连杆零件加工工艺设计表
连杆零件的锻模设计

连杆零件的锻模设计目录一.设计锻件图 (3)二.绘制锻件图 (8)三.设计终锻模膛 (9)四.确定锻造设备吨位 (13)五.设计预锻模膛 (14)六.绘制计算毛坯图 (15)七.确定坯料尺寸 (25)八.制坯模膛设计 (26)九.连杆锤锻模结构设计 (31)总结 (33)参考文献 (35)一.设计锻件图1.确定分模面分模面选在最大直径中部,如图下图所示。
把复杂形状放在上模,利用锻锤打击惯性使上模成型饱满,又可以利用锻件自重从上模容易脱出。
根据零件图很容易确定上下模对称直线分模。
分模面零件图2.确定加工余量和公差初估算锻件的质量为1.4kg;经查表40钢材质系数为M1;形状复杂系数属s3级。
S= mfmn=140024⨯⨯4⨯7.8510=0.19,查表5—3得水平方向和厚度方向的单边加工余量为 1.7~2.2mm,取2mm。
经查表5—4得高度公差为2.0 1.40.6+-mm,长度公差为2.8 1.90.9+-mm,宽度公差为2.2 1.50.7+-mm,错差公差为0.6mm残留飞边公差为0.7mm。
厚度公差经查表5—5,为2.0 1.50.6+-mm。
因该连杆机械加工时以大小头断面为定位基准,为保证平面度锻件在热处理、清理后要增加一道压印工序(平面冷精压)。
压印后机加工余量单边取0.75mm压印所需余量单边为0.4mm,则压印后大小头高度为(38+2×0.75)mm=39.5±0.2mm,模锻后大小头高度为(38+2×0.75+2×0.4)mm=40.3mm,考虑到保证压印有余量,模锻后厚度公差调整为1.3 1.00.3+-mm.考虑到大头叉部成型困难,故宽度公差增加,压印后,水平方向压印略有增加,故加工余量可适当减少,表现在宽度公差取3.5 2.51.0+-mm,长度公差取1.5 1.50+mm.表2-6 锤上模锻水平方向尺寸公差(mm)表2-7 内、外表面的加工余量Z1(单面)(mm)3.确定模锻斜度为了使锻件易于从模堂中取出,一般锻件与模堂壁接触部分须带一定的斜度,这斜度称为模锻斜度。
连杆的加工工艺分析

发动机连杆加工工艺分析与设计摘要因为连杆是活塞式发动机和压缩机的主要零件之一,其大头孔与曲轴连接,小头孔通过活塞销与活塞连接,其作用是将活塞的气体压力传送给曲轴,又收曲轴驱动而带动活塞压缩汽缸中的气体。
连杆承受的是冲击动载荷,因此要求连杆质量小,强度高。
所以在安排工艺过程时,按照“先基准后一般”的加工原则。
连杆的主要加工表面为大小头孔和两端面,较重要的加工表面为连杆体和盖的结合面及螺栓孔定位面。
由于连杆既是传力零件,又是运动件,不能单靠加大连杆尺寸来提高其承载能力,须综合材料选用、结构设计。
在对其设计中我们先对连杆工艺过程分析,联系实际通过对其具体设计的了解进行连杆机械加工工艺过程分析及其一些机械加工余量、工序尺寸的确定。
关键词:发动机,连杆,定位基面,工艺设计目录第一章发动机的概述 (1)1.1发动机的定义 (1)1.2发动机的发展历史 (1)1.3发动机的分类 (2)1.4发动机的总体结构 (2)第二章连杆的分析 (3)2.1连杆的作用 (3)2.2连杆的结构特点 (3)2.3连杆的工艺分析 (4)第三章连杆工艺规程设计 (7)3.1确定连杆的材料和毛坯 (7)3.2连杆的机械加工工艺过程 (7)3.4连杆的机械加工工艺过程的夹紧方法 (8)第四章连杆机械加工工艺过程分析 (9)4.1.工艺过程的安排 (9)4.2连杆主要加工表面的工序安排 (9)4.3连杆机械加工工艺路线 (10)第五章机械加工余量、工序尺寸的确定 (12)5.1大头孔两端面的加工余量及工序尺寸 (12)5.2小头孔端面加工余量及工序尺寸 (12)5.3小头孔的加工余量及工序尺寸 (12)5.4大头孔的加工余量及工序尺寸 (13)5.5螺栓孔加工余量及工序尺寸 (13)5.6小头油孔加工余量及工序尺寸 (13)5.7连杆盖定位销孔加工余量及工序尺寸 (14)5.8小头油孔加工余量及工序尺寸 (14)5.9确定切削用量及工时 (14)5.10工艺卡片的制订 (15)谢辞 (29)参考资料 (30)附录 (31)第一章发动机的概述1.1发动机的定义发动机,又称为引擎,是一种能够把一种形式的能转化为另一种更有用的能的机器,通常是把化学能转化为机械能。
汽车连杆的加工工艺及夹具设计
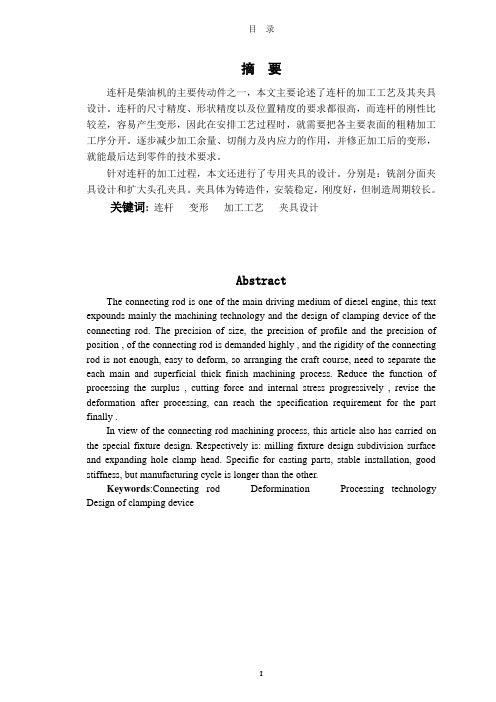
磨
以基面和一侧面定位装夹工件,磨连杆体和盖的结合面
M7350
9
铣
以基面及结合面定位装夹工件,铣连杆体和盖 mm 8mm斜槽
X62组合夹具或专用工装
10
锪
以基面、结合面和一侧面定位,装夹工件,锪两螺栓座面 mm,R11mm,保证尺寸 mm
X62W
11
钻
钻2— 10mm螺栓孔
Z3050
12
扩
先扩2— 12mm螺栓孔,再扩2— 13mm深19mm螺栓孔并倒角
连杆的作用是把活塞和曲轴联接起来,使活塞的往复直线运动变为曲柄的回转运动,以输出动力。因此,连杆的加工精度将直接影响柴油机的性能,而工艺的选择又是直接影响精度的主要因素。反映连杆精度的参数主要有5个:(1)连杆大端中心面和小端中心面相对连杆杆身中心面的对称度;(2)连杆大、小头孔中心距尺寸精度;(3)连杆大、小头孔平行度;(4)连杆大、小头孔尺寸精度、形状精度;(5)连杆大头螺栓孔与接合面的垂直度。
摘 要
连杆是柴油机的主要传动件之一,本文主要论述了连杆的加工工艺及其夹具设计。连杆的尺寸精度、形状精度以及位置精度的要求都很高,而连杆的刚性比较差,容易产生变形,因此在安排工艺过程时,就需要把各主要表面的粗精加工工序分开。逐步减少加工余量、切削力及内应力的作用,并修正加工后的变形,就能最后达到零件的技术要求。
根据机械加工工艺手册第一卷表3225表32262271平面加工的工序余量mm单面加工方法单面余量经济精度工序尺寸表面粗糙度毛坯4312540320it10100388100it805038205038170mm2连杆铸造出来的总的厚度为h38mm182确定工序尺寸及其公差根据机械制造技术基础课程设计指导教程表229表2341大头孔各工序尺寸及其公差铸造出来的大头孔为55mm工序名称工序基本余量工序经济精度工序尺寸最小极限尺寸表面粗糙度111911191230123063一次粗镗12301230125扩孔2小头孔各工序尺寸及其公差根据机械制造技术基础课程设计指导教程表229表230工序名称工序基本余量工序经济精度工序尺寸最小极限尺寸表面粗糙度29033290521008429084计算工艺尺寸链191连杆盖的卡瓦槽的计算maxmax2525mmminmin247mmesesa020005025mmeieia020010030mmeiaesa055mm25mm2525mm192连杆体的卡瓦槽的计算maxmax835mmminminesesa035mmeieia020mmeiaesa035020055mm110工时定额的计算1101铣连杆大小头平面选用x52k机床根据机械制造工艺设计手册表2481选取数据铣刀直径d100mm切削速度v60mm铣刀齿数z475rmin根据表3131按机床选取n500mimml11550mml2mm基本时间t011min按表2546辅助时间t018min1102粗磨大小头平面选用m7350磨床根据机械制造工艺设计手册表24170选取数据砂轮直径d40mm磨削速度v03mm0033mmr1588rmin根据表3148按机床选取n磨削工时为
