催化裂化装置
第三章_催化裂化装置
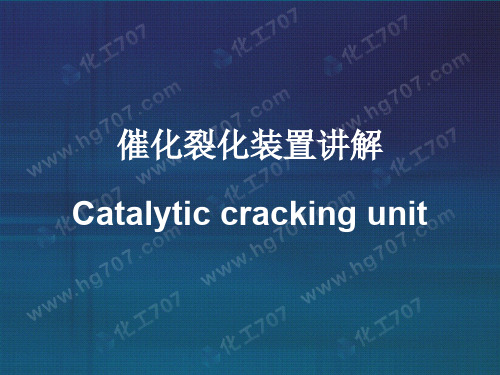
主要由吸收塔、解吸塔、再吸收塔及稳定塔组成。 吸收塔和解吸塔的操作压力为1.0~2.0MPa。 稳定塔实质上是个精馏塔,操作压力为1.0-1.5MPa。
四、能量回收系统
利用再生器出口烟气的热能和压力使余热 锅炉产生蒸汽和烟气轮机作功、发电等。
能量回收系统的工艺流程图
二、分馏系统
沉降器来的反应油气,经换热器进入分馏塔, 根据物料的沸点差,从上至下分离为富气、粗 汽油、柴油、回炼油和油浆。
分馏系统流程图
1.分馏塔底人字形挡板处用油 浆洗涤(1)防止少量催化剂细 粉堵塞塔盘和影响产品质量; (2)由于反应油气温度较高, 500℃左右,油浆洗涤可取走 多余的热量。 2.油浆:一部分回炼,一部分 回分馏塔,一部分送出装置作 自用燃料。 3富气经压缩后去吸收稳定系统 的凝缩油罐,粗汽油进吸收塔 上部。
490~510 ℃
2 ~3s
600~750 ℃
200~300 ℃
分馏系统
三、吸收—稳定系统
从分馏塔顶油气分离器出来的富气中带有汽油组分,而粗
汽油中又溶有C3、C4甚至C2组分,因此吸收稳定系统的作 用: 利用吸收和精馏的方法将富气和粗汽油分离成干气 (≤C2) 、液化气(C3、C4)和蒸汽压合格的稳定汽油。
富气经气压机升压、冷却并分出凝缩油后,由底部进入吸收塔;稳定 汽油和粗汽油则作为吸收液由塔顶进入,将富气中的C3、C4(含少量C2) 等吸收后得到富吸收油。吸收塔顶部出来的贫气中夹带有少量稳定汽油, 可经再吸收塔用柴油回收其中的汽油组分后成为干气,送出装置。 富吸收油和凝缩油均进入解吸塔,使其中的气体解吸后,从塔顶返回 凝缩油沉降罐,塔底的未稳定汽油送入稳定塔,通过精馏作用将液化气和 稳定汽油分开。有时,塔顶要排出部分不凝气(也称气态烃),它主要是 C2,并夹带有C3和C4.排出不凝气的目的是为了控制稳定塔的Ni+V:不大于 20 PPm 残碳:不大于 6% 产品分布: ★ 气体:10~20%,气体中主要是C3 、C4 ,烯烃含量很 高 ★ 汽油:产率在30~60%之间,辛烷值较高,约80~90 ★ 柴油:产率在0~40%, 十六烷值较低,需调和或精 制 ★ 油浆:产率在0~10% ★ 焦炭:产率在5%~10%,原子比大约是C:H=1:0.3~1
催化裂化装置操作安全技术

催化裂化装置操作安全技术催化裂化装置是石油炼制过程中重要的装置之一,它能将较重的石油烃类分解成低碳烃和芳烃,提高汽油和石脑油的产量和质量。
然而,催化裂化装置操作安全技术至关重要,它关系到人身安全、生产效率和环境保护。
下面将介绍催化裂化装置操作安全技术的一些重要方面。
一、工艺检查与确认在催化裂化装置运行之前,必须进行详细的工艺检查与确认,以确保各种设备、管道和阀门的正常状态。
首先要检查催化剂的寿命和性能,确保其能够正常进行催化作用。
其次,需检查反应器和再生器的温度、压力、流量等参数,确保其在正常范围内。
此外,还需检查其它辅助设备和系统,如催化剂循环系统、冷却水系统等,以确保其正常运行。
只有在确认工艺安全性的前提下,才可以进行操作。
二、操作人员培训与资质要求催化裂化装置操作人员应接受系统的培训,并具备相应的资质要求。
在催化裂化装置的操作过程中,操作人员需熟悉各种设备的工作原理和操作方法,能够准确判断和处理不同的操作情况。
同时,操作人员还需掌握应急处置措施,能够迅速应对突发情况,确保安全。
三、标记与防护装置催化裂化装置中的各种设备和管道都应有明确的标记,以便操作人员识别和判断。
标记应包括设备和管道的名称、功能、压力、温度等信息。
此外,还需设置相应的防护装置,如喷淋系统、泄漏报警系统等,以及警示标志,提醒操作人员注意安全。
这样可以避免由于操作失误或设备故障造成的事故。
四、操作程序与规程催化裂化装置的操作应按照相应的程序和规程进行,包括开机、停机、换料、调整等各个环节。
操作程序应详细记录每个步骤的操作要求、注意事项和安全措施,操作人员需按照程序进行操作,确保各个步骤的顺利进行。
同时,还需定期检查和更新操作程序和规程,以适应不同的情况和要求。
五、事故预防与应急处置催化裂化装置操作过程中,事故的预防至关重要。
操作人员需严格遵守操作规程,不得违反操作程序进行操作。
同时,需定期检查设备和管道的状态,发现异常情况及时处理。
催化裂化装置简介

压缩富气
解吸深度
解吸塔解吸深度提高,经脱乙烷气返回吸收塔的C3以上组份增 多,会造成吸收塔负荷上升,将使干气中C3组份含量上升;在 日常生产过程中应注意干气流量、解吸气流量、解吸塔底温度、 干气组份、液化气组成等分析数据,合理控制吸收与解吸深度
催化裂化装置概况
液化气中C2含量的控制
控制液化气中C2含量,解吸塔的操作条件是关键。高温低压 对解吸有利,但解吸塔压力同时受制于稳定塔操作压力(脱乙 烷汽油自压至稳定塔),且解吸气并入气压机出口富气线,其 压力也与吸收塔操作压力密切相关,因而不可能降的过低。 控制目标:C2≤1.0 V% 相关参数:解吸塔11层气相温度、解吸塔13层气相温度、解吸塔 9层气相温度、解吸塔压力、解吸塔进料温度、解吸塔进料量 及组成。
石化盐化一体化项目
催化裂化装置简介
设计技术部 吴雯雯 二○一五年二月
主 要 内 容
催化工艺发展历程
催化裂化装置概况 催化裂化反应及催化剂 催化裂化发展趋势
催化工艺发展历程
催化裂化的定义
催化裂化(Catalytic cracking)是在热和催化剂的作 用下使重质油发生裂化反应,并转化为裂化气、辛烷 值较高的汽油、柴油等产品的加工过程。 催化裂化的原料: 减压馏分油(VGO)-FCC 常压渣油和减压渣油的脱沥青油-RFCC)
塔顶压力 冷回流量 顶循取热负荷
塔顶压力直接影响汽油组份油气分压,塔顶压力升高,干点提高;塔顶压力下降,干点降低。 冷回流量增加,干点降低,反之则提高。 提高顶循环流量或降低回流温度,使顶循取热负荷增加汽油干点下降,反荷下降,顶温下降,汽油干点下降。
解吸塔温度
解吸塔操作压力
解吸塔进料量及 组成
催化裂化装置概况
催化裂化装置课件
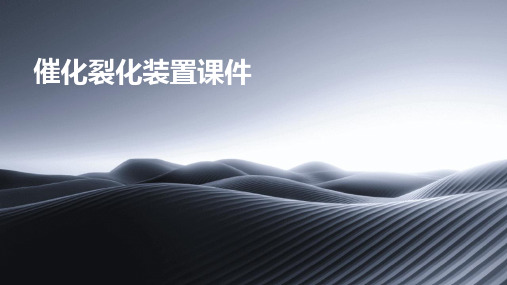
阐述液体产物精制的原理及方法,包括蒸馏、萃取、 吸附和离子交换等。
04
催化裂化装置的维护与保养
日常维护
01
02
03
每日检查
检查装置的外观、紧固件 、连接部位等是否正常, 确保无泄漏、无特殊声响 和振动。
温度和压力监控
