做强科室核心业务,提升公司资源和装备管理能力(设备设施科)111011
设备科年度工作总结——提升设备运行效率,促进企业转型升级
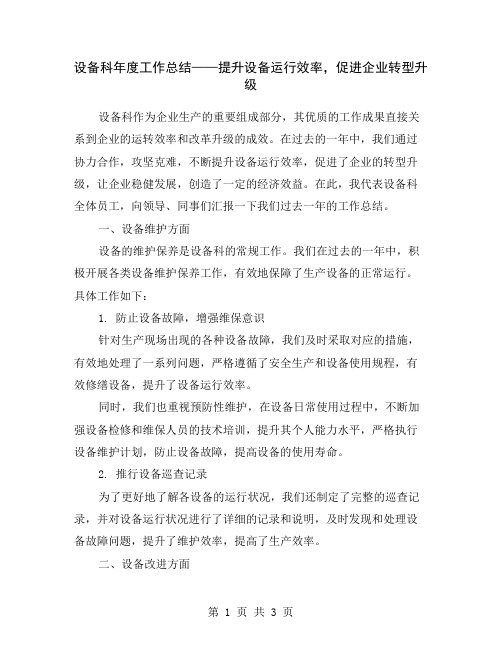
设备科年度工作总结——提升设备运行效率,促进企业转型升级设备科作为企业生产的重要组成部分,其优质的工作成果直接关系到企业的运转效率和改革升级的成效。
在过去的一年中,我们通过协力合作,攻坚克难,不断提升设备运行效率,促进了企业的转型升级,让企业稳健发展,创造了一定的经济效益。
在此,我代表设备科全体员工,向领导、同事们汇报一下我们过去一年的工作总结。
一、设备维护方面设备的维护保养是设备科的常规工作。
我们在过去的一年中,积极开展各类设备维护保养工作,有效地保障了生产设备的正常运行。
具体工作如下:1. 防止设备故障,增强维保意识针对生产现场出现的各种设备故障,我们及时采取对应的措施,有效地处理了一系列问题,严格遵循了安全生产和设备使用规程,有效修缮设备,提升了设备运行效率。
同时,我们也重视预防性维护,在设备日常使用过程中,不断加强设备检修和维保人员的技术培训,提升其个人能力水平,严格执行设备维护计划,防止设备故障,提高设备的使用寿命。
2. 推行设备巡查记录为了更好地了解各设备的运行状况,我们还制定了完整的巡查记录,并对设备运行状况进行了详细的记录和说明,及时发现和处理设备故障问题,提升了维护效率,提高了生产效率。
二、设备改进方面在企业经济增长的背景下,不断推进设备改进,运用新的技术和设备,以满足市场需求,适应经济发展的快速变化。
设备科在过去一年也取得了不少的成绩,具体工作如下:1. 新设备引进为了满足多元化的市场需求,我们不断引进新的先进技术和新型设备,具备了更强的生产力和竞争力。
在研发新设备和引进新技术的过程中,我们特别重视准确了解市场需求。
并且,我们也以市场反馈为指导,定期优化设备的配置和使用方法,以提高设备的生产效率和性能。
2. 设备智能化升级生产自动化、智能化水平越来越高,我们设备科也积极响应国家政策,大力推进设备的智能化升级工作。
通过对现有设备的差异化改善和智能化升级,不仅能够提升生产效率,减少人力成本,同时,还能够提高生产环境的清洁度,保障生产的安全性。
科室提升业务能力方案

科室提升业务能力方案在如今的竞争激烈的医疗行业,科室提升其业务能力是非常重要的。
那么,该如何提升呢?在本文里,我们将提出一些可行的方案。
1. 加强人员培训人员培训是科室提升业务能力的基础。
精心设计培训计划,培训不仅应包括新员工,也包括老员工,以保证他们的信息更新和技能更新。
为此,我们可以考虑采取以下培训方式:•在线培训课程:如今,许多知名医疗机构为人员提供在线培训课程。
这些课程的优点是成本低、灵活、可定制等。
•现场培训:现场参观和探讨可以帮助员工更好地理解科室的业务,加深他们对业务的理解和认识。
•培训班、研讨会:这种形式的培训可以让员工深度学习和掌握某一具体的领域的知识,从而提高其能力。
2. 开展专项业务学习活动专项学习活动指的是以业务为主题,针对性开展的学习活动。
如今,各地培训机构、高校和科技企业都开展了各种形式的学习活动,我们可以积极参与这些活动。
这样不仅可以增加员工对市场的敏感度和业务知识,还可以拓宽员工的视野,了解其他同行的做法和成功经验。
3. 开展科研项目科研项目可以让科室的员工不仅掌握科学知识,也可以接触到行业内前沿技术或科研项目。
在开展科研项目过程中,员工不断地迭代、逐渐完善手段和方法,练就了优秀的技能。
通过科研项目,员工将会有更加深刻的理解,并不断提升自己的能力水平,这将为科室发展提供源源不断的添砖加瓦。
4. 营造良好氛围良好的团队氛围是提升业务能力的核心。
我们应该通过制定良好的团队建设计划,培养成员间互帮互助、相互扶持的良好氛围。
在工作中,我们应该激发员工的工作热情和创造力,让每个人都尽情发挥自己的才能。
通过这种方式,就可以凝聚起团队的能量,使团队在协调一致的情况下顺畅地进行业务的开展和发展。
结语科室提升业务能力不是一朝一夕的事情,需要全体成员的努力和贡献。
作为科室领导者,应该改变传统的管理模式,了解员工的需求,并制定相应的解决方案。
通过加强人员培训、开展专项业务学习活动、开展科研项目和营造良好氛围等措施,科室才能够不断提升业务水平,为患者提供更加优质的服务。
设备部门的职能与岗位职责的持续优化与提升
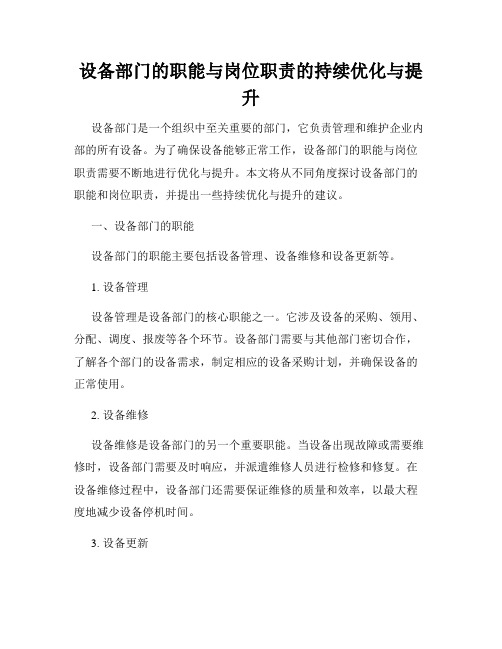
设备部门的职能与岗位职责的持续优化与提升设备部门是一个组织中至关重要的部门,它负责管理和维护企业内部的所有设备。
为了确保设备能够正常工作,设备部门的职能与岗位职责需要不断地进行优化与提升。
本文将从不同角度探讨设备部门的职能和岗位职责,并提出一些持续优化与提升的建议。
一、设备部门的职能设备部门的职能主要包括设备管理、设备维修和设备更新等。
1. 设备管理设备管理是设备部门的核心职能之一。
它涉及设备的采购、领用、分配、调度、报废等各个环节。
设备部门需要与其他部门密切合作,了解各个部门的设备需求,制定相应的设备采购计划,并确保设备的正常使用。
2. 设备维修设备维修是设备部门的另一个重要职能。
当设备出现故障或需要维修时,设备部门需要及时响应,并派遣维修人员进行检修和修复。
在设备维修过程中,设备部门还需要保证维修的质量和效率,以最大程度地减少设备停机时间。
3. 设备更新设备更新是设备部门的长期职能之一。
由于科技的不断进步和设备老化的现象,设备部门需要定期评估和更新现有设备。
通过更新设备,企业可以提高生产效率,降低维修成本,保持竞争力。
二、设备部门的岗位职责设备部门涉及的岗位职责包括设备管理员、设备维修工程师和设备更新规划员等。
1. 设备管理员设备管理员负责设备的管理和调度。
他们需要进行设备的登记和分类,并负责设备的存放和领用。
同时,设备管理员还需要根据各部门的需求,合理安排设备的使用和分配。
2. 设备维修工程师设备维修工程师是设备部门的核心力量。
他们负责设备的检修和维护,并及时解决设备故障。
设备维修工程师还需要定期进行设备的保养,以延长设备的使用寿命。
3. 设备更新规划员设备更新规划员负责评估和规划设备的更新工作。
他们需要与其他部门合作,了解企业的发展需求和设备的更新周期,制定合理的设备更新计划,并通过预算等方式寻找适合的设备供应商。
三、持续优化与提升的建议为了不断提升设备部门的职能与岗位职责,以下是一些建议。
提升部门人员的业务能力,计划实施方法

