齿轮的高频淬火处理
行星齿轮的热处理工艺

行星齿轮的热处理工艺行星齿轮传动装置的重量,一般情况下正比于齿轮的重量,而齿轮的重量与其材料和热处理硬度有很大关系。
例如在相同功率下,渗碳淬火齿轮的重量将是调质齿轮重量的1/3左右。
所以针对行星齿轮减速机的结构特点和齿轮的载荷性质,应该广泛采用硬齿面齿轮。
获得硬齿面齿轮的热处理方法很多,如表面淬火,整体淬火、渗碳淬火、渗氮等,应根据行星齿轮减速机的特点考虑选定。
1、表面淬火常见的表面淬火方法有高频淬火(对小尺寸齿轮)和火焰淬火(对大尺寸齿轮)两种。
表面淬火的淬硬层包括齿根底部时,其效果最好。
表面淬火常用材料为碳的质量分数约0.35%~0.5%的钢材,齿面硬度可达45~55HRC。
2、渗碳淬火渗碳淬火齿轮具有相对最大的承载能力,但必须采用精加工工序(磨齿)来消除热处理变形,以保证精度。
渗碳淬火齿轮常用渗碳前碳的质量分数为0.2%~0.3%的合金钢,其齿面硬度常在58%~62%HRC的范围内。
若低于57HRC时,齿面强度显著下降,高于62HRC时则脆性增加。
轮齿心部硬度一般以310~330HBW为宜。
渗碳淬火齿轮的硬度,从轮齿表面至深层应逐渐降低,而有效渗碳深度规定为表面至深层应逐渐降低,而有效渗碳深度规定为表面至硬度52.5HRC处的深度。
渗碳淬火在轮齿弯曲疲劳强度方面的作用除使心部硬度有所提高外,还在于有表面的残余压应力,它可使轮齿最大拉应力区的应力减小。
因此磨齿时不能磨齿根部分,滚齿时要用留磨量滚刀。
3、渗氮采用渗氮可保证轮齿在变形最小的条件下达到很高的齿面硬度和耐磨性,热处理后可不再进行最后的精加工,提高了承载能力。
这对于不易磨齿的内齿轮来说,具有特殊意义。
4、想啮合齿轮的硬度组合当大、小齿轮均为软齿面时,小齿轮的齿面硬度应高于大齿轮。
而当两轮均为硬齿面且硬度较高时,则取两轮硬度相同。
选择好的行星齿轮减速机材料,有利于提高齿轮减速机的承载力及使用寿命对于行星齿轮,用20CrMnTi渗碳淬火比用42CrMo淡化好,一般内齿轮用42CrMo淡化.。
高频淬火频率范围
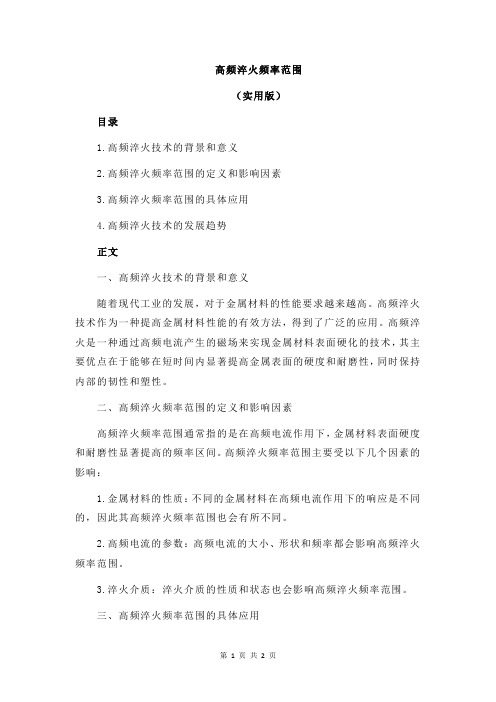
高频淬火频率范围
(实用版)
目录
1.高频淬火技术的背景和意义
2.高频淬火频率范围的定义和影响因素
3.高频淬火频率范围的具体应用
4.高频淬火技术的发展趋势
正文
一、高频淬火技术的背景和意义
随着现代工业的发展,对于金属材料的性能要求越来越高。
高频淬火技术作为一种提高金属材料性能的有效方法,得到了广泛的应用。
高频淬火是一种通过高频电流产生的磁场来实现金属材料表面硬化的技术,其主要优点在于能够在短时间内显著提高金属表面的硬度和耐磨性,同时保持内部的韧性和塑性。
二、高频淬火频率范围的定义和影响因素
高频淬火频率范围通常指的是在高频电流作用下,金属材料表面硬度和耐磨性显著提高的频率区间。
高频淬火频率范围主要受以下几个因素的影响:
1.金属材料的性质:不同的金属材料在高频电流作用下的响应是不同的,因此其高频淬火频率范围也会有所不同。
2.高频电流的参数:高频电流的大小、形状和频率都会影响高频淬火频率范围。
3.淬火介质:淬火介质的性质和状态也会影响高频淬火频率范围。
三、高频淬火频率范围的具体应用
高频淬火频率范围在许多工业领域都有广泛的应用,例如:
1.轴承行业:高频淬火技术可以提高轴承的耐磨性和寿命。
2.齿轮行业:高频淬火技术可以提高齿轮的硬度和耐磨性。
3.刀具行业:高频淬火技术可以提高刀具的硬度和耐磨性,从而提高其使用寿命。
四、高频淬火技术的发展趋势
随着科技的进步和工业的发展,高频淬火技术也在不断地发展和完善。
高频淬火与中频淬火

高频淬火与中频淬火
高频淬火的频率高,淬火层浅。
如齿轮的轮齿表面淬火。
中频淬火频率低一些,淬火层要厚一些。
主要适用于轴类零件。
基本原理:工件放入感应器(线圈)内,当感应器中通入一定频率的交变电流时,周围即产生交变磁场。
