设计失效分析DFMEA经典案例剖析_1606126253
DFMEA失效模式分析报告-案例

DFMEA失效模式分析报告-案例1. 引言本文档旨在提供针对某一特定产品的DFMEA(设计失效模式及影响分析)报告。
该报告基于针对该产品的失效模式分析的结果,旨在识别和评估潜在的设计失效模式及其潜在影响。
2. 背景信息产品名称:(产品名称)产品型号:(产品型号)报告日期:(报告日期)3. 方法论在分析失效模式之前,我们采用以下方法进行了系统的DFMEA分析:1. 收集产品设计文档和相关技术资料;2. 召开团队会议,对产品进行全面的功能分析;3. 根据功能分析,确定可能存在的失效模式;4. 对每个失效模式进行评估,包括严重程度、频率和发现难度的评估;5. 提出各种可能的故障根本原因;6. 提出相应的纠正措施和预防措施,以减轻潜在的失效模式对产品造成的影响。
4. 失效模式分析及评估在DFMEA分析中,我们发现以下潜在的失效模式及其评估结果:4.1 失效模式1- 描述:(失效模式1的详细描述)- 严重程度:(对产品的影响程度评估,如高、中、低)- 频率:(失效模式发生的频率评估,如高、中、低)- 发现难度:(失效模式的可发现程度评估,如高、中、低)- 根本原因:(该失效模式发生的可能原因)4.1.1 纠正措施- 描述:(纠正该失效模式的措施)4.1.2 预防措施- 描述:(预防该失效模式的措施)4.2 失效模式2- 描述:(失效模式2的详细描述)- 严重程度:(对产品的影响程度评估,如高、中、低)- 频率:(失效模式发生的频率评估,如高、中、低)- 发现难度:(失效模式的可发现程度评估,如高、中、低)- 根本原因:(该失效模式发生的可能原因)4.2.1 纠正措施- 描述:(纠正该失效模式的措施)4.2.2 预防措施- 描述:(预防该失效模式的措施)......5. 结论本报告中,我们对产品的失效模式进行了深入的分析和评估。
通过识别各个失效模式并提出相应的纠正和预防措施,我们能够最大程度地减少潜在的设计失效,并提升产品的质量和可靠性。
设计失效分析DFMEA经典案例剖析

——六步搞定DFMEA表格
纲要 一:重大质量问题实例 二:DFMEA的重大作用 DFMEA的重大作用 三:DFMEA基本概念相关 DFMEA基本概念相关 四:DFMEA表格标准格式 DFMEA表格标准格式 五:DFMEA应用与表格制作实战 DFMEA应用与表格制作实战 六:趣例分享 七:豆浆机常见失效点分组讨论并作DFMEA练习 豆浆机常见失效点分组讨论并作DFMEA练习 分组讨论并作DFMEA
DFMEA •Design Failure Mode Effect Analysis: : 设计失效模式及后果分析 •失效模式 指设计(制造)过程无法达到预定或规 失效模式: 失效模式 指设计(制造) 定的要求所表现出的特征; 坏品、 定的要求所表现出的特征;如:坏品、不良设备状 况等; 况等 •后果 指失效模式对客户 包括下工序 所造成的影响 后果: 包括下工序)所造成的影响 后果 指失效模式对客户(包括下工序 所造成的影响;
•设计之前预先进行风险分析,确保设计水平。 设计之前预先进行风险分析,确保设计水平。
是正文内容部分,这里是正文 内容部分,这里是正文内容部分, 这里是正文内容部分,这 里是正文内容部分,这里是正 文内容部分,这里是正文内 容部分,这里是正文内:重大质量问题实例
一:重大质量问题实例
