合成铸铁的生产及应用
利用废钢生产合成铸铁的增碳工艺及控制

1 . 4 增 碳剂 加入 工艺方 法 的设计 为 了研 究加入 工 艺对增 碳剂 的吸 收效 果 的影
响 ,试验 设计 了以下 3 种 增碳 剂加入 方法 :
1 )中问加入法 ( 方 法①) , 即废 钢加入 熔化 后 ,
加入 增碳 剂 ,迅速 覆盖 回炉料 ;
增碳 剂 的质量 好坏 直接 影 响到铁 液 的质量 好
1 . 3 . 1 增碳 剂类型 的选 用
作者 简介 :陈 忠士f 1 9 6 6 铁 的熔炼 与铸 造 。
第 2期
陈 忠 士 :利 用 废 钢 生 产 合 成 铸 铁 的增 碳 工 艺及 控 制
1 0 1
2 试验结 果与分析
坏 ,因此在 生产 时 ,对 于增碳 剂 的选 择显 得至 关
重要。
2 )压 底加入 法( 方法② ) , 即增 碳剂 置于 炉底 ,
再加 入废 钢 ,熔化 后再 加入 回炉料 ;
3 )分 层加 入法 ( 方 法③ ) ,即废 钢熔 化 后分批
加 入增 碳剂 ,并迅 速覆 盖 回炉料 。
1 试验条件与要求
1 . 1 熔炼炉
采用 容量 为 1 5 0 k g和 5 0 0 k g中频感 应 电炉 ,
用 于生产 性试 验 。
1 . 2 废钢 与 回炉铁 1 1废钢 :选 用低 S 、低 P 、低 Mn的碳 钢 , 其 它合金 及杂 物不 得混入 其 中 。 2 )回炉料 :使用材 质相 近 的 同类 回炉 料 ,不 得将 不 同牌 号、 不 同种 类 的回炉铁 混在 一起 加入 。 1 . 3 增碳 剂的 选用
1 0 0
机 电技术
2 0 1 3 年4 月
利用废钢生产合成铸铁 的增碳工艺及控制
铸铁表面原位合成TiC/A3Ti复合材料
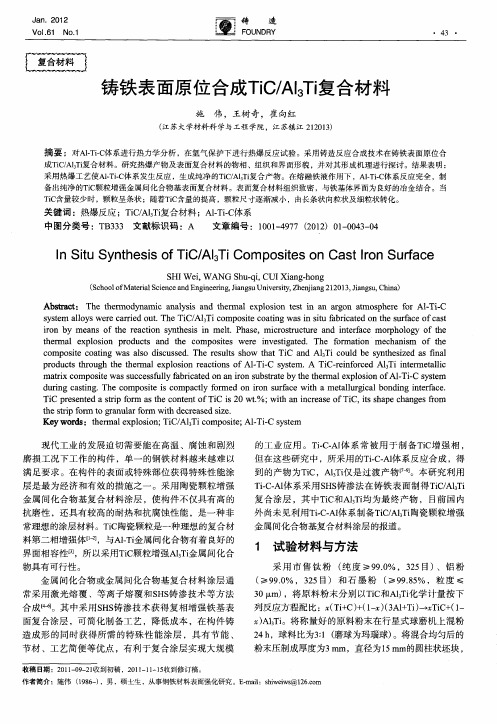
铸铁表面原 位合成TC Aai i/ l 复合材料 T
施 伟 ,王树奇,崔向红
( 江苏大学材料科 学与工程 学院,江苏镇 江 2 2 1) 10 3
摘要 :对A.i 体系进行热力学分析 , 1 . TC 在氩气保护下进行热爆反应试验。采用铸造反应合成技术在铸铁表面原位合
作者简介 :施伟 ( 8 一 ,男 ,硕士生 , 事钢铁 材料表 面强化研究 。E m i h e s 2 . r 1 6) 9 从 — a :si i @16 o l w w cn
Jn 2 2 a . O1
F OUNDRY
V0 . 1 N0 1 1 6 .
致密 度为4 %~ 0 0 6 %,在 10。 2 C下真 空干燥 6h 自然冷 并 却到室温 。采用P A. V 水泥砂造 型 ,并用 5 %的P 水溶 VA
Ab ta t T e tem o y a c a ay i n h r a x l s n ts n a ro t s h r o — iC src : h h r d n mi n lss a d tem le po i eti n ag n amo p ee f rAl . o T
收稿 日 : 0 1 0 — 1 期 2 1 - 9 2 收到初稿 ,2 1- 1 1收到修订稿。 0 1 1- 5
xA i ) 1 。将称 量好 的原 料粉 末在 行星式 球磨 机上 混粉 T 2 ,球料 比为31 ( 为玛瑙球 ) 4h : 径 为 1 5 mm的圆柱状坯 块 ,
-
-
5 0 60 7 0
-
-
8 0
液将 干燥 后 的预制 块粘 固在铸 型表 面 ( 图1 , 自然 见 )
铸铁知识介绍

铸造知识介绍铸造:是一种金属材料的成形方法。
将熔融金属浇注、压射或吸入铸型型腔,凝固后成为具有一定形状和性能的铸件。
铸造方法有砂型铸造和特种铸造,既可用手工单件小批量生产,也可用机械化、自动化生造型方法大量成批生产。
铸造流程:制模——造型——烘干——熔炼——孕育处理——炉前分析——浇注——落砂清理——去浇冒口——铸件检验及缺陷分析——铸铁及熔炼白口铸铁:白口铸铁中的碳全部以渗透碳体(Fe 3c )形式存在,因断口呈亮白色。
故称白口铸铁,由于有大量硬而脆的Fe 3c ,白口铸铁硬度高、脆性大、很难加工。
因此,在工业应用方面很少直接使用,只用于少数要求耐磨而不受冲击的制件,如拔丝模、球磨机铁球等。
大多用作炼钢和可锻铸铁的坯料。
灰口铸铁;铸铁中的碳大部或全部以自由状态片状石墨存在。
断口呈灰色。
它具有良好铸造性能、切削加工性好,减磨性,耐磨性好、加上它熔化配料简单,成本低、广泛用于制造结构复杂铸件和耐磨件。
灰口铸铁按基体组织不同,分为铁素体基灰口铸铁、珠光体+铁素体基灰口铸铁和珠光体基灰口铸铁三类。
由于灰口铸铁内存在片状石墨,而石墨是一种密度小,强度低、硬度低、塑性和韧性趋于零的组分。
它的存在如同在钢的基体上存在大量小缺口,即减少承载面积,又增加裂纹源,所以灰口铸铁强度低、韧性差,不能进行压力加工。
为改善其性能,在浇注前在铁水中加入一定量的硅铁,硅钙等孕育剂,使珠光体基体细化,石墨变细小而均匀分布,经过这种孕育处理的铸铁。
称为孕育铸铁。
灰口铸铁的牌号、性能组织及用途见下表,国家标准根据直径30mm 单铸试棒的抗拉强度,将灰铸铁分为六个牌号。
牌号中的“HT ”是“灰铁”的汉语拼音的第一个大写字母,其后面的数字表示该牌号灰铸铁的最小抗拉强度。
灰铸铁的牌号及力学性能指标(GB5675-85)铸铁的化学成份对灰铸铁的组织有很大影响,各种牌号的灰铸铁的化学成份与铸件壁厚有关,下表数据供参考。
碳和硅是灰铸铁中最主要的化学成份,它们都是强烈促进石墨化的元素,对铸铁的组织和性能起着决定性影响。
铸铁熔炼使用碳化硅的几点体会
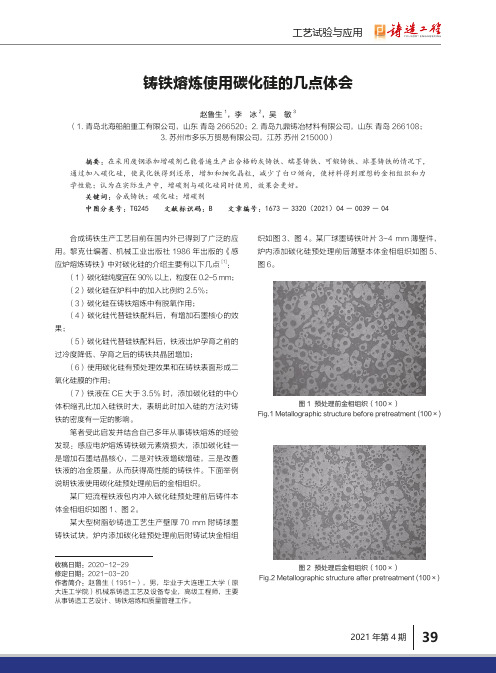
40 2021 年第 4 期
工艺试验与应用
未熔融分解的碳化硅颗粒铸件 SEM 表面形貌和 EDS 分析结果如图 9。
图 7 碳化硅块 Fig.7 Silicon carbide block
1.3 铸造用高纯度碳化硅
近期国内研究表明,铸铁熔炼若使用碳化硅的纯度要 达95% 以上,能起到细化铸铁组织、改善铁液的冶金质 量,大幅度提高材料的力学性能等作用。但是使用成本相 对较高,使高纯度碳化硅在一般铸铁件应用中受到限制。
