最新制氢培训讲义
《制氢站培训资料》课件

3 火灾风险
4 安全管理方法
在制氢站操作过程中,由于氢气具有极高 的燃烧性,一旦发生火灾,后果将不堪设 想,因此火灾防控非常重要。
为确保制氢站的安全运行,需要采取严格 的安全管理方法,包括安全培训、检查维 护和事故应急预案等。
制氢站的技术细节
主要设备
工艺流程
常见故障及排除方法
了解制氢站的主要设备,如氢 气发生器、纯化系统和储氢罐, 以及它们的工作原理和性能。
详细介绍制氢站的工艺流程, 包括反应步骤、气体分离和净 化过程,以及储氢和供气系统。
掌握制氢站的常见故障,并了 解如何快速诊断和解决问题, 确保制氢站的稳定运行。
制氢站的维护保养
1 日常维护
2 周期性维护
了解制氢站的日常维护工作,包括设备检 查、清洁、润滑和参数监测,确保设备的 良好运行。
指导制氢站的周期性维护,如更换部件、 校准仪器和进行性能测试,保证设备的长 期稳定性。
《制氢站培训资料》PPT 课件
# 制氢站培训资料PPT课件大纲
本次课程将全面介绍制氢站的基础知识、安全问题、技术细节、维护保养以 及未来发展趋势,为您深入了解制氢站提供全方位指导。
制氢站基础知识
定义
制氢站是一种用于产生氢气的设施,可以应 用于多个领域,如能源产业和化工行业。
主要原理
制氢站利用化学反应或电解作用将水分解为 氢气和氧气,其中最常用的方法是蒸汽重整 和碱性电解。
分类
制氢站根据生产方式可分为化学法和电解法, 每种方法有不同的优缺点。
工作流程
制氢站的工作流程包括氢气产生、氢气纯化、 储存和供应,保证持续稳定的氢气供应。
制氢站的安全问题
1 爆炸风险
2 泄漏风险
制氢站因为涉及氢气的产生和储存,存在 爆炸风险,必须采取严格的安全措施来防 止事故发生。
制氢原理及设备培训资料

制氢原理及设备培训资料一、制氢原理氢气(H2)是无色无味的气体。
它是气体中最轻的(只有同体积空气重量的1/14.28),具有最大的扩散速度,容易通过各种细小的空间。
因而氢气具有高导热性,氢气的导热系数是空气的6.69倍,CO2的10.5倍,N2的6.2倍。
在氢气中噪音较小,而且绝缘材料不易受氧化和电晕的危害。
经过严格处理的氢气可以保证发动机内部的清洁。
氢气的优良特性使它非常适合作为大型发电机的冷却介质。
工业上制取氢气的方法有以下几种:一是将水蒸气通过灼热的煤焦炭,可取纯度只有75%左右的氢气;二是将水蒸气通过灼热的铁,可制纯度在97%以下的氢气;三是由水煤气中提取氢气,它的纯度也较低;四是电解水制取氢气,它的纯度高达99%以上。
因此,用于冷却发电机的氢气,都是由电解水制取的。
所谓电解,就是借助直流电的作用,将溶解在水中的电解质分解成新物质的过程。
简单的说就是利用直流电分解物质的过程。
有些溶有电解质的水溶液通电以后,分解出来的两种新物质,与原来的电解质完全没有关系,被分解的是作为溶剂的水。
例如:硫酸、氢氧化钠、氢氧化钾等。
这是因为纯水的电离度很小,导电能力极差,是弱电解质,没有以上的电解质,就不会被分离成氢气和氧气。
当氢氧化钠水溶液通电时,在阴极上电解液中的H+(水电解后产生的)受阴极的吸引而移向阴极,最后接受电子析出氢气,就会有如下反应:4H++4e=2H2t在阳极上,电解液中的OH受阳极吸引而向阳极移动,最后放出电子而成为水和氧气:40H-4e=2⅛0+O2t阴阳合起来的总反应式为:240二=二=2H2t+O2T从总反应式中可以看出,电解水制氢时每产出两体积的氢气,同时就会产生一体积的氧气。
二、制氢设备生产的ZHDQ-32∕10■以其优良的性能在发电企业得到较广泛的应用。
下面对这一系统作以简要介绍:(一)制氢设备主要技术参数:氢气产量:H760mmHg氧气产量:5Nm3∕h;氢气纯度:299.8%(经干燥纯化后可达99.998%);氧气纯度:299.2%;氢气湿度:<4g/Nn?H2电解槽工作压力:3.14Mpa(可在0.8~3∙14MPa之间任何压力下运行)电解小室数:62个;小室电流:370A循环碱量:400~900L∕h;分离器液位:600~800mm;差压:-20~+20mm;电解液:26%NaOH水溶液或者30%KOH水溶液整流柜:电流W740A,电压62~72V;电解槽直流电耗:4.8KWh∕Nm3Hz; 未含干燥器功率2.2KW制氢机电源:AC380V50Hz;干燥器工作压力:3.0Mpa∕0.8~3.0Mpa(干燥/再生)干燥器工作温度:室温/160~230°C(干燥/再生)干燥器电源:AC220V50Hz;供氢母管压力:0.8~1.OMPa;压缩空气气源:压力0.3~0∙7MPa,含油量V5mg∕m3,露点比环境温度低10℃;冷却水源:温度W30°C,压力20.3MPa;漏氢量:0.2~1.0% (二)制氢设备规范:(1)电解槽的外形及各零部件的作用电解槽是压滤式结构,由六(八)根大螺栓和二块端压板夹紧成一体,从外表正面看是圆柱体结构。
