控轧控冷的应用
30MnSi生产工艺中控轧控冷技术应用

浅谈30MnSi生产工艺中控轧控冷技术的应用摘要:本文介绍了唐银高速线材使用先进的控轧控冷技术,通过合理控制钢的化学成分、加热温度、轧制温度、变形量、变形速度及冷却速度进行生产30mnsi的生产,2010开始生产并取得了良好的效果,赢得了用户的好评。
关键词:控轧控冷 30mnsi 冷却速度工艺流程轧制温度1、前言:30mnsi盘条钢属于预应力钢棒,又称预应力混凝土用钢棒、pc 钢棒等,由于具有高强韧性、低松弛性、与混泥土握裹力强、良好的可焊性、镦锻性、节省材料等特点,随着现代工业和建筑业的发展,已被广泛应用于高强度预应力混凝土离心管桩、电杆、高架桥墩、铁路轨枕等预应力构件中。
市场对建筑基础用pc钢棒的需求量愈来愈大,高强度预应力钢棒用盘条的使用量逐年增加,各大中小型钢铁企业也加大了生产研发的力度[1]。
2、30mnsi盘条的应用前景近几年来,随着我国沿海经济的飞速发展,建筑业发展速猛。
据相关资料2004年全国pc钢棒实际销售量达100多万吨,该钢种具有广阔的市场前景。
由于30mnsi盘条对质量要求比较严格,尤其是对化学成分、钢的纯净度、盘条的表面质量及尺寸[2]。
唐银公司生产的30mnsi盘条规格主要有¢8、¢10、¢12,并严格制定了企业标准。
30mnsi盘条的成功研发,使唐银公司的产品竞争力有了进一步的提高,标着唐银钢厂由生产普钢型向优特钢型转变的目标迈进了一步!3、30mnsi盘条的化学成分:唐银钢铁有限公司高线车间生产的30mnsi热轧盘条产品尺寸精度执行gb/t14981-2009标准,尺寸精度执行c级标准;30mnsi盘条设计的化学成分、力学性能分别与用户签订了相应的技术协议。
4、唐银公司高速线材生产工艺流程及分析唐银公司高速线材生产线是2008年2月投产的国产全连续式高速无扭线材轧钢生产线,全线28架轧机,目前使用最快轧速高达85 m / s。
生产工艺主要设备包括汽化冷却步进梁式加热炉、高压水除鳞、平立交替粗中轧机组、悬臂辊环式预精轧机组、顶交 45°摩根五代重型无扭精轧机组、控制冷却水冷段、测径仪、夹送辊、吐丝机、斯太尔摩风冷辊道、集卷站、p / f钩式运输机等。
控轧控冷的应用

3.合金元素的作用 在HRB400盘条生产中,钒、钒-氮、铌、钛 微合金化成分在20Mnsi基础上分别增加 0.04%-0.12%V、 0.02%-0.04%Nb , 0.02%-0.05%Ti,强化机制主要为析出强化 和细晶强化
HRB400盘条的组织是铁素体+珠光体.钒、铌微合金元素 在控轧控冷中的作用主要有:(1)加热时抑制 奥氏体晶粒长 大;(2)变形时抑制奥氏体再结晶;(3)相变时使铁素体晶粒 细化;(4)相间或铁素体基体析出强化。 钒的溶解度较大,热变形时一般处于固溶状态,对再结晶 过程抑制较小,它的主要作用是奥氏体向铁素体转变时相间 或铁素体基体析出强化.细晶强化作用较小.但是氮的加 入.在奥氏体中VN的溶解度与NbC相当,变形时诱导析出 的VN能抑制奥氏体再结晶和阻止晶粒长大。 铌的最突出的作用是抑制高温变形的再结晶,扩大了再结 晶温度范围,微量的铌能起到显著的细晶强化效果和中等的 析出强化效果。在非再结晶区累计变形能诱导相变获得超细 铁素体晶粒
合金元素在钢中的作用
A 加热阻止奥氏体长大 随着加热温度的提高及保温时间的延长,奥氏体晶粒变得 粗大。微合金元素形成高度弥散的碳氮化合物小颗粒.可以 对奥氏体晶界起固定作用.从而阻止奥氏体晶粒长大.即提 高了钢的粗化温度 当Nb、Ti含量在0.10%时, 可以提高奥氏体粗化温度 到1050~1100℃,V在小 于0.10% 时,阻止晶粒长 大的作用不大.在950 ℃ 左右奥氏体晶粒就开始粗 化。
1.4 控轧控冷的应用
主讲:王庆娟
控制轧制的优点如下:
(1)可以在提高钢材强度的同时提高钢材的低温韧性。 (2)可以充分发挥铌、钒、钛等微量元素的作用。
控制轧制工艺的缺点:
(1)要求较低的轧制变形温度和一定的道次压下率,因 此增大了轧制负荷。 (2)由于要求较低的终轧温度,大规格产品需要在轧制 道次之间待温,降低轧机生产率。
棒材轧制中控制轧制和控制冷却的应用

棒材轧制中控制轧制和控制冷却的应用姓名:迟璐全班级:学号:棒材轧制中控制轧制和控制冷却的应用迟璐全材料成型及控制工程12级[摘要]控制轧制(Contorlled Rollign)是在热轧过程中通过对金属加热制度、变形制度和温度制度的合理控制,使热朔性变形与固态相变结合,以获得细小晶粒组织,使钢材具有优异的综合力学性能的轧制新工艺。
控制冷却(controlled Cooling)是控制轧后钢材的冷却速度达到改善钢材组织和性能的目的。
控制轧制和控制冷却相结合能将热轧钢材的两种强化效果相加,进一步提高钢材的强韧性和获得合理的综合力学性能。
并介绍了棒材轧制过程中控制轧制和控制冷却工艺的特点,金属学理论。
分析了控制轧制和控制冷却工艺对热轧棒材的影响,并提出目前需要研究的问题。
[关键词]热轧棒材控制轧制控制冷却ABSTRACT:Controlled rolling is in the process of hot rolled through the metal heating system, reasonable control of the deformation and temperature, and to integrate the thermal plastic deformation and solid-state phase transformation to obtain fine grain structure, make the excellent comprehensive mechanical properties of steel rolling process. Is controlled cooling after controlled rolling steel cooling speed to achieve the purpose of improving the microstructure and mechanical properties of steel. Controlled rolling and controlled cooling could add those two kinds of reinforcement effect of hot rolling steel, further improve the tenacity of steel and have a reasonable comprehensive,mechanical,properties.Anintroductionwasmadetothefeaturesandmetallo graphicaltheoryofrollingcontrolandcoolingcontrolprocessesduringbarrolling.Theeffects oftherollingcontrolandcoolingcontrolprocessesonthehotrolledbarswereanalyzed.Proble mstoberesearchedatpresentwerealsoputforward.KEY WORDS: hotrolledbars rollingcontrol coolingcontrol1.引言控制轧制和控制冷却技术是近十多年来国内外新发展起来的轧钢生产新技术,受到国际冶金界的重视。
控轧控冷技术应用