2 铸造用碳化硅的使用粒度要求
2.1 碳化硅随废钢熔炼前期添加
在 铸 铁 炉 料 中, 因 为 碳 化 硅 熔 融 形 成 二 氧 化 硅 膜 及其阻碍作业和需要较高的溶解温度。为了加速融化吸 收,随废钢前期加入的碳化硅粒度1~5 mm,从而减少 铁液氧化,增加石墨核心,持续改善铁液冶金质量,此 时碳化硅的吸收率一般高于90%。
图 6 预处理后金相组织(100×) Fig.6 Metallographic structure after pretreatment (100×)
1.2 冶金用碳化硅纯度要求
除了感应电炉熔炼铸铁使用纯度在 90% 左右碳化 硅之外,国内大量生产出口供应炼钢脱氧或者供应冲天 炉使用的冶金碳化硅块,纯度在 50%~60%。该碳化硅 块依据客户对硅、碳及碳化硅纯度要求,加水泥或其他 粘结剂搅拌均匀压制成形,固化干燥,保证冲天炉加料 冲击不碎,如图 7。这种碳化硅块冲天炉中熔炼中正常 使用,可以减少铁液氧化,提供铁液碳硅含量,适当提 高冲天炉铁液温度,对冲天炉熔炼净化铁液、提高冶金 质量有好处,熔后炉渣显色偏淡。
织如图 3、图 4。某厂球墨铸铁叶片 3~4 mm 薄壁件, 炉内添加碳化硅预处理前后薄壁本体金相组织如图 5、 图 6。
硅强化铁素体球墨铸铁的研究与应用
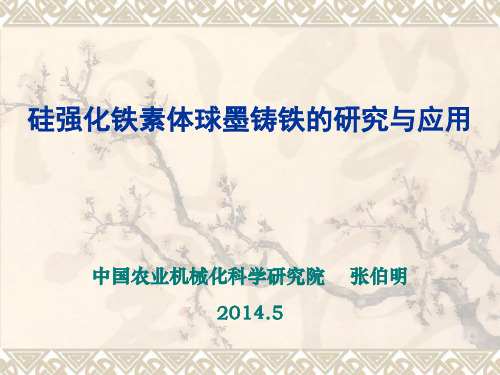
和断裂韧性来取代; 3.扩大应用的试验。
同上 同上
基体 F(P<5%
P+F P
HBW 135-180
170-230 130-270
背 景2
国外的铸铁都采取合成铸铁的技术来生产,即金属料都用 废钢及回炉料组成;
为减轻产品重量,世界各国都在提高材料性能上下功夫。 钢材在提高强度时,使用了不少合金元素。 Mn量可高达0.8% 以上,同事还有比Mn作用更强的珠光体稳定元素Cu、Cr、V存 在,从而给获得高伸长率的球墨铸铁牌号增加了困难;
203,203 203,203 203,203
保定华龙
长期以来都用高硅来生产500-7的 球墨铸铁:在Mn量0.36%~0.4%时,用 Si3.06%~3.20%,抗拉强度在509~ 540MPa,伸长率都在12%~14%。
山东一家铸造企业
今后的研究方向
1.各种元素组合对力学性能的影响; 2.讨论和研究冲击性能指标对零件设计有多大
EN-GJS-600-10 5.3110
~4.3
≤0.05
≤0.50
注意:1.由于其他合金元素的存在,Si量可适当降低; 2.Mn量降低时,例如在0.30,机加工性能和伸长率会更好。
生产中要注意的问题
1. 要优化孕育技术:硅量提高后,在铸件的厚壁部分容 易出蠕虫状石墨,在其总量不大于20%时,不影响力学性能。在 壁厚大于20mm时,要选用合适的孕育剂来保证全部是球状和 团球状石墨;
德国400-18牌号球墨铸铁的典型成分(质量分数,%)
元素
C
Si
Mn
P
S
Mg
含量 3.5~3.6 2.4~2.5 0.15~0.2 ~0.02 <0.009 ~0.04
合成铸铁技术在发动机缸体上的应用
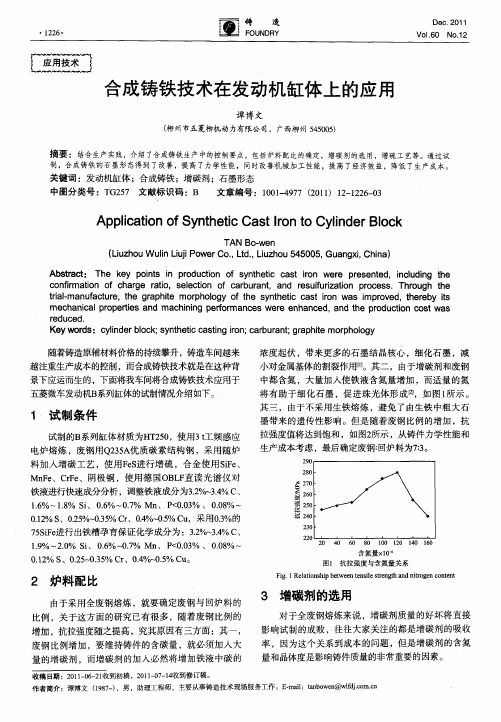
til n f cu e h r p i r h lg ft e s n h t a t r n wa mpo e ,t e e y i r — a ma u a t r ,te g a ht mo p oo y o h y te i c s i s i r v d h r b t e c o s
生产 成本考虑 ,最后 确定废钢: 回炉料为73 :。
Mne re F 、CF 、阴极铜 ,使用德国O L 直读光谱仪对 BF
铁液进行 陕速成分分析 ,调整铁液成分为 3 % 3 % C . ~. 2 4 、
16 ~18 S 、 0 6 ~0 7 M n P 0 0 % 、 0 0 % ~ .% .% i .% .% 、 < .3 .8
五菱微 车发 动机B 系列缸体的试制情 况介绍如下 。
浓度 起伏 ,带来 更 多的石 墨结 晶核 心 ,细化 石 墨 ,减
小对金属基体的割裂作用【 ” 。其二 ,由于增碳剂和废钢 中都含氮 , 大量加入使铁液含氮量增加 ,而适量 的氮 将有助于细化石墨 ,促进珠光体形成[ 2 1 图1 ,如 所示 。
制 ,合成铸铁的石墨形态得到 了改善 ,提高 了力学性能 ,同时改善机械加工性能,提高 了经济效 益,降低 了生产成本 。
关键 词 :发 动机缸体 ;合成 铸铁 ;增碳剂 ;石墨形态 中图分 类号 :T 27 文 献标识 码 :B G5 文章 编号 :10—97 (0 1—260 0 147 2 1) 2 12— 3 1
推广合成铸铁应用的若干工艺技术问题
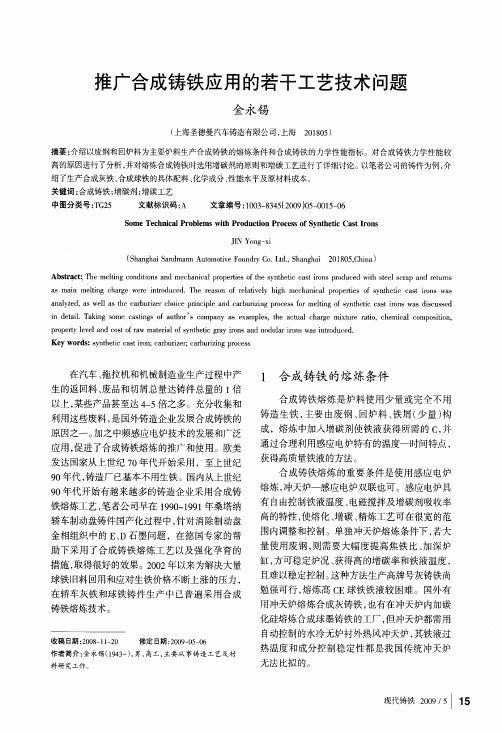
推广合成铸铁应用的若干工艺技术问题金永锡(上海圣德曼汽车铸造有限公司,上海201805)摘要:介绍以废钢和回炉料为主要炉料生产合成铸铁的熔炼条件和合成铸铁的力学性能指标。
对合成铸铁力学性能较高的原因进行了分析,并对熔炼合成铸铁时选用增碳剂的原则和增碳工艺进行了详细讨论。
以笔者公司的铸件为例,介绍了生产合成灰铁、合成球铁的具体配料、化学成分、性能水平及原材料成本。
