风电球铁件球化处理工艺现状及发展的一点设想共26页文档
大断面风电球墨铸铁铸件的技术控制

作者简介: 王星 (!06%&!.5) , 男, 汉族, 湖北荆州人, 毕业于太原理 工大学材料加工工程专业,主要从事熔炼技术及新材料的研究 工作。
! 熔炼过程中存在的问题
由于大断面风电球墨铸铁铸件质量大、尺寸
!"!" # ! 现代铸铁
球 墨 铸 铁
'()*+,- .-(/
大、 壁厚, 铸造时的热容量大, 凝固缓慢, 极易造成 球化衰退与孕育衰退,从而导致铸件的组织和基 体发生变化, 特别是在铸件的心部更加严重。 如笔 者公司生产的 $%& '( 轮毂和 )%" '( 轮毂, 虽然 浇注质量分别只有 !" * 和 $$ *,但最大壁厚却达 到了 $++ ,,。 另外, 笔者公司生产的 - '( 轮毂、 . '( 轮毂和底座,其中部分铸件不仅浇注质量 达到 !!+ *, 而且最大壁厚达到 $"+ ,,。 厚壁处由于冷却速度慢必然会引起石墨球 粗大, 石墨球数减少, 使石墨球产生畸变, 形成各 种非球状石墨, 主要有蠕虫状、 爆裂状和碎块状。 同时由于凝固时溶质元素的再分配还会出现严 重的元素偏析及晶间碳化物、 反白口、 缩孔、 缩松 等一系列问题, 其结果会导致风电球墨铸铁件的 力学性能变差, 特别是伸长率及低温性能明显降 低, 从而制约大断面风电球墨铸铁的推广使用。 随着风电行业的快速发展, 对大断面球铁件 的内外质量和技术条件要求越来越高, 对铸造工 作者也提出了新的挑战和机遇。 针对大断面风电球铁稳定化生产中存在的 问题, 结合笔者公司生产大型风电球铁件的实践 经验, 现从以下几个方面对稳定生产大断面风电 球铁件的技术控制要点进行介绍。
球铁生产中的几项技术处理

球铁生产中的几项技术处理球铁生产中的几项技术处理摘要:讨论了球铁的熔炼方案和炉料选择;分析了脱硫方法与工艺;阐述了球化剂、孕育剂中元素的作用,选用原则及使用要点。
近年来,我国球铁产量增长很快,由1998年的143万吨增至2001年的近300万吨,它在铸件总产量中约占21%,高于一般国家而比工业发达国家低8~10%。
随着制造业的世界性转移,未来我国作为世界加工业工厂的地位必将加强,我国球铁的产量和品质也将会有更大的发展。
本文仅简述球铁生产中的几项技术处理。
一、熔炼方案优质球铁需由高温、低硫、洁净,且化学成分准确而少干扰元素的原铁液为保障。
高温熔炼有利于铁液的洁净化。
因此,足够高的熔炼温度和必要的出炉温度十分重要。
除了市政类铸件外,机械、动力、容器和离心铸管等类球铁件,应采用感应熔炼或冲天炉-感应炉双联。
由于焦炭价格上涨和环保方面的考虑,新建铸造厂采用感应炉熔炼的倾向十分明显。
感应炉熔炼元素烧失少,成分把握准确,过热温度容易调整。
由于电磁搅拌作用,铁液的含气量、含氧量较低,成分与温度的均匀度高,也没有冲天炉的焦炭增硫。
不过,电磁搅拌清除固体夹渣物的作用并不彻底。
因此,感应炉熔炼仍希望炉料尽量洁净。
与工频炉相比,中频炉的电效率和热效率高,熔炼时间短,用电省,占地较少,投资较低,无需开炉块(或留液),生产灵活,改变铁液牌号方便,优势明显。
随着变频器功率的大型化,原来工频炉在大容量炉子中的地位也将为中频炉所替代。
当今,中频炉的发展方向是:①提高吨功率,实现高效、快熔。
②功率连续可调,适应不同升温和保温能力的需要。
③变频。
如在熔化期用高频率,提升功率快速熔化;在后期用低频率,以加大搅拌力,促进增碳和合金成分的调整。
