物料需求计划表格式
产品bom表格式
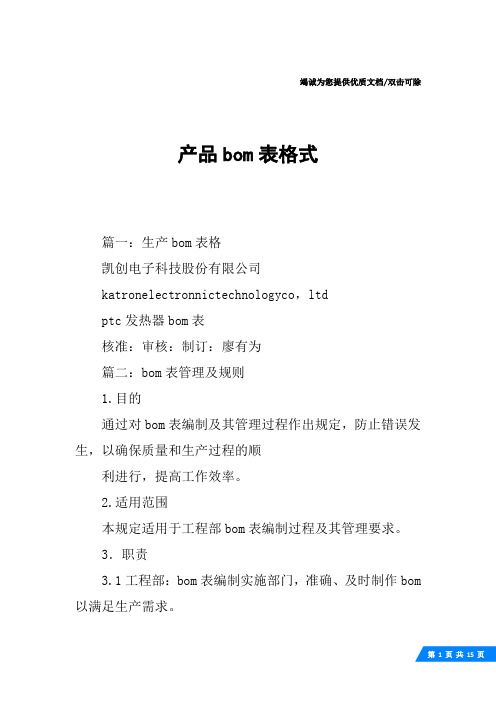
竭诚为您提供优质文档/双击可除产品bom表格式篇一:生产bom表格凯创电子科技股份有限公司katronelectronnictechnologyco,ltdptc发热器bom表核准:审核:制订:廖有为篇二:bom表管理及规则1.目的通过对bom表编制及其管理过程作出规定,防止错误发生,以确保质量和生产过程的顺利进行,提高工作效率。
2.适用范围本规定适用于工程部bom表编制过程及其管理要求。
3.职责3.1工程部:bom表编制实施部门,准确、及时制作bom 以满足生产需求。
3.2物控计划处:提供本期生产任务资料,并督导bom 表编制完成。
3.3生产部:bom表接受单位,及时反馈信息至工程部。
4.bom编制及管理流程4.1bom结构说明:不同的机种有不同的bom。
一份综合的bom由阶层、序号、料号、描述、单位用量组成。
所谓的阶层也就是物料在产品中的结构位置,父项与子项的关系,单层bom是针对一个阶层的物料清单。
4.2对编制或修订bom的时机:4.2.1市场部提供客户之bom或设计变更通知,交工程部进行物料编号和本公司bom编制或修订。
4.2.2bom编制或修订后经工程部经理核准后由文件管制中心列管,并分发相关部门。
4.3bom的发出时机:bom要在投产之前发出。
.4.4bom表编制依据4.4.1bom制作依据为《产品配置表》、《物料编码表》4.4.2编制的类型为产品结构树形产品结构树的层次结构必须反映产品的功能划分与组成;必须考虑产品的生产和商务需求。
在产品的总体设计方案完成后,要通过产品结构树来实现产品的功能划分,将产品实物化。
产品结构树的完成是产品总体设计完成的标志之一。
例如:成品-1309l主板上盖宏旭钢件银色主板上盖宏旭钢件银色面漆主板上盖宏旭钢件银色镭雕-1309l主板上盖宏旭钢件银色底中漆素材-1309l主板上盖宏旭钢件白色油漆:700-底漆油漆:800-中漆镀材:铟丝油漆:900-面漆备注:具体格式见bom表格式模板。
物料需求计划

3、现有库存量(POH)
其概念与MPS中的概念相同,指每周需求被满足之后手头仍有的库存量。该记录随着每周 进货或出货的情况而更新,未来各周的POH则可计算的出
4、计划订货入库量 (PR)
含义是,计划订货或生产、但订单尚未发出的订货量。这个量的意义是要保持POH的量不 低于安全库存(在MPS中未考虑安全库存,保持POH非负即可)。对于某些不需要安全库
某办公家具公司,其两种主要产品(即企业要出厂的最终产品)是办公用椅A和B,其需 求大致稳定:产品A每周需30个,产品B每周需20个。这两种产品都需要用到一种支架部
件C。因此,对C的平均需求量是每周50个。A和B的装配期是1周
如右图示,在这种格式中,左上方通常要标出产品名称及其性质(如右图中,表明C是支 架部件),右上方表示计划因子,通常包括三项:生产批量、生产周期和安全库存量。 在本例中,C的批量是230个,生产周期为2周,安全库存量为50个。这些计划因子的量都 需要预先选定。当这些值发生变化以后,管理人员必须及时更新库存记录。下面首先来
存的中间物料,则如同MPS,其意义是要保持POH非负
在库存记录中所表示的PR量应包括这两种情况: 1)在POH出现短缺(或为负值或小于安全库存量)的当周制订一个PR量,其值的大小应是POH大于等于安全库存 2)继续计算其后各周的POH,当又出现短缺时,制订下一个PR量
5、计划发出订货量 (plannedorderreleas
基本计算模式
物料需求计划(MRP)的制定需要三个关键信息:MPS、BOM、库存记录
MPS
主生产计划
BOM
物料清单
库存记录
在MRP的制定过程中,库存记录的计算方法构成了MRP的基本计算模型
SAP物料需求计划(MRP)流程

流程名称:物料需求计划(MRP)流程流程编号及版本号编号:EYANG_BPD_PP_SCN002_01版本:V2.0流程定义文件签署表业务流程定义文件是描述未来在SAP R/3中处理业务的详细流程定义,其中所涉及的SAP功能已得到项目组成员的接受并已签署。
版本修改历史图例:流程说明SAP输出1流程说明:1.1 流程概述:本流程用于描述并规范SAP系统MRP相关数据的维护,以及MRP运行结果的处理流程。
由于生产的特殊性,比如成品替代、联产品、多重BOM、一物多码、物料等级等,因此不能从成品层开始跑MRP,而是要通过开发,分解到测试半成品一层,再运行MRP。
运行MRP的目的并非取代人工计划,而是为了如下目的:A、系统给出的建议,与人工计划相互验证,相互促进,从而使计划更加合理,更加有依据;B、根据运行MRP的结果,来反应BOM、销单、采购单、库存、工单的异常情况,从而促进相关业务规范,形成闭环。
