辉光离子渗氮
辉光离子渗氮表面强化技术在汽车拉延模中的应用

辉光离子渗氮表面强化技术在汽车拉延模中的应用徐小清(上海大众汽车有限公司冲压中心 上海 201805)摘要:以桑塔纳轿车覆盖件拉延模为例,本文介绍了辉光等离子氮化技术在轿车拉延模大型面表面强化处理方面的应用,分析了该技术应用中的特点,最后给出了应用实例。
关键词:拉延模拉延模离子渗氮1,引言汽车覆盖件的冷冲模具,特别是拉延成形模具,由于工作条件较差,影响因素多,造成工作表面塑性变形失效和磨损失效,因而对其工作表面的强度、光洁度、硬度和耐磨性等都有较高的要求。
目前桑塔纳轿车覆盖件拉延模主要是德国和国内生产的。
德国模具成型部分的材料主要采用GGG70和GGG70L(德国牌号),属于球墨铸铁,这种材料的强度高、耐磨性好,表面具有良好的储油性能,基本可以满足冲压生产的要求,而国内生产的拉延模具其材料大都采用MoCr铸铁(球铁也仅在QT500以下,且球化效果不理想)等铸造后加工成形的,这种材料性能界于灰口铸铁和球墨铸铁之间,其耐磨性、硬度等指标都比较差,即使进行了火焰淬火等工艺的热处理,在工作一段时间,模具型面的磨损加大,其表面性能也会大幅下降,从而导致冲压件出现各种表面缺陷,例如拉毛、表面瘪塘等,必须对模具进行维修,严重影响了冲压的生产的质量和生产效率。
据统计,桑塔纳轿车覆盖件拉深模的在线维修中,由于型面问题的维修占据了近70~80%的维修时间。
因此目前对国内生产的拉延模都要求进行表面强化处理,以弥补材料性能的不足。
目前模具型面的表面强化方法有很多,例如电镀法、化学热处理、激光强化、喷丸处理等,其中有些方法还处于试验探索阶段,但有些方法已经成功应用于工程中,本文就介绍一种行之有效的热处理方法——辉光等离子氮化技术,该技术已经在桑塔纳轿车覆盖件模具得到应用,取得了较好的效果。
由于轿车覆盖件拉延模具有形面复杂、表面状况多变的特点,与合金类的小零件、小模具相比,在渗氮处理中有其特殊性,因此本文重点介绍了覆盖件的渗氮处理工艺。
氮化处理的工艺
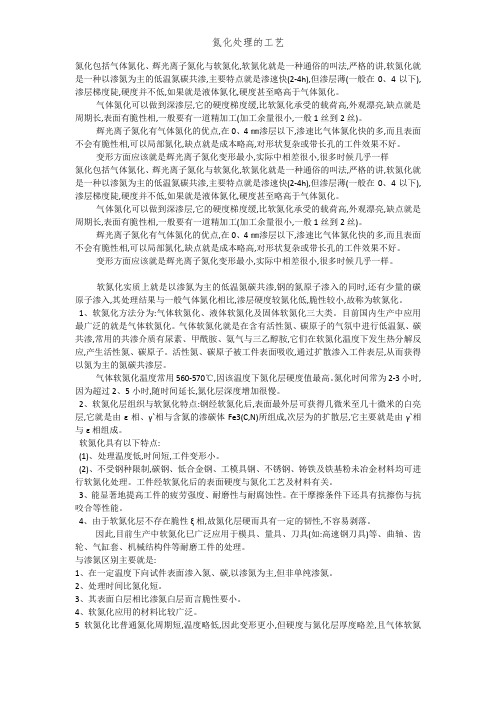
氮化包括气体氮化、辉光离子氮化与软氮化,软氮化就是一种通俗的叫法,严格的讲,软氮化就是一种以渗氮为主的低温氮碳共渗,主要特点就是渗速快(2-4h),但渗层薄(一般在0、4以下),渗层梯度陡,硬度并不低,如果就是液体氮化,硬度甚至略高于气体氮化。
气体氮化可以做到深渗层,它的硬度梯度缓,比软氮化承受的载荷高,外观漂亮,缺点就是周期长,表面有脆性相,一般要有一道精加工(加工余量很小,一般1丝到2丝)。
辉光离子氮化有气体氮化的优点,在0、4㎜渗层以下,渗速比气体氮化快的多,而且表面不会有脆性相,可以局部氮化,缺点就是成本略高,对形状复杂或带长孔的工件效果不好。
变形方面应该就是辉光离子氮化变形最小,实际中相差很小,很多时候几乎一样氮化包括气体氮化、辉光离子氮化与软氮化,软氮化就是一种通俗的叫法,严格的讲,软氮化就是一种以渗氮为主的低温氮碳共渗,主要特点就是渗速快(2-4h),但渗层薄(一般在0、4以下),渗层梯度陡,硬度并不低,如果就是液体氮化,硬度甚至略高于气体氮化。
气体氮化可以做到深渗层,它的硬度梯度缓,比软氮化承受的载荷高,外观漂亮,缺点就是周期长,表面有脆性相,一般要有一道精加工(加工余量很小,一般1丝到2丝)。
辉光离子氮化有气体氮化的优点,在0、4㎜渗层以下,渗速比气体氮化快的多,而且表面不会有脆性相,可以局部氮化,缺点就是成本略高,对形状复杂或带长孔的工件效果不好。
变形方面应该就是辉光离子氮化变形最小,实际中相差很小,很多时候几乎一样。
软氮化实质上就是以渗氮为主的低温氮碳共渗,钢的氮原子渗入的同时,还有少量的碳原子渗入,其处理结果与一般气体氮化相比,渗层硬度较氮化低,脆性较小,故称为软氮化。
1、软氮化方法分为:气体软氮化、液体软氮化及固体软氮化三大类。
目前国内生产中应用最广泛的就是气体软氮化。
气体软氮化就是在含有活性氮、碳原子的气氛中进行低温氮、碳共渗,常用的共渗介质有尿素、甲酰胺、氨气与三乙醇胺,它们在软氮化温度下发生热分解反应,产生活性氮、碳原子。
离子渗氮——精选推荐
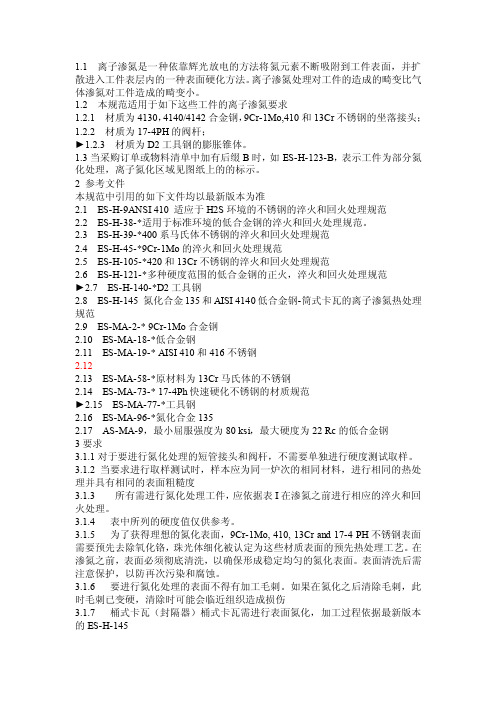
1.1 离子渗氮是一种依靠辉光放电的方法将氮元素不断吸附到工件表面,并扩散进入工件表层内的一种表面硬化方法。
离子渗氮处理对工件的造成的畸变比气体渗氮对工件造成的畸变小。
1.2 本规范适用于如下这些工件的离子渗氮要求1.2.1 材质为4130,4140/4142合金钢,9Cr-1Mo,410和13Cr不锈钢的坐落接头;1.2.2 材质为17-4PH的阀杆;►1.2.3 材质为D2工具钢的膨胀锥体。
1.3当采购订单或物料清单中加有后缀B时,如ES-H-123-B,表示工件为部分氮化处理,离子氮化区域见图纸上的的标示。
2 参考文件本规范中引用的如下文件均以最新版本为准2.1 ES-H-9ANSI 410 适应于H2S环境的不锈钢的淬火和回火处理规范2.2 ES-H-38-*适用于标准环境的低合金钢的淬火和回火处理规范。
