分解炉的温度控制
分解炉温度的控制目的在于控制分解率

分解炉温度的控制目的在于控制分解率分解炉温度的控制目的在于控制分解率。
C1出口温度主要受入窑生料量的影响,其次是预热器排风量及尾煤燃烧情况。
对于前者,控制入窑生料量的稳定是控制热工制度稳定的关键。
我们常说“五稳保一稳”,“五稳”指“入窑生料量、生料成分稳,给煤量、燃煤成分稳,设备运转稳定”,“一稳”指“热工制度稳定”。
在“五稳”中烧成操作可控制的只有入窑生料量和给煤量两个,而给煤量是由入窑生料量的大小来决定。
所以说控制入窑生料量的稳定是控制热工制度稳定的关键。
对于后者,预热器出口CO%与预热器排风量及尾煤燃烧情况的好坏密切相关。
二、压力与气氛制度:压力与气氛是相互联系密不可分的。
例如我们要求窑尾O2%0.7-1.0%,CO%无或者很少,亦即保持窑内的还原或氧化气氛。
在窑头给煤量一定的情况下,要达到上述要求就必须通过调节喷煤管的风量匹配及窑炉风量匹配来达到。
对于分解炉出口要求O2%3.0-4.0%,预热器出口一般要求3.0%左右.根据我在操作和生产调试的经验认为,预热器出口O2%偏下限控制在2.5-3.0%时在烧成上比较易于控制,电耗煤耗方面也比较经济。
前提条件是分解炉炉容合适,尾煤能在分解炉内完全燃烧或只有少量在五级旋风筒内燃烬。
预热器出口O2%2.5-3.0%与3.0-3.5%的区别在于,相同投料量的情况下拉风量不一样,亦即C1出口负压比3.0-3.5%时要小一些。
产生的后果是分解炉内风速降低物料滞留时间延长,炉内煤粉燃烬度提高,旋风筒收尘效率增加。
明显的区别是O2%2.5-3.0%时C1出口温度要比3.0-3.5%时要低5-10度。
三、热平衡制度:“热平衡”比较容易理解,“热量收入=热量支出”,热量收入包括煤粉燃烧产生热、物料化学反应热、熟料回收热等,热量支出包括生料分解吸热、加热空气和物料耗热、胴体散热、熟料和空气带走的热量等。
热平衡牵涉到物料与气流的平衡。
稳定的热工制度反映在热平衡上,收入与支出的各子项也相对稳定。
分解炉的温度控制

B56T1(℃) 793 780 767 767 759
CO含量(%) 0.07 0.06 0.06 0.07 0.09
从表中可见,该预分解窑在一定的范围内,分解炉的燃烧用量比例存在着一个最佳值。在该条件下,最佳值为约61.5%,此时其热耗最低。大于或少于此值,热耗均增加。也就是说,在一定产量范围内的某窑,分解炉喂煤量既不是越高越好,也不是越低越好。分解炉喂煤的比例与热耗的关系不是线性的,而是非线性的。有的统计得出两者的关系是线性的结论,认为窑头喂煤越多越好或分解炉喂煤越多越好,实际上是最佳值的某一侧,从而产生分解炉用燃料比例与热耗关系是线性关系的错觉而已。
从燃料燃烧的角度来看,分解炉内燃料的燃烧与回转窑内燃料燃烧有许多不同之处。回转窑内燃料燃烧温度比分解炉内高得多,回转窑内燃料燃烧明显是受扩散控制的,而分解炉内燃料燃烧则有所不同。由于分解炉温度远低于回转窑内燃料燃烧温度,故煤在分解炉内的燃烧时间受煤种类的影响比回转窑内的影响大得多。如广东云浮水泥厂FCB分解炉容积偏小,结构上亦存在一些问题,当使用低挥发分、高灰分的低热值煤时,还原气氛十分严重,迅速导致结皮堵塞;而采用高挥发分、低灰分的高热值煤时情况则有所改善。煤粉细度对于回转窑内的燃烧是相当敏感的,因为其是受扩散控制,即受边界层扩散时输送速率的控制;而煤粉细度对分解炉内燃烧的影响就没有在回转窑内那样敏感了。
还需说明的是,分解炉的通风量对分解炉出口温度及末级旋风筒下部温度亦有影响。即使分解炉的喂煤量、物料量不变,但通风量改变,亦会产生影响。当通风量过大,分解炉内气流速度过快,燃料及物料在分解炉内停留时间不足;反之,当通风量过小,供气不足,燃料燃烧同样受影响。总之,通风量的波动,窑风量与分解炉风量的分配不当,都会影响分解炉燃料的燃烧,从而导致分解炉出口温度与最末一级旋风筒下部温度的异常。
在DCS系统中实现分解炉温度与喷煤量自动控制

个 相 对稳定 的温度且 不 可太高 或太低 。因温度 太
的, 具 体温度 控 制系统 结构 框 图见 图 1 。
高 会造 成 预热 器堵 塞 ;太低 则导 致碳 酸 盐分 解不 充
分, 加大了窑系统的分解任务。因此分解炉 的温度 控 制 对整 个 回转 窑 运 转热 工 状 况 的稳 定至 关 重要 , 降低分解炉温度波动并与喂煤量达到协调控制是生
泵 用模 糊 P I D控 制 系 统 试 运行 以来 效 果 良好 。
当分解炉温度在上位机界面的设定值 为 8 4 5℃时 , 温度稳定控制在 8 4 5 c I = 左右 , 波动非常小 ( ± 5 ℃) , 线 性关 系良好 。表 1 为 回转窑运行的部分数据。