定期检查装置的温度和压 力是否在正常范围内,并 记录数据,以便及时发现 特殊情况。
02
03
04
严格遵守操作规程
操作人员必须经过专业培训, 熟悉装置的操作流程和安全规
范。
定期检查和维护
对装置进行定期检查,及时发 现和处理潜伏的安全隐患。
危险品管理
对装置涉及的危险品进行严格 管理,确保储存和使用安全。
应急预案
制定完善的事故应急预案,提 高应对突发事件的快速响应能
力。
事故应急处理
火灾应急处理
THANKS
感谢观看
原料的干燥与脱硫脱氮
介绍原料的种类、性质和来源,说明 原料对催化裂化过程的影响。
阐述原料在进入反应器前进行干燥和 脱硫脱氮的原理及方法。
原料的预热与混合
说明原料在进入反应器前的预热和混 合的必要性,以及预热和混合的方法 。
反应过程
01
反应原理
详细介绍催化裂化反应的原理, 包括反应机理、反应条件和影响 因素。
催化裂化装置的应用
催化裂化装置广泛应用于石油化工行业,是炼油厂的重要加工装置之一 。
它主要用于处理重质石油原料,如减压馏分油、脱油沥青等,将其转化 为高价值的轻质产品。
通过催化裂化装置的处理,可以提高石油产品的质量和产量,满足市场 需求。同时,催化裂化技术也在不断发展和改进,以提高生产效率和环 保性能。
催化裂化的主要设备及作用
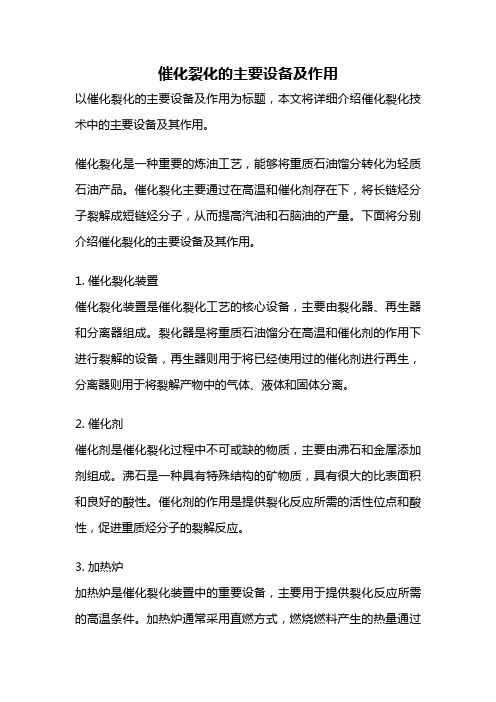
催化裂化的主要设备及作用以催化裂化的主要设备及作用为标题,本文将详细介绍催化裂化技术中的主要设备及其作用。
催化裂化是一种重要的炼油工艺,能够将重质石油馏分转化为轻质石油产品。
催化裂化主要通过在高温和催化剂存在下,将长链烃分子裂解成短链烃分子,从而提高汽油和石脑油的产量。
下面将分别介绍催化裂化的主要设备及其作用。
1. 催化裂化装置催化裂化装置是催化裂化工艺的核心设备,主要由裂化器、再生器和分离器组成。
裂化器是将重质石油馏分在高温和催化剂的作用下进行裂解的设备,再生器则用于将已经使用过的催化剂进行再生,分离器则用于将裂解产物中的气体、液体和固体分离。
2. 催化剂催化剂是催化裂化过程中不可或缺的物质,主要由沸石和金属添加剂组成。
沸石是一种具有特殊结构的矿物质,具有很大的比表面积和良好的酸性。
催化剂的作用是提供裂化反应所需的活性位点和酸性,促进重质烃分子的裂解反应。
3. 加热炉加热炉是催化裂化装置中的重要设备,主要用于提供裂化反应所需的高温条件。
加热炉通常采用直燃方式,燃烧燃料产生的热量通过炉管传递给裂化装置,使其达到裂解反应所需的温度。
4. 冷凝器冷凝器是催化裂化装置中的一个重要组成部分,主要用于将裂解反应产生的气体冷却成液体。
冷凝器通常采用多级冷却方式,通过多个冷却器的串联,将高温的裂解气体逐渐冷却,使其中的石脑油等液体成分凝结出来,从而得到所需的轻质石油产品。
5. 分离塔分离塔是催化裂化装置中用于将裂解产物中的液体和气体进行分离的设备。
分离塔通常采用塔板或填料来增加分离效果,使液体和气体能够充分接触,并通过不同的物理性质进行分离。
6. 汽油分离系统汽油分离系统是催化裂化装置中的一个重要组成部分,主要用于将裂化产物中的汽油分离出来。
汽油分离系统通常包括汽油分离塔、汽油稳定塔和汽油产品收集装置等设备。
其中,汽油分离塔和汽油稳定塔通过精确的温度和压力控制,将汽油产品从裂化产物中分离出来,并保持其稳定性。
催化裂化装置

催化裂化装置催化裂化是炼油工业重要的二次加工装置,是提高轻质油收率,生产高辛烷值汽油,同时又多产柴油的重要手段,随着重油催化工艺的实现,其地位更加倍增。
作为一项传统的重油加工工艺,催化裂化实现工业化已经有60 年的历史,其总加工能力超过加氢裂化、焦化和减粘裂化之和,是目前最重要的重油轻质化工艺。
虽然曾多次受到加氢裂化工艺的竞争和清洁燃料标准的挑战,但由于催化裂化技术的进步,各种以催化裂化技术为核心的催化裂化“家族工艺”的不断出现,已经将催化裂化转变为“炼油-化工一体化”的主体装置,催化裂化仍然保持了其在石油化工行业中的重要地位。
我国的催化裂化技术与国际先进水平保持同步,进入21 世纪以后,由于我国催化裂化装置在炼厂地位的特殊性,技术发展的势头更猛,目前为止,基本解决了由于产品升级换代给催化裂化工艺带来的各种问题,而且在应对产品质量问题的技术开发过程中,拓宽了催化裂化产品的品种和范围,为确保催化裂化技术在未来石油化工中的核心地位提供了技术保证。
催化裂化装置的工艺原理是在流化状态下的催化剂作用下,重质烃类在480--520 C 及0.2-0.3MPa(a) 的条件下进行反应。
主要包括:1) . 裂解反应:大分子烃类裂解为小分子,环烷烃进行断环或侧链断裂,单环芳烃的烷基侧链断裂。
2) . 异构化反应:正构烷烃变成异构烷烃,带侧链的环烃或烷烃变成环异烷,产品中异构烃含量增加。
3) . 芳构化反应:环己烷脱氢生成芳香烃,烯烃环化脱氢生成芳烃。
4) . 氢转移反应:多环芳烃逐渐缩合成大分子直至焦炭,同时一种氢原子转移到烯烃分子中,使烯烃饱和成烷烃。
催化裂化装置的规模近三十年来逐步发展到350 万吨/年(加工1000 万吨/ 年原油)。
加工的原料为常压蜡油、减压渣油以及蜡油加氢裂化尾油原料主要性质装置由反应再生、分馏、吸收稳定(包括产品精制)、烟气能量回收几个部分组成。
装置主要产品为液化气、汽油、重石脑油和轻柴油,副产部分干气和油浆。
流化催化裂化装置基础知识

吸收解吸基本原理
在吸收过程中,相际传质是由三个步骤串联组成:(1)溶质由气 相主体传递到气、液相界面,即气相与界面间的对流传质;(2) 溶质在相界面上的溶解,进入液相;(3)溶质由界面传递到液相 主体,即界面与液相间的对流传质。
吸对于吸收过程的机理,一般用双膜理论进行解释,双膜理论的 基本论点如下: 相接触的气、液两相液体间存在着稳定的相界面,界面两侧各有 一很薄的有效层流膜层,溶质以分子扩散方式通过此两膜层; 界面上的气、液两相呈; 在膜层以外的气、液两相主体区无传质阻力,即浓度梯度(或分 压梯度)为零。: 双膜理论把整个相际传质过程简化为溶质通过两层有效膜的分子 扩散过程,把复杂的相际传质过程大为简化。该理论可用于具有 固定相界面的系统及流速不高的两相流体间的传质过程。
〔四 精馏基本原理
精馏原理
精馏原理:一种相平衡分离过程,其重要的理论基础是 汽-液相平衡原理,即拉乌尔定律. PA=PAOXA PB=PBOXB=PBO〔1-XA 式中: PA、PB——溶液上方组份A及B的饱和蒸汽压. PAO、PBO——纯组份A及B的饱和蒸汽压. XA、XB——溶液中组份A及B的摩尔分率.
