基于DOE法的注塑成型工艺仿真优化
基于Moldflow与正交试验的注塑工艺参数优化设计
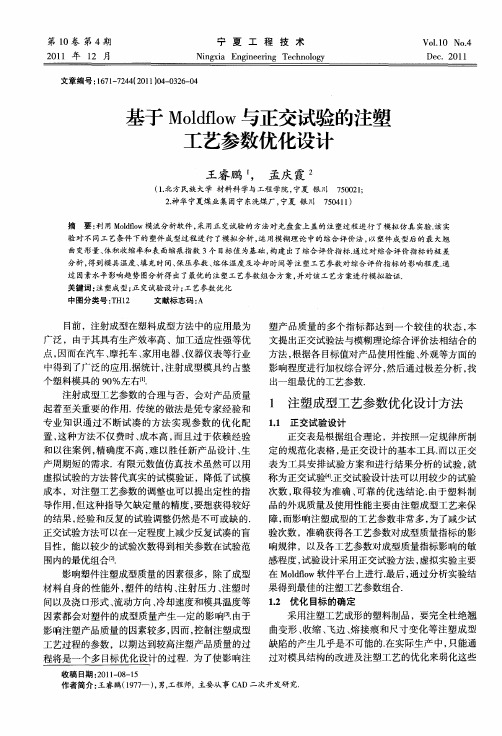
21 年 1 月 01 2
宁 夏 工 程 技 术
Ni g i En i e i g n xa gne rn Te h o o y c n lg
V0 .0 11 No4 .
De . 2 l o 01
文章编号 :6 1 74 (0 )4 0 2— 4 17 — 2 4 2 1 0 — 3 6 0 1
塑产 品质量 的多个 指 标都 达 到 一个 较 佳 的状 态 , 本
文提出正交试验法与模糊理论综合评价法相结合的 方法 , 根据各 目标值对产品使用性能 、 外观等方面的 影响程度进行加权综合评分 , 然后通过极差分析 , 找 出一组最优 的工艺参数.
起着至关重要的作用. 传统的做法是凭专家经验和 专业知识通过不断试凑 的方法实现参数 的优化 配 置, 这种方法不仅费时、 成本高 , 而且过于依赖经验
工艺过程的参数,以期达到较高注塑产品质量 的过 程将是一个多 目标优化设计的过程. 为了使影响注
收稿 日期 :0 10 — 5 2 1- 8 1 作者简介 : 王睿鹏( 97 ) 男, 17一 , 工程师,主要从事 C D二 次开发研究 A
第 4期
王睿鹏等 : 基于 M l o o fw与正交试验 的注塑工艺参数优化设计 d l
验对不 同工 艺条件下的塑件成型过程进行 了模拟分析 , 用模糊理论 中的综合评价 法, 运 以塑件成型后 的最大翘 曲变形量、 体积收缩率和表 面缩痕指数 3个 目标值 为基础 , 构建 出了综合评价指标 . 通过对综合 评价指标的极 差 分析 , 得到模具温度、 填充 时间、 保压参数 、 熔体温度及 冷却时间等注塑工艺参数 对综合评价指标 的影 响程度. 通
基于cae的pp塑料件注射成型工艺参数的影响及优化
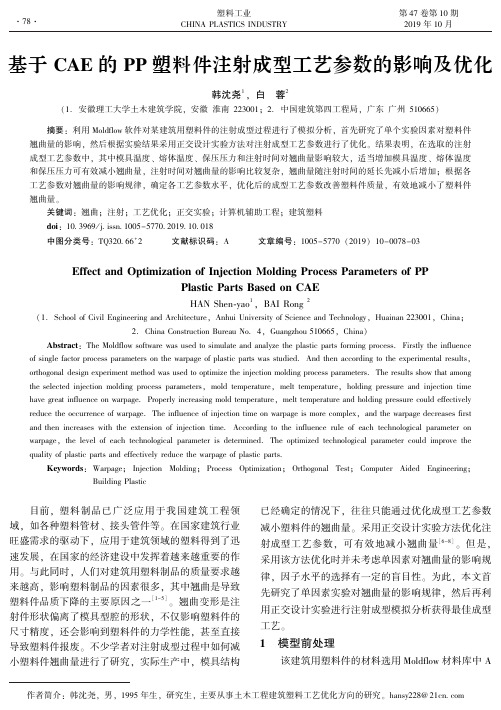
翘曲量的影响ꎬ 然后根据实验结果采用正交设计实验方法对注射成型工艺参数进行了优化ꎮ 结果表明ꎬ 在选取的注射
成型工艺参数中ꎬ 其中模具温度、 熔体温度、 保压压力和注射时间对翘曲量影响较大ꎬ 适当增加模具温度、 熔体温度
Plastic Parts Based on CAE
HAN Shen ̄yao1 ꎬ BAI Rong
2
(1. School of Civil Engineering and Architectureꎬ Anhui University of Science and Technologyꎬ Huainan 223001ꎬ Chinaꎻ
第 47 卷第 10 期
2019 年 10 月
塑料工业
CHINA PLASTICS INDUSTRY
78
基于 CAE 的 PP 塑料件注射成型工艺参数的影响及优化
韩沈尧1 ꎬ 白 蓉2
(1. 安徽理工大学土木建筑学院ꎬ 安徽 淮南 223001ꎻ 2. 中国建筑第四工程局ꎬ 广东 广州 510665)
域ꎬ 如各种塑料பைடு நூலகம்材、 接头管件等ꎮ 在国家建筑行业
减小塑料件的翘曲量ꎮ 采用正交设计实验方法优化注
旺盛需求的驱动下ꎬ 应用于建筑领域的塑料得到了迅
射成型工艺参数ꎬ 可有效地减小翘曲量 [6-8] ꎮ 但是ꎬ
速发展ꎬ 在国家的经济建设中发挥着越来越重要的作
用ꎮ 与此同时ꎬ 人们对建筑用塑料制品的质量要求越
the selected injection molding process parametersꎬ mold temperatureꎬ melt temperatureꎬ holding pressure and injection time
基于正交试验的注射成型工艺参数优化方法研究

A@ B2 0. 982 0. 989 0. 992 0. 010
C 0. 989 0. 983 0. 990 0. 007
C2
D 0. 996 0. 989 0. 978 0. 018
D3
E 1. 001 0. 986 0. 976 0. 025
B @ C1 0. 997 0. 979 0. 987 0. 018
注: k 1、k 2、k 3 ) ) ) 1、2、3 水平的翘曲值之和; k 12、k 22、k 32) ) ) 1、2、3 水平的翘曲值之和的平方; SSj ) ) ) j 因 数偏差 平方和。
表 5 翘曲变形方差分析表
方差来源 A B
A@ B C D E
B@ C F
误差e 误差e 总和
偏差平方和 0. 100 4 0. 107 0 0. 008 5 0. 010 4 0. 010 0. 008 8 0. 000 6 0. 002 7 0. 008 6 0. 020 4 0. 257 0
模具工业 2010 年第 36 卷第 6 期
9
3. 2 试验结果精度与因素作用影响分析 应用方差法可精确估计试验误差的大小, 考察
各因素对试验结果的影响程度、作用是否显著, 分 析交互作用的影响大小, 确定最终优化方案。在考
察各因素的效应或交互作用是否显著中, 需要通过 F 检验法进行判断。由表 4、5 中的分析数据可计算 出各因素以及因素间的交互作用的 F 因素值, 并用 F 临界值进行判断, 得出表 5 所示方差数据分析结
D
E B @ C1 G
e 1 B @ C2 e 2
e3
1 1( 45) 1( 170) 1
1
1( 1) 1( 15) 1( 40)
基于DOE实验设计方法的聚丙烯焊接工艺优化
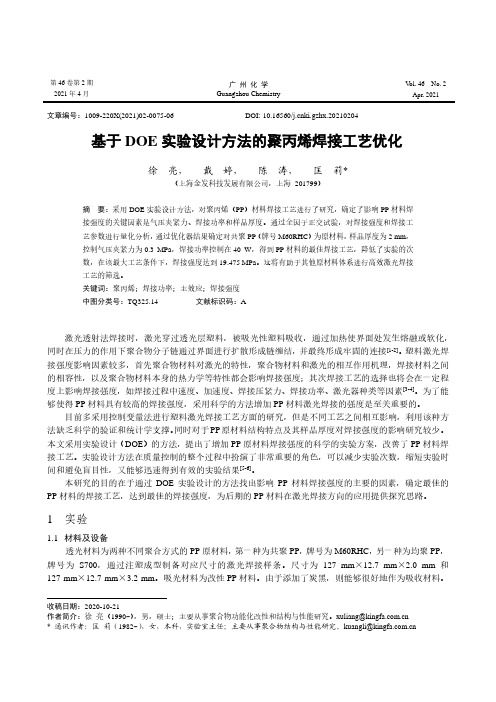
第46卷第2期2021年4月广州化学Guangzhou ChemistryV ol. 46 No. 2Apr. 2021文章编号:1009-220X(2021)02-0075-06 DOI:10.16560/ki.gzhx.20210204基于DOE实验设计方法的聚丙烯焊接工艺优化徐亮,戴婷,陈涛,匡莉*(上海金发科技发展有限公司,上海201799)摘要:采用DOE实验设计方法,对聚丙烯(PP)材料焊接工艺进行了研究,确定了影响PP材料焊接强度的关键因素是气压夹紧力、焊接功率和样品厚度。