制氢培训课件
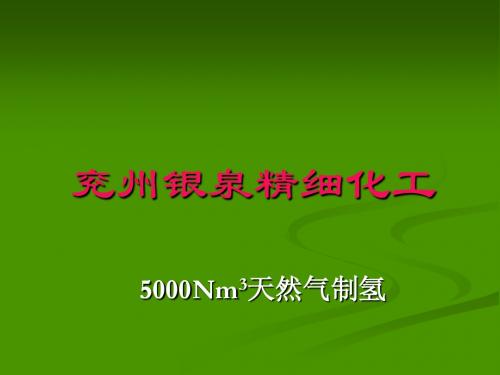
绝热加氢工艺流程图
1、转化的基本原理
转化型式:一段转化+二段转化;一段转化
烃类水蒸汽转化主要反应有: CnHm+nH2O=nCO+(n+m/2)H2 ① CO+3H2=CH4+H2O △Ho298 =-206kJ/mol ② CO+H2O=CO2+H2 △Ho298 =-41kJ/mol ③ 以甲烷为主的气态烃,蒸汽转化过程 较为简单,主要发生上述反应,最终产品 气组成由反应②③平衡决定。
4、变温加氢工艺
220℃
350 ~ 380℃
原料气
适用原料: 烯烃含量不 限制
去转化炉
原料预热炉 变温加氢反应器 绝热加氢反应器 氧化锌脱硫反应器
绝热加氢工艺流程图
1、绝热加氢工艺
250 ~ 390℃ 320 ~ 370℃
原料气
适用原料: 烯烃含量小 于7%一下
去转化炉 原料预热炉 加氢反应器 氧化锌脱硫
4.中温变换部分 由转化气蒸汽发生器(E4001)来的360-380℃ 转化气进入中温变换反应器,在催化剂的 作用下发生变换反应,将变换气中CO降至 3%左右。中变气经锅炉给水第二预热器预 热锅炉给水,锅炉给水第一预热器预热锅 炉给水,除盐水预热器预热除盐水回收大 部分预热后,在经中变器水冷器降温至40℃, 并经分水后进入PSA部分。
蒸汽转化过程反应原理
而轻石脑油,由于其组成较为复杂,有烷 烃、环烷烃、芳烃等,因此,除上述反应外, 在不同的催化床层,还发生高级烃的热裂解、 催化裂解、脱氢、加氢、积炭、氧化、变换、 甲烷化等反应,最终产品气组成仍由反应②③ 平衡决定。 烃类水蒸汽转化反应是体积增大的强吸热反 应,低压、高温、高水碳比有利于上述反应的 进行。 工程设计选择:高压、高温、低水碳比
生物制氢技术上课讲义
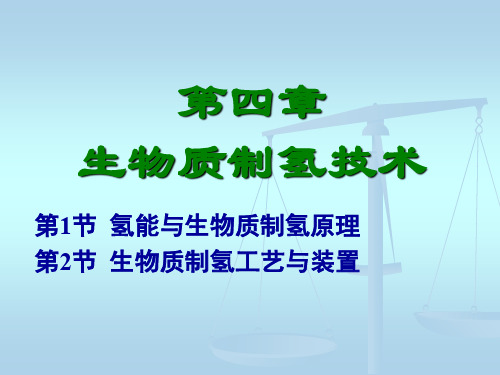
热化学转化法制氢原理
生物质热裂解制氢
生物质热裂解是在隔绝空气或供给少量空气的条件下使生 物质受热而发生分解的过程。 一般生物质热解产物有可燃气体、生物油和木炭。根据工 艺的控制不同可得到不同的目标产物。
生物质热裂解制氢就是对生物质进行加热使其分解为可燃 气体和烃类。 为增加气体中的氢含量,需要对热解产物再进行催化裂解, 使烃类物质继续裂解,对热解气体进行重整,将甲烷和一 氧化碳也转化为氢气。 最后采用变压吸附或膜分离的方式分离出氢气。
熟练掌握:生物质制氢原理
1.1 氢的性质与氢能利用
1.1.1氢的性质
物理性质
通常状况下氢气是无色、无味、无毒的气体,极难溶于水, 不易液化。 氢气是所有气体中最轻的,只有空气密度的1/14。氢有固、 液、气三态,在液化和固化后质量密度和能量密度都大大 提高。 在所有的气体中,氢的比热容最大、热导率最高、黏度最 低,是良好的冷却工质和载热体。 氢的热值很高,约为汽油热值的3倍,高于所有的化石燃 料和生物质燃料,且燃烧效率很高。
第四章 生物质制氢技术
第1节 氢能与生物质制氢原理 第2节 生物质制氢工艺与装置
主要教学内容及要求:
了解:氢的能源特性,生物法制氢的各种途径, 几种主要的生物质制氢装置
理解:微生物产氢途径,光合微生物制氢反应器 运行原理
掌握:生物质制氢的特点,不同的制氢途径及其 特点,主要的生物质制氢的工艺类型
1.2 生物质制氢的基本原理
1.2.1热化学转化法制氢 生物质气化制氢
生物质热裂解制氢 生物质超临界转化制氢、 生物质产品重整制氢
(生物质热解油的水蒸气重整制氢、甲醇和乙醇的水蒸气重整 制氢、甲烷重整制氢等)
热化学转化可以从生物质中获得更多的可用能源(H2、CO等),并 可在生物质气化反应器固定床和流化床中进行大规模的生产,热化工 过程易于控制。
制氢操作培训课件
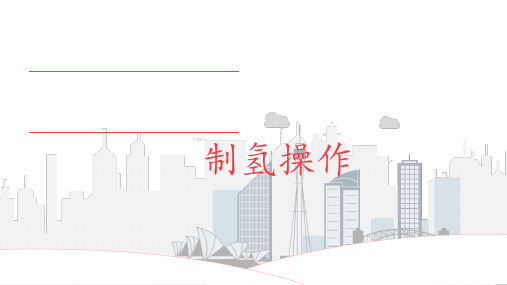
脱硫单元
• 系统循环量的控制 • 出系统粗氢气产品质量的控制 • 系统腐蚀的控制 • 胺液的降解 • 消泡剂的添加 • 气化脱硫与MDEA脱硫对比
脱硫单元