关键词:合成铸铁;增碳剂;增碳工艺中_图分类号:T G25文献标识码:A文章编号:1003—8345(2009)05—0015一06S o m e Tec hn i ca l Pr obl em s w i t h Produ c t i o n Proc es s of Sy nm et i c C a s t I r onsJI N Y ong—xi(Sha ngha i Sandm ann A ut om ot i ve Fo und l y C o.L t d.,Shang hai201805,Chi na)A bs t r ac t:The m el t i ng condi t i ons a nd m e chani ca l pr oper t i es of t he s ynt het i c c as t i r ons pr oduced w i t h s teel s cm p a nd r et um s as m ai n m el t i ng ch ar g e w er e i n t r odu ced.T he r eas on of r elat i vel y hi g h m e c hani cal pr oper t i es of s ynt het i c c as t i r ons w a s anal yz ed,as w el l as t hecar bu r i zer choi ce pr i nci pl e a nd car bur i zi ng pr o cess f br m el t i ng of s ynt het i c c a st i r ons w as di scus sed i n det a i l.T ak i ng s o m e cas t i ngs of aut hor’s com pany as ex am p l e s,t he act ual ch ar g e m i xt ur e r at i o,eh em i cal com pos i t i on,pr op er t y l evel and c o s t of r a w m at er i al of s ynt het i c gr ay i r ons a nd no du l ar i r ons w as i nt roduced.K e y w o r ds:syn t het i c c as t i m n;car bu“zer;car bu r i zi ng pm c e ss在汽车、拖拉机和机械制造业生产过程中产生的返回料、废品和切屑总量达铸件总量的l倍以上,某些产品甚至达4~5倍之多。
合成铸铁生产缸体铸件的工艺技术
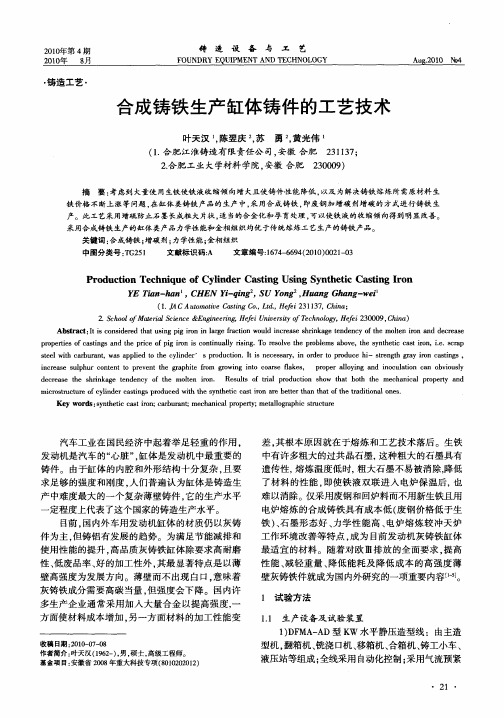
p o e t s o a t g n h r e o i rn i o t u l sn . o r s le t e p o l ms a o e t e s n h t a t r n ..s r p rp r e fc s n s a d t e p c fp g i sc n i al r i g T e ov h r b e b v , h y t e i e s o ,i i i i o n yi c i e ca se l t ab r n ,wa p l d t h yi d r S p o u t n ti n c sa y n o d rt r d c i sr n t r y i n c si g te h e r u a t wi s a p i o t e c l e r d ci .I s e e s r ,i r e o p u e h - t g h g a r a t s, e n o o e o n i c e s up u o t n o p e e tt e g a h t r m o n n o c a s a e , n r a e s l h r c n e t t r v n h r p i fo g wi g i t o r e f k s e r l p o e l yn n n c l t n c n o v o sy r p r al i g a d i o u ai a b iu l o o
提高电炉铸铁的绝密方法
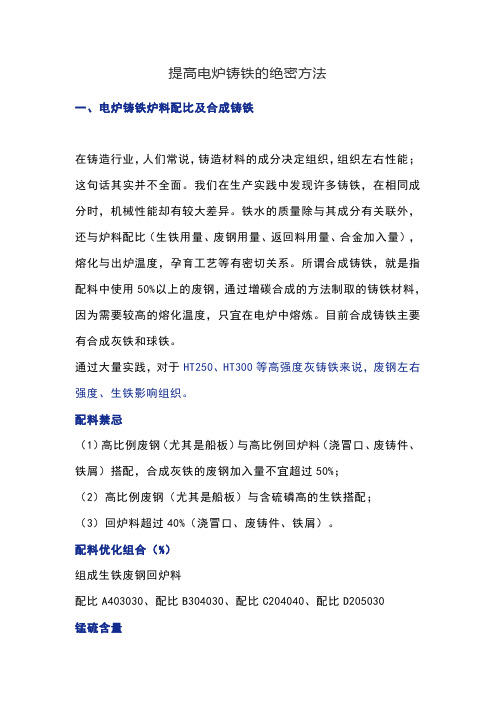
提高电炉铸铁的绝密方法一、电炉铸铁炉料配比及合成铸铁在铸造行业,人们常说,铸造材料的成分决定组织,组织左右性能;这句话其实并不全面。
我们在生产实践中发现许多铸铁,在相同成分时,机械性能却有较大差异。
铁水的质量除与其成分有关联外,还与炉料配比(生铁用量、废钢用量、返回料用量、合金加入量),熔化与出炉温度,孕育工艺等有密切关系。
所谓合成铸铁,就是指配料中使用50%以上的废钢,通过增碳合成的方法制取的铸铁材料,因为需要较高的熔化温度,只宜在电炉中熔炼。
目前合成铸铁主要有合成灰铁和球铁。
通过大量实践,对于HT250、HT300等高强度灰铸铁来说,废钢左右强度、生铁影响组织。
配料禁忌(1)高比例废钢(尤其是船板)与高比例回炉料(浇冒口、废铸件、铁屑)搭配,合成灰铁的废钢加入量不宜超过50%;(2)高比例废钢(尤其是船板)与含硫磷高的生铁搭配;(3)回炉料超过40%(浇冒口、废铸件、铁屑)。
配料优化组合(%)组成生铁废钢回炉料配比A403030、配比B304030、配比C204040、配比D205030锰硫含量需要提高硬度时锰的含量可达 1.0-1.2%,但不要求相应提高硫的含量(关于灰铁中的硫含量,另行分析)。
某公司为了节约成本,多用废钢,在两个月内试制合成高牌号灰铸铁,废钢用量一度达60%,有一段时间除加入废钢外另加回炉料和少量铁屑,最初质量不错,但一段时间后发现铸件批量缩孔、缩松和有白色硬斑,并且持续不断越来越严重。
此缺陷成因:初步判断是铁水中MnS的含量过高而引起的铸件显微缩孔、缩松,MnS富集形成白色硬斑。
这是由于高牌号灰铁HT300成分要求Mn含量较高(1%左右),加之废钢自身锰也高(船板中的16锰钢含Mn在1.6%),而废钢中的S以及回炉铁(包括铁屑)中的S 和锰反应产生的MnS在炉料中的积累达到一定程度,就会产生过量,从而产生上述缺陷。
为了减少铁水中的MnS含量,一般用加入一定量的优质新生铁(低S低Mn)来调整,另外提高孕育效果,可使MnS细化,减弱其不良影响。
有关合成铸铁的一些问题

有关合成铸铁的一些问题1、什么叫合成铸铁?传统的铸铁熔炼,其炉料组成是以新生铁为主,配加回炉料和少比例的废钢,加废钢的目的是为了降低铁液中的含碳量。
