锻压工艺基础 工程材料讲稿共120页文档
合集下载
锻压工艺讲解课件
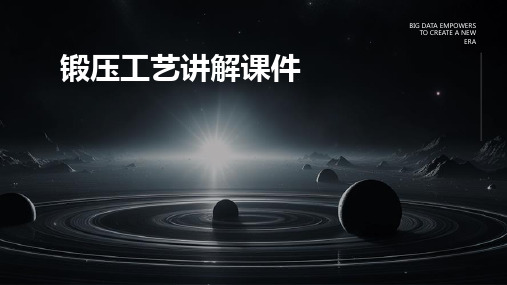
锻造工艺参数
控制锻造工艺参数,如变形程度、锻造速度等, 保证产品质量。
冷却
冷却目的
将锻件快速冷却至室温,提高其 硬度和强度。
冷却方式
采用适当的冷却方式,如空冷、水 冷等,根据材料和产品要求选择。
冷却工艺参数
控制冷却工艺参数,如冷却速度、 时间等,确保锻件组织和性能符合 要求。
热处理
热处理目的
01
3
模锻锤的模具设计和制造较为复杂,且对原材料 的质量要求较高。
液压机
液压机是一种以液体压力为动力 源的锻压设备,通过液压系统将 油泵产生的压力传递到工作缸, 实现对金属坯料的加压和变形。
液压机具有较大的压力和较小的 冲击力,适用于精密、复杂和大
型锻件的加工。
液压机的结构较为复杂,制造成 本和维护成本较高。
核电、火电等领域的压 力容器和管道。
刀具、模具等精密零件 的制造。
锻压工艺的优缺点
优点 可制造出形状复杂、精度高的零件。
可提高金属的力学性能和耐腐蚀性能。
锻压工艺的优缺点
•Байду номын сангаас可实现批量生产,降低生产成本。
锻压工艺的优缺点
缺点 生产周期较长,不适合小批量生产。
需要大量的能源和原材料。 对设备和工艺要求较高,需要专业技术人员操作。
06
锻压工艺发展趋势与未来展望
锻压工艺发展趋势
高效化
随着科技的发展,锻压工艺正朝着高效化方向发 展。通过改进工艺流程、提高设备性能和优化生 产管理,实现更快速、高效的生产,提高生产效 率和产品质量。
绿色化
随着环保意识的提高,锻压工艺正朝着绿色化方 向发展。通过采用环保材料、优化工艺流程、降 低能耗和减少废弃物排放等措施,实现锻压生产 的环保和可持续发展。
控制锻造工艺参数,如变形程度、锻造速度等, 保证产品质量。
冷却
冷却目的
将锻件快速冷却至室温,提高其 硬度和强度。
冷却方式
采用适当的冷却方式,如空冷、水 冷等,根据材料和产品要求选择。
冷却工艺参数
控制冷却工艺参数,如冷却速度、 时间等,确保锻件组织和性能符合 要求。
热处理
热处理目的
01
3
模锻锤的模具设计和制造较为复杂,且对原材料 的质量要求较高。
液压机
液压机是一种以液体压力为动力 源的锻压设备,通过液压系统将 油泵产生的压力传递到工作缸, 实现对金属坯料的加压和变形。
液压机具有较大的压力和较小的 冲击力,适用于精密、复杂和大
型锻件的加工。
液压机的结构较为复杂,制造成 本和维护成本较高。
核电、火电等领域的压 力容器和管道。
刀具、模具等精密零件 的制造。
锻压工艺的优缺点
优点 可制造出形状复杂、精度高的零件。
可提高金属的力学性能和耐腐蚀性能。
锻压工艺的优缺点
•Байду номын сангаас可实现批量生产,降低生产成本。
锻压工艺的优缺点
缺点 生产周期较长,不适合小批量生产。
需要大量的能源和原材料。 对设备和工艺要求较高,需要专业技术人员操作。
06
锻压工艺发展趋势与未来展望
锻压工艺发展趋势
高效化
随着科技的发展,锻压工艺正朝着高效化方向发 展。通过改进工艺流程、提高设备性能和优化生 产管理,实现更快速、高效的生产,提高生产效 率和产品质量。