交变磁场的电磁感应作用使工件内产生封闭的感应电流──涡流。
感应电流在工件截面上的分布很不均匀,工件表层电流密度很高,向内逐渐减小, 这种现象称为集肤效应。
工件表层高密度电流的电能转变为热能,使表层的温度升高,即实现表面加热。
电流频率越高,工件表层与内部的电流密度差则越大,加热层越薄。
在加热层温度超过钢的临界点温度后迅速冷却,即可实现表面淬火。
三维网技术论坛0 {# r* ?* b# d; ^
根据交变电流的频率高低,可将感应加热热处理分为超高频、高频、超音频、中频、工频5类。
①超高频感应加热热处理所用的电流频率高达27兆赫,加热层极薄,仅约0.15毫米,可用于圆盘锯等形状复杂工件的薄层表面淬火。
②高频感应加热热处理所用的电流频率通常为200~300千赫,加热层深度为0.5~2毫米,可用于齿轮、汽缸套、凸轮、轴等零件的表面淬火。
③超音频感应加热热处理所用的电流频率一般为20~30千赫,用超音频感应电流对小模数齿轮加热,加热层大致沿齿廓分布,粹火后使用性能较好。
④中频感应加热热处理所用的电流频率一般为2.5~10千赫,加热层深度为2~8毫米,多用于大模数齿轮、直径较大的轴类和冷轧辊等工件的表面淬火。
⑤工频感应加热热处理所用的电流频率为50~60赫,加热层深度为10~15毫米,可用于大型工件的表面淬火。
45钢高频淬火
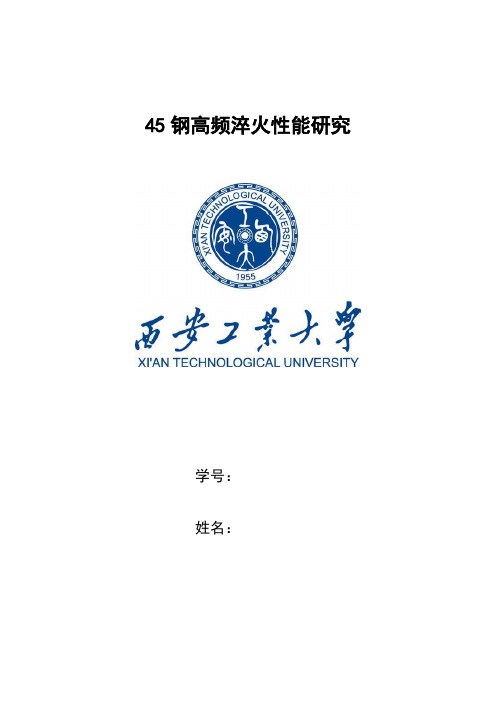
45钢高频淬火性能研究学号:姓名:45钢高频淬火性能研究45钢经过调质处理后,有良好的综合性能,广泛应用于各种重要零件,如连杆,齿轮,轴类,不同的热处理工艺得到不同的工艺性能。
本文研究了感应加热表面淬火对于45钢组织性能的影响,采用感应加热表面淬火技术对45钢进行表面强化,对所获得试件的淬硬层进行显微硬度测试。
利用金相显微镜对试件淬硬层的组织、厚度进行研究分析。
同时与正火并调质件进行硬度、金相组织等方面的比较。
结果表明经过高频感应加热淬火后45钢的表面性能明显改善,表面为淬火马氏体,而心部仍为正火组织,使得试件既耐磨又有很强的韧性,所得的工艺参数将被作为生产实践的参考依据。
关键词: 45钢高频感应淬火金相硬度目录第一章前言.............................................. 错误!未定义书签。
(一)感应加热淬火工艺概述.. (1)(二)感应加热淬火技术特点 (2)(三)高频感应淬火技术的应用.......................... -错误!未定义书签。
(四)感应加热淬火技术的发展............................ 错误!未定义书签。
(五)感应淬火常见问题及原因............................ 错误!未定义书签。
(六)45钢齿轮热处理................................... 错误!未定义书签。
第2章工艺方案制定与实验过程............................ 错误!未定义书签。
(一)工艺设定.......................................... 错误!未定义书签。
(二)实验过程.......................................... 错误!未定义书签。
(1)实验目的......................................... 错误!未定义书签。
齿轮高频淬火工作原理

齿轮高频淬火设备采用感应加热,其感应器一般是输入中频或高频交流电(1000-300000Hz或更高)的空心铜管,感应加热的原理是:将齿轮等工件放到感应器内,产生的交变磁场,又在工件中产生出同频率的感应电流,这种感应电流在工件内的分布是不均匀的,利用这个集肤效应,可使齿轮等工件表面迅速加热,在几秒钟内表面温度上升到800-1000℃,而心部温度升高很小,从而满足我们的要求。