2.3 ES-H-39-*400系马氏体不锈钢的淬火和回火处理规范2.4 ES-H-45-*9Cr-1Mo的淬火和回火处理规范2.5 ES-H-105-*420和13Cr不锈钢的淬火和回火处理规范2.6 ES-H-121-*多种硬度范围的低合金钢的正火,淬火和回火处理规范►2.7 ES-H-140-*D2工具钢2.8 ES-H-145 氮化合金135和AISI 4140低合金钢-筒式卡瓦的离子渗氮热处理规范2.9 ES-MA-2-* 9Cr-1Mo合金钢2.10 ES-MA-18-*低合金钢2.11 ES-MA-19-* AISI 410和416不锈钢2.122.13 ES-MA-58-*原材料为13Cr马氏体的不锈钢2.14 ES-MA-73-* 17-4Ph快速硬化不锈钢的材质规范►2.15 ES-MA-77-*工具钢2.16 ES-MA-96-*氮化合金1352.17 AS-MA-9,最小屈服强度为80 ksi,最大硬度为22 Rc的低合金钢3要求3.1.1对于要进行氮化处理的短管接头和阀杆,不需要单独进行硬度测试取样。
低温化学热处理方法——离子渗氮

低温化学热处理方法——离子渗氮1、原理简述离子渗氮时,首先用真空泵向炉内抽气,当真空度达到1.33Pa后,通入氨、氮混合气体,至炉压升至约70Pa时接通电源,在阴极(工件)与阳极间施加直流电压,使炉内气体放电,其伏安特性曲线如下图所示。
当阴阳极电压升到下图中c点对应的数值时,工件上开始产生辉光,这个电压称为辉光点燃电压。
起辉后极间电压陡降,随后电流在电源电压增加而极间电压基本不变的情况下不断增大。
此时工件上辉光的覆盖面迅速增大,至图中d点工件表面完全被辉光覆盖,cd段称为正常辉光区。
超过d点时电流再增加,阴阳电压也上升。
极间电压达到e点后又开始陡降,此时开始发生弧光放电。
de段称为异常辉光区,e点以后称为弧光放电区。
离子渗氮通常是在异常辉光区进行。
在这个区段可通过控制电压调节电流,从而控制工件的加热温度,但注意避免弧光放电。
电源控制系统应能在发生弧光时自动切断电源熄灭弧光,然后自动点燃辉光,继续工作。
▲气体放电的伏安特性曲线在真空离子渗氮炉中,氮氢混合气体中的氮被电离成离子,它们轰击钢件表面,使之溅射出铁原子,并与等离子区的氮原子及电子结合形成化合物FeN,FeN吸附在工件表面后,又在离子轰击作用下逐步分解为低价氮化物和氮原子,使之渗入工件内部。
因此,氮由气相转入固相而实现渗氮主要是通过碰撞离解产生的大量活性氮原子渗入工件来实现的。
2、离子渗氮层性能(1)渗氮层的硬度渗层的硬度及其分布,是衡量渗氮效果和使用性能的主要指标。
离子渗氮与常规渗氮工艺相比,在硬度方面无明显差别。
但离子渗氮可以通过调节工艺参数来控制渗层组织,获得理想的、平缓的硬度分布。
碳钢、铸铁的化合物层薄,硬度低(<800HV),主要靠固溶强化,扩散层的硬度仅比心部略高(300~500HV)。
含合金氮化物形成元素的钢,如结构钢、工具钢、高速钢等经离子渗氮后,由于高硬度的合金氮化物弥散强化作用,而使得表面具有很高的硬度。
(2)耐磨性足够厚的化合物层,具有较好的抗腐蚀、耐磨损的能力。
NiTi记忆合金的辉光离子渗氮表面改性的开题报告
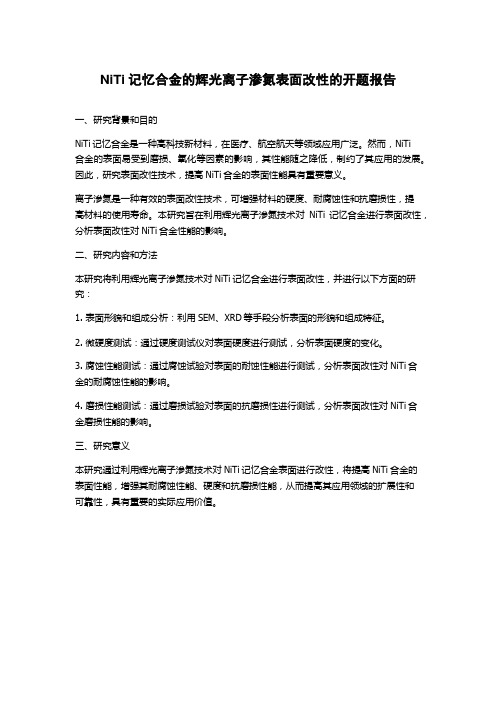
NiTi记忆合金的辉光离子渗氮表面改性的开题报告
一、研究背景和目的
NiTi记忆合金是一种高科技新材料,在医疗、航空航天等领域应用广泛。
然而,NiTi
合金的表面易受到磨损、氧化等因素的影响,其性能随之降低,制约了其应用的发展。
因此,研究表面改性技术,提高NiTi合金的表面性能具有重要意义。
离子渗氮是一种有效的表面改性技术,可增强材料的硬度、耐腐蚀性和抗磨损性,提
高材料的使用寿命。
本研究旨在利用辉光离子渗氮技术对NiTi记忆合金进行表面改性,分析表面改性对NiTi合金性能的影响。
二、研究内容和方法
本研究将利用辉光离子渗氮技术对NiTi记忆合金进行表面改性,并进行以下方面的研究:
1. 表面形貌和组成分析:利用SEM、XRD等手段分析表面的形貌和组成特征。
2. 微硬度测试:通过硬度测试仪对表面硬度进行测试,分析表面硬度的变化。
3. 腐蚀性能测试:通过腐蚀试验对表面的耐蚀性能进行测试,分析表面改性对NiTi合金的耐腐蚀性能的影响。
4. 磨损性能测试:通过磨损试验对表面的抗磨损性进行测试,分析表面改性对NiTi合金磨损性能的影响。
三、研究意义
本研究通过利用辉光离子渗氮技术对NiTi记忆合金表面进行改性,将提高NiTi合金的表面性能,增强其耐腐蚀性能、硬度和抗磨损性能,从而提高其应用领域的扩展性和
可靠性,具有重要的实际应用价值。
离子氮化硬度和深度

离子氮化硬度和深度离子渗氮作为强化金属表面的一种利用辉光放电现象,将含氮气体电离后产生的氮离子轰击零件表面加热并进行氮化,获得表面渗氮层的离子化学热处理工艺,广泛适用于铸铁、碳钢、合金钢、不锈钢及钛合金等。
零件经离子渗氮处理后,可显著提高材料表面的硬度,使其具有高的耐磨性、疲劳强度,抗蚀能力及抗烧伤性等。