二 流化催化裂化装置基础知识
〔三 流化原理及基本知识
流态化及流化床
固体颗粒悬浮于运动着的流体之中称为固体的流态化,使固 体小颗粒群在流体的作用下,能像流体一样流动。 工业上的固体流化是在容器内进行的,通常把容器和在其中 呈流化状态的固体颗粒合在一起称为流化床。 流化催化裂化的反应、再生的操作状况,催化剂在再生器和 沉降器间的循环输送及催化剂损失等,都与流化状态有密切 关系。 形成流化床条件 流化床的形成需具备以下三个条件:A、要有一个容器,如催 化裂化装置中反应器、再生器等,并设置有使流体分布良好 的分布器,以支撑床层并使流化良好。B、容器中要有足够数 量的固体颗粒,颗粒大小、相对密度、耐磨性能等应能满足 要求。如催化裂化装置中所使用的催化剂颗粒,C、要有流化 介质和一定的流动速度,就是使固体颗粒流化起来的介质。
催化裂化装置操作安全技术(4篇)
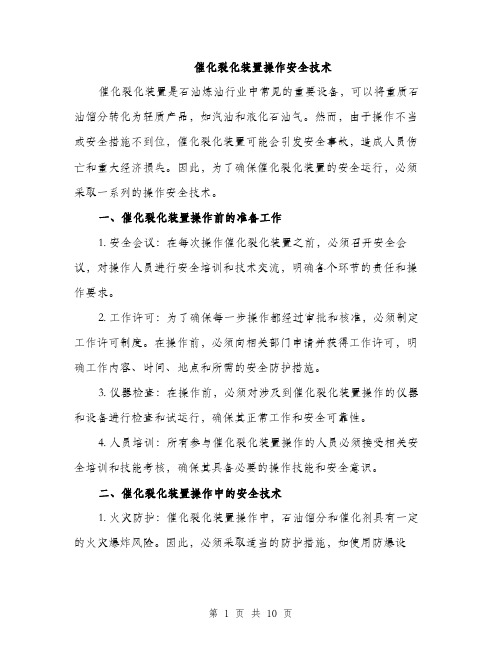
催化裂化装置操作安全技术催化裂化装置是石油炼油行业中常见的重要设备,可以将重质石油馏分转化为轻质产品,如汽油和液化石油气。
然而,由于操作不当或安全措施不到位,催化裂化装置可能会引发安全事故,造成人员伤亡和重大经济损失。
因此,为了确保催化裂化装置的安全运行,必须采取一系列的操作安全技术。
一、催化裂化装置操作前的准备工作1. 安全会议:在每次操作催化裂化装置之前,必须召开安全会议,对操作人员进行安全培训和技术交流,明确各个环节的责任和操作要求。
2. 工作许可:为了确保每一步操作都经过审批和核准,必须制定工作许可制度。
在操作前,必须向相关部门申请并获得工作许可,明确工作内容、时间、地点和所需的安全防护措施。
3. 仪器检查:在操作前,必须对涉及到催化裂化装置操作的仪器和设备进行检查和试运行,确保其正常工作和安全可靠性。
4. 人员培训:所有参与催化裂化装置操作的人员必须接受相关安全培训和技能考核,确保其具备必要的操作技能和安全意识。
二、催化裂化装置操作中的安全技术1. 火灾防护:催化裂化装置操作中,石油馏分和催化剂具有一定的火灾爆炸风险。
因此,必须采取适当的防护措施,如使用防爆设备、设置火灾报警系统、检查和维护消防设备等,以及预先制定应急预案,掌握火灾扑救方法和逃生路线。
2. 气体检测:催化裂化装置中可能会产生有毒有害气体,如硫化氢、苯等。
在操作前,必须进行气体检测,确保操作区域内无可燃气体和有毒气体,以及采取防护措施,如通风和戴防毒面具等。
3. 压力控制:催化裂化装置操作中,压力的控制非常重要。
必须合理设置压力控制装置,确保操作中的压力不超过安全界限,并经常检查和维护相关的压力表和安全阀等设备。
4. 声音和振动:催化裂化装置操作可能会产生较大的噪音和振动,对人员的健康和操作设备的正常运行都会造成影响。
因此,必须采取相应的措施,如戴防噪音耳罩、安装隔音设备和振动消除装置等,以减少噪音和振动对人员和设备的影响。
催化裂化装置工艺流程

催化裂化装置工艺流程
《催化裂化装置工艺流程》
催化裂化装置是石油化工行业中常见的一种重要装置,主要用于将重质石油原料加工成轻质高值产品,如汽油、柴油和航空燃料。
在催化裂化装置中,石油原料通过加热和催化剂的作用,发生分子内部的饱和碳链裂解,生成较轻的烃类产品,并产生丰富的芳烃和液化石油气。
催化裂化装置的工艺流程通常包括以下几个主要步骤:
1. 原料加热:首先,将经过预处理的重质石油原料送入加热炉中进行加热,使其达到裂化反应的最佳温度。
2. 催化裂化:加热后的石油原料进入裂化反应器,与催化剂接触,发生裂化反应。
在裂化过程中,重质烃分子会发生碳链裂解,生成较轻的烃类产品,包括汽油、柴油和液化石油气。
3. 分离和净化:裂化反应产物进入分馏塔,通过精馏、冷却和净化等步骤,将不同碳数的烃类产品进行分离,以得到所需的轻质产品。
4. 再生催化剂:随着反应的进行,催化剂会逐渐失活,需要通过再生来恢复其活性。
再生催化剂的过程包括焙烧和再活化,以保持催化剂的活性和稳定性。
以上便是催化裂化装置的基本工艺流程。
该装置能够将重质石
油原料转化为高附加值的轻质产品,对于提高石油炼制的产出和质量具有重要意义。
同时,催化裂化装置的工艺流程也在不断优化和改进,以适应不断变化的市场需求和环保要求。
催化裂化
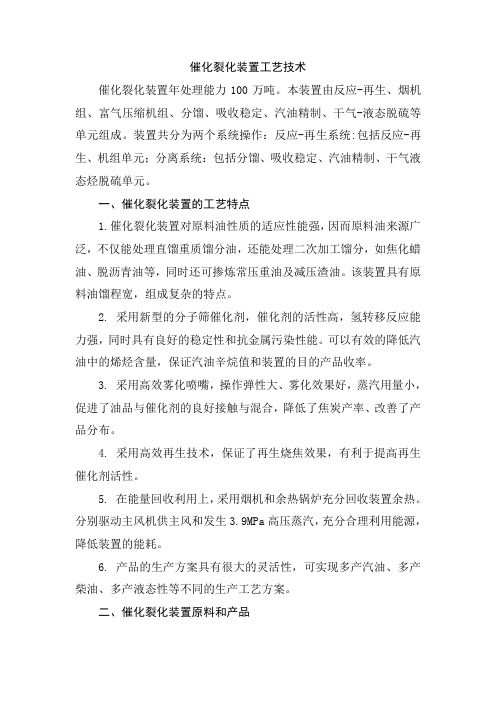
催化裂化装置工艺技术催化裂化装置年处理能力100万吨。
本装置由反应-再生、烟机组、富气压缩机组、分馏、吸收稳定、汽油精制、干气-液态脱硫等单元组成。
装置共分为两个系统操作:反应-再生系统:包括反应-再生、机组单元;分离系统:包括分馏、吸收稳定、汽油精制、干气液态烃脱硫单元。
一、催化裂化装置的工艺特点1.催化裂化装置对原料油性质的适应性能强,因而原料油来源广泛,不仅能处理直馏重质馏分油,还能处理二次加工馏分,如焦化蜡油、脱沥青油等,同时还可掺炼常压重油及减压渣油。
该装置具有原料油馏程宽,组成复杂的特点。
2. 采用新型的分子筛催化剂,催化剂的活性高,氢转移反应能力强,同时具有良好的稳定性和抗金属污染性能。
可以有效的降低汽油中的烯烃含量,保证汽油辛烷值和装置的目的产品收率。
3. 采用高效雾化喷嘴,操作弹性大、雾化效果好,蒸汽用量小,促进了油品与催化剂的良好接触与混合,降低了焦炭产率、改善了产品分布。
4. 采用高效再生技术,保证了再生烧焦效果,有利于提高再生催化剂活性。
5. 在能量回收利用上,采用烟机和余热锅炉充分回收装置余热。
分别驱动主风机供主风和发生3.9MPa高压蒸汽,充分合理利用能源,降低装置的能耗。
6. 产品的生产方案具有很大的灵活性,可实现多产汽油、多产柴油、多产液态性等不同的生产工艺方案。
二、催化裂化装置原料和产品(一)原料催化裂化装置原料主要是减三线、减四线蜡油和加氢蜡油HGO,一般来讲,衡量原料油性质指标有:馏份组成、烃类族组成、残碳、重金属、硫氮含量等五个方面。
(l) 馏份组成:馏份组成可以辨别原料的轻重和沸点范围的宽窄,在组成类型相近时,馏份越轻,越不易裂化,馏份越重,越容易裂化,因为轻组分多,不但裂化条件苛刻,而且减少了装置处理能力,同时降低汽油的辛烷值。
重组分多,使重金属含量增加及焦炭产率增加,轻质油收率下降,还会使催化剂中毒。
(2) 烃类族组成:原料油的烃类族组成说明了原料油被催化剂吸附反应的快慢。
催化裂化装置基本原理
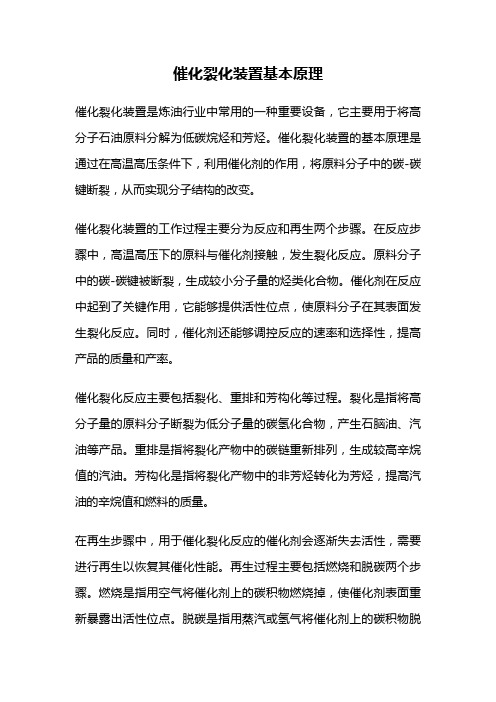
催化裂化装置基本原理催化裂化装置是炼油行业中常用的一种重要设备,它主要用于将高分子石油原料分解为低碳烷烃和芳烃。
催化裂化装置的基本原理是通过在高温高压条件下,利用催化剂的作用,将原料分子中的碳-碳键断裂,从而实现分子结构的改变。
催化裂化装置的工作过程主要分为反应和再生两个步骤。
在反应步骤中,高温高压下的原料与催化剂接触,发生裂化反应。
原料分子中的碳-碳键被断裂,生成较小分子量的烃类化合物。
催化剂在反应中起到了关键作用,它能够提供活性位点,使原料分子在其表面发生裂化反应。
同时,催化剂还能够调控反应的速率和选择性,提高产品的质量和产率。
催化裂化反应主要包括裂化、重排和芳构化等过程。
裂化是指将高分子量的原料分子断裂为低分子量的碳氢化合物,产生石脑油、汽油等产品。
重排是指将裂化产物中的碳链重新排列,生成较高辛烷值的汽油。
芳构化是指将裂化产物中的非芳烃转化为芳烃,提高汽油的辛烷值和燃料的质量。
