蒸汽发生器工艺设计要点
节能型煮茧蒸汽发生器系统设计

节能型煮茧蒸汽发生器系统设计随着社会科技的不断发展,人们对于节能环保的要求也越来越高。
在传统的茧丝生产过程中,蒸汽发生器系统是不可或缺的设备之一。
为了满足节能环保的要求,需要对蒸汽发生器系统进行改进和优化,设计一套节能型煮茧蒸汽发生器系统。
一、系统组成1. 燃料供给系统:将环保的生物质燃料连接到蒸汽发生器系统,确保燃料的供给平稳可靠。
2. 燃烧系统:将生物质燃料燃烧产生的热能转换成蒸汽能量,确保燃烧效率高、排放清洁。
3. 蒸汽产生系统:通过燃烧释放的热能使水蒸发产生蒸汽,同时保证蒸汽的纯净度。
4. 蒸汽输送系统:将产生的蒸汽输送到煮茧设备中,确保蒸汽输送的稳定性和高效率。
5. 排放系统:对燃烧排放的废气进行处理,达到环保排放标准。
二、系统设计原则1. 节能:在系统设计中,应充分考虑能源利用效率,尽量降低能源的消耗。
2. 环保:尽量减少废气排放,采用清洁燃料进行燃烧,降低对环境的影响。
3. 安全:系统设计必须符合相关的安全标准,保证设备运行过程中人员和设备的安全。
4. 高效:优化系统结构和运行参数,确保系统运行效率高,减少能源浪费。
5. 可靠:系统设计考虑设备运行稳定性和可靠性,减少设备故障对生产的影响。
三、关键技术1. 燃烧控制技术:通过智能控制系统实现燃烧过程的精准控制,提高燃烧效率并降低废气排放。
2. 蒸汽产生技术:采用高效的蒸汽产生技术,减少水的消耗,并提高蒸汽的产生效率。
3. 能量回收技术:对烟气中的余热进行回收利用,提高热能利用效率,降低能源消耗。
4. 智能控制技术:通过传感器和智能控制系统实现对系统运行状态的监测和调节,提高系统的自动化程度。
四、系统优势1. 节能环保:通过优化设计和先进技术的应用,实现能源利用效率的提高,降低废气排放,达到节能环保的目的。
2. 高效稳定:系统设计考虑设备运行稳定性和可靠性,确保系统长时间稳定运行,提高生产效率。
4. 经济实惠:系统设计合理,运行成本低,能源消耗少,长期运行下来能够带来显著的经济效益。
蒸汽发生器技术要求

蒸汽发生器技术要求
蒸汽发生器技术要求包括以下几个方面:
1. 蒸汽产量:根据应用需求确定蒸汽发生器的额定蒸汽产量,确保能满足工艺或设备的需求。
2. 蒸汽压力:根据工艺或设备的要求确定合适的蒸汽压力范围。
3. 热效率:蒸汽发生器应具备高热效率,即在给定的燃料或能源消耗下,能够产生更多的蒸汽。
提高热效率有利于节能和减少对环境的污染。
4. 安全性:蒸汽发生器应具备完善的安全保护装置,如过热保护、低水位保护、压力过高保护等,确保设备运行安全可靠。
5. 控制系统:蒸汽发生器应配备先进的控制系统,能够实现对蒸汽产量、压力、温度等参数的精确控制和调节。
6. 维护保养:蒸汽发生器应设计可靠、易于维护的结构,降低维护成本和停机时间。
7. 环保性能:蒸汽发生器应符合环境保护要求,包括低排放、减少废气和废水的排放等。
综上所述,蒸汽发生器技术要求主要包括产量、压力、热效率、安全性、控制系统、维护保养和环保性能等方面。
高压蒸汽发生器的设计和研发

高压蒸汽发生器的设计和研发第一章:引言高压蒸汽发生器是一种利用化石燃料、核能以及可再生能源等作为热源,通过水蒸汽来转化为机械能或电能的设备。
随着能源危机的加剧以及环保意识的不断增强,高压蒸汽发生器的研究和应用也日益受到重视。
本文将从高压蒸汽发生器的设计和研发两个方面进行深入探讨。
第二章:高压蒸汽发生器的设计2.1 理论基础高压蒸汽发生器的设计需要依据热力学和流体力学理论进行分析和计算。
其中,理想的高压蒸汽发生器应该能够达到以下几个目标:高效、安全、稳定、节能、环保等。
2.2 设计参数在设计高压蒸汽发生器时,需要考虑以下几个参数:蒸发量、蒸汽压力、蒸汽温度、管道直径、燃料种类、燃烧方式等。
这些参数的选取将直接影响设备的性能指标和安全程度。
2.3 结构设计高压蒸汽发生器主要包括水箱、加热管、蒸汽出口、安全阀、控制系统等部分。
在设计时,需要考虑到这些部分的配合和结构的合理性,以确保设备的正常运行和安全性。
2.4 材料选用高压蒸汽发生器的压力、温度和腐蚀等因素对制造材料的选择提出了较高的要求。
常用的材料包括碳钢、合金钢、不锈钢等,需要根据实际情况进行选择。
第三章:高压蒸汽发生器的研发3.1 研究方向高压蒸汽发生器的研究方向主要包括新型材料应用、燃料种类拓展、高效节能技术、环保技术等。
通过这些方面的研究和创新,可以不断提高高压蒸汽发生器的性能和安全性。
3.2 技术创新在高压蒸汽发生器的研发过程中,需要不断进行技术创新。
目前,一些新技术被广泛应用于高压蒸汽发生器中,如计算机辅助设计、自动控制技术、超声波技术等,在提高设备质量和降低生产成本方面发挥着重要作用。
3.3 实用性和推广高压蒸汽发生器的研发和创新不仅仅是一项科学研究,更是一项实用性的技术工作。
因此,在实践中需要注重设备的实用性和推广。
同时也需要注意,在推广应用过程中需配合一系列的政策法规和标准要求。
第四章:结论和展望高压蒸汽发生器在现代工业生产中具有广泛的应用,其性能的提高对工业生产的效率和能耗等方面都有着重要作用。
供暖蒸汽发生器设计

供暖蒸汽发生器设计
随着冬季的到来,供暖蒸汽发生器成为了大家关注的焦点。
而如何设计一款高效、安全、节能的供暖蒸汽发生器则是制造商们需要解决的难题。
本文将从以下几个方面探讨供暖蒸汽发生器的设计:
1. 材料选择:供暖蒸汽发生器承受高温高压的环境,因此需要选用高温合金钢等材料。
2. 结构设计:蒸汽发生器的结构设计需要考虑到内部的燃烧室、水管、管板等部分的布局,以及对于燃料的供给和排烟的设计。
3. 热力学计算:根据供暖面积和热负荷大小,进行热力学计算,确定蒸汽发生器的燃料消耗量和蒸汽产生量。
4. 安全措施:蒸汽发生器在高温高压下存在一定的安全隐患,需要设计安全阀、水位报警器等安全措施。
5. 环保设计:在设计过程中,需要考虑到蒸汽发生器的排放问题,选用低污染的燃料、使用高效的烟气净化设备等措施。
通过以上几个方面的综合考虑,设计出一款高效、安全、节能、环保的供暖蒸汽发生器,不仅能够满足人们的需求,也能够对环境做出贡献。
- 1 -。
节能型煮茧蒸汽发生器系统设计

