加工高酸值原油的方法及防腐措施
高酸原油加工防腐蚀技术(山东讲课)
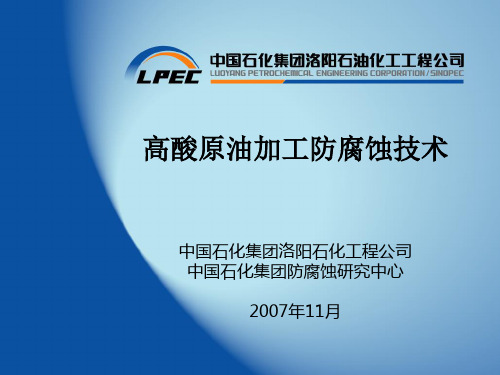
辽河原油
渤海锦州 9-3
喀麦隆 Lokele
巴西 Marlim
乍得 Doba
蜡含量, %
6.0
7.5
4.30
1.55
2.92
-
胶质+沥青质, % 17.7 12.58 18.54 18.16 12.50 16.98
22.8
硫含量 %
0.32 0.131 0.20
0.27
0.42
0.68
0.16
氮含量 %
18
加工高酸原油的 主要腐蚀
19
三、加工高酸原油的主要腐蚀
在加工过程中的腐蚀突出表现在以下几个方面: 1)酸值高,存在严重的高温环烷酸腐蚀; 2)电脱盐难度增加,低温部位腐蚀程度增加; 3)原油中氮含量高,在加工过程中形成含氮腐 蚀介质; 4)高酸原油的盐含量高,重金属含量高,尤其 是金属钙、镍的含量高,容易引起二次加工装置的 催化剂中毒、催化剂床层堵塞以及高温换热器等结 垢、结焦。
汽油酸度
煤油酸度
柴油酸度 蜡油酸值 渣油酸值
mgKOH/100ml mgKOH/100ml mgKOH/100ml mgKOH/g mgKOH/g
3.95
8.28
127.4
5.67
0.80
6.98
61.1
126.6
2.93
6.65
88.25
3.33
153.44
12.98
36.00
9.92
9.40
152.3
23
温度
环烷酸腐蚀受温度的影响比较大,在200℃以下环烷酸 对设备几乎不造成腐蚀,而当温度升高至200℃以上时,随 着温度升高腐蚀逐渐加剧。
Gutzeide等人的实验表明:温度每升高55℃,碳钢和低 合金钢腐蚀速度增加2倍。
加工高硫高酸原油注意事项

加工高硫、高酸原油注意事项常减压装置单独加工马瑞油,硫含量高达2.9%并含有硫化氢,给储运、装置加工带来很大安全隐患,并且严重影响产品质量,各生产环节要注意防止硫化氢中毒,装置要24小时不间断巡检。
对加工高硫、高酸原油安全注意事项重申如下:高硫高酸原油对装置的影响:高硫、高酸原油中的比重大、硫含量和重金属含量高,深度脱盐较为困难。
加工这类原油能够造成设备腐和催化剂中毒以及环境污染。
如电脱盐装置会因原油乳化而影响脱盐效果,从而造成分馏塔顶腐性,还会造成分馏塔、加热炉等设备高温部位的腐蚀。
加工高酸原油带来的腐性问题主要集中在蒸馏装置,而加工高硫原油带来的腐性问题,贯穿于整个原油加工过程中。
高温硫化物的腐性是指240℃以上的部位元素硫、硫化氢和硫醇等形成的腐蚀。
典型的高温硫化物腐蚀存在于常、减压塔的下部及塔底管线,常压渣油和减压渣油换热器,催化裂化装置分馏塔的下部,以及焦化装置高温部位等。
在高温条件下,活性硫与金属直接反应它出现在与物流接触的各个部位,表现为均匀腐性,其中以硫化氢的腐位性最强。
燃料重油中通常含有1%-3%的硫及硫化物,在燃烧中大部分生成SO2,其中约有1%-5%在一定条件下反应生成SO3,对设备几乎不发生腐性,但当它与烟气中的水蒸汽结合形成硫酸蒸汽时,在装置的落点部位发生凝结,严重腐蚀设备。
环烷酸腐蚀经常发生在酸值大于0.5mgKOH/g, 温度在270-400℃之间高流速介质中。
它与金属表面或硫化铁膜直接反应生成环烷酸铁,环烷酸铁是油溶性的,再加上介质的流动,使金属表面不断暴露并受到腐性,故环烷酸腐蚀的金属表面清洁,光滑无垢。
在物料的高温高流速区域,环烷酸腐呈顺流向产生的尖锐边缘的流线沟槽,在低流速区域,则呈边缘锐利的凹坑状。
环烷酸腐蚀都发生在塔盘、塔壁、转油线等部位。
另外由于环烷酸盐具有表面活性,会造成油品乳化,从而引起装置操作波动,并造成塔顶腐蚀。
装置在加工此类原油时要做好安全防范措施并从生产工艺上进行调整,保证产品质量合格和污水处理合格。
加工含硫含酸原油的腐蚀与控制
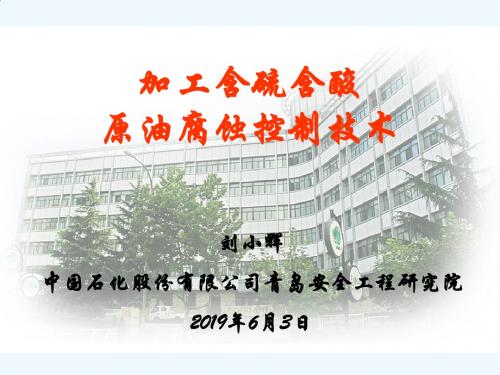
二、劣质原油加工技术现状及发展趋势
美国腐蚀工程师协会NACE颁布了很多关于炼 厂硫腐蚀防护方面的标准和实践指南。其第八技 术组(炼厂腐蚀委员会,NACE T-8 Group)发表 了很多专业论文,对腐蚀机理进行研究以及防腐 蚀工程应用进行总结。一些研究机构和公司在缓 蚀剂、材质表面改性、涂层防护以及腐蚀监检测 等方面开展了研究和应用。
二、劣质原油加工技术现状及发展趋势
2009年下半年平均加工利润排序已变为: 高硫>低硫>含硫>含酸,含酸原油的加工效 益已从 4月份排第一位,退至最后末位。
二、劣质原油加工技术现状及发展趋势
高酸原油加工的防腐和工艺技术近年来已得到 长足进步。中国石化对高酸原油加工起步较早,有 一定的技术和市场优势。但由于包括中国在内的高 酸原油加工能力提升迅猛,使得国际市场上出现了 相互争夺高酸原油现货资源的状况,从而使得加工 高酸原油的盈利空间受到限制。与其它品种进口原 油的毛利差大大缩小,甚至更差,这一状况可能随 油价涨跌有所变化,但高酸原油加工的暴利时代可 能已经过去。
