石脑油芳构化操作规程
芳构化规程
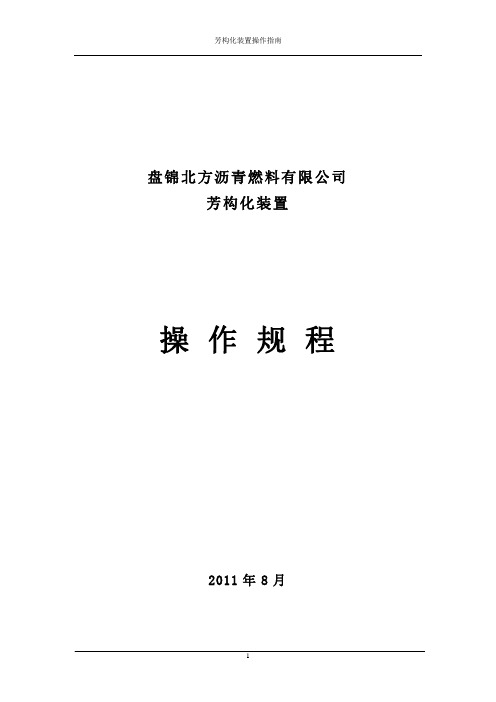
盘锦北方沥青燃料有限公司芳构化装置操作规程2011年8月第一章装置概况1基本概况1.1装置设计生产能力10万吨/年。
1.2装置开工时数7200小时。
石脑油和碳四非临氢改质催化剂和工艺技术,可以将低辛烷值的汽油组分,如直馏石脑油和加氢焦化石脑油以及含烯烃的碳四,转化为几乎不含烯烃的高辛烷值汽油调和组分,用于调合汽油,在保证辛烷值基本不降低的同时,可以降低调合汽油的烯烃含量和密度。
汽油非临氢改质过程包括选择性裂解、异构、齐聚、环化、脱氢等一系列复杂反应。
可大幅提高汽油辛烷值。
10万吨/年石脑油改质装置主要包括下列几部分:反应、吸收解吸、汽油稳定以及催化剂再生。
(1)、反应部分来自装置外的液化气进装置后与来自装置外的石脑油按照比例混合进料,经反应产物换热器(E3101/AB)换热后进入原料加热炉(F3101)加热后进入反应器(R3101)反应后,反应产物出反应器后首先进入稳定塔底重沸器(E3108),然后进入闪蒸塔,塔底液相经煤油冷却器E3107冷却后送至成品油罐区,塔顶气相进入反应产物换热器(E3101/AB)与原料换热后进入反应产物空冷器进行冷却(A3101),再进入反应产物水冷器进一步冷却到40℃左右,进入吸收稳定部分。
随着反应的进行,催化剂上的结焦量会逐步增加,当产品质量不能满足要求时,需将反应停止,进行反应器烧焦再生处理.烧焦开始前,先启动再生循环气压缩机,从压缩机入口处引入氮气,增压的氮气经过换热器(E-3101)换热,然后经加热炉(F-3101)加热,进入反应器(R-3101)进行热氮吹扫操作,由反应器出的气体经E-3101换热(三通跨过E-112、E-108),再经空冷器(A-101)和水冷器(E-103)冷却,以逐步带出反应器中的油气。
当反应器中的油气达到安全要求,并且反应器入口温度达到烧焦需要的温度时,从压缩机K-3101入口处引入空气,开始烧焦作业,要求控制循环气初始氧浓度不高于0.5v%。
新编芳构化操作规程
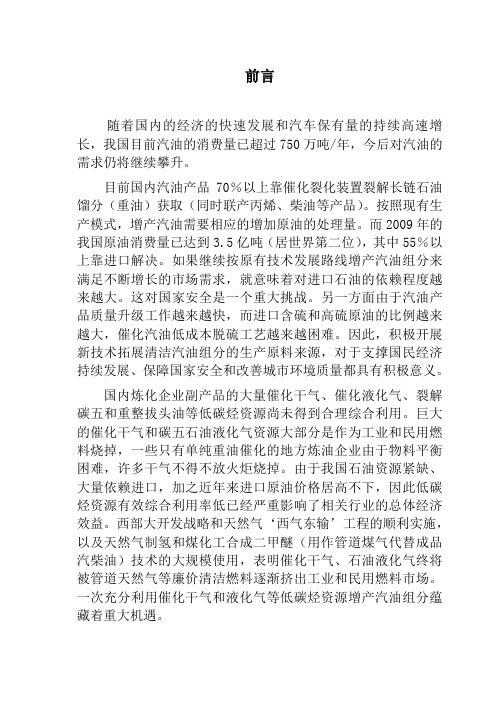
前言随着国内的经济的快速发展和汽车保有量的持续高速增长,我国目前汽油的消费量已超过750万吨/年,今后对汽油的需求仍将继续攀升。
目前国内汽油产品70%以上靠催化裂化装置裂解长链石油馏分(重油)获取(同时联产丙烯、柴油等产品)。
按照现有生产模式,增产汽油需要相应的增加原油的处理量。
而2009年的我国原油消费量已达到3.5亿吨(居世界第二位),其中55%以上靠进口解决。
如果继续按原有技术发展路线增产汽油组分来满足不断增长的市场需求,就意味着对进口石油的依赖程度越来越大。
这对国家安全是一个重大挑战。
另一方面由于汽油产品质量升级工作越来越快,而进口含硫和高硫原油的比例越来越大,催化汽油低成本脱硫工艺越来越困难。
因此,积极开展新技术拓展清洁汽油组分的生产原料来源,对于支撑国民经济持续发展、保障国家安全和改善城市环境质量都具有积极意义。
国内炼化企业副产品的大量催化干气、催化液化气、裂解碳五和重整拔头油等低碳烃资源尚未得到合理综合利用。
巨大的催化干气和碳五石油液化气资源大部分是作为工业和民用燃料烧掉,一些只有单纯重油催化的地方炼油企业由于物料平衡困难,许多干气不得不放火炬烧掉。
由于我国石油资源紧缺、大量依赖进口,加之近年来进口原油价格居高不下,因此低碳烃资源有效综合利用率低已经严重影响了相关行业的总体经济效益。
西部大开发战略和天然气‘西气东输’工程的顺利实施,以及天然气制氢和煤化工合成二甲醚(用作管道煤气代替成品汽柴油)技术的大规模使用,表明催化干气、石油液化气终将被管道天然气等廉价清洁燃料逐渐挤出工业和民用燃料市场。
一次充分利用催化干气和液化气等低碳烃资源增产汽油组分蕴藏着重大机遇。
目录第一章工艺技术规程 (7)一、装置概况 (7)1.装置简介 (7)2.装置特点 (7)3.装置组成 (7)4.原料来源 (8)5.物料平衡 (8)6.原料、产品技术规格 (8)6.1原料性质 (8)6.2产品质量 (10)6.3催化剂的规格 (10)二、工艺原理 (11)1.反应原理 (11)2.催化剂的干燥 (13)三、工艺指标 (13)四、公用工程及其消耗指标 (14)1.公用工程 (14)1.1用水负荷 (14)1.2用电负荷 (15)1.3用汽负荷 (16)1.4燃料气用量 (17)1.5催化剂消耗 (17)21.6压缩空气消耗 (17)1.7氮气消耗 (18)2.三废排放 (18)2.1废气 (18)2.2废水 (18)2.3废渣 (18)3.安全、卫生、环保 (18)4.生产过程中主要物料的危险性 (19)4.1火灾爆炸危险性 (19)4.2毒性物质危害 (19)4.3噪声危害 (19)4.4高温热源 (20)4.5主要危险场所 (20)4.6安全防护 (20)第二章开工规程 (21)一、开工前准备工作 (21)1.对装置进行全面检查 (22)2.开工具备的条件 (22)二、开工步骤 (23)1.开工确认 (23)2.引碳四到燃气缓冲罐 (23)3.加热炉点火升温、装置进行氮气升温 (23)4.反应进料 (24)35.系统升温和调整操作 (24)6.调整产品质量 (25)第三章操作指南 (26)一、反应再生系统 (26)二、吸收稳定、脱重系统 (33)1.吸收稳定任务 (33)2.工艺流程 (33)3.吸收稳定岗位职责及操作 (35)4.正常操作 (36)5.非正常操作法 (42)6.脱重岗位职责 (45)7.操作原则 (46)第四章停工规程 (47)一、停工准备工作 (47)二、停工步骤 (48)1.预处理及反应系统 (48)2.吸收稳定系统 (48)3.脱重塔系统 (48)三、装置临时停工管线及设备维修 (49)四、装置停工退料 (49)1.正常停工退料 (49)2.要求 (49)3.排液 (49)44.