1.2 使用范围:需求分工厂:本流程中,有两次手工拆分。
一次是拆分自制与外购(深加工部分),深加工部分在深加工工厂下建独立需求,其余的放在自定义表里。
另一次是拆分金宇阳和深宇各自的测试半成品需求量,两者都在深宇工厂下建独立需求,后续用系统标准的MRP,会自动考虑工厂各层物料的库存。
MRP在各工厂级运行,在工厂下产生建议,可以用权限控制各工厂自行采购或集团采购。
关于长采购周期物料,由于3个月的销售预测不能覆盖长采购周期的物料,因此需要设置安全库存方能借助系统的MRP功能产生采购建议。
设置安全库存和采购周期节点,属物料主数据MRP视图维护,未在本流程图中体现,但本周流程中的运行MRP环节,若用MD01全工厂所有物料运行,则设置安全库存的长采购周期物料也同时产生采购申请。
1.3 流程相关原则:为了保证系统运行的MRP结果能用来指导生产计划和采购计划,需要如下业务相应规范:✧物料主数据中MRP参数设置合理:比如生产周期、采购周期、批量、策略、特殊采购类型等✧BOM表,生产周期,采购周期的准确性✧销售订单形成闭环,即,未完全交货的销售订单在确认客户不再交货的情况下,设置拒绝✧生产订单形成闭环,即,未完全交货的生产订单在确认不再继续生产的情况下,设置技术完成✧采购订单形成闭环,即,未完全交货的采购订单在确认不再收货的情况下,设置“交货已完成”标识✧对过期的独立需求及时清理1.4 流程涉及SAP术语解释与未来系统关键参数确定1.1.1计划独立需求计划独立需求,是在没有客户订单的情况下,在系统中录入的需求源,用以运行MRP,从而产生生产计划和采购计划,一般把销售预测数据作为计划独立需求的来源。
物料表的编制规则
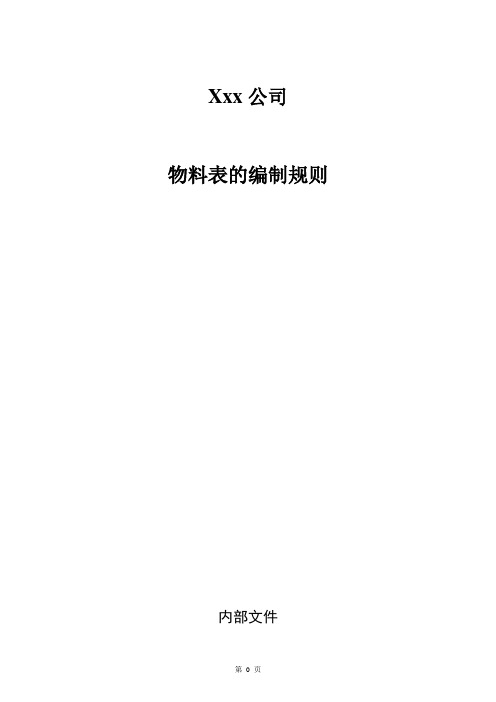
Xxx公司物料表的编制规则内部文件第0 页1.物料表的概念BOM(“Bill of Material”,“物料清单”)是指产品所需零部件明细表,即所有与生产该产品有关的物料的统称,此处称物料表。
2.物料表的作用物料表作为产品结构的描述性文件,在目前企业日新月异的ERP管理系统中起到非常重要的作用,它的主要作用及意义如下:2.1 它是生成物料需求计划的基本信息,是联系主生产计划和物料需求计划的桥梁;2.2 物料工艺路线可以根据BOM来生成产品的总工艺路线;2.3为采购外协加工提供依据;2.4为生产线提供依据;2.5成本数据可以根据物料清单来计算;2.6提供制定销售价格的依据;2.7针对公司本身的需求,规范BOM的编制,加强对它的管理,可以防止和减少错误发生,确保质量和生产过程的顺利,提高工作效率;3.物料表的格式物料表的上方填写本产品的代码编号名称型号规格客户型号等信息,表单明细栏可按着具体需求填写编码、材料及规格、单位、用量、重量、备注等。
4.物料表中物料的分层为了表达产品的结构层次和制作工艺,更好的对物料进行管理,在创建物料表的时候可以对物料进行分层。
5.物料表中的物料编码5.1根据公司本身的产品类别和所需物料的特点,可以对其分类并按统一的规则进行编码5.2在公司的物料管理中,物料编码不可重复;同一个物料也不可出现多个编码。
6.其他6.1在图号栏录入有零件图物料的图纸的图号6.2 物料表与图纸里物料的名称规格等属性保持一致,并且各属性的描述要符合公司自己的规范6.3标准件的描述按国家标准或行业标准即可6.4 材料及规格栏的填写主张先写规格,然后写材料及牌号等6.5备注栏:可填写装配位置、加工方法等特殊事项。
6.6在物料表的上方要注明产品的型号、名称、同时也要在规格栏注明电压、功率、频率及安规、食品、环保等认证要求,还需填写产品代码(即物料编码)、文件编号和版本。
6.7不能通过规格栏的描述确定的物料(包括包装材料)都要画零件图然后填写图号6.8在前期其他物料表的制作中已经建立并存在的物料在新建的物料表中要直接借用,要严格控制新增物料的添加,避免同一个物料建立多个物料编码7.物料表的编制审批与受控物料表由产品工程师起草编制,并由相关人员对其进行校对审批,通过后交给档案管理部门受控,同时由档案管路部门将复印副本发给需要的部门使用。
什么叫物料清单

物料清单(BOM)一,什么BOM表物料清单(Bill of Material, BOM)是指产品所需零部件明细表及其结构.在MRP2中,物料一词有着广泛的含义,它是所有产品,半成品,在制品,原材料,配套件,协作件,易耗品等等与生产有关的物料的统称.采用计算机辅助企业生产管理,首先要使计算机能够读出企业所制造的产品构成和所有要涉及的物料,为了便于计算机识别,必须把用图示表达的产品结构转化成某种数据格式,这种以数据格式来描述产品结构的文件就是物料清单,即是BOM.它是定义产品结构的技术文件,因此,它又称为产品结构表或产品结构树.BOM是由双亲件及子件所组成的关系树.BOM可以是自顶向下分解的形式或是以自底向上跟踪的形式提供信息.