材料成型概论 第五讲 线棒材生产工艺
棒材车间生产工艺流程
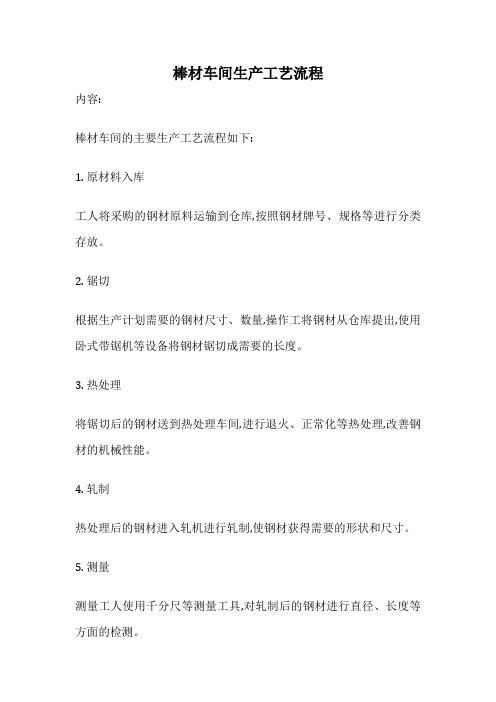
棒材车间生产工艺流程
内容:
棒材车间的主要生产工艺流程如下:
1. 原材料入库
工人将采购的钢材原料运输到仓库,按照钢材牌号、规格等进行分类存放。
2. 锯切
根据生产计划需要的钢材尺寸、数量,操作工将钢材从仓库提出,使用卧式带锯机等设备将钢材锯切成需要的长度。
3. 热处理
将锯切后的钢材送到热处理车间,进行退火、正常化等热处理,改善钢材的机械性能。
4. 轧制
热处理后的钢材进入轧机进行轧制,使钢材获得需要的形状和尺寸。
5. 测量
测量工人使用千分尺等测量工具,对轧制后的钢材进行直径、长度等方面的检测。
6. 标记
对检测合格的棒材进行打标,标明钢材牌号、规格、长度等信息。
7. 包装
工人使用牛皮纸等材料对标记完成的棒材进行包装。
8. 成品出库
按照产品编号、客户信息等对包装后的成品棒材进行堆放,然后使用叉车等设备运送到成品仓库。
以上是棒材车间从原材料入库到成品出库的主要生产工艺流程。
各环节的操作规范有利于保证棒材产品的质量。
棒材生产线工艺流程

轧钢生产工艺流程1、棒材生产线工艺流程钢坯验收→加热→轧制→倍尺剪切→冷却→剪切→检验→包装→计量→入库(1)钢坯验收〓钢坯质量是关系到成品质量的关键,必须经过检查验收。
①、钢坯验收程序包括:物卡核对、外形尺寸测量、表面质量检查、记录等。
②、钢坯验收依据钢坯技术标准和内控技术条件进行,不合格钢坯不得入炉。
(2)、钢坯加热钢坯加热是热轧生产工艺过程中的重要工序。
①、钢坯加热的目的钢坯加热的目的是提高钢的塑性,降低变形抗力,以便于轧制;正确的加热工艺,还可以消除或减轻钢坯内部组织缺陷。
钢的加热工艺与钢材质量、轧机产量、能量消耗、轧机寿命等各项技术经济指标有直接关系。
②、三段连续式加热炉所谓的三段即:预热段、加热段和均热段。
预热段的作用:利用加热烟气余热对钢坯进行预加热,以节约燃料。
(一般预加热到300~450℃)加热段的作用:对预加热钢坯再加温至1150~1250℃,它是加热炉的主要供热段,决定炉子的加热生产能力。
均热段的作用:减少钢坯内外温差及消除水冷滑道黑印,稳定均匀加热质量。
③、钢坯加热常见的几种缺陷a、过热钢坯在高温长时间加热时,极易产生过热现象。
钢坯产生过热现象主要表现在钢的组织晶粒过分长大变为粗晶组织,从而降低晶粒间的结合力,降低钢的可塑性。
过热钢在轧制时易产生拉裂,尤其边角部位。
轻微过热时钢材表面产生裂纹,影响钢材表面质量和力学性能。
为了避免产生过热缺陷,必须对加热温度和加热时间进行严格控制。
b、过烧钢坯在高温长时间加热会变成粗大的结晶组织,同时晶粒边界上的低熔点非金属化合物氧化而使结晶组织遭到破坏,使钢失去应有的强度和塑性,这种现象称为过烧。
过烧钢在轧制时会产生严重的破裂。
因此过烧是比过热更为严重的一种加热缺陷。
过烧钢除重新冶炼外无法挽救。
避免过烧的办法:合理控制加热温度和炉内氧化气氛,严格执行正确的加热制度和待轧制度,避免温度过高。
c、温度不均钢坯加热速度过快或轧制机时产量大于加热能力时易产生这种现象。
棒线材生产工艺

一、棒线材生产现状1.2007年全国钢铁总产量达到4.9亿吨,其中棒线材的产量在总产量中比例接近40%,生产线近400条,钢铁生产明显过热;2.支撑棒线材生产的三大需求点:公路建设、住宅建设和城镇化建设随着今年下半年以来全球金融动荡,国家银根紧缩以上三个的领域投资速度明显下降,需求减弱,市场疲软;3.国际上游原料价格不断上涨,成本压力不断加大。
在这种情况下作为棒线材生产厂家,要生存下来必须开发新的产品品种,贴近市场客户需求,在生产中严格执行工艺要求提高产品质量,努力增加本厂产品的市场竞争力!棒线材的种类和用途棒材——一种简单断面型材,一般以条状交货,断面形状有圆形、方形和六角形,以及建筑用螺纹钢筋(周期断面)等;线材——是热轧产品中断面面积最小,长度最长而且以盘卷状态交货的产品,断面形状有圆形、方形、六角形和异型。
国外一般将棒材的直径定义为9~300毫米,线材的直径定义为5~40毫米,呈盘卷状态交货的产品最大直径规格为40 毫米(现在已突破60mm)。
国内一般定义为棒材直径为10~50毫米,线材一般为5~10 毫米。
棒线材的用途十分广泛,除了建筑用的螺纹钢筋和线材等被直接用作成品外,一般都要经过深加工才能制成产品。
表 1.1为棒、线的分类及其用途。
表1.1 棒、线材的产品分类和用途钢种用途一般机械零件、标准件钢筋混凝土建筑汽车零件、机械零件、标准件重要得汽车零件、机械零件、标准件汽车、机械用弹簧机械零件和标准件切削刀具、钻头、模具、手工工具轴承各种不锈钢制品冷拔各种丝材、钉子、金属网丝汽车轮胎用帘线焊条表1.2 市场对部分棒、线材产品的质量要求和生产对策冷加工材:硬线、轮胎用线材本厂产品种类及部分质量要求1.螺纹钢:(1)端部剪切正直,可以满足客户采用套筒机械联接得要求;(2)钢筋表面不准有裂纹、结疤和折叠;(3)国内要求螺纹钢表面不准存在回火马氏体。
2.碳结钢:(1)表面不得有裂纹、折叠、结疤和夹杂;(2)表面允许有局部发纹、拉裂、凹坑、麻点和刮痕,但不得超出允许得偏差;(3)表面缺陷允许清除,但是清除处应圆滑无棱角,不允许横向清除,清除宽度不得小于清除深度得 5倍,清除深度不得超过该尺寸圆钢的允许负偏差;(4)不得有分层和缩孔残余,不得有高度大于5毫米的毛刺,用压力剪切的条钢端部允许有局部变形。
线棒工序工艺流程简介
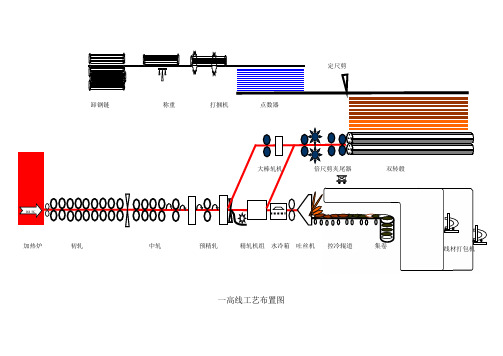
一高线工艺布置图钢坯加热炉 初轧 中轧 预精轧 精轧机组 水冷箱 吐丝机 控冷辊道 集卷 卸钢链 称重 打捆机 点数器 大棒轧机 倍尺剪夹尾器 双转毂 定尺剪 线材打包机二高线工艺布置图加 热 钢坯出炉 2 4 8 6 10 12 14 15-16 17-18 6架粗轧机 1#剪 6架中轧机 2#剪 2架中轧机 4架预精轧机组 NTM RSM 集卷站1、一高线1.1 一高线简介线棒工序一高线作业区为线棒材复合生产线,其中线材生产线是国内最早引进的现代化高速线材生产线之一,其轧机关键设备从德国德马克公司引进,电控系统从瑞典ABB公司成套引进。
