散热器的制作技术
电子散热器技术手册

电子散热器技术手册
引言:
电子设备的快速发展和不断升级,使得电子产品的散热问题越来越突出。
由于电子设备在工作过程中产生大量的热量,如果不能有效地散热,将会导致设备过热,从而影响设备的稳定性和寿命。
为了解决这个问题,电子散热器技术应运而生。
第一章:电子散热器的基本原理
1.1 散热的重要性
1.2 散热的基本原理
1.3 电子散热器的作用和分类
第二章:电子散热器的设计与选择
2.1 散热器的设计要点
2.2 散热器的选择原则
2.3 散热器的材料与工艺
第三章:散热器的传热机制
3.1 导热与传热的区别
3.2 传热机制的分类
3.3 散热器的传热性能评估指标
第四章:散热器设计与模拟软件
4.1 散热器设计软件概述
4.2 散热器模拟软件的原理和应用
4.3 散热器设计实例分析
第五章:电子散热器的优化与改进
5.1 散热器的优化方法
5.2 散热器的改进技术
5.3 散热器的未来发展趋势
结论:
电子散热器技术是解决电子设备散热问题的重要手段之一。
本手册详细介绍了电子散热器的基本原理、设计与选择、传热机制、设计与模拟软件以及优化与改进等方面的内容。
随着电子设备的不断发展和创新,散热器技术也在不断演进和改进。
未来,我们可以期待更高效、更可靠的散热器技术的出现,进一步满足电子设备对散热需求的提升。
片式散热器的技术规范

变压器用片式散热器的技术规范一、片式散热器的适用范围:变压器类产品采用的一种热交换器,外形结构属于金属板片式。
二、片式散热器的工作原理:变压器油箱内处于上部的热油进入片式散热器上集油管,流过散热片,再从片式散热器的下集油管流回变压器的油箱。
当热油在散热片内流动时,将热量传到空气中,达到散热的目的。
三、片式散热器的分类1、按安装方式分固定式:即PG型,不用安装法兰,片式散热器直接焊接在变压器油箱的箱壁上;可拆式:即PC型,片式散热器通过法兰连接在变压器油箱上。
2、按冷却方式分自冷式:片式散热器通过空气自然对流散发热量;风冷式:片式散热器通过风机吹风(底吹或侧吹)散发热量;强油风冷式:片式散热器通过管路泵强迫变压器油循环并利用风机吹风散发热量。
3、按散热器结构分普通式:散热片的中心距相同,如:PC3000-30/520;鹅颈式:散热片分为长片和短片•,长片和短片的中心距不同,一般短片的数量为2~4片,如:PC2200(1800)-28(2)/52004、按散热器规格分片宽:480mm、52Omm两种;中心距:lOOOmm-4000mm;散热片数量:10片~38片。
四、片式散热器的作用:油浸式电力变压器运行时,内部绕组、铁芯等部件会产生损耗,损耗转换为热量并通过变压器油的热传导和对流作用传递给油箱壁,使绕组、铁芯、油箱壁及油面温度上升。
而温升直接影响到绕组绝缘材料的寿命,因此必须把温升控制在一定的范围内,所以采用散热器散热是必须的!不同容量、不同电压等级的变压器油箱周围按其热损耗安装相应数量的片式散热器,尤其是变压器容量逐渐增大时必须选用大型散热器,以散发足够的热量。
五、片式散热器的片式散热器是为油浸式电力变压器、电抗器等配套使用的冷却装置,是遵循中华人民共和国机械行业标准《变压器用片式散热器》JB/T5347-2013设计制作而成的。
其中散热器的散热片是采用优质冷轧钢卷板,在计算机自动控制的自动流水线上加工成型。
半导体制冷手机散热器原理

半导体制冷手机散热器原理
半导体制冷技术是一种新型的散热方式,它在手机等电子设备中的应用日益广泛。
半导体制冷手机散热器能够有效地降低设备的温度,提高设备的性能和稳定性。
制冷原理
半导体制冷手机散热器的主要原理是基于热电效应。
当电流通过半导体器件时,会在两个不同材料之间产生温差,从而形成冷热两侧。
这个温差可以被有效地利用来实现制冷效果。
半导体散热器内部通常包含多个半导体材料,如硒化铋、铋锑合金等,这些材料能够产生热电效应并达到制冷效果。
散热原理
半导体制冷手机散热器在散热过程中主要通过两种方式来降低设备的温度。
一
种是通过热传导,即将设备产生的热量传导到散热器表面,利用散热器的大面积来加速散热。
另一种是通过制冷效果,即通过半导体制冷的原理将热量直接从设备内部移除。
实际应用
在手机等电子设备中,半导体制冷手机散热器广泛应用于高性能设备和游戏手
机中。
这种散热器不仅可以提高设备性能,减少性能衰减,还能有效地延长设备的使用寿命。
未来随着半导体技术的进步,半导体制冷手机散热器将在电子设备中扮演更为重要的角色。
总结一下,半导体制冷手机散热器通过利用热电效应实现制冷效果,通过热传
导和制冷效果来降低设备温度,广泛应用于高性能设备和游戏手机中,未来将在电子设备中扮演更为重要的角色。
散热器技术要求
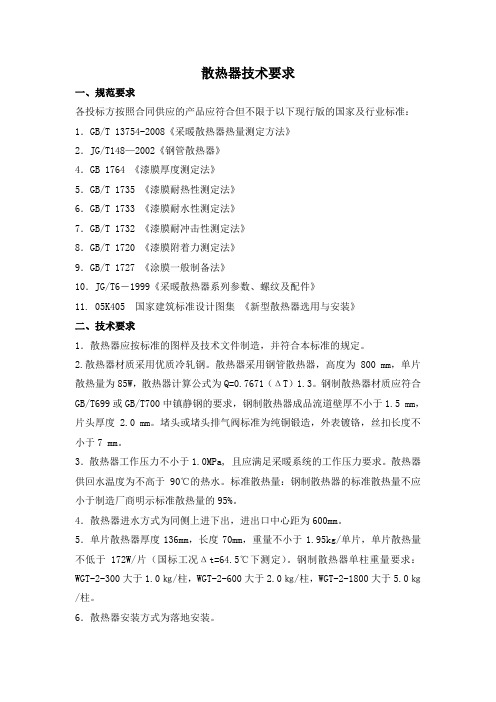
散热器技术要求一、规范要求各投标方按照合同供应的产品应符合但不限于以下现行版的国家及行业标准:1.GB/T 13754-2008《采暖散热器热量测定方法》2.JG/T148—2002《钢管散热器》4.GB 1764 《漆膜厚度测定法》5.GB/T 1735 《漆膜耐热性测定法》6.GB/T 1733 《漆膜耐水性测定法》7.GB/T 1732 《漆膜耐冲击性测定法》8.GB/T 1720 《漆膜附着力测定法》9.GB/T 1727 《涂膜一般制备法》10.JG/T6-1999《采暖散热器系列参数、螺纹及配件》11. 05K405 国家建筑标准设计图集《新型散热器选用与安装》二、技术要求1.散热器应按标准的图样及技术文件制造,并符合本标准的规定。
2.散热器材质采用优质冷轧钢。
散热器采用钢管散热器,高度为800 mm,单片散热量为85W,散热器计算公式为Q=0.7671(ΔT)1.3。
钢制散热器材质应符合GB/T699或GB/T700中镇静钢的要求,钢制散热器成品流道壁厚不小于1.5 mm,片头厚度2.0 mm。
堵头或堵头排气阀标准为纯铜锻造,外表镀铬,丝扣长度不小于7 mm。
3.散热器工作压力不小于1.0MPa, 且应满足采暖系统的工作压力要求。
散热器供回水温度为不高于90℃的热水。
标准散热量:钢制散热器的标准散热量不应小于制造厂商明示标准散热量的95%。
4.散热器进水方式为同侧上进下出,进出口中心距为600mm。
5.单片散热器厚度136mm,长度70mm,重量不小于1.95kg/单片,单片散热量不低于172W/片(国标工况Δt=64.5℃下测定)。
钢制散热器单柱重量要求:WGT-2-300大于1.0㎏/柱,WGT-2-600大于2.0㎏/柱,WGT-2-1800大于5.0㎏/柱。
6.散热器安装方式为落地安装。
7.暖气片外表面应在良好的预处理后采用静电喷塑工艺,涂层为白色,漆膜表面应光滑、平整、均匀,不得有气泡、堆积、流淌和漏喷;底漆厚度不得小于15μm,漆膜厚度不得小于60μm;漆膜附着力应达到GB/T 1720规定的1-3级要求;漆膜耐冲击性能应符合GB/T 1732的规定。
散热器铜铝结合工艺

