印刷色差标准检验规范1)010
色差仪的标准
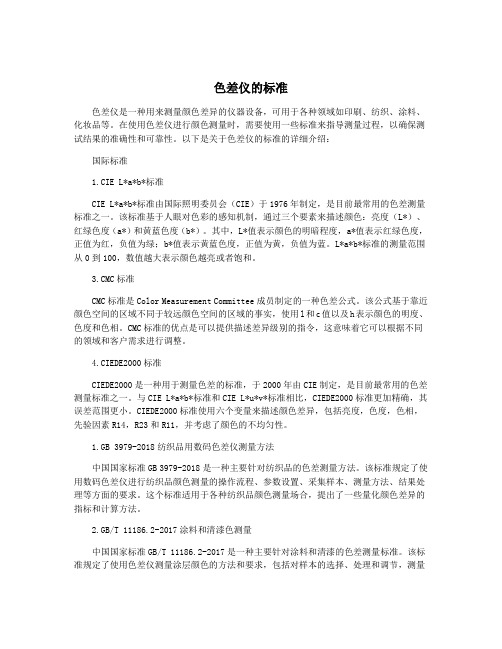
色差仪的标准色差仪是一种用来测量颜色差异的仪器设备,可用于各种领域如印刷、纺织、涂料、化妆品等。
在使用色差仪进行颜色测量时,需要使用一些标准来指导测量过程,以确保测试结果的准确性和可靠性。
以下是关于色差仪的标准的详细介绍:国际标准1.CIE L*a*b*标准CIE L*a*b*标准由国际照明委员会(CIE)于1976年制定,是目前最常用的色差测量标准之一。
该标准基于人眼对色彩的感知机制,通过三个要素来描述颜色:亮度(L*)、红绿色度(a*)和黄蓝色度(b*)。
其中,L*值表示颜色的明暗程度,a*值表示红绿色度,正值为红,负值为绿;b*值表示黄蓝色度,正值为黄,负值为蓝。
L*a*b*标准的测量范围从0到100,数值越大表示颜色越亮或者饱和。
3.CMC标准CMC标准是Color Measurement Committee成员制定的一种色差公式。
该公式基于靠近颜色空间的区域不同于较远颜色空间的区域的事实,使用l和c值以及h表示颜色的明度、色度和色相。
CMC标准的优点是可以提供描述差异级别的指令,这意味着它可以根据不同的领域和客户需求进行调整。
4.CIEDE2000标准CIEDE2000是一种用于测量色差的标准,于2000年由CIE制定,是目前最常用的色差测量标准之一。
与CIE L*a*b*标准和CIE L*u*v*标准相比,CIEDE2000标准更加精确,其误差范围更小。
CIEDE2000标准使用六个变量来描述颜色差异,包括亮度,色度,色相,先验因素R14,R23和R11,并考虑了颜色的不均匀性。
1.GB 3979-2018纺织品用数码色差仪测量方法中国国家标准GB 3979-2018是一种主要针对纺织品的色差测量方法。
该标准规定了使用数码色差仪进行纺织品颜色测量的操作流程、参数设置、采集样本、测量方法、结果处理等方面的要求。
这个标准适用于各种纺织品颜色测量场合,提出了一些量化颜色差异的指标和计算方法。
外观检验判定标准

同色点:与相邻区域属同一色系但色调有差异的点
硬划痕:由于硬物摩擦而造成产品表面有深度的划痕。
细划痕:没有深度的划痕。
熔接线:塑料熔体在型腔中流动时,遇到阻碍物(型芯等物体)时,熔体在绕过阻碍物后不能很好的融合,于是在塑料件的表面形成一条明显的线,叫做熔接线。
N/A
B
表面颗粒
允许
不计
B
异色点
允许
不计
B
丝印不全
可辨识,无歧义
不计
B
近色点
允许
不计
B
色差
允许
不计
B
变色、脏污
直径D≤5mm
不计
B
腐蚀、生锈
生锈不允许
0
B
缩水:当塑料熔体通过一个较薄的截面后,其压力损失很大,很难继续保持很高的压力来填充在较厚截面而形成的凹坑。
色差:产品表面呈现出与标准样品(客户承认样品)的颜色的差异,称为色差。
桔皮:在烤漆层或面漆表层上的一般波纹或花斑纹外观。
顶白/顶凸:由于塑料件的包紧力大,顶杆区域受到强大的顶出力所产生的白印或凸起。
W≤0.03mm忽略不计,显示状态下不允许可见划痕
1
划伤
有明显手感的划痕
L≤1mm,W≤0.05mm,N≤1
1
B
点状缺陷(磨伤、异物、针孔、表面颗粒等)
0.05mm²<S≤0.1mm²,允许1点,DS≥25mm;;
2
B
0.1mm²<S≤0.15mm²,不允许;0.05mm²以内不计
1
脏污
不允许
0
B
异物
点状
参照点要求执行
N/A
印刷品的色差检测.