蒸汽吹扫 (50)五、紧急停工 (51)第五章加热炉操作规程 (51)一、点火具备的条件 (51)二、加热炉点火 (51)三、加热炉运行 (52)四、正常运行要求 (52)五、加热炉正常操作 (53)六、日常检查 (53)七、加热炉不正常现象处理 (54)八、加热炉的维修和保养 (60)第六章基础设备操作规程 (60)一、离心泵 (60)1、离心泵的开、停车与切换 (60)2.注意事项 (62)3.巡回检查 (62)4.离心泵的维护 (62)5.常见故障及解决方法 (63)二、冷换设备 (63)三、空气冷却器 (64)四、安全阀 (65)五、火炬 (65)第七章专用设备操作规程 (66)5一、再生压缩机 (66)1.准备工作 (66)2.开工步骤 (66)3.正常停车 (66)4.紧急停车 (66)5.一般故障及处理方法 (67)第八章事故处理预案 (68)一、加热炉管破裂 (68)二、循环水中断 (69)三、突然停电 (70)四、停仪表风 (71)五、重沸器大盖泄漏处理 (72)六、机泵泄漏处理 (73)七、塔、容器、换热设备发生火灾处理 (73)第九章安全生产及环境保护 (74)一、装置中有毒物质参数及危害 (74)二、冬季安全操作法 (80)三、中毒病人的抢救 (80)第十章设备明细表 (83)6第一章工艺技术规程一、装置概况1. 装置简介装置设计规模为15万吨/年,由辽宁省石油化工规划设计院设计,设计弹性60%-120%,年开工周期按7500小时计。
石脑油芳构化生产工艺

石脑油芳构化生产工艺石脑油是一种石油产品,主要由碳氢化合物组成,是一种重要的石油化工原料。
是通过对石脑油进行加氢裂化和催化重整等过程,将其转化为芳香烃类产品的工艺,是一种重要的石化工艺之一。
1.石脑油芳构化生产工艺的原理石脑油芳构化是将石脑油中的不饱和烃和环烷烃经加氢裂化和重整反应,转化为芳香烃类产品的过程。
在加氢裂化过程,石脑油中的不饱和烃被加氢饱和,形成环烷烃,然后经过重整反应,环烷烃再发生脱氢、脱碳等反应,生成苯、甲苯、二甲苯等芳香烃类产品。
2.石脑油芳构化生产工艺的步骤(1)催化裂化:将石脑油在催化剂的作用下进行裂化反应,生成乙烯、丁烯、丙烯等烯烃和环烷烃,这些烃类是后续芳构化反应的原料。
(2)加氢处理:将裂化生成的烯烃和环烷烃经过加氢处理,使其发生氢化反应,生成相应的饱和烃。
(3)芳构化反应:经过加氢处理后的烷烃在催化剂的作用下进行芳构化反应,脱氢、脱碳、重排等反应,最终生成苯、甲苯、二甲苯等芳香烃类产品。
(4)产品分离、纯化:将芳构化反应生成的混合芳烃产品进行分离、纯化,得到高纯度的苯、甲苯、二甲苯等芳香烃产品。
3.石脑油芳构化生产工艺的优点(1)利用率高:石脑油芳构化生产工艺可以有效利用石脑油中的烃类原料,将其转化为有较高附加值的芳香烃产品。
(2)产品多样性:通过芳构化反应可以得到苯、甲苯、二甲苯等多种芳香烃产品,可以满足不同行业的需求。
(3)环保节能:石脑油芳构化生产工艺中涉及到的加氢、催化等反应都是在相对温和的条件下进行的,不会产生大量废气、废水等环境污染问题。
总的来说,石脑油芳构化生产工艺是一种重要的石化工艺,可以有效转化石脑油中的烃类原料为芳香烃产品,具有利用率高、产品多样性、环保节能等优点。
在今后的工业发展中,这种工艺将会得到更广泛的应用和推广。
芳构化的系统升温和调整操作

芳构化的系统升温和调整操作1)反应系统a 在醚后液化气和石脑油进入反应器之后,逐渐调整F201炉出口温度从150℃至200℃之间,观察有无温升发生,如果没有温升,则继续升温直至有温升,反应被引发。
注意观察反应器R201床层各点温度变化情况,当温升逐渐变小时,说明反应减弱,则继续提高炉出口温度,让R201温度达到300℃以上。
继续观察R201床层温度分布。
当R201上部温度达到350℃时,小量给反应中间进料,观察R201床层温度分布。
须知在反应中间进料开始进入反应器时,各换热器还没有热源,反应中间进料的温度很低而且呈液态,故在开始给反应中间进料时,要控制小流量,以防反应被“扑灭”。
当反应逐渐正常,反应器温度控制在300-350℃。
在此过程中须时刻注意反应进料量和反应中间进料量的调节,使反应器床层温度达到平衡。
b 观察反应产物凝液分离罐V204液位,当其达到预先设定的控制范围时,即开启去吸收解吸塔T201的反应液泵P204,并建立反应产物凝液分离罐V204液位自动控制。
2) 吸收稳定系统a 观察吸收解吸塔T201底液位和温度,当其达到预先设定的控制范围时,即开启去稳定塔T202的吸收解吸塔底泵P205和稳定塔进料泵P203,并建立T201底液位和产物气液分离罐V203液位自动控制。
b 观察稳定塔T202底液位和温度,当其达到预先设定的控制范围时,即开启去吸收解吸塔T201顶的吸收剂泵P207,并按要求实施吸收剂流量的自动控制。
随后开启P206吸收解吸塔中段循环泵,同时开启塔T202底去脱重塔T203的调节阀,并实施T202底液位自动控制。
c 按工艺要求建立稳定塔T202顶压力控制。
观察稳定塔回流罐V205液位,当其达到预先设定的控制范围时,即开启稳定塔顶回流泵P208,并建立稳定塔顶温度自动控制。
同时建立稳定塔回流罐V205液位自动控制,将稳定塔顶产物由稳定塔回流罐V205经稳定塔顶回流泵P208一部分送去V-212,一部分作为稳定塔回流,另一部分去反应。
煤基石脑油半再生催化重整制芳烃的工艺
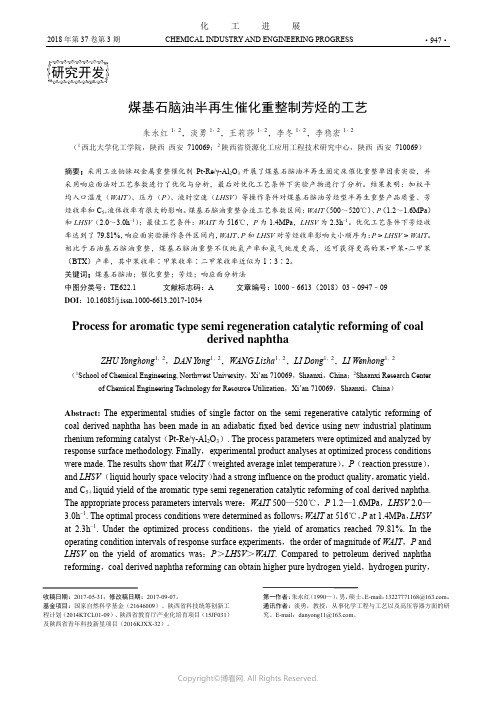
2018年第37卷第3期 CHEMICAL INDUSTRY AND ENGINEERING PROGRESS·947·化 工 进展煤基石脑油半再生催化重整制芳烃的工艺朱永红1,2,淡勇1,2,王莉莎1,2,李冬1,2,李稳宏1,2(1西北大学化工学院,陕西 西安 710069;2陕西省资源化工应用工程技术研究中心,陕西 西安 710069) 摘要:采用工业铂铼双金属重整催化剂Pt-Re/γ-Al 2O 3开展了煤基石脑油半再生固定床催化重整单因素实验,并采用响应面法对工艺参数进行了优化与分析,最后对优化工艺条件下实验产物进行了分析。