控轧控冷技术在螺纹钢生产中的应用摘要:采用控轧控冷的方法用20Mnsi生产400 MPa级的Ⅲ级钢筋,可以降低成本。
用热模拟试验机测定了20MnSi钢的动态CCT曲线,确定了开发20MnSiⅢ级钢筋的生产试验方案,所生产的螺纹钢筋的性能指标达到了Ⅲ级钢筋的标准要求。
关键词:20MnSi;螺纹钢筋;控轧控冷;钢筋是重要的建筑用钢材,其应用非常广泛,用量也很大。
随着建筑行业的迅猛发展,对热轧螺纹钢筋的性能要求越来越高。
工业发达国家,如德国、美国等国家的建筑用钢已淘汰了低强度的Ⅱ级钢筋这一等级,并以400 MPa级的Ⅲ级钢筋来替代。
Ⅲ级钢筋具有强度高,综合性能好的优点,采用Ⅲ级以上钢筋代替Ⅱ级钢筋可节约钢材约10%~15%,而我国建筑用钢筋的80%为20MnSiⅡ级钢筋,为此我国正在大力推广应用400 MPa级的Ⅲ级钢筋,研制和开发高强度钢筋已是势在必行。
400 MPa级的Ⅲ级钢筋的生产工艺目前主要有两种,一是在20MnSi中加入微量合金元素钒(或铌、钛),二是采用控轧控冷的方法,而前者的成本较高。
钢筋的控轧控冷是通过控制钢材在轧制过程中的温度变化和轧后冷却过程的工艺参数,以得到细小均匀的相变组织,从而获得强度、塑性、韧性均好的优良产品。
采用控轧控冷方法可节约合金元素,降低成本;同时可简化工序,降低能耗,具有显著的经济效益和社会效益。
笔者采用控轧控冷的方法进行了Ⅲ级钢筋的试验开发工作。
1试验材料及方法为了准确地确定合理的控轧控冷工艺参数,在Gleeble-2000热模拟机上测定了动态CCT曲线。
试验用钢20MnSi的化学成分(质量分数,%)为:0.21 C,1.44 Mn,0.47 Si,0.028 S,0.023 P。
CCT曲线的测定:采用 10 mm×12 mm的圆棒试样,在Gleeble-2000热模拟试验机上将试样加热到1 150℃,保温5 min后以10℃·s-1的冷却速度分别冷却到900℃和1 050℃,保温20 s后分别进行50%的单道次变形,然后分别以1、2、10、15、50℃·s-1的冷却速度冷却到室温,测得热膨胀曲线,结合金相法绘制出两个变形温度下的动态CCT曲线。
控轧控冷工艺的发展及应用

控轧控冷工艺的发展及应用摘要控轧控冷工艺是把钢坯加热到适宜的温度,轧制时控制变形量和变形温度及轧后按工艺要求来冷却钢材。
控轧主要用于轧制细晶粒结构钢,主要原理是在终轧后当钢板在轧机上运行至“再结晶”完成的温度时,选用合适水冷方式获得理想延展性和韧性。
关键词变形量变形温度再结晶1 前言1.1 控轧控冷就是控制轧制和控制冷却,也叫TMCP(热机械变形轧制)+ACC。
比较适合于低碳微合金钢,特别是Nb、V 、Ti复合的。
1.2 控制轧制:是在调整钢的化学成分的基础上,通过控制加热温度、开轧温度,轧制过程温度、变形制度等工艺参数,控制奥氏体状态和相变产物的组织状态,从而达到控制钢材组织性能的目的.1.3 控制冷却:是通过控制热轧钢材轧后的冷却条件来控制奥氏体组织状态、控制相变条件、控制碳化物析出行为、控制相变后钢的组织和性能。
1.4 TMCP:控制轧制和控制冷却技术结合起来,能够进一步提高钢材的强韧性和获得合理的综合性能,并能够降低合金元素含量和碳含量,降低生产成本。
通过控轧控冷生产工艺可以使钢板的抗拉强度和屈服强度平均提高约40~60MPa,在低温韧性、焊接性能、节能、降低碳当量、节省合金元素以及冷却均匀性、保持良好板形方面都有无可比拟的优越性。
2 发展历程2.1 控轧控冷工艺主要是用于生产板材的技术。
该技术的核心是在轧制过程中通过控制加热温度、轧制过程、冷却条件等工艺参数,改善钢材的强度、韧性、焊接性能。
2.2 控制轧制工艺主要用于含有微量元素的低碳钢种,钢中常含有铌、钒、钛,其总量一般小于0.1%。
依据《塑性变形和轧制原理》控制轧制的内容是控制轧制参数,包括温度、变形量等,以控制再结晶过程,获得所要求的组织和性能。
根据塑性变形、再结晶和相变条件,控制轧制可分为三阶段,如下所述。
(1)在奥氏体再结晶区控制轧制:适用于轧制低碳优质钢普通碳素钢低合金高强度钢。
(2)在奥氏体未再结晶区控制轧制:适用于轧制含有微量合金元素的低碳钢,如含铌钛钒得低碳钢。
控制轧制和控制冷却技术的应用课件

(7)半无头轧制 半无头轧制工艺:将几块中间坯焊接在一起,然 后通过精轧机进行连续轧制。在进入卷取机之 前,用一台高速飞剪将其分切到要求的卷重。
作用: 1)有利于生产超薄带钢和宽而薄的带钢,拓宽产 品大纲; 2)稳轧制条件以利于产品质量; 3)消除了与穿带和甩尾的麻烦; 4)显著提高了轧机的作业率和金属收得率。
(4)步进式加热炉布置的薄板坯连铸连轧生产 线
缓冲时间的大小取决于步进炉内钢坯的存放量, 一般设计上可以考虑缓冲时间取1.5-2.0h。
(5)单流单机座炉卷轧机(TSP)
适合多品种、低投资为目的的配置方式。采用单 机座炉卷轧机,铸坯厚度为50-70mm,最小产品厚 度1.5mm,设计年产量为50万t。最大缺点:带钢 表面粗糙度不好 。
10 控制轧制和控制冷却技术的应 用
10.1 控制轧制和控制冷却技术在钢板生产 中的应用 10.1.1 热轧带钢的控制轧制和控制冷却 5个步骤: 1) 加热中,微合金化元素碳氮化合物的溶 2) 解。 2)再结晶临界温度以下施以大的变形。
3) 微合金化元素碳氮化合物的变形诱导析 出延缓再结晶。 4)未再结晶并强烈变形的奥氏体发生相变。 5)分配冷却剂量来控制冷却和调整所 需要的卷取温度。
10.1.4.5 薄板坯连铸连轧生产线的配置 典型的薄板坯连铸连轧生产线工艺流程: 钢水中间包结晶器二冷区飞剪机 均热炉高压水除鳞(立辊轧边机) (粗轧机组)保温炉高压水除鳞 精轧机组近距离卷取机层流冷却远 距离卷取机打包入库。
(1)只有精轧机的薄板坯连铸连轧生产线
两条生产线的区别: 这种配置线铸坯厚度约为50-70mm,设计年产量多 在150万t,产品最小厚度1.0mm。
控制轧制及控制冷却技术在型钢生产中的应用

控制轧制及控制冷却技术在型钢生产中的应用一、引言型钢是一种重要的金属材料,在建筑、汽车制造、机械制造等领域具有广泛的应用。
为了提高型钢的质量和性能,控制轧制及控制冷却技术被广泛应用于型钢生产中。
这些技术通过精确控制轧制工艺参数和冷却过程,可以有效提高型钢的强度、塑性和表面质量,满足不同领域对型钢材料性能的需求。
二、控制轧制技术的应用1. 调整轧制温度和速度在型钢轧制中,通过调整轧制温度和轧制速度,可以控制晶粒的细化和晶格的取向,从而提高型钢的强度和塑性。
尤其是在热轧过程中,通过精确控制轧制温度和速度,可以有效控制晶粒生长,减少析出相的尺寸,使得型钢的晶粒细化,提高强度和硬度。
2. 控制轧制力和变形量通过精确控制轧制力和变形量,可以有效调整型钢的组织结构和力学性能。
在轧制过程中,通过监测轧辊力和变形量,可以实现对型钢的细微调整,达到提高型钢性能的目的。
在轧制高强度型钢时,通过增加轧制力和变形量,可以有效提高型钢的强度和硬度。
3. 控制轧制辊形状通过选择合适的轧辊形状,可以实现更加精确的型钢轧制。
不同形状的轧辊对型钢的变形和组织结构有着不同的影响,因此通过调整轧辊的形状,可以实现对型钢结构和性能的精细控制。
三、控制冷却技术的应用1. 控制冷却速度在型钢生产中,通过控制冷却速度,可以实现对型钢组织和性能的调整。
在快速冷却条件下,型钢的组织结构更加均匀,晶粒更加细小,从而提高了型钢的强度和韧性。
在慢速冷却条件下,型钢的组织结构更加致密,表面质量更好,适用于高表面质量要求的场合。
2. 控制冷却介质不同的冷却介质对型钢的冷却效果和组织结构有着不同的影响。
通过选择合适的冷却介质,可以实现对型钢组织和性能的精细调控。
