极坐标插补摘要
CNC系统常见术语详解

CNC系统常见术语详解摘要: 增量编码器(Increment pulse coder)回转式位置测量元件,装于电动机轴或滚珠丝杠上,回转时发出等间隔脉冲表示位移量。
由于没有记忆元件,故不能准确代表机床的位置。
只有在机床回零,建立了机床坐标系的零点后,...增量编码器(Increment pulse coder)回转式位置测量元件,装于电动机轴或滚珠丝杠上,回转时发出等间隔脉冲表示位移量。
由于没有记忆元件,故不能准确代表机床的位置。
只有在机床回零,建立了机床坐标系的零点后,才能表示出工作台或刀具的位置。
使用时应该注意的是,增量编码器的信号输出有两种方式:串行和并行。
个别数控系统与此对应有串行接口和并行接口。
绝对值编码器(Absolute pulse coder)回转式位置测量元件,用途与增量编码器相同,带有记忆元件,可以实时地反映机床的实际位置。
关机后的位置也不会丢失,机床开机后不用回零点,即可立即投入加工运行。
与增量编码器一样,使用时应注意脉冲信号的串行与并行输出。
主轴定向(Orientation)为了执行主轴定位或者换刀,必须将机床主轴在回转的圆周方向定位与于某一转角上,作为动作的基准点。
一般有以下4种方法:用位置编码器定向、用磁性传感器定向、用外部一转信号(如接近开关)定向、外部机械方法定向。
双驱动控制(Tandem control)对于大工作台,一个电动机的力矩不足以驱动时,可以用两个电动机协同驱动。
两个轴中一个是主动轴,另一个为从动轴。
主动轴接收" target="_blank" class="relatedlink">CNC的控制指令,从动轴增加驱动力矩。
刚性攻丝(Rigid tapping)攻丝操作不使用浮动卡头而是由主轴的回转与攻丝进给轴的同步运行实现。
主轴回转一转,攻丝轴的进给量等于丝锥的螺距,这样可提高精度和效率。
欲实现刚性攻丝,主轴上必须装有位置编码器(通常是1024脉冲/每转),并要求编制相应的梯形图,设定有关的系统参数。
巧用极坐标插补指令在车铣复合机床上加工异形零件
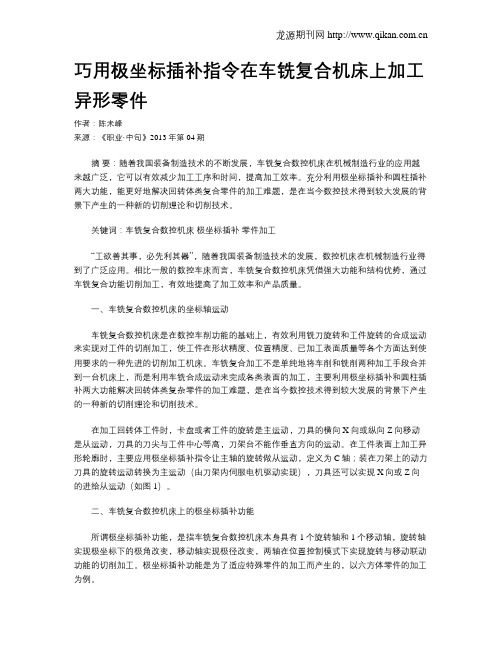
巧用极坐标插补指令在车铣复合机床上加工异形零件作者:陈未峰来源:《职业·中旬》2013年第04期摘要:随着我国装备制造技术的不断发展,车铣复合数控机床在机械制造行业的应用越来越广泛,它可以有效减少加工工序和时间,提高加工效率。
充分利用极坐标插补和圆柱插补两大功能,能更好地解决回转体类复合零件的加工难题,是在当今数控技术得到较大发展的背景下产生的一种新的切削理论和切削技术。
关键词:车铣复合数控机床极坐标插补零件加工“工欲善其事,必先利其器”,随着我国装备制造技术的发展,数控机床在机械制造行业得到了广泛应用。
相比一般的数控车床而言,车铣复合数控机床凭借强大功能和结构优势,通过车铣复合功能切削加工,有效地提高了加工效率和产品质量。
一、车铣复合数控机床的坐标轴运动车铣复合数控机床是在数控车削功能的基础上,有效利用铣刀旋转和工件旋转的合成运动来实现对工件的切削加工,使工件在形状精度、位置精度、已加工表面质量等各个方面达到使用要求的一种先进的切削加工机床。
车铣复合加工不是单纯地将车削和铣削两种加工手段合并到一台机床上,而是利用车铣合成运动来完成各类表面的加工,主要利用极坐标插补和圆柱插补两大功能解决回转体类复杂零件的加工难题,是在当今数控技术得到较大发展的背景下产生的一种新的切削理论和切削技术。
在加工回转体工件时,卡盘或者工件的旋转是主运动,刀具的横向X向或纵向Z向移动是从运动,刀具的刀尖与工件中心等高,刀架台不能作垂直方向的运动。
在工件表面上加工异形轮廓时,主要应用极坐标插补指令让主轴的旋转做从运动,定义为C轴;装在刀架上的动力刀具的旋转运动转换为主运动(由刀架内伺服电机驱动实现),刀具还可以实现X向或Z向的进给从运动(如图1)。
二、车铣复合数控机床上的极坐标插补功能所谓极坐标插补功能,是指车铣复合数控机床本身具有1个旋转轴和1个移动轴,旋转轴实现极坐标下的极角改变,移动轴实现极径改变,两轴在位置控制模式下实现旋转与移动联动功能的切削加工。
极坐标插补功能在车铣复合加工中心的应用

・
模 具 制 造 技 术
・
极坐标插补功能在车铣复合加 工 中心 的应用
高 升
中山市技师 学院 ( 广 东中 山 5 2 8 4 0 0 )
【 摘要】极 坐标插补功 能是利用车铣 复合加工 中心加 工端 面轮廓的关键技 术, 在加 工回转
体产品 的端 面多边形轮廓或 多边形 凹槽时, 为提 高生产效率 , 并且能方便保证相对位 置的 加 工精度 , 可选择在车铣复合加 工 中心上利用极 坐标插补功 能进行加工, 这样 能够完成 一 次装夹 , 符合工序 集中的加 工原则 。 关键词 : 车铣复合加 工: 极 坐标插补; 工序 集中
c o n c e nt r a t i o n
极坐标插补摘要
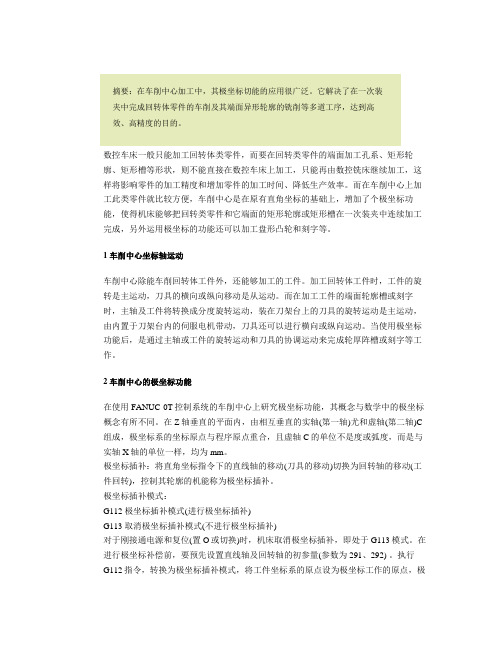
摘要:在车削中心加工中,其极坐标切能的应用很广泛。
它解决了在一次装夹中完成回转体零件的车削及其端面异形轮廓的铣削等多道工序,达到高效、高精度的目的。
数控车床一般只能加工回转体类零件,而要在回转类零件的端面加工孔系、矩形轮廓、矩形槽等形状,则不能直接在数控车床上加工,只能再由数控铣床继续加工,这样将影响零件的加工精度和增加零件的加工时间、降低生产效率。
而在车削中心上加工此类零件就比较方便,车削中心是在原有直角坐标的基础上,增加了个极坐标功能,使得机床能够把回转类零件和它端面的矩形轮廓或矩形槽在一次装夹中连续加工完成,另外运用极坐标的功能还可以加工盘形凸轮和刻字等。
1 车削中心坐标轴运动车削中心除能车削回转体工件外,还能够加工的工件。
加工回转体工件时,工件的旋转是主运动,刀具的横向或纵向移动是从运动。
而在加工工件的端面轮廓槽或刻字时,主轴及工件将转换成分度旋转运动,装在刀架台上的刀具的旋转运动是主运动,由内置于刀架台内的伺服电机带动,刀具还可以进行横向或纵向运动。
当使用极坐标功能后,是通过主轴或工件的旋转运动和刀具的协调运动来完成轮厚阵槽或刻字等工作。
2 车削中心的极坐标功能在使用FANUC-0T控制系统的车削中心上研究极坐标功能,其概念与数学中的极坐标概念有所不同。
在Z轴垂直的平面内,由相互垂直的实轴(第一轴)尤和虚轴(第二轴)C 组成,极坐标系的坐标原点与程序原点重合,且虚轴C的单位不是度或弧度,而是与实轴X轴的单位一样,均为mm。
极坐标插补:将直角坐标指令下的直线轴的移动(刀具的移动)切换为回转轴的移动(工件回转),控制其轮廓的机能称为极坐标插补。