结果表明:加权平均入口温度(WAIT )、压力(P )、液时空速(LHSV )等操作条件对煤基石脑油芳烃型半再生重整产品质量、芳烃收率和C 5+液体收率有很大的影响。
煤基石脑油重整合适工艺参数区间:WAIT (500~520℃)、P (1.2~1.6MPa )和LHSV (2.0~3.0h –1);最佳工艺条件:WAIT 为516℃,P 为1.4MPa ,LHSV 为2.3h –1。
优化工艺条件下芳烃收率达到了79.81%,响应面实验操作条件区间内,WAIT 、P 和LHSV 对芳烃收率影响大小顺序为:P > LHSV > WAIT 。
相比于石油基石脑油重整,煤基石脑油重整不仅纯氢产率和氢气纯度更高,还可获得更高的苯-甲苯-二甲苯(BTX )产率,其中苯收率∶甲苯收率∶二甲苯收率近似为1∶3∶2。
关键词:煤基石脑油;催化重整;芳烃;响应面分析法中图分类号:TE622.1 文献标志码:A 文章编号:1000–6613(2018)03–0947–09 DOI :10.16085/j.issn.1000-6613.2017-1034Process for aromatic type semi regeneration catalytic reforming of coalderived naphthaZHU Yonghong 1,2,DAN Yong 1,2,WANG Lisha 1,2,LI Dong 1,2,LI Wenhong 1,2(1School of Chemical Engineering, Northwest University ,Xi’an 710069,Shaanxi ,China ;2Shaanxi Research Centerof Chemical Engineering Technology for Resource Utilization ,Xi’an 710069,Shaanxi ,China )Abstract: The experimental studies of single factor on the semi regenerative catalytic reforming of coal derived naphtha has been made in an adiabatic fixed bed device using new industrial platinum rhenium reforming catalyst (Pt-Re/γ-Al 2O 3). The process parameters were optimized and analyzed by response surface methodology. Finally ,experimental product analyses at optimized process conditions were made. The results show that WAIT (weighted average inlet temperature ),P (reaction pressure ),and LHSV (liquid hourly space velocity )had a strong influence on the product quality ,aromatic yield ,and C 5+ liquid yield of the aromatic type semi regeneration catalytic reforming of coal derived naphtha. The appropriate process parameters intervals were :WAIT 500—520℃,P 1.2—1.6MPa ,LHSV 2.0—3.0h –1. The optimal process conditions were determined as follows :WAIT at 516℃,P at 1.4MPa ,LHSV at 2.3h –1. Under the optimized process conditions ,the yield of aromatics reached 79.81%. In the operating condition intervals of response surface experiments ,the order of magnitude of WAIT ,P and LHSV on the yield of aromatics was :P >LHSV >WAIT . Compared to petroleum derived naphtha reforming ,coal derived naphtha reforming can obtain higher pure hydrogen yield ,hydrogen purity ,第一作者:朱永红(1990—),男,硕士。
十万吨芳构化操作规程

目录十万吨操作规程 (2)1 概述 (2)1.1原料规格 (2)1.2催化剂组分及性质 (2)1.3反应条件及反应结果 (2)2 分析项目及方法 (2)3正常开工和停工 (3)3.1.工艺过程描述及操作条件 (3)3.2开工方案及步骤 (4)3.3长时间停工步骤 (6)3.4短暂停工步骤 (7)4 事故处理 (7)4.1事故处理原则 (7)4.2紧急停工 (7)4.3反应器温度迅速上升、出现飞温现象 (8)4.4停循环水 (8)4.5短暂(晃电)停电 (8)4.6停净化风 (9)4.7燃气不足或燃气中断 (9)5附:工艺流程图 (9)十万吨操作规程1 概述本次开工是用装有南通扬子催化剂有限公司催化剂的大反应器进行轻油芳构化,进料量最大10t/h轻油及3t/h液化气。
1.1原料规格山东仕通芳构化原料为外购轻油跟内部油,内部油先切除轻、重组分,保留C6~C9馏程段组分作为芳构化原料。