对于高强度型钢,可以采用高效的水冷或气体冷却,快速降温,实现对型钢强度和硬度的提高。
3. 控制冷却方式在型钢生产中,采用不同的冷却方式,可以实现对型钢的细微调整。
采用直接水冷或间接水冷,可以分别实现快速和慢速的冷却效果,从而满足不同型钢的冷却需求。
钢材控轧控冷工艺的技术研究及应用
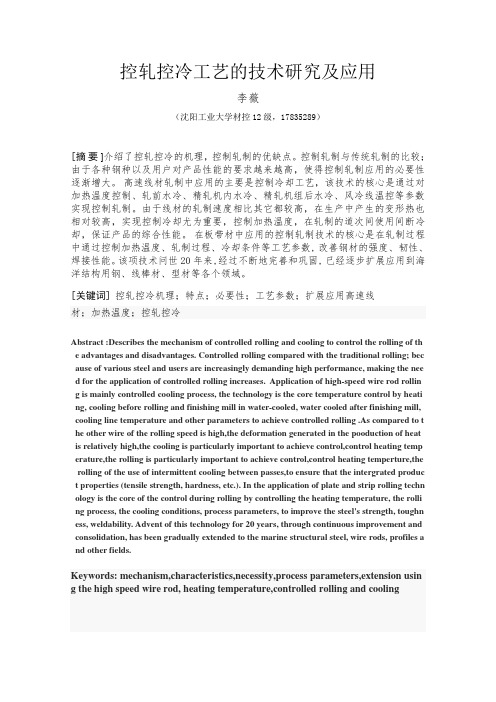
控轧控冷工艺的技术研究及应用李薇(沈阳工业大学材控12级,17835289)[摘要 ]介绍了控轧控冷的机理,控制轧制的优缺点。
控制轧制与传统轧制的比较;由于各种钢种以及用户对产品性能的要求越来越高,使得控制轧制应用的必要性逐渐增大。
高速线材轧制中应用的主要是控制冷却工艺,该技术的核心是通过对加热温度控制、轧前水冷、精轧机内水冷、精轧机组后水冷、风冷线温控等参数实现控制轧制。
由于线材的轧制速度相比其它都较高,在生产中产生的变形热也相对较高,实现控制冷却尤为重要,控制加热温度,在轧制的道次间使用间断冷却,保证产品的综合性能。
在板带材中应用的控制轧制技术的核心是在轧制过程中通过控制加热温度、轧制过程、冷却条件等工艺参数,改善钢材的强度、韧性、焊接性能。
该项技术问世20年来,经过不断地完善和巩固,已经逐步扩展应用到海洋结构用钢、线棒材、型材等各个领域。
[关键词]控轧控冷机理;特点;必要性;工艺参数;扩展应用高速线材;加热温度;控轧控冷Abstract :Describes the mechanism of controlled rolling and cooling to control the rolling of th e advantages and disadvantages. Controlled rolling compared with the traditional rolling; bec ause of various steel and users are increasingly demanding high performance, making the nee d for the application of controlled rolling increases. Application of high-speed wire rod rollin g is mainly controlled cooling process, the technology is the core temperature control by heati ng, cooling before rolling and finishing mill in water-cooled, water cooled after finishing mill, cooling line temperature and other parameters to achieve controlled rolling .As compared to t he other wire of the rolling speed is high,the deformation generated in the pooduction of heat is relatively high,the cooling is particularly important to achieve control,control heating temp erature,the rolling is particularly important to achieve control,control heating temperture,the rolling of the use of intermittent cooling between passes,to ensure that the intergrated produc t properties (tensile strength, hardness, etc.). In the application of plate and strip rolling techn ology is the core of the control during rolling by controlling the heating temperature, the rolli ng process, the cooling conditions, process parameters, to improve the steel's strength, toughn ess, weldability. Advent of this technology for 20 years, through continuous improvement and consolidation, has been gradually extended to the marine structural steel, wire rods, profiles a nd other fields.Keywords: mechanism,characteristics,necessity,process parameters,extension usin g the high speed wire rod, heating temperature,controlled rolling and cooling1引言控制轧制(C-R)和控制冷却(C-C)技术的研究始于1890年二次世界大战的德国,当时科研人员对钢铁产品的加热工条件、材质及显微金相组织之间的关系进行了非系统的零散研究。
控轧控冷工艺基本原理
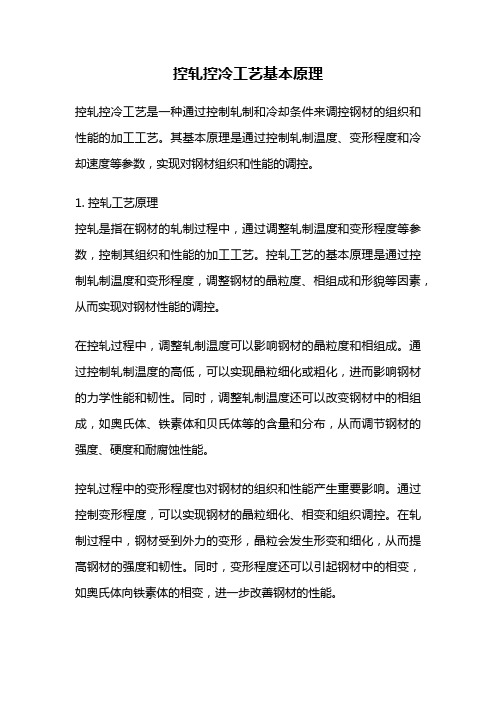
控轧控冷工艺基本原理控轧控冷工艺是一种通过控制轧制和冷却条件来调控钢材的组织和性能的加工工艺。
其基本原理是通过控制轧制温度、变形程度和冷却速度等参数,实现对钢材组织和性能的调控。
1. 控轧工艺原理控轧是指在钢材的轧制过程中,通过调整轧制温度和变形程度等参数,控制其组织和性能的加工工艺。
控轧工艺的基本原理是通过控制轧制温度和变形程度,调整钢材的晶粒度、相组成和形貌等因素,从而实现对钢材性能的调控。
在控轧过程中,调整轧制温度可以影响钢材的晶粒度和相组成。
通过控制轧制温度的高低,可以实现晶粒细化或粗化,进而影响钢材的力学性能和韧性。
同时,调整轧制温度还可以改变钢材中的相组成,如奥氏体、铁素体和贝氏体等的含量和分布,从而调节钢材的强度、硬度和耐腐蚀性能。
控轧过程中的变形程度也对钢材的组织和性能产生重要影响。
通过控制变形程度,可以实现钢材的晶粒细化、相变和组织调控。
在轧制过程中,钢材受到外力的变形,晶粒会发生形变和细化,从而提高钢材的强度和韧性。
同时,变形程度还可以引起钢材中的相变,如奥氏体向铁素体的相变,进一步改善钢材的性能。
2. 控冷工艺原理控冷是指在钢材的冷却过程中,通过调整冷却速度和冷却方式等参数,控制其组织和性能的加工工艺。
控冷工艺的基本原理是通过控制冷却速度,调整钢材的组织和性能。
在控冷过程中,调整冷却速度可以影响钢材的相组成和组织形貌。
通过控制冷却速度的快慢,可以实现钢材中相的相变和组织的调控。
当冷却速度较快时,钢材中的相变会受到限制,从而形成细小的相和均匀的组织。
相反,当冷却速度较慢时,钢材中的相变会较为充分,形成较大的相和不均匀的组织。
不同的冷却速度会影响钢材的强度、硬度和韧性等性能。
控冷过程中的冷却方式也会对钢材的组织和性能产生影响。
