因造成的漏钢
跑锥度和偏振等设备故障是常见的引起漏钢的因素。
•跑锥度引起的漏钢 在结晶器液面和铸坯上没有黏结漏钢的特征,而在漏钢后的结晶器 上,可以测得窄面锥度较明显的变小(负锥度)。其控制是采取措施,固定好窄面锥 度。 •偏振引起的漏钢 产生偏振有如下三个原因: ①偏心轮轴承间隙大或轴承磨损 由于偏心轮轴承间隙大或轴承磨损,造成四个偏心轮在同一时刻不能产生相等的振幅,造
③拉速或温度的波动较大,造成保护渣无法适应Байду номын сангаас注条件的急剧变化
④推渣工不按要求加入保护渣,液面覆盖不均匀,时多时少,人为造成保 护渣性能不良。 ⑤浸入式水口的插入深度不合适,引起结晶器内流场状态不良, 造成保护渣融化不好,甚至卷渣,产生了可能漏钢的条件。
二、造成漏钢的原因
A、工艺及操作原因造成的漏钢:
产生表面裂纹或坯壳脱离不彻底,严重时,会产生漏钢
⑦结晶器宽、窄面水量不匹配,产生较严重的角部裂纹,引起漏钢。 ⑧结晶器冷却水水质差,造成结晶器铜板水槽结垢、藻类堵塞等,引起坯壳冷却 不均匀,甚至坯壳脱离不彻底,导致漏钢。
三、漏钢的识别和控制
1、由保护渣熔化不良造成的漏钢
•看渣面
• 性能好的保护渣 ①粉渣的铺展性好,渣面平整而均匀,②渣面活跃,有小火苗均匀跳 动,③渣层具有均匀的三层结构:30毫米左右的粉渣层、5毫米左右的烧结层、15毫米
板坯连铸机漏钢事故的原因分析及防止 精品
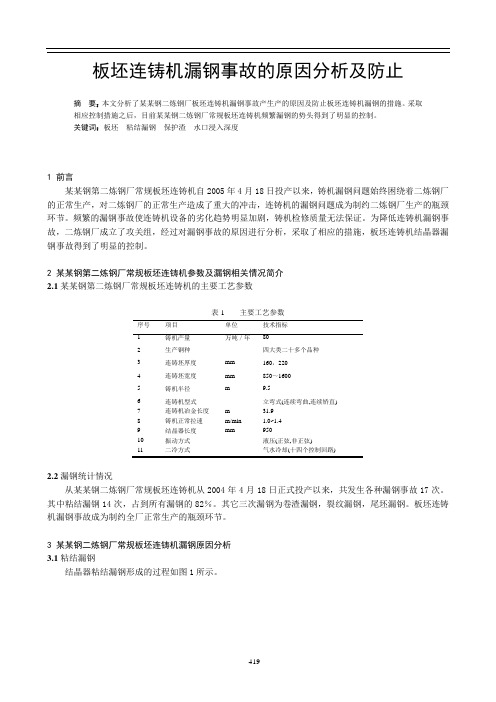
板坯连铸机漏钢事故的原因分析及防止摘要:本文分析了某某钢二炼钢厂板坯连铸机漏钢事故产生产的原因及防止板坯连铸机漏钢的措施。
采取相应控制措施之后,目前某某钢二炼钢厂常规板坯连铸机频繁漏钢的势头得到了明显的控制。
关键词:板坯粘结漏钢保护渣水口浸入深度1 前言某某钢第二炼钢厂常规板坯连铸机自2005年4月18日投产以来,铸机漏钢问题始终困绕着二炼钢厂的正常生产,对二炼钢厂的正常生产造成了重大的冲击,连铸机的漏钢问题成为制约二炼钢厂生产的瓶颈环节。
频繁的漏钢事故使连铸机设备的劣化趋势明显加剧,铸机检修质量无法保证。
为降低连铸机漏钢事故,二炼钢厂成立了攻关组,经过对漏钢事故的原因进行分析,采取了相应的措施,板坯连铸机结晶器漏钢事故得到了明显的控制。
2 某某钢第二炼钢厂常规板坯连铸机参数及漏钢相关情况简介2.1某某钢第二炼钢厂常规板坯连铸机的主要工艺参数表1 主要工艺参数铸机产量万吨/年2 生产钢种四大类二十多个品种3 连铸坯厚度mm 160,2204 连铸坯宽度mm 850~16005 铸机半径m 9.56 连铸机型式立弯式(连续弯曲,连续矫直)7 连铸机冶金长度m 31.98 铸机正常拉速m/min 1.0~1.49 结晶器长度mm 95010 振动方式液压(正弦,非正弦)11 二冷方式气水冷却(十四个控制回路)2.2漏钢统计情况从某某钢二炼钢厂常规板坯连铸机从2004年4月18日正式投产以来,共发生各种漏钢事故17次。
其中粘结漏钢14次,占到所有漏钢的82%。
其它三次漏钢为卷渣漏钢,裂纹漏钢,尾坯漏钢。
板坯连铸机漏钢事故成为制约全厂正常生产的瓶颈环节。