这里是正文内容部分, 这里是正文内容部分,这里 是正文内容部分,这里是正文 内容部分,这里是正文内容部分, 这里是正文内容部分,这 里是正文内容部分,这里是正 文内容部分,这里是正文内 容部分,这里是正文内 容部分,这里是正文
如果DFMEA得到有效应用与执行: 得到有效应用与执行: 如果 得到有效应用与执行
三:DFMEA基本概念相关 基本概念相关
汽车制动系统设计DFMEA案例分析
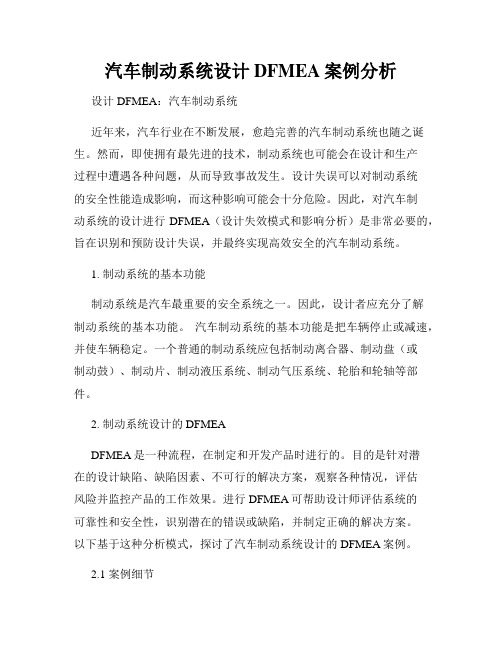
汽车制动系统设计DFMEA案例分析设计DFMEA:汽车制动系统近年来,汽车行业在不断发展,愈趋完善的汽车制动系统也随之诞生。
然而,即使拥有最先进的技术,制动系统也可能会在设计和生产过程中遭遇各种问题,从而导致事故发生。
设计失误可以对制动系统的安全性能造成影响,而这种影响可能会十分危险。
因此,对汽车制动系统的设计进行DFMEA(设计失效模式和影响分析)是非常必要的,旨在识别和预防设计失误,并最终实现高效安全的汽车制动系统。
1. 制动系统的基本功能制动系统是汽车最重要的安全系统之一。
因此,设计者应充分了解制动系统的基本功能。
汽车制动系统的基本功能是把车辆停止或减速,并使车辆稳定。
一个普通的制动系统应包括制动离合器、制动盘(或制动鼓)、制动片、制动液压系统、制动气压系统、轮胎和轮轴等部件。
2. 制动系统设计的DFMEADFMEA是一种流程,在制定和开发产品时进行的。
目的是针对潜在的设计缺陷、缺陷因素、不可行的解决方案,观察各种情况,评估风险并监控产品的工作效果。
进行DFMEA可帮助设计师评估系统的可靠性和安全性,识别潜在的错误或缺陷,并制定正确的解决方案。
以下基于这种分析模式,探讨了汽车制动系统设计的DFMEA案例。
2.1 案例细节应用DFMEA对新型汽车制动系统进行评估。
制动系统的开发人员已确定了一系列的模式,包括安装端口、材料、制动系统的阀门、抽吸和压力泵、筒和活塞,以及几个不同的操作组件。
同时,汽车制动系统设计还考虑了传动控制、电子系统和机械系统等方面,以确保高效安全的设计。
2.2 评估模式评估模式是DFMEA的重要组成部分。
为了进行制动系统的评估,需要确定系统中的各个子部件,并评估每个子系统的失效模式。
失效模式是指系统中可能发生的错误模式或缺陷,例如材料错误,设备质量问题或人员操作不当等。
每个失效模式都伴随着一个或多个潜在的后果,因此,准确评估失效模式是必要的。
2.3 评估影响对于每种失效模式,需要评估其潜在的影响。
设计失效分析DFMEA经典案例剖析通用课件
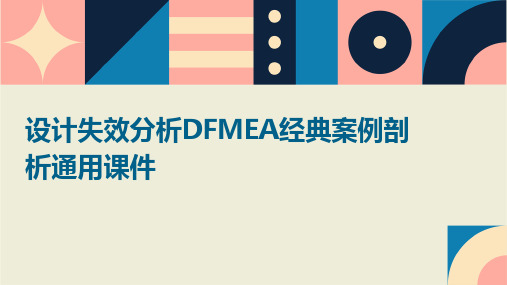
将DFMEA的应用范围从汽车行业 扩展到其他制造业领域,为更多产 品的可靠性设计和改进提供支持。
引入新技术
随着技术的不断发展,DFMEA 可引入新的工具和方法,提高 分析的效率和准确性。
加强培训与意识提升
通过培训和宣传活动,提高企业员 工对DFMEA的认识和应用能力, 促进其在产品设计和管理中的广泛 应用。
01
确定产品或系统的研究范围,明确分析对象和目标 。
02
考虑产品或系统的生命周期,包括研发、生产、使 用和维修等阶段。
03
确定研究的重点,如关键功能、高风险区域或特定 设计领域。
构建功能、性能、可靠性和安全性清单
01
列出产品或系统的所有功能和性能要求。
02 分析各功能和性能对可靠性、安全性的需求和影 响。
评估失效模式对设备操作准确性和安全性的影响程度。
改进措施
提出针对失效模式的改进措施,如优化按钮设计、改善 显示效果等。
04
案例剖析与启示
案例一剖析与启示