外采轻油指标如下表表1-1 原料要求备注:建议采购饱和烃含量高的轻油。
1.2催化剂组分及性质表1-2 催化剂物化性质1.3反应条件及反应结果1.3.1反应条件表1-3 反应条件表2 分析项目及方法表2-1 分析项目及频次3正常开工和停工3.1.工艺过程描述及操作条件3.1.1工艺过程描述本装置由反应系统、稳定系统和分馏系统组成。
原料轻油通过原料罐,由泵送出,经换热器E601A/B、E602、E603 A/B、E611(导热油预热)、E604换热后去加热炉F601加热至所需的反应温度,然后送入反应器R602顶部进料。
由R602出来的反应产物温度较高,先送到分馏塔作为塔底再沸器E608热源,跨过E606再去E604作为原料的最后一段换热,从E604出来的反应产物经E603A/B进一步换热后,经稳定塔进料水冷换热器E610去稳定塔T-601作为该塔进料。
稳定塔顶产物为液化气和少量不凝气,经换热器E601A/B与原料液化气换热,再进入冷却器E605A/B、E612A/B冷凝冷却,然后进入V601进行气液分离,液化气经P-602泵一部分作为T-601回流,另一部分作为产品液化气出装置进入罐区。
直馏石脑油芳构化改质工艺的研究
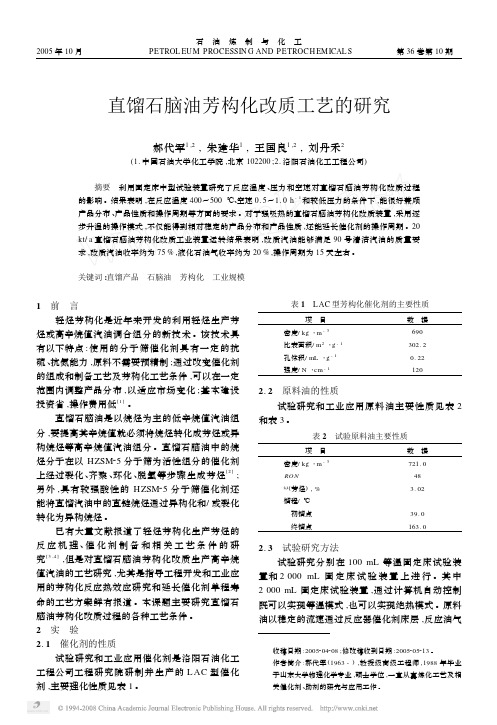
收稿日期:2005204208;修改稿收到日期:2005205213。
作者简介:郝代军(1963-),教授级高级工程师,1988年毕业于山东大学物理化学专业,硕士学位,一直从事炼化工艺及相关催化剂、助剂的研究与应用工作。
直馏石脑油芳构化改质工艺的研究郝代军1,2,朱建华1,王国良1,2,刘丹禾2(1.中国石油大学化工学院,北京102200;2.洛阳石油化工工程公司) 摘要 利用固定床中型试验装置研究了反应温度、压力和空速对直馏石脑油芳构化改质过程的影响。
结果表明,在反应温度400~500℃、空速0.5~1.0h -1和较低压力的条件下,能很好兼顾产品分布、产品性质和操作周期等方面的要求。
对于强吸热的直馏石脑油芳构化改质装置,采用逐步升温的操作模式,不仅能得到相对稳定的产品分布和产品性质,还能延长催化剂的操作周期。
20kt/a 直馏石脑油芳构化改质工业装置运转结果表明,改质汽油能够满足90号清洁汽油的质量要求,改质汽油收率约为75%,液化石油气收率约为20%,操作周期为15天左右。
关键词:直馏产品 石脑油 芳构化 工业规模1 前 言轻烃芳构化是近年来开发的利用轻烃生产芳烃或高辛烷值汽油调合组分的新技术。
该技术具有以下特点:使用的分子筛催化剂具有一定的抗硫、抗氮能力,原料不需要预精制;通过改变催化剂的组成和制备工艺及芳构化工艺条件,可以在一定范围内调整产品分布,以适应市场变化;基本建设投资省,操作费用低[1]。
直馏石脑油是以烷烃为主的低辛烷值汽油组分,要提高其辛烷值就必须将烷烃转化成芳烃或异构烷烃等高辛烷值汽油组分。
直馏石脑油中的烷烃分子在以HZSM 25分子筛为活性组分的催化剂上经过裂化、齐聚、环化、脱氢等步骤生成芳烃[2];另外,具有较强酸性的HZSM 25分子筛催化剂还能将直馏汽油中的直链烷烃通过异构化和/或裂化转化为异构烷烃。
已有大量文献报道了轻烃芳构化生产芳烃的反应机理、催化剂制备和相关工艺条件的研究[3,4],但是对直馏石脑油芳构化改质生产高辛烷值汽油的工艺研究,尤其是指导工程开发和工业应用的芳构化反应热效应研究和延长催化剂单程寿命的工艺方案鲜有报道。
(海)异构化操作规程(精)

异构化装置操作规程I目录前言 (1)第一篇概况 (3)第一章装置任务及物料平衡 (3)第一节装置规模及特点 (3)第二节生产技术方案 (3)第三节物料平衡 (3)第二章工艺流程 (5)第二篇工艺原理及操作参数选择 (6)第一章目的和任务 (6)第二章化学反应机理 (6)第三章催化剂 (7)第四章操作参数 (9)第三篇装置开停工 (11)第一章开工准备的条件 (11)第二章开工前的准备 (11)第一节原材料准备 (11)第二节全面检查 (12)第三节设备、工艺管线的冲洗、吹扫及管线试压 (13)第四节系统气密 (14)第五节系统干燥 (16)第六节催化剂、干燥剂装填 (17)第三章装置开工步骤 (20)第一节开工准备 (20)第二节催化剂干燥及还原 (20)第三节反应部分进油开工 (21)第四章装置停工 (22)第一节停工前准备工作 (22)第二节正常停工步骤 (22)II 海南炼化异构化装置操作规程第三节停工后冲洗吹扫 (23)第四篇岗位操作法 (24)第一章总述 (24)第一节主要操作条件 (24)第二节主要质量指标 (24)第三节分析项目规定 (25)第二章操作参数变化与调节 (26)第一节正常生产操作调节 (26)第二节生产不正常的原因及调节方法 (27)第五篇事故处理 (29)第一章紧急停工 (29)第一节紧急停工原则 (29)第二节紧急停工步骤 (29)第二章事故处理 (30)第一节瞬时间停电 (30)第二节长时间停电 (30)第三节停水 (30)第四节停风 (31)第五节反应温度超高 (31)第六节爆炸、着火、管线破裂或严重泄漏 (31)第六篇装置安全与环保 (33)第一章安全 (33)第一节一般防火防爆规定 (33)第二节安全生产制度 (33)第二章环保 (34)第一节环保管理制度 (34)第二节环保管理 (34)第三节可燃性气体、有毒有害气体 (35)第四节环境大气及噪声 (35)异构化装置操作规程1 C5/C6烷烃异构化操作规程前言提高汽油辛烷值,增加发动机的压缩比对汽车工业的节能和提高汽车性能具有重大意义。
芳构化反应系统工艺流程

芳构化反应系统工艺流程(总4页)本页仅作为文档封面,使用时可以删除This document is for reference only-rar21year.March芳构化反应系统工艺流程混合碳四液化汽和石脑油是在KCIA-Ⅱ分子筛催化剂的作用下,经过碳四烯烃的叠合、脱氢环化、脱氢芳构化及烷烃的裂解等系列催化反应,生成混合芳烃,及副产品液化汽和干气。
反应是强放热反应。