如果氧化是在氮化结束后停炉过程中产生的,则仅影响外观质量,对渗层硬度、深度无影响。
1.离子氮化工艺技术的内涵及原理离子氮化是为了提高工件表面耐磨性、耐疲劳性、耐蚀性及耐高温等性能,利用等离子辉光放电在离子氮化设备内制备氮化层的一种工艺方法。
离子氮化分三个阶段,第一阶段活性氮原子产生,第二阶段活性氮原子从介质中迁移到工件表面,第三阶段氮原子从工件表面转移到芯部。
其中第一阶段电离和第三阶段扩散机制比较清楚,第二阶段活性氮原子如何从介质中迁移到工件表面的机理尚存争议,普遍认可的是“溅射-沉积”理论。
具体原理为:高能离子轰击工件表面,铁原子脱离基体飞溅出来和空间中的活性氮原子反应形成渗氮铁,渗氮铁分子凝聚后再沉积到工件表面。
渗氮铁在一定的渗氮温度下分解成含氮量更低的氮铁化合物,释放出氮原子,渗氮铁不断形成为一定厚度的渗氮层。
2.离子氮化工艺技术的发展历史(1)1932年德国人B.Berghaus发明。
3.离子氮化工艺技术的优点(1)工件涂层可根据预期性能要求通过调节氮、氢及其他(如碳、氧、硫等)气氛的比例调整实现相组成调节。
(2)制备涂层时间是普通渗氮的三分之一到五分之一,效率高。
(3)制备过程十分清洁而无需防止公害,无需额外加热和检测设备,能够获得均匀的温度分布,能源消耗是气体渗氮的40~70%,节能环保;耗气量极少(仅为气体渗氮的百分之几),可大大减少离子氮化的常见缺陷;适用的材质和温度范围广泛。
(4)工件制备完涂层后可获得无氧化的加工表面,表面光洁度高,变形量小。
4.离子氮化工艺技术的难点(1)空心阴极效应限制了在带小孔、间隙和沟槽零件中的应用(2)边角效应导致导致工件边角部位硬度和其余部位不一致(3)不同结构工件混装时温度的控制和测量存在困难(4)零件表面产生弧光放电(打弧)造成等离子不稳定或高洁净工件表面损伤5.离子氮化工艺技术应用常见问题(1)硬度低。
依靠辉光放电的离子渗氮技术自上世纪70 年代以来已获得广泛应用
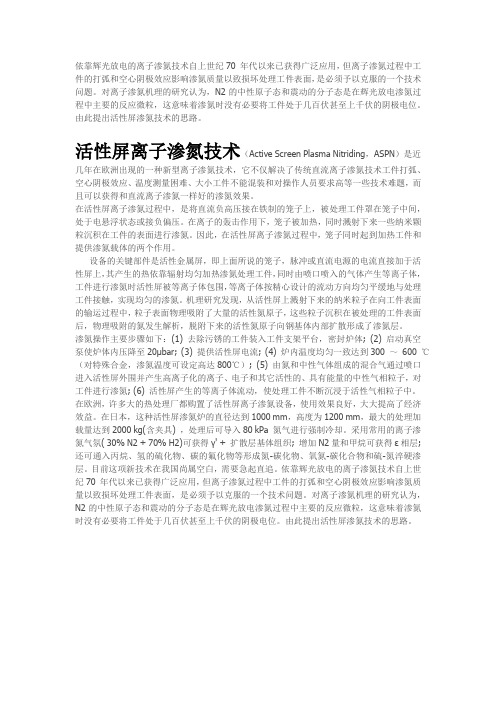
依靠辉光放电的离子渗氮技术自上世纪70 年代以来已获得广泛应用,但离子渗氮过程中工件的打弧和空心阴极效应影响渗氮质量以致损坏处理工件表面,是必须予以克服的一个技术问题。
对离子渗氮机理的研究认为,N2的中性原子态和震动的分子态是在辉光放电渗氮过程中主要的反应微粒,这意味着渗氮时没有必要将工件处于几百伏甚至上千伏的阴极电位。
由此提出活性屏渗氮技术的思路。
活性屏离子渗氮技术(Active Screen Plasma Nitriding,ASPN)是近几年在欧洲出现的一种新型离子渗氮技术,它不仅解决了传统直流离子渗氮技术工件打弧、空心阴极效应、温度测量困难、大小工件不能混装和对操作人员要求高等一些技术难题,而且可以获得和直流离子渗氮一样好的渗氮效果。
在活性屏离子渗氮过程中,是将直流负高压接在铁制的笼子上,被处理工件罩在笼子中间,处于电悬浮状态或接负偏压。
在离子的轰击作用下,笼子被加热,同时溅射下来一些纳米颗粒沉积在工件的表面进行渗氮。
因此,在活性屏离子渗氮过程中,笼子同时起到加热工件和提供渗氮载体的两个作用。
设备的关键部件是活性金属屏,即上面所说的笼子,脉冲或直流电源的电流直接加于活性屏上,其产生的热依靠辐射均匀加热渗氮处理工件,同时由喷口喷入的气体产生等离子体,工件进行渗氮时活性屏被等离子体包围,等离子体按精心设计的流动方向均匀平缓地与处理工件接触,实现均匀的渗氮。
机理研究发现,从活性屏上溅射下来的纳米粒子在向工件表面的输运过程中,粒子表面物理吸附了大量的活性氮原子,这些粒子沉积在被处理的工件表面后,物理吸附的氮发生解析,脱附下来的活性氮原子向钢基体内部扩散形成了渗氮层。
渗氮操作主要步骤如下:(1) 去除污锈的工件装入工件支架平台,密封炉体; (2) 启动真空泵使炉体内压降至20μbar; (3) 提供活性屏电流; (4) 炉内温度均匀一致达到300 ~600 ℃(对特殊合金,渗氮温度可设定高达800℃); (5) 由氮和中性气体组成的混合气通过喷口进入活性屏外围并产生高离子化的离子、电子和其它活性的、具有能量的中性气相粒子,对工件进行渗氮; (6) 活性屏产生的等离子体流动,使处理工件不断沉浸于活性气相粒子中。
等离子渗氮加工
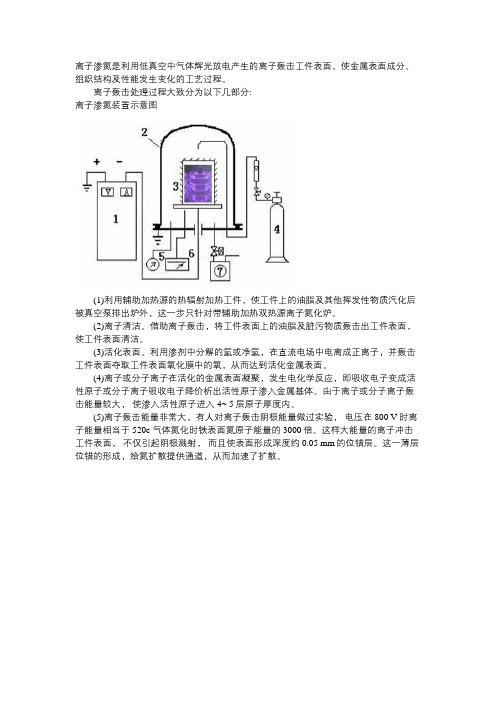
离子渗氮是利用低真空中气体辉光放电产生的离子轰击工件表面,使金属表面成分、组织结构及性能发生变化的工艺过程。
离子轰击处理过程大致分为以下几部分:
离子渗氮装置示意图
(1)利用辅助加热源的热辐射加热工件,使工件上的油脂及其他挥发性物质汽化后被真空泵排出炉外,这一步只针对带辅助加热双热源离子氮化炉。
(2)离子清洁。
借助离子轰击,将工件表面上的油脂及脏污物质轰击出工件表面,使工件表面清洁。
(3)活化表面。
利用渗剂中分解的氢或净氢,在直流电场中电离成正离子,并轰击工件表面夺取工件表面氧化膜中的氧,从而达到活化金属表面。
(4)离子或分子离子在活化的金属表面凝聚,发生电化学反应,即吸收电子变成活性原子或分子离子吸收电子降价析出活性原子渗入金属基体。