高频淬火,是指利用高频电流(30K-1000KHZ)使工件表面局部进行加热、冷却,获得表面硬化层的热处理方法,是对齿轮等工件进行一定深度的表面强化,而心部基本上保持不变,因而具有高强度、高耐磨性和高韧性的天热点,又因是局部加热,所以能显著减少淬火变形,降减能源消耗。
齿轮高频淬火设备的用途:
一、热处理行业:各种电动工具齿轮轴的高频淬火热处理;各种齿轮、各种拔叉、各种花键轴、传动半轴、各种小轴曲柄销、各种摇臂、摇臂轴等高频淬火热处理;五金工具高频淬火热处理,如老虎钳、锤、大力钳、扳手。
二、锻压行业:标准件,紧固件的透热成型;五金工具透热,如钳子,扳手等加热透热成型;钢管透热成型,如弯管等;钢板加热,折弯成型。
三、钎焊:黄铜、紫铜的应用;硬质合金刀具的焊接,如车刀、铣刀、绞刀;探矿用的钻头焊接、如一字钻头,羊角钻头的焊接;金刚石刀头的焊接,如金刚石锯片、磨具、锯齿焊接。
高频淬火工艺守则(新)

高频淬火工艺守则高频设备是主要用于表面淬火的热处理设备,但是现阶段一般中小型工厂因产品数量少,品种多,又使用万能淬火机床并且还缺乏测温装置和能量控制机构,所以仍是手工操作。
这就要求操作者有熟练的技术水平来掌握。
一、高频加热的基本原理在置于高频电流感应器中的钢铁工件内,产生频率相等、方向相反的感应电流(即所谓涡流),同时反复被磁化的钢铁的磁滞损失,使电磁能转变为热能,将工件加热到淬火温度。
在高频加热过程中将有以下两个效应特别的显示出来。
1、邻近效应:高频电流与其感生电流相互邻近的现象。
2、集肤效应(或叫趋肤效应)感生电流集中于被加热工件表面的特性。
二、特性1、设备应具备以下条件方可使用:(1) 设备必须按说明书规定调试合格后方可交付生产者使用。
(2) 水压指数正常,水压继电器及阀门开关灵敏可靠,且内部循环水管无漏水现象。
(3) 设备所有指示灯指示正常,仪表指示准确。
(4) 自动空气开关及过流继电器动作灵敏可靠。
(5) 电源电压在±10%范围内。
(6) 反馈及耦合线圈的手轮旋转灵活,指示准确。
(7) 高频室内温度在15-35℃之间使用设备室温<15或>35℃要经研究后方可使用,其它事项要按使用说明书使用。
2、设备的启用:(1)闸流管及空气二极管的灯丝分三步送电,除新设备外,正常使用的设备可分两步送电。
第一步预热加全压的2/3,为3.5-4V,待20-30分钟后,加全压5±0.25。
振荡管送电也分两步,预热电压为22-23V,工作到位33V。
预热时间与闸流管相同。
(2)把移相变阻器手轮置于最左边位置,合上整流高压开关,阳极电压应指6.75KV左右,逐渐转动移相器至右端,电压应平稳升至13.5KV左右,正常使用时应在11-13KV。
除螺纹退火,小零件加热处,低于10KV的电压,一般不采用。
(3)感应器中置入工件,接通加热电源,仔细观察阳极电流表、栅极电流表所示的数值。
以便决定反馈耦合手轮是否需进一步调节,工作时应使其在最佳工作状态,阳极电流与栅极电流应约为5:1,最大阳极电流不得超过12A,栅极电流不得超过2.5A。
20CrMnTi汽车变速箱齿轮的热处理工艺

20CrMnTi汽车变速箱齿轮的热处理工艺一、学习目标知识目标:·熟悉感应加热表面淬火原理、特点及应用;·了解火焰表面淬火原理、特点及应用;·了解化学热处理过程;·掌握渗碳、渗氮和碳氮共渗原理、特点、常用方法及应用。
能力目标:·能根据零件的化学成分、性能要求和技术条件,合理选择表面淬火和化学热处理方法。
二、任务引入变速箱齿轮位于汽车传动部分,用于传递扭矩与动力、调整速度。
由于传递扭矩,齿根要承受较大的弯曲应力和交变应力;由于变速箱齿轮转速变化范围广,齿轮表面承受较大的接触应力,并在高速下承受强烈的磨擦力;由于工作时不断换档,轮齿之间经常要承受换档造成的冲击与碰撞。
这就要求齿轮表面有高硬度和高耐磨性;齿面有高的接触疲劳强度;心部有较高的强度和高韧性。
图2-25所示20CrMnTi汽车变速箱齿轮的热处理技术要求如下:1.渗碳层表面含碳量为0.80~1.05%;2.渗碳层深度为0.80~1.3mm;3.淬火回火后齿面硬度为58~62HRC,心部硬度为33~48HRC。
