最新对高速线材生产中控轧控冷的分析
对高速线材生产中控轧控冷的分析.doc
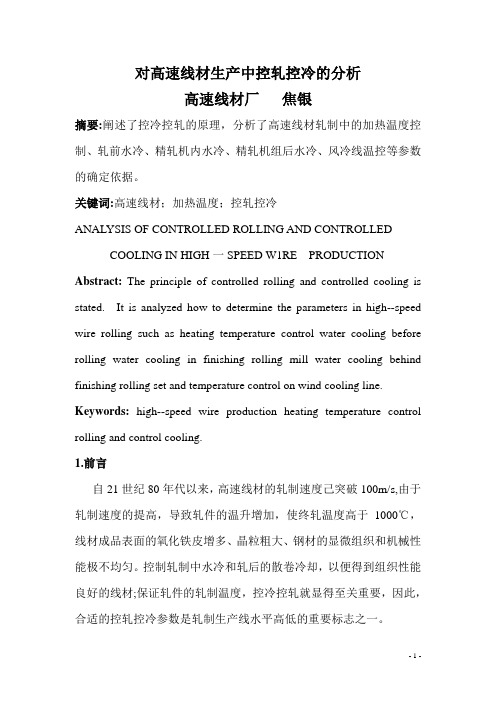
对高速线材生产中控轧控冷的分析高速线材厂焦银摘要:阐述了控冷控轧的原理,分析了高速线材轧制中的加热温度控制、轧前水冷、精轧机内水冷、精轧机组后水冷、风冷线温控等参数的确定依据。
关键词:高速线材;加热温度;控轧控冷ANALYSIS OF CONTROLLED ROLLING AND CONTROLLED COOLING IN HIGH一SPEED W1RE PRODUCTION Abstract:The principle of controlled rolling and controlled cooling is stated. It is analyzed how to determine the parameters in high--speed wire rolling such as heating temperature control water cooling before rolling water cooling in finishing rolling mill water cooling behind finishing rolling set and temperature control on wind cooling line. Keywords:high--speed wire production heating temperature control rolling and control cooling.1.前言自21世纪80年代以来,高速线材的轧制速度己突破100m/s,由于轧制速度的提高,导致轧件的温升增加,使终轧温度高于1000℃,线材成品表面的氧化铁皮增多、晶粒粗大、钢材的显微组织和机械性能极不均匀。
控制轧制中水冷和轧后的散卷冷却,以便得到组织性能良好的线材;保证轧件的轧制温度,控冷控轧就显得至关重要,因此,合适的控轧控冷参数是轧制生产线水平高低的重要标志之一。
钢材控轧控冷工艺的技术研究及应用
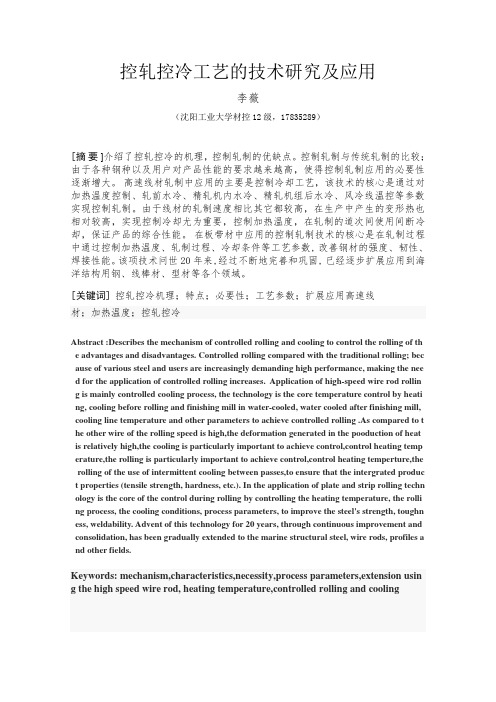
控轧控冷工艺的技术研究及应用李薇(沈阳工业大学材控12级,17835289)[摘要 ]介绍了控轧控冷的机理,控制轧制的优缺点。
控制轧制与传统轧制的比较;由于各种钢种以及用户对产品性能的要求越来越高,使得控制轧制应用的必要性逐渐增大。
高速线材轧制中应用的主要是控制冷却工艺,该技术的核心是通过对加热温度控制、轧前水冷、精轧机内水冷、精轧机组后水冷、风冷线温控等参数实现控制轧制。
由于线材的轧制速度相比其它都较高,在生产中产生的变形热也相对较高,实现控制冷却尤为重要,控制加热温度,在轧制的道次间使用间断冷却,保证产品的综合性能。
在板带材中应用的控制轧制技术的核心是在轧制过程中通过控制加热温度、轧制过程、冷却条件等工艺参数,改善钢材的强度、韧性、焊接性能。
该项技术问世20年来,经过不断地完善和巩固,已经逐步扩展应用到海洋结构用钢、线棒材、型材等各个领域。
[关键词]控轧控冷机理;特点;必要性;工艺参数;扩展应用高速线材;加热温度;控轧控冷Abstract :Describes the mechanism of controlled rolling and cooling to control the rolling of th e advantages and disadvantages. Controlled rolling compared with the traditional rolling; bec ause of various steel and users are increasingly demanding high performance, making the nee d for the application of controlled rolling increases. Application of high-speed wire rod rollin g is mainly controlled cooling process, the technology is the core temperature control by heati ng, cooling before rolling and finishing mill in water-cooled, water cooled after finishing mill, cooling line temperature and other parameters to achieve controlled rolling .As compared to t he other wire of the rolling speed is high,the deformation generated in the pooduction of heat is relatively high,the cooling is particularly important to achieve control,control heating temp erature,the rolling is particularly important to achieve control,control heating temperture,the rolling of the use of intermittent cooling between passes,to ensure that the intergrated produc t properties (tensile strength, hardness, etc.). In the application of plate and strip rolling techn