二、劣质原油加工技术现状及发展趋势
2008年12月26日印度信赖公司位于印度古 吉拉特邦(Gujarat)的贾姆纳格尔(Jamnagar) 炼厂 2期开车,已于今年 3月中旬投入正常运 营。
二、劣质原油加工技术现状及发展趋势
据了解,该装置一次加工能力为 58万桶/日(约 3000万吨/年),设计标准为加工 API度为 24的 重质中间基原油,具有良好的加工适应性和灵活 性,可以加工来自美洲委内瑞拉、墨西哥和中东 等地区的重质高硫高酸原油,其中中东约占总进 口量的55%,其他地区大约占45%。其它地区的原 油油种主要包括西非的奎都、达丽亚、扎菲若, 苏丹的达混合油以及巴西的马林、阿尔巴克拉原 油等。
加工高酸原油的防腐措施探讨
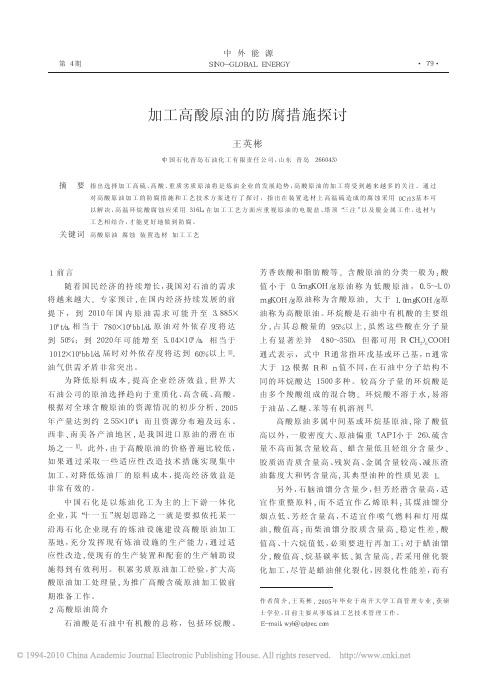
2RCOOH+FeS→Fe(OOCR)2+H2S 环烷酸铁破坏了硫化亚铁保护膜, 引起了设备 的腐蚀。 3.3 高酸原油加工防腐对策 3.3.1 装置选材 根据目前掌握的环烷酸原油性质, 原油中所含 的 石 油 酸 向 重 组 分 发 展 , 例 如 蓬 莱 19- 3 油 田 原 油 : 320  ̄350℃馏 分 酸 度 值 达 到 6.802, 350  ̄370℃馏 分 酸 度 值 为 7.66, 370 ̄395℃馏 分 酸 度 值 为 9.32, 395 ̄ 425℃馏 分 酸 度 值 更 是 高 达 9.52, 560℃以 上 馏 分 酸 度 值 为 8.52, 所 含 的 石 油 酸 占 全 部 原 油 所 含 石 油 酸 的 48%[3]。 因 此 , 重 质 环 烷 酸 原 油 加 工 过 程 中 受 到 环烷酸腐蚀威胁的装置远远超出了以前高酸原油 加工过程中腐蚀的范围, 这就要求加工环烷酸原油 炼油厂装置选材时, 必须结合这些情况, 统一考虑, 控制腐蚀的发生。另外, 环烷酸原油一般氮含量较 高 , 催 化 裂 化 装 置 吸 收 解 吸 系 统 低 温 H2S- HCN- H2O 型 腐 蚀 问 题 , 以 及 催 化 裂 化 再 生 器 、三 旋 等 设 备 防 止 NOx- H2S- H2O 型 腐 蚀 体 系 造 成 的 腐 蚀 开 裂 问题在装置选材时也要做好周到考虑。 S- H2S- RSH - RCOOH 型 腐 蚀 的 影 响 因 素 除 去 环 烷 酸 浓 度 ( 酸 值 大 于 0.5mgKOH/g) 和 温 度 (270  ̄ 280℃和 350 ̄400℃两 个 范 围 )外 , 还 受 流 速 的 影 响 。 环烷酸的腐蚀部位都集中在流速高的地方, 流速增 加, 腐蚀速率也增加。 环烷酸形成可溶性的腐蚀产物, 硫化氢则形成 不溶性的腐蚀产物。当两者腐蚀作用同时进行, 如 果含硫量低于某临界值, 则腐蚀程度加重, 即环烷 酸破坏了硫化物腐蚀产生的硫化亚铁保护膜, 生成
高酸原油加工的腐蚀与防护

高酸原油加工的腐蚀与防护引言随着原油资源的日益紧缺,高酸原油的加工及利用已成为当前炼油行业的一项重要工作。
然而,高酸原油会对加工设备产生腐蚀,从而对生产带来不利影响。
本文将探讨高酸原油加工过程中的腐蚀问题及其防护方法。
高酸原油的定义高酸原油是指含有较高酸值的原油。
一般来说,酸值越高,腐蚀性就越大。
在高酸原油中,主要的酸类成分是硫酸、硝酸、有机酸等。
此外,含有杂质和硫化物的原油也具有较高的腐蚀性。
高酸原油加工中的腐蚀问题由于高酸原油具有较强的酸性,其在加工中会对设备和管线产生严重的腐蚀问题,导致设备寿命缩短、性能下降、安全隐患增加等问题。
腐蚀类型高酸原油加工中常见的腐蚀类型如下:•粘附腐蚀:高酸原油中的酸类成分会粘附到金属表面上,形成一层薄膜,这层薄膜中的有机物和金属中的氧发生反应,从而引发腐蚀。
•晶间腐蚀:高酸原油中的酸性物质会促进晶间腐蚀的发生,从而使设备和管道产生脆化和断裂。
•点蚀腐蚀:高酸原油中的杂质和硫化物等物质会形成点蚀,从而导致设备表面出现小孔和凸起。
腐蚀影响高酸原油加工过程中的腐蚀问题会对设备和管线的使用寿命和性能造成不良的影响,具体表现如下:•设备寿命缩短:高酸原油加工对设备产生的腐蚀作用会导致设备寿命缩短,从而增加了生产成本。
•性能下降:高酸原油加工对设备的腐蚀作用会导致设备的性能下降,生产效率降低。
•安全隐患:高酸原油加工过程中,管道和设备的腐蚀会导致破裂和泄漏,可能会产生严重的安全隐患。
防腐保护技术在高酸原油加工中,防腐保护技术的应用非常重要。
以下是一些有效的防腐保护技术。
1. 涂层技术针对高酸原油的腐蚀问题,涂层技术是一种重要的防护方法。
所选涂层应具有耐酸蚀、耐磨损、耐高温等特点,并需经过专业检测。
将这些涂层应用于设备和管道表面,则能有效地防止高酸原油产生腐蚀作用。
