子午线轮胎用原材料性能要求及成品检测
半钢子午线轮胎外观检测

一、成品外观质量的检查项目和外观缺陷修饰
轮胎成品的外观质量检查就是认真细致的检查每 条轮胎成品的胎里和胎外的质量,并按技术规定的外 观质量标准和等级标准进行分类和分级。 成品外观质量的检查目前仍采用手触和目测的方 法来进行检查。当轮胎外观质量将影响到使用质量, 则要按技术规定的质量标准判定为次品或废品。 成品外观质量检查的方式一种是检查人员人工滚 动轮胎进行检查。一种是将轮胎放到外观检查机上进 行检查。其方式是硫化后的轮胎从辊道线上取下,套 在慢速的锥形辊筒上先作外表的全面检查,接着将轮 胎放上扩胎机,扩开两个胎圈进行胎里的全面检查。 锥形辊筒和扩胎机都安装在辊道的两侧。
修饰或修补过的轮胎需再一次进行检查,认 为符合外观质量标准的可入库存放。对于加热修 补的轮胎,如若第一次修补后,修补的部位仍未 达到质量标准,就不能进行第二次加热修补,避 免轮胎修补部位经二次加热修补后,该部位的胶 料过硫,影响轮胎使用质量。
ห้องสมุดไป่ตู้
其他缺陷还有多 种缺陷暂不细讲。
X光检查 X光机大体上有X射线发生器及配套装 臵、辊道、装卸胎机构、撑胎器等够构成。 轿车及轻卡子午胎一般进行重启检查;全 钢载重子午胎则进行费重启检查。轿车及 轻卡子午胎的某种规格在产品质量稳定期 时一般按5%~10%的百分率进行X光抽查; 不稳定时期要增加抽查量,甚至100%检测。 全钢载重子午胎必须100%进行X光检测。
(2)、轮胎的外观缺陷属于面积较大或较深的, 要先将缺陷部位用软轴小砂轮打磨,清净打磨部 位的表面,再涂刷专用的粘合胶浆,待胶浆干燥 后,补贴专用的快速硫化胶片压实,并用刀子削 平整,做到补贴的胶片不要过厚或过薄,而后在 修补的部位放上电烙铁模或通蒸汽的修补模型, 用夹具夹压住进行局部的快速硫化。修补硫化的 时间是根据修补用的胶片的厚度来确定。
子午胎胶料半成品及成品质量缺陷产生原因分析
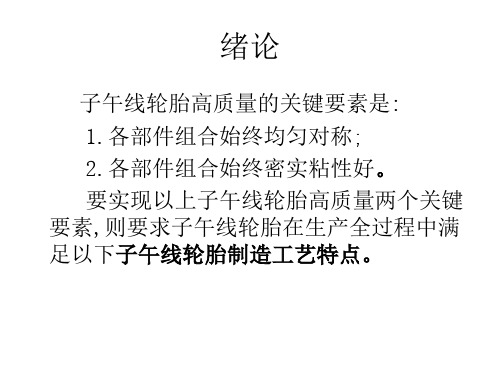
九.胶帘布裁断常见的质量缺陷 产生原因
1.帘布裁断宽度不符合技术标准 产生原因: 1.1.设定裁断宽度不合适; 1.2.定长递布装置运行不稳定等。 2.帘布裁断角度不符合标准 产生原因: 2.1.设定裁断角度不合适; 2.2.钢丝帘布不平整; 2.3.压延的钢丝帘布边部卷取不齐等。
九.胶帘布裁断常见的质量缺陷 产生原因
5.胶料喷霜 喷霜是一种由于配合剂析出胶料表面而形成
一层类似“白霜”的现象,多数情况下是硫黄析 出,也有是某些配合剂(如某些品种防老剂、间苯 二酚,石蜡等)的析出。
产生原因: 5.1混炼温度过高,排胶温度过高; 5.2硫黄颗粒大小不均,称量不准确; 5.3硫黄、防老剂、促进剂、白色填料等选用不 当; 5.4混炼胶压片过程中胶温过高等。
3.表面不光滑、粘性差 产生原因: 3.1.挤出机各部位温度不符合技术规定; 3.2.压延辊筒的温度不符合技术规定; 3.3.胶料混炼不均; 3.4.胶料的门尼粘度过低粘辊等。
六.内衬层常见的质量缺陷 产生原因
4.喷霜或有自硫胶 产生原因: 4.1.胶料的存放时间过长; 4.2.胶料有自硫或混入其它胶料或混炼不均; 4.3.返回胶掺用过多或返回胶是多次返回的; 4.4..机头排胶温度过高等。 5.复合差级不符合技术标准 产生原因: 5.1过渡层或气密层拉伸宽度发生变化; 5.2.定中心装置不灵敏等。
三.纤维胶帘布常见质量缺陷产生原因
3.胶料与帘布附着不好,掉皮 产生原因: 3.1.帘布未干燥好; 3.2.压延辊筒温度过低; 3.3.胶料门尼粘度过高; 3.4.帘布表面有污染; 3.5.干燥后帘布温度过低等。 4. 胶帘布表面粗糙 产生原因: 4.1.胶料热炼不均匀,供胶温度低; 4.2.压延辊筒温度过低; 4.3.胶料有自硫等。
子午线轮胎骨架材料的检点及判定方法

科学技术创新2020.18胎体帘线和带束层是轮胎重要的骨架材料,胎体帘线像人的骨架对身体一样,除了要承受轮胎部分应力外,还有缓冲性和稳定尺寸的作用,带束层是主要的受力部件,主要作用是固定胎体及增加胎面的刚性。
由此可见,材料对于轮胎发挥性能至关重要性材料,如果出现异常会使轮胎的性能打折扣,甚至存在安全隐患。
当轮胎的胎体帘线拉伸过紧时,胎肩部位的胎里容易出现露线或内衬层渗透进胎体帘线,由此容易引发胎肩脱层或轮胎漏气;当帘线过松时,在轮胎的胎圈或胎侧区域,反包帘线容易出现波浪,由此容易导致胎圈区域裂口或帘布脱层导致轮胎的耐久性能变差。
当带束层钢丝稀疏时,会导致带束层的安全倍数下降;当带束层呈波浪状时,轮胎胎面的磨耗和抓地性能会变差;此外,如果带束层接头钢丝过度重叠和端头上翘,则会影响轮胎的耐久性能。
由于轮胎的胎体帘线和带束层均包裹在轮胎的内部,无法直接进行观测,传统的方法是将轮胎按照规定进行切割和打磨从而获取轮胎的切片,再对轮胎的切片进行目视检查,进而判定骨架材料是否存在异常情况。
这种方法比较直观和可行,但不够充分且判断上存在一定的主观性,因此有必要进一步给出明确的方法以便进行综合全面的判定。
上述已经提到,对于轮胎胎体帘线的检测,传统的方法包括对于轮胎的切片通过目视检查胎圈钢丝底部帘线的松紧程度、检查胎圈钢丝是否存在明显的变形和移位,这样不够细致也不够具体,因而判定结果会存在一定的主观性,如果判定结果不当,会影响轮胎的使用性能和安全性能。
鉴于上述所存在的问题,在结合现有方法的基础之上,提供一种更为具体的判定方法,以最大限度的规避轮胎的成品材料出现品质和质量问题。
本方法即提供了一种对于子午线轮胎胎体帘线和带束层是否异常的判定方法,用于具体地检查轮胎胎体帘线和带束层是否合格。
所述轮胎胎体帘线的判定方法具体包括以下的步骤:步骤(a )将轮胎按照规定进行切割,切片的宽度约为20~30mm ,对于轮胎的切片要进行打磨处理,保证轮胎切片的切面上能够清晰地看到胎体帘线和带束层等骨架材料,然后对轮胎的切片尤其是轮胎胎圈钢丝底部的帘线进行仔细的检查,了解胎体帘线松紧程度是否适宜;步骤(b )对轮胎的切片在胎肩部位进行切割,观察内衬层与帘线之间的渗透关系;步骤(c )将轮胎的胎侧进行剥离,然后检查帘线是否发生弯曲,具体如下。
子午线轮胎生产所需的天然胶品质要求

颜色标志
绿 留在45μ m筛上的杂质 含量%(m/m),最大 值 塑性初值,最小值 塑性保持率,最小值 氮含量,%(m/m)最 大值 挥发物含量,% (m/m),最大值 灰分含量,%(m/m), 最大值 颜色指数,最大值 绿 绿 褐 红 黄