2001年底,酒钢公司又在原高线厂房成品跨增加大规格直条棒材精轧机、棒材高速上料系统及精整设备,使其成为即具备盘卷线材生产能力,又具备直条棒材生产能力的线、棒复合生产线。
新建的棒材生产线关键设备达到世界领先水平,是国内第一条速度超过30m/s的单线棒材生产线,其主要机械设备由意大利西马克公司引进,电控系统从德国西门子公司引进。
一高线具有线、棒材共50万吨的年设计生产能力,其中高速棒材产能30万吨,高速线材产能20万吨,棒材捆重4吨,线材卷重1吨,目前已达到60万吨的能力,可进行线材和棒材的交替生产,以满足不同用户的需求。
一高线采用大断面连铸方坯,一火成材,大压缩率使组织均匀、致密,先进的自动张力控制和多活套无张力控制保证了轧件通条尺寸均匀,线材精轧机组采用大辊径碳化钨辊环,产品表面光洁美观,精轧前、精轧内和精轧后都采取了有效的轧件水冷措施,产品理化性能得以合理控制,其优良的加工使用性能得到了用户的一致好评。
目前一高线可生产普通碳素钢、焊接用钢、中高碳钢和合金结构钢五大类钢钟,这些钢种都具有成熟的生产工艺和质量控制手段,投放市场以来深受用户的欢迎。
1.2 一高线工艺流程生产时从原料库将150方、6米长(150mm×150mm×6000mm)的钢坯吊放到加热炉上料台架上,进行入炉加热,按加热工艺规定将钢坯加热好后,用出钢机将钢坯推出炉子进行轧制。
棒材轧制(生产)工艺

目录热轧带肋钢筋的生产工艺及车间设计摘要:从工艺配置,设备选型,工艺控制,平面布置,设备等多方面介绍了热轧带肋钢筋的生产工艺及车间平面布置的情况,并提供了热轧线上主要机组的工艺技术参数。
关键词:热轧带肋钢筋,工艺,平面布置,设备。
Abstract: Focused on the process configuration, equipment selection, process control, layout, equipment, etc., and introduces the rolled ribbed bars production craft and workshop layout, and provides the hot line of main technical parameters.Key words:Rolled ribbed bars, craft, layout, equipment。
第一张热轧带肋钢筋国内外发展概况及建厂的必要性与可行性分析1.1螺纹钢筋市场分析与前景展望螺纹钢筋广泛应用于普通混凝土结构和预应力混凝土结构,是房屋、桥梁、隧道、水坝、桩基等建筑设施的重要材料,在国民经济中占有极其重要的地位,是我国重点发展和研究的钢材品种之一。
目前,我国有四十多个厂家生产螺纹钢筋,产量逐年上升,1982年全国总产量近166万吨,除了满足国内需要外,近年来出口钢筋数量迅速增加,1981年为18万吨,1982年约30万吨;1983年预计可达35万吨。
国内生产的螺纹钢筋,规格有小6一小40毫米,其中小40毫米规格主要供出口。
钢筋的强度级别主要为GB1499一79标准规定的1级和l级钢筋。
W级钢筋产量较低。
目前,各厂家生产螺纹钢筋的工艺,基本上为热轧、随后在冷床上空冷的传统流程。
控制轧制尚未应用于生产。
仅有少数厂家开展了轧后控制冷却工艺的试验生产。
螺纹钢筋的纹型,国内l、l 级钢筋大部分按首钢、唐钢和冶金部建筑研究总院共同制定的《热轧月牙纹钢筋技术条件》生产纵横筋不相交的月牙纹钢筋,少数仍采用国际规定的人字纹型;F级钢筋则采用不带纵筋的连续螺旋型。
棒材生产工艺简述
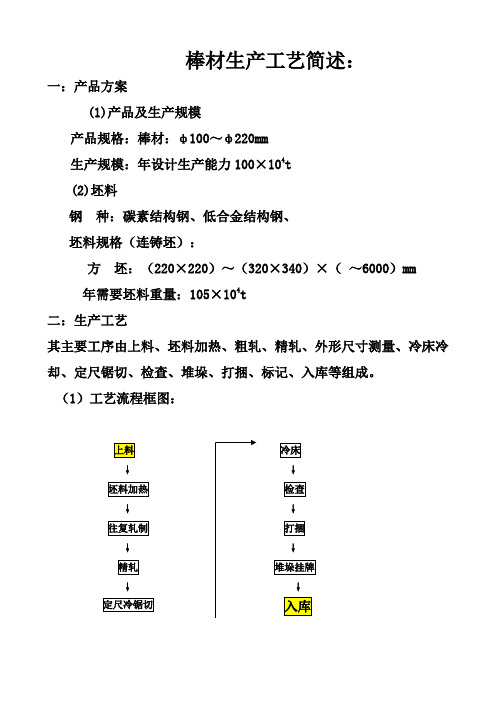
棒材生产工艺简述:一:产品方案(1)产品及生产规模产品规格:棒材:ф100~ф220mm生产规模:年设计生产能力100×104t(2)坯料钢种:碳素结构钢、低合金结构钢、坯料规格(连铸坯):方坯:(220×220)~(320×340)×(~6000)mm年需要坯料重量:105×104t二:生产工艺其主要工序由上料、坯料加热、粗轧、精轧、外形尺寸测量、冷床冷却、定尺锯切、检查、堆垛、打捆、标记、入库等组成。
(1)工艺流程框图:↓↓↓↓↓↓↓(2)工艺流程简介所有轧线设备均布置在+0.00m平台上,轧线标高为+1.40m。
当生产时,合格的连铸钢坯以单根方式从连铸热坯出坯台架送入输送辊道,输送辊道将坯料向前输送。
(坯料在输送辊道运输过程中经设在辊道中的坯料秤称重,自动显示纪录每根坯料的重量。
可不选)在输送辊道上不合格的坯料(人工右眼检查、表面缺陷、弯曲度过大和目测测长不符合要求的坯料),可由设在输送辊道侧面的剔除装置剔出。
合格的坯料输送到+2.00m 平台的辊道上,通过炉前顶钢机送入加热炉。
热送坯料进入加热炉的温度约为≈600°C左右。
当采用冷坯生产时,坯料以4~5根成组方式经输送辊道向前输送,(在输送过程中进行称重,)在辊道的另一侧设有不合格钢坯剔除装置,经人工检查表面缺陷和弯曲度达不到要求的坯料在此剔出。
坯料后经提升机构将坯料提升到+2.00m平台的辊道上,通过入炉辊道送入加热炉加热。
蓄热推钢式加热炉按不同钢种的加热制度,将坯料加热到980~1150°C。
加热好的钢坯在推钢机的推动下从炉前滑道滑出,出炉后的钢坯由输送辊道运送到粗轧机组第一架轧机中。
不合格的钢坯由钢坯剔除装置在此剔出。
钢坯首先进入粗轧机组(ф750x2)中轧制,最后送往一架两辊成品精轧机(ф650)轧制。
粗轧和中轧为往返式轧制。
合格钢坯经机前运输辊道送至第一架开坯ф750轧钢机,经机后升降台抬送与机前翻钢板翻钢,轧制4道次后,由机前移钢机送往ф750二架轧机,轧件经机后升降台抬送与机前翻钢板翻钢,轧制3道次后经二架轧机机后输送辊道,送至ф650二辊式成品精轧机,在经轧机前设有气动翻钢装置,当成品进入合金扭转导槽时,由设在机前的红外线检测仪检测到信号并发出指令,使气缸动作,完成精轧机前的翻钢,使平椭圆转为立椭圆,精轧机经过一道次轧制形成所需成品。