2. 材料选择正确认识原油的酸性,根据酸值和组成选择适合的材料,如含锆或钛的合金结构,操作期间需要引起关注。
炼油厂加工高硫高酸值原油遇到的问题及对策
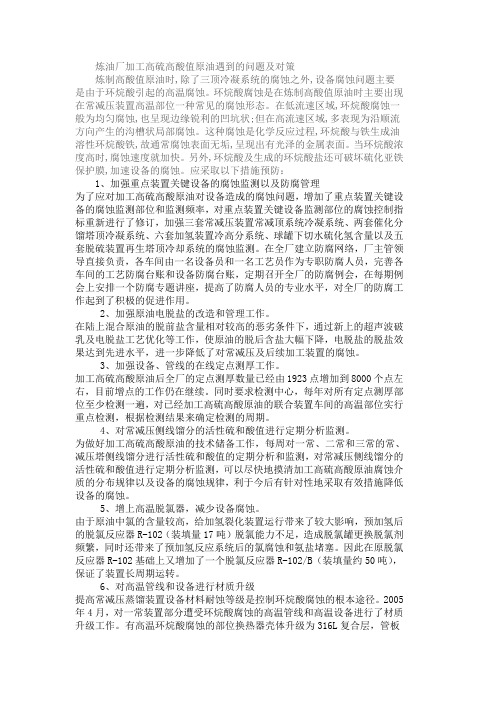
炼油厂加工高硫高酸值原油遇到的问题及对策炼制高酸值原油时,除了三顶冷凝系统的腐蚀之外,设备腐蚀问题主要是由于环烷酸引起的高温腐蚀。
环烷酸腐蚀是在炼制高酸值原油时主要出现在常减压装置高温部位一种常见的腐蚀形态。
在低流速区域,环烷酸腐蚀一般为均匀腐蚀,也呈现边缘锐利的凹坑状;但在高流速区域,多表现为沿顺流方向产生的沟槽状局部腐蚀。
这种腐蚀是化学反应过程,环烷酸与铁生成油溶性环烷酸铁,故通常腐蚀表面无垢,呈现出有光泽的金属表面。
当环烷酸浓度高时,腐蚀速度就加快。
另外,环烷酸及生成的环烷酸盐还可破坏硫化亚铁保护膜,加速设备的腐蚀。
应采取以下措施预防:1、加强重点装置关键设备的腐蚀监测以及防腐管理为了应对加工高硫高酸原油对设备造成的腐蚀问题,增加了重点装置关键设备的腐蚀监测部位和监测频率,对重点装置关键设备监测部位的腐蚀控制指标重新进行了修订,加强三套常减压装置常减顶系统冷凝系统、两套催化分馏塔顶冷凝系统、六套加氢装置冷高分系统、球罐下切水硫化氢含量以及五套脱硫装置再生塔顶冷却系统的腐蚀监测。
在全厂建立防腐网络,厂主管领导直接负责,各车间由一名设备员和一名工艺员作为专职防腐人员,完善各车间的工艺防腐台账和设备防腐台账,定期召开全厂的防腐例会,在每期例会上安排一个防腐专题讲座,提高了防腐人员的专业水平,对全厂的防腐工作起到了积极的促进作用。
2、加强原油电脱盐的改造和管理工作。
在陆上混合原油的脱前盐含量相对较高的恶劣条件下,通过新上的超声波破乳及电脱盐工艺优化等工作,使原油的脱后含盐大幅下降,电脱盐的脱盐效果达到先进水平,进一步降低了对常减压及后续加工装置的腐蚀。
3、加强设备、管线的在线定点测厚工作。
加工高硫高酸原油后全厂的定点测厚数量已经由1923点增加到8000个点左右,目前增点的工作仍在继续。
同时要求检测中心,每年对所有定点测厚部位至少检测一遍,对已经加工高硫高酸原油的联合装置车间的高温部位实行重点检测,根据检测结果来确定检测的周期。
加工高硫原油常减压装置防腐管理及措施
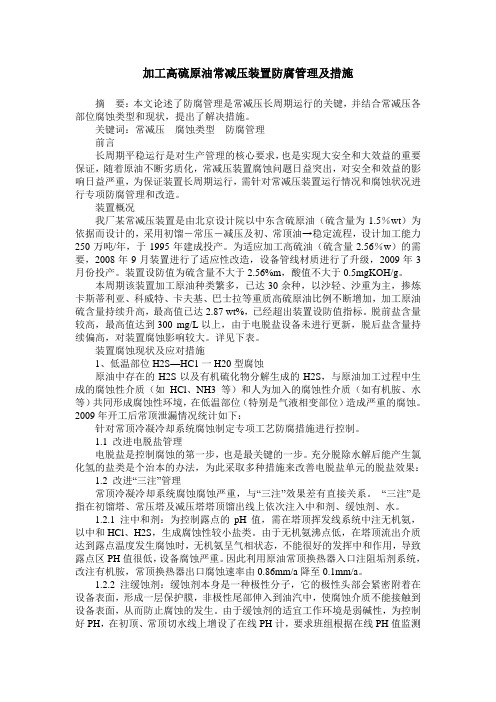
加工高硫原油常减压装置防腐管理及措施摘要:本文论述了防腐管理是常减压长周期运行的关键,并结合常减压各部位腐蚀类型和现状,提出了解决措施。
关键词:常减压腐蚀类型防腐管理前言长周期平稳运行是对生产管理的核心要求,也是实现大安全和大效益的重要保证,随着原油不断劣质化,常减压装置腐蚀问题日益突出,对安全和效益的影响日益严重,为保证装置长周期运行,需针对常减压装置运行情况和腐蚀状况进行专项防腐管理和改造。
装置概况我厂某常减压装置是由北京设计院以中东含硫原油(硫含量为1.5%wt)为依据而设计的,采用初馏-常压-减压及初、常顶油→稳定流程,设计加工能力250万吨/年,于1995年建成投产。
为适应加工高硫油(硫含量2.56%w)的需要,2008年9月装置进行了适应性改造,设备管线材质进行了升级,2009年3月份投产。
装置设防值为硫含量不大于2.56%m,酸值不大于0.5mgKOH/g。
本周期该装置加工原油种类繁多,已达30余种,以沙轻、沙重为主,掺炼卡斯蒂利亚、科威特、卡夫基、巴士拉等重质高硫原油比例不断增加,加工原油硫含量持续升高,最高值已达2.87 wt%,已经超出装置设防值指标。
脱前盐含量较高,最高值达到300 mg/L以上,由于电脱盐设备未进行更新,脱后盐含量持续偏高,对装置腐蚀影响较大。
详见下表。
装置腐蚀现状及应对措施1、低温部位H2S—HC1一H20型腐蚀原油中存在的H2S以及有机硫化物分解生成的H2S,与原油加工过程中生成的腐蚀性介质(如HCl、NH3等)和人为加入的腐蚀性介质(如有机胺、水等)共同形成腐蚀性环境,在低温部位(特别是气液相变部位)造成严重的腐蚀。
2009年开工后常顶泄漏情况统计如下:针对常顶冷凝冷却系统腐蚀制定专项工艺防腐措施进行控制。
1.1 改进电脱盐管理电脱盐是控制腐蚀的第一步,也是最关键的一步。
充分脱除水解后能产生氯化氢的盐类是个治本的办法,为此采取多种措施来改善电脱盐单元的脱盐效果:1.2 改进“三注”管理常顶冷凝冷却系统腐蚀腐蚀严重,与“三注”效果差有直接关系。
加工高酸原油常减压蒸馏装置腐蚀原因分析及防腐措施
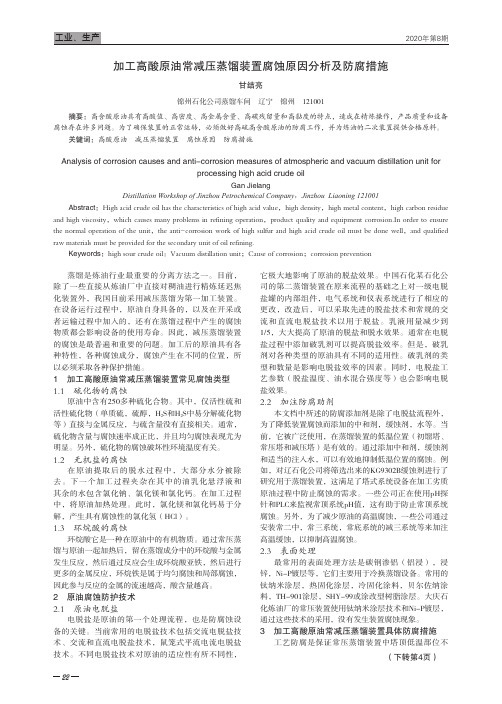
蒸馏是炼油行业最重要的分离方法之一。
目前,除了一些直接从炼油厂中直接对稠油进行精炼延迟焦化装置外,我国目前采用减压蒸馏为第一加工装置。