④双供电,即一套电源两个换炉开关,分别联系两个炉体。
在两炉间任意分配功率,实现两炉同熔,或一熔一保,确保随时能向浇注线提供铁液。
也可以在一炉熔炼的同时另一炉进行炉衬烧结。
⑤自动化管理。
如对熔化保温,炉衬预热烧结实行可编程自动化作业,对电源和炉衬状况进行诊断和故障处理等。
关于球墨铸铁球化处理工艺的探讨 高才炜
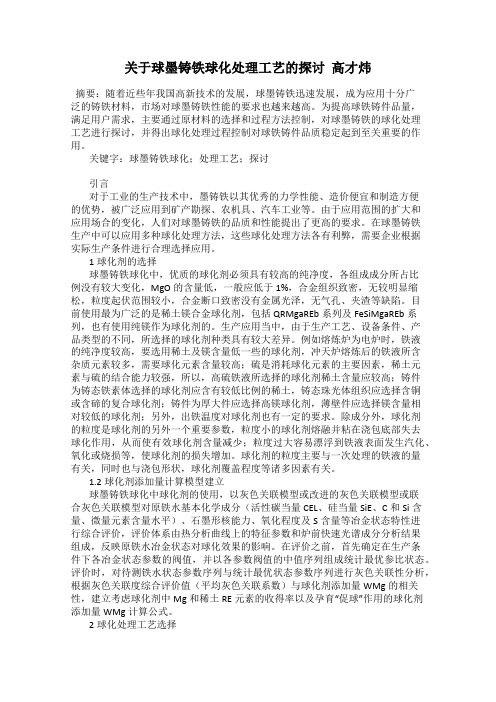
3.1原、辅材料选择
球磨铸铁对于原材料的选择过程中,熔炼高韧性球墨铸铁的主要材料是废钢(低碳钢)、增碳剂、硅铁、回炉料、球化剂、孕育剂等。原材料应无油、无锈、低锰、低硫、成分明确。
3.2熔炼操作
接下来的熔炼操作需要按比例称料,然后按顺序向中频电炉内加料,加料顺序为:回炉料→废钢→增碳剂→硅铁→回炉料→废钢。送电开始熔炼。全部炉料添加完毕,升温至1480~1500℃,增碳时间5~10min,扒渣取样进行光谱分析。若成分符合原铁液成分要求,调至1430~1470℃的工艺温度,开始出铁球化处理。若成分不满足要求,按比例调整成分,取样化验,直至满足要求为止,升温至工艺要求的球化温度出铁。
2.2冲入法
儿冲入法是在我国当前的工业技术中最广泛的球化处理方法,通常是使用堤坝式球化处理包。为了降低铁液和镁之间反应的剧烈程度以及镁蒸气的挥发速率,冲入法通常使用含镁量较低的合金球化剂。冲入法在所有球化处理方法当中具有高的应用比例,主要原因为设备成本低、处理方法简单、对操作的要求较低,不需要复杂的技术支持,生产过程比较灵活。冲入法的不足之处在于生产环境恶劣,并造成严重污染。同时球化合金的效率低,烧损严重,造成资源浪费。另外,冲入法所用的合金一般要求高硅,这会导致铁液的增硅幅度很高,甚至达到0.8%,以上两个因素结合使得铁液的精确控制无法实现。
1.2球化剂添加量计算模型建立
球墨铸铁球化中球化剂的使用,以灰色关联模型或改进的灰色关联模型或联合灰色关联模型对原铁水基本化学成分(活性碳当量CEL、硅当量SiE、C和Si含量、微量元素含量水平)、石墨形核能力、氧化程度及S含量等冶金状态特性进行综合评价,评价体系由热分析曲线上的特征参数和炉前快速光谱成分分析结果组成,反映原铁水冶金状态对球化效果的影响。在评价之前,首先确定在生产条件下各冶金状态参数的阀值,并以各参数阀值的中值序列组成统计最优参比状态。评价时,对待测铁水状态参数序列与统计最优状态参数序列进行灰色关联性分析,根据灰色关联度综合评价值(平均灰色关联系数)与球化剂添加量WMg的相关性,建立考虑球化剂中Mg和稀土RE元素的收得率以及孕育“促球”作用的球化剂添加量WMg计算公式。
我国球化剂与球化工艺的现状及发展
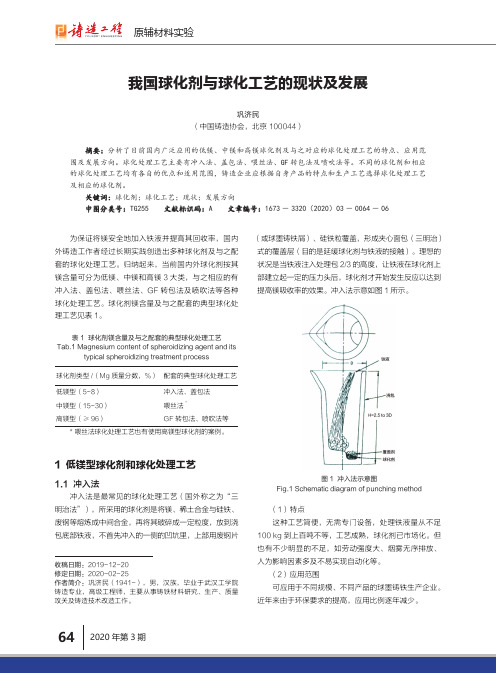
为保证将镁安全地加入铁液并提高其回收率,国内外铸造工作者经过长期实践创造出多种球化剂及与之配套的球化处理工艺。
归纳起来,当前国内外球化剂按其镁含量可分为低镁、中镁和高镁3大类,与之相应的有冲入法、盖包法、喂丝法、GF转包法及喷吹法等各种球化处理工艺。
球化剂镁含量及与之配套的典型球化处理工艺见表1。
表 1 球化剂镁含量及与之配套的典型球化处理工艺Tab.1 Magnesium content of spheroidizing agent and its typical spheroidizing treatment process球化剂类型/(Mg质量分数,%)配套的典型球化处理工艺低镁型(5~8)冲入法、盖包法中镁型(15~30)喂丝法*高镁型(≥96)GF转包法、喷吹法等* 喂丝法球化处理工艺也有使用高镁型球化剂的案例。