节能型煮茧蒸汽发生器系统设计全文共四篇示例,供读者参考第一篇示例:节能型煮茧蒸汽发生器系统设计随着人们对能源和环境的关注不断增加,节能环保已经成为了当今社会的主题之一。
在工业生产中,煮茧蒸汽发生器是一种常见的设备,用于为煮茧机提供蒸汽,从而完成蚕茧的煮化。
传统的煮茧蒸汽发生器存在能耗高、效率低、排放污染等问题。
设计一种节能型煮茧蒸汽发生器系统成为了当前亟待解决的技术难题。
1. 节能型煮茧蒸汽发生器系统的设计要点要设计一套节能型的煮茧蒸汽发生器系统,首先需要对传统系统进行全面的分析,明确存在的问题和改进的方向。
需要充分考虑系统的整体设计,包括蒸汽发生器、燃烧系统、余热利用、控制系统等方面的优化。
还需要考虑设备的安全性和稳定性,确保系统在长期运行中能够稳定可靠地提供蒸汽。
2. 节能型煮茧蒸汽发生器的关键技术在设计节能型煮茧蒸汽发生器系统时,需要解决一系列关键技术问题。
首先是燃烧系统的优化,采用高效燃烧技术和清洁燃烧技术,减少燃料的消耗和燃烧产生的污染物。
其次是余热利用技术的应用,将蒸汽发生过程中产生的余热进行回收利用,提高能源利用效率。
还需要考虑控制系统的智能化,实现对系统运行状态的实时监控和调整,确保系统能够以最佳状态运行。
4. 节能型煮茧蒸汽发生器系统的应用前景设计一套节能型煮茧蒸汽发生器系统,不仅可以提高生产效率,节约能源成本,还能减少对环境的影响,符合当今社会对能源和环境的要求。
该系统具有广阔的应用前景,在丝绸生产、纺织工业和其他相关行业中得到广泛应用。
设计一套节能型煮茧蒸汽发生器系统是当前亟待解决的技术难题,需要充分考虑系统的整体设计和各个关键技术,提出切实可行的设计方案,以满足工业生产对能源和环境的要求。
只有不断推进技术创新,不断提高系统的能效,才能真正实现节能减排,推动工业生产的可持续发展。
第二篇示例:节能型煮茧蒸汽发生器系统设计随着社会经济的发展和人们生活水平的提高,节能环保已经成为人们日常生活中越来越重要的话题。
生物质蒸汽发生器设计要点

生物质蒸汽发生器设计要点摘要:针对生物质蒸汽发生器使用的越来越广泛,部分产品在同等水容积下出力不同的问题进行分析,即在小于30L水容积下生物质蒸汽发生器的受热面如何配置才能达到最佳。
关键词:生物质蒸汽发生器;小于30L;水容积与受热面的配置引言随着我国经济发展,蒸汽发生器其具有免报检、性能高等特点,在中小型企业中越来越得到广泛的应用,在产品需求量大的同时伴随着产品质量不过关,水容积超标等问题,本文主要讨论在小于30L水容积限制条件下如何达到0.5t/h 的蒸发量。
设计理念本设计采用自然循环整体螺旋翅片管换热技术,受热面布置有辐射受热面、对流受热面、过热受热面、预热受热面。
汽水端实现预热-蒸发-过热这一过程。
设计基本参数2.1生物质蒸汽发生器设计参数锅炉型号:DZG0.5-0.8/340-S额定蒸发量(t/h):0.5额定压力(MPa):0.8过热蒸汽温度(℃):340给水温度(℃): 20冷空气温度(℃): 20排污率(%): 5设计燃料:生物质颗粒2.2燃料参数(收到基成分%)锅炉总体布局及结构特点3.1锅炉总体布局本设计采用DZG结构形式,即卧式单锅筒纵置式,炉排为固定炉排,配有鼓风机、引风机,给料减速机、布袋除尘器、控制系统[1]等辅机。
3.2结构特点DZG0.5-0.8/340-S型锅炉为单锅筒纵置式自然循环水管锅炉,主要受热面分为:辐射受热面3.5m2、对流受热面8.9m2、过热受热面6.2m2、预热受热面11.1m2。
锅炉本体分为上锅筒,下左右集箱,三者由整体螺旋翅片管连接,构成炉膛及对流受热面。
过热器布置在对流受热面与省煤器之间。
炉体外侧砌有炉墙及保温材料[2]。
整体螺旋翅片管为φ32×3.5的无缝管(20-GB/T 3087-2008),每米管长受热面积约为0.53m2。
过热器:过热器为φ32×3.5的光管,烟速8.6m/s。
省煤器:省煤器管为整体螺旋翅片管φ38×3.5,给水温度20℃,出口水温97℃,烟气速度12m/s。
蒸汽发生器设计范文