表1 2 0 1 0 年9 至1 1 月窑运行数据数据
率来 达 到调 节分解 炉 出 口温 度 的 目的。 D C S 程序中 P I D功 能 可 以实 现对 控制 对 象 的精
分解炉的温度是一个纯滞后 、 大惯性 、 非线性的 复杂控制对象, 影响 因素很多, 各因素之间耦合性 强, 因而难 以用 常规控制方法进行控制, 实际生产 中主要靠操作者凭经验来操控 。当温度过低时, 需
1 问题及 其原 因分 析
系统 的对 象惯 性小 , 工 作频率 高 , 可 以提 高系统 误差
葛 洲坝 宜城 水 泥有 限公 司 5 0 0 0 t / d 新 型 干法 水 泥 生 产线 于 2 0 0 9年 1 0月投 产 。 在试 生 产 过程 中出 现 了 因分解 炉温 度波
分分解 , 提高了熟料 的产质量 、 降低操作员劳动强 度、 大幅降低了尾煤煤耗 。
3 结 语
通 过 对 分解 炉生 产 工 艺 的分 析 , 设 计 了一 种 适
分解炉温度控制的几个问题
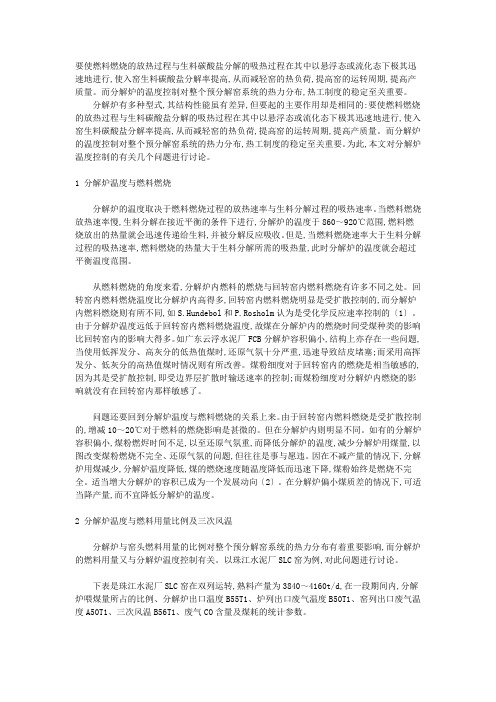
要使燃料燃烧的放热过程与生料碳酸盐分解的吸热过程在其中以悬浮态或流化态下极其迅速地进行,使入窑生料碳酸盐分解率提高,从而减轻窑的热负荷,提高窑的运转周期,提高产质量。
而分解炉的温度控制对整个预分解窑系统的热力分布,热工制度的稳定至关重要。
分解炉有多种型式,其结构性能虽有差异,但要起的主要作用却是相同的:要使燃料燃烧的放热过程与生料碳酸盐分解的吸热过程在其中以悬浮态或流化态下极其迅速地进行,使入窑生料碳酸盐分解率提高,从而减轻窑的热负荷,提高窑的运转周期,提高产质量。
而分解炉的温度控制对整个预分解窑系统的热力分布,热工制度的稳定至关重要。
为此,本文对分解炉温度控制的有关几个问题进行讨论。
1 分解炉温度与燃料燃烧分解炉的温度取决于燃料燃烧过程的放热速率与生料分解过程的吸热速率。
当燃料燃烧放热速率慢,生料分解在接近平衡的条件下进行,分解炉的温度于860~920℃范围,燃料燃烧放出的热量就会迅速传递给生料,并被分解反应吸收。
但是,当燃料燃烧速率大于生料分解过程的吸热速率,燃料燃烧的热量大于生料分解所需的吸热量,此时分解炉的温度就会超过平衡温度范围。
从燃料燃烧的角度来看,分解炉内燃料的燃烧与回转窑内燃料燃烧有许多不同之处。
回转窑内燃料燃烧温度比分解炉内高得多,回转窑内燃料燃烧明显是受扩散控制的,而分解炉内燃料燃烧则有所不同,如S.Hundebol和P.Rosholm认为是受化学反应速率控制的〔1〕。
由于分解炉温度远低于回转窑内燃料燃烧温度,故煤在分解炉内的燃烧时间受煤种类的影响比回转窑内的影响大得多。
如广东云浮水泥厂FCB分解炉容积偏小,结构上亦存在一些问题,当使用低挥发分、高灰分的低热值煤时,还原气氛十分严重,迅速导致结皮堵塞;而采用高挥发分、低灰分的高热值煤时情况则有所改善。
煤粉细度对于回转窑内的燃烧是相当敏感的,因为其是受扩散控制,即受边界层扩散时输送速率的控制;而煤粉细度对分解炉内燃烧的影响就没有在回转窑内那样敏感了。
氨分解炉参数

氨分解炉参数1. 简介氨分解炉是用来分解液氨的装置,其主要作用是将液氨气化并分解。
氨分解炉是化工、制氢等行业中常见的设备之一,其参数对于氨分解炉的性能和安全保障至关重要。
2. 氨分解炉的参数(1)炉体压力炉体压力是氨分解炉的重要参数之一。
其设置的原则是在保证工艺条件的前提下,按照炉管的承压能力来确定。
通常情况下,炉体压力设置为0.3~0.5MPa。
(2)炉体温度炉体温度是氨分解炉另一个关键参数。
氨气的分解需要一定的温度和热量,炉体温度设置在600℃ ~800℃之间比较合适,一般设定为700℃左右。
(3)氨气流量通常情况下,氨气的分解速度是很慢的,为了提高分解速度,需要增大氨气的流量,一般设置在200~400m³/h之间。
(4)催化剂数量选择适量催化剂对于氨分解炉的运行有极大帮助。
过多的催化剂会使催化剂的活性质减弱,使得反应效率下降;过少的催化剂则可能需要增加反应时间,影响生产效率。
一般情况下,催化剂的添加量为6%~10%左右。
(5)氨分解炉设计氨分解炉的设计也是十分重要的。
炉体内应设置适当的隔板和搅拌装置,以均匀分布氨气和催化剂。
并且在炉管连接处需要设置密封装置,以保证气体的流动性能。
3. 注意事项氨分解炉工艺条件的设置应根据具体情况进行调整。
不同的原料质量、生产工艺、生产规模等都会对工艺参数有所影响。
在确定工艺参数时,需要进行适当的试验和检测,以保证氨分解炉的高效稳定运行。