ology is the core of the control during rolling by controlling the heating temperature, the rolli ng process, the cooling conditions, process parameters, to improve the steel's strength, toughn ess, weldability. Advent of this technology for 20 years, through continuous improvement and consolidation, has been gradually extended to the marine structural steel, wire rods, profiles a nd other fields.Keywords: mechanism,characteristics,necessity,process parameters,extension usin g the high speed wire rod, heating temperature,controlled rolling and cooling1引言控制轧制(C-R)和控制冷却(C-C)技术的研究始于1890年二次世界大战的德国,当时科研人员对钢铁产品的加热工条件、材质及显微金相组织之间的关系进行了非系统的零散研究。
中高碳钢棒线材的控冷工艺及主要类型

B、对棒线材冷却工艺的要求:
1)二次铁皮要少,以减少金属消耗和二 次加工前的酸耗和酸洗时间;
2)冷却速度要适当,要根据不同品种, 控制冷却工艺参数,得到所需要的组织;
3)要求整根轧件性能均匀。
路漫漫其悠远
(4)棒线材控制冷却的分类
根据轧后控制冷却所得到的钢的组织不同,分 为珠光体型控制冷却、马氏体型控制冷却。
(Ar3)的提高,相变后的铁素体晶粒容易长大,造 成力学性能降低。为了细化铁素体晶粒,减少珠 光体片层间距,阻止碳化物在高温下析出,以提 高析出强化效果而采用控制冷却工艺。
路漫漫其悠远
(2)高碳钢控冷的基本概述
控制冷却过程是通过控制轧后三个不同冷却阶段的工 艺参数,来得到不同的相变组织。分别称为一次、二次和 三次冷却。
路漫漫其悠远
e、Stelmor控冷工艺近年来的发展和改进
主要内容:
①斯太尔摩线的总长度有加长的趋势;
②辊道段数增多; ③大风量高风压冷却风机使线材的抗拉强度显著提高; ④风机台数增加,近期新建的高速线材车间有采用14台; ⑤调节风量的电动“佳灵”(OPTIFLEX)装置被普遍采用,使线 圈两侧搭接处加强送风,更好的解决线材强度的均匀性; ⑥保温段的总长度亦趋于加长,有的已达90m; ⑦冷却段的各段输送辊道均为爬坡式。 ⑧实心的耐热铸铁传动辊两端加工有散热的翅片,避免轴承过度 受热; ⑨在输送机的2、4、6、8段内设有振动辊,以消除“热死点”效应。 改善通条性能,防止拉拔断裂; 路漫漫其悠远 ⑩辊道采用交流变频电机,单独进行速度控制。
路漫漫其悠远
穿水冷却线材断面温度的变化简图
a、珠光体型控制冷 b、马氏体型控制冷
却
却
为了获得有利于拉拔的索 氏体组织,线材轧后应由奥氏 体化温度急冷至索氏体相变温 度下进行等温转变,其组织可 得到索氏体。
高速线材轧后的控制冷却技术
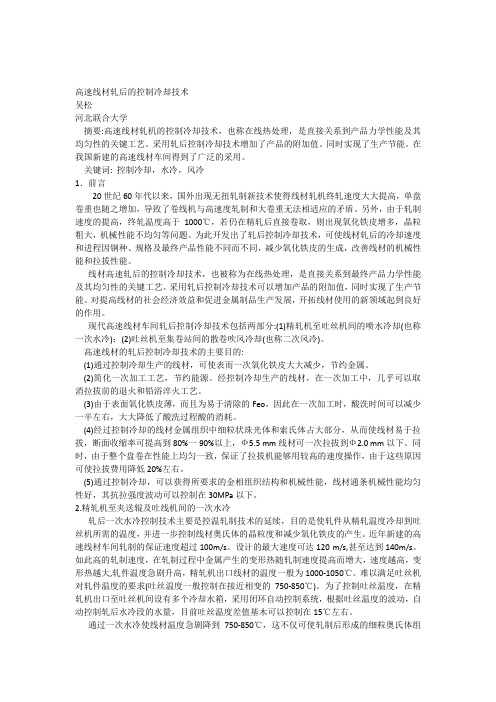
高速线材轧后的控制冷却技术吴松河北联合大学摘要:高速线材轧机的控制冷却技术,也称在线热处理,是直接关系到产品力学性能及其均匀性的关键工艺。
采用轧后控制冷却技术增加了产品的附加值。
同时实现了生产节能。
在我国新建的高速线材车间得到了广泛的采用。
关键词: 控制冷却,水冷,风冷1.前言20世纪60年代以来,国外出现无扭轧制新技术使得线材轧机终轧速度大大提高,单盘卷重也随之增加,导致了卷线机与高速度轧制和大卷重无法相适应的矛盾。
另外,由于轧制速度的提高,终轧温度高于1000℃,若仍在精轧后直接卷取,则出现氧化铁皮增多,晶粒粗大,机械性能不均匀等问题。
为此开发出了轧后控制冷却技术,可使线材轧后的冷却速度和进程因钢种、规格及最终产品性能不同而不同,减少氧化铁皮的生成,改善线材的机械性能和拉拔性能。
线材高速轧后的控制冷却技术,也被称为在线热处理,是直接关系到最终产品力学性能及其均匀性的关键工艺。
采用轧后控制冷却技术可以增加产品的附加值,同时实现了生产节能。
对提高线材的社会经济效益和促进金属制品生产发展,开拓线材使用的新领域起到良好的作用。
现代高速线材车间轧后控制冷却技术包括两部分:(1)精轧机至吐丝机间的喷水冷却(也称一次水冷);(2)吐丝机至集卷站间的散卷吹风冷却(也称二次风冷)。
高速线材的轧后控制冷却技术的主要目的:(1)通过控制冷却生产的线材,可使表而一次氧化铁皮大大减少,节约金属。
(2)简化一次加工工艺,节约能源。
经控制冷却生产的线材,在一次加工中,几乎可以取消拉拔前的退火和铅浴淬火工艺。
(3)由于表面氧化铁皮薄,而且为易于清除的Feo,因此在一次加工时,酸洗时间可以减少一半左右,大大降低了酸洗过程酸的消耗。
(4)经过控制冷却的线材金属组织中细粒状珠光体和索氏体占大部分,从而使线材易于拉拔,断面收缩率可提高到80%一90%以上,Ф5.5 mm线材可一次拉拔到Ф2.0 mm以下。
同时,由于整个盘卷在性能上均匀一致,保证了拉拔机能够用较高的速度操作,由于这些原因可使拉拔费用降低20%左右。
高速线材生产中的控轧控冷技术分析

高速线材生产中的控轧控冷技术分析摘要:对于生产高速线材来说,控轧控冷技术工艺一方面与所生产的线材质量密切相关,另一方面也与控轧控冷设备性能有关,这就需要在生产高速线材过程中,不断创新优化控轧控冷工艺,以不断提升产品质量与生产效率,使工业发展需求得到满足。