连接杆零件工艺及夹具设计.doc

专业:数控技术及应用班级:姓名:学号:指导老师:一、设计题目(附图):连接杆零件机械加工工艺规程制订及第工序工艺装备设计。
二、设计条件:l、零件图;2、生产批量:中批量生产。
三、设计内容:1、零件图分析:l)、零件图工艺性分析(结构工艺性及技术条件分析);2)、绘制零件图;2、毛坯选择:1)、毛坯类型;2)、余量确定;3)、毛坯图。
3、机械加工工艺路线确定:1)、加工方案分析及确定;2)、基准的选择;3)、绘制加工工艺流程图(确定定位夹紧方案)。
4、工艺尺寸及其公差确定:1)、基准重合时(工序尺寸关系图绘制);2)、利用尺寸关系图计算工序尺寸;3)、基准不重合时(绘制尺寸链图)并计算工序尺寸。
5、设备及其工艺装备确定:6、切削用量及工时定额确定:确定每道工序切削用量及工时定额。
7、工艺文件制订:1)、编写工艺设计说明书;2)、填写工艺规程;(工艺过程卡片和工序卡片)8、指定工序机床夹具设计:1)、工序图分析;2)、定位方案确定;3)、定位误差计算;4)、夹具总装图绘制。
9、刀具、量具没计。
(绘制刀具量具工作图)10、某工序数控编程程序设计。
四、上交资料(全部为电子文稿):1、零件机械加工工艺规程制订设计说明书一份;(按统一格式撰写)2、工艺文件一套(含工艺流程卡片、每一道工序的工序卡片含工序附图);3、机床夹具设计说明书一份;(按统一格式撰写)4、夹具总装图一张(A4图纸);零件图两张(A4图纸);5、刀量具设计说明书一份;(按统一格式撰写)6、刀具工作图一张(A4图纸);量具工作图一张(A4图纸)。
7、数控编程程序说明书五、起止日期:2009 年11 月2 日一2009 年12 月25 日(共8 周)六、指导教师:七、审核批准:教研室主任:系主任:年月日八、设计评语:九、设计成绩:年月日目录第一部分工艺设计说明书-------------------------------------------------------------------31.零件工艺性分析--------------------------------------------------------------------31.1零件图合理性分析--------------------------------------------------------------------31.2零件结构功用分析----------------------------------------------------------------41.3零件结构工艺性分析----------------------------------------------------------------41.4件技术要求分析--------------------------------------------------------------------42.毛坯选择----------------------------------------------------------------------------------52.1 毛坯类型的确定----------------------------------------------------------------------52.2 毛坯余量确定------------------------------------------------------------------------52.3毛坯-零件合图草图----------------------------------------------------------------63.机加工工艺路线确定------------------------------------------------------------------63.1 加工方法分析确定-------------------------------------------------------------------63.2定位基准的选择-----------------------------------------------------------------------73.3加工顺序的安排与定位基准选择----------------------------------------------------83.4加工阶段的划分---------------------------------------------------------------------103.5加工阶段的划分说明----------------------------------------------------------------113.6主要机加工工序简图---------------------------------------------------------------134.工序尺寸及公差确定--------------------------------------------------------------175.设备及工艺装备确定------------------------------------------------------------175.1 机床的选用------------------------------------------------------------------------175.2 刀具的选用------------------------------------------------------------------------186.切削用量与工时定额的确定------------------------------------------------------18 第二部分夹具说明书------------------------------------------------------------------------201.