ISO 247 ISO 244 ISO 1656 ISO 2007
挥发物含量,%(m/m), 0.8 最大值 氮含量,%(m/m),最 大值 塑性初值(Po) ,最小值 0.6 30
塑性保持率PRI ,最小 值 颜色指数,最大值
60
75
75
70
60
50
ISO 2930
-
6
-
-
-
-
ISO 4660
中国天然胶标准
越南天然胶标准
SVR 3L 性能指标 典型值 留在45μ m筛上的杂质含 量%(m/m),最大值 灰分含量,%(m/m), 最大值 0.017 0.144 极限值 0.03 0.50 0.80 0.60 35 60 4 典型值 0.050 0.325 0.26 0.37 38 75 极限值 0.08 0.60 0.80 0.60 30 50 典型值 0.041 0.318 0.30 0.36 34 54 极限值 0.16 0.80 0.80 0.60 30 40 典型值 0.015 0.148 0.23 0.38 72 60 极限值 0.02 0.40 0.80 0.60 60 60±5 TCVN 3769:2004 TCVN 3769:2004 TCVN 3769:2004 TCVN 3769:2004 TCVN 3769:2004 TCVN 3769:2004 TCVN 3769:2004 TCVN 3769:2004 SVR 10 SVR 20 SVR CV60 检验方法
化学工业部关于加强子午线轮胎研制、生产、质量管理的若干规定(试行)

化学工业部关于加强子午线轮胎研制、生产、质量管理的若干规定(试行)文章属性•【制定机关】化学工业部(已撤销)•【公布日期】1989.10.15•【文号】[89]化橡字第617号文•【施行日期】1989.10.15•【效力等级】部门规章•【时效性】现行有效•【主题分类】质量管理和监督正文化学工业部关于加强子午线轮胎研制、生产、质量管理的若干规定(试行)(1989年10月15日以(89)化橡字第617号文发布)第一章总则第一条子午线轮胎是尼龙斜交轮胎的换代产品,其产品性能优越,生产技术复杂,工艺要求严格。
为加强生产建设的宏观控制和产品质量管理,确保子午线轮胎的质量和声誉,特制定本规定。
第一条本规定适用于轮胎制造行业,凡加工子午线轮胎的单位都必须严格执行本规定。
第二章研制与试产第三条进行子午线轮胎研制要有化学工业部或省、自治区、直辖市下达的正式计划为依据。
各省、自治区、直辖市化工厅(局)下达计划前应征得化学工业部(以下简称部)同意。
第四条企业研制子午线轮胎必须具备以下基本条件:1.产品有较大的用户和销售市场。
2.有先进成熟可靠的技术来源。
3.有原材料供应渠道。
4.有完善的子午线轮胎生产工艺装备,并形成生产线。
密炼、压延、压出、成型、硫化和成品检测主要工序能满足生产工艺的要求。
5.子午线轮胎与斜交轮胎分开生产,实行单独管理。
第五条根据不同品种,试生产数量应控制在3000条至5000条以下,试生产时间为2年左右。
第六条对试生产期间出厂的产品必须打上不易脱落的“试制品”字样,否则一经查出,则按不合格品论处。
第三章鉴定与投产第七条任何品种、规格的子午线轮胎投产前,必须经研制、试产、鉴定的程序。
产品鉴定分两级管理,属国内首家研制的品种、规格,或由部下达的各种研制计划,其产品由部组织鉴定。
鉴定计划于当年第一季度提出。
其他品种、规格由主管省、自治区、直辖市化工厅(局)鉴定。
鉴定资料须事先报部审查同意后,再履行鉴定手续,鉴定证书报部备案。
全钢子午线轮胎新新用橡胶常用胶种跟性能
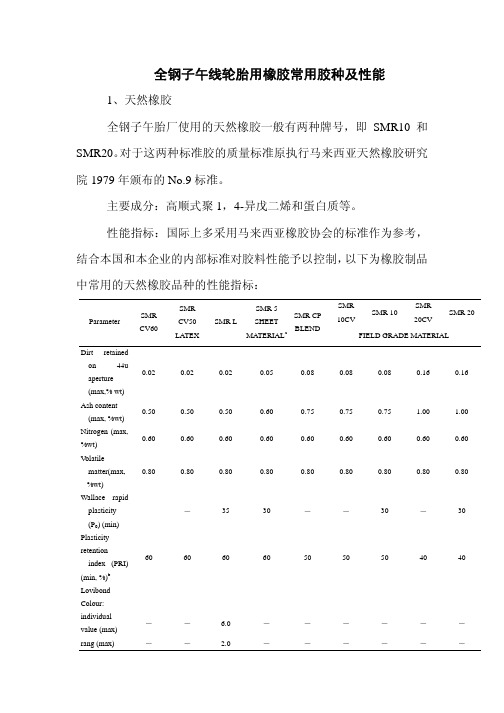
全钢子午线轮胎用橡胶常用胶种及性能1、天然橡胶全钢子午胎厂使用的天然橡胶一般有两种牌号,即SMR10和SMR20。
对于这两种标准胶的质量标准原执行马来西亚天然橡胶研究院1979年颁布的No.9标准。
主要成分:高顺式聚1,4-异戊二烯和蛋白质等。
性能指标:国际上多采用马来西亚橡胶协会的标准作为参考,结合本国和本企业的内部标准对胶料性能予以控制,以下为橡胶制品中常用的天然橡胶品种的性能指标:SMR 10CV SMR 10SMR20CVSMR 20Parameter SMRCV60SMRCV50LATEXSMR LSMR 5SHEETMATERIAL aSMR CPBLENDFIELD GRADE MATERIALDirt retainedon 44uaperture(max,% wt)0.02 0.02 0.02 0.05 0.08 0.08 0.08 0.16 0.16Ash content(max, %wt)0.50 0.50 0.50 0.60 0.75 0.75 0.75 1.00 1.00 Nitrogen (max,%wt)0.60 0.60 0.60 0.60 0.60 0.60 0.60 0.60 0.60 V olatilematter(max,%wt)0.80 0.80 0.80 0.80 0.80 0.80 0.80 0.80 0.80 Wallace rapidplasticity(P0) (min)-35 30 --30 -30 Plasticityretentionindex (PRI)(min, %)b60 60 60 60 50 50 50 40 40LovibondColour:individualvalue (max)-- 6.0 ------rang (max) -- 2.0 ------Mooney viscosity ML(1+4)100 ℃b 60(+5, -5) 50(+5, -5)--65(+7, -5)c-c-Cure dR R R - R R -R-Colour coding markerBlack BlackLightGreenLight GreenBlue Magenta Brown Yellow RedPlastic wrapcolourTransparent Transparent Transparent Transparent Transparent Transparent Transparent Transparent TransparentPlastic stripcolour Orange