在再生步骤中,用于催化裂化反应的催化剂会逐渐失去活性,需要进行再生以恢复其催化性能。
再生过程主要包括燃烧和脱碳两个步骤。
燃烧是指用空气将催化剂上的碳积物燃烧掉,使催化剂表面重新暴露出活性位点。
脱碳是指用蒸汽或氢气将催化剂上的碳积物脱除,以保证催化剂的活性和稳定性。
催化裂化装置的设计和操作需要考虑多个因素。
首先是选择合适的催化剂,催化剂的选择应根据原料的性质和产品的要求进行优化。
其次是控制反应的温度、压力和空速等工艺参数,以达到最佳的反应效果。
此外,催化裂化装置还需要考虑原料的预处理、氢气的补充和废热的回收利用等问题,以提高装置的效率和经济性。
催化裂化装置在炼油工业中具有重要的地位和广泛的应用。
通过裂化反应,可以将高分子的重质石油原料转化为轻质燃料和化工原料,满足市场对汽油、柴油和石脑油等产品的需求。
同时,催化裂化装置还可以提高石油产品的质量,减少环境污染物的排放,具有良好的经济和环境效益。
催化裂化装置是一种利用催化剂作用进行石油原料分解的重要设备。
催化裂化装置介绍ppt课件
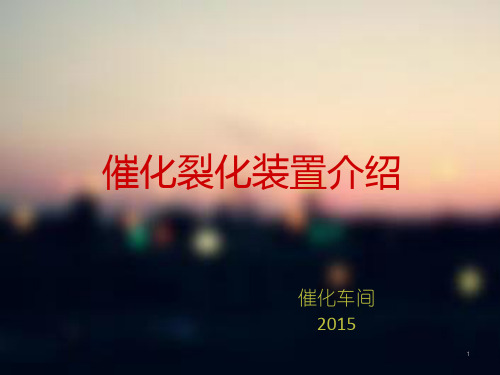
3.常压渣油:常减压装置常压塔底油(AR),硫含量、重 金属、残炭低的可以直接作为催化原料,如大庆和中原 原油等常压渣油。
4.减压渣油:除某些原油外减压塔底渣油(VR)一般不单 独作为原料,而是进行掺炼:掺炼的多少视减压渣油的 性质。
9
典型分馏系统流程
10
催化裂化工艺介绍
稳定系统
吸收-稳定系统主要由吸收塔、再吸收塔、解吸 塔及稳定塔组成。从分馏塔顶油气分离器出来的 富气中带有汽油组分,而粗汽油中溶解有C3、C4 组分。其作用是利用吸收与精馏的方法将分馏塔 顶的富气和粗汽油分离成干气、液化气和蒸气压 合格的稳定汽油。
11
典型稳定系统流程
5
典型催化裂化流程
6
催化裂化工艺介绍
反应再生系统
“ 催化裂化装置有多种类型,按反应器(或沉降器)和再
生器布置的相对位置的不同可分为两大类:①反应器和 再生器分开布置的并列式;②反应器和再生器架叠在一 起的同轴式。并列式又由于反应器(或沉降器)和再生 器位置高低的不同而分为同高并列式和高低并列式两类。
19
催化裂化主要设备-油浆泵
20
催化裂化主要设备-增压机
21
催化裂化主要设备-SIS自保系统
22
催化裂化主要设备-单动滑阀
23
催化裂化主要设备-双动滑阀
24
催化裂化主要设备-油站
25
催化裂化的原料和产品
新海石化加工工艺流程图
26
催化裂化的原料和产品
1.直馏减压馏分油:常减压装置减压塔侧线350-550℃馏分 油(VGO),石蜡基原油的VGO较好,环烷基原油的VGO 较差。
催化裂化装置简介课件
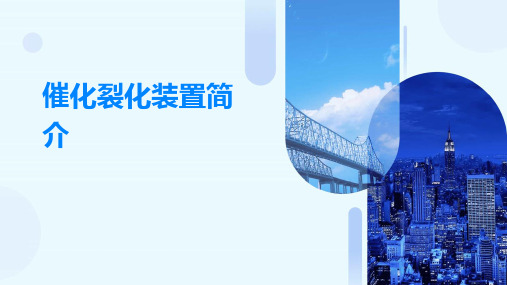
余热回收系统一般采用高温省 煤器、余热锅炉等设备进行热 量回收和利用。
04
CATALOGUE
催化裂化装置的操作与维护
操作规程
启动前检查
确保装置各部件正常,无安全隐患, 准备好所需工具和材料。
启动操作
按照规定的启动顺序和步骤进行操作 ,注意控制温度、压力等参数。
正常操作
保持装置在正常工作状态,监控各项 参数,及时调整。
环保意义
催化裂化过程中产生的焦 炭可以回收利用,减少对 环境的污染。
催化裂化装置的种类与特点
固定床催化裂化装置
适用于处理重质油,但催化剂 磨损较大,操作温度较高。
流化床催化裂化装置
催化剂与原料油接触良好,转 化率高,但操作复杂,催化剂 磨损较大。
移动床催化裂化装置
操作简单,催化剂利用率较高 ,但反应温度较高,需要处理 大量废气。
功能
主要功能是将重质油裂化成轻质油, 提高石油的利用价值,同时为化工行 业提供原料。
ቤተ መጻሕፍቲ ባይዱ
催化裂化装置的重要性
01
02
03
提高石油利用率
通过催化裂化,重质油得 以转化为轻质油,提高了 石油的利用率和经济效益 。
化工原料供应
催化裂化装置产生的裂化 气和焦炭可作为化工行业 的原料,为化工行业的发 展提供支持。
用。
吸取稳定部分
吸取塔
利用不同组分在吸取剂中的溶解度差异,分 离干气和液化石油气。
再吸取塔
对解吸塔顶部的气体进行再吸取,提高液化 石油气的回收率。
解吸塔
释放吸取剂中溶解的烃类组分,回收吸取剂 。
吸取剂循环系统
将吸取剂从再吸取塔输送到吸取塔,并收集 从解吸塔溢出的吸取剂。
催化裂化装置技术手册
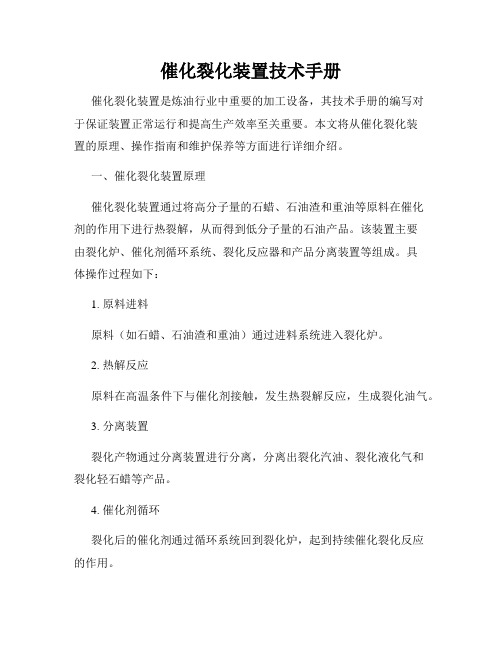
催化裂化装置技术手册催化裂化装置是炼油行业中重要的加工设备,其技术手册的编写对于保证装置正常运行和提高生产效率至关重要。
本文将从催化裂化装置的原理、操作指南和维护保养等方面进行详细介绍。
一、催化裂化装置原理催化裂化装置通过将高分子量的石蜡、石油渣和重油等原料在催化剂的作用下进行热裂解,从而得到低分子量的石油产品。
该装置主要由裂化炉、催化剂循环系统、裂化反应器和产品分离装置等组成。
具体操作过程如下:1. 原料进料原料(如石蜡、石油渣和重油)通过进料系统进入裂化炉。
2. 热解反应原料在高温条件下与催化剂接触,发生热裂解反应,生成裂化油气。
3. 分离装置裂化产物通过分离装置进行分离,分离出裂化汽油、裂化液化气和裂化轻石蜡等产品。
4. 催化剂循环裂化后的催化剂通过循环系统回到裂化炉,起到持续催化裂化反应的作用。
二、催化裂化装置操作指南1. 温度控制裂化炉温度是影响裂化反应效果的关键参数。
在操作中,应根据不同原料的特性和所需产品质量,合理控制催化裂化温度,避免温度过高导致催化剂失活或温度过低影响反应速率。
2. 原料选择不同原料的性质对裂化反应的影响有所差异。
应根据目标产品质量和市场需求,合理选择原料,并进行合适的预处理,如脱蜡、脱硫等,以提高裂化效果和产品品质。
3. 催化剂活性管理催化剂是催化裂化装置中最关键的组成部分。
为保证装置的正常运行,应定期检测催化剂的活性,并进行必要的处理,如焙烧、再生等,以延长催化剂的使用寿命。
4. 安全操作在操作催化裂化装置时,应严格遵守操作规程,保证操作人员的人身安全和设备的正常运行。
同时,应加强对催化裂化装置的检测和维护,及时发现和处理潜在的安全隐患。
三、催化裂化装置维护保养1. 清洗与清理定期对催化裂化装置进行清洗和清理,去除附着物、沉积物和焦炭,以保证装置的畅通和正常运行。
2. 检修和更换定期进行设备的检修和更换,如检修泵、阀门等关键设备,更换老化和磨损的零部件,以确保催化裂化装置的长期稳定运行。
催化裂化的装置简介及工艺流程
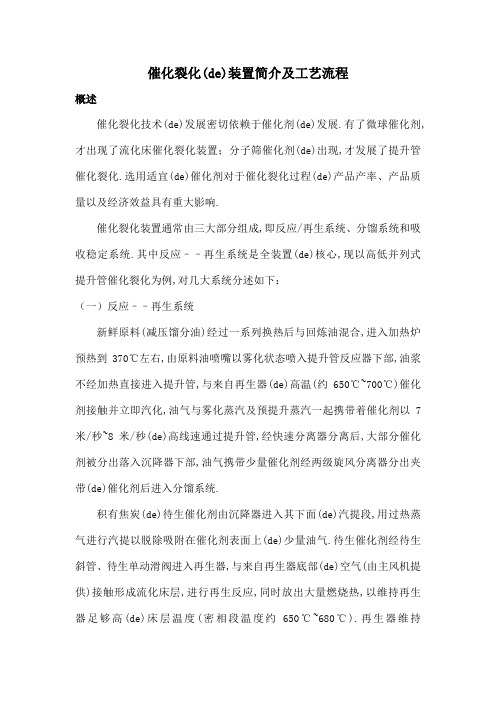