图2-25 汽车变速箱齿轮简图三、相关知识在机械设备中,有许多零件(如齿轮、曲轴、活塞销等)是在冲击载荷及表面摩擦条件下工作的,这类零件表面需具有高硬度和高耐磨性,而心部需要足够的塑性和韧性。
为满足这类零件的性能要求,须进行表面热处理。
常用的表面热处理方法有表面淬火及化学热处理两种。
(一)钢的表面淬火表面淬火是通过快速加热,使钢件表层奥氏体化,然后迅速冷却,使表层形成一定深度的淬硬组织——马氏体,而心部仍保持原来塑性、韧度较好的组织的热处理工艺。
在钢的表面淬火法中,感应加热淬火应用最广。
1.感应加热表面淬火感应加热表面淬火时,将工件放在铜管制成的感应器内,即图2-26所示装置中,感应器中通入一定频率的交流电,以产生交变磁场,于是工件内部就会产生频率相同、方向相反的感应电流(涡流)。
由于涡流的趋肤效应,使涡流在工件截面上的分布是不均匀的,表面电流密度大,心部电流密度小。
齿轮齿面高频淬火工艺

齿轮齿面高频淬火工艺齿轮作为机械传动系统中重要的零部件,其质量和性能直接关系到整个机械设备的运行效果。
为了提升齿轮的硬度和耐磨性,高频淬火工艺应运而生。
本文将介绍齿轮齿面高频淬火工艺的原理、过程和应用。
一、原理齿轮齿面高频淬火工艺是利用高频电磁感应加热的原理,在齿轮齿面上形成高温区域,然后迅速冷却,使齿面达到所需的硬度。
其主要原理如下:1. 高频电磁感应加热:通过高频电源产生高频电流,经过感应线圈产生高频磁场,齿轮齿面在高频磁场中感应出涡流,从而产生热量。
2. 热传导:齿面所产生的热量会迅速传导到整个齿轮,使齿轮表面温度升高。
3. 快速冷却:通过喷水、喷气等方式进行快速冷却,使齿轮齿面迅速冷却至所需的温度,形成高硬度。
二、过程齿轮齿面高频淬火工艺的过程一般包括以下几个步骤:1. 准备工作:选择适合的高频电源和感应线圈,根据齿轮的材质和尺寸确定加热参数。
2. 加热:将齿轮放置在感应线圈中,开启高频电源,使齿面产生高温区域,加热时间一般为几秒至几十秒。
3. 冷却:加热后立即进行快速冷却,可以通过喷水、喷气等方式进行,冷却时间一般为几秒至几十秒。
4. 温度控制:通过控制加热时间和冷却时间,控制齿轮齿面的温度,以达到所需的硬度。
三、应用齿轮齿面高频淬火工艺在机械制造领域中有着广泛的应用,主要体现在以下几个方面:1. 提升齿轮硬度:高频淬火可以使齿轮表面的硬度显著提高,提高齿轮的耐磨性和承载能力,延长齿轮的使用寿命。
2. 改善齿轮的表面质量:高频淬火可以消除齿轮表面的毛刺和氧化层,提高齿面的光洁度和平整度,减小齿轮的摩擦和噪音。
3. 提高生产效率:高频淬火具有加热速度快、冷却均匀等优点,可以大幅度提高齿轮的生产效率,缩短生产周期。
4. 适用于各种材质和尺寸的齿轮:高频淬火适用于各种材质的齿轮,包括低碳钢、高碳钢、合金钢等,也适用于各种尺寸的齿轮,从小型齿轮到大型齿轮都可以进行高频淬火处理。
齿轮齿面高频淬火工艺通过高频电磁感应加热和快速冷却的方式,可以提升齿轮的硬度和耐磨性,改善齿轮的表面质量,提高生产效率,适用于各种材质和尺寸的齿轮。
齿轮的材料及热处理
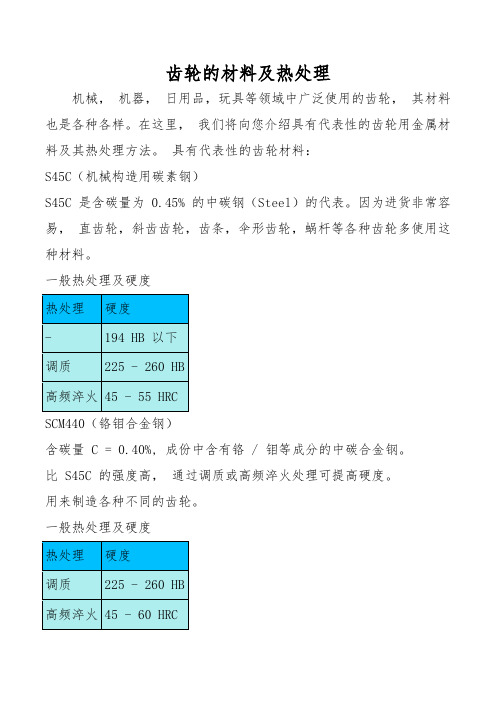
齿轮的材料及热处理机械,机器,日用品,玩具等领域中广泛使用的齿轮,其材料也是各种各样。
在这里,我们将向您介绍具有代表性的齿轮用金属材料及其热处理方法。
具有代表性的齿轮材料:S45C(机械构造用碳素钢)S45C 是含碳量为 0.45% 的中碳钢(Steel)的代表。
因为进货非常容易,直齿轮,斜齿齿轮,齿条,伞形齿轮,蜗杆等各种齿轮多使用这种材料。
一般热处理及硬度SCM440(铬钼合金钢)含碳量 C = 0.40%, 成份中含有铬 / 钼等成分的中碳合金钢。
比 S45C 的强度高,通过调质或高频淬火处理可提高硬度。
用来制造各种不同的齿轮。
