脱硫石灰石耗量分析
脱硫石灰石耗量分析
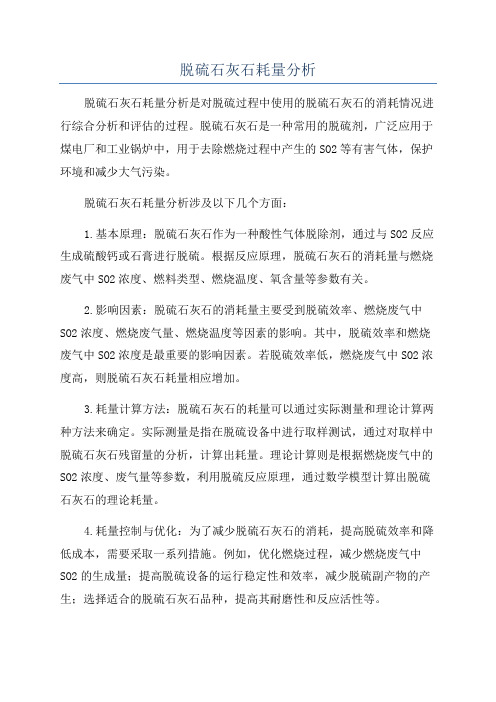
脱硫石灰石耗量分析脱硫石灰石耗量分析是对脱硫过程中使用的脱硫石灰石的消耗情况进行综合分析和评估的过程。
脱硫石灰石是一种常用的脱硫剂,广泛应用于煤电厂和工业锅炉中,用于去除燃烧过程中产生的SO2等有害气体,保护环境和减少大气污染。
脱硫石灰石耗量分析涉及以下几个方面:1.基本原理:脱硫石灰石作为一种酸性气体脱除剂,通过与SO2反应生成硫酸钙或石膏进行脱硫。
根据反应原理,脱硫石灰石的消耗量与燃烧废气中SO2浓度、燃料类型、燃烧温度、氧含量等参数有关。
2.影响因素:脱硫石灰石的消耗量主要受到脱硫效率、燃烧废气中SO2浓度、燃烧废气量、燃烧温度等因素的影响。
其中,脱硫效率和燃烧废气中SO2浓度是最重要的影响因素。
若脱硫效率低,燃烧废气中SO2浓度高,则脱硫石灰石耗量相应增加。
3.耗量计算方法:脱硫石灰石的耗量可以通过实际测量和理论计算两种方法来确定。
实际测量是指在脱硫设备中进行取样测试,通过对取样中脱硫石灰石残留量的分析,计算出耗量。
理论计算则是根据燃烧废气中的SO2浓度、废气量等参数,利用脱硫反应原理,通过数学模型计算出脱硫石灰石的理论耗量。
4.耗量控制与优化:为了减少脱硫石灰石的消耗,提高脱硫效率和降低成本,需要采取一系列措施。
例如,优化燃烧过程,减少燃烧废气中SO2的生成量;提高脱硫设备的运行稳定性和效率,减少脱硫副产物的产生;选择适合的脱硫石灰石品种,提高其耐磨性和反应活性等。
总结而言,脱硫石灰石耗量分析是对脱硫过程中使用的脱硫石灰石的消耗情况进行评估和优化的重要工作。
通过深入分析影响因素和耗量计算方法,可以有效控制脱硫石灰石的消耗,提高脱硫效率,降低运营成本,实现环境保护和经济效益的双重目标。
脱硫石灰石耗量分析
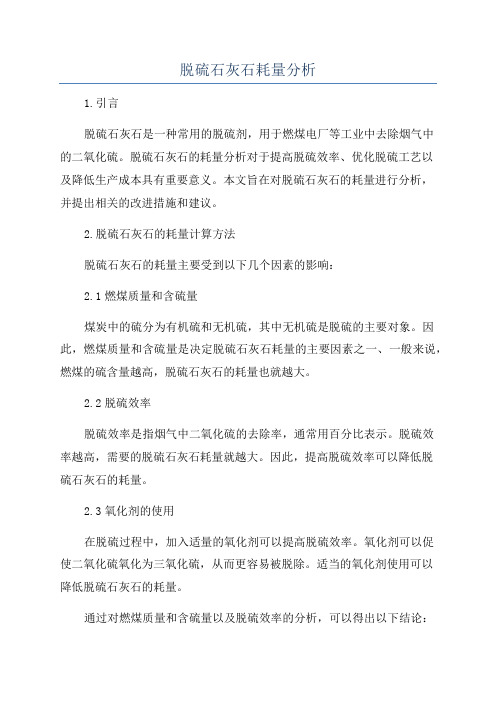
脱硫石灰石耗量分析1.引言脱硫石灰石是一种常用的脱硫剂,用于燃煤电厂等工业中去除烟气中的二氧化硫。
脱硫石灰石的耗量分析对于提高脱硫效率、优化脱硫工艺以及降低生产成本具有重要意义。
本文旨在对脱硫石灰石的耗量进行分析,并提出相关的改进措施和建议。
2.脱硫石灰石的耗量计算方法脱硫石灰石的耗量主要受到以下几个因素的影响:2.1燃煤质量和含硫量煤炭中的硫分为有机硫和无机硫,其中无机硫是脱硫的主要对象。
因此,燃煤质量和含硫量是决定脱硫石灰石耗量的主要因素之一、一般来说,燃煤的硫含量越高,脱硫石灰石的耗量也就越大。
2.2脱硫效率脱硫效率是指烟气中二氧化硫的去除率,通常用百分比表示。
脱硫效率越高,需要的脱硫石灰石耗量就越大。
因此,提高脱硫效率可以降低脱硫石灰石的耗量。
2.3氧化剂的使用在脱硫过程中,加入适量的氧化剂可以提高脱硫效率。
氧化剂可以促使二氧化硫氧化为三氧化硫,从而更容易被脱除。
适当的氧化剂使用可以降低脱硫石灰石的耗量。
通过对燃煤质量和含硫量以及脱硫效率的分析,可以得出以下结论:3.1含硫量高的燃煤需要更多的脱硫石灰石来达到相同的脱硫效果。
因此,在采购脱硫石灰石时应选择合适的品种和规格。
3.2提高脱硫效率可以降低脱硫石灰石的耗量。
可以通过优化脱硫工艺、提高吸收效果等方式来实现。
3.3适量的氧化剂使用可以提高脱硫效率,但过量的使用会导致脱硫石灰石的浪费。
因此,需要在实际操作中进行合理调控。
4.改进措施和建议基于以上分析,我们可以提出以下改进措施和建议:4.1加强煤炭质量管理,选择低硫煤,从源头上降低脱硫石灰石的耗量。
4.2优化脱硫工艺,提高脱硫效率,减少脱硫石灰石的使用量。
4.3对氧化剂使用进行精确控制,避免浪费。
4.4定期开展脱硫石灰石的耗量监测和分析,及时发现问题并采取相应措施。
4.5加强脱硫石灰石的储存和管理,确保其质量和使用效果。
5.结论脱硫石灰石的耗量分析对于提高脱硫效率、降低生产成本具有重要意义。
电厂脱硫石灰石用量计算公式
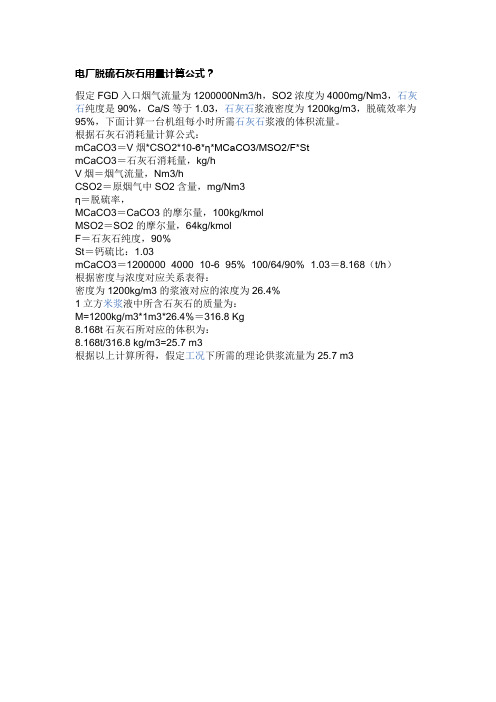
电厂脱硫石灰石用量计算公式?