蒸汽发生器设计范文首先,设计者需要确定蒸汽发生器的工作压力和温度。
这取决于具体应用的要求,例如蒸汽发生器用于发电厂时,通常需要较高的工作压力和温度。
设计者需要考虑到材料的强度和耐高温性能,以确保蒸汽发生器可以安全运行。
其次,设计者需要选择合适的加热方式。
常见的加热方式包括直接加热和间接加热。
直接加热是指将燃料直接燃烧,将热量传递给液体以产生蒸汽。
间接加热是指使用燃烧产生的热量加热介质,再用介质将热量传递给液体。
设计者需要根据实际情况选择最合适的加热方式,并确保燃烧过程的安全性和高效性。
第三,设计者还需要考虑蒸汽发生器的热效率。
热效率指的是将液体转化为蒸汽所利用的能量比例。
提高热效率可以减少能源消耗和环境污染。
为了提高热效率,设计者可以考虑使用热回收技术,例如烟气余热回收和废热利用。
另外,蒸汽发生器的控制系统也是设计的重要部分。
控制系统可以监测和控制蒸汽发生器的压力、温度和流量等参数,以确保蒸汽发生器的安全运行。
控制系统可以通过传感器和反馈机制来实现,设计者需要选择合适的控制策略和控制器来满足具体要求。
最后,设计者还需要考虑蒸汽发生器的维护和保养。
蒸汽发生器在长时间运行后会出现一些问题,例如结垢、腐蚀和泄漏等。
设计者需要将这些问题考虑在内,并采取相应的措施,例如定期清洗、维修和更换部件等。
总之,蒸汽发生器的设计需要综合考虑安全性、效率性和环保性等因素。
通过选择合适的工作压力和温度、加热方式、热回收技术和控制系统,并定期进行维护和保养,可以保证蒸汽发生器的安全运行和高效运作。
设计者需要根据具体应用的需求和条件来进行设计,以实现最佳的性能和效益。
纯蒸汽发生器设计标准是什么
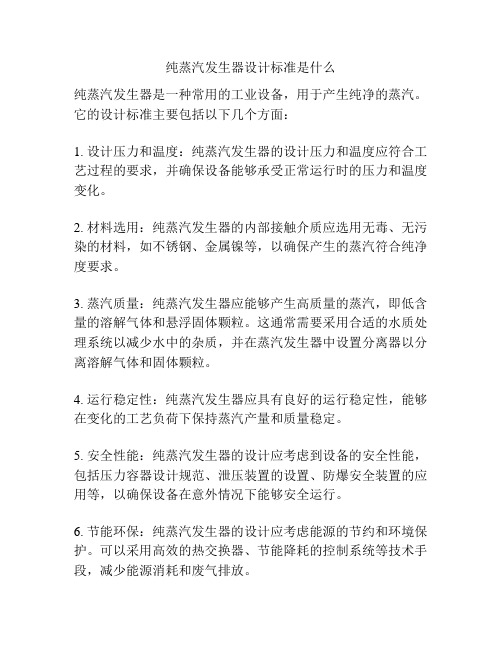
纯蒸汽发生器设计标准是什么
纯蒸汽发生器是一种常用的工业设备,用于产生纯净的蒸汽。
它的设计标准主要包括以下几个方面:
1. 设计压力和温度:纯蒸汽发生器的设计压力和温度应符合工艺过程的要求,并确保设备能够承受正常运行时的压力和温度变化。
2. 材料选用:纯蒸汽发生器的内部接触介质应选用无毒、无污染的材料,如不锈钢、金属镍等,以确保产生的蒸汽符合纯净度要求。
3. 蒸汽质量:纯蒸汽发生器应能够产生高质量的蒸汽,即低含量的溶解气体和悬浮固体颗粒。
这通常需要采用合适的水质处理系统以减少水中的杂质,并在蒸汽发生器中设置分离器以分离溶解气体和固体颗粒。
4. 运行稳定性:纯蒸汽发生器应具有良好的运行稳定性,能够在变化的工艺负荷下保持蒸汽产量和质量稳定。
5. 安全性能:纯蒸汽发生器的设计应考虑到设备的安全性能,包括压力容器设计规范、泄压装置的设置、防爆安全装置的应用等,以确保设备在意外情况下能够安全运行。
6. 节能环保:纯蒸汽发生器的设计应考虑能源的节约和环境保护。
可以采用高效的热交换器、节能降耗的控制系统等技术手段,减少能源消耗和废气排放。
7. 维护和清洁性:纯蒸汽发生器的设计应便于维护和清洁。
例如,设备内部应考虑到清洗的便利性,如设置清洗孔、积水孔、防垢措施等。
综上所述,纯蒸汽发生器的设计标准主要包括设计压力和温度、材料选用、蒸汽质量、运行稳定性、安全性能、节能环保和维护清洁性等方面。
这些标准的合理应用可以确保纯蒸汽发生器的正常运行,并满足工艺过程对蒸汽质量和纯净度的要求。
节能型煮茧蒸汽发生器系统设计
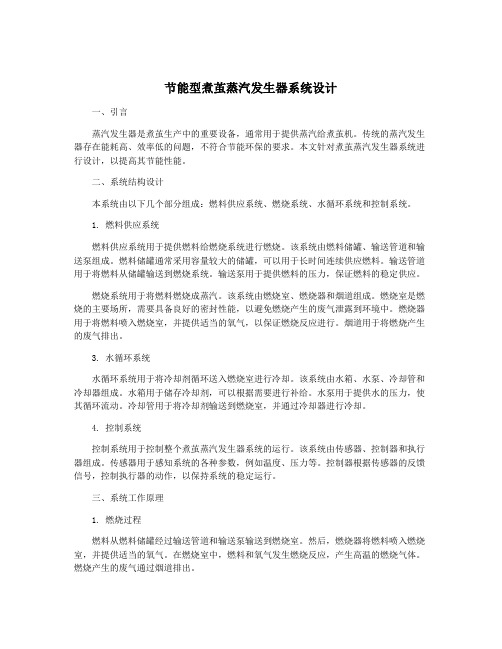
节能型煮茧蒸汽发生器系统设计一、引言蒸汽发生器是煮茧生产中的重要设备,通常用于提供蒸汽给煮茧机。
传统的蒸汽发生器存在能耗高、效率低的问题,不符合节能环保的要求。
本文针对煮茧蒸汽发生器系统进行设计,以提高其节能性能。
二、系统结构设计本系统由以下几个部分组成:燃料供应系统、燃烧系统、水循环系统和控制系统。
1. 燃料供应系统燃料供应系统用于提供燃料给燃烧系统进行燃烧。
该系统由燃料储罐、输送管道和输送泵组成。
燃料储罐通常采用容量较大的储罐,可以用于长时间连续供应燃料。
输送管道用于将燃料从储罐输送到燃烧系统。
输送泵用于提供燃料的压力,保证燃料的稳定供应。
燃烧系统用于将燃料燃烧成蒸汽。
该系统由燃烧室、燃烧器和烟道组成。
燃烧室是燃烧的主要场所,需要具备良好的密封性能,以避免燃烧产生的废气泄露到环境中。
燃烧器用于将燃料喷入燃烧室,并提供适当的氧气,以保证燃烧反应进行。
烟道用于将燃烧产生的废气排出。
3. 水循环系统水循环系统用于将冷却剂循环送入燃烧室进行冷却。
该系统由水箱、水泵、冷却管和冷却器组成。
水箱用于储存冷却剂,可以根据需要进行补给。
水泵用于提供水的压力,使其循环流动。
冷却管用于将冷却剂输送到燃烧室,并通过冷却器进行冷却。
4. 控制系统控制系统用于控制整个煮茧蒸汽发生器系统的运行。
该系统由传感器、控制器和执行器组成。
传感器用于感知系统的各种参数,例如温度、压力等。
控制器根据传感器的反馈信号,控制执行器的动作,以保持系统的稳定运行。
三、系统工作原理1. 燃烧过程燃料从燃料储罐经过输送管道和输送泵输送到燃烧室。
然后,燃烧器将燃料喷入燃烧室,并提供适当的氧气。
在燃烧室中,燃料和氧气发生燃烧反应,产生高温的燃烧气体。
燃烧产生的废气通过烟道排出。
2. 蒸汽生成过程在燃烧过程中,冷却剂从水箱经过水泵输送到燃烧室进行冷却。
冷却剂在与高温燃烧气体接触的吸收了大量的热量,使其温度升高,从而变成蒸汽。
随后,蒸汽经过冷却管输送到需要蒸汽的设备,例如煮茧机。
《3t导热油蒸汽发生器焊接设计 》
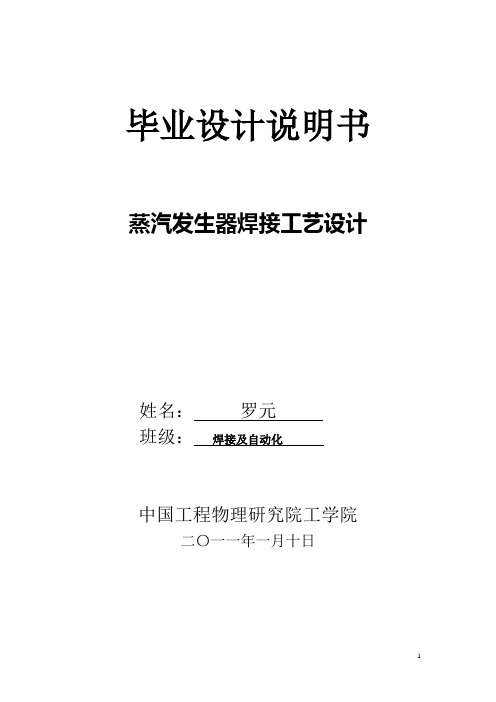
毕业设计说明书蒸汽发生器焊接工艺设计姓名:罗元班级:焊接及自动化中国工程物理研究院工学院二〇一一年一月十日3t蒸汽发生器焊接工艺设计目录1. 蒸汽发生器的用途┄┄┄┄┄┄┄┄┄┄┄┄┄┄┄┄┄┄┄┄┄┄┄┄┄┄┄┄ 32. 蒸汽发生器的组成┄┄┄┄┄┄┄┄┄┄┄┄┄┄┄┄┄┄┄┄┄┄┄┄┄┄┄┄┄33. 蒸汽发生器的工艺分析┄┄┄┄┄┄┄┄┄┄┄┄┄┄┄┄┄┄┄┄┄┄┄┄┄┄┄33.1技术特性┄┄┄┄┄┄┄┄┄┄┄┄┄┄┄┄┄┄┄┄┄┄┄┄┄┄┄┄┄┄┄┄┄4 3.2技术要求┄┄┄┄┄┄┄┄┄┄┄┄┄┄┄┄┄┄┄┄┄┄┄┄┄┄┄┄┄┄┄┄┄53.3对焊接接头的技术要求┄┄┄┄┄┄┄┄┄┄┄┄┄┄┄┄┄┄┄┄┄┄┄┄┄┄┄54. 蒸汽发生器的制造工艺设计┄┄┄┄┄┄┄┄┄┄┄┄┄┄┄┄┄┄┄┄┄┄┄┄┄6 4.1下料┄┄┄┄┄┄┄┄┄┄┄┄┄┄┄┄┄┄┄┄┄┄┄┄┄┄┄┄┄┄┄┄┄┄134.2边缘加工┄┄┄┄┄┄┄┄┄┄┄┄┄┄┄┄┄┄┄┄┄┄┄┄┄┄┄┄┄┄┄14 4.3筒体的卷弯、封头成型、盘管的制作┄┄┄┄┄┄┄┄┄┄┄┄┄┄┄┄┄┄┄┄┄14 4.4封头与筒体的组装工艺要求┄┄┄┄┄┄┄┄┄┄┄┄┄┄┄┄┄┄┄┄┄┄┄┄15 4.5壳体的组装┄┄┄┄┄┄┄┄┄┄┄┄┄┄┄┄┄┄┄┄┄┄┄┄┄┄┄┄┄┄┄16 4.6附件的组装┄┄┄┄┄┄┄┄┄┄┄┄┄┄┄┄┄┄┄┄┄┄┄┄┄┄┄┄┄┄┄16 4.7焊接方法的选择┄┄┄┄┄┄┄┄┄┄┄┄┄┄┄┄┄┄┄┄┄┄┄┄┄┄┄┄┄17 4.8焊接工艺设计┄┄┄┄┄┄┄┄┄┄┄┄┄┄┄┄┄┄┄┄┄┄┄┄┄┄┄┄┄┄194.9无损探伤┄┄┄┄┄┄┄┄┄┄┄┄┄┄┄┄┄┄┄┄┄┄┄┄┄┄┄┄┄┄┄┄┄305. 设计体会┄┄┄┄┄┄┄┄┄┄┄┄┄┄┄┄┄┄┄┄┄┄┄┄┄┄┄┄┄┄┄┄30 参考文献┄┄┄┄┄┄┄┄┄┄┄┄┄┄┄┄┄┄┄┄┄┄┄┄┄┄┄┄┄┄┄┄┄30设计说明书设计题目:蒸汽发生器焊接工艺设计一、蒸汽发生器的用途蒸汽发生器与导热油炉配套使用,广泛应用于食品加工、橡胶、木材加工、油脂等行业,满足了只用一台导热油炉并同时产生蒸汽的工艺要求,节省了大量的设备投资和人工费用。
纯蒸汽发生器标准
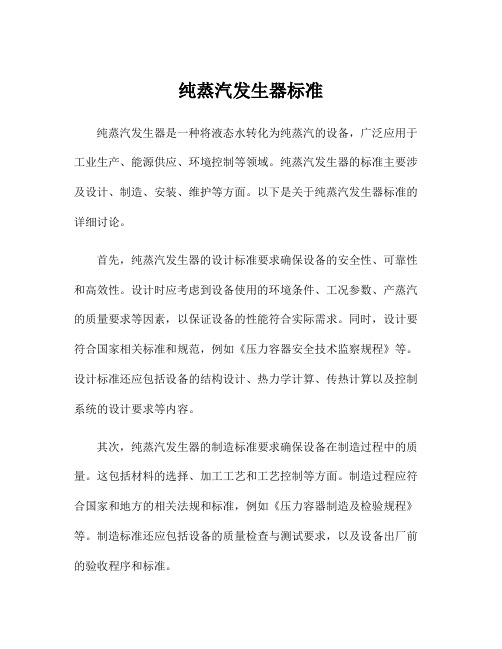
纯蒸汽发生器标准纯蒸汽发生器是一种将液态水转化为纯蒸汽的设备,广泛应用于工业生产、能源供应、环境控制等领域。
纯蒸汽发生器的标准主要涉及设计、制造、安装、维护等方面。
以下是关于纯蒸汽发生器标准的详细讨论。
首先,纯蒸汽发生器的设计标准要求确保设备的安全性、可靠性和高效性。
设计时应考虑到设备使用的环境条件、工况参数、产蒸汽的质量要求等因素,以保证设备的性能符合实际需求。
同时,设计要符合国家相关标准和规范,例如《压力容器安全技术监察规程》等。
设计标准还应包括设备的结构设计、热力学计算、传热计算以及控制系统的设计要求等内容。
其次,纯蒸汽发生器的制造标准要求确保设备在制造过程中的质量。
这包括材料的选择、加工工艺和工艺控制等方面。
制造过程应符合国家和地方的相关法规和标准,例如《压力容器制造及检验规程》等。
制造标准还应包括设备的质量检查与测试要求,以及设备出厂前的验收程序和标准。
纯蒸汽发生器的安装标准要求确保设备能够安全、可靠地运行。
安装前应制定详细的施工方案和工艺流程,并根据设备的尺寸、结构和重量等因素,选用适当的起重设备和安装工具。
安装过程要注意与设备的连接方式、绝缘材料选择、管道安装及焊接等方面,以确保设备的可靠性和安全性。
设备安装后,还应进行全面的检查和试运行,以验证设备的运行状况和性能,确保其满足设计要求。
纯蒸汽发生器的维护标准要求确保设备在运行过程中保持良好的工作状态和性能。
维护工作包括设备的定期检查、维护、保养和修理等方面。
维护标准应明确维护工作的频率、内容和方法,并要求设备管理人员具备相关的维护技能和知识。
维护工作还应记录在册,并包括设备的维护记录、故障处理记录、安全事故记录等内容。
此外,维护标准还应制定设备的寿命周期管理计划,包括设备的更新与淘汰计划。
需要指出的是,纯蒸汽发生器的标准制定应参考国家和地方的相关法规和标准。
同时,还应考虑到不同行业和应用领域的特殊要求。
例如,食品行业对纯蒸汽的要求要更为严格,应制定相应的食品级纯蒸汽发生器标准。
高压蒸汽发生器的热工设计和优化

