单回路温度控制例子
精馏塔提留段温度单回路控制 --过控专业终稿

中北大学课程设计说明书学生姓名:学号:31学院:机械与动力工程学院专业:过程装备与控制工程题目:精馏塔提馏段温度单回路控制方案设计指导教师:刘广璞职称: 教授闫宏伟职称: 教授2014年1月10日中北大学课程设计任务书2013/2014 学年第 1 学期学院:机械与动力工程学院专业:过程装备与控制工程学生姓名:学号:31课程设计题目:精馏塔提馏段温度单回路控制方案设计起迄日期:2013年12月30日~2014年1月10日课程设计地点:中北大学指导教师:刘广璞闫宏伟系主任:黄晋英下达任务书日期: 2013年12月30日课程设计任务书目录1 精馏塔工作原理及结构特性 (7)1.1精馏原理以及工业流程 (7)1.2精馏塔的特性 (7)1.2.1精馏塔的静态特性 (7)1.2.2精馏塔的动态特性 (9)2 控制系统设计 (10)2.1 精馏塔提留段温度控制系统设计方案 (10)2.2 精馏塔提馏段被控变量的选择 (10)2.3 提馏段温度控制系统温度检测点选择 (11)3 硬件选型 (11)4 框图设计与PID参数控制 (15)4.1 精馏塔提馏段温度单回路方框图设计 (16)4.2 各环节传递函数总结 (16)4.3 调节器控制规律 (16)5 系统的Simulink仿真 (17)6 课程设计总结 (19)参考文献 (20)1. 精馏塔工作原理及结构特点1.1精馏原理以及工业流程精馏操作分为连续精馏和间歇精馏,本设计的研究对象是连续精馏的过程。
连续精馏的流程装置如下图所示。
图1.1连续精馏装置工艺流程图[7]其操作过程是:原料液经预热加热到一定温度后,进入精馏塔中的进料板,料液在进料板上与自塔上部下降的回流液体汇合后,在逐板下流,最后流入塔底再沸器中,液体在逐板下降的同时,它与上升的蒸汽在每层塔板上相互接触,同时进行部分汽化和部分冷凝的质量和能量的传递过程。
操作时,连续从再沸器中取出的部分液体作为塔底产品,部分液体汽化产生上升蒸汽,从塔底回流入塔内出塔顶蒸汽进入冷凝器中被冷凝成液体,并将部分冷凝液用泵送回塔顶作为回流液体,其余部分经冷却器后被送出作为塔顶产品。
乳化物干燥器温度单回路控制系统设计
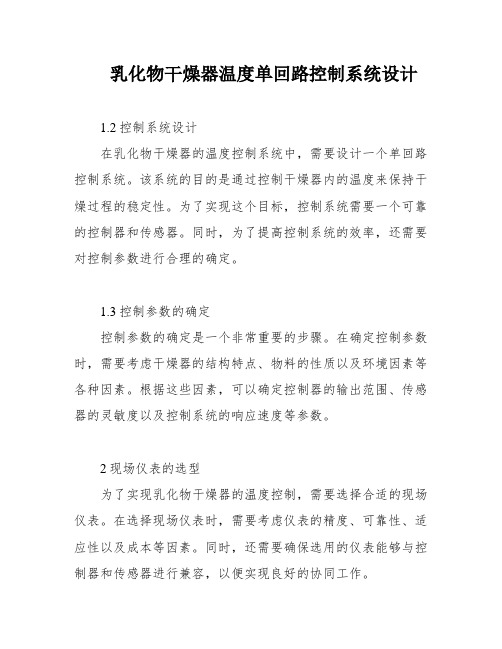
乳化物干燥器温度单回路控制系统设计1.2控制系统设计在乳化物干燥器的温度控制系统中,需要设计一个单回路控制系统。
该系统的目的是通过控制干燥器内的温度来保持干燥过程的稳定性。
为了实现这个目标,控制系统需要一个可靠的控制器和传感器。
同时,为了提高控制系统的效率,还需要对控制参数进行合理的确定。
1.3控制参数的确定控制参数的确定是一个非常重要的步骤。
在确定控制参数时,需要考虑干燥器的结构特点、物料的性质以及环境因素等各种因素。
根据这些因素,可以确定控制器的输出范围、传感器的灵敏度以及控制系统的响应速度等参数。
2现场仪表的选型为了实现乳化物干燥器的温度控制,需要选择合适的现场仪表。
在选择现场仪表时,需要考虑仪表的精度、可靠性、适应性以及成本等因素。
同时,还需要确保选用的仪表能够与控制器和传感器进行兼容,以便实现良好的协同工作。
3系统方块图的确定为了更好地理解乳化物干燥器的温度控制系统,需要绘制系统方块图。
系统方块图可以清晰地展示控制系统的各个组成部分及其之间的关系。
通过系统方块图,可以更好地理解控制系统的工作原理,从而更好地进行系统的调试和维护。
4调节器算法的确定和参数的确定4.1调节器控制规律在乳化物干燥器的温度控制系统中,需要选择合适的调节器控制规律。
常用的调节器控制规律包括比例控制、积分控制和微分控制等。
根据干燥器的结构特点和物料的性质等因素,可以选择合适的调节器控制规律。
4.2各环节传递函数及参数的确定为了实现乳化物干燥器的温度控制,需要确定各个环节的传递函数及其参数。
在确定传递函数及参数时,需要考虑控制系统的稳定性、响应速度以及抗干扰能力等因素。
通过合理地选择传递函数及参数,可以实现乳化物干燥器温度的精确控制。
5系统的Simulink仿真为了验证乳化物干燥器的温度控制系统的性能,需要进行Simulink仿真。
通过Simulink仿真,可以模拟实际控制系统的工作情况,从而更好地了解系统的性能和稳定性。
过程控制综合设计单回路温度PLC控制系统设计
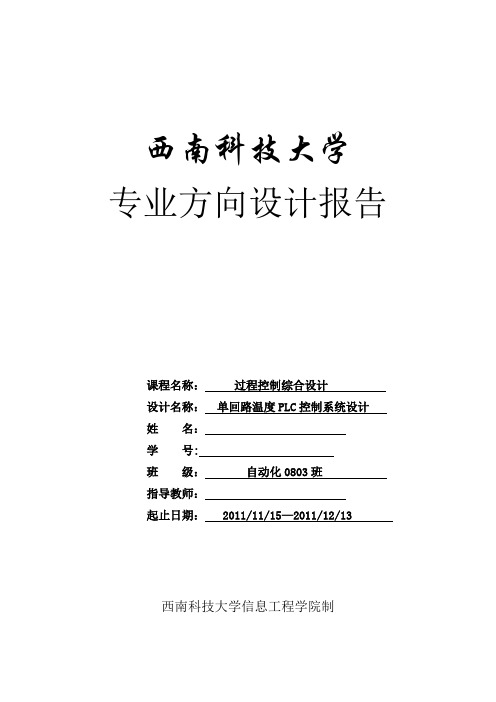
西南科技大学专业方向设计报告课程名称:过程控制综合设计设计名称:单回路温度PLC控制系统设计姓名:学号:班级:自动化0803班指导教师:起止日期:2011/11/15—2011/12/13西南科技大学信息工程学院制方向设计任务书学生班级:自动0803班学生姓名:韦汉林学号:20085082 设计名称:单回路温度PLC控制系统起止日期:2011/11/15—2011/12/312-13 指导教师:姜官武方向设计学生日志单回路温度PLC控制系统摘要:本文研究了PLC对单回路温度的PID控制过程以及对组态软件MCGS和模拟量扩展模块EM235的学习与运用。
重点学习了step7-200的PID编程模块,理解并掌握了PLC的PID模块的运用于相关的参数设定及整定方法,通过利用step7-200编程,实现了对温度的PID控制。
重点学习了组态软件的系统结构以及怎样在组态软件MCGS中绘制相关数据对象以及对数据对象进行相关的属性设置和怎样进行MCGS与PLC的联机调试,通过学习,成功的利用MCGS实现了对温度控制的在线监控。