提升部门人员的业务能力,计划实施方法说实话提升部门人员业务能力这事,我一开始也是瞎摸索。
我试过搞那种集中培训,把大家都聚在一起,就像把一群小鸭子赶到一起上课一样。
我请了公司里比较厉害的前辈来当讲师。
可是呢,效果不太好。
为啥呢?因为太枯燥啦,大家就像听天书似的,听得迷迷糊糊。
也不管听懂没听懂,好像完成任务一样坐在那。
我这才知道,光靠这种传统的集中培训可不行。
后来我又想,也许一对一辅导会好点。
这就好比给每棵小树苗单独浇水施肥。
我自己亲自上阵,辅导了几个员工。
可麻烦来了,这效率低得很,我自己也疲惫不堪,而且其他员工会觉得不公平,怎么他们没有这种特殊待遇呢。
再后来呀,我觉得实践出真知。
就给大家扔到实际项目里,让他们自己摸着石头过河。
结果就乱套了,业务新手完全不知所措,老员工也是压力山大,边做项目边骂我这个决策愚蠢。
经过这几次失败,我终于有点觉悟了。
我弄出了个混合的办法。
首先呢,还是继续搞培训,但我让培训变得更有趣。
举个例子,讲销售技巧的时候,找了些搞笑的营销案例视频给大家放,然后展开讨论,这就像在游戏里找攻略一样,大家积极性一下就起来了。
其次呢,就是搞模拟项目。
不是直接上真项目,大家分组来模拟操作,小组之间还可以竞争。
谁要是表现好呢,就奖励小礼品,这就像小时候谁考一百分就奖励个小红花一样。
这时候大家都特用心,毕竟谁也不想被比下去啊。
我现在也还在摸索,不确定还有没有更好的方法。
不过我觉得让业务强的同事分享经验也很重要,有人可能想问,这和培训不差不多吗?不一样的,培训比较官方,同事分享就像朋友唠嗑,更轻松更实用。
在分享的时候,我会让分享者重点说自己遇到的坑是怎么爬出来的,这样别人也能学到很多真东西。
还有一点我觉得也不能忽视,那就是要给员工一些自我学习的时间和资源。
就好比给你一块地,你想种啥自己决定,但是我给你种子和工具。
我在办公室里设了个小书架,放了很多专业书籍,也给了大家线上学习的账号,他们可以根据自己的短板去学习提升。
做强科室核心业务,提升公司资源和装备管理能力(设备设施科)111011范文

做强科室核心业务,提升公司资源和装备管理能力设备设施科作为技术部主管设备设施运行管理的部门,在完善和强化体系能力、推进预防保全、控制运行成本、提升资源保障能力、及厂房设施建设等方面均做了大量的努力,并逐步取得成效。
目前设备设施科面临三个主要课题:提升设备可动率、控制维修成本和培训维修人员能力,由于维修系统资源分散在工厂各车间,从而对设备设施科体系管理和协调能力提出了考验。
围绕这三个课题,结合科室核心业务,我们拟从如下七个方面进行能力提升。
一、提升科内各岗位业务能力,改善工作效率随着公司的发展,设备科业务的不断重新认识和扩大,逐步显现出人力资源不足的问题,从而导致部分人员重复兼岗,负荷较重,部分人员岗位与工作内容不匹配。
纠其原因,除了硬性的岗位资源得不到公司及时补充之外,还有科室人员自身能力问题。
部分人员业务能力不强、工作主动性不够,缺乏忧患意识。
我们的对策是:1、继续开展业务交流及培训,各岗位清晰岗位职责和工作流程。
年内,科内进行了多轮业务交流及培训,初步明晰了相关人员对流程、岗位职能等的认识。
在此基础上,我们将结合技术部的整体培训计划,逐步针对岗位基础技能和专用技能进行培训,有效提升人员工作能力和效率。
2、建立各岗位工作标准及目标,并以此评价个人工作。
我们将对科长KPI指标进行分解,真正落实到个人,发挥个人绩效考核的推动作用。
为确保目标完成,逐步通过标准化工作,明确各岗位工作标准,使所有人员知道应该做什么,怎么去做。
我们将利用科周例会或专题学习会,让各岗位轮流讲解岗位说明书,在交流和互动中,提升全体人员对岗位责任的认知。
3、公平、公正、公开,调动和提升各岗位人员能动性。
严格考核,从考勤、业务能力、工作量、工作质量、固定指标完成情况等多个维度评价科内人员,利用科务会进行总结、评点、通报,并结合适度的奖惩,个人约谈等措施,本着公平、公正、公开的原则,调动和提升各岗位人员主观能动性。
4、加强计划管理。
怎样干好设备科工作总结

