GB T 6414-1999铸件尺寸公差
机械制造技术试题库(附答案)

机械制造技术试题库(附答案)一、单选题(共50题,每题1分,共50分)1、用易熔材料做制成模样,然后用造型材料将其表面包覆,经过硬化后再将模样熔去,从而制成无分型面的铸型壳,最后经涛注而获得铸件的方法,称之为()A、压力铸造B、离心铸造C、熔模铸造D、金属型铸造正确答案:C2、车削细长轴,要使用中心架和跟刀架来增加工件的( _ )A、弯曲变形B、稳定性C、刚性D、钢性正确答案:C3、粗基准是指( )A、未经加工的毛坯表面作定位基准B、精加工时的定位基准C、粗加工的的定位基准D、已加工表面作定位基准正确答案:A4、影响刀具强度的最大因素是( )A、背吃刀量B、切削速度C、进给量正确答案:A5、粗加工时,应取( )A、较大前角B、大小均可C、较小前角D、不确定正确答案:C6、企业资源管理(计划)是()B、ERPC、CIMSD、FMS正确答案:B7、结构复杂的零件毛坯形式一般选( )A、铸造件B、焊接件C、锻造件D、型材正确答案:A8、一般单件、小批生产多遵循(A、基准重合B、工序分散C、基准统一D、工序集中正确答案:D9、【2012年湖南省职业技能鉴定试卷-中级车工理论知识考核】麻花钻的两个螺旋槽表面就是()A、副后刀面B、切削平面C、前刀面D、主后刀面正确答案:C10、粗车时为了提高生产率,选用切削用量时,应首先取较大的( )A、进给量B、切削速度C、切削力D、背吃刀量正确答案:D11、切削( )金属时,常得到带状切屑A、刚性B、韧性C、塑性正确答案:C12、刀具磨损时,国际标准组织规定以1/2背吃刀量处( )测定的A、基面上B、后刀面上C、前刀面上D、切削刀刃上正确答案:B13、铸造、锻造等属于()A、热加工B、冷加工C、机械加工D、切削加工正确答案:A14、( )总余量是指零件从( )整个加工过程中某一表面所切除金属层的总厚度。
A、粗加工到精加工B、一个工序C、所有工序D、毛坯变为成品正确答案:D15、90°车刀中的90°指。
公差标准与规范

公
差
等
级
公称尺寸(对应表面的较长边)
>30-
120
>120
Hale Waihona Puke -400>400-1000
>1000-
2000
>2000-
4000
>4000-
8000
>8000-
12000
>12000-
16000
>16000-
20000
>20000
E
±
±1
±
±2
±3
±4
±5
±6
±7
±8
630
5
7
10
14
18
22
630
1000
1
2
4
6
8
11
16
20
25
1000
1600
7
9
13
18
23
29
1600
2500
8
10
15
21
26
33
2500
4000
4
9
12
17
24
30
38
4000
6300
7
10
14
20
28
35
40
6300
10000
11
16
23
32
40
50
注:①铸件基本尺寸系指图样上给定的尺寸,应包括机械加工余量和起模斜度。
±4
±6
±8
±10
±12
±14
±16
C
±3
±4
±6
铸件检验标准

铝合金铸造件检验技术条件(试行)1 内容及适用范围本标准根据GB/T 1173-1995及GB/T 9438-1999的相关内容,规定了铝合金铸件的分类和铸件的外观质量、内在质量以及铸件修补等内容的技术要求与检验规则等。
本标准适用于我公司采用金属型铸造所生产的制动器上、下泵体等铸件(不含压力铸造)。
根据工作条件、用途以及在使用过程中如果损坏,所能造成的危害程度,将铸件分类如下:2 技术要求2.1 化学成分2.1.1合金的化学成分根据GB/T 1173-1995的规定,应符合表2-1及表2-2的规定。
2.1.2当使用杂质总和来表示杂质含量时,如无特殊规定,其中每一种未列出的元素含量不大于0.02%。
2.2 状态2.2.1铸件按表2-3的规定,呈铸态或热处理状态供应。
注:在保证合金机械性能前提下,可以不加铍(Be)。
2.3 机械性能2.3.1 每批铸件应按其类别检验机械性能。
2.3.2 合金及其铸件的机械性能应符合表2-3的规定。
2.4外观质量2.4.1铸件在进行表面粗糙度、表面缺陷、尺寸等外观质量检验之前,飞边、溢流口、隔皮等应清理干净、平整,但不可在非加工表面上留有明显的凿痕,且宽度不得超过2mm。
2.4.2铸件的表面粗糙度Ra为6.3μm以上。
2.4.3非加工表面的浇冒口,应清理到与铸件表面齐平;待加工表面的浇冒口残留量应不大于3mm。
2.4.4清除飞翅、夹砂等多肉类缺陷,铸件的内外表面由于型芯及顶杆的磨损所产生的飞边、毛刺应清除干净。
2.4.5根据顾客图样或技术文件的要求,铸件表面可进行喷砂处理。
2.4.6铸件上作为基准用的部位应平整,不允许存在任何凸起痕迹,装饰面上不允许有推杆痕迹(图样上注明)。
2.4.7非加工表面上,由于模具组合镶并或受分型面影响而形成的铸件表面高低不平差值不得超过0.3mm。
2.4. 8非加工表面上,不允许有超过表2-4(Ⅰ)级规定的花纹、麻面和有色斑点。
2.4.9铸件尺寸应符合图样的要求。
城市道路检查井盖技术规范
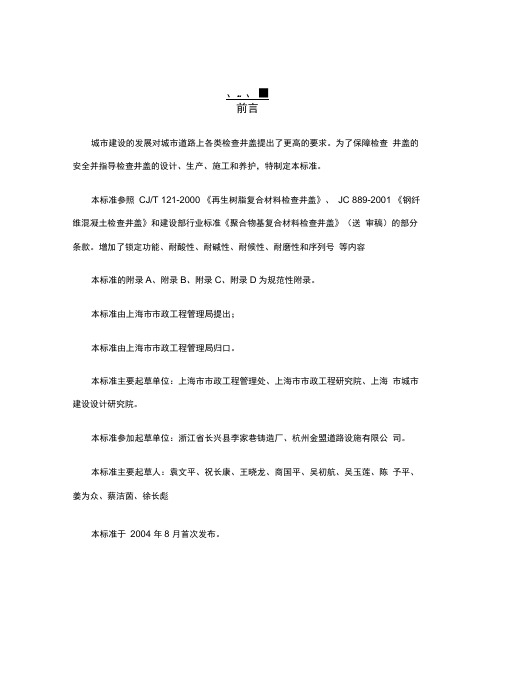