高压蒸汽发生器的热工设计和优化高压蒸汽发生器是一种重要的热工设备,广泛应用于工业生产和能源领域。
它的主要功能是将水加热并转化为蒸汽,提供高温高压的蒸汽用于机械功、发电或化工生产等。
高压蒸汽发生器的热工设计和优化是保证其安全、高效、可靠运行的关键。
本文将探讨高压蒸汽发生器的热工设计和优化。
一、高压蒸汽发生器的基本原理高压蒸汽发生器是一种换热器,根据传热方式的不同分为直接加热式和间接加热式两种。
直接加热式高压蒸汽发生器是直接将燃烧产生的高温烟气或燃气与水混合,在内部燃烧室中进行热交换,将水加热并转化为蒸汽。
间接加热式高压蒸汽发生器则是通过热传导方式在高温壳体内传递热量,将水加热并转化为蒸汽。
无论是直接加热式还是间接加热式,高压蒸汽发生器的基本原理都是利用热量的传递,将水加热至沸点以上,在一定的压力下转化为高温高压的蒸汽。
二、高压蒸汽发生器的热工设计高压蒸汽发生器的热工设计是指利用热力学原理和换热原理,确定高压蒸汽发生器的结构参数、冷却面积、传热系数、热负荷等技术参数,以满足制定的工艺要求和性能指标。
高压蒸汽发生器的热工设计需要考虑以下几个方面:1. 蒸汽流量和温度高压蒸汽发生器的蒸汽流量和温度是设计的重要参数。
在实际的工作过程中,为了保证高效的能源利用和生产效率,高压蒸汽发生器的蒸汽输出需能够满足工艺要求,同时减少能源的浪费。
因此,在热工设计中需要根据实际需要和流量计算来确定高压蒸汽发生器的蒸汽流量和温度。
2. 冷却面积和传热系数高压蒸汽发生器内部的热交换面积和传热系数是影响换热效率的关键因素。
在热工设计中需要考虑内部流场、气体的流动和传热过程,进而优化高压蒸汽发生器的冷却面积和传热系数。
在设计时,需要选择合适的流体和材料,提高壁面传热系数,增加换热面积,以提高高压蒸汽发生器的效率。
3. 热负荷和质量流量在热工设计中需要考虑高压蒸汽发生器的热负荷和质量流量。
热负荷是指每单位时间内传递的热量,是高压蒸汽发生器设计时的重要技术参数。
核工程中的蒸汽发生器设计与优化