1 低镁型球化剂和球化处理工艺1.1 冲入法冲入法是最常见的球化处理工艺(国外称之为“三明治法”),所采用的球化剂是将镁、稀土合金与硅铁、废钢等熔炼成中间合金,再将其破碎成一定粒度,放到浇包底部铁液,不首先冲入的一侧的凹坑里,上部用废钢片(或球墨铸铁屑)、硅铁粒覆盖,形成夹心面包(三明治)式的覆盖层(目的是延缓球化剂与铁液的接触)。
理想的状况是当铁液注入处理包2/3的高度,让铁液在球化剂上部建立起一定的压力头后,球化剂才开始发生反应以达到提高镁吸收率的效果。
冲入法示意如图1所示。
图1 冲入法示意图Fig.1 Schematic diagram of punching method(1)特点这种工艺简便,无需专门设备,处理铁液量从不足100 kg到上百吨不等,工艺成熟,球化剂已市场化。
但也有不少明显的不足,如劳动强度大、烟雾无序排放、人为影响因素多及不易实现自动化等。
(2)应用范围可应用于不同规模、不同产品的球墨铸铁生产企业。
近年来由于环保要求的提高,应用比例逐年减少。
我国球化剂与球化工艺的现状及发展巩济民(中国铸造协会,北京 100044)摘要:摘要:分析了目前国内广泛应用的低镁、中镁和高镁球化剂及与之对应的球化处理工艺的特点、应用范围及发展方向。
大型风电球墨铸铁件的生产实践

球化率( %) 基体组织
60 ̄70
90 ̄95
珠光体>65% ̄75% 珠光体>30% ̄40%
③球化采用堤坝冲入法, 球化剂选用德国进 口特殊产品, 加入量为铁液量的 1.8%;
3 存在的问题及对策
④铁液冲入包内 1/2 后进行孕育处理, 加入 75FeSi 为 铁 液 量 的 0.8%, 块 度 20 ̄30 mm, 需 预 先烘烤;
32 现代铸铁 2007 / 6
( 3) 熔化工艺 ①用本溪生铁启炉; 熔清后加入废钢; 炉内 铁 液 温 度( 1 410±10) ℃, 停 电 , 扒 渣 , 取 炉 前 试 样, 检测 C、Si、Mn、P、S 含量。根据炉前分析结 果 , 调 整 炉 内 原 铁 液 成 分 , 要 求 为 : w( C) 3.8% ̄
系统和低温石墨化退火工艺, 选择合理的化学成分, 控制球化处理与孕育处理, 可生产出各项性能指标合格的风电铸
件。
关键词: 球墨铸铁; 铸造工艺; 低温石墨化退火
中图分类号: T255
文献标识码: B
文章编号: 1003- 8345( 2007) 06- 0031- 04
Pr oduction Pr actice of Heavy Nodular Ir on Castings Used for Wind Tur bine Gener ator
Gray and Nodular Irons
灰
铸
铁
及
球
回火工艺曲线见图 3; 铸态及热处理后各项性能
墨
铸
指标见表 1。图表结果基本满足了技术要求。
铁
表 1 铸态及热处理后性能对照表 Tab.1 Properties comparison between as- cast condition
球铁及其球化不良问题探讨分析

球铁及其球化不良问题探讨分析岗铁的应用使人类文明进入了铁器时代。
球墨铸铁的诞生,是继人类发明炼钢技术之后,在黑色金属应用技术方面又一次大的技术创新,是20世纪材料科学最重大的技术进展之一。