、尸■、■前言城市建设的发展对城市道路上各类检查井盖提出了更高的要求。
为了保障检查井盖的安全并指导检查井盖的设计、生产、施工和养护,特制定本标准。
本标准参照CJ/T 121-2000 《再生树脂复合材料检查井盖》、JC 889-2001 《钢纤维混凝土检查井盖》和建设部行业标准《聚合物基复合材料检查井盖》(送审稿)的部分条款。
增加了锁定功能、耐酸性、耐碱性、耐候性、耐磨性和序列号等内容本标准的附录A、附录B、附录C、附录D为规范性附录。
本标准由上海市市政工程管理局提出;本标准由上海市市政工程管理局归口。
本标准主要起草单位:上海市市政工程管理处、上海市市政工程研究院、上海市城市建设设计研究院。
本标准参加起草单位:浙江省长兴县李家巷铸造厂、杭州金盟道路设施有限公司。
本标准主要起草人:袁文平、祝长康、王晓龙、商国平、吴初航、吴玉莲、陈予平、姜为众、蔡洁茵、徐长彪本标准于2004 年8 月首次发布。
城市道路检查井盖技术规范1 范围本标准规定了以高强度钢纤维混凝土或聚合物基复合材料为原材料,经机械成型工艺制成的城市道路检查井盖(以下简称“井盖”)的承载等级、技术要求、试验方法、检验规则、标志、贮存和运输。
本标准适用于城市道路机动车俩行驶或停放场所的检查井盖,也适用于人行道、广场、绿化带等行人通行的场所、场地的检查井盖。
本市公路等机动车俩行驶或停放场所的检查井盖,可参照本标准的相应条款执行。
2 规范性引用文件下列文件中的条款通过在本标准中的引用而成为本标准的条款。
凡是注日期的引用文件,其随后所有的修改单(不包括勘误的内容)或修订版均不适用于本标准,然而,鼓励根据本标准达成协议的各方研究是否可使用这些文件的最新版本。
凡是不注日期的引用文件,其最新版本适用于本标准。
GB/T 1040 塑料拉伸性能试验方法GB/T 1041 塑料压缩性能试验方法GB/T 1043硬质塑料简支梁冲击试验方法GB/T 6414-1999铸件尺寸公差与机械加工余量GB/T 8810硬质泡沫塑料吸水率试验方法GB/T 9341塑料弯曲性能试验方法GB/T 12988无机地面材料耐磨性试验方法GBJ 82-1985普通混凝土长期性能和耐久性能试验方法CECS 13 :1989钢纤维混凝土试验方法3 术语和定义列术语和定义适用于本标准3.1检查井(人孔)manhole在地下管线设施中用于管线连接、检查、维护和安装设备的构筑物3.2检查井盖manhole cover and frame检查井口可开启的封闭物,由井座和井盖组成3.3井座manhole frame检查井盖中固定于检查井口的部分,用于安放井盖。
3、尺寸精度

分享熔模铸件重企标准的验证数据——铸件尺寸精度与表面质量潘玉洪熔模铸造能生产出形状复杂、尺寸精度较高的铸件。
铸件尺寸精度是标准中的一项重要内容,尺寸精度要求过高,势必产生大量的废品,提高生产成本;尺寸精度要求过低,失去熔模铸造的意义。
如何确定熔模铸件的尺寸精度、表面粗糙度和表面质量呢?一、铸件的尺寸精度1、影响铸件尺寸精度的因素为了确定熔模铸件合理的尺寸精度,国内、外的熔模铸造工作者做了大量的实验研究,也得出了一些极为宝贵的数据和资料。
影响熔模铸件尺寸精度的因素很多,它不仅与一些固定的因素有关,还与一些极为活跃的变动因素有关。
铸件尺寸精度是一个多变因素的函数。
对于固定因素,如铸件的结构、材质、形状和大小,应在设计压型时给予考虑;压型造成的偏差,一般可以通过修改压型予以消除。
对于活跃的变动因素,如蜡模的收缩、型壳的膨胀以及金属液冷凝时的收缩等,应严加控制。
铸件的最终尺寸是上述各因素的代数和。
(1)蜡模在压型尺寸一定的前提下,蜡模的尺寸与蜡料的性能(如蜡料的种类,配比等)、压注时的蜡料温度、压型温度、压注时的压力和保压时间,蜡模冷却介质的温度、冷却时间、取模早晚以及蜡模在收缩过程中是否受阻等诸因素有关。
作者试验结果:蜡料为石蜡与硬脂酸各占50%,室温22℃,蜡料温度为46~48℃,压力4~5Kgf/mm2,保压1min,取出蜡模在水中冷却1h后,检测8种零件800Pcs蜡模尺寸,当蜡模自由收缩的收缩率为0.2~0.6%时,蜡模的合格率为92%;阻碍收缩的收缩率为0.2~0.6%时,蜡模的合格率为94%;为此确定蜡模的收缩率为0.2%~0.6%。
(2)型壳型壳的膨胀率与构成型壳的耐火材料和粘结剂等因素有关。
据有关资料介绍,型壳的温度与型壳的尺寸关系见表1:表1 型壳的温度对其尺寸的影响正常情况下熔模铸造采用热壳浇注温度≥800℃,这时型壳的膨胀率为0.96%。
(3)金属液的收缩金属液冷却的收缩率与金属材质和浇注条件以及铸件在浇注系统中的位置等因素有关。
压铸件检验规范
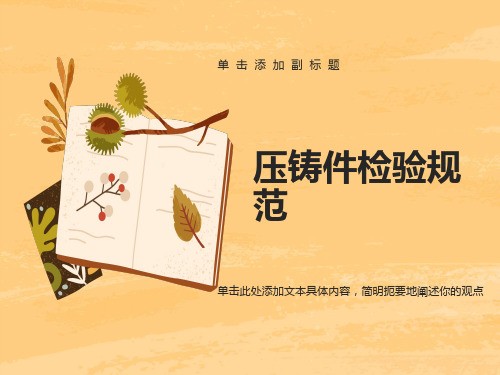
1/10
1/5
所在面上不允许超过的数量
2处
2处
离铸件边缘不小于mm
4
4
两冷隔间距不小于mm
10
10
3
擦伤
深度不大于mm
0.05
0.1
0.25
浇口部位增加一倍可接受
同上
面积不大于总面积的%
3
5
10
4
凹陷
凹陷深度不大于mm
0.1
0.3
0.5
装饰面不允许,非装饰面1~2级,内表面3级。
0.2mm2
任意1平方厘米的范围内≤3个