3 某某钢二炼钢厂常规板坯连铸机漏钢原因分析3.1粘结漏钢结晶器粘结漏钢形成的过程如图1所示。
在钢水浇注过程中,结晶器弯月面的钢水处于异常活跃的状态。
如图1所示,由于各种原因,浇铸过程中流入坯壳与结晶器铜壁之间的液态渣被阻断,当结晶器铜板与初生坯壳的摩擦力大于初生坯壳的强度时,初生坯壳被拉断,与铜板产生粘结。
板坯连铸机粘接漏钢事故分析.doc

YJ0701-板坯连铸机粘接漏钢事故分析案例简要说明:依据国家职业标准和冶金技术专业教学要求,归纳提炼出所包含的知识和技能点,弱化与教学目标无关的内容,使之与课程学习目标、学习内容一致,成为一个承载了教学目标所要求知识和技能的教学案例。
该案例是连续铸钢事故分析与处理案例,体现了连续铸钢等岗位工艺参数、凝固理论知识点和具体岗位操作步骤,与本专业连续铸钢等课程事故预防与处理单元的教学目标相对应。
使用,更适合在连续铸钢工等工种的职工培训中使用:通过本案例复习课程内容并将知识系统整理,解决生产实际问题。
本案例可迁移为其他事故预防的教学,学生通过本案例学习,具有加他事故分析的能力。
板坯连铸机粘接漏钢事故分析1背景介绍某中型转炉炼钢厂,采用喷吹颗粒镁预脱硫,拥有三座loot的转炉,采用CAS-OBs LF炉、RH精炼装置,四台不同断面的大型厚板坯连铸机,连铸机采用双排热电偶漏钢预报装置。
该厂主要生产管线、船板等中厚板。
2主要内容2.1事故经过2012年12月26 R,某铸机浇注浇次1212826(断面2000mmX250mm,钢种45-1)第21炉2Q08199浇注4: 46时发生结晶器外弧粘连漏钢,至当日22:00处理完毕,共造成铸机非计划停浇17小时14分,构成粘连漏钢事故。
2.1.1精炼处理2Q08199炉次是3#LF炉处理,使用12#钢包,包龄44次。
钢水到站后热修包报12#钢包为止常周转包,但在处理过程中升温速度慢,温降异常。
铸机要点4:20,要温1538°C。
2Q08199炉次在3廿LF炉处理61min,加热40min,软吹4mino 具体处理过程如下:3:15到站,到站温度1514°C, 3: 17进加热位并加入一批渣料。
3:20第一次升温,3: 33停止(升温13min),测温1506°C,取钢样。
3:35第二次升温,3:45钢样成分回来后,调硅铁133kg、镭铁61kg、碳粉60kg, 3:54升温结束。
- 1、下载文档前请自行甄别文档内容的完整性,平台不提供额外的编辑、内容补充、找答案等附加服务。
- 2、"仅部分预览"的文档,不可在线预览部分如存在完整性等问题,可反馈申请退款(可完整预览的文档不适用该条件!)。
- 3、如文档侵犯您的权益,请联系客服反馈,我们会尽快为您处理(人工客服工作时间:9:00-18:30)。
双流板坯连铸机漏钢率的分析
【摘要】自投产以来,漏钢率一直比较高,严重影响了生产的顺行,通过对近年来漏钢事故数据的分析,采取了一系列措施,在降低漏钢率方面发挥了有效的作用,很好地控制了漏钢事故的发生。
【关键词】漏钢;热流;摩擦力
前言
在连铸生产过程中,漏钢作为最严重的生产事故,会对整个生产过程造成重大影响,在处理漏钢过程中工人劳动强度增大,还极易发生安全事故。