虽然应用控轧控冷技术能够获取性能与组织都比较理想的钢材,然而,在操作实际过程中,会受到很多控制因素的影响,尤其是冷却控制,在对相关因素予以充分考虑的基础上,应强化技术创新和应用实践,通过不断摸索,实现控轧控冷效果的提升,使控轧控冷技术能够更好地为高速线材生产工艺提供服务。
本文主要研究生产高速线材所应用到的控轧控冷技术,以期能够提升高速线材性能,满足工业生产需求。
关键词:高速线材;控轧控冷技术;工业生产在国内工业化发展中,钢铁材料发挥着重要作用,尤其是作为重要钢铁材料的线材,被广泛应用于工业生产中。
线材是轧制钢铁后生产出来,线材的性能、质量等与生产工艺、生产设备关联性较大,其中包括控制冷却、控制轧制等工艺。
生产工艺、设备不同,所产高速线材性能差别也比较明显[1]。
因为轻重工业中需要应用到高速线材,所以不断提升高速线材生产质量,确保高速线材产品优异性能,对我国工业发展极具重要意义。
本文主要研究生产高速线材所应用到的控轧控冷技术,以期能够提升高速线材性能,满足工业生产需求。
1.高速线材控轧控冷原理为与市场发展相适应,钢铁材料既要持续提升性能,又要不断丰富钢铁种类,如何在确保钢材韧性前提下,提高钢材强度,是当前工业生产与发展所关注的重要话题。
控轧控冷技术能够在优化钢材性能基础上,简化钢材冶炼流程,是生产高速线材所用到的一种重要工艺。
所谓控制轧制,就是对热轧期间的金属变形、加热以及温度等进行有效控制,保证热塑性变形与固态相变细化组织相结合,使钢材焊接、韧性以及刚度等力学性能得到优化。
控制冷却,指的是通过最佳速度对轧后钢材进行冷却,改善钢材性能和组织。
所以,控轧控冷工艺有助于热轧钢材有效实现相变与形变,从而生产出性能更好的钢材。
高速线材生产中的控轧控冷

综合信息区域治理随着技术的不断进步,高速线材的生产速度越来越快,要想保证轧件的温度,那么控轧控冷就尤为重要,所以合适的控轧控冷参数的确定是评判生产线水平的重要标准。
一、控轧控冷参数的确定控轧分为加热温度控制,加热温度控制,精轧前水冷控制,精轧后水冷控制,精轧机组间水冷控制,吐丝温度控制,风冷线的温度控制。
1.1加热温度控制目前,高层设备的高层设备制造商普遍采用控制轧制技术。
为了实现控制轧制的目的,温度从钢坯脱模时开始进行控制,要求钢坯的加热温度低于常温轧制时的温度。
它可以保证最终产品的质量,同时可以减少钢坯表面的脱碳,节约燃料,降低钢材的生产成本。
现有的线材生产线中,合金钢比例较高,加热炉采用步进式加热炉,其加热功能完全可以满足各种钢种的温度要求。
经过比较分析后,典型的钢种轧制温度是:碳素结构钢980±20℃、合金结构钢960±20℃、弹簧、轴承钢950±20℃。
同时要求钢坯出炉温度均匀,断面温差小于30℃。
1.2轧前水冷为了控制进入精轧机的轧机温度,在轧机前加入水冷罐,降低轧件温度,达到控制轧制的目的。
通过控制水箱内水冷喷嘴的开启度和开启数量,可以使水冷箱温度下降后,降温100-150℃,然后经过一个温度恢复段,使轧件的芯、表温度均匀,温差控制在±30℃左右,不影响下一道次的轧制。
在该机组上理论上计算和设计了高线设备实际检测的水冷参数如下:精加工前的槽长(1套)6.11m,回收段的长度37m,正向水冷喷嘴出水压力300kPa,反向水冷喷嘴出口压力700kPa。
1.3精整线中的水冷为了防止由精轧机的高轧制速度引起的轧制件的温度上升,在精轧机的机架之间增加了水冷装置;为了保证轧件的均匀冷却,将水冷装置安装在滚圆与椭圆框架之间,高速轧机制造商增加了单位间距(900-1200mm),其目的是控制水冷后轧件的温升,以消除轧制由于过高的轧制温度而形成粗糙的晶粒导致线材的缺陷减少。
线材生产中的控制轧制和控制冷却技术

线材生产中的控制轧制和控制冷却技术线材是现代工业生产中使用频繁的一种材料,它广泛应用于电线电缆、机械制造、建筑材料等行业。
在线材生产过程中,控制轧制和控制冷却技术是关键的环节,它们直接影响着线材的质量、机械性能和用途范围。
一、控制轧制控制轧制是指通过改变轧制变形量、轧制温度、轧制速度、轧制力等因素,控制金属材料的形变和微观组织,达到调整线材力学性能、改善表面质量和优化产品用途的目的。
1、轧制变形量控制轧制变形量是指轧制前后的减压变化,它对线材的力学性能和表面质量有着直接影响。
为了保证线材的质量稳定和合格率,轧制变形量控制必须精准可靠,并考虑到批量变化和轧制型号的特定要求。
目前,国内外的轧制变形量控制采用电液伺服技术,通过实时监测轧制变形量变化,及时控制系统参数的变化,保证线材轧制变形量的稳定。
2、轧制温度控制轧制温度是指线材在轧制时的温度,它对线材的力学性能和表面质量有着重大影响。
过高或过低的温度会导致线材的晶粒过大或过小,从而影响线材的硬度、韧性和塑性等力学性能。
为了提高线材的机械性能和用途范围,轧制温度控制必须准确可靠,并考虑到金属材料的温度敏感性和轧制工艺的特定要求。
目前,国内外的轧制温度控制采用激光测温技术或红外线测温技术,通过实时监测线材温度变化,及时调整轧制温度,保证线材轧制温度的稳定。
3、轧制速度控制轧制速度是指线材在轧制过程中的速度,它对线材的表面质量和机械性能有着直接影响。
过高或过低的轧制速度会导致线材表面的纹路不均匀和线材的硬度、韧性等力学性能下降。
为了提高线材的表面质量和机械性能,轧制速度控制必须准确可靠,并考虑到轧制型号的特定要求。
目前,国内外的轧制速度控制采用伺服电机技术或电磁流体技术,通过实时监测线材的速度变化,及时调整轧制速度,保证线材轧制速度的稳定。
二、控制冷却控制冷却是指针对金属材料在热加工过程中产生的内应力、变形、晶粒长大等现象,通过采用不同的冷却方式和工艺参数,调整金属材料的组织和性能。
控轧控冷技术的研究现状及发展论

控轧控冷技术的研究现状及发展摘要:本文介绍了控轧控冷工艺的发展历史、工艺原理以及控轧控冷工艺,叙述了近些年来国内外发展与应用以及今后的展望。