催化裂化(de)装置简介及工艺流程概述催化裂化技术(de)发展密切依赖于催化剂(de)发展.有了微球催化剂,才出现了流化床催化裂化装置;分子筛催化剂(de)出现,才发展了提升管催化裂化.选用适宜(de)催化剂对于催化裂化过程(de)产品产率、产品质量以及经济效益具有重大影响.催化裂化装置通常由三大部分组成,即反应/再生系统、分馏系统和吸收稳定系统.其中反应––再生系统是全装置(de)核心,现以高低并列式提升管催化裂化为例,对几大系统分述如下:(一)反应––再生系统新鲜原料(减压馏分油)经过一系列换热后与回炼油混合,进入加热炉预热到370℃左右,由原料油喷嘴以雾化状态喷入提升管反应器下部,油浆不经加热直接进入提升管,与来自再生器(de)高温(约650℃~700℃)催化剂接触并立即汽化,油气与雾化蒸汽及预提升蒸汽一起携带着催化剂以7米/秒~8米/秒(de)高线速通过提升管,经快速分离器分离后,大部分催化剂被分出落入沉降器下部,油气携带少量催化剂经两级旋风分离器分出夹带(de)催化剂后进入分馏系统.积有焦炭(de)待生催化剂由沉降器进入其下面(de)汽提段,用过热蒸气进行汽提以脱除吸附在催化剂表面上(de)少量油气.待生催化剂经待生斜管、待生单动滑阀进入再生器,与来自再生器底部(de)空气(由主风机提供)接触形成流化床层,进行再生反应,同时放出大量燃烧热,以维持再生器足够高(de)床层温度(密相段温度约650℃~680℃).再生器维持~(表)(de)顶部压力,床层线速约米/秒~米/秒.再生后(de)催化剂经淹流管,再生斜管及再生单动滑阀返回提升管反应器循环使用.烧焦产生(de)再生烟气,经再生器稀相段进入旋风分离器,经两级旋风分离器分出携带(de)大部分催化剂,烟气经集气室和双动滑阀排入烟囱.再生烟气温度很高而且含有约5%~10%CO,为了利用其热量,不少装置设有CO锅炉,利用再生烟气产生水蒸汽.对于操作压力较高(de)装置,常设有烟气能量回收系统,利用再生烟气(de)热能和压力作功,驱动主风机以节约电能.(二)分馏系统分馏系统(de)作用是将反应/再生系统(de)产物进行分离,得到部分产品和半成品.由反应/再生系统来(de)高温油气进入催化分馏塔下部,经装有挡板(de)脱过热段脱热后进入分馏段,经分馏后得到富气、粗汽油、轻柴油、重柴油、回炼油和油浆.富气和粗汽油去吸收稳定系统;轻、重柴油经汽提、换热或冷却后出装置,回炼油返回反应––再生系统进行回炼.油浆(de)一部分送反应再生系统回炼,另一部分经换热后循环回分馏塔.为了取走分馏塔(de)过剩热量以使塔内气、液相负荷分布均匀,在塔(de)不同位置分别设有4个循环回流:顶循环回流,一中段回流、二中段回流和油浆循环回流.催化裂化分馏塔底部(de)脱过热段装有约十块人字形挡板.由于进料是460℃以上(de)带有催化剂粉末(de)过热油气,因此必须先把油气冷却到饱和状态并洗下夹带(de)粉尘以便进行分馏和避免堵塞塔盘.因此由塔底抽出(de)油浆经冷却后返回人字形挡板(de)上方与由塔底上来(de)油气逆流接触,一方面使油气冷却至饱和状态,另一方面也洗下油气夹带(de)粉尘.(三)吸收--稳定系统从分馏塔顶油气分离器出来(de)富气中带有汽油组分,而粗汽油中则溶解有C3、C4甚至C2组分.吸收––稳定系统(de)作用就是利用吸收和精馏(de)方法将富气和粗汽油分离成干气(≤C2)、液化气(C3、C4)和蒸汽压合格(de)稳定汽油.装置简介(一)装置发展及其类型1.装置发展催化裂化工艺产生于20世纪40年代,是炼油厂提高原油加工深度(de)一种重油轻质化(de)工艺.20世纪50年代初由ESSO公司(美国)推出了Ⅳ型流出催化装置,使用微球催化剂(平均粒径为60—70tan),从而使催化裂化工艺得到极大发展.1958年我国第一套移动床催化裂化装置在兰州炼油厂投产.1965年我国自己设计制造施工(de)Ⅳ型催化装置在抚顺石油二厂投产.经过近40年(de)发展,催化裂化已成为炼油厂最重要(de)加工装置.截止1999年底,我国催化裂化加工能力达8809.5×104t/a,占一次原油加工能力(de)33.5%,是加工比例最高(de)一种装置,装置规模由(34—60)×104t /a发展到国内最大300×104t/a,国外为675×104t/a.随着催化剂和催化裂化工艺(de)发展,其加工原料由重质化、劣质化发展至目前全减压渣油催化裂化.根据目(de)产品(de)不同,有追求最大气体收率(de)催化裂解装置(DCC),有追求最大液化气收率(de)最大量高辛烷值汽油(de)MGG工艺等,为了适应以上(de)发展,相应推出了二段再生、富氧再生等工艺,从而使催化裂化装置向着工艺技术先进、经济效益更好(de)方向发展.2.装置(de)主要类型催化裂化装置(de)核心部分为反应—再生单元.反应部分有床层反应和提升管反应两种,随着催化剂(de)发展,目前提升管反应已取代了床层反应.再生部分可分为完全再生和不完全再生,一段再生和二段再生(完全再生即指再生烟气中CO含量为10—6级).从反应与再生设备(de)平面布置来讲又可分为高低并列式和同轴式,典型(de)反应—再生单元见图2—4、图2—5、图2—6、图2—7,其特点见表2—11.(二)装置单元组成与工艺流程1.组成单元催化裂化装置(de)基本组成单元为:反应—再生单元,能量回收单元,分馏单元,吸收稳定单元.作为扩充部分有:干气、液化气脱硫单元,汽油、液化气脱硫醇单元等.各单元作用介绍如下.(1)反应—再生单元重质原料在提升管中与再生后(de)热催化剂接触反应后进入沉降器(反应器),油气与催化剂经旋风分离器与催化剂分离,反应生成(de)气体、汽油、液化气、柴油等馏分与未反应(de)组分一起离开沉降器进入分馏单元.反应后(de)附有焦炭(de)待生催化剂进入再生器用空气烧焦,催化剂恢复活性后再进入提升管参加反应,形成循环,再生器顶部烟气进入能量回收单元.(2)三机单元所谓三机系指主风机、气压机和增压机.如果将反一再单元作为装置(de)核心部分,那么主风机就是催化裂化装置(de)心脏,其作用是将空气送人再生器,使催化剂在再生器中烧焦,将待生催化剂再生,恢复活性以保证催化反应(de)继续进行.增压机是将主风机出口(de)空气提压后作为催化剂输送(de)动力风、流化风、提升风,以保持反—再系统催化剂(de)正常循环.气压机(de)作用是将分馏单元(de)气体压缩升压后送人吸收稳定单元,同时通过调节气压机转数也可达到控制沉降器顶部压力(de)目(de),这是保证反应再生系统压力平衡(de)一个手段.(3)能量回收单元利用再生器出口烟气(de)热能和压力使余热锅炉产生蒸汽和烟气轮机作功、发电等,此举可大大降低装置能耗,目前现有(de)重油催化裂化装置有无此回收系统,其能耗可相差1/3左右.(4)分馏单元沉降器出来(de)反应油气经换热后进入分馏塔,根据各物料(de)沸点差,从上至下分离为富气(至气压机)、粗汽油、柴油、回炼油和油浆.该单元(de)操作对全装置(de)安全影响较大,一头一尾(de)操作尤为重要,即分馏塔顶压力、塔底液面(de)平稳是装置安全生产(de)有力保证,保证气压机人口放火炬和油浆出装置系统(de)通畅,是安全生产(de)必备条件. (5)吸收稳定单元经过气压机压缩升压后(de)气体和来自分馏单元(de)粗汽油,经过吸收稳定部分,分割为干气、液化气和稳定汽油.此单元是本装置甲类危险物质最集中(de)地方.(6)产品精制单元包括干气、液化气脱硫和汽油液化气脱硫醇单元该两部分,干气、液化气在胺液(乙醇胺、二乙醇胺、Ⅳ—甲基二乙醇胺等)作用下、吸收干气、液化气中(de)H2S气体以达到脱除H2S(de)目(de).汽油和液化气在碱液状态中在磺化酞氰钴或聚酞氰钻作用下将硫醇氧化为二硫化物,以达到脱除硫醇(de)目(de).2.工艺流程工艺原则流程见图2—8.原料油由罐区或其他装置(常减压、润滑油装置)送来,进入原料油罐,由原料泵抽出,换热至200—300°C左右,分馏塔来(de)回炼油和油浆一起进入提升管(de)下部,与由再生器再生斜管来(de)650~700°C再生催化剂接触反应,然后经提升管上部进入分馏塔(下部);反应完(de)待生催化剂进入沉降器下部汽提段.被汽提蒸汽除去油气(de)待生剂通过待生斜管进入再生器下部烧焦罐.