分解是从上层物料开始将其展开成下层零件,跟踪是从零件开始得到上层物料.将最终产品的需求或主生产计划中的项目分解成零件需求是MRP建立所有低层零件计划的关键一步.如果低层零件计划存在问题,通过跟踪就能确定生成这一零件需求的上层物料.为了便于计算机管理和处理的方便,BOM 必须具有某种合理的组织形式,而且为了便于在不同的场合下使用BOM,BOM还应有多种组织形式和格式.BOM是MRP2系统中最重要的基础数据其组织格式设计和合理与否直接影响到系统的处理性能,因此,根据实际的使用环境,灵活地设计合理且有效的BOM是十分重要的.BOM不仅是MRP2系统中重要的输入数据,而且是财务部门核算成本,制造部门组织生产等的重要依据,因此,BOM的影响面最大,对它的准确性要求也最高.采取有力措施,正确地使用与维护BOM是系统运行期间十分重要的工作,必须引起足够的重视.此外,BOM还是CIMS/MIS与CAD,CAPP等子系统的重要接口,是系统集成的关键之处,因此,用计算机实现BOM管理时,应充分考虑它于其他子系统的信息交换问题.BOM信息被用于MRP计算,成本计算,库存管理.BOM有各种形式,这些形式取决于它的用途,BOM的具体用途有:1.是计算机识别物料的基础依据.2.是编制计划的依据.3.是配套和领料的依据.4.根据它进行加工过程的跟踪.5.是采购和外协的依据.6.根据它进行成本的计算.7.可以作为报价参考.8.进行物料追溯.9.使设计系列化,标准化,通用化.二,BOM的使用在任何制造环境中,不同的部门和系统都为不同的目的使用BOM,每个部门和系统都从BOM中获取特定的数据.主要的BOM用户有:设计部门设计部门既是BOM的设计者,又是BOM的使用者.就使用而言,无论何时,当产品结构发生变化,或对某个零件进行重新设计,该部门都要从BOM中获取所有零件的信息及其相互间的结构信息,只有得到这些信息,才能对其进行定义,描述或修改.●工艺部门工艺部门根据BOM信息建立各零件的制造工艺和装配件的装配工艺.并确定加工制造过程中应使用的工装,模具等.●生产部门生产部门使用BOM来决定零件或最终产品的制造方法,决定领取的物料清单.●产品成本核算部门该部门利用BOM中每个自制件或外购件的当前成本来确定最终产品的成本.●物料需求计划(MRP)系统BOM是MRP的主要输入信息之一,它利用BOM决定主生产计划项目时,需要哪些自制件和外购件,需要多少,何时需要.三,BOM的构造问题:前面已经提到,BOM是系统中最重要的基础数据库,它几乎与企业中的所有职能部门都有关系,BOM构造的好坏,直接影响到系统的处理性能和使用效果.因此,根据实际环境,,灵活地构造BOM是十分关键的.就一般情况而言,构造BOM 应注意以下方面.1.在BOM中,每一个项目(零件)必须有一个唯一的编码.对于同一个项目,不管它出现在哪些产品中,都必须具有相同的编码.对于相似的项目,不管它们的差别有多么小,也必须使用不同的编码.2.为了管理上的方便,有时可以将同一零件的不同状态视为几个不同的项目,构造在产品的BOM中.3.BOM中的零件,部件的层次关系一定要反映实际装配过程,在实际装配中,有时不一定把某些零件装配成某个有名称的组件,或者由于工艺上的考虑需要将某些零件归在一起加工(例如箱子与箱盖).形成临时组件,但这些组件在产品的零件明细表和装配图上并没有反映出来,但必须在计划管理中反映出来,这就需要在BOM中设置一种物理上并不存在的项目,通常称为”虚单”或”虚拟件”,其目的是简化MRP的编程过程和减少零件之间的影响.4.根据生产实际情况,有时为了强化某些工装,模具的准备工作,还可以将这些工具构造在BOM中.这样就可以将一些重要的生产准备工作纳入计划中.有时为了控制某个重要的零件在加工过程中的某些重要环节,比如,进行质量检测等,还可将同一个零件的不同加工状态视为不同的零件,构造在BOM中.5.为了满足不同部门获取零件的不同信息,可以灵活地设计BOM中每个项目的属性.例如,计划方面的,成本方面,库存方面,订单方面.四,BOM的维护BOM是任何管理系统中基础中的基础,如果没有BOM,就无法制造出同样的产品,为此要想提高生产管理系统的效率,BOM的正确与否是十分重要的.(1)不正确BOM造成影响●一些项目为BOM所遗漏,造成零件短缺.●BOM中列入了一些不必要的项目,导致零件过多储备.●由于缺件的数量过多,导致制造的低效率.●订单不能按期交货●质量低下●计划缺乏可信性●不正确的产品成本●废弃的库存(2)BOM中发生错误的环节●工程部门产生BOM时●为BOM准备数据时●BOM数据录入时(3)正确维护BOM的方法●指定专人负责维护BOM●经常监测BOM,检查项目数量及其生效日期●对工程改变进行分类●危机性改变—立即完成.如,产品不能实现其功能,或不利于安全时.●紧急性改变—迅速完成.如,工程部门设置一个合理日期来完成改变●常规改变—从经济实用角度要求变化时再完成.●通知要进行的工程改变●实施工程改变。