《棒线材生产特点及工艺》课件
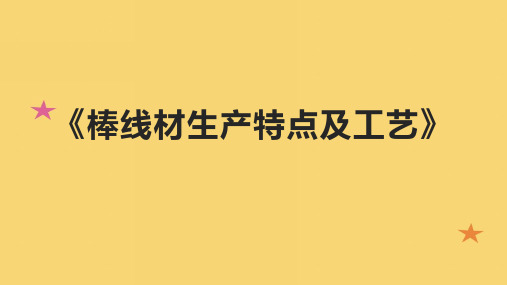
2023/12/18
12
2023/12/18
13
2023/12/18
14
生产特点及工艺
冷却和精整
线材:
精轧
水冷
吐丝机
检查
包装
散卷控制冷却
集卷
2023/12/18
15
上料台架 钢坯辊道 称重台 加热炉加热 钢坯出炉 高压水除鳞 夹送钢坯 粗轧机轧制 6HV 1#飞剪切头 中轧机组轧制6HV
2#飞剪切头 预精轧机组轧制 6HV 水箱冷却 3#飞剪切头 精轧机组轧制10 水箱冷却 减定径机组轧制 水箱冷却 线材测径 夹送吐丝
外车间热处理
收集Leabharlann 精整棒材入库2023/12/18
10
生产特点及工艺
2.2线材生产工艺
坯料:
✓ 连铸坯为主,初轧坯 ✓ 方坯:120-150mm,坯料长Max:22M ✓ 检查与清理严格
加热和轧制
冷坯加热 (连铸坯热装加热)
粗轧
中轧
(线材预精
轧)
精轧
2023/12/18
11
生产特点及工艺
✓ 线材轧制的加热温度较低 ; ✓ 步进式加热炉; ✓ 坯料两端加热温度高于中间温度; ✓ 轧制速度快,小辊径,高转速; ✓ 线材的合适轧制方式是连轧; ✓ 机架多,分工细; ✓ 轧机平立(VH布置)交替布置,线材轧机的机架数为21-28架; ✓ 线材的孔型:箱-椭圆-圆
棒 、 线 材 的 断 面 形 状 简 单 , 用 量 巨 大 , 适 于 进 行 大 规模的专业化生产。(国内占总产量40%,世界最高)
线 材 的 断 面 尺 寸 是 热 轧 材 中 最 小 的 , 所 用 的 轧 机 是 最小型的。轧件的总延伸非常大,需要的轧制道次 很多。
棒材生产工艺
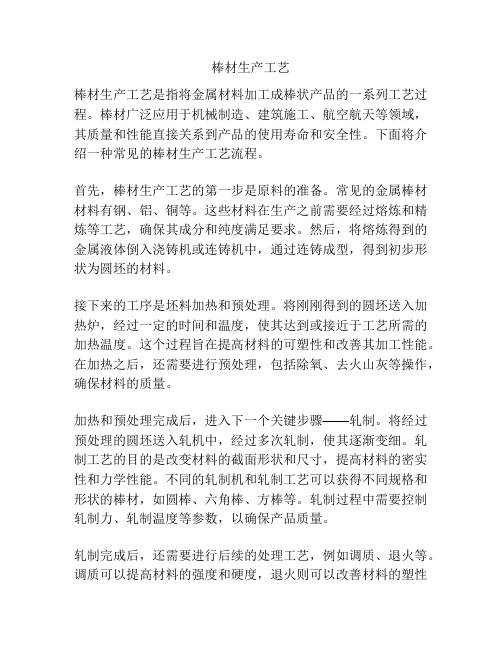
棒材生产工艺棒材生产工艺是指将金属材料加工成棒状产品的一系列工艺过程。
棒材广泛应用于机械制造、建筑施工、航空航天等领域,其质量和性能直接关系到产品的使用寿命和安全性。
下面将介绍一种常见的棒材生产工艺流程。
首先,棒材生产工艺的第一步是原料的准备。
常见的金属棒材材料有钢、铝、铜等。
这些材料在生产之前需要经过熔炼和精炼等工艺,确保其成分和纯度满足要求。
然后,将熔炼得到的金属液体倒入浇铸机或连铸机中,通过连铸成型,得到初步形状为圆坯的材料。
接下来的工序是坯料加热和预处理。
将刚刚得到的圆坯送入加热炉,经过一定的时间和温度,使其达到或接近于工艺所需的加热温度。
这个过程旨在提高材料的可塑性和改善其加工性能。
在加热之后,还需要进行预处理,包括除氧、去火山灰等操作,确保材料的质量。
加热和预处理完成后,进入下一个关键步骤——轧制。
将经过预处理的圆坯送入轧机中,经过多次轧制,使其逐渐变细。
轧制工艺的目的是改变材料的截面形状和尺寸,提高材料的密实性和力学性能。
不同的轧制机和轧制工艺可以获得不同规格和形状的棒材,如圆棒、六角棒、方棒等。
轧制过程中需要控制轧制力、轧制温度等参数,以确保产品质量。
轧制完成后,还需要进行后续的处理工艺,例如调质、退火等。
调质可以提高材料的强度和硬度,退火则可以改善材料的塑性和韧性。
这些处理工艺一般需要在特定的温度和时间条件下进行,以达到预期的效果。
最后,对生产的棒材进行表面处理、检验和包装等工序。
表面处理包括酸洗、喷砂等,以去除材料表面的氧化皮、污染物等。
检验过程需要对棒材的尺寸、形状、化学成分等进行检测,以确保产品符合标准要求。
最后,将检验合格的棒材经过包装,方便存储、运输和销售。
综上所述,棒材生产工艺是一个复杂的过程,涉及多个环节和工序。
每个步骤都需要严格控制和操作,以确保产品质量。
随着科技的进步和工艺的创新,棒材的生产工艺也在不断改进和发展,以满足不断变化的市场需求。
棒材工艺流程
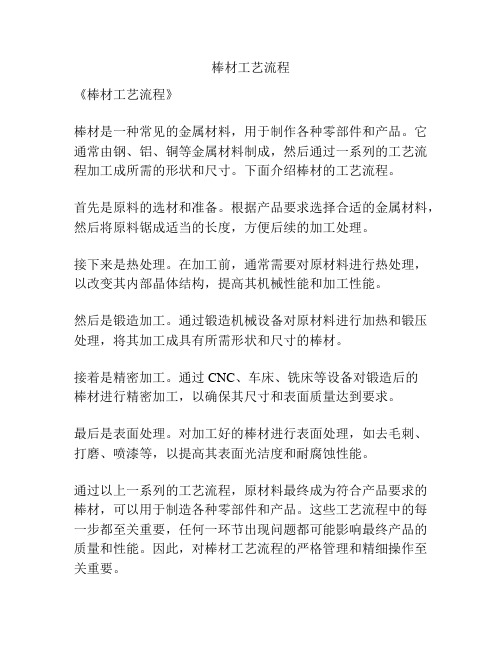
棒材工艺流程
《棒材工艺流程》
棒材是一种常见的金属材料,用于制作各种零部件和产品。
它通常由钢、铝、铜等金属材料制成,然后通过一系列的工艺流程加工成所需的形状和尺寸。
下面介绍棒材的工艺流程。
首先是原料的选材和准备。
根据产品要求选择合适的金属材料,然后将原料锯成适当的长度,方便后续的加工处理。
接下来是热处理。
在加工前,通常需要对原材料进行热处理,以改变其内部晶体结构,提高其机械性能和加工性能。
然后是锻造加工。
通过锻造机械设备对原材料进行加热和锻压处理,将其加工成具有所需形状和尺寸的棒材。
接着是精密加工。
通过CNC、车床、铣床等设备对锻造后的
棒材进行精密加工,以确保其尺寸和表面质量达到要求。
最后是表面处理。
对加工好的棒材进行表面处理,如去毛刺、打磨、喷漆等,以提高其表面光洁度和耐腐蚀性能。
通过以上一系列的工艺流程,原材料最终成为符合产品要求的棒材,可以用于制造各种零部件和产品。
这些工艺流程中的每一步都至关重要,任何一环节出现问题都可能影响最终产品的质量和性能。
因此,对棒材工艺流程的严格管理和精细操作至关重要。
棒材车间生产工艺流程

棒材车间生产工艺流程英文回答:The production process in a bar mill workshop typically involves several steps to transform raw materials into finished products. Here is a general outline of the process:1. Raw Material Preparation: The first step is to prepare the raw materials, which usually consist of steel billets or ingots. These raw materials are inspected for quality and then heated in a furnace to a specific temperature for further