离子渗氮的常见缺陷及原因
渗氮工艺
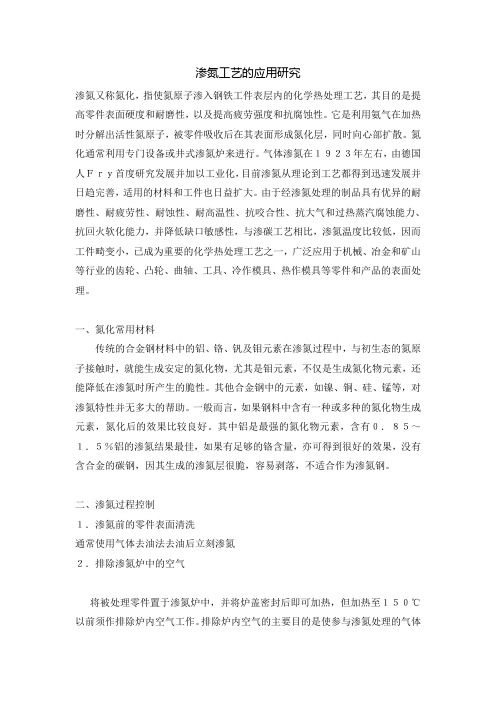
渗氮工艺的应用研究渗氮又称氮化,指使氮原子渗入钢铁工件表层内的化学热处理工艺,其目的是提高零件表面硬度和耐磨性,以及提高疲劳强度和抗腐蚀性。
它是利用氨气在加热时分解出活性氮原子,被零件吸收后在其表面形成氮化层,同时向心部扩散。
氮化通常利用专门设备或井式渗氮炉来进行。
气体渗氮在1923年左右,由德国人Fry首度研究发展并加以工业化,目前渗氮从理论到工艺都得到迅速发展并日趋完善,适用的材料和工件也日益扩大。
由于经渗氮处理的制品具有优异的耐磨性、耐疲劳性、耐蚀性、耐高温性、抗咬合性、抗大气和过热蒸汽腐蚀能力、抗回火软化能力,并降低缺口敏感性,与渗碳工艺相比,渗氮温度比较低,因而工件畸变小,已成为重要的化学热处理工艺之一,广泛应用于机械、冶金和矿山等行业的齿轮、凸轮、曲轴、工具、冷作模具、热作模具等零件和产品的表面处理。
一、氮化常用材料传统的合金钢材料中的铝、铬、钒及钼元素在渗氮过程中,与初生态的氮原子接触时,就能生成安定的氮化物,尤其是钼元素,不仅是生成氮化物元素,还能降低在渗氮时所产生的脆性。
其他合金钢中的元素,如镍、铜、硅、锰等,对渗氮特性并无多大的帮助。
一般而言,如果钢料中含有一种或多种的氮化物生成元素,氮化后的效果比较良好。
其中铝是最强的氮化物元素,含有0.85~1.5%铝的渗氮结果最佳,如果有足够的铬含量,亦可得到很好的效果,没有含合金的碳钢,因其生成的渗氮层很脆,容易剥落,不适合作为渗氮钢。
二、渗氮过程控制1.渗氮前的零件表面清洗通常使用气体去油法去油后立刻渗氮2.排除渗氮炉中的空气将被处理零件置于渗氮炉中,并将炉盖密封后即可加热,但加热至150℃以前须作排除炉内空气工作。
排除炉内空气的主要目的是使参与渗氮处理的气体只有氨气和氮气两种气体,防止氨气分解时与空气接触而发生爆炸性气体,及防止被处理零件及支架的表面氧化。
3.氨的分解率渗氮是其它合金元素与初生态的氮接触而进行(初生态氮的产生,由氨气与加热中的零件接触时零件本身成为触媒而促进氨的分解),虽然在各种分解率的氨气下,皆可渗氮,但一般都采用15~30%的分解率,并按渗氮所需厚度保持4~10小时,处理温度保持在520℃左右。
离子渗氮常见缺陷
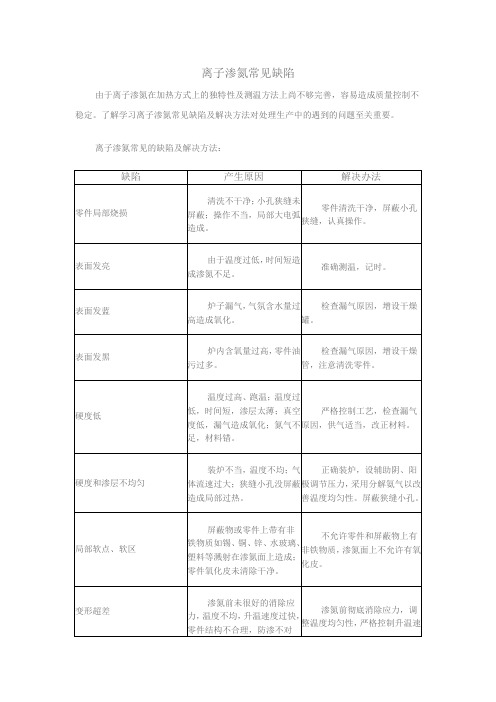
装炉不当,温度不均;气体流速过大;狭缝小孔没屏蔽造成局部过热。
正确装炉,设辅助阴、阳极调节压力,采用分解氨气以改善温度均匀性。屏蔽狭缝小孔。
局部软点、软区
屏蔽物或零件上带有非铁物质如锡、铜、锌、水玻璃、塑料等溅射在渗氮面上造成;零件氧化皮未清除干净。
不允许零件和屏蔽物上有非铁物质,渗氮面上不允许有氧化皮。
变形超差
渗氮前未很好的消除应力,温度不均,升温速度过快,零件结构不合理,防渗不对称。
渗氮前彻底消除应力,调整温度均匀性,严格控制升温速率,改进设计注意对称屏蔽。
显微组织出现网状或鱼骨状氮化物
温度过高,氮势过高。表面脱碳层未加工掉。
控制温度和氮势,零件不允许有尖角。增加预先热处理后的切削留量。
不锈钢渗不上氮,或渗层极浅,不均匀。
表面发亮
由于温度过低,时间短造成渗氮不足。
准确测温,记时。
表面发蓝
炉子漏气,气氛含水量过高造成氧化。
检查漏气原因,增设干燥罐。
表面发黑
炉内含氧量过高,零件油污过多。
检查漏气原因,增设干燥管,注意清洗零件。
硬度低
温度过高、跑温;温度过低,时间短,渗层太薄;真空度低,漏气造成氧化;氮气不足,材料错。
严格控制工艺,检查漏气原因,供气适当,改正材料。
炉内含氧量过高,造成氧化;氮势过低、温度过低。
检查漏气,增设干燥管;适当提高气氛或延长渗氮时间,提高渗氮温度,增设铁质附加阴极。
离子渗氮常见缺陷
由于离子渗氮在加热方式上的独特性及测温方法上尚不够完善,容易造成质量控制不稳定。了解学习离子渗氮常见缺陷及解决方法对处理生产中的遇到的问题至关重要。源自离子渗氮常见的缺陷及解决方法:
缺陷
产生原因
离子渗氮过高
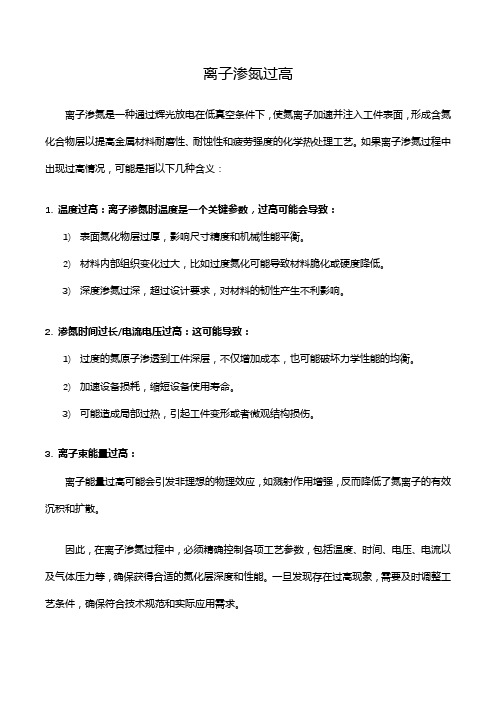
离子渗氮过高
离子渗氮是一种通过辉光放电在低真空条件下,使氮离子加速并注入工件表面,形成含氮化合物层以提高金属材料耐磨性、耐蚀性和疲劳强度的化学热处理工艺。
如果离子渗氮过程中出现过高情况,可能是指以下几种含义:
1. 温度过高:离子渗氮时温度是一个关键参数,过高可能会导致:
1)表面氮化物层过厚,影响尺寸精度和机械性能平衡。
2)材料内部组织变化过大,比如过度氮化可能导致材料脆化或硬度降低。
3)深度渗氮过深,超过设计要求,对材料的韧性产生不利影响。
2. 渗氮时间过长/电流电压过高:这可能导致:
1)过度的氮原子渗透到工件深层,不仅增加成本,也可能破坏力学性能的均衡。
2)加速设备损耗,缩短设备使用寿命。
3)可能造成局部过热,引起工件变形或者微观结构损伤。
3. 离子束能量过高:
离子能量过高可能会引发非理想的物理效应,如溅射作用增强,反而降低了氮离子的有效沉积和扩散。
因此,在离子渗氮过程中,必须精确控制各项工艺参数,包括温度、时间、电压、电流以及气体压力等,确保获得合适的氮化层深度和性能。
一旦发现存在过高现象,需要及时调整工艺条件,确保符合技术规范和实际应用需求。
离子氮化
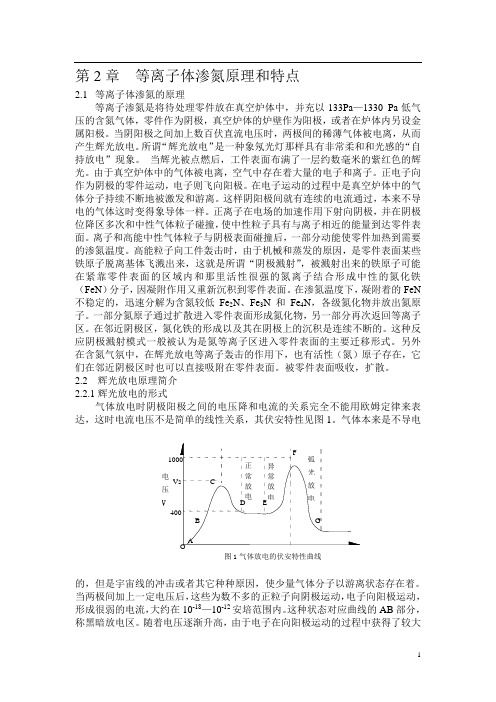