MRP计划表例题

mrp计算原理:根据主生产计划(mps)、库存计划、物料清单(bom),制定物料需求计划(mrp) 主要公式:毛需求量=独立需求量+相关需求量 计划库存量=上期期末库存量+本期订单产出量+本期预计入库量-毛需求量 净需求量=本期毛需求量-上期库存量-本期预计入库量+安全库存量 bom中各物料的数量关系 高层次与其下一层在数量上的倍数关系,由下一层旁边括号内的数字决定。
例如: ab┌───┼───┐┌───┼───┐ d(1) e(2) c(1) e(1) f(2) c(1) ┌─┴─┐ ┌─┴─┐ ┌─┴─┐ e(1) f(1) f(2) d(1) f(2) d(1) ┌─┴─┐ ┌─┴─ e(1) f(1) e(1) f(1) c、d、e、f的相关需求关系式为: c=a+b d=a+ce=2a+b+d f=2b+d+2c 计算mrp时注意三个问题 1.是否有安全库存 2.是否有批量限制 3.提前期是多少 例题1:已知1个a由2个b和1个c组成,1个b由1个d和1个c组成,各物料的提前期均为1周,下表是客户对产品a的订单需求表,运用mrp求a产品的物料需求计划。
例题2.某家具公司组装餐桌,具体部件包括4个桌腿和1个桌面,提前期分别为2周和3周,组装需要1周的时间,公司接到40张餐桌的订单,需要在第5周交货,另外70张要在第7周交货,当前库存中有6张完工的餐桌,80张桌腿和44张桌面,请利用mrp求出公司的订货计划。
练习题: 主生产计划: bom: 库存信息以及提前期: 物料的需求计划: 例题3:某厂生产产品x,产品x的需求量见表1,并已知安全库存为3件,批量为25件,投入提前期为1周,期初库存为8件,期初计划到货为20件。
1件产品x需要2个部件y,并已知部件y每周作为备件外售需要量为4件,安全库存为12件,批量为60件,投入提前期为1周,期初库存为18件,计划第1周入库50件,试用mrp方法编制x和部件y的生产作业计划。
物料需求计划
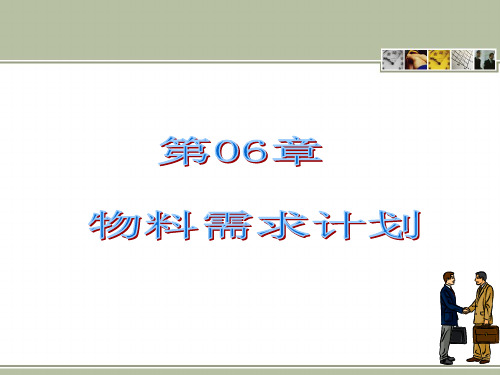
MRP既是一种较精确的生产计划系统, MRP既是一种较精确的生产计划系统,又是一种有效的物料控 既是一种较精确的生产计划系统 制系统, 协调生产的物料需求和库存之间的差距, 如图6 制系统 , 协调生产的物料需求和库存之间的差距 , 如图 6-1所 示。
物料需求 划功能
6.2 MRP作用与意义 作用与意义
物料需求计划(MRP): 物料需求计划(MRP): MPS 求 进 主要解决五个问题: 现MPS 证 ,主要解决五个问题: 开, 实
要生产什么?生产多少? 来源于MPS) 要生产什么?生产多少?(来源于MPS) MPS 要用到什么?(根据BOM展开) 要用到什么? 根据BOM展开) BOM展开 已经有了什么? 根据物品库存信息、即将到货或产出信息) 已经有了什么?(根据物品库存信息、即将到货或产出信息) 还缺什么? 计算出结果) 还缺什么?(计算出结果) 何时安排? 计算出结果) 何时安排?(计算出结果)
6.1 MRP概念及内容 MRP概念及内容 MRP作用与意义 6.2 MRP作用与意义 6.3 物 料 清 单 6.4 MRP基本原理 MRP基本原理 MRP计算模型 6.5* MRP计算模型 MRP的编制 6.6 MRP的编制 6.7 本 章 小 结 思考练习题
6.1 MRP概念及内容 概念及内容
6.3 物 料 清 单
物料清单(产品结构树, Material,BOM): 物料清单(产品结构树,Bill of Material,BOM):指产品所 需零部件明细表及其结构的技术文件。为了便于计算机识别, 需零部件明细表及其结构的技术文件。为了便于计算机识别, 把用图示表达的产品结构转化成某种数据格式, 把用图示表达的产品结构转化成某种数据格式,这种以数据 格式来描述产品结构的文件就是物料清单。 格式来描述产品结构的文件就是物料清单。
Mrp系统
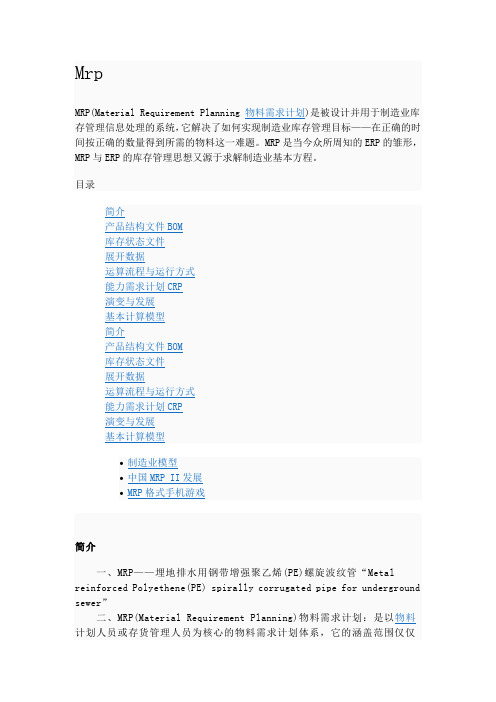
MrpMRP(Material Requirement Planning 物料需求计划)是被设计并用于制造业库存管理信息处理的系统,它解决了如何实现制造业库存管理目标——在正确的时间按正确的数量得到所需的物料这一难题。
MRP是当今众所周知的ERP的雏形,MRP与ERP的库存管理思想又源于求解制造业基本方程。
目录简介一、MRP——埋地排水用钢带增强聚乙烯(PE)螺旋波纹管“Metal reinforced Polyethene(PE) spirally corrugated pipe for underground sewer”二、MRP(Material Requirement Planning)物料需求计划:是以物料计划人员或存货管理人员为核心的物料需求计划体系,它的涵盖范围仅仅为物料管理这一块。