X=0.490R+0.310G+0.200B Y=0.177R+0.812G+0.011B Z= 0.010G+0.990B
。
色空间的转换
CIELAB 色彩空间是直接从CIEXYZ 色彩空间上发展起来的 , 它们之间的关系是非线性的,相应的转换公式如下: L*=116×(Y/Y0)1/3-16 Y/Y0>0.00858 L*=903.3×Y/Y0 Y/Y0<0.00858 a*=500[(X/X0)1/3-(Y/Y0)1/3] b*=200[(Y/YO)1/3-(Z/Z0)1/3] 注:其中X、Y、Z是物体的三刺激值;X0、YO、ZO为CIE标 准照明体的三刺激值 ; L*表示心理明度 ; a*, b*为心理色 度。
谢谢观赏
引起色差的原因
3.印刷工艺引起的色差 (1)色序安排形成的色差,主要从油墨的转移覆盖率角度加以 考虑。 (2)胶印过程中水墨平衡形成的色差,是最常见、最直接的由 墨量大小宏观控制产生的差异。 (3)胶印、凸印、凹印等不同的印刷方式和印刷原理,形成的 墨层厚度、印刷压力不同等引起的色差。 (4)印刷中单色印刷机与多色印刷机的不同、干压干与湿压湿 印刷类型的不同,形成油墨颜色的饱和度不同而引起的色 差。
分光光度计检测法
当△L *<0,说明印刷样张的颜色比标准样张的颜色深, 暗调部分图像易损失,印刷时黑墨含量过高或油墨转移量 不够。 若△a *>0、△b *>0,则说明印刷样张偏橙色,配墨 时黄墨和品红墨含量过高或油墨转移量过多; 若△a *>0、△b *<0,则说明印刷样张偏红,配墨时 品红墨含量过高或油墨转移量过多; 若△a *<0、△b *>0,则说明印刷样张偏绿,配墨时 黄墨和青墨含量过高或油墨转移量过多; 若△a *<0、△b *<0,则说明印刷样张偏青,配墨时 青墨含量过高或油墨转移量过多; 若△a *和△b *的值接近零,则说明印刷样张偏灰,配墨 时黑墨含量过高或油墨转移量过多。
印刷品质量检验要求
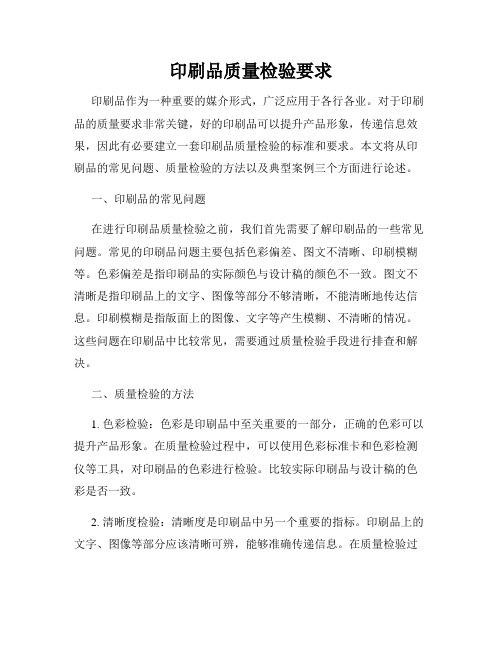
印刷品质量检验要求印刷品作为一种重要的媒介形式,广泛应用于各行各业。
对于印刷品的质量要求非常关键,好的印刷品可以提升产品形象,传递信息效果,因此有必要建立一套印刷品质量检验的标准和要求。
本文将从印刷品的常见问题、质量检验的方法以及典型案例三个方面进行论述。
一、印刷品的常见问题在进行印刷品质量检验之前,我们首先需要了解印刷品的一些常见问题。
常见的印刷品问题主要包括色彩偏差、图文不清晰、印刷模糊等。
色彩偏差是指印刷品的实际颜色与设计稿的颜色不一致。
图文不清晰是指印刷品上的文字、图像等部分不够清晰,不能清晰地传达信息。
印刷模糊是指版面上的图像、文字等产生模糊、不清晰的情况。
这些问题在印刷品中比较常见,需要通过质量检验手段进行排查和解决。
二、质量检验的方法1. 色彩检验:色彩是印刷品中至关重要的一部分,正确的色彩可以提升产品形象。
在质量检验过程中,可以使用色彩标准卡和色彩检测仪等工具,对印刷品的色彩进行检验。
比较实际印刷品与设计稿的色彩是否一致。
2. 清晰度检验:清晰度是印刷品中另一个重要的指标。
印刷品上的文字、图像等部分应该清晰可辨,能够准确传递信息。
在质量检验过程中,可以使用放大镜等工具,对印刷品上的文字和图像进行放大检验,确保其清晰度符合要求。
3. 对比度检验:对比度是印刷品中的又一个重要指标,它决定了印刷品上的图像和文字与底色之间的清晰度和比较。
在质量检验过程中,可以使用对比度仪器等工具,对印刷品上的对比度进行检测,确保其合适。
4. 印刷质量检验:印刷过程中常见的问题还包括油墨的涂布均匀性、图像的重影与偏移等。
在质量检验过程中,可以使用显微镜等工具,对印刷品的细节进行检测,确保印刷质量符合要求。
三、典型案例为了更好地理解印刷品质量检验的要求,我们可以通过一些典型案例进行说明。
1. 案例一:某公司为了产品推广,设计了一款彩页印刷品进行宣传。
然而,在印刷品交付后,发现印刷品上的色彩与设计稿存在较大差异,严重影响了产品的形象。
印刷品类检验规范
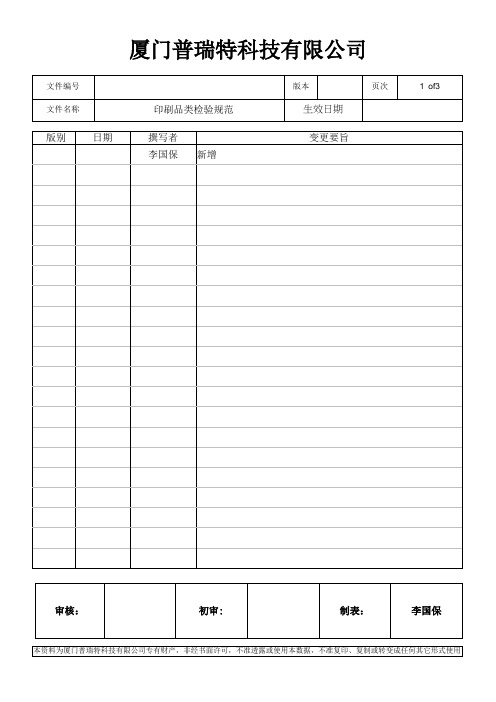
文件编号版本页次 1 of3 文件名称印刷品类检验规范生效日期版别日期撰写者变更要旨李国保新增审核:初审: 制表:李国保文件编号版本页次 2 of3 文件名称印刷品类检验规范生效日期1.目的规范印刷品检验标准,为IQC检验印刷品提供方法和判定依据。
2.范围适用于IQC对印刷品进行来料检验。
3.使用仪器和设备卷尺、游标卡尺。
4.抽样方案按MIL-STD-105E LEVEL-II一般正常单次抽样,重:0.65,轻微:2.5,其中尺寸检查,试装检查采用每批抽样N=5,C=0的特检方式进行检查。