关键词:控扎控冷;TMCP; 超快冷技术;热轧一、概述控扎控冷是一项具有丰富理论内容和较大实用价值的轧钢新技术,其特点是把利用塑性变形得到钢材外部几何形状的热加工成形过程与控制改善钢材的组织状态,提高钢材性能的物理冶金过程有机结合起来,简单地说就是把将钢的热变形与相变有机的结合起来。
其突出的优点是:可大幅度提高低碳钢、低合金钢钢材的强韧性;提高热轧钢材性能合格率;同时可简化工序,节省能耗,节约合金,具有显著地经济效益和社会效益[1]。
控制轧制(C - R) 和控制冷却(C - C) 技术的研究始于1890年至二次世界大战期间的德国,当时科研人员对钢铁制品的热加工条件、材质及显微金相组织之间的关系进行了非系统的零散研究,只是定性地揭示了热加工条件和材质间的关系。
到了20世纪60年代初期, 在美国科研人员定性地解释了热轧后的钢材继续发生奥氏体再结晶的动力学变化后, 这才从理论上某种程度地解释了控制轧制技术。
到了20世纪60年代末期, 科研人员通过试验发现, 添加微量元素铌(Nb) 对提高单纯轧制钢。
材的强度有效。
随后进一步的研究表明, 造成铌系钢材高强度的原因,是由于微细铌碳氮化合物的铁素体析出相强化造成的。
同期英国钢铁研究机构对轧制钢材的显微结构和机械性能的定量关系、铌、钒(V)的强化机理, 控制轧制原理等进行研究, 证实了依靠物理冶金基础, 进行合理的合金成分的设计和轧制条件的设定, 便能达到所期望的钢材目标性能值和显微组织。
到了20世纪70年代,对钢材强度、低温韧性、焊接性能要求更高了,而此时仅仅依靠传统的控制轧制技术远远不够。
于是在奥氏体控制轧制的基础上, 还需要控制冷却速度来控制相变本身, 于是开始了真正意义的控轧控冷技术的应用二、控扎控冷的原理控轧控冷技术的基本原理就是控制热轧条件,经过相变过程在奥氏体(γ)的基体上,形成高密度的铁素体(α)晶核,从而在相变后, 达到细化钢材的组织结构[3]。
线材生产中的控制轧制和控制冷却技术

应采用轧后快速冷却。因为如果轧后慢冷 , 则变形奥氏体 晶粒将在冷却过程中长大 , 相变后得 到粗 大的铁 素体组 织。由于冷却缓慢 , 由奥 氏体转变的珠光体粗大, 片层 问 距加厚。这种组织的力学性能较低 。对于低温终轧的线 材 , LG 终 ̄ u奥氏体处于未再结晶温度 区域 , , 由于变形影响 温度提高, 终轧后奥氏体很快就相变 , 形成铁素体。这
着重叙述 了线材 生产 中控制轧制和控制冷却技术的机理、 特点 、 、 用及斯 太尔摩冷却 工艺。 方式 应
关键词 :线材 生产 中图分类号 :l T ̄l 控制轧制 控制冷却 斯 太尔摩冷却工 艺 (0 10 08 0 2 1 )2— 07— 5 文献标识码 : A 文章编号 :02一 10  ̄
a p iain o o told r l n d C n r l d c o i g tc nq e a d semo o t l d c oi g tc n l gc lp o e s a e man y d — p l t fC n r l ol g a o t l o l e h iu n tl r C n r l o ln e h o o ia r c s r il e c o e i n oe n oe s rb d c e. i
一种轧钢过程控冷的方法
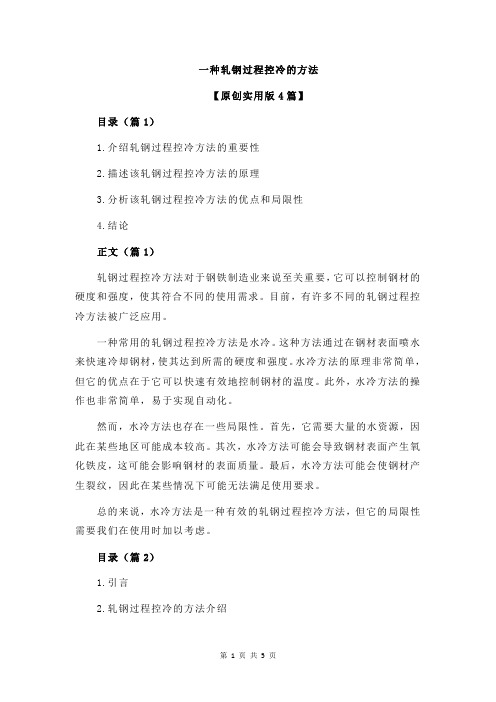
一种轧钢过程控冷的方法【原创实用版4篇】目录(篇1)1.介绍轧钢过程控冷方法的重要性2.描述该轧钢过程控冷方法的原理3.分析该轧钢过程控冷方法的优点和局限性4.结论正文(篇1)轧钢过程控冷方法对于钢铁制造业来说至关重要,它可以控制钢材的硬度和强度,使其符合不同的使用需求。
目前,有许多不同的轧钢过程控冷方法被广泛应用。
一种常用的轧钢过程控冷方法是水冷。
这种方法通过在钢材表面喷水来快速冷却钢材,使其达到所需的硬度和强度。
水冷方法的原理非常简单,但它的优点在于它可以快速有效地控制钢材的温度。
此外,水冷方法的操作也非常简单,易于实现自动化。
然而,水冷方法也存在一些局限性。
首先,它需要大量的水资源,因此在某些地区可能成本较高。
其次,水冷方法可能会导致钢材表面产生氧化铁皮,这可能会影响钢材的表面质量。
最后,水冷方法可能会使钢材产生裂纹,因此在某些情况下可能无法满足使用要求。
总的来说,水冷方法是一种有效的轧钢过程控冷方法,但它的局限性需要我们在使用时加以考虑。
目录(篇2)1.引言2.轧钢过程控冷的方法介绍3.传统轧钢过程控冷方法的不足4.热轧钢板的优点5.结论正文(篇2)一、引言轧钢是一种重要的金属加工过程,通过轧制将金属坯料加工成各种形状的金属制品。
在轧钢过程中,控冷是一种关键的技术,它能够控制金属的冷却速度,从而控制金属的微观结构和机械性能。
本文将介绍轧钢过程控冷的方法。
二、轧钢过程控冷的方法介绍轧钢过程控冷的方法有很多种,其中比较常用的有水冷、风冷、干冷等。
水冷和风冷都是通过强制对流来实现金属的冷却,而干冷则是通过辐射和对流传热来实现金属的冷却。
这些方法都有其优缺点,例如水冷和风冷成本较低,但冷却速度较慢;干冷冷却速度较快,但成本较高。
三、传统轧钢过程控冷方法的不足传统的轧钢过程控冷方法存在着一些不足,比如冷却速度慢、能源消耗大、环境污染严重等。
这些问题已经引起了人们的关注,因此需要寻找更加高效、环保的控冷方法。
影响高线产品冷镦性能轧钢因素的分析及控制

影响高线产品冷镦性能轧钢因素的分析及控制摘要:本文首先阐述了高线产品冷镦性能的影响因素,并重点探讨了高线冷镦钢产品顶锻开裂的控制措施。
关键词:高线;冷镦性能;因素;措施高线生产中,具体的影响因素会以不同形式影响产品冷镦性能,导致产品顶锻开裂。
为提高线材产品冷镦性能,需分析高线生产中具体影响因素的来源,并提出相应的控制措施。
一、高线产品冷镦性能的影响因素1、坯料表面缺陷1)坯料表面重皮。
钢锭浇注时,由于钢水的喷溅,铸锭表面会出现重皮。
经初轧开坯轧制,重皮更加隐蔽,很难找到,经酸洗后就会暴露出来。
在坯料表面未得到有效清理时,轧制后,重皮缺陷部分拉长,冷镦钢线材表面形成一个小而断续的裂纹源,影响产品冷镦性能。