在设备运行过程中,原油自身具备的,以及在开采或者运输过程中加入的,还有在蒸馏过程中产生的腐蚀物质都会影响设备的使用寿命。
因此,减压蒸馏装置的腐蚀是最普遍和重要的问题。
加工后的原油具有各种特性,各种腐蚀成分,腐蚀产生在不同的位置,所以必须采取各种保护措施。
1 加工高酸原油常减压蒸馏装置常见腐蚀类型1.1 硫化物的腐蚀原油中含有250多种硫化合物。
其中,仅活性硫和活性硫化物(单质硫,硫醇,H2S和H2S中易分解硫化物等)直接与金属反应,与硫含量没有直接相关。
通常,硫化物含量与腐蚀速率成正比,并且均匀腐蚀表现尤为明显。
另外,硫化物的腐蚀破坏性环境温度有关。
1.2 无机盐的腐蚀在原油提取后的脱水过程中,大部分水分被除去。
下一个加工过程夹杂在其中的油乳化悬浮液和其余的水包含氯化钠、氯化镁和氯化钙。
在加工过程中,将原油加热处理。
此时,氯化镁和氯化钙易于分解,产生具有腐蚀性的氯化氢(HCl)。
1.3 环烷酸的腐蚀环烷酸它是一种在原油中的有机物质。
通过常压蒸馏与原油一起加热后,留在蒸馏成分中的环烷酸与金属发生反应,然后通过反应会生成环烷酸亚铁,然后进行更多的金属反应,环烷铁是属于均匀腐蚀和局部腐蚀,因此参与反应的金属的流速越高,酸含量越高。
2 原油腐蚀防护技术2.1 原油电脱盐电脱盐是原油的第一个处理流程,也是防腐蚀设备的关键。
当前常用的电脱盐技术包括交流电脱盐技术、交流和直流电脱盐技术,鼠笼式平流电流电脱盐技术。
不同电脱盐技术对原油的适应性有所不同性,它极大地影响了原油的脱盐效果。
中国石化某石化公司的第二蒸馏装置在原来流程的基础之上对一级电脱盐罐的内部组件,电气系统和仪表系统进行了相应的更改,改造后,可以采取先进的脱盐技术和常规的交流和直流电脱盐技术以用于脱盐。
乳液用量减少到1/5,大大提高了原油的脱盐和脱水效果。
高酸原油

本世纪以来,随着国际原油价格的一路攀升,国内许多炼油厂在成本压力下开始炼制价格较低的高酸值原油,设备防环烷腐蚀问题也同时提到议事日程。
腐蚀监测技术是掌握设备腐蚀状态的有效手段,炼制高酸值原油设备的腐蚀程度可以通过不同的腐蚀监测方法进行跟踪,从而指导生产的安全运行。
l 环烷酸腐蚀彰晌因素影响环烷酸高温腐蚀的主要因素有原油的总酸值(TAN)、温度、硫含量、流速和设备材质等。
物料的物性、流动状态、气液相状态、压力及物料中环烷酸盐等也会间接影响环烷酸腐蚀速率的大小。
1。
1 酸值酸值是影响环烷酸高温腐蚀最主要的因素。
一般认为当原油的TAN大子0。
5 mgKOH/g时,就存在环烷酸腐蚀,且TAN值越高,腐蚀越严重。
由于TAN 值只代表整体酸性(包括环烷酸以外的酸性),而油品中环烷酸是混合酸,沸点也不同,因此,对设备的某一具体位置来说,工艺物料中的真实酸值才真正反映其腐蚀性。
这一事实对腐蚀监测有一定的指导意义,实施腐蚀监测之前要了解环烷酸在各种馏分中的分布情况。
1。
2 温度(l~3]温度也是影响环烷酸高温腐蚀的主要因素,在177℃就能发现环烷酸的腐蚀现象。
在生产实践中,当温度达到232℃以上时,碳钢的腐蚀速率比较明显,随着温度升高,腐蚀速率加快。
在一定的酸值下,温度每上升55.5℃,环烷酸对碳钢和低合金钢的腐蚀速率增加3倍。
当温度在370℃左右时环烷酸腐蚀最严重,超过400℃时,由于环烷酸开始热分解,腐蚀速率下降。
生产实践中,腐蚀速率随温度的变化还受到高温硫腐蚀的影响。
环烷酸腐蚀有两个显著的温度区,第一是274℃左右的碱三线蜡油,第二是345~385℃的常压塔进料段、常底、减四线、减压塔进料和减压塔底。
l。
3 流速阳[4~5]流速和流态是影响环烷酸腐蚀非常重要的因素。
在高温及高流速下,酸值在很低水平(0.3KOHmg/g)的油液,比高酸值(1.5~1。
8 KOHmg/g)的油液更有腐蚀性。
实践表明在炼油设备的弯头、三通和泵中产生的湍流会加速设备的腐蚀。
加工含硫含酸原油的腐蚀问题和对策论文

加工含硫含酸原油的腐蚀问题和对策论文加工含硫含酸原油的腐蚀问题和对策论文【摘要】随着近年来国内几大油田都进入了二次和三次采油期,原油酸值和腐蚀性都增加。
而进口原油特别是中东原油的增加,使得加工原油硫含量较高,这给石油的炼制和防腐提出了更高的要求。
【关键词】含硫含酸原油腐蚀问题对策加工高硫原油与加工高酸原油带来的腐蚀问题是不同的,加工高酸原油带来的腐蚀问题主要集中在蒸馏装置,而加工高硫原油时,由于原油中的非活性硫不断向活性硫转变,使硫腐蚀不仅存在于一次加工装置,也同样存在于二次加工装置,甚至延伸到下游化工装置,贯穿于炼油的全过程中。
硫在原油的不同馏分中的含量和存在的形式不尽相同,但都随沸点的升高而增加,并且富集于渣油中。
因此,有必要对炼油装置的腐蚀类型和防护措施做一个简单的综述。
1 几种主要腐蚀类型在原油加工过程中,主要有硫腐蚀和环烷酸腐蚀。
其中,硫腐蚀不是孤立存在的。
硫和无机盐、环烷酸、氮化物、水、氢、氨等其它腐蚀性介质共同作用,形成多种复杂的腐蚀环境。