工序尺寸精度分析--------------------------------------------------------------------202.定位方案的确定----------------------------------------------------------------------203.定位元件的确定---------------------------------------------------------------------214.定位误差的计算--------------------------------------------------------------------225.夹紧方案及元件确定-------------------------------------------------------------236.图-------------------------------------------------------------------------------------23第三部分刀具设计说明书----------------------------------------------------------------261.尺寸精度分析--------------------------------------------------------------------------262.刀具类型确定--------------------------------------------------------------------------263.刀具设计参数确定------------------------------------------------------------------264.刀具工作草图-----------------------------------------------------------------------27 第四部分量具设计说明书---------------------------------------------------------------281.量具类型的确定----------------------------------------------------------------------282.极限量具尺寸公差的确定----------------------------------------------------------283.极限量具尺寸公差带图-------------------------------------------------------------284.极限量具结构设计-------------------------------------------------------------------29第五部分数控编程-------------------------------------------------------------------------32 1.确定编程圆点,编程坐标点-----------------------------------------------------32 2.加工顺序、走刀路线及工艺路线的确定---------------------------------------323. 数值的计算---------------------------------------------------------------------------324. 刀具的选择----------------------------------------------------------------------------325. 编写数控加工程序---------------------------------------------------------------33 第六部分设计总结-------------------------------------------------------------------------35的七部分参考文献-------------------------------------------------------------------------36第一部分工艺设计说明书1.零件图工艺性分析图1.11.1零件图合理性分析该图基本结构设计较为合理,但原零件图上有些部分的绘图出现问题在设计前需要进行说明更正。
机械加工工艺过程卡片(连杆)

机械加工工艺过程卡片(连杆)1.零件名称:连杆2.零件材料:45号钢(轴承表面淬硬)3.零件图号:XXX-XXX-XXX4.工艺流程:(1)设备:平面磨床(2)工艺过程:切削加工(3)操作工序:a.夹紧工件b.调整砂轮回转方向c.调整砂轮至合适位置d.启动机床(空转)e.进给手柄接触工件f.开始磨削g.调整进给速度h.调整工序参数i.完成工艺过程(4)工艺要求:a.加工面精度:IT8b.表面粗糙度:Ra0.63c.无划伤、裂纹、气孔等缺陷5.设备及工具:a.平面磨床b.砂轮c.夹具d.工件轴承支撑e.尺子、千分尺6.工艺参数:a.磨削速度:25m/sc.每次进给量:0.03mmd.每分钟磨削量:8~10mme.主轴转速:1000r/min7.安全操作:a.操作前需检查设备完好性,切勿带有松动零件或异物。
b.操作中严禁拆卸、调整设备部件。
c.操作后关闭机床电源,清除设备上的切削液并进行设备保养。
d.操作时需戴好安全帽、手套等防护设备,不得穿松散衣物。
8.维护保养:a.平时需定期检查设备零部件磨损情况并予以更换。
b.定期对砂轮进行磨石、清洗、调整。
c.清理设备上固定在夹具上的金属屑、切屑等杂物。
d.定期涂抹润滑油,保证机床各部件运转顺畅。
9.质量控制:a.进行严格的质量检测程序,对于加工精度不符合要求的工件予以返工或废品处理。
b.对于符合质量要求的工件进行喷砂抛光处理。
c.定期对设备进行校准,保证加工精度和表面粗糙度符合要求。
d.要求工艺人员自觉遵守操作规程,对于不符合操作规程情况进行追究和整改。
柴油机连杆零件机械加工工艺过程卡片及工序卡(第一部分)_百度解析
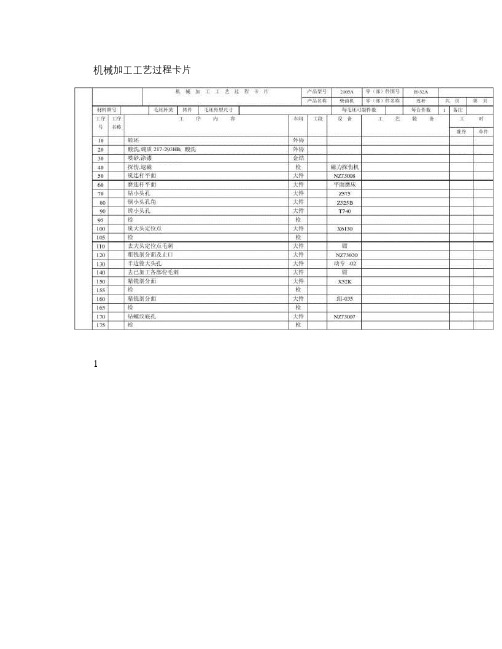
机械加工工艺过程卡片1
3
4
5
6
7
9
10