一直以来,熔炼球铁大多数只加5%-10%废钢,保持着在不产生石墨漂浮的情况下,遵循高碳低硅大孕育的原则,认为碳当量高,尤其是碳高有利于铸铁的自补缩,不容易产生缩孔缩松缺陷,因此尽量少加废钢是很自然的事,而在灰铸铁的熔炼中,因知道降低碳含量,能减少割裂铸铁金属基体中的石墨量,而有效的增加强度,碳越低,强度就越高,所以依灰铸铁的牌号不同,配加一定比例的废钢,以达到各牌号所需的含碳量,相当长一个时期,我们生产的铸铁牌号不高,很多小型企业还不要求牌号,大多生产的牌号只为HT150,HT200和HT250,,因此所加废钢比例就低,大多在15-35%范围内,认为多加废钢,铸件缩性大,因此不敢多用。
现在知道,炉料的组成是对铸铁件的质量有很大影响的,在铸铁的熔炼中,我国长期的采用低比例的废钢配比,是否是我国在同样CE下强度不如国外高,而强度相当时,CE又比人家的低,因而铸造性能恶化,是值得我们探讨的。
近些年来,我国铸造界热门的话题有两个,一个是风电,高铁等所用的高韧性低温铁素体球铁,提高性能措施之一就是要用高纯生铁,第二个就是合成铸铁,提倡多用废钢和加增碳技术来提高铸铁性能,这两项技术都牵涉到炉料的合理应用,认识到了精料出精品的内在含义。
应当说是我们在铸铁件的生产中的一种进步。
到底为什么叫合成铸铁,在铸铁件的生产中,炉料以废钢为主,不加生铁或少用生铁,然后就是加入本厂的回炉料,并用增碳技术达到所需的含碳量,这就叫合成铸铁吗?这种新的配料所获得的铸铁,虽然与老工艺相比在炉料单目上大体相同,只是各组分加入比例不同而已,但在铸铁的性能上有了很大的提高,因此对这种工艺所获得的铸铁,取一个新的名词,叫合成铸铁,表示与原传统工艺的区别。
看到美国铸造协会1974年年刊上一篇有关铸铁生产所用增碳剂的文章内,提到自然界本没有铁元素,它是由铁矿石经高炉用焦炭还原而获得,它把这种铁称之为合成铁,或人造铁(Synthetic iron)因而用这种铁生产的铸铁件叫做合成铸铁也算说得有理。
高强度高碳当量灰铸铁生产工艺问题2—合理地使用增碳剂
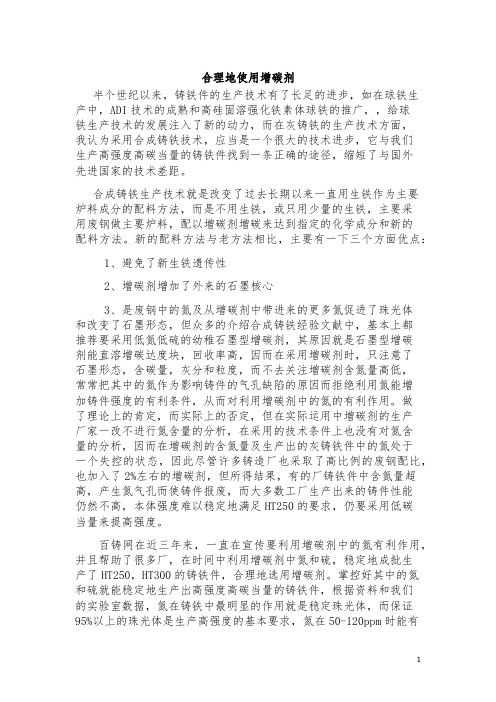
合理地使用增碳剂半个世纪以来,铸铁件的生产技术有了长足的进步,如在球铁生产中,ADI技术的成熟和高硅固溶强化铁素体球铁的推广,,给球铁生产技术的发展注入了新的动力,而在灰铸铁的生产技术方面,我认为采用合成铸铁技术,应当是一个很大的技术进步,它与我们生产高强度高碳当量的铸铁件找到一条正确的途径,缩短了与国外先进国家的技术差距。
合成铸铁生产技术就是改变了过去长期以来一直用生铁作为主要炉料成分的配料方法,而是不用生铁,或只用少量的生铁,主要采用废钢做主要炉料,配以增碳剂增碳来达到指定的化学成分和新的配料方法。
新的配料方法与老方法相比,主要有一下三个方面优点:1、避免了新生铁遗传性2、增碳剂增加了外来的石墨核心3、是废钢中的氮及从增碳剂中带进来的更多氮促进了珠光体和改变了石墨形态,但众多的介绍合成铸铁经验文献中,基本上都推荐要采用低氮低硫的幼稚石墨型增碳剂,其原因就是石墨型增碳剂能直溶增碳达度块,回收率高,因而在采用增碳剂时,只注意了石墨形态,含碳量,灰分和粒度,而不去关注增碳剂含氮量高低,常常把其中的氮作为影响铸件的气孔缺陷的原因而拒绝利用氮能增加铸件强度的有利条件,从而对利用增碳剂中的氮的有利作用。
做了理论上的肯定,而实际上的否定,但在实际运用中增碳剂的生产厂家一改不进行氮含量的分析,在采用的技术条件上也没有对氮含量的分析,因而在增碳剂的含氮量及生产出的灰铸铁件中的氮处于一个失控的状态,因此尽管许多铸造厂也采取了高比例的废钢配比,也加入了2%左右的增碳剂,但所得结果,有的厂铸铁件中含氮量超高,产生氮气孔而使铸件报废,而大多数工厂生产出来的铸件性能仍然不高,本体强度难以稳定地满足HT250的要求,仍要采用低碳当量来提高强度。
百铸网在近三年来,一直在宣传要利用增碳剂中的氮有利作用,并且帮助了很多厂,在时间中利用增碳剂中氮和硫,稳定地成批生产了HT250,HT300的铸铁件,合理地选用增碳剂。
掌控好其中的氮和硫就能稳定地生产出高强度高碳当量的铸铁件,根据资料和我们的实验室数据,氮在铸铁中最明显的作用就是稳定珠光体,而保证95%以上的珠光体是生产高强度的基本要求,氮在50-120ppm时能有效地抑制铁素体的生成,而当含量过高时有产生氮气孔的危险,我们控制厚大件的氮含量不超过80ppm,中小件不超过120ppm作为控制界限。
HT350高牌号合成铸铁的工艺实践
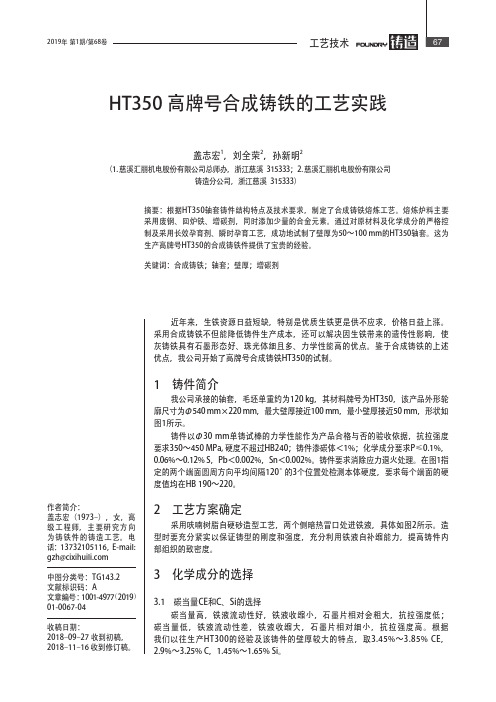
HT350高牌号合成铸铁的工艺实践盖志宏1,刘全荣2,孙新明2(1. 慈溪汇丽机电股份有限公司总师办,浙江慈溪 315333;2. 慈溪汇丽机电股份有限公司铸造分公司,浙江慈溪 315333)摘要:根据HT350轴套铸件结构特点及技术要求,制定了合成铸铁熔炼工艺。
熔炼炉料主要采用废钢、回炉铁、增碳剂,同时添加少量的合金元素。
通过对原材料及化学成分的严格控制及采用长效孕育剂、瞬时孕育工艺,成功地试制了壁厚为50~100 mm的HT350轴套。
这为生产高牌号HT350的合成铸铁件提供了宝贵的经验。
关键词:合成铸铁;轴套;壁厚;增碳剂作者简介:盖志宏(1973-),女,高级工程师,主要研究方向为铸铁件的铸造工艺。
电话:137********,E-mail: gzh@中图分类号:TG143.2文献标识码:A文章编号 :1001-4977 (2019)01-0067-04收稿日期:2018-09-27收到初稿,2018-11-16收到修订稿。
近年来,生铁资源日益短缺,特别是优质生铁更是供不应求,价格日益上涨。
采用合成铸铁不但能降低铸件生产成本,还可以解决因生铁带来的遗传性影响,使灰铸铁具有石墨形态好、珠光体细且多、力学性能高的优点。
鉴于合成铸铁的上述优点,我公司开始了高牌号合成铸铁HT350的试制。
1 铸件简介我公司承接的轴套,毛坯单重约为120 kg,其材料牌号为HT350,该产品外形轮廓尺寸为Φ540 mm×220 mm,最大壁厚接近100 mm,最小壁厚接近50 mm,形状如图1所示。
铸件以Φ30 mm单铸试棒的力学性能作为产品合格与否的验收依据,抗拉强度要求350~450 MPa, 硬度不超过HB240;铸件渗碳体<1%;化学成分要求P≤0.1%,0.06%~0.12% S,Pb<0.002%,Sn<0.002%。
