注塑成型工艺参数及其影响
注塑成型工艺流程及工艺参数
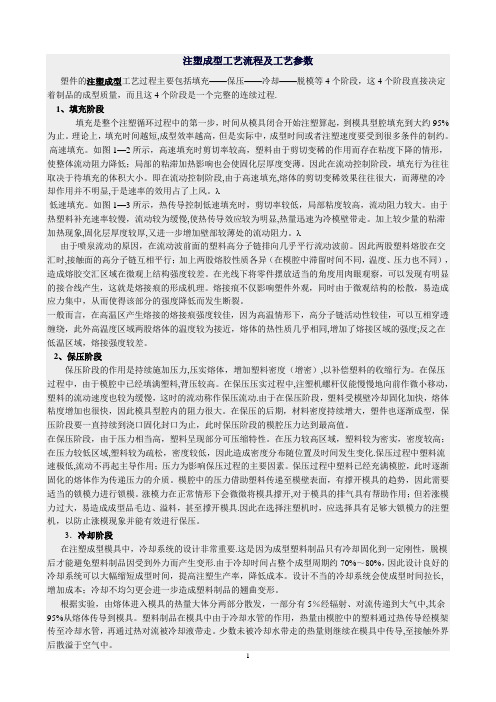
注塑成型工艺流程及工艺参数塑件的注塑成型工艺过程主要包括填充——保压——冷却——脱模等4个阶段,这4个阶段直接决定着制品的成型质量,而且这4个阶段是一个完整的连续过程.1、填充阶段填充是整个注塑循环过程中的第一步,时间从模具闭合开始注塑算起,到模具型腔填充到大约95%为止。
理论上,填充时间越短,成型效率越高,但是实际中,成型时间或者注塑速度要受到很多条件的制约。
高速填充。
如图1—2所示,高速填充时剪切率较高,塑料由于剪切变稀的作用而存在粘度下降的情形,使整体流动阻力降低;局部的粘滞加热影响也会使固化层厚度变薄。
因此在流动控制阶段,填充行为往往取决于待填充的体积大小。
即在流动控制阶段,由于高速填充,熔体的剪切变稀效果往往很大,而薄壁的冷却作用并不明显,于是速率的效用占了上风。
λ低速填充。
如图1—3所示,热传导控制低速填充时,剪切率较低,局部粘度较高,流动阻力较大。
由于热塑料补充速率较慢,流动较为缓慢,使热传导效应较为明显,热量迅速为冷模壁带走。
加上较少量的粘滞加热现象,固化层厚度较厚,又进一步增加壁部较薄处的流动阻力。
λ由于喷泉流动的原因,在流动波前面的塑料高分子链排向几乎平行流动波前。
因此两股塑料熔胶在交汇时,接触面的高分子链互相平行;加上两股熔胶性质各异(在模腔中滞留时间不同,温度、压力也不同),造成熔胶交汇区域在微观上结构强度较差。
在光线下将零件摆放适当的角度用肉眼观察,可以发现有明显的接合线产生,这就是熔接痕的形成机理。
熔接痕不仅影响塑件外观,同时由于微观结构的松散,易造成应力集中,从而使得该部分的强度降低而发生断裂。
一般而言,在高温区产生熔接的熔接痕强度较佳,因为高温情形下,高分子链活动性较佳,可以互相穿透缠绕,此外高温度区域两股熔体的温度较为接近,熔体的热性质几乎相同,增加了熔接区域的强度;反之在低温区域,熔接强度较差。
2、保压阶段保压阶段的作用是持续施加压力,压实熔体,增加塑料密度(增密),以补偿塑料的收缩行为。
pa12注塑工艺参数

pa12注塑工艺参数(原创版)目录1.PA12 的概述2.PA12 注塑工艺的参数3.参数对注塑过程的影响4.参数的调整和优化5.总结正文一、PA12 的概述PA12,即聚十二内酰胺,是一种热塑性树脂。
由于其具有优良的力学性能、化学稳定性和耐热性,被广泛应用于汽车、电子、医疗等领域的零部件制造。
在众多的加工方法中,注塑成型是 PA12 应用最广泛的加工方式。
二、PA12 注塑工艺的参数PA12 注塑工艺的参数主要包括以下几类:1.温度参数:包括熔体温度、模具温度、冷却水温度等。
2.压力参数:包括注射压力、保压压力、冷却压力等。
3.速度参数:包括注射速度、开模速度、合模速度等。
4.时间参数:包括注射时间、保压时间、冷却时间等。
三、参数对注塑过程的影响注塑工艺参数对 PA12 制品的质量和生产效率有着重要影响:1.温度参数:熔体温度过高或过低都会影响 PA12 的流动性,进而影响制品的尺寸和表面质量;模具温度对制品的冷却速度和脱模性有直接影响;冷却水温度则影响制品的冷却速度,进而影响制品的收缩率和内应力。
2.压力参数:注射压力过大或过小都会影响 PA12 在模具中的填充情况,进而影响制品的尺寸和表面质量;保压压力和冷却压力则影响制品的内应力和变形。
3.速度参数:注射速度过快或过慢都会影响 PA12 在模具中的填充情况,进而影响制品的尺寸和表面质量;开模速度和合模速度则影响制品的成型周期和质量。
4.时间参数:注射时间过短或过长都会影响 PA12 在模具中的填充情况,进而影响制品的尺寸和表面质量;保压时间、冷却时间过短或过长都会影响制品的内应力和变形。
四、参数的调整和优化在实际生产过程中,需要根据制品的实际需求和注塑机的性能,对PA12 注塑工艺参数进行调整和优化。
一般来说,可以通过调整注射速度、注射压力、保压时间和冷却时间等参数,来达到优化制品质量、提高生产效率的目的。
五、总结PA12 注塑工艺参数对制品的质量和生产效率有着重要影响。
注塑成型工艺参数对注塑件缩痕影响的研究

影 响 。 不 同 的工 艺 参 数 进 行 了分 析 , 定 出 用于 注 塑 成 型 的 较 合 适 的 工艺 参 数 。 研 究 结 果 表 明 : 体 温 度 、 具 温 度 的 对 确 熔 模
太多 , 设计 的效 率低 , 计 的 时 间周 期太 长 , 设 留给 制造
调 试 的时间太短 。设 计 过 程 中缺 乏 先 进 的技 术手 段 ,
对 产 品 、 具进行 分 析 、 拟 , 具 制 造 后试 模 的合 格 模 模 模
( . o g i uXix Go g h n ,S axn c t n l& T c nclC l g ,S axn 1 0 0,Chn ; 1 T n xn y n i n c e gXi h oigVo ai a o e h ia ol e h oig3 2 0 e ia
prc sig pa a ees wee o t n d. Th e ul fr s ac s o t tde r a ig m ett mp r tr o esn r m tr r baie e r s t o e e r h h w ha c e sn l e e au e, mo d tmpe au e s l e r t r
潼 塑 威 型 参 数 对 潼 塾 件 缩 疲 影 响 研 究
傅 建 钢 傅 晓锦 ,
( . 兴职业技 术 学院 通信 与信 息 工程 系 , 江 绍兴 3 2 0 ; 1绍 浙 10 0 2 上 海 电机 学 院 机械 学院 , 海 2 0 4 ;. . 上 0 2 5 3 绍兴文 理 学院 ,浙江 绍兴 3 2 0 ) 10 0
注塑压力、保压压力和背压对注塑成型的影响