极坐标插补模式:G112 极坐标插补模式(进行极坐标插补)G113 取消极坐标插补模式(不进行极坐标插补)对于刚接通电源和复位(置O或切换)时,机床取消极坐标插补,即处于G113模式。
在进行极坐标补偿前,要预先设置直线轴及回转轴的初参量(参数为291、292) 。
巧用极坐标插补指令在车铣复合机床上加工异形零件
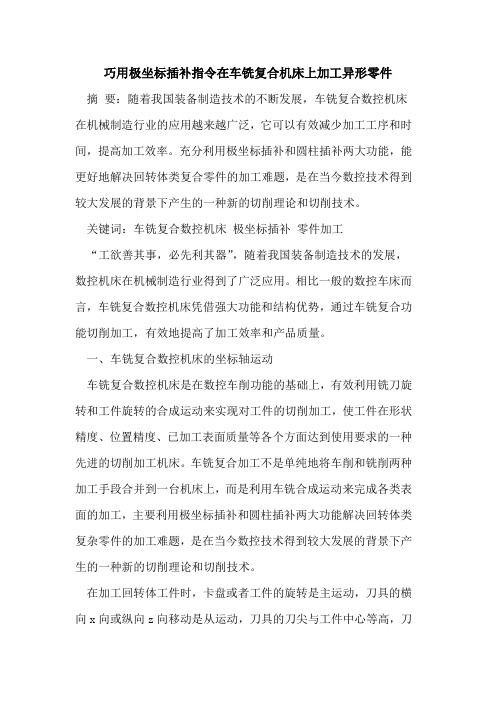
巧用极坐标插补指令在车铣复合机床上加工异形零件摘要:随着我国装备制造技术的不断发展,车铣复合数控机床在机械制造行业的应用越来越广泛,它可以有效减少加工工序和时间,提高加工效率。
充分利用极坐标插补和圆柱插补两大功能,能更好地解决回转体类复合零件的加工难题,是在当今数控技术得到较大发展的背景下产生的一种新的切削理论和切削技术。
关键词:车铣复合数控机床极坐标插补零件加工“工欲善其事,必先利其器”,随着我国装备制造技术的发展,数控机床在机械制造行业得到了广泛应用。
相比一般的数控车床而言,车铣复合数控机床凭借强大功能和结构优势,通过车铣复合功能切削加工,有效地提高了加工效率和产品质量。
一、车铣复合数控机床的坐标轴运动车铣复合数控机床是在数控车削功能的基础上,有效利用铣刀旋转和工件旋转的合成运动来实现对工件的切削加工,使工件在形状精度、位置精度、已加工表面质量等各个方面达到使用要求的一种先进的切削加工机床。
车铣复合加工不是单纯地将车削和铣削两种加工手段合并到一台机床上,而是利用车铣合成运动来完成各类表面的加工,主要利用极坐标插补和圆柱插补两大功能解决回转体类复杂零件的加工难题,是在当今数控技术得到较大发展的背景下产生的一种新的切削理论和切削技术。
在加工回转体工件时,卡盘或者工件的旋转是主运动,刀具的横向x向或纵向z向移动是从运动,刀具的刀尖与工件中心等高,刀架台不能作垂直方向的运动。
在工件表面上加工异形轮廓时,主要应用极坐标插补指令让主轴的旋转做从运动,定义为c轴;装在刀架上的动力刀具的旋转运动转换为主运动(由刀架内伺服电机驱动实现),刀具还可以实现x向或z向的进给从运动(如图1)。
二、车铣复合数控机床上的极坐标插补功能所谓极坐标插补功能,是指车铣复合数控机床本身具有1个旋转轴和1个移动轴,旋转轴实现极坐标下的极角改变,移动轴实现极径改变,两轴在位置控制模式下实现旋转与移动联动功能的切削加工。
极坐标插补功能是为了适应特殊零件的加工而产生的,以六方体零件的加工为例。
华中8型数控装置连接说明书-V1.0
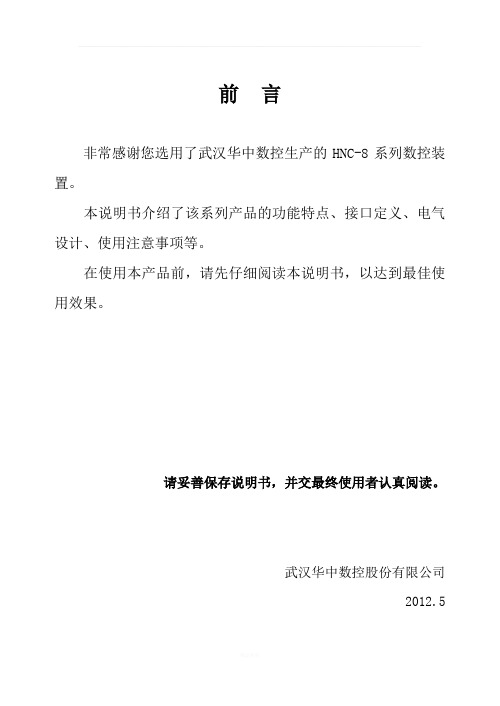
2、系统选件
① 手持单元(选件)
□标准手摇脉冲发生器
□标准2坐标或3坐标选择(3轴以上可选配)
□3种倍率选择
□紧急停止按钮
□工作指示灯
②总线式I/O单元
□通过总线最多可扩展16个I/O单元;
□支持NCUC(火线接口、光纤接口可选);
□HIO-1000A型I/O单元可提供1个通讯子模块和8个功能子模块插槽;HIO-1000B型I/O单元可提供1个通讯子模块和5个功能子模块插槽;
□具有直线插补、圆弧插补、极坐标插补、圆柱面插补、螺旋线插补等,支持旋转、缩放、镜像、固定循环、螺纹切削、刀具补偿、用户宏程序、软限位等功能。
□支持龙门轴同步、动态轴释放/捕获、通道间同步等功能。
□小线段连续加工功能,特别适合于CAD/CAM设计的复杂模具零件加工。
□采用总线式PLC I/O单元,输入/输出最多分别支持1024点。
图2.2.2aB系列数控装置接口图-正面
XS2:标准PS/2键盘接口;
XS5:RS232串行接口;
XS7:USB接口(USB2.0);
图2.2.2b B系列数控装置接口图-背面板
XS6:NCUC总线接口
XS8:手持单元接口
XT1:外部电源开、电源关、急停接口
图2.2.3aC系列数控装置接口图-上面板正面
□内置RS232通讯接口,轻松实现机床数控通讯。
□支持高速以太网数据交换。
□1MB程序断电存储区,支持CF卡扩展,最大至2GB。
□支持USB热插拔。
□1GB RAM加工内存缓冲区。
□自定义G代码功能。
□后台编辑和蓝图编程功能(选件)。
□采用国际标准G代码编程,与各种流行的CAD/CAM自动编程系统兼容。
关于车铣削复合加工编程的基本方法解析

关于车铣削复合加工编程的基本方法解析摘要:随着我国经济社会发展进入新时代,产业转型升级势在必行。
企业所生产零件的复杂度和精度提出了高要求,为提高产品质量及加工效率,高端数控机床的应用就尤为重要,以车铣削复合加工技术为主要代表的高端机床现已在企业中大量应用。
通过案例分析来车铣削复合加工技术的应用,以供相关技术人员参考。
关键词:车铣削复合复合加工多轴加工 MTS数控仿真在《中国制造2025》发展战略的大背景下,随着我国经济社会发展进入新时代,各行各业出现了新的发展趋势,高端装备制造业成为推动工业转型升级的重要引擎。
随着我国产业转型升级的不断深入,企业所生产零件的复杂性也在不断增加。
许多集成化程度高的零件如果采用传统的工艺进行制造往往需要经过车、铣、钻、镗、磨削等多工种与多工序交叉加工才能完成,由于零件需要多次换夹,不仅大大增加了零件加工的准备时间,降低了零件的可靠性,而且零件的加工精度也没法保证,为进一步提高产品质量和加工效率,这种提质、增效、降本的诉求,引发了在传统数控车床上加装旋转动力头的变革,也由此实现了车铣复合加工。
然而复合加工技术已然成为了目前国际机械加工领域上最流行的加工工艺之一。
1、车铣复合加工技术简介数控车铣复合机床是复合加工机床的一种主要机型,通常是在数控车床上实现平面铣削、钻孔、攻丝、铣槽等铣削加工工序,具有车削、铣削、镗削等复合功能。
车铣复合机床就是为适应市场单件小批、快捷生产需求以及新工艺对机床在各方面的要求而开发的。
车铣复合加工具有保持工序集中、节省作业面积、减少机床和夹具数量、消除或减少工件重新安装定位次数、免去工件间的搬运和储存、提高工件加工精度、缩短加工周期的优势,是当前世界机床技术发展潮流。
2、车铣复合机床与传统机床加工的优势与常规数控加工工艺相比,复合加工具有的突出优势主要表现在以下几个方面。
(1) 减少装夹次数,提高加工精度。
(2) 缩短产品制造工艺链,提高生产效率。
数控车铣中心C轴手工编程实例
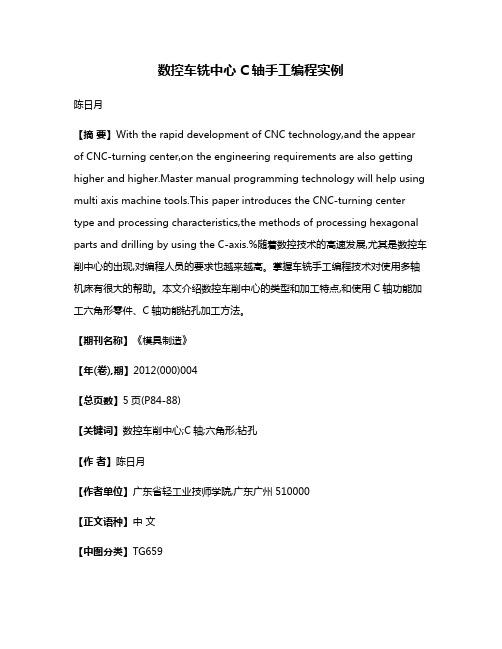