5.判定条件5.1目视距离约30cm,任何角度。
5.2扫视时间5秒/次左右,自然光或灯光下。
6.检验方法6.1外观:用目测法,将实体与图纸或样品相比较,观察实体的颜色、丝印等是否均能与样品相符。
(备注:针对按键彩片,请用灯照或者实装方式进行漏光检验。
)6.2尺寸:用游标卡卷尺测量。
6.3试装:将印刷品和相对物进行组装,观察其相互间的位置,间隙、松紧度等情况。
说明书类产品只需进行外观检查。
6.4包装:目测法。
文件编号版本页次 3 of3 文件名称印刷品类检验规范生效日期7.缺陷分类检验项目缺陷内容缺陷分类A B C外观1.印刷品内容与样品不一致,错印,漏印,多印。
2.颜色与样品不一致,颜色错,严重色差。
3.轻微色差。
4.重影、脏污。
5.体缺画、断笔、毛边。
6.破损、皱折。
7.切边不整齐,歪斜。
8.说明书缺页、重页、装订序列号混乱。
9.粘性不良,易撕掉。
10.系列号标贴错误。
11.漏打装订钉。
12.装订钉严重生锈,突出刮手。
13.漏光√√√√√√√√√√√√√尺寸外形尺寸不在承认规格范围内。
√试装1.无法试装或过松过紧。
2.孔位偏移√√包装1.无标识(内、外包装都需要标识)2.标识错误(如代码错误或者标识不全)3.产品混装(不同产品混在一起)4.未按指定材料包装5.包装材料破损√√√√√文件编号版本页次 4 of3 文件名称印刷品类检验规范生效日期8.常见不良缺陷图片:9.相关表单:9.1 进料检验报告 [PRT-QP-1201]9.2 进料异常反馈单 [PRT-QP-1202]。
印刷检验标准
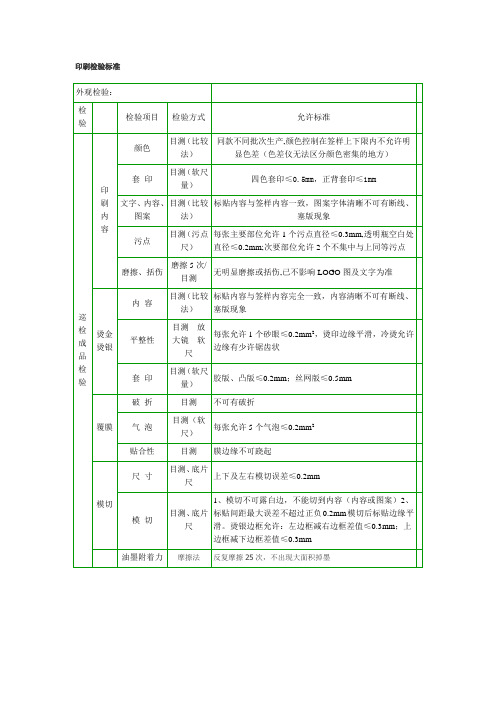
套印
目测(软尺量)
胶版、凸版≤0.2mm;丝网版≤0.5mm
覆膜
破折
目测
不可有破折
气泡
目测(软尺)
每张允许5个气泡≤0.2mm2
贴合性
目测
膜边缘不可跷起
模切
尺寸
目测、底片尺
上下及左右模切误差≤0.2mm
模切
目测、底片尺
1、模切不可露白边,不能切到内容(内容或图案)2、标贴间距最大误差不超过正负0.2mm模切后标贴边缘平滑。烫银边框允许:左边框减右边框差值≤0.3mm;上边框减下边框差值≤0.3mm
印刷检验标准
外观检验:
检验
检验项目
检验方式
允许标准
巡
检
成
品
检
验
印
刷
内
容
颜色
目测(比较法)
同款不同批次生产,颜色控制在签样上下限内不允许明显色差(色差仪无法区分颜色密集的地方)
套印
目测(软尺量)
四色套印≤0.5mm,正背套印≤1mm
文字、内容、图案
目测(比较法)
标贴内容与签样内容一致,图案字体清晰不可有断线、塞版现象
污点
目测(污点尺)
每张主要部位允许1个污点直径≤0.3mm,透明瓶空白处直径≤0.2mm;次要部位允许2个不集中与上同等污点
磨擦、括伤
磨擦5次/目测
无明显磨擦或括伤,已不影响LOGO图及文字为准
烫烫银
内容
目测(比较法)
标贴内容与签样内容完全一致,内容清晰不可有断线、塞版现象
平整性
目测 放大镜 软尺
油墨附着力
摩擦法
反复摩擦25次,不出现大面积掉墨
印刷品质量标准
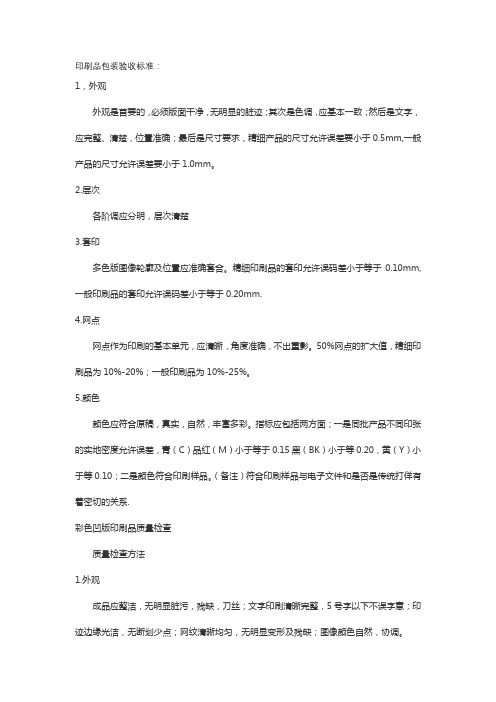
印刷品包装验收标准:1,外观外观是首要的,必须版面干净,无明显的脏迹;其次是色调,应基本一致;然后是文字,应完整、清楚,位置准确;最后是尺寸要求,精细产品的尺寸允许误差要小于0.5mm,一般产品的尺寸允许误差要小于1.0mm。
2.层次各阶调应分明,层次清楚3.套印多色版图像轮廓及位置应准确套合。
精细印刷品的套印允许误码差小于等于0.10mm,一般印刷品的套印允许误码差小于等于0.20mm.4.网点网点作为印刷的基本单元,应清晰,角度准确,不出重影。
50%网点的扩大值,精细印刷品为10%-20%;一般印刷品为10%-25%。
5.颜色颜色应符合原稿,真实,自然,丰富多彩。
指标应包括两方面;一是同批产品不同印张的实地密度允许误差,青(C)品红(M)小于等于0.15黑(BK)小于等0.20,黄(Y)小于等0.10;二是颜色符合印刷样品。
(备注)符合印刷样品与电子文件和是否是传统打佯有着密切的关系.彩色凹版印刷品质量检查质量检查方法1.外观成品应整洁,无明显脏污,残缺,刀丝;文字印刷清晰完整,5号字以下不误字意;印迹边缘光洁,无断划少点;网纹清晰均匀,无明显变形及残缺;图像颜色自然,协调。
2套印画面主题部位,实地印刷误差应不大于0.5mm,网纹印刷误差应不大于0.3mm;画面次要部位,实地印刷误差应不大于0.8mm,网纹印刷误差应不大于0.6mm。