关键词:PLC PID控制 MCGS 温度控制Single loop temperature PLC control system Abstract:This paper studies the PLC to single loop temperature PID control process and configuration software MCGS and analog quantities EM235 expansion module of the study and the application。
Selective learned the step7-200 PID programming module, understand and master the PLC PID module used to related parameters are set and setting method, through the use of step7-200 programming, realize the temperature of the PID control。
单回路控制系统实验过程控制实验指导书模板
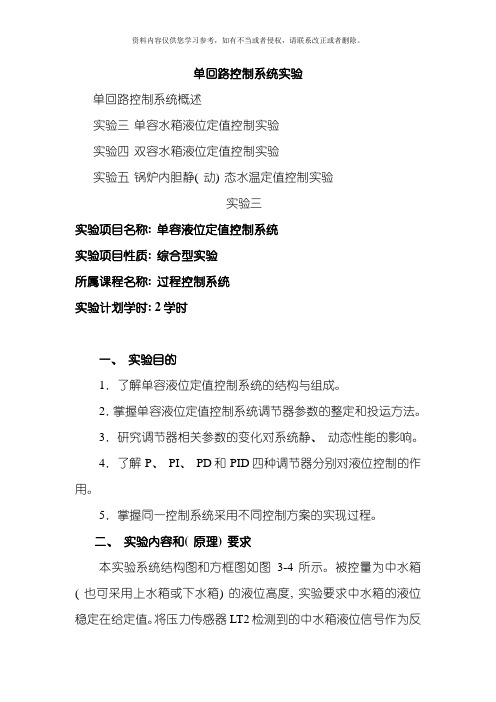
单回路控制系统实验单回路控制系统概述实验三单容水箱液位定值控制实验实验四双容水箱液位定值控制实验实验五锅炉内胆静( 动) 态水温定值控制实验实验三实验项目名称: 单容液位定值控制系统实验项目性质: 综合型实验所属课程名称: 过程控制系统实验计划学时: 2学时一、实验目的1.了解单容液位定值控制系统的结构与组成。
2.掌握单容液位定值控制系统调节器参数的整定和投运方法。
3.研究调节器相关参数的变化对系统静、动态性能的影响。
4.了解P、PI、PD和PID四种调节器分别对液位控制的作用。
5.掌握同一控制系统采用不同控制方案的实现过程。
二、实验内容和( 原理) 要求本实验系统结构图和方框图如图3-4所示。
被控量为中水箱( 也可采用上水箱或下水箱) 的液位高度, 实验要求中水箱的液位稳定在给定值。
将压力传感器LT2检测到的中水箱液位信号作为反馈信号, 在与给定量比较后的差值经过调节器控制电动调节阀的开度, 以达到控制中水箱液位的目的。
为了实现系统在阶跃给定和阶跃扰动作用下的无静差控制, 系统的调节器应为PI或PID控制。
三、实验主要仪器设备和材料1.实验对象及控制屏、SA-11挂件一个、计算机一台、万用表一个;2.SA-12挂件一个、RS485/232转换器一个、通讯线一根;3.SA-44挂件一个、CP5611专用网卡及网线、PC/PPI通讯电缆一根。
四、实验方法、步骤及结果测试本实验选择中水箱作为被控对象。
实验之前先将储水箱中贮足水量, 然后将阀门F1-1、F1-2、F1-7、F1-11全开, 将中水箱出水阀门F1-10开至适当开度, 其余阀门均关闭。
具体实验内容与步骤按二种方案分别叙述。
( 一) 、智能仪表控制1.按照图3-5连接实验系统。
将”LT2中水箱液位”钮子开关拨到”ON”的位置。
图3-4 中水箱单容液位定值控制系统(a)结构图(b)方框图图3-5 智能仪表控制单容液位定值控制实验接线图2.接通总电源空气开关和钥匙开关, 打开24V开关电源, 给压力变送器上电, 按下启动按钮, 合上单相Ⅰ、Ⅲ空气开关, 给智能仪表及电动调节阀上电。
燃烧式工业窑炉温度单回路控制方案设计
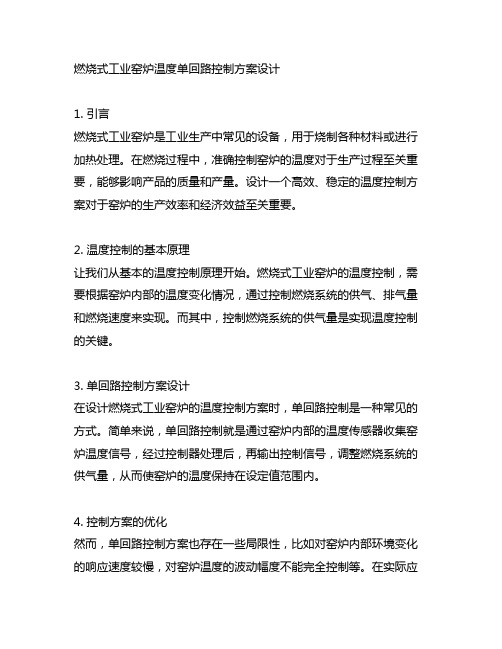
燃烧式工业窑炉温度单回路控制方案设计1. 引言燃烧式工业窑炉是工业生产中常见的设备,用于烧制各种材料或进行加热处理。
在燃烧过程中,准确控制窑炉的温度对于生产过程至关重要,能够影响产品的质量和产量。
设计一个高效、稳定的温度控制方案对于窑炉的生产效率和经济效益至关重要。
2. 温度控制的基本原理让我们从基本的温度控制原理开始。
燃烧式工业窑炉的温度控制,需要根据窑炉内部的温度变化情况,通过控制燃烧系统的供气、排气量和燃烧速度来实现。
而其中,控制燃烧系统的供气量是实现温度控制的关键。
3. 单回路控制方案设计在设计燃烧式工业窑炉的温度控制方案时,单回路控制是一种常见的方式。
简单来说,单回路控制就是通过窑炉内部的温度传感器收集窑炉温度信号,经过控制器处理后,再输出控制信号,调整燃烧系统的供气量,从而使窑炉的温度保持在设定值范围内。
4. 控制方案的优化然而,单回路控制方案也存在一些局限性,比如对窑炉内部环境变化的响应速度较慢,对窑炉温度的波动幅度不能完全控制等。
在实际应用中,需要对单回路控制方案进行优化。
可以采用先进的控制算法,如模糊控制、PID控制等,来提高控制系统的稳定性和响应速度。
另外,结合窑炉的实际工况,可以在控制系统中加入预测模型,从而实现对窑炉温度变化的提前预警和调整。
5. 个人观点和理解在我看来,针对燃烧式工业窑炉的温度控制,单回路控制方案是一种有效的方式,但需要在实际应用中不断优化和改进。
通过结合先进的控制算法和预测模型,能够更好地实现对窑炉温度的精准控制,从而提高生产效率和产品质量。
总结在燃烧式工业窑炉的温度控制方案设计中,单回路控制是一种常见的方式,但需要在实际应用中进行优化。
通过引入先进的控制算法和预测模型,能够提高控制系统的稳定性和响应速度,实现对窑炉温度的精准控制。
在文章中,我们从基本的温度控制原理出发,进一步探讨了单回路控制方案的设计和优化。
并结合个人观点和理解,对燃烧式工业窑炉的温度控制进行了全面的解析。
单回路控制

一、单回路控制系统1一个简单控制系统由那几部分组成?各有什么作用?2 什么是简单控制系统?试画出简单控制系统典型方块图。
答:所谓简单控制系统,通常是指由一个被控对象、一个检测元件及传感器(或变送器)、一个调节器和一个执行器所构成单闭环控制系统,有时也称为单回路控制系统。
简单控制系统典型方块图如下图所示。
题2 方块图3在石油化工生产过程中,常常利用液态丙烯汽化吸收裂解气体热量,使裂解气体温度下降到规定数值上。