主要用于非独立性需求(相关性需求)性质的库存控制。
从MRP到ERP制造资源计划(Manufacturing Resources Planning简称MRPⅡ:将公司高层管理与中层管理结合在一起,以制造资源计划为活动核心,促使企业管理循环的动作,达到最有效的企业经营。
其涵盖范围包含了企业的整个生产经营体系,包括经营目标、销售策划、财务策划、生产策划、物料需求计划、采购管理、现场管理、运输管理、绩效评价等等各个方面。
企业怎样才能在规定的时间,规定的地点,按照规定的数量得到真正需要的物料,换句话说,就是库存管理怎样才能符合生产计划的要求,这是物料需求计划所解决的。
MRP起初出现在美国,并由美国生产与库存管理协会倡导而发展起来的。
MRP是一种以计算机为基础的编制生产与实行控制的系统,它不仅是一种新的计划管理方法,而且也是一种新的组织生产方式。
MRP的出现和发展,引起了生产管理理论和实践的变革。
MRP是根据总生产进度计划中规定的最终产品的交货日期,规定必须完成各项作业的时间,编制所有较低层次零部件的生产进度计划,对外计划各种零部件的采购时间与数量,对内确定生产部门应进行加工生产的时间和数量。
《ERP》Unit_05_物料需求计划与能力需求计划
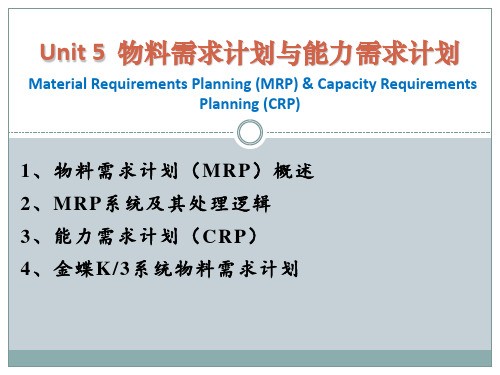
举例:表上作业法
21
准备 MRP 处理所需的各种输入,将 MPS 作为确认的生产订单
下达传给MRP。
根据产品的BOM,从第一层项目起,逐层处理各个项目直至
最低层处理完毕为止。
A
LT=2
0层
低位码处理
A
LT=2
0层
LT=1
B(1)
C(2)
LT=2
1层
LT=1
B(1)
1层
C(2)
1.00 1.00 1.00
M-----自制件
《ERP原理与应用》
B-----外购件
15
16
A B(1) C(2) D(2)
0层 1层 2层 3层 4层
低层码 / 低位码: 相同的元件出现 在不同的层次 上——采用低层 码技术处理,即 取其最低层次号,
D(3) G(3kg)
C(2)
E(3)
D(3)
A 2 (0 层)周
B 1 (1 层)周
C 2 (2 层)周
总需要量 预计到货量 0 现有数 净需要量 计划发出订货量 总需要量 预计到货量 2 现有数 净需要量 计划发出订货量 总需要量 预计到货量 5 现有数 净需要量 计划发出订货量
20 5 10 15 15 15 5
22
15
-5 5 26
《ERP原理与应用》
Unit 5 物料需求计划与能力需求计划
Material Requirements Planning (MRP) & Capacity Requirements Planning (CRP)
1 、物料需求计划 ( MRP )概述 2 、 MRP 系统及其处理逻辑 3 、能力需求计划 ( CRP )
MRP计划表例题

mrp计算原理:根据主生产计划(mps)、库存计划、物料清单(bom),制定物料需求计划(mrp)主要公式:毛需求量=独立需求量+相关需求量计划库存量=上期期末库存量+本期订单产出量+本期预计入库量-毛需求量净需求量=本期毛需求量-上期库存量-本期预计入库量+安全库存量 bom中各物料的数量关系高层次与其下一层在数量上的倍数关系,由下一层旁边括号内的数字决定。
例如:a b┌───┼───┐┌───┼───┐ d(1)e(2) c(1) e(1) f(2) c(1) ┌─┴─┐┌─┴─┐┌─┴─┐ e(1) f(1) f(2)d(1) f(2) d(1) ┌─┴─┐┌─┴─ e(1)f(1) e(1) f(1) c、d、e、f的相关需求关系式为: c=a+b d=a+ce=2a+b+d f=2b+d+2c 计算mrp时注意三个问题 1.是否有安全库存 2.是否有批量限制 3.提前期是多少例题1:已知1个a由2个b和1个c组成,1个b由1个d和1个c组成,各物料的提前期均为1周,下表是客户对产品a的订单需求表,运用mrp求a产品的物料需求计划。
例题2.某家具公司组装餐桌,具体部件包括4个桌腿和1个桌面,提前期分别为2周和3周,组装需要1周的时间,公司接到40张餐桌的订单,需要在第5周交货,另外70张要在第7周交货,当前库存中有6张完工的餐桌,80张桌腿和44张桌面,请利用mrp求出公司的订货计划。
练习题:主生产计划:bom:库存信息以及提前期:物料的需求计划:例题3:某厂生产产品x,产品x的需求量见表1,并已知安全库存为3件,批量为25件,投入提前期为1周,期初库存为8件,期初计划到货为20件。
1件产品x需要2个部件y,并已知部件y每周作为备件外售需要量为4件,安全库存为12件,批量为60件,投入提前期为1周,期初库存为18件,计划第1周入库50件,试用mrp方法编制x和部件y的生产作业计划。