1、外观:版面干净,无明显脏污;色调一致;文字完整、清楚,位置准确;无切割不良、飞边;尺寸允许误差小于1.0mm。
2、层次:各阶调应分明,层次清楚。
3、套印:多色版图像轮廓及位置应准确套合,套印允许误码差小于等于0.20mm。
4、网点:网点应清晰,角度准确,不出重影,50%网点的扩大值为10%-25%。
5、颜色:颜色符合原稿,同批产品不同印张的实地密度允许误差,青(C)品红(M)小于等于0.15,黑(BK)小于等于0.20,黄(Y)小于等于0.10。
色差等级国标标准

色差等级国标标准
色差等级国标标准是指国家标准GB/T 250-2014《塑料色差评定方法》中规定的色差等级分类标准。
该标准是为了评价塑料制品外观质量而制定的,其主要目的是通过对色差值的测量和判定,来确定塑料制品的色差等级,以指导生产和质检工作。
根据GB/T 250-2014标准,色差等级分为五个等级,分别是0级、1级、2级、3级和4级。
其中,0级表示无色差,1级表示色差较小,2级表示色差一般,3级表示色差较大,4级则表示色差很大。
每个等级还有具体的数值范围,如0级的色差值应小于0.5,1级的色差值应在0.5~1.5之间,2级的色差值应在1.5~3之间,以此类推。
在进行色差评定时,需要使用色差仪来进行测量,并根据测得的色差值与标准中规定的数值范围进行比较,以确定塑料制品的色差等级。
在评定时,还需要考虑塑料制品的实际应用场景和要求,以确定是否达到了需要的色差等级。
总之,色差等级国标标准是一项非常重要的标准,它能够帮助生产和质检工作人员更好地评价塑料制品的外观质量,提高产品的质量和市场竞争力。
印刷检验标准

印刷检验标准印刷品质量的好坏直接关系到产品的形象和品牌的形象,因此印刷检验标准显得尤为重要。
在印刷检验过程中,需要遵循一定的标准和规范,以确保印刷品的质量稳定和一致性。
本文将从印刷检验标准的意义、内容和实施方法等方面进行探讨。
首先,印刷检验标准的意义非常重大。
印刷检验标准是印刷品质量控制的依据,它可以帮助印刷厂和印刷企业确保印刷品的质量稳定,减少因质量问题带来的损失。
同时,印刷检验标准也是印刷品质量管理的重要手段,可以帮助企业建立起科学的质量管理体系,提高生产效率,降低生产成本,提高产品竞争力。
其次,印刷检验标准的内容主要包括印刷品的尺寸、印刷质量、印刷色彩、印刷纸张等方面。
在印刷品的尺寸检验中,需要检查印刷品的长、宽、厚度等尺寸参数是否符合要求。
在印刷质量检验中,需要检查印刷品的印刷精度、清晰度、色彩饱和度等质量指标是否符合要求。
在印刷色彩检验中,需要检查印刷品的色彩准确度、色彩一致性等色彩指标是否符合要求。
在印刷纸张检验中,需要检查印刷品所使用的纸张的质量、厚度、光泽度等参数是否符合要求。
最后,印刷检验标准的实施方法主要包括目视检验、测量检验和实验室检验等。
在目视检验中,检验人员需要通过肉眼观察印刷品的外观质量,包括印刷质量、印刷色彩、印刷纸张等方面。
在测量检验中,检验人员需要使用测量工具对印刷品的尺寸、厚度、色彩等参数进行精密测量。
在实验室检验中,检验人员需要将印刷品送至实验室进行进一步的质量检测,以确保印刷品的质量稳定和一致性。
综上所述,印刷检验标准是印刷品质量控制的重要依据,它的实施可以帮助企业确保印刷品的质量稳定和一致性,提高产品竞争力。
因此,印刷企业在生产过程中需要严格遵循印刷检验标准,加强对印刷品质量的监控和管理,以提高产品的质量和市场竞争力。
印刷色差10%标准__理论说明

印刷色差10%标准理论说明1. 引言1.1 概述在印刷领域中,色差是一个非常重要的概念。
它指的是实际印刷品与预期输出之间的颜色偏差或误差。
色差问题对于印刷品的质量和可视效果有着直接影响,并且也可能导致客户不满意,增加了重新生产的成本。
因此,准确地控制印刷色差对于确保印刷品质量至关重要。
1.2 文章结构本文将详细介绍印刷色差10%标准的理论说明。
首先,我们将定义和解释色差及其意义。
然后,我们将讨论影响印刷色差的因素,以便更好地理解产生色差的原因。
接下来,我们将阐述印刷色差10%标准的基本原理,并介绍如何实现和应用这一标准进行测量、评估和控制印刷色差。
此外,在文章的后部分,我们还将对色差10%标准进行优缺点分析,并展望未来发展或提出相关建议。
1.3 目的本文旨在全面介绍印刷色差10%标准及其理论说明。
通过具体解释色差的定义和意义,探讨影响印刷色差的因素,并详细阐述印刷色差10%标准的基本原理和应用方法,读者将能够更好地理解色差问题,并学习如何在实际印刷过程中进行有效的色差控制。
最后,深入分析该标准的优缺点,我们将帮助读者全面了解这一标准并为未来发展提供合理建议。