而环烷酸和硫的相互作用和相互制约、促进使腐蚀问题变得错综复杂。
不同的原油中含有不同类型的硫化物,它们的含量和存在形式既能抑制又能促进环烷酸腐蚀,从而导致硫化物既可增强又可降低含酸原油的腐蚀性。
大致有以下几种腐蚀类型。
1.1湿硫化氢腐蚀原油中存在的H2S以及有机硫化物在不同条件下逐步分解生成的H2S,与原油加工过程中生成的腐蚀性介质(如HCl、NH3等)和人为加入的腐蚀性介质(如有机胺、水等)共同形成腐蚀性环境,在装置的低温部位(特别是气液相变部位)造成严重的腐蚀。
1.2高温硫腐蚀高温硫化物的腐蚀是指240℃温度以上的部位元素硫、硫化氢和硫醇等活性硫形成的腐蚀。
表现为均匀腐蚀,其中以硫化氢的腐蚀性最强。
化学反应如下:H2S+Fe→FeS+H;S+Fe→FeS;RSH+Fe→FeS+不饱和烃。
1.3高温环烷酸腐蚀环烷酸腐蚀经常发生在酸值大于0.5mgKOH/g、温度在270~400℃之间高流速的工艺介质中。
加工高酸原油的常减压装置的防腐技术初探
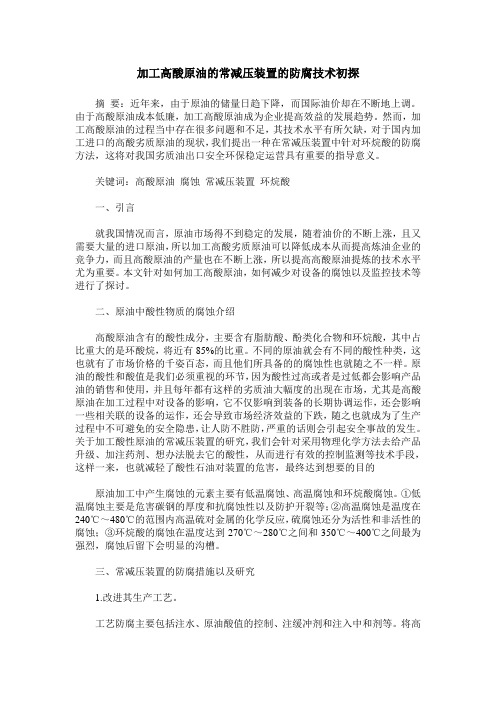
加工高酸原油的常减压装置的防腐技术初探摘要:近年来,由于原油的储量日趋下降,而国际油价却在不断地上调。
由于高酸原油成本低廉,加工高酸原油成为企业提高效益的发展趋势。
然而,加工高酸原油的过程当中存在很多问题和不足,其技术水平有所欠缺,对于国内加工进口的高酸劣质原油的现状,我们提出一种在常减压装置中针对环烷酸的防腐方法,这将对我国劣质油出口安全环保稳定运营具有重要的指导意义。
关键词:高酸原油腐蚀常减压装置环烷酸一、引言就我国情况而言,原油市场得不到稳定的发展,随着油价的不断上涨,且又需要大量的进口原油,所以加工高酸劣质原油可以降低成本从而提高炼油企业的竞争力,而且高酸原油的产量也在不断上涨,所以提高高酸原油提炼的技术水平尤为重要。
本文针对如何加工高酸原油,如何减少对设备的腐蚀以及监控技术等进行了探讨。
二、原油中酸性物质的腐蚀介绍高酸原油含有的酸性成分,主要含有脂肪酸、酚类化合物和环烷酸,其中占比重大的是环酸烷,将近有85%的比重。
不同的原油就会有不同的酸性种类,这也就有了市场价格的千姿百态,而且他们所具备的的腐蚀性也就随之不一样。
原油的酸性和酸值是我们必须重视的环节,因为酸性过高或者是过低都会影响产品油的销售和使用,并且每年都有这样的劣质油大幅度的出现在市场,尤其是高酸原油在加工过程中对设备的影响,它不仅影响到装备的长期协调运作,还会影响一些相关联的设备的运作,还会导致市场经济效益的下跌,随之也就成为了生产过程中不可避免的安全隐患,让人防不胜防,严重的话则会引起安全事故的发生。
关于加工酸性原油的常减压装置的研究,我们会针对采用物理化学方法去给产品升级、加注药剂、想办法脱去它的酸性,从而进行有效的控制监测等技术手段,这样一来,也就减轻了酸性石油对装置的危害,最终达到想要的目的原油加工中产生腐蚀的元素主要有低温腐蚀、高温腐蚀和环烷酸腐蚀。
①低温腐蚀主要是危害碳钢的厚度和抗腐蚀性以及防护开裂等;②高温腐蚀是温度在240℃~480℃的范围内高温硫对金属的化学反应,硫腐蚀还分为活性和非活性的腐蚀;③环烷酸的腐蚀在温度达到270℃~280℃之间和350℃~400℃之间最为强烈,腐蚀后留下会明显的沟槽。
高酸高硫油加工的电脱盐及高温腐蚀控制
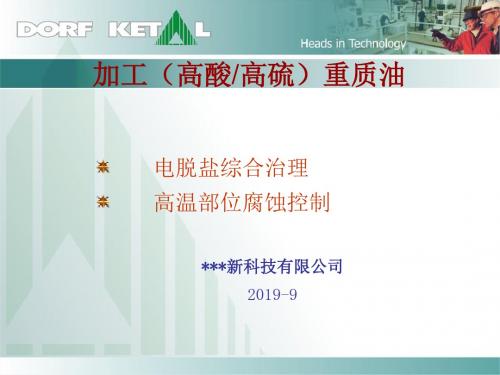
乳化可以带来诸如电脱盐操作紊乱、脱盐效果差、原油带水、塔顶 腐蚀、换热器结垢、影响后续工艺操作等一系列问题。
破乳剂
破乳机理: 破乳剂的作用是 破坏乳化膜,改 变水滴的表面张 力,促使水滴结 合凝聚成大水滴 ,然后由于其重 力因素沉积,得 以油水分离。
(R-O)n – P – (OH)(3-n)
• 硫代磷酸盐
(R-O)n – PS – (OH)(3-n)
缓蚀剂与铁形成:铁-氧-磷键化合物 Fe – O – P – (O-R)n / (OH)(2-n)
高温缓蚀剂
含硫缓蚀剂为有机聚硫化合物:
R – Sx – (R or H) 缓蚀剂与铁反应形成致密的聚硫化铁保护膜附着在 金属表面,抑制腐蚀反应
MOC 321 SS #20 CS #20 CS #20 CS #20 CS #20 CS 321 SS 5%Cr 5% Cr
Sulfur Content
% 1.5 <1.5
<1.5
<1.5
<1.5
2 - 3.5
2 - 3.5
2 - 3.5 3.5
Highest temperature
TAN
in this zone
监测环烷酸腐蚀
监测环烷酸腐蚀比监测其它的腐蚀更难:
• 工艺物流温度高,对监测的设备以及人员要求高。 • 工艺操作条件改变,腐蚀位置也相应的发生改变:温度、流
速、原油掺炼情况。
监测手段
腐蚀探针 挂片 测厚 氢通量 馏分油中铁离子
谢谢!!!