Orange TransparentOpaque WhiteOpaque WhiteOpaque WhiteOpaque WhiteOpaque WhiteOpaque WhiteaTwo sub-grades of SMR 5 are SMR 5RSS and SMR 5ADS which areprepared by direct baling of ribbed smoked sheet and air-dried sheet (ADS), respectively.b Special producer limits and related controls are also imposed by theRRIM to provide additional safeguard.c The Mooney viscosities of SMR 10CV and SMR 20CV are, atpresent ,not of specification status. They are , however, controlled at the producer and to 60(+7,-5) for SMR 10C and 65(+7,-5) for SMR 20C.d Rheograph and cure test data (delta torque, optimum cure time andscorch) are provided.目前在子午线轮胎生产企业中最常用的品种是:SMR 20和SMR 10,对于这两种产品在使用中的主要区别是:(1)杂质含量:SMR 10<SMR 20,(2)塑性保持率:SMR 10>SMR 20。
子午线轮胎质量分析

论据分析
通过各部位材料能量耗散所占比例分配可以看出,轮胎材料滞后损失能量 (生热量)主要集中在胎面部位,其次是胎圈部位。就是说胎面胎圈部位 材料能量耗散分布所占的比例最大,产生的滞后损失就大,产生的热量相 应也大,同时对应部件越易出现问题。 1、轮胎在滚动时,胎肩部位所受到的交变应力(即,拉伸,压缩,剪切 各种应力同时存在的多项应力)最大也最复杂,产生滞后损失而生热量最 大,出现问题的几率就大。 2、带束层承受着胎体的60——75%的应力,所以带束层端点蠕动量最 大,生热量就大,端点包胶就容易脱离,从而造成肩部脱层/带束层端点 松散。 3、轮胎内磨擦产生的能量消耗占轮胎总能量消耗的80%以上。 4、胎圈部位出现问题多的原因也是如此。 5、子午线轮胎由于胎体帘线呈子午向(径向)排列,在负荷状态下胎侧 径向变形大,因侧向刚性低,胎侧胶承受的应力高。在此情况下,胎侧中 部橡胶经受双向伸张(这也是造成胎侧拉链爆的原因之一),而胎圈区 和胎面边端则为双向压缩,从而致使胎圈区产生屈挠裂口或导致带束层与 胎面边端脱层。
轮胎在使用过程中, 各部位材料能量耗散分布所占比例
胎面39%.带束层8%,胎体帘布6%,基部 胶5%。 胎冠及胎肩部位材料能量耗散合计为58%。 胎圈14%,三角胶13%,胎体帘布6%。 子口部位材料能量耗散合计为33%。 内衬层8%,胎侧胶7%,胎体帘布6%。 胎侧部位材料能量耗散合计21%。
客户服务培训
全钢载重子午线轮胎 质量鉴定知识
轮胎损坏的原因1
使用问题:超载、不标准气压、非标轮辋及轮辋变形或爆破、 车况不良、使用环境与轮胎性能不匹配、撞击、扎伤、急转弯/ 转弯半径过小、急刹车。 性能问题(能力问题):如超载性能、高速性能、散热性能。 性能问题实际与使用问题也有关系。也是受大环境的影响,人 为或少数人不能改变的问题。 制造问题:胶部件脱层(气泡、杂质、粘合不好)、部件之间 无差级或带束层上偏(一般发生在成型工序)、部件尺寸或性 能不合格或胎侧及内衬层接头过大、胎体帘布稀线(一般在压 延裁断帘布尾线部分时)、辟缝(成型定型压力过大或扯拉用 力过大时易造成辟缝)、帘线交叉。 人为制造:用人为制造假病象来掩盖轮胎出现的真实问题。
轮胎材料检测项目 轮胎材料检测标准和方法

轮胎材料检测项目轮胎材料检测标准和方法轮胎作为汽车的关键部件,是汽车性能的一个重要体现。
为了确保汽车行驶安全、乘坐舒适和节约燃料,国内外针对轮胎材料性能检测的试验颁布了多项标准。
这些标准随着我国汽车工业和交通运输业的发展被不断完善,并已列入安全性能检测的技术要求中,本文就轮胎材料检测标准和方法的问题详细的为大家介绍一下。
检测橡塑材料检测实验室可轮胎材料检测服务。
作为第三方检测中心,机构拥有CMA、CNAS检测资质,检测设备齐全、数据科学可靠。
轮胎材料检测项目拉伸强度扯断伸长率、扯断永久变形、静负荷性能、老化后拉伸强度变化率绝对值等。
轮胎材料检测方法1、热轧机法和烘箱法轮胎制造行业是天然和合成橡胶的用户之一。
轮胎的安全和质量需要进行严格的控制,并且所有的原材料都必须经过多项质量测试。
对生橡胶的水分和其他易挥发物质含量规定了两种分析方法:热轧机法和烘箱法。
例如水分含量<1%(典型值为0.20%~0.40%MC,有的水分含量甚至更低),如果水分过高将对生产成型工艺有着重大的影响。
2、卤素干燥法,可以为橡胶行业更好、更快的测定方法,从而生产出高质量、高可靠性的轮胎。
目前塑胶、橡胶行业在产品的生产、注塑、成型工艺控制过程中由于原料水分过大而导致产品出现裂痕、起泡、缩水等系列现象。
卤素快速水分检测仪已被广泛引用到塑胶、橡胶行业不同品种类型的原料、半成品、成品等生产过程中。
轮胎检测标准GB/T2983-2023摩托车轮胎系列GB/T9749-2023力车轮胎性能试验方法GB/T22036-2023轮胎惯性滑行通过噪声测试方法GB/T22628-2023摩托车轮胎滚动周长试验方法GB/T23664-2023汽车轮胎无损检验方法X射线法HG/T 2906-2023力车轮胎静负荷性能试验方法GB/T23663-2023汽车轮胎纵向和横向刚性试验方法。
子午线轮胎执行标准-概述说明以及解释
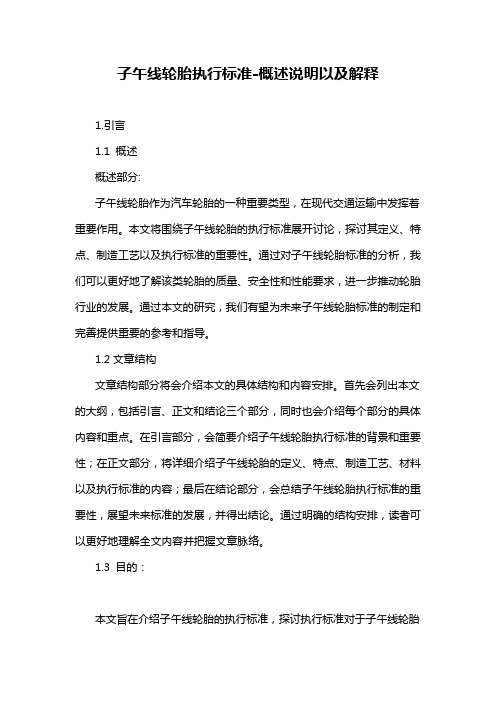
子午线轮胎执行标准-概述说明以及解释1.引言1.1 概述概述部分:子午线轮胎作为汽车轮胎的一种重要类型,在现代交通运输中发挥着重要作用。
本文将围绕子午线轮胎的执行标准展开讨论,探讨其定义、特点、制造工艺以及执行标准的重要性。
通过对子午线轮胎标准的分析,我们可以更好地了解该类轮胎的质量、安全性和性能要求,进一步推动轮胎行业的发展。