铸件要求消除应力退火处理。
在图1指定的两个端面圆周方向平均间隔120°的3个位置处检测本体硬度,要求每个端面的硬度值均在HB 190~220。
合成铸铁的研究及应用
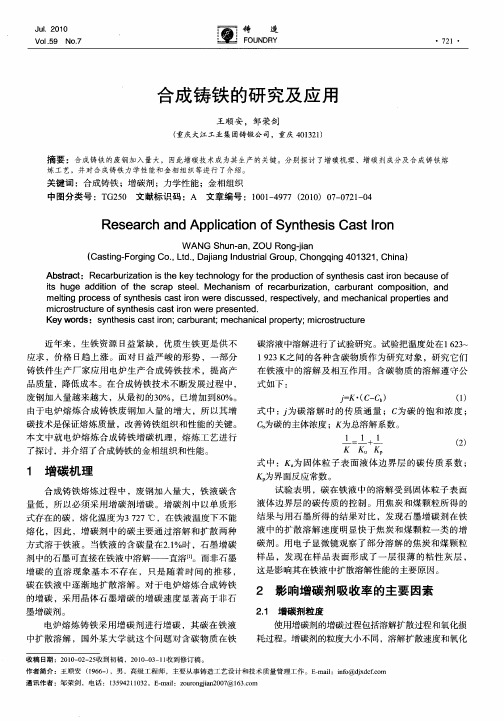
近 年来 ,生铁 资源 1益 紧缺 ,优 质生 铁更 是供 不 3 应求 ,价格 日趋 上涨 。面对 日益严 峻 的形势 ,一 部分 铸 铁件 生产 厂 家应用 电炉 生产 合成 铸铁 技术 ,提 高产 品质量 ,降低成 本 。在合 成铸铁 技术不 断发展过 程 中 , 废 钢加入 量越来 越 大 ,从 最初 的3 % ,已增 加到 8 %。 0 0 由于 电炉熔 炼合成 铸铁 废钢 加 入量 的增 大 ,所 以其 增
Re e c n pia in o n h ss Ca tI s ar ha d Ap l t fSy t e i s r c o on
WAN u - n Z o gj n G Sh na , OU R n -a i ( a t gF rigCo, t.D j n d sr l o p C o g ig4 12 , hn ) C si —ogn .Ld, ai gI uta Gru , h n qn 0 3 1 C ia n a n i
碳技术 是保证熔炼 质量 ,改善铸铁 组织和 性能 的关 键 。
碳溶液 中溶解进 行 了试验研究 。试验把 温度处在 1 2 ~ 3 6
1 2 间 的各 种含 碳物质 作 为研究对 象 ,研 究它 们 3 9 K之
在铁 液 中的 溶解及 相互 作用 。含 碳物 质 的溶解 遵守 公
Ab ta t Re a b r a ini h e c n lg r h r d c ino y t e i a ti n b c u e o sr c : c r u i t st e k yt h oo yf e p o u t f nh ss c s o e a s f z o e o t o s r i u e a dt ft e s r p se 1 t h g d ion o h ca t e .Me h ns s i c a im o e a b r a in a b r n o p st n f r c r u i t ,c r u a t c m o io ,a d z o i n m et g p o e so y t e i a ti n we e ds u s d r s e t ey a d m e h nc l r e t sa d ln r c s fs n h ssc s o r ic s e , e p ci l, n c a ia op re n i r v p i
合成球墨铸铁金相组织缺陷产生原因及解决办法

2021年 第2期 热加工98铸造C a s t i n g合成球墨铸铁金相组织缺陷产生原因及解决办法曹琨1,2,胡克潮2,赵子文1,2,苏义祥31.兰州兰石能源装备工程研究院有限公司 甘肃兰州 7303142.甘肃省高端铸锻件工程技术研究中心 甘肃兰州 7303143.兰州理工大学材料科学与工程学院 甘肃兰州 730050摘要:采用光学显微镜、扫描电镜分析了合成球墨铸铁生产过程中常见金相组织缺陷,包括石墨漂浮、球化不良、球化失败、碳化物超标、缩松和缩孔等问题,并提出工艺控制要点及解决措施,为生产同类铸件提供了可借鉴经验。
关键词:合成铸铁;金相组织;球墨铸铁;工艺控制1 序言球墨铸铁件具备中高强度和韧性、优异的耐磨性和减振性以及良好的铸造工艺性能等特点,是目前最具发展潜力的“以铁代钢”的铸造材料[1,2]。
目前,许多铸造企业开始采用废钢增碳技术(即合成铸铁)替代铸造生铁生产球墨铸铁件的方法来降低成本。
用该方法熔炼的球墨铸铁力学性能十分优异,铸态下力学性能可达到QT700-2级别材料要求,无需进行正火处理(只进行去应力退火),能够减少一火次能源消耗,符合国家倡导的绿色可持续发展理念[3]。
与传统生铁熔炼方式不同,合成球墨铸铁熔炼过程中原铁液化学成分发生改变,生产过程中如果控制不当容易出现较多铸造缺陷。
目前,应用合成球墨铸铁技术的报道较多[4-12],但是对于合成球墨铸铁在生产过程中的自身特性、容易出现的质量问题及关键控制要点的报道甚少。
本研究主要从金相组织角度出发,针对生产过程中常见的金相组织缺陷进行分析并提出解决方案。
2 石墨漂浮合成球墨铸铁的核心是将废钢中的碳含量(w C 为0.2%左右)增至工艺要求范围(w C 为3.6%~3.9%),如果碳含量超标(w C ≥4.0%),则会出现石墨漂浮现象,如图1所示。
从图中可以看出石墨呈开花状、爆裂状,这种组织降低了球墨铸铁力学性能和表面质量。
腐蚀态金相照片显示,石墨周围铁素体组织呈破碎状,使珠光体含量达到95%,抗拉强度453~532M P a ,屈服强度431~477M P a ,伸长率1.5%~3%,硬度208~214HBW ,表明开花、爆裂状石墨对基体组织产生明显割裂作用,降低了产品力学性能。
铸铁的发展现状况与应用前景简介
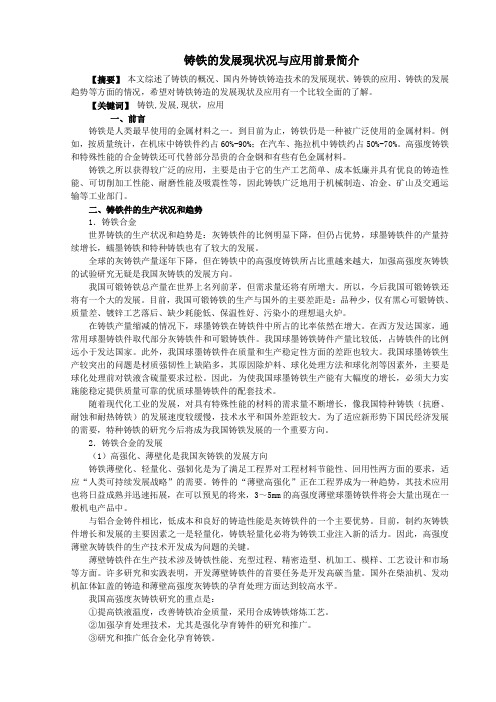
铸铁的发展现状况与应用前景简介【摘要】本文综述了铸铁的概况、国内外铸铁铸造技术的发展现状、铸铁的应用、铸铁的发展趋势等方面的情况,希望对铸铁铸造的发展现状及应用有一个比较全面的了解。
【关键词】铸铁,发展,现状,应用一、前言铸铁是人类最早使用的金属材料之一。
到目前为止,铸铁仍是一种被广泛使用的金属材料。
例如,按质量统计,在机床中铸铁件约占60%-90%;在汽车、拖拉机中铸铁约占50%-70%。
高强度铸铁和特殊性能的合金铸铁还可代替部分昂贵的合金钢和有些有色金属材料。
铸铁之所以获得较广泛的应用,主要是由于它的生产工艺简单、成本低廉并具有优良的铸造性能、可切削加工性能、耐磨性能及吸震性等,因此铸铁广泛地用于机械制造、冶金、矿山及交通运输等工业部门。
二、铸铁件的生产状况和趋势1.铸铁合金世界铸铁的生产状况和趋势是:灰铸铁件的比例明显下降,但仍占优势,球墨铸铁件的产量持续增长,蠕墨铸铁和特种铸铁也有了较大的发展。