表 1 产品x的需求量篇二:mrp计算题mrp库存管理练习题1、购买零件a的前置时间是4周,零件a现有数量为22件,另外在第4周的预计到达量为20件,今后8周对零件a的需求量如表6-31所示。
物料需求计划计算举例
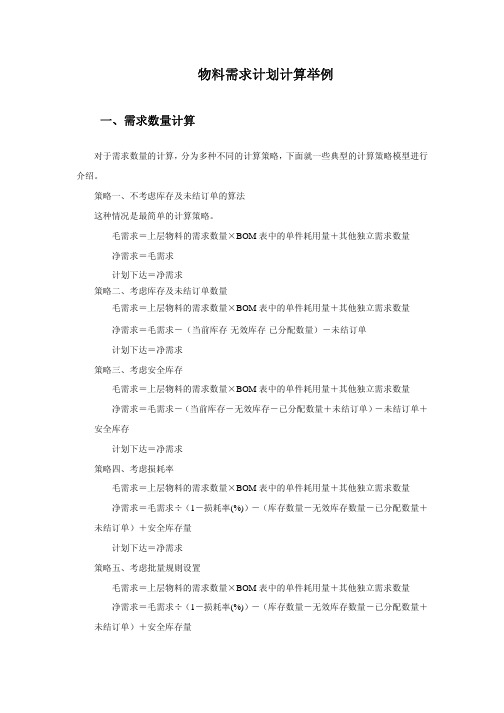
计划完工日期(调整后)=计划完工日期(调整前)+提前期余量
计划开工日期(调整后)=计划开工日期(调整前)+提前期余量
5、考虑工厂日历
如果计划开工日期和计划完工日期中间的时间段落在工厂日历的休息日,计划开工日期
和计划完工日期相应做顺延调整。
对于一些大型的企业,其组织结构可能还包括一些子公司、部门、生产车间等下级部门,
需要注意的是,如果物料的批量原则是 POQ 时,物料的订货周期(P)将影响到计划 完工日期。
2、计算物料的订货提前期 订货提前期=固定订货提前期+变动订货提前期 变动订货提前期=取大整数(变动订货提前期系数×订货批量÷变动提前期批量) 3、计算计划开工日期 计划开工日期=计划完工日期-订货提前期 物料需求计划在计算时,必须考虑工厂日历和提前期余量设置情况。 4、增加提前期余量调整
=2007 年 11 月 18 日 同时因为 2007 年 11 月 17 日和 2007 年 11 月 18 日为双休日,相应的计划开工日期再次 向前提前至工作日,计划完工日期为工作日,保持不变。 计划完工日期=2007 年 11 月 27 日 计划开工日期=2007 年 11 月 18 日-2 天
00
1
1
1
20
00
00
00
2
2
2
00
00
00
在策略二情况下,由于考虑了当前库存和未结订单的数量,塑料套的净需求发生了变化。 具体计算步骤如下:
毛需求=上层物料的需求数量×BOM 表中的单件耗用量+独立需求 =100×1×2+10 =210
净需求=毛需求-(当前库存-无效库存-已分配数量)-未结订单 =210-(10-4-3)-5 =202
=120 由于三脚架的批量增量为 120,所以本次最终的计划下达数量为 120.
Openbravo ERP介绍(一)

本文是我苦熬了一周时间整理出来的,欢迎各位浏览和转载,但麻烦阁下注明出处:转自王良明的博客。
这样能鼓励鼓励一下俺呢,以后还有更多的奉献,呵呵。
【注意:很多朋友询问安装了OB后用Openbravo登录进去看到的菜单只是一个框架,那是由于OB的特性决定的,您必须要切换角色才能看到具体的业务菜单。
切换角色的办法是:登录后点击左上角的用户名-->然后就可以更改角色了-->确认之后就可以操作业务功能菜单了】。
在网站上排名开源ERP类旁榜首,那应该是真金白银的——不光有华丽的外表,更应该有稳定的内核。
经过本人的一番长时间的实验测试,果然名不虚传。
本文我从以下几方面谈谈我个人的看法:1. OpenbravoERP的发行1.1.Openbravo ERP版本的成长1.2.版本类型:社区版和专业版2.系统要求2.1.OpenbravoERP运行环境2.2.本地化3.OpenbravoERP概况4.功能介绍4.1.应用字典(AD)4.2.通用设置(General Setup)4.3. 主数据管理(Master Data Management)4.4. 采购管理(Procurement Management)4.5. 库存管理(Warehouse Management)4.6. 生产管理(Production Management)4.7. 物料需求计划(Materials Requirement Planning)4.8. 销售管理(Sales Management)4.9. 项目管理(Project & Service Management)4.10. 财务管理(Financial Management)5.业务操作流程简介6.附录6.1.快捷键1.OpenbravoERP的发行1.1. Openbravo ERP版本的成长1)、阿发/贝塔版本(alpha/beta):在阿发版本阶段,我们每周发行一个阿发版本,当条件成熟时发行一个贝塔版本。
MRP计划表例题【范本模板】
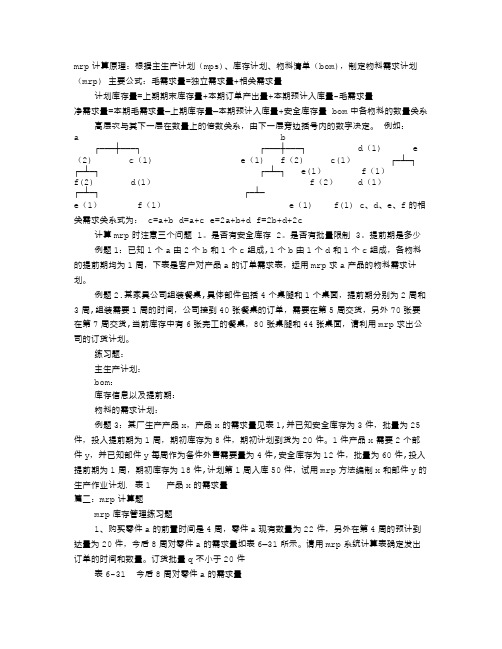
mrp计算原理:根据主生产计划(mps)、库存计划、物料清单(bom),制定物料需求计划(mrp) 主要公式:毛需求量=独立需求量+相关需求量计划库存量=上期期末库存量+本期订单产出量+本期预计入库量-毛需求量净需求量=本期毛需求量—上期库存量—本期预计入库量+安全库存量 bom中各物料的数量关系高层次与其下一层在数量上的倍数关系,由下一层旁边括号内的数字决定。