通过本文的研究,我们有望为未来子午线轮胎标准的制定和完善提供重要的参考和指导。
1.2文章结构文章结构部分将会介绍本文的具体结构和内容安排。
首先会列出本文的大纲,包括引言、正文和结论三个部分,同时也会介绍每个部分的具体内容和重点。
在引言部分,会简要介绍子午线轮胎执行标准的背景和重要性;在正文部分,将详细介绍子午线轮胎的定义、特点、制造工艺、材料以及执行标准的内容;最后在结论部分,会总结子午线轮胎执行标准的重要性,展望未来标准的发展,并得出结论。
通过明确的结构安排,读者可以更好地理解全文内容并把握文章脉络。
1.3 目的:本文旨在介绍子午线轮胎的执行标准,探讨执行标准对于子午线轮胎行业的重要意义和作用。
通过对子午线轮胎执行标准的分析和解读,我们可以更深入地了解子午线轮胎的制造工艺、材料和质量标准,进一步推动轮胎行业的发展和规范化。
同时,本文也旨在引起轮胎生产企业和相关部门的重视,促使他们更加严格地遵守子午线轮胎的执行标准,提高轮胎产品的质量和安全性,保障消费者的权益和安全。
最终,通过对子午线轮胎执行标准的深入研究和探讨,促进轮胎行业的健康发展,推动我国轮胎行业向着更加规范和标准化的方向迈进。
2.正文2.1 子午线轮胎的定义和特点子午线轮胎是一种采用子午线布置胎带的轮胎,通常是钢丝帘子午线轮胎。
子午线轮胎相比于斜交轮胎具有以下特点:1. 结构稳定:子午线轮胎采用钢丝帘和胎带的结构,使得轮胎更加稳定,提高了行驶安全性。
2. 耐磨耐用:子午线轮胎使用高强度的材料,耐磨性和耐用性都比较优秀,可以减少更换次数,降低使用成本。
子午线轮胎的质量检验
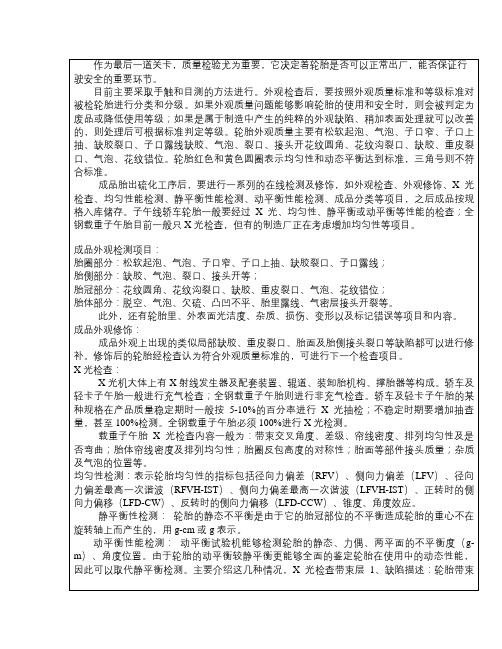
作为最后一道关卡,质量检验尤为重要,它决定着轮胎是否可以正常出厂,能否保证行驶安全的重要环节。
目前主要采取手触和目测的方法进行。
外观检查后,要按照外观质量标准和等级标准对被检轮胎进行分类和分级。
如果外观质量问题能够影响轮胎的使用和安全时,则会被判定为废品或降低使用等级;如果是属于制造中产生的纯粹的外观缺陷、稍加表面处理就可以改善的,则处理后可根据标准判定等级。
轮胎外观质量主要有松软起泡、气泡、子口窄、子口上抽、缺胶裂口、子口露线缺胶、气泡、裂口、接头开花纹圆角、花纹沟裂口、缺胶、重皮裂口、气泡、花纹错位。
轮胎红色和黄色圆圈表示均匀性和动态平衡达到标准,三角号则不符合标准。
成品胎出硫化工序后,要进行一系列的在线检测及修饰,如外观检查、外观修饰、X光检查、均匀性能检测、静平衡性能检测、动平衡性能检测、成品分类等项目,之后成品按规格入库储存。
子午线轿车轮胎一般要经过X光、均匀性、静平衡或动平衡等性能的检查;全钢载重子午胎目前一般只X光检查,但有的制造厂正在考虑增加均匀性等项目。
成品外观检测项目:胎圈部分:松软起泡、气泡、子口窄、子口上抽、缺胶裂口、子口露线;胎侧部分:缺胶、气泡、裂口、接头开等;胎冠部分:花纹圆角、花纹沟裂口、缺胶、重皮裂口、气泡、花纹错位;胎体部分:脱空、气泡、欠硫、凸凹不平、胎里露线、气密层接头开裂等。
此外,还有轮胎里、外表面光洁度、杂质、损伤、变形以及标记错误等项目和内容。
成品外观修饰:成品外观上出现的类似局部缺胶、重皮裂口、胎面及胎侧接头裂口等缺陷都可以进行修补。
修饰后的轮胎经检查认为符合外观质量标准的,可进行下一个检查项目。
X光检查:X光机大体上有X射线发生器及配套装置、辊道、装卸胎机构、撑胎器等构成。
轿车及轻卡子午胎一般进行充气检查;全钢载重子午胎则进行非充气检查。
轿车及轻卡子午胎的某种规格在产品质量稳定期时一般按5-10%的百分率进行X光抽检;不稳定时期要增加抽查量,甚至100%检测。
成品胎检测方法及其检测设备

4 不圆度检测 • 径向不圆度:充气轮胎运转试验时发现径向不均匀, 充气压力:7巴,标准轮辋 • 一次谐波(mm),方向轮条形花纹≤1.5,驱动轮块形 花纹≤2.2; • 峰值之间(mm) (仅适于非一次谐波测量),方向轮条 形花纹≤2.0,驱动轮块形花纹≤2.5;如果统计质量发 现一级质量合格率低于95%,则需对产品做100%的 该项检测。 • 侧向不园度:一侧或两侧胎侧和/或胎肩部位不平整, 充气压力:7巴,标准轮辋 • 不平之处间距60mm,≤0.8mm, • 如果统计质量发现一级质量合格率低于95%,则需 对产品做100%的该项检测。
3.2.2侧向力波动LFV:受载轮胎在固定负荷半径和 恒定速度下,每转一周自身反复出现的侧向力的 波动值。 侧向力偏差侧向力偏差主要反映了轮胎的摆动性。 如果侧向力偏差过大,就会使汽车在行驶中摇摇 摆摆,方向盘把握不住,影响其操纵性能。 • 主要影响因素:有胎侧厚度不均、两条胎侧重量不一、胎侧接
头过大、冠部材料上偏等
3.2.7轮胎专用均匀性试验设备
3.2.7.1、轮胎专用均匀性试验设备应该包括: • a、主轴,装有可调宽度轮辋,轮胎可简便地安装 在该轮辋上; • b、试验转鼓,其轴与主轴平行; • c、给轮胎加负荷的装置,该装置在试验过程中能 使轮胎与转鼓间的轴距保持恒定; • d、当轮胎和转鼓以规定的速度旋转时,有测量径 向力和侧向力的装置。
1.3.4 轮胎花纹沟深度 • 用游标卡尺(或专用量具)测量。测量时,应 避开胎面磨耗标志。游标卡尺(或专用量具) 应保持与花纹沟底部相互垂直。 • 纵向花纹轮胎,在轮胎圆周四等分处的四点上 测量靠近胎冠中心线的花纹沟深度。 • 横向和越野花纹轮胎,在胎肩到胎冠中心线间 1/2处,测量轮胎圆周四等分处四点上的花纹沟 深度。
工程子午线轮胎用钢帘线标准

工程子午线轮胎用钢帘线标准
一、引言
二、钢帘线的选材
钢帘线是由高强度钢丝制成的,用于增强轮胎的结构强度和稳定性。
为了确保工程子午线轮胎的质量,钢帘线的选材需要符合以下要求:
1.强度要求:钢帘线必须具有足够的强度来承受工程载荷,其强度水平应根据轮胎的设计要求来确定。
2.防锈性能:钢帘线需要具备良好的防锈性能,以确保在潮湿环境下轮胎结构不受损。
3.耐热性能:钢帘线在工作过程中需要承受较高的温度,因此需要具备良好的耐热性能,以确保轮胎不会出现热疲劳断裂等问题。
三、钢帘线的结构要求
1.表面形态:钢帘线的表面应平整、光滑,不得出现毛刺、裂纹等缺陷。
2.支撑性:钢帘线需要具备足够的支撑性能,以确保其在轮胎结构中的定位和固定。
3.弯曲性能:钢帘线在轮胎结构中需要经历较大的弯曲变形,因此需要具备良好的弯曲性能,以确保轮胎变形后能够回复到初始状态。