不同的冷却方式,如空冷、水冷、油冷等,具有不同的冷却速度和冷却效果。
通过选择合适的冷却方式,可以实现钢材组织的定向调控,从而达到钢材性能的要求。
3. 控轧控冷工艺的应用控轧控冷工艺广泛应用于钢材的生产和加工过程中。
控轧控冷技术在轴承钢生产中的应用

控轧控冷技术在轴承钢生产中的应用关键词:控制轧制控制冷却轴承钢细化晶粒一引言随着现代科学技术的发展,滚动轴承的使用量日益增加。
轴承的主要损坏形式是接触疲劳破坏,因此要求轴承钢具有高的接触疲劳强度,同时具有高的耐磨性和良好的工艺性能。
GCr15 具有良好的综合性能,因而成为轴承行业中应用最为广泛的钢种之一。
控轧控冷是在轧制过程中通过控制加热温度、轧制过程、冷却条件等工艺参数,改善钢材的强度、韧性、焊接性能。
该项技术问世20年来,经过不断地完善和巩固,已经逐步扩展到海洋结构用钢、管线、型材等各个领域。
将控轧控冷技术应用于轴承钢能使得钢材的综合性能得到大幅提高,取得巨大的经济效益。
二控制轧制控制轧制(Controlled rolling):热轧过程中通过对金属加热制度、变形制度和温度制度的合理控制,使热塑性变形与固态相变结合,获得细小晶粒组织,使钢材具有优异的综合力学性能的轧制新工艺。
1 控制轧制的类型控制轧制方式示意图(a) 奥氏体再结晶区控轧;(b) 奥氏体未再结晶区控轧;(c) (γ+α)两相区控轧(1)奥氏体再结晶区控制轧制(又称I型控制轧制)奥氏体再结晶区控制轧制的主要目的是通过对加热时粗化的初始奥氏体晶粒反复进行轧制再结晶使之细化,并从而使奥氏体到铁素体相变后得到细小的铁素体晶粒。
并且,相变前的奥氏体晶粒越细,相变后的铁素体晶粒也变的越细。
把钢相变前的奥氏体晶粒直径和相变后的奥氏体晶粒直径之比成为γ/α变换比。
当奥氏体晶粒粗大时此比值远远大于1,即由一个奥氏体晶粒可以产生几个铁素体晶粒。
当相变前的奥氏体晶粒细小时,该γ/α变换比接近于1,所以,在仅仅由于再结晶奥氏体晶粒微细化而引起的奥氏体的晶粒细化方面存在一个极限。
奥氏体再结晶区轧制是通过再结晶使奥氏体晶粒细化,从这种意义上说,它实际上是控制轧制的准备阶段。
奥氏体再结晶区域通常是在约950℃以上的温度范围。
(2)奥氏体未再结晶区控制轧制(又称Ⅱ型控制轧制)在奥氏体未再结晶区进行控制轧制时,γ晶粒沿轧制方向伸长,γ晶粒内部产生形变带。
控轧控冷技术在品种钢生产中的应用

控轧控冷技术在品种钢生产中的应用张洪涛吴影亮白玉红(唐山建龙实业有限公司热轧二厂)【摘要】主要介绍温度控制在生产过程中对组织性能的影响,目前生产过程中存在的问题及解决办法【关键词】控制轧制控制冷却终轧温度卷取温度1.前言中宽带厂从筹建到现在生产已有3年多的历史,随着工艺、设备的完善及激烈的市场竞争的影响,我们经历了一条曲折、艰难的前进道路。
目前在公司各级领导的支持下,我厂成功开发了SPA-H、08AL、510L、345B等品种钢,为企业带来了无限生机。
从品种钢开发工作中我们回过头来进行总结,如何进一步提高品种钢产品质量、优化性能应是目前的关键,从我们轧钢厂来讲今后如何利用控轧控冷技术来提高品种钢质量应列入工作日程中。
2.控制轧制与控制冷却的定义2.1控制轧制的定义:控制轧制从理论上讲是适当地控制钢的化学成分、加热温度、变形温度、变形条件(包括每个道次的变形量、总变形量、变形速度)及冷却速度等工艺参数,从而大幅度提高钢材综合性能,控制轧制的主要优点是改善钢材的组织,提高钢材的综合力学性能。
2.2控制冷却的定义:控制冷却是指控制轧制之后,对奥氏体向铁素体相变温度区间进行某种程度的快速冷却,使相变组织细化,甚至相变成新的组织,以获得更高的强度和更优良的韧性。
从我厂现有设备和生产过程看,控制轧制与控制冷却主要讲的是指生产过程中的温度控制。
3.温度控制对组织性能的影响温度是热连轧生产过程中的几个重要的工艺参数之一,由于温度将直接影响到热轧轧制力,特别是精轧机组各机架的轧制温度是保证厚度、板形及宽度的关键,带钢全长上的温度分布的均匀性将直接影响产品的厚度、板形和宽度的均匀性。
依据钢的内部组织对不同的钢种、不同的性能要求,有不同的轧制温度范围,最重要的是保证终轧温度和卷取温度。
3.1终轧温度对带钢质量有直接影响终轧温度的高低,在很大程度上决定了轧后钢材的内部金相组织和力学性能。
为了得到细小而均匀的铁素体晶粒,终轧温度应略高于Ar3相变点,此时钢的晶粒为单相奥氏体晶粒,组织均匀,轧后带钢有良好的力学性能。
控轧控冷技术在钢材生产中的应用
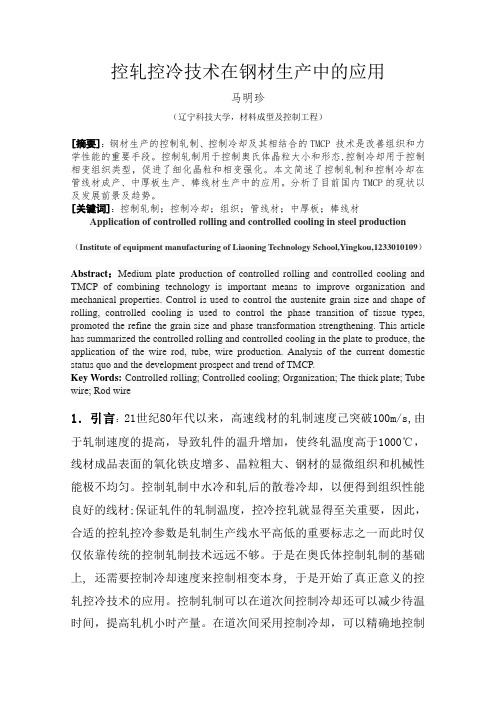
控轧控冷技术在钢材生产中的应用马明珍(辽宁科技大学,材料成型及控制工程)[摘要]:钢材生产的控制轧制、控制冷却及其相结合的TMCP 技术是改善组织和力学性能的重要手段。
控制轧制用于控制奥氏体晶粒大小和形态,控制冷却用于控制相变组织类型,促进了细化晶粒和相变强化。
本文简述了控制轧制和控制冷却在管线材成产、中厚板生产、棒线材生产中的应用。
分析了目前国内TMCP的现状以及发展前景及趋势。
[关键词]:控制轧制;控制冷却;组织;管线材;中厚板;棒线材Application of controlled rolling and controlled cooling in steel production(Institute of equipment manufacturing of Liaoning Technology School,Yingkou,1233010109)Abstract:Medium plate production of controlled rolling and controlled cooling and TMCP of combining technology is important means to improve organization and mechanical properties. Control is used to control the austenite grain size and shape of rolling, controlled cooling is used to control the phase transition of tissue types, promoted the refine the grain size and phase transformation strengthening. This article has summarized the controlled rolling and controlled cooling in the plate to produce, the application of the wire rod, tube, wire production. Analysis of the current domestic status quo and the development prospect and trend of TMCP.Key Words:Controlled rolling; Controlled cooling; Organization; The thick plate; Tube wire; Rod wire1.引言:21世纪80年代以来,高速线材的轧制速度己突破100m/s,由于轧制速度的提高,导致轧件的温升增加,使终轧温度高于1000℃,线材成品表面的氧化铁皮增多、晶粒粗大、钢材的显微组织和机械性能极不均匀。
控制轧制于控制冷却