绿色化
随着环保意识的提高,锻压工艺正朝着绿色化方 向发展。通过采用环保材料、优化工艺流程、降 低能耗和减少废弃物排放等措施,实现锻压生产 的环保和可持续发展。
锻压成形的工艺基础

• 锻压成形的工艺基础 6. 影响金属锻造性能的因素
(2)工艺条件
变形温度对塑性及变形抗力影响很大 变形速度 应力状态
锻压成形
• 锻压成形的工艺基础 6. 影响金属锻造性能的因素
1)变形温度对塑性及变形抗力影响很大
适当提高变形温度有利于改善金属的锻造性能 温度过高会使金属产生氧化、脱碳、过热等缺陷,甚至使锻 件产生过热而报废 应严格控制锻造温度
锻压成形
• 锻压成形的工艺基础 4. 金属的冷加工和热加工
(1)冷加工
金属在再结晶温度以下进行的塑性变形称为冷加工 冷变形金属存在残余应力和塑性差等缺点 需要中间退火,才能继续变形
锻压成形
• 锻压成形的工艺基础 4. 金属的冷加工和热加工
(2)热加工
热加工是在结晶温度以上进行的 变形后只有再结晶组织而无冷变形强化现象
机械制造基础
锻压成形
❖ 锻压成形的工艺基础
1. 金属塑性变形的实质
金属塑性变形是金属晶体每个晶粒内部的变形和晶粒间的相对 移动、晶粒转动的综合结果
图 单晶体滑移示意图
锻压成形
❖ 锻压成形的工艺基础
1. 金属塑性变形的实质
金属塑性变形是金属晶体每个晶粒内部的变形和晶粒间的相对 移动、晶粒转动的综合结果
锻压成形
• 锻压成形的工艺基础 6. 影响金属锻造性能的因素
2)变形速度
一方面当变形速度较大时,由于再结晶过程来不及完成,冷 变形强化不能及时消除,而使锻造性能变差
另一方面,当变形速度很高时,变形功转化的热来不及散发, 锻件温度升高,又能改善锻造性能
利用高速锻锤可以锻造在常规没备上难以锻造成形的高强 度低塑性金属
锻压成形
• 锻压成形的工艺基础 6. 影响金属锻造性能的因素
(2)工艺条件
变形温度对塑性及变形抗力影响很大 变形速度 应力状态
锻压成形
• 锻压成形的工艺基础 6. 影响金属锻造性能的因素
1)变形温度对塑性及变形抗力影响很大
适当提高变形温度有利于改善金属的锻造性能 温度过高会使金属产生氧化、脱碳、过热等缺陷,甚至使锻 件产生过热而报废 应严格控制锻造温度
锻压成形
• 锻压成形的工艺基础 4. 金属的冷加工和热加工
(1)冷加工
金属在再结晶温度以下进行的塑性变形称为冷加工 冷变形金属存在残余应力和塑性差等缺点 需要中间退火,才能继续变形
锻压成形
• 锻压成形的工艺基础 4. 金属的冷加工和热加工
(2)热加工
热加工是在结晶温度以上进行的 变形后只有再结晶组织而无冷变形强化现象
机械制造基础
锻压成形
❖ 锻压成形的工艺基础
1. 金属塑性变形的实质
金属塑性变形是金属晶体每个晶粒内部的变形和晶粒间的相对 移动、晶粒转动的综合结果
图 单晶体滑移示意图
锻压成形
❖ 锻压成形的工艺基础
1. 金属塑性变形的实质
金属塑性变形是金属晶体每个晶粒内部的变形和晶粒间的相对 移动、晶粒转动的综合结果
锻压成形
• 锻压成形的工艺基础 6. 影响金属锻造性能的因素
2)变形速度
一方面当变形速度较大时,由于再结晶过程来不及完成,冷 变形强化不能及时消除,而使锻造性能变差