怎样干好设备科工作总结
设备科工作是一个需要高度专业知识和技能的领域,它涉及到设备的安装、维护、保养和修理等工作。
在这个领域里,要想取得好的成绩,需要具备一定的工作技巧和方法。
下面就让我们一起来总结一下怎样才能干好设备科工作。
首先,要有扎实的专业知识。
设备科工作是一个高度专业化的领域,需要掌握
大量的专业知识才能胜任。
因此,作为一名设备科工作者,首先要对设备的结构、原理、工作方式等方面有深入的了解,只有这样才能在实际工作中做到游刃有余。
其次,要具备良好的技术技能。
设备科工作需要具备一定的技术技能,比如焊接、电气维修、机械维修等。
这些技能是设备科工作的基础,只有掌握了这些技能,才能在实际工作中解决各种设备故障和问题。
再次,要有丰富的实践经验。
在设备科工作中,实践经验是非常重要的。
只有
通过实际的工作实践,才能不断积累经验,提高工作能力。
因此,作为一名设备科工作者,要多参与实际工作,积累丰富的实践经验。
最后,要注重团队合作。
设备科工作往往需要多人合作完成,因此,团队合作
能力也是非常重要的。
在工作中,要善于与同事合作,共同解决问题,提高工作效率。
总之,要想干好设备科工作,需要具备扎实的专业知识、良好的技术技能、丰
富的实践经验和良好的团队合作能力。
只有这样,才能在设备科工作中取得好的成绩。
设备科个人工作总结:提升团队效率的关键

设备科个人工作总结:提升团队效率的关键20xx年是一个充满挑战的一年,虽然我们也经历着各种阵痛与挣扎,但我们最终还是熬过了这一年。
回顾过去,我认为我们设备科团队的一个重要任务是提升团队效率,这也是我们在未来的工作中需要一直追寻的目标。
下面是我对这一目标的一些思考和总结:一、掌握项目管理的关键项目管理是我们工作中最基本也是最重要的技能之一。
通过对项目的掌控和管理,我们可以有效地提升团队效率。
具体来说,我们需要掌握以下技能:1.项目计划管理。
通过有效的计划管理,我们可以确保项目按时完成,避免时间和资源的浪费。
2.风险管理。
在项目执行过程中,我们需要时刻警惕各种可能发生的风险,及时采取措施,以确保项目的成功完成。
3.沟通管理。
沟通是项目管理中最重要的一环。
我们需要保证沟通的及时、准确、有效,避免各种沟通误解和信息断层。
二、技术能力与创新意识的结合在设备科团队中,我们需要不断提升技术能力,不断探索新的技术路径。
对于技术人员来说,技术能力的提升是我们工作的核心,但技术能力的提升不能停留在与当前技术相关的范围中,我们还需要具备创新意识,学会将不同的技术、工具和方法相互结合,融入到实际的项目中,解决实际问题,提升工作效率。
三、团队协作与领导力的培养团队协作和领导力的培养是设备科团队升级提升的关键。
在团队级别上,我们需要不断加强团队协作。
无论是在技术领域还是管理方面,我们都需要团队协作的力量才能更好地完成我们的任务。
同时,在管理层面上,我们需要培养一批有领导力的人才,带领团队向前发展。
四、学习与反思在团队提升的过程中,学习和反思尤为重要。
我们需要密切关注项目执行过程中的各种问题和细节,及时进行反思和总结。
同时,我们还需要持续地学习新的知识和技能,保持快速学习和适应能力。
总之,提升团队效率是设备科团队未来工作的重要目标。
我们需要掌握项目管理、发挥创新意识、强化团队协作和领导力、持续学习和反思。
相信我们设备科团队在不断努力下,未来的发展一定会更加美好。
公司设备科年度总结(3篇)
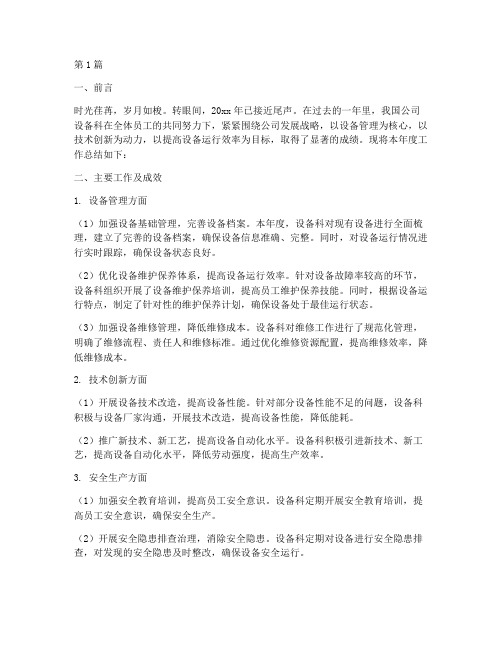
第1篇一、前言时光荏苒,岁月如梭。
转眼间,20xx年已接近尾声。
在过去的一年里,我国公司设备科在全体员工的共同努力下,紧紧围绕公司发展战略,以设备管理为核心,以技术创新为动力,以提高设备运行效率为目标,取得了显著的成绩。
现将本年度工作总结如下:二、主要工作及成效1. 设备管理方面(1)加强设备基础管理,完善设备档案。
本年度,设备科对现有设备进行全面梳理,建立了完善的设备档案,确保设备信息准确、完整。
同时,对设备运行情况进行实时跟踪,确保设备状态良好。
(2)优化设备维护保养体系,提高设备运行效率。
针对设备故障率较高的环节,设备科组织开展了设备维护保养培训,提高员工维护保养技能。
同时,根据设备运行特点,制定了针对性的维护保养计划,确保设备处于最佳运行状态。
(3)加强设备维修管理,降低维修成本。
设备科对维修工作进行了规范化管理,明确了维修流程、责任人和维修标准。
通过优化维修资源配置,提高维修效率,降低维修成本。
2. 技术创新方面(1)开展设备技术改造,提高设备性能。
针对部分设备性能不足的问题,设备科积极与设备厂家沟通,开展技术改造,提高设备性能,降低能耗。
(2)推广新技术、新工艺,提高设备自动化水平。
设备科积极引进新技术、新工艺,提高设备自动化水平,降低劳动强度,提高生产效率。
3. 安全生产方面(1)加强安全教育培训,提高员工安全意识。
设备科定期开展安全教育培训,提高员工安全意识,确保安全生产。
(2)开展安全隐患排查治理,消除安全隐患。
设备科定期对设备进行安全隐患排查,对发现的安全隐患及时整改,确保设备安全运行。
(3)加强应急管理,提高应急处置能力。
设备科制定了应急预案,并定期组织应急演练,提高应急处置能力。
4. 节能减排方面(1)加强能源管理,降低能源消耗。
设备科对设备能耗进行实时监测,发现异常情况及时处理,降低能源消耗。
(2)推广节能技术,提高能源利用效率。
设备科积极推广节能技术,提高能源利用效率,降低企业运营成本。
设备科新版工作计划
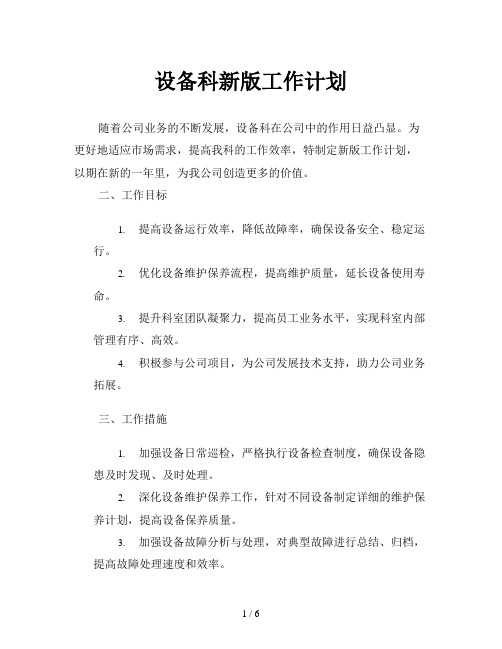
设备科新版工作计划随着公司业务的不断发展,设备科在公司中的作用日益凸显。
为更好地适应市场需求,提高我科的工作效率,特制定新版工作计划,以期在新的一年里,为我公司创造更多的价值。
二、工作目标1.提高设备运行效率,降低故障率,确保设备安全、稳定运行。
2.优化设备维护保养流程,提高维护质量,延长设备使用寿命。
3.提升科室团队凝聚力,提高员工业务水平,实现科室内部管理有序、高效。
4.积极参与公司项目,为公司发展技术支持,助力公司业务拓展。
三、工作措施1.加强设备日常巡检,严格执行设备检查制度,确保设备隐患及时发现、及时处理。
2.深化设备维护保养工作,针对不同设备制定详细的维护保养计划,提高设备保养质量。
3.加强设备故障分析与处理,对典型故障进行总结、归档,提高故障处理速度和效率。
4.积极开展设备改造升级工作,根据公司需求和技术发展,引进新技术、新设备,提升设备性能。
5.加强科室内部培训,提高员工业务水平,提升团队整体素质。
6.加强与其他科室的沟通与协作,形成工作合力,共同推进公司业务发展。
四、工作进度安排1.第一季度:完成设备检查制度的修订,加强日常巡检,对设备进行一轮全面维护保养。
2.第二季度:开展设备故障分析与处理培训,提高科室员工故障处理能力。
3.第三季度:针对设备运行情况,进行设备改造升级,提升设备性能。
4.第四季度:组织科室内部培训,提高员工业务水平,提升团队整体素质。
五、工作总结本计划执行周期为一年,期间科室需严格按照计划开展工作,并根据实际情况进行调整。
年底对各项工作进行总结,分析计划的实施效果,为下一版计划的制定依据。
本计划自发布之日起执行,如有未尽事宜,可根据实际情况予以调整。
科室全体成员应认真贯彻执行,共同推进科室工作发展。
《篇二》设备科新版工作计划一、工作目标1.提高设备运行效率,降低故障率,确保设备安全、稳定运行。
2.优化设备维护保养流程,提高维护质量,延长设备使用寿命。
3.提升科室团队凝聚力,提高员工业务水平,实现科室内部管理有序、高效。
设备科工作计划(精选)