processing.2. Heating and Rolling: Once the raw materials are heated to the desired temperature, they are fed into arolling mill. In the rolling mill, the heated billets or ingots are passed through a series of rollers that apply pressure to shape and form the material into long,cylindrical bars. This process is called hot rolling.3. Cooling and Cutting: After the bars are rolled, they are typically cooled in a water or air cooling bed toreduce their temperature. Once cooled, the bars are cutinto desired lengths using a cutting machine. The cut bars are then inspected for quality and any defects arerectified.4. Surface Treatment: Depending on the requirements of the end product, the bars may undergo surface treatment processes such as descaling, shot blasting, or pickling. These processes help remove any impurities or scale fromthe surface of the bars, ensuring a smooth and clean finish.5. Quality Control: Throughout the production process, quality control measures are implemented to ensure that the bars meet the required specifications. This includesregular inspections, testing of mechanical properties, and dimensional checks.6. Packaging and Storage: Once the bars pass thequality control checks, they are packaged and prepared for shipment or storage. Packaging methods may vary dependingon the size and type of bars produced. The finished barsare stored in a designated area until they are ready to be transported to customers.中文回答:棒材车间的生产工艺流程通常包括几个步骤,将原材料转化为成品。
棒材制作工艺

棒材制作工艺
棒材制作工艺是一种重要的制造工艺,用于生产各种类型的棒材产品。
这种工艺通常包括以下步骤:原材料的准备和加工、毛坯的铸造和轧制、成品的精加工和检验等。
在制作棒材的过程中,原材料的选择和处理非常关键。
通常使用的原材料包括钢、铝、铜等金属材料,以及塑料、木材等非金属材料。
这些原材料需要进行一系列的处理,如加热、冷却、拉伸、裁剪等,以获得所需的形状和尺寸。
随后,毛坯将被铸造或轧制成所需的形状和尺寸。
铸造是通过将熔化的金属或其他材料倒入模具中,并让其凝固成为所需形状的过程。
而轧制则是通过将毛坯通入轧机中,经过多次轧制和拉伸,以达到所需的精度和尺寸。
最后,成品需要进行精加工和检验。
这包括切割、钻孔、打磨、检测等步骤。
这些步骤旨在确保产品符合规格要求,并满足客户的需求。
总的来说,棒材制作工艺是一项复杂的制造工艺,需要高度的专业技能和精益求精的精神。
只有通过良好的原材料选择和加工、精确的生产工艺,以及严格的质量控制,才能生产出高质量的棒材产品。
- 1 -。
线材生产工艺及特点 ppt课件
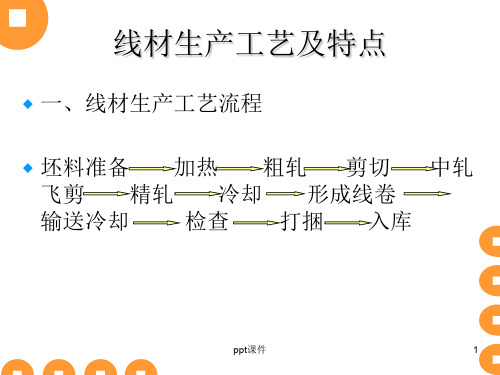
ppt课件
24
ppt课件
25
连续式线材轧机的精轧机种类
水平二辊式:精轧机可分为1~2组,每组6~8架二
辊水平轧机。轧件在每组精轧机中实现2~4线扭转 轧制、轧制速度为25~30m/s,盘重为500~1000kg。
平-立交替式:即精轧机是由水平辊和立辊交替布置
的4~6架二辊轧机组成,轧机采用单独传动。轧件 在精轧机组中实行多路单线无扭轧制,为与粗轧、
一中轧机组多用二辊水平轧机,二中轧机组有使用 二辊水平轧机的,也有使用平-立交替轧机的。也有 的中轧机组全部使用平-立交替轧机。
中轧机组位于粗轧机组之后,所轧制的轧件尺寸与 粗轧机组相比较小,所以中轧机组轧辊直径一般要
比粗轧机组小。
ppt课件
14
(3)精轧机组的布置形式
1)横列式布置:精轧机组采用横列式布置,
中轧机组平衡,一般精轧分四路。轧制速度为30~
45m/s,盘重为500~1000kg。该轧机设备重量大, 占地面积大,而且电控设备复杂。
ppt课件
26
45°无扭轧机:该轧机实际上是平-立交替式
轧机的变种。虽然前后两架轧机的轧辊轴线 是垂直的,但均与地面交45°角。由2~4路, 每路由8~1O架二辊轧机组成,采用集体传动。
耳子
线材表面沿长度方向形成的条状凸起叫耳子。 耳子可分为双边耳子,单边耳子和错边耳子。
ppt课件
34
ppt课件
35
双边耳子一般是由于来料尺寸过大,造成金