1、控制轧制:在热轧过程中,通过对金属加热制度、变形制度和温度制度的合理控制,使热塑性形变与固态相变相结合,以获得细小的晶粒组织,使钢材具有优异的综合力学性能的轧制技术2、控制冷却:通过对控制轧后的钢材的冷却速度来改善钢材的组织性能.3、金属的强化:通过合金化,塑性变形和热处理等手段来提高金属的强度。
4、固溶强化:添加溶质元素使固溶体强度提高的方法.5、韧性:材料在塑性变形和断裂所吸收能量的能力。
6、微合金钢:钢种的合金含量小于0.1%。
7、IF钢:无间隙原子钢8、不锈钢:具有良好的抗腐蚀性能和抗氧化性的钢.9、变形抗力:在一定条件下材料变形单位面积的抵抗变形的力.10、在线常化工艺:在热轧无缝钢管中在轧管延伸工序后将钢管按常化热处理要求冷却到某一温度后在进加热炉然后就行减径轧制按照一定的速度冷却到常温。
11、变形温度贝氏体处理化工艺:在钢管轧制过程中不直接加热到马氏体温度一下,而是快速冷却带中温以后再置于静止的空气中冷却、以变形奥氏体转变为贝氏体省去回火工序。
12、高温变形淬火:钢管在稳定的奥氏体区域变形,而且一般温度在再结晶温度以上然后进行淬火,已获得马氏体组织。
13、低温相变淬火:将钢管加热到奥氏体状态,经一段保温冷却到Ac1高于M的某一中间温度进行变形后淬火的工艺。
14、非调质钢:将调质钢的化学成分进行调解并对轧制过程进行控制不进行调制其性能达到调制的水平。
1、控制轧制是指在热轧过程中通过对金属加热制度,温度制度,保险制度的控制而获得细小的晶粒2、控制冷却是控制轧后钢材的冷却速度来改善组织性能。
3、钢材的强化方法有固溶强化,变形强化,沉淀强化,弥散强化,亚晶强化,细晶强化,相变强化。
4、影响材料韧性有,化学成分,气体和夹杂物,晶粒细化,形变的影响,形变细化5、动态结晶是晶粒细化提高扩孔性的手段6、控制轧制的目标是为了获得较小的铁素体组织7、加快冷却速度可以获得细小的铁素体晶粒所以不产生奥氏体组织为界限8、贝氏体是结构性能钢有校坏的塑形焊接性能强韧性微合金钢是指钢中的合金元素总量小于0。
自动控轧控冷系统在棒材生产线的应用

自动控轧控冷系统在棒材生产线的应用杨宇桥张永(山东石横特钢有限公司,山东肥城271612)应用科技蹄5要]随着国家淘汰落后产能步伐的加大,降低生产成本提高钢材}生能的控轧控冷技术应用前景将十分广阔。
自动控轧控冷技术在当前已得到快速发展,用这种方法生产的钢铁产品已经得到广泛应用。
法键词]控轧控冷;电气自动化;棒材控轧控冷和热处理技术是现代轧钢生产中节约能源、提高产品竞争能力的新技术和新工艺,也是将轧制工程学、塑性加工理论、金属材料学、传热学和流体力学等学科结合为一体的一门新学科,是金属压力加工专业的前沿技术。
控轧控冷广泛应用于各种带钢、中厚板、宽厚板的生产实践中,但目前国内大量的棒线材生产线在设计时定位较低,仅考虑普通的圆钢或螺纹钢生产,不具备控轧控冷工艺条件。
有不少棒线材生产线已经自主研发出控轧控冷的生产工艺,但是开始也往往缺少完善的检测和控制技术,造成钢材性能不稳定、可控性差、不合格品多等等现象,因此采用自动控轧控冷系统是棒材生产线的发展趋势。
1控轧控冷的工艺流程和技术原理控轧是指在热轧过程中通过对金属加热制度、变形制度和温度制度的合理控制,使塑性变形和固态相变相结合,以获得细小晶粒组织,使钢材具有优异的综合力学性能的轧制工艺。
控冷是指控制轧后钢材的冷却速度达到改善钢材组织和性能的热处理技术。
将控制轧制和控制冷却这两种强化手段相结合能够进一步提高钢材的强韧性,并获得良好的综合力学性能。
控轧控冷的主要工艺流程为:钢坯加热一粗、中轧轧制——精轧控制——{L后冷却。
11钢坯加热.在炉内加热使钢坯温度均匀性达标的,要尽量缩短高温停留时间,避免形成过于粗大奥氏体晶粒。
由于一些合金元素对奥氏体化临界温度起到很大作用,因此温度制度的确定必须与钢种相结合。
/J、型棒线材生产中一般要求钢坯出炉温度不低于950。
C。
12粗、中{L车L制一般粗中轧采用常规轧制工艺体晶粒反复轧制、再结晶使之细化,终组织晶粒细化做好;隹备。
中厚钢板新一代控轧控冷装备技术及应用
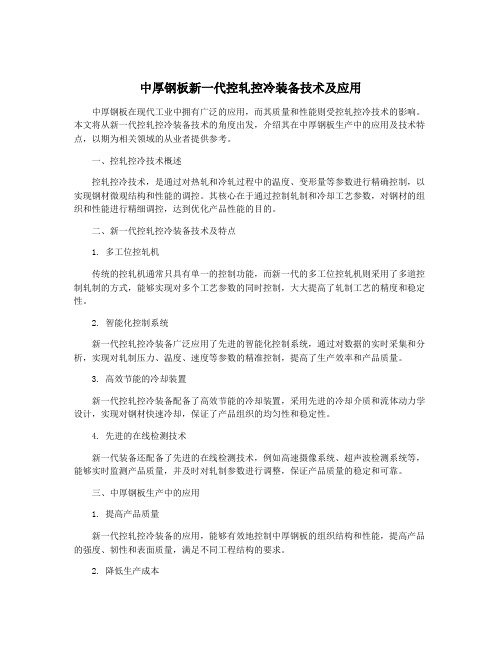
中厚钢板新一代控轧控冷装备技术及应用中厚钢板在现代工业中拥有广泛的应用,而其质量和性能则受控轧控冷技术的影响。
本文将从新一代控轧控冷装备技术的角度出发,介绍其在中厚钢板生产中的应用及技术特点,以期为相关领域的从业者提供参考。
一、控轧控冷技术概述控轧控冷技术,是通过对热轧和冷轧过程中的温度、变形量等参数进行精确控制,以实现钢材微观结构和性能的调控。
其核心在于通过控制轧制和冷却工艺参数,对钢材的组织和性能进行精细调控,达到优化产品性能的目的。
二、新一代控轧控冷装备技术及特点1. 多工位控轧机传统的控轧机通常只具有单一的控制功能,而新一代的多工位控轧机则采用了多道控制轧制的方式,能够实现对多个工艺参数的同时控制,大大提高了轧制工艺的精度和稳定性。
2. 智能化控制系统新一代控轧控冷装备广泛应用了先进的智能化控制系统,通过对数据的实时采集和分析,实现对轧制压力、温度、速度等参数的精准控制,提高了生产效率和产品质量。
3. 高效节能的冷却装置新一代控轧控冷装备配备了高效节能的冷却装置,采用先进的冷却介质和流体动力学设计,实现对钢材快速冷却,保证了产品组织的均匀性和稳定性。
4. 先进的在线检测技术新一代装备还配备了先进的在线检测技术,例如高速摄像系统、超声波检测系统等,能够实时监测产品质量,并及时对轧制参数进行调整,保证产品质量的稳定和可靠。
三、中厚钢板生产中的应用1. 提高产品质量新一代控轧控冷装备的应用,能够有效地控制中厚钢板的组织结构和性能,提高产品的强度、韧性和表面质量,满足不同工程结构的要求。
2. 降低生产成本新一代装备采用了高效节能的冷却装置和智能化控制系统,能够有效地降低生产能耗,减少原材料的浪费,提高生产效率,降低生产成本。
3. 提高生产效率新一代控轧控冷装备的精准控制和智能化调整功能,能够实现对生产过程的自动化控制,提高了生产效率和设备利用率,减少了人为因素对产品质量的影响。
四、结语随着新一代控轧控冷装备技术的不断进步和应用,中厚钢板的生产质量不断提高,产品性能得到了显著提升,满足了各种工程结构对材料性能的要求。
控制轧制及控制冷却技术在型钢生产中的应用
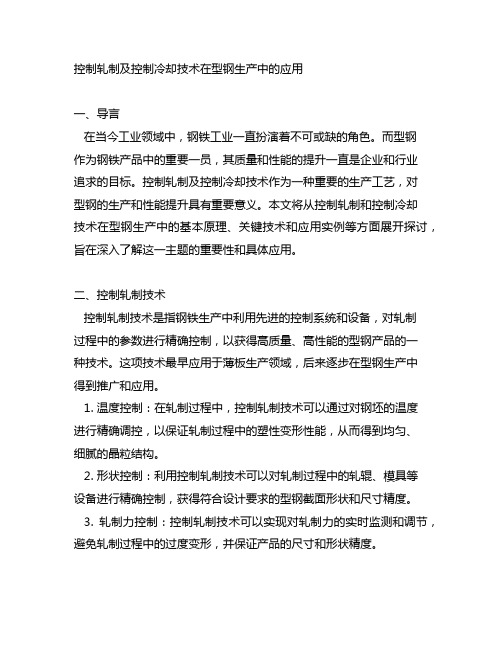
控制轧制及控制冷却技术在型钢生产中的应用一、导言在当今工业领域中,钢铁工业一直扮演着不可或缺的角色。
而型钢作为钢铁产品中的重要一员,其质量和性能的提升一直是企业和行业追求的目标。
控制轧制及控制冷却技术作为一种重要的生产工艺,对型钢的生产和性能提升具有重要意义。
本文将从控制轧制和控制冷却技术在型钢生产中的基本原理、关键技术和应用实例等方面展开探讨,旨在深入了解这一主题的重要性和具体应用。
二、控制轧制技术控制轧制技术是指钢铁生产中利用先进的控制系统和设备,对轧制过程中的参数进行精确控制,以获得高质量、高性能的型钢产品的一种技术。
这项技术最早应用于薄板生产领域,后来逐步在型钢生产中得到推广和应用。
1. 温度控制:在轧制过程中,控制轧制技术可以通过对钢坯的温度进行精确调控,以保证轧制过程中的塑性变形性能,从而得到均匀、细腻的晶粒结构。
2. 形状控制:利用控制轧制技术可以对轧制过程中的轧辊、模具等设备进行精确控制,获得符合设计要求的型钢截面形状和尺寸精度。
3. 轧制力控制:控制轧制技术可以实现对轧制力的实时监测和调节,避免轧制过程中的过度变形,并保证产品的尺寸和形状精度。
三、控制冷却技术控制冷却技术是指在型钢生产过程中,通过对冷却过程的控制,使钢材在冷却过程中获得理想的组织和性能。