例如:a b┌───┼───┐ ┌───┼───┐ d(1) e(2) c(1) e(1) f(2) c(1)┌─┴─┐ ┌─┴─┐ ┌─┴─┐ e(1) f(1)f(2) d(1) f(2) d(1)┌─┴─┐ ┌─┴─e(1) f(1) e(1) f(1) c、d、e、f的相关需求关系式为: c=a+b d=a+c e=2a+b+d f=2b+d+2c计算mrp时注意三个问题 1。
是否有安全库存 2。
是否有批量限制 3。
提前期是多少例题1:已知1个a由2个b和1个c组成,1个b由1个d和1个c组成,各物料的提前期均为1周,下表是客户对产品a的订单需求表,运用mrp求a产品的物料需求计划。
例题2.某家具公司组装餐桌,具体部件包括4个桌腿和1个桌面,提前期分别为2周和3周,组装需要1周的时间,公司接到40张餐桌的订单,需要在第5周交货,另外70张要在第7周交货,当前库存中有6张完工的餐桌,80张桌腿和44张桌面,请利用mrp求出公司的订货计划。
练习题:主生产计划:bom:库存信息以及提前期:物料的需求计划:例题3:某厂生产产品x,产品x的需求量见表1,并已知安全库存为3件,批量为25件,投入提前期为1周,期初库存为8件,期初计划到货为20件。
1件产品x需要2个部件y,并已知部件y每周作为备件外售需要量为4件,安全库存为12件,批量为60件,投入提前期为1周,期初库存为18件,计划第1周入库50件,试用mrp方法编制x和部件y的生产作业计划.表1 产品x的需求量篇二:mrp计算题mrp库存管理练习题1、购买零件a的前置时间是4周,零件a现有数量为22件,另外在第4周的预计到达量为20件,今后8周对零件a的需求量如表6—31所示。
MRP

MRPMRP(Material Requirement Planning)物料需求计划:是以物料计划人员或存货管理人员为核心的物料需求计划体系,它的涵盖范围仅仅为物料管理这一块。
主要用于非独立性需求(相关性需求)性质的库存控制。
制造资源计划(Manufacturing Resources Planning简称MRPⅡ:将公司高层管理与中层管理结合在一起,以制造资源计划为活动核心,促使企业管理循环的动作,达到最有效的企业经营。
其涵盖范围包含了企业的整个生产经营体系,包括经营目标、销售策划、财务策划、生产策划、物料需求计划、采购管理、现场管理、运输管理、绩效评价等等各个方面。
企业怎样才能在规定的时间,规定的地点,按照规定的数量得到真正需要的物料,换句话说,就是库存管理怎样才能符合生产计划的要求,这是物料需求计划所解决的。
MRP起初出现在美国,并由美国生产与库存管理协会倡导而发展起来的。
MRP是一种以计算机为基础的编制生产与实行控制的系统,它不仅是一种新的计划管理方法,而且也是一种新的组织生产方式。
MRP的出现和发展,引起了生产管理理论和实践的变革。
MRP是根据总生产进度计划中规定的最终产品的交货日期,规定必须完成各项作业的时间,编制所有较低层次零部件的生产进度计划,对外计划各种零部件的采购时间与数量,对内确定生产部门应进行加工生产的时间和数量。
一旦作业不能按计划完成时,MRP系统可以对采购和生产进度的时间和数量加以调整,使各项作业的优先顺序符合实际情况。
物料需求计划(Material Requirements Planning),是一种企业管理软件,实现对企业的库存和生产的有效管理。
物料需求计划是以物料计划人员或存货管理人员为核心的物料需求计划体系,它的涵盖范围仅仅为物料管理这一块。
物料需求计划是一种以计算机为基础的生产计划与控制系统,它根据总生产进度计划中规定的最终产品的交货日期,编制所构成最终产品的装配件、部件、零件的生产进度计划、对外的采购计划、对内的生产计划。
第6章 物料需求计划(MRP)
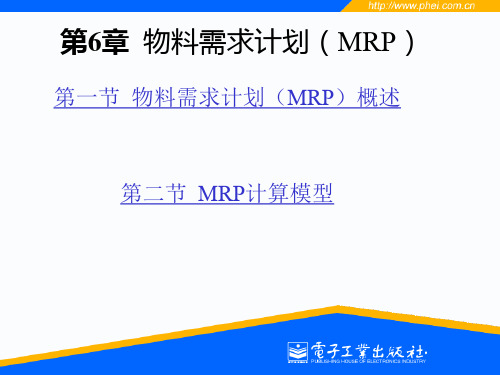
二、MRP计算步骤
• 2.物料需求计划计算具体步骤 • (1)计算物料毛需求量。考虑相关需求和低位码推算计划期全
部的毛需求。 • 项目毛需求量=项目独立需求+父项的相关需求 • 其中: • 父项的相关需求=父项的计划订单数量×项目用量因子 • (2)推算PAB初值。考虑毛需求推算特定时段的预计库存量。 • PAB初值=上期末预计可用库存量+计划接收量-毛需求量 • (3)计算净需求量。考虑安全库存推算特定时段的净需求量。 • 当PAB初值≥安全库存时,净需求=0 • 当PAB初值<安全库存时,净需求=安全库存-PAB初值
一、MRP概念及作用
• 2.MRP的基本依据 • MRP的基本依据是:① 主生产计划(
MPS);② 物料清单(BOM);③ 库存 信息。它们的逻辑流程关系如图6.1所示 。
一、MRP概念及作用
一、MRP概念及作用
• 3.MRP作用 • ① 要生产(含采购和制造)什么?生产(含采购和制造)多
少?(来自MPS) • ② 要用到什么?(根据BOM展开可知) • ③ 已经有了什么?(根据物料库存信息、即将到货的信息或