1)工艺流程及说明:A.加热反应部分加热反应单元包括原料-产物换热器、加热炉、反应器、等单元设备操作。
由MTBE或罐区来的原料C4和石脑油分别进入原料缓冲罐(V202、V201)。
原料C4经泵P202提升后,经计量控制,一线送至原料-产物换热器E201,另一线送至产物-注冷料换热器E202;石脑油经泵P201提升后经计量控制,与一线原料C4混合送至原料-产物换热器E201。
混合原料分别经原料-产物换热器E201、E203、加热炉F201加热至280-390℃后由反应器R201顶部进入反应器。
部分原料液化气(或贫稀液化气)经产物-注冷料换热器E202加热汽化后,经计量控制分两线由反应器R201中部两催化剂床层之间注入反应器,以便于调节反应床层温度。
反应产物由反应器R201底部采出分别经原料-产物换热器E203、(E-202)、E201换热后进入产物气液分离罐V203,罐底部凝液经泵P203提升后计量控制后进入稳定塔;罐顶分离出的气相经产物空冷器AC201、产物水冷器E204冷却至40℃后进入产物凝液分离罐V204,罐顶部采出为不凝气,进入吸收解吸塔T201中部塔板,底部采出液相,经泵P204提升后进入吸收解吸塔中部塔板。
B.催化剂再生部分反应进行一段时间后,随着反应器R201中催化剂表面结焦的增加,催化剂表面活性降低,当检测到产品质量不能满足要求时,需将反应器R201切换出反应系统进行催化剂烧焦再生处理。
催化剂再生采用氮气和空气作为再生气体,并控制再生气体中的氧含量,以防止反应催化剂床层再生烧焦超温破坏催化剂。
石脑油芳构化操作规程
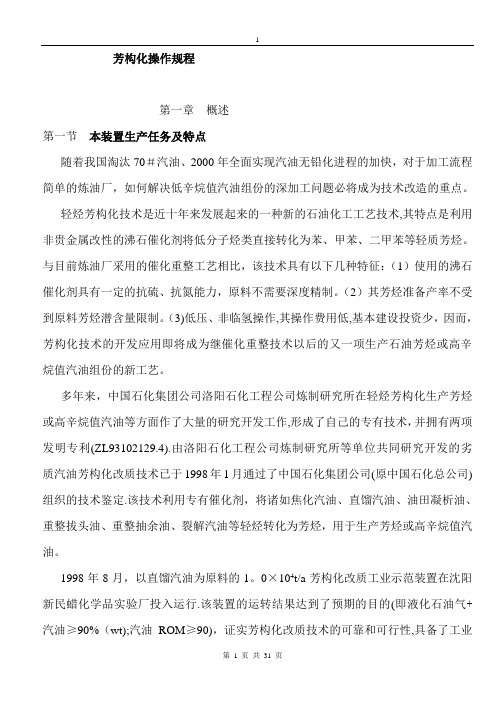
芳构化操作规程第一章概述第一节本装置生产任务及特点随着我国淘汰70#汽油、2000年全面实现汽油无铅化进程的加快,对于加工流程简单的炼油厂,如何解决低辛烷值汽油组份的深加工问题必将成为技术改造的重点。
轻烃芳构化技术是近十年来发展起来的一种新的石油化工工艺技术,其特点是利用非贵金属改性的沸石催化剂将低分子烃类直接转化为苯、甲苯、二甲苯等轻质芳烃。
与目前炼油厂采用的催化重整工艺相比,该技术具有以下几种特征:(1)使用的沸石催化剂具有一定的抗硫、抗氮能力,原料不需要深度精制。
(2)其芳烃准备产率不受到原料芳烃潜含量限制。
(3)低压、非临氢操作,其操作费用低,基本建设投资少,因而,芳构化技术的开发应用即将成为继催化重整技术以后的又一项生产石油芳烃或高辛烷值汽油组份的新工艺。
多年来,中国石化集团公司洛阳石化工程公司炼制研究所在轻烃芳构化生产芳烃或高辛烷值汽油等方面作了大量的研究开发工作,形成了自己的专有技术,并拥有两项发明专利(ZL93102129.4).由洛阳石化工程公司炼制研究所等单位共同研究开发的劣质汽油芳构化改质技术已于1998年1月通过了中国石化集团公司(原中国石化总公司)组织的技术鉴定.该技术利用专有催化剂,将诸如焦化汽油、直馏汽油、油田凝析油、重整拔头油、重整抽余油、裂解汽油等轻烃转化为芳烃,用于生产芳烃或高辛烷值汽油。
1998年8月,以直馏汽油为原料的1。
0×104t/a芳构化改质工业示范装置在沈阳新民蜡化学品实验厂投入运行.该装置的运转结果达到了预期的目的(即液化石油气+汽油≥90%(wt);汽油ROM≥90),证实芳构化改质技术的可靠和可行性,具备了工业应用的条件。
目前,广西田东石油化工总厂是一个加工原油18万吨的小型炼厂。
在国家强制取消70#汽油的生产和销售后,该厂将有2万吨的直馏汽油无法作为汽油调和组分出厂,因此,采用洛阳石化工程公司开发的劣质汽油调和组分出的劣质汽油芳构化改质技术就能很好地解决这一问题。
芳烃分离操作规程
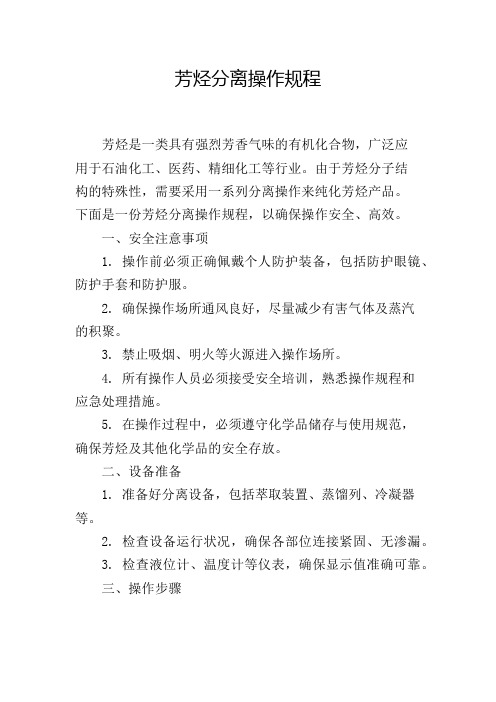
芳烃分离操作规程芳烃是一类具有强烈芳香气味的有机化合物,广泛应用于石油化工、医药、精细化工等行业。
由于芳烃分子结构的特殊性,需要采用一系列分离操作来纯化芳烃产品。
下面是一份芳烃分离操作规程,以确保操作安全、高效。
一、安全注意事项1. 操作前必须正确佩戴个人防护装备,包括防护眼镜、防护手套和防护服。
2. 确保操作场所通风良好,尽量减少有害气体及蒸汽的积聚。
3. 禁止吸烟、明火等火源进入操作场所。
4. 所有操作人员必须接受安全培训,熟悉操作规程和应急处理措施。
5. 在操作过程中,必须遵守化学品储存与使用规范,确保芳烃及其他化学品的安全存放。
二、设备准备1. 准备好分离设备,包括萃取装置、蒸馏列、冷凝器等。
2. 检查设备运行状况,确保各部位连接紧固、无渗漏。
3. 检查液位计、温度计等仪表,确保显示值准确可靠。
三、操作步骤1. 将原料进料至萃取装置中,加入适量溶剂进行萃取。
调节萃取器温度和压力,控制好进料速度,确保分离效果。
2. 将萃取液输送至蒸馏列进行蒸馏分离。
控制蒸馏温度和压力,根据芳烃的沸点和馏分组成进行分离。
3. 冷凝分离出的芳烃馏分并收集。
4. 将芳烃馏分进行后续处理,如除水、脱色等,以进一步提高产品质量。
5. 对废水和废气进行处理,确保环境安全与污染防治。
四、质量控制1. 在操作过程中,每小时进行一次产品质量抽样测试,确保产品符合规定标准。
2. 对芳烃馏分进行关键指标的检测,如密度、折射率、饱和度等。
3. 对废水和废气进行抽样测试,确保其排放符合环保要求。
五、事故应急处理1. 发生事故时,立即切断电源或关闭相关设备,采取紧急堵漏措施,防止泄漏扩散。
2. 通知应急救援人员,进行事故处理和清理。
3. 当有人员中毒时,应及时将其送往医院,并保持呼吸道通畅。
六、操作结束1. 操作结束后,关闭各设备的开关,清理操作现场,保持设备和现场的干净整洁。
2. 将废弃物、废水、废气等无害化处理,遵守环保要求。
3. 对设备进行日常维护保养,及时修复和更换损坏部件。
- 1、下载文档前请自行甄别文档内容的完整性,平台不提供额外的编辑、内容补充、找答案等附加服务。
- 2、"仅部分预览"的文档,不可在线预览部分如存在完整性等问题,可反馈申请退款(可完整预览的文档不适用该条件!)。