我国古代工匠早在2000年前就已制造出具有球状石墨的铸铁,分析表明上述铸铁件不含镁或稀土元素,是采用高纯木炭生铁熔剂,在金属型中浇注,经热处理后制成。
但由于这种工艺难于大量生产,因而这种古代球铁的独特技艺没有流传至今。
现代球墨铸铁采用向铁液中添加球化剂的方法使其在铸态下析出球状石墨,使得球墨铸铁真正登上了工业应用的舞台。
世界铸铁件的生产状况和趋势是,灰铸铁件的比例明显下降,但仍占优势。
球墨铸铁件的产量持续增长,蠕墨铸铁和特种铸铁也有了较大的发展。
我国球墨铸铁件在质量和生产稳定性方面的差距也较大。
我国球墨铸铁生产较突出的问题是材质强韧性上、缺陷多,其原因除炉料、球化处理方法和球化剂等因素外,主要是球化处理前对铁液含硫量要求过松。
因此,为使我国球墨铸铁生产能有大幅度的增长,必须大力实施能稳定提供质量可靠的优质球墨铸铁件的配套技术。
现在就球铁常见的缺陷球化不良结合我们单位的实际系统地进行论述一下。
球化剂的合理选用和稀土(RE)元素的加入是实现高强度薄壁球墨铸铁铸造的关键。
⑴该技术的核心是在铸造(熔炼)工艺中要保证RE/S=2~2.5。
球化剂要选用Fe-Si-Mg-RE-Ca 系材料,其中稀土元素(Ce、La、Pr)的加入并使之与硫保持一定比例是球化技术的关键。
试验证实,当RE/S<2时,出现球化不良;RE/S>2.5、Mg/S>5时,易出现白口,同时严格控Wp<0.04%、WBi=0.003%~0.007%。
灰铸铁铸件所产生的各种铸造缺陷(如缩孔、气孔、渣孔、夹砂、冷隔、浇不足等)都会在生产稀土镁球墨铸铁时产生。
球墨铸铁常见缺陷有球化不良(球铁处理不成)、球化衰退、缩松、皮下气孔等缺陷。
球化不良是稀土镁球墨铸铁经常遇到的问题之一。
球墨铸铁与球化剂的现状和发展
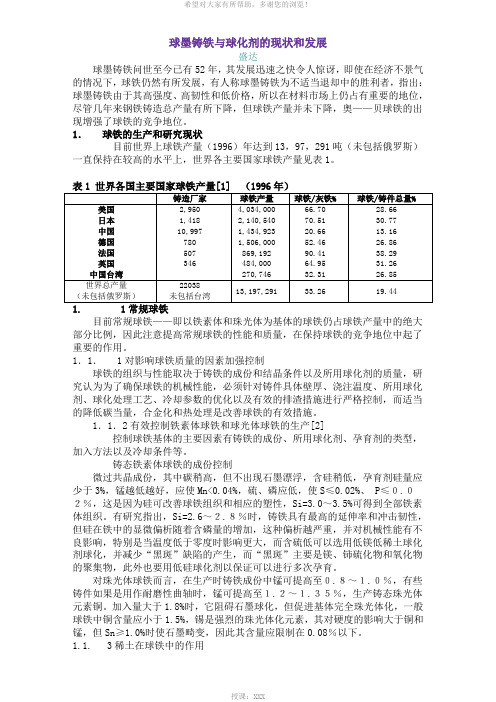
球墨铸铁与球化剂的现状和发展盛达球墨铸铁问世至今已有52年,其发展迅速之快令人惊讶,即使在经济不景气的情况下,球铁仍然有所发展,有人称球墨铸铁为不适当退却中的胜利者,指出:球墨铸铁由于其高强度、高韧性和低价格,所以在材料市场上仍占有重要的地位,尽管几年来钢铁铸造总产量有所下降,但球铁产量并未下降,奥——贝球铁的出现增强了球铁的竞争地位。
1.球铁的生产和研究现状目前世界上球铁产量(1996)年达到13,97,291吨(未包括俄罗斯)一直保持在较高的水平上,世界各主要国家球铁产量见表1。
铸造厂家球铁产量球铁/灰铁%球铁/铸件总量%美国日本中国德国法国英国中国台湾2,9501,41810,9977805073464,034,0002,140,5401,434,9231,506,000869,192484,000270,74666.7070.5120.6652.4690.4164.9532.3128.6630.7713.1626.8638.2931.2626.85世界总产量(未包括俄罗斯)22038未包括台湾13,197,29133.2619.44目前常规球铁——即以铁素体和珠光体为基体的球铁仍占球铁产量中的绝大部分比例,因此注意提高常规球铁的性能和质量,在保持球铁的竞争地位中起了重要的作用。
1.1.1对影响球铁质量的因素加强控制球铁的组织与性能取决于铸铁的成份和结晶条件以及所用球化剂的质量,研究认为为了确保球铁的机械性能,必须针对铸件具体壁厚、浇注温度、所用球化剂、球化处理工艺、冷却参数的优化以及有效的排渣措施进行严格控制,而适当的降低碳当量,合金化和热处理是改善球铁的有效措施。