第2章 等离子体渗氮原理和特点2.1 等离子体渗氮的原理等离子渗氮是将待处理零件放在真空炉体中,并充以133Pa —1330 Pa 低气压的含氮气体,零件作为阴极,真空炉体的炉壁作为阳极,或者在炉体内另设金属阳极。
当阴阳极之间加上数百伏直流电压时,两极间的稀薄气体被电离,从而产生辉光放电。
所谓“辉光放电”是一种象氖光灯那样具有非常柔和和光感的“自持放电”现象。
当辉光被点燃后,工件表面布满了一层约数毫米的紫红色的辉光。
由于真空炉体中的气体被电离,空气中存在着大量的电子和离子。
正电子向作为阴极的零件运动,电子则飞向阳极。
在电子运动的过程中是真空炉体中的气体分子持续不断地被激发和游离。
这样阴阳极间就有连续的电流通过,本来不导电的气体这时变得象导体一样。
正离子在电场的加速作用下射向阴极,并在阴极位降区多次和中性气体粒子碰撞,使中性粒子具有与离子相近的能量到达零件表面。
离子和高能中性气体粒子与阴极表面碰撞后,一部分动能使零件加热到需要的渗氮温度。
高能粒子向工件轰击时,由于机械和蒸发的原因,是零件表面某些铁原子脱离基体飞溅出来,这就是所谓“阴极溅射”,被溅射出来的铁原子可能在紧靠零件表面的区域内和那里活性很强的氮离子结合形成中性的氮化铁(FeN )分子,因凝附作用又重新沉积到零件表面。
在渗氮温度下,凝附着的FeN不稳定的,迅速分解为含氮较低Fe 2N 、Fe 3N 和 Fe 4N ,各级氮化物并放出氮原子。
一部分氮原子通过扩散进入零件表面形成氮化物,另一部分再次返回等离子区。
在邻近阴极区,氮化铁的形成以及其在阴极上的沉积是连续不断的。
这种反应阴极溅射模式一般被认为是氮等离子区进入零件表面的主要迁移形式。
另外在含氮气氛中,在辉光放电等离子轰击的作用下,也有活性(氮)原子存在,它们在邻近阴极区时也可以直接吸附在零件表面。
被零件表面吸收,扩散。
2.2 辉光放电原理简介2.2.1辉光放电的形式气体放电时阴极阳极之间的电压降和电流的关系完全不能用欧姆定律来表达,这时电流电压不是简单的线性关系,其伏安特性见图1。
不锈钢表面离子渗氮技术
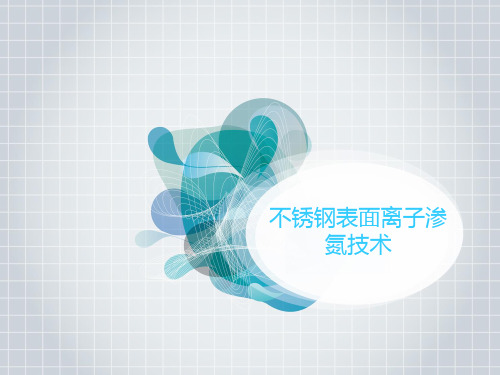
•
渗氮后的不锈钢硬度和耐磨性均有显著提高。但是常规的离子渗氮容易 在不锈钢表面形成CrN而使基体出现贫铬,进而降低不锈钢的耐蚀性。所以, 尽管经离子渗氮处理后不锈钢的表面硬度、耐磨性和抗擦伤、抗胶合能力有 大幅度提高,但若处理不当,容易发生表层剥落、硬化层(渗氮层) 厚度不均 匀以及耐腐蚀性大幅下降等质量问题。
不锈钢表面离子渗 氮技术
•
Hale Waihona Puke 不锈钢应用范围十分广泛。面对当前资源严重短缺的现状,采用各种强 化措施来改善已开发不锈钢钢种的性能,进一步发挥各种不锈钢的优势,拓 展其应用范围,是一项迫切而意义深远的工作。表面改性处理是低成本而有 效提高材料表面硬度、耐磨性和抗疲劳性能的重要方法。
•
由于不锈钢表面氧化膜的存在,使一般的气体渗氮很难进行。虽然表面 活化处理后的不锈钢可以进行气体渗氮处理,但是工序复杂,不易控制,所 以人们逐渐采用了一些新的渗氮工艺技术。离子渗氮技术就是其中应用最广 的一种。常规离子渗氮是在 500~560℃温度下的N2和H2或NH3混合气氛中 进行的。由于离子渗氮能直接去除不锈钢表面的钝化膜,并易于实现局部渗 氮和较容易控制氮势,在不锈钢表面强化方面显示出较大优越性。对一些马 氏体不锈钢进行离子渗氮的结果表明,离子渗氮可有效地在不锈钢表面形成 一定厚度的渗氮层,而不需要进行去除氧化膜的预处理。
•
与渗氮相似,对不锈钢进行渗碳处理也可分为气体渗碳和离子渗碳两大 类型。传统气体渗碳温度很高,一般在800~1000℃,所以对不锈钢很少使 用,主要采用低温离子渗碳技术。低温离子渗碳处理通常在550℃以下进行, 所用气体为H2和CH4或C2H2的混合气体。/
•
为了避免高温下形成CrN,损害不锈钢固有的耐蚀性,必须发展低温处 理方法。上世纪80年代研发了等离子体低温渗氮研究,很好地解决了奥氏体 不锈钢经处理后耐蚀性降低的技术难题。该技术的关键是在低温下(350~ 450℃) 进行,以避免形成CrN而使基体贫铬后耐蚀性下降。
离子氮化质量探讨
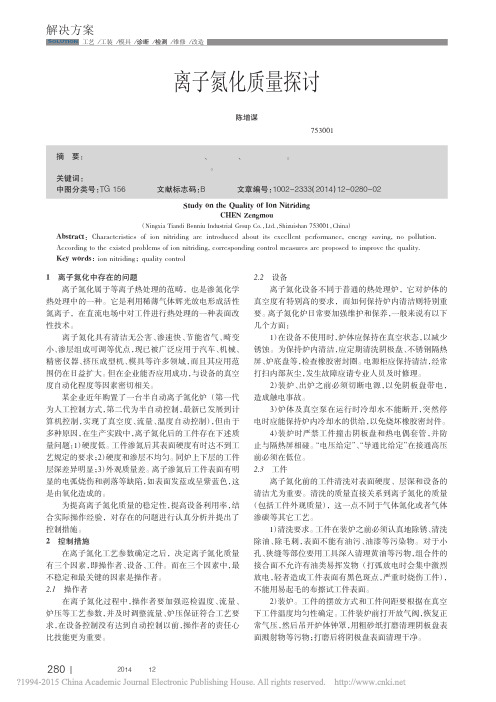
作者简介: 陈增谋, 男, 工程师, 主要从事金属材料普通热处理及化学 热处理渗碳、 渗氮表面处理工艺研究、 应用等。 收稿日期: 2014-07-30
Abstract: Characteristics of ion nitriding are introduced about its excellent performance, energy saving, no pollution. According to the existed problems of ion nitriding, corresponding control measures are proposed to improve the quality. Key words : ion nitriding ; quality control
机械工程师
2014 年第 12 期
281
与测量方式的组合进行分类, 分析了组成环对封闭环的贡献度, 得到了公差传递系数 。 平面尺寸链; 约束方式; 测量方式; 传递系数 关键词:
中图分类号: TG 801
ZHAO Yuanqiang ,
文献标志码: B
LI Qiaoling ,
文章编号: 1002-2333 (2014 ) 12-0281-02
0
引
言
[1]
即已知封闭环, 求所有或部分组成环 [5]。极限法即是把公 ) ; 统计法即平方和开 差简单相加, 得到总成公差, 如式 (1 方法, 计算如式 (2 ) :
n
汽车车身装焊偏差来源众多 , 设计时就需对装焊尺 寸链进行计算, 大部分都是采用一维分析的方法。 在一些 特殊情况下,应当引入二维计算以使理论分析与现实情 况更为接近。 文献 [2] 、 [3] 介绍了车身外覆盖件相关尺寸 链的一维计算方法,同时也指出了一维尺寸链计算的局 限性。平面尺寸链又叫二维尺寸链, 因为其计算复杂, 角 度投影关系梳理困难,所以大多简化为一维问题进行近 似替代。本文把单个组成环从整个尺寸链条中取出单独 分析, 只要明确了单个组成环的分析处理方法, 便能把复 杂的平面尺寸链问题化整为零, 逐一解决。 1 尺寸链的概念与计算方法 尺寸链的计算按计算目的的不同分为正向计算和逆 向计算,按计算的严格程度不同可以采用极限法计算和 统计法计算 [4]。正向计算是已知各部件的公差即组成环, 计算总成件的公差即封闭环。逆向计算是在已制定好总 成件的总公差范围后, 对各组成零部件的公差进行分配, 装炉时要注意工件的放置位置, 对于空心零件应尽量 对称分布, 以保证工件的散热条件尽量相同。对于局部防 渗工件, 防渗一般采用屏蔽法, 常用螺钉、 盖板、 铁皮等作 为屏蔽物。 放上试样 (一般放在工件上, 能代表工件的实际 温度的地方 ) , 用汽油布擦一下炉底密封圈和钟罩法兰, 罩 上炉盖, 然后将放气阀旋紧, 接上炉罩上的阳极块接头。 2.4 外观质量 外观质量差的多数原因是炉子漏气真空度不好, 气 氛中含水及含氧量过多。出炉后工件表面发蓝或呈紫蓝 色, 这是氧化造成的。 3 结 语 离子氮化是一种新的热处理工艺,本文结合设备现
钢的渗碳和渗氮

钢的渗碳---就是将低碳钢在具有丰富碳的介质中加热到高温(一般为900--950C),使活性碳原子渗入钢的表面,以获得高碳的渗层组织。
随后经淬火和低温回火,使表面具有高的硬度、耐磨性及疲劳抗力,而心部仍保持足够的强度和韧性。
渗碳钢的化学成分特点 :(1)渗碳钢的含碳量一般都在0.15--0.25%范围内,对于重载的渗碳体,可以提高到0.25--0.30%,以使心部在淬火及低温回火后仍具有足够的塑性和韧性。
但含碳量不能太低,否则就不能保证一定的强度。
(2)合金元素在渗碳钢中的作用是提高淬透性,细化晶粒,强化固溶体,影响渗层中的含碳量、渗层厚度及组织。
在渗碳钢中通常加入的合金元素有锰、铬、镍、钼、钨、钒、硼等。
常用渗碳钢可以分碳素渗碳钢和合金渗碳钢两大类。
(1)碳素渗碳钢中,用得最多的是15和20钢,它们经渗碳和热处理后表面硬度可达56--62HRC。
但由于淬透性较低,只适用于心部强度要求不高、受力小、承受磨损的小型零件,如轴套、链条等。
(2)低合金渗碳钢如20Cr、20Cr2MnVB、20Mn2TiB等,其渗透性和心部强度均较碳素渗碳钢高,可用于制造一般机械中的较为重要的渗碳件,如汽车、拖拉机中的齿轮、活塞销等。
(3)中合金渗碳钢如20Cr2Ni4、18Cr2N4W、15Si3MoWV等,由于具有很高的淬透性和较高的强度及韧性,主要用以制造截面较大、承载较重、受力复杂的零件,如航空发动机的齿轮、轴等。
固体渗碳;液体渗碳;气体渗碳---渗碳温度为900--950C,表面层w(碳)为0.8--1.2%,层深为0.5--2.0mm。
渗碳后的热处理---渗碳工件实际上应看作是由一种表面与中心含量相差悬殊码复合材料。
渗碳只能改变工件表面的含碳量,而其表面以及心部的最终强化则必须经过适当的热处理才能实现。
渗碳后的工件均需进行淬火和低温回火。
淬火的目的是使在表面形成高碳马氏体或高碳马氏体和细粒状碳化物组织。
低温回火温度为150--200C 。
4Cr5MoV1Si模具钢离子渗氮层组织的影响因素
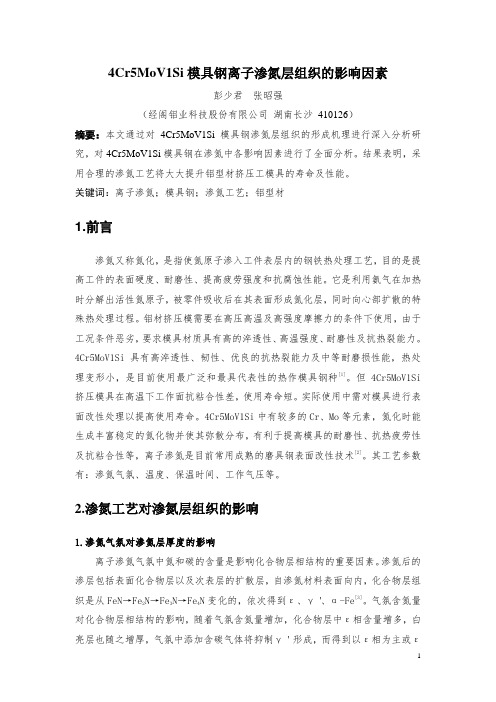
4Cr5MoV1Si模具钢离子渗氮层组织的影响因素彭少君张昭强(经阁铝业科技股份有限公司湖南长沙410126)摘要:本文通过对4Cr5MoV1Si模具钢渗氮层组织的形成机理进行深入分析研究,对4Cr5MoV1Si模具钢在渗氮中各影响因素进行了全面分析。
结果表明,采用合理的渗氮工艺将大大提升铝型材挤压工模具的寿命及性能。
关键词:离子渗氮;模具钢;渗氮工艺;铝型材1.前言渗氮又称氮化,是指使氮原子渗入工件表层内的钢铁热处理工艺,目的是提高工件的表面硬度、耐磨性、提高疲劳强度和抗腐蚀性能。
它是利用氨气在加热时分解出活性氮原子,被零件吸收后在其表面形成氮化层,同时向心部扩散的特殊热处理过程。
铝材挤压模需要在高压高温及高强度摩擦力的条件下使用,由于工况条件恶劣,要求模具材质具有高的淬透性、高温强度、耐磨性及抗热裂能力。
4Cr5MoV1Si具有高淬透性、韧性、优良的抗热裂能力及中等耐磨损性能,热处理变形小,是目前使用最广泛和最具代表性的热作模具钢种[1]。
但4Cr5MoV1Si 挤压模具在高温下工作面抗粘合性差,使用寿命短。
实际使用中需对模具进行表面改性处理以提高使用寿命。