合格(装饰面)
0.3~0.6mm2
整个被检面积≤10个(占总面积的1/6)
合格(非装饰面)
小于1mm2
任意1平方厘米的范围内≤3个砂眼的密集性不超过所在面积的1/6
非直观面
注:大于1mm以上的砂眼允许的数目;各产品在设计加工时,在总技术要求里具体写出。也可与厂家协商后确定。
14
16
18
20
>400~1000
—
—
—
—
—
2
3
4
5
6
8
10
12
14
16
18
>1000~400
—
—
—
—
—
—
2
3
4
5
6
8
10
12
14
16
>4000~10000
—
—
—
—
—
—
—
2
3
4
5
6
8
铝合金铸造件检验技术条件
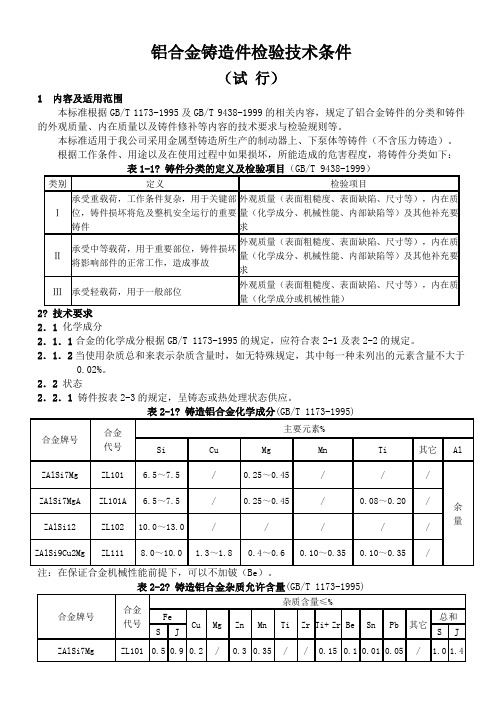
铝合金铸造件检验技术条件(试行)1 内容及适用范围本标准根据GB/T 1173-1995及GB/T 9438-1999的相关内容,规定了铝合金铸件的分类和铸件的外观质量、内在质量以及铸件修补等内容的技术要求与检验规则等。
本标准适用于我公司采用金属型铸造所生产的制动器上、下泵体等铸件(不含压力铸造)。
根据工作条件、用途以及在使用过程中如果损坏,所能造成的危害程度,将铸件分类如下:2?技术要求2.1 化学成分2.1.1合金的化学成分根据GB/T 1173-1995的规定,应符合表2-1及表2-2的规定。
2.1.2当使用杂质总和来表示杂质含量时,如无特殊规定,其中每一种未列出的元素含量不大于0.02%。
2.2 状态2.2.1铸件按表2-3的规定,呈铸态或热处理状态供应。
注:在保证合金机械性能前提下,可以不加铍(Be)。
2.3 机械性能2.3.1 每批铸件应按其类别检验机械性能。
2.3.2 合金及其铸件的机械性能应符合表2-3的规定。
2.4外观质量2.4.1铸件在进行表面粗糙度、表面缺陷、尺寸等外观质量检验之前,飞边、溢流口、隔皮等应清理干净、平整,但不可在非加工表面上留有明显的凿痕,且宽度不得超过2mm。
2.4.2铸件的表面粗糙度Ra为6.3μm以上。
2.4.3非加工表面的浇冒口,应清理到与铸件表面齐平;待加工表面的浇冒口残留量应不大于3mm。
2.4.4清除飞翅、夹砂等多肉类缺陷,铸件的内外表面由于型芯及顶杆的磨损所产生的飞边、毛刺应清除干净。
2.4.5根据顾客图样或技术文件的要求,铸件表面可进行喷砂处理。
2.4.6铸件上作为基准用的部位应平整,不允许存在任何凸起痕迹,装饰面上不允许有推杆痕迹(图样上注明)。
2.4.7非加工表面上,由于模具组合镶并或受分型面影响而形成的铸件表面高低不平差值不得超过0.3mm。
2.4. 8非加工表面上,不允许有超过表2-4(Ⅰ)级规定的花纹、麻面和有色斑点。
2.4.9铸件尺寸应符合图样的要求。
铸件外观质量检验规范
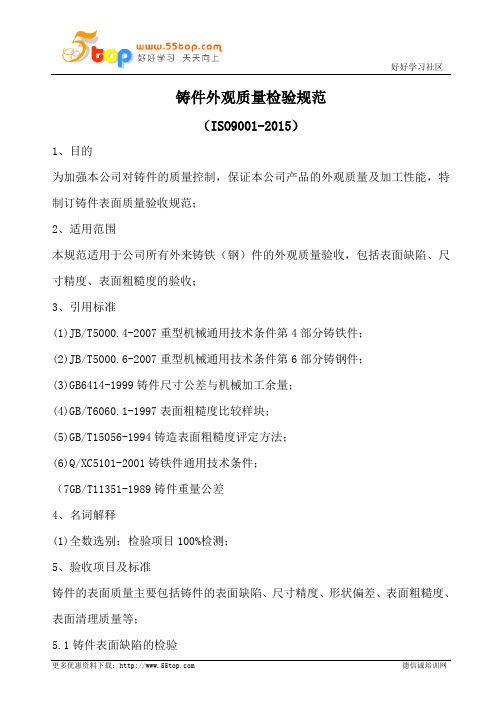
铸件外观质量检验规范(ISO9001-2015)1、目的为加强本公司对铸件的质量控制,保证本公司产品的外观质量及加工性能,特制订铸件表面质量验收规范;2、适用范围本规范适用于公司所有外来铸铁(钢)件的外观质量验收,包括表面缺陷、尺寸精度、表面粗糙度的验收;3、引用标准(1)JB/T5000.4-2007重型机械通用技术条件第4部分铸铁件;(2)JB/T5000.6-2007重型机械通用技术条件第6部分铸钢件;(3)GB6414-1999铸件尺寸公差与机械加工余量;(4)GB/T6060.1-1997表面粗糙度比较样块;(5)GB/T15056-1994铸造表面粗糙度评定方法;(6)Q/XC5101-2001铸铁件通用技术条件;(7GB/T11351-1989铸件重量公差4、名词解释(1)全数选别:检验项目100%检测;5、验收项目及标准铸件的表面质量主要包括铸件的表面缺陷、尺寸精度、形状偏差、表面粗糙度、表面清理质量等;5.1铸件表面缺陷的检验5.1.1表面缺陷检验的一般要求(1)铸件非加工表面上的浇冒口必须清理得与铸件表面同样平整,加工面上的浇冒口残留量应符合技术要求,若无要求,则按表8执行;(2)在铸件上不允许有裂纹、通孔、穿透性的冷隔和穿透性的缩松、夹渣等机械加工不能去除的缺陷;(3)铸件非加工表面的毛刺、披缝、型砂、砂芯等应清理干净;(4)铸件一般待加工表面,允许有不超过加工余量范围内的任何缺陷存在;重要加工面允许有不超过加工余量2/3的缺陷存在,但裂纹缺陷应予清除;加工后的表面允许存在直径*长度*深度小于等于2*2*2的非连片孔洞的铸造缺陷;(5)作为加工基准面(孔)和测量基准的铸件表面,平整度小于等于2.0毫米、粗糙度Ra50以内;(6)铸件表面气孔、砂眼、夹渣面积不大,但比较分散或者有连片麻点的表面不予接收;(7)除技术要求特别注明的铸件外,对于表面有气孔、缩孔、砂眼等缺陷的铸钢件允许补焊,但铸铁件未经允许不得焊补(铸铁件实行一案一判的原则)但补焊面积不允许超过铸件面积的10%,焊接质量应符合JB/T5000.7-2007标准要求,补焊后必须退火、机械性能达到图纸要求,且不得有渗漏及影响外观的缺陷;5.1.2铸件外观质量等级缺陷项目等级A B C飞边不允许飞边高度≤1.5毫米允许不易于伤手的飞边毛刺不允许允许不易于伤手的毛刺允许不易伤手的毛刺孔眼气孔 