由于离子或分子离子轰击能量较大,使渗入活性原子进入4~ 5层原子厚度内。
(5)离子轰击能量非常大,有人对离子轰击阴极能量做过实验,电压在800 V时离子能量相当于520e 气体氮化时铁表面氮原子能量的3000倍。
这样大能量的离子冲击工件表面,不仅引起阴极溅射,而且使表面形成深度约0.05 mm的位错层。
这一薄层位错的形成,给氮扩散提供通道,从而加速了扩散。
渗氮知识
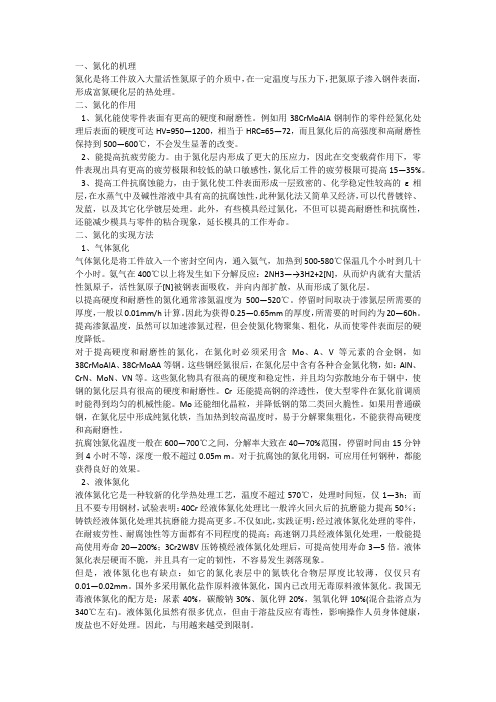
一、氮化的机理氮化是将工件放入大量活性氮原子的介质中,在一定温度与压力下,把氮原子渗入钢件表面,形成富氮硬化层的热处理。
二、氮化的作用1、氮化能使零件表面有更高的硬度和耐磨性。
例如用38CrMoAlA钢制作的零件经氮化处理后表面的硬度可达HV=950—1200,相当于HRC=65—72,而且氮化后的高强度和高耐磨性保持到500—600℃,不会发生显著的改变。
2、能提高抗疲劳能力。
由于氮化层内形成了更大的压应力,因此在交变载荷作用下,零件表现出具有更高的疲劳极限和较低的缺口敏感性,氮化后工件的疲劳极限可提高15—35%。
3、提高工件抗腐蚀能力,由于氮化使工件表面形成一层致密的、化学稳定性较高的ε相层,在水蒸气中及碱性溶液中具有高的抗腐蚀性,此种氮化法又简单又经济,可以代替镀锌、发蓝,以及其它化学镀层处理。
此外,有些模具经过氮化,不但可以提高耐磨性和抗腐性,还能减少模具与零件的粘合现象,延长模具的工作寿命。
二、氮化的实现方法1、气体氮化气体氮化是将工件放入一个密封空间内,通入氨气,加热到500-580℃保温几个小时到几十个小时。
氨气在400℃以上将发生如下分解反应:2NH3—→3H2+2[N],从而炉内就有大量活性氮原子,活性氮原子[N]被钢表面吸收,并向内部扩散,从而形成了氮化层。
以提高硬度和耐磨性的氮化通常渗氮温度为500—520℃。
停留时间取决于渗氮层所需要的厚度,一般以0.01mm/h计算。
因此为获得0.25—0.65mm的厚度,所需要的时间约为20—60h。
提高渗氮温度,虽然可以加速渗氮过程,但会使氮化物聚集、粗化,从而使零件表面层的硬度降低。
对于提高硬度和耐磨性的氮化,在氮化时必须采用含Mo、A、V等元素的合金钢,如38CrMoAlA、38CrMoAA等钢。
这些钢经氮很后,在氮化层中含有各种合金氮化物,如:AlN、CrN、MoN、VN等。
这些氮化物具有很高的硬度和稳定性,并且均匀弥散地分布于钢中,使钢的氮化层具有很高的硬度和耐磨性。
新型LDMC离子渗氮设备简介

等离子体渗氮(辉光离子氮化)工艺作为一种有效的钢铁及合金表面强化技术在工业上已得到广泛的应用,与其他渗氮相比,离子渗氮具有渗速快、渗层脆性疏松理想、零件变形小、有利于不锈钢、铸铁渗氮、节能、无污染等特点。
七十至八十年代,以直流电源(即LD系列)设备进行离子渗氮,问题明显突出,装炉要求严格。
以曲轴为例:曲轴渗氮前必须对其油孔、平衡孔进行封堵,其中若有一孔未堵或封堵件在渗氮过程中有一件掉落,渗氮将无法进行(尤其在渗氮保温时),甚至会出现弧光损伤曲轴的现象。
比表面较大的零件,表面渗氮电流密度往往不足以保证离子渗氮所必须的下限值,如有些小规格的气门杆在满装炉渗氮时,气门杆渗氮表面会出现点蚀,另外因为表面电流的原因,辅助加热渗氮设备应用也受到限制,弧点能量过大,一些比较光亮的零件,在渗氮时表面往往会出现弧光斑点,直流电源渗氮电源限流电阻过大,尤其在大功率设备,电源发热严重。
对于深孔、深槽处理困难等等。
这些问题直接影响了离子渗氮工艺在生产的应用。
八十年代末,国外开展了脉冲电源等离子体渗氮设备工艺的研究,对此《国外金属热处理》曾作了大量报道,引起了国内同行和专家的极大关注。
九十年代初国内开始研制脉冲电源。
以IGBT作为开关器件,最大输出功率300kV A的大功率脉冲离子渗氮电源。
经过几年的推广表明,脉冲电源为离子渗氮工艺的发展提供有力的支持。
LDMC系列大功率脉冲电源等离子体渗氮设备广泛应用于机械、石油化工、航空航天、军工兵器、汽车发动机等行业。
对挤压机螺杆、精密丝杠和主轴、发动机曲轴、钛和钛合金零件、工模具、气门杆和缸套、活塞环等的渗氮处理。
从一九九五年投放市场以来已在广西玉柴机器股份公司、东风汽车公司发动机厂、文登天润曲轴有限公司、仪征双环活塞环有限公司、东风朝阳柴油机公司、丹东五一八内燃机配件厂、本溪曲轴厂、大连海事大学等国内几十家大、中型企业提供了近百台大功率脉冲电源等离子体渗氮设备。
深受用户好评。
1998年该设备由国家经济贸易委员会认定为“国家级新产品”。
离子渗氮用脉冲电源的研制
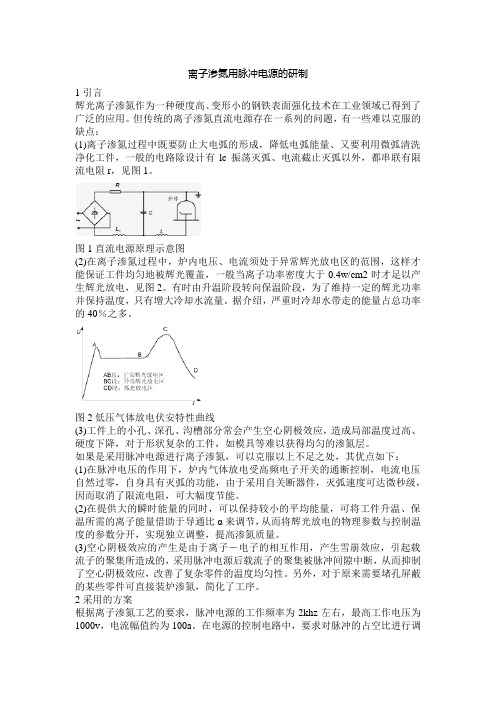
离子渗氮用脉冲电源的研制1引言辉光离子渗氮作为一种硬度高、变形小的钢铁表面强化技术在工业领域已得到了广泛的应用。
但传统的离子渗氮直流电源存在一系列的问题,有一些难以克服的缺点:(1)离子渗氮过程中既要防止大电弧的形成,降低电弧能量、又要利用微弧清洗净化工件,一般的电路除设计有lc振荡灭弧、电流截止灭弧以外,都串联有限流电阻r,见图1。