假定FGD入口烟气流量为1200000Nm3/h,SO2浓度为4000mg/Nm3,石灰石纯度是90%,Ca/S等于1.03,石灰石浆液密度为1200kg/m3,脱硫效率为95%,下面计算一台机组每小时所需石灰石浆液的体积流量。
根据石灰石消耗量计算公式:
mCaCO3=V烟*CSO2*10-6*η*MCaCO3/MSO2/F*St
mCaCO3=石灰石消耗量,kg/h
V烟=烟气流量,Nm3/h
CSO2=原烟气中SO2含量,mg/Nm3
η=脱硫率,
MCaCO3=CaCO3的摩尔量,100kg/kmol
MSO2=SO2的摩尔量,64kg/kmol
F=石灰石纯度,90%
St=钙硫比:1.03
mCaCO3=1200000×4000×10-6×95%×100/64/90%×1.03=8.168(t/h)
根据密度与浓度对应关系表得:
密度为1200kg/m3的浆液对应的浓度为26.4%
1立方米浆液中所含石灰石的质量为:
M=1200kg/m3*1m3*26.4%=316.8 Kg
8.168t石灰石所对应的体积为:
8.168t/316.8 kg/m3=25.7 m3
根据以上计算所得,假定工况下所需的理论供浆流量为25.7 m3。
脱硫系统设计-石灰石 - 石膏湿法脱硫

脱硫系统设计---- 石灰石 - 石膏湿法脱硫1 脱硫系统设计的初始条件在进行脱硫系统设计时,所需要的初始条件一般有以下几个:(1)处理烟气量,单位:m3/h或Nm3/h;(2)进气温度,单位:℃;(3)SO2初始浓度,单位:mg/m3或mg/Nm3;(4)SO2排放浓度, 单位:mg/m3或mg/Nm3;2 初始条件参数的确定2.1 处理风量的确定处理烟气量的大小是设计脱硫系统的关键,一般处理烟气量由业主方给出或从除尘器尾部引风机风量大小去确定。
处理风量还存在标况状态(Nm3/h)和工况状态(m3/h)的换算,换算采用理想气体状态方程:PV = nRT(P、n、R均为定值)V1/T1=V2/T2V1: mg/Nm3,T1:273K; V2: mg/m3,T2:t+273K(t为进气温度);怀化骏泰提供的是工况烟气量是300000m3/h,烟气温度150℃,经上述公式转换得出标况烟气量193600 Nm3/h(液气比计算用标况烟气量)2.2 进气温度的确定进气温度为经过除尘后进入脱硫塔的烟气温度值,进气温度大小关系到脱硫系统烟气量的换算和初始SO2浓度换算。
2.3 SO2初始浓度的确定SO2初始浓度一般由业主方给出,并且由此计算脱硫系统中各项设备参数,也是系统选择液气比的重要依据。
SO2初始量计算公式如下:S+O2→SO232 64C SO2=2×B×S ar/100×ηso2/100×109C SO2-SO2初始量,mg; B-锅炉BMCR负荷时的燃煤量,t/h;S ar-燃料的含S率,%;ηso2-煤中S变成SO2的转化率,%,一般取0.85;怀化骏泰提供的是4000 mg/Nm32.4 SO2排放浓度的确定一般根据所在地区环保标准确定。
二氧化硫排放限值与烧煤、油、气有关,与新建或改造锅炉有关,与地区有关,设计之前需要查看当地环保排放标准。
按照国家标准,污染物排放浓度需按公式折算为基准氧含量排放浓度,所以实测的排放浓度还需要经过折算,燃煤锅炉按基准含氧量O2=6%进行折算,c = c’× (21 - O2) / (21 - O2’)式中c –大气污染物基准氧含量排放浓度 , mg/m3;c’—实测的大气污染物排放浓度, mg/m3; 38 mg/m3O2’-- 实测的含氧量 ,%; 15%O2 -- 基准含氧量 ,%; 6%计算: SO2浓度(6%O2)=38×(21-6)/(21-15)=95mg/m3,结果也是与在线监测值相符根据在线监测电脑上显示实测的大气污染物排放浓度, 实测的含氧量,我们可以自己计算出折算值.当然电脑上也给我们自动折算并且给出了折算值,但是这个值怎么来的,我们需要知道,怀化骏泰的排放浓度是100mg/ m3,折算值,不是实测值,3 脱硫系统的设计计算3.1 参数定义(1)液气比(L/G ):即单位时间内浆液喷淋量和单位时间内流经吸收塔的烟气量之比.单位为L/m3;)/3()/(h m h L 的湿烟气体积流量单位时间内吸收塔入口单位时间内浆液喷淋量液气比石灰石法液气比范围在8l/m3-25l/m3之间,一般认为12.2就可以了(液气比超过某个值后,脱硫效率的提高非常缓慢,而且提高液气比将使浆液循环泵的流量增大,增加循环泵的设备费用,塔釜的体积增大.增大脱硫塔制造成本,同时还会提高吸收塔的压降,加大增压风机的功率及设备费用)通过液气比可以计算出循环浆液量Q 循 = 12.2 × 193600 / 1000 = 2362 m3/h(2)钙硫比(Ca/S ):理论上脱除1mol 的S 需要1mol 的Ca ,但在实际反应设备中,反应条件并不处于理想状态,一般需要增加脱硫剂的量来保证一定的脱硫效率,因此引入了Ca/S 的概念。
石灰石-石膏法脱硫数据计算

估计
泵与风机冷却用水
Mwq
t/h
估计
单套脱硫装置耗水量
Mw
t/h
Mgyc+Mgys+Mww+Mwe+Mgyw+Mwq
总的脱硫装置耗水量
Mw'
t/h
n*Mw
氧化空气量计算:
序号
名称
符号
单位
计算公式或数值来源
需氧量
Vo2
kg/h
SO2---1/2O2
kmol/h
Vo2/32
需空气量
Vk
Nm3/h
Vo2/32*22.41/0.21
2)
二氧化物
VRO20
Nm3/kg
0.01866(Car+0.375Sar)
3)
水蒸汽
VH2O0
Nm3/kg
0.111Har+0.0124Mar+0.0161V0
3
燃烧产物实际体积
Vy'
Nm3/kg
Vy0+0.0161(alfa'-1)V0+(alfa'-1)V0
4
干烟气量
Vgy'
Nm3/kg
VRO20+VN20+(alfa'-1)V0
烟气比热kcal/Nm3.℃100℃