一般热处理及硬度SCM415(铬钼合金钢)低碳合金钢(C = 0.15%)的代表材料。
一般情况下,经渗碳淬火处理后使用。
材料热处理后的强度高于 S45C 及 SCM440。
使用表面硬度在 55 ∼60HRC 左右。
SUS303(不锈钢:18Cr-8Ni 钢)不锈钢,正如其名是不容易生锈的钢(Stainless Steel )。
奥氏体系的不锈钢基本上为非磁性。
不锈钢材的齿轮主要使用在食品机械等需要避免生锈的机械中。
与 SUS303 的成分相似的不锈钢材料还有 SUS304。
它的耐蚀性能高于SUS303。
铸造铜合金铸造铜合金是制造蜗轮的主要材料。
一般有铸造磷青铜(CAC502)铝青铜(CAC702)等。
啮合对手的蜗杆的材料大多使用S45C/SCM440/SCM415 等钢材。
蜗杆与蜗轮使用不同材料是为了防止蜗杆蜗轮啮合时由于滑动而引起的齿面胶合及过度磨损等。
6-2 具有代表性的热处理什么是淬火?为了提高钢材的硬度,将材料加热到高温(约 800℃)后快速冷却。
根据冷却介质,分为油冷 / 水冷 / 喷射冷却等不同种类。
淬火后的钢材过脆,为了增加钢材的韧性,一般需要再进行回火处理。
纯铁即使经过淬火处理也不会变硬。
钢材的含碳量在 0.35% 以上的话,淬火硬化可能。
什么是调质处理?调质处理是将淬火及高温回火相结合,调整钢材 ( 钢件 ) 硬度 / 强度 / 靭性的热处理。
齿轮齿面高频淬火工艺

齿轮齿面高频淬火工艺
齿轮齿面高频淬火是通过高频电流引起齿面表面瞬间加热、快速淬火
并迅速冷却的一种淬火工艺。
该工艺的原理是将高频电流传输到齿面表面,通过涡流的形式产生热量,使齿面表面温度迅速升高,然后使用冷却剂对
齿面进行淬火处理,使齿面达到理想的硬度和强度。
相比传统的热处理方法,齿轮齿面高频淬火具有以下优势:
1.高效性:高频淬火不需要先加热整个工件,只需要针对齿面进行加
热淬火,因此处理速度更快。
2.工艺性:高频淬火可以进行细节处的处理,可以得到更均匀的硬度;同时,处理后不会引起变形或变色等不良后果。
3.质量稳定性:高频淬火的温度和淬火时间可以通过计算机控制实现,在整个加工过程中具有高度的稳定性和一致性。
齿轮齿面高频淬火是目前齿轮热处理中的一种非常先进和有效的技术
之一。
由于其能够在保证质量的同时提高效率和性能,因此成为了齿轮加
工领域中的一项重要技术。
齿轮高频淬火

齿轮高频淬火齿轮高频淬火是一种常用的齿轮表面处理技术,其目的是提高齿轮的硬度和耐磨性。
本文将从淬火原理、工艺流程、优点和应用等方面,介绍齿轮高频淬火的相关知识。
一、淬火原理齿轮高频淬火是利用高频感应加热技术,在齿轮表面局部加热至淬火温度,然后迅速冷却,使齿轮表面发生相变,从而提高其硬度。
这种淬火方式具有以下特点:1. 局部加热:只对齿轮表面进行加热,不影响齿轮的整体性能。
2. 快速冷却:迅速冷却可以使齿轮表面形成致密的马氏体组织,提高硬度。
3. 淬火温度控制:通过调整加热功率和加热时间,可以精确控制淬火温度,以满足不同齿轮的要求。
二、工艺流程齿轮高频淬火的工艺流程主要包括以下几个步骤:1. 清洗:将齿轮表面的油污和杂质清洗干净,以保证淬火效果。
2. 预热:将齿轮整体加热至一定温度,以减少温度梯度,防止齿轮变形。
3. 加热:利用高频感应加热设备对齿轮表面进行局部加热,使其达到淬火温度。
4. 淬火:迅速冷却齿轮表面,使其形成马氏体组织。
5. 温度回火:将齿轮加热至一定温度,保持一段时间,以减少残余应力和改善齿轮的韧性。
6. 冷却:将齿轮冷却至室温,完成整个淬火工艺。
三、优点齿轮高频淬火具有以下优点:1. 提高齿轮的硬度:淬火后,齿轮表面的硬度可以达到50-60HRC,大大提高了齿轮的耐磨性。
2. 改善齿轮的强度:淬火后,齿轮表面形成的马氏体组织可以提高齿轮的强度和承载能力。
3. 减少齿轮变形:高频淬火过程中的快速冷却可以减少齿轮的热变形,保证齿轮的精度和几何形状。