• (1)系统循环量的控制
•
富液循环量要<543m3/h,流速过快容易导致腐蚀
•
变换装置出口至T4201该段管线伴热不用投用
尽可能低,减少饱和水夹带以及灰尘夹带。(带水意味着带灰)
待蒸汽超过临界值后随着系统温度的升高压力会逐渐稳定。
• (2)进料温度控制
•
主要从系统物料平衡考虑
• (3)出料温度的监控
•
T4103出口温度
磷酸盐加药装置操作
• 低于30cm配置药剂,最终加水量控制在100cm。 • 搅拌器待药剂完全溶解后停运。 • 加药量根据系统补水负荷、排污量、磷酸根含量、PH及时调整。
引申:
系统压力的控制
1、系统气量 2、变换反应的好坏 3、脱硫循环量、溶剂温度的控 制、再生效果的好坏。 4、VPSA/PSA的有效吸附。 5、压缩机的运行情况。
变换催化剂的维护
• 4催化剂毒物
•
砷含量(煤中含有砷元素)
•
砷的主要来源为原料煤,气化装置使用的烟煤中砷的含量一般为
0.75~176ppm。工艺气中的砷含量为煤中所含砷的14%~22%,其余存在于粗渣
合物发生了分子链的无规则断裂、侧基和低分子的消除反应,致使聚合度
和相对分子质量下降。
•
①温度高降解
•
128℃,设计采用150℃ 蒸汽,待压缩单元正常运行后采用的是200℃
蒸汽。温度的控制要严格执行工艺指标。
•
②与氧气接触降解
脱硫单元
• (5) 消泡剂的添加 • 在胺液运行过程中加入消泡剂应慎重考虑。必须在确认溶剂已经发泡后
制氢站培训教材12页word

氢气的制取和发电机的冷却第一节发电机的冷却方式1. 发电机冷却的重要性发电机运转时要发生能量消耗,这是有一种能(机械能)转变为另一种能(电能)时所不可避免的。
这些损耗的能量,最后都变成了热量,致使发电机的转子、定子、定子绕组等各部件的温度升高。
因为发电机的部件都是有铜质和铁质材料制成的,所以把这种能量消耗叫做铜损和铁损。
为了保证发电机能在绕组绝缘材料允许的温度下长期运行,必须及时地把铜损和铁损所产生的热量导出,使发电机各主要部件的温升经常保持在允许的范围内。
否则,发电机的温升就会继续升高,使绕组绝缘老化,出力降低,甚至烧坏,影响发电机的正常运行。
因此,必须连续不断地将发电机产生的热量导出,这就需要强制冷却。
2. 发电机常用的冷却方式发电机的冷却是通过冷却介质将热量传导出去来实现的。
常用的冷却方式有:2.1 空气冷却。
容量小的发电机(两万千瓦以下)多采用空气冷却,即使空气有发电机内部通过,将热量带出。
这种冷却方式效率差,随着发电机容量的增大已逐渐被淘汰。
2.2 水冷却。
把发电机转子和定子绕组线圈的铜线作成空心,运行中使高纯度的水通过铜线内部,带出热量使发电机冷却。
这种冷却方式比空气冷却效果好,但必须有一套水质处理系统和良好的机械密封装置。
目前,大型机组多采用这种冷却方式。
2.3 氢气冷却。
氢气对热的传导率是空气的六倍以上,加以它是最轻的一种气体,对发电机转子的阻力最小,所以大型发电机多采用氢气冷却方式,即将氢气密封在发电机内部,使其循环。
循环的氢气再由另设的冷却器通水冷却。
氢气冷却有可分为氢气与铜线直接接触的内冷式(直接冷却)和氢气不直接与铜线接触的外冷式两种。
当前除了小容量(25MW及以下)汽轮发电机仍采用空气冷却外,功率超过50MW的汽轮发电机都广泛采用了氢气冷却,氢气、水冷却介质混用的冷却方式。
在冷却系统中,冷却介质可以按照不同的方式组合,归纳起来一般有以下几种:2.3.1 定、转子绕组和定子铁芯都采用氢表面冷却,即氢外冷;2.3.2 定子绕组和定子铁芯采用氢表面冷却,转子绕组采用直接冷却(即氢内冷);2.3.3 定、转子绕组采用氢内冷,定子铁芯采用氢外冷;2.3.4 定子绕组水内冷,转子绕组氢内冷,定子铁芯采用氢外冷,即水氢氢冷却方式;2.3.5 定、转子绕组水内冷,定子铁芯空气冷却,即水水空冷却方式;2.3.6 定、转子绕组水内冷,定子铁芯氢外冷,即水水氢冷却方式。
制氢车间HAZOP培训课件
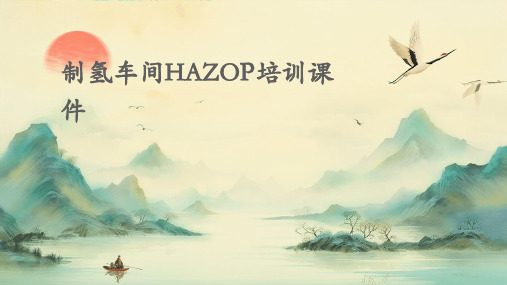
执行分析
按照分析计划,对制氢车间的工 艺流程进行逐一分析,使用引导 词系统对每个节点进行偏差识别 和风险评估。
风险矩阵与安全措施评估
根据分析结果,制定风险矩阵, 对每个风险进行等级划分,评估 现有安全措施的有效性,并提出 相应的改进建议。
引导词系统与使用
定义引导词 根据制氢车间的工艺特点和操作 条件,选择合适的引导词,如流 量、压力、温度、液位等,用于 描述工艺参数的偏差。