加工(高酸/高硫)重质油
超重质高酸值原油的加工进行探讨

超重质高酸值原油的加工进行探讨1、前言随着原油的不断勘探和开发,重质高酸值原油会被不断的发现和开采,这部分原油的加工方法也逐渐引起人们的重视。
通常把比重较大的原油称为重质原油。
酸值低于0.3 mgKOH/g的原油称为低酸值原油,酸值为0.5~1.0 mgKOH/g的原油称为含酸原油,酸值大于1.0 mgKOH/g的原油称为高酸值原油。
针对硫含量大于1.0%的高硫原油的加工方法国内已积累了许多宝贵的经验,含酸原油和高酸值原油也已在许多炼油厂进行了掺炼,但是重质高酸值原油的独立加工,国内还没成熟的经验,本文就采用延迟焦化工艺对超重质高酸值原油的加工进行探讨。
2、原油性质及特点下表为几种重质高含酸原油的性质。
该类原油的主要特点是密度大、酸值高、粘度大、胶质含量高、重金属含量高、硫含量低。
该类原油的加工难度主要体现在①酸值高,对设备及管线腐蚀严重;②常压石脑油、煤油、柴油的收率偏低,且柴油的酸值较高。
另外还有其它多项指标不合格;③蜡油酸值高、难裂化、做催化原料时轻油收率偏低;④金属含量较高,对电脱盐带来困难。
3、加工方案选择确定原油加工方案一般是根据原油的性质和对目的产品的要求通过优化比较寻找目的产品多、产品质量好、加工流程短、投资低、能耗低、经济效益好的加工流程。
根据上述原油的特点,针对常减压拔出率较高的高酸值原油,应先采用常减压装置进行分馏,石脑油通过重整处理后生产高辛烷值汽油,煤油、柴油去加氢精制,蜡油去加氢裂化,减压渣油通过延迟焦化工艺处理。
针对常压拔出率较高,减压拔出率较低的高酸值原油。
可以只进行常压分馏、常压渣油直接进延迟焦化装置处理。
针对常减压拔出率均较低的重质高酸值原油,如辽河超稠油、苏丹稠油,可以直接采用延迟焦化装置进行加工。
延迟焦化装置生产的石脑油经加氢处理后可作为重整原料或乙烯裂解原料,焦化柴油经加氢精制后作为优质柴油外销,焦化蜡油作为加氢裂化原料或作为催化裂化原料。
由于高酸值原油的硫含量较低,可生产低硫优质焦炭,焦化富气可作为制氢装置的原料。
炼油厂防腐蚀培训资料加工高酸值原油腐蚀与防护对策
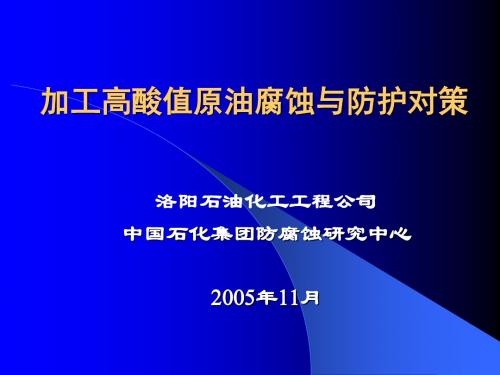
2.3.1 H2S-HCN-H2O型腐蚀
腐蚀形态 在该环境下,对碳钢为均匀减薄、氢鼓 泡及硫化物应力腐蚀开裂;对奥氏体不 锈钢为硫化物应力腐蚀开裂。 防护措施 采用水洗的办法,将氰化物脱出;或者 注入多硫化物有机缓蚀剂。
2.3.2 NOx-H2S- H2O型腐蚀
NOx-H2S-H2O型腐蚀体系给催化裂化再生 器、三旋等设备造成腐蚀开裂,产生穿 透性裂纹,严重威胁装置的正常生产。 防护措施 增加保温材料,提高壁温,防止结露; 或采用内喷合金涂层的电化学防护方法, 防止裂纹开裂。
该类型腐蚀应以工艺腐蚀为主,材料防 腐为辅 工艺防腐采用“一脱三注” 材料升级双相不锈钢、钛材或Monel合金
2.2 环烷酸高温腐蚀
2.2.1 环烷酸高温腐蚀的特点
腐蚀特点 发生在220-400℃,腐蚀产物溶于油,腐 蚀的金属表面粗糙而光洁,呈沟槽状。 影响因素 温度、流速和环烷酸含量(酸值)
24.3
25.28 172.4
0.05
0.03 0.03
1.75
4.76 1.69
痕迹
痕迹 痕迹
2005.4.9
2005.4.9 2005.4.9 2005.4.10 2005.4.10 2005.4.11 2005.4.11
加工高酸值原油腐蚀与防护对策
洛阳石油化工工程公司 中国石化集团防腐蚀研究中心 2005年11月
目录
1 高酸原油性质特点 2 加工高酸原油的典型问题 3 防腐中心开展的工作 4 加工高酸原油其它注意事项 5 需要进一步研究的内容 6 结束语
1 高酸原油性质特点
原油
渤海 蓬莱 19-3
密度,kg/m3(20℃)
渤海 锦州 9-3
浅谈高酸原油的腐蚀与防腐技术

浅谈高酸原油的腐蚀与防腐技术王树勇【摘要】With the decreasing of oil resources, oil refining enterprises more and more inclined to claoose mgn acla crude oil as raw material. High acid crude oil caused serious corrosion to the equipment in the production process, which attracted wide attention both at home and abroad. The harm of high acid crude oil and the necessity of protection were briefly described, and the corresponding anti - corrosion measures and the material selection program of equipment and piping were proposed.%随着石油资源的日益减少,炼油企业越来越倾向于选用高酸原油作为原料。