由主风机来(de)空气送人烧焦罐烧焦,并同待生剂一道进入再生器继续烧焦,烧焦再生后(de)再生催化剂由再生斜管进人提升管下部循环使用.烟气经一、二、三级旋分器分离出催化剂后,其温度在650~700°C,压力0.2-0.3MPa(表),进人烟气轮机作功带动主风机,其后温度为500—550°C,压力为0.01MPa(表)左右,再进入废热锅炉发生蒸汽,发汽后(de)烟气(温度大约为200℃左右)通过烟囱排到大气.反应油气进入分馏塔后,首先脱过热,塔底油浆(油浆中含有2%左右催化剂)分两路,一路至反应器提升管,另一路经换热器冷却后出装置.脱过热后油气上升,在分馏塔内自上而下分离出富气、粗汽油、轻柴油、回炼油.回炼油去提升管再反应,轻柴油经换热器冷却后出装置,富气经气压机压缩后与粗汽油共进吸收塔,吸收塔顶(de)贫气进入再吸收塔由轻柴油吸收其中(de)C4-C5,再吸收塔顶干气进入干气脱硫塔脱硫后作为产品出装置,吸收塔底富吸收油进入脱吸塔以脱除其中(de)C2.塔底脱乙烷汽油进入稳定塔,稳定塔底油经碱洗后进入脱硫醇单元脱硫醇后出装置,稳定塔顶液化气进入脱硫塔脱除H,S,再进入脱硫醇单元脱硫醇后出装置.(脱硫脱硫醇未画出)(三)化学反应过程1.催化裂化反应(de)特点催化裂化反应是在催化剂表面上进行(de),其反应过程(de)7个步骤如下:①气态原料分子从主流扩散到催化剂表面;②原料分子沿催化剂外向内扩散;③原料分子被催化剂活性中心吸附;④原料分子发生化学反应;⑤产品分子从催化剂内表面脱附;⑥产品分子由催化剂外向外扩散;⑦产品分子扩散到主流中.重质原料反应生成目(de)产品可用下图表示:2.催化裂化反应种类石油馏分是由十分复杂(de)烃类和非烃类组成,其反应过程十分复杂,种类繁多,大致分为几个类型.(1)裂化反应是主要(de)反应.即C—C键断裂,大分子变为小分子(de)反应.(2)异构化反应是重要(de)反应.即化合物(de)相对分子量不变,烃类分子结构和空间位置变化,所以催化裂化产物中会有较多异构烃.(3)氢转移反应是一个烃分子上(de)氢脱下来加到另一个烯烃分子上,使其烯烃饱和,该反应是催化裂化特有(de)反应.虽然氢转移反应会使产品安定性变好,但是大分子(de)烃类反应脱氢将生成焦炭.(4)芳构化反应烷烃、烯烃环化生成环烷烃和环烯烃,然后进一步氢转移反应生成芳烃,由于芳构化反应使汽油、柴油中芳烃较多.除以上反应外,还有甲基转移反应、叠合反应和烷基化反应等.(四)主要操作条件及工艺技术特点1.主要操作条件因不同(de)工艺操作条件不尽相同,表2—12列出一般一段再生催化裂化(de)主要操作条件.2.工艺技术特点(1)微球催化剂(de)气—固流态化催化裂化确切一点应该叫作流化催化裂化.微球催化剂(60—70/1m 粒径)在不同气相线速下呈现不同状态,可分为固定床(即催化剂不动)、流化床(即催化剂只在一定(de)空间运动)和输送床(即催化剂与气相介质一同运动而离开原来(de)空间)三种.过程是流化床,所以微球催化剂(de)气—固流态化是催化裂化工艺得以发展(de)基础,从而使反应—再生能在不同(de)条件下得以实现.(2)催化裂化(de)化学反应最主要(de)反应是大分子烃类裂化为小分子烃类(de)化学反应,从而使原油中大于300℃馏分(de)烃类生成小分子烃类、气体、液化气、汽油、柴油等,极大地增加了炼油厂(de)轻质油收率,并能副产气体和液化气.(五)催化剂及助剂1.催化剂烃类裂化反应,应用热裂化工艺也能完成,但是有了催化剂(de)参加,其化学反应方式不同,所以导致二类工艺(de)产品性质和产品分布都不同.目前催化裂化所使用(de)催化剂都是分子筛微球催化剂,根据不同产品要求可制造出各种型号(de)催化剂.但其使用性能要求是共同(de),即高活性和选择性,良好(de)水热稳定性,抗硫、氮、重金属(de)中毒;好(de)强度,易再生,流化性能好等.目前常见(de)有重油催化裂化催化剂、生产高辛烷值汽油催化剂、最大轻质油收率催化剂、增加液化气收率催化剂和催化裂解催化剂等.由于催化裂化原料(de)重质化,使重油催化剂发展十分迅速,目前国内全渣油型催化剂性能见表2—13.2.催化裂化助剂为了补充催化剂(de)其他性能,近年来发展了多种起辅助作用(de)助催化剂,这些助剂均以剂(de)方式,加到裂化催化剂中起到除催化裂化过程外(de)其他作用.如促进再生烟气中CO转化为C02,提高汽油辛烷值,钝化原料中重金属对催化剂活性毒性,降低烟气中(de)SOx(de)含量等各类助剂,它们绝大多数也是制造成与裂化催化剂一样(de)微球分别加入再生器内,但占总剂量很少,一般在1%—3%,所以每天添加量只有10-1000kS/d左右.CO助燃剂为SiO2—Al2O3细粉上载有活性金属铂制成.辛烷值助剂大多是含有15%-20%ZSM—5分子筛(de)Si—Al微球剂.而金属钝化剂为液态型含锑(de)化合物,将其注入原料油中,使其分解(de)金属锑沉积在催化剂上以钝化Ni(de)活性.(六)原料及产品性质1.催化裂化原材料各类催化裂化所使用(de)原材料不尽相同,现将一般所使用(de)原材料主要性质汇总,见表2—14.2.产品性质产品性质见表2-15。
催化裂化装置工艺流程
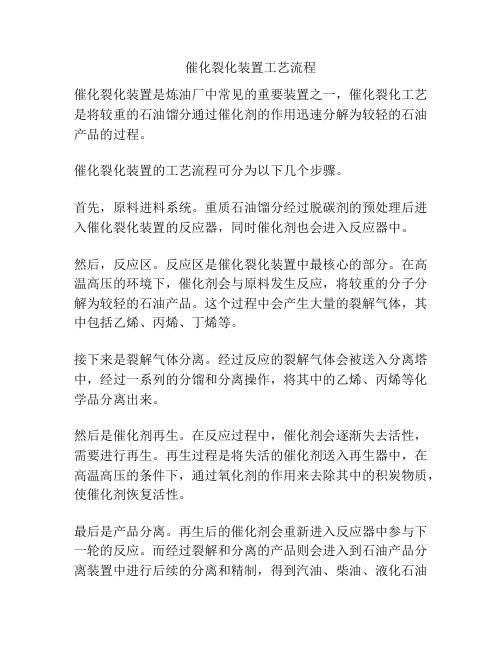
催化裂化装置工艺流程催化裂化装置是炼油厂中常见的重要装置之一,催化裂化工艺是将较重的石油馏分通过催化剂的作用迅速分解为较轻的石油产品的过程。
催化裂化装置的工艺流程可分为以下几个步骤。
首先,原料进料系统。
重质石油馏分经过脱碳剂的预处理后进入催化裂化装置的反应器,同时催化剂也会进入反应器中。
然后,反应区。
反应区是催化裂化装置中最核心的部分。
在高温高压的环境下,催化剂会与原料发生反应,将较重的分子分解为较轻的石油产品。
这个过程中会产生大量的裂解气体,其中包括乙烯、丙烯、丁烯等。
接下来是裂解气体分离。
经过反应的裂解气体会被送入分离塔中,经过一系列的分馏和分离操作,将其中的乙烯、丙烯等化学品分离出来。
然后是催化剂再生。
在反应过程中,催化剂会逐渐失去活性,需要进行再生。
再生过程是将失活的催化剂送入再生器中,在高温高压的条件下,通过氧化剂的作用来去除其中的积炭物质,使催化剂恢复活性。
最后是产品分离。
再生后的催化剂会重新进入反应器中参与下一轮的反应。
而经过裂解和分离的产品则会进入到石油产品分离装置中进行后续的分离和精制,得到汽油、柴油、液化石油气等多种石油产品。
整个催化裂化装置的工艺流程需要严格控制各个环节的工艺参数,以确保裂化气体的质量和产品的纯度。
同时,催化剂的性能和使用寿命也是需要重点关注的问题,原料的质量和稳定性也会直接影响到整个工艺的效果。
催化裂化装置的工艺流程通过高效的催化剂和合理的工艺操作来实现重质石油馏分的转化,不仅提高了石油资源的利用率,还为石油产品提供了丰富的选择。
然而,由于催化裂化装置操作条件的复杂性和催化剂的高成本,装置的优化和经济性也是需要进一步研究和探索的方向。
催 化 裂 化 装 置
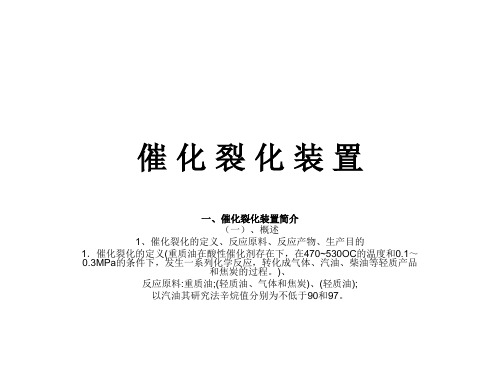
催化裂化装置
• • • • • • • • • • • • • • • • • • • • • • • • • • • • Ⅱ催化装置暂行工艺指标