图1直流电源原理示意图(2)在离子渗氮过程中,炉内电压、电流须处于异常辉光放电区的范围,这样才能保证工件均匀地被辉光覆盖,一般当离子功率密度大于0.4w/cm2时才足以产生辉光放电,见图2。
有时由升温阶段转向保温阶段,为了维持一定的辉光功率并保持温度,只有增大冷却水流量。
据介绍,严重时冷却水带走的能量占总功率的40%之多。
图2低压气体放电伏安特性曲线(3)工件上的小孔、深孔、沟槽部分常会产生空心阴极效应,造成局部温度过高、硬度下降,对于形状复杂的工件,如模具等难以获得均匀的渗氮层。
如果是采用脉冲电源进行离子渗氮,可以克服以上不足之处,其优点如下:(1)在脉冲电压的作用下,炉内气体放电受高频电子开关的通断控制,电流电压自然过零,自身具有灭弧的功能,由于采用自关断器件,灭弧速度可达微秒级,因而取消了限流电阻,可大幅度节能。
(2)在提供大的瞬时能量的同时,可以保持较小的平均能量,可将工件升温、保温所需的离子能量借助于导通比α来调节,从而将辉光放电的物理参数与控制温度的参数分开,实现独立调整,提高渗氮质量。
(3)空心阴极效应的产生是由于离子-电子的相互作用,产生雪崩效应,引起载流子的聚集所造成的,采用脉冲电源后载流子的聚集被脉冲间隙中断,从而抑制了空心阴极效应,改善了复杂零件的温度均匀性。
另外,对于原来需要堵孔屏蔽的某些零件可直接装炉渗氮,简化了工序。
2采用的方案根据离子渗氮工艺的要求,脉冲电源的工作频率为2khz左右,最高工作电压为1000v,电流幅值约为100a。
在电源的控制电路中,要求对脉冲的占空比进行调节,对炉内温度实现pid调节控制,对打弧进行检测与保护。
氮化处理的工艺
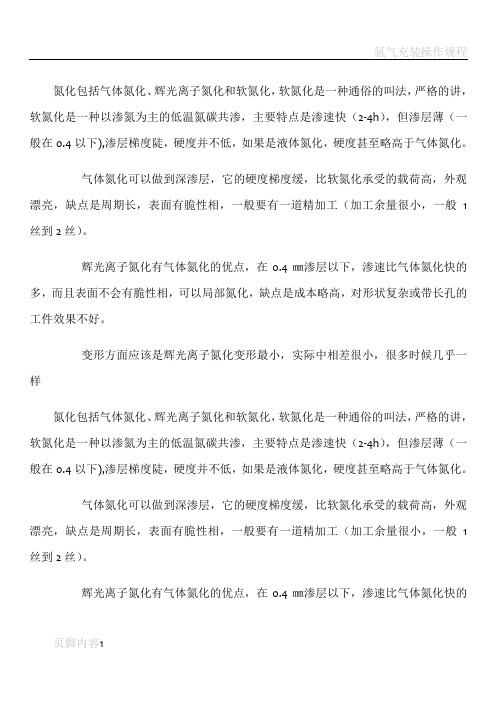
氮化包括气体氮化、辉光离子氮化和软氮化,软氮化是一种通俗的叫法,严格的讲,软氮化是一种以渗氮为主的低温氮碳共渗,主要特点是渗速快(2-4h),但渗层薄(一般在0.4以下),渗层梯度陡,硬度并不低,如果是液体氮化,硬度甚至略高于气体氮化。
气体氮化可以做到深渗层,它的硬度梯度缓,比软氮化承受的载荷高,外观漂亮,缺点是周期长,表面有脆性相,一般要有一道精加工(加工余量很小,一般1丝到2丝)。
辉光离子氮化有气体氮化的优点,在0.4㎜渗层以下,渗速比气体氮化快的多,而且表面不会有脆性相,可以局部氮化,缺点是成本略高,对形状复杂或带长孔的工件效果不好。
变形方面应该是辉光离子氮化变形最小,实际中相差很小,很多时候几乎一样氮化包括气体氮化、辉光离子氮化和软氮化,软氮化是一种通俗的叫法,严格的讲,软氮化是一种以渗氮为主的低温氮碳共渗,主要特点是渗速快(2-4h),但渗层薄(一般在0.4以下),渗层梯度陡,硬度并不低,如果是液体氮化,硬度甚至略高于气体氮化。
气体氮化可以做到深渗层,它的硬度梯度缓,比软氮化承受的载荷高,外观漂亮,缺点是周期长,表面有脆性相,一般要有一道精加工(加工余量很小,一般1丝到2丝)。
辉光离子氮化有气体氮化的优点,在0.4㎜渗层以下,渗速比气体氮化快的多,而且表面不会有脆性相,可以局部氮化,缺点是成本略高,对形状复杂或带长孔的工件效果不好。
变形方面应该是辉光离子氮化变形最小,实际中相差很小,很多时候几乎一样。
软氮化实质上是以渗氮为主的低温氮碳共渗,钢的氮原子渗入的同时,还有少量的碳原子渗入,其处理结果与一般气体氮化相比,渗层硬度较氮化低,脆性较小,故称为软氮化。
1、软氮化方法分为:气体软氮化、液体软氮化及固体软氮化三大类。
目前国内生产中应用最广泛的是气体软氮化。
气体软氮化是在含有活性氮、碳原子的气氛中进行低温氮、碳共渗,常用的共渗介质有尿素、甲酰胺、氨气和三乙醇胺,它们在软氮化温度下发生热分解反应,产生活性氮、碳原子。
渗氮工艺

渗氮渗氮,是在一定温度下一定介质中使氮原子渗入工件表层的化学热处理工艺。
常见有液体渗氮、气体渗氮、离子渗氮。
传统的气体渗氮是把工件放入密封容器中,通以流动的氨气并加热,保温较长时间后,氨气热分解产生活性氮原子,不断吸附到工件表面,并扩散渗入工件表层内,从而改变表层的化学成分和组织,获得优良的表面性能。
如果在渗氮过程中同时渗入碳以促进氮的扩散,则称为氮碳共渗。
常用的是气体渗氮和离子渗氮。
目录原理应用气体渗氮离子渗氮氮碳共渗辉光离子氮化渗氮前的处理渗氮前的生产准备原理应用渗入钢中的氮一方面由表及里与铁形成不同含氮量的氮化铁,一方面与钢中的合金元素结合形成各种合金氮化物,特别是氮化铝、氮化铬。
这些氮化物具有很高的硬度、热稳定性和很高的弥散度,因而可使渗氮后的钢件得到高的表面硬度、耐磨性、疲劳强度、抗咬合性、抗大气和过热蒸汽腐蚀能力、抗回火软化能力,并降低缺口敏感性。
与渗碳工艺相比,渗氮温度比较低,因而畸变小,但由于心部硬度较低,渗层也较浅,一般只能满足承受轻、中等载荷的耐磨、耐疲劳要求,或有一定耐热、耐腐蚀要求的机器零件,以及各种切削刀具、冷作和热作模具等。
渗氮有多种方法,常用的是气体渗氮和离子渗氮。
钢铁渗氮的研究始于20世纪初,20年代以后获得工业应用。
最初的气体渗氮,仅限于含铬、铝的钢,后来才扩大到其他钢种。