数控车铣中心C轴手工编程实例陈日月【摘要】With the rapid development of CNC technology,and the appear of CNC-turning center,on the engineering requirements are also getting higher and higher.Master manual programming technology will help using multi axis machine tools.This paper introduces the CNC-turning center type and processing characteristics,the methods of processing hexagonal parts and drilling by using the C-axis.%随着数控技术的高速发展,尤其是数控车削中心的出现,对编程人员的要求也越来越高。
掌握车铣手工编程技术对使用多轴机床有很大的帮助。
本文介绍数控车削中心的类型和加工特点,和使用C轴功能加工六角形零件、C轴功能钻孔加工方法。
【期刊名称】《模具制造》【年(卷),期】2012(000)004【总页数】5页(P84-88)【关键词】数控车削中心;C轴;六角形;钻孔【作者】陈日月【作者单位】广东省轻工业技师学院,广东广州510000【正文语种】中文【中图分类】TG6591 引言伴随加工件的日益复杂化、精度等级以及加工效率的提高,多轴向、高转速成为数控机床必备的条件,除了加工中心走向机能复合化外,车床方面已由早期的卧式车床开发出许多新的加工型态,例如双刀塔、立式车床、倒立车床、以及车铣复合等概念机种,以顺应新时代加工方式的需求。
车铣复合机床集成了车削和铣削的加工方法,其中车铣概念复合机无疑是一项新技术结合的数控机床杰作,最大的优点在于:可轻易地在同一机床上做复杂零件的加工。
极坐标下逐点比较法的直线插补

极坐标下逐点比较法的直线插补
极坐标下逐点比较法是一种常用的直线插补方法。
该方法通过对起点和终点的极角和极径进行逐点比较,从而得出直线插补的路径。
具体实现方式为:假设起点坐标为(r1,theta1),终点坐标为(r2,theta2),插补点数为n,插补过程中每个点的极角为thetai,极径为ri。
则有如下计算过程:
1. 计算极径比值k: k=(r2-r1)/(n-1)
2. 逐点计算极径: ri = r1+k*(i-1)
3. 逐点计算极角: thetai = theta1+(theta2-theta1)*(ri-r1)/(r2-r1)
4. 根据得到的极角和极径,可以得到每个插补点的坐标。
该方法简单易用,适用于大部分直线插补场景。
但在终点和起点之间存在明显弯曲的情况下,该方法可能会导致插补精度降低,需要采用其他插补方法。
车床数控系统的多边形加工实现

车床数控系统的多边形加工实现陈鹏【摘要】在生产生活中需要使用到多边形类零部件,如螺母、螺栓、管接头等.此类零部件需求量大、精度要求低、种类规格繁多,因此如何高效率、低成本地生产此类零部件成了摆在我们面前的一大难题.本文将介绍一种通过在车床数控系统中增加多边形加工功能的方法来达到高效率、低成本的这一加工要求.本文以广州数控设备有限公司生产的GSK980TC3系列总线式车床数控系统(以下简称“980TC3车床系统”)为例增加多边形加工功能.【期刊名称】《机电产品开发与创新》【年(卷),期】2018(031)005【总页数】3页(P96-98)【关键词】车床数控系统;多边形加工;GSK980TC3【作者】陈鹏【作者单位】广州数控设备有限公司,广东广州510530【正文语种】中文【中图分类】TG680 引言随着先进制造、自动化技术的快速发展。
近年来,在工艺品、机械、电子、航空航天等各个领域扁方体、三面体、四面体、六面体、八面体甚至任意面体等类似多面体类零件应用越来越多,加工这样的零件通常的加工方法是冲床冲压成型、车床或铣床上通过多道工序加工完成。
这些方式都各有优缺点:如冲床冲压成型加工一次成型虽加工效率高,但缺点是精度低、产品单一、更换模具成本高;车床加工需使用极坐标插补功能进行加工,虽加工精度高,但加工效率较低;铣床加工虽精度高,但工序多、效率低、综合成本高。
而在普通数控车床上通过增加刀盘轴和伺服主轴,控制系统增加多边形加工控制算法可以实现高效率的任意多边形的加工,并通过轴向移动从而实现多面体的加工。
以下以广州数控设备有限公司生产的980TC3总线式车床数控系统为例来讲述如何实现多边形加工。
1 多边形加工原理多边形加工是指通过使工件与刀具按一定的比率旋转,将工件的形状加工成多边形的加工,如图1所示。
通过改变工件和刀具的旋转速度比或刀具的安装数量,可以把工件加工成三边形、四边形、六边形甚至任意多边形。
图1 多边形加工示意图Fig.1 Polygon turning diagram把工件及刀具的半径分别设为A、B,把工件和刀具的旋转角速度分别设为α、β。
极坐标圆弧插补算法的计算仿真与实验验证

第5期2017年5月组合机床与自动化加工技术Modular Machine Tool & Automatic Manufacturing TechniqueNo. 5May 2017文章编号:l 〇〇l -2265(2017)05 -0032 -04D 01:10. 13462/j. cnki. mmtamt. 2017. 05.009极坐标圆弧插补算法的计算仿真与实验验证+来旭辉,许燕,周建平(新疆大学机械工程学院,乌鲁木齐830047)摘要:为减少铸造成型开模周期提高零件生产效率和质量,搭建了极坐标成型平台。
阐述了极坐标相对直角坐标的优势,根据极坐标堆焊成型设备的结构综合逐点比较法及时间分割法,对极坐标下 的圆?瓜插补算法进行了研究和探索,提出了极坐标模式下的逐点比较插补算法,对极坐标特有的插 补特殊点和关键点的插补精度进行了优化,并编写可视化软件对插补过程仿真分析。
最后设计圆筒 插补实验通过对比得出该算法稳定可行。