此外,氨分解炉的安全性也需要引起重视。
在分解过程中,需要保证气体不外漏,并通过相应的防爆装置以保证运行的安全性。
4. 总结氨分解炉的参数对氨气分解效率和安全有着重要的影响。
在生产和实验中,应根据实际工艺条件合理设置各项参数,并保证设备的安全性。
同时,需要依靠实验和检测结合工艺条件的优化来提高氨分解炉的效率和稳定性。
材料工程技术专业《分解炉的热工性能》

分解炉的热工性能分解炉生产工艺对热工条件的要求如下。
①炉内气流温度不宜超过950°C,以防系统产生结皮、堵塞。
②燃烧速度要快,以保证供应碳酸盐分解所需要的大量的热量。
③保持窑炉系统较高的热效率和生产效率。
〔一〕分解炉内燃料的燃烧1、无焰燃烧与辉焰燃烧当煤粉进入分解炉后,悬游于气流中,经预热、分解、燃烧发出光和热,形成一个个小火星,无数的煤粉颗粒便形成无数的迅速燃烧的小火焰。
这些小火焰浮游布满炉内,从整体看,看不见一定轮廓的有形火焰。
所以分解炉中煤粉的燃烧并非一般意义的无焰燃烧,而是充满全炉的无数小火焰组成的燃烧反响。
有人把分解炉内的燃烧称为辉焰燃烧,这主要指分解炉内将料粉或煤粉均匀分散于高温气流中,使粉料颗粒受热达一定温度后,固体颗粒发出光、热辐射而呈辉焰。
但并不能看到有形的火焰而只见满炉发光。
分解炉内无焰燃烧的优点是燃料均匀分散,能充分利用燃烧空间,不易形成局部高温。
燃烧速度较快,发热能力较强。
燃烧大致有两种动力学机制。
〔1〕以化学反响控制的机制,其燃烧特点如下。
①燃烧与温度的关系,提高温度可大大提高反响速度。
燃烧速率与温度成指数关系。
②炭粒燃尽时间T与其初始直径成正比。
〔2〕以氧气向煤粒外表扩散控制的机制,特点如下。
①燃烧受温度的影响较小。
②炭粒燃尽时间与其初始直径的平方成正比。
③燃烧与气流流速和湍流度密切相关。
通常煤燃烧在低温下受化学反响控制,在高温下受扩散控制,大约在1000°C左右时发生转变。
2、煤粉的着火着火就是煤的燃烧速率大于系统散热速率时的状态,而煤的着火点也就是导致燃烧速率大于散热速率时的分界点的温度值。
因而煤的着火点并不是一个固有的物理性质常数,它与具体系统的散热条件有关,不同的散热特性方程将有不同的着火点。
在无CaCO3的条件下,一般燃烧炉中气流温度非恒温,而是随燃烧而变化。
在这种条件下,煤的着火点可下降。
这是因为分解炉炉体向周围环境的散热较燃烧的放热可忽略不计,而CaCO3分解吸热很大,往往超过煤的放热速率。
氨分解岗位操作规程
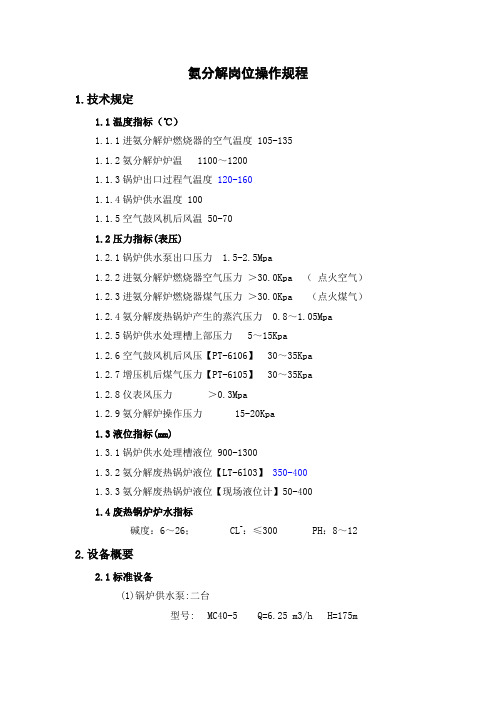
氨分解岗位操作规程1.技术规定1.1温度指标(℃)1.1.1进氨分解炉燃烧器的空气温度 105-1351.1.2氨分解炉炉温1100~12001.1.3锅炉出口过程气温度120-1601.1.4锅炉供水温度 1001.1.5空气鼓风机后风温 50-701.2压力指标(表压)1.2.1锅炉供水泵出口压力 1.5-2.5Mpa1.2.2进氨分解炉燃烧器空气压力>30.0Kpa (点火空气)1.2.3进氨分解炉燃烧器煤气压力>30.0Kpa (点火煤气)1.2.4氨分解废热锅炉产生的蒸汽压力 0.8~1.05Mpa1.2.5锅炉供水处理槽上部压力 5~15Kpa1.2.6空气鼓风机后风压【PT-6106】 30~35Kpa1.2.7增压机后煤气压力【PT-6105】 30~35Kpa1.2.8仪表风压力>0.3Mpa1.2.9氨分解炉操作压力 15-20Kpa1.3液位指标(mm)1.3.1锅炉供水处理槽液位 900-13001.3.2氨分解废热锅炉液位【LT-6l03】350-4001.3.3氨分解废热锅炉液位【现场液位计】50-4001.4废热锅炉炉水指标碱度:6~26; CL-:≤300 PH:8~12 2.设备概要2.1标准设备(1)锅炉供水泵:二台型号:MC40-5 Q=6.25 m3/h H=175m附电机:Y180M-2W N=22kW(2)煤气增压机:型号: ML32WD Q=7.49m3/min P=39kPa附电机:YB160m-4 N=11KW(3)空气鼓风机:二台型号:D30-61-1.5 Q=30m3/min P=49kPa附电机: YB225M-2 N=45kW2.2非标准设备(1)氨分解炉: 一台总重64.053t DN1800/2600 H=8070(2)废热锅炉: 一台单重:8.000t F=115m2(3)锅炉供水处理槽:一台单重:4.215t V=23.4m3(4)空气预热器:一台单重:1.425t F=38.1m2(5)燃烧器:一台单重:1.705t3.工艺说明从蒸氨塔C-2302来的氨汽,在蒸汽夹套管内预热,然后进入氨分解炉H-6101,在1100℃-1200℃高温和镍催化剂的作用下,氨和氰化氢等氮化物被催化分解,生成氮、氢和一氧化碳。