下图是一个简化丙烯冷却器温度控制系统。
被冷却物料是乙烯裂解气,其温度要求控制在(15±1.5)℃。
如果温度太高,冷却后气体会包含过多水分,对生产造成有害影响;如果温度太低,乙烯裂解气会产生结晶析出,杜塞管道。
题3 图丙烯冷却器(1)指出系统中被控对象、被控变量和操作变量各是什么?(2)试画出该控制系统组成方块图。
答:(1)被控对象为丙烯冷却器;被控变量为乙烯裂解气出口温度;操作变量为气态丙烯流量。
(3)该系统方块图:题3 方块图4反应温度控制系统示意图。
A、B两种物料进入反映,通过改变进入夹套冷却水流量来控制反应器内温度保持不变。
图中TT表示温度变送器,TC便是温度控制器。
试画出该温度控制系统方块图,并指出该控制系统中被控对象、被控变量、操作变量及可能影响被控变量变化扰动各是什么?题4图反应器温度控制系统答:反应器温度控制系统中被控对象为反应器;被控变量为反应器内温度;操作变量为冷却水流量;干扰为A、B物料流量、温度、浓度、冷却水温度、压力及搅拌器转速。
反应器温度控制系统方块图:题4方块图5 乙炔发生器是利用电石和水来产生乙炔气装置。
为了降低电石消耗量,提高乙炔收率,确保生产安全,设计了如图所示温度控制系统。
工艺要求发生器温度控制在(80±1)℃。
试画出该温度控制系统方块图,并指出图中被控对被控变量、操作变量及可能存在扰动。
题5图乙炔发生器分别为乙炔答:乙炔发生器温度控制系统方块图如下图所示(图中T、TO 发生器温度及其设定值)。
温度单回路控制实验

温度单回路控制实验一.实验目的通过实验掌握单回路控制系统的构成。
学生可自行设计,构成单回路温度控制系统,并采用经验法整定单回路控制系统的PID参数。
二.实验装置面板图三.实验内容:1. 设计单回路温度控制系统,并进行正确接线。
2. 熟悉组态王软件的使用和参数设置的方法。
3. 温度单回路闭环控制系统的参数整定和分析。
四.实验接线图及设备所用设备:水泵、变频器、压力变送器、主回路调节阀、副回路调节阀、可控硅、热电阻、温度变送器、牛顿模块(输入、输出)。
五.控制系统原理图3.将变频器控制选择开关放在“内控”位置,使水泵在恒压供水状态下工作,打开加热筒进水阀V1(在实验装置面板背面),将加热圆筒内注满水(观察加热圆筒外玻璃管液位计显示),直至出水管有水流出。
4.确认接线无误并且加热筒注满水后,接通加热器电源,在实验界面中,手动自动按钮选择手动,同时调整PID设定中的U(K)0使流量约为12%左右,U(K)约为200左右,保持U(K)0与U(K)不变。
5.待加热筒水温稳定后(观察PV值,不变化为稳定),设定PID参数,加给定值扰动,即调整给定值SP,使SP大于PV。
6.在实验界面中,手动自动按钮选择自动,选择实时曲线,观察温度变化。
7. 同时可点击“历史曲线”按钮,观察温度响应的历史曲线,并进行数据分析。
8. 重复实验步骤5、6,完成不同PID参数整定,使温度响应达到接近4:1衰减曲线。
七.注意事项1.接线后未经教师检查严禁接通总电源。
2. 循环水从水槽经底部水管由水泵抽出流过调节阀Ⅰ,流量计Ⅰ,电磁阀V1到达加热圆筒,加热筒水满后由上部水管溢出经V10到达下水箱并由下水箱流回到水槽。
若加热筒内无水或水不够时打开加热器,则会报警以避免干烧。
3.不要频繁修改PID参数,待温度稳定后再进行修改。
4. 验曲线以计算机截图的方式进行保存,打印后附于实验报告后。
精馏塔提留段温度单回路控制
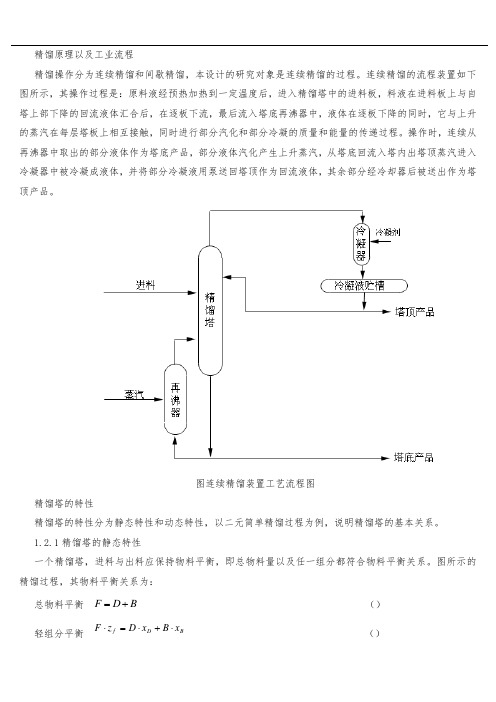
精馏原理以及工业流程精馏操作分为连续精馏和间歇精馏,本设计的研究对象是连续精馏的过程。
连续精馏的流程装置如下图所示,其操作过程是:原料液经预热加热到一定温度后,进入精馏塔中的进料板,料液在进料板上与自塔上部下降的回流液体汇合后,在逐板下流,最后流入塔底再沸器中,液体在逐板下降的同时,它与上升的蒸汽在每层塔板上相互接触,同时进行部分汽化和部分冷凝的质量和能量的传递过程。
操作时,连续从再沸器中取出的部分液体作为塔底产品,部分液体汽化产生上升蒸汽,从塔底回流入塔内出塔顶蒸汽进入冷凝器中被冷凝成液体,并将部分冷凝液用泵送回塔顶作为回流液体,其余部分经冷却器后被送出作为塔顶产品。
图连续精馏装置工艺流程图精馏塔的特性精馏塔的特性分为静态特性和动态特性,以二元简单精馏过程为例,说明精馏塔的基本关系。
1.2.1精馏塔的静态特性一个精馏塔,进料与出料应保持物料平衡,即总物料量以及任一组分都符合物料平衡关系。
图所示的精馏过程,其物料平衡关系为:总物料平衡 B D F += () 轻组分平衡BD f x B x D z F ⋅+⋅=⋅ ()由式()和()联立可得:B B f D x x z D Fx +-=)(B D fD x x z x F D --= ()式中 F 、D 、B ——分别为进料、顶馏出液和底馏出液流量;fz 、D x 、B x ——分别为进料、顶馏出液和底馏出液中轻组分含量。
从上述关系可看出:当F D 增加时将引起顶、底馏出液中轻组分含量减少,即D x 、B x 下降。
而当F B 增加时将引起顶、底馏出液中轻组分含量增加。
即D x 、B x 上升。
然而,在F D (或F B )一定,且f z一定的条件下并不能完全确定D x 、B x 的数值,只能确定D x 与Bx 之间的比例关系,也就是一个方程只能确定一个未知数。
要确定D x 与B x 两个因数,必须建立另一个关系式:能量平衡关系。
在建立能量平衡关系时,首先要了解一个分离度的概念。
【系统】温度单回路控制系统的设计与实现

【关键字】系统广东白云学院毕业设计(论文)题目:温度单回路控制系统的设计与实现学生姓名:王春雁学号:08班级: 07电气自动化(1)班专业:自动化所在系: 电子信息工程系指导教师:艾运阶完成日期:温度单回路控制系统的设计与实现摘要对于过程控制系统设计和运行而言,控制方案的选择和调节器参数整定是两个重要的内容。