2.常见的铜铝结合工艺扦焊扦焊是采用熔点比母材熔点低的金属材料作为焊料,在低于母材熔点而高于焊料熔点的温度下,利用液态焊料润湿母材,填充接头间隙,然后冷凝形成牢固接合界面的焊接方法。
主要工序有:材料前处理、组装、加热焊接、冷却、后处理等工序。
常用的扦焊方式是锡扦焊,铝表面在空气中会形成一层非常稳定的氧化层(AL2O3),使铜铝焊接难度较高,这是阻碍焊接的最大因素。
必须要将其去除或采用化学方法将其去除后并电镀一层镍或其它容易焊接的金属,这样铜铝才能顺利焊接在一起。
散热片上的铜底是进行热的传导,要求的不仅是机械强度,更重要的是焊接的面积要大(焊着率要高),才能有效地提升散热效能,否则不断不会提升散热效能,反而会使其比全铝合金的散热片更加糟糕。
贴片、螺丝锁合贴片工艺是将薄铜片通过螺丝与铝制底面结合,这样做的主要目的是增加散热器的瞬间吸热能力,延长一部分本身设计成熟的纯铝散热器的生命周期。
经过测试发现:在铝散热片底部与铜块之间使用高性能导热介质,施加80Kgf的力压紧后用螺丝将其锁紧,其散热效果与铜铝焊接的效果相当,同样达到了预计的散热效能提升幅度。
这种方法较焊接简单, 而且品质稳定,制程简单,投入设备成本较焊接低,不过只是作为改进,所以性能提升不明显。
虽然有散热膏填充,铜片与铝底之间的不完全接触仍然是热量传递的最大障碍。
塞铜嵌铜圣保罗散热器塞铜方式主要有两种,一种是将铜片嵌入铝制底板中,常见于用铝挤压工艺制造的散热器中。
由于铝制散热器底部的厚度有限,嵌入铜片的体积也受到限制。
增加铜片的主要目的是加强散热器的瞬间吸热能力,而且与铝制散热器的接触也很有限,所以大多数情况下,这种铜铝散热器比铝制散热器的效果好不了多少,在接触不良的情况下,甚至为妨碍散热。
还有一种是将铜柱嵌入鳍片呈放射状的铝制散热器中。
Intel原装散热器就是采用了这样的设计。
铜柱的体积较大,与散热器的接触较为充分。
采用铜柱后,散热器的热容量和瞬间吸热能力都能增长。
散热技术的技术路线
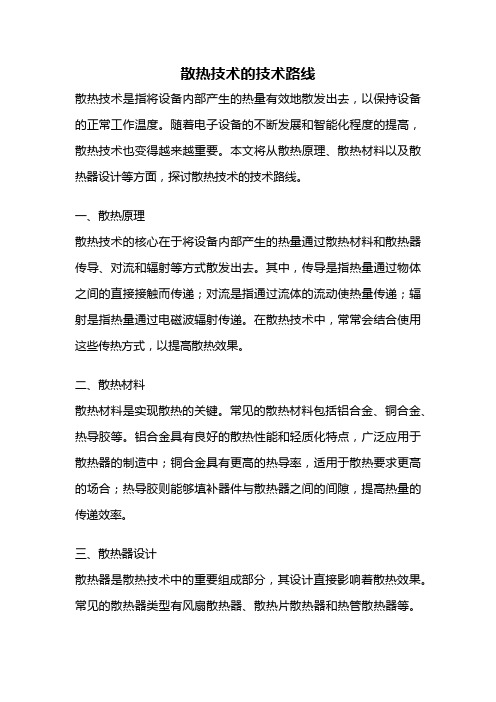
散热技术的技术路线散热技术是指将设备内部产生的热量有效地散发出去,以保持设备的正常工作温度。
随着电子设备的不断发展和智能化程度的提高,散热技术也变得越来越重要。
本文将从散热原理、散热材料以及散热器设计等方面,探讨散热技术的技术路线。
一、散热原理散热技术的核心在于将设备内部产生的热量通过散热材料和散热器传导、对流和辐射等方式散发出去。
其中,传导是指热量通过物体之间的直接接触而传递;对流是指通过流体的流动使热量传递;辐射是指热量通过电磁波辐射传递。
在散热技术中,常常会结合使用这些传热方式,以提高散热效果。
二、散热材料散热材料是实现散热的关键。
常见的散热材料包括铝合金、铜合金、热导胶等。
铝合金具有良好的散热性能和轻质化特点,广泛应用于散热器的制造中;铜合金具有更高的热导率,适用于散热要求更高的场合;热导胶则能够填补器件与散热器之间的间隙,提高热量的传递效率。
三、散热器设计散热器是散热技术中的重要组成部分,其设计直接影响着散热效果。
常见的散热器类型有风扇散热器、散热片散热器和热管散热器等。
风扇散热器通过风扇的转动产生气流,增强对流散热效果;散热片散热器利用大面积的散热片增加散热面积,提高散热效率;热管散热器则通过热管的工作原理将热量传导到散热片上,实现高效散热。
四、散热技术的发展趋势随着电子设备的不断发展和性能的提升,对散热技术的要求也越来越高。
未来的散热技术将朝着以下几个方向发展:1. 散热材料的优化:研发更高导热性能的散热材料,如石墨烯等,以提高散热效果。
2. 散热器结构的创新:设计更加紧凑、高效的散热器结构,减小设备体积的同时提高散热效率。
3. 液态散热技术的应用:利用液态冷却剂进行散热,提高散热效果,同时降低噪音和能耗。
4. 相变材料的利用:利用相变材料的相变过程吸收和释放大量热量,实现高效散热。
5. 智能化散热控制:通过传感器和控制系统实时监测设备的温度和负载情况,调整散热风扇的转速和散热器的工作状态,实现精确的散热控制。
散热器的主流成型技术