2. 印刷色差10%标准理论说明2.1 色差的定义和意义印刷色差是指在印刷过程中,所制作的印品与预定色彩之间的差异。
色差的出现可能会影响印刷品的质量和观感,因此准确地控制印刷色差对于保证产品质量和满足客户要求非常重要。
2.2 影响印刷色差的因素印刷色差受到多种因素的影响,包括选取的油墨颜色、版材特性、纸张吸收性能、油墨传输等。
油墨配方和调制过程中存在微小误差,同时版面排版、套印精度等也可能导致色彩偏移。
2.3 印刷色差10%标准的基本原理印刷色差10%标准是一种常用于衡量和评估印刷品质量的标准。
该标准规定了在实际可视条件下,允许出现不超过10%的颜色偏移。
这意味着,对于任何一个给定颜色,其偏移范围应限制在该颜色空间的10%之内。
该标准的制定基于人眼对色彩变化的感知和识别能力。
印刷品的色差检测与控制
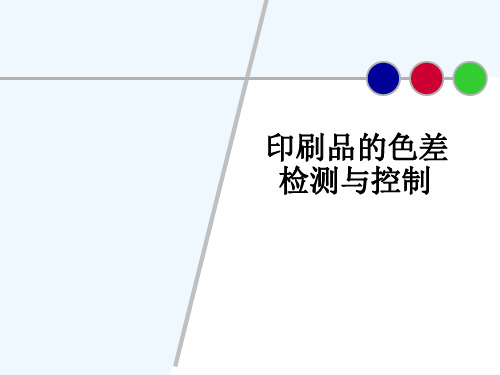
• 结论
• 利用基于CCD图像数据采集技术设计了对于印刷品色彩的检测平台,
并在LabVIEW软件平台上进行仿真研究,实验仿真结果表明CCD色彩 向量和色彩密度之间存在较好的一致性关系,检测系统具有测量精 度高、自动化程度高以及扩展性强等特点。应用结果表明该系统能 够满足印刷品色彩检测要求,提高了测试效率。在其它色度检测领 域中,也具有良好的科研价值和应用前景。
3、色差的控制措施
• 1)定期维护保养设备
• 保持设备状态的稳定,是保证印刷质量的首要前提。要保持正常的设备
状态,关键是对设备进行定期的维护和保养,以提高印机的适用性和经 济性。产品的质量预防为主,定期保养的内容包括清洁、润滑、设备的 精度调整、橡皮布的更换及垫衬的定期更换等。其中设备的精度调整是 关键,包括辊的基本设定、滚筒问压力调整、包衬值等都有具体的方法 和数据调节,平时要做的只是按要求对设备进行保养工作。
者的差异。△E表示两种 • 色彩的CIEL*a*b*色彩空间之间的距离,用来表示总色彩差别和建立定 量色彩公差,例如对于印品和签样样张,分别测出其L*、a*、b*。值, 可计算两者之间的色差△E:
• 实验研究
• 实验利用系统和爱色丽£旧45分光光度计对标准色板和不同颜色的印品
进行对比检测,其中标准色板采用2006年版湖北新华印务有限公司专用 色谱,测量条件为D50光源,2°视场,显示CIEl976标准色度系统色度 数值,实验测定了13种色板的颜色,结果如表1所示。 • 表1爱色丽DTP45测量值与系统实测值比较
• 4)基本的操作方法
• ①印刷前,最好先用洁版和水擦拭印版,再进行校版。校版后,根据原
稿或付印样,先确定一个墨量,跑一批过版纸;如果上一批印品吃墨量 大,尽量放的过版纸多一些,把墨辊上的余墨跑干净,以便保持传递油 墨的稳定性。
彩盒检验标准检验规范 -

文件名称目的:掌握彩盒的检验标准,使来料质量更好地符合我公司的品质要求。
2. 适用范围:适用于本公司所有彩盒、贴纸、彩卡等产品的检验。
3. 参考依据:3.1:A面为正面,产品在正确的使用过程中,面对使用者的一面为正面。
3.2:B面为底面,相对于正面的下部为底面。
3.3:C面为右侧面,相对于正面的右侧为右侧面。
3.4:D面为背面,相对于正面的反面为背面。
3.5:E面为顶部,相对于正面的正上部分为顶部。
3.6:F面为左侧面,相对于正面的右侧为左侧面。
4. 产品表面等级划分:产品表面等级根据产品的重要程度,可划分为:A级面,B级面,C级面。
4.1:A级面:客人经常能够看到的表面。
如彩盒正面和正上方,在不移动或转动产品时都能看到的表面。
4.2:B级面:在不移动产品的情况下,客人偶尔能够看到的表面。
如彩盒的侧面和后面,彩盒下部。
4.3:C级面:客人在移动产品或转动产品,或产品被打开后,才可以看到的表面。
如彩盒底面,彩盒内部面, (通常表面不作处理的面)。
5. 检验的条件:5 .1:物件放置于距人体50CM距离,在自然光或40W的日光灯下,光线从人体的后上方45度角或与人眼视线呈90度角照射(正前方以45度照射),被检测物体表面与人眼视线呈45度角。
5.2:检验者眼睛视力良好(≥1.0以上),不能有近视或色盲或弱视等不良现象。
5.3:观察时间为5秒。
文件名称5.4:观察物件不在反光的条件进行观察。
6 .缺陷等级及判定标准:6.1: 缺陷等级定义:6.1.1:致命缺陷:产品缺陷可能会导致对人体生命造成伤害或危及生命.如:血液或不明污染物,放射性物质,有毒物质或液体,腐蚀性物质、logo错误等。
6.1.2:严重缺陷:产品缺陷可能会影响产品的使用性或功能缺失,或者严重影响产品的观赏性,对人体可能造成伤害,或不可擦拭的污物,或缺失重要标识.如产品无法使用,不定位,或严重损伤,破裂,锋利尖角,功能或警告标识等。