本文以水箱为控制对象,主要介绍温度检测传感器、温度变送器、智能PID控制器以及可控硅调节器构成温度控制系统的参数选择和设计。
设计过零触发控制器,实现温度控制系统的参数整定和系统的投运。
采用实验方法对PID控制参数进行工程整定,提出该系统合理的水温自动控制系统的实现方法和控制参数整定方法。
关键词:温度控制;PID调节器;参数整定TEMPERATURE SINGLE CONTROL SYSTEM DESIGN AND IMPLEMENTATIONABSTRACTFor process control system design and operation is concerned, control scheme selection and regulator parameters setting are two important content. This article based on the water tank for control object , mainly introduces temperature detection sensor, the temperature transmitter, intelligent PID controller and SCR regulator constitute a temperature control system parameter selection and design. Design zero trigger controller, realize temperature control system parameter setting and put the system into operation. Adopt experiment methods PID control parameters for engineering setting, puts forward the reasonable temperature system of the automatic control system realization and control parameter setting method.Keyword: Temperature control ;PID regulator ;Parameters setting目录第一章论绪1.1课题背景及目的目前,国外温度控制系统及仪表正朝着高精度智能化、小型化等方面快速发展。
实验5 单回路温度控制
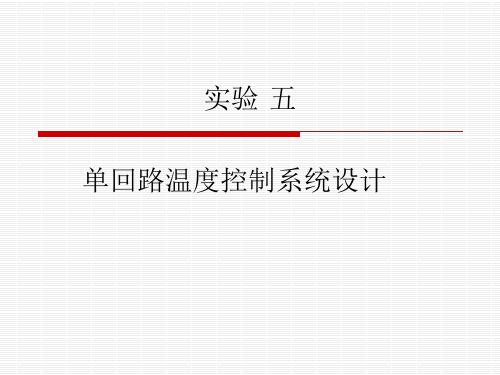
一、实验任务
1、根据仿真结果,设计模拟锅炉内胆温度单回路 温度控制系பைடு நூலகம்(夹套中冷却水); 2、用仿真PI参数为预设参数,进行单闭环温度控 制系统调节器参数的整定(约4:1); 3、记录整定过程的阶跃响应曲线 ,说明PI参数对 系统性能指标衰减比、超调量、稳定时间的影响。
2、含盘管的流量对象数学模型是什么形式? 3、用MATLAB进行下面液位单回路系统设计 和PI参数整定
W ( s) 1 s 1
四、思考题
1、消除系统的余差为什么采用PI调节器, 而不采用纯积分器? 2、在温度控制系统中,为什么用PID控制, 系统的性能并不比用PI控制有明显地改善? 3、如果锅炉内胆不采用循环水,那么锅炉 夹套的温度控制效果会怎样?
参考接线
五、预 习
1、如何建立含盘管的流量对象的数学模型?
二、实验原理
图1 锅炉内胆水温控制系统的结构示意图
模拟锅炉的内胆控制任务就是在电加热丝 不断加热的过程中保持锅炉内胆的水温不变, 即控制锅炉内胆水温等于给定值; 实验进行前必须先通过电动调节阀支路给锅 炉内胆打水,当水位上升至适当高度才开始加热, 并在加热过程中不再加水。
锅炉内胆水温的定值控制系统整定过程中至 少做两组PI参数,比较。
图2 锅炉内胆动态水温控制系统的方框图
三、实验报告
1、单回路温度定值控制系统的方案、框图、 结构图。 2、单回路温度定值控制系统接线和实验过 程; 3、记录进行调节器参数工程整定过程的阶 跃响应曲线,比较输出结果; 4、说明P、I参数大小对响应曲线性能指标 衰减比、超调量、稳定时间的影响。
实验十 锅炉动态水温度PID单回路控制
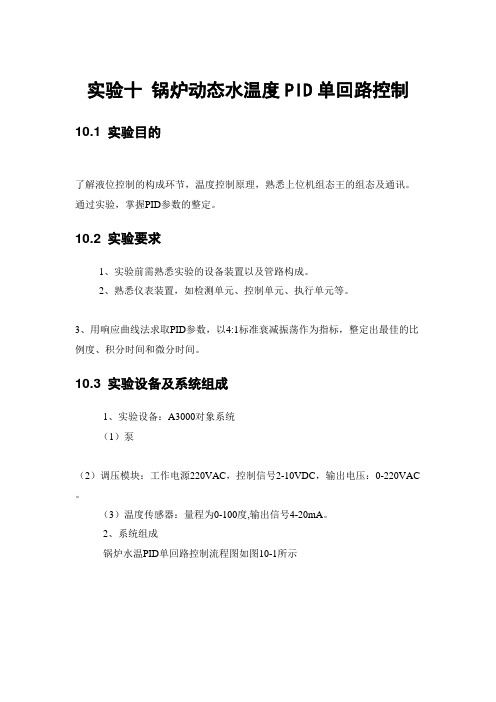
实验十锅炉动态水温度PID单回路控制10.1 实验目的了解液位控制的构成环节,温度控制原理,熟悉上位机组态王的组态及通讯。
通过实验,掌握PID参数的整定。
10.2 实验要求1、实验前需熟悉实验的设备装置以及管路构成。
2、熟悉仪表装置,如检测单元、控制单元、执行单元等。
3、用响应曲线法求取PID参数,以4:1标准衰减振荡作为指标,整定出最佳的比例度、积分时间和微分时间。
10.3 实验设备及系统组成1、实验设备:A3000对象系统(1)泵(2)调压模块:工作电源220VAC,控制信号2-10VDC,输出电压:0-220VAC 。
(3)温度传感器:量程为0-100度,输出信号4-20mA。
2、系统组成锅炉水温PID单回路控制流程图如图10-1所示图10-1 锅炉水温PID单回路控制3、测点清单测点清单如表10-1所示:表10-1 锅炉水温PID单回路控制测点清单水介质由泵P101(变频器U101驱动)从水箱V104中加压获得压头,当锅炉内的水量达到测试需要的高度后,关闭手阀QV115,打开手阀QV114,从而使锅炉、水泵P101构成一个循环回路;其中,锅炉的温度由TE101测得。
本例为定值自动调节系统,可控硅GZ101功率为操纵变量,TE101为被控变量,采用PID调节来完成。