4. 提高生产效率:高频感应加热技术具有加热速度快、温度控制精确等优点,可以大大提高生产效率。
四、应用领域齿轮高频淬火广泛应用于各个行业的齿轮制造中,特别是对于高精度、高负载的齿轮产品,更是必不可少的工艺。
主要应用领域包括:1. 汽车工业:汽车变速箱、差速器等关键部件的齿轮。
2. 机械工业:工程机械、冶金机械等的传动齿轮。
3. 航空航天工业:飞机、火箭等航空航天器的传动齿轮。
齿轮超高频热处理

齿轮超高频热处理
齿轮是机械传动中常用的元件之一,其负责传递动力和扭矩。
因此,齿轮的耐磨性和耐久性是非常重要的。
为了提高齿轮的性能,超高频热处理技术被广泛应用于齿轮的制造过程中。
齿轮超高频热处理是一种通过电磁感应加热工艺实现的热处理方法。
这种方法的优点在于它可以快速、均匀地加热齿轮,从而实现齿轮的淬火和回火处理。
由于这种方法的加热速度非常快,因此可以有效地避免齿轮的变形和裂纹,从而提高齿轮的质量和耐久性。
齿轮超高频热处理的工艺流程是比较简单的。
首先,需要将齿轮放入超高频热处理设备中,然后通过电磁感应加热齿轮。
当齿轮的温度达到所需的淬火温度时,将齿轮快速冷却,以实现淬火处理。
接着,将齿轮进行回火处理,从而消除淬火过程中产生的脆性和应力。
齿轮超高频热处理的优点在于它可以快速、均匀地加热齿轮,从而实现齿轮的淬火和回火处理。
由于这种方法的加热速度非常快,因此可以有效地避免齿轮的变形和裂纹,从而提高齿轮的质量和耐久性。
此外,这种方法还可以提高齿轮的硬度和耐磨性,从而延长齿轮的使用寿命。
然而,齿轮超高频热处理也存在一些缺点。
首先,这种方法的设备和工艺成本比较高,因此对于中小型企业来说,成本会比较高。
其次,这种方法的加热速度非常快,因此需要控制好加热和冷却的时
间,否则会影响齿轮的质量和性能。
总的来说,齿轮超高频热处理是一种非常有效的齿轮制造技术。
它可以提高齿轮的质量和性能,从而延长齿轮的使用寿命。
但是,在应用这种技术的过程中,需要注意控制好加热和冷却的时间,以确保齿轮的质量和性能。
20mncr5高频热处理工艺

20mncr5高频热处理工艺20MnCr5是一种合金结构钢,常用于制造齿轮、轴承等零件。
对于20MnCr5的热处理工艺,常见的有淬火和回火。
淬火是将工件加热到适当的温度(一般为550-650摄氏度),然后迅速冷却,以增加其硬度。
回火则是将淬火后的工件再次加热到适当的温度,然后缓慢冷却,以降低其硬度并改善其韧性。
此外,高频热处理工艺可以用于提高20MnCr5的强度、韧性和耐磨性,以及细化晶粒,提高齿轮的精度和使用寿命。
在高频热处理过程中,应注意控制加热速度、保温时间和冷却速度,以避免工件变形和开裂。
最后,具体的热处理工艺应根据产品要求和生产条件来确定,可以参考相关文献或咨询专业技术人员。
20MnCr5是一种低碳合金钢,常用于制造齿轮等机械零部件。
对于20MnCr5的高频热处理,一般采用渗碳渗氮的方法,主要包括以下步骤:坯料热处理:首先对20MnCr5的坯料进行均匀加热,然后进行正火或退火处理,以消除前期冷加工或热加工所产生的应力,并提高坯料的加工性能。
精确切割:对经过均匀加热的坯料进行精确的切割,以准备进行后续的高频热处理。
高频感应加热:将切好的坯料进行高频感应加热,达到适当的温度。
高频感应加热可以在短时间内使表面温度迅速升高,而内部温度升高较慢,实现局部加热。
渗碳渗氮处理:将热处理后的坯料放入含有碳、氮的气体环境中,进行渗碳渗氮处理。
这一步骤有助于提高表面硬度和耐磨性。
淬火:对已经渗碳渗氮处理的坯料进行淬火,以增加其硬度和强度。
淬火介质可以选择淬火油或水,具体取决于所需的性能。
回火:对淬火后的坯料进行回火处理,以降低硬度,提高韧性。
回火温度和时间的选择需要根据具体要求来确定。
机械加工:进行最终的机械加工,以获得所需的形状和尺寸。
需要注意的是,具体的高频热处理工艺参数和条件会因厂家、设备和工件要求而有所不同,因此在进行具体的高频热处理时,最好咨询专业的材料工程师或热处理工程师,以确保达到预期的性能和质量。