另一方面,当变形速度很高时,变形功转化的热来不及散发, 锻件温度升高,又能改善锻造性能
利用高速锻锤可以锻造在常规没备上难以锻造成形的高强 度低塑性金属
锻压成形
• 锻压成形的工艺基础 6. 影响金属锻造性能的因素
工程材料与机械制造基础(锻压)

合金具有好的锻造性。
• 低碳钢、低合金钢及铝合金锻造性好,高合金钢的锻造性差, 铸铁不能锻造。
§ 11-3自由锻造
一、概述 1、自由锻的概念 将加热后的坯料放在铁砧上,在压力或冲击力的作用下使其 自由变形获得锻件的方法。 2、自由锻的分类 手工自由锻和机器自由锻。 3、自由锻的特点 坯料的变形不受模具限制,设备和工具的通用性大,锻件的 重量不受限制,是生产大型锻件的唯一方法。但是,生产率 低,锻件精度低,加工余量大,只适合于单件小批量生产形 状简单件。
外缘凸出或凹进尺寸大于1.5板厚。
拉深件:
• 1)外形力求简单、对称。 • 2)尽量避免深度过大。 • 3)拉深件圆角半径应尽量大,以利于成形和减少
拉深次数。 • 对复杂结构可采用冲焊结合锻压也是获得零件毛坯的主要方法之一。与铸造所不同的是, 锻压是利用材料具有塑性的原理,在固态下使材料产生塑性 变形而获得锻压件。由于固态下金属的变形难度较大,所以, 锻压不能生产形状非常复杂,尤其是内腔很复杂的零件。但 是同样的材料锻压件的机械性能比铸件好,所以,锻造主要
3)应尽量避免窄沟、深槽、深孔和多孔结构。
三、曲柄压力机上模锻
1、与锤上模锻相比其特点: 1)滑块行程固定,机身结构刚性大,导轨的导向精度高。 2)设有上下顶出装置,可自动脱模,故锻件的模锻斜度小。 3)变形是在滑块的一次行程中完成,变形比较均匀,力学 性能均匀一致。 4)对坯料产生的是静压力,这对变形速度敏感的低塑性材 料的成型更有利。 5)生产率高,无冲击和震动,故劳动条件好。但设备复杂, 造价高,需要其它辅助设备。因此主要用于具有现代化辅助 设备的大厂模锻件的大批量生产。
3、模锻工艺规程的制订
1)绘制锻件图(选择分模面、加工余量和模锻公差、连皮、 模锻斜度和圆角半径) 2)计算坯料质量和尺寸 3)选择模锻工序 4)选择锻造设备 5)确定锻造温度范围
• 低碳钢、低合金钢及铝合金锻造性好,高合金钢的锻造性差, 铸铁不能锻造。
§ 11-3自由锻造
一、概述 1、自由锻的概念 将加热后的坯料放在铁砧上,在压力或冲击力的作用下使其 自由变形获得锻件的方法。 2、自由锻的分类 手工自由锻和机器自由锻。 3、自由锻的特点 坯料的变形不受模具限制,设备和工具的通用性大,锻件的 重量不受限制,是生产大型锻件的唯一方法。但是,生产率 低,锻件精度低,加工余量大,只适合于单件小批量生产形 状简单件。
外缘凸出或凹进尺寸大于1.5板厚。
拉深件:
• 1)外形力求简单、对称。 • 2)尽量避免深度过大。 • 3)拉深件圆角半径应尽量大,以利于成形和减少
拉深次数。 • 对复杂结构可采用冲焊结合锻压也是获得零件毛坯的主要方法之一。与铸造所不同的是, 锻压是利用材料具有塑性的原理,在固态下使材料产生塑性 变形而获得锻压件。由于固态下金属的变形难度较大,所以, 锻压不能生产形状非常复杂,尤其是内腔很复杂的零件。但 是同样的材料锻压件的机械性能比铸件好,所以,锻造主要