设备科工作计划(精选)一、背景分析设备科作为公司的重要部门,主要负责公司设备的购置、维护和管理工作,对公司的运营和生产发挥着关键作用。
在当前市场竞争激烈的情况下,不断提高设备科的工作效率和服务水平,对于公司的可持续发展至关重要。
二、工作目标1.提高设备科内部管理水平,确保设备的正常运行和可靠性。
2.优化设备采购流程,降低采购成本,并保证采购设备的质量和性能。
3.完善设备维护体系,确保设备的正常运行和延长设备的使用寿命。
4.提升设备科员工的专业素质和工作效率,建设高素质的设备维护团队。
三、工作内容1.内部管理:(1)建立健全设备档案管理体系,完善设备台账,做到设备信息全面、准确。
(2)加强对设备维修和保养记录的统计和分析,及时发现设备故障和问题,并采取有效的措施进行处理。
(3)完善设备使用和管理制度,加强设备的使用和保养教育,提升设备管理水平。
2.设备采购:(1)建立标准的设备采购流程,明确采购责任,确保采购程序的公平、公正。
(2)与供应商建立长期稳定的合作关系,争取更好的采购价格和优质的产品。
(3)加强对设备市场的了解和跟踪,及时掌握新产品和新技术的信息,为公司创新发展提供支持。
3.设备维护:(1)建立设备维护计划,定期检查设备设施的运行状况,及时排除隐患,防止设备故障对生产造成影响。
(2)加强设备日常保养工作,包括清洁、润滑、调整等,保证设备的正常运行状态。
(3)加强设备故障排查和处理工作,提高故障处理的效率和准确性。
4.人员培训:(1)组织设备维修员工参加相关培训和学习,提高技术水平和维修能力。
(2)加强知识共享和团队建设,提高团队的凝聚力和协作性。
(3)定期开展设备维护培训,提高员工对设备维护工作的认识和重视程度。
四、工作计划1.制定设备管理制度和流程,于XX年X月前完成制定和审批,并向相关部门进行宣传和培训。
2.建立设备档案管理系统,于XX年X月前完成设备信息的录入和整理工作,并于每月定期更新。
科室管理能力提升工程方案

科室管理能力提升工程方案一、前言随着医疗行业的不断发展,科室管理在医院运营中的重要性日益凸显。
科室作为医院内部重要的组成部分,其管理能力的提升对于整个医院的运营效率和服务质量具有重要意义。
因此,科室管理能力的提升工程成为了当前医院发展的重要任务之一。
本文将围绕科室管理能力提升展开讨论,主要包括科室管理水平的现状分析、科室管理能力提升的必要性、提升科室管理能力的工程方案等内容。
通过此方案的实施,将有助于提升医院科室管理水平,促进医院整体发展。
二、科室管理水平的现状分析1.1 科室管理工作存在的问题目前,许多医院的科室管理工作存在一些普遍问题,主要表现在以下几个方面:(1)科室管理模式单一,缺乏创新性。
很多科室管理工作停留在传统的管理模式上,缺乏创新性,无法满足医院发展的需要。
(2)科室管理人员素质不高。
一些科室管理人员缺乏专业知识和管理技能,对科室管理规范认识不足,导致管理水平较低。
(3)科室管理工作流程不畅。
科室管理工作流程繁琐,沟通不畅,信息传递不及时,导致管理效率较低。
1.2 科室管理水平的局限性由于现有科室管理水平的局限性,导致了以下几个方面的问题:(1)科室管理效率低下,影响医院运营效率。
科室管理流程繁琐,效率低下,影响了医院的整体运营效率。
(2)科室管理质量参差不齐,影响医院服务质量。
由于科室管理水平不一,导致了各科室服务质量参差不齐,影响了患者体验和医院声誉。
(3)科室管理风险较高,影响医院发展稳定。
当前科室管理水平较低,存在着很多管理风险,如医疗事故风险、医疗纠纷风险等,严重影响了医院的发展稳定。
三、科室管理能力提升的必要性从上述现状分析可以看出,科室管理能力的提升具有迫切的必要性,主要表现在以下几个方面:3.1 提高医院运营效率科室管理能力的提升有助于优化科室管理流程,提高管理效率,从而提高医院整体的运营效率。
科室管理工作的便捷化和信息化将为医院的整体管理工作提供有力的支持。
3.2 提升医院服务质量科室管理能力的提升可以有效提升医院的服务质量,保证患者得到更好的医疗服务。
设备管理部门的核心能力提升计划