案例名称
某汽车刹车系统设计失效
案例描述
某汽车在行驶过程中突然出现刹车失灵,导致严重事故。经过调查发 现,设计阶段未充分考虑高温环境下刹车油膨胀问题。
提出改进措施和建议,降 低设计失效风险,提高产 品或系统的可靠性、安全 性。
03
经典案例选择与介绍
案例选择标准
案例的典型性
选择具有代表性的案例,能够体现DFMEA分析的基本原则和方 法。
案例的实用性
案例应具有实际应用价值,能够帮助企业解决实际问题。
案例的完整性
案例应包含完整的DFMEA分析过程,包括功能定义、功能分析 、失效模式分析、失效影响分析和改进措施等。
汽车空调系统设计DFMEA案例分析

汽车空调系统设计DFMEA案例分析DFMEA简介DFMEA(Design Failure Mode and Effects Analysis,设计失效模式与影响分析)是一种常用的质量管理工具,用于在产品设计阶段识别并解决潜在的失效模式及其影响。
本文将以汽车空调系统设计为案例,探讨如何应用DFMEA来提高汽车空调系统设计的安全性和可靠性。
一、设计失效模式与影响分析(DFMEA)DFMEA是一种以系统化和有序方式对产品设计进行评估和分析的方法。
它的主要目的是识别可能的失效模式、评估其严重程度以及制定相应的纠正和预防措施。
下面我们将根据DFMEA的步骤,对汽车空调系统进行案例分析。
1. 制定DFMEA团队与范围首先,确定参与DFMEA的团队成员,包括汽车空调系统设计的工程师、质量控制专家、测试工程师等。
明确DFMEA的范围和目标,以汽车空调系统各个子系统为分析对象。
2. 识别失效模式对汽车空调系统设计进行全面的分析,列举可能的失效模式。
比如,制冷剂泄漏、温度控制失效、空调系统过热等。
3. 确定失效模式的可能原因针对每个失效模式,分析其潜在的原因,如设计不当、材料选择不当、制造工艺缺陷等。
以制冷剂泄漏为例,可能的原因包括密封件老化、接口松动等。
4. 评估失效的严重程度对每个失效模式进行严重程度评估,考虑其对汽车空调系统性能、安全性和可靠性的影响。
以温度控制失效为例,可能导致车内温度无法调节,对车内乘客的舒适度产生较大影响。
5. 确定控制措施针对每个失效模式确定相应的预防和纠正措施,以减少失效概率和降低失效的严重程度。
比如,在设计阶段增加密封件的检测和更换计划,严格控制安装过程中的接口紧固力矩。
6. 跟踪执行和评估效果实施控制措施后,跟踪其执行情况,并对效果进行评估。
通过实际数据的反馈,不断优化和改善汽车空调系统的设计。
二、汽车空调系统DFMEA案例分析以下是针对汽车空调系统的DFMEA案例分析,以帮助读者更好地理解DFMEA方法的应用。
DFMEA案例分析

项目刹车盘停止汽车时需要超过规定的力在没有系统要求的情况下,允许汽车畅通行驶允许力从刹车片向车轴传递
必须向车轴施加规定的阻力矩传递的阻力矩不够功能要求失效模式
一经要求,即停止行车(考虑行驶环境条件,如潮湿)在规定距离和重力下,使行驶在干燥沥青路上的汽车停止
汽车无法停止
汽车停止,但超出规定距离缩短制动盘寿命,削弱汽车控制顾客无法开动车辆DFMEA分析案例
后果汽车控制削弱-不符合法规汽车控制削弱-不符合法规不符合法规系统在无指令情况下启动,汽车移动部分受阻
系统在无指令情况下启动,汽车不能移动
盘式刹车系统椭圆孔直径设计错误
膜片厚度不够
膜片预负载过小膜片阀不传送扭矩压盘轴尺寸过小
由于插接件结构、颜色相同导致错误装配电流过大电机过载烧毁液压管材料不恰当,加工时皱折破裂,制动液流失
防腐保护不充分,引起机械结合点腐蚀