通过全因子正交试验,对焊接强度和焊接工艺参数进行量化分析,通过优化器结果确定对共聚PP(牌号M60RHC)为原材料,样品厚度为2 mm,控制气压夹紧力为0.3 MPa,焊接功率控制在40 W,得到PP材料的最佳焊接工艺,降低了实验的次数,在该最大工艺条件下,焊接强度达到19.475 MPa。
这将有助于其他原材料体系进行高效激光焊接工艺的筛选。
关键词:聚丙烯;焊接功率;主效应;焊接强度中图分类号:TQ325.14 文献标识码:A激光透射法焊接时,激光穿过透光层塑料,被吸光性塑料吸收,通过加热使界面处发生熔融或软化,同时在压力的作用下聚合物分子链通过界面进行扩散形成链缠结,并最终形成牢固的连接[1-2]。
塑料激光焊接强度影响因素较多,首先聚合物材料对激光的特性,聚合物材料和激光的相互作用机理,焊接材料之间的相容性,以及聚合物材料本身的热力学等特性都会影响焊接强度;其次焊接工艺的选择也将会在一定程度上影响焊接强度,如焊接过程中速度、加速度、焊接压紧力、焊接功率、激光器种类等因素[3-4]。
为了能够使得PP材料具有较高的焊接强度,采用科学的方法增加PP材料激光焊接的强度是至关重要的。
目前多采用控制变量法进行塑料激光焊接工艺方面的研究,但是不同工艺之间相互影响,利用该种方法缺乏科学的验证和统计学支撑。
同时对于PP原材料结构特点及其样品厚度对焊接强度的影响研究较少。
基于正交试验和Moldflow的注塑制品表面质量成型工艺优化设计

翘 曲量 以及缩痕指数 的影响 , 并通过 对试验数 据的 分析 处理 , 得到优 化 的成 型 工艺参数 , 而 实现 了注 塑工艺参数 从
设计的优化。
关键词
M lf w 正 交试 验 od o l
注塑
翘 曲 缩痕
目前注 塑制 品在社 会生 活 的各个领 域 已经得 到 了相 当普遍 的应 用 。 随着 科 技 的发 展 , 注塑 制 品也
1 手机 电池盖材 料 的选择
22 .
最 图 2 最 佳 浇 口位 置分 析结 果
正交 试验
笔 者设 计 选 用 的注 塑 制 品为 手 机 电池 盖 , 图 如
( ) 验 指标 的确 定 1试
1 所示 。制 品要 求表 面光 滑 , 耐磨 , 且 有 足够 的强 并
度, 选用 具 有 良好 综 合 性 能 的 ( 烯 腈/ 二 烯/ 丙 丁 苯
l 2 3 1 2 3 1 2 3
C
1 2 3 2 3 1 3 】 2
翘 曲量/ mm
越 来越精 密化 、 杂 化 , 复 同时对 制 品 的形 状 、 寸 精 尺 度 以及 表面质 量 的要 求 也 越来 越 高 , 而要 获 得 高 质
置 较好 的 区域 , 果如 图 2所 示 。由图 2可知 , 口 结 浇
位 置处 在制 品 中间部 分 比较 好 。
最佳 浇 口位置
=
10 0 .0
最l 好
量 的注塑 制 品 , 注射 成 型 工 艺 的优 化 设 计 则 是 必不 可少 的。笔者采 用正 交试 验法 和 Mo f w仿 真模拟 lo d l 相结 合 的方 法 , 助 C E软 件平 台 , 借 A 通过 试 验分 析 ,
基于CAE和DOE技术的注射成型工艺优化

基于C AE和DOE技术的注射成型工艺优化黄松王喜顺(华南理工大学机械与汽车工程学院,广州510640)摘要以打印机上盖为例,以体积收缩率、翘曲量和沉降斑指数为考察指标,结合CAE和DOE技术研究了模具温度、熔体温度、注射时间、保压压力和保压时间五个工艺参数对考察指标的影响,用DOE软件回归拟合得到体积收缩率、翘曲和沉降斑指数的预测模型,并运用该模型求解最佳的工艺参数,通过试验验证了该方法的可行性。
关键词注射成型CAE DOE工艺参数优化随着塑料工业的飞速发展,许多企业使用C AE 技术对注射成型过程进行模拟分析并预测潜在的问题,以提高一次试模率,达到降低生产成本、缩短生产周期的目的。
成型工艺参数的优化设置在一定范围内能克服成型缺陷,提高制品质量。
但影响制品质量的工艺参数比较多,而且各参数之间存在非线性和强耦合特性,设计师往往需要花费大量的时间进行C AE模拟才能获得合适的参数组合。
为了获得最佳的工艺参数组合,众多学者对此进行了研究, G.H.Choi等[1]应用ANN技术建立工艺参数和制品质量指标之间的神经网络关系模型,并采用自适应优化算法优化工艺参数。
郑晓培等[2]结合CAE和Taguch i技术研究了工艺参数对(丙烯晴/丁二烯/苯乙烯)共聚物、高密度聚乙烯和聚丙烯注塑制品沉降斑的影响,并对工艺参数进行了优化。
H.Okte m 等[3]基于田口试验方法、信噪比及均方差分析等方法,利用三水平的L27和L9等正交试验表,以最大翘曲量和最大体积收缩率为目标,对薄壳塑料制品的注射成型参数进行了优化设计。
钟浩东等[4]提出一个利用注射成型软件Mol d fl o w与遗传算法结合对熔接痕长度和位置进行优化的方法,经过多代搜索,最终获得对应于熔接痕长度与位置最佳的注射时间、熔体温度、模具温度、浇口位置等工艺参数。
D OE技术是一种研究试验数据的获得和科学地分析处理试验数据与结果的方法。
回归分析是其常用的数据分析方法,回归分析的主要内容为:¹从一组数据出发确定某些变量之间的定量关系式,即建立数学模型并估计其中的未知参数。
基于DOE的工艺参数及交互作用对塑件翘曲变形影响