属在成品过充满而形成双边耳子。钢温低、 轧件在成品孔中倒钢等原因也会产生双边耳 子。为防止双边耳子,应调整好来料尺寸, 使轧件正确进入成品孔。并把入口导卫装正, 安牢,将轧件扶正。
材料成型概论-第五讲-线棒材生产工艺

预应力钢丝及钢绞线
子!I二 纯
rilJ 1ÚI
高应力弹簧钢丝
焊丝用线材
飞雪/
冷镦钢丝用线材:螺钉、螺帽、螺栓等紧固件
轴承钢丝用线材 滚珠、滚锥、滚针
5.3 线材的生产工艺及设备
5.3.1 线材热轧工艺一般流程
坯料→加热→粗轧→中轧→预精轧→精轧→控制冷 却 →吐丝机→散卷控制冷却→集卷→钩式冷却→检 验→ 标记包装。
( 2 ) 1988 ~ 1992 年 , 国 产 线 材 有 很 大 改 观 , 高 线 比 近 30%,线材自给率达100%,进口逐年减少,出口 逐年增加,历 史性变化的1991年,线材出口大于进口。
(3)1993~1994年,国产线材大幅增长,但满足不了国 民经济迅猛增长的需求,造成线材大量进口,线材自给率降 到历史最低点57%。
我国线材轧Байду номын сангаас情况
目前我国拥有线材轧机近110套,其中复二重轧机占一 半,横列式线材轧机有近30套(将逐步被淘汰);其余40多 套属于高速线材轧机,其中从国外引进的高水平线材轧机有 20多套,国产高速线材轧机有近20套。2004年,全国线材生 产中,高线比已经超过55%;但优质硬线比约10%,精炼比 不 到30%。
从20世纪90年代开始,我国线材高速化改造达到了高 潮, 到2007年,我国已建成高速线材生产线58条。当前,由 于普 线市场竞争越来越激烈,利润空间越来越小,国内各高 线厂 都把目光投向利润空间相对较高的优线产品的开发与生 产。
我国线材轧机情况
(l)1986年前,无高速线材轧机,高线比为零;线材自 给率为60%。国内线材缺口很大,每年进口线材200~300万 吨。国产线材质量较差,盘重小、化学成分不稳定、表面质 量差、尺寸公差大、性能也较差等。
棒材工艺流程

棒材工艺流程棒材是一种常见的金属制品,广泛应用于建筑、机械制造和汽车制造等行业。
下面是一篇关于棒材工艺流程的简要介绍,主要包括原材料准备、熔炼、连铸、轧制和检测等环节。
首先,棒材的制造需要准备合适的原材料。
一般来说,金属棒材常用的原材料有高品质的铁矿石、废金属和铜等。
这些原材料需要经过矿石破碎、矿石选矿和冶炼等工艺,将其转化为合适的金属材料。
接下来是熔炼环节。
将准备好的原材料投入到高温熔炉中,经过高温融化和混合反应,使金属材料达到一定的纯度和均质性。
通过控制熔炼的温度、时间以及添加适量的助熔剂,可以进一步改善金属的物理和化学性质。
然后是连铸环节。
在熔融的金属材料进一步凝固之前,将其倒入连铸机中,通过连续铸造将其转化为连续的坯料。
连铸机主要由结晶器、导向器和铸坯机构成,通过合理的工艺参数选择和控制,可以获得理想的铸坯形状和尺寸。
接下来是轧制环节。
将连铸得到的坯料送入轧机进行粗轧、精轧和终轧等多道次变形加工。
轧机通常由多台辊组成,通过轧制力的作用,将坯料逐渐压扁、拉长,并通过不同的辊型和通道设计,实现不同截面形状和尺寸的棒材。
最后是检测环节。
在棒材制造的过程中,需要对产品进行质量检测和控制,以保证产品的合格率和性能。
常见的检测方法包括外观检验、尺寸测量、力学性能测试和化学成分分析等。
通过严格的质量控制,可以确保棒材达到设计要求,并满足客户的需求。
综上所述,棒材的制造过程包括原材料准备、熔炼、连铸、轧制和检测等环节。
每个环节都需要严格按照工艺要求和质量标准进行操作,从而获得符合要求的棒材产品。
随着科学技术的发展和工艺装备的更新,棒材制造技术也在不断进步,以满足市场对高质量金属产品的需求。
棒线材生产工艺培训
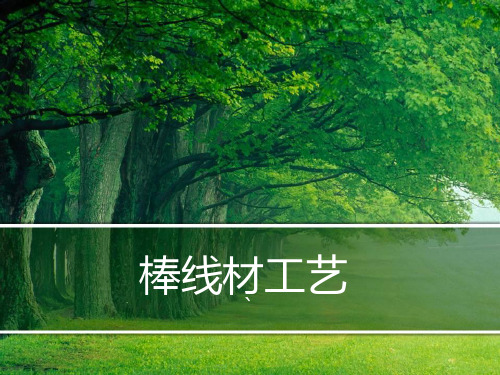
棒材主要设备及工艺特点
全轧线共有18架轧机,分为粗轧、中轧、精轧机组。
轧机平-立交替布置的轧机组成,其中:1-10架为闭口轧机, 11-18架为短应力线轧机,第14、16、18架为平/立可转换轧 机,各架轧机均由直流电机单独传动,在中轧机组及精轧机 组前各设一台启停式飞剪对轧件进行切头、切尾及事故碎断。 整个轧线采用全连续、全无扭轧制,粗、中轧机组采用微张 力轧制,精轧机组之间和精轧机组各架轧机之间均设置立活 套,实行无张力控制轧制。根据产品规格的不同,粗轧机组 轧出的Ф72mm圆轧件在中轧和精轧机组轧制6~12道次, Ф12~40mm带肋钢筋(其中:Ф12~22mm带肋钢筋用切分 法生产) 、Ф18-22树脂锚杆用热轧钢筋。成品最大轧制速 度为18m/s。
非常错误的,加热温度是钢坯在加热炉加热时检 测元件检测到的炉膛温度。 开轧温度过高容易发生堆钢事故,并且燃料消耗 增加,开轧温度过低又使轧机负载增大,致使电 力消耗变大,并切对轧辊、导卫等都带来不利。 所以生产过程中控制好开轧温度是非常关键的。 根据钢种不同开轧温度也不相同,例如我们现在 生产使用开轧温度为1000°±50°。
我厂使用的几种滚动导卫
中轧滚动导卫
精轧导卫
我厂使用的几种滚动导卫
预切分滚动进口导卫
四切分切分导卫
活套动作过程
立式活套和水平活套的区别只是起套方向 不同,水平活套是气缸推动起套辊向水平 方向运动,而立式活套是起套辊向上抬起。
活套台
压辊
起套辊
起套辊
压辊
轧机
压辊
轧机
孔型系统及其特点
棒材的孔型系统:平箱→方箱→ 椭圆→圆 →… →椭圆→圆, 即除了第一和第二道次外都是椭圆与圆交替布置的孔型系统。
棒材加工工艺流程详细