关键词:极坐标成型;堆焊成型;逐点比较法;可视化软件 中图分类号:TH 16;TG 65 文献标识码:AComputational Simulation and Experimental Verification of Polar Circular Interpolation AlgorithmLAI Xu -hui,XU Yan , ZHOU Jian-ping(School of Mechanical Engineering , Xinjiang University , Urumqi 830047,China )Abstract : In order to reduce the casting mold cycle and improve the production efficiency and quality of the parts , a polar coordinate welding forming equipment was developed . The advantage of polar coordinates rela tive to rectangular coordinates is expounded , So we combines the structure of polar coordinate FDM equip ment with the interpolation theory of the point by point comparison method to research and explore the arc interpolation algorithm in polar coordinates , we put forward a complete set of interpolation algorithm and op timized the interpolation precision of the special points and the key points , and then simulate the interpolation process by visual software . Finally , the design of cylinder interpolation experiments show that the algorithm is stable and feasible .Key words : polar forming ; surfacing forming ; point by point comparison ; visualization software〇引言金属快速成型是先进制造技术的重要分支,按照加 工方式的不同可以分为电弧加工,激光加工和等离子加 工等,诸如此类轮廓加工设备大多为直角框架结构或回 转悬臂结构[1],其中直角框架结构是在直角坐标的基础 上进行开发研制的,对于回转悬臂结构则更适合结合自 身特点以极坐标为基础进行配套软件开发,基于极坐标 的加工设备可以很好地实现对圆锥曲线,阿基米德螺旋 线等用极坐标参数描述的轨迹的拟合[2],可以在同等条 件下加工出比直角坐标精度更高的工件,旋转结构可快 速对零件内部进行圆弧填充,保证成型后的零件具有良 好的径向力学性能[3],并且表面轮廓以弧线过渡,有效地 避免了阶梯状外形的出现,成型后的金属零件可以直接 或经过少量机械加工后就投人使用。
g12.1

极坐标插补( G12.1, G13.1 )2007/04/14 21:12极坐标插补( G12.1, G13.1 )极坐标插补用于轮廓控制使笛卡尔坐标系编程指令转换为直线轴(刀具的移动)和旋转轴的移动(工件的旋转).此功能常用于凸轮轴的磨削.[ 格式 ]G12.1:极坐标插补模式开始(极坐标插补功能打开)G13.1:极坐标插补模式取消(极坐标插补功能关闭)[ 说明 ]■ 极坐标插补平面G12.1启用极坐标插补模式,并选择极坐标插补平面.极坐标插补在此平面执行. 旋转轴 (虚轴)(单位;mm或inch)直线轴(单位mm或inch)局部坐标系原点(G52指令)或是工件坐标系的原点[ 极坐标插补平面 ]当开机或系统复位,极坐标插补是取消状态(G13.1)极坐标插补的直线轴和旋转轴必须在参数(No.5460和5461)中设定.注意)在G12.1使用之前的平面要取消.当指定G13.1后再存贮.当系统复位时极坐标插补取消,使用G17,G18或 G19选择的平面恢复使用.■ 极坐标插补移动的距离和进给率假想轴的坐标单位与直线轴的单位相同(mm/inch)进给率的单位是mm/min或inch/min.在极坐标插补模式,编程指令用极坐标插补平面的笛卡尔坐标指定.旋转轴的位址使用平面的第二轴(假想轴)的位址.不管平面的第一轴指定的是直径还是半径与该平面没有指定旋转轴时的第一轴一样.假想轴在指定G12.1后坐标为0时建立.极坐标插补在G12.1指定后的起始角度假设刀具的位置为0°.■ 在极坐标插补模式中可以指定的G码G01 ………………… 直线插补G02,G03 ………… 圆弧插补G04 ………………… 暂停,确实停止G40,G41,G42 …… 刀具半径补正(极坐标插补轨迹在刀具半径补正之后)G65,G66,G67 …… 用户巨指令G90,G91 ………… 绝对指令,相对指令G94,G95 ………… 每分钟进给,每转进给■ 极坐标平面中的圆弧插补在极坐标插补平面作圆弧插补(G02或G03)的圆弧半径的位址根据该平面的第一轴(直线轴)来决定.当直线轴是X轴或平行于X轴时I和J在Xp-Yp平面内.当直线轴是Y轴或平行于Y轴时J和K在Yp-Zp平面内.当直线轴是Z轴或平行于Z轴时K和I在Zp-Xp平面内.■ 在极坐标插补模式不在极坐标插补平面沿轴向的移动刀具通常沿这些轴移动,而不依赖极坐标插补.■ 在极坐标插补模式当前位置的显示显示实际坐标.也显示在极坐标插补平面(笛卡尔坐标系)在单节中的残余距离. [ 限制 ]■ 极坐标插补的坐标系在指定G12.1之前,要设定局部坐标系(或工件坐标系)回转轴的中心为坐标系的原点.在G12.1模式,坐标系不能被改变(G92,G52,G53相关坐标系复位,G54到G59等).■ 刀具半径补正指令极坐标插补(G12.1或G13.1)模式不能在刀具半径补正模式(G41或G42)中开始或结束.G12.1或G13.1必须在刀具半径补正取消模式(G40)指定.■ 刀具长度偏移量指令刀具长度偏移量必须在极坐标插补取消模式在G12.1指定之前指定.不能在极坐标插补模式指定.甚至在极坐标插补模式不能改变偏移量值.■ 刀具偏移量指令刀具偏移量必须在G12.1模式之前指定.在G12.1模式不能改变偏移量.■ 程序再启动在G12.1模式中的单节,程序不能再启动.■ 旋转轴的切削进给率在笛卡尔坐标系中极坐标插补使刀具移动转换为旋转轴(C轴)和直线轴(X轴)的移动.当刀具移动接近工件的中心时,C轴的进给率向量变得很大,有可能超过C 轴的最大进给率(参数No.1422中设定)引起报警.为防止C轴的进给率超过C轴的最大进给率,指定位址F来减小进给率或者改动程序使刀具(使用刀具半径补正时的刀具中心)不靠近工件的中心.注意)三条直线L1,L2和L3,ΔX是在笛卡尔坐标系用位址F指定进给率每单位时间刀具移动的距离.象刀具移动从L1到L2到L3,在坐标系中对应ΔX每单位时间刀具移动的角度从θ1到θ2到θ3.