润滑不到位引起机械结合点僵硬
从踏板到刹车片力的传递减少汽车超过XX 公里后停止液压管材料不恰当,加工时皱折破裂,制动液流失
连接器力矩规范不正确,制动液流失
密封设计,引起的主气缸真空锁闭
防腐保护不充分,机械连接断裂
从踏板到刹车片没有力的传递汽车不停止起因
机理失效模式。
设计失效分析DFMEA经典案例剖析完整版.ppt

• 20世纪 60年代,美国宇航界首次研究开发 FMEA;
• 1974年,美国海军建立第一个 FMEA 标准;
• 1976年,美国国防部首次采用 FMEA 标准;
• 70年代后期,美国汽车工业开始运用 FMEA;
• 80年代中期,美国汽车工业将 FMEA 运用于生產过程中;
• 90年代,美国汽车工业将 FMEA 纳入 QS9000 标准;在 TQS9000体系中,是4.20统计技术这个要素中的首要审核项 目
•设计之前 是正文内容部分,这里是正文
预先进行风内险容这部分里分是,析正这文里,内是容正确部文分内保,容这部设分,计水平。
里是正文内容部分,这里是正 文内容部分,这里是正文内
容部分,这里是正文内 容部分,这里是正文
精心整理
14
四:DFMEA表格标准格式
精心整理
15
四:DFMEA标准格式
这里是正文内容部分, 这里是正文内容部分,这里 是正文内容部分,这里是正文 内容部分,这里是正文内容部分, 这里是正文内容部分,这 里是正文内容部分,这里是正 文内容部分,这里是正文内
• 09年8月,三合一外审正式提出对九阳的“DFMEA”应用要求
,对我们目前的FMEA状况较为不满;以后可能会作为一个主
要内容进行审核。
精心整理
11
三:DFMEA基本概念相关——FMEA的类型
DFMEA PFMEA SFMEA AFMEA PFMEA SFMEA MFMEA
设计失效模式及后果分析 过程失效模式及后果分析 服务失效模式及后果分析 应用失效模式及后果分析 采购失效模式及后果分析 子系统失效模式及后果分析 机器失效模式及后果分析
DFMEA理论与实战
——六步搞定DFMEA表格
设计失效分析DFMEA经典案例剖析

六:DFMEA应用与表格制作实战第2步 ——找失效点之5-重要程度分级
级别(重要程度) 本栏目可用于对零件、子系统或系统的产品特性分级 (如关键、主要、重要、重点等),它们可能需要附加的 过程控制。 任何需要特殊过程控制的对象应用适当的字母或符号在 设计FMEA表格中的“分级”栏中注明,并应“建议措施” 栏中记录。 每一个在设计FMEA中标明有特殊过程控制要求的对象 在过程FMEA当中也应标明那些特殊的过程控制。 严重度分级: a) 确定级别要根据经验、要小组讨论,大家形成共识. b) 对整车的影响,假设零件(分析)装入整体运行 c) 可依FMEA手册参考制作自己的FMEA中严重度分级, 但要遵守大原则: CC(关键性特性)9-10级 SC(重要特性) 5 - 8级 (5级以上均要措施对策,5级以下可以考虑。)
a)成立小组(一般以3~4 人)可作为多方论证小组 中的子组 b)资料准备: •QFD设计要求 •可靠性、质量目标 •明确产品的使用环境 •类似产品的FMA/FTA资料 •工程标准 特殊特性明细表 c)各系统、子系统、各部门 逻辑影响关系
五、方块图的运用与指导作用:
产品的方块示意图表示了产品部件之间的物理和物流关系。方块图 的结构有不同的方法和形式。 方块图指出了在设计范围内部件和子系统之间的相互关系。这相互 关系包括:信息流、能量、力或流体。目标是理解系统的要求或输入, 输入活动的执行或功能的执行,和可交付性或输出。 图可能是方块用线连接而成,每一个方块与产品的一个主要部件或 过程的一个主要步骤相对应。线表示产品部件是怎样相关的,或相互的 界面。对于方块图,组织须以最好的方法或格式来做。 用于准备 DFMEA 的方块图应有复印件与DFMEA 附在一起。
典型的失效机理可能包括但不限于:屈服、疲 劳、材料不稳定性、蠕变、磨损和腐蚀。
设计失效模式及后果分析DFMEA-案例
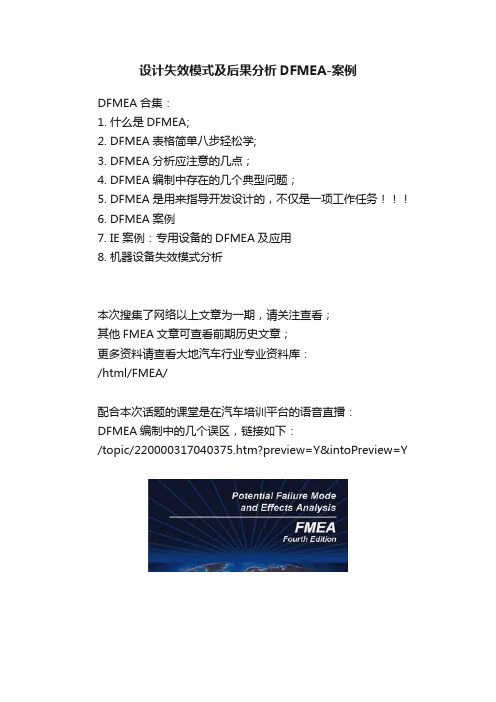
设计失效模式及后果分析DFMEA-案例DFMEA合集:1.什么是DFMEA;2.DFMEA表格简单八步轻松学;3.DFMEA分析应注意的几点;4.DFMEA编制中存在的几个典型问题;5.DFMEA是用来指导开发设计的,不仅是一项工作任务6.DFMEA案例7.IE案例:专用设备的DFMEA及应用8.机器设备失效模式分析本次搜集了网络以上文章为一期,请关注查看;其他FMEA文章可查看前期历史文章;更多资料请查看大地汽车行业专业资料库:/html/FMEA/配合本次话题的课堂是在汽车培训平台的语音直播:DFMEA编制中的几个误区,链接如下:/topic/220000317040375.htm?preview=Y&intoPreview=Y6 DFMEA 案例案例一:DFMEA的案例分析DFMEA是一种以预防为主的可靠性设计分析技术,该技术的应用有助于企业提高产品质量,降低成本,缩短研发周期。
目前,DFMEA已在航空航天以及国外的汽车行业得到了较为广泛的应用,并显示出了巨大的威力;但在国内汽车行业并没有系统地展开,也没有发挥其应有的作用。
以DFMEA在国产汽油机节流阀体的改进设计中的实施为例,对改进后的DFMEA的实施方法和流程进行阐述。
一、实施DFMEA存在的困难发动机为完成其相应的功能,组成结构复杂,零部件的数量也很庞大,如不加选择地对所有的零部件和子系统都实施DFMEA,将会耗费大量人力、物力和时间,对于初次实施DFMEA的企业几乎是不可能完成的工作。
为此,需要开发一种方法,能够从发动机的子系统/零部件中选择出优先需要进行分析的对象。
发动机由曲柄连杆机构、配气机构、燃油供给系统、进气系统、冷却系统和润滑系统等组成,各机构和系统完成相应的功能。
子系统的下级部件或组件通常需要配合完成相应的功能,在描述这些部件或组件的功能时,不仅应该描述其独立完成的功能,还应描述与其他部件配合完成的功能。
组成发动机的零部件种类很多,不仅包括机械零部件还有电子元件,电子部件的故障模式已经较为规范和完整,但机械系统及其零部件的故障模式相当复杂,不仅没有完整且规范的描述,二者之间还有一定的重复,为DFMEA工作的开展带来了困难,故需要为机械系统及其零部件建立相应的故障模式库。
DFMEA设计潜在失效模式及后果分析

7
項目
潛在失 潛在失效
潛在原因/ 8 現行設計控制
建議行動 責任與目標
行動結果
效模式 之效應 功能
失效機制
嚴 重 性
等 級
發 預防性 生 頻 率
探測性
風 難險 檢優 度先
數
完成日期 已採取行動 風
嚴發難險 重生檢優 性度度先
數
9
10
11
12 13
14
15
16
17 18 19
20
21
22
8
FMEA表格
0.010 / 1000
發生度
10 9 8 7 6 5 4 3 2 132
FMEA表格
• 現行設計控制
➢ 現有的設計控制可以預防或驗證出該失效模式 及/或失效原因
➢ 一般可分為下 2 種設計控制
1.