注塑压力、保压压力和背压对注塑成型的影响
在注塑成型的过程中我们经常会遇到三个压力参数,这几个参数分别是注塑压力、保压压力和背压,这些压力参数设置对注塑成型及制品有什么影响呢?下面由小编为大家介绍一下。
1.注塑压力
注塑压力是指注塑时作用于螺杆头部的熔体压强。
用于克服塑料流经喷嘴、流道、浇口及模腔内的流动阻力,并使型腔压实。
注塑压力的大小与塑料的品种、塑料件的复杂程度、塑料件的壁厚、喷嘴的结构形式、模具浇口的尺寸及注塑件的类型等许多因素有关,通常取
40-200MPa。
2.保压压力
保压压力是指注塑后螺杆并不立即后退,仍继续对前端熔体施加压力。
在保压阶段,模腔能的塑料因为冷却收缩而体积变小,这时若浇口未冻结,螺杆在保压压力的作用下缓慢前进,使塑料继续注射入型腔进行补缩。
一般保压压力≤注射压力。
3.背压
背压又称为塑化压力,是指注塑机螺杆顶部的熔体在螺杆转动后退时所受到的压力。
背压是通过调节注塑液压缸的回油阻力控制的。
背压是注塑成型工艺中很重要的参数,直接影响熔体的充模和塑件的质量。
在下一节内容中,小编会为大家详细地介绍背压的影响,敬请关注。
pa12注塑工艺参数
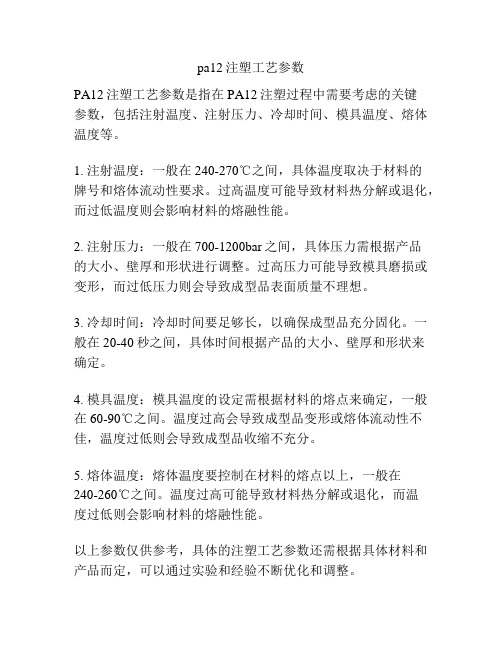
pa12注塑工艺参数
PA12注塑工艺参数是指在PA12注塑过程中需要考虑的关键
参数,包括注射温度、注射压力、冷却时间、模具温度、熔体温度等。
1. 注射温度:一般在240-270℃之间,具体温度取决于材料的
牌号和熔体流动性要求。
过高温度可能导致材料热分解或退化,而过低温度则会影响材料的熔融性能。
2. 注射压力:一般在700-1200bar之间,具体压力需根据产品
的大小、壁厚和形状进行调整。
过高压力可能导致模具磨损或变形,而过低压力则会导致成型品表面质量不理想。
3. 冷却时间:冷却时间要足够长,以确保成型品充分固化。
一般在20-40秒之间,具体时间根据产品的大小、壁厚和形状来
确定。
4. 模具温度:模具温度的设定需根据材料的熔点来确定,一般在60-90℃之间。
温度过高会导致成型品变形或熔体流动性不佳,温度过低则会导致成型品收缩不充分。
5. 熔体温度:熔体温度要控制在材料的熔点以上,一般在
240-260℃之间。
温度过高可能导致材料热分解或退化,而温
度过低则会影响材料的熔融性能。
以上参数仅供参考,具体的注塑工艺参数还需根据具体材料和产品而定,可以通过实验和经验不断优化和调整。
pa6十gf30的成型工艺参数
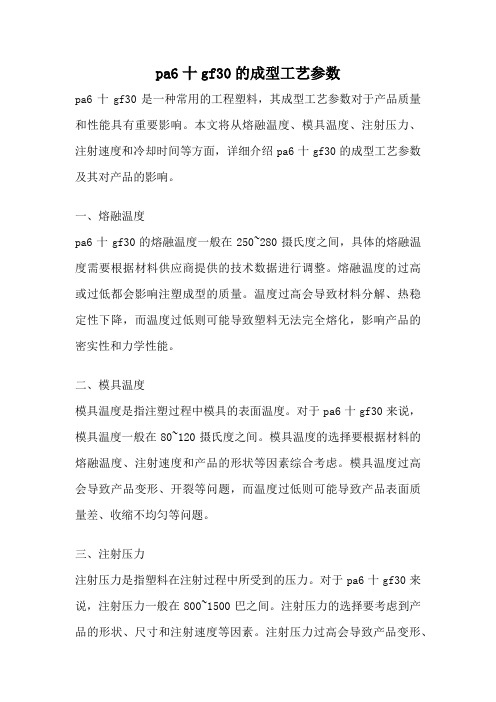
pa6十gf30的成型工艺参数pa6十gf30是一种常用的工程塑料,其成型工艺参数对于产品质量和性能具有重要影响。
本文将从熔融温度、模具温度、注射压力、注射速度和冷却时间等方面,详细介绍pa6十gf30的成型工艺参数及其对产品的影响。
一、熔融温度pa6十gf30的熔融温度一般在250~280摄氏度之间,具体的熔融温度需要根据材料供应商提供的技术数据进行调整。
熔融温度的过高或过低都会影响注塑成型的质量。
温度过高会导致材料分解、热稳定性下降,而温度过低则可能导致塑料无法完全熔化,影响产品的密实性和力学性能。
二、模具温度模具温度是指注塑过程中模具的表面温度。
对于pa6十gf30来说,模具温度一般在80~120摄氏度之间。
模具温度的选择要根据材料的熔融温度、注射速度和产品的形状等因素综合考虑。
模具温度过高会导致产品变形、开裂等问题,而温度过低则可能导致产品表面质量差、收缩不均匀等问题。
三、注射压力注射压力是指塑料在注射过程中所受到的压力。
对于pa6十gf30来说,注射压力一般在800~1500巴之间。
注射压力的选择要考虑到产品的形状、尺寸和注射速度等因素。
注射压力过高会导致产品变形、翘曲等问题,而压力过低则可能导致产品缺陷、热断裂等问题。
四、注射速度注射速度是指塑料在注射过程中的流动速度。
对于pa6十gf30来说,注射速度一般在5~15cm/s之间。
注射速度的选择要考虑到产品的形状、尺寸和注射压力等因素。
注射速度过高会导致产品表面粗糙、气泡等问题,而速度过低则可能导致产品收缩不均匀、短射等问题。
五、冷却时间冷却时间是指产品在模具中冷却的时间。
对于pa6十gf30来说,冷却时间一般在20~60秒之间。
冷却时间的选择要考虑到产品的厚度、尺寸和材料的熔融温度等因素。
冷却时间过短会导致产品收缩不完全、变形等问题,而时间过长则可能导致生产效率低下、成本增加等问题。
pa6十gf30的成型工艺参数对于产品的质量和性能至关重要。
注塑工艺参数对塑料产品成型的影响
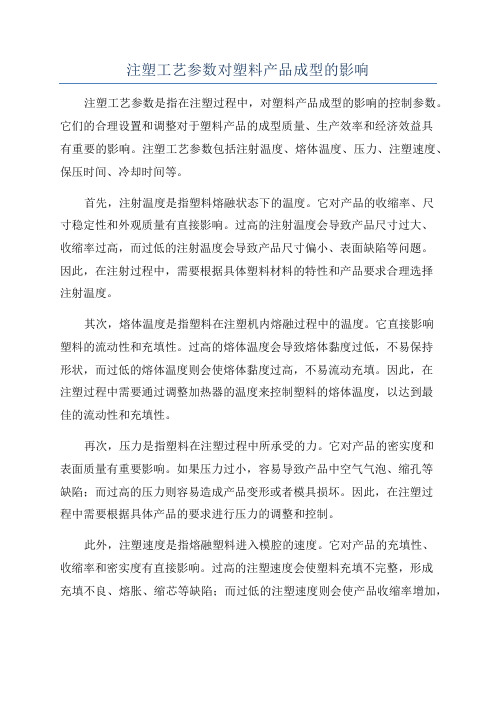
注塑工艺参数对塑料产品成型的影响注塑工艺参数是指在注塑过程中,对塑料产品成型的影响的控制参数。
它们的合理设置和调整对于塑料产品的成型质量、生产效率和经济效益具有重要的影响。
注塑工艺参数包括注射温度、熔体温度、压力、注塑速度、保压时间、冷却时间等。
首先,注射温度是指塑料熔融状态下的温度。
它对产品的收缩率、尺寸稳定性和外观质量有直接影响。
过高的注射温度会导致产品尺寸过大、收缩率过高,而过低的注射温度会导致产品尺寸偏小、表面缺陷等问题。
因此,在注射过程中,需要根据具体塑料材料的特性和产品要求合理选择注射温度。
其次,熔体温度是指塑料在注塑机内熔融过程中的温度。
它直接影响塑料的流动性和充填性。
过高的熔体温度会导致熔体黏度过低,不易保持形状,而过低的熔体温度则会使熔体黏度过高,不易流动充填。
因此,在注塑过程中需要通过调整加热器的温度来控制塑料的熔体温度,以达到最佳的流动性和充填性。
再次,压力是指塑料在注塑过程中所承受的力。
它对产品的密实度和表面质量有重要影响。
如果压力过小,容易导致产品中空气气泡、缩孔等缺陷;而过高的压力则容易造成产品变形或者模具损坏。