4Cr5MoV1Si中有较多的Cr、Mo等元素,氮化时能生成丰富稳定的氮化物并使其弥散分布,有利于提高模具的耐磨性、抗热疲劳性及抗粘合性等,离子渗氮是目前常用成熟的磨具钢表面改性技术[2]。
其工艺参数有:渗氮气氛、温度、保温时间、工作气压等。
2.渗氮工艺对渗氮层组织的影响1.渗氮气氛对渗氮层厚度的影响离子渗氮气氛中氮和碳的含量是影响化合物层相结构的重要因素。
渗氮后的渗层包括表面化合物层以及次表层的扩散层,自渗氮材料表面向内,化合物层组织是从FeN→Fe2N→Fe3N→Fe4N变化的,依次得到ε、γ'、α-Fe[3]。
气氛含氮量对化合物层相结构的影响,随着气氛含氮量增加,化合物层中ε相含量增多,白亮层也随之增厚,气氛中添加含碳气体将抑制γ'形成,而得到以ε相为主或ε单相结构的化合物层。
离子氮化
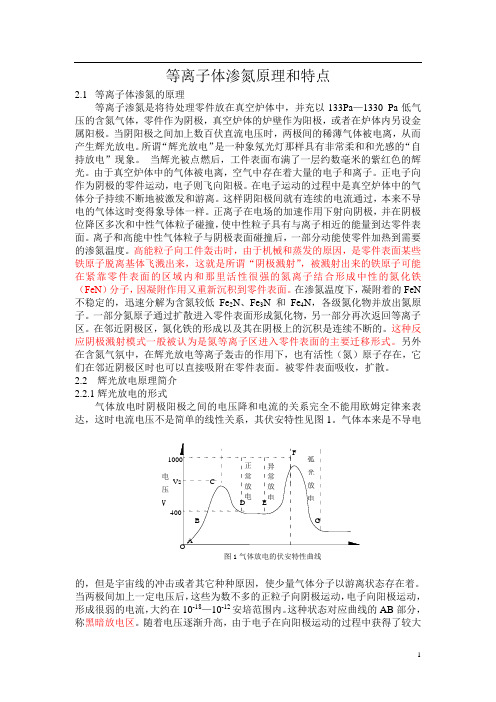
等离子体渗氮原理和特点2.1 等离子体渗氮的原理等离子渗氮是将待处理零件放在真空炉体中,并充以133Pa —1330 Pa 低气压的含氮气体,零件作为阴极,真空炉体的炉壁作为阳极,或者在炉体内另设金属阳极。
当阴阳极之间加上数百伏直流电压时,两极间的稀薄气体被电离,从而产生辉光放电。
所谓“辉光放电”是一种象氖光灯那样具有非常柔和和光感的“自持放电”现象。
当辉光被点燃后,工件表面布满了一层约数毫米的紫红色的辉光。
由于真空炉体中的气体被电离,空气中存在着大量的电子和离子。
正电子向作为阴极的零件运动,电子则飞向阳极。
在电子运动的过程中是真空炉体中的气体分子持续不断地被激发和游离。
这样阴阳极间就有连续的电流通过,本来不导电的气体这时变得象导体一样。
正离子在电场的加速作用下射向阴极,并在阴极位降区多次和中性气体粒子碰撞,使中性粒子具有与离子相近的能量到达零件表面。
离子和高能中性气体粒子与阴极表面碰撞后,一部分动能使零件加热到需要的渗氮温度。
高能粒子向工件轰击时,由于机械和蒸发的原因,是零件表面某些铁原子脱离基体飞溅出来,这就是所谓“阴极溅射”,被溅射出来的铁原子可能在紧靠零件表面的区域内和那里活性很强的氮离子结合形成中性的氮化铁(FeN )分子,因凝附作用又重新沉积到零件表面。
在渗氮温度下,凝附着的FeN不稳定的,迅速分解为含氮较低Fe 2N 、Fe 3N 和 Fe 4N ,各级氮化物并放出氮原子。
一部分氮原子通过扩散进入零件表面形成氮化物,另一部分再次返回等离子区。
在邻近阴极区,氮化铁的形成以及其在阴极上的沉积是连续不断的。
这种反应阴极溅射模式一般被认为是氮等离子区进入零件表面的主要迁移形式。
另外在含氮气氛中,在辉光放电等离子轰击的作用下,也有活性(氮)原子存在,它们在邻近阴极区时也可以直接吸附在零件表面。
被零件表面吸收,扩散。
2.2 辉光放电原理简介2.2.1辉光放电的形式气体放电时阴极阳极之间的电压降和电流的关系完全不能用欧姆定律来表达,这时电流电压不是简单的线性关系,其伏安特性见图1。
关于离子氮化
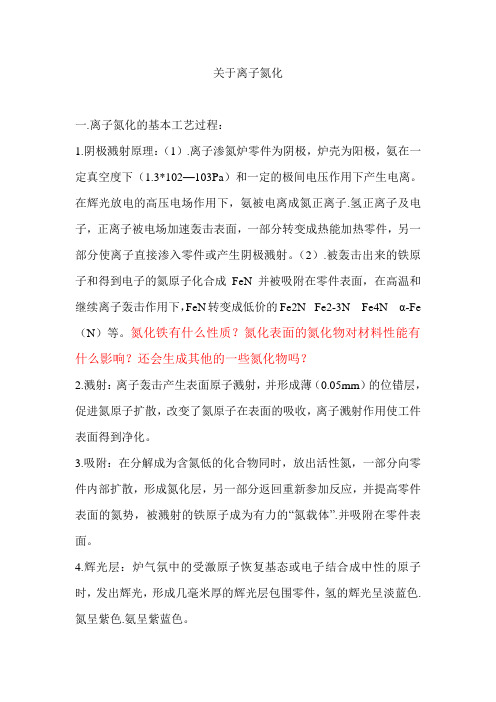
关于离子氮化一.离子氮化的基本工艺过程:1.阴极溅射原理:(1).离子渗氮炉零件为阴极,炉壳为阳极,氨在一定真空度下(1.3*102—103Pa)和一定的极间电压作用下产生电离。
在辉光放电的高压电场作用下,氨被电离成氮正离子.氢正离子及电子,正离子被电场加速轰击表面,一部分转变成热能加热零件,另一部分使离子直接渗入零件或产生阴极溅射。
(2).被轰击出来的铁原子和得到电子的氮原子化合成FeN并被吸附在零件表面,在高温和继续离子轰击作用下,FeN转变成低价的Fe2N Fe2-3N Fe4N α-Fe (N)等。
氮化铁有什么性质?氮化表面的氮化物对材料性能有什么影响?还会生成其他的一些氮化物吗?2.溅射:离子轰击产生表面原子溅射,并形成薄(0.05mm)的位错层,促进氮原子扩散,改变了氮原子在表面的吸收,离子溅射作用使工件表面得到净化。
3.吸附:在分解成为含氮低的化合物同时,放出活性氮,一部分向零件内部扩散,形成氮化层,另一部分返回重新参加反应,并提高零件表面的氮势,被溅射的铁原子成为有力的“氮载体”.并吸附在零件表面。
4.辉光层:炉气氛中的受激原子恢复基态或电子结合成中性的原子时,发出辉光,形成几毫米厚的辉光层包围零件,氢的辉光呈淡蓝色.氮呈紫色.氨呈紫蓝色。
二.离子渗氮的工艺操作及注意事项:1.同炉处理的工件应为同种或表面积和质量之比接近的工件。
工件至阳极的距离应大致相等,并大于30mm。
工件之间应有足够大的距离并要求均匀,在工件偏低位置放置辅助阴极或辅助阳极,安放试样时应考虑温度,尽量和工件一致。
2.工件上有1-4mm孔槽易引起打弧,D4-10mm的孔槽会造成温度不均匀,锈蚀工件清洗干净后方可入炉。
3.工件装炉后,密封炉盖和放气嘴,接通阴阳极导线。
预热并校正真空计,氨气热分解炉应提前升温。
4.起动真空泵使炉子逐渐达到要求的真空度,并打开气阀充入少量的热分解氨气,使炉压在1.3—13.3Pa左右。
钢的渗碳和渗氮
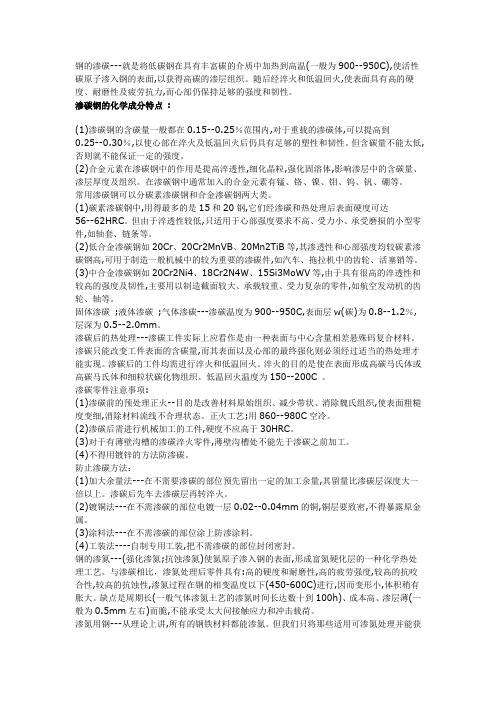
钢的渗碳---就是将低碳钢在具有丰富碳的介质中加热到高温(一般为900--950C),使活性碳原子渗入钢的表面,以获得高碳的渗层组织。
随后经淬火和低温回火,使表面具有高的硬度、耐磨性及疲劳抗力,而心部仍保持足够的强度和韧性。