的控制 2.
的控制
預防該失效模式/效 應/原因/機制出現 或減低出現頻次
用分析或測試方式, 可以失效模式/效應 /原因/機制出現前 偵查出來
➢ 是量度失效的風險指數 ➢ 數值愈高,代表風失效風險愈高 ➢ 應在設計發展過程前盡早完成控制
37
FMEA表格
• 建議行動
➢ RPN排序完成後,應該對排序最高的、 極為重要的項目首先採取行動
➢ 建議先處理高於 100分風險度的項目 ➢ 不論RPN指數為多少,應對一些高嚴重
性(S)的項目多加留意,例如S=9, 10
➢ 應根據公司過住的記錄,自行訂立指標 ➢ 設計小組對 評定準則和分級規則應意見
一致,即使因為個別產品分析作了修改也 應一致
31
發生度(O)的提議指標
失效發生的可能性
很高: 持續的ห้องสมุดไป่ตู้效 高: 反複發生的失效 中等: 偶然發生的失效
DFMEA设计失效模式影响与后果分析报告

DFMEA设计失效模式影响及后果分析由谁进行设计失效模式及后果分析?由对设计具有影响的各部门代表组成的跨部门小组进行供应商也可以参加切不要忘记客户小组组长应是负责设计的工程师跨职能部门小组5-9人,来自:系统工程零部件设计工程试验室材料工程工艺过程工程装备设计制造质量管理怎样进行设计失效模式及后果分析?提要组建跨职能部门设计失效模式及后果分析DFMEA小组列出失效模式、后果和原因评估the severity of the effect (S) 影响的严重程度the likelihood of the occurrence (O) 可能发生的机会and the ability of design controls to detect failure modes and/or their causes (D) 探测出失效模式和/或其原因的设计控制能力怎样进行设计失效模式及后果分析?提要Calculate the risk priority number (RPN) to prioritize corrective actions 计算风险优先指数(RPN)以确定应优先采取的改进措施怎样进行设计失效模式及后果分析?提要Plan corrective actions 制订纠正行动计划Perform corrective actions to improve the product 采取纠正行动,提高产品质量Recalculate RPN 重新计算风险优先指数(RPN)怎样进行设计失效模式及后果分析?提要先在草稿纸上进行分析;当小组达成一致意见后,再将有关信息填在设计失效模式及后果分析FMEA表上use fishbone and tree diagrams liberally 充分利用鱼骨图和树形图trying to use the FMEA form as a worksheet leads to confusion and messed-up FMEAs 若将FMEA表当做工作单使用,就会造成混乱,使FMEA一塌糊涂建议1. 组建一个小组并制订行动计划绝不能由个人单独进行设计失效模式及后果分析,因为:由个人进行会使结果出现偏差进行任何活动,都需要得到其他部门的支持应指定一个人(如组长)保管设计失效模式及后果分析FMEA表格应将小组成员的和部门填入设计失效模式及后果分析FMEA表格2. 绘制产品功能结构图一种图示方法,其中包括:用块表示的各种组件(或特性)用直线表示的各组件之间的相互关系适当的详细程度结构图3. 列出每个组件的功能功能系指该组件所起的作用以下列形式说明功能:Verb + Object + Qualifier动词+宾语+修饰词例如:insulates core 使型芯绝缘assures terminal position in connector 确保端子与接头连接到位protects tang from smashing, etc. 防止柄脚被压碎,等Don't forget auxiliary functions as well a primary functions 不要忘记基本功能和辅助功能Often, components work together to perform a function 通常,多个组件一起行使某一功能Hint: Use the Block Diagram! 提示:利用结构图!4. 