产品名称柴油机零(部)件名称车间大件老连杆连杆工序号 120 毛坯外型尺寸共( 43)页第( 8 )页材料牌号工序名称粗铣剖分面及止口毛坯种类每毛坯可制件数每台件数设备名称设备型号 NZ73020 设备编号同时加工件数 1 夹具编号夹具名称切削液工序工时准终 H-32-221-06 工步号工步内容工艺装备主轴转速切削速度连杆剖分面粗铣刀进给量切削深度进给次数工步工时机动
辅助单件 r/min 粗铣剖分面至尺寸粗铣止口至尺寸 75 75 m/min 22.4 24.7 mm/r 0.80 0.80 mm 4.5 4.5 1 描图 1 1 描校底图号装订号设计(日期)审核(日期)标准化(日期)会签(日期)标记处数更改文件号签字日期标记处数更改文件号签字日期机械加工工序卡片产品型号产品名称 2105A 柴油机零(部)件图号零(部)件名称 H-32A 连杆共( 43 )页第( 9 )页 11
车间工序号 130 工序名称半边镗大头孔每毛坯可制件数材料牌号毛坯种类毛坯外型尺寸每台件数设备名称粗镗大头孔专机夹具编号设备型号设备编号同时加工件数 1 夹具名称切削液工位器具编号工位器具名称准终工序工时单件 H-32-734-06 工步号工步内容工艺装备主轴转速切削速度连杆大头孔粗镗夹具进给量切削深度进给次数工步工时机动辅助 r/min 半边镗大头孔至尺寸 270
m/min 62.77 mm/r 0.25 mm 5 1 描描图校 1 底图号装订号设计(日期)审核(日期)标准化(日期)会签(日期)标记处数更改文件号签字日期标记处数更改文件号签字日期 12。
发动机连杆-工艺过程卡、工序卡(新版)

1.基面向外装夹,精铣体结合面至尺寸 、
平面度0.025,粗糙度1.6
2.基面向外装夹,精铣盖结合面,保证结合面距大于43,平面度0.025,垂直度0.08
3.体盖分别钻中心孔
4.体盖分别扩中心孔,保证中心距90
5.体盖分别铰销钉孔,保证尺寸,中心距90
6.钳工去毛刺,清洗
7.装销钉
2.标记面向外装夹,扩螺栓孔至尺寸 ,保证中心距
。
3.铰螺栓孔至尺寸 ,对称度0.25,位置度0.18
4.体盖螺栓孔倒角
5.钳工去毛刺
加工中心
中心钻,麻花钻,铰刀
16
精磨上下两平面
1.同时磨两平面,保证尺寸 表面粗糙度0.8,大头孔平行度0.025,垂直度0.015,小头孔平面对称度0.25
M7350
砂轮
17
精半精镗小头孔至
3.精镗大头孔至尺寸
4.精镗小头孔至尺寸,
5.小头孔倒角 ,保证倒角面粗糙度12.5
6.钳工去毛刺
加工中心
硬质合金刀
18
钻小头油孔
1.标记面向外装夹,钻油孔,加工至尺寸
2.标记面向外装夹,钻阶梯孔,加工至
3.孔口倒角
加工中心
加工中心
镗刀
8
铣体盖螺栓凸台面
1.基面向外装夹,粗铣体、盖凸台面,保证尺寸
2..基准面向外装夹,精铣体、盖凸台面,保证尺寸
加工中心
铣刀
9
锯断
1.基面向外装夹,锯断连杆,保证尺寸190
锯床
锯条
10
粗铣体盖结合面
1.基面向外装夹,铣体结合面,保证尺寸
2.基面向外装夹,铣盖结合面,保证尺寸
加工中心
连杆零件的机械加工工艺规程和专用夹具设计
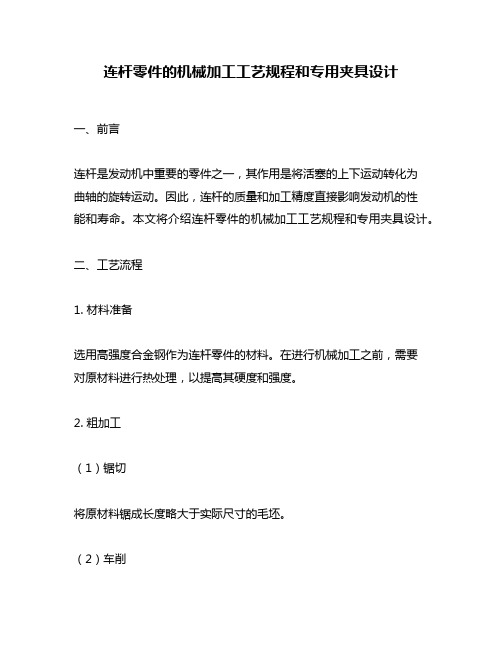
连杆零件的机械加工工艺规程和专用夹具设计一、前言连杆是发动机中重要的零件之一,其作用是将活塞的上下运动转化为曲轴的旋转运动。
因此,连杆的质量和加工精度直接影响发动机的性能和寿命。
本文将介绍连杆零件的机械加工工艺规程和专用夹具设计。
二、工艺流程1. 材料准备选用高强度合金钢作为连杆零件的材料。
在进行机械加工之前,需要对原材料进行热处理,以提高其硬度和强度。
2. 粗加工(1)锯切将原材料锯成长度略大于实际尺寸的毛坯。
(2)车削采用车床进行粗加工,先将毛坯两端面加工成平行面,然后进行外圆柱面、内孔等基本形状的车削。
(3)铣削采用立式铣床进行粗加工,主要是对连杆头部进行铣削,并开出油孔等结构。
3. 精密加工(1)磨削采用平面磨床和圆柱磨床对外圆柱面、内孔和连杆头等进行精密加工。
(2)钻孔采用钻床对油孔等细小结构进行加工。
(3)拉削采用拉床对轴向槽、键槽等进行加工。
4. 热处理将加工好的连杆零件进行热处理,以提高其硬度和强度。
通常采用淬火和回火的方式进行处理。
5. 组装将经过热处理的连杆零件组装到曲轴上,并进行调整,以确保其与其他零件的配合精度和运动平稳性。
三、专用夹具设计为了保证连杆零件在机械加工过程中的精度和稳定性,需要设计专用夹具。
下面介绍一种常见的夹具设计方案:1. 夹具整体结构该夹具主要由夹紧块、支撑块、定位块、压板等组成。
其中,夹紧块负责固定毛坯,支撑块负责支撑毛坯,在车削时起到了很好的辅助作用;定位块则是为了确保毛坯在夹具中的位置准确;压板则是为了防止毛坯在车削时发生移动。
2. 夹具夹紧方式该夹具采用机械夹紧的方式,通过螺旋压板来实现对毛坯的夹紧。
在进行车削等加工时,需要根据不同工序进行调整,以确保毛坯的稳定性和精度。
3. 夹具使用注意事项在使用该夹具时,需要注意以下几点:(1)夹具的各个部位需要经常清洗和润滑,以保证其正常运作。
(2)在进行车削等加工时,需要根据不同工序进行调整,并且要保证毛坯与夹具之间的接触面积充分。
连杆零件加工工序工艺卡
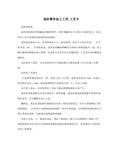
连杆零件加工工序,工艺卡连杆的结构连杆是较细长的变截面非圆形杆件,其杆身截面从大头到小头逐步变小,以适应在工作中承受的急剧变化的动载荷。
连杆是由连杆大头、杆身和连杆小头三部分组成,连杆大头是分开的,一半与杆身为一体,一半为连杆盖,连杆盖用螺栓和螺母与曲轴主轴颈装配在一起。
为了减少磨损和磨损后便于修理,在连杆小头孔中压人青铜材套,大头孔中装有薄壁金属轴瓦。
为方便加工连杆,可以在连杆的大头侧面或小头侧面设置工艺凸台或工艺侧面。
连杆的工艺特点(1)连杆体和盖厚度不一样,改善了加工工艺性。
连杆盖厚度为31mm,比连杆杆厚度单边小3.8mm,盖两端面精度产品要求不高,可一次加工而成。
由于加工面小,冷却条件好,使加工振动和磨削烧伤不易产生。
连杆杆和盖装配后不存在端面不一致的问题,故连杆两端面的精磨不需要在装配后进行,可在螺栓孔加工之前。
螺栓孔、轴瓦对端面的位置精度可由加工精度直接保证,而不会受精磨加工精度的影响。
(2)连杆小头两端面由斜面和一段窄平面组成。
这种楔形结构的设计可增大其承压面积,以提高活塞的强度和刚性。
在加工方面,与一般连杆相比,增加了斜面加工和小头孔两斜面上倒角工序;用提高零件定位及压头导向精度来避免衬套压偏现象的发生,但却增加了压衬套工序加工的难度。
(3)带止口斜结合面。
连杆结合面结构种类较多,有平切口和斜切口,还有键槽形、锯齿形和带止口的。
该连杆为带止口斜结合面.明确毛坯状况连杆材料一般采用45钢或40Cr、45Mn2等优质钢或合金钢,近年来也有采用球墨铸铁的。