渗碳钢的化学成分特点:(1)渗碳钢的含碳量一般都在0.15--0.25%范围内,对于重载的渗碳体,可以提高到0.25--0.30%,以使心部在淬火及低温回火后仍具有足够的塑性和韧性。
但含碳量不能太低,否则就不能保证一定的强度。
(2)合金元素在渗碳钢中的作用是提高淬透性,细化晶粒,强化固溶体,影响渗层中的含碳量、渗层厚度及组织。
在渗碳钢中通常加入的合金元素有锰、铬、镍、钼、钨、钒、硼等。
常用渗碳钢可以分碳素渗碳钢和合金渗碳钢两大类。
(1)碳素渗碳钢中,用得最多的是15和20钢,它们经渗碳和热处理后表面硬度可达56--62HRC。
但由于淬透性较低,只适用于心部强度要求不高、受力小、承受磨损的小型零件,如轴套、链条等。
(2)低合金渗碳钢如20Cr、20Cr2MnVB、20Mn2TiB等,其渗透性和心部强度均较碳素渗碳钢高,可用于制造一般机械中的较为重要的渗碳件,如汽车、拖拉机中的齿轮、活塞销等。
(3)中合金渗碳钢如20Cr2Ni4、18Cr2N4W、15Si3MoWV等,由于具有很高的淬透性和较高的强度及韧性,主要用以制造截面较大、承载较重、受力复杂的零件,如航空发动机的齿轮、轴等。
固体渗碳;液体渗碳;气体渗碳---渗碳温度为900--950C,表面层w(碳)为0.8--1.2%,层深为0.5--2.0mm。
渗碳后的热处理---渗碳工件实际上应看作是由一种表面与中心含量相差悬殊码复合材料。
渗碳只能改变工件表面的含碳量,而其表面以及心部的最终强化则必须经过适当的热处理才能实现。
渗碳后的工件均需进行淬火和低温回火。
淬火的目的是使在表面形成高碳马氏体或高碳马氏体和细粒状碳化物组织。
低温回火温度为150--200C 。
常用材料离子渗氮

新工艺大幅提高氮化渗层或缩短氮化工艺时间。
本企业通过长时间研究,多次实验后发现一种新的工艺方式。
在单位时间内大幅度提高渗层或缩短工艺时间上有了极大的提高。
主要使用了改变工艺和介质的两中方式。
典型材料和实验结果:注:实验过程为保证结果统一性,是按照同一标准进行实验。
本公司可根据客户技术需要调整工艺时间。
脉冲等离子体渗氮技术渗氮是在一定条件下将氮渗入金属表面从而提高金属材料表面综合机械性能的一种表面热处理方法。
它广泛用于铸铁、碳钢、合金钢、不锈钢及钛金属等材料的表面强化、提高材料表面硬度、抗疲劳强度、抗腐蚀性能和抗粘接能力。
一、常用的渗氮方法常用的渗氮方法有:固体渗氮、液体渗氮、气体渗氮、脉冲气体渗氮(气体周期改变)、直流等离子体渗氮(又称辉光离子氮化)、脉冲等离子体渗氮(电源周期供电)等。
从渗入的机理来看,主要有两大类:第一类基于浓度梯度:如固体渗氮(已很少采用)、液体渗氮、气体渗氮等,这类渗氮通常采用电炉将采用的含氮介质加热,通过含氮介质传递热能够,使被处理零件达到处理温度,以浓度梯度作为氮元素渗入的驱动力。
第二类基于电场的作用:如直流等离子体渗氮、脉冲等离子体渗氮等。
在一定的真空条件下,通过微量的含氮气体,利用辉光放电产生电子和离子,离子直接轰击零件传递热能,使被处理零件达到处理温度,通过离子、活性原子与表面的复杂作用将氮元素渗入金属表面。
近年来人们通过尝试在真空容器内周期性供气来改善渗氮结果也获得了成功。
其加热方式应归与第一类,这类方式通过气体周期性的变化,能获得更多的活性原子一定程度上改变了渗氮效果,与基于电场的作用有某种类似。
无论是基于第一类还是第二类渗氮原理,尽管氮元素与零件的表面相互作用不尽相同,但在渗入金属内部后渗层深度的增长仍然符合扩散定律。
二、各种渗氮方法优缺点比较我们把几种渗氮方法的特点比较列入下表:在等离子体渗氮工艺产生以前,主要的渗氮方式为:液体渗氮、气体渗氮。
早期的液体渗氮方式含氰化物。
离子渗氮的常见缺陷
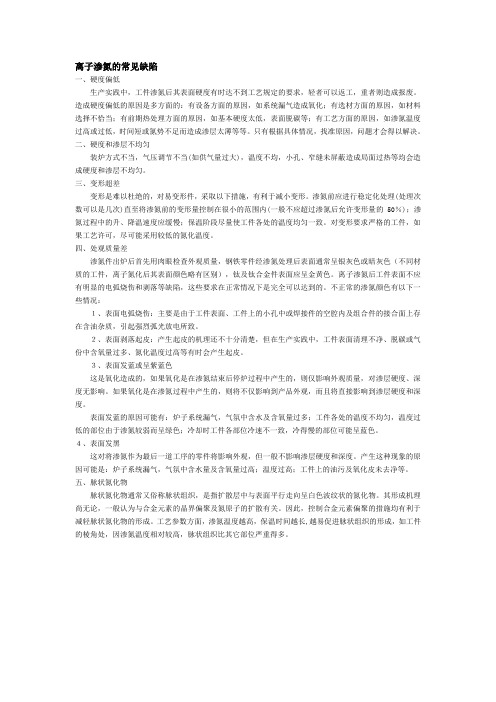
离子渗氮的常见缺陷一、硬度偏低生产实践中,工件渗氮后其表面硬度有时达不到工艺规定的要求,轻者可以返工,重者则造成报废。
造成硬度偏低的原因是多方面的:有设备方面的原因,如系统漏气造成氧化;有选材方面的原因,如材料选择不恰当;有前期热处理方面的原因,如基本硬度太低,表面脱碳等;有工艺方面的原因,如渗氮温度过高或过低,时间短或氮势不足而造成渗层太薄等等。
只有根据具体情况,找准原因,问题才会得以解决。
二、硬度和渗层不均匀装炉方式不当,气压调节不当(如供气量过大),温度不均,小孔、窄缝未屏蔽造成局面过热等均会造成硬度和渗层不均匀。
三、变形超差变形是难以杜绝的,对易变形件,采取以下措施,有利于减小变形。
渗氮前应进行稳定化处理(处理次数可以是几次)直至将渗氮前的变形量控制在很小的范围内(一般不应超过渗氮后允许变形量的50%);渗氮过程中的升、降温速度应缓慢;保温阶段尽量使工件各处的温度均匀一致。
对变形要求严格的工件,如果工艺许可,尽可能采用较低的氮化温度。
四、处观质量差渗氮件出炉后首先用肉眼检查外观质量,钢铁零件经渗氮处理后表面通常呈银灰色或暗灰色(不同材质的工件,离子氮化后其表面颜色略有区别),钛及钛合金件表面应呈金黄色。
离子渗氮后工件表面不应有明显的电弧烧伤和剥落等缺陷,这些要求在正常情况下是完全可以达到的。
不正常的渗氮颜色有以下一些情况:1、表面电弧烧伤:主要是由于工件表面、工件上的小孔中或焊接件的空腔内及组合件的接合面上存在含油杂质,引起强烈弧光放电所致。
2、表面剥落起皮:产生起皮的机理还不十分清楚,但在生产实践中,工件表面清理不净、脱碳或气份中含氧量过多、氮化温度过高等有时会产生起皮。