kcal/Nm3.℃200℃
i1kcal/Nm3.℃插值法: tpy
i2插值法求85℃比热
t℃t=126-i2*(85-50)/i1
i3kcal/Nm3.℃插值法: t
塔内烟气放热量
Q1
kJ/h
V ' * i3*4.18*(t-50)
石灰石-石膏湿法脱硫工艺的基本原理
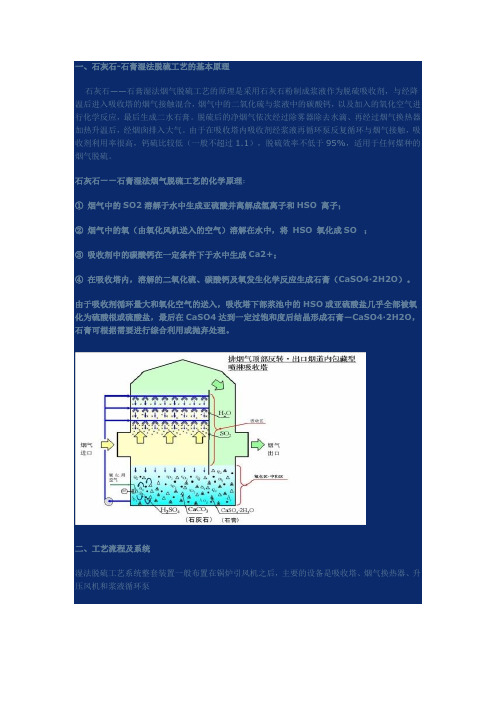
一、石灰石-石膏湿法脱硫工艺的基本原理石灰石——石膏湿法烟气脱硫工艺的原理是采用石灰石粉制成浆液作为脱硫吸收剂,与经降温后进入吸收塔的烟气接触混合,烟气中的二氧化硫与浆液中的碳酸钙,以及加入的氧化空气进行化学反应,最后生成二水石膏。
脱硫后的净烟气依次经过除雾器除去水滴、再经过烟气换热器加热升温后,经烟囱排入大气。
由于在吸收塔内吸收剂经浆液再循环泵反复循环与烟气接触,吸收剂利用率很高,钙硫比较低(一般不超过1.1),脱硫效率不低于95%,适用于任何煤种的烟气脱硫。
石灰石——石膏湿法烟气脱硫工艺的化学原理:①烟气中的SO2溶解于水中生成亚硫酸并离解成氢离子和HSO 离子;②烟气中的氧(由氧化风机送入的空气)溶解在水中,将HSO 氧化成SO ;③吸收剂中的碳酸钙在一定条件下于水中生成Ca2+;④在吸收塔内,溶解的二氧化硫、碳酸钙及氧发生化学反应生成石膏(CaSO4·2H2O)。
由于吸收剂循环量大和氧化空气的送入,吸收塔下部浆池中的HSO或亚硫酸盐几乎全部被氧化为硫酸根或硫酸盐,最后在CaSO4达到一定过饱和度后结晶形成石膏—CaSO4·2H2O,石膏可根据需要进行综合利用或抛弃处理。
二、工艺流程及系统湿法脱硫工艺系统整套装置一般布置在锅炉引风机之后,主要的设备是吸收塔、烟气换热器、升压风机和浆液循环泵我公司采用高效脱除SO2的川崎湿法石灰石-石膏工艺。
该套烟气脱硫系统(FGD)处理烟气量为定洲发电厂#1和#2机组(2×600MW)100%的烟气量,定洲电厂的FGD系统由以下子系统组成:(1)吸收塔系统(2)烟气系统(包括烟气再热系统和增压风机)(3)石膏脱水系统(包括真空皮带脱水系统和石膏储仓系统)(4)石灰石制备系统(包括石灰石接收和储存系统、石灰石磨制系统、石灰石供浆系统)(5)公用系统(6)排放系统(7)废水处理系统1、吸收塔系统吸收塔采用川崎公司先进的逆流喷雾塔,烟气由侧面进气口进入吸收塔,并在上升区与雾状浆液逆流接触,处理后的烟气在吸收塔顶部翻转向下,从与吸收塔烟气入口同一水平位置的烟气出口排至烟气再热系统。
关于脱硫系统单塔与双塔、单塔双循环的的对比选择与建议

关于脱硫系统单塔与双塔的的对比选择与建议传统石灰石—石膏湿法脱硫效率通常可以达到97~98%左右。
若燃煤的硫份(收到基)范围为1.5-2.0%,则根据1%收到基硫分,脱硫入口硫含量为2200mg/m3测算,以出口二氧化硫为35 mg/m3为基准,对硫份(收到基)范围为1.5-2.0%时,对应脱硫效率为99%~99.2%。
脱硫效率超过99%之后,需要对传统石灰石—石膏湿法脱硫工艺进行提效改进,采用传统单塔是不能满足本工程要求的。
目前,已经发展出多种可提高脱硫效率的技术,并在工程中得到应用。
主要有单塔双循环技术(国电龙源)、串塔或双塔双循环、单塔双区(上海龙净)、U型液柱塔(重庆远达环保)等多种技术可供选择。
根据《中国大唐集团公司燃煤火电工程典型推荐技术组合方案(2014 年试行版)》中对脱硫工艺选择的规定如下:1)方案一,FGD 工艺,每台炉设置一套石灰石-石膏湿法烟气脱硫工艺,不设GGH,不设旁路烟道,采用单塔单循环,FGD 监控用DCS与机组DCS 一体化。
2)可根据煤质含硫量高低、环保排放限值要求,选择单塔或双塔方案;煤质含硫量小于1.3%,单塔脱硫效率在98%以内,能满足排放标准的,采用单塔单循环方案;煤质含硫量大于1.3%,单塔脱硫效率大于98%以上,仍不能满足排放标准的,可选用单塔双循环或双塔双循环等高效脱硫技术。
在我厂拟计划采用燃煤的硫份(收到基)范围为2.0%的情况下,达标排放情况下(二氧化硫为20 mg/m3),脱硫效率不低于99.64%。
U形塔技术预期脱硫效率与双塔双循环方案相当。
该方案存在投资高、运行费用相对较高、运行业绩较少等问题,同时由于液柱塔喷射液柱由所有循环泵母管供给,循环泵母管故障或单台泵故障均会造成环保指标超标,可靠性较低。
单塔双区技术与普通吸收塔区别仅在于对普通吸收塔浆池进行了不可靠的分区(提高浆池高度,布置射流泵),使之形成非纯粹的氧化区和吸收区,理论上脱硫效率较单塔有所提高,但较双循环系统低。
脱硫系统石灰石浆液流量计算

某电厂的一台300MW燃煤机组,装有湿法石灰石—石膏烟气脱硫装置,其入口烟气流量为1070659Nm 3/h,进口烟气氧量为6%,SO 2浓度为1985mg/Nm 3,石灰石纯度是92%,Ca/S等于1.03,石灰石浆液密度为1230kg/m 3,脱硫效率为91%,试计算该脱硫装置每小时所需石灰石浆液的体积流量是多少?解:根据石灰石消耗量计算公式:332226,10CaCO CaCO RG SO rawgas SO R t SO M m V c F M η−=××××÷×S式中:3CaCO m =石灰石消耗量,kg/hRG V =烟气流量:1070659Nm 3/h2,SO rawgas c =原烟气中SO 2含量:1985mg/Nm 32SO η=脱硫率,91%3CaCO M =CaCO 3的摩尔量,100.09kg/kmol2SO M =SO 2的摩尔量,64.06kg/kmolR F =石灰石纯度,92%S t =钙硫比:1.0336100107065919851091%92% 1.0364−=××××÷×CaCO m=2125.2581×0.91×1.5625÷0.92×1.03=3.3832(t/h)根据密度与含固量的换算公式1211100%11S S ρωρ−=×−式中:ω=质量分数(含固量),%1S ρ=石灰石的浆液密度,kg/m 