核工程中的蒸汽发生器设计与优化蒸汽发生器是核工程中一个非常重要的设备,它在核电站中起到将核能转化为电能的关键作用。
本文将介绍蒸汽发生器的设计原理、优化方法以及一些相关的挑战和问题。
蒸汽发生器的设计原理是基于热交换的原理。
在核电站中,核燃料通过核反应释放的热能被用来加热工质(通常是水)并产生蒸汽。
这个过程通过蒸汽发生器来实现,蒸汽发生器一般由大量的热交换管和壳体组成。
在设计蒸汽发生器时,有几个关键的因素需要考虑。
首先是热交换管的设计。
热交换管通常是由导热性能很好的材料,如不锈钢或铜合金制成。
在设计热交换管时,需要考虑到管内流体和管外流体的传热和流动特性,以及管道的强度和可靠性。
同时,还需要考虑如何提高热交换效率,以增加蒸汽产生的能力。
除了热交换管的设计,蒸汽发生器的壳体也是需要考虑的设计参数之一。
壳体应该具备足够的强度和稳定性,以承受高温和高压环境下的工作条件。
同时,还需要考虑如何优化壳体的换热效率,以提高蒸汽发生器的整体性能。
在蒸汽发生器的设计过程中,还需要考虑其他一些因素,如流体流动的压降、材料的选择、管道的布局等。
这些因素都会对蒸汽发生器的性能产生影响,并需要在设计过程中进行综合考虑和优化。
蒸汽发生器的优化方法可以从多个方面进行。
首先,可以优化热交换管和壳体的结构和材料,以提高传热效率和强度。
其次,可以通过改变流体流动方式和流速,以及改善管道的布局,来减小压降和提高换热效率。
此外,还可以采用先进的流体力学模拟和优化算法,来辅助设计和优化蒸汽发生器。
然而,蒸汽发生器设计和优化中也存在一些挑战和问题。
首先,由于核电站的特殊工作环境,蒸汽发生器需要具备较高的安全性和可靠性。
这就要求在设计和优化过程中考虑到各种可能的事故和故障情况,并采取相应的措施来防范和应对。
其次,蒸汽发生器设计和优化需要综合考虑多个因素,包括热力学特性、流体力学特性、材料力学特性等。
这就需要设计人员具备多学科的知识和技能,并进行综合的分析和优化。
蒸汽发生器设计、制造技术要求