3)应尽量避免窄沟、深槽、深孔和多孔结构。
三、曲柄压力机上模锻
1、与锤上模锻相比其特点: 1)滑块行程固定,机身结构刚性大,导轨的导向精度高。 2)设有上下顶出装置,可自动脱模,故锻件的模锻斜度小。 3)变形是在滑块的一次行程中完成,变形比较均匀,力学 性能均匀一致。 4)对坯料产生的是静压力,这对变形速度敏感的低塑性材 料的成型更有利。 5)生产率高,无冲击和震动,故劳动条件好。但设备复杂, 造价高,需要其它辅助设备。因此主要用于具有现代化辅助 设备的大厂模锻件的大批量生产。
3、模锻工艺规程的制订
1)绘制锻件图(选择分模面、加工余量和模锻公差、连皮、 模锻斜度和圆角半径) 2)计算坯料质量和尺寸 3)选择模锻工序 4)选择锻造设备 5)确定锻造温度范围
锻造工艺过程PPT课件

Ⅵ 弯曲件
拔长,分段,错移,打 圆,扭转
第9页/共12页
镦粗,冲孔,在心轴上 扩孔,定径
镦粗,冲孔,在心轴上 拔长,打圆
拔长,弯曲
四、自由锻造锻件的结构工艺性
自由锻造锻件结构设计的原则是:除满足使用性能要求外,还要考虑 自由锻造的设备、工具及工艺特点,尽量使锻件外形简单,易于锻造
自由锻造锻件结构工艺性见下表。
本
需锻件的工艺 过程。如镦粗、
工 拔长、冲孔、
序 弯曲、扭转、
错移等
第6页/共12页
基本工序是
改变坯料形
状、尺寸以
基
获得所需锻 件的:工艺
过程。如镦
本 粗、拔长、
冲孔、弯曲、
工 扭转、错移 等
序
修整工序是用
修 来修整锻件表
面缺陷,使其
整 符合图样要求。
工 如校正、平整、 序 滚圆等
第7页/共12页
第3页/共12页
第四节 自由锻造
一、自由锻造的特点及设备(视频)
(1) 改善组织结构,提高力学性能。通过锻打,金属内部粗晶 结构被打碎;气孔、缩孔、裂纹等缺陷被压合,提高了致密性,金 属的纤维流线在锻件截面上合理分布,提高了金属的力学性能。
(2) 成本低,经济性合理。锻压设备、工具通用性好, 生产准备周期短,便于更换产品。
第2页/共12页
2.过热、过烧
过热是指金属加热温度过高,加热时间过 长而引起晶粒粗大的现象。过热使钢坯的可锻 性和力学性能下降,必须通过退火处理来细化 晶粒以消除过热组织,不能进行退火处理的钢 坯可通过反复锻打来改善晶粒度。
二、锻造成形
金属加热后,就可锻造成形,根据锻造时 所用的设备、工模具及成形方式的不同,可将 锻造成形分为自由锻成形、模锻成形和胎模锻 成形等。
拔长,分段,错移,打 圆,扭转
第9页/共12页
镦粗,冲孔,在心轴上 扩孔,定径
镦粗,冲孔,在心轴上 拔长,打圆
拔长,弯曲
四、自由锻造锻件的结构工艺性
自由锻造锻件结构设计的原则是:除满足使用性能要求外,还要考虑 自由锻造的设备、工具及工艺特点,尽量使锻件外形简单,易于锻造
自由锻造锻件结构工艺性见下表。
本
需锻件的工艺 过程。如镦粗、
工 拔长、冲孔、
序 弯曲、扭转、
错移等
第6页/共12页
基本工序是
改变坯料形
状、尺寸以
基
获得所需锻 件的:工艺
过程。如镦
本 粗、拔长、
冲孔、弯曲、
工 扭转、错移 等
序
修整工序是用