这项技术的应用可以有效提高型钢的强度、韧性和耐磨性等性能,同时降低产品的变形和裂纹率。
1. 冷却介质控制:通过选择不同的冷却介质和控制冷却速度,可以使型钢获得不同的组织和性能,如马氏体组织、贝氏体组织等,从而满足不同领域对型钢性能的要求。
2. 温度控制:在控制冷却技术中,对冷却过程中的温度进行精确控制,可以有效控制组织相变,并获得理想的力学性能,如强度、韧性等。
3. 冷却速度控制:通过对型钢冷却速度进行控制,可以获得不同的组织和性能,如快速冷却可以获得细小的组织和高强度,而缓慢冷却则可以得到较好的塑性和韧性。
四、控制轧制及控制冷却技术在型钢生产中的应用实例1. 控制轧制技术在型钢生产中的应用:某钢铁企业引进了先进的控制轧制系统和设备,通过对轧制过程中的温度、形状和轧制力等参数进行精确控制,生产出了高精度、高强度的型钢产品,受到了市场的广泛认可。
浅谈30MnSi生产工艺中控轧控冷技术的应用

道 、集 卷站、P/ F 钩 式运输机 等。生产线采
用控 轧控冷 工艺 ,依据 制定 的工艺制度对钢 材进 行尺寸 精度控制 、温度控制 , 以满足 成 品尺 寸 、性 能要 求 。 4 . 1 高线 生 产 工 艺 流程 : 加 热炉 加热 一 一 高压水 除鳞一 一粗轧 机组一 一 1 群 飞剪 一一 中轧机组 一 一2 群 飞剪 预精轧机 组 一一 预水冷水箱 一 一3 飞 剪一 一侧活套一 一卡断 剪一 一精 轧机组一 一 水冷 水箱一 一测径仪 一 一 夹送 辊一 一吐 丝 机 一 一延迟 型斯 太尔摩 风 冷线一 一集 卷站 一P/F钩式运输机一一打包机一一称重 、 挂牌一一集卷 、入库 ; 4 .2 加 热 温 度 加热温 度影 响轧前 的原始奥 氏体 晶粒大 小 ,各 道次 的轧制温度及 终轧温度影 响道次 之 间和 终轧后 的奥 氏体再 结晶程度及 再结 晶 后 的晶粒大小 。加热温度 也影响开 轧及终轧 温度。3 0 Mn S i 盘条的加热温度控制在 9 8 O ~
一
架桥 墩、铁 路轨枕等预 应力构 件中 。市场 对 建筑基础用 P C钢棒 的需求 量愈来愈大, 高强 度预 应力钢 棒用盘条 的使用量 逐年增加 ,各 大 中小型钢 铁企业也加 大 了生产研发 的力度
。一2 、3 0 Nhomakorabean s l 盘条 的应用 前景
近几 年来 ,随着我 国沿海经 济的飞速 发 展 ,建筑业发展速猛 。据相关 资料 2 0 0 4 年 全 国P C钢棒实际销售量达 1 0 0多万 吨, 该钢 种 具有广阔 的市场前景 。 由于 3 0 Mn S i 盘条对 质 量要 求比较严格 ,尤其 是对化 学成 分、钢 的 纯净度、盘条 的表面质量及 尺寸【 2 】 。唐银 公司 生产 的 3 O Mn S i 盘条规格主要有 8 、 1 0 、 1 2 ,并严格制定 了企业标 准。3 0 Mn S i 盘 条的 成功研发 ,使唐 银公 司的产 品竞争 力有 了进 步 的提 高 ,标着 唐银钢 厂 由生产 普钢型 向 优特 钢型转变的 目标迈进 了一步 1
控轧控冷工艺在盘螺降锰中的应用

控轧控冷工艺在盘螺降锰中的应用发表时间:2018-05-21T16:52:35.757Z 来源:《基层建设》2018年第4期作者:宣文娟[导读] 摘要:通过对控轧控冷工艺的应用,能够促进其组织细化和晶粒细化,进而增加盘螺的韧性和强度,保证其抗拉强度和屈服强度较高。中天钢铁集团有限公司江苏常州 213011摘要:通过对控轧控冷工艺的应用,能够促进其组织细化和晶粒细化,进而增加盘螺的韧性和强度,保证其抗拉强度和屈服强度较高。通过实际应用可以得出,在盘螺降锰中应用控轧控冷工艺,效果显著,其屈服度和强度的比例能够很好的满足抗震钢筋的需求,有效的减少了资源消耗,且合金使用成本也明显降低,进而企业的经济效益得到明显增加。关键词:盘螺;控轧控冷;工艺改进一、控轧控冷工艺概述控轧控冷工艺属于一种板材生产技术,其技术核心主要就是在板材轧制的过程中,通过对冷却条件、轧制过程中、加热温度等工艺参数进行合理控制,进而改变板材的焊接、韧性以及强度性能。随着科学技术的快速发展,控轧控冷工艺已经逐渐巩固和完善。
轧控冷可以简单的理解为控制轧制和冷却过程,在Ti、v、Nb等复合低碳微合金钢中得到良好的应用。控制轧制的基础是对钢材的化学成分进行调节,进而控制变形制度、轧制温度、加热温度等工艺参数,对相变产物组织形式和奥氏体状态进行合理控制,进而有效的提升钢材组织性能;控制冷却指的是对钢材轧制后的冷却条件进行控制,通过控制相变条件、奥氏体组织状态以及碳化物析出行为,来改变其性能。通过对控轧控冷工艺的使用,能够显著的提高钢材的综合性能和强韧性,并降低其中的碳元素含量和合金元素含量,通过对贵重合金元素的节约,生产钢材的成本大大降低。相较于普通生产工艺来说,在应用控轧控冷工艺之后,钢板的屈服强度和抗拉强度大约能提升60Mpa左右,在板形保持、冷却均匀性、合金元素节省、碳元素含量降低等多个方面都具有明显优势。二、生产螺纹钢盘条的工艺流程盘螺的生产工艺流程为:第一步热装和冷装连铸钢坯,第二步是在加热炉中进行加热,第三步是出钢机出炉,第四步是通过出炉辊道进行运输,第五步是6架粗轧机组,第六步是切头、事故碎断1群剪,第七步是4架预精轧机组,第八步是预水冷箱,第九步是切头、事故碎断2飞剪,第十步是10架精轧机组,第十一步是3组水冷箱及均温段,第十二步是夹送辊,第十二步是吐丝机,第十三步是延迟型斯太尔摩运输线,第十四步是集卷站集卷,第十五步是P/F钩式悬挂运输机,第十六步是打包,第十七步是称重,第十八步是挂标签,最后是入成品库。三、在盘螺降锰中对控轧控冷工艺的应用(一)常规轧制在相关制作规范中要求,盘螺的抗拉强度需要≥540Mpa,屈服强度需要≥400Mpa,根据实验步骤的不同可以生产出成分不同的两批方坯,主要是坯料中锰成分含量不同。通过常规轧制可以得出,高猛成分盘螺的强度平均是438Mpa,平均锰含量为1.32%;低锰成分盘螺的强度平均是423Mpa,平均锰含量为1.06%。(二)轧后控冷工艺轧制轧后控冷工艺指的是对钢材轧后的余热进行利用,给予相应的冷却速度,对其相变过程进行合理控制,其中不需要对其进行热处理,在其冷却过程进行控制的目的是为了模拟出铅浴淬火过程,进而保证线材能够具有一定的索氏体组织,该组织的综合机械性能比较好。对于线材轧后冷却控制来说,可以将其分为空冷段相变冷却和水冷段强制冷却两个阶段。空冷区和水冷区两个部分共同构成控制冷却工艺,经过水冷控制线材达到相应温度之后,就能够进行吐丝,在风冷线上直条线材呈散圈状分布,实现风冷处理。在本次研究过程中,在常规工艺轧制之后,小批量的低锰成分盘螺通过控轧控冷工艺进行试制,通过传统高猛盘螺比较可以得出以下几个结论:(一)控制加热温度加热炉中的加热时间和加热温度,会在很大程度上对钢坯的性能的组织产生直接影响。虽然终轧温度对钢坯组织性能所产生的影响比较大,但是加热温度的不同会对冷却过程中线材的组织机理转变形成影响。一般来说,根据盘螺性质的独特性,其加热温度需要控制在(1100±5O)℃的范围内,并将开轧温度控制在970~C左右。(二)控制轧制温度在盘螺塑性变形过程中,精轧是最后一个环节,而对于精轧环节来说,实质上也是奥氏体形成再结晶的重要阶段,而且轧制的温度会直接影响到奥氏体再结晶形核的具体个数,随着轧制温度的升高,再结晶形核的个数就会逐渐减少,但是如果想实现盘螺最终珠光体或组织索氏体出现细化,提高其强度和韧性的话,其再结晶形核的个数则是越多越好,这也就表示应该降低轧制温度。因此,在满足工艺条件的基础上,应该尽可能的降低入精轧的温度,一般可以将其控制在830℃左右。