培训安排
为期一周的集中培训,每天6小时,共 计30小时。培训对象为制氢车间的操 作员、工艺工程师和技术人员。
培训效果评估与改进
评估方式
通过理论考试、小组讨论和个人报告等形式对培训效果进行评估。
改进措施
根据评估结果,对培训内容和方式进行改进,以提高培训效果和质量。同时, 定期组织复训和更新培训课件,以适应制氢车间工艺和安全要求的变化。
制氢车间HAZOP培训课 件
• HAZOP简介 • HAZOP基本概念 • HAZOP分析方法 • HAZOP分析实践 • HAZOP培训与提升 • HAZOP应用与发展趋势
01
HAZOP简介
HAZOP的定义
是一种基于风险的评估方法,用于识别和评估工艺系统中的潜在危险和操 作问题。
通过分析工艺流程图和操作规程,HAZOP研究确定可能发生的偏离,并 评估这些偏离对人员、环境和设备的影响。
分析实施与记录
成立分析小组
组建具备HAZOP分析经验和制氢 车间知识的专业团队。
实施分析
按照HAZOP分析的步骤和方法, 对制氢车间的工艺流程、设备、 操作等进行全面分析,识别潜在 的危险和操作偏差。
记录分析结果
详细记录每个偏差及其潜在的风 险和后果,为后续评估和报告编 写提供依据。
制氢车间培训资料
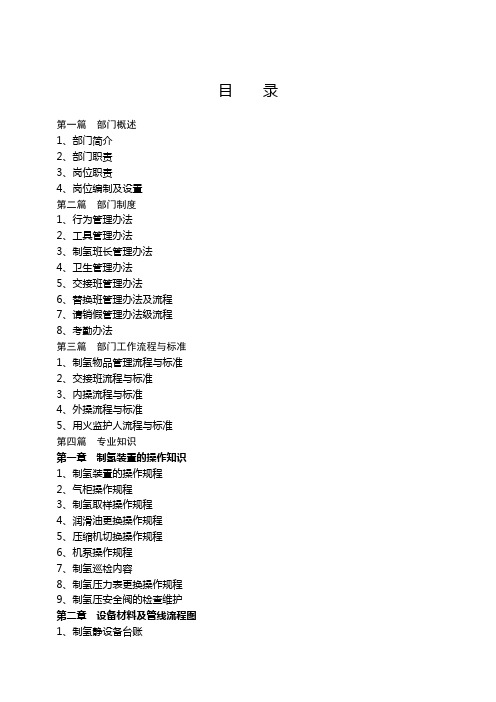
目录第一篇部门概述1、部门简介2、部门职责3、岗位职责4、岗位编制及设置第二篇部门制度1、行为管理办法2、工具管理办法3、制氢班长管理办法4、卫生管理办法5、交接班管理办法6、替换班管理办法及流程7、请销假管理办法级流程8、考勤办法第三篇部门工作流程与标准1、制氢物品管理流程与标准2、交接班流程与标准3、内操流程与标准4、外操流程与标准5、用火监护人流程与标准第四篇专业知识第一章制氢装置的操作知识1、制氢装置的操作规程2、气柜操作规程3、制氢取样操作规程4、润滑油更换操作规程5、压缩机切换操作规程6、机泵操作规程7、制氢巡检内容8、制氢压力表更换操作规程9、制氢压安全阀的检查维护第二章设备材料及管线流程图1、制氢静设备台账2、制氢机泵设备明细表3、制氢车间管道明细表第三章安全消防知识1、预防硫化氢中毒安全知识2、空呼器的使用保养知识3、火灾扑救知识4、安全事故事例5、灭火器的使用知识6、事故处理知识7、检火人职责知识8、停工检修的安全知识9、进入生产装置的安全知识10、外来人员的安全知识第五篇应急预案1、制氢体停电事故的处理预案2、制氢开工预案3、制氢停工预案4、制氢事故处理预案5、气柜电事故的处理预案6、气柜瓦斯泄漏预案7、转化进料脱硫不合格处理预案8、转化炉管出现热斑、热带、热管的处理预案9、装置外来燃料中断的处理预案10、H2S中毒救护及预防预案。
制氢讲义

制氢讲义1、为什么要用氢气冷却转子绕组、定子铁芯?1、发电机在运行中产生磁感应的涡流损失和线阻损失,这部分能量损失转变为热量,使发电机的转子和定子发热。
发电机线圈的绝缘材料因温度升高而引起绝缘强度降低,会导致发电机绝缘击穿事故的发生,所以必须不断地排出由于能量损耗而产生的热量。
2、 空气冷却20世纪30年代末期以前,汽轮发电机基本上处于单一的空气冷却阶段。
空气冷却在结构上最简单,费用最低廉,维护最方便,这些显著的优点使得空气冷却首先得到了应用和发展。
随着电网容量的增大,要求提高汽轮发电机的容量。
为了提高容量,需要增加电磁负荷,导致电磁损耗增大,从而引起电机发热量的增加要强化冷却就必须加大通风量,这必然引起通风损耗的增大,而通风损耗(含风摩耗)占总损耗的40%,这就使得电机的效率降低。
另外,空气冷却的定转子绕组的温升也较高,影响绝缘的寿命。
氢气冷却当电机的单机容量达到一定水平时,空冷技术在效率和温升等方面逐渐暴露出不足,为了寻求更加有效的冷却方式,人们发展了氢冷技术。
从20世纪30年代末,容量大于50MW的汽轮发电机逐步过渡到氢气冷却。
氢气的比重小,纯氢的密度仅为空气的1/14,导热系数为空气的7倍,在同一温度和流速下,放热系数为空气的1 4~1 5倍,粘度最小,导热系数最高。
由于密度小,因此,在相同气压下,氢气冷却的通风损耗、风摩耗均为空气的1/10,而且通风噪声亦可减小。
氢冷电机的效率提高了,而且温升明显下降。
由于电机内氢气必须维持规定纯度,为此必须额外设置一套供氢装置,给设计和安装带来了困难。
另外,密封防爆问题始终是氢气冷却电机安全运行的一个隐患。