换句话说,C轴在刀具移动越靠近工件中心进给率变大.C的进给率向量有可能超过C轴的最大进给率因为刀具的移动在笛卡尔坐标系中要转换成C轴和X轴的移动.ΔXθ1 L1θ2 L2θ3 L3L:是刀具中心到工件中心的垂直距离R:C轴的最大切削进给率(deg/min)极坐标插补速度指定位址F用下列公式给出.指定速度在计算公式的允许值之下.公式提供的是理论值,实际上要根据计算误差比理论值稍微低一点.F〈L×R×π/ 180 (mm/min)[ 举例 ]极坐标插补程序举例基于X轴(直线轴)和C轴(旋转轴)假想C轴C轴程序轨迹刀具半径补正后N204 N203 的轨迹N205 N202 N201N208 X轴N200N206 N207Z轴O0001 ;:N010 T0101;:N0100 G90 G00 X60.0 C0 Z_ ; 快速到起始位置N0200 G12.1 ; 极坐标插补开始N0201 G42 G01 X20.0 F_ ;N0202 C10.0 ;N0203 G03 X10.0 C20.0 R10.0 ;N0204 G01 X-20.0 ; 几何编程N0205 C-10.0 ; (基于笛卡尔坐标X-C'平面) N0206 G03 X-10.0 C-20.0 I10.0 J0 ;N0207 G01 X20.0 ;N0208 C0 ;N0209 G40 X60.0 ;N0210 G13.1 ; 极坐标插补取消N0300 Z_ ;N0400 X_ C_ ;::N0900 M30 ;。
毕业论文《典型轴类零件数控车床加工编程设计与工艺设计》

典型轴类零件数控车床加工编程设计与工艺设计摘要数控车床是应用数控技术的车床,也就是装了数控系统的车床,是严格按照从外部输入加工程序来自动对被加工零件进行车削加工。
它是综合应用计算机、自动控制、自动检测及精密机械等高科技的产物数控技术是现代制造业实现自动化、柔性化、集成化生产的基础,离开了数控技术,先进制造技术就成了无本之木。
数控技术的广泛使用给机械制造业生产方式、生产结构、管理方式带来深刻的变化,它的关联效益和辐射能力更是难以估计。
数控技术及数控装备已成为关系国家战略和体现国家综合国力水平的重要基础性产业,其水平高低是衡量一个国家制造业现代化程度的核心标志,实现加工机床及生产过程数控化,已经成为当今制造业的发展方向。
本论文主要通过对典型轴类零件的加工工艺分析和加工编程设计,进一步了解与掌握数控原理的理解,零件的识图与合理加工工艺的设计,并且进一步加强对数控G代码编程的熟练应用。
关键词数控加工工艺编程 G代码The typical shaft parts CNC lathe programming design and process designAbstract CNC lathe application lathe CNC technology, lathe CNC system that is installed, in strict accordance with the input from the external processing program to automatically turning machining parts to be machined.It is a comprehensive application of computer, automatic control, automatic detection and precision machinery and other high-tech products CNC technology is the modern manufacturing automation, flexible foundation for integrated production, left the CNC technology, advanced manufacturing technology became a forest without trees. The extensive use of CNC technology to bring profound changes to the mode of production, machinery manufacturing, production structure, management style, and its associated benefits and the ability to radiate more difficult to estimate. NC and CNC equipment has become the country's strategy and reflects the country's comprehensive national strength level of basic industry, the level of core mark is a measure of the degree of modernization of a country's manufacturing industry, numerical control machine tools and production process has become manufacturing the development direction of the industry.This thesis through the typical shaft parts processing technology analysis and processing of programming designed to further understanding and mastery the CNC understanding of the principles, parts of the knowledge map and reasonable process design, and further strengthen the skilled application of CNC G-code programming.Keywords CNC machining process programming G code目录引言 (3)第一章数控技术 (4)1.1 国内外数控发展概况 (4)1.2数控技术发展趋势 (5)1.2.1性能发展方向 (5)1.2.2 功能发展方向 (7)第二章零件图纸设计与分析 (11)2.1 零件图纸设计 (11)2.2 机床的选择 (11)第三章零件的夹具与刀具设计 (13)3.1 数控机床夹具 (13)3.1.1机床夹具的组成 (13)3.1.2机床夹具的作用 (15)3.1.3 零件的夹具设计 (16)3.2 数控机床的刀具 (16)3.2.1 数控刀具的分类 (16)3.2.2 数控刀具的选用 (17)3.3.3 零件的刀具选用 (22)第四章零件的加工工艺 (23)4.1 数控车削的加工工艺内容 (23)4.2数控车削的加工工艺分析 (23)4.2.3 零件的工艺步骤 (26)第五章零件切削用量的选定 (27)5.1 切削用量的选择 (27)5.2 切削用量的内容 (27)第六章零件主要操作步骤及程序的编制 (29)6.1加工顺序及路线 (29)6.2机床的操作步骤: (29)6.3零件的安装及装夹方式 (29)夹具是机床的一种附加装置,工件的装夹与数控车床一般使用三爪自动定心卡盘装夹工件。