由早期的铝到现在的铜、合金,由机箱里的可以忽略的位置窜升至CPU、显卡的保护神,除了证明CPU和显卡等设备的发热量增大之外,散热器也成为了切割、成型、抛光等等跟金属加工工艺的技术体现。
时下散热器的主流成型技术多为如下几类:1.CoolerMaster主推的铝挤压技术;2.AVC主推的插齿技术;3.Thermalright,Tt等主推的回流焊接技术;4.Skiving—精密切割技术。
精密切割技术的优点是勿庸置疑的,那么它与其他散热片成型方式比较有何优势、劣势?下面我们来逐一分析:铝挤压(Extruded)技术:铝,作为地壳中含有量最高的金属,成本低是其主要特点,并且由于铝挤压技术含量及设备成本相对较低广为众用,如Foxconn,Coolermaster,九州风神等。
但随着CPU主频的不断提升,铝挤压工艺已尽显疲态,除了增大散热面积及更换大风量风扇之外别无他法。
但随之而来的是空间的受限,扣具安装难度的增加,以及大风量风扇带来的噪音。
由铝挤压技术派生出来的一种技术就是铜铝结合,常见的有扦焊、螺丝锁合、热胀冷缩结合、机械式压合等。
作为铝挤压技术的增强型工艺,铜铝结合技术虽然有效的解决了前面提到的问题,但今后的路也许不会好走。
因为铜铝结合技术的最大问题就是异种金属之间的介面热阻问题,挤压成型的铝散热片跟铜块(柱)的接触面之间的紧密及氧化等客观因素直接影响散热器的散热效果,如果工艺上不能完全符合规范,那么成品效果甚至会不如全铝结构的散热器。
此主题相关图片如下:折叶(Fold FIN)技术:是将单片的鳍片排列以特殊材料焊接在散热片底板上,由于鳍片可以达到很薄,鳍片间距也非常大,在单位面积可以使有效散热面积倍增,从而大大提高散热效果。
Fold FIN技术也很复杂,一般厂家很难保证金属折叶和底部接触紧密,如果这点做得不好,散热效果会大打折扣。
除了Foxocn n将此技术应用到早期产品PKP 020之外未见其他量产产品入市,现在也只有在某些显卡上才能见到它的身影了。
汽车散热器技术

汽车散热器技术汽车水冷发动机散热器由冷却用的散热器芯部、进水室和出水室三部分组成。
冷却液在散热器芯内流动,空气从散热器芯外高速流过,冷却液和空气通过散热器芯部进行热量交换。
目前,汽车散热器的结构形式可分为直流型和横流型两大类。
散热器芯部的结构形式主要有管片式和管带式两大类。
管片式散热器芯部是由许多细的冷却管和散热片构成,冷却管大多采用扁圆形截面,以减小空气阻力,增加传热面积。
管带式散热器是由波纹状散热带和冷却管相间排列经焊接而成。
与管片式散热器相比,管带式散热器在同样的条件下,散热面积可以增加12%左右,另外散热带上开有扰动气流的类似百叶窗的孔,以破坏流动空气在散热带表面上的附着层,提高散热能力。
开百叶窗波状带的散热器传热效率同普通平片散热片相比可提高160%。
二、散热器对材料的要求传热系数是评价散热器散热性能的重要参数,散热器材料的导热性能和焊接质量对其影响很大。
散热器的工作条件恶劣,一般位于汽车前端迎风处,不仅要经受风吹雨淋和汽车废气的污染,还要承受反复的热循环和周期性的振动。
另外,散热器内长期流动着冷却液,对散热器有锈蚀及腐蚀作用。
因此,为保证散热器可靠地发挥散热作用,对其材料性能有如下要求:必须具有良好的导热性能,具有一定的强度和较强的耐腐蚀性,具有良好的加工性能及钎焊性能,具有良好的经济性。
目前,常用的散热器材料主要有铜、铝和工程塑料等。
三、散热片的材料散热片选用导热系数较高的材料对提高热传导效率很有帮助,在金属的导热性方面,银的导热系数最高,其次是铜、铝。
银的价格昂贵,不适宜做散热材料,目前比较常用是铜、铝及铝合金。
铝的导热系数低,但通过增加鳍片增大散热面积,也能起到较好的散热效果。
散热片的主要材料和成型技术可分为:全铝散热器这是传统散热器,具有生产工艺简单、易于加工、材料成本低廉,价格便宜等优点。
缺点是,整体散热效果欠佳。
铝是汽车工业使用较多的金属材料,也是汽车轻量化的首选材料。
铝的最大优势是质量轻,比重仅为铜的三分之一,铝资源远较铜丰富,成本也远低于铜;虽然铝的热传导率较铜低,仅为铜的60%,但由于铜散热器存在热传导率更低的锡保护层,使得铝散热器的热效率反而要高于铜散热器。
电子散热器技术手册

电子散热器技术手册概述电子散热器是一种用于电子设备散热的技术装置。
随着电子设备的发展,其功率密度也逐渐增加,导致散热成为一个重要的问题。
电子散热器的作用是通过有效地导出电子设备产生的热量,维持设备的稳定运行温度。
本技术手册将介绍电子散热器的原理、分类、设计要点以及常见散热器的优缺点等内容。
原理电子散热器的原理是利用散热介质的导热特性,将电子设备产生的热量传导到散热器表面,并通过散热器表面的散热方式将热量释放到周围环境中。
常见的散热介质包括铝合金、铜、热管等。
分类根据散热介质的不同,电子散热器可以分为以下几类:1.铝合金散热器:铝合金散热器由铝材料制成,具有良好的导热性能和散热效果。
其结构简单,散热片较为密集,适用于一般功率密度较低的电子设备。
2.铜散热器:铜散热器由铜材料制成,具有较高的导热性能和散热效果。
相比于铝合金散热器,铜散热器在散热性能方面具有更好的表现,适用于功率密度较高的电子设备。
3.热管散热器:热管散热器是一种利用热管传导热量的散热装置。
热管由内部填充工质的密封管路组成,可有效地传输热能。
热管散热器具有较高的散热效果和较小的体积,适用于功率密度较高且空间受限的电子设备。
设计要点设计电子散热器时需要考虑以下几个要点:1.散热面积:散热面积是影响散热效果的重要因素。
散热器的散热面积应尽可能大,以增加热量的散发面积,提高散热效果。
2.散热片结构:散热器的散热片结构应设计合理,以增加散热器表面积,提高热量的辐射和对流散热效果。
3.散热介质选择:不同的散热介质具有不同的导热性能和散热特性。
在设计电子散热器时,需要根据设备的功率密度和散热要求选择合适的散热介质。
4.散热器布局:电子设备通常存在多个散热点,因此在设计电子散热器时需要合理布局,确保每个散热点都能够得到有效的散热。
优缺点不同类型的电子散热器具有各自的优缺点:1.铝合金散热器具有制造成本低、散热效果可靠等优点,但其散热性能相对较低。
2.铜散热器具有较高的散热性能和导热性能,但制造成本较高。
生产片式散热器设备技术性能指标的详细描述