6.1.3:轻微缺陷:产品缺陷可能会影响产品的观赏性,但不影响产品的结构/功能和使用性.如可擦拭污物,标识模糊,产品表面轻微划伤等。
印刷品检验标准
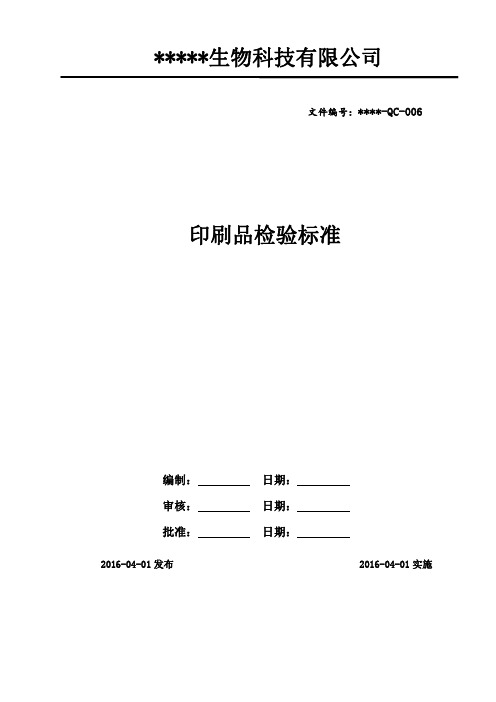
*****生物科技有限公司文件编号:****-QC-006印刷品检验标准编制:日期:审核:日期:批准:日期:2016-04-01发布2016-04-01实施文件更改记录更改单号更改页码更改内容修订版本状态更改人审核人批准人印刷品检验标准版次A/0页码共3页第1页1.0目的:确保公司因生产需要而购进的包装材料符合规定要求。
2.0适用范围:适用于本公司采购的各种印刷品,包括背板、说明书等。
3.0权责区分:3.1采购部按此标准进行包装材料的采购。
3.2品管部按此标准进行包装材料的检验。
3.3供应商提供符合标准要求的包材。
3.4针对来货包材潜在或已经发生的异常,我司出具《纠正/预防措施记录表》,供应商在收到之日起五天内给予我司回复。
配合力度作为供应商评审的依据。
4.0作业流程图:无5.0作业程序:5.1质量标准:5.1.1外观检验项目5.1.1.1印刷:图案清晰、规范、无错版、缺版;色块颜色均匀,无其它色斑;印刷反白处鲜明,无毛边,无油墨堆积痕迹;文字、符号清晰,符合标准封样。
5.1.1.2套印:套色吻合准确、无重影现象;图案清晰,光泽柔和,不允许出现明显色差现象。
5.1.1.3成型:表面光滑无折皱、变形现象。
5.1.1.4模切:模切规范光滑、不得有毛边毛刺。
5.1.1.5包装要求:以双方确认的包装为准、并附出厂检验报告。
5.1.2功能性检验项目5.1.2.1尺寸:尺寸符合所定标准,允许公差±0.5mm。
5.1.2.2油墨耐晒性:黄变灯下十二小时色块不得出现黄变、褪色等现象。
5.1.2.3可读性:条形码不得读不出来。
5.2验收规则:5.2.1外观检验项目采用GB2828.1一般检查水平Ⅱ级一次抽样方案。
印刷品检验标准版次A/0页码共3页第2页****生物科技有限公司编号****-QC-006印刷品检验标准版次A/0页码共3页第3页外观检测合格质量水平AQL值的采用和缺陷种类缺陷类别AQL值缺陷种类A类0.65纸卡破损、缺印、缺字、错版、规格、条码错误、混品种;斑点、污点大于1mm、变形、边缘开口B类 1.50脱膜大于1mm、明显色差、重影、污迹、版面偏移、明显擦伤、折皱、字体印刷不全、不清、套印不准C类 2.50轻微脏污(可擦去)、模切有毛边、外包装破损、脏及未按要求封箱注1:印有产品名称、产品标志的一面为正面;2:印有产品说明、用法等内容的一面为背面,除正面与背面外为侧面;5.2.2功能性检验项目抽样方案:尺寸、条码检测按每批10个样本数随机抽检;油墨耐晒性按同一供应商每五批抽检一次,10个样本数随机抽检;任一样品任一项目不得出现不合格。
印刷厂质量检验标准

印刷厂质量检验标准一、前言随着社会的发展,印刷品在我们的生活中扮演着至关重要的角色。
无论是书籍、报纸、杂志,还是包装盒、宣传单页等,都离不开印刷品的存在。
保证印刷品的质量,对于确保我们获得满意的成品非常重要。
而印刷厂则是负责将设计图转化为实际印刷品的关键环节。
为了确保印刷品的质量达到客户的要求,印刷厂需要制定严格的质量检验标准。
二、印刷品质量检验标准的目的印刷品质量检验标准的目的是确保印刷品在生产过程中的每个环节都符合预期的质量标准。
这不仅可以提高印刷品的质量,还可以节约时间和资源,最终提高客户满意度。
三、印刷品质量检验标准的要求1. 印刷品的颜色准确度印刷品的颜色准确度是衡量印刷品质量的重要指标之一。
印刷厂需要通过使用准确的颜色标准、控制好印刷机的油墨浓度和色彩平衡等方法,确保印刷品的颜色与设计图完全一致。
2. 印刷品的清晰度和细节印刷品的清晰度和细节对于提高印刷品的可读性和观赏性非常重要。
印刷厂应该对印刷机进行定期保养,确保不会出现印刷模糊、断点或印刷漏色等问题。
此外,印刷厂还应该确保印刷品的文字、图片等细节清晰可辨。
3. 印刷品的包装和保护印刷品在运输过程中容易受到损坏,因此包装和保护也成为质量检验的重要环节。
印刷厂需要确保印刷品的包装符合相关的标准,并采取适当的保护措施,以确保印刷品完好无损地到达客户手中。
4. 印刷品的规范性印刷品的规范性包括印刷品的尺寸、格式、折页等方面。
印刷厂需要严格按照客户的要求制作印刷品,并在质量检验过程中确认印刷品是否符合相关的规范。
5. 印刷品的耐久性印刷品的耐久性是指印刷品的质量能够持久地保持在预期水平。
印刷厂在生产过程中需要选择适当的材料,并进行相应的后处理,以确保印刷品在使用过程中不易破损、褪色或变形。