加工高酸原油的过程中会对设备造成严重的腐蚀,这个问题已经引起国内外的广泛关注。
本文简单描述了高酸原油的危害及防腐的必要性,并提出了相应的工艺防腐措施及设备和管道的选材方案。
【期刊名称】《广州化工》【年(卷),期】2012(040)014【总页数】2页(P38-39)【关键词】腐蚀;防腐措施;选材【作者】王树勇【作者单位】茂名瑞派石化工程有限公司,广东茂名525011【正文语种】中文【中图分类】TE8近年来,随着油田采出程度的加大,原油的酸值越来越高。
目前世界原油市场上高酸原油的产量每年约占全球原油总产量5.5%左右,并且每年还以0.3%的速度增长[1]。
高酸原油加工防腐蚀技术(山东讲课)
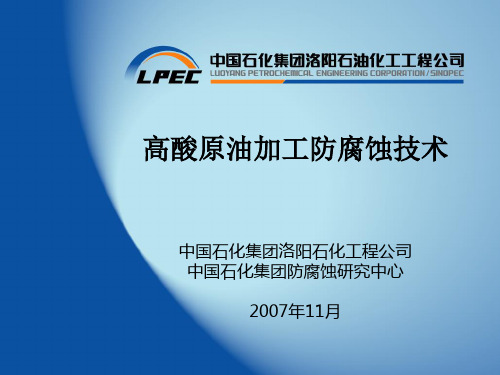
一、加工高酸原油的意义
4、国际市场高酸原油价格一直较低。2005年高酸 原油的折扣是10~15美元/桶,2006年苏丹达混原油的 折扣高达28美元/桶。
5、炼油厂必须是一个低成本的生产企业,选择加 工高酸原油,能大幅度降低原油采购成本,提高炼油 企业的加工效益及竞争力。
7
高酸原油的性质
8
二、高酸原油的性质
4
一、加工高酸原油的意义
5
一、加工高酸原油的意义
2、2006年,国际油价明显呈现高位震荡走势, WTI均价仍达到了66.2美元/桶,同比上涨了9.5美元/ 桶,炼油业延续了上年的困境,全年炼油业仍整体亏损 391亿元。
3、高酸值原油是世界石油资源的重要部分,近几 年每年约增加3‰,高酸原油的产量已占原油总产量 的5~5.5%。国内渤海湾等海域高酸原油的全面开发, 更加促进了对含酸和高酸原油的加工。
25
2 低温H2S-HCl-H2O型腐蚀
(1)腐蚀特征
H2S-HCl-H2O型腐蚀主要发生在蒸馏装置的塔顶及冷凝 冷却器系统。
对于碳钢为均匀腐蚀,0Cr13钢为点蚀,奥氏体不锈钢 则为氯化物应力腐蚀开裂。
(2)腐蚀部位
H2S-HCl-H2O型腐蚀主要集中在初馏塔和常压塔顶部 (顶部五层塔盘及其上部)及塔顶冷凝冷却器系统、减压塔 顶。
高酸原油加工防腐蚀技术
中国石化集团洛阳石化工程公司 中国石化集团防腐蚀研究中心
2007年11月
1
主要内容
一、加工高酸原油的意义 二、高酸原油的性质 三、加工高酸原油的主要腐蚀 四、防护措施 五、LPEC防腐技术
2
加工高酸原油的意义
3
一、加工高酸原油的意义
1、我国是一个石油资源相对短缺的国家,加工原 油大量依靠进口,对国际石油资源的依赖度程度不断 增加。2006年,石油表观消费量3.46亿吨,其中原油 产量1.84亿吨,净进口1.62亿吨,对外依存度47%,均 创历史新高。中石化加工原油1.46亿吨,进口原油1.1 亿吨。
加工高硫高酸原油蒸馏装置的腐蚀原因分析及防护措施
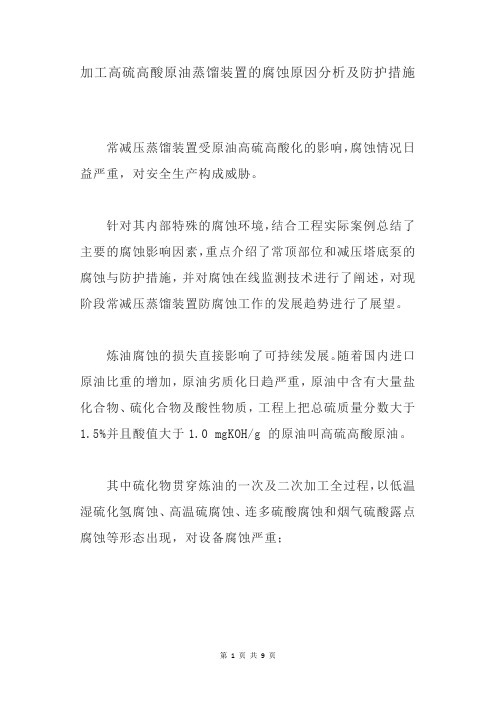
加工高硫高酸原油蒸馏装置的腐蚀原因分析及防护措施常减压蒸馏装置受原油高硫高酸化的影响,腐蚀情况日益严重,对安全生产构成威胁。
针对其内部特殊的腐蚀环境,结合工程实际案例总结了主要的腐蚀影响因素,重点介绍了常顶部位和减压塔底泵的腐蚀与防护措施,并对腐蚀在线监测技术进行了阐述,对现阶段常减压蒸馏装置防腐蚀工作的发展趋势进行了展望。
炼油腐蚀的损失直接影响了可持续发展。
随着国内进口原油比重的增加,原油劣质化日趋严重,原油中含有大量盐化合物、硫化合物及酸性物质,工程上把总硫质量分数大于1.5%并且酸值大于1.0mgKOH/g的原油叫高硫高酸原油。
其中硫化物贯穿炼油的一次及二次加工全过程,以低温湿硫化氢腐蚀、高温硫腐蚀、连多硫酸腐蚀和烟气硫酸露点腐蚀等形态出现,对设备腐蚀严重;高酸原油的部分含氧化合物会以环烷酸的形式存在,对常减压等装置高温部位产生严重腐蚀;作为一次加工的入口,对常减压蒸馏装置开展腐蚀研究显得尤其重要。
一、腐蚀影响因素1.硫化物的腐蚀原油中的硫及其化合物多达250种以上,其中只有活性硫及活性硫化物(如单质硫、硫醇、H2S及易分解为H2S 的硫化物)可以与金属直接发生反应,而与总硫含量无直接关系。
一般而言,硫化物含量与其腐蚀破坏性成正比,具体表现为均匀腐蚀,此外,硫化物腐蚀破坏性与环境温度相互关联。