蒸汽发生器设计、制造技术要求二○○八年一月目录1.设备功能2.安全分级、抗震类别和质保分级3.遵循导则、规范和标准4.设计技术要求5.结构描述6.主要材料和焊接材料7.供货和服务范围8.制造和验收要求9.包装、运输和贮存要求10.运行、维修要求1.设备功能蒸汽发生器为压水堆核电厂一、二回路之间的换热设备,来自反应堆冷却剂进入蒸汽发生器的一次侧,通过U形管将热量传给二次侧的介质,产生汽-水混合物,汽水混合物经过内置式汽水分离器分离成饱和蒸汽和水,经干燥器干燥后成为干饱和蒸汽(温度不超过5%)。
蒸汽从蒸汽出口管嘴流出驱动汽轮发电机组作功发电。
蒸汽发生器为高温高压的压力容器,蒸汽发生器的传热管作为一、二次侧介质的隔离屏障,其安全性和可靠性必须得到充分保证。
2.安全分级、抗震类别和质保分级3.遵循导则、规范和标准3.1管理导则NRC,RG1.26 核电站的含汽水-水,以及含放射性废物的部件的质量组分级和标准NRG,同RG1.29 有关地震的设计分类IAEA50-C/SG-Q(1996) 核电厂和其他核设施安全的质量保证HAF102 核电厂设计安全规定HAD103/01 核电厂运行限值和条件HAD103/07 核电厂在役检查3.2ASME和ASTM规范(2006年版)ASME规范第II卷材料技术条件第III卷第一册NB及附录E 核动力装置设备第V卷无损检测第IX卷焊接及钎焊评定第XI卷核动力装置设备在役检查规程ASTM规范:E185,E228,A262,A370,A508,A3883.3国家标准(最新版)GB/T:228, 229, 232, 699, 1804, 1954, 2649, 2650, 2651, 2652, 2653, 2654, 3280, 4237, 4334.5, 4338, 68034.设计技术要求4.1设计准则a. 蒸汽发生器的材料(包括母材,焊材,螺栓件及附件材料)的规格及质量应符合国内外有关标准要求。
供暖蒸汽发生器设计
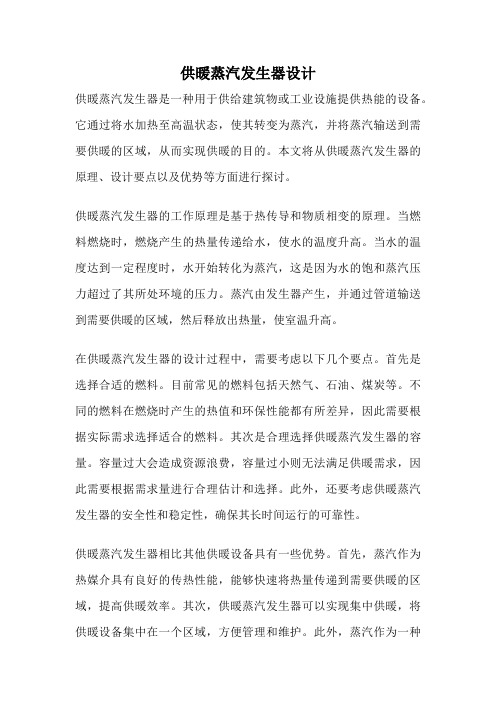
供暖蒸汽发生器设计供暖蒸汽发生器是一种用于供给建筑物或工业设施提供热能的设备。
它通过将水加热至高温状态,使其转变为蒸汽,并将蒸汽输送到需要供暖的区域,从而实现供暖的目的。
本文将从供暖蒸汽发生器的原理、设计要点以及优势等方面进行探讨。
供暖蒸汽发生器的工作原理是基于热传导和物质相变的原理。
当燃料燃烧时,燃烧产生的热量传递给水,使水的温度升高。
当水的温度达到一定程度时,水开始转化为蒸汽,这是因为水的饱和蒸汽压力超过了其所处环境的压力。
蒸汽由发生器产生,并通过管道输送到需要供暖的区域,然后释放出热量,使室温升高。
在供暖蒸汽发生器的设计过程中,需要考虑以下几个要点。
首先是选择合适的燃料。
目前常见的燃料包括天然气、石油、煤炭等。
不同的燃料在燃烧时产生的热值和环保性能都有所差异,因此需要根据实际需求选择适合的燃料。
其次是合理选择供暖蒸汽发生器的容量。
容量过大会造成资源浪费,容量过小则无法满足供暖需求,因此需要根据需求量进行合理估计和选择。
此外,还要考虑供暖蒸汽发生器的安全性和稳定性,确保其长时间运行的可靠性。
供暖蒸汽发生器相比其他供暖设备具有一些优势。
首先,蒸汽作为热媒介具有良好的传热性能,能够快速将热量传递到需要供暖的区域,提高供暖效率。
其次,供暖蒸汽发生器可以实现集中供暖,将供暖设备集中在一个区域,方便管理和维护。
此外,蒸汽作为一种无色、无味、无毒的气体,在使用过程中不会对室内空气质量产生污染,对人体健康无害。
供暖蒸汽发生器是一种高效、环保的供暖设备。
它通过将水加热转化为蒸汽,将热能输送到需要供暖的区域,实现供暖的目的。
在设计过程中,需要考虑燃料选择、容量估计以及安全性等因素。
相比其他供暖设备,供暖蒸汽发生器具有传热性能好、集中供暖、无污染等优势。
通过合理的设计和运行,供暖蒸汽发生器能够为人们提供温暖舒适的居住和工作环境。
节能型煮茧蒸汽发生器系统设计

节能型煮茧蒸汽发生器系统设计随着经济的高速发展和人们生活水平的提高,传统的蚕茧煮茧蒸汽发生器系统已经无法满足生产的需求。
传统的蒸汽发生器系统通常存在能源利用不充分、污染严重、安全隐患大等问题,不适合现代节能环保的要求。
为了适应新的形势,提高生产效率和质量,降低生产成本,保护环境,节能型煮茧蒸汽发生器系统应运而生。
一、系统工作流程节能型煮茧蒸汽发生器系统包括四个主要的部分,分别是原水处理部分、蒸汽发生部分、蒸汽供应部分和废气处理部分。
1. 原水处理部分原水需要进行脱盐和除铁处理。
脱盐是为了保证蒸汽的纯净度,避免因为水质问题导致的设备堵塞和腐蚀;除铁是为了防止水中的铁离子对设备造成损坏。
2. 蒸汽发生部分蒸汽发生部分是系统的核心部分。
系统采用了高效节能的蒸汽发生设备,根据生产需求和茧子的煮制特点,合理调配设备的数量和规格,提高蒸汽发生的效率。
在系统中还加入了能量回收装置,对废热进行回收利用,进一步提高节能效果。
蒸汽供应部分是将蒸汽输送到生产现场的部分。
系统采用了高效的输送管道和阀门,减少了能量的损耗,同时也对蒸汽进行了一定程度的除油和净化处理,保证蒸汽的纯净度。
在系统运行时会产生大量的废气,为了避免废气对环境的污染,系统中加入了废气处理设备,对废气进行脱硫、除尘和洁净处理,达到排放标准。
二、系统设计理念设计节能型煮茧蒸汽发生器系统的初衷是为了提高生产效率和质量,降低生产成本,保护环境。
在系统设计中,我们充分考虑了节能、环保、安全等因素。
1. 节能节能是系统设计的首要原则。
系统中采用了高效节能的蒸汽发生设备,并且在系统中加入了能量回收装置,充分利用废热,减少了能源的浪费。
系统中还采用了节能型输送管道和阀门,并对蒸汽进行了除油和净化处理,减少了能量的损耗。
2. 环保环保是当今社会发展的重要理念,系统在设计中充分考虑了环保因素。
原水处理部分对水质进行严格的处理,蒸汽发生部分和废气处理部分对废气进行了充分的处理和净化,保证了废气排放的环保标准,减少了对环境的污染。
纯蒸汽发生器设计方法