因此,在注塑过程中需要根据具体产品的要求进行压力的调整和控制。
此外,注塑速度是指熔融塑料进入模腔的速度。
它对产品的充填性、收缩率和密实度有直接影响。
过高的注塑速度会使塑料充填不完整,形成充填不良、熔胀、缩芯等缺陷;而过低的注塑速度则会使产品收缩率增加,尺寸不稳定。
因此,在注塑过程中需要通过调整注塑机的注射速度来控制注塑速度,以达到产品质量要求。
保压时间是指塑料在注塑过程中保持一定压力的时间。
它对产品的密实度、尺寸稳定性和缺陷情况有直接影响。
保压时间过长会使产品收缩率过大,尺寸偏大;保压时间过短则会导致产品尺寸偏小、表面缺陷等问题。
因此,在注塑过程中需要根据具体产品的要求和塑料材料的特性进行保压时间的调整和设定。
最后,冷却时间是指塑料在注塑过程中冷却的时间。
它对产品的尺寸稳定性、变形和序列产能有重要影响。
工艺参数对注塑制品质量的影响相关分析

36技术应用与研究一、1.工艺参数对注塑制品质量的影响方面分析据有关调查显示,我国大多数注塑制品的生产过程中都会由于工艺参数的设定以及应用等存在不同的制品生产效果,并由此对注塑制品自身的质量产生直接性影响。
对于工艺参数对注塑制品质量的相关性影响分析,需要从实际的影响内容、工艺参数变化以及原因等多个角度入手,进而为提高注塑制品的质量措施研究奠定基础。
下面展开详细的论述。
1.影响内容一般而言,在工艺参数的设定过程中,对于注塑制品质量的影响主要集中在尺寸设定、表面缺陷以及翘曲变形等三方面。
具体地,在尺寸设定上的影响是通过分析不同的工艺参数设定差异对于实际的注塑制品中收缩率的大小分析,进而直接对于注塑制品的尺寸等质量内容产生决定性影响。
在翘曲变形的影响上则是由于注塑制品中注塑工艺的应用会使得其在成型时由于浇注和冷却系统的功能而使得注塑制品出现翘曲变形。
最后,在对于表面缺陷等质量问题的影响是直接由于工艺参数对于实际注塑成型的过程存在的关键性影响而导致注塑制品表现出现一系列的缺陷。
2.影响原因调查显示,在经过工艺参数的设定之后,注塑制品的质量主要是受到制品结构、胜场模具、原材料、注塑工艺、工艺参数以及扰动等多种因素的影响。
其中,工艺参数的存在是极容易导致注塑制品质量出现问题的。
具体的影响原因上见表1。
表1 工艺参数对注塑制品质量的影响原因分析质量问题阶段原因制品尺寸注塑工艺参数设定影响制品收缩率、效果保压压力与时间、模具与熔体温度、注射压力的不同设定差异翘曲变形注塑工艺参数设定影响成型过程表面缺陷注塑工艺参数设定影响物料成型状态 通过对上表的分析可以发现:保压压力、保压时间、模具温度、熔体温度、注射压力等五种工艺参数的设定是直接影响到注塑制品质量的关键性因素,需要在具体的生产过程中从注塑制品的成型、物料监督到收缩等加强检测分析。
二、工艺参数对注塑制品质量改进的实践分析上面已经对工艺参数对注塑制品质量的相关影响等进行了初步的分析和实际情况介绍,可以发现:目前我国存在的注塑制品的质量问题大多集中在尺寸、翘曲变形以及表现缺陷等三个角度,并通过不同阶段的生产过程而造成最终的质量问题。
注塑成型工艺参数说明

注塑成型注塑成型工艺参数工艺参数工艺参数说明说明说明一.干燥温度定义:为保证成型质量而事先对聚合物进行干燥所需要的温度作用:1.去除原料中的水份.2.确保成品质量设定原则: 1.聚合物不致于分解或结块(聚合) 2.干燥时间尽量短,干燥温度尽量低而不致于影响其干燥效果. 3.干燥温度和时间因不同原料而异.注:1,A 表示用热风干燥机.2,D 表示用除湿干燥机.3,*表示通常不需干燥.4,**表示干燥依条件类别而定,最好材料供货商确认.二.料温定义: 为保证成型顺利进行而设加在料管上之温度.作用: 保证聚合物塑化(熔胶)良好,顺利充模,成型.设定原则: (1)不致引起塑料分解碳化. (2)从加料断至喷嘴依次上升. (3)喷嘴温度应比料筒前断温度略低. (4)依材料种类不同而所需温度不同. (5)不至对制品产生坏的质量影响.三.模温定义: 制品所接触的模腔表面温度作用: 控制影响产品在模腔中的冷却速度,以及制品的表观质量.设定原则: (1)考虑聚合物的性质. (2)考虑制品大小和形状. (3)考虑模具的结构.浇道系统.四.注射速度定义: 在一定压力作用下,熔胶从喷嘴注射到模具中的速度 .作用: (1)注射速度提高将使充模压力提高. (2)提高注射速度可使流动长度增加,制质量量均匀. (3)高速射出时粘度高,冷速快,适合长流程制品. (4)低速时流动平稳,制品尺寸稳定.设定原则: (1) 防止撑模及避免产生溢边. (2)防止速度过快导致烧焦. (3)保证制品质量的前提下尽量选择高速充填,以缩短成型周期.五.熔胶速度定义: 塑化过程中螺杆熔胶时的转速 .作用: 影响塑化能力,塑化质量的重要参数,速度越高,熔体温度越高,塑化能力越强 .设定原则: (1)熔胶速度调整时一般由低向高逐渐调整. (2)螺杆直径大于50MM之机台转速应控制在50RPM以下,小于50MM之机台应控制在100RPM以下为宜.六.射压定义: 螺杆先端射出口部位发生之最大压力,其大小与射出油缸内所产生油压紧密关连 . 作用: 用以克服熔体从喷嘴--流道--浇口--型腔的压力损失,以确宝型腔被充满,获得所需的制品.设定原则: (1)必在注塑机的额定压力范围内. (2)设定时尽量用低压. (3)尽量避免在高速时采用高压,以免异常状况发生七.背压定义: 塑料在塑化过程建立在熔腔中的压力 .作用: (1)提高熔体的比重. (2)使熔体塑化均匀. (3)使熔体中含气量降低.提高塑化质量设定原则: (1)背压的调整应考虑塑料原料的性质. (2)背压的调整应参考制品的表观质量和呎寸精度八.锁模压力定义: 合模系统为克服在注射和保压阶段使模具分开的胀模力而施加在模具上的闭紧力. 作用: (1)保证注射和保压过程中模具不致于被胀开 (2)保证产品的表观质量. (3)保证产品的尺寸精度.