4.接头强度:钢帘线的接头强度需要满足相关标准要求,确保接头处不会因为强度不足而断裂。
四、钢帘线的质量控制
1.检验标准:钢帘线的质量控制需要根据相关国家和行业标准进行,包括强度、外观、尺寸等方面的检验。
2.抽样检验:工厂应该对供应的钢帘线进行抽样检验,确保其质量符合标准要求。
3.记录和追溯:每批钢帘线应该记录其生产厂家、批次等信息,以方便质量问题的溯源和追踪。
五、结论
通过对工程子午线轮胎用钢帘线的标准制定,可以保证钢帘线的质量和性能,从而确保轮胎的质量和使用寿命。
钢帘线的选材、结构要求和质量控制都需要严格执行相关的标准,以确保轮胎能够承受重载工作环境下的挑战。
同时,对钢帘线的检验、记录和追溯也是工厂必须执行的质量管理措施。
子午线轮胎用原材料性能要求及成品检测

子午线轮胎用原材料性能要求及成品检测目录1 对原材料质量首要的要求2 子午线轮胎用天然橡胶3 子午线轮胎用合成橡胶4 子午线轮胎半成品部件的性能要求5 子午线轮胎的成品检测1 对原材料质量首要的要求子午线轮胎的生产,与斜交轮胎相比,除要求生产厂的装备、工艺控制、生产管理和测试水平要有较大提高外,对所用原材料品种、质量控制和应用技术也提出了更为严格的要求。
使用性能稳定、均匀一致的高质量原材料,是生产高质量子午线轮胎的重要保证条件之一。
2 子午线轮胎用天然橡胶2.1总的要求及包装(1) 胶块应无木材、金属、纤维、石料等之类的外来物。
(2) 橡胶必须基本上无模压,但表面上的干燥模痕不受此限。
橡胶中离散的斑点虽无限制,但不容许有“原始的”(未干燥)橡胶。
(3) 颜色等级鉴别(4) 每一块胶用0.4 cm厚的聚乙烯塑料布包装。
每块胶周围放白色的聚乙烯塑料布条,用红色字母写上等级号。
包装好的胶块放在适合的托架上,每层用0.08/0.10mm厚的红色聚乙烯塑料布隔开。
注:在某些使用开炼机塑炼的地方,胶块需要用0.08/0.10mm厚的聚乙烯塑料布包装,以便卸袋,在某些情况下,如果适合,也可以要求用滑石粉处理胶块。
(5) 每一胶块重——33.3 kg(6) 胶块规格——680mmX 340mmX 150/180mm(7) 标准托架规格——1425mmX1100mm(8) 收到的橡胶必须无由于非橡胶组合分(例如篦麻油)腐烂造成的有害气味。
*聚乙烯要求符合下列技术条件:熔点105℃以下,比重0.92和溶解指数最小2.0。
2.2标准橡胶的规格子午线轮胎最常用的天然橡胶是标准橡胶TSR 10和TSR 20。
天然橡胶由于综合性能良好,可以单独使用,制作各种橡胶制品,也可与其他合成橡胶并用,以改进其他橡胶的性能,如成型粘性,拉伸强度,撕裂强度等,从而提高橡胶制品的全面性能。
天然橡胶生胶强度和自粘性好,胎胚形状易保持。
轮胎越大,天然橡胶比例越高。
卡客车子午线轮胎工艺100条
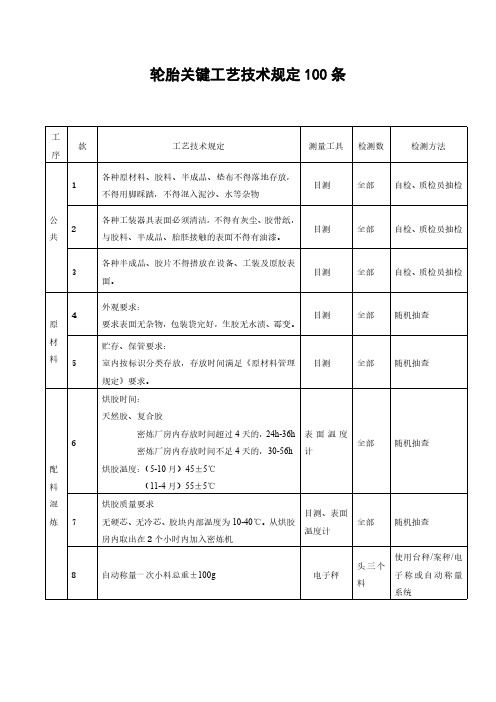
轮胎关键工艺技术规定100条工序款工艺技术规定测量工具检测数检测方法公共1各种原材料、胶料、半成品、垫布不得落地存放,不得用脚踩踏,不得混入泥沙、水等杂物目测全部自检、质检员抽检2各种工装器具表面必须清洁,不得有灰尘、胶带纸,与胶料、半成品、胎胚接触的表面不得有油漆。
目测全部自检、质检员抽检3各种半成品、胶片不得搭放在设备、工装及原胶表面。
目测全部自检、质检员抽检原材料4外观要求:要求表面无杂物,包装袋完好,生胶无水渍、霉变。
目测全部随机抽查5贮存、保管要求:室内按标识分类存放,存放时间满足《原材料管理规定》要求。
目测全部随机抽查配料混炼6烘胶时间:天然胶、复合胶密炼厂房内存放时间超过4天的,24h-36h密炼厂房内存放时间不足4天的,30-56h烘胶温度:(5-10月)45±5℃(11-4月)55±5℃表面温度计全部随机抽查7烘胶质量要求无硬芯、无冷芯、胶块内部温度为10-40℃。
从烘胶房内取出在2个小时内加入密炼机目测、表面温度计全部随机抽查8自动称量一次小料总重±100g电子秤头三个料使用台秤/案秤/电子称或自动称量系统9母胶小料总重:±100g硫磺促进剂总量称量公差:0-1kg:±10g1-4kg:±20g>4kg±30g配合剂总量称量公差0-2kg±20g2-6kg:±40g>6kg±50g电子秤头三个料使用台秤/案秤/电子称或自动称量系统10母炼胶小料停放时间≤7天终炼胶小料停放时间≤3天间甲树脂、钴盐≤3天(避光、低温)记录全部自检、质检员抽查11炭黑总重公差±0.20kg白炭黑总重公差±0.20kg电子称各三个料使用台秤/案秤/电子称或自动称量系统12生胶用量公差±0.2kg母胶用量公差±0.2kg电子称各三个料使用台秤/案秤/电子称或自动称量系统13油料用量公差±0.15kg油罐温度:85±15℃,油管、油料秤保持在50-90℃电子称各三个料使用台秤/案秤/电子称或自动称量系统14密炼机母胶混炼压力0.50±0.05Mpa终炼胶混炼压力0.40±0.05MPa压力表一台随机抽查15温控侧壁:30±5℃下顶栓:30±5℃转子:35±5℃机台显示随机抽查16混炼胶重量差:按配方总重每个料公差±1.5%磅秤随机抽查17母炼胶排胶温度K405≤130℃其余胶种≤160℃;母炼时进胶温度为135℃终炼胶排胶温度:普通硫磺≤105℃不溶性硫磺≤95℃表面温度计每班三个料终炼胶在开炼机上包辊后,打卷测胶卷内温度,探针插三次,取最高值18混炼胶收取温度:母胶≤45℃,终炼胶≤40℃点温计首末件随机抽查19混炼胶存放温度5℃-45℃表面温度计三个料随机抽查(从每架胶料的第二层以下胶片中部测量20母胶停放时间4h-1个月胶浆母胶4h-3个月终炼胶停放时间8h-15天其中带束层胶、胎体胶为8h-7天钢圈挂胶8h-3个月胶浆终炼胶8h-2个月全部随机抽查21胶片表面隔离剂均匀,无堆积和未干现象目测全部随机抽查22胶片打字必须有班次、日期、机台编号、胶料代号等内容。
成品外观检测
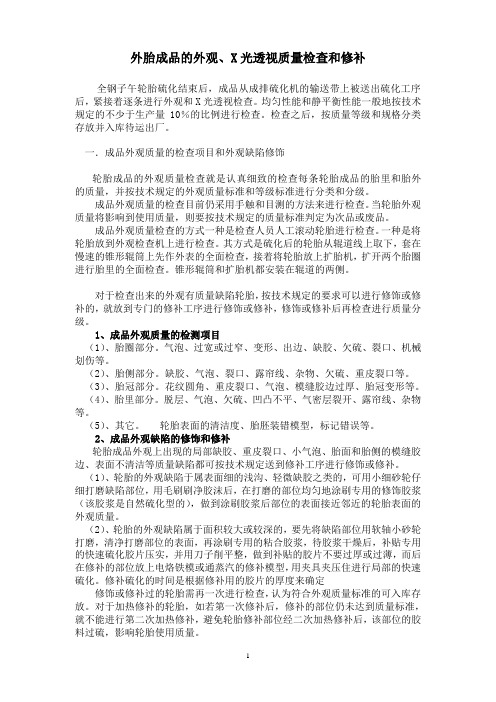
外胎成品的外观、X光透视质量检查和修补全钢子午轮胎硫化结束后,成品从成排硫化机的输送带上被送出硫化工序后,紧接着逐条进行外观和X光透视检查。
均匀性能和静平衡性能一般地按技术规定的不少于生产量10%的比例进行检查。
检查之后,按质量等级和规格分类存放并入库待运出厂。