四、印刷品质量检验的方法和流程印刷厂可以通过以下方法和流程进行质量检验:1.视觉检查:通过肉眼对印刷品的颜色、清晰度、细节等进行检查,确认是否符合标准。
印刷品检验标准

轻微缺陷(Min:1.0):缺陷已超过标准要求范围,但不影响产品可用性的一种缺陷
5.2、印刷品不良缺陷定义
a、表面脏污:因生产环境因素或工作台面不整洁等原因造成的脏污;
b、字体模糊:油墨点、断笔或胶水渍;
c、油墨点、断字: 彩盒字体断字,字体周围有油墨点;
d、破损:印刷品因外力致使的破损;
检验项目
不良现象状态描述
允许误差范围
检验仪器
缺陷系列
CRJ
MAJ
MIN
印刷
封面
打花、擦花、刮花
A封面:不可有;
B封面:套底长度﹤20㎜,宽度<0.25㎜,不多于2条。
测卷尺或直尺
√
墨杠、水杠
A封面:不起杠;B封面、封底:眼睛距离被测物30㎝目视不明显。
测卷尺或直尺
√
烫金
掉粉(金烫)、脏污、糊版现象
不允许
目测
√
烫银
走位
无需套位的,烫印走位可在1㎜内;需套位的,烫印走位小于0.3㎜。
目测、菲林尺
√
凸凹压模
爆纸现象
不允许
目测
√
走位
无需套位的、走位可在2㎜内,需套位的走位小于0.3㎜
目测、菲林尺
√
过胶
起泡
封面不可有:封底面积﹤0.7m㎡,不多于2点,距离大于100㎜
菲林尺,卷尺目测
√
耐磨、测试
磨花
不允许
目测
图案机身位不允许,其他位置长度﹤20㎜,宽度﹤0.25㎜,不多于2条,且距离在100㎜以上
目测、卷尺,直尺、菲林尺
√
装订类别
与要求及承认样板不一致
不允许
平版印刷品质量要求及检验标准
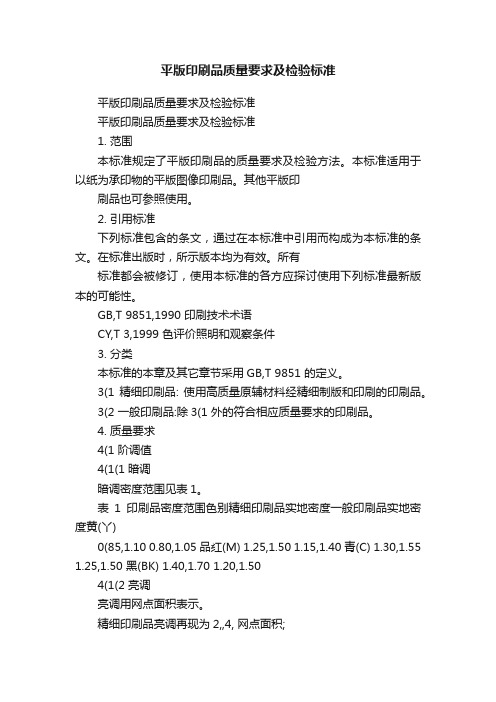
平版印刷品质量要求及检验标准平版印刷品质量要求及检验标准平版印刷品质量要求及检验标准1. 范围本标准规定了平版印刷品的质量要求及检验方法。
本标准适用于以纸为承印物的平版图像印刷品。
其他平版印刷品也可参照使用。
2. 引用标准下列标准包含的条文,通过在本标准中引用而构成为本标准的条文。
在标准出版时,所示版本均为有效。
所有标准都会被修订,使用本标准的各方应探讨使用下列标准最新版本的可能性。
GB,T 9851,1990 印刷技术术语CY,T 3,1999 色评价照明和观察条件3. 分类本标准的本章及其它章节采用GB,T 9851 的定义。
3(1 精细印刷品: 使用高质量原辅材料经精细制版和印刷的印刷品。
3(2 一般印刷品:除3(1 外的符合相应质量要求的印刷品。
4. 质量要求4(1 阶调值4(1(1 暗调暗调密度范围见表1。
表1印刷品密度范围色别精细印刷品实地密度一般印刷品实地密度黄(丫)0(85,1.10 0.80,1.05 品红(M) 1.25,1.50 1.15,1.40 青(C) 1.30,1.55 1.25,1.50 黑(BK) 1.40,1.70 1.20,1.504(1(2 亮调亮调用网点面积表示。
精细印刷品亮调再现为2,,4, 网点面积;一般印刷品亮调再现为3,,5, 网点面积。
4(2 层次亮、中、暗调分明,层次清楚。
4(3 套印多色版图像轮廓及位置应准确套合,精细印刷品的套印允许误差?0(10mm 一般印刷品的套印允许误差?0(20mm。
4(4 网点l网点清晰,角度准确,不出重影。
精细印刷品50, 网点的增大值范围为10,,20,; 一般印刷品50, 网点的增大值范围为10,,25, 。
4(5 相对反差值(K 值)K值应符合表2的规定。
表2相对反差值(K值)范围色别精细印刷品的K值一般印刷品的K值黄0( 25,0(35 0( 20,0(30 品红、青、黑0( 35,0(45 0( 30,0(404(6 颜色颜色应符合原稿,真实、自然、协调。
染料的色差标准

染料的色差标准
染料的色差标准因不同的应用和行业而异,但一般来说,色差在10%以上
即可被认为是可察觉的。
色差的标准可以通过比较标准样品和实际样品的颜色来评估,通常使用色差计或目视评估方法。
色差的标准也可以根据不同的行业和用途而有所不同,例如纺织品、化妆品、食品等。
对于纺织品行业,色差标准通常采用灰卡评级或色差计测量,其中灰卡评级分为1-5级,5级为无色差,1级为最大色差。
色差标准还与批次控制和质量控制有关,例如批差控制在灰卡4级以上,左中右色差控制在4-5级以上,批差△E<1(内控以内)。
染料色差标准的制定需要考虑多种因素,包括染料的质量和纯度、纤维的种类和性质、染色工艺和条件、颜色的视觉感知等。
因此,在实际应用中,需要根据具体情况制定相应的色差标准,以确保产品质量和满足客户需求。
印刷检验标准
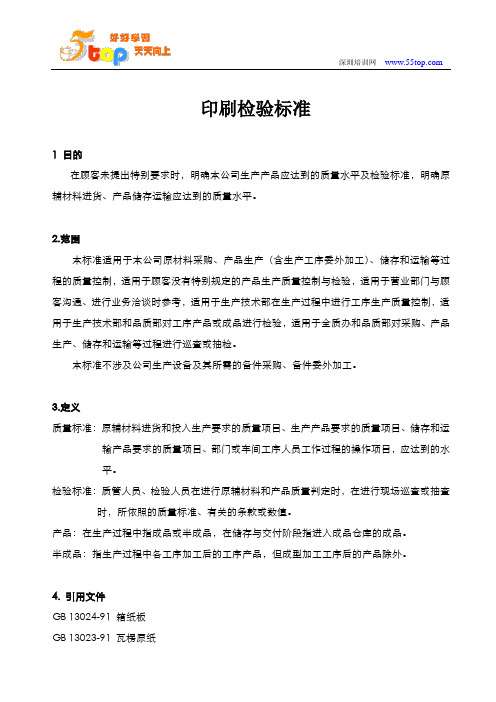