为了加热均匀,我们使用动态循环水,把锅炉的水搅动起来。
另外电加热管功率为4.5KW,加热过程相对较快,散热过程相对较慢。
实验前手阀打开关闭情况:需要打开的手阀:QV115、QV111、QV112;需要关闭的手阀:QV103、QV113、QV114;10.4 操作步骤和调试1、编写控制器算法程序,下装调试;编写测试组态工程,连接控制器,进行联合调试。
2、依照实验内容,选择合适水流管路。
3、控制柜上电,启动变频器和水泵P101(变频器使用面板操作模式,全部为50Hz)。
4、将锅炉的水装至中间高度。
一定要超过最低液位,例如联锁保护灯亮起。
基于组态软件的温度单回路过程控制系统设计综述

工业过程控制课程设计题目:基于组态软件的温度单回路过程控制系统设计院系名称:电气工程学院专业班级:学生姓名:学号:指导教师:设计地点:设计时间:2012-6-25~2012-6-29设计成绩:指导教师:本栏由指导教师根据大纲要求审核后,填报成绩并签名。
工业过程控制课程设计任务书学生姓名专业班级学号题目基于组态软件的温度单回路过程控制系统设计课题性质课程设计课题来源自拟题目指导教师主要内容通过某种组态软件,结合实验室已有设备,按照定值系统的控制要求,根据较快较稳的性能要求,采用单闭环控制结构和PID控制规律,设计一个具有较美观组态画面和较完善组态控制程序的压力单回路过程控制系统。
任务要求1. 根据压力单回路过程控制系统的具体对象和控制要求,独立设计控制方案,正确选用过程仪表。
2. 根据压力单回路过程控制系统A/D、D/A和开关I/O的需要,正确选用过程模块。
3. 根据与计算机串行通讯的需要,正确选用RS485/RS232转换与通讯模块。
4. 运用组态软件,正确设计压力单回路过程控制系统的组态图、组态画面和组态控制程序。
5. 提交包括上述内容的课程设计报告。
主要参考资料[1] 组态王软件及其说明文件.[2] 吴勤勤. 控制仪表及装置[M].北京:化学工业出版社,2007.[3] 陈夕松,汪木兰.过程控制系统[M].北京:科学出版社,2005.8.[4] 邵裕森,戴先中.过程控制工程.北京:机械工业出版社,2000.审查意见指导教师签字:年月日摘要锅炉是化工、冶炼、发电等作为公用民用部门必不可少的主要动力设备,其产品是蒸汽,即将一次能源(煤炭、石油、提燃气等)转换为二次能源(蒸汽)。
工业锅炉是工业生产的重要设备,往往直接影响生产的正常进行和产品的质量、产量和成本。
工业锅炉又是能耗极大的设备,在整个工业生产的能源消耗中占相当大的比重。
而燃煤锅炉又是一种广泛实用的工业锅炉,广泛地应用于国民经济各个领域。
温度控制是控制系统中最为常见的控制类型,主要由温度传感器、温度调节仪、执行装置、被控对象四个部分组成。
温度单回路设计
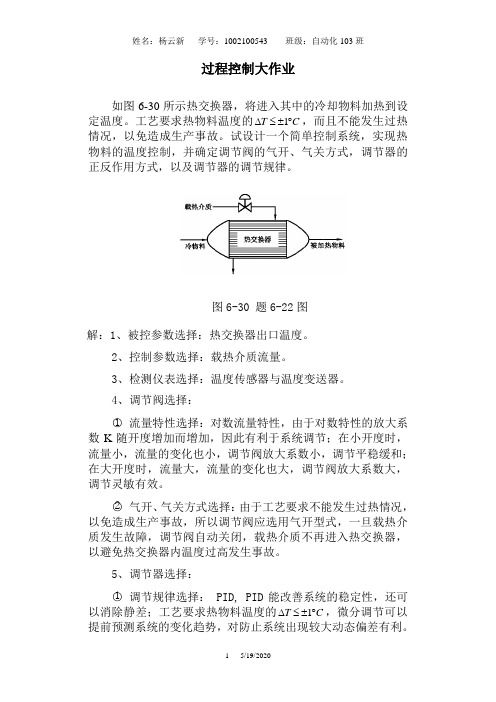
过程控制大作业如图6-30所示热交换器,将进入其中的冷却物料加热到设定温度。
工艺要求热物料温度的C∆1,而且不能发生过热≤T︒±情况,以免造成生产事故。
试设计一个简单控制系统,实现热物料的温度控制,并确定调节阀的气开、气关方式,调节器的正反作用方式,以及调节器的调节规律。
图6-30 题6-22图解:1、被控参数选择:热交换器出口温度。
2、控制参数选择:载热介质流量。
3、检测仪表选择:温度传感器与温度变送器。
4、调节阀选择:○1流量特性选择:对数流量特性,由于对数特性的放大系数K随开度增加而增加,因此有利于系统调节;在小开度时,流量小,流量的变化也小,调节阀放大系数小,调节平稳缓和;在大开度时,流量大,流量的变化也大,调节阀放大系数大,调节灵敏有效。
○2气开、气关方式选择:由于工艺要求不能发生过热情况,以免造成生产事故,所以调节阀应选用气开型式,一旦载热介质发生故障,调节阀自动关闭,载热介质不再进入热交换器,以避免热交换器内温度过高发生事故。
5、调节器选择:○1调节规律选择: PID, PID能改善系统的稳定性,还可以消除静差;工艺要求热物料温度的C∆1,微分调节可以≤T︒±提前预测系统的变化趋势,对防止系统出现较大动态偏差有利。
○2正反作用方式选择:由于载热介质流量增大,热交换器出口温度也增大,所以选反作用方式。
系统各环节正、负符号判别:被控过程:+;变送器:+;调节阀:+;根据系统构成负反馈条件:各环节符号之积必为“-”,则调节器为“-”。
6、画出控制系统流程图:如图所示。
7、画出控制系统方框图:如图所示。
8、简述控制系统工作原理:载热介质流量加大(或减小),由于TC为反作用,故其输出降低(或升高),因而气开型的调节阀关小(或开大),载热介质流量减少(或增加)以及时克服载热介质流量的影响,因而减小以致消除载热介质流量对热交换器出口物料温度的影响,提高了控制质量。
冷物料流量加大(或减小),热交换器出口物料温度降低(或升高),反作用的TC输出增加(或减少),于是气开型的调节阀开大(或关小),载热介质增加(或减少)以使热交换器出口物料温度增加(或减少),起到负反馈的控制作用。
单回路控制系统实验指导书10_1_.5

单回路控制系统PID参数整定实验指导书一、实验目的:本实验装置以管式电炉为被控对象,用Honeywell通用数字式控制器,依据所提出的技术要求,可以构成不同形式的温度控制系统。
通过实验可进一步了解和掌握控制系统的构成;各单元在控制系统中的作用、要求,调校方法;以及控制系统的参数整定。
通过控制系统实验,进一步加深和巩固过程控制系统课的学习,锻炼和提高分析问题,解决问题的能力。
二、实验中的工艺要求:1.炉中部给定温度200摄氏度。
2.主要干扰因素:①管式电炉加热丝的供电电压、频率的变化②电炉内外的热对流注:以上提出的工艺要求也可以在实验中依据具体条件而有所改变。
三、实验内容:1.设计单回路温度控制系统,并进行正确接线。