- 3、如文档侵犯您的权益,请联系客服反馈,我们会尽快为您处理(人工客服工作时间:9:00-18:30)。
芳构化操作规程第一章概述第一节本装置生产任务及特点随着我国淘汰70#汽油、2000年全面实现汽油无铅化进程的加快,对于加工流程简单的炼油厂,如何解决低辛烷值汽油组份的深加工问题必将成为技术改造的重点。
轻烃芳构化技术是近十年来发展起来的一种新的石油化工工艺技术,其特点是利用非贵金属改性的沸石催化剂将低分子烃类直接转化为苯、甲苯、二甲苯等轻质芳烃。
与目前炼油厂采用的催化重整工艺相比,该技术具有以下几种特征:(1)使用的沸石催化剂具有一定的抗硫、抗氮能力,原料不需要深度精制。
(2)其芳烃准备产率不受到原料芳烃潜含量限制。
(3)低压、非临氢操作,其操作费用低,基本建设投资少,因而,芳构化技术的开发应用即将成为继催化重整技术以后的又一项生产石油芳烃或高辛烷值汽油组份的新工艺。
多年来,中国石化集团公司洛阳石化工程公司炼制研究所在轻烃芳构化生产芳烃或高辛烷值汽油等方面作了大量的研究开发工作,形成了自己的专有技术,并拥有两项发明专利(ZL93102129.4)。
由洛阳石化工程公司炼制研究所等单位共同研究开发的劣质汽油芳构化改质技术已于1998年1月通过了中国石化集团公司(原中国石化总公司)组织的技术鉴定。
该技术利用专有催化剂,将诸如焦化汽油、直馏汽油、油田凝析油、重整拔头油、重整抽余油、裂解汽油等轻烃转化为芳烃,用于生产芳烃或高辛烷值汽油。
1998年8月,以直馏汽油为原料的1.0×104t/a芳构化改质工业示范装置在沈阳新民蜡化学品实验厂投入运行。
该装置的运转结果达到了预期的目的(即液化石油气+汽油≥90%(wt);汽油ROM≥90),证实芳构化改质技术的可靠和可行性,具备了工业应用的条件。
目前,广西田东石油化工总厂是一个加工原油18万吨的小型炼厂。
在国家强制取消70#汽油的生产和销售后,该厂将有2万吨的直馏汽油无法作为汽油调和组分出厂,因此,采用洛阳石化工程公司开发的劣质汽油调和组分出的劣质汽油芳构化改质技术就能很好地解决这一问题。
第二节生产基本原理及技术概述2.1轻烃芳构化的化学反应机理轻烃分子在HZSM-5分子筛催化剂上的反应较为复杂,一般认为包括裂化、齐聚、环化和脱氢四个主要步骤。
烃分子首先裂化成低分子“碎片”再经过正碳离子机理“连接”成环,通过脱氢转移生成芳烃。
由于受到分子在HZSM-5沸石上的芳构化产品分布相近。
烃分子在HZSM-5沸石孔道内的裂化反应遵循正碳离子反应,但由于HZSM-5沸石上的芳构化反应是一个择形催化过程,烃分子在这种沸石上的裂化不同于一般的裂化规律。
由于孔道开口及孔道内扩散空间的约束,直链更容易接近内表面酸性中心而优先裂化。
如不同结构烷烃的裂化速率的大小顺序为:直链烷烃﹥单侧链烷烃﹥双侧链烷烃烃分子首先裂化成低分子烯烃,进而生成BTX的反应历程,可以描述为图1所示的过程。
+ →CH3-CH2-CH-CH3+CH3-CH2-CH=CH2← CH3-CH2-CH-CH3CH3-CH2-CH-CH2CH3-CH2-CH-CH3→CH3-C6H4-CH3CH3-CH-CH2-CH2环化脱氢图1低分子烃类芳构化反应历程2.2原料对芳构化反应性能的影响HZSM-5催化剂对各种轻烃原料的芳构化均有很好的适应性,但是原料组成对芳构化过程仍存在一定的影响,主要表现在以下几个方面。
原料组成愈不饱和以及碳数愈多,则愈容易转化为芳烃。
碳数相同的烃类转化为芳烃时,芳构化反应所需要的强度按下列顺序增加:双烯<<烯烃<<环烷烃<<烷烃原料的性能强烈地影响催化剂的失活速率。
缺氢的原料更易结焦,而导致催化剂的失活速率更快,缩短了催化剂的寿命。
烷烃原料的芳构化是高度吸热的反应,而烯烃原料的芳构化过程,依据非芳构化物的组成,可能是放热反应,反应中产生的氢气愈多则吸热性愈强,将原料掺合到一定氢含量的水平,可使芳构化在近于热平衡(吸、放热相等)的情况下进行。
2.3轻烃芳构化催化剂的开发轻烃芳构化催化剂的发展主要经历两个阶段:HASM-5及其金属改性的分子筛催化剂和杂沸石筛催化剂。
轻烃芳构化过程的早期研究是采用HZSM-5型分子筛催化剂。
而后,为了弥补芳构化催化剂在芳构化活性、产物液相收率和芳烃选择性不高的缺点,研究者对HZSM-5分子筛进行了改性。
HZSM-5分子筛单金属改性组分一般用Zn或者Ca。
为了改善催化剂的稳定性,国内外开发了添加第二改性组分的催化剂,其中铂锌、铂锌镓等催化剂的单程寿命达200小时,但是铂的加入提高了催化剂的生产成本。
目前将Ni或AI作为第二改性金属,也取得了较好的效果:不但能增加催化剂的稳定性,而且还能改善催化剂的活性和选择性。
[经过多年努力,洛阳石化工程公司炼制研究所开发出LAC系列芳构化催化剂,适用于直镏汽油芳构化性质装置,取得满意的工业试验结果。
工业运转结果表明:对于直镏汽油芳构化性质生产高辛烷值汽油和组分,LAC-3型芳构化催化剂具有良好的活性、选择性、稳定性及抗结焦性能。
2.4工艺条件对轻烃芳构化过程的影响影响轻烃芳构化反应需要足够高的反应温度。
不同的原料,所需的最低温度相差很大,烯烃可低于370℃,而丙烷则需538℃。
直镏汽油芳构化过程从宏观上表现为强的吸热反应。
从化学热力学方面考虑,提高反应温度有利于芳烃产率的增加,使产品中芳烃含量一直保持较高的水平;从化学动力学方面考虑,提高反应温度能增加化学反应速度,更有利于直镏汽油向芳烃化合物转化。
但是过高的反应温度促使热裂化等副反应加剧,导致干气和焦炭产率增加。
因此,芳构化反应温度选择400-530℃为宜。
进料空速的大小,对装置的处理量越大,因此装置的相对投资费用和操作费用就越低。
但是进料空速越大,反应物料在催化剂床层内停留时间就越短,化学反应就不能充分进行。
综合考虑各方面因素,选择的进料空速为1.0h-1左右比较合适,这样,在产品分布较合理的情况下,催化剂又具有较长的单程运转周期。
经典的脱氢环化反应或脱氢环化二聚反应都不能在压力下运行,因为它们对氢分压是十分敏感的。