设定原则: (1)合模力的大小依据产品的大小,机台的大小而定. (2)一般来说,在保证产品不出毛头的情况下,合模力 要求越小越好. (3)合模力的设定不应超出机台之额定压力.九.保压定义: 从模腔填满塑料,继续施加于模腔塑料上的注射压力,直至浇口完全冷却封闭的一段时间,要靠一个相当高的压力支技,这个压力叫保压.作用: (1)补充靠近浇口位置的料量,并在浇口冷却封闭以前制止模腔中尚未硬化的塑料在残余压力作用倒流,防止制件收缩,避免缩水,减少真空泡. (2)减少制件因受过大的注射压力而易产生粘模爆裂或弯曲.设定原则: (1)保压压力及速度通常设定至塑料充满模腔时最高压力及速度的50~60% (2)保压时间的长短与料温有关,温度高的浇口封闭时间长,保压时间也长. (3)保压与产品投影面积及壁厚有关,厚而大者需要的时间较长. (4)保压与浇口呎寸形状,大小有关. 保压切换位置,计量长度及松退行程设定十.计量行程定义: 塑化开始后,螺杆在旋转过程中,由注射终止位置开始在塑料熔体的作用力下后退,直至后退限位开关为止,这个过程称为计量行程.作用: 保证有足够的塑料充填模腔,以获得所需外观和呎寸的制品.设定原则: (1)计量行程要依据产品的大小及机台大小而设定. (2)计量行程不能太大,以免注射多余的塑料在料管中停留的时间太长而引起碳化. (3)计量行程不能太小,以确保充填有足够的计量及避免螺杆与喷嘴发生机械损伤,应有3~5mm的缓冲量.十一.射出行程定义: 注射过程中螺杆所处的位置变化作用: 结合速度,压力控制塑料流动状态设定原则: (1)计量完位置由成品之充填量决定,通常在此值上加3~5mm绶冲量来决定最终设定. (2)向第二速的转换点,通常切换至充满热浇道,料头位置. (3)向第三速的转换点,用成型品的90%的充填程度来设定切换位置. (4)保压切换点一般设定在成品的90%的充填程度之位置. (注:以上以四段为例)十二.松退量定义: 螺杆预塑(计量)到位后又直线地倒退一段距离,这个后退的动作称为后松退,松退的距离称为松退量或防延量.作用: 后松退的作用是使计量室中的熔体比容增加,内压下降,防止熔体从计量室向外流出.设定原则: (1)可视塑料原料的粘度,相对密度和制品的实际情况进行设定,较大的松退量会使熔体混杂汽泡,影响制品质量. (2)松退量的设定应与螺杆转速,背压相适应. (3)对于粘度较大的原料象PC料可不设松退量.十三.缓冲量定义: 螺杆注塑完拮,并不希望把螺杆中头部的熔料全部射出,还希望留一些.形成一个祭料量,此料量即为缓冲量.作用: (1)防止螺杆头部与喷嘴接触发生机械破坏事故. (2)控制注射量的重复精度设定原则: (1)缓冲量不宜过大,也不宜过小,过大,会使得余料过多,造成压力损失及原料降解,过小,则达不到缓冲之目的. (2)缓冲量的确定,一般取3~5mm为宜.十四.周期定义: 从开模终了开始到下一次注射冷却完毕后的开模终了所用的时间作用: 保证制品成型并完全冷却定型设定原则: (1)周期尽可能短. (2)缩短周期必须在保证产品质量的前提下进行十五.冷却时间定义: 产品冷却固化而脱模后又不致于发生变形所需的时间作用: (1)让制品固化 (2)防止制品变形设定原则: (1)冷却时间是周期时间的重要组成部分,在保证制品质量的前提下尽可能使其短. (2)冷却时间因熔体的温度,模具温度,产品大小及厚度而定.十六.保压时间定义: 为防止注射后塑料倒流以及冷却补缩作用,在注塑完后继续施加的压力作用: (1)防止注塑完后熔体倒流. (2)冷却收缩的补缩作用设定原则: (1)保压时间因制品厚度不同而异. (2)保压时间要因熔料温度的高低而异,温度高者所需时间长,低者则短. (3)为提高生产效率,在保证制质量量的前提下应尽可能使保压时间短.十七.射出时间定义: 熔体在充满整个型腔所用的时间 .作用: 射出时间由射出压力,射出速度以及制品的大小等因素来决定设定原则: (1)在保证制品成型的条件下尽可能让射出时间短. (2)射出时间受料温,模温等因素的影响.十八.熔胶时间定义: 注射终止后,螺杆到达计量终止位置所需要的时间作用: 保证熔胶充分设定原则: (1)由螺杆转速和背压相互控制. (2)不要让熔融塑料体在螺杆中停留的时间过长,以免引起塑料在长时间的高温状态下分解,碳化.十九.干燥时间定义: 利用干燥设备事先对原料进行干燥所需要的时间作用: (1)增进表面光泽,提高抗弯曲及拉伸强度,避免内部裂纹和气泡. (2)提高塑化能力,缩短成型周期. (3)降低原料中水份及湿气.设定原则: (1)干燥时间因原料的不同而不同. (2)干燥时间的设定要适宜,太长会使得干燥效率降低甚至会使原料结块,太短则干燥效果不佳.。
注塑成型工艺参数对制品质量影响的实验研究

郑州大学硕士学位论文注塑成型工艺参数对制品质量影响的实验研究姓名:***申请学位级别:硕士专业:材料加工工程指导教师:申长雨;王利霞20060425郑州大学工学硕十学位论文图1.4简化的注塑成型设备示意图Figl-4s妇plmedInjecdonMoldingMachine1.4注塑成型质量控制发展趋势注塑成型技术已经是一项比较成熟的技术,但是随着注塑制品在家电、汽车等高科技领域的应用,对制品的质量、性能及产品更新换代提出了更高的要求。
高质量高精度高灵敏度的严格要求成为阻止塑料制品快速进入这些高尖领域的限制和束缚。
注塑成型是一个多变量的过程,在注塑成型过程中,影响制品质量的因素可以分为四类:机器参数、材料参数、工艺参数和扰动。
其中机器参数同注望成型机直接相关用以表征机器的机械特征,它包括:料筒温度、喷嘴温度、液压系统背压、螺杆旋转速度、模具温度及注塑机和模具的几何特征等。
材料参数为注塑材料的一些典型特征,一般由材料供应商提供,包括材料的流变性能、热物理性能(包括密度、分子组成、分子量、比热和热传导率等等)。
工艺参数反映了成型过程中材料的状态,受机器参数、材料参数的影响,注塑成型过程中的典型工艺参数有:熔体温度、熔体压力及它们在型腔中的分布、熔体注射速率、模具内的热流分布等等。