生产片式散热器设备技术性能指标的详细描述片式散热器是一种常见的散热设备,广泛应用于各类工业和家用设备中。
其技术性能指标对于产品的整体效率和性能有着重要的影响。
本文将详细描述片式散热器的几个重要技术性能指标及其意义。
1.散热面积:散热面积是片式散热器的一个重要指标。
散热面积越大,散热能力越强。
因此,设计者常常会根据实际需要和散热条件选择不同面积的散热器。
2.热阻:热阻是衡量散热器散热性能的一个重要指标。
它表示单位面积上的温度差与单位时间内的热流的比值。
热阻越小,表示散热器的散热效率越高。
3.材料热导率:散热器的材料热导率是指材料导热的能力。
材料热导率越高,表示散热器能够快速将热量从散热面传递到散热介质,提高散热效率。
4.吸附性能:吸附是指散热器表面对流体中的气体或溶解质的吸附能力。
片式散热器的吸附性能影响其热传导特性和散热机理,因此需要设计特殊的材料或处理工艺来提高散热器的吸附性能。
5.阻力损失:阻力损失是指流体在流经散热器过程中因摩擦而产生的压力损失。
阻力损失过大会影响散热器的工作效率,因此设计者需要考虑散热器的结构和几何参数,使得阻力损失尽可能小。
6.清洁性:清洁性是散热器的一个重要指标,特别是对于长期使用的散热器来说。
如果散热器难以清洗,会导致积灰和污染,从而降低其散热效果和寿命。
因此,散热器设计中需要考虑易于清洗和维护的因素。
7.可靠性:散热器的可靠性是指其在长期使用过程中保持一定的散热性能和结构稳定性的能力。
散热器需要在各种恶劣环境和负荷条件下正常工作,因此材料的选择和制造工艺对保证散热器的可靠性非常重要。
8.成本效益:成本效益是指散热器在购买、使用和维护过程中所带来的经济效益。
一方面,散热器的造价要尽量低,另一方面,散热器的散热效果要足够好,从而在实际应用中能够达到理想的经济效益。
综上所述,片式散热器的技术性能指标包括散热面积、热阻、材料热导率、吸附性能、阻力损失、清洁性、可靠性和成本效益等。
铝型材散热器加工技术工艺和产品的创新点

铝型材散热器加工技术工艺和产品的创新点说起铝型材散热器,哎呀,真的是一个“不得不提”的存在!我们日常生活中,像家电、电脑、手机这些东西,哪一个不需要散热器呢?不过,别小看这个小小的散热器,它可不简单!这背后可藏着不少的技术活儿。
你想啊,铝型材散热器不光要做得漂亮,还得能“消耗”掉那些让设备过热的热量,不然机器就可能因为温度过高而卡死、死机,那可真是麻烦到家了。
现在的铝型材散热器在制作工艺和产品创新上,真的是有点“牛”得不行!咱得说说铝型材的材料。
铝材这个东西,轻巧不说,还散热性能好,尤其是铝型材,利用它做散热器,不仅外观帅气,还能有效提高散热效率。
所以,这铝型材的使用,简直是“天作之合”,可以说是大自然送给我们的宝贵财富了。
铝型材加工工艺一开始其实挺简单的,铝材经过挤压、拉伸成型,再经过表面处理,不管是阳极氧化,还是喷涂,都能提升它的性能和外观。
不过,这不意味着铝型材散热器的制作就完事了。
哎哟,技术的门槛可高着呢!想要把散热器做得既高效又美观,还得用上一些创新技术,才能脱颖而出。
比如,传统的散热器一般都是把热量通过表面辐射到空气中,然而,随着科技发展,简单的散热方式早就不能满足现代设备的需求了。
现在,不少铝型材散热器开始采用“多通道结构”技术,这个就有点意思了,表面通过增加通道的数量,可以加大热量的散发面积。
让散热更高效,不用担心热量堆积得像“锅底巴”的那样,机器一热就死机。
你看这技术,就像是给散热器开了“外挂”,散热性能瞬间提升,简直是“游刃有余”。
不仅如此,今天的铝型材散热器还在材质选择上做了不少文章。
以前用的都是纯铝材料,现在呢,很多厂家开始加入一些镁、铜等元素,改善铝的导热性能。
简单来说,就是让散热器不仅轻盈,还能更迅速地把热量带走。
就像是给设备装了一个“超级散热系统”,热量不见了,设备也就更稳定。
铝型材的可塑性强,能做出各种形状,这样的创新,让散热器的外形不再单调,设计师可以根据客户的需求,设计出各种各样的个性化产品。
铝质散热器技术要求
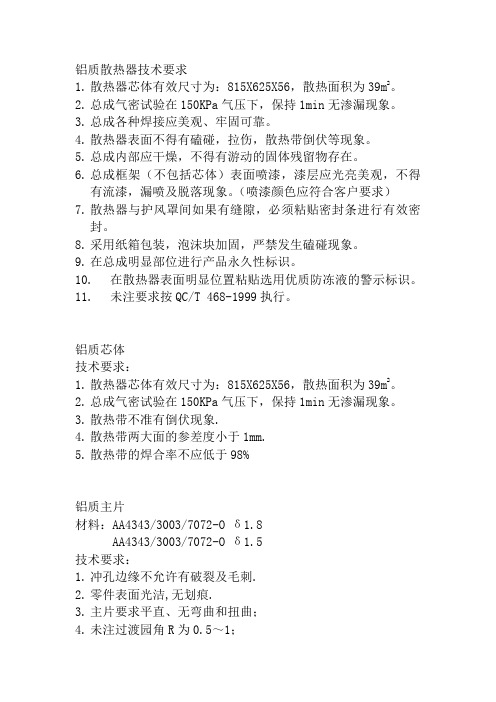
铝质散热器技术要求1.散热器芯体有效尺寸为:815X625X56,散热面积为39m2。
2.总成气密试验在150KPa气压下,保持1min无渗漏现象。
3.总成各种焊接应美观、牢固可靠。
4.散热器表面不得有磕碰,拉伤,散热带倒伏等现象。
5.总成内部应干燥,不得有游动的固体残留物存在。
6.总成框架(不包括芯体)表面喷漆,漆层应光亮美观,不得有流漆,漏喷及脱落现象。
(喷漆颜色应符合客户要求)7.散热器与护风罩间如果有缝隙,必须粘贴密封条进行有效密封。
8.采用纸箱包装,泡沫块加固,严禁发生磕碰现象。
9.在总成明显部位进行产品永久性标识。
10.在散热器表面明显位置粘贴选用优质防冻液的警示标识。
11.未注要求按QC/T 468-1999执行。
铝质芯体技术要求:1.散热器芯体有效尺寸为:815X625X56,散热面积为39m2。
2.总成气密试验在150KPa气压下,保持1min无渗漏现象。
3.散热带不准有倒伏现象.4.散热带两大面的参差度小于1mm.5.散热带的焊合率不应低于98%铝质主片材料:AA4343/3003/7072-O δ1.8AA4343/3003/7072-O δ1.5技术要求:1.冲孔边缘不允许有破裂及毛刺.2.零件表面光洁,无划痕.3.主片要求平直、无弯曲和扭曲;4.未注过渡园角R为0.5~1;5.装配前清洗;铝质散热管材料:AA4343/3003/7072-H24 δ0.30技术要求:1.散热管要求平直.2.散热管应耐不低于4.22MPa的爆破压力。
.3.散热管两端无毛刺,管口无变形.4.散热管表面无凹凸现象.5.散热管无油及污物.铝质散热带材料:AA3003+1.5%Zn-H14 δ0.08技术要求:1.散热带边缘无翘曲,破裂现象.2.百叶窗开窗均匀-致,无撕裂现象.铝质加强板材料:AA4343/3003/7072-H14 δ1.5技术要求:1.侧板应平直,不得弯曲及扭曲。
2.零件表面应光洁无毛刺。
散热器的主流成型技术