32S ρ=石灰石的密度,取2.71×103 kg/m 311 1.23100%11 2.71ω−=×− =10.813100%10.369−×−=0.2964×100%=29.64%根据石灰石浆液的质量流量计算公式: 33CaCO suspension CaCO m m c =式中:suspension m =石灰石浆液质量流量,t/h 3CaCO m =石灰石消耗量,t/h 3CaCO c =石灰石浆液的含固量,% 3.383229.64%= suspension m=11.4143(t/h)石灰石浆液的体积流量计算公式 suspensionsuspension suspensionm V ρ=式中:suspension V =石灰石浆液体积流量,m 3/h suspension m =石灰石浆液质量流量,kg/h suspension ρ=石灰石浆液的密度,kg/m 33311.4143101.2310×=× suspension V=9.2799 m3/h。
石灰石
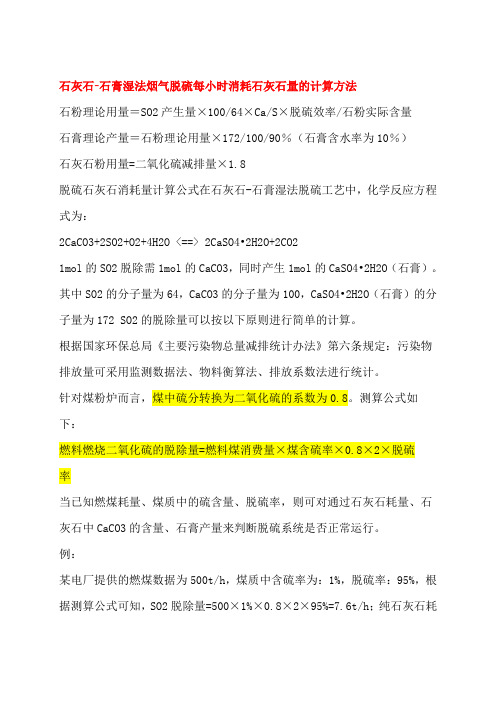
石灰石-石膏湿法烟气脱硫每小时消耗石灰石量的计算方法石粉理论用量=SO2产生量×100/64×Ca/S×脱硫效率/石粉实际含量石膏理论产量=石粉理论用量×172/100/90%(石膏含水率为10%)石灰石粉用量=二氧化硫减排量×1.8脱硫石灰石消耗量计算公式在石灰石-石膏湿法脱硫工艺中,化学反应方程式为:2CaCO3+2SO2+O2+4H2O <==> 2CaSO4•2H2O+2CO21mol的SO2脱除需1mol的CaCO3,同时产生1mol的CaSO4•2H2O(石膏)。
其中SO2的分子量为64,CaCO3的分子量为100,CaSO4•2H2O(石膏)的分子量为172 SO2的脱除量可以按以下原则进行简单的计算。
根据国家环保总局《主要污染物总量减排统计办法》第六条规定:污染物排放量可采用监测数据法、物料衡算法、排放系数法进行统计。
针对煤粉炉而言,煤中硫分转换为二氧化硫的系数为0.8。
测算公式如下:燃料燃烧二氧化硫的脱除量=燃料煤消费量×煤含硫率×0.8×2×脱硫率当已知燃煤耗量、煤质中的硫含量、脱硫率,则可对通过石灰石耗量、石灰石中CaCO3的含量、石膏产量来判断脱硫系统是否正常运行。
例:某电厂提供的燃煤数据为500t/h,煤质中含硫率为:1%,脱硫率:95%,根据测算公式可知,SO2脱除量=500×1%×0.8×2×95%=7.6t/h;纯石灰石耗量为:7.6÷64×100=11.875t/h,考虑石灰石纯度为92%,Ca/S比为1.03,则石灰石耗量为:11.875×1.03÷92%=13.59t/h;折算到浆液时为每小时消耗38.5m3/h(30%浆液浓度);石膏产量为:7.6÷64×172=20.425t/h.湿法脱硫系统物料平衡一、计算基础数据(1)待处理烟气烟气量:1234496Nm3/h(wet)、1176998 Nm3/h(dry)烟气温度:114℃烟气中SO2浓度:3600mg/Nm3二、平衡计算(1)原烟气组成计算(2)烟气量计算质量流量和体积流量的关系:质量流量(kg/h)=体积流量(Nm3/h)×密度(kg/m3) 1、①→②(增压风机出口→GGH出口):取GGH的泄漏率为0.5%,则GGH出口总烟气量为1234496 Nm3/h×(1-0.5%)=1228324Nm3/h=1629634kg/h 泄漏后烟气组分不变,但其质量分别减少了0.5%,见下表。
(整理)脱硫石灰石耗量分析
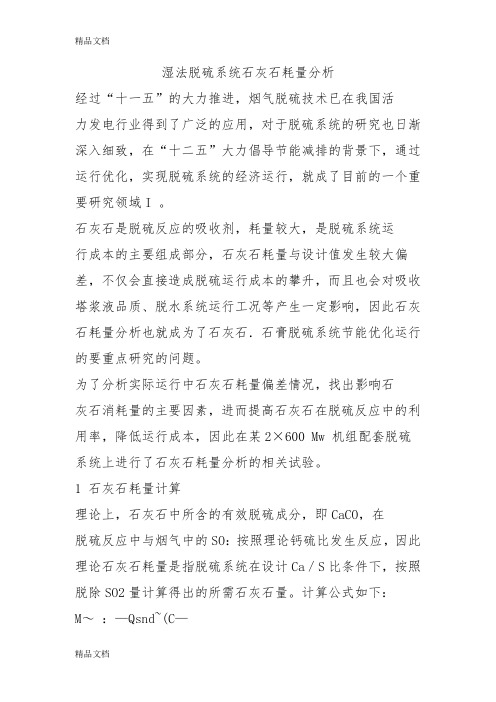
湿法脱硫系统石灰石耗量分析经过“十一五”的大力推进,烟气脱硫技术已在我国活力发电行业得到了广泛的应用,对于脱硫系统的研究也日渐深入细致,在“十二五”大力倡导节能减排的背景下,通过运行优化,实现脱硫系统的经济运行,就成了目前的一个重要研究领域I 。
石灰石是脱硫反应的吸收剂,耗量较大,是脱硫系统运行成本的主要组成部分,石灰石耗量与设计值发生较大偏差,不仅会直接造成脱硫运行成本的攀升,而且也会对吸收塔浆液品质、脱水系统运行工况等产生一定影响,因此石灰石耗量分析也就成为了石灰石.石膏脱硫系统节能优化运行的要重点研究的问题。
为了分析实际运行中石灰石耗量偏差情况,找出影响石灰石消耗量的主要因素,进而提高石灰石在脱硫反应中的利用率,降低运行成本,因此在某2×600 Mw 机组配套脱硫系统上进行了石灰石耗量分析的相关试验。
1 石灰石耗量计算理论上,石灰石中所含的有效脱硫成分,即CaCO,在脱硫反应中与烟气中的SO:按照理论钙硫比发生反应,因此理论石灰石耗量是指脱硫系统在设计Ca/S比条件下,按照脱除SO2量计算得出的所需石灰石量。
计算公式如下:M~:—Qsnd~(C—sl-Cs2)××⋯ l000000 64式中:Mcaco3——理论石灰石耗量,kg/ll;Q5 d——标干烟气量, Nm ha(6%02); csl一一原烟气s02浓度,mg/Nm (6%02);Cs2一一净烟气SO2浓度,mg/Nm (6%O2);收稿日期:2012.12-10戴新(1970一),男,高级工程师。
丰镇,012100n一一石灰石纯度,试验期间为89.4%;——设计钙硫比, 1.03。
实际脱硫反应中,由于石灰石反应活性、杂质含量等因素影响,石灰石实际耗量会与理论值存在一定偏差,通常实际石灰石消耗量是通过实际脱硫反应中投加到吸收塔内的石灰石浆液量和浆液密度计算得出,计算公式如下:M c 川式中:^ aCO3——实际石灰石耗量,kg/h; P ——石灰石密度,P =2.6 g/cm ;P ——石灰石浆液密度,g/cm ;——每小时石灰石浆液量,m /h。
脱硫物料平衡计算