( 1 . Sc ho o l o f El e c t r on i c a nd M e c ha ni c a l Eng i ne e r i ng, Pa n z hi hu a U n i v e r s i t y, Pa n z h i hu a, Si c hua n, 61 7 0 0 0;2 .Fa c ul t y of Me c ha ni c a l a nd El e c t r i c a l Eng i ne e r i ng, Kun mi n g Uni v e r s i t y of Sc i e nc e a n d Te c h no l o gy, Kunmi n g, Yu nna n, 6 50 0 9 3) Ab s t r a c t : Ta ki n g t h e c a r s ha d e a s a n e x a mpl e, t he e f f e c t s of p r o c e s s p a r a me t e r s a nd t he i r i nt e r a c t i o n o n t he wa r p a ge we r e s t ud i e d by M ol d f l o w a nd DOE. The f a c t o r s o f r e l a t i n g t o t h e pr o du c t q ua l i t y we r e s c r e e ne d ou t a nd f u r t he r o pt i mi z e d . Or t ho go n a l t e s t pr o g r a m wa s e s t a bl i s he d, a n d t h e s c i e n t i f i c b a s i s o f r e a s o na b l e s e l e c t i ng p r oc e s s p a —
基于正交试验的注射成型工艺参数优化方法研究

注: k 1、k 2、k 3 ) ) ) 1、2、3 水平的翘曲值之和; k 12、k 22、k 32) ) ) 1、2、3 水平的翘曲值之和的平方; SSj ) ) ) j 因 数偏差 平方和。
表 5 翘曲变形方差分析表
方差来源 A B
A@ B C D E
B@ C F
误差e 误差e 总和
偏差平方和 0. 100 4 0. 107 0 0. 008 5 0. 010 4 0. 010 0. 008 8 0. 000 6 0. 002 7 0. 008 6 0. 020 4 0. 257 0
Optimization of injection molding process parameters based on orthogonal experiment
HU Yong, XIE Wen_ling, WANG Jia ( Sichuan Provincial Key Laboratory of Process Equipment and Control, Sichuan University of Science
1引 言 注射成型过程中注射工艺参数的选择直接影
响制品质量。为此, 结合正交试验法和注射模拟分 析软件 Moldflow, 设计成 型工艺 试验方 案, 运 用 Moldflow 软件进行注射成型模拟, 对获取的试验结 果进行极差分析、方差分析, 确定各因素及其交互 作用对试验指标影响的显著程度, 提出试验因素的 最优水平和试验范围内的最优组合, 即注射工艺参
E3
)
G 0. 993 0. 996 0. 973 0. 023
B @ C2 0. 990 0. 983 0. 990 0. 007
G3
)
表 4 翘曲变形试验数据分析
基于DOE的实验设计在产品质量改进中的应用研究
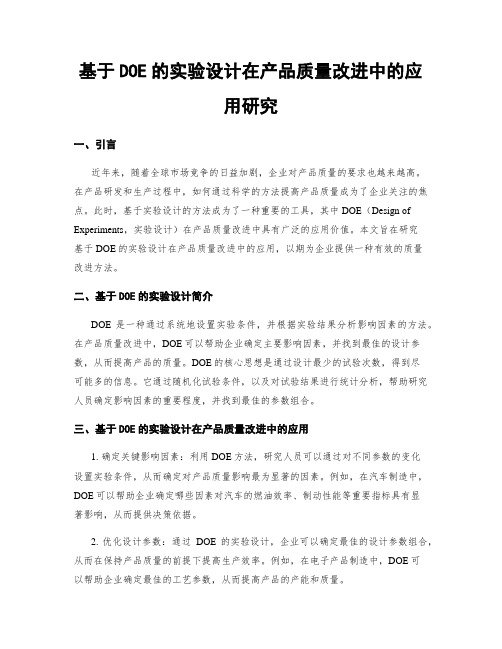
基于DOE的实验设计在产品质量改进中的应用研究一、引言近年来,随着全球市场竞争的日益加剧,企业对产品质量的要求也越来越高。
在产品研发和生产过程中,如何通过科学的方法提高产品质量成为了企业关注的焦点。
此时,基于实验设计的方法成为了一种重要的工具,其中DOE(Design of Experiments,实验设计)在产品质量改进中具有广泛的应用价值。
本文旨在研究基于DOE的实验设计在产品质量改进中的应用,以期为企业提供一种有效的质量改进方法。
二、基于DOE的实验设计简介DOE是一种通过系统地设置实验条件,并根据实验结果分析影响因素的方法。
在产品质量改进中,DOE可以帮助企业确定主要影响因素,并找到最佳的设计参数,从而提高产品的质量。
DOE的核心思想是通过设计最少的试验次数,得到尽可能多的信息。
它通过随机化试验条件,以及对试验结果进行统计分析,帮助研究人员确定影响因素的重要程度,并找到最佳的参数组合。
三、基于DOE的实验设计在产品质量改进中的应用1. 确定关键影响因素:利用DOE方法,研究人员可以通过对不同参数的变化设置实验条件,从而确定对产品质量影响最为显著的因素。
例如,在汽车制造中,DOE可以帮助企业确定哪些因素对汽车的燃油效率、制动性能等重要指标具有显著影响,从而提供决策依据。
2. 优化设计参数:通过DOE的实验设计,企业可以确定最佳的设计参数组合,从而在保持产品质量的前提下提高生产效率。
例如,在电子产品制造中,DOE可以帮助企业确定最佳的工艺参数,从而提高产品的产能和质量。
3. 识别交互影响:在某些情况下,不同因素之间可能存在交互作用,即一个因素的变化会影响其他因素的效果。
通过DOE的实验设计,企业可以确定不同因素之间的交互影响,并找到最佳的参数组合。
例如,在药物研发中,DOE可以帮助企业确定药物配方中不同成分之间的交互影响,从而提高药物的疗效。
4. 验证改进效果:DOE方法可以帮助企业设计不同条件下的实验,通过对试验结果进行分析,验证质量改进的效果。
基于CAE与正交试验的多指标注塑成型工艺参数优化
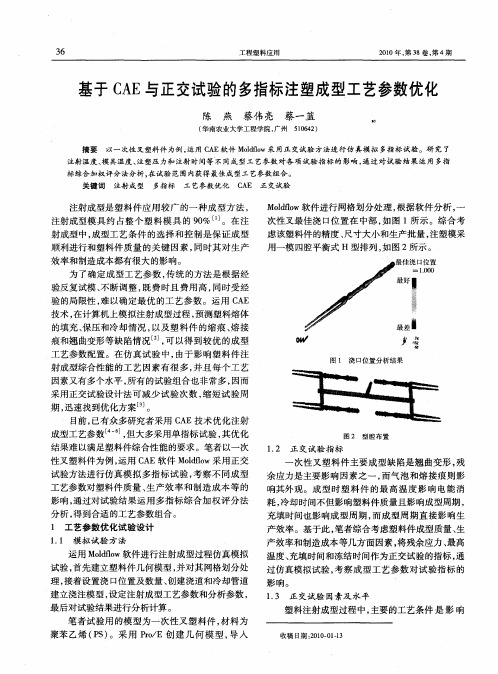
轻
图 1 浇 口位 置 分 析 结 果
期 , 速找 到优化 方案 J 迅 。 目前 , 已有众 多研究 者采 用 C E技术 优 化 注射 A 成型工艺参数 J但大多采用单指标试验 , , 其优化 结 果难 以满 足塑料 件综 合性 能 的要求 。笔 者 以一次 性叉 塑料 件为 例 , 运用 C E软件 Mo fw采 用 正交 A ll do
1 工艺 参数 优化 试验 设计
1 1 模拟 试验 方 法 .