列出质量要求a customer want or desire 客户的期望或要求could seriously affect customer perception 有可能严重影响客户的看法could lead to a customer complaint 有可能导致客户投诉Hint: Use QFD 提示:使用质量功能展开5. 列出潜在的失效模式a defect, flaw, or other unsatisfactory condition in the product that is caused by a design weakness 由设计缺陷造成的产品缺陷、瑕疵或其它令人不满意的情况典型的失效模式- breaks - cracks破碎断裂- corrodes - sticks腐蚀粘结- unseats - deforms/melts未到位变形/熔化提示从前两个步骤做起:功能质量要求AIAG将失效模式定义为产品不能实现其设计意图的一种方式。
质量管理工具--DFMEA的案例分析

质量管理工具--DFMEA的案例分析质量管理工具--DFMEA的案例分析质量管理工具--DFMEA的案例分析DFMEA是一种以预防为主的可靠性设计分析技术,该技术的应用有助于企业提高产品质量,降低成本,缩短研发周期。
目前,DFMEA已在航空航天以及国外的汽车行业得到了较为广泛的应用,并显示出了巨大的威力;但在国内汽车行业并没有系统地展开,也没有发挥其应有的作用。
以DFMEA在国产汽油机节流阀体的改进设计中的实施为例,对改进后的DFMEA的实施方法和流程进行阐述。
发动机为完成其相应的功能,组成结构复杂,零部件的数量也很庞大,如不加选择地对所有的零部件和子系统都实施DFMEA,将会耗费大量人力、物力和时间,对于初次实施DFMEA的企业几乎是不可能完成的工作。
为此,需要开发一种方法,能够从发动机的子系统/零部件中选择出优先需要进行分析的对象。
发动机由曲柄连杆机构、配气机构、燃油供给系统、进气系统、冷却系统和润滑系统等组成,各机构和系统完成相应的功能。
子系统的下级部件或组件通常需要配合完成相应的功能,在描述这些部件或组件的功能时,不仅应该描述其独立完成的功能,还应描述与其他部件配合完成的功能。
组成发动机的零部件种类很多,不仅包括机械零部件还有电子元件,电子部件的故障模式已经较为规范和完整,但机械系统及其零部件的故障模式相当复杂,不仅没有完整且规范的描述,二者之间还有一定的重复,为DFMEA工作的开展带来了困难,故需要为机械系统及其零部件建立相应的故障模式库。
实施DFMEA的准备工作由于在发动机设计中实施DFMEA要遇到较多困难,故作者建议,在具体实施DFMEA之前,需要做好建立较为完善的故障模式库并确定DFMEA的详细分析对象等准备工作。
1.建立故障模式库的方法发动机的组成零部件多、结构复杂,大多数零部件在运行时还会有相互作用,导致零部件、子系统和系统的故障模式不仅复杂,各层次的故障模式还会相互重复,需要为发动机建立一个故障模式库;该模式库不仅应该包含发动机中所有子系统和零部件的故障模式,还能够反映出该故障模式究竟属于哪一个零部件或系统,其建模流程如下图所示。
设计失效分析DFMEA经典案例剖析
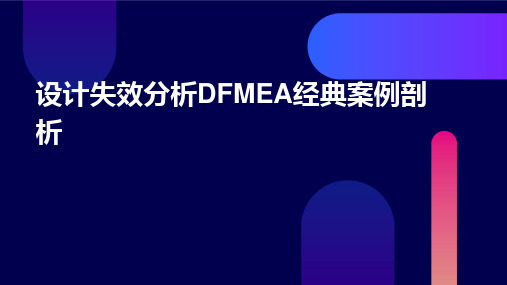
优质的产品是企业赢得市场 份额的关键因素之一。通过 DFMEA分析优化产品设计, 可以提高产品的竞争力,帮
助企业抢占市场份额。
增加企业收益
提高产品质量、降低生产成 本和增强市场竞争力都可以 为企业带来更多的收益。
07
总结与展望
DFMEA应用现状及挑战
01
应用现状
02 广泛应用于产品设计阶段,以预防潜在的设计缺 陷。
根据风险等级划分结果,优先处 理高风险失效模式,制定相应的 改进措施。
02
改进措施实施与验 证
实施改进措施后,对产品进行重 新评估,确保改进措施的有效性。
03Βιβλιοθήκη 持续改进在产品生命周期中持续进行 DFMEA分析,不断优化产品设 计,提高产品质量和可靠性。
03
经典案例一:汽车零部件设计 失效分析
案例背景介绍
改进措施实施及效果验证
改进措施
针对识别出的失效模式和原因,采取了相应的改进措施,如优化散热设计、改进电源管理模块、修复软件编码错误和 内存泄漏等。
效果验证