1.1.2有效控制铁素体球铁和球光体球铁的生产[2]控制球铁基体的主要因素有铸铁的成份、所用球化剂、孕育剂的类型,加入方法以及冷却条件等。
铸态铁素体球铁的成份控制微过共晶成份,其中碳稍高,但不出现石墨漂浮,含硅稍低,孕育剂硅量应少于3%,锰越低越好,应使Mn<0.04%,硫、磷应低,使S≤0.02%、 P≤0.02%,这是因为硅可改善球铁组织和相应的塑性,Si=3.0~3.5%可得到全部铁素体组织。
球铁的发展及应用

球铁的发展及应用球铁的吨位增加和市场渗透是很惊人的,这种材料决不能看到达到了它的全部潜力。
基于这一点,现在不生产球铁的铸铁厂,建议很好地重新考虑这方面的可能性。
节能要求导致基本上重新设计零件,以达到重量轻、效率高,这就必然要提醒设计者集中注意材料。
球铁正日益被认为能提供高的强度一重量特性,并且能以比较低的成本生产。
铸铁管与机械制造业是球墨铸铁的两个最大的用户。
球墨铸铁在汽车、机车与车辆、农业机械、机床、冶金机械、通用机械、动力机械、纺织机械、城市工程机械及配件、铸铁管等生产中获得了广泛的应用。
目前,我厂中速机曲轴就是球墨铸铁生产。
发动机曲轴的受力情况很复杂,它承受着扭矩、弯矩和冲击等负荷,因此,对曲轴的材料提出了较高的要求。
另外,曲轴的铸造表面要求光洁、平整、不粘砂、不错箱,内部宏观组织不得有疏松、缩孔、气孔、裂纹、夹渣等缺陷存在。
球铁的铸造工艺特点1、易产生氧化皮、夹渣和皮下气孔。
球铁铁水中常存有硫化镁、氧化镁等,经球化处理后,还残留一定数量的镁或稀土元素,使铁水的物理化学性质发生一定的变化,铁水处于强烈的脱氧状态。
如果铁水在浇注系统中形成过分的紊流、飞溅,则易卷入气体,发生氧化并产生大量的二氧化物,造成夹渣。
2、铁水经球化处理后,温度降低,使铁水流动性变差,表面张力比灰铸铁高40一60%,可见浇注温度对球铁的流动性影响很大,这就要求球铁的浇注系统尺寸要比普通灰铸铁的大些。
3、球铁的体收缩较大,缩松、缩孔倾向较大。
当球铁铁水浇人铸模后,由于铸型的激冷作用,使与铸型相接触的铁水的温度迅速降至凝固点以下,形成了一层较灰铸铁薄得多的凝固层。
球铁凝固厚度的增长率,仅为灰铸铁的1/6,因此,球铁浇注后在较长一段时间内,凝固始终是在一个刚性较差、较薄的塑性固体壳内进行。
壳内的球铁铁水每析出1%的硅,就要使铁水体积增加2%以上,由于铁水中镁的阻碍石墨化作用,造成了石墨化滞后现象严重,结果是缩前膨胀比普通灰铸铁大2—5倍,所以,在壳内的铁水就会产生了凝固内压力。
风电球铁件表面“白斑”缺陷的分析与解决

风电球铁件表面“白斑”缺陷的分析与解决王美喜;刘杰;韩生泰;余帆;占进【摘要】在生产大型风电球墨铸铁件时,发现铸件表面偶有粉末状“白斑”.经过形貌和成分分析,显示其主要为硅的氧化物,针对这一问题提出以下改进措施:1)合理控制复合型醇基涂料中骨料的比例;2)加强涂料涂层的耐磨性;3)保证热风时间,增强型腔干燥度;4)控制涂料波美度,提高涂刷性能.实践证明以上措施可行,基本消除了铸件表面“白斑”缺陷.【期刊名称】《铸造设备与工艺》【年(卷),期】2018(000)003【总页数】3页(P44-46)【关键词】风电铸件;球墨铸铁;白斑;铸造涂料【作者】王美喜;刘杰;韩生泰;余帆;占进【作者单位】江苏吉鑫风能科技股份有限公司,江苏江阴214422;江苏吉鑫风能科技股份有限公司,江苏江阴214422;江苏吉鑫风能科技股份有限公司,江苏江阴214422;江苏吉鑫风能科技股份有限公司,江苏江阴214422;江苏吉鑫风能科技股份有限公司,江苏江阴214422【正文语种】中文【中图分类】TG245笔者公司采用呋喃树脂自硬砂铸造工艺,主要生产风电球墨铸铁件,产品涉及轮毂、底座、主轴、盘和轴承座等,铸件重量达2 t~80 t不等。