氨分解炉安全操作规程
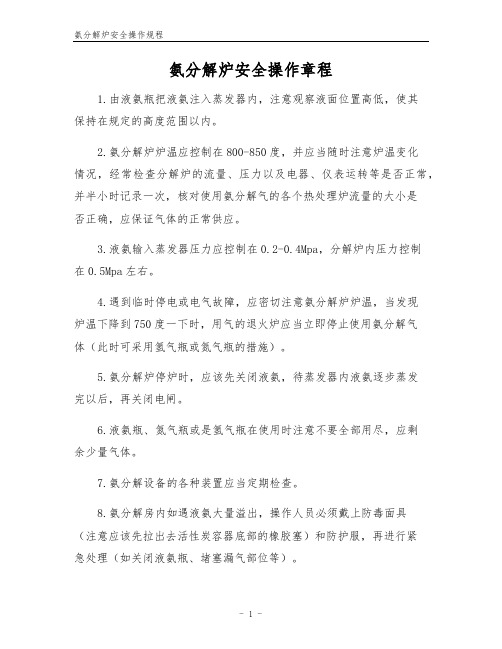
氨分解炉安全操作章程
1.由液氨瓶把液氨注入蒸发器内,注意观察液面位置高低,使其
保持在规定的高度范围以内。
2.氨分解炉炉温应控制在800-850度,并应当随时注意炉温变化
情况,经常检查分解炉的流量、压力以及电器、仪表运转等是否正常,并半小时记录一次,核对使用氨分解气的各个热处理炉流量的大小是
否正确,应保证气体的正常供应。
3.液氨输入蒸发器压力应控制在0.2-0.4Mpa,分解炉内压力控制
在0.5Mpa左右。
4.遇到临时停电或电气故障,应密切注意氨分解炉炉温,当发现
炉温下降到750度一下时,用气的退火炉应当立即停止使用氨分解气
体(此时可采用氢气瓶或氮气瓶的措施)。
5.氨分解炉停炉时,应该先关闭液氨,待蒸发器内液氨逐步蒸发
完以后,再关闭电闸。
6.液氨瓶、氮气瓶或是氢气瓶在使用时注意不要全部用尽,应剩
余少量气体。
7.氨分解设备的各种装置应当定期检查。
8.氨分解房内如遇液氨大量溢出,操作人员必须戴上防毒面具
(注意应该先拉出去活性炭容器底部的橡胶塞)和防护服,再进行紧
急处理(如关闭液氨瓶、堵塞漏气部位等)。
9.操作人员如因氨气刺激而发生昏倒现象,应当立即抢救并离开现场,同时必须用清水不断洗其眼部。
分解炉的控制方法

分解炉控制对于窑外分解窑来说,分解炉是其核心部分,它不仅承担了系统中燃料燃烧,气固换热,碳酸盐分解的任务,而且对整个烧成系统的热力分布,热工制度的稳定起着至关重要的作用,虽然现在应用的分解炉型式众多,结构各异,但其特点和具有的功能基本上都是一样的,都属于高温气固多相流反应器,且具有悬浮床的特征。
对于中控窑操作者来说:分解炉温度(包括分解炉本体温度和出口温度)是最重要的检测控制参数之一,因为它不但表征了生料在分解炉内的预分解情况,也就是生料在分解炉中分解率的高低(分解率的高低直接影响着回转窑运转的稳定性和熟料产、质量以及能耗的高低);同时也表征了燃料在分解炉中的燃烧情况。
因此,作为中控窑操作员来说,要想操作好预分解窑,首先必须保证分解炉的热工制度稳定,要想使分解炉的热工制度稳定,就必须搞清楚以下几个问题:(1)燃料在分解炉中的燃烧传热特性及其影响因素;(2)生料在分解炉中的吸热分解速度及其影响因素;(3)气流在分解炉中运动对燃料燃烧放热和生料分解吸热的影响;(4)分解炉温度高低对回转窑煅烧的影响;(5)分解炉温度调节控制的原则与方法;(6)分解炉温度异常情况的原因与处理等。
下面就这几个问题谈一下个人的看法与认识。
不足之处,尚请指正。
一、燃料在分解炉中的燃烧、传热特性及其影响因素1.燃料在分解炉中的燃烧特性在分解炉中,燃料的燃烧传热特性与回转窑内燃料的燃烧传热特性有着本质上的区别。
回转窑内燃料的燃烧是扩散控制的过程,其火焰必须与回转窑内的煅烧制度相适应,即要求有一定的火焰形状、长度和温度。
通常我们所说的火焰形状为“毛笔头状”、“棒槌状”以及不正常时形成的“球形”火焰,“舔料形”火焰等就是这一特征的体现。
而当煤粉颗粒喷入分解炉后,在旋流和喷腾作用的影响下,使得煤粉颗粒浮游于热气流中,经过预热,分解——煤中的挥发分吸收热量放出氮、氢、氧等,燃烧发出光和热,形成一个一个的小火星,无数的煤粉颗粒便形成无数个迅速燃烧的小火星,这些小火星实质上也就是一个个的小火焰,它们在气流的悬浮作用下充满整个分解炉,从而在整个分解炉内都形成燃烧区。
控制分解炉温度的意义
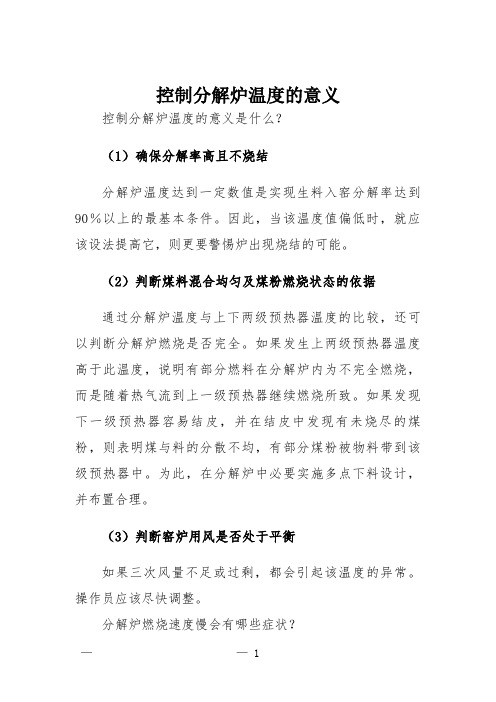
控制分解炉温度的意义
控制分解炉温度的意义是什么?
(1)确保分解率高且不烧结
分解炉温度达到一定数值是实现生料入窑分解率达到90%以上的最基本条件。
因此,当该温度值偏低时,就应该设法提高它,则更要警惕炉出现烧结的可能。
(2)判断煤料混合均匀及煤粉燃烧状态的依据
通过分解炉温度与上下两级预热器温度的比较,还可以判断分解炉燃烧是否完全。
如果发生上两级预热器温度高于此温度,说明有部分燃料在分解炉内为不完全燃烧,而是随着热气流到上一级预热器继续燃烧所致。
如果发现下一级预热器容易结皮,并在结皮中发现有未烧尽的煤粉,则表明煤与料的分散不均,有部分煤粉被物料带到该级预热器中。
为此,在分解炉中必要实施多点下料设计,并布置合理。
(3)判断窑炉用风是否处于平衡
如果三次风量不足或过剩,都会引起该温度的异常。
操作员应该尽快调整。
分解炉燃烧速度慢会有哪些症状?