当然,这些参数虽然被划分在不同的范围内,但是相互之间有着密切关系,互相产生影响。
机器参数、材料参数决定了工艺参数。
对工艺参数的要求,直接影响到机器参数、材料参数的选取,从而确定出相应的注塑机和对应材料。
由于复杂的动态工艺及材料特性,使得注塑技术难以预测及控制制件的质量。
因此,如何提高注塑制品质量和性能成为该领域的重要研究课题。
注塑成型l31是复杂的多变量、非线性且具有周期性的非稳态过程。
成型过程中聚合物在型腔中的状态如压力、温度、形态等直接决定了制品的质量,因此如何实现机器设置参数和熔体状态参数之间的闭环控制成为注塑成型技术的研究热4第三章工艺参数对制品质量的交互影响分析因子之间存在交互作用15“。
tpr注塑成型工艺参数
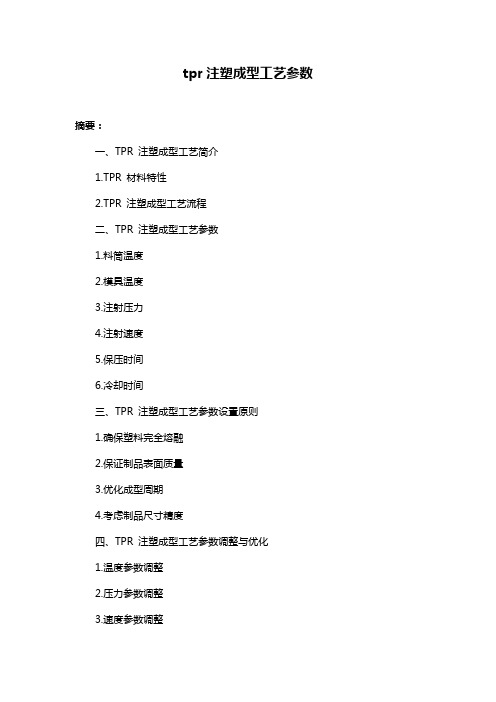
tpr注塑成型工艺参数摘要:一、TPR 注塑成型工艺简介1.TPR 材料特性2.TPR 注塑成型工艺流程二、TPR 注塑成型工艺参数1.料筒温度2.模具温度3.注射压力4.注射速度5.保压时间6.冷却时间三、TPR 注塑成型工艺参数设置原则1.确保塑料完全熔融2.保证制品表面质量3.优化成型周期4.考虑制品尺寸精度四、TPR 注塑成型工艺参数调整与优化1.温度参数调整2.压力参数调整3.速度参数调整4.时间参数调整正文:TPR 注塑成型工艺是一种将热塑性弹性体(TPR)通过注塑机进行加工制造的工艺。
TPR 材料具有优异的弹性和耐磨性,广泛应用于汽车、电子、家电等领域。
本文将详细介绍TPR 注塑成型工艺的参数设置及优化方法。
一、TPR 注塑成型工艺简介TPR 材料是一种具有橡胶与塑料特性的材料,具有较高的弹性、强度和耐磨性。
TPR 注塑成型工艺流程包括:原料准备、注塑机调试、模具安装、注射成型、制品取出、冷却定型等步骤。
二、TPR 注塑成型工艺参数1.料筒温度:料筒温度是影响TPR 材料熔融的重要参数。
适当的料筒温度可以确保塑料完全熔融,避免因温度过低导致塑料不能完全熔融,或因温度过高导致塑料降解。
2.模具温度:模具温度会影响制品的表面质量和尺寸精度。
适当的模具温度可以降低制品的内应力,提高制品的表面质量。
3.注射压力:注射压力是影响TPR 注塑成型工艺的关键参数。
合适的注射压力可以保证制品的密度和强度,避免制品出现缺陷。
4.注射速度:注射速度过快或过慢都会影响制品的质量。
合适的注射速度可以保证制品的尺寸精度,避免出现熔接痕、气泡等缺陷。
5.保压时间:保压时间过长或过短都会影响制品的质量。
合适的保压时间可以保证制品的密度和强度,避免出现缺陷。
6.冷却时间:冷却时间过长或过短都会影响制品的尺寸和性能。
合适的冷却时间可以保证制品的尺寸精度,避免制品变形或破裂。
三、TPR 注塑成型工艺参数设置原则1.确保塑料完全熔融:料筒温度、注射压力和注射速度等参数需相互配合,确保塑料能够完全熔融,避免出现缺料、熔接痕等缺陷。
abs注塑成型工艺参数
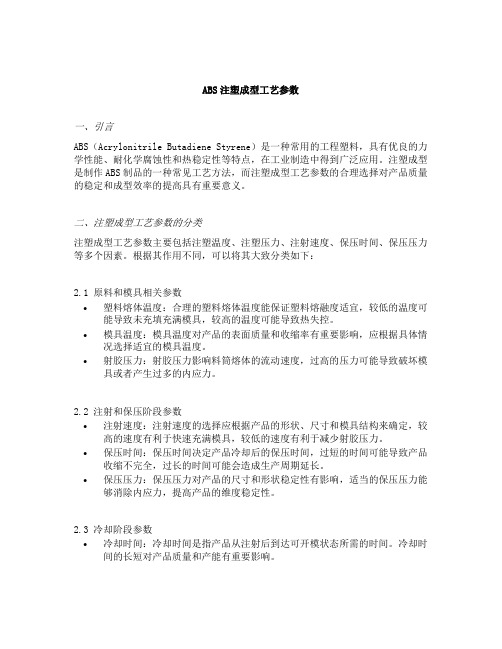
ABS注塑成型工艺参数一、引言ABS(Acrylonitrile Butadiene Styrene)是一种常用的工程塑料,具有优良的力学性能、耐化学腐蚀性和热稳定性等特点,在工业制造中得到广泛应用。
注塑成型是制作ABS制品的一种常见工艺方法,而注塑成型工艺参数的合理选择对产品质量的稳定和成型效率的提高具有重要意义。
二、注塑成型工艺参数的分类注塑成型工艺参数主要包括注塑温度、注塑压力、注射速度、保压时间、保压压力等多个因素。
根据其作用不同,可以将其大致分类如下:2.1 原料和模具相关参数•塑料熔体温度:合理的塑料熔体温度能保证塑料熔融度适宜,较低的温度可能导致未充填充满模具,较高的温度可能导致热失控。
•模具温度:模具温度对产品的表面质量和收缩率有重要影响,应根据具体情况选择适宜的模具温度。
•射胶压力:射胶压力影响料筒熔体的流动速度,过高的压力可能导致破坏模具或者产生过多的内应力。
2.2 注射和保压阶段参数•注射速度:注射速度的选择应根据产品的形状、尺寸和模具结构来确定,较高的速度有利于快速充满模具,较低的速度有利于减少射胶压力。
•保压时间:保压时间决定产品冷却后的保压时间,过短的时间可能导致产品收缩不完全,过长的时间可能会造成生产周期延长。
•保压压力:保压压力对产品的尺寸和形状稳定性有影响,适当的保压压力能够消除内应力,提高产品的维度稳定性。
2.3 冷却阶段参数•冷却时间:冷却时间是指产品从注射后到达可开模状态所需的时间。
冷却时间的长短对产品质量和产能有重要影响。
•冷却介质温度:冷却介质温度应根据产品的特性和要求来选择,较低的温度有利于快速冷却,但也可能导致产品收缩不均匀。
三、优化注塑成型工艺参数的方法合理选择注塑成型工艺参数可以提高产品的质量和生产效率,以下是一些优化方法的介绍:3.1 实验设计方法通过正交试验和统计方法,选取不同工艺参数的组合进行试验,从而确定最佳参数组合,达到产品的最佳质量。
注塑工艺参数对塑料产品成型的影响
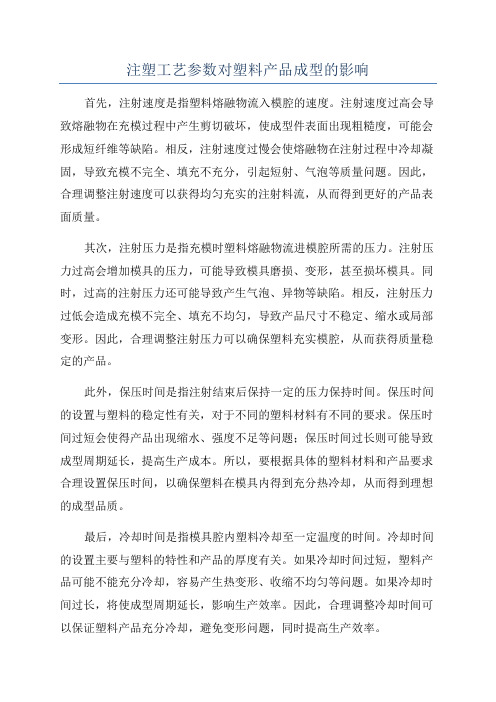
注塑工艺参数对塑料产品成型的影响首先,注射速度是指塑料熔融物流入模腔的速度。
注射速度过高会导致熔融物在充模过程中产生剪切破坏,使成型件表面出现粗糙度,可能会形成短纤维等缺陷。
相反,注射速度过慢会使熔融物在注射过程中冷却凝固,导致充模不完全、填充不充分,引起短射、气泡等质量问题。
因此,合理调整注射速度可以获得均匀充实的注射料流,从而得到更好的产品表面质量。
其次,注射压力是指充模时塑料熔融物流进模腔所需的压力。
注射压力过高会增加模具的压力,可能导致模具磨损、变形,甚至损坏模具。
同时,过高的注射压力还可能导致产生气泡、异物等缺陷。