从70年代开始,渗氮从理论到工艺都得到迅速发展并日趋完善,适用的材料和工件也日益扩大,成为重要的化学热处理工艺之一。
气体渗氮一般以提高金属的耐磨性为主要目的,因此需要获得高的表面硬度。
它适用于38CrMoAl等渗氮钢。
渗氮后工件表面硬度可达HV850~1200。
渗氮温度低,工件畸变小,可用于精度要求高、又有耐磨要求的零件,如镗床镗杆和主轴、磨床主轴、气缸套筒等。
但由于渗氮层较薄,不适于承受重载的耐磨零件。
气体参氮可采用一般渗氮法(即等温渗氮)或多段(二段、三段)渗氮法。
前者是在整个渗氮过程中渗氮温度和氨气分解率保持不变。
金属钛辉光离子氮化制备氮化钛膜层的研究
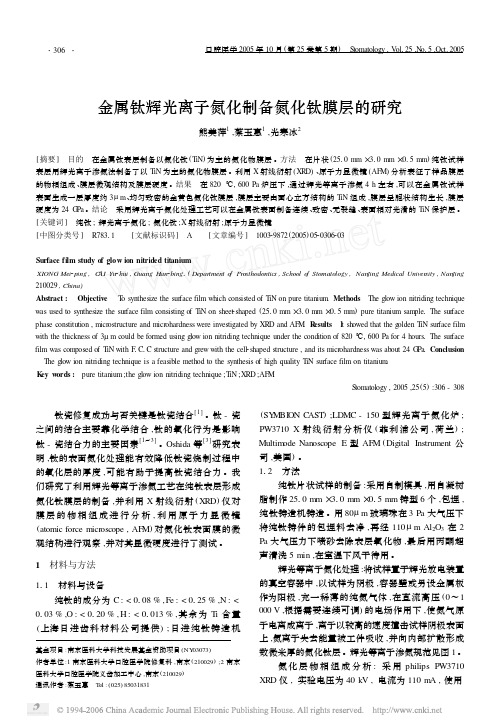
金属钛辉光离子氮化制备氮化钛膜层的研究熊美萍1,蔡玉惠1,光寒冰2[摘要] 目的 在金属钛表层制备以氮化钛(T iN )为主的氮化物膜层。
方法 在片状(2510mm ×310mm ×015mm )纯钛试样表层用辉光离子渗氮法制备了以T iN 为主的氮化物膜层。
利用X 射线衍射(XRD )、原子力显微镜(AF M )分析表征了样品膜层的物相组成、膜层微观结构及膜层硬度。
结果 在820℃,600Pa 炉压下,通过辉光等离子渗氮4h 左右,可以在金属钛试样表面生成一层厚度约3μm 、均匀致密的金黄色氮化钛膜层,膜层主要由面心立方结构的T iN 组成,膜层呈胞状结构生长,膜层硬度为24G Pa 。
结论 采用辉光离子氮化处理工艺可以在金属钛表面制备连续、致密、无裂缝、表面相对光滑的T iN 保护层。
[关键词] 纯钛;辉光离子氮化;氮化钛;X 射线衍射;原子力显微镜[中图分类号] R78311 [文献标识码] A [文章编号] 100329872(2005)0520306203Surface film study of glow ion nitrided titaniumXIONG Mei 2ping ,C AI Yu 2hui ,Guang Han 2bing 1(Department o f Prosthodontics ,School o f Stomatology ,Nanjing Medical Univer sity ,Nanjing210029,China )Abstract : Objective T o synthesize the surface film which consisted of T iN on pure titanium 1Methods The glow ion nitriding technique was used to synthesize the surface film consisting of T iN on sheet 2shaped (2510mm ×310mm ×015mm )pure titanium sample 1The surface phase constitution ,microstructure and microhardness were investigated by XRD and AF M 1R esults It showed that the g olden T iN surface film with the thickness of 3μm could be formed using glow ion nitriding technique under the condition of 820℃,600Pa for 4hours 1The surface film was composed of T iN with F 1C 1C structure and grew with the cell 2shaped structure ,and its microhardness was about 24G Pa 1Conclusion The glow ion nitriding technique is a feasible method to the synthesis of high quality T iN surface film on titanium 1K ey w ords : pure titanium ;the glow ion nitriding technique ;T iN ;XRD ;AF MS tomatology ,2005,25(5):306-308基金项目:南京医科大学科技发展基金资助项目(NY 03073)作者单位:1南京医科大学口腔医学院修复科,南京(210029);2南京医科大学口腔医学院义齿加工中心,南京(210029)通讯作者:蔡玉惠 T el :(025)85031831 钛瓷修复成功与否关键是钛瓷结合[1]。
辉光离子渗氮在汽车模具表面处理的应用
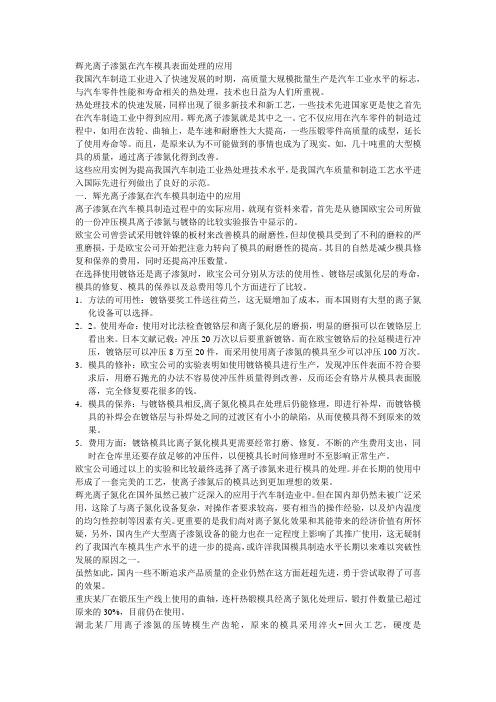
辉光离子渗氮在汽车模具表面处理的应用我国汽车制造工业进入了快速发展的时期,高质量大规模批量生产是汽车工业水平的标志,与汽车零件性能和寿命相关的热处理,技术也日益为人们所重视。