一.成品外观质量的检查项目和外观缺陷修饰轮胎成品的外观质量检查就是认真细致的检查每条轮胎成品的胎里和胎外的质量,并按技术规定的外观质量标准和等级标准进行分类和分级。
成品外观质量的检查目前仍采用手触和目测的方法来进行检查。
当轮胎外观质量将影响到使用质量,则要按技术规定的质量标准判定为次品或废品。
成品外观质量检查的方式一种是检查人员人工滚动轮胎进行检查。
一种是将轮胎放到外观检查机上进行检查。
其方式是硫化后的轮胎从辊道线上取下,套在慢速的锥形辊筒上先作外表的全面检查,接着将轮胎放上扩胎机,扩开两个胎圈进行胎里的全面检查。
锥形辊筒和扩胎机都安装在辊道的两侧。
对于检查出来的外观有质量缺陷轮胎,按技术规定的要求可以进行修饰或修补的,就放到专门的修补工序进行修饰或修补,修饰或修补后再检查进行质量分级。
1、成品外观质量的检测项目(1)、胎圈部分。
气泡、过宽或过窄、变形、出边、缺胶、欠硫、裂口、机械划伤等。
(2)、胎侧部分。
缺胶、气泡、裂口、露帘线、杂物、欠硫、重皮裂口等。
(3)、胎冠部分。
花纹圆角、重皮裂口、气泡、模缝胶边过厚、胎冠变形等。
(4)、胎里部分。
脱层、气泡、欠硫、凹凸不平、气密层裂开、露帘线、杂物等。
(5)、其它。
轮胎表面的清洁度、胎胚装错模型,标记错误等。
2、成品外观缺陷的修饰和修补轮胎成品外观上出现的局部缺胶、重皮裂口、小气泡、胎面和胎侧的模缝胶边、表面不清洁等质量缺陷都可按技术规定送到修补工序进行修饰或修补。
(1)、轮胎的外观缺陷于属表面细的浅沟、轻微缺胶之类的,可用小细砂轮仔细打磨缺陷部位,用毛刷刷净胶沫后,在打磨的部位均匀地涂刷专用的修饰胶浆(该胶浆是自然硫化型的),做到涂刷胶浆后部位的表面接近邻近的轮胎表面的外观质量。
全钢丝子午线轮胎胎圈成型作业要点
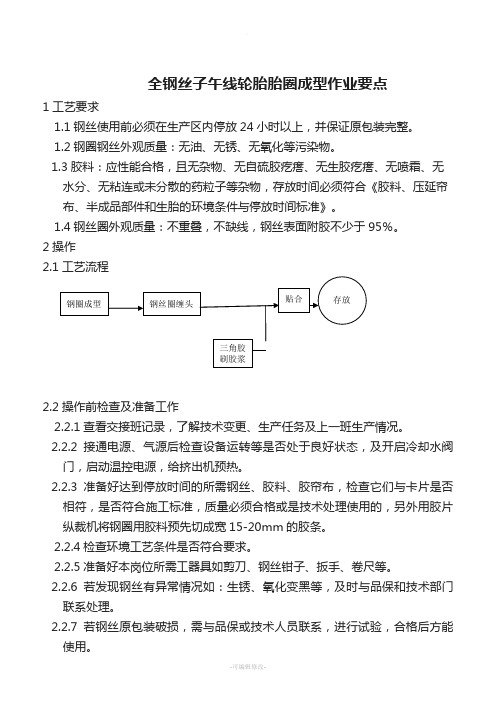
全钢丝子午线轮胎胎圈成型作业要点1工艺要求1.1钢丝使用前必须在生产区内停放24小时以上,并保证原包装完整。
1.2钢圈钢丝外观质量:无油、无锈、无氧化等污染物。
1.3胶料:应性能合格,且无杂物、无自硫胶疙瘩、无生胶疙瘩、无喷霜、无水分、无粘连或未分散的药粒子等杂物,存放时间必须符合《胶料、压延帘布、半成品部件和生胎的环境条件与停放时间标准》。
1.4钢丝圈外观质量:不重叠,不缺线,钢丝表面附胶不少于95%。
2操作2.1工艺流程2.2操作前检查及准备工作2.2.1查看交接班记录,了解技术变更、生产任务及上一班生产情况。
2.2.2接通电源、气源后检查设备运转等是否处于良好状态,及开启冷却水阀门,启动温控电源,给挤出机预热。
2.2.3准备好达到停放时间的所需钢丝、胶料、胶帘布,检查它们与卡片是否相符,是否符合施工标准,质量必须合格或是技术处理使用的,另外用胶片纵裁机将钢圈用胶料预先切成宽15-20mm的胶条。
2.2.4检查环境工艺条件是否符合要求。
2.2.5准备好本岗位所需工器具如剪刀、钢丝钳子、扳手、卷尺等。
2.2.6若发现钢丝有异常情况如:生锈、氧化变黑等,及时与品保和技术部门联系处理。
2.2.7若钢丝原包装破损,需与品保或技术人员联系,进行试验,合格后方能使用。
2.3生产工艺过程及注意和要求:2.4结束生产2.4.1清除机头胶料,关机。
2.4.2清理操作区域和设备,收拾好工器具。
2.4.3填写交接班记录3安全注意事项3.1开机前检查急停开关是否灵敏。
4.常见故障及排除常见质量缺陷一般处理方法。
子午工程胎 成品胎检测标准
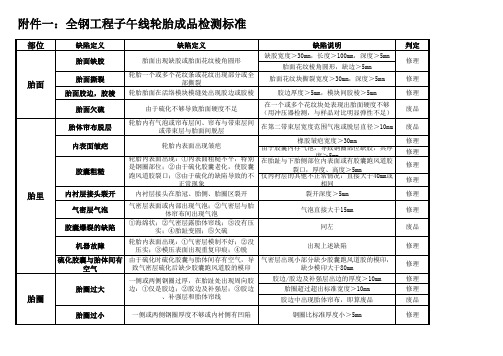
缺陷说明
缺胶宽度>30mm,长度>100mm,深度>5mm
判定
修理
胎面
胎面胶边, 胎面胶边,胶棱 胎面欠硫 胎体帘布脱层 内表面皱疤
胶囊粗糙
内衬层接头裂开
胎里
气密层气泡 胶囊爆裂的缺陷 机器故障
出现上述缺陷 气密层出现小部分缺少胶囊跑风道胶的模印, 缺少模印大于80mm 胶边/胶边及补强层出边的厚度>10mm
杂质— 杂质—其他
杂质
模具不洁 杂质— 杂质—喷涂
修理 修理
杂质— 杂质—防粘剂
修理
备注: 其中有一项判为废品, 备注:1.其中有一项判为废品,即判为刻品 2.其中有一项判为修品(无废品分项), ),即判为修品 2.其中有一项判为修品(无废品分项),即判为修品 3.所有分项都为合格的, 3.所有分项都为合格的,即判为合格品
胎侧
胎侧欠硫 胎侧被传送带损坏 胎肩缺胶 胎肩部打褶
废品 修理 修理 修理 修理 修理
胎肩
胎肩气泡
胎肩胶边或胶棱 杂质—胶边 杂质—
一侧或两侧胎肩在对应于模缝处出现胶边或所有胎侧模板与活络模块间的胶边、胶棱厚度>5mm 修理 胶棱 外表面:留下印痕深度>5mm 轮胎内表面、外表面出现硫化上一条胎时留 修理 在模具或胶囊上的胶边 内部:留下印痕深度>5mm 外表面:留下印痕深度>3mm 轮胎内表面、外表面、在胎内各部件间出现 杂质 内部:留下印痕深度>2mm 轮胎外表面任一处由于模具表面不洁出现印记 轮胎出现:①喷涂液流动而产生的印痕;② 喷涂过多出现的浅坑 内部:留下印痕深度>5mm 轮胎在胎侧/胎面部位出现:①甘油斑点;② 周向裂口;③胶纹 甘油斑:胎面部位周向裂口和重皮,深度> 3mm,长度>1/8周长 模具凹痕深度>3mm,直径>10mm 外表面:留下印痕深度>3mm 修理
工程子午线轮胎用钢帘线标准

工程子午线轮胎用钢帘线标准
规格标准是工程子午线轮胎用钢帘线标准的核心内容之一,它包括钢
帘线的构造参数、线径公差、花纹规格和结构尺寸等。
其中,钢帘线的构
造参数包括帘线层数和每层帘线的股数。
线径公差指的是钢帘线线径允许
的变异范围。
花纹规格是指钢帘线表面的花纹形状和线型。
结构尺寸则是
指钢帘线的宽度、厚度和长度等。
物理性能要求是工程子午线轮胎用钢帘线标准的另一个重要内容,它
包括帘线强度、应变硬化系数、拉伸弹性模量和断裂延伸率等性能指标。
帘线强度是指钢帘线材料在拉伸过程中所能承受的最大力。
应变硬化系数
是指钢帘线在受到应力后硬度的变化情况。
拉伸弹性模量是指钢帘线在拉
伸过程中的弹性变形能力。
断裂延伸率是指钢帘线断裂前的延伸程度。
试验方法是工程子午线轮胎用钢帘线标准的另一个重要内容,它用于
评估钢帘线的物理性能指标是否符合要求。
试验方法包括拉伸试验、硫化
性能试验、撕裂强度试验和疲劳性能试验等。
其中,拉伸试验是评估钢帘
线强度和延展性的重要指标,硫化性能试验用于评估钢帘线与胶料的粘接