时下散热器的主流成型技术多为如下几类:一、铝挤型散热片铝挤压(Extruded)技术:铝,作为地壳中含有量最高的金属,成本低是其主要特点,并且由于铝挤压技术含量及设备成本相对较低,所以铝材质很早就应用在散热器市场。
铝挤技术简单的说就是将铝锭高温加热至约520~540℃,在高压下让铝液流经具有沟槽的挤型模具,作出散热片初胚,然再对散热片初胚进行裁剪、剖沟等处理后就做成了我们常见到的散热片。
一般常用的铝挤型材料为 AA6063,其具有良好热传导率(约160~180 W/m.K)与加工性,为最普遍应用之制程。
不过由于受到本身材质的限制散热鳍片的厚度和长度之比不能超过1:18,所以在有限的空间内很难提高散热面积,故铝挤散热片散热效果比较差,很难胜任现今日益攀升的高频率CPU。
二、铝压铸型散热片除铝挤型外,另一个常被用来制造散热片的制程方式为铝压铸型散热片。
其制程系将铝锭熔解成液态后,填充入金属模型内,利用压铸机直接压铸成型,制成散热片,采用压注法可以将鳍片做成多种立体形状,散热片可依需求作成复杂形状,亦可配合风扇及气流方向作出具有导流效果的散热片,且能做出薄且密的鳍片来增加散热面积,因工艺简单而被广泛采用。
一般常用的压铸型铝合金为ADC12,由于压铸成型性良好,适用于做薄铸件,但因热传导率较差(约 96 W/m.K),现在国内多以 AA1070 铝料来做为压铸材料,其热传导率高达 200 W/m.K 左右,具有良好的散热效果,但是以 AA1070 铝料来压铸存在着一些如下所述之问题:(1)压铸时表面流纹及氧化渣过多,会降低热传效果。
(2)冷却时内部微缩孔偏高,实质热传导率降低(K<200 W/m.K)。
(3)模具易受侵蚀,致寿命较短。
(4)成型性差,不适合薄铸件。
(5)材质较软,容易变型。
随着CPU主频的不断提升,为了达到较好的散热效果,采用压铸工艺生产的铝质散热器体积不断加大,给散热器的安装带来了很多问题,并且这种工艺制作的散热片有效散热面积有限,要想达到更好的散热效果势必提高风扇的风量,而提高风扇风量又会产生更大的噪音。
电子散热器技术手册 (2)

电子散热器技术手册
抱歉,我无法提供实时的电子散热器技术手册。
然而,如果您需要了解关于电子散热器的技术信息,我可以为您提供一些基本概念和常见的散热器类型。
1. 散热器概述:
散热器是一种用于散热的设备,通过增大散热面积和改变热量传输方式,将热量从热源转移到周围环境。
2. 散热器类型:
- 散热片:采用铝或铜等材料制成,通过增大散热面积和空气对流来散热。
- 散热风扇:结合散热片和风扇,通过强制空气对流来提高散热效果。
- 热管:采用一种特殊的液体或气体来传导热量,将热量从热源传递到散热器。
- 液冷散热器:采用水或其他液体来吸收热量,并通过热交换器将热量传递到空气中。
3. 散热器设计考虑因素:
- 散热功率:根据热源产生的功率来选择合适的散热器类型和规格。
- 散热面积:散热器的散热面积越大,散热效果越好。
- 空气流通:为散热器提供充足的空气流通,以提高散热效果。
- 材料导热系数:选择导热系数高的材料,以提高散热效率。
- 散热器布局:合理布局散热器,避免热量集中。
请注意,以上只是一些基本概念,具体散热器的设计和使用还需要根据具体应用和要求进行详细考虑。
如果您需要更专业的技术手册,请咨询相关厂商或领域专家。
热管散热器原理

热管散热器原理
热管散热器是一种利用热管技术进行散热的设备,其原理是利用热管的热传导
和相变特性,将热量从热源传导到散热器表面,再通过散热器表面的散热片将热量散发到空气中,从而达到散热的目的。
热管是一种利用液体在低温端蒸发、在高温端凝结的原理,将热量从一个地方
传导到另一个地方的热传导设备。
热管内部充满了一定量的工质,通常是一种低沸点的液体,如水、乙醇等。
当热管的一端受热时,工质在低温端蒸发,形成高压蒸汽,蒸汽压力推动蒸汽流向高温端,然后在高温端凝结成液体,释放出潜热。
这样,热量就被有效地从低温端传导到高温端。
热管散热器的工作原理是将热管与散热片相结合,形成一个整体的散热系统。
热管的一端与热源接触,通过热传导将热量传导到热管的另一端,而热管的另一端与散热片相连接,通过热传导将热量传递给散热片。
散热片的表面积较大,能够更快地将热量散发到周围的空气中,从而实现散热的效果。
热管散热器具有散热效率高、体积小、重量轻、可靠性高等优点。
由于热管本
身是一种 passively driven 的热传导元件,不需要外部能源,因此可以在各种恶劣
的环境下工作。
同时,热管散热器的结构简单,制造成本低,易于集成和安装,因此在各种电子设备和工业设备中得到了广泛的应用。
总的来说,热管散热器利用热管的热传导和相变特性,通过热传导将热量从热
源传导到散热器表面,再通过散热器表面的散热片将热量散发到空气中,从而实现散热的效果。
其优点是散热效率高、体积小、重量轻、可靠性高,适用于各种恶劣环境下的散热需求。
因此,在电子设备和工业设备中具有广泛的应用前景。
笔记本散热器的工作原理