而HZSM-5催化剂上的芳构化反应,则在较高的压力下操作并无有害影响,不过一般都在常压下或低压下进行。
第三节工艺流程说明芳构化改质装置工艺流程见附图。
3.1反应部分由于直镏汽油芳构化改质反应为强的吸热反应,需采用分段加热的方式实现整个反应过程。
反应部分采用了两台加热炉,一台为原料加热炉,一台为中间产物加热炉。
反应器为三台,加热炉反应器之间联接相应跨线,使三台反应器以一定形式串联使用,从而达到分段反应的目的,芳构化装置采用模拟移动床循环反应再生方式实现连续操作,反应器中两台反应,一台再生。
该装置反应系统流程的特点为:每个操作周期的前反应器均是采用前一周期未经再生的后反应器。
正常操作状态为其中两台反应器串联反应,另一台反应器则处于再生或等待状态。
自装置外来的经原料泵(P101A,B)送至原料油-反应产物换热器(E101A,B),换热至泡点(171℃),进入芳构化反应器(R101A)顶部。
芳构化反应器(R101A)出来的中间反应产物进入中间反应产物加热炉(F102)再加热,进入芳构化反应器(R101B)顶部。
自芳构化反应器出来的反应产物换热后送入催化装置吸收稳定系统。
3.2再生部分芳构化催化剂的再生部分采用氮气中配空气的方式对失活催化剂进行烧焦再生。
由于再生气需要干燥及脱硫,因而再生部分设再生气干燥及脱硫器各一台。
A 催化剂再生本装置的再生系统是一个闭路循环系统,再生气循环使用。
再生时再生系统中应充满氮气,并补进一定量的空气,以保证再生气的氧含量。
自系统来的氮气和净化压缩空气(补充用)按比例分别计量进入再生气分液罐(V103)分液后,经再生气压缩机(C102)升压到0.55Mpa(A)进入再生气换热器(E104)与循环气体换热后,进入再生气换热器(E104)与循环气体换热后,进入再生气加热炉(F103)加热至530℃去芳构化反应器,从床层顶部自上而下进行烧焦。
烧焦后高温烟气经再生气换热器(E104)与再生气换热后,由再生气冷却器(E105)冷却至40℃,进入再生气分液罐(V103)分液,经再生气脱硫器(D101)脱除微量二氧化硫和再生干燥器(D102)脱除其中微量水分后进入再生气压缩机(C102)循环操作。
为节省氮气用量,再生气体循环使用,并根据反应器床层温度变化情况,随时补充空气。
b.干燥剂再生再生气干燥器(D102)内干燥剂在使用一段时期后需要再生以脱除干燥剂吸附的过时水分。
催化剂再生操作时在干燥器(D102)出口采再生烟气分析其露点,当再生烟气露点高于-25℃时则干燥剂需要再生。
在催化剂再生结束后应将流程切换为干燥剂再生流程,进行干燥剂再生。
干燥剂再生温度为200℃,再生时间为5h。
再生气体为净化风或再生烟气。
再生气进入再生气分液罐(V103)分液,再经过再生气脱硫器后(D101)后,返回再生气压缩机(C102)升压。
升压的后的再生气经再生气换热器(E104)与循环气体换热后,进入再生气加热炉(F103)加热至200℃后,进入再生气干燥器(D102)脱除干燥剂吸附的水份。
从干燥器出来的再生气进入再生气换热器(E104)后,再经再生器冷却器(E105)冷却后,进入再生气分液罐(V103)。
再生气循环使用。
球形3A分子筛技术见表-1c 脱硫剂的更换时间为两年,装置运行两年后将其卸出更换新脱硫剂。
第四节原料性质及产品质量控制指标本芳构化装置设计原料为田东直镏汽油。
原料性质见表-24.1芳构化装置的产品分布及性质本芳构化装置的目的产品为高辛烷值汽油及液化石油气,同时副产的少量干气可作为料气使用。
本装置生产90#无铅汽油的产品分布及物料平衡见表-3。
本装置生产90#无铅汽油的性质见表-4,生产装置产品、中间产物及工艺指标分析项目次见表-5。
表-1 球形3A分子筛技术条件指标名称Ф1.5-1.7Ф3.0-3.3一级品合格品一级品合格品磨耗率, % ≤0.40 0.60 0.40 0.60 堆积率,g/ml ≥0.68 0.60 0.68 0.60 粒度,% ≥96.0 95.0 96.0 95.0 静态水吸附,% ≥20.0 19.0 20.0 19.0 抗压强度, (N/颗)≥44.0 59.0静态乙烯吸附,mg/g ≤3.0包装品含水量,%≤1.5表-2田东原油直镏汽油性质表-3 芳构化装置生产90#无铅汽油的产品分布及物料平衡项目90#汽油生产方案干气/m% H2m%CH4/m% C2H6/m%6.650.811.612.20项目田东直镏汽油密度/kg.m-3溴价/gBr.(100g)-1胶质/mg.(100ml)-1腐蚀/(Cu,50℃,3h) 诱导期/min硫/μg.g-1氮/μg.g-1馏程/℃IBM10%50%90%FBP 740.40.687.01a>48034<562.095.0119.0144.0172.5液化气m%C3H8/m%C3H6/m%C4H10/m%C4H8/m%液体收率/m%焦炭+损失、同% 18.81 10.33 3.35 3.92 1.20 73.28 1.27表-4 90#无铅高辛烷值汽油的性质项目90#汽油性质密度/kg.m3胶质/mg.(100ml)-1腐蚀(Cu,50℃,3h)诱导期/min芳烃/m%RONMON镏程/℃IBP10%50%90%FBP 7844.61a>48043.8490.281.044.089.0122.5157.0202.0表-5 生产控制分析样品名称分析项目分析次数备注直镏汽油比重、镏程三天一次反应中间油、粗汽油折光率、芳烃含量每班二次稳定汽油比重、镏程、蒸汽压折光率、芳烃含量辛烷值每天一次每班二次三天一次辛烷值开工初级每班一次富气组成分析每天一次再生烟气组成分析每班一次再生周期采样露点每周期一次再生周期采样第五节主要操作条件1.