3、表面发蓝或呈紫蓝色这是氧化造成的,如果氧化是在渗氮结束后停炉过程中产生的,则仅影响外观质量,对渗层硬度、深度无影响。
如果氧化是在渗氮过程中产生的,则将不仅影响到产品外观,而且将直接影响到渗层硬度和深度。
表面发蓝的原因可能有:炉子系统漏气,气氛中含水及含氧量过多;工件各处的温度不均匀,温度过低的部位由于渗氮较弱而呈绿色;冷却时工件各部位冷速不一致,冷得慢的部位可能呈蓝色。
渗氮工艺常见问题
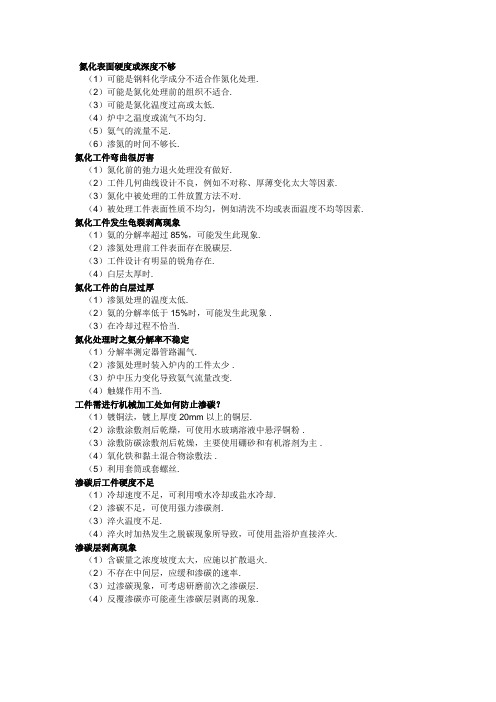
氮化表面硬度或深度不够(1)可能是钢料化学成分不适合作氮化处理.(2)可能是氮化处理前的组织不适合.(3)可能是氮化温度过高或太低.(4)炉中之温度或流气不均匀.(5)氨气的流量不足.(6)渗氮的时间不够长.氮化工件弯曲很厉害(1)氮化前的弛力退火处理没有做好.(2)工件几何曲线设计不良,例如不对称、厚薄变化太大等因素.(3)氮化中被处理的工件放置方法不对.(4)被处理工件表面性质不均匀,例如清洗不均或表面温度不均等因素. 氮化工件发生龟裂剥离现象(1)氨的分解率超过85%,可能发生此现象.(2)渗氮处理前工件表面存在脱碳层.(3)工件设计有明显的锐角存在.(4)白层太厚时.氮化工件的白层过厚(1)渗氮处理的温度太低.(2)氨的分解率低于15%时,可能发生此现象 .(3)在冷却过程不恰当.氮化处理时之氨分解率不稳定(1)分解率测定器管路漏气.(2)渗氮处理时装入炉内的工件太少 .(3)炉中压力变化导致氨气流量改变.(4)触媒作用不当.工件需进行机械加工处如何防止渗碳?(1)镀铜法,镀上厚度20mm以上的铜层.(2)涂敷涂敷剂后乾燥,可使用水玻璃溶液中悬浮铜粉 .(3)涂敷防碳涂敷剂后乾燥,主要使用硼砂和有机溶剂为主 .(4)氧化铁和黏土混合物涂敷法 .(5)利用套筒或套螺丝.渗碳后工件硬度不足(1)冷却速度不足,可利用喷水冷却或盐水冷却.(2)渗碳不足,可使用强力渗碳剂.(3)淬火温度不足.(4)淬火时加热发生之脱碳现象所导致,可使用盐浴炉直接淬火.渗碳层剥离现象(1)含碳量之浓度坡度太大,应施以扩散退火.(2)不存在中间层,应缓和渗碳的速率.(3)过渗碳现象,可考虑研磨前次之渗碳层.(4)反覆渗碳亦可能產生渗碳层剥离的现象.。
氮化工艺中的事项
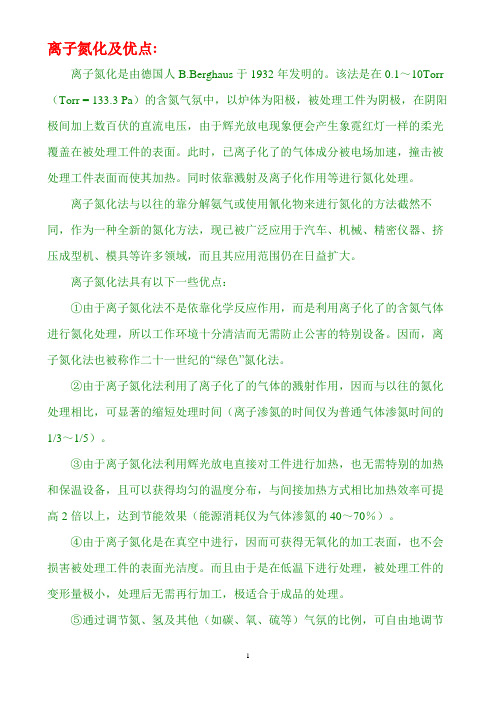
离子氮化及优点:离子氮化是由德国人B.Berghaus于1932年发明的。
该法是在0.1~10Torr (Torr = 133.3 Pa)的含氮气氛中,以炉体为阳极,被处理工件为阴极,在阴阳极间加上数百伏的直流电压,由于辉光放电现象便会产生象霓红灯一样的柔光覆盖在被处理工件的表面。
此时,已离子化了的气体成分被电场加速,撞击被处理工件表面而使其加热。
同时依靠溅射及离子化作用等进行氮化处理。
离子氮化法与以往的靠分解氨气或使用氰化物来进行氮化的方法截然不同,作为一种全新的氮化方法,现已被广泛应用于汽车、机械、精密仪器、挤压成型机、模具等许多领域,而且其应用范围仍在日益扩大。
离子氮化法具有以下一些优点:①由于离子氮化法不是依靠化学反应作用,而是利用离子化了的含氮气体进行氮化处理,所以工作环境十分清洁而无需防止公害的特别设备。
因而,离子氮化法也被称作二十一世纪的“绿色”氮化法。
②由于离子氮化法利用了离子化了的气体的溅射作用,因而与以往的氮化处理相比,可显著的缩短处理时间(离子渗氮的时间仅为普通气体渗氮时间的1/3~1/5)。
③由于离子氮化法利用辉光放电直接对工件进行加热,也无需特别的加热和保温设备,且可以获得均匀的温度分布,与间接加热方式相比加热效率可提高2倍以上,达到节能效果(能源消耗仅为气体渗氮的40~70%)。
④由于离子氮化是在真空中进行,因而可获得无氧化的加工表面,也不会损害被处理工件的表面光洁度。
而且由于是在低温下进行处理,被处理工件的变形量极小,处理后无需再行加工,极适合于成品的处理。
⑤通过调节氮、氢及其他(如碳、氧、硫等)气氛的比例,可自由地调节化合物层的相组成,从而获得预期的机械性能。
⑥离子氮化从380℃起即可进行氮化处理,此外,对钛等特殊材料也可在850℃的高温下进行氮化处理,因而适应范围十分广泛。
⑦由于离子氮化是在低气压下以离子注入的方式进行,因而耗气量极少(仅为气体渗氮的百分之几),可大大降低处离子氮化的常见缺陷:一、硬度偏低生产实践中,工件氮化后其表面硬度有时达不到工艺规定的要求,轻者可以返工,重者则造成报废。
离子渗氮常见缺陷
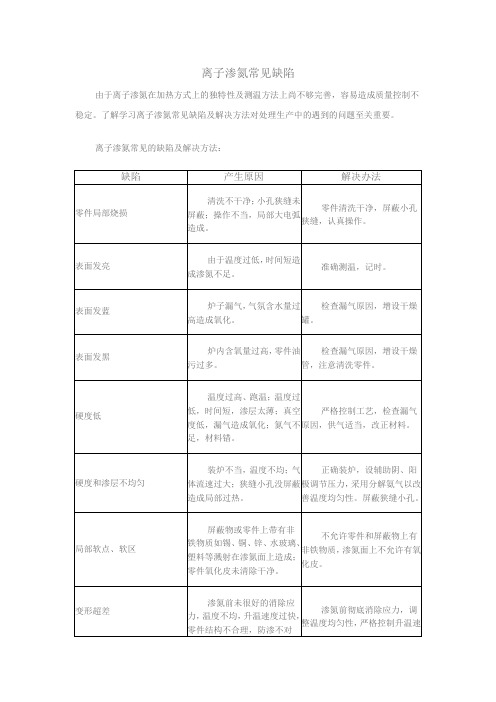
渗氮前未很好的消除应力,温度不均,升温速度过快,零件结构不合理,防渗不对称。
渗氮前彻底消除应力,调整温度均匀性,严格控制升温速率,改进设计注意对称屏蔽。
显微组织出现网状或鱼骨状氮化物
温度过高,氮势过高。表面脱碳层未加工掉。
控制温度和氮势,零件不允许有尖角。增加预先热处理后的切削留量。
不锈钢渗不上氮,或渗层极浅,不均匀。
硬度和渗层不均匀
装炉不当,温度不均;气体流速过大;狭缝小孔没屏蔽造成局部过热。
正确装炉,设辅助阴、阳极调节压力,采用分解氨气以改善温度均匀性。屏蔽狭缝小孔。
局部软点、软区
屏蔽物或零件上带有非铁物质如锡、铜、锌、水玻璃、塑料等溅射在渗氮面上造成;零件氧化皮未清除干净。