2)坯料表面裂纹。
高速线材轧制可消除坯料表面在表面氧化及延伸作用下产生的细小裂纹;由于氧化层的存在,较大的裂纹无法通过压合消除,高线轧制后被拉长,残留在产品表面,冷镦钢线材表面形成细小且断续的裂纹,影响产品冷镦性能。
3)坯料表面尖锐过度。
例如,坯料表面重皮、裂纹等缺陷清理质量不高,造成坯料表面棱角锐利过度。
在高线轧制时,棱角会翻倒,由于热氧化层的存在,缺陷不能弥合并残留在冷镦钢制品表面,对产品的冷镦性能产生不利影响。
2、高线生产调整。
高线生产调整是影响产品冷镦性能的主要因素。
1)轧制压下量调整。
轧制过程中,若轧制压下量调整不当,轧件的延伸率分布不均匀,某道次压下量过大,造成过盈,轧件上会出现双侧耳子现象。
耳子经后续道次轧制后,成品上形成折叠,影响冷镦钢产品的冷镦性能。
冷顶锻检验中,缺陷表现为双侧对称通长纵裂或双侧对称断续微裂。
2)轧制中心线调整。
轧件上单侧耳子由轧件中心偏离轧制中心线或导卫偏离孔型引起。
在后续道次轧制后,耳子会在成品上发生折叠,从而影响线材产品冷镦性能。
冷顶锻检验时,缺陷为单侧通长纵向裂纹。
3)孔型轴向调整。
由于轧机轴向定位精度得不到保证或调整不当,导致轧件上的错辊压痕由错辊引起。
控制轧制于控制冷却

1、控制轧制:在热轧过程中,通过对金属加热制度、变形制度和温度制度的合理控制,使热塑性形变与固态相变相结合,以获得细小的晶粒组织,使钢材具有优异的综合力学性能的轧制技术2、控制冷却:通过对控制轧后的钢材的冷却速度来改善钢材的组织性能.3、金属的强化:通过合金化,塑性变形和热处理等手段来提高金属的强度。
4、固溶强化:添加溶质元素使固溶体强度提高的方法.5、韧性:材料在塑性变形和断裂所吸收能量的能力。
6、微合金钢:钢种的合金含量小于0.1%。
7、IF钢:无间隙原子钢8、不锈钢:具有良好的抗腐蚀性能和抗氧化性的钢.9、变形抗力:在一定条件下材料变形单位面积的抵抗变形的力.10、在线常化工艺:在热轧无缝钢管中在轧管延伸工序后将钢管按常化热处理要求冷却到某一温度后在进加热炉然后就行减径轧制按照一定的速度冷却到常温。
11、变形温度贝氏体处理化工艺:在钢管轧制过程中不直接加热到马氏体温度一下,而是快速冷却带中温以后再置于静止的空气中冷却、以变形奥氏体转变为贝氏体省去回火工序。
12、高温变形淬火:钢管在稳定的奥氏体区域变形,而且一般温度在再结晶温度以上然后进行淬火,已获得马氏体组织。
13、低温相变淬火:将钢管加热到奥氏体状态,经一段保温冷却到Ac1高于M的某一中间温度进行变形后淬火的工艺。
14、非调质钢:将调质钢的化学成分进行调解并对轧制过程进行控制不进行调制其性能达到调制的水平。
1、控制轧制是指在热轧过程中通过对金属加热制度,温度制度,保险制度的控制而获得细小的晶粒2、控制冷却是控制轧后钢材的冷却速度来改善组织性能。
3、钢材的强化方法有固溶强化,变形强化,沉淀强化,弥散强化,亚晶强化,细晶强化,相变强化。
4、影响材料韧性有,化学成分,气体和夹杂物,晶粒细化,形变的影响,形变细化5、动态结晶是晶粒细化提高扩孔性的手段6、控制轧制的目标是为了获得较小的铁素体组织7、加快冷却速度可以获得细小的铁素体晶粒所以不产生奥氏体组织为界限8、贝氏体是结构性能钢有校坏的塑形焊接性能强韧性微合金钢是指钢中的合金元素总量小于0。
高速线材轧后控制冷却工艺分析
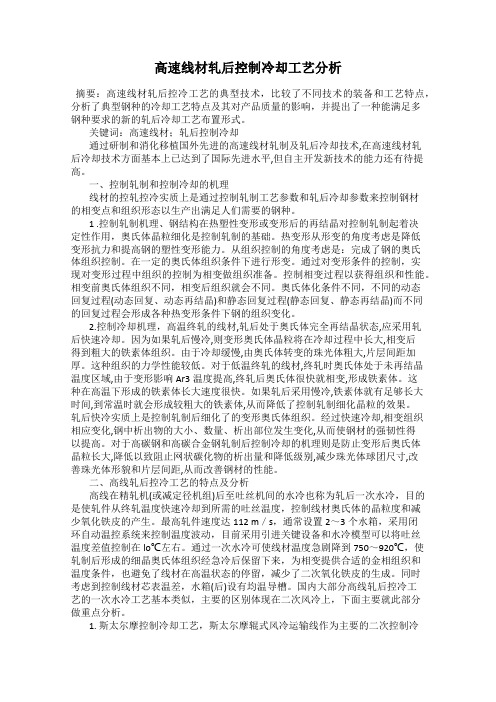
高速线材轧后控制冷却工艺分析摘要:高速线材轧后控冷工艺的典型技术,比较了不同技术的装备和工艺特点,分析了典型钢种的冷却工艺特点及其对产品质量的影响,并提出了一种能满足多钢种要求的新的轧后冷却工艺布置形式。
关键词:高速线材;轧后控制冷却通过研制和消化移植国外先进的高速线材轧制及轧后冷却技术,在高速线材轧后冷却技术方面基本上已达到了国际先进水平,但自主开发新技术的能力还有待提高。
一、控制轧制和控制冷却的机理线材的控轧控冷实质上是通过控制轧制工艺参数和轧后冷却参数来控制钢材的相变点和组织形态以生产出满足人们需要的钢种。
1 .控制轧制机理、钢结构在热塑性变形或变形后的再结晶对控制轧制起着决定性作用,奥氏体晶粒细化是控制轧制的基础。
热变形从形变的角度考虑是降低变形抗力和提高钢的塑性变形能力。
从组织控制的角度考虑是:完成了钢的奥氏体组织控制。
在一定的奥氏体组织条件下进行形变。
通过对变形条件的控制,实现对变形过程中组织的控制为相变做组织准备。
控制相变过程以获得组织和性能。
相变前奥氏体组织不同,相变后组织就会不同。
奥氏体化条件不同,不同的动态回复过程(动态回复、动态再结晶)和静态回复过程(静态回复、静态再结晶)而不同的回复过程会形成各种热变形条件下钢的组织变化。
2.控制冷却机理,高温终轧的线材,轧后处于奥氏体完全再结晶状态,应采用轧后快速冷却。
因为如果轧后慢冷,则变形奥氏体晶粒将在冷却过程中长大,相变后得到粗大的铁素体组织。
由于冷却缓慢,由奥氏体转变的珠光体粗大,片层间距加厚。
这种组织的力学性能较低。
对于低温终轧的线材,终轧时奥氏体处于未再结晶温度区域,由于变形影响Ar3温度提高,终轧后奥氏体很快就相变,形成铁素体。
这种在高温下形成的铁素体长大速度很快。
如果轧后采用慢冷,铁素体就有足够长大时间,到常温时就会形成较粗大的铁素体,从而降低了控制轧制细化晶粒的效果。
轧后快冷实质上是控制轧制后细化了的变形奥氏体组织。
经过快速冷却,相变组织相应变化,钢中析出物的大小、数量、析出部位发生变化,从而使钢材的强韧性得以提高。
棒线材控制轧制和控制冷却技术的研究及应用
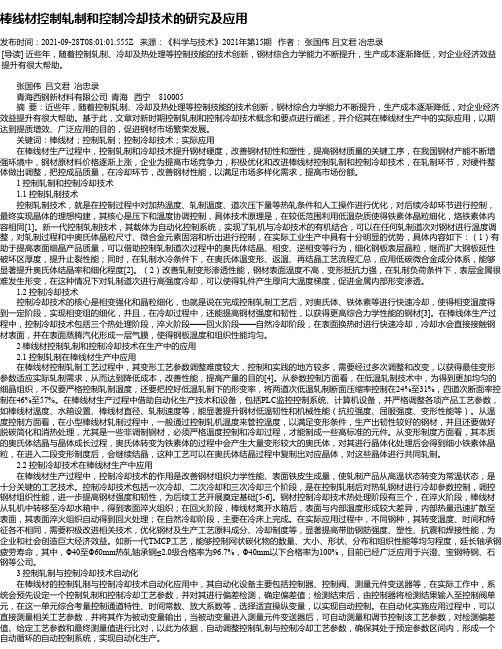
棒线材控制轧制和控制冷却技术的研究及应用发布时间:2021-09-28T08:01:01.555Z 来源:《科学与技术》2021年第15期作者:张国伟吕文君冶忠录[导读] 近些年,随着控制轧制、冷却及热处理等控制技能的技术创新,钢材综合力学能力不断提升,生产成本逐渐降低,对企业经济效益提升有很大帮助。