100cm 2面积内允许直径不大于φ2mm 深度不超过壁厚1/4的孔眼2个,两处距离>60mm ;整个铸件不超过4个100cm 2面积内允许直径不大于φ3mm 深度不超过壁厚1/3的孔眼2处,两处距离>60mm ;整个铸件不超过8个不致于影响强度,其余不做要求 针孔 渣眼 缩孔 不致于影响强度裂纹 不允许 不允许不允许 冷隔 沟槽 夹砂结疤 不允许 100cm 2面积内允许面积不超过8cm 2的缺陷2处;整个铸件不超过4处不致于影响强度 皱皮 不允许 不明显引人注意缩陷不允许不允许 不允许缺肉1、一般零部件采用B 级精度,在检查过程中,如有一个或多个项目超出B 级精度要求的零部件均判定为不合格;2、影响到零部件安全、性能的部位,外观质量采用A 级精度,如果有一个或多个项目超出规定级精度要求的零部件均判定为不合格;5.2铸件尺寸的检验 5.2.1铸件毛坯尺寸公差铸件尺寸公差应按毛坯图或技术条件规定的尺寸公差等级执行,当技术文件未规定尺寸公差时,则应以GB6414为依据,并按照下表选定公差值(粗线框内为推荐使用公差等级);毛坯铸件基本尺寸(mm )尺寸公差等级CT12CT13 CT14 CT15 CT16 ≤10~16 4.4 --- --- --- --- >16~25 4.6 6 8 10 12 >25~40 5.0 7 9 11 14 >40~63 5.6 8 10 12 16 >63~100 6 9 11 14 18 >100~160 7 10 12 16 20 >160~250 8 11 14 18 22 >250~400912162025。
机床铸件技术要求及验收
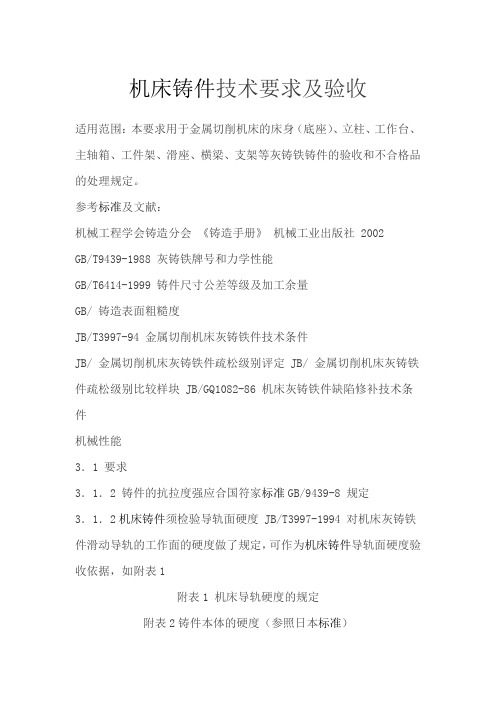
机床铸件技术要求及验收适用范围:本要求用于金属切削机床的床身(底座)、立柱、工作台、主轴箱、工件架、滑座、横梁、支架等灰铸铁铸件的验收和不合格品的处理规定。
参考标准及文献:机械工程学会铸造分会《铸造手册》机械工业出版社 2002GB/T9439-1988 灰铸铁牌号和力学性能GB/T6414-1999 铸件尺寸公差等级及加工余量GB/ 铸造表面粗糙度JB/T3997-94 金属切削机床灰铸铁件技术条件JB/ 金属切削机床灰铸铁件疏松级别评定 JB/ 金属切削机床灰铸铁件疏松级别比较样块 JB/GQ1082-86 机床灰铸铁件缺陷修补技术条件机械性能3.1 要求3.1.2 铸件的抗拉度强应合国符家标准GB/9439-8 规定3.1.2机床铸件须检验导轨面硬度 JB/T3997-1994 对机床灰铸铁件滑动导轨的工作面的硬度做了规定,可作为机床铸件导轨面硬度验收依据,如附表1附表1 机床导轨硬度的规定附表2铸件本体的硬度(参照日本标准)注:1,当导轨厚度大于60mm时,附表1 中的下限值允许降低5HBS。
2,要求表面淬火的导轨,附表1中的下限值应当提高5HBS。
当表面硬度达不到表中要求时,须在设计的许可下,由供需双方协商依据金相组织进行铸件验收。
3.1.3 表面贴塑(或其他耐磨材料)或者不属于滑动摩擦的导轨面,其表面硬度值可依照附表2 中的重要件作为参考。
3.2 检验方法3.2.1 抗拉强度采用Φ30 单铸试棒加工成试样测定。
试样的制作和试验方法应符合GB/9439-88 规定。
3.2.2 硬度的测定直接在铸件导轨面上进行。
导轨长度小于2500 时测定应不少于三点,大于2500 铸件重量大于5吨时应不少于四点。
3.3 检验规则3.3.1 批量划分:根据JB/T3997-94 规定,每包铁水浇注的铸件为一个批量,每批量铸件须提供一组试棒;如同一牌号铁水熔化量大,每包铁水均严格采用一定形式的工艺控制(光谱分析、热分析、及三角试样检验)时,可每炉次同牌号铁水浇一组试棒。
铸件外观质量检验规范
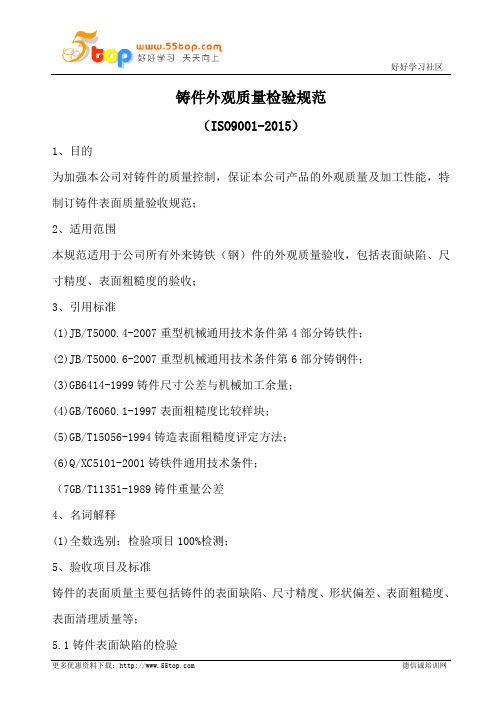
铸件外观质量检验规范(ISO9001-2015)1、目的为加强本公司对铸件的质量控制,保证本公司产品的外观质量及加工性能,特制订铸件表面质量验收规范;2、适用范围本规范适用于公司所有外来铸铁(钢)件的外观质量验收,包括表面缺陷、尺寸精度、表面粗糙度的验收;3、引用标准(1)JB/T5000.4-2007重型机械通用技术条件第4部分铸铁件;(2)JB/T5000.6-2007重型机械通用技术条件第6部分铸钢件;(3)GB6414-1999铸件尺寸公差与机械加工余量;(4)GB/T6060.1-1997表面粗糙度比较样块;(5)GB/T15056-1994铸造表面粗糙度评定方法;(6)Q/XC5101-2001铸铁件通用技术条件;(7GB/T11351-1989铸件重量公差4、名词解释(1)全数选别:检验项目100%检测;5、验收项目及标准铸件的表面质量主要包括铸件的表面缺陷、尺寸精度、形状偏差、表面粗糙度、表面清理质量等;5.1铸件表面缺陷的检验5.1.1表面缺陷检验的一般要求(1)铸件非加工表面上的浇冒口必须清理得与铸件表面同样平整,加工面上的浇冒口残留量应符合技术要求,若无要求,则按表8执行;(2)在铸件上不允许有裂纹、通孔、穿透性的冷隔和穿透性的缩松、夹渣等机械加工不能去