设计煤种校核煤种一、项目概况 、项目设计条件元素分析□□□□□□□□1)规模 2)燃料 75t/h煤3)脱硫工艺 石灰石-石膏湿法 4)吸收剂 石灰石 5)副产品石膏6)脱水系统真空皮带脱水机7)再加热方式:无8)烟气量 112000Nm3/h (湿基)x2(100%BMCR )9)FGD 入口温度135°C(设计),141°C(最大) 10)FGD 入口SO2浓度 40001m3(干基)11)FGD 入口粉尘浓度<200mg/Nm3(干基,6%02)12)FGD 出口温度(进烟囱)>50 13)除雾器出口含水量<75mg/Nm3(干基) 14)吸收剂耗量<7.8t/h15)工艺水消耗量<8.6t/h 16)副产品石膏含水量<15% 17)电力消耗<12700kWh/h18)脱硫效率>92% 19)系统可用率>95%5.1.2设计条件1)煤质分析2.1FGD 装置条件 项目 单位Car 59.95 65.71 Har2.252.36Oar%0.570.9Nar%0.940.74Sar% 2.29 2.29工业分析Var%9.07.0Aar%27.0320.0Mar%7.08.0Mad% 2.17 1.67低位发热量kj/kg2146524668100%BMCR燃煤消耗量t/h(每台134.89134.89炉)2)烟气设计条件项目单位100%BMCR35%BMCR FGD入口烟气流量Nm3/h(湿基)1256682517256 FGD入口烟气流量Nm3/h(干基)1193075492172 FGD入口烟气温度°C131103 FGD入口烟气压力Pa00粉尘浓度mg/Nm3180.5164.6 SO2浓度ppm(dry)17611652Nm3/h2101813烟气含水量Vol%(dry) 5.06 4.85烟气含氧量Vol%(dry)7.468.29 CO2Vol%(dry)12.2911.53 N2Vol%(dry)80.0780.01 HCL ppm(dry)25.223.0HF ppm(dry) 11.2 10.2资料确认注意事项:1)由于烟气设计资料,常常会以不同的基准重复出现多次,(如:干基\湿基,标态\实际态,6%02\实际O2等),开始计算前一定要核算统一,如出现矛盾,必须找出正确的一组数据,避免原始数据代错。
石灰石-石膏湿法脱硫化学分析
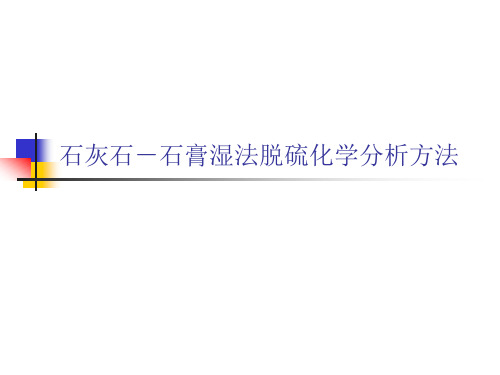
试样的烘干条件
石灰石 105~110℃下烘2小时 石膏和石膏浆液40~45 ℃下干燥
2、石灰石
2.1 CaO含量分析
方法参考GB/T 5762-2000 第14页氧化钙的测定(代用法) 原理:在酸性溶液中,加氟化钾,消除硅酸的干扰后, 在pH13以上的强碱中,以三乙醇胺为掩蔽剂,CMP为 指示剂,用EDTA溶液滴定。 注意点:1.指示剂的用量 2.终点的判断 3.计算公式
(3)影响沉淀溶解度的因素
影响沉淀平衡的因素很多,如同离子效应、盐效应,酸效应、 配位效应等。
同离子效应
当沉淀反应达到平衡后,若向溶液中加入含某一构晶离子的试剂 或溶液,则沉淀的溶解度减小,这一效应称为同离子效应。
盐效应
在难溶电解质的饱和溶液中,由于加入了强电解质而增大沉淀溶 解度的现象.称为盐效应。例如用Na2SO4作沉淀剂测定Pb2+时, 生成PbSO4。当PbSO4沉淀后,继续加入Na2SO4,就同时存在同离 子效应和盐效应。
EDTA滴定法 重量法(GB/T5484-2000)
重量法测三氧化硫含量
方法提要: 方法提要:在 酸 性 溶液中,用氯化钡溶液沉淀硫酸盐,经过滤灼 烧后,以硫酸钡形式称量,测定结果以三氧化硫计。 分析过程: 分析过程: 1.试样的分解 试样的分解。称 取 约 0.2 g 试样,置于300mL烧杯中,加人 试样的分解 30~40m L水使其分散。加10 mL盐酸(1+1),将溶液加热微沸5 min。用中速滤纸过滤,用热水洗涤10~12次。 2.沉淀。调整滤液体积至200 mL煮沸,在搅拌下滴加15 mL氯化 钡溶液,继续煮沸数分钟,然后移至温热处静置4h或过夜(此时溶 液的体积应保持在200 mL )。用慢速滤纸过滤,用温水洗涤,直 至检验无氯离子为止。 3.灰化、灼烧、称量。将沉淀及滤纸一并移人已灼烧恒量的瓷柑 祸中,灰化后在800 C的马弗炉内灼烧30 min,取出琳涡置于干 燥器中冷却至室温,称量。反复灼烧,直至恒量。
石灰石-石膏法脱硫计算

0.077
mwater,vapourised=
21200 kg/h
V m water,saturation
water,vapourised water,saturation
=
取
Vwater,saturation=
27179.49 Nm³/h 27000 Nm³/h
12 吸收塔出口净烟气的计算
Vwater,vapourised,cleangas=Vwater+Vwater,saturatio
633000 Nm³/h
mwet=
913200 kg/h
mdry=
848000 kg/h
Vwater
84000 Nm³/h
mwatewr
65520 kg/h
T1=
48 °C
O2=
%(dry)
SO2=
200 mg/m³
SO2,6%O2=
219 mg/m³
14 废水流量的计算
假定烟气中HCl的浓度CHCl,fluegas=
取
Qa’=
6.8 m³/kg
3
标准状况下理论烟气量(空气含湿量为12.93g/m ³)
Qs’=
1.867(CY+0.375SY)+11.2HY+1.24WY+0.016Qa'+0.79Qa'+0.8NY
=
7.345681 m³/kg
4 标准状况下实际烟气量
取
Qs’=
7.35 m³/kg
空气过剩系数
α=
mhydrocyclone,underflow s,hydrocyclone,underflow
=
石灰石石膏湿法脱硫物料衡算(简单步骤)
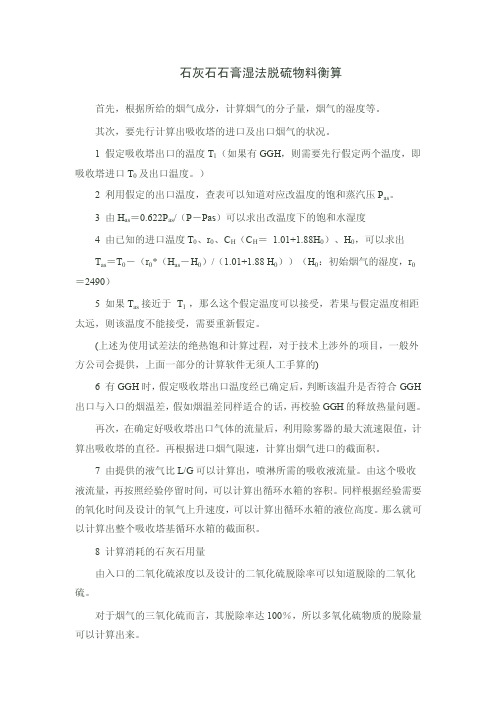
石灰石石膏湿法脱硫物料衡算首先,根据所给的烟气成分,计算烟气的分子量,烟气的湿度等。