相反,注射压力过低会造成充模不完全、填充不均匀,导致产品尺寸不稳定、缩水或局部变形。
因此,合理调整注射压力可以确保塑料充实模腔,从而获得质量稳定的产品。
此外,保压时间是指注射结束后保持一定的压力保持时间。
保压时间的设置与塑料的稳定性有关,对于不同的塑料材料有不同的要求。
保压时间过短会使得产品出现缩水、强度不足等问题;保压时间过长则可能导致成型周期延长,提高生产成本。
所以,要根据具体的塑料材料和产品要求合理设置保压时间,以确保塑料在模具内得到充分热冷却,从而得到理想的成型品质。
最后,冷却时间是指模具腔内塑料冷却至一定温度的时间。
冷却时间的设置主要与塑料的特性和产品的厚度有关。
如果冷却时间过短,塑料产品可能不能充分冷却,容易产生热变形、收缩不均匀等问题。
如果冷却时间过长,将使成型周期延长,影响生产效率。
因此,合理调整冷却时间可以保证塑料产品充分冷却,避免变形问题,同时提高生产效率。
总之,注塑工艺参数的设置对于塑料产品的成型质量和性能有着重要的影响。
通过合理调整注射速度、注射压力、保压时间和冷却时间等参数,可以获得质量稳定、表面质量良好的塑料产品。
因此,在注塑生产过程中,应根据具体的塑料材料特性和产品要求,选择合适的工艺参数,以提高注塑成型的质量和效率。
注塑工艺及参数设定

注塑工艺及参数设定首先,注射压力是指在注射过程中,由于塑料熔体注入模腔而产生的压力。
注射压力过大会造成模具过度开合,导致制品尺寸偏大,表面粗糙,甚至可能造成模具损坏;而注射压力过小则会使制品的充填不充分,导致短射或者气孔等缺陷。
注射压力的设定要根据材料的特性和模具的结构来确定。
其次,注射速度是指熔融塑料进入模腔的速度。
注射速度过快会造成破坏模具或者产生气泡等缺陷,而注射速度过慢会使制品的表面产生瑕疵。
注射速度的设定要根据材料的流动性和产品的结构来确定。
保压时间是指塑料在模腔内保持一定压力以保证制品的密实度和尺寸稳定性的时间。
保压时间过长会造成注塑周期延长,产量降低;保压时间过短会导致制品的表面缩短、收缩变形。
保压时间的设定需要根据产品的结构和材料的特性来确定。
保压压力是指在注射结束后,通过保持一定的压力来排除模具内的气体和缩短产品的填充时间的压力。
保压压力过大会导致产品产生变形,甚至可能导致模具损坏;保压压力过小会使得产品的尺寸稳定性降低。
保压压力的设定需要根据产品的形状和材料的特性来确定。
注射温度是指塑料熔融后进入模腔的温度。
注射温度过高会使材料分解、气泡产生、雪花状漏料等缺陷,而注射温度过低会导致进料不良、机器健康下降等不良问题。
注射温度的设定需要根据材料的熔点范围和热稳定性来确定。
冷却时间是指模具中塑料冷却至足够硬度以便脱模的时间。
冷却时间过短会导致产品收缩变形,冷却时间过长会使注塑周期延长。
冷却时间的设定需要根据产品的厚度和材料的热传导性来确定。
除了以上参数外,注塑工艺还包括模具温度、制品质量要求、模腔排气处理、材料干燥要求等各种工艺因素。
正确设置注塑工艺参数能够保证产品质量、提高生产效率和生产效益。
所以在实际生产中,根据产品的特性和要求,合理设定注塑工艺参数是至关重要的。
注塑成型工艺参数

注塑成型工艺参数注塑成型工艺参数是指在注塑成型过程中,需要控制和调节的各项参数,以确保成品的质量和生产效率。
合理的工艺参数可以提高产品的表面质量、尺寸精度和机械性能,并且能够降低注塑成型过程中的能耗和材料浪费。
以下是一些常见的注塑成型工艺参数。
1. 温度控制:包括模具温度和熔融温度。
模具温度通常由模具表面温度和模具加热方式决定,可以根据产品要求和材料特性进行调整。
熔融温度是指塑料在加热器中熔融的温度,要根据塑料材料的熔融温度范围进行控制。
2. 注射速度:包括前注速度、中注速度和后注速度。
注射速度会影响产品充填、压实和回缩的情况,要根据产品的形状和尺寸来进行调整。
3. 压力控制:包括注射压力、保压压力和冷却时间。
注射压力是指将熔融塑料推入模具腔中所需的压力,在注射阶段要保持稳定。
保压压力是指将注射阶段后的保压力维持在一定的压力下,以消除产品缩合和保持产品的尺寸稳定。
冷却时间是指产品从注射到冷却凝固的时间,要根据产品的尺寸和壁厚来设定。
4. 注射容积和保压时间:控制注塑机注塑的塑化量和保压时间可以对产品的质量和尺寸稳定性产生影响。
通常会根据产品的尺寸和重量来设定。
5. 射胶时间:指塑料熔融状态到注射压板位置所需的时间。
射胶时间会受到机器性能和模具结构的影响,要根据具体情况进行调整。
6. 温度差压力控制:可以通过控制同一模具中不同位置的温度和口径差压力,实现产品表面的一些特殊要求,如充填均匀性和防止白点等。
7. 冷却系统:良好的冷却系统对于控制产品的尺寸稳定性和表面质量非常重要。
可以通过冷却系统设计合理、水路畅通,并配有适当的冷却介质,来控制冷却速度和温度。
总的来说,注塑成型工艺参数的合理设定可以提高注塑成型的效率,并且可以保证产品的质量。
不同的产品需要根据其尺寸、形状、材料特性和要求来进行参数的调整。
同时,需要根据实际生产情况进行不断的调试和优化,以达到最佳的注塑成型效果。
继续写相关内容:8. 塑料材料选择:注塑成型工艺参数与所选用的塑料材料密切相关。
注塑成型工艺参数解析【详尽版】

一、注塑成型工艺流程可以简单的表示如下:上一周期——闭模——填充——保压——回胶——冷却——开模——脱模——下一周期在填充保压降段,模腔压力随时间推移而上升,填充满型腔之后压力将保持在一个相对静态的状态,以补充由于收缩而产生的胶量不足,另外此压力可以防止由于注射的降低而产生的胶体倒流现象,这就是保压阶段,保压完了之后模腔压力逐渐下降,并随时间推移理论上可以降到零,但实际并不为零,所以脱模之后制品内部内存内应力,因而有的产品需经过后处理,清除残存应力。
所谓应力,就是来傅高子链或者链段自由运动的力,即弯曲变形,应力开裂、缩孔等。