除的缺陷;(3)铸件非加工表面的毛刺、披缝、型砂、砂芯等应清理干净;(4)铸件一般待加工表面,允许有不超过加工余量范围内的任何缺陷存在;重要加工面允许有不超过加工余量2/3的缺陷存在,但裂纹缺陷应予清除;加工后的表面允许存在直径*长度*深度小于等于2*2*2的非连片孔洞的铸造缺陷;(5)作为加工基准面(孔)和测量基准的铸件表面,平整度小于等于2.0毫米、粗糙度Ra50以内;(6)铸件表面气孔、砂眼、夹渣面积不大,但比较分散或者有连片麻点的表面不予接收;(7)除技术要求特别注明的铸件外,对于表面有气孔、缩孔、砂眼等缺陷的铸钢件允许补焊,但铸铁件未经允许不得焊补(铸铁件实行一案一判的原则)但补焊面积不允许超过铸件面积的10%,焊接质量应符合JB/T5000.7-2007标准要求,补焊后必须退火、机械性能达到图纸要求,且不得有渗漏及影响外观的缺陷;5.1.2铸件外观质量等级缺陷项目等级A B C飞边不允许飞边高度≤1.5毫米允许不易于伤手的飞边毛刺不允许允许不易于伤手的毛刺允许不易伤手的毛刺孔眼气孔 100cm 2面积内允许直径不大于φ2mm 深度不超过壁厚1/4的孔眼2个,两处距离>60mm ;整个铸件不超过4个100cm 2面积内允许直径不大于φ3mm 深度不超过壁厚1/3的孔眼2处,两处距离>60mm ;整个铸件不超过8个不致于影响强度,其余不做要求 针孔 渣眼 缩孔 不致于影响强度裂纹 不允许 不允许不允许 冷隔 沟槽 夹砂结疤 不允许 100cm 2面积内允许面积不超过8cm 2的缺陷2处;整个铸件不超过4处不致于影响强度 皱皮 不允许 不明显引人注意缩陷不允许不允许 不允许缺肉1、一般零部件采用B 级精度,在检查过程中,如有一个或多个项目超出B 级精度要求的零部件均判定为不合格;2、影响到零部件安全、性能的部位,外观质量采用A 级精度,如果有一个或多个项目超出规定级精度要求的零部件均判定为不合格;5.2铸件尺寸的检验 5.2.1铸件毛坯尺寸公差铸件尺寸公差应按毛坯图或技术条件规定的尺寸公差等级执行,当技术文件未规定尺寸公差时,则应以GB6414为依据,并按照下表选定公差值(粗线框内为推荐使用公差等级);毛坯铸件基本尺寸(mm )尺寸公差等级CT12CT13 CT14 CT15 CT16 ≤10~16 4.4 --- --- --- --- >16~25 4.6 6 8 10 12 >25~40 5.0 7 9 11 14 >40~63 5.6 8 10 12 16 >63~100 6 9 11 14 18 >100~160 7 10 12 16 20 >160~250 8 11 14 18 22 >250~400912162025>400~630 10 14 18 22 28 >630~1000 11 16 20 25 32 >1000~1600 13 18 23 29 37 >1600~2500 15 21 26 33 42 >25004000 17 24 30 38 49 >4000~6300 20 28 35 44 56 >6300~100002332405064注:1、毛坯铸件基本尺寸是指机械加工前毛坯铸件的尺寸,包括加工余量和起模斜度; 2、毛坯基本尺寸按铸件最大尺寸选取,该铸件较小尺寸公差等级与最大尺寸公差等级相同;3、壁厚采用低一级的公差等级;4、公差带应对称于毛坯铸件基本尺寸配置,例:基本尺寸30mm ,CT13公差值为±7mm ;如有特殊要求非对称式配置时,应在技术要求中单独列出公差范围;5.2.2铸件分型面处最大错型值应不得超过表2所示公差值,当需进一步限制错型量时,应从表中选取;公差等级CT 错型值(mm )11~13 1.5 14~162.55.2.3铸件加工余量应符合表的规定,有特殊要求的表面应在技术要求中单独标注加工余量;最大轮廓尺寸加工余量一个面顶面加量≤30 4 2>30~50 5 >50~180 6 >180~315 7 >315~500 8 >500~800 103>800~1250 12 >1250~1600 144>1600~250016>2500~3150 18>3150~4000 205>4000~6300 25>6300~10000 30 7注:1、属于该铸件的较小尺寸的加工余量与最大轮廓尺寸的加工余量相同;2、此表加工余量仅指一个面的加工余量,对于柱面和两面加工的铸件,铸件轮廓尺寸应为最终机械加工后成品尺寸与两倍加工余量之和;5.3表面粗糙度检测表面粗糙度总体检测原则依据图纸要求,当图纸无要求是执行国标GB/T15056;5.3.1一般情况下,表面粗糙度要求Ra50,铸件难以清理的部位,局部允许Ra100,待加工表面允许降低1级;5.3.2.