印刷检验标准1 目的在顾客未提出特别要求时,明确本公司生产产品应达到的质量水平及检验标准,明确原辅材料进货、产品储存运输应达到的质量水平。
2.范围本标准适用于本公司原材料采购、产品生产(含生产工序委外加工)、储存和运输等过程的质量控制,适用于顾客没有特别规定的产品生产质量控制与检验,适用于营业部门与顾客沟通、进行业务洽谈时参考,适用于生产技术部在生产过程中进行工序生产质量控制,适用于生产技术部和品质部对工序产品或成品进行检验,适用于全质办和品质部对采购、产品生产、储存和运输等过程进行巡查或抽检。
本标准不涉及公司生产设备及其所需的备件采购、备件委外加工。
3.定义质量标准:原辅材料进货和投入生产要求的质量项目、生产产品要求的质量项目、储存和运输产品要求的质量项目、部门或车间工序人员工作过程的操作项目,应达到的水平。
检验标准:质管人员、检验人员在进行原辅材料和产品质量判定时,在进行现场巡查或抽查时,所依照的质量标准、有关的条款或数值。
产品:在生产过程中指成品或半成品,在储存与交付阶段指进入成品仓库的成品。
半成品:指生产过程中各工序加工后的工序产品,但成型加工工序后的产品除外。
4. 引用文件GB 13024-91 箱纸板GB 13023-91 瓦楞原纸QB 1011-91 单面涂布白板纸ZBY 32024-90 白卡纸GB/T 10335-1995 铜版纸GB 7705-1987 平版装潢印刷品GB/T17497-1988 柔性版装潢印刷品GB/T 6544-1999 瓦楞纸板GB 6543-86 瓦楞纸箱GB 2828-1987 逐批检查计数及抽样表GB/T 6545-1998 瓦楞纸板耐破强度的测定方法GB/T 6546-1998 瓦楞纸板边压强度的测定方法GB/T6547-1998 瓦楞纸板厚度的测定方法GB/T 6548-1998 瓦楞纸板粘合强度的测定方法5 原辅材料质量标准5.1.1 原纸进货质量标准a) 箱纸板——根据GB 13024-91 箱纸板结合我公司实际情况,将箱纸板分为4级:高档箱纸板(一等)、普通箱纸板(二等)、普通箱纸板(三等)、挂面纸(四等)。
- 1、下载文档前请自行甄别文档内容的完整性,平台不提供额外的编辑、内容补充、找答案等附加服务。
- 2、"仅部分预览"的文档,不可在线预览部分如存在完整性等问题,可反馈申请退款(可完整预览的文档不适用该条件!)。
- 3、如文档侵犯您的权益,请联系客服反馈,我们会尽快为您处理(人工客服工作时间:9:00-18:30)。
1.目的:为了有效控制制程质量,确保生产畅通,特制定本规范。
2.范围:适用于印刷工序的检验操作规范。
3. 职责:
3.1 印刷车间主管或组长负责生产任务的分配、生产进度的控制,首件产品的
确认以及生产异常的处理并对潜在的可能发生的问题提出改善措施,进行预防及控制;
3.2 印刷机长负责版面的安装、调试、生产任务的执行,同时机长或助手在生
产过程对产品的自检及生产异常的反馈。
4.内容:色差管理规定与控制
4.1 每次印刷生产时,必须做好首件确认,由当班带班人员现场签字确认,并
且要复一张膜进行比对,当颜色达到要求后方可进行批量生产。
4.2 长单分批生产时,必须要求在版上注明是第几次生产,便于后工序的区
分,防止批次之间的颜色不一致。
4.3 生产过程中每板印完后的倒数第5张统一都要收起来,并与首件样进行
比对,便于控制整批产品的颜色走向,及时发现及时纠正,防止大批量的色差产生。
4.4 印刷机长必须提高抽检的频次,刚开始第一板没100张都要抽取样张对
一次颜色,顺开3000张以后,每300张抽取一次样品核对颜色。
4.5 为了防止长单PS版网点磨损,造成颜色变浅,要求每次印刷印到4万张
后,必须将网点版进行替换,严格执行,避免网点慢慢的变化,没有被及时发现。
4.6 生产过程中,如果发现纸毛比较多,彩印要经常性的停机清洗,防止堆粉
在橡皮上,造成颜色变深。
4.7 品管人员必须协助核对颜色,跟踪产品的质量,经常性独立核对生产的产
品与样稿之间的颜色情况。
4.8 印刷专色产品时,必须借助密度仪进行颜色控制,主要控制的产品为,15%
银露牛奶花生产品,及金双汇系列产品,必须控制颜色,标准值Δ必须控制在1.5以内。
银鹭产品色差控制重点:
系列:桂圆莲子八宝:主要控制碗旁边渐变平网,底色不能偏浅。
要重点控制,且量较大。
桂圆八宝:但是要注意八宝粥系列底色。
4.9 最后要求后工序分批入库,分批出货,共同控制色差。
4.10 作业不良数量应清点,单独存放,生产报表上应填写作业不良数,由巡检清
点后方可报废。
4.11使用表单
《生产计划》、《生产工作单》、《印刷生产日报表》、《首件确认记录表》。