设备管理部门的核心能力提升计划下载温馨提示:该文档是我店铺精心编制而成,希望大家下载以后,能够帮助大家解决实际的问题。
文档下载后可定制随意修改,请根据实际需要进行相应的调整和使用,谢谢!并且,本店铺为大家提供各种各样类型的实用资料,如教育随笔、日记赏析、句子摘抄、古诗大全、经典美文、话题作文、工作总结、词语解析、文案摘录、其他资料等等,如想了解不同资料格式和写法,敬请关注!Download tips: This document is carefully compiled by theeditor. I hope that after you download them,they can help yousolve practical problems. The document can be customized andmodified after downloading,please adjust and use it according toactual needs, thank you!In addition, our shop provides you with various types ofpractical materials,such as educational essays, diaryappreciation,sentence excerpts,ancient poems,classic articles,topic composition,work summary,word parsing,copy excerpts,other materials and so on,want to know different data formats andwriting methods,please pay attention!以下是一份设备管理部门的核心能力提升计划示例:**一、目标**:提升设备管理部门的整体能力和效率**二、核心能力提升方向**:1. **专业技术能力**:加强对新设备、新技术的学习和掌握。
加强科室业务能力建设

加强科室业务能力建设随着社会的发展和医疗技术的进步,医院科室的业务能力建设变得越来越重要。
科室业务能力建设是指通过一系列的措施和方法,提高科室的运营能力和服务质量,达到科室发展和医院整体发展的目标。
本文将从科室业务流程优化、人员培训提升、科研创新和信息化建设四个方面探讨如何加强科室业务能力建设。
一、科室业务流程优化科室的业务流程是科室运营的基础,优化科室的业务流程对提高效率和质量具有重要意义。
首先,科室需明确各个环节的工作流程和责任分工,确保工作的有序进行。
其次,科室应注重信息的流动和沟通,通过建立科室内部的信息共享平台,及时传递和交流工作信息,避免信息断层和冗余。
另外,科室应定期开展业务流程评估和改进,发现问题及时进行调整和优化,提高工作效率和质量。
二、人员培训提升科室的业务能力和素质与人员的培训和提升密切相关。
科室应加强对医务人员的培训,提高其专业知识和技能水平。
培训内容可包括新技术、新设备的操作和应用、疾病诊治的前沿知识等。
此外,科室还应注重团队合作和沟通能力的培养,通过开展团队建设活动和交流研讨会,增强团队协作和沟通的能力,提高工作效率和质量。
三、科研创新科研创新是科室业务能力建设的重要组成部分。
科室应积极开展科研工作,通过科研项目和论文的撰写和发表,提高科室的学术水平和影响力。
此外,科室还应鼓励医务人员参与临床研究和学术交流活动,增强科室的创新能力和竞争力。
科研创新不仅可以提高科室的学术地位,还能为患者提供更好的医疗服务和治疗方案。
四、信息化建设信息化建设是现代医院发展的重要方向,也是加强科室业务能力建设的必然要求。
科室应积极推进信息化建设,通过建立和完善科室信息系统,实现信息的共享和管理。
科室信息系统可包括电子病历、医学影像、医药管理等。
信息化建设不仅可以提高工作效率和质量,还能为医务人员和患者提供更便捷和准确的服务。
加强科室业务能力建设是医院发展的重要方向。
科室应通过优化业务流程、人员培训提升、科研创新和信息化建设等方面加强业务能力建设。
科室主任如何提升医院科室的竞争力与核心能力

科室主任如何提升医院科室的竞争力与核心能力医院科室作为医疗机构的核心组成部分,其竞争力和核心能力的提升对于医院的发展至关重要。
作为科室主任,如何有效地提升科室的竞争力和核心能力,是一个需要认真思考和努力实践的问题。
本文将从人员管理、科研创新、服务质量和团队合作等方面探讨科室主任提升医院科室竞争力与核心能力的方法。
首先,科室主任应注重人员管理。
科室的竞争力和核心能力离不开科室成员的积极参与和发展。
科室主任应根据科室的需求,合理配置人员,确保科室的人员结构合理,专业能力强。
此外,科室主任还应关注科室成员的职业发展,提供培训机会和晋升通道,激励科室成员不断学习和进步。
通过科室成员的积极参与和发展,科室的竞争力和核心能力将得到有效提升。
其次,科室主任应注重科研创新。
科研创新是医院科室提升竞争力和核心能力的重要途径。
科室主任应鼓励科室成员积极参与科研项目,提供必要的支持和资源。
科室主任还可以组织科研讨论会、学术交流会等活动,促进科研成果的共享和交流。
通过科研创新,科室的学术影响力和技术水平将得到提升,进而提升科室的竞争力和核心能力。
第三,科室主任应注重服务质量。
医院科室的核心能力之一就是提供高质量的医疗服务。
科室主任应建立科室的服务标准和流程,确保科室成员严格按照标准和流程执行工作。
科室主任还应加强患者沟通和关怀,提高患者满意度。
同时,科室主任应不断关注患者的需求和反馈,及时进行改进和优化。
通过提供高质量的医疗服务,科室的竞争力和核心能力将得到提升。
最后,科室主任应注重团队合作。
科室的竞争力和核心能力离不开科室成员之间的良好合作。
科室主任应建立团队合作的机制和文化,鼓励科室成员之间的交流和合作。
科室主任还应根据科室成员的特长和优势,合理分配工作任务,发挥每个人的潜力。
通过团队合作,科室的协同效应将得到发挥,进而提升科室的竞争力和核心能力。
综上所述,科室主任在提升医院科室竞争力和核心能力方面有着重要的作用。
提升科室运营管理水平

提升科室运营管理水平引言随着医疗行业的快速发展和竞争的加剧,科室运营管理对于一个医疗机构的成功变得越来越重要。
科室运营管理涉及到人力资源管理、财务管理、设备管理、过程改进等多个方面,能否高效地管理这些运营活动直接影响着医疗机构的综合实力和竞争优势。
因此,提升科室运营管理水平成为医疗机构迫切需要解决的问题。
1. 优化人力资源管理科室运营管理的核心是人员管理,因此优化人力资源管理是提升科室运营管理水平的关键。
以下是一些提升人力资源管理的方法:1.1 建立明确的岗位职责和工作流程明确的岗位职责和工作流程对于科室的运作至关重要。
科室应该清楚地定义每个岗位的职责,并建立清晰的工作流程,确保任务能够顺利地分配和执行。
1.2 加强员工培训和能力提升提升员工的专业能力和职业素养是提高科室运营管理水平的重要途径。
机构可以通过定期的培训课程、学术交流和外部培训等方式来提升员工的专业技能和管理能力。
1.3 建立良好的沟通机制和团队合作氛围良好的沟通机制和团队合作氛围对于科室运营管理的顺利开展非常重要。
科室应建立有效的沟通渠道,确保信息能够及时流通。
同时,鼓励员工间的合作和团队精神,共同推动科室运营管理的发展。
2. 加强财务管理良好的财务管理是科室运营管理的基础,只有保持良好的财务状况,科室才能有足够的资金来支持运营活动和发展。
以下是一些加强财务管理的方法:2.1 建立科学的预算制度科室应制定详细的年度预算,并根据预算进行科学的资金分配。
预算制度可以帮助科室掌握资金使用情况,避免过度支出或浪费。
2.2 做好成本控制和效益评估科室应定期进行成本控制和效益评估,及时发现和解决运营成本过高和效益低下的问题。
通过合理控制成本,科室可以提高经济效益,增强竞争力。
2.3 加强内部审计和风险管理内部审计和风险管理是保障财务安全的重要手段。
科室应建立健全的内部审计制度,及时发现和纠正财务管理中的问题。
同时,要制定风险管理计划,防范和应对可能出现的风险。
设备科年度工作计划