余 应力 是 主要影 响 因 素 之一 , 气 泡 和熔 接 痕则 影 而 响其外 观 。成 型 时 塑 料 件 的最 高 温 度 影 响 电能 消 耗, 冷却 时间不但 影 响塑料 件 质量且 影 响成 型周期 , 充填 时间也 影 响成 型 周期 , 成 型周 期 直 接 影 响 生 而
2 结果 与分 析
间。笔者以注射温度 、 模具温度、 注塑压力和注射时 间 4个成 型 工艺 参 数作 为正 交 试验 因素 , 分别 用 A、
B、 、 c D表 示 。假设 各 因素 之 间 不存 在 交 互 作 用 , 每 个 因素设 置 3个 水 平 , 用 。3 ) 选 ( 正交 表 进 行 试 验 设计 。正 交试 验 的 因素水平 根 据 Mo f w软件 系统 lo d l
工艺参 数 配置 。在 仿 真试 验 中 , 于影 响 塑 料 件 注 由 射成 型综 合 性能 的 工 艺 因素 有 很 多 , 且 每 个 工 艺 并 因素又有 多个 水平 , 有 的试验组 合 也非 常多 , 所 因而
采 用正交 试 验设计 法 可 减 少 试 验 次 数 , 短试 验 周 缩
验反 复试模 、 断调 整 , 费时 且 费 用 高 , 不 既 同时 受经 验 的局 限性 , 以确 定 最 优 的工 艺 参 数 。运 用 C E 难 A
复杂塑件的注塑成型模拟及工艺参数优化的开题报告
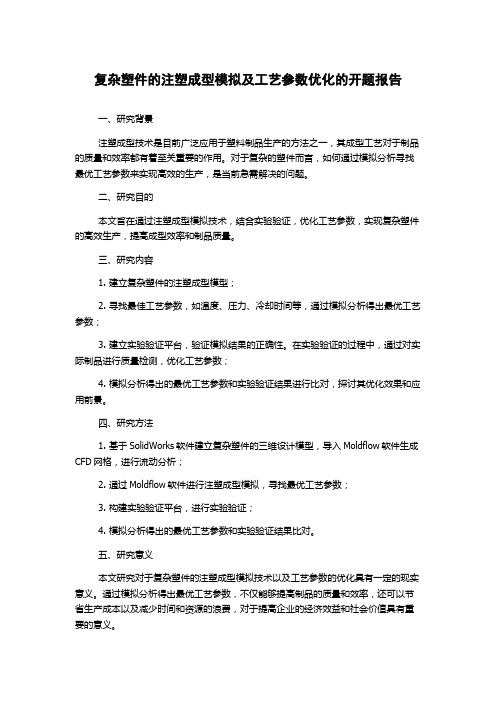
复杂塑件的注塑成型模拟及工艺参数优化的开题报告
一、研究背景
注塑成型技术是目前广泛应用于塑料制品生产的方法之一,其成型工艺对于制品的质量和效率都有着至关重要的作用。
对于复杂的塑件而言,如何通过模拟分析寻找最优工艺参数来实现高效的生产,是当前急需解决的问题。
二、研究目的
本文旨在通过注塑成型模拟技术,结合实验验证,优化工艺参数,实现复杂塑件的高效生产,提高成型效率和制品质量。
三、研究内容
1. 建立复杂塑件的注塑成型模型;
2. 寻找最佳工艺参数,如温度、压力、冷却时间等,通过模拟分析得出最优工艺参数;
3. 建立实验验证平台,验证模拟结果的正确性。
在实验验证的过程中,通过对实际制品进行质量检测,优化工艺参数;
4. 模拟分析得出的最优工艺参数和实验验证结果进行比对,探讨其优化效果和应用前景。
四、研究方法
1. 基于SolidWorks软件建立复杂塑件的三维设计模型,导入Moldflow软件生成CFD网格,进行流动分析;
2. 通过Moldflow软件进行注塑成型模拟,寻找最优工艺参数;
3. 构建实验验证平台,进行实验验证;
4. 模拟分析得出的最优工艺参数和实验验证结果比对。
五、研究意义
本文研究对于复杂塑件的注塑成型模拟技术以及工艺参数的优化具有一定的现实意义。
通过模拟分析得出最优工艺参数,不仅能够提高制品的质量和效率,还可以节省生产成本以及减少时间和资源的浪费,对于提高企业的经济效益和社会价值具有重要的意义。
_运用DOE实验设计优化锌铝合金压铸件电镀工艺参数
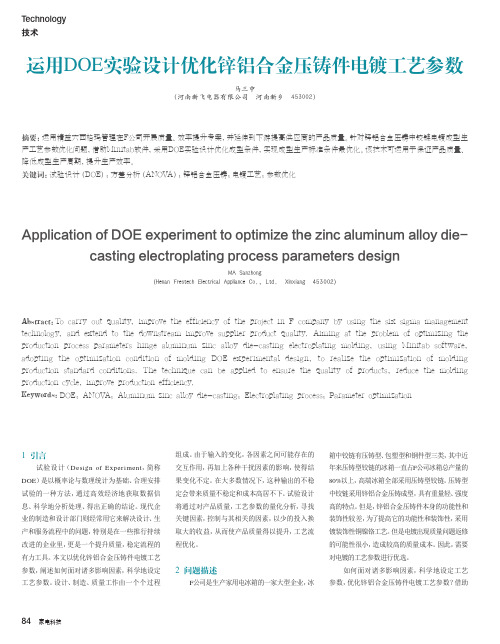
运用DOE实验设计优化锌铝合金压铸件电镀工艺参数
马三中 (河南新飞电器有限公司 河南新乡 453002)
摘要:运用精益六西格玛管理在F公司开展质量、效率提升专案,并延伸到下游提高供应商的产品质量。针对锌铝合金压铸中铰链电镀成型生 产工艺参数优化问题,借助Minitab软件,采用DOE实验设计优化成型条件,实现成型生产标准条件最优化。该技术可运用于保证产品质量、 降低成型生产周期,提升生产效率。 关键词:试验设计(DOE);方差分析(ANOVA);锌铝合金压铸;电镀工艺;参数优化
参考文献 [1] 马逢时等编著. 《六西格玛管理统计指南》. 中国人民 大学出版社. 2008 [2] 马林,何桢主编. 《六西格玛管理》. 中国人民大学出 版社. 2008 [3] 巫江,宋宏春,李小联,魏丹. 基于DOE的注塑成型工 艺参数优化. 制造业信息化. 2011(1) [4] 罗军,宋德朝. 基于Minitab的质量控制技术在制造过 程中的应用[J]. 现代制造工程.2009(2):10-20 [5] 王爱荣. 实用锌铝合金压铸件镀装饰性铜镍铬工艺. 腐蚀与防护. 2002(3)
图2 因子正态、效应图
图3 各因子主效应及交互效应图
图4 立方图
参数设置进行批量生产。 3.3.10 铬层厚度提高改善效果验证 我们收集5月6~18日的铬层厚度数据25组
(每组4个数据),进行了正态性检验,工序能力 分析,Cpk明显提高。从Xbar-R图中可以看出铬 层厚度得到了有效监控,均值达到了0.57mm。我 们运用假设检验以验证改进前后平均铬层厚度 是否提高:从改进前和改进后的产品中随机抽取 N=10的样品,测量其铬层厚度。
差的正态性检验图符合正态分布。误差的分布相 当随机,残差与观测之间没有明显关系。
基于正交实验的注塑件成型工艺参数优化设计[设计+开题+综述]
![基于正交实验的注塑件成型工艺参数优化设计[设计+开题+综述]](https://img.taocdn.com/s3/m/a310e964d15abe23492f4d49.png)
开题报告机械设计制造及其自动化基于正交实验的注塑件成型工艺参数优化设计一、选题的背景与意义随着塑料制品在工业中的应用日益普遍,塑料制品被广泛的应用应用于工业、农业及日常生活中。
尤其是在宁波,可以说宁波是注塑产品的家乡。
近年来,塑料模具发展最为迅速,在国内模具工业产值中塑料模具所占比例不断扩大。
同时各种注塑机的发展也是极为快速。
塑料模具与注塑的迅速发展是和注塑件产品的发展有直接关系的,可见近年我国注塑件产品的发展是多么惊人。