2.熟悉数字调节器的使用和参数设置的方法。
3.单回路闭环控制系统的参数整定和分析。
四、实验装置:整套实验装置由管式加热炉,交流调压器,测温元件,控制柜,计算机,台式记录仪组成。
通过控制柜上的接线端子,用导线连接,可构成单回路、串级等控制系统,并可完成对象特性的测定,调节器参数整定等实验。
实验装置仪表选型介绍:⑴主调节器:通用数字控制器Honeywell DC330E-K0-100-20⑵副调节器:通用数字控制器Honeywell DC230B-C0-0A-11⑶数字交流电压表WP-E812-00-N⑷数字交流电流表WP-E814-02-N⑸指针直流电流表2085,4~20mA⑹数字温度变送器WP-C903-02-03-HL⑺可控硅电压调整器ZK-1⑻接触式调压器TDGC2-3, 3KV A⑼热电偶K型,测量范围0~1300摄氏度⑽台式记录仪LM17-2A⑾管式加热炉1000W五、实验主要步骤:1.设计单回路温度控制系统,在实验装置上用导线连接,完成单回路控制系统的构成。
2.熟悉数字控制器(Honeywell DC3300)的使用,了解P、I、D、参数的设置方法,具体操作请参照仪表使用说明进行。
换热器出口温度单回路控制

换热器出口温度单回路控制(总11页)--本页仅作为文档封面,使用时请直接删除即可----内页可以根据需求调整合适字体及大小--1、概述换热器又叫做热交换器(heat exchanger),是化工、石油、动力、食品及其它许多工业部门的通用设备,在生产中占有重要地位。
本次课程设计我要完成换热器出口温度单回路控制系统设计,单回路控制系统又称简单控制系统,是指由一个控制对象、一个检测元件及变送器、一个调节器和一个执行器所构成的闭合系统,方框图如下:图1、单回路控制系统方框图单回路控制系统结构简单、易于分析设计,投资少、便于施工,并能满足一般生产过程的控制要求,因此在生产中得到广泛应用。
设计一个控制系统,首先应对被控对象做全面的了解。
除被控对象的动静态特性外,对于工艺过程、设备等也需要比较深入的了解;在此基础上,确定正确的控制方案,包括合理选择被控变量与操纵变量,选择合适的检测变送原件及检测位置,选用恰当的执行器、调节器以及调机器控制规律等;最后将调节器的参数整定到最佳值。
2、换热器温度控制原理以及控制方案的确定换热器温度控制过程有如下特点:换热器温度控制系统是由温度变送器、调节器、执行器和被控对象组成的闭合回路。
被调参数经检测元件测量并由温度变送器转换处理获得测量信号,测量值与给定值的差值送入调节器,调节器对偏差信号进行运算处理后输出控制作用。
换热器温度控制系统的工艺流程如下:冷流体和热流体分别通过换热器的壳程和管程,通过热传导,从而使冷流体的出口温度升高。
冷流体通过循环泵流经换热器的壳程,出口温度稳定在设定值附近。
热流体通过多级泵流经换热器的管程,与冷流体热交换后流回蓄水池,循环使用。
从控制任务要求可知,换热器温度控制系统是单点、恒值控制。
且题目要求用单回路控制系统,控制范围和控制精度要求一般,功能上无特殊要求,采用广泛使用的PID 控制。
图2 PID 控制系统原理图PID 控制是偏差比例(P )、偏差积分(I )、偏差微分(D )控制的简称。
换热器出口温度单回路控制

1、概述换热器又叫做热交换器(heat exchanger),是化工、石油、动力、食品及其它许多工业部门的通用设备,在生产中占有重要地位。
本次课程设计我要完成换热器出口温度单回路控制系统设计,单回路控制系统又称简单控制系统,是指由一个控制对象、一个检测元件及变送器、一个调节器和一个执行器所构成的闭合系统,方框图如下:图1、单回路控制系统方框图单回路控制系统结构简单、易于分析设计,投资少、便于施工,并能满足一般生产过程的控制要求,因此在生产中得到广泛应用。
设计一个控制系统,首先应对被控对象做全面的了解。
除被控对象的动静态特性外,对于工艺过程、设备等也需要比较深入的了解;在此基础上,确定正确的控制方案,包括合理选择被控变量与操纵变量,选择合适的检测变送原件及检测位置,选用恰当的执行器、调节器以及调机器控制规律等;最后将调节器的参数整定到最佳值。
2、换热器温度控制原理以及控制方案的确定换热器温度控制过程有如下特点:换热器温度控制系统是由温度变送器、调节器、执行器和被控对象组成的闭合回路。
被调参数经检测元件测量并由温度变送器转换处理获得测量信号,测量值与给定值的差值送入调节器,调节器对偏差信号进行运算处理后输出控制作用。
换热器温度控制系统的工艺流程如下:冷流体和热流体分别通过换热器的壳程和管程,通过热传导,从而使冷流体的出口温度升高。
冷流体通过循环泵流经换热器的壳程,出口温度稳定在设定值附近。
热流体通过多级泵流经换热器的管程,与冷流体热交换后流回蓄水池,循环使用。
从控制任务要求可知,换热器温度控制系统是单点、恒值控制。
且题目要求用单回路控制系统,控制范围和控制精度要求一般,功能上无特殊要求,采用广泛使用的PID 控制。
图2 PID 控制系统原理图PID 控制是偏差比例(P )、偏差积分(I )、偏差微分(D )控制的简称。
控制系统由PID 控制器和被控对象组成。
PID 控制器是一种线性控制器,它根据给定值r (t )与实际输出值y (t )构成偏差,将偏差比例、积分和微分控制,通过线性组合构成控制量,对被控对象进行控制,故称PID 控制器。
第五章 单回路控制系统
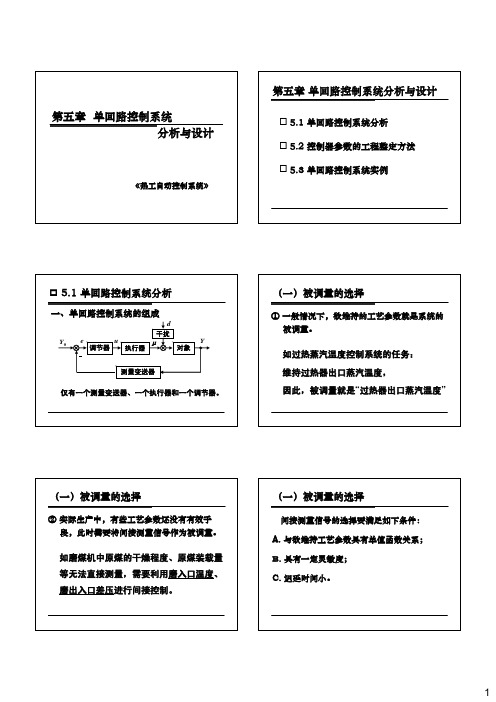
第五章单回路控制系统分析与设计《热工自动控制系统》第五章单回路控制系统分析与设计5.1 单回路控制系统分析 5.2 控制器参数的工程整定方法 5.3 单回路控制系统实例5.1 单回路控制系统分析调节器执行器对象测量变送器Y 0dY干扰euμ仅有一个测量变送器、一个执行器和一个调节器。