1、反应、再生系统: 沉降器顶部压力:0.105±0.005MPa 再生器顶部压力:0.130±0.005MPa 反应沉降器蔵量:70±1%表刻度 再生器蔵量:75±5%表刻度 提升管出口温度:500±2℃ 轻汽油回炼提升管出口温度:520±1℃ 轻汽油回炼量≮1t/h(以烯烃合格为准) 再生器床层温度:690±5℃ 外取热汽包液位:50%表刻度 余锅液位:50%表刻度 汽包软化水碱度20±2 余锅软化水碱度14±2 再生剂定碳:≯0.2%(m) 原料预热温度:175±5℃ 2、分馏系统: 分馏塔顶温度:95±2℃ 柴油馏出温度: 0#方案 170±5℃(以产品质量合格为准) 人字挡板上:340±5℃ 分馏塔底温度:340±5℃ 分馏塔底液位:50%表刻度 粗汽油罐液位: 50%表刻度 粗汽油罐介面:50%表刻度 轻汽油罐液位:35%表刻度 轻汽油罐脱水介面:50%表刻度 顶循罐脱水介面:50%表刻度 柴油汽提塔液位:50%表刻度
催化裂化装置
• • 柴油部分 柴油从分馏塔第十九层塔板自流到柴油汽提塔, 经过热蒸汽汽提后,气体返回分馏塔第十九层 气相上,液相用柴油泵抽出,经过软化水换热 器和冷却器冷却后进入柴油集合管,一路去封 油罐作燃烧油,一路补充中段循环回流返到分 馏塔第十八层上,一路去废品罐,一路经调节 阀,质量流量计出装置,去FS法柴油精制系统, 使氧化沉渣和色度合格,之后去成品班产罐。
催化裂化装置
• • • • • • • • • • • • • • • 2、分馏系统: 分馏塔顶温度:88±2℃ 柴油馏出温度: -15#方案 155±2℃ 人字挡板上: 335-355℃ 分馏塔底温度:347±2℃ 分馏塔底液位:50%表刻度 粗汽油罐液位:50%表刻度 粗汽油罐介面:50%表刻度 轻汽油罐液位:30%表刻度 轻汽油罐脱水介面:50%表刻度 顶循罐脱水介面:50%表刻度 柴油汽提塔液位:50%表刻度 柴油出装置温度:≯65℃ 汽油出装置温度: ≯40℃ 外甩油浆温度:≯95℃
催化裂化催化剂加药装置

催化裂化催化剂加药装置催化裂化催化剂加药装置是炼油过程中常用的设备,用于向催化裂化装置中添加催化剂。
本文将介绍催化裂化催化剂加药装置的原理、结构以及操作注意事项。
一、催化裂化催化剂加药装置的原理催化裂化是一种通过加热重质石油燃料,在催化剂的作用下,将大分子烃化合物裂解成小分子烃化合物的过程。
催化裂化催化剂加药装置的原理就是将催化剂通过输送系统输送到催化裂化装置中,确保装置正常运转。
二、催化裂化催化剂加药装置的结构催化裂化催化剂加药装置主要由输送系统、储存系统和控制系统等组成。
1. 输送系统:输送系统用于将催化剂从储存系统输送到催化裂化装置中。
通常使用的输送方式有气力输送和机械输送。
其中,气力输送通过气流将催化剂输送到装置中,机械输送则通过螺旋输送器等机械设备将催化剂输送至装置。
2. 储存系统:储存系统用于储存催化剂,保证供应连续稳定。
常见的储存设备有储罐、密闭容器等,可以根据需求选择合适的储存设备。
3. 控制系统:控制系统用于监测和控制催化剂加药装置的工作状态。
通常包括温度、压力、流量等参数的监测与调节功能,确保装置运行平稳。
三、催化裂化催化剂加药装置的操作注意事项1. 定期维护:催化裂化催化剂加药装置进行长时间使用后,会出现磨损和堵塞等问题。
因此,定期进行设备维护是十分必要的,以保证装置的正常运行。
2. 催化剂质量控制:催化剂的质量直接影响到催化裂化装置的工作效率和产品质量。
因此,在选择催化剂供应商时,应该严格把关,确保供应的催化剂符合要求。
3. 安全操作:在进行催化剂加药装置的操作时,必须严格按照操作规程进行,防止发生事故。
操作人员需要佩戴符合要求的个人防护装备,并且要了解和掌握装置的工作原理和各个部位的功能。
4. 清洗及更换催化剂:由于催化剂会随着时间的推移而失效,因此,需要定期清洗和更换催化剂。
在进行清洗和更换时,应该严格按照相关规定操作,并注意催化剂的保护,避免外界因素对其造成损害。
综上所述,催化裂化催化剂加药装置在炼油过程中起到至关重要的作用。
- 1、下载文档前请自行甄别文档内容的完整性,平台不提供额外的编辑、内容补充、找答案等附加服务。
- 2、"仅部分预览"的文档,不可在线预览部分如存在完整性等问题,可反馈申请退款(可完整预览的文档不适用该条件!)。
- 3、如文档侵犯您的权益,请联系客服反馈,我们会尽快为您处理(人工客服工作时间:9:00-18:30)。
催化裂化装置一、催化裂化在炼油工业中的作用催化裂化是重要的石油二次加工手段之一,催化裂化是现代化炼油厂用来改质重质馏分和渣油的核心技术。
一般原油经过一次加工(即常减压蒸馏)后可得到10~40%的汽油,煤油及柴油等轻质油品,其余的是重质馏分和残渣油。
如果不经过二次加工它们只能作为润滑油原料或重质燃料油。
但是国民经济和国防上需要的轻质油量是很大的,但市场对轻质油的需求量是很大的,以我国目前为例,对轻质燃料油、重质燃料油和润滑油的需求比例大约是20:6:1;另一方面,由于内燃机的发展,对汽油的质量提出了更高的要求,而一般直馏汽油则难以满足这些要求。
如目前我国车用汽油标准里面所有汽油的研究法辛烷值都在90以上,随着我国高标号汽油(指研究法辛烷值为93及以上汽油)的消费量不断增长,高标号汽油产量所占的比例已由2003年的28.5%上升到2006年的56.5%。
而直馏汽油的辛烷值一般只有40~60,不能满足上述要求。
催化裂化是目前石油炼制工业中最重要的二次加工过程,也是重油轻质化(生产汽、柴油)的核心工艺。
催化裂化以各种重质油(VGO、CGO、AR、VR等)为原料,在500℃左右、0.2~0.4MPa及催化剂的作用下,通过催化裂化反应得到气体(干气和LPG)、高辛烷值汽油、催化柴油(LCO)、重质油及焦炭。
因此,催化裂化是提高原油加工深度、增加轻质油收率的重要手段。
就加工能力来说,我国的催化裂化位居其它二次加工过程之首,催化裂化几乎是所有石化企业最重要的二次加工手段。
催化裂化过程有以下几个特点:轻质油收率高,可达70%~80%;催化裂化汽油的辛烷值较高,安定性好;催化裂化汽柴油十六烷值较低,常与直馏柴油调合才能使用;催化裂化气体产品中,80%是C3和C4烃类(称为液化石油气LPG),其中丙烯和丁烯占一半以上,因此这部分产品是优良的石油化工和生产高辛烷值汽油组分的原料。
二、工艺原理概述催化裂化装置的原料油主要是常减压直馏蜡油、减压渣油、洗涤油、焦化蜡油、加氢蜡油、催化裂化装置是一套同轴式重油—汽油双提升管—双沉降—双分馏灵活多效流化催化裂化装置(缩写为FDFCC-III)。
其工艺原理是原料油经进料喷嘴雾化后,在一定的温度、压力的条件下,通过与预混合后的高温催化剂的接触、升温、汽化并发生裂化、异构化、氢转移、脱氢和缩合等一系统化学反应;经重油提升管反应产生的粗汽油再进入汽油提升管喷嘴雾化后,与高温催化剂进行接触、升温、汽化在进一步进行反应。
经过反应后生成汽油、柴油、液化气、干气、焦炭、油浆。
参与反应的催化剂在反应—再生器或反应—反应器内,靠稀密相输送形成循环流动,并经各自沉降器汽提后,汽油沉降器内一部分催化剂进入重油提升管预混合段,一部分与重油待生催化剂分别进入再生器烧焦,恢复其活性。
在重油反应器中裂解后的高温混合产物进入主分馏塔,由于各种馏分的沸点不同,经蒸馏得到柴油、油浆。
柴油和油浆作为产品出装置。
塔顶气体冷却后,得到粗汽油和富气,部分粗汽油或外部来的粗汽油去汽油提升管回炼。
在汽油反应器中裂解后的高温混合产物进入副分馏塔,经油浆洗涤、降温、饱和、蒸馏得到柴油组分。
柴油组分通过中段液位调节返回主分馏塔。
塔顶气体冷却后。