(三)控轧控冷系统在精轧之前,需要1组预水冷水箱,长度和恢复段长度分别为8m、12m,水箱的降温能力为100℃。在精轧之后,需要3组控冷水箱,每组长度和恢复段长度都是8m,水箱的降温能力为100℃。另外还需要佳灵、风门、保温罩、大风量风机(10台)、斯太尔摩控制冷却线等装置。(四)控制吐丝温度控制吐丝温度是开始相变温度控制的重要方面。冷却段数量的多少会对吐丝温度的大小产生直接影响,并对奥氏体晶粒的具体尺寸产生间接影响。当轧件在经过精轧处理之后,奥氏体就会逐渐转变为其他相,但是在转变之前,奥氏体还存在着晶粒长大、再结品、恢复等过程,而在这一过程中会受到时间、温度等多种因素的影响,这也就是所谓的吐丝温度控制。在一般情况下,时间越长、温度越高,所形成的奥氏体晶粒也会之间增大。这也就表示,盘螺在出现相变之前,吐丝温度会影响着奥氏体品粒的尺寸大小。在相关调查研究结果中显示,随着逐渐增加的吐丝温度,盘螺的强度指标会增加;随着逐渐降低的吐丝温度,盘螺的塑性指标会增加,最佳的吐丝温度在810℃一850℃范围内。(五)控制冷却速度对冷却速度进行控制,实质上就是控制辊道和冷却风机的速度,其中辊道速度会在很大程度上受到轧件速度、直径、线还间距等因素的影响,其中最关键的是需要对线还间距进行有效控制,而盘螺直径与线还间距密切相关,这也就表示最终的冷却效果实质上是由线还间距距离决定的。在生产实践中可以得出,当辊道冷却速度使不同盘螺环距离>40mm的话,在快速冷却时候的速度就是获得细珠光体的最佳速度;当其距离为40mm的时候,两者之间热量的影响能够达到最小化,进而风机的风量会决定着冷却速度。由此可以得出,标准型冷却工艺参数的最佳间距值为40mm,这也就是控制辊道速度的界限值。除此之外,逐渐增加的辊道速度,并错开盘条搭接点,将热点影响消除,进而使同圈强度均匀性提高。以免在冷却速度比较低的话,析出Fe3C,这样就会限制拉拔。四、工艺改进根据目前使用的机械轧制设备和工艺,为了提高冷却工艺和控制轧制温度,还需要采取相应的措施做出进一步的改进和优化,这可以通过以下一个方面来实现:一是适当的增加风机风量:二是用水冷导槽代替盘圆出口空过导槽;三是住精轧奇架中加入冷却水路,将其末端压力控制在1.0MPa,这样一来轧制温度和吐丝温度都会有所降低;四是及时的更换水冷箱。保证其冷却性能的良好;五是将冷却水管加入中轧出口,保证钢表面的前后温度差为20℃。五、结束语盘螺属于一种热轧带肋钢筋,是通过高速线材轧机批量生产出来的,盘条是其主要的交货状态,一般规格比较小。对于盘螺来说,其强度比较大,与光圆钢筋相比较来说,其握紧力比较好,因此在各个行业和领域中都得到广泛应用,具有比较大的市场需求量。但是目前生产盘螺的成本比较高,企业难以获得良好的经济效益和社会效益,因此就必须加强对工艺的改进和优化,降低其中的锰含量。为了更好的保证盘螺的韧性和强度,就必须加强度控轧控冷工艺的应用,这样在满足标准要求的同时,能够最大限度的减少成本投入。参考文献:[1]郑团星,郭继亮,邱雄文,等.螺纹盘条生产技术的开发与应用[J].钢铁研究,2013,(3):50—52.。
控轧空冷综述

控轧控冷在棒线材中的应用班级:摘要:线材为了获得高强度、高韧性的综合性能, 可以采用不同的控制轧制工艺来达到。
关键词:控轧空冷应用线材前言控制轧制和控制冷却技术作为提高产品的组织性能,降低钢材生产成本,提高企业经济效益上起着巨大的作用。
正文一.控轧控冷概述1.控轧控冷概念(1)控制轧制:在热轧过程中,通过对金属加热制度、变形制度和温度制度的合理控制,使热塑性变形与固态相变相结合,以获得细小晶粒组织,从而得到较高的综合性能的轧制工艺。
(2)控制冷却:控制轧后钢材的冷却速度达到改善钢材组织和性能的目的。
2.控制轧制的优点如下:(1)可以在提高钢材强度的同时提高钢材的低温韧性。
(2)可以充分发挥铌、钒、钛等微量元素的作用。
3.控制轧制工艺的缺点:(1)要求较低的轧制变形温度和一定的道次压下率,因此增大了轧制负荷。
(2)由于要求较低的终轧温度,大规格产品需要在轧制道次之间待温,降低轧机生产率。
4.控制冷却工艺的优点(1)节约能耗、降低生产成本。
利用轧后钢材余热,给予一定的冷却速度控制其相变过程,从而可以取代轧后正火处理和淬火加回火处理,节省了二次加热的能耗,减少了工序,缩短了生产周期,从而降低了生产成本。
(2)可以降低奥氏体相变温度,细化室温组织。
轧后控制冷却能够降低奥氏体相变温度,对同一晶粒度级别的奥氏体,低温相变后会使,晶粒明显细化,使珠光体片层间隔明显变薄。
(3)可以降低钢的碳当量。
采用轧后控制冷却工艺有可能减少钢中的碳含量及合金元素加入量,达到降低碳当量的效果。
(4)道次间控制冷却可以减少待温时间,提高轧机小时产量。
在道次间采用控制冷却,可以精确地控制终轧温度,减少轧件停下来等待降温的时间。
5.控制轧制、控制冷却工艺参数控制特点(1)控制钢坯加热温度。
根据对钢材性能的要求来确定钢坯加热温度,对于要求强度高而韧性可以稍差的微合金钢,加热温度可以高于1200℃,对以韧性为主要性能指标的钢材,则必须控制其加热温度在1150 ℃以下。
- 1、下载文档前请自行甄别文档内容的完整性,平台不提供额外的编辑、内容补充、找答案等附加服务。
- 2、"仅部分预览"的文档,不可在线预览部分如存在完整性等问题,可反馈申请退款(可完整预览的文档不适用该条件!)。
- 3、如文档侵犯您的权益,请联系客服反馈,我们会尽快为您处理(人工客服工作时间:9:00-18:30)。
日本有的厂将轧件温度冷却至 650℃、进入无扭精轧机组轧制, 再经斯 太尔摩冷却线,这样可得到退化珠光体组织, 到球化退火时, 退火时间 可缩短
一、终轧温度的设定
1) 高碳钢、 低合金高强度钢以及冷镦钢之类线材的终轧温度 对于强度和韧性要求较严格线材,要求奥氏体晶粒细化 (粗晶粒冲击韧性 差) 、 脱层薄, 所以它们的终轧温度不能过高, 一般应控制在930980℃ 。 2) 低碳软钢、 碳素焊条钢线材的终轧温度 对强度性能要求不高, 主要用于拉拔铁丝、 制钉等用途的由于含碳量低, 奥氏体化温度高, 所以终轧温度应相应高一些, 一般可设定在9801050℃ 。 3) 轴承钢线材的终轧温度 对于轴承钢, 为了避免网状碳化物形成, 在轧机能力许可的情况下, 应 该使终轧温度可能低于900℃ 。如不能达到, 则需在轧后快冷至 650℃左 右保温。 4) 奥氏体-铁素体型不锈钢线材的终轧温度 对某些奥氏体-铁素体型不锈钢, 为了让碳化物充分溶解, 以便在后续冷 却中得到固溶处理的效果, 必须进行高温终轧。终轧温度一般不低于 1050 ℃ 。终轧温度的控制可通过增加或减少精轧机机架间水冷量和精轧 机前水箱水量来实现。
合金元素在钢中的作用
A 加热阻止奥氏体长大 随着加热温度的提高及保温时间的延长,奥氏体晶粒变得 粗大。微合金元素形成高度弥散的碳氮化合物小颗粒.可以 对奥氏体晶界起固定作用.从而阻止奥氏体晶粒长大.即提 高了钢的粗化温度
当Nb、Ti含量在0.10%时, 可以提高奥氏体粗化温度 到1050~1100℃,V在小 于0.10% 时,阻止晶粒长 大的作用不大.在950 ℃ 左右奥氏体晶粒就开始粗 化。
二、 吐丝温度的设定
它是控制相变开始温度的关键参数。在斯太尔摩控冷工艺中, 一般根 据钢种和用途的不同将吐丝温度控制在760-900℃。部分钢种选用下列 吐丝温度:
对低、 中碳钢为了提高强度, 应降低吐丝温度, 而对高碳钢, 则要提高 吐丝温度才能获得强度的增加。
对有些以强度为主的线材, 如建筑用钢筋, 为了提高其抗拉强度, 有意将吐丝 温度设定得很低 ( 600℃以下) , 让其表面形成马氏体, 然后在后续冷却中利 用芯部余热进行自回火而得到回火马氏体。这样处理使线材抗拉强度大大提高。