一、单回路控制系统的组成(一)被调量的选择如过热蒸汽温度控制系统的任务:维持过热器出口蒸汽温度,因此,被调量就是“过热器出口蒸汽温度”①一般情况下,欲维持的工艺参数就是系统的被调量。
(一)被调量的选择如磨煤机中原煤的干燥程度、原煤装载量等无法直接测量,需要利用磨入口温度、磨出入口差压进行间接控制。
②实际生产中,有些工艺参数还没有有效手段,此时需要将间接测量信号作为被调量。
(一)被调量的选择间接测量信号的选择要满足如下条件:A. 与欲维持工艺参数具有单值函数关系;B. 具有一定灵敏度;C. 迟延时间小。
(二)控制量的选择★选择工艺上允许作为控制手段的变量工艺上的主要物料量不应选择不可控的变量(二)控制量的选择工艺上的主要物料量:蒸汽流量给水流量省煤器蒸汽流量过热器汽包给水阀~MW(三)控制通道和扰动通道ty (t )跟随给定值rty (t )克服扰动dry 0y 0td (t )d 0td (t )d 0r-G P (s )G C (s )G D (s )E (s )U (s )D (s )Y (s )R (s )(四)影响控制品质的主要因素被控对象特性调节器特性——客观存在,不可改变——不同的调节器有不同的调节规律,其特点不同,应根据不同对象和生产工艺要求确定热工控制系统设计应从如下四方面入手①根据生产过程的要求,确定被控制量和控制量,拟定控制系统结构;②建立系统的数学模型(机理/试验);③在一定条件下对系统进行动态性能研究;④工程设计:控制设备选择、系统安装设计等。
5.1 单回路控制系统分析二、对象特性对控制系统的影响-G P (s )G C (s )G D (s )E (s )U (s )D (s )Y (s )R (s )两组特征参数:控制通道:放大系数K 、时间常数T 、迟延时间τ;扰动通道:放大系数K D 、时间常数T D 、迟延时间τD 。
燃烧式工业窑炉温度单回路控制方案设计
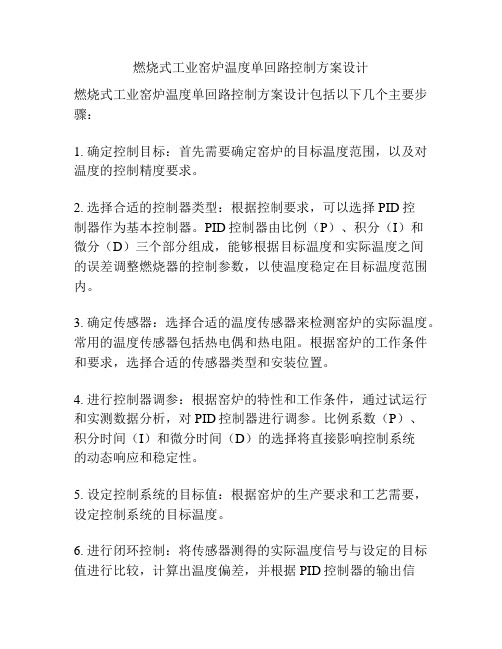
燃烧式工业窑炉温度单回路控制方案设计
燃烧式工业窑炉温度单回路控制方案设计包括以下几个主要步骤:
1. 确定控制目标:首先需要确定窑炉的目标温度范围,以及对温度的控制精度要求。
2. 选择合适的控制器类型:根据控制要求,可以选择PID控
制器作为基本控制器。
PID控制器由比例(P)、积分(I)和
微分(D)三个部分组成,能够根据目标温度和实际温度之间
的误差调整燃烧器的控制参数,以使温度稳定在目标温度范围内。
3. 确定传感器:选择合适的温度传感器来检测窑炉的实际温度。
常用的温度传感器包括热电偶和热电阻。
根据窑炉的工作条件和要求,选择合适的传感器类型和安装位置。
4. 进行控制器调参:根据窑炉的特性和工作条件,通过试运行和实测数据分析,对PID控制器进行调参。
比例系数(P)、
积分时间(I)和微分时间(D)的选择将直接影响控制系统
的动态响应和稳定性。
5. 设定控制系统的目标值:根据窑炉的生产要求和工艺需要,设定控制系统的目标温度。
6. 进行闭环控制:将传感器测得的实际温度信号与设定的目标值进行比较,计算出温度偏差,并根据PID控制器的输出信
号对燃烧器进行调节,使温度保持在目标温度范围内。
7. 监控与维护:定期对控制系统进行检查和维护,确保其正常运行。
同时,根据实际生产情况和要求,适时调整控制系统的参数。
需要注意的是,在实际设计中,还需要考虑到窑炉的加热、冷却和保温等过程,并结合温度曲线来对控制系统进行进一步优化。
此外,还要考虑窑炉内部的温度分布均匀性以及燃烧器的燃烧效率等因素。
因此,在实际工程中,可能还需要根据具体情况进行相应的调整和改进。
单回路温度控制例子详解
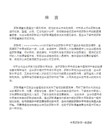
返 回 上 页 下 页
主控制模 块流程
返 回
上 页
下 页
五、输出通道的自检
间接参数判断法 指根据模拟量输入通道 的采样值的变化情况来判断 模拟量输出通道或开关量输 出通道是否正常。
例如
一个输出数字量控制泵的启停,管路已安装流量 检测,在流量检测回路没有故障情况下(上述直接参数 判断法自检可以保障),不仅可依据流量有无变化情况 来判断该开关、驱动电路、继电器、交流接触器、热 继电器、电机、泵以及现场连线是否正常,而且可以 根据泵的流量特性在线判断泵的性能优劣。
返 回 上 页 下 页
三、 PID控制算法的实现
位置式PID算法计算公式
Pout(t)=Kp*e(t)+Ki×Sum_e(t)+Kd*(e(t)-e(t-1))
基本偏差为 e(t) ,表示当前测量值与设定目标值之间 的差值,结果可以是正或负,设定目标作为被减数的话,正 数表示还没有达到设定值,负数表示已经超过了设定值。 累 计 偏 差 Sum_e(t)=e(t)+e(t-1)+e(t-2)+ … +e(1) 是 每次偏差值的代数和。 相对偏差 e(t)-e(t-1) 是用本次的基本偏差减去上一次 的基本偏差,以考察当前被控量的变化趋势,有利于快速反 应。
- 1、下载文档前请自行甄别文档内容的完整性,平台不提供额外的编辑、内容补充、找答案等附加服务。
- 2、"仅部分预览"的文档,不可在线预览部分如存在完整性等问题,可反馈申请退款(可完整预览的文档不适用该条件!)。
- 3、如文档侵犯您的权益,请联系客服反馈,我们会尽快为您处理(人工客服工作时间:9:00-18:30)。
9)温度零点标定;
功能需求
10)参数保存; 11)上位机目标温度值设定;
12)上位机实时温度波形曲线图显 示;
返 回
上 页
下 页
总体设计思路
返 回
上 页
下 页
操作模式
本系统可用3个按键实现模式切换和参数修 改操作,这3个键分别定义为模式键、数值增加 键和数值减少键。