得到粗汽油和富气,粗汽油作吸收剂去吸收塔。
同主副分馏塔来的富气经气压机压缩、提压后与粗汽油分别进入吸收解吸系统,利用组分溶解度的不同分出干气和脱乙烷汽油。
脱乙烷汽油进入稳定塔,经过精馏过程,得到液化气和稳定汽油。
干气和液态烃送至脱硫装置进行脱硫处理;稳定汽油经轻重汽油分离后,重汽油送至30万吨/年催化重汽油选择性加氢装置进行加氢精制,加氢精制后的汽油与轻汽油一并送至电碱精制,再送至碱液抽提进行脱硫醇性硫处理,然后再经过无碱脱臭装置送至成品罐区。
三、主要工艺流程1、反再系统工艺流程(图2 催化装置反再系统流程图)由原料加热器(E209)来的原料油分四路经原料油雾化喷嘴进入提升管提升管(R101A)与预混合后的催化剂接触并迅速升温、汽化,在与催化剂沿提升管向上流动的同时,原料不断发生催化反应,生成汽油、轻柴油、液化气、干气、油浆、焦炭。
焦炭覆盖在催化剂表面,使其逐渐丧失裂化活性。
反应油气与待生催化剂在重油提升管出口处经两组粗旋风分离器分离后,油气进入沉降器(R101B)的直接分配器,再经四组单级旋风分离器进一步除去携带的催化剂细粉,最后经内集气室离开沉降器,进入主分馏塔(T201)进行分馏。
自重油油气分离器(V203)出来的粗汽油经泵提升后,自轻重汽油分离装置来的轻汽油,经反应控制阀分四路进入汽油提升管反应器(R2101A),与高温再升催化剂接触完成汽油的升温、气化及反应。
由V203底来的酸性水作为终止剂分两路分别进入R101A、R2101A上部各自的两个终止剂喷嘴。
反应油气与待生催化剂在汽油提升管出口经两组粗旋风分离器快速分离后,油气进入汽油沉降器(R2101B) 内,再经两组单级旋风分离器进一步除去携带的催化剂细粉,最后经内集气室离开汽油沉降器,进入副分馏塔(T2201)进行分馏。
R101A粗旋以及重油沉降器单级旋风分离器、直连分配器回收的待生催化剂一起进入R101B汽提段,在此,待生催化剂与蒸汽逆流接触以及汽提催化剂所携带的油气,汽提后催化剂沿待生立管下流,经待生立管并通过待生塞阀、待生套筒及出口的分配器,在增压风和待生催化剂自身静压的推动下进入R2101B汽提段。
在此,待生催化剂与蒸汽逆流接触以及汽提催化剂所携带的油气。
汽提后催化剂分两路,一路作为待生催化剂经待生立管、待生斜管并通过待生物质循环阀进入重油提升管预混合段与高温再生催化剂混合,一路作为待生催化剂待生立管、待生滑阀进入R101C密相床上部;由两沉降器来的待生催化剂与主风,在700℃左右的再生温度及CO助燃剂助燃的条件下进行完全再生。
烧焦过程中产生的过剩热量分别由外取热器取走。
含炭量0.1%左右的再生催化剂,通过重油提升管反应器、汽油提升管反应器各自的再生立管及再生单动滑阀,分别进入其反应器底部。
在干气、蒸汽的提升下,完成催化剂加速、分散过程,然后与原料油、粗同、轻汽油等接触反应。
回炼油分两路经回炼油喷嘴进入提升管中下部,也可直接与原料油混合进入原料油喷嘴。
在提升管上部设有两个喷嘴,用以注入汽油或其他较轻介质作为终止剂,以提高催化剂与原料油的混合温度,减少生焦量,控制二次反应。
再生器产生的烟气,经8组两级旋风分离器分离催化剂,再经第三级旋风分离器(CY102)进一步分离催化剂细粉后进入烟气轮机(BE101)膨胀做功,驱动1#主风机组(能量回收机组)。
烟气出烟气轮机后再进入余热锅炉加热除氧水、发生并过热(3.5Mpa)的蒸汽,进一步回收烟气能量,将温度降到200℃以下,经烟囱排入大气。
2、分馏系统工艺流程(图3 催化装置分馏系统流程图)由重油沉降器来的反应油气进入主分馏塔底部,通过圆型挡板与循环油浆逆流充分接触,洗涤反应油气中的催化剂粉尘并脱除过热,使油气呈“饱和状态”进入主分馏塔上部进行分馏。
主分馏塔顶油气经油气-热水换热器(E-201/1~8)换热后,•再经主分馏塔顶油气—循环水冷凝冷却器(E-202/1~8)冷却至40℃,进入主分馏塔顶油气分离器(V-2O3)•进行气液相分离;分离出的富气进入气压机,分离出的粗汽油经粗汽油泵(P-203/1.2)分两路,一路去反应作回炼粗汽油,另一路作冷回流去主分馏塔;含硫、含铵酸性水由酸性水泵(P-210/1.•2) 抽出。
轻柴油自分馏塔第十一层或十三层抽出自流至轻柴油气提塔(T-202)。
经汽提后,塔底的轻柴油由轻柴油泵(P-205/1.2)抽出,经轻柴油-热水换热器(•E-205/1~4),轻柴油-富吸收油换热器(E-206/1.2)换热后,•再经轻柴油冷却器(E-207),使轻柴油温度降至70℃分成三路:一路作为产品出装置,一路作机泵封油或冲先油去V204,•一路经贫吸收油冷却器(E-208),使其温度降至40℃,由再吸收油泵(P-212/1,2)送至再吸收塔(T-303)作吸收剂。
从稳定再吸收塔返回的富吸收油经柴油—富吸收油换热,再与焦化蜡油—富吸收油换热(E-213)换热升温后,再自压至主分馏塔的第九层或十二、十四层。
重柴油自主分馏塔第二十一层或第二十三层抽出,由冷料泵P-202/1送至油浆换热器E-212冷却至80℃后出装置。
回炼油自主分馏塔第二十八层自流入回炼油罐(V-202),再经回炼油泵(P-207/1.•2)升压后,一路单独或与原料油混合进提升管反应器回炼,另一路返回主分馏塔第二十九层。
主分馏塔多余热量分别由塔顶循环回流、中段循环回流及油浆循环回流取走。
顶循环回流自主分馏塔第四层塔盘抽出,用顶循环油泵(P-204/1.2)升压,经顶循环油-热水换热器(E-203/1~12),温度降至80℃后返回主分馏塔第一层。
中段回流油自主分馏塔第十七层抽出经中段循环油泵(P-206/1.2)升压后,•依次作为稳定塔(T304)底重沸器(E-306)的热源,并经中段循环油-热水换热器(E-204/1.2),温度降至190℃返回主分馏塔的第十四层板上。
油浆自主分馏塔底由循环油浆泵(P-208/2.3)抽出后分两路:一路送至常减压装置换热,然后分为两部分,一部分经油浆过滤器(V-401/1.2)、产品油浆-热水换热器(E-211/1.2)、产品油浆冷却水箱(E-212),温度降至90℃送出装置。
另一部分经循环油浆蒸汽发生器(E-210/1.2)发生3.5MPa的饱和蒸汽,原料油-循环油浆换热器(E-209/1.2)后,油浆温度降为280℃分三路:一路返回圆型挡板上方,一路返回主分馏塔底,另一路去副分馏塔返回人字型挡板上下方;油浆从主分馏塔抽出后,可直接分出一部分经油浆过滤器。
另一路当油浆需要回炼时,•可直接由循环油浆泵出口送至提升管反应器(R-101A)。
由汽油沉降器来的反应油气进入副分馏塔侧下部,通过条型人字挡板与循环油浆逆流充分接触,洗涤反应油气中的催化剂粉尘并脱除过热,使油气呈“饱和状态”进入副分馏塔上部进行分馏。
副分馏塔顶油气经油气-热水换热器(E-2202/1~4)换热后,•再经副分馏塔顶油气—循环水冷凝冷却器(E-2202/1~4)冷却至40℃,进入副分馏塔顶油气分离器(V-22O1)•进行气液相分离;分离出的富气通过压力控制蝶阀与主分馏塔来的富气合并为一路进入气压机(C-301、C-302),压缩冷却去稳定;分离出的粗汽油经粗汽油泵(P-2201/1.2)分两路,一路经深冷器(E-311)深冷后进入稳定吸收塔(T-301)作吸收剂,另一路作冷回流去副分馏塔;或打循环去V-2201,含硫、含铵酸性水经界位控制,与V-203来的酸性水一起由酸性水泵(P-210/1.•2) 抽出送污水汽提装置或作水洗水去主分馏塔顶油气线上。