钢制连杆都用模锻制造毛坯。
连杆毛坯的锻造工艺有两种方案:将连杆体和盖分开锻造;连杆体和盖整体锻造。
整体锻造或分开锻造的选择决定于锻造设备的能力,显然整体锻造需要有大的锻造设备拟定工艺路线;连杆的尺寸精度、形状精度和位置精度的要求都很高,但刚度又较差,容易产生变形。
连杆的主要加工表面为大小头孔、两端面、连杆盖与连杆体的接合面和螺栓等。
柴油机连杆零件机械加工工艺过程卡片及工序卡知识讲解

柴油机连杆零件机械加工工艺过程卡片及工序卡知识讲解柴油机连杆是柴油机中重要的零件之一,它连接曲轴和活塞,将曲轴的旋转运动转化为活塞的往复运动,从而驱动柴油机的工作。
柴油机连杆的机械加工工艺过程卡片及工序卡是用来记录和指导柴油机连杆的加工过程和工艺参数的。
1.零件名称:柴油机连杆2.材料:一般为45钢、40Cr、20CrNiMo等合金钢3.工艺路线:将柴油机连杆的加工过程按顺序列出来,包括加工工序和加工方法。
4.重要加工尺寸:记录柴油机连杆的重要加工尺寸和公差要求。
5.设备:记录用于加工柴油机连杆的设备,如车床、铣床、磨床等。
6.夹具:记录用于夹紧柴油机连杆的夹具,以确保加工精度和安全性。
7.工艺参数:包括切削速度、进给量、切削刃数、冷却液等参数,用于指导实际加工过程。
8.检查和试验要求:记录柴油机连杆的检查和试验要求,包括尺寸测量、表面质量和硬度等。
1.材料选型和切割:根据设计要求和机械性能要求选择合适的材料,并使用切割工具将材料切割成合适尺寸的坯料。
2.粗车:使用车床进行粗车加工,将连杆的外形加工到接近最终尺寸。
3.粗铣:使用铣床进行粗铣加工,加工连杆上的凸台、凹槽等特殊形状。
4.精车:使用车床进行精车加工,将连杆的主轴孔和大端孔加工到最终尺寸和精度要求。
5.苦挤:在车床上进行苦挤加工,将连杆上的小端孔和销孔加工到最终尺寸。
6.精铣:使用铣床进行精铣加工,加工连杆上的油孔、油槽等细小结构。
7.精磨:使用磨床进行精磨加工,提高连杆的表面精度和光洁度,并满足尺寸和形状的公差要求。
8.清洗和检验:使用清洗设备进行清洗,对连杆进行尺寸和形状的检查,确保加工质量和精度。
9.装配:将各个部分进行装配,并进行试验验证,确保连杆的性能和质量。
以上是柴油机连杆的机械加工工艺过程卡片及工序卡的知识讲解,通过对加工工艺过程和工序的记录和指导,可以提高柴油机连杆的加工效率和质量,确保柴油机的正常运行。
连杆机械加工工艺流程及工艺装备设计方案

连杆机械加工工艺流程及工艺装备设计方案1. 引言连杆是机械工程中常用的零件之一,用于将转动运动转变为往复运动。
为了保证连杆的准确性和可靠性,需要进行机械加工。
本文将介绍连杆机械加工的工艺流程,并提出相应的工艺装备设计方案。
2. 加工工艺流程连杆的加工工艺流程通常包括以下几个步骤:2.1 材料准备首先需要根据设计要求选择合适的材料,常见的连杆材料有铸铁、钢材等。
在材料准备阶段,需要对材料进行检验,确保材料的质量符合要求。
2.2 车削加工车削加工是连杆加工的主要工艺之一。
在车削加工中,需要使用车床进行加工,在加工过程中,根据设计要求进行车削操作,将连杆的外形和尺寸加工到合适的精度。
2.3 钻孔加工除了车削加工外,还需要进行钻孔加工,以便安装其他零件。
钻孔加工可以使用钻床进行,根据设计要求进行钻孔操作,并确保钻孔的位置和尺寸的准确性。
2.4 磨削加工磨削加工可以提高连杆的精度和表面质量。
磨削加工可以使用磨床进行,根据设计要求进行磨削操作,将连杆的表面磨削到合适的精度和光洁度。
2.5 组装与调试加工完成后,需要进行连杆的组装与调试。
在组装过程中,需要根据装配要求进行部件的安装,确保各部件的相互配合良好。
完成组装后,需要进行调试,验证连杆的性能和可靠性。
3. 工艺装备设计方案为了确保连杆的加工工艺顺利进行,需要设计相应的工艺装备。
以下是连杆机械加工工艺装备的设计方案:3.1 车床车床是连杆机械加工中不可缺少的工艺装备之一。
选择合适的车床可以实现对连杆进行精确的车削加工。
根据连杆的尺寸和材料,可以选择合适的车床类型,如平面车床、立式车床等。
3.2 钻床钻床主要用于连杆的钻孔加工。
选择合适的钻床可以实现对连杆钻孔的准确性和效率。
根据连杆的钻孔要求,可以选择合适的钻床类型,如立式钻床、卧式钻床等。
3.3 磨床磨床可以提高连杆的加工精度和表面质量。
选择合适的磨床可以实现对连杆的磨削加工。
根据连杆的磨削要求,可以选择合适的磨床类型,如平面磨床、圆柱磨床等。
典型零件(连杆)的工艺及工装毕业设计
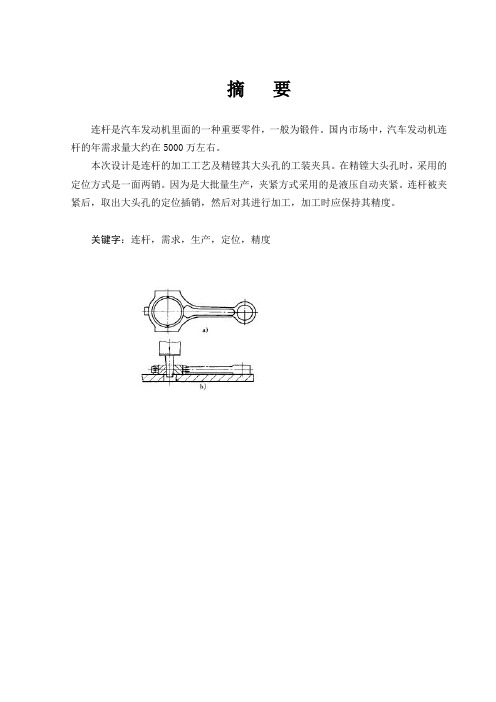
摘要连杆是汽车发动机里面的一种重要零件,一般为锻件。
国内市场中,汽车发动机连杆的年需求量大约在5000万左右。
本次设计是连杆的加工工艺及精镗其大头孔的工装夹具。
在精镗大头孔时,采用的定位方式是一面两销。
因为是大批量生产,夹紧方式采用的是液压自动夹紧。
连杆被夹紧后,取出大头孔的定位插销,然后对其进行加工,加工时应保持其精度。
关键字:连杆,需求,生产,定位,精度ABSTRACTLinkage is an automotive engine inside an important part, generally forgings. Domestic market, the car engine connecting rod in the annual demand of about 50 million or so.The design of the connecting rod processing and precision boring big holes in its fixture. Precision Boring bulk of the hole, the position is a two way marketing. Because of mass production, clamping methods make use of automatic hydraulic clamping. Linkage was clamping, removal of the bulk of positioning bolt hole, then its processing, and processing should maintain its accuracy.Keywords: linkage, demand, production, positioning, accuracy前言制造业特别是机械制造业是国民经济的支柱产业,现代制造业正在改变着人们的生产方式、生活方式、经营管理模式乃至社会的组织结构和文化。
机械加工工艺过程卡片及工序卡