二、注塑成型的主要参数1、料筒温度注塑胶料温度,熔体温度对熔体的流动性能起主要作用,由于塑胶没有具体的熔点,所谓熔点是一个熔融状态下的温度段,塑胶分子链的结构与组成不同,因而对其流动性的影响也不同,刚性分子链受温度影响较明显,如PC、PPS等,而柔性分子链如:PA、PP、PE等流动性通过改变温度并不明显,所以应根据不同的材料来调校合理的注塑温度。
2、注射速度注射速度是熔体在炮筒内(亦为螺杆的推进速度)的速度(MM/S)注射速度决定产品外观、尺寸、收缩性,流动状况分布等,一般为先慢——快——后慢,即先用一个较的速度是熔体更过主流道,分流道,进浇口,以达到平衡射胶的目的,然后快速充模方式填充满整个模腔,再以较慢速度补充收缩和逆流引起的胶料不足现象,直到浇口冻结,这样可以克服烧焦,气纹,缩水等品质不良产生。
3、注射压力注射压力是熔体克服前进所需的阻力,直接影响产品的尺寸,重量和变形等,不同的塑胶产品所需注塑压力不同,对于象PA、PP等材料,增加压力会使其流动性显著改善,注射压力大小决定产品的密度,即外观光泽性。
4、模具温度模具温度,有些塑胶料由于结晶化温度高,结晶速度慢,需要较高模温,有些由于控制尺寸和变形,或者脱模的需要,要较高的温度或较低温度,如PC一般要求60度以上,而PPS为了达到较好的外观和改善流动性,模温有时需要160度以上,因而模具温度对改善产品的外观、变形、尺寸,胶模方面有不可抵估的作用。
注塑成型工艺标准参数

+\注塑成型工艺参数第一节注塑工艺参数在制品和模具确立以后,注塑工艺参数的选择和调整对制质量量将产生直接影响。
注塑工艺详细是指温度、压力、速度、时间等相关参数,实质成型中应综合考虑,在能保证制质量量(如外观、尺寸精度、机械强度等)和成型作业效率(如成型周期)的基础上来决定。
只管不一样的注塑机调理方式各有所异,可是对工艺参数的设定和调整项目基本是相同的。
注塑工艺参数与注塑机的设计参数是相关系的,可是在这里主假如从注塑工艺角度理解这些参数。
一、注塑参数1.注射量:注射量是指注塑机螺杆(或柱塞)在注射时,向模具内所注射的物料熔体量(g )。
所以,注射量是由聚合物的物理性能及螺杆中料筒中的推动容积来确立的。
因而可知,选择注射量时,一方面一定充足地知足制品及其浇注系统的总用料量,另一方面一定小于注塑机的理论注射容积。
假如选用用注射量过小则会因注射量不足而使制品产生各样缺点,但过大又造成能源的浪费。
所以注塑料机不行用来加工小于注射量10% 或超出注射量70% 的制品,据统计世界上制品生产厂家大概有1/3的能源浪费在不合理地机型选择上。
2.计量行程(预塑行程):每次注射程序停止后,螺杆是处在料筒的最前地点,当预塑程序抵达时,螺杆开始旋转,物料被输送到螺杆头部,螺杆在物料的反压力作用下退后,直至遇到限位开关为止。
这个过程称计量过程或预塑过程,螺杆退后的距离称计量容积,也正是注射容积,其计量行程也正是注射行程。
所以制品所需的注射量是用计量行程工来调整的。
由此可知,注射量的大小与计量行程的精度相关,假如计量行程调理太小会造成注射量不足,假如计量行程调整太大,使料筒前部每次注射后的余料太多,使熔体温度不均或过热分解, 计量行程的重复精度的高低会影响注射量的颠簸 . 料温沿计量行程的散布是不均匀的,增添计量行程会加剧料温的不均匀性 . 螺杆转速、预塑背压和料筒的温度都将对熔体温度和温差有明显地影响 .在注射前处于螺杆头部计量室外中的熔体温度最高,固然也有温差,但在这时较小,在注射后,螺杆槽中熔体的温度最低, 逗留一段时间以后熔体温度上涨.这类温差能够采纳调整螺杆转速轴向背压或使用新式螺杆等方法使其获得改良。
- 1、下载文档前请自行甄别文档内容的完整性,平台不提供额外的编辑、内容补充、找答案等附加服务。
- 2、"仅部分预览"的文档,不可在线预览部分如存在完整性等问题,可反馈申请退款(可完整预览的文档不适用该条件!)。
- 3、如文档侵犯您的权益,请联系客服反馈,我们会尽快为您处理(人工客服工作时间:9:00-18:30)。
注塑成型工艺参数及其影响
11209040112 黄卓
摘要:塑料材料在生活中所占比例越来越高,而对于其质量的要求也越来越高,
注塑成型作为重要的生产手段,对技术的提高也越来越迫切,而注塑成型制品的影响因素较多,但注塑成型加工工艺条件是重要的影响因素之一,下面将会介绍个个工艺参数对于制品性能的影响。
关键词:注塑成型工艺参数
一、注塑成型概念
传统的模具设计和工艺参数设置主要依赖于设计者的经验和技巧,模具设计的合理性只有靠反复的试模和修模,工艺参数的设置也只能靠反复的试模来进行修改,缺乏科学依据,生产周期长,成本高,质量也难以保证。
而对成型过程进行模拟,在模具制造之前就可发现设计中的问题,使模具设计和工艺参数设置建立在科学的分析基础之上,可缩短生产周期,提高制品质量。
随着对制品质量要求的提高,对成型过程进行预测己经成为设计不可缺少的环节。
因此,建立注塑成型过程熔体在模腔中流动和传热的数学模型,并采用数值仿真方法实现成型过程的模拟具有重要的意义。
由于成型过程的工艺参数直接决定了熔体在模腔中的流动状态,对制品质量有着最直接最深远的影响,因此找到制品成型的最优工艺条件,对成型过程进行工艺控制,是提高塑料制品质量的有效途径。
这是因为,成型过程中,精密的成型机械、合理的模具设计和优良的材料性能只有在合理的成型工艺设置下刁`能体现出来另一方面,成型机械、模具设计和材料性能的缺陷有时可通过合适的成型工艺设置来弥补。
由此可见,注塑成型工艺对制品质量有着至关重要的作用
二、注塑工艺条件及其影响
1、注塑压力
注射压力指的是在注射过程中螺杆顶部或柱塞对于塑料熔体所加载的压力。
它的作用是对于使熔料混合和塑化,螺杆(或柱塞)必须提供克服固体粒子和熔料在料筒和喷嘴中的流动阻力。
使得塑料熔体以一定的速度来充满型腔,在型腔充满熔体后注射压力起到压实的作用。
从而使得塑件致密,并对熔料因冷却而产生的收缩进行补料,从而使塑件保持精确的形状,获得所需要的性能。