笔记本散热器的工作原理
笔记本电脑散热器的工作原理是通过一系列技术手段来降低电脑内部温度,以保持硬件运行的稳定性并防止过热。
1. 导热原理:散热器通常由导热材料制成,如铝或铜。
它们可以有效地传导热量,将热量从电脑内部传递到散热器表面。
2. 散热片:散热器上有许多薄片状结构,称为散热片。
这些散热片增加了表面积,以提高热辐射效率,并加速热量的散发。
3. 风扇:大多数笔记本电脑散热器配备了一个或多个风扇。
风扇通过产生气流将热空气从散热器表面排出。
风扇的转速可以根据需要进行调整。
4. 热传导管:一些高端笔记本电脑散热器采用了热传导管技术。
热传导管由内部和外部两层金属组成,内层连接到散热片,外层连接到散热器。
它们通过液态冷却剂的循环,将热量从高温区域传导到低温区域。
5. 散热粘合剂:在一些笔记本电脑散热器的制造中,散热片和散热器之间使用散热粘合剂进行连接。
散热粘合剂能够填充散热片和散热器之间的空隙,提高热量的传导效率。
综上所述,笔记本电脑散热器通过导热材料、散热片、风扇、热传导管等组成的结构来将内部的热量散发到外部,以保证电脑的正常运行,并增加硬件的寿命。
汽车散热器总成技术条件

3.2.5 对于管带式结构,每条散热带实际波数与设计波数之差,允许为设计波数的±2%。计算出现小数时,应取整数。波距应均匀,以任意连续10个波距为一组测量,其实际波距数值与设计波距数值之差,应不大于设计波距的±10%。
3.耐扭振性能试验次数:2.0×106。
4.压力循环性能试验次数:7.0×104
3.4 塑料水室与塑料护风罩的性能要求
3.4.1 耐高温性能按4.8进行,外观无龟裂、破裂、表面粘附等现象,外形及尺寸无变化。
3.4.2 耐低温性能按4.9进行,外观无龟裂、破裂、表面粘附等现象,外形及尺寸无变化。
3.4.3 耐高低温交变性能按4.10进行,外观无龟裂、破裂、表面粘附等现象,外形及尺寸无变化。
3.4.4 耐冲击性性能按4.11进行,冲击强度≥200 J/m2。
3.4.5 耐振动性性能按4.4中的条件与散热器总成一起进行,外观无龟裂、破裂、表面粘附等现象,外形及尺寸无变化,同时不允许有泄漏现象。
4 试验方法
4.1密封性能试验
将散热器注满水后倒出,沥水5min,然后将所有孔口堵死,浸入常温水槽内,散热器内部通以压力为复式加水口盖出气阀开启压力1.5倍的压缩空气,保压1min。
3.3.4 经表2规定的振动次数后,不能出现裂纹、脱焊、漏水等机械损伤,耐振性能试验按4.4进行。
3.3.5 经表2规定的试验次数后,不能出现裂纹、脱焊、漏气等机械损伤,耐高温压力脉冲性能试验按4.5进行。判定是否漏气的标准是将散热器除油后按4.1进行密封性能检查。
家用燃气热水器的半导体散热技术和散热器设计

家用燃气热水器的半导体散热技术和散热器设计随着科技的不断进步,家用燃气热水器在我们的日常生活中扮演着越来越重要的角色。
为了满足用户对高效、安全和节能的要求,燃气热水器的散热技术和散热器设计变得至关重要。
本文将探讨家用燃气热水器的半导体散热技术和散热器设计,以使其更加高效和可靠。
首先,让我们来了解家用燃气热水器中的半导体散热技术。
半导体材料的散热特性通常由热导率和热阻来衡量。
在家用热水器中,使用半导体材料来优化散热是非常有效的。
半导体材料的一个关键特点是能够快速传导热量,从而将热量有效地传输到散热器上。
此外,半导体材料还具有较低的热阻,可以帮助提高散热效率。
针对于家用热水器,半导体散热技术的应用可以通过增加散热器的接触面积和改善散热材料的热导性来实现。
首先,增加散热器的接触面积可以提高热量的散发速率。
可以使用鳍片散热器来实现这一目标,鳍片散热器通过增加外表面积来提高热量的传导效率。
其次,改善散热材料的热导性也是提高半导体散热技术性能的重要方法。
选择热导率高的散热材料,如铜或铝,可以提高散热器的散热效率。
除了半导体散热技术,散热器的设计也是影响燃气热水器散热性能的关键因素。
一个好的散热器设计应该具备以下几个方面的考虑。
首先,散热器的大小和形状需要经过合理的设计。
散热器的尺寸应该能够容纳热水器内部的散热元件,并且在限定空间内提供足够的散热表面积。
当散热表面积过小时,热量无法快速散发,从而导致热水器过热。
而当散热表面积过大时,会增加成本和材料的使用量。
因此,合理的散热器大小和形状设计对于保证热水器的高效运行非常重要。
其次,散热器的材料也需要经过精心选择。
常见的散热器材料包括铝、铜和不锈钢等。
铝材料具有良好的散热性能和轻质的特点,但也存在易腐蚀和耐久性较差的问题。
铜材料则具有良好的导热性能和耐用性,但相比之下较重。
因此,根据实际情况和要求,选择合适的散热器材料非常重要。
在散热器设计中,散热风扇也扮演着重要的角色。
散热技术之热管技术简介