其次,要先行计算出吸收塔的进口及出口烟气的状况。
1 假定吸收塔出口的温度T1(如果有GGH,则需要先行假定两个温度,即吸收塔进口T0及出口温度。
)2 利用假定的出口温度,查表可以知道对应改温度的饱和蒸汽压P as。
3 由H as=0.622P as/(P-Pas)可以求出改温度下的饱和水湿度4 由已知的进口温度T0、r0、C H(C H= 1.01+1.88H0)、H0,可以求出T as=T0-(r0*(H as-H0)/(1.01+1.88 H0))(H0:初始烟气的湿度,r0=2490)5 如果T as接近于T1,那么这个假定温度可以接受,若果与假定温度相距太远,则该温度不能接受,需要重新假定。
(上述为使用试差法的绝热饱和计算过程,对于技术上涉外的项目,一般外方公司会提供,上面一部分的计算软件无须人工手算的)6 有GGH时,假定吸收塔出口温度经已确定后,判断该温升是否符合GGH 出口与入口的烟温差,假如烟温差同样适合的话,再校验GGH的释放热量问题。
再次,在确定好吸收塔出口气体的流量后,利用除雾器的最大流速限值,计算出吸收塔的直径。
再根据进口烟气限速,计算出烟气进口的截面积。
7 由提供的液气比L/G可以计算出,喷淋所需的吸收液流量。
由这个吸收液流量,再按照经验停留时间,可以计算出循环水箱的容积。
同样根据经验需要的氧化时间及设计的氧气上升速度,可以计算出循环水箱的液位高度。
那么就可以计算出整个吸收塔基循环水箱的截面积。
8 计算消耗的石灰石用量由入口的二氧化硫浓度以及设计的二氧化硫脱除率可以知道脱除的二氧化硫。
对于烟气的三氧化硫而言,其脱除率达100%,所以多氧化硫物质的脱除量可以计算出来。
同样对于氯化氢、氟化氢而言,它们的脱除率一般在95%以上,因此可以计算到这两者的脱除量。
8.1 石灰石的计算消耗量石灰石的消耗量按照钙硫比及脱除氯/氟化物的消耗比可以计算出石灰石的实际消耗量。
脱硫系统采用石灰石粉经济性分析

采用石灰石粉作为吸收剂的经济性分析张江1. 情况简介我公司脱硫系统吸收剂原设计采用直径小于20mm的石灰石,经湿式球磨机研磨达到250目通过率大于90%、含固率25%的石灰石浆液。
两座吸收塔最大石灰石消耗量为10.3t/h,脱硫系统设计含硫量为0.67%,实际燃用煤种含硫量为0.52%,实际双塔消耗石灰石量为110-120t/天。
设1座混凝土石灰石储仓,储仓的总容量按2台锅炉在BMCR工况运行3天(日利用20 h 计)的石灰石耗量设计,有效容积为460m3。
经调研:大唐盘电公司因石灰石质量较差曾发生影响脱硫效率的问题,已将吸收剂改为石灰石粉,外购石灰石粉采取罐车运输,使用事故浆液箱作为石灰石粉混合箱,增加2台浆液输送泵实现向石灰石浆液箱供浆;大唐盘电公司原湿式球磨机浆液制备系统处于备用保养状态,计划占用一座灰库作为石灰石粉事故储仓。
国华浙能公司脱硫系统为干式球磨机石灰石粉制备系统,单台吸收塔区域设计有日石灰石粉储仓及2台浆液输送泵,石灰石粉运输采取罐车装载,满足脱硫系统运行需要。
2. 系统改造初步方案在现有石灰石料仓西侧增设石灰石粉仓,底部设浆液箱及2台浆液输送泵。
按2台锅炉在BMCR工况运行3天(日利用20 h 计)的石灰石粉耗量设计,两座吸收塔最大石灰石消耗量为10.3t/h,石灰石粉堆积密度按1.1 t/ m3计算,需要增加容积560m3石灰石粉仓(底部设置气化装置)、增加两台给料机、粉仓顶部设置布袋除尘器。
外购的石灰石粉由封闭式罐车运输,使用罐车自带气源将石灰石粉送入石灰石粉仓。
通过粉仓底部电动给料机、落粉管进入浆液箱,按加水搅拌后,通过浆液循环泵输送至浆液供应箱,供脱硫系统运行消耗。
电动给料机出力按15t/h考虑,浆液混配箱有效容积需达到75 m3,混配箱实际容积需达到90 m3,(直径5.4米,高4米),两座吸收塔最大石灰石消耗量为10.3t/h,按20h计算,需配置浆液206吨,每日混配箱系统需运行14小时,(目前实际日消耗石灰石120吨,每日混配箱系统需运行8小时。
电厂脱硫用石灰石标准

电厂脱硫用石灰石标准电厂脱硫是指利用石灰石等原料制备石灰乳,通过喷射或浆液法将石灰乳喷入烟气中,与烟气中的二氧化硫发生化学反应,将二氧化硫转化为硫酸盐,达到减少大气污染的目的。
在电厂脱硫工艺中,石灰石的质量和标准对脱硫效果起着至关重要的作用。
本文将介绍电厂脱硫用石灰石的标准及相关要求。
首先,电厂脱硫用石灰石应符合国家相关标准,包括石灰石的化学成分、颗粒大小、含水量、堆积密度等指标。
其中,化学成分是石灰石的重要特征之一,主要包括钙含量、镁含量、硅含量等。
合格的石灰石应具有较高的钙含量,低的镁含量和硅含量,以保证脱硫反应的高效进行。
此外,石灰石的颗粒大小和含水量也直接影响着脱硫工艺的稳定性和效果,因此在选用石灰石时需严格按照标准要求进行筛选和检测。
其次,电厂脱硫用石灰石的标准还包括了石灰石的采购、储存和使用等方面的要求。
在采购环节,应选择具有生产许可证和质量合格证明的正规生产厂家,避免购买劣质产品影响脱硫效果。
在储存和使用过程中,石灰石应储存在干燥通风的库房内,避免受潮结块影响使用效果。
同时,在投入脱硫系统前,需对石灰石进行颗粒破碎和筛分,确保颗粒大小符合要求,以保证脱硫工艺的稳定运行。
最后,电厂脱硫用石灰石的标准也涉及了脱硫工艺中的操作和管理要求。
在脱硫系统运行中,需定期对石灰石投加量、浆液浓度、喷射均匀性等进行监测和调整,保证脱硫效果达到设计要求。
同时,对石灰石的消耗量和脱硫效率进行统计分析,及时发现和解决问题,确保脱硫系统的稳定运行。
总的来说,电厂脱硫用石灰石标准的制定和执行对于保障电厂脱硫工艺的稳定运行和脱硫效果的达标具有重要意义。
只有严格按照标准要求选择、采购、储存和使用石灰石,才能确保脱硫工艺的高效、稳定运行,减少大气污染,保护环境。
电厂脱硫石灰石用量计算公式
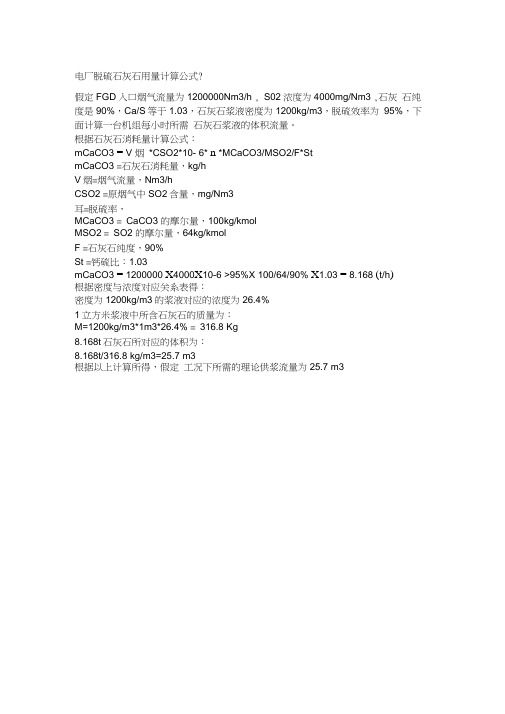
电厂脱硫石灰石用量计算公式?