有时生产中会碰到这样的现象:分解率并不低,可以达到90%以上,但分解炉的出口温度要高于炉中40℃以上,尤其是在烧挥发份较低的无烟煤时。
由于燃烧速度慢,导致仍有部分燃料不能在炉内燃烧,大量热量未在炉内放出,使上一级预热器温度比分解炉温度高,出现温度倒挂现象,使C1筒出口温度升高,增加熟料热耗,也直接影响到下一级预热器温度与窑尾温度过分升高。
造成如下后果:
(4)垂直上升烟道结皮严重,还会使窑尾部分的窑衬上结挂较厚的窑皮,甚至成圈,如果不及时改变这种非正常状态,后窑口向外倒料,就会迫使窑止料停窑处理(5)迫使窑头加补上煤,使分解炉的用煤量由60%提高到70%,从而束缚了窑系统产量的提高
遇到这种现象,如果不认真分析,往往会归结于窑头煤粉燃烧不好所致。
中控操作-分解炉操作控制
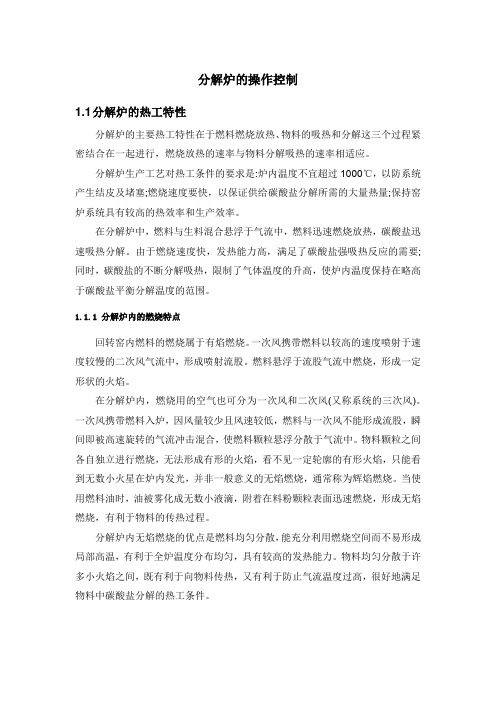
分解炉的操作控制1.1 分解炉的热工特性分解炉的主要热工特性在于燃料燃烧放热、物料的吸热和分解这三个过程紧密结合在一起进行,燃烧放热的速率与物料分解吸热的速率相适应。
分解炉生产工艺对热工条件的要求是:炉内温度不宜超过1000℃,以防系统产生结皮及堵塞;燃烧速度要快,以保证供给碳酸盐分解所需的大量热量;保持窑炉系统具有较高的热效率和生产效率。
在分解炉中,燃料与生料混合悬浮于气流中,燃料迅速燃烧放热,碳酸盐迅速吸热分解。
由于燃烧速度快,发热能力高,满足了碳酸盐强吸热反应的需要;同时,碳酸盐的不断分解吸热,限制了气体温度的升高,使炉内温度保持在略高于碳酸盐平衡分解温度的范围。
1.1.1分解炉内的燃烧特点回转窑内燃料的燃烧属于有焰燃烧。
一次风携带燃料以较高的速度喷射于速度较慢的二次风气流中,形成喷射流股。
燃料悬浮于流股气流中燃烧,形成一定形状的火焰。
在分解炉内,燃烧用的空气也可分为一次风和二次风(又称系统的三次风)。
一次风携带燃料入炉,因风量较少且风速较低,燃料与一次风不能形成流股,瞬间即被高速旋转的气流冲击混合,使燃料颗粒悬浮分散于气流中。
物料颗粒之间各自独立进行燃烧,无法形成有形的火焰,看不见一定轮廓的有形火焰,只能看到无数小火星在炉内发光,并非一般意义的无焰燃烧,通常称为辉焰燃烧。
当使用燃料油时,油被雾化成无数小液滴,附着在料粉颗粒表面迅速燃烧,形成无焰燃烧,有利于物料的传热过程。
分解炉内无焰燃烧的优点是燃料均匀分散,能充分利用燃烧空间而不易形成局部高温,有利于全炉温度分布均匀,具有较高的发热能力。
物料均匀分散于许多小火焰之间,既有利于向物料传热,又有利于防止气流温度过高,很好地满足物料中碳酸盐分解的热工条件。
1.1.2分解炉内的传热在分解炉内,燃料燃烧速度很快,发热能力很高。
料粉分散于气流中,在悬浮状态下,气固相之间的传热面积极大,传热速率极快,燃烧放出的大量热量在很短的时间内被物料所吸收,既达到很高的分解率,又防止气流温度过高。
生料入窑分解率和分解炉温度的控制
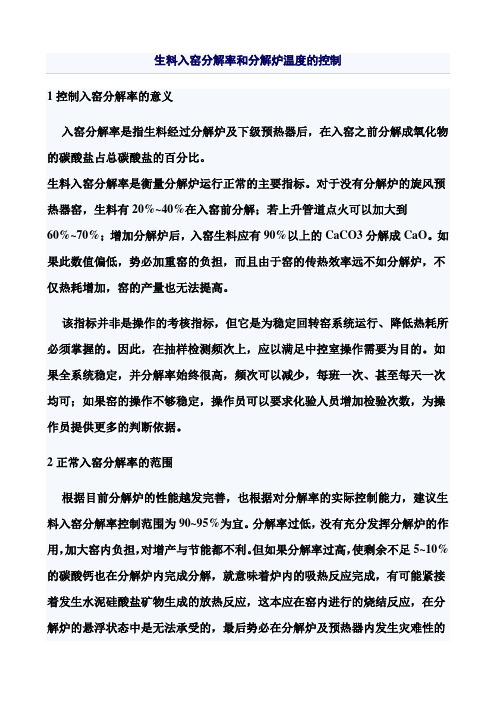
1控制入窑分解率的意义入窑分解率是指生料经过分解炉及下级预热器后,在入窑之前分解成氧化物的碳酸盐占总碳酸盐的百分比。
生料入窑分解率是衡量分解炉运行正常的主要指标。
对于没有分解炉的旋风预热器窑,生料有20%~40%在入窑前分解;若上升管道点火可以加大到60%~70%;增加分解炉后,入窑生料应有90%以上的CaCO3分解成CaO。
如果此数值偏低,势必加重窑的负担,而且由于窑的传热效率远不如分解炉,不仅热耗增加,窑的产量也无法提高。
该指标并非是操作的考核指标,但它是为稳定回转窑系统运行、降低热耗所必须掌握的。
因此,在抽样检测频次上,应以满足中控室操作需要为目的。
如果全系统稳定,并分解率始终很高,频次可以减少,每班一次、甚至每天一次均可;如果窑的操作不够稳定,操作员可以要求化验人员增加检验次数,为操作员提供更多的判断依据。
2正常入窑分解率的范围根据目前分解炉的性能越发完善,也根据对分解率的实际控制能力,建议生料入窑分解率控制范围为90~95%为宜。
分解率过低,没有充分发挥分解炉的作用,加大窑内负担,对增产与节能都不利。
但如果分解率过高,使剩余不足5~10%的碳酸钙也在分解炉内完成分解,就意味着炉内的吸热反应完成,有可能紧接着发生水泥硅酸盐矿物生成的放热反应,这本应在窑内进行的烧结反应,在分解炉的悬浮状态中是无法承受的,最后势必在分解炉及预热器内发生灾难性的烧结堵塞。
应该说,正是这个5%尚未完成分解的生料阻止了完成分解后的温度剧升,那种想象进一步提高分解率,便可以挖掘提高窑产量的潜力,将是很危险的。
3控制分解炉温度的意义⑴可确保分解率高又不烧结的必须。
分解炉温度达到一定数值是实现生料入窑分解率达到90% 以上的最基本条件。
因此,当该温度值偏低时,就应该设法提高它;但是如果此温度过高,则更要警惕炉内出现烧结的可能。