设备科年度工作计划一、总体目标设备科是公司的重要部门之一,负责公司设备设施的管理和维护工作。
为了更好地完成设备管理工作,提高设备设施的使用率和可靠性,为公司的生产和经营提供保障,设备科将制定以下年度工作计划:1. 提高设备设施的维护管理水平,减少故障率,降低维修成本,延长设备寿命;2. 加强设备设施的技术改造和更新,提高设备的生产效率和质量;3. 完善设备设施管理制度和工作流程,提高设备管理的规范化和科学化水平。
二、具体工作内容1. 完善设备设施管理制度(1)修订、完善设备管理制度和工作规范,明确各项管理制度的责任部门和具体内容;(2)建立设备台账和档案管理制度,做到设备管理细化、规范化;(3)建立设备设施故障维修记录和维护记录,做好设备设施的维修和保养工作。
2. 提高设备设施的维护管理水平(1)加强设备设施的巡检和保养工作,提高设备的可靠性和稳定性;(2)建立预防性维护制度,做好设备设施的定期检修和保养;(3)开展设备设施的故障分析和处理工作,减少设备的故障率。
3. 加强设备设施的技术改造和更新(1)对老旧设备进行技术改造和更新,提高设备的生产效率和质量;(2)引进新型设备设施,提高公司的竞争力和市场份额;(3)加强设备设施的维修技术培训,提高设备维修人员的技能水平。
4. 加强设备管理的信息化建设(1)建立设备管理的信息化平台,实现设备管理的数字化和网络化;(2)建立设备设施的远程监控系统,提高设备管理的智能化水平;(3)加强设备管理的数据分析和统计工作,为设备管理提供科学依据。
三、年度工作计划安排1. 第一季度工作计划(1)修订设备设施管理制度,建立设备台账和档案管理制度;(2)做好设备设施的巡检和保养工作,完善设备的维护记录;(3)开展老旧设备的技术改造和更新工作,提高设备的生产效率。
2. 第二季度工作计划(1)建立预防性维护制度,做好设备的定期检修和保养;(2)开展设备设施故障分析和处理工作,减少设备的故障率;(3)加强设备管理的信息化建设,建立设备管理的信息化平台。
科室提升业务能力方案

科室提升业务能力方案概述科室提升业务能力是现代医疗体系中的一个必不可少的环节。
随着医疗技术的不断发展和更加严格的医疗管理要求,医院内各个科室需要不断提升自身的业务能力,以确保患者的医疗安全和医院的发展。
本文将介绍一个科室提升业务能力的方案,旨在帮助医院科室更好地实现自身能力的提升。
方案1. 人员培训在现代医疗体系中,医生、护士和其他医院工作人员需要不断学习和更新自己的知识。
因此,科室内部应该制定并实施有效的人员培训计划,以满足每个人的培训需求。
人员培训计划可以根据科室的特点和自身需求来制定,可以包括以下方面的内容:•专业知识培训:对于医护人员而言,不断更新专业知识是非常必要的。
科室可以邀请专业的讲师来讲授具体的专业知识,或者通过线上教育平台、课件等方式进行学习。
•职业素养培训:作为医护人员,不仅要有丰富的专业知识,还需要具备良好的职业素养。
科室可以邀请专业的心理医生或管理人员来讲授,或通过线上教育平台等方式进行学习。
•科技应用培训:随着科技的不断更新,各种新型设备和技术不断地涌现。
科室可以邀请相关厂商或专业人士来讲授新技术应用,帮助医护人员更好地掌握科技应用。
2. 工作流程优化在医院中,各个科室都有各自的工作流程和标准,这些流程和标准直接关系到患者治疗、医疗质量和医院形象。
因此,科室需要不断优化工作流程,从而提高服务效率、降低失误率和提升患者满意度。
工作流程优化可以从以下方面入手:•流程分析:详细分析工作流程中每一步的流程和标准,了解可能存在的问题和瓶颈。
•优化方案:根据分析结果提出相应的优化方案,涉及的方面包括医疗流程、协作机制、设备使用、信息化建设等。
•流程管理:推行优化后的新工作流程,加强流程的管理和标准化,例如制定流程指南、进行流程培训等。
3. 团队建设一个高效的医疗团队是科室提升业务能力的基础。
科室应该加强团队建设,培养团队凝聚力和协作能力,从而提高业务能力的整体水平。
团队建设可以从以下方面入手:•建设团队文化:设定科室团队的核心价值观,建设积极向上、互敬互信、崇尚协作的团队文化。
设备科年终总结:注重员工培训,提高团队协作力

设备科年终总结:注重员工培训,提高团队协作力2023年,设备科年终总结:注重员工培训,提高团队协作力时光匆匆,转眼间就到了2023年的年底。
设备科的一年也即将画上句号。
在这一年中,我们积极探索新技术,努力提高团队协作力,注重员工培训,取得了一定的成绩。
在此,让我们来看看这一年的总结。
一、积极探索新技术随着科技的快速发展,只有跟上时代的步伐,才能不断提高我们的工作效率。
设备科在这方面也做出了努力。
在今年,我们加强了对于新技术的学习和掌握,特别是物联网、5G、云计算、人工智能等方面的知识积累和应用。
我们不断地探索新的技术和方法,不断提高我们的技术实力,以更好地服务我们的客户。
二、努力提高团队协作力一个团队的协作力是衡量一个团队是否成功的重要指标。
在这一年中,设备科也注重了团队协作力的提高。
我们加强了部门间的沟通和交流,使得不同部门之间的工作协调更加顺畅。
我们采用了一些新的工作方式,如远程协同工作、共享文档等,来提高团队的协作效率和沟通效率。
同时,我们也加强了对于团队氛围的营造,举办各种团队活动,增强了团队凝聚力。
三、注重员工培训员工是一个企业的核心,也是企业能否长期发展的关键。
在这一年中,设备科注重了员工的培训和成长。
我们开展各种培训活动,如技能培训、管理培训、心理培训等,来提高员工的综合素质和工作能力。
我们还鼓励员工自主学习,提供了各种学习资源和平台,让员工能够在工作中不断成长和提高,更好地为企业服务。
四、努力提高客户满意度客户是我们的衣食父母,客户满意度是衡量企业服务质量的重要指标。
在这一年中,设备科也注重了客户满意度的提高。
我们加强了与客户的沟通和联络,及时了解客户需求,提供更加专业和贴心的服务。
我们也采用一些新的服务方式,如在线服务、智能化服务等,来提高客户的服务体验和满意度。
以上是设备科2023年的年终总结。
在这一年中,我们不断探索新技术,努力提高团队协作力,注重员工培训,提高客户满意度。
科室提升业务能力方案