不允许零件和屏蔽物上有非铁物质,渗氮面上不允许有氧化皮。
表面发亮
由于温度过低,时间短造成渗氮不足。
准确测温,记时。
表面发蓝
炉子漏气,气氛含水量过高造成氧化。
检查漏气原因,增设干燥罐。
表面发黑
炉内含氧量过高,零件油污过多。
检查漏气原因,增设干燥管,注意清洗零件。
硬度低
温度过高、跑温;温度过低,时间短,渗层太薄;真空度低,漏气造成氧化;氮气不足,材料错。
严格控制工艺,检查漏气原因,供气适当,改正材料。
离子渗氮常见缺陷
由于离子渗氮在加热方式上的独特性及测温方法上尚不够完善,容易造成质量控制不稳定。了解学习离子渗氮常见缺陷及解决方法对处理生产中的遇到的问题至关重要。
离子渗氮常见的缺陷及解决方法:
缺陷
产生原因
解决办法
零件局部烧损
清洗不干净;小孔狭缝未屏蔽;操作不当,局部大电弧造成。
零件清洗干净化;氮势过低、温度过低。
离子渗氮的常见缺陷及原因
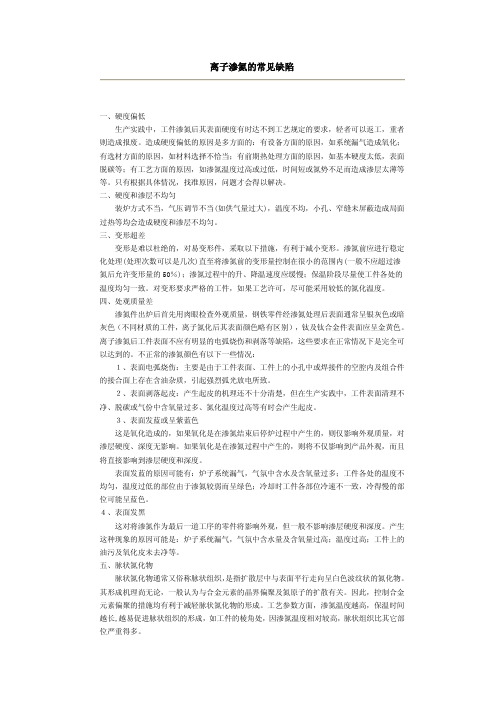
离子渗氮的常见缺陷一、硬度偏低生产实践中,工件渗氮后其表面硬度有时达不到工艺规定的要求,轻者可以返工,重者则造成报废。
造成硬度偏低的原因是多方面的:有设备方面的原因,如系统漏气造成氧化;有选材方面的原因,如材料选择不恰当;有前期热处理方面的原因,如基本硬度太低,表面脱碳等;有工艺方面的原因,如渗氮温度过高或过低,时间短或氮势不足而造成渗层太薄等等。
只有根据具体情况,找准原因,问题才会得以解决。
二、硬度和渗层不均匀装炉方式不当,气压调节不当(如供气量过大),温度不均,小孔、窄缝未屏蔽造成局面过热等均会造成硬度和渗层不均匀。
三、变形超差变形是难以杜绝的,对易变形件,采取以下措施,有利于减小变形。
渗氮前应进行稳定化处理(处理次数可以是几次)直至将渗氮前的变形量控制在很小的范围内(一般不应超过渗氮后允许变形量的50%);渗氮过程中的升、降温速度应缓慢;保温阶段尽量使工件各处的温度均匀一致。
对变形要求严格的工件,如果工艺许可,尽可能采用较低的氮化温度。
四、处观质量差渗氮件出炉后首先用肉眼检查外观质量,钢铁零件经渗氮处理后表面通常呈银灰色或暗灰色(不同材质的工件,离子氮化后其表面颜色略有区别),钛及钛合金件表面应呈金黄色。
离子渗氮后工件表面不应有明显的电弧烧伤和剥落等缺陷,这些要求在正常情况下是完全可以达到的。
不正常的渗氮颜色有以下一些情况:1、表面电弧烧伤:主要是由于工件表面、工件上的小孔中或焊接件的空腔内及组合件的接合面上存在含油杂质,引起强烈弧光放电所致。
2、表面剥落起皮:产生起皮的机理还不十分清楚,但在生产实践中,工件表面清理不净、脱碳或气份中含氧量过多、氮化温度过高等有时会产生起皮。
3、表面发蓝或呈紫蓝色这是氧化造成的,如果氧化是在渗氮结束后停炉过程中产生的,则仅影响外观质量,对渗层硬度、深度无影响。
如果氧化是在渗氮过程中产生的,则将不仅影响到产品外观,而且将直接影响到渗层硬度和深度。
表面发蓝的原因可能有:炉子系统漏气,气氛中含水及含氧量过多;工件各处的温度不均匀,温度过低的部位由于渗氮较弱而呈绿色;冷却时工件各部位冷速不一致,冷得慢的部位可能呈蓝色。
氮化工艺中的事项
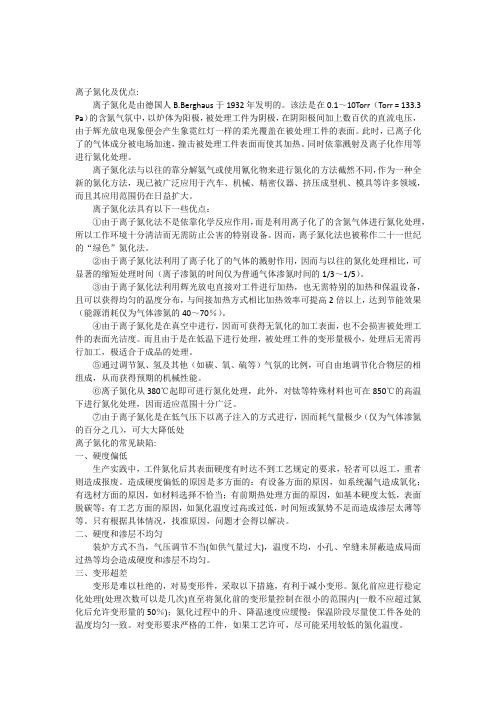
离子氮化及优点:离子氮化是由德国人B.Berghaus于1932年发明的。
该法是在0.1~10Torr(Torr = 133.3 Pa)的含氮气氛中,以炉体为阳极,被处理工件为阴极,在阴阳极间加上数百伏的直流电压,由于辉光放电现象便会产生象霓红灯一样的柔光覆盖在被处理工件的表面。
此时,已离子化了的气体成分被电场加速,撞击被处理工件表面而使其加热。
同时依靠溅射及离子化作用等进行氮化处理。
离子氮化法与以往的靠分解氨气或使用氰化物来进行氮化的方法截然不同,作为一种全新的氮化方法,现已被广泛应用于汽车、机械、精密仪器、挤压成型机、模具等许多领域,而且其应用范围仍在日益扩大。
离子氮化法具有以下一些优点:①由于离子氮化法不是依靠化学反应作用,而是利用离子化了的含氮气体进行氮化处理,所以工作环境十分清洁而无需防止公害的特别设备。
因而,离子氮化法也被称作二十一世纪的“绿色”氮化法。
②由于离子氮化法利用了离子化了的气体的溅射作用,因而与以往的氮化处理相比,可显著的缩短处理时间(离子渗氮的时间仅为普通气体渗氮时间的1/3~1/5)。
③由于离子氮化法利用辉光放电直接对工件进行加热,也无需特别的加热和保温设备,且可以获得均匀的温度分布,与间接加热方式相比加热效率可提高2倍以上,达到节能效果(能源消耗仅为气体渗氮的40~70%)。
④由于离子氮化是在真空中进行,因而可获得无氧化的加工表面,也不会损害被处理工件的表面光洁度。
而且由于是在低温下进行处理,被处理工件的变形量极小,处理后无需再行加工,极适合于成品的处理。
⑤通过调节氮、氢及其他(如碳、氧、硫等)气氛的比例,可自由地调节化合物层的相组成,从而获得预期的机械性能。
⑥离子氮化从380℃起即可进行氮化处理,此外,对钛等特殊材料也可在850℃的高温下进行氮化处理,因而适应范围十分广泛。
⑦由于离子氮化是在低气压下以离子注入的方式进行,因而耗气量极少(仅为气体渗氮的百分之几),可大大降低处离子氮化的常见缺陷:一、硬度偏低生产实践中,工件氮化后其表面硬度有时达不到工艺规定的要求,轻者可以返工,重者则造成报废。
渗氮层硬度偏低是怎么回事?

渗氮层硬度偏低是怎么回事?