棒材加工工艺流程详细English Answer:The process of manufacturing bars from billets involves several critical steps that transform the raw material into the desired final product. Here's a detailed overview of the typical bar processing workflow:1. Billet Preparation: The process starts with billets, which are semi-finished steel blocks of varying shapes and sizes. These billets are carefully inspected and prepared to ensure they meet the required specifications.2. Heating: Billets are heated to a specific temperature range in a furnace to make them pliable and suitable for further processing. This step is crucial to achieve the desired material properties and facilitate subsequent operations.3. Rolling: The heated billets are passed through aseries of rollers, which gradually reduce their cross-sectional area and increase their length. This process, known as rolling, imparts the desired shape and dimensionsto the bars.4. Cooling: After rolling, the bars are cooled in a controlled manner to achieve the desired metallurgical properties. Cooling can be achieved through various methods, such as air cooling, water cooling, or controlled cooling.5. Finishing: The cooled bars undergo various finishing processes to enhance their surface quality and meetspecific requirements. These processes may include straightening, cutting, and grinding.6. Inspection and Testing: The finished bars are thoroughly inspected and tested to ensure they adhere tothe desired specifications. This includes dimensional checks, surface quality assessment, and mechanical property testing.7. Packaging and Storage: Once inspected and approved,the bars are packaged and stored appropriately to prevent damage and maintain their quality until they are ready for use in downstream applications.中文回答:棒材加工工艺流程。
棒线材的生产工艺

棒线材的生产工艺
棒线材是一种常用的金属制品,具有广泛的应用领域,如建筑、汽车、电子等。
它的生产工艺主要包括原料准备、熔炼、连铸、轧制和冷加工等环节。
首先是原料准备环节。
棒线材的主要原料是铝合金、铜合金、钢等金属,必须经过精细的配料和熔炼处理。
在配料时,需要根据产品的要求确定合适的配比,将各种金属原料按比例混合。
然后,将混合好的原料送入熔炉进行熔炼。
熔炼过程中,需要控制好温度和气氛的参数,以确保原料完全熔化。
接下来是连铸环节。
熔炼好的金属液体通过连铸工艺被注入到连铸机中。
连铸机上装有多个均匀排列的结晶器,金属液体经过结晶器内的冷却水,逐渐凝固形成棒线材的预制坯料。
连铸过程中,为了保证产品质量,需要控制好冷却水的温度和流量,以及坯料的拉拔速度。
然后是轧制环节。
通过连铸得到的预制坯料需要经过轧机的轧制加工,使其变为符合规格要求的棒线材。
轧制过程中,预制坯料首先经过粗轧机,使其变形为长条形的棒线坯。
然后通过中轧机和精轧机进行多次轧制,使其直径逐渐减小,同时恢复其金属的纤维结构和晶粒度。
最后是冷加工环节。
轧制好的棒线材还需要经过冷加工的处理,以进一步改善其物理性能。
常见的冷加工方式包括拉拔、拉伸、扭转等。
通过冷加工,棒线材的直径和长度可以进一步调整,同时可以提高其强度、硬度和韧性等性能。
总之,棒线材的生产工艺包括原料准备、熔炼、连铸、轧制和冷加工等环节。
每个环节都需要精确控制各项参数,以保证最终产品的质量和性能。
只有通过严格的生产工艺流程和质量控制措施,才能生产出符合要求的棒线材产品。
棒材工艺教程轧制原理

棒材工艺教程:轧制原理1. 简介轧制是一种常用的金属加工工艺,用于将金属材料加工成条形、面板或棒材的形状。
棒材是一种常见的金属产品,广泛应用于建筑、制造和其他行业。
本教程将介绍棒材的轧制原理及相关工艺。
2. 轧制方法棒材的轧制主要有两种方法,分别是冷轧和热轧。
2.1 冷轧冷轧是指在常温下对金属进行轧制。
其主要工艺流程包括下述几个步骤:1.材料准备:选择适当的金属材料,并根据需要将其切割成合适的尺寸。
2.加热退火:将材料加热至一定温度,然后进行退火处理,以改善材料的塑性和可加工性。
3.直道轧制:将加热退火后的材料送入轧辊间,通过轧制机构的作用,将材料逐渐压制成所需的形状。
轧辊间的间隙可以根据需要进行调整,以控制棒材尺寸的精度。
4.冷却处理:轧制后的棒材需要进行冷却处理,以提高材料的强度和硬度。