3、本厂1100MW发电机定子绕组直接水内冷,转子绕组直接氢内冷,定子铁芯氢冷由于发电机都是高转速的汽轮发电机组,由于其转速很高,为3000转/分钟,为降低离心力,其发电机设计成直径短而轴向长度很长的样子。
由于长度太长,发电机中部的热量不易散出,所以需要专门的发电机冷却系统。
制氢站安全培训课件

•制氢站概述•制氢站安全操作规程•制氢站危险源与风险分析•制氢站安全事故案例分析•制氢站安全培训与演练•制氢站安全管理建议与展望010102制氢站的定义与特点非常严重。
流程。
制氢站的工作原理电解水制氢利用电解水技术将水分解为氧气和氢气,通常需要大量电力作为能源。
天然气重整制氢通过高温和催化剂的作用将天然气转化为氢气和一氧化碳的混合气体。
生物质气化制氢利用生物质在缺氧条件下进行热解气化,生成含有一氧化碳和氢气的气体。
严格遵守安全操作规程和定期进行安全检查是确保制氢站安全运行的关键措施。
提高员工的安全意识和应急处理能力也是制氢站安全管理的重要环节。
制氢站的安全管理对于保障人员安全和企业财产安全至关重要。
制氢站的安全管理重要性02010204操作前的准备检查制氢站周围环境是否安全,无明火、无易燃易爆物品,无人员逗留。
确认制氢设备、管道、阀门等设施完好,无泄漏、无异常声响。
穿戴好防护用品,如防爆型眼镜、化学防护服、防静电鞋等。
准备好操作工具,如扳手、螺丝刀、测压仪等。
03严格按照制氢设备操作规程进行操作,不得擅自更改操作程序。
制氢过程中,应保持室内通风良好,防止氢气浓度过高引起窒息。
定期检查制氢设备、管道、阀门等设施的密封性,确保无泄漏。
制氢过程中,如发现异常情况,应立即停止操作,并报告上级领导。
01020304操作过程中的安全注意事项操作后的安全检查03氢气泄漏高压操作静电和雷电人员误操作制氢站的危险源识别制氢站内设备摩擦产生的静电或雷电可能引发火灾或爆炸。
操作人员未按照规定程序进行操作,可能导致设备损坏或人身伤害。
制氢站的风险评估制氢站的风险控制措施04某制氢站因设备老化、维护不当,导致氢气泄漏并引发爆炸。
事故经过事故原因事故教训设备未及时检修,安全防护措施不到位。
加强设备维护,定期进行安全检查,确保设备处于良好状态。
030201事故原因事故经过日常巡检不到位,未能及时发现隐患。
事故教训强化日常巡检,确保及时发现并处理隐患。
制氢装置的运行培训资料

制氢装置的运行培训资料一、启动前准备(一)制氢机清洗制氢机正式投运前应进行除盐水清洗,以除去设备在加工过程中存留在各部件内部的机械杂质。
清洗前设备的所有阀门应处于关闭状态;启动冷却水泵供冷却水。
接通控制柜电源。
打开除盐水罐进水门,此时水罐为空的,UFC磁翻转液位计下限自动接通,水罐自动补水门开,当水位到达上限时此门自动关闭。
打开碱液循环泵冷却水进水门(注:只要泵运转,此门都应打开以冷却电机);打开除盐水罐供水门、系统供水(碱)门、碱液过滤器出口门、碱液过滤器入口门、氧侧事故排空门、氢侧事故排空门,手动启动碱液循环泵,慢慢打开流量调节门。
当氢、氧分离器液位升到中部时,关流量调节门,停碱液循环泵,关系统供水(碱)门。
打开碱液循环泵进口门,启动碱液循环泵,用流量调节门调节流量至最大,冲洗系统1~2小时。
关闭流量调节门,打开系统回水(碱)门、除盐水罐回水门、电解槽回水(碱)门、除盐水罐排污门,将系统水抽回除盐水罐并排放;关系统回水(碱)门,停泵,关碱液循环泵进口门、除盐水罐回水门、电解槽回水(碱)门,当除盐水罐内水放完后关闭除盐水罐排污门,打开碱液过滤器排污门和电解槽两侧排污门,放净系统内存水。
按上述方法反复进行2〜3次,直至排出液清洁为止;若发现排出液不清洁,应联系检修清洗碱液过滤器滤网。
此外,首次试运时,还应用10%电解液整体试运48小时以上,启、停机操作同正常运行操作,以进一步清洗制氢机。
(二)气密实验设备安装完毕后,需对制氢系统进行全面的气密实验。
按清洗中有关步骤将除盐水打入制氢系统至氢、氧分离器液位计中部。
将氮气钢瓶与系统充氮口连接,关闭框架I与外界联系的所有阀门。
打开系统内阀门,通过系统充氮门向系统内充入氮气,使系统压力缓缓升至3.2Mpa,关系统充氮门,用肥皂水检查所有阀门接头、法兰连接及管路焊口等部位,如有泄漏,排除后继续进行,直至不漏为止;保压12小时以上,泄漏量平均每小时不超过0.5%为合格。
《制氢培训》课件

和可持续发展中的前景。
结束语
通过本次制氢培训,您已了解制氢的基本概念、应用领域和未来发展趋势。期待您在未来的工作中应用这些知
识!感谢您参加制氢培训!