热处理技术的快速发展,同样出现了很多新技术和新工艺,一些技术先进国家更是使之首先在汽车制造工业中得到应用。
辉光离子渗氮就是其中之一。
它不仅应用在汽车零件的制造过程中,如用在齿轮、曲轴上,是车速和耐磨性大大提高,一些压锻零件高质量的成型,延长了使用寿命等。
而且,是原来认为不可能做到的事情也成为了现实。
如,几十吨重的大型模具的质量,通过离子渗氮化得到改善。
这些应用实例为提高我国汽车制造工业热处理技术水平,是我国汽车质量和制造工艺水平进入国际先进行列做出了良好的示范。
一.辉光离子渗氮在汽车模具制造中的应用离子渗氮在汽车模具制造过程中的实际应用,就现有资料来看,首先是从德国欧宝公司所做的一份冲压模具离子渗氮与镀铬的比较实验报告中显示的。
欧宝公司曾尝试采用镀锌镍的板材来改善模具的耐磨性,但却使模具受到了不利的磨粒的严重磨损,于是欧宝公司开始把注意力转向了模具的耐磨性的提高。
其目的自然是减少模具修复和保养的费用,同时还提高冲压数量。
在选择使用镀铬还是离子渗氮时,欧宝公司分别从方法的使用性、镀铬层或氮化层的寿命,模具的修复、模具的保养以及总费用等几个方面进行了比较。
1.方法的可用性:镀铬要奖工件送往荷兰,这无疑增加了成本,而本国则有大型的离子氮化设备可以选择。
2.2。
使用寿命:使用对比法检查镀铬层和离子氮化层的磨损,明显的磨损可以在镀铬层上看出来。
日本文献记载:冲压20万次以后要重新镀铬。
而在欧宝镀铬后的拉延模进行冲压,镀铬层可以冲压8万至20件,而采用使用离子渗氮的模具至少可以冲压100万次。
3.模具的修补:欧宝公司的实验表明如使用镀铬模具进行生产,发现冲压件表面不符合要求后,用磨石抛光的办法不容易使冲压件质量得到改善,反而还会有铬片从模具表面脱落,完全修复要花很多的钱。
氮化处理的工艺
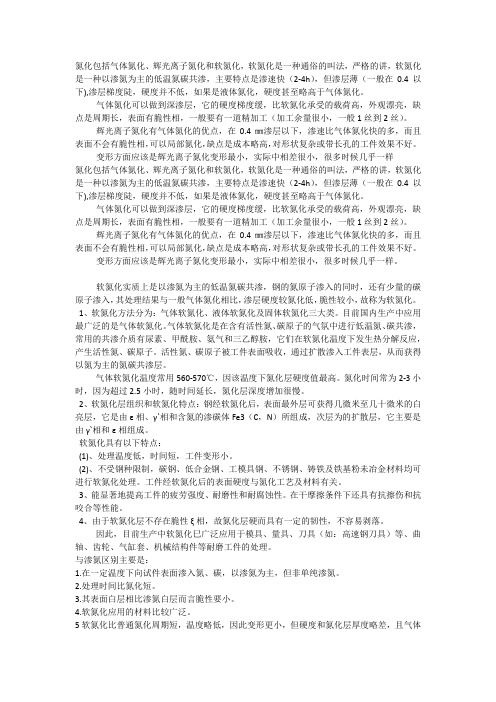
氮化包括气体氮化、辉光离子氮化和软氮化,软氮化是一种通俗的叫法,严格的讲,软氮化是一种以渗氮为主的低温氮碳共渗,主要特点是渗速快(2-4h),但渗层薄(一般在0.4以下),渗层梯度陡,硬度并不低,如果是液体氮化,硬度甚至略高于气体氮化。
气体氮化可以做到深渗层,它的硬度梯度缓,比软氮化承受的载荷高,外观漂亮,缺点是周期长,表面有脆性相,一般要有一道精加工(加工余量很小,一般1丝到2丝)。
辉光离子氮化有气体氮化的优点,在0.4㎜渗层以下,渗速比气体氮化快的多,而且表面不会有脆性相,可以局部氮化,缺点是成本略高,对形状复杂或带长孔的工件效果不好。
变形方面应该是辉光离子氮化变形最小,实际中相差很小,很多时候几乎一样氮化包括气体氮化、辉光离子氮化和软氮化,软氮化是一种通俗的叫法,严格的讲,软氮化是一种以渗氮为主的低温氮碳共渗,主要特点是渗速快(2-4h),但渗层薄(一般在0.4以下),渗层梯度陡,硬度并不低,如果是液体氮化,硬度甚至略高于气体氮化。
气体氮化可以做到深渗层,它的硬度梯度缓,比软氮化承受的载荷高,外观漂亮,缺点是周期长,表面有脆性相,一般要有一道精加工(加工余量很小,一般1丝到2丝)。
辉光离子氮化有气体氮化的优点,在0.4㎜渗层以下,渗速比气体氮化快的多,而且表面不会有脆性相,可以局部氮化,缺点是成本略高,对形状复杂或带长孔的工件效果不好。
变形方面应该是辉光离子氮化变形最小,实际中相差很小,很多时候几乎一样。
软氮化实质上是以渗氮为主的低温氮碳共渗,钢的氮原子渗入的同时,还有少量的碳原子渗入,其处理结果与一般气体氮化相比,渗层硬度较氮化低,脆性较小,故称为软氮化。
1、软氮化方法分为:气体软氮化、液体软氮化及固体软氮化三大类。
目前国内生产中应用最广泛的是气体软氮化。
气体软氮化是在含有活性氮、碳原子的气氛中进行低温氮、碳共渗,常用的共渗介质有尿素、甲酰胺、氨气和三乙醇胺,它们在软氮化温度下发生热分解反应,产生活性氮、碳原子。
- 1、下载文档前请自行甄别文档内容的完整性,平台不提供额外的编辑、内容补充、找答案等附加服务。
- 2、"仅部分预览"的文档,不可在线预览部分如存在完整性等问题,可反馈申请退款(可完整预览的文档不适用该条件!)。
- 3、如文档侵犯您的权益,请联系客服反馈,我们会尽快为您处理(人工客服工作时间:9:00-18:30)。
一.离子氮化工艺
离子氮化是一种可以显著提高钢铁零件表面硬度﹑耐磨损﹑耐疲劳和耐腐蚀性能的化学热处理工艺。
将欲处理零件置于真空炉体内,在真空条件下,往炉内充以稀薄的含氮气体(如氨气或氮氢混合气体)。
零件接离子电源阴极,炉体接阳极,阴阳极接数百伏直流电压。
由于电场作用,炉内稀薄气体被电离,氮离子定向撞击阴极(零件),零件表面产生辉光放电并被加热。
在一定气氛和一定温度下,零件表面复合、吸收氮原子,形成高浓度的含氮层并向心部扩散,经过一段时间,得到工艺要求所需要的氮化层。
离子氮化工艺由于其节能﹑省气﹑效率高﹑质量好﹑无污染等优点,在动力﹑机床﹑石化机械﹑轻纺机械﹑摸具等行业中得到了广泛应用。
二.离子氮化设备
设备主要用于机械零件的离子氮化、离子氮碳共渗(软氮化)等离子化学热处理工艺,使
机械零件表面改性,获得所需要的机械性能和物理化学性能。