5.切割定尺:将冷却后的棒材按照需要的长度进行切割。
2.2 热轧热轧是指在高温下对金属进行轧制。
其工艺流程与冷轧有所差异:1.加热:将金属材料加热至合适的温度,通常高于其再结晶温度。
高温能够提高金属的塑性,使得轧制更加容易进行。
2.轧制:将加热后的金属材料送入预热轧机中,通过轧辊的作用将材料压制成所需的形状。
3.冷却处理:热轧后的棒材需要进行冷却处理,以提高材料的强度和硬度。
4.切割定尺:将冷却后的棒材按照需要的长度进行切割。
3. 轧制原理3.1 原理介绍轧制原理可以简单地描述为:通过轧辊施加的力使金属材料发生塑性变形,从而改变其断面形状和尺寸。
轧制过程中,材料在轧辊间经历了挤压、剪切、弯曲等力的作用,最终实现了棒材的塑性变形。
3.2 轧辊和轧制力轧辊是轧机中最重要的部件之一,它们负责施加压力,并将材料引导到适当位置。
轧制力由辊缝、轧制速度、材料性质等因素决定。
对于冷轧,辊缝较小,轧制力会比热轧大;而对于热轧,辊缝较大,轧制力较小。
3.3 形变和再结晶轧制过程中,金属材料会发生塑性变形。
随着变形的进行,材料的应力和形变逐渐增加,超过一定程度后,材料内部会发生再结晶现象。
- 1、下载文档前请自行甄别文档内容的完整性,平台不提供额外的编辑、内容补充、找答案等附加服务。
- 2、"仅部分预览"的文档,不可在线预览部分如存在完整性等问题,可反馈申请退款(可完整预览的文档不适用该条件!)。
- 3、如文档侵犯您的权益,请联系客服反馈,我们会尽快为您处理(人工客服工作时间:9:00-18:30)。
表5.1 棒线材的产品品种及用途
注:碳钢及低合金结构钢的碳当量Wce
钢 种
碳钢 中、高碳钢 焊接用钢 弹簧钢 滚动轴承钢 冷顶锻用钢 不锈钢 工具钢 低合金钢
制品名称及用途
混凝土配筋、镀锌低碳钢丝、制钉、螺丝、金属网、电缆、 通讯线 螺丝、自行车辐条、胶管钢丝、发条、钢丝床、伞骨、衣架、 钢丝绳、预应力钢丝、钢绞线 焊条、焊丝 弹簧、钢丝 滚珠、滚柱 铆钉、螺栓、螺帽 防腐金属网、不锈钢焊条、耐热及非磁弹簧、高级铆钉、医 用缝合针 量具、刀具、模具、制针、钟表用钢丝、工具、琴弦 螺纹钢筋
3. 线材轧制的特点
3.高速无扭转轧机具有特殊的孔型系统
三角-弧边三角-圆孔型
椭圆-椭圆-圆孔型
弧菱-弧菱-圆孔型
椭-圆-椭-圆孔型
平-平-椭圆-圆孔型
5.3.2 线材生产特点
4.线材轧机形式及布置特点
二辊式或三辊式开坯机、平/立二辊式轧机,悬臂式 轧机、45°无扭轧机、Y型轧机、双机座复二重式。 开坯机 + 连轧机组的半连续式布置 粗轧连轧机组 + 复二重围盘式的半连续式布置 全连续式布置 轧机台数多、布置较复杂
5.3.2 线材生产特点
2.加热特点 加热温度尽量高,坯料尾部温度稍高; 加热氧化脱碳少,钢坯不发生扭曲,不产生过热 过烧等; 加热炉采用端进侧出,或侧进侧出; 加热炉有:推钢式、步进式两种。
线材加热炉型式有两种
推钢式加热炉
通常为端进侧出 式,炉尾有推钢 机 ,炉头出钢机, 将钢坯推出加热炉
步进式加热炉
水箱
Water Boxes
夹送辊
Pinch Roll
往P/F线 to P/F Line
线材生产工序和车间布置
线材生产工序和车间布置
5.3.2 线材生产特点
由于线材断面小,长度大,并且要求的尺 寸精确和表面质量较高。生产特点如下: 1.坯料特点 2.加热特点 3.线材轧制的特点 4.线材轧机形式及布置特点 5.线材精整的特点
5.2 线棒材的品种及分类
按断面形状分: 圆、方、六角、扇形和异形断面、螺纹钢(带肋钢筋) 按化学成分分: 1.软线(普通低碳钢)- 2.硬线(中高碳素钢)- 3.焊线(焊条用)- 4.合金钢线材- 4.不锈钢线材及特殊钢线材(轴承、工具、精密等)
80-90%
5.2 线材的品种及分类
按用途分类
1.热轧状态直接使用—— 建筑螺纹钢筋和线材包装 用; 2.二次加工后使用—— 拔丝、制钉等金属制品生产 商品钢丝及专用弹簧钢丝、焊丝、冷镦钢丝、 镀锌钢丝、通讯线、轮胎钢丝及钢帘线、 高强度钢丝及钢绞线、轴承钢丝、工具钢丝、 不锈钢丝、各种钢丝绳、钢钉、标准件等等。 发达国家线材加工比在70%左右,我国为30%左右
Water Box
C&D剪
C&D Shear
侧活套 Sidelooper
水箱 Water Boxes
减定径机 Reducing and Sizing Mill 3#A 3#B 4#
吐丝机 Laying Head
STELMOR冷却线 STELMOR Cooling Line
集卷 Reform Station
5.2 棒材的品种及分类
棒材:
全部是传统型式的轧机设备,最新建设的生产线平、 立交替布置,精轧部分的轧机可旋转位置,呈水平和 垂直两种状态布置。水平布置可切分轧制;平、立交 替为单根轧制。
高速棒材: 精轧机组为高线机型,即辊环悬臂式轧机。 大棒材: 在传统轧机前面加开坯机,用于生产更大规格的 产品
高线轧机种类: 按轧辊的组装形式分
Y型轧机由7~13 架组成连轧机组 每架均由三个互 成120°布置的盘 状轧辊成。 相邻倒置布置, 轧制时无须扭转 翻钢。
高线轧机种类: 按轧辊的组装形式分
45°轧机由8~10 架组成连轧机组 每对轧辊均与地 平面成45°角, 前后两架轧辊轴 线互成90 °布置 轧制时无须扭转 翻钢。由1台或 2台直流电机带动
(1)初轧坯
对钢坯内部质量的要求是: (1)钢坯低倍组织不得有肉眼可见的缩孔、分层、 气泡、裂缝、白点等; (2)对优质碳索结构钢和弹簧钢、轴承钢、冷撤钢 等合金钢种,根据需方要求做高倍检验,检查脱碳 层,检查钢中非金属夹杂,检查晶粒度是否达到规 定的要求。
(2)连铸坯
连铸坯最常见的表面缺陷是针孔及氧化结疤。 针孔要求磨去,严重时报废。100mm×100mm的高碳 钢方坯允许有2mm深的针孔。氧化结疤局部磨光即 可清除。 连铸坯因表面缺陷报废量约为钢锭的一半。严 格控制冶炼及浇注过程可以生产无缺陷连铸坯。 连铸坯的内部质量常以偏析、中心疏松和裂纹 的有无和轻重为判断依据。
通常为侧进侧出 式,炉内进钢辊 道.