但是与发达国家相比,国内的模具技术要落后国外近20年。
因此在注塑产品的进一步发展利用上我们还任重而道远。
同样,由于注射成型过程中的成型条件(如注射压力、螺杆背压、注射速度、注射量、锁模力、料筒温度、掸具温度)的选择不当或模具本身存在的问题,因而会使注塑制品出现许多不良现象和缺陷。
这是该领域的一大难题,解决这一难题对注塑件产品的发展有举足轻重的意义。
二、研究的基本内容与拟解决的主要问题:2.1基本内容:利用Moldflow软件对一款注塑件进行成型质量分析。
熟悉和掌握完整的注塑模具的流动分析过程,通过设计正交实验的方法来获得比较合理的成型工艺参数的方法2.2拟解决的主要问题:学习Moldflow,熟练掌握该软件的操作,从而能够利用其进行注塑成型质量分析;学习正交实验的设计方法与应用;通过设计正交实验进行不同成型工艺的流动分析,以缩痕最小为目标确定最佳的成型工艺;三、研究的方法与技术路线:3.1研究方法:3.1.1 Moldflow软件进行注塑成型质量分析的方法;3.1.1.1 几何建模3.1.1.2 网格划分3.1.1.3 浇口位置及数量的确定3.1.1.4 材料及工艺参数设置3.1.2 正交实验的设计方法;基本试验方法:3.1.2.1 取出试验的影响因素、水平,理出因素、水平表;3.1.2.2 在确定因素、水平之后,就要选一张合适的正交表来安排实验方案;3.1.2.3 按照制作的正交表进行试验;3.1.2.4 用正交表分析实验结果—极差分析,得出影响大的因素;3.1.2.5 得出结论。
基于响应面模型的注塑件精密成型工艺优化
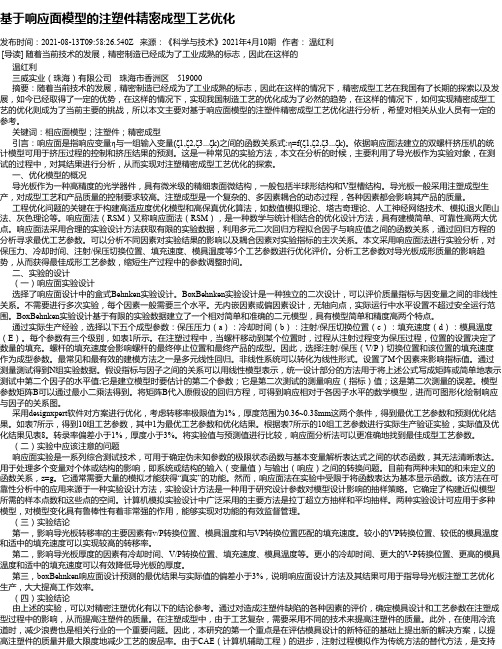
基于响应面模型的注塑件精密成型工艺优化发布时间:2021-08-13T09:58:26.540Z 来源:《科学与技术》2021年4月10期作者:温红利[导读] 随着当前技术的发展,精密制造已经成为了工业成熟的标志,因此在这样的温红利三威实业(珠海)有限公司珠海市香洲区 519000摘要:随着当前技术的发展,精密制造已经成为了工业成熟的标志,因此在这样的情况下,精密成型工艺在我国有了长期的探索以及发展,如今已经取得了一定的优势,在这样的情况下,实现我国制造工艺的优化成为了必然的趋势,在这样的情况下,如何实现精密成型工艺的优化则成为了当前主要的挑战,所以本文主要对基于响应面模型的注塑件精密成型工艺优化进行分析,希望对相关从业人员有一定的参考。
关键词:相应面模型;注塑件;精密成型引言:响应面是指响应变量η与一组输入变量(ζ1,ζ2,ζ3...ζk)之间的函数关系式:η=f(ζ1,ζ2,ζ3...ζk)。
依据响应面法建立的双螺杆挤压机的统计模型可用于挤压过程的控制和挤压结果的预测。
这是一种常见的实验方法,本文在分析的时候,主要利用了导光板作为实验对象,在测试的过程中,对其结果进行分析,从而实现对注塑精密成型工艺优化的探索。
一、优化模型的概况导光板作为一种高精度的光学器件,具有微米级的精细表面微结构,一般包括半球形结构和V型槽结构。
导光板一般采用注塑成型生产,对成型工艺和产品质量的控制要求较高。
注塑成型是一个复杂的、多因素耦合的动态过程,各种因素都会影响其产品的质量。
工程优化问题的关键在于构建高适应度优化模型和高保真优化算法,如数值模拟理论、塔古奇理论、人工神经网络技术、模拟退火爬山法、灰色理论等。
响应面法(RSM)又称响应面法(RSM),是一种数学与统计相结合的优化设计方法,具有建模简单、可靠性高两大优点。
响应面法采用合理的实验设计方法获取有限的实验数据,利用多元二次回归方程拟合因子与响应值之间的函数关系,通过回归方程的分析寻求最优工艺参数。
基于实例的注塑模设计与成型工艺优化 方里元
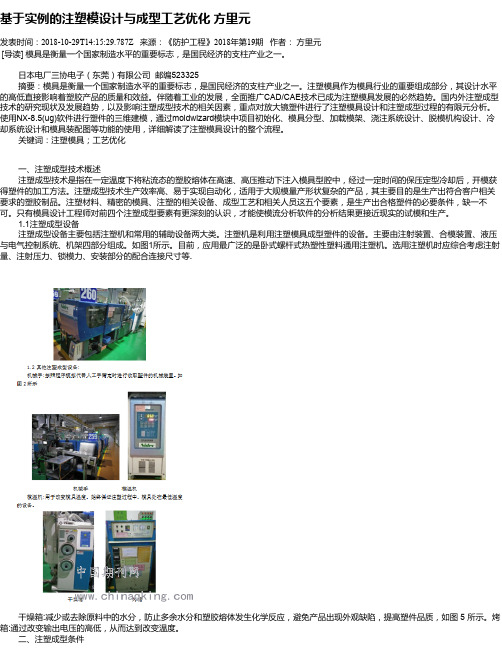
基于实例的注塑模设计与成型工艺优化方里元发表时间:2018-10-29T14:15:29.787Z 来源:《防护工程》2018年第19期作者:方里元[导读] 模具是衡量一个国家制造水平的重要标志,是国民经济的支柱产业之一。
日本电厂三协电子(东莞)有限公司邮编523325 摘要:模具是衡量一个国家制造水平的重要标志,是国民经济的支柱产业之一。
注塑模具作为模具行业的重要组成部分,其设计水平的高低直接影响着塑胶产品的质量和效益。
伴随着工业的发展,全面推广CAD/CAE技术已成为注塑模具发展的必然趋势。
国内外注塑成型技术的研究现状及发展趋势,以及影响注塑成型技术的相关因素,重点对放大镜塑件进行了注塑模具设计和注塑成型过程的有限元分析。
使用NX-8.5(ug)软件进行塑件的三维建模,通过moldwizard模块中项目初始化、模具分型、加载模架、浇注系统设计、脱模机构设计、冷却系统设计和模具装配图等功能的使用,详细解读了注塑模具设计的整个流程。
关键词:注塑模具;工艺优化一、注塑成型技术概述注塑成型技术是指在一定温度下将粘流态的塑胶熔体在高速、高压推动下注入模具型腔中,经过一定时间的保压定型冷却后,开模获得塑件的加工方法。
注塑成型技术生产效率高、易于实现自动化,适用于大规模量产形状复杂的产品,其主要目的是生产出符合客户相关要求的塑胶制品。
注塑材料、精密的模具、注塑的相关设备、成型工艺和相关人员这五个要素,是生产出合格塑件的必要条件,缺一不可。
只有模具设计工程师对前四个注塑成型要素有更深刻的认识,才能使模流分析软件的分析结果更接近现实的试模和生产。
1.1注塑成型设备注塑成型设备主要包括注塑机和常用的辅助设备两大类。
注塑机是利用注塑模具成型塑件的设备。
主要由注射装置、合模装置、液压与电气控制系统、机架四部分组成。
如图1所示。
目前,应用最广泛的是卧式螺杆式热塑性塑料通用注塑机。