张国伟吕文君冶忠录青海西钢新材料有限公司青海西宁 810005摘要:近些年,随着控制轧制、冷却及热处理等控制技能的技术创新,钢材综合力学能力不断提升,生产成本逐渐降低,对企业经济效益提升有很大帮助。
基于此,文章对新时期控制轧制和控制冷却技术概念和要点进行阐述,并介绍其在棒线材生产中的实际应用,以期达到提质增效、广泛应用的目的,促进钢材市场繁荣发展。
关键词:棒线材;控制轧制;控制冷却技术;实际应用在棒线材生产过程中,控制轧制和冷却技术提升钢材硬度,改善钢材韧性和塑性,提高钢材质量的关键工序,在我国钢材产能不断增强环境中,钢材原材料价格逐渐上涨,企业为提高市场竞争力,积极优化和改进棒线材控制轧制和控制冷却技术,在轧制环节,对硬件整体做出调整,把控成品质量,在冷却环节,改善钢材性能,以满足市场多样化需求,提高市场份额。
1 控制轧制和控制冷却技术1.1 控制轧制技术控制轧制技术,就是在控制过程中对加热温度、轧制温度、道次压下量等热轧条件和人工操作进行优化,对后续冷却环节进行控制,最终实现晶体的理想构建,其核心是压下和温度协调控制,具体技术原理是,在较低范围利用低温杂质使得铁素体晶粒细化,烙铁素体内容相同[1]。
新一代控制轧制技术,其载体为自动化控制系统,实现了轧机与冷却技术的有机结合,可以在任何轧制道次对钢材进行温度调整,对轧制过程和中奥氏体晶粒尺寸、微合金元素固溶和析出进行控制,在实际工业生产中具有十分明显的优势,具体内容如下:(1)有助于提高表面细晶产品质量,可以借助控制轧制道次过程中的奥氏体结晶、相变、逆相变等行为,细化钢板表层晶粒,继而扩大钢板延性破坏区厚度,提升止裂性能;同时,在轧制水冷条件下,在奥氏体温变形、返温、再结晶工艺流程汇总,应用低碳微合金成分体系,能够显著提升奥氏体结晶率和细化程度[2]。
对高速线材生产中控轧控冷的分析

对高速线材生产中控轧控冷的分析摘要:线材在轻重工业产业中占有重要的地位,高速线材是轧钢中的一类,对高速线材的生产设备及生产工艺进行研究和设计,对现代钢铁工业的发展和需求有着战略性意义。
关键词:高速线材;加热温度;控轧控冷;我国新型工业化的发展,钢铁材料产业充当着非常重要的地位,线材生产是钢铁轧制生产的一项重要内容,线材产品的质量和性能与其生产设备和生产工艺有着密切的关系,其中控制轧制和控制冷却技术对高速线材生产有着较大的影响。
轧机的设备组成不同,生产工艺的不同,其产出的线材性能也就不同。
一、控轧控冷技术的研究现状我国在线材生产过程中,控轧控冷技术有着非常重要的作用,钢材强度、韧度等性能是通过添加一些添加剂在一定温度下控制得到的。
将钢材中奥氏体向铁素体发生转变,使钢材的组织发生大规模的相变,从而使强度发生大幅度的变化。
而控制轧制就是通过控制热轧钢材时的温度和压力等条件达到最佳值,从而热轧钢材省略热处理的过程并且能达到与正火相同的组织结构。
因此轧制钢材可以通过强化压下和控制冷却等技术来提高钢材的性能,达到或超过有热处理钢材的性能。
控制冷却就是指在控制轧制后,为了弥补单一控制技术不能使相变组织细微化的不足,在奥氏体向铁素体相变的温度区域进行某种程度快速冷却,以此获得更高的强度。
为了获得所需要的组织和性能,可以利用控制轧制过程中线材热轧后的余热,用一定的生产工艺控制线材的冷却速度。
我国的轧制工艺有很大进步和发展,但是高速线材生产中控轧控冷技术的改进、完善、提高、更专业提出了更高的要求。
当今的高线厂生产中设备及工艺存在着很多问题,钢材的产量低,钢材性能差,合格率不到95%。
二、控制轧制控制轧制广义地解释为从轧前的加热到最终轧制道次为止的整个轧制过程的控制,即通过全部热轧条件的最优化,人为地调整奥氏体的状态,使其在后续的冷却过程中相变为期望的细晶组织,以得到良好的强度和韧性的加工过程,其操作如图1所示。
图1各种轧制程序的模式线材的控制轧制可以减少脱碳,控制晶粒尺寸,改善钢的冷变形性能,控制抗拉强度及显微组织,取消热处理,减少氧化铁皮。
高速线材生产中的控轧控冷技术探究
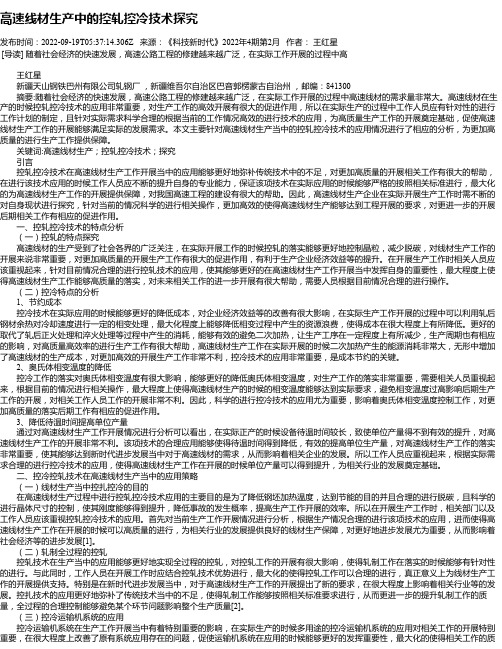
高速线材生产中的控轧控冷技术探究发布时间:2022-09-19T05:37:14.306Z 来源:《科技新时代》2022年4期第2月作者:王红星[导读] 随着社会经济的快速发展,高速公路工程的修建越来越广泛,在实际工作开展的过程中高王红星新疆天山钢铁巴州有限公司轧钢厂,新疆维吾尔自治区巴音郭楞蒙古自治州,邮编:841300摘要:随着社会经济的快速发展,高速公路工程的修建越来越广泛,在实际工作开展的过程中高速线材的需求量非常大。
高速线材在生产的时候控轧控冷技术的应用非常重要,对生产工作的高效开展有很大的促进作用,所以在实际生产的过程中工作人员应有针对性的进行工作计划的制定,且针对实际需求科学合理的根据当前的工作情况高效的进行技术的应用,为高质量生产工作的开展奠定基础,促使高速线材生产工作的开展能够满足实际的发展需求。
本文主要针对高速线材生产当中的控轧控冷技术的应用情况进行了相应的分析,为更加高质量的进行生产工作提供保障。
关键词:高速线材生产;控轧控冷技术;探究引言控轧控冷技术在高速线材生产工作开展当中的应用能够更好地弥补传统技术中的不足,对更加高质量的开展相关工作有很大的帮助,在进行该技术应用的时候工作人员应不断的提升自身的专业能力,保证该项技术在实际应用的时候能够严格的按照相关标准进行,最大化的为高速线材生产工作的开展提供保障,对我国高速工程的建设有很大的帮助。
因此,高速线材生产企业在实际开展生产工作时需不断的对自身现状进行探究,针对当前的情况科学的进行相关操作,更加高效的使得高速线材生产能够达到工程开展的要求,对更进一步的开展后期相关工作有相应的促进作用。