G12.1文档
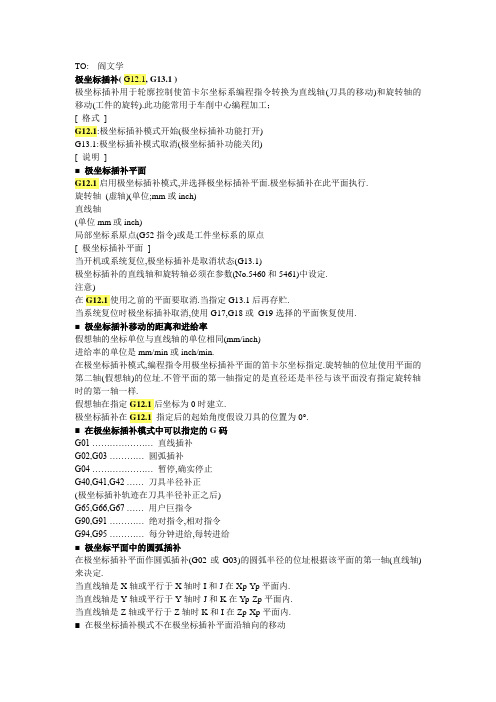
TO: 阎文学极坐标插补( G12.1, G13.1 )极坐标插补用于轮廓控制使笛卡尔坐标系编程指令转换为直线轴(刀具的移动)和旋转轴的移动(工件的旋转).此功能常用于车削中心编程加工;[ 格式]G12.1:极坐标插补模式开始(极坐标插补功能打开)G13.1:极坐标插补模式取消(极坐标插补功能关闭)[ 说明]■ 极坐标插补平面G12.1启用极坐标插补模式,并选择极坐标插补平面.极坐标插补在此平面执行.旋转轴(虚轴)(单位;mm或inch)直线轴(单位mm或inch)局部坐标系原点(G52指令)或是工件坐标系的原点[ 极坐标插补平面]当开机或系统复位,极坐标插补是取消状态(G13.1)极坐标插补的直线轴和旋转轴必须在参数(No.5460和5461)中设定.注意)在G12.1使用之前的平面要取消.当指定G13.1后再存贮.当系统复位时极坐标插补取消,使用G17,G18或G19选择的平面恢复使用.■ 极坐标插补移动的距离和进给率假想轴的坐标单位与直线轴的单位相同(mm/inch)进给率的单位是mm/min或inch/min.在极坐标插补模式,编程指令用极坐标插补平面的笛卡尔坐标指定.旋转轴的位址使用平面的第二轴(假想轴)的位址.不管平面的第一轴指定的是直径还是半径与该平面没有指定旋转轴时的第一轴一样.假想轴在指定G12.1后坐标为0时建立.极坐标插补在G12.1指定后的起始角度假设刀具的位置为0°.■在极坐标插补模式中可以指定的G码G01 ………………… 直线插补G02,G03 ………… 圆弧插补G04 ………………… 暂停,确实停止G40,G41,G42 …… 刀具半径补正(极坐标插补轨迹在刀具半径补正之后)G65,G66,G67 ……用户巨指令G90,G91 ………… 绝对指令,相对指令G94,G95 ………… 每分钟进给,每转进给■ 极坐标平面中的圆弧插补在极坐标插补平面作圆弧插补(G02或G03)的圆弧半径的位址根据该平面的第一轴(直线轴)来决定.当直线轴是X轴或平行于X轴时I和J在Xp-Yp平面内.当直线轴是Y轴或平行于Y轴时J和K在Yp-Zp平面内.当直线轴是Z轴或平行于Z轴时K和I在Zp-Xp平面内.■ 在极坐标插补模式不在极坐标插补平面沿轴向的移动刀具通常沿这些轴移动,而不依赖极坐标插补.■ 在极坐标插补模式当前位置的显示显示实际坐标.也显示在极坐标插补平面(笛卡尔坐标系)在单节中的残余距离.[ 限制]■ 极坐标插补的坐标系在指定G12.1之前,要设定局部坐标系(或工件坐标系)回转轴的中心为坐标系的原点.在G12.1模式,坐标系不能被改变(G92,G52,G53相关坐标系复位,G54到G59等).■ 刀具半径补正指令极坐标插补(G12.1或G13.1)模式不能在刀具半径补正模式(G41或G42)中开始或结束.G12.1或G13.1必须在刀具半径补正取消模式(G40)指定.■ 刀具长度偏移量指令刀具长度偏移量必须在极坐标插补取消模式在G12.1指定之前指定.不能在极坐标插补模式指定.甚至在极坐标插补模式不能改变偏移量值.■ 刀具偏移量指令刀具偏移量必须在G12.1模式之前指定.在G12.1模式不能改变偏移量.■ 程序再启动在G12.1模式中的单节,程序不能再启动.■ 旋转轴的切削进给率在笛卡尔坐标系中极坐标插补使刀具移动转换为旋转轴(C轴)和直线轴(X轴)的移动.当刀具移动接近工件的中心时,C轴的进给率向量变得很大,有可能超过C轴的最大进给率(参数No.1422中设定)引起报警.为防止C轴的进给率超过C轴的最大进给率,指定位址F来减小进给率或者改动程序使刀具(使用刀具半径补正时的刀具中心)不靠近工件的中心.注意)三条直线L1,L2和L3,ΔX是在笛卡尔坐标系用位址F指定进给率每单位时间刀具移动的距离.象刀具移动从L1到L2到L3,在坐标系中对应ΔX每单位时间刀具移动的角度从θ1到θ2到θ3.换句话说,C轴在刀具移动越靠近工件中心进给率变大.C的进给率向量有可能超过C轴的最大进给率因为刀具的移动在笛卡尔坐标系中要转换成C轴和X轴的移动.ΔXθ1 L1θ2 L2θ3 L3L:是刀具中心到工件中心的垂直距离R:C轴的最大切削进给率(deg/min)极坐标插补速度指定位址F用下列公式给出.指定速度在计算公式的允许值之下.公式提供的是理论值,实际上要根据计算误差比理论值稍微低一点.F〈L×R×π/ 180 (mm/min)[ 举例]极坐标插补程序举例基于X轴(直线轴)和C轴(旋转轴)假想C轴C轴程序轨迹刀具半径补正后N204 N203 的轨迹N205 N202 N201N208 X轴N200N206N207Z轴O0001 ;:N010 T0101;:N0100 G90 G00 X60.0 C0 Z_ ; 快速到起始位置N0200 G12.1 ; 极坐标插补开始N0201 G42 G01 X20.0 F_ ;N0202 C10.0 ;N0203 G03 X10.0 C20.0 R10.0 ;N0204 G01 X-20.0 ; 几何编程N0205 C-10.0 ; (基于笛卡尔坐标X-C'平面)N0206 G03 X-10.0 C-20.0 I10.0 J0 ;N0207 G01 X20.0 ;N0208 C0 ;N0209 G40 X60.0 ;N0210 G13.1 ; 极坐标插补取消N0300 Z_ ;N0400 X_ C_ ;::N0900 M30 ;。
极坐标插补原理

极坐标插补原理你看啊,在普通的坐标世界里,我们有直角坐标,横横竖竖的,就像城市里方方正正的街道一样。
但极坐标就不一样啦,它就像是在一个大圆盘上玩游戏。
极坐标有个原点,就像圆盘的中心,然后每个点呢,是用距离原点的长度和跟某个起始方向的夹角来表示的。
那极坐标插补是怎么回事呢?想象一下你要在这个极坐标的圆盘上画画。