选用注塑机时应综合考虑注射量、注射压力、锁模力、安装部分的配合连接尺寸等.干燥箱:减少或去除原料中的水分,防止多余水分和塑胶熔体发生化学反应,避免产品出现外观缺陷,提高塑件品质,如图 5 所示。
基于遗传算法和Moldflow的注塑过程优化与仿真
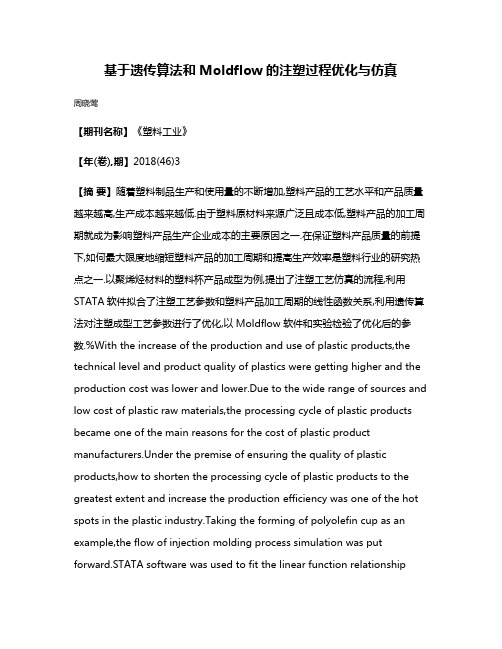
基于遗传算法和Moldflow的注塑过程优化与仿真周晓莺【期刊名称】《塑料工业》【年(卷),期】2018(46)3【摘要】随着塑料制品生产和使用量的不断增加,塑料产品的工艺水平和产品质量越来越高,生产成本越来越低.由于塑料原材料来源广泛且成本低,塑料产品的加工周期就成为影响塑料产品生产企业成本的主要原因之一.在保证塑料产品质量的前提下,如何最大限度地缩短塑料产品的加工周期和提高生产效率是塑料行业的研究热点之一.以聚烯烃材料的塑料杯产品成型为例,提出了注塑工艺仿真的流程,利用STATA软件拟合了注塑工艺参数和塑料产品加工周期的线性函数关系,利用遗传算法对注塑成型工艺参数进行了优化,以Moldflow软件和实验检验了优化后的参数.%With the increase of the production and use of plastic products,the technical level and product quality of plastics were getting higher and the production cost was lower and lower.Due to the wide range of sources and low cost of plastic raw materials,the processing cycle of plastic products became one of the main reasons for the cost of plastic product manufacturers.Under the premise of ensuring the quality of plastic products,how to shorten the processing cycle of plastic products to the greatest extent and increase the production efficiency was one of the hot spots in the plastic industry.Taking the forming of polyolefin cup as an example,the flow of injection molding process simulation was put forward.STATA software was used to fit the linear function relationshipbetween injection molding process parameters and processing cycle of plastic products,the genetic algorithm was used to optimize the injection molding process parameters,and Moldflow software and experiments were used to test the optimized parameters.【总页数】4页(P67-70)【作者】周晓莺【作者单位】义乌工商职业技术学院机电信息学院,浙江义乌322000【正文语种】中文【中图分类】TQ320.66+2【相关文献】1.基于遗传算法的注塑成型充模过程优化 [J], 刘春太;肖长江;申长雨2.基于Moldflow的手机外壳注塑成型过程中充填分析及设计优化 [J], 吴燕华;王宏霞;朱芬芳3.微孔注塑成型过程的Moldflow模拟仿真 [J], 韩云;林有希4.AutodeskMoldflow注塑成型仿真软件实现塑料件和注塑模具的全方位优化[J],5.基于Moldflow的注塑阀门应用与仿真 [J], 修雪颖;汪圣尧;黄兆阁因版权原因,仅展示原文概要,查看原文内容请购买。
DOE在注射成型工艺参数多目标优化中的应用
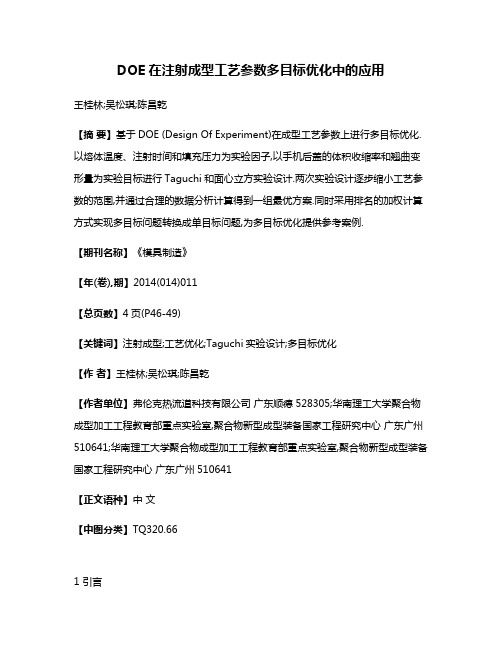
DOE在注射成型工艺参数多目标优化中的应用王桂林;吴松琪;陈昌乾【摘要】基于DOE (Design Of Experiment)在成型工艺参数上进行多目标优化.以熔体温度、注射时间和填充压力为实验因子,以手机后盖的体积收缩率和翘曲变形量为实验目标进行Taguchi和面心立方实验设计.两次实验设计逐步缩小工艺参数的范围,并通过合理的数据分析计算得到一组最优方案.同时采用排名的加权计算方式实现多目标问题转换成单目标问题,为多目标优化提供参考案例.【期刊名称】《模具制造》【年(卷),期】2014(014)011【总页数】4页(P46-49)【关键词】注射成型;工艺优化;Taguchi实验设计;多目标优化【作者】王桂林;吴松琪;陈昌乾【作者单位】弗伦克热流道科技有限公司广东顺德528305;华南理工大学聚合物成型加工工程教育部重点实验室,聚合物新型成型装备国家工程研究中心广东广州510641;华南理工大学聚合物成型加工工程教育部重点实验室,聚合物新型成型装备国家工程研究中心广东广州510641【正文语种】中文【中图分类】TQ320.661 引言注射成型的过程中受到多种工艺因素的影响,如熔体温度、注射时间、填充压力、保压时间等,同时熔体在多因素环境下的流动过程十分复杂。
另外,随着塑件的复杂化、精密化,塑件对各项目标参数都有严格的要求。