假定FGD入口烟气流量为1200000Nm3/h , S02浓度为4000mg/Nm3 ,石灰石纯度是90%,Ca/S等于1.03,石灰石浆液密度为1200kg/m3,脱硫效率为95%,下面计算一台机组每小时所需石灰石浆液的体积流量。
根据石灰石消耗量计算公式:
mCaCO3 = V 烟*CSO2*10- 6* n *MCaCO3/MSO2/F*St
mCaCO3 =石灰石消耗量,kg/h
V烟=烟气流量,Nm3/h
CSO2 =原烟气中SO2含量,mg/Nm3
耳=脱硫率,
MCaCO3 = CaCO3 的摩尔量,100kg/kmol
MSO2 = SO2 的摩尔量,64kg/kmol
F =石灰石纯度,90%
St =钙硫比:1.03
mCaCO3 = 1200000 X4000X10-6 >95%X 100/64/90% X1.03 = 8.168 (t/h)
根据密度与浓度对应关系表得:
密度为1200kg/m3的浆液对应的浓度为26.4%
1立方米浆液中所含石灰石的质量为:
M=1200kg/m3*1m3*26.4% = 316.8 Kg
8.168t石灰石所对应的体积为:
8.168t/316.8 kg/m3=25.7 m3
根据以上计算所得,假定工况下所需的理论供浆流量为25.7 m3。
某机组脱硫系统石灰石粉耗升高的分析与研究

某机组脱硫系统石灰石粉耗升高的分析与研究发布时间:2021-05-08T03:04:36.532Z 来源:《中国电业》(发电)》2021年第1期作者:李波[导读] 石灰石粉耗增加一方面造成脱硫系统经济性下降,同时对脱硫系统的安全运行带来不利影响。
平顶山姚孟发电有限责任公司河南省平顶山市 467000摘要:本文主要结合某机组脱硫系统石灰石粉耗升高的事件,综合分析引起石灰石粉耗异常升高的原因,进而从原因着手,从系统运行方式优化、消泡剂规范使用、运行精细化调整等方面提出针对性的措施,解决了石灰石粉耗异常升高的技术难题,提高了脱硫系统运行的经济性,保障了脱硫系统的安全运行。
关键词:石灰石粉耗;石膏浆液;精细化调整Analysis and research on the increase of limestone powder consumption in desulfurization system of a unitLiBoPingDingShanYaoMengPowerGenerationCo.,Ltd, pingdingshan,467000,ChinaSummary:In this paper, the causes of the abnormal increase of limestone powder consumption in the desulfurization system of a unit are comprehensively analyzed, and then the causes are analyzed, from the aspects of system operation mode optimization, standard use of Defoamer, fine operation adjustment and so on, pointed measures are put forward to solve the technical problem of abnormal increase of limestone powder consumption and improve the operating economy of the desulfurization system, the Safe Operation of the desulfurization system is ensured.Key words: Limestone powder consumption, gypsum slurry, fine adjustment0前言目前火电厂脱硫系统大多采用石灰石-石膏湿法脱硫工艺,但是随着环保管控的日益严格,尤其是超洁净排放改造后,脱硫系统上游以及脱硫系统本身的因素,引起脱硫系统石灰石粉耗的增加成为行业内比较突出的问题,石灰石粉耗增加一方面造成脱硫系统经济性下降,同时对脱硫系统的安全运行带来不利影响。
- 1、下载文档前请自行甄别文档内容的完整性,平台不提供额外的编辑、内容补充、找答案等附加服务。
- 2、"仅部分预览"的文档,不可在线预览部分如存在完整性等问题,可反馈申请退款(可完整预览的文档不适用该条件!)。
- 3、如文档侵犯您的权益,请联系客服反馈,我们会尽快为您处理(人工客服工作时间:9:00-18:30)。
湿法脱硫系统石灰石耗量分析
经过“十一五”的大力推进,烟气脱硫技术已在我国活
力发电行业得到了广泛的应用,对于脱硫系统的研究也日渐深入细致,在“十二五”大力倡导节能减排的背景下,通过运行优化,实现脱硫系统的经济运行,就成了目前的一个重要研究领域I 。
石灰石是脱硫反应的吸收剂,耗量较大,是脱硫系统运
行成本的主要组成部分,石灰石耗量与设计值发生较大偏差,不仅会直接造成脱硫运行成本的攀升,而且也会对吸收塔浆液品质、脱水系统运行工况等产生一定影响,因此石灰石耗量分析也就成为了石灰石.石膏脱硫系统节能优化运行的要重点研究的问题。
为了分析实际运行中石灰石耗量偏差情况,找出影响石
灰石消耗量的主要因素,进而提高石灰石在脱硫反应中的利用率,降低运行成本,因此在某2×600 Mw 机组配套脱硫系统上进行了石灰石耗量分析的相关试验。
1 石灰石耗量计算
理论上,石灰石中所含的有效脱硫成分,即CaCO,在
脱硫反应中与烟气中的SO:按照理论钙硫比发生反应,因此理论石灰石耗量是指脱硫系统在设计Ca/S比条件下,按照脱除SO2量计算得出的所需石灰石量。
计算公式如下:M~:—Qsnd~(C—
sl-Cs2)××
⋯ l000000 64
式中:Mcaco3——理论石灰石耗量,kg/ll;Q5 d——标干烟
气量, Nm ha(6%02); csl一一原烟气s02浓度,
mg/Nm (6%02);Cs2一一净烟气SO2浓度,mg/Nm (6%O2);收稿日期:2012.12-10
戴新(1970一),男,高级工程师。
丰镇,012100
n一一石灰石纯度,试验期间为89.4%;——设计钙硫比, 1.03。
实际脱硫反应中,由于石灰石反应活性、杂质含量等因
素影响,石灰石实际耗量会与理论值存在一定偏差,通常实际石灰石消耗量是通过实际脱硫反应中投加到吸收塔内的
石灰石浆液量和浆液密度计算得出,计算公式如下:
M c 川
式中:^ aCO3——实际石灰石耗量,kg/h; P ——石灰石
密度,P =2.6 g/cm ;P ——石灰石浆液密度,g/cm ;——每小时石灰石浆液量,m /h。