比如说,你想画个漂亮的曲线。
极坐标插补就是一种超级聪明的办法,能让机器或者程序准确地沿着你想要的曲线走。
比如说,你要画一个花瓣的形状。
在极坐标里,这个花瓣的每个点都有它自己的距离和角度。
从数学的角度来说,它是根据一定的算法来计算下一个点的位置的。
就好像你要一步一步地走到你想去的地方。
它不是瞎走的哦,而是根据一个规则。
这个规则就像是一个小导游,告诉你,从你现在这个点,按照什么样的距离和角度走,就能到达下一个在曲线上的点。
我们可以把这个过程想象成一个小蚂蚁在圆盘上找宝藏。
小蚂蚁知道宝藏大概在某个方向和某个距离的地方。
它就根据这个极坐标插补的原理,一点一点地朝着宝藏前进。
每走一步,它都重新计算一下方向和距离,确保自己没有走偏。
而且啊,极坐标插补在很多实际的地方都超级有用呢!比如说在数控加工里。
那些数控机床就像是超级精密的大厨,要做出各种各样形状复杂的零件。
如果是直角坐标的话,有些形状做起来可费劲了。
但是用极坐标插补,就像是找到了一条捷径。
它可以很轻松地做出那些有弧度、有曲线的零件,就像大厨轻松地做出漂亮的雕花蛋糕一样。
再说说在绘图软件里吧。
当你想要画一些很有艺术感的图案,像是那种螺旋形状或者像星星一样有很多角的形状。
极坐标插补就能让你的绘图工具像有了魔法一样,准确地画出你心中的图案。
你不需要费很大的力气去计算每个点的直角坐标,只要告诉软件你想要的极坐标的规则,它就可以自动地生成漂亮的图形啦。
线切割极坐标插补装置

说明书线切割用极坐标插补装置技术领域本实用新型涉及模具加工制造技术领域,特别是应用在快走丝线切割机床中的一种旋转极坐标插补装置。
背景技术在模具加工中,经常会遇到外廓对称或是由一些很规律的几何要素,并且廓形还是一些较为复杂的方程曲线、列表曲线所组成的各种盘、柱类零件。
例如:链轮冲模、阿基米德曲线凸轮、齿轮、摆线齿轮、精密冷冲模的凸凹模锥体加工,等等。
鉴于这类模具具有精度高(一般尺寸,廓形精度0.01)、要求一致性好。
所以有条件的厂家都使用慢走丝线切割。
众所周知慢走丝的普及因受到价格制约,中小型的模具公司不一定在推广它的使用。
并且昂贵的设备必然会有高的维护,消耗,折旧费用,并用慢走丝切的锥度精度也不尽人意。
有些复杂廓形的曲线用机床所带的编程软件并不能成形(没带有这类方程曲线生成器)要将曲线手工化分成若干道并计算坐标值逐点逼近,程序动辙有3~4百道,费时耗工。
因而要开发生产此类产品,对于中小型的模具公司便是一个阻碍。
如果利用快走丝,克服它加工尺寸精度低、光洁度差,并且减少手工计算量的问题,加工此类零件成本必然会降低。
实用新型内容快走丝在切割工件时,由于丝筒正反转涨力不恒定,震动的问题,使之解决高光洁度较为困难。
然而相对情况下,其机床在X的正向(L1)加工时光洁度、尺寸精度、稳定性要好于其余方向,黑白条纹几乎没有。
我们利用以上条件,从几何定义出发,设计了一成型夹具——数控分度头,本实用新型解决的技术问题:一种用快走丝就可以切割出由复杂方程曲线、列表曲线所定义的各种盘、柱类高精度零件的高变速比(6000:1)的旋转极坐标插补装置,有效提高快走丝的利用率。
本实用新型采用的技术方案:旋转极坐标插补装置,具有变速箱(23),步进电机(28)通过电机座(27)连接在变速箱(23)上。
第一蜗杆(24)通过联轴器(50)和步进电机(28)相连接,并且第一蜗杆(24)的两端有轴承(39)(46)支撑在变速箱(23)壳体内,Ⅲ轴的两端轴承通过Ⅲ轴上压盖(54)和Ⅲ轴下压盖(43)作为轴向间隙的调整装置加上轴承垫(53)的压紧作用可以使Ⅲ轴的轴向蹿动得到限制。
双轴极坐标下的插补算法研究(精)
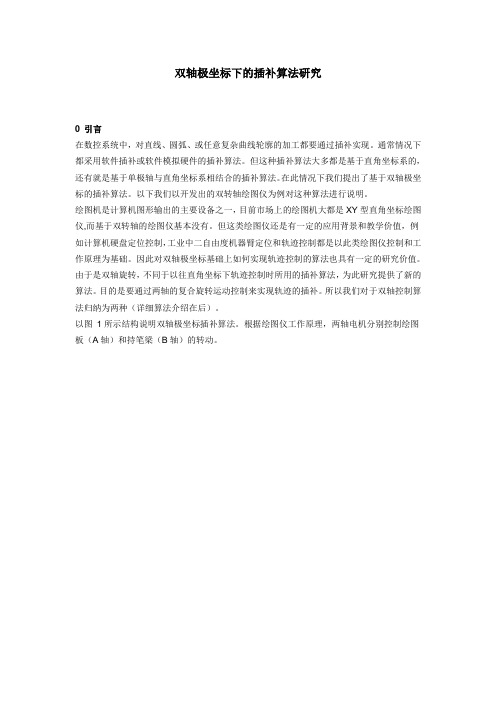
双轴极坐标下的插补算法研究0 引言在数控系统中,对直线、圆弧、或任意复杂曲线轮廓的加工都要通过插补实现。
通常情况下都采用软件插补或软件模拟硬件的插补算法。
但这种插补算法大多都是基于直角坐标系的,还有就是基于单极轴与直角坐标系相结合的插补算法。
在此情况下我们提出了基于双轴极坐标的插补算法。
以下我们以开发出的双转轴绘图仪为例对这种算法进行说明。
绘图机是计算机图形输出的主要设备之一,目前市场上的绘图机大都是XY型直角坐标绘图仪,而基于双转轴的绘图仪基本没有。
但这类绘图仪还是有一定的应用背景和教学价值,例如计算机硬盘定位控制,工业中二自由度机器臂定位和轨迹控制都是以此类绘图仪控制和工作原理为基础。
因此对双轴极坐标基础上如何实现轨迹控制的算法也具有一定的研究价值。
由于是双轴旋转,不同于以往直角坐标下轨迹控制时所用的插补算法,为此研究提供了新的算法。
目的是要通过两轴的复合旋转运动控制来实现轨迹的插补。
所以我们对于双轴控制算法归纳为两种(详细算法介绍在后)。
以图1所示结构说明双轴极坐标插补算法。
根据绘图仪工作原理,两轴电机分别控制绘图板(A轴)和持笔梁(B轴)的转动。
3 两种算法的分析比较总的来说,双轴极坐标插补和平面两自由度机械手这两种算法均可以实现系统要求的绘图功能,插补后的图形比较吻合要画的图形,这一点可以通过仿真效果图看出来。
比较如下:(1)双轴极坐标插补算法关键是要解决两轴速度与笔头绘图速度的(2)两自由度机械手算法关键要解决多解问题,末端操作器速度问题可以利用雅可比矩阵解决。
4 参考文献1.《机械电子工程设计》,杨平廉仲主编,国防工业出版社;2.《交流电机数字控制系统》李永东编著,机械工业出版社;3.《MC系列运动控制器手册》-长沙:长沙力鼎科技有限公司;20014.《伺服系统设计指导》,金钰,胡祐德,李向春编著,北京理工大学出版社;5.《伺服系统原理与设计》,胡德等著,北京理工大学出版社;6.《现代交流伺服系统》,秦忆等编著,华中理工大学出版社;。
- 1、下载文档前请自行甄别文档内容的完整性,平台不提供额外的编辑、内容补充、找答案等附加服务。
- 2、"仅部分预览"的文档,不可在线预览部分如存在完整性等问题,可反馈申请退款(可完整预览的文档不适用该条件!)。
- 3、如文档侵犯您的权益,请联系客服反馈,我们会尽快为您处理(人工客服工作时间:9:00-18:30)。
摘要:在车削中心加工中,其极坐标切能的应用很广泛。
它解决了在一次装
夹中完成回转体零件的车削及其端面异形轮廓的铣削等多道工序,达到高
效、高精度的目的。
数控车床一般只能加工回转体类零件,而要在回转类零件的端面加工孔系、矩形轮廓、矩形槽等形状,则不能直接在数控车床上加工,只能再由数控铣床继续加工,这样将影响零件的加工精度和增加零件的加工时间、降低生产效率。