离子氮化软氮化学名“氮碳共渗”。
实质是以渗氮为主的低温氮碳共渗,钢的氮原子渗入的同时,还有少量的碳原子渗入,其处理结果与一般气体氮化相比,渗层硬度较氮化低,脆性较小,故称为软氮化。
离子氮化作为一种工件表面热处理工艺手法,能提高工件的耐磨、耐疲劳、耐蚀及耐高温的特性,在生产中得到广泛应用,但是由于工艺不正确或操作不当,往往造成出现渗氮硬度低、硬度不均匀,表面有氧化色等缺陷,影响了工件的使用周期,因此分析原因、探讨方法、调整工艺,显得十分重要。
离子氮化渗氮层硬度偏低会降低工件的耐磨性能,减少工件的使用周期,分析原因我们会发现:
1)渗氮模具表层含氮量低,这是由于渗氮时炉温偏高或者在渗氮一阶段的氨分解率过高,即炉内氮气氛过低。
2)模具预先热处理后基体硬度太低。
3)渗氮炉密封不良、漏气或新的渗氮罐。
预防措施:
1)适当降低渗氮温度。
对控温仪表要经常校正,保持适当的渗氮温度。
2)工件装炉后应缓慢加热,在渗氮一阶段应适当降低氨分解率,运用渗氮气氛全因素监测系统,准确还原原始气氛中的氨裂解率、氢含量和氮势。
3)离子氮化渗氮炉要密封,对漏气的马弗罐应及时更换,新渗氮罐要进行预渗氮,通过系统全程监测,使炉内氨分解率达到平稳。
来源:武汉等离子渗氮炉有限公司。
渗氮质量缺陷及形成原因
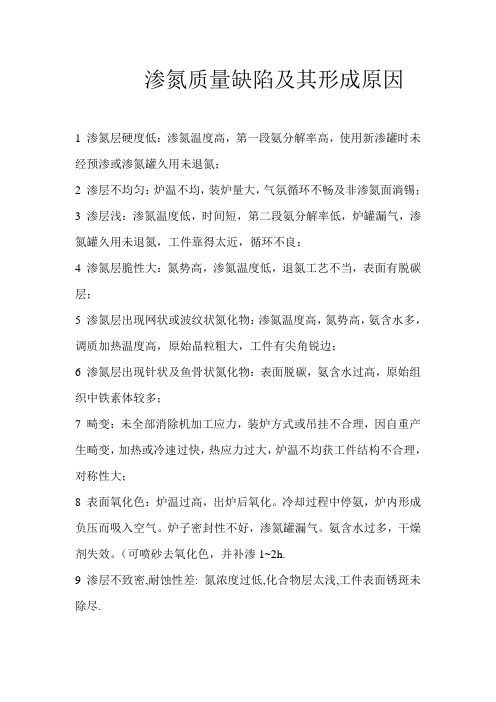
渗氮质量缺陷及其形成原因
1 渗氮层硬度低:渗氮温度高,第一段氨分解率高,使用新渗罐时未经预渗或渗氮罐久用未退氮;
2 渗层不均匀:炉温不均,装炉量大,气氛循环不畅及非渗氮面淌锡;
3 渗层浅:渗氮温度低,时间短,第二段氨分解率低,炉罐漏气,渗氮罐久用未退氮,工件靠得太近,循环不良;
4 渗氮层脆性大:氮势高,渗氮温度低,退氮工艺不当,表面有脱碳层;
5 渗氮层出现网状或波纹状氮化物:渗氮温度高,氮势高,氨含水多,调质加热温度高,原始晶粒粗大,工件有尖角锐边;
6 渗氮层出现针状及鱼骨状氮化物:表面脱碳,氨含水过高,原始组织中铁素体较多;
7 畸变:未全部消除机加工应力,装炉方式或吊挂不合理,因自重产生畸变,加热或冷速过快,热应力过大,炉温不均获工件结构不合理,对称性大;
8 表面氧化色:炉温过高,出炉后氧化。
冷却过程中停氨,炉内形成负压而吸入空气。
炉子密封性不好,渗氮罐漏气。
氨含水过多,干燥剂失效。
(可喷砂去氧化色,并补渗1~2h.
9 渗层不致密,耐蚀性差: 氮浓度过低,化合物层太浅,工件表面锈斑未除尽.。
- 1、下载文档前请自行甄别文档内容的完整性,平台不提供额外的编辑、内容补充、找答案等附加服务。
- 2、"仅部分预览"的文档,不可在线预览部分如存在完整性等问题,可反馈申请退款(可完整预览的文档不适用该条件!)。
- 3、如文档侵犯您的权益,请联系客服反馈,我们会尽快为您处理(人工客服工作时间:9:00-18:30)。
离子渗氮的常见缺陷
一、硬度偏低
生产实践中,工件渗氮后其表面硬度有时达不到工艺规定的要求,轻者可以返工,重者则造成报废。
造成硬度偏低的原因是多方面的:有设备方面的原因,如系统漏气造成氧化;有选材方面的原因,如材料选择不恰当;有前期热处理方面的原因,如基本硬度太低,表面脱碳等;有工艺方面的原因,如渗氮温度过高或过低,时间短或氮势不足而造成渗层太薄等等。
只有根据具体情况,找准原因,问题才会得以解决。
二、硬度和渗层不均匀
装炉方式不当,气压调节不当(如供气量过大),温度不均,小孔、窄缝未屏蔽造成局面过热等均会造成硬度和渗层不均匀。
三、变形超差
变形是难以杜绝的,对易变形件,采取以下措施,有利于减小变形。
渗氮前应进行稳定化处理(处理次数可以是几次)直至将渗氮前的变形量控制在很小的范围内(一般不应超过渗氮后允许变形量的50%);渗氮过程中的升、降温速度应缓慢;保温阶段尽量使工件各处的温度均匀一致。
对变形要求严格的工件,如果工艺许可,尽可能采用较低的氮化温度。
四、处观质量差
渗氮件出炉后首先用肉眼检查外观质量,钢铁零件经渗氮处理后表面通常呈银灰色或暗灰色(不同材质的工件,离子氮化后其表面颜色略有区别),钛及钛合金件表面应呈金黄色。
离子渗氮后工件表面不应有明显的电弧烧伤和剥落等缺陷,这些要求在正常情况下是完全可以达到的。
不正常的渗氮颜色有以下一些情况:
1、表面电弧烧伤:主要是由于工件表面、工件上的小孔中或焊接件的空腔内及组合件的接合面上存在含油杂质,引起强烈弧光放电所致。
2、表面剥落起皮:产生起皮的机理还不十分清楚,但在生产实践中,工件表面清理不净、脱碳或气份中含氧量过多、氮化温度过高等有时会产生起皮。
3、表面发蓝或呈紫蓝色
这是氧化造成的,如果氧化是在渗氮结束后停炉过程中产生的,则仅影响外观质量,对渗层硬度、深度无影响。
如果氧化是在渗氮过程中产生的,则将不仅影响到产品外观,而且将直接影响到渗层硬度和深度。
表面发蓝的原因可能有:炉子系统漏气,气氛中含水及含氧量过多;工件各处的温度不均匀,温度过低的部位由于渗氮较弱而呈绿色;冷却时工件各部位冷速不一致,冷得慢的部位可能呈蓝色。
4、表面发黑
这对将渗氮作为最后一道工序的零件将影响外观,但一般不影响渗层硬度和深度。
产生这种现象的原因可能是:炉子系统漏气,气氛中含水量及含氧量过高;温度过高;工件上的油污及氧化皮未去净等。
五、脉状氮化物
脉状氮化物通常又俗称脉状组织,是指扩散层中与表面平行走向呈白色波纹状的氮化物。
其形成机理尚无论,一般认为与合金元素的晶界偏聚及氮原子的扩散有关。
因此,控制合金元素偏聚的措施均有利于减轻脉状氮化物的形成。
工艺参数方面,渗氮温度越高,保温时间越长,越易促进脉状组织的形成,如工件的棱角处,因渗氮温度相对较高,脉状组织比其它部位严重得多。
离子渗氮后零件的“肿胀”现象及防治对策
攻关项目 2006年3月15日
一、“肿胀”的本质
离子渗氮后零件的“肿胀”实际上是零件尺寸变化的一种表现形式。
尺寸变化是由于渗氮时工件表面吸收了大量的氮原子,生成各种氮化物或工件表层原始组织的晶格常数增大所致,宏观上则表现为表层体积的略微增加。
渗氮后零件的“肿胀”是一种普遍现象。
各种氮化方法(气体氮化、液体氮化和离子氮化)处理后的零件或多或少总会存在一定的“肿胀”。
但应该说明的是:离子渗氮后零件的“肿胀量”较其它氮化方法要小。
这是因为:离子渗氮中的“阴极溅射”有使尺寸缩小的作用,因而抵消了一部分渗氮“肿胀量”。
二、影响“肿胀”的因素
渗氮后尺寸的胀大量取决于零件表层的吸氮量。
因而,影响吸氮量的因素均是影响“肿胀”的因素。
影响“肿胀”的因素主要有:材料中合金元素的含量、渗氮温度、渗氮时间、渗氮气氛中的氮势等。
材料中合金元素含量越高,零件氮化后的“肿胀”越大。
渗氮温度愈高、渗氮时间愈长,零件氮化后的“肿胀”愈大。
渗氮气氛的氮势越高,零件氮化后的“肿胀”愈大。
三、“肿胀”的防治办法
前以述及,“肿胀”是氮化过程中一种必然的现象,因此要彻底杜绝“肿胀”是不现实的。
我们此处所说的“防治”主要有两种含义:一是尽可能减小“肿胀”量;二是在“肿胀”不可避免的情况下,掌握“肿胀”规律,省去氮化后的再次加工。
1、减小“肿胀”的方法
①根据工件的服役条件,正确选用材料。
避免因追求工件性能而盲目使用“好”材料(高合金钢)的现象。
②根据工件的服役条件,提出合理的氮化要求,避免片面追求氮化层深度和硬度的现象。
③正确做好氮化前的预先热处理工作和“稳定化”处理,预先热处理工艺参数的制定必须正确,操作必须合理。
对形状复杂的零件,在最终精加工前必须进行一次或几次“稳定化”处理。
④在工艺允许的前提下,适当降低氮化温度,缩短渗氮时间。
⑤在保证渗氮层性能的前提下,调整渗氮气氛。
⑥合理装炉,确保同炉工件温度的均匀性。
2、“肿胀”规律,省去氮化后的再次加工
一般说来,在选材、工艺制定正确的前提下,如能合理装炉,正确操作,则工件的“肿胀”是有一定规律的。
掌握了“肿胀”的规律后,即可在氮化处理前的最后一道加工工序中根据“肿胀”量使工件尺寸处于负偏差,工件经氮化处理后尺寸可正好处于要求的尺寸公差范围内,因而可省去氮化后的再次加工。