科室提升业务能力方案背景医院作为一个特殊的组织,其科室作为基本单位,对医疗服务质量的提升具有至关重要的作用。
然而,在现实中,一些科室的业务能力相对较弱,影响了该科室服务水平和医院整体声誉,因此,如何提升科室业务能力成为了一个亟待解决的问题。
现状分析对于一些业务能力弱的科室,常见的问题表现为:•服务态度不佳:部分医务人员表现出不专业、冷漠、不耐烦、对患者态度恶劣等问题,影响了医院形象和服务质量;•业务能力不足:部分医务人员因为资历不够,对病情判断不精确、诊断不准确、治疗方法不科学,导致治疗效果不佳或者耗时较长等问题;•交流不畅:因为语言沟通障碍、文化差异等原因,医务人员与患者之间的交流往往不够顺畅,导致无法充分了解患者需要的服务。
方案设计针对上述问题,提升科室业务能力,需要采取综合性的措施,包括以下几个方面:人员培训1.服务态度培训:针对服务态度不佳的医务人员,加强服务态度培训,切实提高医务人员的服务水平,增强医院的服务品牌影响力;2.就医流程培训:加强医务人员对就医流程的了解,指导医务人员规范就医流程,缩短就医时间,提高工作效率;3.业务技能培训:加强医务人员对各种常见病及其治疗的认识和理解,提升医务人员的诊治能力,达到更高水平的治疗效果。
环境整改1.提升设施设备:提高设备水平和设备维护保养,加强环境整治,提升医院整体形象;2.完善服务流程:配备管理人员,加速患者的就医速度,为患者提供更好的服务体验。
建立科室文化1.建立科室文化:打造团结和谐的科室文化氛围,增强医务人员的归属感和荣誉感,提高工作积极性;2.建立医患交流渠道:建立与患者沟通的渠道,定期开展医患交流活动,加强医患信任,增进交流。
实施计划1.人员培训:加强教育培训,定期开展业务和职业素养提升培训;2.环境整改:实现设施与设备提升,加强人性化设计,优化就医环境;3.建立科室文化:营造医院良好文化氛围,稳定优质人员队伍,减少人员流动率;4.建立医患交流渠道:增加医患交流机会,改变医患之间的敌对关系,营造良好的医患关系。
- 1、下载文档前请自行甄别文档内容的完整性,平台不提供额外的编辑、内容补充、找答案等附加服务。
- 2、"仅部分预览"的文档,不可在线预览部分如存在完整性等问题,可反馈申请退款(可完整预览的文档不适用该条件!)。
- 3、如文档侵犯您的权益,请联系客服反馈,我们会尽快为您处理(人工客服工作时间:9:00-18:30)。
做强科室核心业务,提升公司资源和装备管理能力设备设施科作为技术部主管设备设施运行管理的部门,在完善和强化体系能力、推进预防保全、控制运行成本、提升资源保障能力、及厂房设施建设等方面均做了大量的努力,并逐步取得成效。
目前设备设施科面临三个主要课题:提升设备可动率、控制维修成本和培训维修人员能力,由于维修系统资源分散在工厂各车间,从而对设备设施科体系管理和协调能力提出了考验。
围绕这三个课题,结合科室核心业务,我们拟从如下七个方面进行能力提升。
一、提升科内各岗位业务能力,改善工作效率随着公司的发展,设备科业务的不断重新认识和扩大,逐步显现出人力资源不足的问题,从而导致部分人员重复兼岗,负荷较重,部分人员岗位与工作内容不匹配。
纠其原因,除了硬性的岗位资源得不到公司及时补充之外,还有科室人员自身能力问题。
部分人员业务能力不强、工作主动性不够,缺乏忧患意识。
我们的对策是:1、继续开展业务交流及培训,各岗位清晰岗位职责和工作流程。
年内,科内进行了多轮业务交流及培训,初步明晰了相关人员对流程、岗位职能等的认识。
在此基础上,我们将结合技术部的整体培训计划,逐步针对岗位基础技能和专用技能进行培训,有效提升人员工作能力和效率。
2、建立各岗位工作标准及目标,并以此评价个人工作。
我们将对科长KPI指标进行分解,真正落实到个人,发挥个人绩效考核的推动作用。
为确保目标完成,逐步通过标准化工作,明确各岗位工作标准,使所有人员知道应该做什么,怎么去做。
我们将利用科周例会或专题学习会,让各岗位轮流讲解岗位说明书,在交流和互动中,提升全体人员对岗位责任的认知。
3、公平、公正、公开,调动和提升各岗位人员能动性。
严格考核,从考勤、业务能力、工作量、工作质量、固定指标完成情况等多个维度评价科内人员,利用科务会进行总结、评点、通报,并结合适度的奖惩,个人约谈等措施,本着公平、公正、公开的原则,调动和提升各岗位人员主观能动性。
4、加强计划管理。
从2010年开始,我们已经开始实行科室、班组计划管理。
2011年,我们将延续这一做法,并扩大到重要项目管理,利用科周例会,或专门例会进行计划点检,逐步培养员工学会按计划做事,进而提升工作效率。
5、利用体系能力提升平台,和先进科室对标,提升设备设施科体系创新能力。
公司体系能力提升平台提供了我们一个好的学习和提升窗口,我们将积极对标先进科室,查找自身差距,依据八大要素导向,逐渐做强科室核心管理能力,并提升创新能力。
利用科周例会,定期公示科内人员体系能力提升平台积累情况,对积累不力的人员进行公开通报,并进行考核。
我们的目标是力争进入体系能力“十佳科室”。
二、强化成本过程管理,降低单车消耗随着轿车公司装备资产的日益扩大,设备科管理的固定资产已经达到57亿元,这些资产包括厂房、设备、工装、模具、夹具、公用设施等。
但另一方面,这些装备的运行成本也日益增加,并对公司整车成本构成现实压力。
年初,仅备件储备就将近1亿,尽管做了降库存工作,还没有达到目标限定的6500万。
2011年度维修费用,包含外委维修费用预计接近1亿元;能源消耗预计超过2个亿。
以上数据告诉我们,成本管理已经提升到刻不容缓的地步。
为此,我们将采取如下措施:1、建立健全成本过程管理的相关标准,逐步由管结果向管好费用发生过程过渡。
今年以来,我们强化了维修费用发生过程的控制,严格审核各车间备件申报,和工厂一道努力压缩库存,并加大了修旧利废的力度。
年初,我们出台了《备件管理方案》,三季度编制发布《备件管理规定》,成本管理向体系化迈进。
今后一年内,我们将逐步总结今年的经验,将成本过程管理标准化。
如编制《生产准备零部件选型推荐标准》、《重要零部件服役期更新周期推荐标准》等文件,构建备件分类管理模型,并对备件申报、审批、上报、订货监控、测试、储存、领用、旧备件返库等过程进行完善。
我们还将通过KPI考核的方式,制定库存定额及消耗定额,把成本纳入车间考核指标,初步建立全过程的成本控制体系。
2、优化各环节控制,强化分析与改善能力。
强化对费用发生动态数据的分析,对发生费用的品种结构、车间分布、设备分布、消耗规律等进行统计,以调整储备结构,优化各环节管理对策,对过程管理进行动态改善。