45钢车床主轴箱齿轮的热处理工艺设计
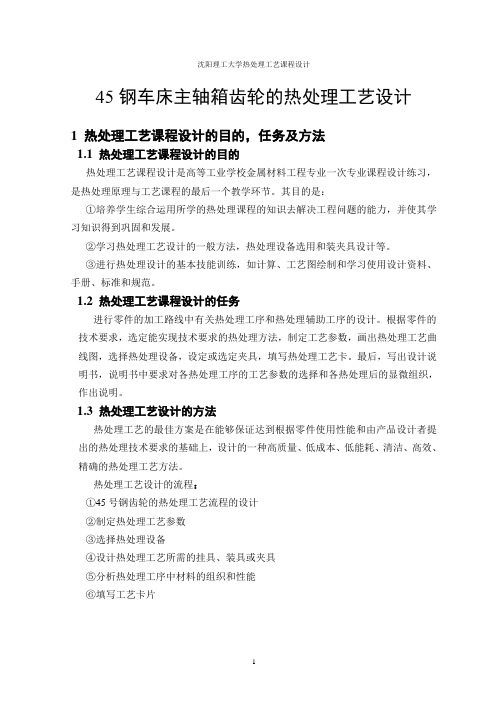
45钢车床主轴箱齿轮的热处理工艺设计1 热处理工艺课程设计的目的,任务及方法1.1 热处理工艺课程设计的目的热处理工艺课程设计是高等工业学校金属材料工程专业一次专业课程设计练习,是热处理原理与工艺课程的最后一个教学环节。
其目的是:①培养学生综合运用所学的热处理课程的知识去解决工程问题的能力,并使其学习知识得到巩固和发展。
②学习热处理工艺设计的一般方法,热处理设备选用和装夹具设计等。
③进行热处理设计的基本技能训练,如计算、工艺图绘制和学习使用设计资料、手册、标准和规范。
1.2 热处理工艺课程设计的任务进行零件的加工路线中有关热处理工序和热处理辅助工序的设计。
根据零件的技术要求,选定能实现技术要求的热处理方法,制定工艺参数,画出热处理工艺曲线图,选择热处理设备,设定或选定夹具,填写热处理工艺卡。
最后,写出设计说明书,说明书中要求对各热处理工序的工艺参数的选择和各热处理后的显微组织,作出说明。
1.3热处理工艺设计的方法热处理工艺的最佳方案是在能够保证达到根据零件使用性能和由产品设计者提出的热处理技术要求的基础上,设计的一种高质量、低成本、低能耗、清洁、高效、精确的热处理工艺方法。
热处理工艺设计的流程:①45号钢齿轮的热处理工艺流程的设计②制定热处理工艺参数③选择热处理设备④设计热处理工艺所需的挂具、装具或夹具⑤分析热处理工序中材料的组织和性能⑥填写工艺卡片2 热处理工艺课程设计的内容2.1 课题简图图2.1 主轴箱齿轮示意图2.2 技术要求车床圆柱齿轮表面进行高频感应淬火调质硬度:200-250HB表面硬度:45-50HRC淬硬层深度:1-2mm工件重量:6 kg生产批量: 6件2.3 主轴箱齿轮材料的选择,工作条件及其性能要求2.3.1 材料的选择根据对齿轮力学性能的要求,应从具有好的综合性能指标这个要素选材,工业生产中常用的金属材料主要是钢、铸铁及合金。
中碳钢的含碳量在0.25%~0.6%,位于低碳钢与高碳钢之间,其性能也同样位于两者之间,有较好的综合性能,因此中碳钢适合做齿轮。
45钢制造齿轮的工程背景和使用要求

45钢制造齿轮的工程背景和使用要求
45钢制成的齿轮,经过热处理调质后获得的索氏体组织,具有高的强度和塑性,且具有一定的韧性。
若45钢制造强度要求较高的齿轮,要求齿轮表面高硬度、高耐磨性,而心部具有高强度和高韧性,调质后可进行高频淬火处理。
但热处理时,由于淬透性差,水淬变形大,裂纹倾向敏感,尤其在40℃左右水淬更为明显。
为此,可参照下面热处理工艺方法进行。
(1)预备热处理。
正火在840~870℃,可代替调质处理作为最后热处理,或为感应加热表面淬火前的预备热处理。
正火后的硬度≤226HBW。
1)加热温度。
加热温度820~860℃,重要件要求变形严格的选用下限温度,碱浴、硝盐浴分级时选用偏高温度,而较大件调质时,为提高淬硬层深度和心部性能,可选用840~860℃的温度,除大件外,一般采用“零”保温。
45钢淬火最高表面硬度为58HRC。
为得到极细的奥氏体晶粒,提高45钢的韧性,降低裂纹敏感性,可采用780℃临界温度淬火。
2)淬火。
45钢的奥氏体稳定性差,需采用双液淬火。
对于要求精密的小齿轮,采用碱浴、硝盐浴120~200℃的分级淬火。
(3)回火。
常用调质回火温度550~620℃,回火后的硬度为200~280HBW,回火后的硬度与回火温度之间的数学表达式如下:HRC=75.46-0.096t
σb=(2263.8-2.65t)(MPa);δ5=(11.39+0.066t)(%)。
式中HRC-洛氏硬度;
σb-抗拉强度,MPa;
t-回火温度(在200℃~700℃范围内)。
齿轮强计算演示.pptx

许用弯曲应力[F]按下式计算
F
F Lim
SF
Flim按图11-10查取
第17页/共40页
图11-10 齿轮的弯曲疲劳极限Flim