因此,必须对各种形势的漏钢进行分析和研究,找出预防和减少漏钢事故的发生的措施。
1.2010年漏钢的统计与分析
2.漏钢形式及原因分析
连铸漏钢的形式较多,主要有开浇漏钢、悬挂漏钢、裂纹漏钢、粘结漏钢、卷渣漏钢等。
2.1开浇漏钢原:开浇漏钢是指引锭头刚拉出结晶器即发生的漏钢事故,主要是由操作的原因引起。
主要原因有:
(1).结晶器密封不良,冷料加入不合适,铁屑层过薄等,钢水从缝隙入渗出。
(2).起步时间过早,凝固坯壳强度不够,造成起步拉断。
(3).起步过程中有异物随钢流进入结晶器坯壳处,造成坯壳出结晶器后漏钢。
2.2悬挂漏钢:结晶器角缝过大,铜板划伤,致使在结晶拉坯阻力增大造成坯壳拉断漏钢
2.3裂纹漏钢:纵裂漏钢是由于保护渣选择不当,保护渣流动不均匀,结晶器传热不均导致坯壳厚度不均匀,冷却时坯壳破裂而产生的。
角部裂纹是沿结晶器窄面凝固厚度不够的坯壳收缩时受到拉伸应力而破裂,拉伸应力是由结晶器窄面锥度减小和窄面传热不均造成的。
2.4卷渣漏钢:由于结晶器渣块或异物裹入凝固壳局部区域,使坯壳厚度太薄造成。
2.5粘结漏钢:粘结性漏钢主要是指结晶器液面波动或者其它原因,导致弯月面附近润滑效果不好,坯壳与结晶器壁之间发生粘结,拉坯摩擦阻力增大,粘结处被拉裂,并向下和两侧扩展,形成“v”破裂线,随着铸坯往下移动,钢水直接与铜板接触,由于冷却水的作用,形成新的坯壳,随着结晶器的振动和铸坯的继续下移,此过程重复出现,直到薄坯壳在出结晶器下口时被拉裂,出现漏钢现象。
漏钢后坯壳四周明显不均匀。
2.5.1保护渣原因:保护渣润滑性能不好是发生粘结漏钢的主要原因。
如果保护渣选择不合适,保护渣的润滑效果就差,导致坯壳与铜板之间的摩擦增大,就有可能发生粘结。
2.5.2钢水原因:钢水中的夹杂物尤其是氧化铝的含量较高,使保护渣变粘,熔化度升高,不利于化渣。
保护渣变性会造成拉坯阻力过大,造成粘结漏;钢液中气体即脱氧情况对连铸粘结也有
非常重要的影响。
一般,由于钢液二次氧化在连铸结晶器有极少量的c-o反应,则不会对结晶器中的铸坯润滑造成影响,但当钢液后吹严重且脱氧不良时,结晶器中仍会进行大量的c— o反应,生成的一氧化碳气体沿结晶器壁大量溢出,严重恶化了润滑条件,渣膜的破坏使得凝固壳与结晶器铜壁直接接触的面积大幅度上升,随之摩擦力显著增大,最终导致粘结漏钢;钢液温度对连铸漏钢也有重要影响,尤其是当钢液过热度较低时,由于结晶器中钢液温度也随之下降,则导致保护渣的熔化不良、液渣层变薄和粉渣层增厚。
当拉速提高到一定程度后,保护渣会在弯月面处形成团块而逐渐失去润滑作用,极易发生粘结漏钢事故。
2.5.3液面波动原因:西区炼钢板坯连铸机结晶器液面控制采用的是涡流自动控制,较稳定地控制液面。
但在浇注的过程中,仍然会出现液面波动,最大液面波动到10mm左右。
结晶器液面波动较大时,往往会造成液渣层补充不上,造成缺渣,使形成的坯壳强度不一,非常容易造成粘结漏钢
3.采取措施
3.1起步漏钢:
(1)严格控制结晶器密封作业,引锭头四周密封严实不能有缝隙和疏松,各种冷料和钉销扑放要合适。
(2)严格控制起步时间在50秒左右,不能少于35秒。