修 来修整锻件表
面缺陷,使其
整 符合图样要求。
工 如校正、平整、 序 滚圆等
第7页/共12页
第3页/共12页
第四节 自由锻造
一、自由锻造的特点及设备(视频)
(1) 改善组织结构,提高力学性能。通过锻打,金属内部粗晶 结构被打碎;气孔、缩孔、裂纹等缺陷被压合,提高了致密性,金 属的纤维流线在锻件截面上合理分布,提高了金属的力学性能。
(2) 成本低,经济性合理。锻压设备、工具通用性好, 生产准备周期短,便于更换产品。
第2页/共12页
2.过热、过烧
过热是指金属加热温度过高,加热时间过 长而引起晶粒粗大的现象。过热使钢坯的可锻 性和力学性能下降,必须通过退火处理来细化 晶粒以消除过热组织,不能进行退火处理的钢 坯可通过反复锻打来改善晶粒度。
二、锻造成形
金属加热后,就可锻造成形,根据锻造时 所用的设备、工模具及成形方式的不同,可将 锻造成形分为自由锻成形、模锻成形和胎模锻 成形等。
材料成型讲义技术_--_第三章锻压_3.2

③平锻机模锻:平锻机是具有镦锻滑块和夹紧滑块 的卧式压力机。
④螺旋压力机模锻:螺旋压力机是靠主螺杆的旋转 带动滑块上下运动,向上实现回程,向下进行锻 打的压力机。
3.2.2 冲压
1.冲压
是使板料经分离或成形而得到制 件的工艺统称。
(1)冲压设备: 1)剪床→把板料切成一定宽度的条料, 为后续的冲压备料。 2)冲床→完成冲压的各道工序, 生产出合格的产品。
镦粗
制坯模膛(体积分配)
拔长 滚挤★
弯曲 …
模锻膛(锻件与坯料切离)
设飞边槽★ 放收缩率
实际锻造时应根据锻件的复杂程度相应 选用单模膛锻模或多模膛锻模。 一般形状简单的锻件 采用仅有终锻模膛的单模膛锻模, 而形状复杂的锻件(如截面不均匀、轴线弯 曲、不对称等)则需采用具有制坯、预锻、 终锻等多个模膛的锻模逐步成形。
特别适于重型、大型锻件生产。
(4)自由锻的基本工序 分类 : 1)辅助工序: 为方便基本工序的操作而预先进行局部小变形 的工序。 如倒棱、压肩等。 2)精整工序: 修整锻件最终形状和尺寸、消除表面不平和歪 斜的工序。如修整鼓形、校平、校直等。 3)基本工序: 锻造过程中直接改变坯料形状和尺寸的工序。 如镦粗、拔长、冲孔、扩孔、弯曲、锻接等。
冲裁软钢、铝合金、铜合金等软材料时:
Z=(6%~8%)δ
冲裁硬钢等材料时:Z=(8%~12%)δ
冲厚板或精度较低的冲裁件时,间隙还可适 当增大。
3)排样:
即冲裁件在板料或带料上的布置方法。
排样原则:合理。
目的:简化模具结构,提高材料利用率。
4)提高冲裁质量的冲压工艺:
当冲裁件剪断面用做工作表面或配合表面时, 常采用整修、挤光、精密冲裁等冲压工艺以提 高冲裁质量。
④螺旋压力机模锻:螺旋压力机是靠主螺杆的旋转 带动滑块上下运动,向上实现回程,向下进行锻 打的压力机。
3.2.2 冲压
1.冲压
是使板料经分离或成形而得到制 件的工艺统称。
(1)冲压设备: 1)剪床→把板料切成一定宽度的条料, 为后续的冲压备料。 2)冲床→完成冲压的各道工序, 生产出合格的产品。
镦粗
制坯模膛(体积分配)
拔长 滚挤★
弯曲 …
模锻膛(锻件与坯料切离)
设飞边槽★ 放收缩率