⑵判断煤料混合均匀及煤粉燃烧状态的依据。
通过分解炉温度与上下两级预热器温度的比较,还可以判断分解炉燃烧是否完全。
氨分解炉操作指导书
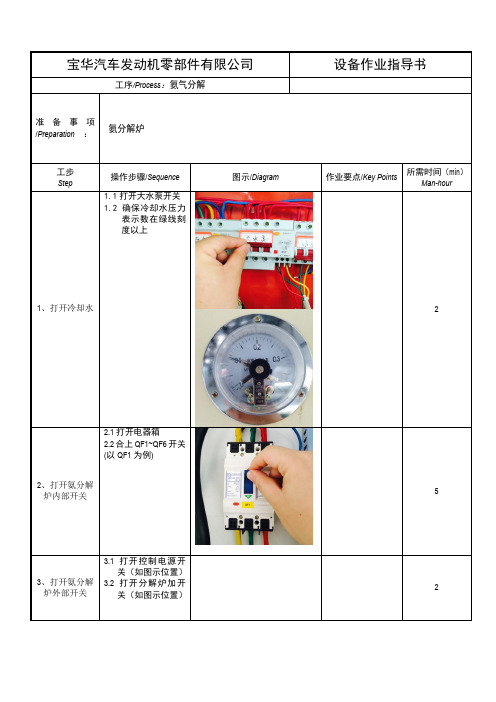
宝华汽车发动机零部件有限公司设备作业指导书工序/Process:氨气分解准备事项/Preparation:氨分解炉工步Step 操作步骤/Sequence 图示/Diagram作业要点/Key Points所需时间(min)Man-hour1、打开冷却水1.1打开大水泵开关1.2 确保冷却水压力表示数在绿线刻度以上22、打开氨分解炉内部开关2.1打开电器箱2.2合上QF1~QF6开关(以QF1为例)53、打开氨分解炉外部开关3.1 打开控制电源开关(如图示位置)3.2 打开分解炉加开关(如图示位置)24.1 按上调或下调按钮调节设定温度,起始设定为400℃。
按“ENT”键确定4.2待指示温度到达400℃以后,保温1小时。
4.3 设定温度调到820℃,直到指示温度达到820℃时4、设置温度3005、输送氨气5.1 关闭排污口阀门5.2 检查压缩空气是否打开5.3 打开氨气阀门56、开始纯化6.1 打开纯化启动开关6.2 打开纯气出口阀27、停止氨气7.1关闭纯气出口7.2 关闭氨气阀7.3打开排污口(开到图示位置)28、降温8.1 关闭分解加热开关8.2按上调或下调按钮调节设定温度,起始设定为200℃59、关机9.1 待指示温度到达200℃以下后,关闭控制电源开关。
9.2拉下QF1~QF65注/Remarks:操作要点提示符,“”代表安全事项;“●”代表工艺要点或需特别注意项目。
编制/日期Made by/Date审核/日期Reviewed by/Date会签/日期Countersignedby/Date批准/日期Approved by/Date。
水泥分解炉温度控制系统设计
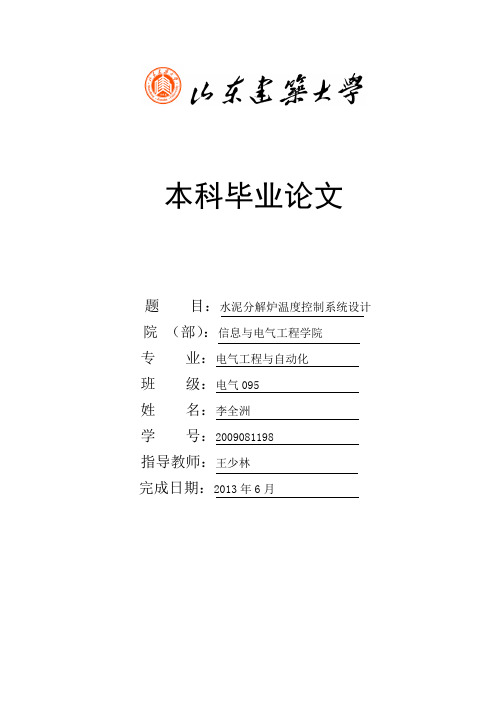
本科毕业论文题目:水泥分解炉温度控制系统设计院(部):信息与电气工程学院专业:电气工程与自动化班级:电气095姓名:李全洲学号:2009081198指导教师:王少林完成日期:2013年6月目录摘要 (IV)ABSTRACT: (V)1 前言 (1)1.1水泥分解技术的发展与现状 (11)1.2论文选题背景和意义 (2)1.2.1 选题背景 (2)1.2.2论文意义 (2)1.3论文的主要工作及思路 (3)1.3.1被控对象分析 (3)1.3.2软件设计分析 (3)1.3.3 构造PID控制器分析 (3)2 水泥分解炉温度控制影响因素分析 (5)2.1分解炉工作原理 (5)2.1.1分解炉的类型 (5)2.1.2 分解炉结构和燃烧机理 (5)2.1.3 煤粉燃烧和碳酸盐分解 (7)2.2分解炉温度影响因素分析 (7)2.2.1 煤粉用量比例 (7)2.2.2 三次风量比例 (8)2.3小结 (8)3 PID控制器设计 (10)3.1控制系统的构成 (10)3.2PID控制器 (10)3.2.1 比例、积分、微分 (10)3.2.2 构造PID控制器 (12)3.3PID最佳调整法 (12)3.3.1 针对无转移函数的PID调整法 (13)3.3.1.1 RELAY FEEDBACK调整法 (13)3.3.1.2在线调整法 (14)3.3.2 针对有转移的函数的PID调整法 (15)3.4分解炉温度控制系统的PID控制器设计 (15)3.4.1 控制系统的组成部分 (15)3.4.2 PID控制器应用分析 (17)3.5小结 (19)4 系统的总体设计 (20)4.1系统的硬件设计 (20)4.1.1 出口气体温度测量原件选择 (20)4.1.2 输出控制变频器选择 (20)4.2系统的软件设计 (21)4.2.1 设计平台 (22)4.2.2 数据库设计 (22)4.2.2.1主界面表 (23)4.2.2.2温度显示表 (23)4.2.2.3煤料显示表 (23)4.2.2.4生料显示表 (24)4.2.3 通讯协议设计 (25)4.2.4 总体界面设计 (26)4.2.4.1生料系统 (26)4.2.4.2煤粉系统 (26)4.2.4.3送风系统 (27)4.2.5 VC6.0中PID变量算法的设计 (28)4.3 现场测试 (33)4.4小结 (33)5 总结与展望 (33)5.1工作总结 (33)5.2设计展望 (33)致谢: (34)参考文献: (35)附表 (39)摘要分解炉是新型干法水泥生产工艺里预分解技术的核心设备,在预分解过程中主要进行煤粉燃烧、气固换热和碳酸盐分解等工作。
浅析窑炉能耗管理的分段温度控制方式

浅析窑炉能耗管理的分段温度控制方式一、分段温度控制的原理1. 温度梯度控制分段温度控制的核心原理是根据待处理物料的特性和窑炉的工艺要求,将窑炉内部的温度分成若干个段,对每个段的温度进行精确控制。