连杆加工工艺过程卡片及工序卡学生姓名届 2013学院(系)机械学院专业机械工程及自动化指导教师职称副教授产品名称连杆总成零件名称连杆盖第(2)页车间工序号工序名称材料牌号02 粗铣盖两大平面45Mn2毛坯种类毛坯外形尺寸每毛坯可制件数每台件数模锻 1 4设备名称设备型号设备编号同时加工件数端面铣床自制 1夹具编号夹具名称切削液J-01 铣夹具工序工时(分)准终单件3.1 工步号工步内容工艺装备主轴转速r/min切削速度m/min进给量mm/r切削深度mm进给次数工步工时机动辅助1 粗铣盖一大平面(先加工凸起面)刀具:端铣刀盘D-01 n=610 v=191 f=0.281t=0.5 0.25 2.85(1)保证加工面距中心线尺寸18.35±0.102t=0.5(2)两大平面对称中心线允差±0.25mm 量具:卡尺3t=0.32 粗铣另一大平面36.720.04t=0.2 (1)其一平面必垂直设计(日期)校对(日期)审核(日期)标准化(日期)会签(日期)标记处数更改文件号签字日期标记处数更改文件号签字日期产品名称连杆总成零件名称连杆体第(3)页车间工序号工序名称材料牌号03 粗铣杆两大平面45Mn2毛坯种类毛坯外形尺寸每毛坯可制件数每台件数模锻 1 4设备名称设备型号设备编号同时加工件数立铣 X52 1夹具编号夹具名称切削液J-02 铣夹量工序工时(分)准终单件3.1 工步号工步内容工艺装备主轴转速r/min切削速度m/min进给量mm/r切削深度mm进给次数工步工时机动辅助1 粗铣盖一大平面(先加工凸起面)刀具:端铣刀盘D-02 n=1180 v=163 s=0.508 t=15 1 0.6 2.5(1)保证加工面距中心线尺寸18.35±0.10(2)两大平面对称中心线允差±0.25mm 量具:卡尺2 粗铣另一大平面36.720.0(1)其中一大平面赢平直不直度≯0.10mm设计(日期)校对(日期)审核(日期)标准化(日期)会签(日期)标记处数更改文件号签字日期标记处数更改文件号签字日期产品名称连杆总成零件名称连杆体第(4)页车间工序号工序名称材料牌号04 钻小头孔45Mn2毛坯种类毛坯外形尺寸每毛坯可制件数每台件数模锻 1 4设备名称设备型号设备编号同时加工件数钻床 Z535 1夹具编号夹具名称切削液J-03 钻夹具乳化液工序工时 (分)准终单件3 工步号工步内容工艺装备主轴转速r/min切削速度m/min进给量mm/r切削深度mm进给次数工步工时机动辅助1 钻连杆小头孔Φ24.530.0+粗糙度6.3 刀具:锥柄钻头Φ24.5 n=195 v=15 f=0.2 1 1.2 1.82 检验Φ24.530.0+孔与小头外圆应同心圆偏差≤0.25mm 量具:卡尺凸起面朝下定位夹紧设计(日期)校对(日期)审核(日期)标准化(日期)会签(日期)标记处数更改文件号签字日期标记处数更改文件号签字日期产品名称连杆总成零件名称连杆体第(5)页车间工序号工序名称材料牌号05 小头孔倒角45Mn2毛坯种类毛坯外形尺寸每毛坯可制件数每台件数模锻 1 4设备名称设备型号设备编号同时加工件数钻床 Z535 1夹具编号夹具名称切削液J-04工序工时 (分)准终单件0.96 工步号工步内容工艺装备主轴转速r/min切削速度m/min进给量mm/r切削深度mm进给次数工步工时机动辅助1 小头孔倒角面角1.520.0 ×45°刀具:锥柄钻头Φ28 n=68 V=6 f=手动 1.52 0.46 0.52 检验尺寸及粗糙度设计(日期)校对(日期)审核(日期)标准化(日期)会签(日期)标记处数更改文件号签字日期标记处数更改文件号签字日期产品名称连杆总成零件名称连杆体和盖第(6)页车间工序号工序名称材料牌号06 粗磨杆盖大平面45Mn2毛坯种类毛坯外形尺寸每毛坯可制件数每台件数模锻 1 4设备名称设备型号设备编号同时加工件数磨床 M7475B 杆16盖50夹具编号夹具名称切削液电磁吸盘乳化液工序工时 (分)准终单件4.09 工步号工步内容工艺装备主轴转速r/min切削速度m/min进给量mm/r切削深度mm进给次数工步工时机动辅助1 粗磨一大平面36.410.0+以平整一大平面定刀具:研轮GB60ZRAP350×40×127 n=1440 v=1582 f纵=3-28 T=0.02 34 2.5 1.59位对称磨削。
汽车发动机连杆caxa零件图-及加工规程分析

•夹具使用 •应具备适应“一面一孔一凸台”的统一精基准。而 大小头定位销是一次装夹中镗出,故须考虑“自为 基准”情况,这时小头定位销应做成活动的,当连 杆定位装夹后,再抽出定位销进行加工。
端面间有配合要求,而连杆小头两端面与
活塞销孔座内档之间没有配合要求。连杆
大头端面间距离尺寸的公差带正好落在连
杆小头端面间距离尺寸的公差带中,这给 连杆的加工带来许多方便。
•螺栓孔的技术要求 •在前面已经说过,连杆在工作过 程中受到急剧的动载荷的作用。这 一动载荷又传递到连杆体和连杆盖 的两个螺栓及螺母上。因此除了对
•大、小头孔轴心线在两个互相垂直方向 的平行度
•两孔轴心线在连杆轴线方向的平行度误 差会使活塞在汽缸中倾斜,从而造成汽缸
壁磨损不均匀,同时使曲轴的连杆轴颈产
生边缘磨损,所以两孔轴心线在连杆轴线
方向的平行度公差较小;而两孔轴心线在
垂直于连杆轴线方向的平行度误差对不均
匀磨损影响较小,因而其公差值较大。两
螺栓及螺母要提出高的技术要求外 ,对于安装这两个动力螺栓孔及端 面也提出了一定的要求。规定:螺 栓孔按IT8级公差等级和表面粗糙度 Ra应不大于6.3μm加工;两螺栓孔 在大头孔剖分面的对称度公差为 0.25 mm。
•有关结合面的技术要求 •在连杆受动载荷时,接合面的歪 斜使连杆盖及连杆体沿着剖分面产 生相对错位,影响到曲轴的连杆轴 颈和轴瓦结合不良,从而产生不均 匀磨损。结合面的平行度将影响到 连杆体、连杆盖和垫片贴合的紧密 程度,因而也影响到螺栓的受力情 况和曲轴、轴瓦的磨损。对于本连 杆,要求结合面的平面度的公差为 小头孔处0.004 mm,大头孔处 0.012mm。
连杆的机械加工工艺及夹具设计(含图纸)
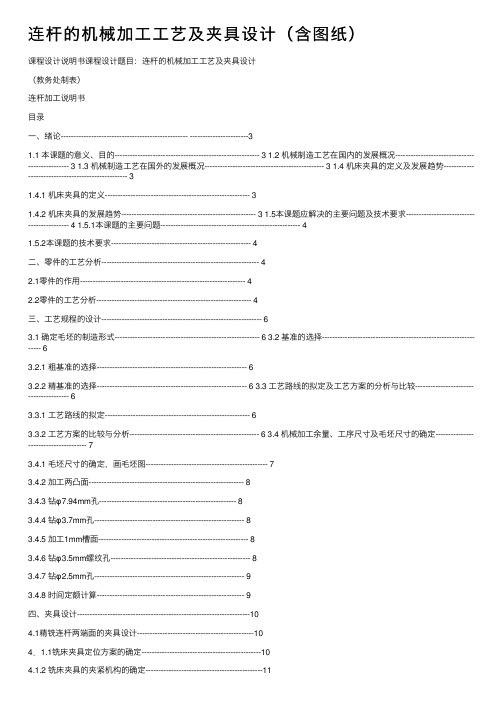