使用面积法作为验收依据面积法常用的比较样块评定铸件表面粗糙度;方法如下:(1)铸造表面粗糙度比较样块应符合GB6060.1-1997标准;(2)按照国标BWZ001-88评定铸件表面粗糙度的等级;(3)铸件的浇道、冒口、修补的残余表面及铸造表面缺陷(如粘砂、结疤等)不列为被检表面;(4)以铸造表面粗糙度比较样块为对照标准,对被检铸件的铸造表面用视觉或触觉的方法进行对比;(5)用样块对比时,应选用适于铸造合金材料和工艺方法的样块进行对比;(6)被检的铸造表面必须清理干净,样块表面和被检表面均不得有锈蚀处;(7)用样块对比时,砂型铸造表面被检点数应符合表的规定;特种铸造表面被检点数应按表8的规定加倍;被检点应平均分布,每点的被检面积不得小于与之对比面的面积;被检铸造表面面积(cm2)<200 200~1000 100~10000 >10000被检点数(个) 不少于2 每200cm2不少于1 每1000cm2不少于1不少于40 (8)当被检铸造表面的粗糙度介于比较样块两级参数值之间者,所确定的被检铸造表面的粗糙度等级为粗的一级;(9)对被检铸造表面,以其80%的表面所达到的最粗表面粗糙度等级,为该铸造表面粗糙度等级;5.3.3铸件表面清理检测5.3.1铸件几何形状必须完整,非加工面上的清理损伤不应大于该处的尺寸偏差,加工面上的损伤不应大于该处加工余量的1/2;5.3.2允许铸件表面有少量的局部低凹或打磨痕迹,在直径不大于8mm,并能保证铸件规定的最小的壁厚;5.3.3为去除铸造缺陷而打磨后的铸件表面粗糙度应与一般铸件表面粗糙度基本一致;5.3.4除特殊情况外,铸件表面允许残留的浇冒口、毛刺,多肉残余量应按表8的要求进行;类别非加工面凸出高度(mm)加工面凸出高度(mm) 外表面非外表面浇冒口残余量-0.5~0.5 <2 <2~4毛刺残余量0 <2 <1~2多肉残余量<1 <2 <25.3.5铸件表面须经过防锈处理,保证在铸件进入面加工时不得有任何的锈蚀;5.3.6铸件表面如有油漆要求的,必须按有关涂装规定执行;5.4铸件重量检测5.4.1对于没有特殊要求的铸件,重量偏差可以不作为验收依据;如果技术条件有要求,供需双方协商后,铸件的重量偏差也应作为验收依据,一般应符合表的规定;公称重量(Kg) ≤200>200~500>500~1000>1000~5000>5000~10000>10000~30000>30000~50000>50000铸件重量上偏差(%)8 7.5 7 6.5 6 5.5 5 4.5。
铝件压铸行业检验规程

文件编号:XXXXXX版本:A/01受到状态:XXXXXXXXXXXXXX有限公司检验规程编制: XXXXXXXXXX审核:批准:实施日期: XXXXXXXXXXXXXXXXX1.目的:明确进入本公司的物资(原材料)以及本公司产品生产过程的检验项目、检验频次、技术要求、检测设备、检验方法、接收准则等。
2.范围:适用于进入本公司的物资(包括外购、原材料)、生产过程的在制品、产品出厂的检验和试验。
说明:当本规程与检验指导书或顾客图纸不一致时,按检验指导书或顾客图纸执行。
3.依据标准:3.1. GB/T15115-2009 压铸铝合金3.2. GB/T20975-2008 铝及铝合金化学分析方法3.3. DIN 1725-2-1983 压铸铝合金3.4. JIS H5302-2006 铝合金压铸件3.5. GB/T15114-2009 铝合金压铸件3.6. GB/T2828.1-2003 计数抽样检验程序3.7. GB/T6414-1999 铸件尺寸公差与机械加工余量3.8. GB/T1804-2000 一般公差线性尺寸的未注公差4.定义:4.1、首检:对每个班次刚开始时或过程发生改变(如人员的变动、换料、设备的调整、设备刀具的调换修磨等)后加工的第一或前几件产品进行的检验。
检验连续生产的1-2件(批)产品,合格后方可继续加工后续产品。
4.2、巡检:对制造过程中进行的定期或随机流动性的抽检,每次抽样1-2件(批)产品。
5.产品质量特性重要度分级:5.1、关键特性(▲):严重影响产品的安全性或法规符合性的产品特性。
5.2、重要特性(△): 影响产品配合、功能、性能或其后续过程的产品特性。
5.3、一般特性(不做标识): 对产品安全性或法规符合性、配合、功能、性能或其后续过程无影响的产品特性。
说明:对于图纸/检验指导书上标注的关键特性、重要特性;在过程检验中作为质控点进行重点关注。
检验频次为1次/h;6.抽样方法和判定标准:6.1 、以件为单位的产品抽样方法,具体按GB/T2828.1-2003,S-4特殊检验水平进行。
不同产品尺寸公差、未注公差的选择

不同产品未注公差的选择
标准名称
标准代号
适用产品种类
公差等级
标记示例
一般公差 未注公差的 线性和角度尺寸的公差 塑料模塑件 尺寸公差 冲压件未注公差极限偏 差
铸件 尺寸公差与机械 加工余量
橡胶制品的公差 第 1 部分:尺寸公差 铝及铝合金挤压型材尺 寸偏差
GB/T 1804—2000 GB/T14486—2008 GB/T15055—2007
不同产品尺寸公差的选择
标准名称
标准代号
适用产品种类
公差等级
塑料模塑件 尺寸公差
GB/T14486—2008 塑料模塑件 分为高精度、一般精度两个等级
6 冲压件尺寸公差
GB/T13914—2002
冲压件
平冲压件分为 11 个等级,即 ST1~ST11 成形冲压件分为 10 个等级,即 FT1~FT10
MT5,标注为:GB/T 14486—MT5
J 0 冲压件
一般公差可分为精密 f、中等 m、粗糙 c、最粗 v 四个等级
如选取中等级别时, 标注为:GB/T 15055—m
A 0 4 水玻璃 D J 2 熔模
批量生产公差等级为 CT7~9