但是面对复杂注射过程,并没有简单的数学关系可以指导设置合理成型的工艺参数。
以前为了寻找较优的工艺参数方案,需要不断试模,针对塑件进行检测分析,费时、费力、成本巨大。
目前,CAE技术虽然可以节省大量成本,但CAE技术的应用仅仅限于在计算机上的反复试验,严重依赖于设计者的经验,尤其很难获得最优化工艺,将CAE技术与DOE 的结合,可方便实现工艺的优化,提高一次试模成功率,降低成本,提高生产效率[1]。
另外,多因素单目标的实验较为简单,可以快速得到较优方案,但是决定塑件的质量是受多方面因素影响的,多因素多目标的优化方案更具有实际意义[2]。
- 1、下载文档前请自行甄别文档内容的完整性,平台不提供额外的编辑、内容补充、找答案等附加服务。
- 2、"仅部分预览"的文档,不可在线预览部分如存在完整性等问题,可反馈申请退款(可完整预览的文档不适用该条件!)。
- 3、如文档侵犯您的权益,请联系客服反馈,我们会尽快为您处理(人工客服工作时间:9:00-18:30)。
摘要注塑成型制品质量控制方面存在的困难主要来源于力学的复杂性和在温度、压力波动下材料行为的不可预测性,研究工艺参数对注塑制品质量的影响关系,建立工艺参数与制品质量之间的关系模型,并用DOE法对工艺进行仿真优化是注塑制品工艺优化的前提。
本文选用半结晶型和无定型ABS两种材料,针对一维流动平板两个方向上的收缩、强度,熔接线强度、制品重量及沉降斑等质量指标进行了实验研究。
研究了工艺参数对质量指标的影响及因素之间的交互作用。
本文主要工作包括以下几方面: 1 工艺参数对制品质量的交互影响分析;2 应用DOE法结合析因分析结果;3.CAE技术结合DOE法进行设计,并用MOLDFLOW进行仿真分析,为质量控制技术提供了工艺模型。
关键词: 注塑成型,正交实验,Moldflow,三维建模,工艺仿真优化,实验设计AbstractQuality control of injection molding products, mainly difficulties from that exist in the complexity of process dynamics and in the temperature and pressure fluctuations unpredictable behavior of materials, of process parameters on product quality of injection molding between the relationship,DOE method with simulation and optimization technology of injection molding products, process optimization is a prerequisite.Semi-crystalline and amorphous ABS we usd in this paper,For a flat that two-dimensional flow direction shrinkage, strength, weld line strength, weight and sink marks and other products, the quality indicators studied. In this paper, include the following:1. Process parameters on product quality of interaction analysis;2. Application of DOE method with the results of factorial analysis;3. CAE design method combined with DOE,Simulation and analysis with MOLDFLOW,quality control technology provides for the process model.Key words:Injection Molding,Orthogonal,Moldflow,Three-dimensional modeling,Process simulation and optimization,design of experiment.目录1.1 引言 (1)1.2 注塑成型工艺过程简介 (1)1.3注塑成型工艺的发展趋势 (2)1.4 注塑成型工艺优化国内外研究概况 (4)1.5本文主要工作内容及其意义 (6)2. 注塑成型工艺参数影响性分析 (8)2.1 压力参数分析 (8)2.1.1注塑压力 (8)2.1.2保压压力 (8)2.1.3 塑化压力(背压) (8)2.2 温度参数分析 (9)2.2.1模具温度 (9)2.2.2熔体温度 (9)2.3时间参数分析 (9)2.3.1注射时间 (9)2.3.2保压时间 (10)2.4注射速度分析 (10)3. 基于DOE法的注塑成型仿真优化 (11)3.1软件Moldflow以及正交实验助手的介绍 (12)3.1.1 moldflow软件简介 (12)3.1.2 正交实验助手介绍 (12)3.2材料的选取及模型的导入 (14)3.3本次实验设计法的分析理论依据 (17)3.3.1.实验基本参数取值范围的确定及输入 (17)3.3.2.正交表的设置及数据生成 (18)3.3.3实验分析类型以及结果的选取 (19)3.4实验设计法的仿真优化过程 (22)3.4.1 Moldflow与正交表的数据结合分析 (22)3.4.2实验数据的反馈与整合 (28)4.模具设计 (31)4.1塑件用途及其性能要求 (31)4.2注射量的计算 (31)4.3锁模力的计算 (31)4.4注塑机的选择及参数 (32)4.5 分型面的确定 (33)4.6 浇注系统的设计 (33)4.7 成型零部件的设计与计算 (37)4.8 推出机构设计 (38)4.9标准模架的选取 (38)4.10 开模行程的校核 (39)4.11 推出脱模机构设计 (40)4.12合模导向机构的设计 (41)4.13 排气系统与冷却系统的设计 (43)5. 结论 (44)5.1设计的总结与创新点: (44)5.2论文所存在的问题及其解决方案: (44)谢辞 (45)参考文献: (46)1.绪论1.1 引言随着科学技术水平的不断提高以及加工方法的改进,塑料这一20世纪才发展起来的新材料已经在我们的日常生活中占据了重要的地位,成为国民经济中不可缺少的一部分。