3
制氢技术的优势与局限性 ⭐️
制氢技术具有高能量密度、零排放和可再生性等优势,但面临成本和储存挑战。
制氢的安全问题
1
制氢的安全性问题 ⚠️
涉及氢气的高压、易燃和爆炸性质,需要特殊的安全措施。
2
制氢的安全措施 ️
包括适当的储存、运输和操作规范,以及应急处理计划。
3
制氢的应急处理
在发生事故或泄漏时,需要迅速采取措施,确保人员和环境安全。
2
制氢在能源领域的应用 ⚡️
作为可再生能源和能源储存的一种形式,制氢被广泛用于能源领域。
3
制氢在工业领域的应用
用于工业用途,如合成氨和炼油等。
制氢的前景
1
制氢技术的发展趋势
包括可持续能源替代传统能源和制氢技术的进一步创新。
2
制氢技术的未来应用
在交通运输、能源储存和工业生产等领域,制氢将发挥重要作用。
《制氢培训》PPT课件
本课程将向您介绍制氢的基本知识和应用。探索制氢的不同方法、领域应
用、安全问题以及经济与环保影响。欢迎参加本次制氢培训!
什么是制氢?
1
定义 ️
2
原理 ⚛️
3
目的
制氢是指通过特定的过程
制氢的原理涉及将水或化
制氢的目的包括提供能源、
将氢气从其他化合物中分
石燃料与催化剂反应产生
考虑设备投资、运营成本
评估制氢过程中产生的排
促进清洁能源的发展,减
和可持续性经济效益等因
经典的制氢培训教材(原理、运行、维护、安全)
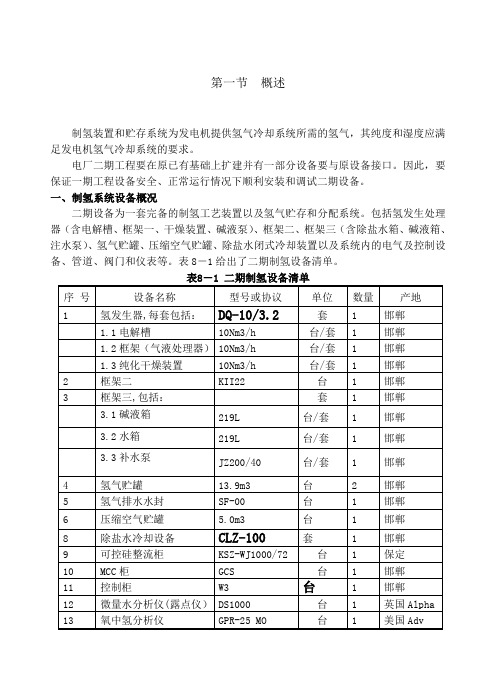
第一节概述制氢装置和贮存系统为发电机提供氢气冷却系统所需的氢气,其纯度和湿度应满足发电机氢气冷却系统的要求。
电厂二期工程要在原已有基础上扩建并有一部分设备要与原设备接口。
因此,要保证一期工程设备安全、正常运行情况下顺利安装和调试二期设备。
一、制氢系统设备概况二期设备为一套完备的制氢工艺装置以及氢气贮存和分配系统。
包括氢发生处理器(含电解槽、框架一、干燥装置、碱液泵)、框架二、框架三(含除盐水箱、碱液箱、注水泵)、氢气贮罐、压缩空气贮罐、除盐水闭式冷却装置以及系统内的电气及控制设备、管道、阀门和仪表等。
表8-1给出了二期制氢设备清单。
1.设备要求1.1 整套设备为组装单元式,单元范围包括所有设备、阀门、管件、支吊架。
同时应提供各单元间的连接管道。
1.2 电解槽连续、间断均可运行。
槽体为碳钢镀镍材质,压缩空气贮罐,氢气贮罐为合金钢,其余设备均为不锈钢材质(1Cr18Ni9Ti)。
1.3 氢气贮罐能耐-19 ℃的低温。
1.4 所有管路阀门均为不锈钢材质(1Cr18Ni9Ti),气管路及碱液管路的阀门和其它参与程控的阀门均采用进口产品。
1.5 到汽机房氢气管应设置二个接口,框架二上还应设置备用氢气接口。
1.6 所有设备在额定条件下应能保证安全运行,电解槽大修周期不少于10年。
2.主要设备性能与参数2.1 电解槽主要技术参数:(安装在氢发生器)2.1.1 氢气产量:10Nm3/h(产氢气量连续可调范围为额定出力的50~100%)。
2.1.2 氧气产量:5Nm3/h2.1.3 氢气纯度:≥99.9%2.1.4 氧气纯度:≥99.3%2.1.5 氢气湿度:<4mg/m32.1.6 电解槽额定工作压力:3.2MPa2.1.7 电解槽工作温度:<90℃2.1.8 电解槽额定工作电流:740A2.1.9 电解槽电解小室工作压力:~2V2.1.10 电解槽单位产氢量直流电耗:4.6kW.h/Nm32.1.11 氢氧分离器液位差:±5mm2.2 氢发生处理器:数量:1套;结构形式:组装框架式,框架材料为碳钢;氢气处理量:10 NmЗ/h;出口氢气含湿量:露点<—55℃。
- 1、下载文档前请自行甄别文档内容的完整性,平台不提供额外的编辑、内容补充、找答案等附加服务。
- 2、"仅部分预览"的文档,不可在线预览部分如存在完整性等问题,可反馈申请退款(可完整预览的文档不适用该条件!)。
- 3、如文档侵犯您的权益,请联系客服反馈,我们会尽快为您处理(人工客服工作时间:9:00-18:30)。
制氢培训讲义制氢装置设计及改造情况1、大连西太平洋石油化工有限公司制氢装置规模为6×104Nm3/h。
两套加氢、脱硫、转化炉、中变采用国内技术;净化系统为变压吸附法,技术为德国林德(Linde)公司专利,引进控制计算机、成套阀门、管线、仪表和吸附剂,吸附罐为国内制作,林德公司制造技术。
设计单位为中国石化北京设计院。
本装置由下列五部分组成:(1)原料油干法加氢、脱硫部分(2)转化及相应对流段热回收部分(3)中温变换及变换气换热冷却部分(4)PSA中变气净化部分(5)开工及循环氢压缩机及酸性水汽提部分装置的加氢、脱硫、转化、中变过程采用两个系列。
PSA部分则为一个系列。
原料设计时以轻质油(重整拔头油或轻石脑油)为主,同时应用少量液化气和ARDS装置弛放干气。
98年7月至今,由于重整装置停工未开,制氢原料改为重整精制油。
产品纯度为H2>99.9%。