这样可以在保证生产质量的前提下,尽可能地减少能耗。
在窑炉内部设置上部、中部和下部三段温度控制,上部温度高,中部温度适中,下部温度低,可以更好地满足物料的不同需求,达到更好的生产效果。
2. 能耗调度控制根据不同时间段窑炉温度的需求和生产计划,合理调度窑炉的温度。
比如在生产高温需求的物料时,窑炉可以提前升温;而在生产低温需求的物料时,则可以将窑炉温度调低。
这样不仅可以降低能耗,还可以更好地满足生产的需要。
二、分段温度控制的具体方式1. 窑炉结构设计要实现分段温度控制,首先需要对窑炉的结构进行合理设计。
比如可以在窑炉内部设置分段隔板或隔断,以便更好地控制窑炉内部的温度分布。
还可以利用高效隔热材料对窑炉进行保温处理,提高窑炉的热能利用效率。
2. 温度控制系统分段温度控制需要一个高效的温度控制系统。
比如可以采用PLC控制系统,通过对温度传感器采集的温度数据进行分析和控制,实现对不同段位温度的精确控制。
还可以利用智能化控制系统,根据不同的生产需求和窑炉内部的温度变化,自动调整窑炉的温度。
3. 能源利用优化在分段温度控制的过程中,还可以通过对燃料的合理利用来进一步降低能耗。
比如可以采用预热技术,利用废热对新鲜物料进行预热;或者采用余热回收技术,将窑炉烟气中的余热回收利用。
这些都可以有效地降低窑炉的能耗。
三、分段温度控制的实际应用1. 氧化铝生产在氧化铝生产中,氧化铝窑炉通常采用分段温度控制的方式。
在窑炉的上部设定高温段,中部设定中温段,下部设定低温段。
这样可以更好地满足氧化铝生产的工艺要求,降低窑炉的能耗,提高氧化铝的生产效率。
2. 水泥生产水泥窑炉的分段温度控制也非常重要。
在水泥窑炉的烧成过程中,对不同温度区域内的物料进行不同的处理,可以更好地控制水泥的质量,并且可以降低能耗,提高生产效率。
分解炉温度的操作与控制

分解炉温度的操作与控制赵晓东;乌洪杰【期刊名称】《水泥工程》【年(卷),期】2014(000)003【总页数】2页(P42-43)【作者】赵晓东;乌洪杰【作者单位】重庆电子工程职业学院建筑与材料学院,重庆401331;重庆电子工程职业学院财经学院,重庆401331【正文语种】中文【中图分类】TQ172.620 前言分解炉温度控制的好坏,将直接影响入窑生料分解率的大小,继而将影响预分解窑的产量、质量及能耗等多项指标,因此研究探讨分解炉温度的操作与控制具有现实意义。
笔者根据自己在水泥企业20多年的生产实践经验,就分解炉温度的操作控制作一总结,供同行参考。
1 分解炉的点火操作控制分解炉具备点火的基本条件有两个:炉内有足够氧气含量;炉内温度达到煤粉燃烧的温度。
(1)对于在线型分解炉,只要窑尾废气温度≥800℃,在没有投料的情况下,向分解炉内喷人适当的煤粉,煤粉就会燃烧,完成分解炉的点火操作。
(2)对于离线型分解炉,其点火操作控制方法取决于炉型。
比如:RSP型分解炉,只要将分解炉通往上一级预热器的锁风阀吊起,即可使来自窑尾的高温废气部分短路进入分解炉内而使炉内温度升高,达到煤粉燃烧的温度,就具备了分解炉的点火条件;MFC型分解炉,由于其位置高度低于窑尾高度,要先进行投料操作,靠经过预热后的生料粉将炉内温度提高到煤粉燃烧的温度,然后再进行分解炉的点火操作,且一定要注意控制投料量与炉底的风压、风量,避免发生压炉现象而导致点火失败。
2 入窑生料分解率的控制入窑生料的分解率是衡量分解炉运行正常与否的主要指标,生产控制中,一般控制入窑生料分解率为90%~95%。
如果分解率过低,就没有充分发挥分解炉的分解功效,影响窑的产量、质量及热耗等指标;如果分解率过高,就意味着炉内的最高温度可以达到1200℃,极有可能在炉内发生形成矿物的固相反应,从而在分解炉内、出口部位及下级预热器下料口等部位产生灾难性的烧结结皮及堵塞,这是预分解窑生产最忌讳发生的!所以不能一味追求入窑生料的分解率而盲目地提高分解炉的温度。
氨水分解温度

氨水分解温度
氨水常温下就可分解。
氨水在常温下就可以发生分解反应产生氨气,但温度升高后其速度会加快。
温度越高,其分解速度越快,该过
程还伴随着氨气的挥发。
这是由于温度越高,分子的运动速率会越快,而气体在水中的溶
解度会减小,所以温度越高,风险越快,释放的气体越多。
氨分解是一个在催化剂作用下的可逆反应,一般用含镍l4%以上
的镍基催化剂。
此反应是一个吸热反应,理想温度为800~860℃。
同
时又是一个气体体积增加的反应,反应前后气体体积增加约2倍,所
以反应的压力不能过高,一般为0.05MPa左右,压力高了不利于氨气
的分解,也会降低催化剂的寿命。
反应式如下:
这一反应为在随着氨气在分解炉内温度的升高而逐步进行的,表
为氨分解时不同温度下气体混合物的成分,从中可以看出,氨气从270℃开始缓慢分解,而到625℃时就基本分解完成,所以分解温度一般都控制在800℃以上。