一、控轧控冷技术的特点分析(一)控轧的特点探究高速线材的生产受到了社会各界的广泛关注,在实际开展工作的时候控轧的落实能够更好地控制晶粒,减少脱碳,对线材生产工作的开展来说非常重要,对更加高质量的开展生产工作有很大的促进作用,有利于生产企业经济效益等的提升。
控轧空冷综述

控轧控冷在棒线材中的应用班级:摘要:线材为了获得高强度、高韧性的综合性能, 可以采用不同的控制轧制工艺来达到。
关键词:控轧空冷应用线材前言控制轧制和控制冷却技术作为提高产品的组织性能,降低钢材生产成本,提高企业经济效益上起着巨大的作用。
正文一.控轧控冷概述1.控轧控冷概念(1)控制轧制:在热轧过程中,通过对金属加热制度、变形制度和温度制度的合理控制,使热塑性变形与固态相变相结合,以获得细小晶粒组织,从而得到较高的综合性能的轧制工艺。
(2)控制冷却:控制轧后钢材的冷却速度达到改善钢材组织和性能的目的。
2.控制轧制的优点如下:(1)可以在提高钢材强度的同时提高钢材的低温韧性。
(2)可以充分发挥铌、钒、钛等微量元素的作用。
3.控制轧制工艺的缺点:(1)要求较低的轧制变形温度和一定的道次压下率,因此增大了轧制负荷。
(2)由于要求较低的终轧温度,大规格产品需要在轧制道次之间待温,降低轧机生产率。
4.控制冷却工艺的优点(1)节约能耗、降低生产成本。
利用轧后钢材余热,给予一定的冷却速度控制其相变过程,从而可以取代轧后正火处理和淬火加回火处理,节省了二次加热的能耗,减少了工序,缩短了生产周期,从而降低了生产成本。
(2)可以降低奥氏体相变温度,细化室温组织。
轧后控制冷却能够降低奥氏体相变温度,对同一晶粒度级别的奥氏体,低温相变后会使,晶粒明显细化,使珠光体片层间隔明显变薄。
(3)可以降低钢的碳当量。
采用轧后控制冷却工艺有可能减少钢中的碳含量及合金元素加入量,达到降低碳当量的效果。
(4)道次间控制冷却可以减少待温时间,提高轧机小时产量。
在道次间采用控制冷却,可以精确地控制终轧温度,减少轧件停下来等待降温的时间。
5.控制轧制、控制冷却工艺参数控制特点(1)控制钢坯加热温度。
根据对钢材性能的要求来确定钢坯加热温度,对于要求强度高而韧性可以稍差的微合金钢,加热温度可以高于1200℃,对以韧性为主要性能指标的钢材,则必须控制其加热温度在1150 ℃以下。
- 1、下载文档前请自行甄别文档内容的完整性,平台不提供额外的编辑、内容补充、找答案等附加服务。
- 2、"仅部分预览"的文档,不可在线预览部分如存在完整性等问题,可反馈申请退款(可完整预览的文档不适用该条件!)。
- 3、如文档侵犯您的权益,请联系客服反馈,我们会尽快为您处理(人工客服工作时间:9:00-18:30)。
对高速线材生产中控轧控冷的分析对高速线材生产中控轧控冷的分析高速线材厂焦银摘要:阐述了控冷控轧的原理,分析了高速线材轧制中的加热温度控制、轧前水冷、精轧机内水冷、精轧机组后水冷、风冷线温控等参数的确定依据。
关键词:高速线材;加热温度;控轧控冷ANALYSIS OF CONTROLLED ROLLING AND CONTROLLEDCOOLING IN HIGH一SPEED W1RE PRODUCTION Abstract: The principle of controlled rolling and controlled cooling is stated. It is analyzed how to determine the parameters in high--speed wire rolling such as heating temperature control water cooling before rolling water cooling in finishing rolling mill water cooling behind finishing rolling set and temperature control on wind cooling line. Keywords: high--speed wire production heating temperature control rolling and control cooling.1.前言自21世纪80年代以来,高速线材的轧制速度己突破100m/s,由于轧制速度的提高,导致轧件的温升增加,使终轧温度高于1000℃,线材成品表面的氧化铁皮增多、晶粒粗大、钢材的显微组织和机械性能极不均匀。
控制轧制中水冷和轧后的散卷冷却,以便得到组织性能良好的线材;保证轧件的轧制温度,控冷控轧就显得至关重要,因此,合适的控轧控冷参数是轧制生产线水平高低的重要标志之一。
2控轧控冷参数的确定控制轧制分为以下几个阶段:加热温度控制,精轧前水冷控制,精轧后水冷控制,精轧机组间水冷控制,吐丝温度控制,风冷线的温度控制。
( 1)加热温度的控制。
目前,装备水平较高的高线生产厂己普遍采用了控制轧制技术,为了达到控轧的目的从钢坯出炉就开始控制温度,要求钢坯的加热温度低于常温轧制时的温度,这既能够保证最终产品的质量,同时又能降低钢坯表面的脱碳,节约燃料,降低钢材的生产成木。
青岛钢铁集团的高速线材生产线,其中碳素钢比例较大,加热炉选用步进梁式加热炉,其加热功能完全能满足各钢种的温度要求,经对比分析确定各钢种的开轧温度为:碳素结构钢:940士20℃高碳钢:950士20℃合金结构钢:940士20℃冷墩钢:940士20℃焊条钢:940士20℃弹簧钢:950士20℃轴承钢:950士20℃螺纹钢:950士20℃同时要求钢坯出炉温度均匀,断面温差小于30℃,为缩小轧制过程中钢坯长度方向的温差,钢坯加热时,距头部和尾部2m范围内的温度应高于中间部分30℃。
(2)轧前水冷。
为了控制进入精轧机的轧件温度,在无扭精轧机组前增设水冷箱,降低轧件温度以达到控制轧制的目的。
通过控制水箱内水冷喷嘴的开启度和开启数量,轧件经过水冷箱温降可下降100- 150℃,然后经过一个温度恢复段,使轧件的芯表温度均匀,温差控制在士30℃左右,不影响下一道次的轧制。