这样有利于形成足够厚度的坯壳,防止起步坯壳过薄漏钢。
(3)中间包烘烧前要认真清理,开浇前要检查,不能让中间包
内有异物,防止开浇时进入结晶。
结晶器内也不能有其它异物。
开浇时中间包内钢液面要保证一定高度,一般不低于400mm,这样有利于杂物上浮而不进入结晶器内。
3.2悬挂漏钢:
(1)严格控制好结晶器角缝,不能大于0.5mm。
防止钢液进入缝隙造成悬挂。
(2)结晶器铜板要保证完整光滑,镀层脱落不能大于1平方厘米,不能有大的划痕。
可以防止拉坯阻力过大而造成漏钢。
(3)结晶器要有合适的倒锥度,可以减小下部气隙厚度,改善传热。
如果倒锥度过小,中间的热阻很大(主要是气隙),不利于传热,坯壳比较薄,当出结晶器下口的时候,如果坯壳经受不住钢水静压力的作用,就容易造成漏钢。
(4)开浇时要用上防护板,防止起步时角部挂钢。
3.3裂纹漏钢:
(1)要选择合适的保护渣,以确保结晶器传热均匀,使坏壳厚度均匀。
(2)对结晶器进行严格的设备管理,定期维护,保证水槽畅通,冷却均匀,保证坯壳厚度均匀。
3.4粘结漏钢:
(1)使用合适的保护渣,操作者密切关注保护渣的熔化情况,每一炉都要测量液渣层厚度,及时计算消耗量,液渣层厚度保证在8-18mm,消耗量不能小于0.4kg/t,发现不合适及时更换保护渣类
型或结晶器内换渣,及时剔除结晶器四周的大渣条。
规范加渣操作,做到少加渣,勤加渣,保证保护渣水分含量小于0.01% ,防止保护渣在保存和使用过程中受潮变性;
(2)提高钢水的质量,加强钢液的脱氧,严格控制钢水的水洁净度,合理控制钢液温度。
(3)严格监视液面波动情况,如液面波动大于10mm时,要及时排查或降低拉速;拉速的调整不能过于频繁,要求每提升0.1m/min 停留20—30秒;定其对振动情况进行检测,生产中如发现偏差大于5mm时要采取降速或停浇处理,并及时进行检修处理。
(4)通过热流图、摩擦力图、和漏钢预报进行监测,并及时采取措施:热流反应的是结晶器传热情况,正常情况下应该是均匀稳定的并且根据工艺参数的变化而变化,当热流出现异常较大的波动时,说明传热情况也发生了变化,此时应该综合分析保护渣、结晶器水流量和温度等信息,当热流值出现连续上升或下降200kw或出现交叉、分岔严重时采取降低拉速、结晶器换渣等处理措施;摩擦力反应的是铸坯拉速方向与结晶器振动之间的相对阻力,正常情况下应该是平稳的,当出现摩擦力异常的增高或下降时,说明坯壳与结晶器之间的润滑情况出现不良,此时应该综合各种信息分析原因,当变化数值超过50kn/m?采取降低拉速、结晶器换渣等处理措施。
综上所述,在监测到热流图、摩擦力图、和漏钢预报出现异常时,及时采取降低拉速、激活粘结循环紧急降速、停浇等措施。
就可以
大大降低粘结漏钢的发生。
4.结语
结合国内其他钢厂板坯连铸漏钢问题,分析了连铸各种漏钢形成的原因,尤其是对粘结漏钢进行了重点分析,认为保证保护渣的润滑作用是解决粘结漏钢的主要原因。
严格管理,规范操作是有效避免开浇漏钢、悬挂漏钢、卷渣漏钢等的有效手段。
主控工密切监视各项工艺参数,包括液面波动、振动偏差、漏钢预报、摩擦力以及钢水的成分和温度等。
发现异常及时采取相应措施,可以大大减少和避免漏钢的发生。