在实施改进措施后,对设备进行了重新测试和验证。结果显示,电池温度明显降低,屏幕闪烁问题得到解决,应用程 序运行稳定且不再崩溃。
经验教训
该案例表明,在设计阶段充分考虑潜在失效模式和影响至关重要。通过DFMEA等方法进行预防性分析, 可以及早发现并解决潜在问题,提高产品的可靠性和安全性。同时,持续改进和优化设计也是提升产品 质量和用户满意度的关键所在。
探测度评估
评估现有控制措施在多大程度上能够探测到失效模式的发生。
风险优先数计算
计算风险优先数(RPN)
将严重度、频度、探测度的评估结果相乘,得到每种失效模式的风险优先数。
dfmea案例结构件

dfmea案例结构件DFMEA(Design Failure Mode and Effects Analysis)是一种设计故障模式和影响分析的方法,用于评估和减少产品或系统设计中的潜在故障和风险。
下面是一个关于结构件的 DFMEA 案例示例:假设我们正在设计一个机械零件,这个零件是一个连接两个部件的关键连接器。
我们可以使用 DFMEA 来评估这个连接器设计中可能发生的潜在故障和风险。
1. 识别设计要素:我们首先需要识别连接器的设计要素,例如几何形状、材料、制造工艺等。
2. 确定潜在故障模式:针对每个设计要素,我们要考虑可能的故障模式。
例如,设计要素可能包括连接器的强度、刚度、密封性等,对应的潜在故障模式可能是强度不足、变形、漏气等。
3. 评估故障后果:对于每个潜在故障模式,我们评估其可能导致的后果。
后果可以分为功能故障、安全风险、性能下降等方面。
例如,连接器强度不足可能导致断裂,从而导致系统失效。
4. 确定故障发生的原因:对于每个故障模式,我们要分析可能的故障原因。
这通常涉及到错误的设计、制造缺陷、材料问题等。
例如,连接器强度不足可能是由于设计计算错误或材料强度不符合要求。
5. 评估和确认风险等级:根据故障的潜在后果和发生概率,给每个故障模式分配风险等级。
这通常是一个定性评估,可以根据风险矩阵或相关的评估工具进行。
6. 提出风险控制措施:为每个高风险故障模式提出相应的风险控制措施,以减轻或消除其影响。
这可能包括改进设计、选择更适合的材料、加强制造过程等。
7. 实施控制措施并持续监测:根据评估的措施,进行设计和制造改进,并确保实施措施的有效性。
同时,持续监测产品性能和故障数据,以便在需要时进行修订和改进。
通过进行 DFMEA,我们可以识别潜在的设计故障模式和风险,并采取相应的控制措施来改进产品设计和减少潜在风险。
这样可以提高产品的可靠性、性能和安全性。
设计失效分析DFMEA经典案例剖析

1. 明确功能(预期功能) 考虑非预期功能,失效模式是针对功能而言: Ⅰ型失效模式:不能完成规定的功能 Ⅱ型失效模式:产生了非预期的、有害的 考虑后果:站在用户将来使用产品的立场:
2.严重度分级: a) 确定级别要根据经验、要小组讨论,大家
形成共识. b) 对整车的影响,假设零件(分析)装入整 体运行
设计FMEA表格中的“分级”栏中注明,并应“建议措施”
栏中记录。
✓ 每一个在设计FMEA中标明有特殊过程控制要求的对象
在过程FMEA当中也应标明那些特殊的过程控制。
严重度分级:
a) 确定级别要根据经验、要小组讨论,大家形成共识.
b) 对整车的影响,假设零件(分析)装入整体运行
5
c) 可依FMEA手册参考制作自己的FMEA中严重度分级,
c) 可依FMEA手册参考制作自己的FMEA中 严重度分级,但要遵守大原则:
CC(关键性特性) 9-10级 SC(重要特性) 5-8级
5级以上均要措施对策,5级以下可以考虑。
五:DFMEA应用与表格制作实战第1步 ——填写表头
注意时间是随 时更新的!
五:DFMEA应用与表格制作实战第2步
——寻找失效点
•失效模式: 指设计(制造)过程无法达到预定或规 定的要求所表现出的特征;如:坏品、不良设备状 况等; •后果: 指失效模式对客户(包括下工序)所造成的影响;
三:DFMEA基本概念相关——定义
•FMEA 是一种用来确认风险的分析方法,它包含: •确认潜在的失效模式并评价其產生的效应; •确认失效模式对客户所產生的影响; •确认潜在的產品/过程失效原因; •确认现有控制產品/过程失效的方法; •确定排除或降低失效改善方这案里这是里;正是文正内文容内部容分部,分这,里