实际锻造时应根据锻件的复杂程度相应 选用单模膛锻模或多模膛锻模。 一般形状简单的锻件 采用仅有终锻模膛的单模膛锻模, 而形状复杂的锻件(如截面不均匀、轴线弯 曲、不对称等)则需采用具有制坯、预锻、 终锻等多个模膛的锻模逐步成形。
特别适于重型、大型锻件生产。
(4)自由锻的基本工序 分类 : 1)辅助工序: 为方便基本工序的操作而预先进行局部小变形 的工序。 如倒棱、压肩等。 2)精整工序: 修整锻件最终形状和尺寸、消除表面不平和歪 斜的工序。如修整鼓形、校平、校直等。 3)基本工序: 锻造过程中直接改变坯料形状和尺寸的工序。 如镦粗、拔长、冲孔、扩孔、弯曲、锻接等。
冲裁软钢、铝合金、铜合金等软材料时:
Z=(6%~8%)δ
冲裁硬钢等材料时:Z=(8%~12%)δ
冲厚板或精度较低的冲裁件时,间隙还可适 当增大。
3)排样:
即冲裁件在板料或带料上的布置方法。
排样原则:合理。
目的:简化模具结构,提高材料利用率。
4)提高冲裁质量的冲压工艺:
当冲裁件剪断面用做工作表面或配合表面时, 常采用整修、挤光、精密冲裁等冲压工艺以提 高冲裁质量。
锻压工艺基础工程材料讲稿

• Y=F0/F〉1,通常Y=2~5 • Y——锻造比; F0——拔长前横截面积; • F——拔长后横截面积. • Y——一般2~5. Y>5力学性能不再提高。
– 纤维组织 用热处理和其他方法均无法消除和改变。
– 使用时,零件最大工作正应力与纤维方向一致,切 应力与纤维方向垂直。且尽可能纤维方向沿零件轮 廓而不被切断最为理想,锻造得法,往往能达理想 状态。图11-1.
锻造加工理论根底
可锻性——常用金属材料经受塑性变形加工 的难易程度。可锻性的优劣是以金属的塑性和变 形抗力来衡量的。
塑性是指金属材料在外力作用下产生永久变 形,而不破坏其完整性的能力。
变形抗力是指金属对变形的抵抗力。 金属的可锻性取决于材料的本质(内因)和塑性 成形的条件(外因)。
二、金属锻造性能 金属塑性大,变形抗力小,锻造容易即锻造性
锻压工艺根底工程材 料讲稿
本章内容
压力加工理论根底 锻造及其工艺根底 冲压及其工艺根底 现代压力加工技术与开展动向
压 论力 基加 础工
理
压力加工概念 特点 种类
金属塑性变形实质
塑性变形对组织和 性能影响
1.1 压力加工的定义
• 压力加工是使金属材料在外力作用下产 生塑性变形,〔永久变形〕以获得所需 形状、尺寸及机械性能的毛坯或零件的 一种加工工艺;
• 变形有先有后 各晶粒相对于外力轴的取向不 同,位向有利的晶粒先变形,且不同晶粒变形量 也不同。一般变形度到达20%,几乎所有晶粒都 可参加变形。
• 各个晶粒的变形必须协调 晶粒不能自由地、 均匀地滑移,它要受到相邻晶粒的牵制,故晶粒 之间要互相配合、协调。如果协调不好,将会导 致塑性下降〔晶界处开裂〕。理论分析指出,要 能协调变形,每个晶粒至少能在5个独立的滑移系 上进展滑移。这样,多晶体变形就比单晶体更复 杂,应变硬化率也大得多。
– 纤维组织 用热处理和其他方法均无法消除和改变。
– 使用时,零件最大工作正应力与纤维方向一致,切 应力与纤维方向垂直。且尽可能纤维方向沿零件轮 廓而不被切断最为理想,锻造得法,往往能达理想 状态。图11-1.