性能,撕裂强度试验用于评估钢帘线的抗撕裂能力,疲劳性能试验则用于
评估钢帘线的耐久性能。
总之,工程子午线轮胎用钢帘线标准是保证产品质量和安全性的基础。
通过规定规格标准、物理性能要求和试验方法,可以确保钢帘线在使用过
程中具有良好的承载能力、抗冲击能力和耐久性,从而提高轮胎的使用寿
命和安全性能。
因此,制定科学合理的工程子午线轮胎用钢帘线标准对于
轮胎行业的发展具有重要意义。
子午线轮胎标准
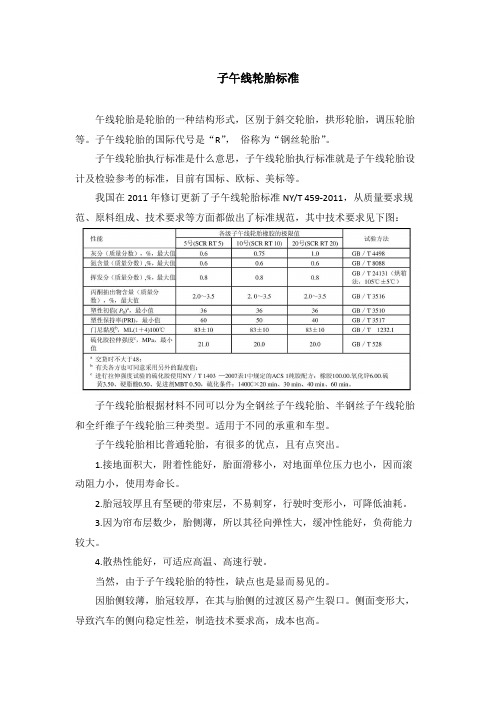
子午线轮胎标准
午线轮胎是轮胎的一种结构形式,区别于斜交轮胎,拱形轮胎,调压轮胎等。
子午线轮胎的国际代号是“R”,俗称为“钢丝轮胎”。
子午线轮胎执行标准是什么意思,子午线轮胎执行标准就是子午线轮胎设计及检验参考的标准,目前有国标、欧标、美标等。
我国在2011年修订更新了子午线轮胎标准NY/T 459-2011,从质量要求规范、原料组成、技术要求等方面都做出了标准规范,其中技术要求见下图:
子午线轮胎根据材料不同可以分为全钢丝子午线轮胎、半钢丝子午线轮胎和全纤维子午线轮胎三种类型。
适用于不同的承重和车型。
子午线轮胎相比普通轮胎,有很多的优点,且有点突出。
1.接地面积大,附着性能好,胎面滑移小,对地面单位压力也小,因而滚动阻力小,使用寿命长。
2.胎冠较厚且有坚硬的带束层,不易刺穿,行驶时变形小,可降低油耗。
3.因为帘布层数少,胎侧薄,所以其径向弹性大,缓冲性能好,负荷能力较大。
4.散热性能好,可适应高温、高速行驶。
当然,由于子午线轮胎的特性,缺点也是显而易见的。
因胎侧较薄,胎冠较厚,在其与胎侧的过渡区易产生裂口。
侧面变形大,导致汽车的侧向稳定性差,制造技术要求高,成本也高。
全钢丝子午线轮胎标准
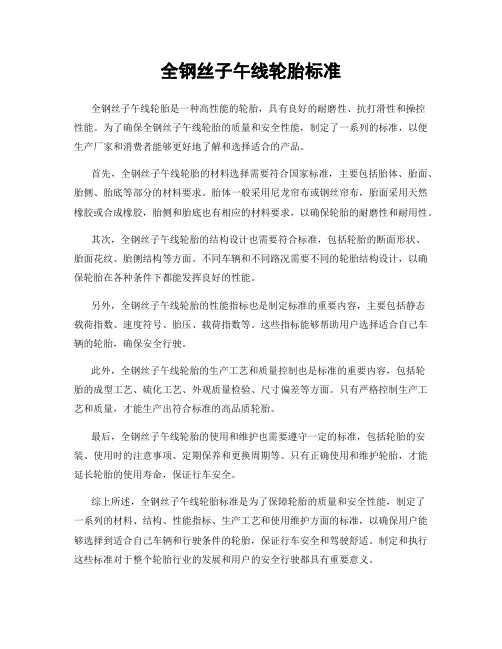
全钢丝子午线轮胎标准全钢丝子午线轮胎是一种高性能的轮胎,具有良好的耐磨性、抗打滑性和操控性能。
为了确保全钢丝子午线轮胎的质量和安全性能,制定了一系列的标准,以便生产厂家和消费者能够更好地了解和选择适合的产品。
首先,全钢丝子午线轮胎的材料选择需要符合国家标准,主要包括胎体、胎面、胎侧、胎底等部分的材料要求。
胎体一般采用尼龙帘布或钢丝帘布,胎面采用天然橡胶或合成橡胶,胎侧和胎底也有相应的材料要求,以确保轮胎的耐磨性和耐用性。
其次,全钢丝子午线轮胎的结构设计也需要符合标准,包括轮胎的断面形状、胎面花纹、胎侧结构等方面。
不同车辆和不同路况需要不同的轮胎结构设计,以确保轮胎在各种条件下都能发挥良好的性能。
另外,全钢丝子午线轮胎的性能指标也是制定标准的重要内容,主要包括静态载荷指数、速度符号、胎压、载荷指数等。
这些指标能够帮助用户选择适合自己车辆的轮胎,确保安全行驶。
此外,全钢丝子午线轮胎的生产工艺和质量控制也是标准的重要内容,包括轮胎的成型工艺、硫化工艺、外观质量检验、尺寸偏差等方面。
只有严格控制生产工艺和质量,才能生产出符合标准的高品质轮胎。
最后,全钢丝子午线轮胎的使用和维护也需要遵守一定的标准,包括轮胎的安装、使用时的注意事项、定期保养和更换周期等。
只有正确使用和维护轮胎,才能延长轮胎的使用寿命,保证行车安全。
综上所述,全钢丝子午线轮胎标准是为了保障轮胎的质量和安全性能,制定了一系列的材料、结构、性能指标、生产工艺和使用维护方面的标准,以确保用户能够选择到适合自己车辆和行驶条件的轮胎,保证行车安全和驾驶舒适。
制定和执行这些标准对于整个轮胎行业的发展和用户的安全行驶都具有重要意义。
- 1、下载文档前请自行甄别文档内容的完整性,平台不提供额外的编辑、内容补充、找答案等附加服务。
- 2、"仅部分预览"的文档,不可在线预览部分如存在完整性等问题,可反馈申请退款(可完整预览的文档不适用该条件!)。
- 3、如文档侵犯您的权益,请联系客服反馈,我们会尽快为您处理(人工客服工作时间:9:00-18:30)。
3.6 高顺式异戊二烯橡胶(IR)
替代NR,混炼胶门尼值低,加工性能好,化学成分与天然胶 相同,生胶强力低。高粘度的粘合配方(子口加强层)采用此胶 有效改进加工性能。由于异戊橡胶纯度高,灰分和凝胶含量较 低,因而质地均匀。异戊橡胶容易塑炼,压出的半成品收缩小, 硫化时胶料流动性好。用于轮胎钢丝子口包布胶和胎圈钢丝挂 胶。
0.8
0.8
0.8 0.8 0.8
0.8
0.8
塑性初值(P0), 最小值
-
30
30
30
30
30
-
塑性保持率(PRI), 最小值
60
60
60
60
50
40
50
拉维邦颜色指数, 最大值
-
6
---
-
-
门尼黏度, ML(1+4)100℃
60±5 ②
-
---
-
③
20CV 红
0.20
1.0 0.6 0.8 - 40 - ③
3.5 卤化丁基橡胶(CIIR或BIIR)
用于轮胎的内衬层(有内胎)或气密层(无内胎)。 轮胎工业中采用的卤化丁基橡胶主要是氯化丁基橡胶和溴化丁基橡胶, 它们均具有空气透过性低的特点,广泛应用于轮胎的气密层配方中,随 卤化丁基橡胶用量的增加,轮胎的气密性能越好。对于无内胎轮胎采用 卤化丁基橡胶能起到保压和保护胎体的作用;对有内胎轮胎主要起保护 胎体免受空气中的氧和水份的侵蚀作用。
子午线轮胎用原材料 性能要求及成品检测
目录
1 对原材料质量首要的要求 2 子午线轮胎用天然橡胶 3 子午线轮胎用合成橡胶 4 子午线轮胎半成品部件的性能要求 5 子午线轮胎的成品检测
1 对原材料质量首要的要求
子午线轮胎的生产,与斜交轮胎相比,除要求生产厂的装备、工艺控制、 生产管理和测试水平要有较大提高外,对所用原材料品种、质量控制和 应用技术也提出了更为严格的要求。 使用性能稳定、均匀一致的高质量原材料,是生产高质量子午线轮胎的 重要保证条件之一。 2 子午线轮胎用天然橡胶 2.1总的要求及包装
目前我国轮胎工业中采用的丁苯橡胶主要是乳聚丁苯橡胶ESBR 1500 和充油乳聚丁苯橡胶ESBR 1712。 由于充油后改善了加工性能,生胶强度高(相对于合成胶而言),且保持 原聚合物的物理机械性能,硫化胶滞后损失小,生热低,耐磨性好,有 好的牵引性能和抗湿滑性等。且充油后产量增大,成本降低。 乳聚丁苯橡胶具有较好的综合性能,它的物理机械性能、加工性能都接 近于天然橡胶,其中耐磨、耐热、耐老化、永久变形和硫化速度等特性 优于天然橡胶。