3、继续推进第三方库存、修旧利废、节能降耗、品种合并等工作。
借助维修培训基地的建成,利用新的硬件平台,我们将加大贵重备件的修旧利废工作。
继续探讨批量零部件的第三方库存方案,减少备件储备,在满足生产必要需求的基础上,最大限度地压缩库存。
鼓励车间做好国产化替代工作,压缩储备品种。
各车间库房实现资源互补,防止重复过量储备。
能源管理方面,将继续推行能源新技术改造,在新工厂建设方面积极营造绿色工厂氛围,并通过标准化(《工厂建设能源管理规划》)预以推进。
加大现场能源检查力度,整治跑冒滴漏,压缩单车能耗。
4、建立备件、能源等应急预案机制。
对备件采购过程周期进行标准化,建立备件采购跟踪机制,减少备件采购延误率。
和国内供货商、集团各公司等建立业务联络体制,实现应急时的资源共享。
在本地寻找和建立部分固定的重要零部件应急维修外部专业公司资源,如电动机、复杂电子系统的专业维修公司等,以实现对车间部分重要零部件故障时的应急维修。
能源方面,和政府管理部门、动能企业建立常态化联络平台,及时交互信息。
关注生产计划,和公司、生产部、工厂及时交换信息,完善重要能源变动信息发布制度,尽力做到提前因对,压缩动能变化点对生产、生活的影响。
公司内利用现有的备用系统和储备资源,合理投送和切换,在非常情况发生时,最大限度降低能源影响。
三、继续借助TPM平台,推进标准化及体系建设,减少故障停台经过近两年的TPM推进,我们发现这是一个非常好的平台。
这段时间内,我们借助这个平台整合了车间维修机构,完善了体系方法,建立了例会制度,通过几十次辅导教会了车间管理设备的一般思路,推行了定期定量预防保全,引导车间逐步学会故障分析和防止故障复发,并推广了许多方法性工具:如作业要领书、单点课、保全阵地、新版故障分析、设备管理基准书、设备档案等,从而使车间在设备管理方面不断增加积累,走向正轨。
但在如下方面仍需努力:1、在瓶颈车间推行“零停台活动”定期组织车间对停台排名及分布情况进行统计分析,并制定对策。
推行故障管理的故障真因分析、缺陷改善、他机点检和标准化方法,使车间熟练管理故障,努力防止故障再发生。
对二厂涂装、一厂冲压等车间进行重点管理跟踪,依据故障前十位问题,积极参加车间例会,组织和指导车间进行问题攻关、缺陷改善,通过年度项目计划和“零停台活动”,消除重大缺陷,减少重大故障。
2、继续在工厂推进更多的设备管理先进工具方法。
尽管我们坚持推进了一系列先进的工具方法,但对标丰田、马自达体系,仍然有许多可以提升之处。
未来的一段时间内,我们将巩固现有已经开展的活动,使这些工具真正为提升开动率发挥支撑作用。
本着一年一个主题的原则,去年我们推行了故障再发生防止管理,今年我们推行了定期定量保全,明年我们将配合公司推行以操作工人为主体的自主维修,以压缩缺陷和不良,防止诱发事实故障,把好故障的第一道关口。
随着基础的不断做实,还将逐步引进失效分析、预见维修等更多的工作方法。
3、推动TPM先进方法、工具体系化、标准化。
我们在今年已经把部分TPM先进的思想和体系方法实行了标准化,大部分好的做法通过修改流程文件进入了公司管理体系。
期间共修改、编制了超过20个管理文件。
下一步的重点,是依托体系文件架构,逐步编制和完善对工厂更有实际指导意义的三级作业管理文件,如《定期定量保全管理规定》、《设备工装点检管理规五、在工厂建设中,提升土建、公用设施项目管理能力在以往的工厂建设过程中,凸显了项目管理能力上的缺失,为此给部门造成比较大的压力。
纠其原因,除了公司项目管理体制造成项目组和部门管理不统一之外,也有自身的管理能力问题,从而亟待提升。
1、全面推进项目计划管理,实行项目实施定期汇报制度。
我们要对标丰田严密的计划管理经验,大力推进项目计划管理。
针对所有工程项目,全部建立并严格实施计划,并在科内定期汇报,调控风险。
2、监控项目节点进度,对延误进度采取弥补措施。
分管领导要监督重要项目节点,对延误进度进行识别并督促采取弥补措施。
3、点检项目节点输出。
要求项目管理人员动态点检进度,明确各节点输出内容,确保项目进度少出现延误。
4、动态识别项目风险点,做好风险规避管理。
对项目风险进行动态识别,明示风险,并计划性地前置风险,进行风险规避。
六、做强能源管理能力,为生产提供可靠动能保障能源管理的任务,一是要最大限度地保证动能供应的可靠性,二是尽量压缩动能消耗。
仿照备件管理经验,动能管理也必须做强过程管理,才能确保目标的达成。
1、对标先进企业,学习外部经验。
组织能源管理人员走出去,向国内同行学习先进管理经验,改善我们的管理方法。
2、完善节能目标责任制落实及评价。
把节能指标分解到基层,落实目标责任制,建立评价体系,做好评价工作。
3、抓好专业厂能源管理体系建设。
利用我们的体系资源优势,指导专业厂建立完备的能源管理体系,通过做强能源使用层的自主管理,来实现能源的优化利用。
4、强化能源现场管理与评价。
定期组织现场检查,对跑冒滴漏及现场管理不良进行通报,必要时给予处罚。
监督用能单位制定整改措施和计划,开展对用能问题的改善。
实行停产必须停机管理,对特殊情况下不能中断动能供应的设备进行重新识别,并悬挂标志。
督促车间做好能源自查自纠工作。
对长期施工项目,实行供应商用能收费管理。
5、节能新技术的推广与应用。
在现有装备环境中,继续主导推进节能新技术的应用工作,引进国家推荐的节能、低污染项目,实施新技术改造。
在工厂建设规划中,积极参与并推动低耗能工厂建设。
七、站在部门整体业务角度,强化与各专业科体系融合能力设备设施科整合到技术部以后,在各专业科配合下,积极与技术部主导业务进行了融合,逐步完善和实现部门全体系上的、装备全生命过程的管理。
但仍有一些工作需要改善:1、加强与部门领导沟通,明确设备设施科定位与职责。
由于对部门领导的战略意图理解不够,个别工作有偏离部门业务主导方向的情况,为此,我们将加强向部门领导的汇报、沟通,明确科室职能定位,更好地在技术部的整体内发挥作用。
2、与各专业科在业务交接点上主动协调、互相支持。
与各科在业务上有时出现职责、流程不清晰问题,对工作有一定的影响。
今后将加大与专业科的业务交流和沟通力度,工作上积极配合,互相支持,实现与各专业科的顺畅合作,共同高质量完成技术部各项工作任务。
3、与各专业科配合,逐步建立相应流程和规范。
从公司层面完善体系流程,逐步使和专业科的接口、业务衔接关系、分工等清晰化、标准化,提升工作效率。
4、主动补位,建立补位意识。
工作上积极覆盖,使部里的问题决不外流,通过积极协调,主动补位,提升部门工作的外在形象,维护技术部整体利益。