用8个数码管显示模式和对应的参数,左边 4个数码管显示模式值,右边4个数码管显示相应 模式对应的参数值。
①设定一个标准的加温周期 T,以T为周期对温度进行采样,获 得温度测量值; ②根据设定值和测量值的偏差,进行PID运算; ③将 PID 的输出转换为 SSR 的通断时间。 PID 的输出为 0 %,则 SSR 接通时间为 0 ,即本周期无输出;如果 PID 输出为 100% ,则 SSR 接通时间为 T ,即本周期为全输出;如果 PID 的输出为 MV (百分数表示),则SSR的接通时间为 T×MV/100,断开时间为 T-T×MV/100。 例如:T=120秒,PID计算结果为1分30秒,则本次2分钟内 就应加温90秒,停30秒;又如T=120秒,PID的计算结果为1 分25秒,则本周期就应加温85秒,停35秒。
简易单回路温度控制器设计
一、功能需求和总体思路
1)设定温度显示、实时温度显示; 2)温度上、下限报警;
功能需求
3)温度上、下限报警值设定;
4)目标温度值设定; 5)放大电路放大倍数设定; 6)P、I、D控制参数的设定;
返 回
上 页
下 页
一、功能需求和总体思路
7)手动加热设定值; 8)手动/自动设定;
返 回 上 页 下 页
三、 PID控制算法的实现
位置式PID算法计算公式
Pout(t)=Kp*e(t)+Ki×Sum_e(t)+Kd*(e(t)-e(t-1))
基本偏差为 e(t) ,表示当前测量值与设定目标值之间 的差值,结果可以是正或负,设定目标作为被减数的话,正 数表示还没有达到设定值,负数表示已经超过了设定值。 累 计 偏 差 Sum_e(t)=e(t)+e(t-1)+e(t-2)+ … +e(1) 是 每次偏差值的代数和。 相对偏差 e(t)-e(t-1) 是用本次的基本偏差减去上一次 的基本偏差,以考察当前被控量的变化趋势,有利于快速反 应。
返 回
上 页
下 页
10种工作模式
模式 0 :温度设定值和温度实时值显示(前 4 位数码管显示温 度设定值,后4位显示实时温度值); 模式1:设置和显示温度上限报警值(0~1200); 模式2:设置和显示温度下限报警值(0~1200); 模式3:设置和显示温度设定值(0~1200); 模式4:设置实时温度采集放大电路的放大倍数; 模式5:设置和显示PID算法中的比例系数(0.00~50.00);
返 回 上 页 下 页
移相控制方式
周波控制方式
周波控制的 输出电路
单片机的 I/0 脚输出低电平时,控制 SSR 使加热元件接通 220V 交流电源,加热元件获得电能,温度升高; I/0 脚输出 高电平时,SSR开路,加热元件两端无电压,停止加热,对象 的温度开始下降。
返 回 上 页 下 页
控制的具体方法
PC → 控制 器 PC ← 控制 器
返回数据
3
0xaa
dataL
dataH
返 回
上 页
下 页
5、温度控制器软件流程及参考程序
控制器的软件由主控制模块、显示按键处理 模块和头文件三大模块组成。 主控制模块主要包括PID计算、控制以及温 度采集等部分。 显示按键处理模块主要包括按键扫描、按 键处理、显示刷新等部分 头文件模块主要用于全局变量声明,在其他模 块可以直接调用此模块内声明的变量。
返 回
上 页
下 页
本系统采用镍铬-镍硅(K分度)热电偶作为 温度传感器。冷端处于室温,热端为加热炉温度, 单片机的A/D通道可以直接采集热电偶信号,经 冷端温度补偿后,再查表K分度则可以得到热端 温度值。 室温的测量可以通过AD590将室温变化为电 压信号,经放大后直接送给单片机的A/D通道, 单片机程序自动完成热电偶信号的采集和冷端信 号的采集,计算出实际的温度测量值。
返 回 上 页 下 页
四、控制器和PC之间的数据通信
单回路控制器RS-232简易数据通信命令格式
命令 启动通信 停止通信 改设定值
字节数 2 2 4
字节1 0xaa 0xaa 0xaa
字节2 0x01 0x02 0x03
字节3
字节4
பைடு நூலகம்
传送方向 PC → 控制 器 PC → 控制 器
dataL
dataH
返 回 上 页 下 页
温度采集 程序流程
返 回
上 页
下 页
PID算法流程
返 回
上 页
下 页
串口中断服 务程序流程
返 回
上 页
下 页
发送数据子 程序流程
返 回
上 页
下 页
返 回
上 页
下 页
返 回 上 页 下 页
主控制模 块流程
返 回
上 页
下 页
五、输出通道的自检
间接参数判断法 指根据模拟量输入通道 的采样值的变化情况来判断 模拟量输出通道或开关量输 出通道是否正常。
例如
一个输出数字量控制泵的启停,管路已安装流量 检测,在流量检测回路没有故障情况下(上述直接参数 判断法自检可以保障),不仅可依据流量有无变化情况 来判断该开关、驱动电路、继电器、交流接触器、热 继电器、电机、泵以及现场连线是否正常,而且可以 根据泵的流量特性在线判断泵的性能优劣。
模式6:设置和显示PID算法中的积分系数(0.00~50.00);
模式7:设置和显示PID算法中的微分系数(0.00~50.00); 模式8:设置和显示手动输出值(0~100)
模式9:手动/自动切换(1:手动;0:自动)
模式10:标定和显示实时温度的零点
返 回 上 页 下 页
二、温度测控电路设计
温度检 测电路
返 回
上 页
下 页
温度控制电路
控制方式
对于加热炉的温度控制可以采用移相 控制或周波控制方式。 通过改变可控硅的导通角来控制输出电 压,从控制加热对象的温度,控制电路 相对复杂,但控制精度比较高。 通过调节一定时间周期内的供电时间比例 (即交流周波数)来控制加热对象在本周期 内获得的电能,从而控制其温度。由于控制 加温的时间比例实现起来相对简单,因此周 波控制方式在温度控制系统获得了比较广泛 的应用,本系统确定采用周波控制方式。