2.无机盐的腐蚀原油在采出后会经过脱水工序除去大部分水,下一加工过程中掺杂在其中的油乳化悬浮液和剩余的水中都含有氯化钠、氯化镁和氯化钙等盐类。
在加工过程中,原油会进行升温处理,这时氯化镁和氯化钙很容易受热分解,生成具有强腐蚀性的氯化氢。
氯化氢直接影响到设备的腐蚀程度,尤其当其与水在露点温度附近时腐蚀破坏最剧烈,该腐蚀形式常发生在塔顶装置及管线系统,研究人员对常减压蒸馏装置常压塔顶内构件的腐蚀进行分析,分别给出了白油和原油中氯化镁和氯化钙随温度增加的水解变化情况(见图1)。
总结得出钙、镁盐的水解程度随温度的升高而提高,大部分的盐在常压炉、常压塔中下部水解,且原油的酸值越高水解的越彻底。
- 1、下载文档前请自行甄别文档内容的完整性,平台不提供额外的编辑、内容补充、找答案等附加服务。
- 2、"仅部分预览"的文档,不可在线预览部分如存在完整性等问题,可反馈申请退款(可完整预览的文档不适用该条件!)。
- 3、如文档侵犯您的权益,请联系客服反馈,我们会尽快为您处理(人工客服工作时间:9:00-18:30)。
加工高酸值原油的方法及防腐措施
随着高酸、高硫原油加工量的不断增加,炼油厂设备腐蚀日趋严重,已影响到炼油装置的安全、稳定、长周期、满负荷、优质生产。
重油装置高温部位通常采用耐腐蚀材料,而蒸馏塔顶低温轻油部位受HCl-H2S-H2O体系的腐蚀,若采用奥氏体不锈钢,则存在Cl-应力腐蚀开裂的问题,因此一般采用化学注剂防腐工艺,即用中和剂降低冷凝系统的酸性物,用缓蚀剂使它在金属表面形成一层保护膜。
传统的做法是采用注氨水的方法中和冷凝液中的酸性物,但露点部位的腐蚀仍会发生。
早在八十年代初我国许多炼油厂即开始了“一脱四注”并取得了较好的效果。
随着时间的推移,在美国到九十年代初已约有80%的炼油厂把注氨改为注有机胺,我国在九十年代已陆续有些炼油厂改注有机胺,有的还同时加入缓蚀剂和分散剂等助剂。
近几年来,随着工艺防腐理论的发展和技术的进步,国内外炼厂开始逐渐采用一剂多用的中和缓蚀剂技术来控制塔顶冷凝系统的腐蚀。
性能良好的中和缓蚀剂既具有中和塔顶冷凝区酸性物的作用,又具有在金属表面成膜的功效,能解决露点腐蚀及铵盐沉积造成的结垢和二次腐蚀问题。
二、防止腐蚀措施
1. 脱盐。
目前大多数炼油厂采用二级脱盐工艺,个别厂已采用三级脱盐工艺,使脱后原油含盐达到石化企业规定标准——小于3mgNaCl/L。
但是在这里需说明一点,即目前的脱盐工艺仅仅是脱除原油中可溶于水的无机盐类,由于其中以碱金属及碱土金属的氯化物为主,故将氯化钙、氯化镁和氯化钠均换算为氯化钠含量并以mgNaCl/L表示,但其中的盐并不一定都是氯化物,也可能是硫酸盐,碳酸盐和石油酸盐,如已发现在新疆及华北一些原油中含有较高的石油酸钙,而氯化物也不一定都是无机氯化物,如上所述原油中还含有氯代烃,这些有机金属化合物和氯代烃,目前的脱盐工艺是不能将其脱除的,它们将带入常压塔,金属盐类将浓缩于渣油中,而氯代烃及硫化物则部份分解进入塔顶馏分而造成腐蚀。
2. 注入中和剂控制塔顶pH值。
目前一些炼油厂曾采用注氨中和塔顶酸性物质,控制塔顶pH值在6-7.5之间,由于氨不能进入塔回流线以下,NH4Cl会堵塞塔盘、降液管,引起垢下腐蚀,而且由于氨的易挥发性,也不易控制中和pH值在理想范围内,随后有人采用单一的中和剂(醇胺、吗啉等),或将其与氨混合使用都未能得到令人满意的结查。
3. 多组份胺类复合中和剂较用单一的胺或氨为好。
我们认为若将多组份复合胺类中和剂与缓蚀剂复配混合使用更好,首先这种直链和环状胺类作为中和剂在塔顶中和时能提供理想的,较窄的pH值控制范围,其次中和形成的盐在油中有足够的溶解性,减少了形成沉淀的倾向。
对于露点以上的腐蚀速率,则应要据塔顶总的蒸汽量的多少,适当增加剂的注入量。
4. 控制塔顶温度,减少塔顶蒸汽凝水量,亦可达到减缓腐蚀的目的。
通过上述分析可知当塔顶温度在100℃或更低时,水蒸汽较易冷凝成水,HCl、H2S溶于其中形成酸性腐蚀介质而引起腐蚀。
因此,适当提高塔顶温度使其达到110℃左右,减少塔顶冷凝水量,则有利于缓解腐蚀速度。
5. 常压塔顶注水不仅可以促使中和剂和缓蚀剂同塔顶的酸性气体较好的混合并将酸性组份稀释,而且可将塔板上沉积的盐垢冲洗除去而减少垢下腐蚀。
新鲜水注入塔内,盐即溶于水,含盐的水可经馏出口抽出。
6. 加强工艺控制分析,做到心中有数。
⑴加强电脱盐装置脱后盐含量分析,尤其有机氯含量的变化。
⑵定期监测,控制常压塔顶物流pH值,建议安装pH在线测定系统。
⑶在常压塔馏出线出口使用电阻探针或挂片进行在线监测,并定期对塔进行壁厚测量。
⑷定期对常压塔顶冷凝水进行Fe2+、Fe3+、Cl-、S2-进行分析,判断腐蚀情况,并根据检测结果随时调整缓蚀剂、中和剂的加入量。