表 3 标准中国橡胶(SCR) 技术要求(GB/T 8081-1999)
各级橡胶的极限值
性能
恒黏胶 浅色胶 (SCR (SCR CV) L)
绿
绿
留在 45μ
筛上的杂质含量 0.05 0.05
/%(质量分数),最大值
塑性初值,最小值 —
30
塑性保持率,最小值 60
60
氮含量/%(质量分
数),最大值
0.6
GB/T 8658-1998 GB/T 1232.1-2000
GB/T 1232.1-2000(使用 ASTM IRB No.7)
表 5 丁苯橡胶 SBR 1712 技术指标 (优级品)
项
目
挥发分,%
指标 ≤0.60
试验方法 GB/T 6737-1997 热辊法
总灰分,%
≤0.50 GB/T 4498-1997 方法 A
0.6
挥发分含量/%(质量
分数),最大值
0.8
0.8
灰分含量/%(质量分
数),最大值
0.6
0.6
颜色指数,最大值 -
6
门尼黏度, ML(1+4)100℃
65±5①
-
5 号胶 10 号胶 (SCR (SCR
5) 10)
颜色标志
绿
褐
20 号胶 (SCR 20)
红
50 号胶 (SCR 50)
黄
0.05 0.10 0.20 0.50
表6 顺丁橡胶 BR 9000 技术要求(优级品)
性能项目 挥发分,%
指标 ≤0.50
试验方法 GB/T 6737 热辊法
总灰分,%
≤0.20 GB/T 4498 方法 A
生胶门尼粘度 ML(1+4)100℃ 45±4 混炼胶门尼粘度 ML(1+4)100℃ ≤65
GB 1232.1 GB 1232.1
留在45μm
筛网上的杂质/% (质量分数),最
0.05
0.05
0.05
0.05
0.10
0.20
0.10
大值
灰分/%(质量分 数),最大值
0.5
0.5
0.5
0.6 0.75 1.0
0.75
氮含量/%(质量分 数),最大值
0.6
0.6
0.6 0.6 0.6
0.6
0.6
挥发分含量/%(质 量分数),最大值
表1 TSR的级别
原材料
特征
控制黏度
全鲜胶乳
浅色橡胶,具有规定的颜色指数
无规定黏度或颜色
生胶片或凝固的混合 胶乳
无规定黏度或颜色
胶园凝胶和/或生胶 片
无规定黏度 控制黏度
级别 CV L WF
5
10或20 10CV或20CV
表2 TSR的技术要求(ISO 2000:2003)
性能 颜色标识
级 别① CV L WF 5 10 20 10CV 绿绿绿绿褐红 褐
GB/T 1232.1-2000 ASTM IRB No.7
丁苯橡胶是不饱和橡胶,其分子结构中双键含量比天然橡胶低,且因为 苯环的存在减少了双键的活性,所以与天然橡胶相比,丁苯橡胶硫化速 度较慢,胶料不易焦烧或过硫,有较好的耐热、耐氧、耐臭氧、耐日光 老化等性能。 丁苯橡胶分子链侧基中带有庞大的苯环,分子链的柔顺性差,内摩擦大, 因此,丁苯橡胶的弹性、强度、耐屈挠龟裂、耐撕裂、耐寒性等不如天 然橡胶。特别是制品在多次变形时生热较大,在加工过程中压延、压出 变形较大,较难加工,且胶料粘着性较差,贴合成型较困难,但与天然 橡胶相比,丁苯橡胶有较好的耐磨性和耐透气性。 丁苯橡胶的物理机械性能和工艺加工性能的不足之处,可以通过调整配 方和工艺条件,或与天然橡胶并用而得到改善。
3.7 低顺式聚丁二烯橡胶(LCBR )
代替高顺式聚丁二烯橡胶,用于子午线轮胎的耐磨胶条(胎圈护胶),工 艺性能好。 载重子午线轮胎的胎圈护胶,靠近轮辋,摩擦力大,要求有较好的形状 保持、耐磨、硬度高,胶料的门尼粘度一般都较高。以前采用高顺式BR, 以高炭黑、低操作油配合等手段来保证胶料的门尼粘度,但生产时胶料 的加工性能较差,门尼粘度易发生波动。而LCBR具有相对分子质量分 布较窄、胶料填充能力大、炭黑混入时间短等特点,尤其是在加工过程 中门尼粘度降低较小,非常适合于子午线轮胎胎圈护胶的性能要求,在
溶液聚合丁苯橡胶在国内一些轿车子午线轮胎厂已逐步使用,但用量与 国外相比仍较小。它的特点是使高速轮胎在保持较好抗湿滑性的同时具 有较低的滚动阻力,适应了近年来对轮胎的绿色环保要求。特别是充油 溶聚丁苯橡胶,在轿车子午线轮胎胎面橡胶的使用,可提高白炭黑的用 量以取代炭黑,大大降低了轮胎的滚动阻力,虽目前用量小,但前景十
检验方法
ISO 249
ISO 247 ISO 1656 ISO 248:1991 (烘箱法100℃±5
℃) ISO 2007 ISO 2930 ISO 4660 ISO 289-1
①制胶原料见表1。 ②有关各方商定的其他黏度值。 ③这些级别的黏度未被规定,因为其可能发生改变,例如,由于老化和加工。然而,该黏度在 生产端一般控制在65(+7,-5) 的范围,或有关方面商定的其他黏度值。
3 子午线轮胎用合成橡胶
3.1 总的说明和包装:
1)所供材料的包装应合理。 2)所供材料应洁净,同时无外杂质。 3)每包胶的重量不得超过制造厂规定重量±2%。 4)每块胶应用不分解的聚乙烯塑料薄膜打包,其塑料熔点≤115 ℃,比重≤0.925,厚度为0.05mm,当使用产品标号塑料条时,此聚 乙烯塑料必须具有与打包胶块用的材料相似的性能。 5)胶块和容器应清楚地标明内装聚合物品种和制造日期。 6)交货应在生产之日起的12天到8个月之间进行。 7)每次装运货应寄送“质量检验报告”。
2.3 标准橡胶的优点
与传统生产的烟片胶相比,标准橡胶(颗粒胶)的优点是 (1) 使用生胶理化性能分级,合理区分和判别天然橡胶的内在质 量; (2) 机械化程度高,生产周期短; (3) 颗粒胶的粒子小,大大增加了与片状胶相比的干燥面积,既 缩短周期又易控制质量; (4) 采用烧油或煤热风干燥,代替木材熏烟,既节约木材,也保 护了森林资源和生态环境。
表4
丁苯橡胶 SBR 1500 技术要求 (优级品)
项目 挥发分,%
指标 ≤0.60
灰分,% 有机酸,%
皂,% 结合苯乙烯,% 生胶门尼粘度 ML(1+4)100
℃
混炼胶门尼粘度 ML(1+4)100 ℃
≤0.50 5.00~7.25
≤0.50 22.5~24.5
47~57
≤88
试验方法
GB/T 6737-1997 热辊法 GB/T 4498-1997 A 法 GB/T 8657-2000 A 法
30
30
30
30
60
50
40
30
0.6
0.6
0.6
0.6
0.8
0.8
0.8
0.8
0.6
0.75
1.0
1.5
-
-
-
-
-