塑料成型技术是指把粉、粒料或液状树脂及添加剂等原料加工成具有一定使用价值的制品的一种技术。
塑料制品性能的优劣及规格多少与成型技术密不可分。
注射成型又称注射模塑或注塑,是塑料加工中重要的成型方法之一,其技术已发展的相当成熟,且应用非常普遍,注塑制品已占领塑料制品总量的30%以上,在国民经济的许多领域有着广泛的应用。
1.2 注塑成型工艺过程简介注塑成型加工过程是一个循环的周期过程,一般包括三个阶段,即注射阶段、保压及压实阶段、固化及冷却阶段。
注塑成型过程如图1-1所示。
图1-1 注塑成型过程注塑成型加工过程从聚合物颗粒通过料斗进入螺杆开始。
首先聚合物颗粒在转动螺杆的输送作用下不断沿螺槽方向向前运动,同时转动的螺杆把机械能转化为热能,使聚合物颗粒得到软化和熔解。
聚合物材料在螺杆剪切热与料筒外部热源的作用下很快塑化并熔融,转变成粘流体并存贮在料筒前端的区域(即存料区)。
与此同时,存料区中的熔体具有一定的压力,当熔体压力大于螺杆后退所要克服的阻力时,螺杆开始一边转动一边向后移动。
直到螺杆碰到行程开关为止。
这一整个过程称为塑化过程。
此后有一螺杆的静止阶段,然后随着螺杆向前运动,熔化的物料通过喷嘴一模具浇道一成型模腔系统的通道,将螺杆头部的塑料熔体注入模具型腔中。
这一过程称为注射过程。
在注射过程中,塑料熔体轴向移动是由螺杆注射速度控制的。
注射一结束,由于熔体和模具的热传导,型腔内的熔体开始固化。
由于固化和冷却的作用,制品会发生收缩,因此为了补充收缩必须在一定的压力作用下,补充物料,这一过程称为压实一保压过程。
在这一阶段,螺杆移动很慢,压力可以进行变化控制。
通过一些冷却介质(通常是冷却水)的流通,热量连续的从模具中通过模具内的钻孔散出,最终制件得到固化。
这就是冷却过程。
在冷却过程中,在螺杆内同时发生了塑化过程。
最后,通过一个排出装置把制件从模具中分离出来(或用手动的方法)。
这时,一个循环过程结束,一个新的循环过程又开始了。
从注塑成型加工的周期过程中,可以看到,螺杆在塑化和注射时,均要发生轴向位移,同时螺杆又处于时转时停的间歇式工作状态,因此形成了螺杆塑化过程的非稳定性。
螺杆在不同阶段的运动如图1-2所示。
图1-2 往复式螺杆的动作顺序A)注射、压实及保压阶段:螺杆轴向向前移动;B)塑化阶段:螺杆一边转动一边后退;C)停留阶段:螺杆处于静止状态1.3注塑成型工艺的发展趋势注塑成型技术已经是一项比较成熟的技术,但是随着注塑制品在家电、汽车等高科技领域的应用,对制品的质量、性能及产品更新换代提出了更高的要求。
高质量高精度高灵敏度的严格要求成为阻止塑料制品快速进入这些高尖领域的限制和束缚。
注塑成型是一个多变量的过程,在注塑成型过程中,影响制品质量的因素可以分为四类:机器参数、材料参数、工艺参数和扰动。
其中机器参数同注塑成型机直接相关用以表征机器的机械特征,它包括:料筒温度、喷嘴温度、液压系统背压、螺杆旋转速度、模具温度及注塑机和模具的几何特征等。
材料参数为注塑材料的一些典型特征,一般由材料供应商提供,包括材料的流变性能、热物理性能(包括密度、分子组成、分子量、比热和热传导率等等)。
工艺参数反映了成型过程中材料的状态,受机器参数、材料参数的影响,注塑成型过程中的典型工艺参数有:熔体温度、熔体压力及它们在型腔中的分布、熔体注射速率、模具内的热流分布等等。
当然,这些参数虽然被划分在不同的范围内,但是相互之间有着密切关系,互相产生影响。
机器参数、材料参数决定了工艺参数。
对工艺参数的要求,直接影响到机器参数、材料参数的选取,从而确定出相应的注塑机和对应材料。
由于复杂的动态工艺及材料特性,使得注塑技术难以预测及控制制件的质量。
因此,如何提高注塑制品质量和性能成为该领域的重要研究课题。
注塑成型是复杂的多变量、非线性且具有周期性的非稳态过程。
成型过程中聚合物在型腔中的状态如压力、温度、形态等直接决定了制品的质量,因此如何实现机器设置参数和熔体状态参数之间的闭环控制成为注塑成型技术的研究热点,该技术的实现将会提高制品质量。
状态变量为机器输入和最终制品质量属性的中间变量,实现注塑成型的精确控制的最大困难在于机器输入和状态变量之间的关系模型与状态变量和制品质量属性之间的关系模型未知。
温度和压力为两个主要状态变量,目前的状态变量监控研究主要集中在温度和压力的监控上,也有关于熔体豁度的监控。
初期的状态控制主要针对单个变量,选用对整个成型周期或对某个阶段影响最大的工艺参数,例如熔体温度或型腔压力,或者针对某个特定目标选择单个工艺参数作为控制变量,而不考虑工艺参数之间的相互影响。
注塑成型过程中各个工艺参数之间的影响程度相当大,控制单一变量很容易使对整个成型过程的控制失去平衡。
研究者们逐渐将研究重点放在了多变量的控制方法上,同时选用对某个阶段或整个成型周期影响较大的几个参数,并尽可能的考虑到所选控制变量之间的相互影响。
注塑成型控制总体结构如图1-3,整个控制系统包括了三层控制。