青岛钢铁集团高速线材厂经过理论计算和对各高线厂的实际考察设计水冷参数如下:精轧前水箱长度(2组) ,4.7m和3.4m,恢复段长度6.415m和7.445m,正向水冷喷嘴水压500KPa,反向水冷喷嘴水压600 KPa。
( 3)精轧机组内水冷。
为了防止因精轧机组轧制速度高引起的轧件温升,在精轧机组的机架间增设了水冷装置;为了保证轧件的冷却均匀,水冷装置设在轧件圆到椭圆机架间;为达到水冷效果各高线轧机生产厂家都增大了机组间距(900--1200mm ),其目的是经过机组间的水冷使轧件的温升得以控制,杜绝因轧制温度过高形成的轧件晶粒粗大面引起线材性能下降的缺点。
水冷管的水压应与水冷箱的一致J并同为一闭环温度控制系统,以达到操作简一、有效的目的。
( 4)精轧机组后的水冷。
精轧后水冷是为了控制合适的吐丝温度,控制线材的晶粒度和减少氧化铁皮层。
经过理论分析和实践表明,线材在900℃以下精轧时晶粒度较细,但没有水冷控制的轧制温度在1000℃以上,在此条件下晶粒非常容易发生再结晶和晶粒长大,所以在精轧机出口布置水冷箱,对热轧后的线材进行快速冷却能够阻止奥氏体晶粒长大并控制其晶粒度,从面改变成品线材的组织得到满足用户要求的产品。
线材在水冷段快速冷却到接近A3温度,可以得到细小的奥氏体晶粒,但同时水冷速度不能过快,否则温度降到600℃以下形成表面马氏体或贝氏体组织,线材的性能无法保证。
所以要严格控制水冷箱中水冷喷嘴的开启度。
为了使线材均温,冷却应是间断性的,以便于中心的热量向表面扩散。
根据D. Lews的理论,线材芯部与表面温差的恢复时间比接近1:4,即经过恢复段的时间约为经过水冷段时间的4倍,这就意味着恢复段的长度最少应为水冷长度的4倍以上。
但青岛钢铁集团高速线材厂因受场地条件的限制,很难提供充分的距离只能尽量让间距大些,所设计的精轧机后水冷参数为:水冷箱长度分别为4.7m和3.4m,恢复段长度4.99m和24.12m,水箱最大温降250℃。
(5)TMB轧机后的水冷吐丝温度对钢材性能影响很大。
斯太尔摩控制冷却的生产经验表明,按照美国A1S1标准分类的低碳钢和中碳钢,在保持其它条件不变的前提下,吐丝温度越高,线材的抗拉强度越低,一般控制在870- 900℃。
为了保证线材性能均匀,一般要求将吐丝温度严格控制在规定范围内,允许波动一般约为士10℃相变区的冷却速度决定了奥氏体的分解转变温度和时间,它对线材的最终组织形态起决定作用。
对于低碳钢线材主要是以铁素体组织为主,从铁碳相图中可看出,在723℃时,在a铁中碳按重量计算,最大溶解度为0.020﹪。
从终轧温度开始急冷将使碳过饱和地溶于铁素体中。
由于总的含碳量低于0.10﹪,几乎不可能形成珠光体。
过剩的碳在铁素体中以二种形式存在,即间隙固溶体、在位错而沉淀和在铁素体中呈弥散沉淀。
后两种形式经常同时发生。
在这种情况下,在位错处引起碳从位错附近的铁素体中析出,从而泞致在区域中形成纯铁素体。
在很弱的冷变形时,由于碳在位错上沉淀时产生位错锚定作用,从而降低了拉拔效率,不利于拉拔,为了防止产生这种锚定作用,提高拉拔效率,要使碳在300℃左右迅速形成稳定碳化物,这样可以得到片状渗碳体沉淀组织。
低碳钢轧后快冷到700℃以下生成的氧化铁皮量大大减少,快冷之后空冷到400- 350℃,在之间保持一定时间约1- 2min',形成稳定而均匀的片状渗碳体。
轧后山于快冷,生成的氧化铁皮以Feo为主。
Fe203只有在700℃以下慢冷时(冷却速度小于40℃/min)才产生。
因此线材在700- 400℃度区间不应采用缓冷,而应保持一定的冷却速度。
在散卷空冷条件下,冷却速度可以达到大于6℃/s。
线材温度低于400℃后采用慢冷。
终轧温度为1040- 1080℃的线材离开轧机后在水冷区立即被急冷到900- 1050,水冷时间控制在0.6s,水冷后温度较高目的是防止线材表而出现淬火组织。
在水冷区控制冷却的目的在于延迟晶粒长大,限制氧化铁皮形成并冷却到接近但又明显高于相变温度的温度。
现在的高速线材厂,一般再精轧机组后设置TMB模块,以提高产品的精度,可以生产帘线钢、胎圈钢丝、钢绞线等产品,在青岛钢铁集团高速线材厂的设计中,再TMB后面设置了第五个水箱,水箱长度3.4m,恢复段长度2.495m,冷却水压力500KPa。
控制终轧温度主要是控制奥氏体晶粒尺寸,一般终轧温度高时,晶粒大。
对于主要用于生产拉拔等用途的低碳软钢、碳素焊条钢等,要求得到低强度、高塑性的粗铁素体组织,终轧温度可相应提高到980-1050℃。
整个轧线的水冷应能通过闭环温度控制系统实现,该控制系统的温度精度要求士5℃,以达到实际轧件温度与理论温度的极度接近,最大限度地实现轧件的温度控制。
图1轧件通过水冷箱时表面和中心的冷却曲线( 5)风冷线温控。
其目的是进行奥氏体相变控制,得到满足用户的要求的线材性能。
根据不同钢种采用延迟型或标准型冷却两种方式。
高速线材厂产品大纲中轴承钢对风冷线长度要求最严格,风冷线应按轴承钢的冷却设计,风冷线长度与终轧速度之比应不小于1:1,轧线设计速度为l15m/s风冷线长度应在116 m左右。
具体设计参数为:运输机分为20段,保温罩27组、风机21台。
运输机速度:标准冷却速度为:0. 55- 1.5 m/s延迟冷却速度为:0.05一0.33m/s.运输机各段的速度可调以控制线圈间隔;同时可使线圈的搭接点改变,避免形成热点,提高线材冷却的均匀性。
通过全过程的轧制控制,能最大程度地满足用户对线材的质量要求。
3结语控制冷却和控制轧制技术的发展己成为现代高速线材轧机必备的手段,所以在项目设计阶段应充分考虑产品特点,采用理论与实际相结合的方法,做出详尽的设计,确保水冷装置可靠使用,从面达到控制轧制的目的。
参考文献:【1】崔忠圻钢铁热处理上海: 上海科技出版社 1979【2】李曼云钢的控制轧制和控制冷却技术手册北京冶金工业出版社 1998 【3】乔德庸高速轧机线材生产冶金工业出版社 1995【4】周建男钢铁生产工艺装备新技术冶金工业出版社 2004【5】日本钢铁协会轧制理论及其应用 1975。