一、钢坯加热温度 钢坯的加热温度主要根据Fe-C相图中组织转变温度来 确定,同时,必须满足轧钢工艺的要求,一般钢坯在 1050~1250℃ 。具体确定加热温度还要看钢种、钢坯 断面规格、控冷开始温度和轧钢工艺及设备的条件。
3. 线材轧制的特点
1.小辊径、高转速 线材小线径、大盘重和线材质量之间矛盾 轧制速度,100m/s 2.机架多、分工细 (一般21~25架) 粗轧机组:大延伸、低转速、多槽轧制 中轧机组: 精轧机组:小延伸、高转速、单槽多线轧制 增大
45优质碳素结构钢,直径6.5mm热轧盘条,C级精度、第5级 盘重(大于2000kg)。
棒材牌号表示
热轧带肋钢筋HRB : Hot rolled Ribbed Bars 《热轧带肋钢筋》新标准(GB1499.2-2007)
HRB 335 ——热轧带肋螺纹钢 σb≥ 455MPa ( 20MnSi ) HRB 400 ——热轧带肋螺纹钢 σb≥ 540MPa HRB 500 ——热轧带肋螺纹钢 σb≥ 630MPa
5.3.2 线材生产特点
1.坯料特点
要求:终轧温度、小线径5.5~22mm,大盘重 采用:初轧坯 连铸坯, 尺寸:90x90~160x160 mm 最大断面160mm,最长22m 坯料表面/内部质量高
(1)初轧坯
对钢坯表面质量的要求是: (1)钢坯端面不得有缩孔、尾孔和分层; (2)钢坯表面应无裂缝、折叠、耳子、结疤、拉裂 和夹杂等缺陷; (3)钢坯表面缺陷必须沿纵向加工清除,清除处应 圆滑、无棱角,清除宽度不得小于清除深度的5 倍,表面清理深度不大于公称厚度的8%。
我国线材轧机情况
(l)1986年前,无高速线材轧机,高线比为零;线材自 给率为60%。国内线材缺口很大,每年进口线材200~300万 吨。国产线材质量较差,盘重小、化学成分不稳定、表面质 量差、尺寸公差大、性能也较差等。 (2 ) 1988~1992年,国产线材有很大改观,高线比近 30%,线材自给率达100%,进口逐年减少,出口逐年增加,历 史性变化的1991年,线材出口大于进口。 (3)1993~1994年,国产线材大幅增长,但满足不了国 民经济迅猛增长的需求,造成线材大量进口,线材自给率降 到历史最低点57%。 (4)1995~1999年,国产线材年净增长200万吨以上, 高速线材产量逐年大幅度提高,到1999年高线比达46.7%,这 是一个可喜变化。
1966年世界上第一套高 速线材轧机诞生,轧制 速度达46.6米/秒。 经过了40多年的发展, 目前,高线轧机已经发 展到第六代,最高速度 达到了140米/秒。
高线轧机的发展:按轧制速度分
第一代,1966~1969年,轧制速度43~50m/s; 第二代,1970~1975年,轧制速度50~60m/s; 第三代,1976~1978年,轧制速度61~75m/s; 第四代,1979~1980年,轧制速度75~80m/s; 第五代,1981~1985年,轧制速度80~100m/s; 第六代,1986年以后,轧制速度100~120m/s。
冷轧带肋钢筋CRB : Cool rolled Ribbed Bars
CRB 550 ——冷轧带肋螺纹钢
预应力钢丝及钢绞线
高应力弹簧钢丝
焊丝用线材
冷镦钢丝用线材:螺钉、螺帽、螺栓等紧固件
轴承钢丝用线材 滚珠、滚锥、滚针
5.3 线材的生产工艺及设备
5.3.1 线材热轧工艺一般流程
坯料→加热→粗轧→中轧→预精轧→精轧→控制冷 却→吐丝机→散卷控制冷却→集卷→钩式冷却→检 验→标记包装。
棒线材的规格和牌号举例
SAE1008 冷拔丝用材, 美国汽车工程师协会标 准;10表示Mn含量低 于1%;08表示碳含量。
《热轧带肋钢筋》新标 准(GB1499.2-2007) 沙钢 BS460B 碳结钢
线材牌号表示
线材牌号
热轧盘条φ6.5-C-V-GB/T14981-94/45-GB699-1999
技术特点
人工喂钢,盘重80 ~ 90kg
125kg 300kg ~ 350kg
20世纪60年代 20世纪70年代
Y型轧机 摩根45°无扭 轧机
>1000kg
普线与高线轧机的区分
40m/s是区分高低速轧机的分水岭 普线轧机:低于40m/s的轧制速度; 高速线材轧机:高于40m/s轧制速度。
高速线材轧机的发展
5.1 线棒材生产的一般概念
线材:φ4.6~38 mm 热轧型材中断面最小。
细长且成盘卷状态交货,称为线材或盘条。
棒材:
常见的品种是圆断面和螺纹钢,以直条形式交货 除此之外还有其他现状的断面棒材,如:方形、 扁形、六角形、八角形等 常见的规格φ14~28 mm ,最大的可达 φ380
mm
5.1 线棒材生产的一般概念
材料成型概论
第一讲 第二讲 第三讲 第四讲 第五讲 第六讲 第七讲 第八讲 第九讲 第十讲 材料成型概述 炼钢炼铁生产 材料塑性成型的基础 钢坯型钢生产 线棒材生产 板带钢生产 钢管生产 挤压拉拔生产 锻压冲压生产 材料成型的发展及应用
第五讲 线棒材生产