理论石灰石耗量和实际石灰石耗量之差,可以在一定程
度上反应石灰石在实际脱硫反应中的活性(投加过量石灰石,造成浆液过饱和,也会增加石灰石实际耗量)。
不同负
荷条件下理论石灰石耗量和实际石灰石耗量对比见表1。
根据上述试验结果计算可出,不同负荷下理论石灰石耗
量均值为4.493 t/h,而实际石灰石耗量均值为5.61 1 t /h,石
灰石多耗用量平均值为1.1l8 ,每天多消耗石灰石约27 t,该厂石灰石进厂价为200元/t,按每运行6000 h计算,由于
理论石灰石耗量和实际石灰石耗量偏差,每年每套脱硫系统运行成本增加134万元,长期运行不仅会大大增加电厂的运行成本,还会造成浆液未反应的碳酸钙含量增加,致使石膏脱水系统运行故障,系统结垢堵塞、浆液过饱和失效的风险大大增加,不利于系统安全稳定运行
2 石灰石耗量影响因素分析
实际运行过程中造成理论石灰石耗量和实际石灰石耗
量偏差较大的原因包括吸收塔浆液pH值控制不当、石灰石28 电站系统工程 2013年第29卷
活性低、石灰石粒度偏高、石灰石及浆液中杂质多等。
为此,就上述影响因素分别进行了石灰石耗量影响试验。
表l 不同负荷下理论石灰石耗量与实际石灰石耗量对比
投运浆液泵浆液pH值石灰石耗量,t·h 出口SO2浓度/mg·m 石灰石成本/元·h。
SO2排污费/元.h 两项合计费用/元.h’
2.1 吸收塔浆液pH影响试验
石灰石的消溶过程要消耗H ,使浆液呈碱性,而石灰
石浆液H 扩散驱动力与浆液的pH值成反比关系,故较低的浆液pH值将使反应向有利于石灰石溶解的方向进行,但pH 值低时H+浓度高,会增加SO:气相阻力,不利于脱硫效率的提高[5】'通常将吸收塔浆液pH值控制在5.2~5.8之间。
从运行经济性的角度考虑,提高pH值,亚硫酸钙的氧
化和石灰石的溶解受到严重抑制,产品中出现大量难以脱水的亚硫酸钙,石灰石的利用率下降,随石膏排出吸收塔未反应的过量石灰石也随之增加(从石膏分析结果看来,部分时段石膏中CaCO 含量高达3.5%,正常情况应低于l%),同时高pH值也会增加系统结构堵塞的风险。
pH变化会引起
石灰石耗量和出口SO2浓度变化,石灰石运行成本和排污费随之变化,500MW 负荷下,pH对石灰石耗量影响见表2。
从表2可以看出,pH值由5_3提高至5.5石灰石浆液耗
量增加1.04 ,增幅为20.7%,脱硫系统运行费用增加16.72%。
此负荷及入口SO2浓度条件下,pH为5.3时,脱
硫系统运行成本最低,但pH低于5.5时,脱硫效率低于90%,因此该负荷条件下pH应保持在5.5左右。
2.2 石灰石粒度影响试验
石灰石颗粒的粒度越小,质量比表面积就越大,其反应
速率也就越大(反应速率与石灰石颗粒比表面积成正比),因此较细的石灰石颗粒的消溶特性就越好,石灰石的利用率相应提高。
但无论在用石灰石粉还是湿式球磨机制浆系统,石灰石粒度越小,就意味着制浆系统所需能耗越高,二者存在平衡关系。
以250目和325目两种粒度为例,利用率与经济性对比见表3。
表3 石灰石粒度对运行成本影响
石灰石反应活性是衡量石灰石品质的一个重要指标,脱
除SO2所需的碱量是通过石灰石粉的溶解来提供,吸收剂的活性会影响石灰石的溶解度和溶解速度,是表示一种在酸性环境中的转化特性。
吸收剂的活性包含吸收荆种类、物化特性和与其反应的酸性环境。
活性较高的石灰石在保持相同石灰石利用率的情况下,在要求相同SO2脱除效率的情况下,石灰石耗量较低。
石灰石反应活性高,石灰石利用率也高,石膏中过剩CaCO 含量低,即石膏纯度高。
不同活性石灰
石耗量见表4。
表4 不同活性石灰石粒度对运行成本影响
可以看出,活性较大的石灰石利用率明显高于低活性石
灰石,同等条件下石灰石耗量较低。
在石灰石原料相对稳定的条件下,可以通过向吸收塔浆液添加有机酸等增效剂,提高石灰石溶解速率的方式来提高石灰石的反应活性。
在吸收
塔浆液中按10 mmol/L的浓度加入DBA后,石灰石溶解速率变化见表5。
表4 不DBA对石灰石溶解速率的影响
溶解速率/% 5min 10min 20min 30min 40min 50min
未加DBA 8.89 11.52 18.15 19.86 21.16 27.64
塑旦里堡垒 !: !:: !!: ! ! :! !: !
可以看出,加入有机酸后,石灰石溶解速率显著增加。
加入DBA后,液相主体中的pH值降低,使得液相主体和
石灰石颗粒表面H 的浓度差增大,从而促进了H 从液相主体向石灰石颗粒表面的传质而增大了石灰石的溶解速率,促进CaCO 在液相的溶解,提高了石灰石的利用率。
嚣粒度,元. h 耗量,1. h 耗量,t. h 石率,%用嚣本/t. h 3结日论
250目 200 3.98 5.02 79.28 1004
325目 220 3.98 4 59 86.71 1010
从表2可以看出,提高石灰石粒度可以显著提高石灰石
的利用率,降低石灰石耗量,但同时石灰石原料成本价增加,总的运行成本略有增加,通常综合考虑粒度对石灰石利用率和成本的影响,石灰石粉粒度控制在为250~325目,具体
控制指标应根据当地石灰石原料价格及利用率综合考量。
2.3 石灰石活性影响试验
(1) 石灰石耗量对湿法脱硫系统运行成本影响较大,提
高石灰石利用率可以有效节约运行成本;
(2) 降低pH有利于石灰石溶解,但会增加SO 吸收阻
力,一般控制浆液pH为5.2~5.8之间:
(3) 石灰石粒度越小,利用率越高,可以降低石灰石耗
量,但也会增加石灰石原料的加工成本,应根据当地石灰石原料价格及利用率综合考量选择合适的石灰(下转第31页) 第3期张步庭等:燃烧调整对NO 排放和锅炉效率的影响 3 l
高NO 排放浓度较大,氧量3.36%32况锅炉效率较高、NO 排放浓度较低。
3.4_3 180 Mw 负荷氧量调整试验
180 MW 负荷氧量调整试验在3个工况下进行,采用缩
腰配风方式,燃尽风全关。
随着氧量的升高,NO 排放浓度升高,灰渣含碳量下降、排烟温度升高、锅炉效率下降。
表8 机组180 MW 负荷下氧量影响
3 结论
通过对300 Mw 亚临界机组双炉膛、四角切圆锅炉的燃
烧调整试验,得到了运行因素对NO 排放、锅炉效率的影响,对同类型锅炉设备的运行调整、改造有一定的借鉴意义。
试验主要结论如下。
(1) 一次风速升高,有利于降低NO ,但是锅炉效率
也会下降。
(2) 配风方式对NO 排放影响较小,针对该锅炉缩腰
配风方式锅炉效率较高、NO 排放较少。
(3) 燃尽风对NO 排放影响较大,随着燃尽风量增加、
NO 排放浓度明显降低,锅炉效率略有下降。
(4) 氧量对NO 排放规律明显,随着氧量增加,NO
排放浓度增加;锅炉效率则需要根据g2、q 情况确定最佳氧量。