纯蒸汽发生器设计方法
纯蒸汽发生器是一种用于生产纯净蒸汽的设备,广泛应用于工业生产、实验室研究和其他领域。
设计一个高效的纯蒸汽发生器对于保证生产过程中的蒸汽质量和生产效率至关重要。
下面我们将介绍一些设计纯蒸汽发生器的方法。
首先,设计纯蒸汽发生器时需要考虑的是材料的选择。
优质的材料可以保证蒸汽发生器的稳定性和耐用性。
通常情况下,不锈钢是一种常用的材料,因为它具有优良的耐腐蚀性和耐高温性能。
此外,合适的密封材料也是设计中需要考虑的重要因素,以确保蒸汽不会泄漏。
其次,设计纯蒸汽发生器时需要考虑的是蒸汽的产生方式。
蒸汽可以通过不同的方式产生,如电加热、燃气加热等。
选择合适的蒸汽产生方式可以根据生产的需要和实际情况来确定。
同时,还需要考虑蒸汽的产生速度和温度控制,以确保蒸汽的质量和稳定性。
另外,设计纯蒸汽发生器时需要考虑的是蒸汽的净化和纯化。
蒸汽的纯度对于很多生产过程来说是至关重要的。
因此,设计中需要考虑加入适当的净化设备,如过滤器、蒸汽分离器等,以保证蒸汽的纯度和质量。
最后,设计纯蒸汽发生器时需要考虑的是设备的控制系统。
一个良好的控制系统可以实现蒸汽的稳定产生和温度的精确控制。
因此,在设计中需要考虑选择合适的控制器和传感器,以保证设备的稳定运行和蒸汽的高质量生产。
总的来说,设计纯蒸汽发生器需要考虑的因素很多,包括材料的选择、蒸汽的产生方式、蒸汽的净化和纯化,以及设备的控制系统等。
只有综合考虑这些因素,才能设计出一个高效稳定的纯蒸汽发生器,满足生产的需要和质量要求。
希望以上的介绍对您有所帮助,谢谢!。
蒸汽发生器设计

n
G1 1 1700 u1 a
-5-
a---单根传热管流通截面; 1 --一回路水平均比容
2.2.3 传热计算 一回路强迫对流换热系数:
1 0.023
传热管导热热阻:
1
di
R f 0.8 Pr 0.3 38057W / m2 ℃
P7 7
u2 2 2 15961Pa 2
蒸汽发生器一回路侧沿程和局部压降之和:
P Pf Pi 178460Pa
i 1
7
2.3.2 二回路侧阻力计算: 以循环倍率 CR 3 为例计算: 2.3.2.1 下降空间阻力 下降空间流道当量直径:
De Dsi Dw0 0.176m
1000Q C 1251.1m2 q
-6-
2.2.4 管束结构设计 传热管设计根数为 1705 根(除去半圆内的 6 根用黑点表示的拉杆) 。在圆形区 域中有 12 根为拉杆, 传热管和拉杆中心均位于图中小正方形的顶点上。 排管见 [附 录 4 程序 2][附录 4 程序 3] 半圆上每一排的根数(包括拉杆) : 67、67、67、67、67、67、67、65、65、65、63、63、61、61、61、59、57、 57、55、53、51、51、49、47、43、41、39、35、33、27、23、17、1
Re
u1' di
11
979120
u '1 —考虑堵管后的流速,通常为 1.05 u1
1 —平均壁温下的动力粘度
根据雷诺数选择紊流光滑管的尼古拉兹公式:
0.0032 0.221Re0.237 0.0117
沿程压降:
蒸汽发生器设计

蒸汽发生器设计为进一步提高生产能力和水解率、降低能耗、最大程度上增加公司效益,公司决定对水解工段进行大规模的技术改造,根据技改后的水解工艺技术参数要求,改造中需增加水解塔、蒸汽发生器等多台设备,现对增加的一台蒸汽发生器进行设计。
一、以已知的工艺参数测算水解蒸汽发生器的各种数据1、已知流量:W=3T/h,压力:P=3.0Mpa, 温度:t=233℃.2、根据已知饱和蒸汽压力、温度可查表知蒸汽流速u=20~40m/s ,密度ρ=15Kg/m3总传热系数K=24~370,K选300导热油在280℃,粘度﹤1cP时流速为1.5~3.5 m/s100℃的水蒸汽热焓值H=2256/4.2=537.62≈540大卡/kg 设备生产厂家提供的经验值:一吨蒸汽需要提供60万大卡热量。
3、测算蒸发器各数据水从25℃的液态转变成235℃,需经过三个过程的变化,需要热量Q水总=Q1 + Q2 + Q3Q1=3000х1х60=180000Q2=3000х540=1612860Q3=3000х1х135=405000Q水总=180000 + 1612860 + 405000=2197860≈2200000大卡(1)导热油列管换热面积Q=KA⊿tA=Q/K⊿t=2200000/300х30≈245 m2A=Q/K⊿t=2200000/300х25≈294 m2A=Q/K⊿t=2200000/300х20≈367 m2生产厂家计算换热面积的方式是:A=Q/K⊿t=1800000/300х30=200m2A=Q/K⊿t=1800000/300х25=240m2A=Q/K⊿t=1800000/300х20=300m2选择换热面积为300m2、列管管径选DN20(此总截面积要小于DN32和DN50)按照常规列管应设计成DN20х13000х2.5长U管。
(2)蒸汽总管直径W=D2∏u/4D12=4х200/3.14х30х3600=0.002359D1=0.0486mD22=4х200/3.14х25х3600=0.002831D2=0.05323设计蒸汽总管直径为DN65,经查表其壁厚为4mm,实际生产厂家通常把蒸汽总管管径选择与导热油输送管相近,直接与分汽缸相连,分汽缸向外输送的各支管可选择DN65或DN50 (3)导热油进出口管径流速 U选2.5 m/s,流量W选80~100m3/hD1=(4W1/3600∏u)0.5、=(4х80/3600х3.14х2.5)0.5=0.1064D2=(4W2/3600∏u)0.5=(4х100/3600х3.14х2.5)0.5=0.119 实际选导热油管直径为DN150,经查表其壁厚4m,蒸发器输汽管直径的选择也应在DN150。
节能型煮茧蒸汽发生器系统设计