全球的灰铸铁产量逐年下降,但在铸铁中的高强度铸铁所占比重越来越大,加强高强度灰铸铁的试验研究无疑是我国灰铸铁的发展方向。
我国可锻铸铁总产量在世界上名列前茅,但需求量还将有所增大。
所以,今后我国可锻铸铁还将有一个大的发展。
目前,我国可锻铸铁的生产与国外的主要差距是:品种少,仅有黑心可锻铸铁、质量差、镀锌工艺落后、缺少耗能低、保温性好、污染小的理想退火炉。
在铸铁产量缩减的情况下,球墨铸铁在铸铁件中所占的比率依然在增大。
在西方发达国家,通常用球墨铸铁件取代部分灰铸铁件和可锻铸铁件。
我国球墨铸铁铸件产量比较低,占铸铁件的比例远小于发达国家。
此外,我国球墨铸铁件在质量和生产稳定性方面的差距也较大。
我国球墨铸铁生产较突出的问题是材质强韧性上缺陷多,其原因除炉料、球化处理方法和球化剂等因素外,主要是球化处理前对铁液含硫量要求过松。
因此,为使我国球墨铸铁生产能有大幅度的增长,必须大力实施能稳定提供质量可靠的优质球墨铸铁件的配套技术。
高强度高碳当量灰铸铁生产工艺问题1-采用合成铸铁
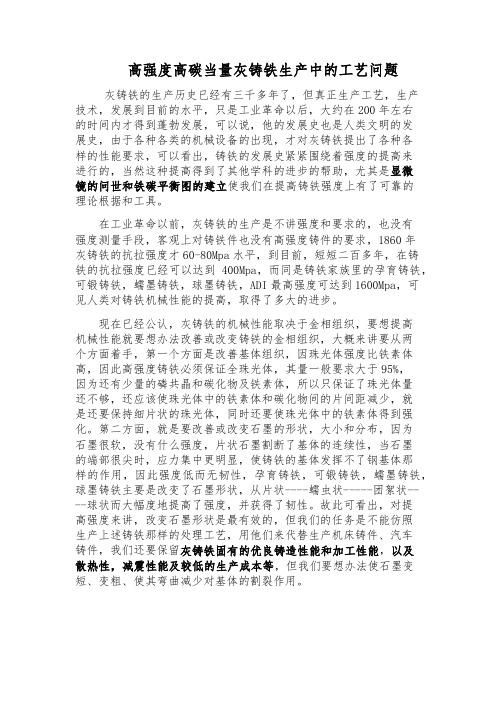
高强度高碳当量灰铸铁生产中的工艺问题灰铸铁的生产历史已经有三千多年了,但真正生产工艺,生产技术,发展到目前的水平,只是工业革命以后,大约在200年左右的时间内才得到蓬勃发展,可以说,他的发展史也是人类文明的发展史,由于各种各类的机械设备的出现,才对灰铸铁提出了各种各样的性能要求,可以看出,铸铁的发展史紧紧围绕着强度的提高来进行的,当然这种提高得到了其他学科的进步的帮助,尤其是显微镜的问世和铁碳平衡图的建立使我们在提高铸铁强度上有了可靠的理论根据和工具。
在工业革命以前,灰铸铁的生产是不讲强度和要求的,也没有强度测量手段,客观上对铸铁件也没有高强度铸件的要求,1860年灰铸铁的抗拉强度才60-80Mpa水平,到目前,短短二百多年,在铸铁的抗拉强度已经可以达到400Mpa,而同是铸铁家族里的孕育铸铁,可锻铸铁,蠕墨铸铁,球墨铸铁,ADI最高强度可达到1600Mpa,可见人类对铸铁机械性能的提高,取得了多大的进步。
现在已经公认,灰铸铁的机械性能取决于金相组织,要想提高机械性能就要想办法改善或改变铸铁的金相组织,大概来讲要从两个方面着手,第一个方面是改善基体组织,因珠光体强度比铁素体高,因此高强度铸铁必须保证全珠光体,其量一般要求大于95%,因为还有少量的磷共晶和碳化物及铁素体,所以只保证了珠光体量还不够,还应该使珠光体中的铁素体和碳化物间的片间距减少,就是还要保持细片状的珠光体,同时还要使珠光体中的铁素体得到强化。
第二方面,就是要改善或改变石墨的形状,大小和分布,因为石墨很软,没有什么强度,片状石墨割断了基体的连续性,当石墨的端部很尖时,应力集中更明显,使铸铁的基体发挥不了钢基体那样的作用,因此强度低而无韧性,孕育铸铁,可锻铸铁,蠕墨铸铁,球墨铸铁主要是改变了石墨形状,从片状----蠕虫状-----团絮状----球状而大幅度地提高了强度,并获得了韧性。
故此可看出,对提高强度来讲,改变石墨形状是最有效的,但我们的任务是不能仿照生产上述铸铁那样的处理工艺,用他们来代替生产机床铸件、汽车铸件,我们还要保留灰铸铁固有的优良铸造性能和加工性能,以及散热性,减震性能及较低的生产成本等,但我们要想办法使石墨变短、变粗、使其弯曲减少对基体的割裂作用。
合成铸铁技术应用于发动机缸体
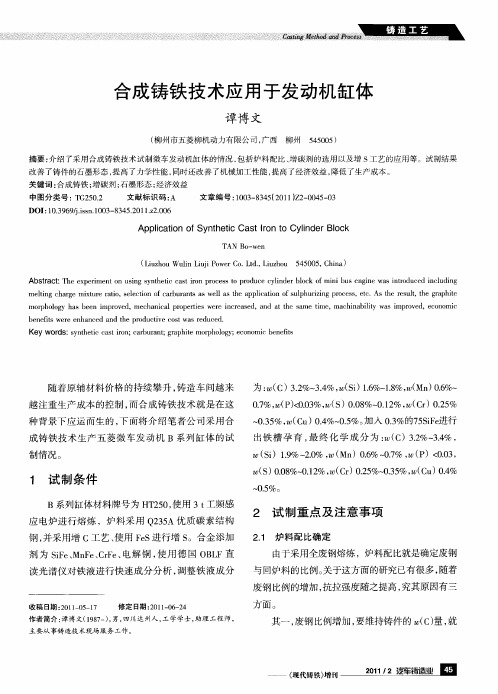
出铁 槽 孕 育 , 终 化 学 成 分 为 : C)3 %~. , 最 ( . 3% 2 4
(i . 2 % , Mn . 0 % , P 0 3 S)1 %~ . W( )06 9 0 %~ . W( )< . , 7 0 ( ) .8 01 %, C ) . %~ . %, ( u 0 % S 0 %~ . ( r 0 5 0 5 w C ) - 0 2 2 3 4
关键词 : 合成铸铁 ; 增碳剂 ; 石墨形态 ; 经济效益
中图分类号 : G 5. T 202 文 献 标 识 码 : A 文 章 编 号 :0 3 84 (0 )2 04 — 3 10 — 3 5 2 1 Z — 0 5 0 1
LFS高纯及超高纯生铁助力中国铸造由大而强
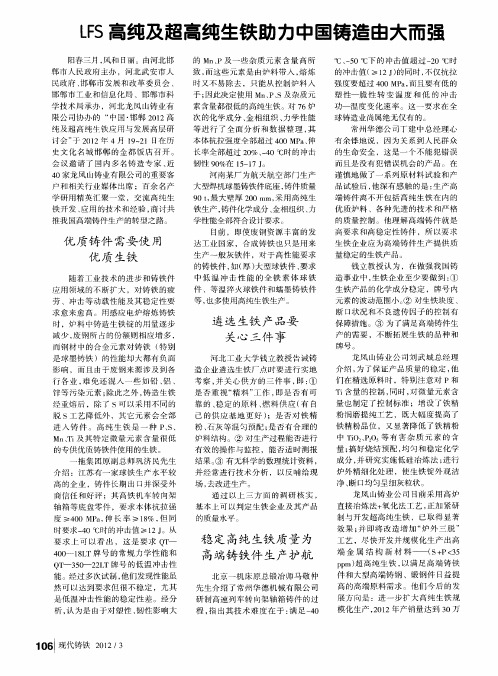
阳春 三 月 , 和 日丽 。由河 北 邯 风
的 Mn P及 一些 杂质元 素含 量高 所 、 致, 而这些 元素是 由炉 料带入 , 熔炼
时 又 不 易 除 去 ,只 能 从 控 制 炉 料 人 手 ; 此 决 定 使 用 Mn P S及 杂质 元 因 、、
4 O 1L 0 一 8 T牌 号 的 常 规 力 学 性 能 和
炉外精 细化处理 ,使 生铁锭 外观 洁 净 、 口均匀呈 细灰 粒状 。 断
龙 风 山 铸 业 公 司 目前 采 用 高 炉 直 接 冶 炼 法 + 化 法 艺 , 加 紧 研 氧 正
基本上 可 以判定生 铁企业及 其产 品
考察 , 并关 心供 方 的三件 事 , : 即 ①
是 否重视 “ 精料 ” 工作 , 即是 否有可 靠的 、 稳定 的原料 、 料供 应 ( 自 燃 有 己的供 应 基地 更好 ) ;是 否 对 铁 精 粉、 石灰 等混匀预配 ; 否有合理 的 是 炉料结构 。② 对生产过程能否 进行
一
永 冠 能 源 科 技 集 团 执 行 长蔡 树 根 先 生 在 致 词 中除 了对 三 届 大赛 所 取 得 的 成 功 和 影 响 表 示 赞 赏 ,对 获 奖 学 生 和指 导老师表示 祝贺外 ,特别强 调 了 企 业 对 人 才 的 需 求 ,希 望 各 大 学 和 在 校 大 学 生 重 视 并 利 用 好 铸 造
是球墨铸铁 )的性能 却大都有 负面
影 响 ,而 且由 于 废 钢 来 源 涉 及 到 各
行 各业 , 免还 混入 一些 如铅 、 、 难 铝