最终产物的体积比为H275%,N225%。
- 1、下载文档前请自行甄别文档内容的完整性,平台不提供额外的编辑、内容补充、找答案等附加服务。
- 2、"仅部分预览"的文档,不可在线预览部分如存在完整性等问题,可反馈申请退款(可完整预览的文档不适用该条件!)。
- 3、如文档侵犯您的权益,请联系客服反馈,我们会尽快为您处理(人工客服工作时间:9:00-18:30)。
分解炉有多种型式,其结构性能虽有差异,但要起的主要作用却是相同的:要使燃料燃烧的放热过程与生料碳酸盐分解的吸热过程在其中以悬浮态或流化态下极其迅速地进行,使入窑生料碳酸盐分解率提高,从而减轻窑的热负荷,提高窑的运转周期,提高产质量。
而分解炉的温度控制对整个预分解窑系统的热力分布,热工制度的稳定至关重要。
为此,作者对分解炉温度控制的有关几个问题进行讨论。
1 分解炉温度与燃料燃烧
分解炉的温度取决于燃料燃烧过程的放热速率与生料分解过程的吸热速率。
当燃料燃烧放热速率慢,生料分解在接近平衡的条件下进行,分解炉的温度于860~920℃范围,燃料燃烧放出的热量就会迅速传递给生料,并被分解反应吸收。
但是,当燃料燃烧速率大于生料分解过程的吸热速率,燃料燃烧的热量大于生料分解所需的吸热量,此时分解炉的温度就会超过平衡温度范围。
从燃料燃烧的角度来看,分解炉内燃料的燃烧与回转窑内燃料燃烧有许多不同之处。
回转窑内燃料燃烧温度比分解炉内高得多,回转窑内燃料燃烧明显是受扩散控制的,而分解炉内燃料燃烧则有所不同。
由于分解炉温度远低于回转窑内燃料燃烧温度,故煤在分解炉内的燃烧时间受煤种类的影响比回转窑内的影响大得多。
如广东云浮水泥厂FCB分解炉容积偏小,结构上亦存在一些问题,当使用低挥发分、高灰分的低热值煤时,还原气氛十分严重,迅速导致结皮堵塞;而采用高挥发分、低灰分的高热值煤时情况则有所改善。
煤粉细度对于回转窑内的燃烧是相当敏感的,因为其是受扩散控制,即受边界层扩散时输送速率的控制;而煤粉
细度对分解炉内燃烧的影响就没有在回转窑内那样敏感了。
问题还要回到分解炉温度与燃料燃烧的关系上来。
由于回转窑内燃料燃烧是受扩散控制的,增减10~20℃对于燃料的燃烧影响是甚微的。
但在分解炉内则明显不同。
如有的分解炉容积偏小,煤粉燃烬时间不足,以至还原气氛重,而降低分解炉的温度,减少分解炉用煤量,以图改变煤粉燃烧不完全、还原气氛的问题,但往往是事与愿违。
因在不减产量的情况下,分解炉用煤减少,分解炉温度降低,煤的燃烧速度随温度降低而迅速下降,煤粉始终是燃烧不完全。
适当增大分解炉的容积已成为一个发展动向。
在分解炉偏小煤质差的情况下,可适当降产量,而不宜降低分解炉的温度。
2 分解炉温度与末级旋风筒温度及物料、燃料情况
燃料在分解炉内燃烧放热,料粉在其中吸热分解;随后,气固两相流离开分解炉进入末级旋风筒,进行气固分离;分离后的物料进入回转窑,而气体进入上一级旋风预热器。
在正常情况下,煤粉在分解炉燃烧完全,分解炉的出口温度会高于最末一级旋风筒下部及其物料的温度。
但是,当分解炉内燃料的燃烧速度慢,燃料燃烧不完全,则未完全燃烧的煤粉在旋风筒内继续燃烧,此时则会使最末一级旋风筒下部及物料的温度比分解炉出口温度还要高。
如云浮水泥厂在1993年8月煤粉质量明显下降,灰分高、热值低,FCB型预分解窑窑头三通道喷煤管未能适应烧这些质量差的煤,熟料煅烧温度低,三次风温明显下降,而低的三次风温又进一步延滞了分解炉内煤粉的燃烧,可谓雪上加霜。
就这样,不完全燃烧的煤粉进入五级旋风筒内继续燃烧,五级旋风筒下部温度比分解炉出口温度
还高。
在这种情况下,废气中CO含量高,还原气氛重,易结皮堵塞,而分解炉的平均温度并不高,入窑物料碳酸盐分解率亦较低,熟料产质量下降。
还需说明的是,分解炉的通风量对分解炉出口温度及末级旋风筒下部温度亦有影响。
即使分解炉的喂煤量、物料量不变,但通风量改变,亦会产生影响。
当通风量过大,分解炉内气流速度过快,燃料及物料在分解炉内停留时间不足;反之,当通风量过小,供气不足,燃料燃烧同样受影响。
总之,通风量的波动,窑风量与分解炉风量的分配不当,都会影响分解炉燃料的燃烧,从而导致分解炉出口温度与最末一级旋风筒下部温度的异常。
分解炉的温度控制还应考虑产量及物料的情况。
当产量较低,即喂料量较小,回转窑的转速亦较慢,此时应相应降低分解炉温度。
因分解炉温度过高,一方面会增加热耗,另一方面还不利于热工制度的稳定,不利于熟料烧成。
反之,当产量较高,在分解炉能力许可的情况下应适当提高分解炉温度,减轻回转窑的热负荷。
但是,当设备富裕能力小,超产时窑系统的平衡是相当脆弱的,遇到小小波动亦难以调整,故提高分解炉温度,提高产量需适度为宜。
而当物料反应活性较差,如石灰石结晶状况较好,晶体尺寸较大,其分解温度较高。
此时应在可能的条件下把分解炉温度控制高一些,以保证入窑物料的分解率。