高线控制轧制技术的目的是减少脱碳,控制晶粒尺寸,控制显微组织与
性能,控制氧化铁皮,节约或取消热处理。
控制上一般采用两段或三段变形制度,由于高线孔型系统一定,因此变 形量调整不大,主要靠温度控制来改善变形奥氏体的组织状态,提高钢 材性能,在设计上采用低温开轧、精轧前后水箱水冷来实现。一般粗轧 在奥氏体再结晶区变形细化晶粒,中轧或精轧在950℃以下轧制,在γ相
提高控轧、控冷钢材强韧性的因素
控制轧制、控制冷却技术在工业中的应用
1.线、 棒材控制轧制技术
控温轧制有如下两种变形制度: A二段变形制度 粗轧在奥氏体再结晶区轧制, 通过反复变形及再结晶细化奥 氏体晶粒; 中轧及精轧在950℃以下轧制, 是在γ 相的未再 结晶区变形, 其累计变形量为60%~70%, 在Ar3附近终轧, 可以得到具有大量变形带的奥氏体未再结晶晶粒, 相变以后 能得到细小的铁素体晶粒。 B 三段变形制度 粗轧在γ 再结晶区轧制, 中轧在950℃以下的γ 未再结晶区 轧制, 变形量为70%, 精轧在Ar3与Ar1(之间的双相区轧制。 这样得到细小的铁素体晶粒及具有变形带的未再结晶奥氏体 晶粒, 相变后得到细小的铁素体晶粒并有亚结构及位错。为 了实现各段变形,必须严格控制各段温度, 在加热时温度不 要过高, 避免奥氏体晶粒长大, 并避免在部分再结晶区中 轧制形成混晶组织, 破坏钢的韧性。
3.合金元素的作用
在HRB400盘条生产中,钒、钒-氮、铌、钛
微合金化成分在20Mnsi基础上分别增加 0.04%-0.12%V、 0.02%-0.04%Nb , 0.02%-0.05%Ti,强化机制主要为析出强化 和细晶强化
HRB400盘条的组织是铁素体+珠光体.钒、铌微合金元素 在控轧控冷中的作用主要有:(1)加热时抑制 奥氏体晶粒长 大;(2)变形时抑制奥氏体再结晶;(3)相变时使铁素体晶粒 细化;(4)相间或铁素体基体析出强化。 钒的溶解度较大,热变形时一般处于固溶状态,对再结晶 过程抑制较小,它的主要作用是奥氏体向铁素体转变时相间 或铁素体基体析出强化.细晶强化作用较小.但是氮的加 入.在奥氏体中VN的溶解度与NbC相当,变形时诱导析出 的VN能抑制奥氏体再结晶和阻止晶粒长大。 铌的最突出的作用是抑制高温变形的再结晶,扩大了再结 晶温度范围,微量的铌能起到显著的细晶强化效果和中等的 析出强化效果。在非再结晶区累计变形能诱导相变获得超细 铁素体晶粒
一般采用降低开轧温度的办法来保证对温度的有效控制。根据几个生产 厂应用控温轧制的经验, 高碳钢 (或低合金钢) 、 低碳钢的粗轧开轧 温度分别为900℃、850℃, 精轧机组入口轧件温度分别为925℃、 870℃, 出口轧件温度分别为900℃、850℃。在设计上, 低碳钢可在 800℃进入精轧机组精轧, 常规轧制方案也可在较低温度下轧制中低碳 钢材, 以促使晶粒细化。 中轧机组前加水冷箱可保证精轧温度控制在900℃、, 而在精轧机处轧 制温度为700~750℃, 压下量为35~45%, 以实现三阶段轧制。 如能在无扭精轧机入口处将钢温控制在950℃、以下, 粗、 中轧可考虑 在再结晶区轧制, 这样可降低对设备强度的要求。
三、相变区的冷却速度控制
相变区冷却速度决定着奥氏体的分解转变温度和时间, 也决定着线材的 最终组织形态, 所以整个控冷工艺的核心问题就是如何控制相变区冷却 速度。
对具有散卷风冷运输和这一类型的冷却工艺来说, 冷却速度的控制取决 于运输机的速度、 风机状态和风量大小以及保温罩盖的开闭。 运输机速度是改变线圈在运输机上布放密度的一种工艺控制参数。通过 改变运输机速度采改变线圈布放密度, 从而控制线材的冷却速度, 这是 散卷冷却运输机的主要功能。 一般说来, 在轧制速度、 吐丝温度以及冷却条件相同的情况下,运输机 的速度越快,线圈布放得越稀, 散热速度越快, 因而冷却速度越快。但 这种关系并非对全部速度范围都成立, 当运输机的速度快到一定值时, 冷却速度达到最大, 即使再增大运输机速度, 冷却速度也不再增加。这 是因为运输机速度加快, 增加了线圈间距, 使线圈之间的相互热影响不 断减小, 直至消失, 此时运输机速度增加, 不能提高冷却效果。相反, 运输机速度加快缩短了盘卷的风冷时间, 反而会降低冷却效果。
末再结晶区变形;或中轧在950℃以下轧制,在γ相未再结晶区变形.精
轧在Ar3与Ar1两相区轧制。
不同产品因钢种、成分及最终用途的不同要求不同的冷却速度,以此来
控制转变时间、相交组织状态。冷却方法主要有两种类型:一类是采用
水冷+运细机散卷风冷(或空冷),典型工艺有斯太尔摩冷却工艺、阿希洛 冷却工艺、施罗曼冷却工艺、达涅利冷却工艺等;另一类是水冷+其他 介质或其他布卷方式冷却,如ED法、
热轧后控制冷却工艺包括三个不同的冷却阶段,一般把从终轧温度开始 到奥氏体向铁素体开始转变温度Ar3的冷却称为一次冷却,把随后至奥氏 体相变完成的整个过程的冷却称为二次冷却.把奥氏体相变完了至室温 的冷却称为三次冷却(空冷)。三个冷却阶段的目的和要求是不同的。 一次冷却的目的是控制热变形后的奥氏体状态.阻止奥氏体晶粒长大, 固定由于变形而引起的位错,加大过冷度,降低相变温度,为相变做组 织上的准备。相变前的组织状态直接影响相变机制和相变产物的形态、 大小和钢材性能。一次冷却的开始快冷温度越接近终轧温度,细化奥氏 体效果越好。 二次冷却在相变过程中控制相变冷却开始温度、冷却速度和停止温度 等,以保证得到所需金相组织与钢材性能。不同钢种根据组织性能的要 求选择不同的冷却速度。低碳钢、低合金钢、微合金钢轧后快冷,可以 得到铁素体和细珠光体及弥散的碳化物;高碳钢、高碳合金钢轧后快冷, 能减小珠光体片层间距;冷撤钢、轴承钢缓冷,等温转变可以得到变态 珠光体、球状或半球状碳化物,节约用户热处理球化退火时间。 三次冷却或空冷,相变结束后采用空冷,固溶在铁素体中的过饱和破 化物随温度降低在不断弥散析出,便其沉淀强化。
1.4 控轧控冷的应用
主讲:王庆娟
控制轧制的优点如下:
(1)可以在提高钢材强度的同时提高钢材的低温韧性。
(2)可以充分发挥铌、钒、钛等微量元素的作用。
控制轧制工艺的缺点:
(1)要求较低的轧制变形温度和一定的道次压下率,因 此增大了轧制负荷。 (2)由于要求较低的终轧温度,大规格产品需要在轧制 道次之间待温,降低轧机生产率。
运输机速度的确定除了与钢种、 规格和性能要求有关之外, 还与轧制速 度有关。
四、集卷温度的确定
集卷温度主要取决于相变结束温度及其后的冷却过程。为了
保证产品性能, 避免集卷后的高温氧化和 FeO 的分解转变 以及改善劳动环境, 一般要求集卷温度在 250以下。有时由 于受冷却条件的限制, 集卷温度可能会高一些, 但不应高 于350。所以, 多数情况下要求集卷段鼓风冷却, 以降低集
控制冷却工艺的优点 (1)节约能耗、降低生产成本。利用轧后钢材余热,给予 一定的冷却速度控制其相变过程,从而可以取代轧后正火处 理和淬火加回火处理,节省了二次加热的能耗,减少了工序, 缩短了生产周期,从而降低了生产成本。 (2)可以降低奥氏体相变温度,细化室温组织。轧后控制 冷却能够降低奥氏体相变温度,对同一晶粒度级别的奥氏体, 低温相变后会使,晶粒明显细化,使珠光体片层间隔明显变 薄。 (3)可以降低钢的碳当量。采用轧后控制冷却工艺有可能 减少钢中的碳含量及合金元素加入量,达到降低碳当量的效 果。 (4)道次间控制冷却可以减少待温时间,提高轧机小时产 量。在道次间采用控制冷却,可以精确地控制终轧温度,减 少轧件停下来等待降温的时间。