锌 等 污 染 元 素 ; 此 之 外 , 造 生 铁 除 铸 经 重 熔 后 ,除 了 S可 以采 用 不 同 的 脱 s工 艺 降 低 外 ,其 它 元 素 会 全 部 进 入 铸 件 。 高 纯 生 铁 是 一 种 P S 、、 Mn 及 其 特 定 微 量 元 素 含 量 很 低 、
合成铸铁在轮类铸件生产中的应用
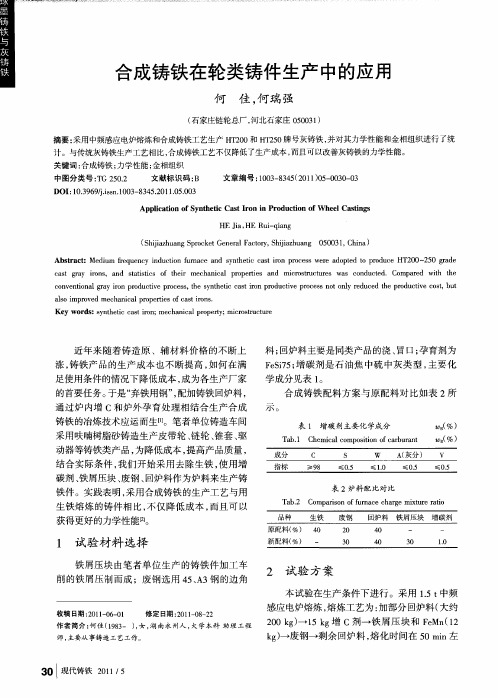
DOI 1. 6 ̄i n10 — 3 5 0 0 . 3 :03 9 .s. 3 8 4 . 1.5 0 9 s 0 2 1 0
合成铸铁在轮 类铸件生产 中的应用
何 佳 , 瑞 强 何
( 石家庄链 轮总厂, 河北石家庄 0 0 3 ) 50 1
摘要 : 采用 中频感应 电炉熔炼 和合成铸铁工艺生产 H 2 0和 H 20牌号灰铸铁 , T0 T5 并对其力学性能和金相组织进行了统 计 。与传统灰铸铁生产工艺相 比, 合成铸铁工艺不仅降低了生产成本 , 而且可 以改善灰铸铁的力学性能 。
c s g a io s n sait s f h i a t ry r n ,a d t t i o t er sc me h n c l r p r e a d c a ia p o e t s n mir sr c u e w s o d ce . C mp r d i c o tu t r s a c n u td o ae wi t e t h h c n e t n lg a o r d ci e p o e s t e s nh t a ti n p o u t e p o e sn t n y r d c d t e p o u t e c s u o v n i a r y i n p o u t r c s , h y t ei c s r r d ci r c s o l e u e h r d ci o t t o r v c o v o v ,b as mp o e c a ia r p riso a t r n . loi rv d me h n c lp o e e fc s io s t Ke r s y t ei a t r n me h nc lp o e y mi r s u tr y wo d :s n h t c s o ; c a ia r p a ; c o t cu e c i r
- 1、下载文档前请自行甄别文档内容的完整性,平台不提供额外的编辑、内容补充、找答案等附加服务。
- 2、"仅部分预览"的文档,不可在线预览部分如存在完整性等问题,可反馈申请退款(可完整预览的文档不适用该条件!)。
- 3、如文档侵犯您的权益,请联系客服反馈,我们会尽快为您处理(人工客服工作时间:9:00-18:30)。
Fig.3
图3合成铸铁石墨形态
中图分类号:TG251 文献标识码:A 文章缡号:1000—836512010)08-1090—04
Research and App¨cation of Synthesis Cast lron
WANG Shun-an,ZOU Rong-jian (Casting-Forging Co.,Ltd.,Dajiang Industrial Group,Chongqing 401321,China) Abstract:Because synthesizes cast irons using large quantity of steel scraps,the carburetion technology becomes the key technology in its production.This article emphatically discusses the smelting technology of synthesis cast iron,from the carburetion principle and the ingredient.And mechanicaI property and the miCrOStructure of synthesized cast iron are also introduced. Key words:Synthesis cast iron;Carburizing agent;Mechanical property;Microstructure
铸造技术
FOUNDRY TECHNOLOGY
V01.31 NO.8 Aug.2010
பைடு நூலகம்
合成铸铁的生产及应用
王顺安,邹荥剑 (重庆大江工业集团铸锻公司,重庆401321) 摘要:熔炼合成铸铁,由于废钢加入量大,增碳技术成为其生产的关键技术。对合成铸铁的增碳原理、铸铁熔炼工艺进行了分 析。结果表明,采用晶体石墨增碳荆,电炉熔炼合成铸铁的增碳速度明显高于非石墨增碳剂;且晶体石墨增碳剂可作为石墨 的外来晶核,促进细片状A型石墨的形成,铁液白口倾向小,力学性能提高。 关键词:合成铸铁;增碳剂;力学性能;金相组织
A
B
A
图1石墨的晶体结构
Fig.1 Graphite crystal structure
图2无定形碳的晶体结构 Fig.2 Amorphous carbon crystal structure
依据增碳剂中碳的晶体结构,增碳剂可分为非晶 体态或晶体态。根据碳在增碳剂中的存在形态,分为 石墨增碳剂和非石墨增碳剂。石墨增碳剂主要有废石 墨电极、石墨电极边角料及碎屑、天然石墨压粒、微晶 石墨等;此外,碳化硅(SiC)具有和石墨相似的六方结 构,也被列为石墨增碳剂的一种特殊形态。非石墨增 碳剂主要有沥青焦、煅烧石油焦、焦炭压粒、煅烧无烟 煤等。铸铁常用的增碳剂主要以晶体态的石墨增碳剂 为主,其主要化学成分见表1。
搅拌有利于碳的溶解和扩散,减少增碳剂浮在 铁液表面被烧损。在增碳剂未完全溶解前,搅拌时 间长,吸收率高。搅拌还可以减少增碳保温时间, 使生产周期缩短,避免铁液中合金元素烧损。但搅 拌时间过长,不仅对炉子的使用寿命有很大影响, 而且在增碳剂溶解后,搅拌会加剧铁液中碳的损 耗。因此,铁液搅拌时间应以保证增碳剂完全溶解 为适宜。 2.5铁液化学成分对增碳剂吸收率的影响
K。——固体粒子表面液体边界层的碳传质系数; K。——界面反应常数。
试验表明,碳在铁液中的溶解受到固体粒子表面