连杆的机械加⼯⼯艺及夹具设计(含图纸)课程设计说明书课程设计题⽬:连杆的机械加⼯⼯艺及夹具设计(教务处制表)连杆加⼯说明书⽬录⼀、绪论-------------------------------------------------- -----------------------31.1 本课题的意义、⽬的--------------------------------------------------------- 3 1.2 机械制造⼯艺在国内的发展概况----------------------------------------------- 3 1.3 机械制造⼯艺在国外的发展概况----------------------------------------------- 3 1.4 机床夹具的定义及发展趋势--------------------------------------------------- 31.4.1 机床夹具的定义--------------------------------------------------------- 31.4.2 机床夹具的发展趋势----------------------------------------------------- 3 1.5本课题应解决的主要问题及技术要求------------------------------------------- 4 1.5.1本课题的主要问题------------------------------------------------------- 41.5.2本课题的技术要求------------------------------------------------------- 4⼆、零件的⼯艺分析-------------------------------------------------------------- 42.1零件的作⽤----------------------------------------------------------------- 42.2零件的⼯艺分析------------------------------------------------------------- 4三、⼯艺规程的设计--------------------------------------------------------------- 63.1 确定⽑坯的制造形式--------------------------------------------------------- 6 3.2 基准的选择----------------------------------------------------------------- 63.2.1 粗基准的选择----------------------------------------------------------- 63.2.2 精基准的选择----------------------------------------------------------- 6 3.3 ⼯艺路线的拟定及⼯艺⽅案的分析与⽐较--------------------------------------- 63.3.1 ⼯艺路线的拟定--------------------------------------------------------- 63.3.2 ⼯艺⽅案的⽐较与分析--------------------------------------------------- 6 3.4 机械加⼯余量、⼯序尺⼨及⽑坯尺⼨的确定-------------------------------------- 73.4.1 ⽑坯尺⼨的确定,画⽑坯图------------------------------------------------ 73.4.2 加⼯两凸⾯------------------------------------------------------------- 83.4.3 钻φ7.94mm孔------------------------------------------------------ 83.4.4 钻φ3.7mm孔----------------------------------------------------------- 83.4.5 加⼯1mm槽⾯----------------------------------------------------------- 83.4.6 钻φ3.5mm螺纹孔------------------------------------------------------- 83.4.7 钻φ2.5mm孔----------------------------------------------------------- 93.4.8 时间定额计算---------------------------------------------------------- 9四、夹具设计--------------------------------------------------------------------104.1精铣连杆两端⾯的夹具设计----------------------------------------------104.1.1铣床夹具定位⽅案的确定-----------------------------------------------104.1.2 铣床夹具的夹紧机构的确定----------------------------------------------114.1.3铣床夹具对⼑装置的确定------------------------------------------------114.1.4 铣床夹具的结构分析----------------------------------------------------11五、总结----------------------------------------------------------------------- 13六、参考⽂献------------------------------------------------------------------- 14⼀、绪论1.1 本课题的意义、⽬的机械制造业是⼀个古⽼⽽永远充满⽣命⼒的⾏业。
- 1、下载文档前请自行甄别文档内容的完整性,平台不提供额外的编辑、内容补充、找答案等附加服务。
- 2、"仅部分预览"的文档,不可在线预览部分如存在完整性等问题,可反馈申请退款(可完整预览的文档不适用该条件!)。
- 3、如文档侵犯您的权益,请联系客服反馈,我们会尽快为您处理(人工客服工作时间:9:00-18:30)。
用量 f=2.86 mm/r。 量 f=2.86 mm/r。
用量 f=2.09 mm/r。 用量 f=2.09 mm/r。 f=2.09 mm/r。
1.6m 。
连杆 主 面 要 面 小头 端面 两端面尺寸 公差等级为 IT12 ,表面 粗 糙 度 Ra 不 大 于 粗铣其中一端面, 粗铣另一端面, 精 精度等级 IT12, 表 面粗糙度 Ra 不大 于 12.5 m ,切削 度等级 IT12, 表面 粗糙度 Ra 不大于 12.5 m ,切削用