锻造加工理论根底
可锻性——常用金属材料经受塑性变形加工 的难易程度。可锻性的优劣是以金属的塑性和变 形抗力来衡量的。
塑性是指金属材料在外力作用下产生永久变 形,而不破坏其完整性的能力。
变形抗力是指金属对变形的抵抗力。 金属的可锻性取决于材料的本质(内因)和塑性 成形的条件(外因)。
二、金属锻造性能 金属塑性大,变形抗力小,锻造容易即锻造性
锻压工艺根底工程材 料讲稿
本章内容
压力加工理论根底 锻造及其工艺根底 冲压及其工艺根底 现代压力加工技术与开展动向
压 论力 基加 础工
理
压力加工概念 特点 种类
金属塑性变形实质
塑性变形对组织和 性能影响
1.1 压力加工的定义
• 压力加工是使金属材料在外力作用下产 生塑性变形,〔永久变形〕以获得所需 形状、尺寸及机械性能的毛坯或零件的 一种加工工艺;
• 变形有先有后 各晶粒相对于外力轴的取向不 同,位向有利的晶粒先变形,且不同晶粒变形量 也不同。一般变形度到达20%,几乎所有晶粒都 可参加变形。
• 各个晶粒的变形必须协调 晶粒不能自由地、 均匀地滑移,它要受到相邻晶粒的牵制,故晶粒 之间要互相配合、协调。如果协调不好,将会导 致塑性下降〔晶界处开裂〕。理论分析指出,要 能协调变形,每个晶粒至少能在5个独立的滑移系 上进展滑移。这样,多晶体变形就比单晶体更复 杂,应变硬化率也大得多。
锻造用原材料及坯料准备讲课文档

现在八页,总共七十五页。
钢的低倍组织 • (1) 偏析 • (2) 缩孔残余 • (3) 白点
现在九页,总共七十五页。
(1) 偏析
• 偏析是钢锭在凝固过程中产生的化学成份以及杂 质的不均匀现象。
• 主要类型有方框偏析、点状偏析和枝晶偏析。 • 碳化物偏析会降低钢的锻造性能,严重者在热加工
过程中零件内部产生较大的拉应力,引起锻件开裂。
现在二十三页,总共七十五页。
(2) 表面脱碳层
• 钢材表面的脱碳层影响零件的强度及疲劳性 能,降低零件的使用寿命。
• 对冷锻成形用毛坯一般要求在退火后车加工 剥皮;退火后不车加工剥皮,那么每边脱碳 层深度不得大于其直径的1.5%。
现在二十四页,总共七十五页。
(3)再结晶组织
• 对于某些零件,为了保证其有较高的韧度和塑 性,需要采用再结晶退火处理。
精锻用有色金属和贵金属
现在二十七页,总共七十五页。
有色金属和贵金属的缺陷
(1)铝合金的氧化膜 在熔炼工程中,敞露的熔体液面与大气
中的水蒸气或其它金属氧化物相互作用形成 的氧化膜,在浇注时被卷入液体金属内部, 铸锭经轧制或锻造,其内部的氧化物被拉成 条状或片状,降低了横向力学性能。
现在二十八页,总共七十五页。
截面椭圆度和截面倾角。V为剪切后的毛坯实际
体积与精锻工艺所要求的毛坯体积的差值,v为
精锻工艺所要求的毛坯体积。
现在三十九页,总共七十五页。
b
图2.4 评价毛坯剪切品质的一些技术参数
f 、k-分别为静、动剪刀形成的压塌深度
cdb--、d截截1-面面分不光别平亮为度带棒;宽料度-直;截径面和倾毛角坯;最小直径;
锻造用钢的宏观缺陷
表面缺陷一般包括裂纹、疤痕、折叠和夹 杂等。
钢的低倍组织 • (1) 偏析 • (2) 缩孔残余 • (3) 白点
现在九页,总共七十五页。
(1) 偏析
• 偏析是钢锭在凝固过程中产生的化学成份以及杂 质的不均匀现象。