注射的压力主要由塑料的种类,注塑机的类型,模具的温度,模具结构,塑件的壁厚来决定的,其中浇注系统的尺寸与结构对于注射压力影响很大。
2、保压压力
当熔体充满型腔后,注射压力所起的作用为对于模内的熔体进行压实,此时我们把注射压力也叫做保压压力,在实际生产中,保压压力应该等于或小于注射时所用压力。
当保压时的压力与注射时的压力相等时,往往会使塑件的收缩率降低,而且可以保证塑件的稳定性以及塑件的力学性能。
但常常也会伴随着脱模时残余应力的增加,造成塑件脱模困难、使塑件容易产生变形、表面划伤等,也容易使塑件产生飞边,影响表观质量。
因此,选择保压压力时需要多方面考虑,慎
重选择。
一般来讲,保压压力对制品的质量影响与注射压力的影响相似。
大多数塑料的保压压力在注射压力的一之间,而具体保压压力的确定,主要考虑塑件材料的特性及制件的结构,并克服熔体从机筒到模腔的流动阻力,将熔料送入型腔并将之压实。
3、塑化压力
塑化压力是指螺杆顶部熔料在螺杆后退时所受到的压力。
它对注射成型的影响主要体现在注射机对物料的塑化效果及其塑化能力方面。
一般来讲,增大塑化压力,螺杆后退速度减小,机筒内熔体受到的压力随之增加。
于是塑化时剪切作用加强,塑化效果提高。
但须往意的是,增大背压的同时,过高的塑化压力一方面因熔体在螺槽边缘的反流和漏流而减少了塑化量,可能引起计量不足,另一方面会使剪切热过高剪切应力过大,有可能使物料降解,产生气泡或烧伤,影响塑件质量。
4、模具温度
模具温度是指在成型过程中的模腔表面的温度,模具温度影响熔体的充模流动行为、制品的冷却速度和成型后的制品性能等。
模温的设定主要取决于熔料的粘度。
熔料粘度较低的可以采取低模温注射以缩短冷却时间,提高生产效率。
熔料粘度较高的应采用高模温注射成型。
一般说来提高模温可以使制件的冷却速率均匀一致,防止凹痕和裂纹等成型缺陷产生。
结晶型塑料的模温控制直接决定了冷却速率,从而进一步决定结晶的速率。
模温高时冷却速率小,结晶速率变大,有利于分子的松弛过程,分子取向效应小。
模温太高,会延长成型周期和使产品发脆。
模温低,冷却速率大,熔料的流动与结晶同步进行,由于熔料在结晶温度+区间停留时间缩短,不利于晶体的生长,造成产品的分子结晶程度较低,影响其使用性能。
此外,模温过低,塑料熔体的流动阻力很大,流速变缓,甚至在充模中凝固妨碍后续进料,使得制件短射,强迫取向大,常造成塑件缺料、凹陷、熔接缝等缺陷。
5、料筒温度
为了保证塑料熔体的正常流动同时又不使其发生变质分解,需要合适的选择料筒温度,平均分子质量大,分子质量分布又较集中的塑料以及玻璃增强塑料都应选择温度较高的料筒温度。
料筒温度一般是按前高后低的原则进行排布,但当塑料中含有过多水费时也可适当提高后端温度。
6、喷嘴温度
为了避免熔体在喷嘴处产生流延现象,通常需要使喷嘴温度略低于料筒最高温度,在生产中一般将低速对空注射的情况下,喷出的溶流不带泡,光滑视为温度合适的标准。
7、熔体温度
熔体温度主要取决于机筒和喷嘴两部分的温度,影响物料的塑化和熔体的注射充模。
注射温度的提高主要有利于改善熔体的流动性,它与制品的很多特性有关。
升高熔体温度,可使塑件内应力、流线方向的冲击强度和挠曲度、拉伸强度等机械力学性能降低,而使垂直于流线方向的冲击强度、流动长度、表面粗糙度等性能有所改善,并可降低制品的后收缩。
从总体上看,提高熔体温度有利于改善充模状况以及在模腔内的传递,降低取向性等,有利于制品的综合性能的提高但过高的温度也不可取。
当熔体温度接近注塑温度范围的上限值时,一方面容易产生较多的气体,使塑件产生气泡、空
洞、变色、烧焦等,也因过多地改善流动性而产生飞边,影响制品表观质量另一方面,过高的温度会使塑料发生降解作用,使塑件强度降低,失去弹性等,影响使用性能。
8、注射时间
注射时间是控制注射速率的参数之一。
注射时间越短,则注射速率越高,注射速率的大小对塑件的性能有很大影响。
提高注射速率可使充模压力提高,有利于充模过程,并使充模中的热量散失减少,模腔温度比较均匀,制品均匀而密实。
同时可降低制品收缩率,减少塑件芯部取向,增加熔接缝强度。
注射速率的提高有益于制品的综合性能,但过高的注射速率会增加压力损失,降低固化层厚度,提高塑件表层取向性,甚至使熔体发生弹性湍流,使塑件容易形成飞边、表面裂纹等。
经实验证明:过高过低的注射速率都会导致冲击强度的下降。
另一方面,过低的注射速率使塑件熔接缝强度下降,总取向作用增大,内应力增高等,影响制品力学性能。
9、保压时间
保压时间和冷却时间的长短也对塑件的质量产生直接影响。
缩短保压时间,会使模腔压力降低加快,有可能产生倒流,使塑件产生缩孔、凹陷等缺陷,并影响塑件尺寸的稳定性。
加长保压时间,可提高塑件尺寸的稳定性避免上述缺陷的发生,得到致密的产品。
同时会使模腔压力提高,改变由于温度不均而产生的内应力。
但会增加脱模难度,有时容易产生表面顶出划伤或将塑件顶弯的现象。
材料塑化时间的长短可影响塑化质量,直接影响产品性能。
时间太短了不能使塑化均匀、温度一致,容易产生硬块、银丝等而太长了又会使熔料因螺杆的作用而发生分解、烧伤等,也给产品质量带来不良影响。
10、特殊工艺影响
振动注塑成型,在高的振动压力下,随着振动频率的提高,制品的拉伸性能和缺口冲击强度明显得到提高。
除此之外超声工艺的加入也能起到良好的效果。
三、结论
注塑成型加工工艺条件对塑料制品的表观和力学性能造成影响,每一个工艺条件参数都相互影响并不是独立的,有些制品的缺陷是相互影响的结果。
参考文献:
【1】路书芬,注塑成型工艺参数对制品质量影响的实验研究,郑州大学硕士学位论文,2006
【2】单岩,王蓓,王刚模具分析技术基础,北京清华大学出版社,2005
【3】刘来英主编,注塑成型工艺,机械工业出版社,2004
【4】卫炜、注塑成型工艺参数多目标优化设计、中南林业科技大学、2009 【5】韦超、注塑模中关键参数对产品性能影响的研究、新僵大学、2013。