第18页/共40页
SF—轮齿弯曲疲劳安全系数,按表11-4查取。
bmn2 z1
[ F ]
设计
m 3 3.2KT1YF cos2 a (u 1)z12[ F ]
第25页/共40页
§11-8 直齿圆锥齿轮传动
一、设计参数 大端参数为标准值,强度计算 时,是以锥齿轮齿宽中点处的
R B/2
当量齿轮作为计算时的依据。
对轴u交角为z290º的直d齿2锥齿轮d传m动1 : z1 d1 dm2
注意:因两个齿轮的σH1= σH2 ,故按此强度准则设计齿 轮传动时,公式中应代入[σH] 1和[σH] 2中较小者。
模数m不能成为衡量齿轮接触强度的依据。
第10页/共40页
式(11-4)和(11-5)适用钢制齿轮,
若为钢对铸铁或铸铁对铸铁,则应将
公式中的系数335分别改为285和250。
许用接触应力[H]按下式计算
cot 1
tg 2
d1 dm1
δ1 δ2
B
锥距: R
d1
2
d2
2
2 2
d1
u2 1 2
当量齿轮的锥距: Rm=R-0.5b两个三角形相似
dm2 d dm是平均分度圆直径
2
dm1 dm2 R 0.5b 1 0.5 b
d1 d2
RR
R
齿部高频淬火操作规程
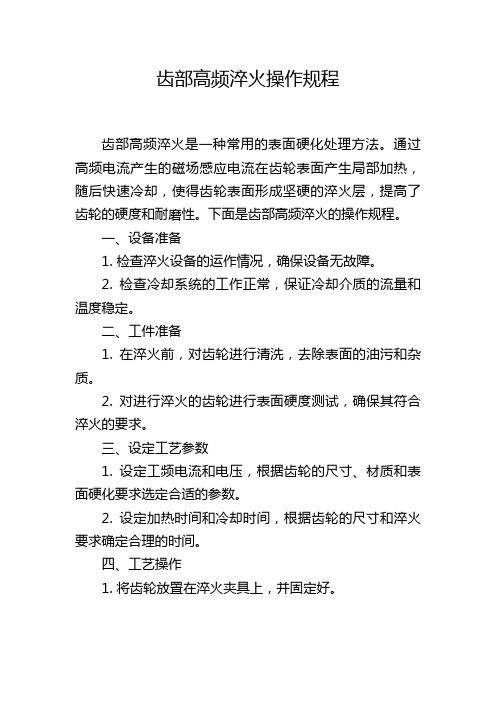
齿部高频淬火操作规程齿部高频淬火是一种常用的表面硬化处理方法。
通过高频电流产生的磁场感应电流在齿轮表面产生局部加热,随后快速冷却,使得齿轮表面形成坚硬的淬火层,提高了齿轮的硬度和耐磨性。
下面是齿部高频淬火的操作规程。
一、设备准备1. 检查淬火设备的运作情况,确保设备无故障。
2. 检查冷却系统的工作正常,保证冷却介质的流量和温度稳定。
二、工件准备1. 在淬火前,对齿轮进行清洗,去除表面的油污和杂质。
2. 对进行淬火的齿轮进行表面硬度测试,确保其符合淬火的要求。
三、设定工艺参数1. 设定工频电流和电压,根据齿轮的尺寸、材质和表面硬化要求选定合适的参数。
2. 设定加热时间和冷却时间,根据齿轮的尺寸和淬火要求确定合理的时间。
四、工艺操作1. 将齿轮放置在淬火夹具上,并固定好。
2. 检查淬火夹具的稳定性,确保齿轮表面与夹具接触良好。
3. 将夹具和齿轮放入淬火设备中,并确保设备密封良好。
4. 打开淬火设备,开始供电加热,根据设定好的工艺参数进行加热。
5. 监控齿轮表面温度的变化情况,确保达到所需的淬火温度。
6. 加热结束后,立即进入冷却阶段,启动冷却系统,进行强制冷却。
7. 监控冷却介质的温度和流量,确保冷却效果良好。
8. 冷却结束后,取出齿轮,并进行工件的清洗和除锈处理。
9. 进行表面硬度测试,确保淬火效果符合要求。
五、安全注意事项1. 操作人员必须穿戴好防护设备,包括耐热手套、防护面罩等。
2. 在加热和冷却过程中,严禁触摸或接近淬火设备和工件。
3. 淬火设备必须定期进行维护和检修,确保设备的正常运行。
4. 在操作过程中,严格遵守操作规程,禁止擅自更改工艺参数。
5. 所有不熟悉操作的人员必须接受培训,并有经验操作人员的指导。
以上是齿部高频淬火的操作规程,通过严格执行操作规程,可以确保淬火质量和操作安全。
齿部高频淬火作为一种高效的表面硬化处理方法,应用广泛于各类齿轮产品的生产中。
齿面高周波

齿面高周波是一种热处理方法,用于提高齿条的齿面硬度和耐磨性。
高周波热处理(高频淬火)是将碳含量0.30%以上的钢材通过感应加热,使材料表面变硬的淬火热处理。
经过高周波热处理的齿条,其齿面及齿顶可以得到高硬度。
然而,高周波热处理可能导致齿根部分无法得到足够的硬化。
因此,针对这种情况,热处理方式可能会改为中周波(又称低频淬火),按照齿形一齿一齿加工,以确保日后机台重传动而不崩齿。
高周波热处理后,还需要进行低温回火处理,以降低材料的硬度并增强其韧性。
此外,为了提高齿面的精度和降低噪音,还需要对齿面进行研磨加工。
以上信息仅供参考,建议咨询热处理专家或查阅相关书籍文献,以获取更准确的信息。