半精铣另一端面, 精铣其中一端面, 精铣另一端面, 精 精度等级 IT8,表 面粗糙度 Ra 不大 于 1.6 m ,切削 度等级 IT8,表面 粗糙度 Ra 不大于 1.6 m , 切削用量
面, 精度等级 IT10, 精度等级 IT10, 表 表面粗糙度 Ra 不 大于 6.3 m ,切削 用量 f=2.09 mm/r。 面粗糙度 Ra 不大 于 6.3 m ,切削
精扩连杆大头端 孔,精度等级 IT11,表面粗糙度 Ra 不 大 于 6.3 m , 切削用量 f=0.8mm/r。
半精镗连杆大头端
精镗连杆大头端
孔, 精度等级 IT10, 孔, 精度等级 IT7, 表面粗糙度 Ra 不 大于 3.2 m ,切削 用量 f=0.2mm/r。 表面粗糙度 Ra 不 大于 0.8 m ,切 削 用 量
0.8m 。
(续) 连杆 主 要 面 盖接 合面 接合面的平 面度应小于 0.02mm, 表 面粗糙度 Ra 不 大 于 粗铣接合面, 精度 等级 IT12, 表面粗 糙 度 Ra 不大 于 12.5 m ,切削用 量 f=1.95mm/r。 粗 车 94m m 外 圆表面, 精度等级 半精铣接合面, 精 度等级 IT11, 表面 粗糙度 Ra 不大于 3.2 m , 切削用量 f=0.6mm/r。 精铣接合面,精度 等级 IT8, 表面粗糙 度 Ra 不 大 于 1.6 m ,切削用量 f=0.3mm/r。 精磨接合面, 精度 等级 IT6,表面粗 糙 度 Ra 不大 于 0.8 m , 切削用量 f=0.16mm/r。
0.8m 。
粗车
94
mm
满足尺寸要 求
94m m , IT12,表面粗糙度
表面粗糙度 Ra 不 大 于 Ra 不 大 于 12.5 m ,切削用 量 f=0.6mm/r。 粗 车
0.12 0.35
面
外圆 表面 次 要 面 粗车
12.5m 。
89.8 求 m m 89.80.12 0.35
mm , 表 面 粗 糙 度 Ra 不 大 于
0.8m 。
f=0.05mm/r。
(续) 螺栓 次 孔 要 孔 孔 满足尺寸要 求 12
0.019 0
粗钻螺栓孔, 精度 等级 IT13, 表面粗 糙 度 Ra 不大 于 12.5 m ,切削用 量 f=1.05mm/r。
粗扩螺栓孔, 精度 等级 IT12, 表面粗 糙 度 Ra 不大 于 6.3 m , 切削用量 f=0.5mm/r。
31
mm
IT12,表面粗糙度 Ra 不 大 于 12.5 m ,切削用
,表面粗糙 度 Ra 不大
于 3.2m 。 量 f=1.95mm/r。 连杆 小头 端孔 满足尺寸要 求 粗钻连杆小头端 孔,精度等级
0.027 0
孔,精度等级 IT9, 孔, 精度等级 IT7, 表面粗糙度 Ra 不 大于 3.2 m ,切削 用量 f=0.6mm/r。 表面粗糙度 Ra 不 大于 0.8 m ,切 削 用 量
37
IT12,表面粗糙度
mm , 表 面 粗 糙 度 Ra 主 孔 要 孔 连杆 大头 孔 不 大 于
Ra 不大于 25 m , Ra 切 削 用 量
f=1.05mm/r。
f=0.05mm/r。
0.8m 。
满足尺寸要 求 61
0.018 0
粗扩连杆大头端 孔,精度等级 IT12,表面粗糙度 Ra 不 大 于 12.5 m ,切削用 量 f=1.05mm/r。
精绞螺栓孔,精度 等级 IT6, 表面粗糙 度 Ra 不 大 于 3.2 m ,切削用量 f=0.05mm/r。
mm , 表 面 粗 糙 度 Ra 不 大 于
3.2m 。
满足尺寸要
89.8
mm 外
外圆 表面
圆表面, 精度等级 IT12,表面粗糙度 Ra 不 大 于 12.5 m ,切削用 量 f=0.6 mm/r。
mm , 表 面 粗 糙 度 Ra 不 大 于
12.5m 。
(续) 连杆 体斜 槽 满足尺寸要 求6
0.24 0.08
粗铣连杆体斜槽, 精度等级 IT12, 表
×
50m m , 面粗糙度 Ra 不大 表面粗糙度 于 12.5 m ,切削
Ra 不 大 于 用量 f=1.95mm/r。
12.5m 。
连杆 次 面 要 面 盖斜 槽 满足尺寸要 求 粗铣连杆盖斜槽, 精度等级 IT12, 表
பைடு நூலகம்
0.24 0.08
×
50m m , 面粗糙度 Ra 不大 表面粗糙度 于 12.5 m ,切削
,表面粗糙 度 Ra 不大
于 3.2m 。 量 f=1.95mm/r。
(续) 连杆 次 面 要 面 盖螺 栓平 台 满足尺寸要 求 粗铣连杆盖螺栓 平台,精度等级
0 0.28
半精铣连盖体螺 栓平台, 精度等级 IT11,表面粗糙度 Ra 不 大 于 3.2 m , 切削用量 f=0.6mm/r。 粗扩连杆小头端 孔,精度等级 IT12,表面粗糙度 不 大 于 12.5 m ,切削用 量 f=0.8mm/r。 粗拉连杆小头端 精镗连杆小头端
附件三:零
名 称
连杆 大头 端两 端面 加工精度要 求 工步 1 两端面尺寸 公差等级为 IT8, 表面粗 糙度 Ra 不 大 于
件
加
工
工
艺
设
计
表
加 工 工 艺 内 容 (注明每一工步的加工方法、精度等级、粗糙度、切削用量) 工步 2 工步 3 半精铣其中一端 工步 4 工步 5 工步 6
粗铣其中一端面, 粗铣另一端面, 精 精度等级 IT12, 表 面粗糙度 Ra 不大 于 12.5 m ,切削 度等级 IT12, 表面 粗糙度 Ra 不大于 12.5 m ,切削用
Ra 不 大 于 用量 f=1.95mm/r。
12.5m 。
连杆 体螺 栓平 台 满足尺寸要 求 粗铣连杆体螺栓 平台,精度等级
0 0.28
半精铣连杆体螺 栓平台, 精度等级 IT11,表面粗糙度 Ra 不 大 于 3.2 m , 切削用量 f=0.6mm/r。
31
mm
IT12,表面粗糙度 Ra 不 大 于 12.5 m ,切削用
用量 f=1.95mm/r。 量 f=1.95mm/r。
12.5m 。
连杆 体接 合面 接合面的平 面度应小于 0.02mm, 表 面粗糙度 Ra 不 大 于 粗铣接合面, 精度 等级 IT12, 表面粗 糙 度 Ra 不大 于 12.5 m ,切削用 量 f=1.95mm/r。 半精铣接合面, 精 度等级 IT11, 表面 粗糙度 Ra 不大于 3.2 m , 切削用量 f=0.6mm/r。 精铣接合面,精度 等级 IT8, 表面粗糙 度 Ra 不 大 于 1.6 m ,切削用量 f=0.3mm/r。 精磨接合面, 精度 等级 IT6,表面粗 糙 度 Ra 不大 于 0.8 m , 切削用量 f=0.16mm/r。