液体边界层的碳传质的控制。用焦炭和煤颗粒所得的
结果与用石墨所得的结果对比,发现石墨增碳剂在铁
液中的扩散溶解速度明显快于焦炭和煤颗粒一类的增 碳剂。用电子显微镜观察了部分溶解的焦炭和煤颗粒
样品,发现在样品表面形成了一层很薄的粘性灰层,这
从动力学和热力学的观点分析,铁液的氧化性与 C—Si—O系的平衡温度有关,即铁液中的O与C、si会 发生反应。而平衡温度随目标C、Si含量不同而发生 变化。铁液在平衡温度以上时,优先发生碳的氧化,C 和0生成C0和CO。,这样,铁液中的碳氧化损耗增 加。因此,在平衡温度以上时,增碳剂吸收率降低。当 增碳温度在平衡温度以下时,由于温度较低,碳的饱和 溶解度降低,同时碳的溶解扩散速度下降,因而收得率 也较低。因此,增碳温度在平衡温度时,增碳剂吸收率 最高。 2.4铁液搅拌对增碳剂吸收率的影响
合成铸铁熔炼过程中,由于废钢加入量大,铁液C 含量低,必须采用增碳剂增碳。增碳剂中以单质形式存 在的碳,熔化温度为3 727℃,在铁液温度下不能熔化, 因此,增碳剂中的碳主要通过溶解和扩散两种方式溶于 铁液。当铁液的含碳量在2.1%时,石墨增碳剂中的石 墨可直接在铁液中溶解直溶[1]。而非石墨增碳的直溶 现象基本不存在,只是随着时间的推移,碳在铁液中逐 渐的扩散溶解。对于电炉熔炼合成铸铁的增碳,采用晶 体石墨增碳的增碳速度显著高于非石墨增碳剂。
当铁液中初始碳含量高时,在一定的溶解极限 下,增碳剂的吸收速度慢,吸收量少,烧损相对较多, 增碳剂吸收率低。当铁液初始碳含量较低时,情况 相反。另外,铁液中硅和硫阻碍碳的吸收,降低增碳 剂的吸收率。而锰元素有助于碳的吸收,提高增碳 剂吸收率。就影响程度而言,硅最大,锰次之,碳、硫
影响较小。因此,实际生产过程中,应先增锰,再增 碳,后增硅。 3增碳剂的分类
表2炉料配比仞(%) Tab.2 Furnace charge ingredient
液表面,通过电炉熔炼时铁液的涡流搅拌或人工搅拌 使晶体石墨增碳剂溶解吸收。 4.2.2 炉外增碳
出铁时,将100 300目的石墨增碳剂放到包内, 或从出铁槽随流冲入,出完铁液后应充分搅拌,尽可能 使碳溶解吸收。碳的吸收率在50%左右。 5合成铸铁的金相组织和性能
Graphite morphology of synthesis cast iron
图4合成铸铁珠光体组织
Fig.4 Pearlite in synthesis cast iron
生铁中有许多粗大的过共晶石墨,这种粗大的石 墨具有遗传性,熔炼过程中很难被消除,削弱了铁液在 凝固过程中石墨化析出的膨胀作用,增大了铁液凝固 过程中的收缩倾向[4]。在普通灰铸铁的生产中,由于 加入大量的生铁,在铸铁的金相组织中常会出现大块 状石墨,而且石墨长度较长(见图5);珠光体数量相对
是影响其在铁液中扩散溶解性能的主要原因。 2影响增碳剂吸收率的主要因素
2.1增碳剂粒度的影响
使用增碳剂的增碳过程包括溶解扩散过程和氧化
损耗过程。增碳剂的粒度大小不同,溶解扩散速度和
万方数据
《铸造技术}08/2010
王顺安等:合成铸铁的生产及应用
氧化损耗速度也就不同,而增碳剂吸收率的高低就取 决于增碳剂溶解扩散速度和氧化损耗速度的综合作 用。在一般情况下,增碳剂颗粒小,溶解速度快,损耗 速度大;增碳剂颗粒大,溶解速度慢,损耗速度小。增 碳剂粒度大小的选择与炉膛直径和容量有关,一般情 况下,炉膛的直径和容量大,增碳剂的粒度要大一些; 反之,增碳剂的粒度要小一些。对于1 t以下电炉熔 炼,晶体石墨粒度要求0.5~2.5 mm;1~3 t电炉熔 炼,晶体石墨粒度要求2.5~5.0 mm;3~10 t电炉熔 炼,晶体石墨粒度要求5.0~20.0 mm;覆盖在浇包中 晶体石墨粒度要求0.5~1.0 mm。 2.2增碳剂加入量的影响
碳熔液中溶解进行了试验研究。试验把温度处在 1 623---,1 923 K之间的各种含碳物质作为研究对象,
研究它们在铁液中的溶解及相互作用。含碳物质的溶
解遵守公式如下:
歹=K·(C—Cb)
式中.f——碳溶解时的传质通量; C——碳的饱和浓度;
Cb——碳的主体浓度;
1
1
1
K——总溶解系数,玄2瓦1十瓦I;
收稿日期:2010—03-01;
修订日期:2010—03—26
作者简介:王顺安(1966一),重庆忠县人,高级工程师.主要从事铸造工
艺设计和技术质量管理工作.
Emillzourongjian2007@163.corn
电炉熔炼铸铁采用增碳剂进行增碳,其碳在铁液
中扩散溶解,国外某大学就这个问题对含碳物质在铁
铸铁常用的增碳剂是一种碳质材料,主要成分 是碳。碳质材料主要有石墨和无定形碳。石墨为 六方层片状结晶(如图1所示),石墨晶体中的碳原 子是层状排列的,在同层原子之间是以共价键结 合,其结合力较强;而层与层之间则是以极性键结 合,其结合力较弱。因此,石墨极易分层剥离,强度 极低。由于石墨晶体具有这样的结构特点,因此在 铁液中长大时就容易长成片状结构[2]。石墨可分 为天然石墨和人造石墨两类,都是铸造行业中广泛 应用的材料[3]。无定形碳也是六方层片状结晶,与 石墨不同之处在于六角形配列不完整,层间距离略 大(如图2所示)。
在一定的温度和化学成分相同的条件下,铁液中 碳的饱和浓度一定。铸铁中碳的溶解极限为[C%]一 1.3 d-O.025 7T一0.31[Si%]一0.33[P%]一0.45 [S%]d-0.028[-Mn%](T为铁液温度)。在一定饱和 度下,增碳剂加入量越多,溶解扩散所需时间就越长, 相应损耗量就越大,吸收率就会降低。 2.3温度对增碳剂吸收率的影响
经过增碳剂增碳处理后的铸铁,由于使用大量的 增碳剂增碳,在铁液中生成了大量弥散分布的非均质 结晶核心,降低了铁液的过冷度,促使生成以A型石 墨为主的石墨组织。同时,由于生铁用量少或不用生 铁,生铁的遗传作用大为削弱,因此使A型石墨片分 枝发达不易长大,使得石墨短小且均匀(见图3)。不 同种类的废钢都含有一定量的氮,由于废钢加入,以及 使用氮气作为喷粉法的载体,使得铸铁中有的氮量较 高,铸铁中氮通过改变铸铁组织中的石墨结构促进珠 光体形成(见图4)。