随着风电主机功率增加,导致铸件壁厚越来越大。
风电铸件比一般厚大球铁件要求高,其铸件表面有磁粉和无损探伤检测要求。
近期,在生产过程中发现,某些厚大壁铸件(如风电轮毂)在开箱落砂后,铸件表面粘附着一层白色粉末状物质,暂称为“白斑”。
“白斑”位于铸件和涂料壳之间,涂料壳剥落正常,剥落后“白斑”一部分留在铸件表面,一部分留在涂料壳上。
铸件经抛丸后,某些局部位置(如拐角处)仍有附着,不易脱落。
这种缺陷处于铸件表面,加大铸件清理打磨工作量,增加成本,甚至延缓交货。
这些“白斑”物质呈白色粉末状,显然不是型砂砂粒形成的。
而且,在铸件有“白斑”的位置脱落的涂料层上,也有相同情况。
经过从生产过程逐步排查,型砂、冶金铁水、人员操作等均无明显异常,考虑“白斑”产生的时间段、问题铸件涉及广等因素,分析“白斑”与处在型砂与铁水之间的涂料有关。
球铁球化处理工艺

第三节 球化处理工艺球化处理主要包括以下内容:(1)铸铁化学成分的选择;(2)球化剂的选择、加入量;(3)球化处理方法;(4)球墨铸铁的孕育处理;(5)球化效果的检验。
球墨铸铁球化处理工艺的制订应充分考虑球墨铸铁的牌号及其对组织的要求、铸件几何形状及尺寸、铸型的冷却能力、浇注时间和浇注温度、铁液中微量元素的影响以及车间生产条件等因素。
一、球墨铸铁化学成分的选择同普通灰铸铁一样,球墨铸铁化学成分主要包括碳、硅、锰、硫、磷五大常见元素。
对于一些对组织及性能有特殊要求的铸件,还包括少量的合金元素。
同普通灰铸铁不同的是,为保证石墨球化,球墨铸铁中还须含有微量的残留球化元素。
下面着重介绍这些元素在球墨铸铁中的作用及其选择原则。
1、碳及碳当量碳是球墨铸铁的基本元素,碳高有助于石墨化。
由于石墨呈球状后石墨对机械性能的影响已减小到最低程度,球墨铸铁的含碳量一般较高,在3.5~3.9%之间,碳当量在4.1~4.7%之间。
铸件壁薄、球化元素残留量大或孕育不充分时取上限;反之,取下限。
将碳当量选择在共晶点附近不仅可以改善铁液的流动性,对于球墨铸铁而言,碳当量的提高还会由于提高了铸铁凝固时的石墨化膨胀提高铁液的自补缩能力。
但是,碳含量过高,会引起石墨漂浮。
因此,球墨铸铁中碳当量的上限以不出现石墨漂浮为原则。
2、硅硅是强石墨化元素。
在球墨铸铁中,硅不仅可以有效地减小白口倾向,增加铁素体量,而且具有细化共晶团,提高石墨球圆整度的作用。
但是,硅提高铸铁的韧脆性转变温度(见图4—6),降低冲击韧性,因此硅含量不宜过高,尤其是当铸铁中锰和磷含量较高时,更需要严格控制硅的含量。
球墨铸铁中终硅量一般在1.4—3.0%。
选定碳当量后,一般采取高碳低硅强化孕育的原则。
硅的下限以不出现自由渗碳体为原则。
图4—6 硅对铁素体球墨铸铁脆性转变温度的影响球墨铸铁中碳硅含量确定以后,可用图4—7进行检验。
如果碳硅含量在图中的阴影区,则成分设计基本合适。
球墨铸铁提高球化率的工艺实用方案范文
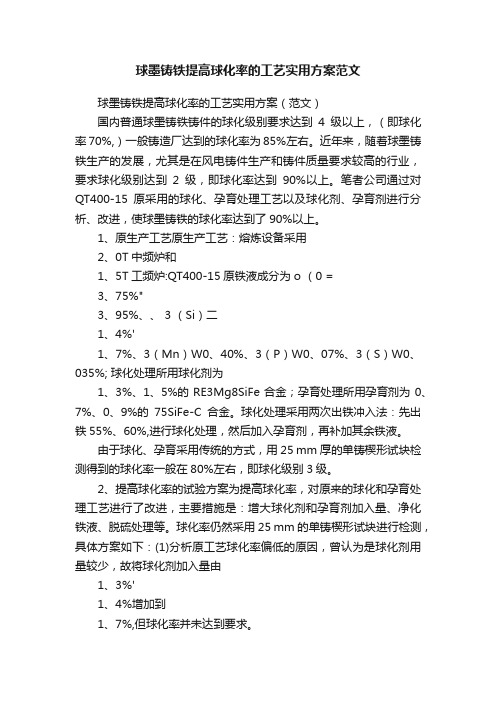