产品主要供常渣油加氢脱硫(ARDS)装置、蜡油加氢精制装置及煤柴油加氢精制装置、聚丙烯用。
施工图设计于1992年12月末完成,1995年末基本建成,1997年7月正式投产。
1998年2月经标定达到设计规模,生产稳定,质量良好。
2.生产装置工艺原理本制氢工艺采用以轻质油(重整拔头油或轻石脑油)为原料.经干法加氢、脱硫后与水蒸汽混合,经催化剂转化产生H2、CO及CO2。
转化气再经中温变换将CO与转化气中水蒸汽反应成CO2同时再产生部分H2。
中变气经换热、冷却分液后进往PSA吸附部分脱除中变气的CH4、CO和CO2,生产纯度为99 9%(v)的氢。
RS+H2→R+H2SH2S+Z n O→Z n S+ H2 OR+ H2 O→CH4+CO+CO2CH4+ H2 O→3 H2+CO-QCO+ H2 O→H2+CO2+Q3.生产装置工艺流程详述本装置设计原料主要是重整拔头油,工艺流程大致可分为五部分:(设计条件)(1)原料脱硫部分(分A、B两系列,以A系列为例,下同)40℃的重整拔头油自装置外进原料缓冲罐D-101,经原料泵P-101/1升压至4.0MPa。
升压后的原料油与从配氢压缩机K-101/1来的3.9MPa的氢气(或ARDS装置干气、富氢)混合进入中变气-原料油蒸发器E-104(管程),换热至360℃后进加氢反应器R-101(入口压力约3.35MPa)。
在加氢反应器内将原料中的有机硫转变成无机硫,同时将原料中的少量烯烃饱和。
R-101出来的约3.25MPa、360℃的加氢后的气体进入两台串联的氧化锌脱硫反应器R-102/1.2(设计流程中考虑了两台反应器可串、可并的操作)。
经氧化锌脱硫后的气体中含硫量由约100PPm(V)降至0.3PPm以下,出口气体压力为3.15MPa。
(2)转化及变换部分:经脱硫合格的气体(烯烃含量1%(V)以下,含硫量0.3PPm以下),与3.50MPa蒸汽混合后进入转化炉F-101原料预热段,正常操作水/碳比控制在3.7~4:1(mol/mol),进入原料预热段前温度为415℃,经预热段后温度为500℃,压力为3.05MPa,进入转化炉F-101辐射段(转化段),转化管内上下分别装有Z-402/Z-405G催化剂,各装一半。
转化炉出口温度725-800℃,压力2.70MPa (绝),碳空速约为890时-1,残余甲烷含量3-7%(V)。
自转化炉管出来的转化气,经转化气废热锅炉ER-101回收热量,转化气温度由800℃降至350~370℃,进入中温变换反应器R-103,选用B-113催化剂,开工初期催化剂活较好,温度控制在低限约340℃,末期可提高到380℃,出口温度≯420℃,CO含量1-3%(干)。
自R-103出来的中变气经E-104(中变气-原料油蒸发器),E-103(1.0MPa蒸汽过热器),ER-102(1.0MPa蒸汽发生器),E-102/1.2(中变气-除氧水换热器)换热至164℃进入D-111(中变气第一分液罐),将冷凝液分离后进入E-101(中变气-除盐水换热器),出口温度146℃进D-112(中变气第二分液罐),分出冷凝液后,经EC-101/1~6(中变气空冷器)及D-113(中变气第三分液罐)分液后进入E-105(中变气水冷器)冷却至40℃经D-114(中变气第四分液罐)分液后进入PSA系统。
(3)转化及变换部分所用锅炉水及蒸汽系统:锅炉用除盐水自外部送来经E-101温度升至104℃进入脱氧槽D-108,用泵P-102/1(锅炉给水泵)抽出进入E-102/1.2,出口温度180℃,分成两部分,一部分进入低压汽包D-107及ER-102,发生1.0MPa蒸汽。
蒸汽再经E-103过热至250℃进入1.0MPa蒸汽管网。
另一部分直接进入中压汽包D-103及转化炉废热锅炉ER-101。
转化气废热锅炉和烟道气废热锅炉均为自然循环式;产3.50Mpa、243℃的饱和蒸汽自汽包引出进入转化炉F-101的蒸汽过热段,过热至435℃后分成两部分,一部分(46.04t/h)与原料气混合,另一部分作为外供蒸汽出装置。
(4)氢气净化部分(两个系列合用一套):自A系列、B系列来的中变气混合后进入PSA系统,进口压力为2.1MPa,氢气回收率88%,出口气体即为产品氢气,其余为尾气。
尾气去两列转化炉用于燃料,不足的用瓦斯,燃烧后的烟道气放大气。
具体情况见表(一)(5)酸性水处理系统:自中变气第一、二、三、四分液罐分出的CO2酸性水(两系列合在一起)进酸性水汽提塔C-101,用1.0MPa蒸汽汽提后进E-108(酸性水-热水换热器)冷却至80℃进泵P-104升压后进E-107(酸性水冷却器),降温至40℃送往全厂脱盐水罐。
«Skip Record If...»仅供学习与交流,如有侵权请联系网站删除谢谢22PSA工艺原理变压吸附工艺是一个物理吸附的过程,以氢和氦为代表的具有高挥发性低极性分子,与其它分子如CO2、CO、N2、烃类相比,没有吸附性能。