热管技术3、热管散热技术热管是一种具有极高导热性能的传热元件,导热能力比普通金属高几百倍。
据相关资料表明,高质量热管的传热效率是铜的1490倍,传递速度可达30m/s,远远高于世界上任何导热金属和传热技术,能到达瞬时传热的效果。
其实热管技术并不是近年才出现的新技术。
它的历史可追溯到上世纪40年代,为了满足二次世界大战的需要,美国通用发电机工程师Gaugler就提出了类似于热管的设计方案,并在1944年取得了专利。
到了1963年,第一根真正的热管被科学家George M.Grover 在美国加里佛尼亚大学的Los Alamos实验室制造出来。
笔者有幸看到了当年第一根热管的设计笔记,但由于字迹潦草,具体内容还请有兴趣的读者自己研究。
热管技术应用广泛,在航空航天、铁路交通、取暖保温中有大规模的使用。
而被引入IT硬件领域,还是上世纪90年代末,最早奔腾2笔记本电脑中出现了热管。
使用目的是为了在压缩体积的条件下取得优秀的散热效果。
随着硬件发热量的提高,现有的传统风冷散热技术已经不能满足散热需求。
于是出现了液冷、半导体制冷、压缩机制冷等散热方式,但由于安全性、稳定性与成本过高等问题无法普及应用。
所以热管这种技术成熟,成本相对较低的技术就被越来越多的台式机散热器采用。
热管的工作原理与特点热管的基本原理与空调等相变制冷类似,也可以说是一个微缩的相变制冷系统。
它是利用高导热性液体相变时吸热蒸发、放热凝结的特性,将热量快速的从吸热端转移到散热端。
从原理示意图上我们可以看出,热管内部液体由于在吸热端受热而气化(按红色箭头的走向),蒸腾到散热端放热后液化(按蓝色箭头走向),最后回流到吸热端这一个循环过程。
这个循环过程是在密闭的金属管体中进行的,不会有液体外漏的不稳定现象,而且热管体积也可控制,适合多种用途。
如果把热管剖开看,我们可以把热管分成管壳、吸液芯和蒸汽通道三个部分:管壳由于必须承受热管内部的真空高压,并且还必须更小的热阻,因此对管材的材料和制造工艺有很高的要求。
- 1、下载文档前请自行甄别文档内容的完整性,平台不提供额外的编辑、内容补充、找答案等附加服务。
- 2、"仅部分预览"的文档,不可在线预览部分如存在完整性等问题,可反馈申请退款(可完整预览的文档不适用该条件!)。
- 3、如文档侵犯您的权益,请联系客服反馈,我们会尽快为您处理(人工客服工作时间:9:00-18:30)。
图片简介:本申请提供一种散热器。
该散热器包括基板(1)和翅片,多个翅片在基板(1)上间隔设置,各翅片上分别设置有过流孔,翅片与气流的来向呈预设夹角,沿着气流的来向,翅片包括最先与气流接触的首端翅片(2)以及最后与气流接触的末端翅片(3),位于首端翅片(2)上的过流孔为首端过流孔(4),位于末端翅片(3)上的过流孔为末端过流孔(5),在首端过流孔(4)和末端过流孔(5)之间的过流孔为中间过流孔(6),中间过流孔(6)均位于首端过流孔(4)和末端过流孔(5)的中心连线上。
根据本申请的散热器,能够打破散热器的翅片表面的层流状态,改善翅片间以及翅片周围的空气流场,增强发热元器件的散热效率。
技术要求1.一种散热器,其特征在于,包括基板(1)和翅片,多个所述翅片在所述基板(1)上间隔设置,各所述翅片上分别设置有过流孔,所述翅片与气流的来向呈预设角,沿着气流的来向,所述翅片包括最先与气流接触的首端翅片(2)以及最后与气流接触的末端翅片(3),位于所述首端翅片(2)上的过流孔为首端过流孔(4),位于所述末端翅片(3)上的过流孔为末端过流孔(5),在所述首端过流孔(4)和所述末端过流孔(5)之间的过流孔为中间过流孔(6),所述中间过流孔(6)均位于所述首过流孔(4)和所述末端过流孔(5)的中心连线上。
2.根据权利要求1所述的散热器,其特征在于,所述中心连线与第一平面之间的夹角为θ1,其中第一平面为同时垂直于所述翅片的迎风面和所述基板(1)的板面的平面,Z1为首端过流孔(4)的中心与第二平面之间的距离,该第二平面为平行于第一平面经过热源区域(7)且与首端过流孔(4)的中心之间距离最小的平面,Z2为首端过流孔(4)的中心与第三平面之间的距离,该第三平面为平行于第一平面,经过热源区域(7)且与首端过流孔(4)的中心之间距离最大的平面,t为θ1的取值角度,L为首端翅片(2)的迎风侧与热源区域(7)之间的距离,D为过流孔的有效径值。
3.根据权利要求2所述的散热器,其特征在于,所有过流孔在沿着中心连线方向上的投影具有重合图形,该重合图形与中心连线之间的最小距离为D1,最大距离为D2,其中D∈[D1,D2]。
4.根据权利要求2所述的散热器,其特征在于,所有过流孔在沿着中心连线方向上的投影具有重合图形,该重合图形具有重心G,过流孔的有效径值D位于重心G与重合图形的最小距离和最大距离之间。
5.根据权利要求1至4中任一项所述的散热器,其特征在于,所述中心连线与所述基板(1)的板面之间的夹角为θ2,其中f(x)为过流孔与基板(1)远离翅片的板面之间的距离,X为散热器整体宽度,T为散热器整体高度,P为热源区域(7)发热量,W为散热器最大换热量,D为有径值,y1为首端过流孔(4)与基板(1)远离翅片的板面之间的距离,y2为首端过流孔(4)与基板(1)安装翅片的板面之间的距离,x1为热源区域(7)与首端翅片(2)在片的排布方向上的距离,x2为热源区域(7)在翅片的排布方向上的长度。
6.根据权利要求2所述的散热器,其特征在于,所述中间过流孔(6)位于梭形区域内,其中梭形区域的两个端点分别为首端过流孔(4)和末端过流孔(5)的圆心。
7.根据权利要求6所述的散热器,其特征在于,所述梭形区域由第一锥形区域和第二锥形区域拼合形成,其中第一锥形区域为以首端过流孔(4)的中心为原点,a%θ1为锥角,以中心连线为旋转轴所形成的锥形区域,第二锥形区域为以末端过流孔(5)的中心为原点,以a%θ1为锥角,以中心连线为旋转轴所形成的锥形域。
8.根据权利要求5所述的散热器,其特征在于,所述中间过流孔(6)位于梭形区域内,其中梭形区域的两个端点分别为首端过流孔(4)和末端过流孔(5)的圆心,所述梭形区域由第一锥形区域和第二锥形区域拼合形成,其中第一锥形区域为以首端过流孔(4)的中心为原点,以b%θ2为锥角,以中心连线为旋转轴所形成的锥形区域,第二锥形区域为以末端过流孔(5)的中心为原点,以b%θ2为锥角,以中心连线为旋转轴所形成的锥形区域。
9.根据权利要求7所述的散热器,其特征在于,a≤40,优选地,a≤30。
10.根据权利要求2或4所述的散热器,其特征在于,所述热源区域(7)为以基板(1)热流密度为散热对象,对热流密度的数值进行等势面绘制,最低等势面热流密度与最高等势面的热流密度占比在5%~100%的区域。