球墨铸铁提高球化率的工艺实用方案范文球墨铸铁提高球化率的工艺实用方案(范文)国内普通球墨铸铁铸件的球化级别要求达到4级以上,(即球化率70%,)一般铸造厂达到的球化率为85%左右。
近年来,随着球墨铸铁生产的发展,尤其是在风电铸件生产和铸件质量要求较高的行业,要求球化级别达到2级,即球化率达到90%以上。
笔者公司通过对QT400-15原采用的球化、孕育处理工艺以及球化剂、孕育剂进行分析、改进,使球墨铸铁的球化率达到了90%以上。
1、原生产工艺原生产工艺:熔炼设备采用2、0T中频炉和1、5T工频炉:QT400-15原铁液成分为o (0 =3、75%"3、95%、、 3 (Si)二1、4%'1、7%、3(Mn)W0、40%、3(P)W0、07%、3(S)W0、035%; 球化处理所用球化剂为1、3%、1、5%的RE3Mg8SiFe合金;孕育处理所用孕育剂为0、7%、0、9%的75SiFe-C合金。
球化处理采用两次出铁冲入法:先出铁55%、60%,进行球化处理,然后加入孕育剂,再补加其余铁液。
由于球化、孕育采用传统的方式,用25 mm厚的单铸楔形试块检测得到的球化率一般在80%左右,即球化级别3级。
2、提高球化率的试验方案为提高球化率,对原来的球化和孕育处理工艺进行了改进,主要措施是:增大球化剂和孕育剂加入量、净化铁液、脱硫处理等。
球化率仍然采用25 mm的单铸楔形试块进行检测,具体方案如下:(1)分析原工艺球化率偏低的原因,曾认为是球化剂用量较少,故将球化剂加入量由1、3%'1、4%增加到1、7%,但球化率并未达到要求。
(2)另一种猜测是认为球化率偏低可能是由于孕育不良或孕育衰退引起,因而试验加大孕育剂量,由0、7%、0、9%增加到1、1%,球化率亦未达到要求。
(3)继续分析认为铁液夹杂较多、球化干扰元素偏高等可能是造成球化率偏低的原因,因而对铁液进行高温净化,高温净化温度一般控制在1500±10°C,但其球化率仍未突破90%。
铸造球铁件,球化过程常见问题及解决方案
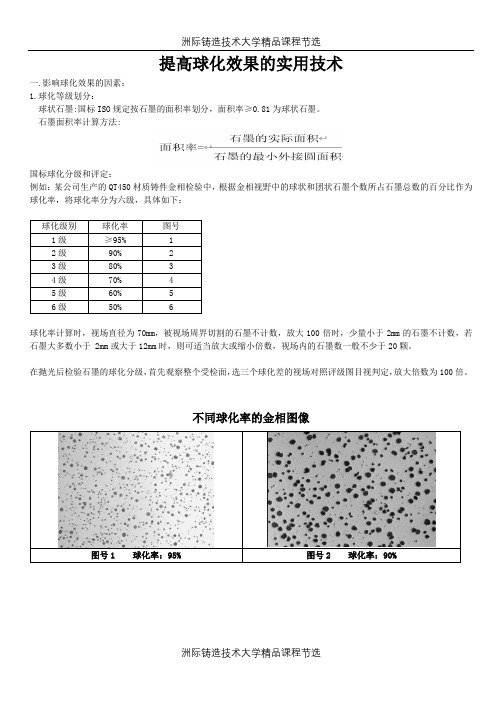
提高球化效果的实用技术一.影响球化效果的因素:1.球化等级划分:球状石墨:国标ISO规定按石墨的面积率划分,面积率≥0.81为球状石墨。
石墨面积率计算方法:国标球化分级和评定:例如:某公司生产的QT450材质铸件金相检验中,根据金相视野中的球状和团状石墨个数所占石墨总数的百分比作为球化率,将球化率分为六级,具体如下:球化率计算时,视场直径为70mm,被视场周界切割的石墨不计数,放大100倍时,少量小于2mm的石墨不计数,若石墨大多数小于 2mm或大于12mm时,则可适当放大或缩小倍数,视场内的石墨数一般不少于20颗。
在抛光后检验石墨的球化分级,首先观察整个受检面,选三个球化差的视场对照评级图目视判定,放大倍数为100倍。
不同球化率的金相图像图号1 球化率:95% 图号2 球化率:90%图号3 球化率:80% 图号4 球化率:70%图号5 球化率:60% 图号6 球化率:50%2.球化可能会出现的问题及解决方案:(1)球化不良:此不良主要体现在炉后成品的残镁分析值低于0.030%(一般标准残镁规格值按照小于0.030%为下限规格值),金相石墨型态一般体现在球状石墨和蠕虫状石墨共存在,或球状石墨、蠕虫状石墨和片状石墨共存在,或蠕虫状石墨和片状石墨共存在,或全部为片状石墨。