六、虚拟件
• 3.BOM中的虚拟件
• “虚拟件”最重要的作用就是简化产品结构的管理,以下用 图6.5的BOM进行说明。
• 在图6.5中,如果对A产品BOM的定义采用图6.5(a)方式, 那么,子件B、C的BOM文件定义过程会重复引用到D、E与F 物料,加大了工作量,并且数据库的存储空间也会增加。而 采用图6.5(b)的定义方式,增加一个“虚拟件”物料K,并 定义K的BOM文件,则B、C的BOM中只需要加入一个子件K ,无须重复加入子件D、E与F物料,从而达到简化BOM的目 的,特别是在多个BOM中有大量的相同子件重复出现时,这 种定义方式的优越性就更加明显。另外,如果虚拟件的子件 发生工程改变,也只影响到虚拟件这一层,不会影响此虚拟 件以上的所有父项。
物料系统方案

一、物料系统方案简介物料系统是指企业为了管理和掌控物料资源而采取的一种管理方案。
通过物料系统,企业可以对物料的采购、库存、使用等过程进行规划、监控和优化,从而提高物料的效率和管理水平。
本文将分析物料系统的功能和特点,并提出一种适用于企业的物料系统方案。
二、物料系统的功能1. 采购管理:物料系统可以帮助企业建立物料供应商数据库,将物料需求与供应商的能力进行匹配,提供采购计划和订单管理功能,实现物料的及时供应。
2. 库存管理:物料系统可以实时监控物料的库存情况,包括数量、批次、质量等信息,以及库存周转率、安全库存等指标。
通过物料系统,企业可以合理安排物料的储存和调配,避免库存积压和缺货的情况发生。
3. 物料需求计划:基于销售计划和生产计划,物料系统可以帮助企业制定物料的需求计划,提前准备所需物料,避免出现生产中断和物料浪费的情况。
4. 物料质量管理:物料系统可以建立物料质量数据库,记录物料的质量检验结果,监控物料的质量问题,并与供应商进行质量管理沟通和改进。
5. 成本控制:物料系统可以对物料的采购、使用和库存情况进行成本的统计和分析,帮助企业识别和控制物料成本的风险点,优化物料采购和使用策略,实现成本的降低。
三、物料系统的特点1. 高度集成:物料系统需要与企业的其他管理系统(如ERP系统、财务系统等)进行有效的集成,实现数据共享和信息流畅,避免重复录入和数据不一致的问题。
2. 灵活性和可扩展性:物料系统需要根据企业的不同需求进行配置和定制,以适应不同行业和企业规模的特点。
同时,物料系统也需要具备可扩展性,能够满足企业发展的需求。
3. 数据安全和隐私保护:物料系统涉及到企业的重要数据和信息,需要具备良好的数据安全性和隐私保护机制,以防止数据泄露和滥用的风险。
四、物料系统方案设计1. 系统架构设计:根据企业的需求和规模,设计物料系统的整体架构,包括前端界面、后端数据库、中间件技术等。
同时,还需要考虑系统的可靠性、可用性和性能等方面的要求。
SAP的物料需求计划

SAP的物料需求计划由于具有准确的和最新的库存数据以及最新的订单数据,物料管理系统是用户编制物料需求计划的基础。
净改变计划物料需求计划的主要功能是监控库存,特别是可以自动地为采购部门生成采购订单建议,这可由不同的需求计划方法实现。
通常情况下,每日结束前用净改变方法编制物料需求计划,即只为库存和需求发生改变的物料编制计划。
较短的运行时间使物料需求计划编制人员以较短的间隔重复净改变计划过程,甚至可以通过预先定义一个计划展望期来缩短运行时间,这意味着物料需求计划总可以得到当前的结果,系统可自动生成有关重要零件和异常情况的信息,即可将物料需求计划人员从日常监控过程中解脱出来。
处理过程在计划运行过程中,系统执行如下:□净需求计算□批量计算□排序□生成采购订单建议□生成异常信息物料需求计划控制人员可通过交互式方法对系统自动生成的物料需求计划进行调整,并可以在线的对某种物料重新单独编制计划。
工厂级计划通常在工厂级执行物料需求计划,系统编制计划时考虑所有库存可用量。
存储地点物料需求计划用户在工厂级编制物料需求计划时,不必单独考虑各个存储地点的库存,可在存储地点级分别编制库存计划,已在个存储地点计划的库存不包含在工厂级的计划中。
基于消耗的计划基于消耗的计划是简单易于使用的的计划过程,用于编制公司中非生产零件的计划,也可用于编制生产工厂中的B类和C类部件或生产工具的计划物料需求计划物料管理系统中"不作物料清单展开的物料需求计划"具有特定的功能,与基于消耗的物料需求计划相对应,这项功能基于已有的销售订单和物料保留量。
用户可为每个工厂的每个零件定义物料需求计划过程,物料也可被定义为不参加自动需求计划生成过程。
采购订单建议系统在按物料的采购类型编制计划对自动生成采购订单建议类型,对于自制的物料,自动生成生产订单;对于外购的物料,可按MRP编制人员选择的条件生成计划订单、采购申请或交货计划。
物料需求计划的基本核心功能是什么?物料需求计划通过净改变计划过程确定物料需求数量,并生成可进一步处理的采购订单建议。