技术说明书散热器技术领域本申请涉及散热技术领域,具体涉及一种散热器。
背景技术目前,由于智能化与集成化的普及,众多的电子元器件发热量较大,却又集中紧凑的安置在同一块电路板上,为了保证元器件长期可靠性,保证设备正常运行,增加散热装置是一个行之有效的方法。
目前的散热方式有:采用散热翅片对发热元器件进行散热,或者采用风扇与翅片组合的方式进行散热,但是由于翅片与发热元器件摆放位置以及风在翅片间风场的影响,导致散热器散热效率低,翅片表面处于层流状态,空气流速低,换热量不足,发热模块的温度持续高温运行,对设备使用影响很大,对于元器的可靠性也造成较大影响。
技术内容因此,本申请要解决的技术问题在于提供一种散热器,能够打破散热器的翅片表面的层流状态,改善翅片间以及翅片周围的空气流场,增强发热元器件的散效率。
为了解决上述问题,本申请提供一种散热器,包括基板和翅片,多个翅片在基板上间隔设置,各翅片上分别设置有过流孔,翅片与气流的来向呈预设夹角,着气流的来向,翅片包括最先与气流接触的首端翅片以及最后与气流接触的末端翅片,位于首端翅片上的过流孔为首端过流孔,位于末端翅片上的过流孔为端过流孔,在首端过流孔和末端过流孔之间的过流孔为中间过流孔,中间过流孔均位于首端过流孔和末端过流孔的中心连线上。
优选地,中心连线与第一平面之间的夹角为θ1,其中第一平面为同时垂直于翅片的迎风面和基板的板面的平面,Z1为首端过流孔的中心与第二平面之间的距离,该第二平面为平行于第一平面,经过热源区且与首端过流孔的中心之间距离最小的平面,Z2为首端过流孔的中心与第三平面之间的距离,该第三平面为平行于第一平面,经过热源区域且与首端过流孔中心之间距离最大的平面,t为θ1的取值角度,L为首端翅片的迎风侧与热源区域之间的距离,D为过流孔的有效径值。
优选地,所有过流孔在沿着中心连线方向上的投影具有重合图形,该重合图形与中心连线之间的最小距离为D1,最大距离为D2,其中D∈[D1,D2]。
优选地,所有过流孔在沿着中心连线方向上的投影具有重合图形,该重合图形具有重心G,过流孔的有效径值D位于重心G与重合图形的最小距离和最大距离间。
优选地,中心连线与基板的板面之间的夹角为θ2,其中f(x)为过流孔与基板远离翅片的板面之间的距离,X为散热器整体宽度,T为散热器整体高度,P为热源区域发热量,W为散热器最大换热量,D为有效径值,y1为首端过流孔与基板远离翅片的板面之间的距离,y2为首端过流孔与基板安装翅片的板面之间的距离,x1为热源区域与首端翅片在翅片的排布方向上距离,x2为热源区域在翅片的排布方向上的长度。
优选地,中间过流孔位于梭形区域内,其中梭形区域的两个端点分别为首端过流孔和末端过流孔的圆心。
优选地,梭形区域由第一锥形区域和第二锥形区域拼合形成,其中第一锥形区域为以首端过流孔的中心为原点,以a%θ1为锥角,以中心连线为旋转轴所形成锥形区域,第二锥形区域为以末端过流孔的中心为原点,以a%θ1为锥角,以中心连线为旋转轴所形成的锥形区域。
优选地,中间过流孔位于梭形区域内,其中梭形区域的两个端点分别为首端过流孔和末端过流孔的圆心,梭形区域由第一锥形区域和第二锥形区域拼合形成其中第一锥形区域为以首端过流孔的中心为原点,以b%θ2为锥角,以中心连线为旋转轴所形成的锥形区域,第二锥形区域为以末端过流孔的中心为原点,以b%θ2为锥角,以中心连线为旋转轴所形成的锥形区域。
优选地,a≤40,优选地,a≤30。
优选地,热源区域为以基板热流密度为散热对象,对热流密度的数值进行等势面绘制,最低等势面热流密度与最高等势面的热流密度占比在5%~100%的区域。
本申请提供的散热器,包括基板和翅片,多个翅片在基板上间隔设置,各翅片上分别设置有过流孔,翅片与气流的来向呈预设夹角,沿着气流的来向,翅片括最先与气流接触的首端翅片以及最后与气流接触的末端翅片,位于首端翅片上的过流孔为首端过流孔,位于末端翅片上的过流孔为末端过流孔,在首端过孔和末端过流孔之间的过流孔为中间过流孔,中间过流孔均位于首端过流孔和末端过流孔的中心连线上。
本申请改变了散热器的气流流动方式,使得气流的向并非沿着翅片的延伸方向,而是沿着过流孔的排布方向,从而使得气流在沿着过流孔流动的过程中,能够有效改变气流流动状态,从而打破散热器的翅片面的层流状态,改善翅片间以及翅片周围的空气流场,增强发热元器件的散热效率。
附图说明图1为本申请实施例的散热器在俯视图上的过流孔分布结构图;图2为本申请实施例的散热器在主视图上的过流孔分布结构图;图3为本申请实施例的散热器的过流孔设置区域范围示意图;图4为本申请实施例的散热器的过流孔有效径值确定过程图。
附图标记表示为:1、基板;2、首端翅片;3、末端翅片;4、首端过流孔;5、末端过流孔;6、中间过流孔;7、热源区域。
具体实施方式结合参见图1至图4所示,根据本申请的实施例,散热器包括基板1和翅片,多个所述翅片在所述基板1上间隔设置,各所述翅片上分别设置有过流孔,所述翅与气流的来向呈预设夹角,沿着气流的来向,所述翅片包括最先与气流接触的首端翅片2以及最后与气流接触的末端翅片3,位于所述首端翅片2上的过流孔为首端过流孔4,位于所述末端翅片3上的过流孔为末端过流孔5,在所述首端过流孔4和所述末端过流孔5之间的过流孔为中间过流孔6,所述中间过流孔6均位于所述首端过流孔4和所述末端过流孔5的中心连线OF上。
本申请改变了散热器的气流流动方式,使得气流的来向并非沿着翅片的延展方向,而是沿着过流孔的排布方向,因此,气流的主流通通道并非是相邻翅片之的间隙,而是过流孔,从而使得气流在沿着过流孔流动的过程中,能够有效改变气流流动状态,从而打破散热器的翅片表面的层流状态,改善翅片间以及翅周围的空气流场,增强发热元器件的散热效率。
在本申请中,气流在沿着过流孔进入到翅片之后,在过流孔中依次流动的过程中,会不断受到翅片的阻挡,因此,一部分气流会从过流孔流过,达到下流孔处,另一部分气流会进入该过流孔所在的翅片与下一个过流孔所在翅片之间的间隙中,然后沿着翅片间隙流动,当气流经最后一个过流孔之后,会存在种情况,一种情况是,过流孔贯穿所有的翅片,此时气流经过过流孔之后离开散热器,并带走散热器的热量;另一种情况是,过流孔穿过部分翅片,另外一分翅片上并未设置过流孔,此时气流穿过过流孔之后,会在下一个翅片位置处收到阻挡,然后沿着该翅片与上一个翅片的间隙四处流动,带走散热器的热量由于气流是从过流孔进入翅片间隙,然后沿着翅片间隙四处流动,因此与现有的气流从翅片因此而沿着气流流向另一侧的散热方式不同,本申请的气流流动过流孔处四散,气流流动路径更短,更加容易把热量带出,此外,这种气流流动由于是从过流孔向着四周流动,且是受到翅片阻挡后产生的流动,因此这种动能够打破翅片表面的层流状态,改善翅片间以及翅片周围的空气流场,增强发热元器件的散热效率。