成套设备由离子电源﹑真空炉体﹑真空获得系统﹑测控温系统﹑供气系统组成。
2.1.离子电源
离子电源分为直流离子电源和脉冲离子电源。
2.1.1.直流离子电源
直流离子电源主要包括整流变压器﹑可控整流电路﹑L-C 振荡灭弧电路﹑截止反馈电路﹑控制电路。
2.1.2.脉冲离子电源
脉冲离子电源是在直流离子电源的基础上加装由 IGBT 元件及控制电路组成的斩波器,通过斩波得到占空比可调的脉冲电流。
脉冲离子电源与直流离子电源相比,能较好地改善空心阴极效应。
脉冲离子电源是在每个工作周内(频率为
1KHZ时,周期为1ms)电流回零,辉光熄灭一次,因而提高了灭弧效率。
脉冲离子电源能实现电压、电流的独立调节,能滿足不同的工艺要求。
脉冲离子电源与直流离子电源相比,节能在15%-20%以上。
2.2.真空炉体
设备的真空炉体分井式(零件吊挂)、罩式(零件堆放)和综合式三种。
真空炉体由炉筒和炉底盘组成。
炉筒体用钢板焊接而成,为双层结构,中间可通水冷却。
各密封面﹝槽﹞用真空橡胶密封圈密封。
炉内装有不銹钢隔热屏﹑阴极盘。
炉筒上开有观察窗。
进气接口装在炉体顶部。
炉底盘上装有阴极输电接口﹑测温接口﹑测压接口﹑抽气接口等。
阴极输电装置由阴极杆、密封件、绝缘垫、承重柱和气隙套组成。
阴极引线通过阴极输电装置与阴极盘相联。
真空炉体必须有良好的密封,以保证工艺对真空度的要求。
根据加工零件尺寸和生产能力的要求,真空炉体必须有足够的工作容积。
2.3.真空获得系统
真空获得系统由旋片式机械真空泵﹑真空
电磁阀﹑真空蝶阀组成,通过真空管道与真空炉体连接。
电阻式真空计用于测量真空炉体真空度。
2.4.测控温系统
测控温系统由热电偶﹑控温电路和控温仪表组成。
由热电偶得到温度毫伏信号,通过控温仪表PID调节和相关电路,精确控制工件温度。
2.5.供气系统
供气系统由氨气瓶、氨气减压器、转子流量计和输气管道组成。
设备配有两只流量计,一只用于氨气流量调节,一只用于渗碳气流量调节,两种气体经过流量计后混合通入炉内,通过调节流量比例可实现氮碳共渗工艺(软氮化)。
三. 离子氮化设备主要技术参数和技术指标
3.1直流离子电源主要参数:
直流输出电压: 0-1000V可调
直流电源最大输出电流:
灭弧方式:LC振荡灭弧和截止灭弧
3.2脉冲电源最大输出电流:
脉冲电源最大输出电流:
占空比(脉冲电源): 0.10-0.85可调脉冲频率(脉冲电源): 1000Hz
控制方式(脉冲电源):定频调宽
输出波形(脉冲电源):矩形方波
3.3炉体部分主要指标:
炉体有效工作容积:视规格和用户要求决定
工作温度:≦650℃
最大装炉量:
极限真空度:≤6.67Pa
压升率:≤0.133Pa/min
仪表控温精度:±1℃
四.设备特点:
1.真空炉体制造增加焊接后时效工序,消除焊后应力,保证各密封面不变形,从而长久
保证真空密封要求。
2.保护截止电路特殊设计,即使阴阳极之间短路,也能自动保护,决不损坏设备和炉内零件。
3.电源的整流电路的可控硅﹑二极管和脉
冲发生电路的IGBT元件全部采用摸块,线路简单,质量可靠。
4.操作按钮互相设有保护,即使操作人员失误操作,也不会损坏设备。
5.动作控制采用固化电路,线路简单,大大提高可靠性。
6.温度控制采用自适应PID调节。
保证控温精度,减少电参数波动。
一.脉冲电源与直流电源相比有很大的改进和优点
(1)脉冲电源能较好地改善空心阴极效应,能抑制在工件小孔、窄缝等处产生的弧光放电。
因此适用于工件形状比较复杂、摆放难以保证一致的场合,也适用于离子渗碳、离子渗金属等由于高温易产生工装变形的场合。
(2)脉冲电源在每个工作周期内(典型为
1ms,其工作频率为1KHz)电流回零,辉光熄灭一次。
因此灭弧频率高,大大减少了清理打弧阶段工件的时间,提高了工作效率。
(3)脉冲电源的灭弧时间较直流电源要短很多。
直流电源通过LC振荡灭弧,灭弧时间约几毫秒,而脉冲电源通过关断IGBT灭弧,灭弧时间为几十微秒。
另外脉冲电源灭弧时弧的能量比同等功率的直流电源小一个数量级。
因此工件上不会出现弧光烧灼情况,保证了工件表面的光洁度。
(4)脉冲电源的工作电压和占空比(占空比为脉冲的有效时间与周期之比)均可独立调节。
在工作期间为了控制辉光功率和工件温度,可工作于高电压、小占空比方式,也可工作于低电压、大占空比方式。
所以辉光电压、电流可单独控制,可满足不同的工艺要求。
二.脉冲电源的组成
整流变压器B1起升压和隔离作用,其输出电压经两组三相全控桥整流成0-1000可调直流电压。
整流输出的直流电压经L1、C滤波,变成更平滑的直流电压供给后面的斩波
电路。
电压反馈电路实现工作电压的可调和确保工作过程中电压的稳定。
过压检测电路检测工作过程中出现的过电压,通过控制器实现保护。
IGBT是脉冲电源的核心元件,由其实现斩波,将连续的直流电压变成频率为1KHz、周期为1毫秒的脉冲电压,脉冲的占空比能在10%--85%变化。
过流检测和弧源检测电路检测工作过程中出现的过电流和弧源,通过控制器实现相应的保护。
温度PID 电路完成给定温度和工件实际温度的偏差运算,通过控制器调节斩波的占空比实现温度的自动控制。