• 主要类型有方框偏析、点状偏析和枝晶偏析。 • 碳化物偏析会降低钢的锻造性能,严重者在热加工
过程中零件内部产生较大的拉应力,引起锻件开裂。
现在二十三页,总共七十五页。
(2) 表面脱碳层
• 钢材表面的脱碳层影响零件的强度及疲劳性 能,降低零件的使用寿命。
• 对冷锻成形用毛坯一般要求在退火后车加工 剥皮;退火后不车加工剥皮,那么每边脱碳 层深度不得大于其直径的1.5%。
现在二十四页,总共七十五页。
(3)再结晶组织
• 对于某些零件,为了保证其有较高的韧度和塑 性,需要采用再结晶退火处理。
精锻用有色金属和贵金属
现在二十七页,总共七十五页。
有色金属和贵金属的缺陷
(1)铝合金的氧化膜 在熔炼工程中,敞露的熔体液面与大气
中的水蒸气或其它金属氧化物相互作用形成 的氧化膜,在浇注时被卷入液体金属内部, 铸锭经轧制或锻造,其内部的氧化物被拉成 条状或片状,降低了横向力学性能。
现在二十八页,总共七十五页。
截面椭圆度和截面倾角。V为剪切后的毛坯实际
体积与精锻工艺所要求的毛坯体积的差值,v为
精锻工艺所要求的毛坯体积。
现在三十九页,总共七十五页。
b
图2.4 评价毛坯剪切品质的一些技术参数
f 、k-分别为静、动剪刀形成的压塌深度
cdb--、d截截1-面面分不光别平亮为度带棒;宽料度-直;截径面和倾毛角坯;最小直径;
锻造用钢的宏观缺陷
表面缺陷一般包括裂纹、疤痕、折叠和夹 杂等。
锻压工艺基础
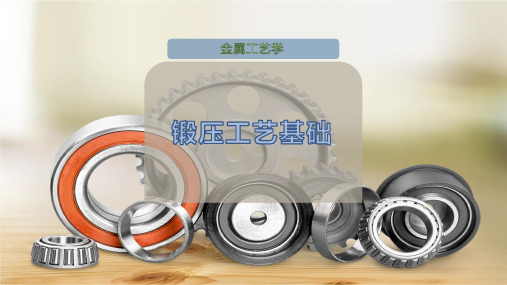
锻压加工方法 需要重型的机器 设备和较复杂的 模具,模具的设 计、制造的周期 长,初期投资费 用高。
1.1 金属的塑性变形
锻压工艺基础
金属塑性变形的实质,经 典理论的解释为:晶粒内部产 生滑移、晶粒间产生滑移和晶 粒发生转动的综合结果。
1.1 金属的塑性变形
锻压工艺基础
单晶体的滑移变形过程
1.1 金属的塑性变形
复” 。
1.2 回复与再结晶
锻压工艺基础
当冷变形强化的金属温度升高到某一临界值时, 金属原子获得足够高的动能,因塑性变形而被拉长的 晶粒及碎晶等将重新生核、结晶,形成新的等轴晶粒, 从而消除了晶格畸变、应力及冷变形强化现象,这一
过程称为“再结晶” 。
1.2 回复与再结晶
锻压工艺基础
变 性 后 的 金 属 在 加 热 时 组 织 和 性 能 的 变 化
锻压工艺基础
单晶体的滑移变形过程
1.1 金属的塑性变形
锻压工艺基础
常温下塑性变形对低碳钢力学性能的影响
1.2 回复与再结晶
锻压工艺基础
当加热温度不高时,原子的扩散能力较弱,不能 引起明显的组织变化,只能使晶格扭曲程度减轻,并 使应力下降,部分地消除冷变形强化现象,即强度、 硬度略有下降,而塑性略有升高,这一过程称为“回
锻压工艺基础
锻压加工方法 与其它加工方 法相比具有以 下优点:
1. 力学性能高
2. 节约金属
3. 生产率高
4. 适应性广
锻压工艺基础
锻压生产虽然具有以上优点,但也受到以下几个方面的制约:
锻件的结构工 艺性要求较高, 形状复杂特别是 内腔形状复杂的 零件或毛坯难以 甚至不能锻压成 形。
通常锻压件 (主要指锻造毛 坯)的尺寸精度 不高,还需配合 削加工等方法 来满足精度要求。