而在车削中心上加工此类零件就比较方便,车削中心是在原有直角坐标的基础上,增加了个极坐标功能,使得机床能够把回转类零件和它端面的矩形轮廓或矩形槽在一次装夹中连续加工完成,另外运用极坐标的功能还可以加工盘形凸轮和刻字等。
1 车削中心坐标轴运动
车削中心除能车削回转体工件外,还能够加工的工件。
加工回转体工件时,工件的旋转是主运动,刀具的横向或纵向移动是从运动。
而在加工工件的端面轮廓槽或刻字时,主轴及工件将转换成分度旋转运动,装在刀架台上的刀具的旋转运动是主运动,由内置于刀架台内的伺服电机带动,刀具还可以进行横向或纵向运动。
当使用极坐标功能后,是通过主轴或工件的旋转运动和刀具的协调运动来完成轮厚阵槽或刻字等工作。
2 车削中心的极坐标功能
在使用FANUC-0T控制系统的车削中心上研究极坐标功能,其概念与数学中的极坐标概念有所不同。
在Z轴垂直的平面内,由相互垂直的实轴(第一轴)尤和虚轴(第二轴)C 组成,极坐标系的坐标原点与程序原点重合,且虚轴C的单位不是度或弧度,而是与实轴X轴的单位一样,均为mm。
极坐标插补:将直角坐标指令下的直线轴的移动(刀具的移动)切换为回转轴的移动(工件回转),控制其轮廓的机能称为极坐标插补。
极坐标插补模式:
G112 极坐标插补模式(进行极坐标插补)
G113 取消极坐标插补模式(不进行极坐标插补)
对于刚接通电源和复位(置O或切换)时,机床取消极坐标插补,即处于G113模式。
在进行极坐标补偿前,要预先设置直线轴及回转轴的初参量(参数为291、292) 。
执行
G112指令,转换为极坐标插补模式,将工件坐标系的原点设为极坐标工作的原点,极
坐标插补在极坐标平面上进行。
极坐标插补平面即第一平面轴(直线轴)和第二平面轴(假想和第一平面轴正交的轴—虚轴)确定的平面。
极坐标插补模式中的指令值就是极坐标插补平面仁的正交坐标系值,平面第二轴(假想的虚轴)指令的地址使用回转轴(参数292)的地址。
指令值的单位和平面轴的单位(mm 或inch)相同在极坐标插补模式中,使用G01、G03和G03指令时,绝对坐标或相对坐标均可。
另外,对于G112指令也可以对刀尖半径R进行补偿,刀尖半径R补偿的路径为极坐标插补进行的路径。
在G41、G42模式下不能直接切换到G112、G113模式,但在G40模式中可以进行极坐标G112、G113 的转换。
根据F确定(F单位
mm/min或inch/min)的极坐标插补平面上的进给速度,即刀具和工件的相对速度,
G112在虚轴的坐标值变为0(即执行G112的位置的角度为0度)时开始进行极坐标插补。
3 使用极坐标指令时的注意事项
1.执行G112 和G113指令时必须在程序中单独使用,并在极坐标系与直角坐标
系之间,还须成对使用。
程序中的实轴尤的坐标用直径值指定,虚轴C的坐标用半径值指定。
2.在机床处于刀具左补偿(G41)和刀具右补偿(G42)状态下,G112 指令不能执行,
机床必须处于刀补取消(G40)状态时,才能执行。
并须将铣刀的半径值输入到
机床刀具几何补偿库中,以获得正确的刀具切削轨迹。
3.在极坐极插补平面上进行圆弧插补(G02、G03)时,圆弧半径的指令方法,即
I、J、K参数的选用,需根据基本坐标系在哪个轴上来确定,也可以由半径R
来指令。
a.直线轴为X轴时,看作X p-Y p平面,使用I、J指令
b.直线轴为Y轴时,看作Y p-Z p平面,使用I、K指令
c.直线轴为Z轴时,看作Z p-Y p平面,使用K、I指令。
4.G112模式中能用的G指令有:G01、G02、G03、GO4(暂停)、G40、G41、
G42
5.刀具长度补偿应在取消极坐标插补后才能进行,在G112模式中不能使用。
另
外在G112模式中也不能变换偏置量的值。
6.G112模式中的程序块,在重新开机时,不能再次被执行。
4 极坐标插补功能的应用
极坐标插补平面是直线轴工轴、虚轴C轴(回转轴)所确定的平面。
对X轴、C轴进行极坐标插补应用的实例。
切削该工件使用Ø2mm的立铣刀进行加工,槽深为2mm 。
在进行编程之前,必须确定加工时刀具切削路线和左端轮廓各点在极坐标平面XOC的坐标值,刀具切削路线为:1→2→3→4→A→B→C→D→E→F→B→G→F
'→E'→D'→B'→A'→F'→C',坐标值为:1(x34.058, c9.5) 2(x-34.058,c9.5) 3(x-34.058,c-9.5) 4(x34.058 , c-9.5) A(x-19.0, c6.0)B(x-19.0, c4.0) C (x-29.0, c4.0)D(x-29.0,c-1.0)E(x-9.0 ,c-1.0)F(x-9.0, c4.0)B(x-19.0, c4.0)G(x-19.0,c-6.0 ) F'(x12.0,c1.0)E'(x12.0,
c5.0)D'(x25.0,c5.0)B'(x25.0,c-5.0)A'(x12.0,c-5.0) C'(x25.0, c1.0)。
以下为加工图2所示零件的程序清单:
指令说明
O0001;程序号
G0 G40 G97 G98 S1000铣刀转速1000r/min
T0101 M03 F30;调用T01号刀具及其刀补
G0 X44.0 CO Z2.0刀具决速接近工件
G112;执行极坐标插补
G01 X34.058 F20;刀具运动至X34.O58位置,进给速度为20mm/min
C9.5;刀具运动至1点位置
Z-2.0 F10;
X-34.058;刀具运动至2点位置
Z2.0;
C-95;刀具运动至3点位置
Z-2.0
X34.058;刀具从3点运动至4点位置
Z2.0;
X-19.0 C6.0;刀具从4点运动至A位置
Z-2.0;
C4.O;刀具从A点运动至B点位置
X-29.0;刀具从B点运动至C点位置
C-1.0;刀具从C点运动至D点位置
X-9.0;刀具从D点运动至E点位置
C4.O;刀具从E点运动至F点位置
X-1.90;刀具从F点运动至B点位置
C-6.0;刀具从B点运动至G点位置
Z2.0;
X12.0 C1.0;刀具从G点运动至F'位置
Z-2.0;
C5.0;刀具从F'点运动至E'点位置
X25.O;刀具从E'点运动至D'点位置
C-5.0;刀具从D'点运动至B'点位置
X12.0;刀其从B'点运动至A'点位置
C1.O;刀具从A'点运动至F'点位置
X24.0;刀具从F'点运动至C'点位置
Z2.0
G113;极坐标插补功能结束
G28 U0 W0 H0 TO M05;X、Y、Z轴回归机械零点.主轴停转
M3O程序结束
5 结论
经过近20年的发展,数控机床已广泛应用在机械制造中,而具有极坐标功能的车削中心在精密机械制造中发挥着重要的作用。
高效多功能是未来数控机床发展的方向,也是金属切削加工发展的方向。