反应再生部分操作条件见表-6、表-7、表-8表-6 反应再生部分操作条件表项目反应再生反应温度℃400-530 530压力Mpa(绝) 0.55 0.55空速h-1进料重量空速0.52、加热炉部分操作条件表-7 加热炉操作条件表条件项目入口出口温度℃压力(表)MPa 温度压力(表)原料加热炉F101 225 0.6 530 0.45 中间产物加热炉F102470 0.4 530 0.35 再生加热炉F103 420 0.46 530 0.36 3、氮气压缩机操作条件表-8 氮气压缩机操作条件表排气量(标)m3/h温度℃压力(表)Mpa 3200 入口出口入口出口40 0.15 0.45第六节设备明细表能耗表3-8 能耗表(计算方法按SYJ1029-83规定)序号项目消耗量燃料低热值或能耗指标总能耗×104MJ/a单位能耗×MJ/a 单位耗量小时耗量年耗量单位数量单位数量单位数量单位数量123 4 5 6 7 8 9 10 11 121 循环水T/t 20 T/h 50 ×104t/a 40 MJ/t 4.19167.6 83.32 电Kwh/t 22 Kwh/t55 ×104kwh/a44 MJ/kwh12.56552.64 276.323 0.8Mpa T/t 0.12 T/h 0.3 ×104t/a0.24MJ/t 3181.97763.67 381.844 净化压缩空气M3/t 20 M3/h 50 ×M3n/a40 MJ/M3n1.6783.5 33.45 燃料气M3/t 63.2 M3/h 158 ×M3n/a126.4MJ/M3n27.053419.121709.56小计2484.92(59.35×104kcal/t)设备明细表一、主要工艺设备表表-10 反应器设备表序号设备名称设备编号设备规格介质名称操作条件数量总重t材质温度℃压力Mpa(A)1 芳构化反应器R101A,B Ф1200×3950(切线距)内装芳构化催化剂10.88m3直镏汽油,干气,液化石油气,粗汽油530 0.55 3 13.515CrMoR2 再生气脱硫器D101 Ф1200×4400(切线距)内装脱硫剂氮气,空气,二氧化硫40 0.25 1 2.4 20R3 再生气干燥器D102 Ф1200×5400(切线距)内装干氮气,空气230 0.35 1 2.8 20R燥剂4.75M3小计 5 表-12 加热炉设备表(采用三台合一形式)序号设备名称设备编号设备规格介质名称操作条件数量总重t材质温度℃压力Mpa(A)1 原料加热炉F101 Q=590kw 直镏汽油530 0.55 12 中间反应产物加热炉F102 Q=115kw 反应产物530 0.55 12 再生气加热炉F103 Q=162kw 再生气530 0.55 1小计 33.压缩机类表-12 主要设备表序号设备名称设备编号设备规格流量m3n/h介质名称操作温度℃操作压Mpa(A)数量轴功率KW电机功率KW入口出口入口出口1 气体压缩机C101A,B 原催化压2100 富气40 0.150.151.352 ~85 110缩机2 再生气压缩机C102 3200 再生气40 0.250.250.551 ~110 132表-13 容器类设备表序号设备名称设备编号设备规格介质名称操作条件数量总重t材质温度℃压力Mpa1 原料油缓冲罐V101 Ф1200×3000(切线距)卧式直镏汽油40 常压1 2.Q235-A2 气液分离罐V102 Ф800×3000(切线距)卧式液化气,汽油40 0.351 1.2Q235―A3 再生气分液罐V103 Ф1000×3000(切线距)卧式再生气40 0.251 1.520R4 再生气压机出口缓冲罐V104 Ф1000×3000(切线距)卧式再生气146 0.551 1.520R5 燃料气分液罐V105 Ф500×2900×6(切线距)立式燃料气40 0.7 1 0.5Q235-B6 放空分液罐V106 Ф1000×3000(切线距)卧式汽油230 0.21 1.520R7 污油罐V107 Ф500×2000(切线距)卧式污油240 0.4 1 0.820R8 0.8Mpa蒸汽分水V108 Ф500×1720立式蒸汽300 0.8 1 0.520R9 净化空气罐V109 Ф1200×4100×10 立式空气40 0.6 1 1.820R9表-14 冷换设备表序号设备名称设备编号设备规格介质名称操作条件数量总重t材质温度℃压力Mpa(A)1 原料油反应产物换热器E101A,B AES400-2.5-15-3/25-2管程:反应产物400 0.41 2 3 10/16MnR壳程:原料油180 0.82 原料油汽化器E102 BIU500-4.0/2.5-25-3/25/4管程:反应产物500 0.5 2 2 15CrMo/16MnR壳程:原料油225 0.73 反应产物E103A,B BES500-1.0-55-6/25-4管程:循环水40 0.5 2 5.510/16MnR冷却器壳程:反应产物200 1.174 再生气换热器E104 Ф600×6000,A=90(B=600)管程:再生气530 0.35 1 4.515CrMo/16MnR壳程:再生气420 0.555 再生气冷却器E105 AES400-1.0-40-6/19-4管程:循环水40 0.5 1 2.110/16MnR壳程:再生气261 0.316 放空气体冷却器E106 BIU400-4.0/4.0-25-3/19-2管程:循环水40 0.5 1 1.810/15CrMoR壳程:放空气体530 0.257 再生气冷却器E107 BUI400-4.0/4.0-25-3/19-2管程:循环水40 0.5 1 1.810/15CrMoR壳程:再生退料530 0.5表-15 机泵设备表序号机泵名编号进口压力Mpa温度℃介质密度kg/m3流量m3/h扬程m介质数量泵型号电机型号称(A)1 原料油泵P101A,B 0.1 40 724 3.49175 2 XDF5-25×7YB132S2-2W2 粗汽油泵P102A,B 0.2 40 712 2.08225 2 XDF2-25×9YB160M1-2W小计4第二章装置开停工操作第一节开工准备工作1 装置的吹扫、清洗1.1吹扫、冲洗的目的通过吹扫及冲洗,清除施工过程中进入设备、管道中的焊渣、泥沙等杂物,以及管道口的油污、铁锈。