如选取公差等级为 CT7 时, 标注为:GB/T 6414—CT7
7 熔模 水玻璃
一般选取公差等级为 CT1~6
铸件 尺寸公差与机械加工余量
GB/T6414—1999 铸钢件 硅胶
一般选取公差等级为 CT1~3
J 0 铝、镁合金压铸件
一般选取公差等级为 CT1~3
A 0 4 橡胶制品的公差 第 1 部分:尺寸公差 GB/T3672.1—2002 模压橡胶制品 一般选取精密 M1、高质量 M2 两个等级
压铸件检验标准
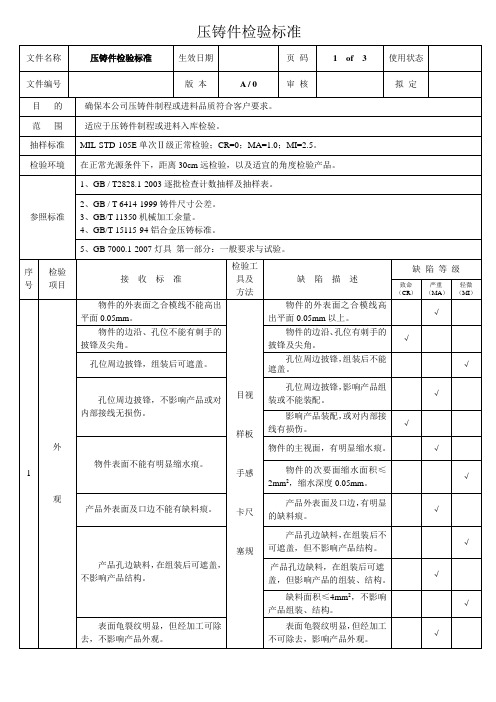
花纹痕迹组装后不能遮盖,其长≤3mm,宽≤0.09mm,深≤0.04mm。
花纹纹痕迹组装后不能遮盖,其长≤4mm,宽≤0.1mm,深≤0.05mm。
√
产品表面及口边、孔位不能有变形现象。
产品表面及口边有明显变形及凹凸不平现象。
√
孔位变形,但不影响组装或组装后可遮盖。
√
孔位变形,影响组装或不能遮盖。
√
机加工后,装配配合性良好且密封度(间隙)小于0.05mm。
装配困难及密封度(间隙)大于0.05mm。
√
孔位不能有打偏、打穿或漏打孔现象。
孔位偏、打穿或漏打孔。
√
备注
1、上述未列出来的检验标准,检验时,请依照“客户要求”、“客户样品”进行验收。
2、本检验标准未尽项目,需检验时可参照行业标准、国标或工程技术文件要求。当检验标准的检验项目在技术要求中未作规定时,可不作检验要求。
产品孔边缺料,在组装后可遮盖,不影响产品结构。
产品孔边缺料,在组装后不可遮盖,但不影响产品结构。
√
产品孔边缺料,在组装后可遮盖,但影响产品的组装、结构。
√
缺料面积≤4mm2,不影响产品组装、结构。
√
表面龟裂纹明显,但经加工可除去,不影响产品外观。
表面龟裂纹明显,但经加工不可除去,影响产品外观。
√
压铸件检验标准
参照标准
1、GB / T2828.1-2003逐批检查计数抽样及抽样表。
2、GB / T 6414-1999铸件尺寸公差。
3、GB/T 11350机械加工余量。
4、GB/T 15115-94铝合金压铸标准。
5、GB 7000.1-2007灯具第一部分:一般要求与试验。
序号
检验
铸造毛坯件检验规范

1、目的为了规范公司对铸造件质量的检验。
2、适用范围适用于公司内所有球墨铸铁材质的产品。
3、引用标准GB /T5612-2008 铸铁牌号表示法GB/T1348-1988 球墨铸铁件GB 231-84 金属布氏硬度试验法GB/T9441-2009 球墨铸铁金相检验GB/T6414-1999 铸件尺寸公差与机械加工余量GB 6060.1-85 表面粗糙度比较样块铸造表面4、验收标准4.1 铸件材质检验标准:4.1.1 球墨铸件材质验收标准应符合GB1348-1988 球墨铸铁的标准,以机械性能(抗拉强度、延伸率)、金相组织为验收依据,硬度及化学成分做为参考。
牌号化学成份重量百分比(%)C Si Mn P S Mg Re CuQT450-10 3.4~3.92.6~3.1≤0.3 ≤0.07 ≤0.030.025~0.060.02~0.04---QT500-7 3.4~3.92.6~3.0≤0.45 ≤0.07 ≤0.030.025~0.060.02~0.04---QT600-3 3.2~3.72.4~2.80.4~0.5≤0.07 ≤0.030.025~0.060.02~0.040.2~0.4牌号机械性能抗拉强度σb(MPa)屈服强度σ0.2(MPa)延伸率δ(%)硬度(HB)QT450-10 ≥450 ≥310 ≥10 160~210 QT500-7 ≥500 ≥320 ≥7 170~270 QT600-3 ≥600 ≥370 ≥3 190~270 4.1.1.3 壳体毛坯件的球墨铸铁材质正火后其珠光体(正火索氏体)组织等级在3级以上。
4.1.2 材质检验取样规范4.1.2.1机械性能检查:机械性能测试的试块,每班次每种牌号至少浇注三根,若铸件进行热处理,必须连同试块一同进行热处理。
二根用于生产厂测试性能(第一根合格则该批次合格,余下试块(留有生产日期、包次标识)留存。
若第一根试块不合格,测试剩余二根,若第二根不合格则该批次产品全部报废,若第二根合格,应加试第三根,合格则判定该炉产品合格,若第三根不合格则该批次产品全部报废)。
铝合金压铸件的标准

铝合金压铸件的标准 The manuscript was revised on the evening of 2021铝合金压铸件1 范围本标准规定了铝合金压铸件(以下简称压铸件)的材质、尺寸公差、角度公差、形位公差、工艺性要求和表面质量。
本标准适用于照相机、光学仪器等产品的铝合金压铸件。
2 规范性引用文件下列文件中的条款通过本标准的引用而成为本标准的条款。
凡是注明日期的引用文件,其随后所有的修改单(不包括勘误的内容)或修订版均不适用于本标准,然而,鼓励根据本标准达成协议的各方研究是否可使用这些文件的最新版本。
凡是不注日期的引用文件,其最新版本适用于本标准。
GB/T 6414—1999 铸件尺寸公差与机械加工余量GB/T 11334—1989 圆锥公差JIS H 5302—1990 压铸铝合金3 压铸铝合金压铸铝合金选用JIS H 5302—1990中的ADC10。