控制球化不良的发生,特别注意以下几点:A.添加球化剂重量的核对或喂丝球化线的喂丝长度核对,确保实际加入量与标准规定的相符。
B.三明治球化温度或喂丝温度一般在1480-1530℃。
C.三明治球化反应时间一般控制大于55秒,喂丝球化速度一般控制19-22米/分钟。
D.三明治球化出炉过程确保电炉的先期铁水冲入到球化包的缓冲室,等缓冲室铁水满后,铁水再漫过球化室。
(有很多出炉铁水冲入不当,造成铁水直接冲到球化室的,造成球化反应提前进行,总的球化反应时间短,导致球化不良。
)E.三明治球化需要在球化包之球化室中的球化剂上侧放置覆盖剂,覆盖剂一般为矽钢片,厚度一般控制在0.3-1.0mm,直径或单边长度为10-30mm,要求无油无锈无杂质。
球化处理工艺

损失了.
第6页/共42页
自建压力加镁包结构图
压力加镁法的优点是,使用纯镁进行球化处理, 镁的吸收率高,可达70℅~80℅;处理过程中的劳动 环境较好.
缺点是,高备费用比较高;操作复杂,严格;处理 时间长铁液降温多;因此需要较高的出炉温度.球 化处理时压力大,容易发生工伤事故.
第7页/共42页
(二)冲入法
第10页/共42页
冲入法球化处理前,就将球化处理包预热到暗红色, 预热的目的是减少铁液热量损失.并且防止覆盖剂下 桩实较紧的合金粘结在包底.球化处理时,将球化合 金堆放在预热的包底,上面覆盖硅铁合金,稍加紧实, 然后再覆盖无锈铁屑,苏打等覆盖剂,铁液过高时,可 盖铁板.
这种方法的优点是,处理方式和设备简单,容易操 作,在生产中有较大的灵活性,一般可使用含镁量较 低(<10℅)的各种合金球化剂.但是该工艺在球化处 理过程中镁光,烟尘非常大,劳动环境差,镁的吸收率 不太高,球化剂消耗量大,球化效果及球铁性能不太 稳定.目前应该改进冲入法或换用其它球化处理工艺.
容易操作的优点.又克服了冲入法中镁氧化烧
第18页/共42页
损严重、吸收率、低球化剂消耗量大劳动 环境差等缺点.多年来人们一直在利用盖包 法的优点进行球铁生产,同时也在不断地努 力克服工艺在使用中的不足之处: (1)包盖起吊困难,操作难度大;(2)在使用冲 天炉连续出铁时,铁液重量难以精确量化.
第19页/共42页
第23页/共42页
1、 铁水加镁喂线处理技术的特点
(1)反应区域内的镁蒸汽相对集中,镁蒸汽泡的 分散度远不如冲入法(或称三明治法)和盖包法 处理时镁蒸汽泡的分散度,因此,镁蒸汽泡会在 反应区域内迅速长大并聚集,并快速逸出,因此, 反应强度较大,镁在铁水中的有效率较低;
球铁活塞环球化处理改进

球铁活塞环球化处理改进
王季明
【期刊名称】《内燃机与配件》
【年(卷),期】2013(000)007
【摘要】本文主要阐述在铸造活塞环毛坯球化处理时作者通过添加辅助球化合金,降低球化剂用量,使球化时反应平稳,铁水吸气少、降温少,铸造废品降低,球径小,机械性能有所提高.
【总页数】3页(P12-13,18)
【作者】王季明
【作者单位】石家庄金刚内燃机零部件集团有限公司
【正文语种】中文
【相关文献】
1.喂丝球化处理工艺在高Si-Mo球铁件中的应用 [J], 莫俊超;张尊乐;贺春;马琦
2.生产球铁铸管的球化处理工艺改进 [J], 张永杰
3.球铁活塞环球化处理改进 [J], 王季明;
4.较大型球铁件铁液的喂线孕育及球化处理工艺 [J], 董立;王亚明;万飞;高军;谭伟;陈丽;孟文玲;许庭国;边蒙
5.球墨铸铁活塞环球化处理的炉前判断 [J], 开柏林
因版权原因,仅展示原文概要,查看原文内容请购买。