由此绝大多数的杂质在粗氢原料中被选择吸附,从而得到高纯度的产品氢。
2.1 概述变压吸附工艺工作于两个不同的压力等级。
●吸附杂质是在高压下完成的,杂质被吸附在吸附剂上。
●解吸或再生是在低压下完成,以便尽可能降低杂质在吸附剂上的吸附,从而达到高的产品氢纯度,PSA在吸附与解吸时,吸附剂上承载的杂质数量相差越大,PSA的氢收率越高。
此工艺过程在常温下进行,再生步骤无须热量,因为吸附过程只有少量放热,解吸和泄压过程中有少量吸热,所以整个工艺过程只有轻微的温度变化,吸附剂不会因为热量的影响而导致失活,所以会有极长的使用寿命。
2.2 吸附和再生循环周期PRESSURE SWING ADSORPTION (PSA)装置是为连续提纯粗氢而设计的,尽管PSA工艺过程从表面上看是连续的过程,实际上它是由多个并列运行步位组成的不连续过程。
总而言之,每一个吸附器都按照一定的规律循环进行,以完成变压吸附工艺过程。
变压吸附工艺过程基于两个基本步骤,吸附和解吸,而解吸步骤是由一连串子步骤组成:●由高压过渡到低压:“泄压”、“提供吹扫”和“排放”。
●在低压下“吹扫”。
●由低压转换到吸附压力:“升压”。
吸附分离工艺是连续提供产品氢的过程,它是由多个装满吸附剂的压力容器、相互连接的管道以及各自的控制阀组成。
在操作过程中,至少一个吸附器处于高压吸附状态,从原料气中分离杂质,与此同时,另外的吸附器在进行再生。
控制程序保证了工艺过程的有序进行,按要求切换处于吸附状态的吸附器,使杂质绝不会通过吸附器窜入产品氢,因此程序必须确保有吸附器处于吸附状态时,另外的吸附器能够得到充分的再生和升压,以取代处于吸附步位即将达到杂质承载能力的吸附器。
吸附原料气自吸附器底部至顶部穿过,如 CO2、烃、CO等杂质被选择吸附在吸附剂表面。
提纯后的产品氢自吸附器顶部排到产品氢总管。
由于该系统尽量利用残留在吸附器中的氢气(在吸附步位后)来均压、升压和给其它吸附器提供吹扫气,因此,PSA系统在氢气利用方面有很高的效率。
在吸附过程中,产品氢纯度保持稳定,在吸附周期结束时,产品氢中开始有微量杂质,这表明吸附器已经吸附满了杂质,需要进行再生。
再生吸附器在吸附步位吸附满了杂质后,再生分四个基本步骤进行:●吸附器按照原料气流向泄压到较低压力,利用该吸附器储存的氢气给其它的吸附器升压或吹扫。
●吸附器逆向泄压,排放至尾气,(供吹扫步位、排放步位),除掉吸附剂上的杂质。
●利用供吹扫步位吸附器提供的氢气或氢气总管的纯氢吹扫该吸附器,除掉吸附剂上残留的杂质。
吸附器利用均压步位提供的纯氢或者氢气总线的纯氢逐步升压到吸附压力。
2.3 产品氢符合设计规范要求的高纯度氢气从吸附器顶部排入产品氢线。
产品氢压力等于原料压力减去PSA单元的压力损失。
2.4 尾气尾气在尾气系统中进行混合,使尾气组成、流量和压力稳定。
尾气系统由两个尾气罐,调节流量压力和分子量的控制器组成。
2.5 工艺条件对PSA装置的影响PSA加工能力表示在给定的操作条件下,所能加工的原料气量。
氢收率是产品氢量与原料气中氢总量的百分比。
以下是对吸附能力和氢收率有影响的主要工艺条件。
原料气加工能力与吸附压力的关系气体组分如CO、CO2、CH4、C2等,在吸附剂上的吸附量随着吸附压力的增加而增加,因此吸附能力随着吸附压力的增加而提高,随着吸附压力降低而减少。
氢收率与吸附压力的关系通常情况下,氢收率随着吸附压力升高而提高,随着吸附压力的降低而降低。
原料起讫加工能力与解吸压力的关系吸附了杂质的吸附器随着压力的降低得到了再生,解吸压力越低再生效果越好,如果解吸压力升高,残留在吸附剂上的杂质的量也升高,结果,吸附能力也随之降低。
因此,吸附能力随着解吸压力的降低而升高,随着解吸压力的升高而降低。
氢收率与解吸压力的关系在通常情况下,氢收率随着解吸压力的降低而升高,随着解吸压力的升高而降低。
2-4原料加工能力与吸附温度和解吸温度的关系吸附剂对原料加工能力随着原料温度上升而降低,但是较高的原料温度会有较好的吹扫效果,最佳的PSA运行温度是15-40,较高的温度是允许的,但是随着温度的上升,会降低吸附能力,应当避免吸附温度低于10,温度与吹扫效果成反比。
等温曲线随着温度上升而降低,吸附和解吸在压力下,影响效果是装载量有较低的差别。
以下图表解释这种效果。
原料气组分吸附器吸附能力取决于被吸附气体的种类与总量,原料气组成的影响可分为以下种类:注意要绝对避免原料气中的液体,因为液体会损坏吸附剂。
产品纯度吸附能力总是随着产品纯度升高而降低,随着产品纯度降低而升高LINDE-PSA专家培训总结一、 PSA开车新旧区别:1.PSA旧版开车有自动均压功能,而在新版中,此功能被取消。
我们认为此功能有两点好处:A.此功能能使PSA自己调整各吸附器压力,尽可能的减少现场手动调整需要的时间和现场阀门开关所带来的不必要的麻烦。