ADC10的化学成分表1给出。
其中铜的含量控制在不大于 %。
a ) 抗拉强度σb :245 MPa;b ) 伸长率δ5 :2 %;c ) 布氏硬度HBS(5/250/30):80。
4 铸件尺寸公差压铸件尺寸公差的代号、等级及数值压铸件尺寸公差的代号为CT。
尺寸公差等级选用GB/T 6414—1999中的CT3 ~CT8。
一般(未注)公差尺寸的公差等级基本规定为:照相机零件按CT6,其他产品零件按CT7。
尺寸公差数值表2给出。
壁厚尺寸公差壁厚尺寸公差一般比该压铸件的一般公差粗一级。
例如:一般公差规定为CT7,壁厚公差则为CT8。
当平均壁厚不大于 mm时,壁厚尺寸公差则与一般公差同级,必要时,壁厚尺寸公差比一般公差精一级。
公差带的位置尺寸公差带应相对于基本尺寸对称分布,即尺寸公差的一半为正值,另一半取负值。
当有特殊要求时,也可采用非对称设置,此时应在图样上注明或在技术文件中规定。
对于有斜度要求的部位,其尺寸公差应沿斜面对称分布。
受分型面及型芯的影响而引起的固定增量和错型值,已包含在尺寸公差数值之内。
“综合法”评定铸件质量等级

“综合法”评定铸件质量等级一、“综合法”评定铸件质量等级的基本思路对一个铸造企业的铸件质量评定,不能只看铸件实物质量,还应注意铸件质量的稳定性和可靠性,这就是用综合法评定铸件质量等级的基本思路。
我国铸造行业制定有(JB/T 7528—1994)标准《铸件质量评定方法》,它规定了采用砂型铸造、金属型铸造、低压铸造和熔模铸造等工艺方法生产的各种金属及合金铸件质量等级的评定方法。
标准指出,通常可从铸件实物质量、技术管理和售后服务三个方面综合评定铸件质量等级。
1.总则1)评定依据是有关标准(即有关的国际标准、现行国家标准、行业标准、国外先进标准或企业标准)或有关技术文件中规定的技术指标。
2)当企业内控标准中规定的技术指标与国家标准或行业标准规定的技术指标不一致时,以较高指标为准。
3)对重大新产品或质量纠纷仲裁的铸件质量评定,则依据有关技术要求规定的检测项目和指标进行。
4)检测项目根据被评定铸件的有关标准或技术文件中规定的项目而定。
5)为确保铸件质量,对铸件的使用性能、寿命、可靠性等有直接影响或起重要作用的关键项质量指标实行质量否决权。
关键项指标的数量则根据对铸件质量的要求确定。
不同种类铸件的关键项指标及数目可以不同。
6)有特殊要求的铸件可以特殊处理。
2.抽样检测的一般规定(1)抽样规定1)抽样对象。
经生产单位质检部门验收合格的成品铸件。
2)抽样方式。
随机抽样。
3)抽样地点。
在生产单位的铸件成品库中抽取。
4)抽样数量。
成批和大量生产的铸件抽样数见表14-1;单件和小批生产的铸件抽样数见表14-2。
表14-1 成批和大量生产的铸件抽样数表14-2 单件和小批生产的铸件抽样数5)抽样基数。
抽样基数见表14-3。
表14-3 抽样基数(2)检测项目、条件及方法铸件质量检测项目包括铸件实物质量、技术管理和售后服务三部分。
铸件实物质量主要分为外部质量和内部质量。
外部质量包括:表面粗糙度、尺寸公差、重量公差、表面缺陷及清理状态;内部质量包括:力学性能、化学成分、金相组织、内部缺陷及耐压试验。
盖铸造工艺设计说明书

盖铸造工艺设计说明书1铸件构造工艺性分析1.1铸件根本情况:铸件材料为ZG310—570,铸件属半圆环厚壁零件,最大直径780mm,最小直径490mm,加工后最大壁厚210mm,最小145mm,加工后净重238Kg,铸件尺寸精度CT14,质量需符合GB/T6414—1999标准,允许深度不大的短小裂纹补焊,加工面不允许有肉眼看见的缩孔、缩松和裂纹等缺陷。
铸件属于中型铸件,属单件小批量生产性质类型。
根据零件三视图,画出铸件三维图如图1-1所示。
图1-1 铸件三维图1.2铸件构造工艺性分析铸件壁厚的适宜性分析铸件壁过薄,铸件将产生浇缺乏、冷隔、浇注流痕等铸造缺陷,铸件壁过厚,将使铸件由于冷却过慢晶粒粗大,也影响铸件的机械性能,因此对于一个具体的铸件,根据其材料与铸造方法,必须有一个最小临界壁厚才能保证其铸造工艺的实施。
由于零件属单件小批量生产类型,因此适宜的铸造方法为砂型铸造,根据材料的类型与铸件最大尺寸,查阅资料[1],从铸件尺寸来看,临界壁厚必须小于39mm,而本铸件最小壁厚为145mm,远远大于临界壁厚,所以本铸件属厚壁件,因此在铸造过程中应想法使金属液快速冷却。
铸件壁的连接过渡圆角铸件的过渡圆角过小,将使连接处产生较大的铸造应力,并有可能造成铸件开裂,对于本铸件来说,铸件尺寸大,铸件收缩亦大,从而铸造应力更大,铸件壁连接转角更易开裂,因此对铸造圆角的大小进展分析具有重要意义。
从图1-2可知,其过渡圆角查阅资料[2]可知,铸造适宜的圆角应在R50较为适宜,本铸件的过渡圆角在图中为R20,此处圆角过小,易在此处产生较大的铸造应力,导致铸件在此处开裂,因此,与厂家协商后,铸造工艺设计中按铸造圆角R50进展设计模样与芯盒。
1.3铸件可能产生的铸造缺陷本铸件属于中型半圆环厚壁铸件,对于此类铸件,铸件由于壁太厚,铸造完成后容易使晶粒粗大,以至于达不到厂家所要求的力学性能,为消除与防止这些缺陷的产生,铸件除快速浇注外,还需采用加冷铁等方法方法。