节能型煮茧蒸汽发生器系统设计随着社会的发展和科技的进步,能源资源的问题越来越受到重视。
在这种背景下,节能型煮茧蒸汽发生器系统的设计成为了一个热门话题。
煮茧蒸汽发生器是丝绸生产过程中必不可少的设备之一,而设计节能型煮茧蒸汽发生器系统能够有效降低能源消耗,减少对环境的影响,提高生产效率和产品质量。
本文将针对节能型煮茧蒸汽发生器系统的设计进行详细介绍。
一、系统结构和原理1.系统结构节能型煮茧蒸汽发生器系统由煮茧蒸汽发生器、蒸汽输送系统、废气处理系统和控制系统组成。
煮茧蒸汽发生器是整个系统的核心部件,它通过燃烧介质(如天然气、柴油等)、加热介质(如电加热管)或其他方式产生高温高压蒸汽,用于煮茧工艺的实施。
蒸汽输送系统主要包括蒸汽管道、阀门、仪表等设备,用于将煮茧蒸汽发生器产生的蒸汽输送到煮茧设备中进行生产加工。
废气处理系统用于处理煮茧过程中产生的废气,减少对环境的污染,保护生态环境。
控制系统是整个系统的核心,它通过对煮茧蒸汽发生器系统的各个部件进行智能控制和调节,实现系统的节能、高效、稳定运行。
2.系统原理节能型煮茧蒸汽发生器系统的设计原理主要包括以下几点:(1)优化燃烧系统:通过对燃烧系统的优化设计,提高燃烧效率,减少能源浪费,降低排放物的产生。
(2)蒸汽回收利用:对煮茧蒸汽发生器产生的废热蒸汽进行回收利用,用于加热介质或其他生产工艺,实现能源的再利用。
(4)废气处理技术:采用先进的废气处理技术,对煮茧过程中产生的废气进行有效处理,达到排放标准,保护环境。
通过以上原理的设计和应用,可以实现节能型煮茧蒸汽发生器系统的高效运行,降低能源消耗,减少对环境的影响,提高生产效率和质量。
二、系统设计与实施1. 燃烧系统设计为了优化燃烧系统,降低能源消耗,提高燃烧效率,可以采用以下设计方案:(1)采用先进的燃烧技术,如燃气锅炉、电加热管等,以实现高效燃烧和能源的有效利用。
(3)采用先进的燃烧控制技术,对燃烧过程进行智能控制和调节,保证燃烧稳定、安全、高效。
- 1、下载文档前请自行甄别文档内容的完整性,平台不提供额外的编辑、内容补充、找答案等附加服务。
- 2、"仅部分预览"的文档,不可在线预览部分如存在完整性等问题,可反馈申请退款(可完整预览的文档不适用该条件!)。
- 3、如文档侵犯您的权益,请联系客服反馈,我们会尽快为您处理(人工客服工作时间:9:00-18:30)。
蒸汽发生器工艺设计目录第一章绪论............................................................................................................... 第二章蒸汽发生器的设计与计算...............................................................................2.1 根据热平衡确定换热量....................................................................................2.2 管径的选取以及传热管数目的确定................................................................2.3 换热面积的计算................................................................................................2.4 管束结构的计算................................................................................................2.5 强度计算............................................................................................................2.6 主要管道内径的计算........................................................................................2.7 一回路水阻力计算............................................................................................2.8 二回路水循环阻力计算....................................................................................2.9 运动压头计算....................................................................................................2.10 循环倍率的确定................................................................................................ 第三章结论与评价.......................................................................................................附录1 蒸汽发生器热力计算表附录2 蒸汽发生器水力计算表附录3 蒸汽发生器强度计算表第一章绪论蒸汽发生器是产生汽轮机所需蒸汽的换热设备。
在核反应堆中,核裂变产生的能量由冷却剂带出,通过蒸汽发生器将热量传递给二回路工质,使其产生具有一定温度一定压力和一定干度的蒸汽。
此蒸汽再进入汽轮机中做功,转换为电能或机械能。
在这个能量转换过程中,蒸汽发生器既是一回路的设备,又是二回路的设备,所以被称为一、二回路的枢纽。
蒸汽发生器作为一回路主设备,主要功能有:1、将一回路冷却剂的热量通过传热管传递给二回路给水,加热给水至沸腾,经过汽水分离后产生驱动汽轮机的干饱和蒸汽;2、作为一回路压力边界,承受一回路压力,并与一回路其他压力边界共同构成防止放射性裂变产物溢出的第三道安全屏障;3、在预期运行事件、设计基准事故工况以及过度工况下保证反应堆装置的可靠运行。
实际运行经验表明,蒸汽发生器能否安全、可靠的运行,对整个核动力装置的经济性和安全可靠性有着十分重要的影响。
据压水堆核电厂事故统计显示,蒸汽发生器在核电厂事故中居重要地位。
一些蒸汽发生器的可靠性是比较低的,它对核电厂的安全性、可靠性和经济效益有重大影响。
因此,各国都把研究与改进蒸汽发生器当做完善压水堆核电厂技术的重要环节,并制定了庞大的科研计划,主要包括蒸汽发生器热工水力分析;腐蚀理论与传热管材料的研制;无损探伤技术;振动、磨损、疲劳研究;改进结构设计,减少腐蚀化学物的浓缩;改进水质控制等。
第二章蒸汽发生器的设计与计算蒸汽发生器的设计计算包括热力计算、水动力计算、强度计算、结构设计等。
热力学计算主要通过传热学知识计算传热管传热面积,然后与管束结构设计相结合可以得到传热管长度、管束直径等结构参数。
强度计算通过压力校验等用于选取蒸汽发生器结构材料、确定结构尺寸等。
蒸汽发生器中要通过强度计算得出的参数有传热管、上下筒体、球形下封头管板等的壁厚。
在强度计算得出参数后要留取一定余量,以满足变工况下出现超压情况的需求。
水动力计算是最后一步,因为只有结构尺寸确定,运动状态已知的情况下水力情况才得以确定。
水力计算包括一回路水阻力计算、二回路水循环阻力计算、运动压头计算等。
其中一回路水阻力计算相对简单主要包括单相水U型管管内摩擦阻力和局部阻力两项;二回路水循环阻力计算及运动压头计算比较复杂。
因为蒸汽发生器内二回路侧流体的水力特性取决于流体工质的性质和状态、流道的结构和几何形态,以及工质的流动形式。
而且计算过程误差较大,往往需要在试验中进一步修正。
二回路水循环阻力包括下降空间阻力、上升空间阻力、汽水分离器阻力等。
而上升空间阻力又包括摩擦阻力、局部阻力、弯管区阻力、加速阻力、流量分配孔阻力五项。
设计中常用图解法来确定循环倍率,即先假设几个不同的循环倍率分别计算其运动压头和总阻力,在直角坐标系作出相应曲线,两根曲线交点即为稳定工况的循环倍率值。
循环倍率值一般取2~5为宜,其值过小会导致传热恶化,腐蚀加剧等;而过大则会增大汽水分离器负荷,使蒸汽干度降低,危机汽轮机安全。
计算过程中水力计算是在结构选型和热力计算之后进行,但是结构设计和热力计算又需要水力计算数据,因此三者往往要反复交替进行,以使设计逐步完善。
2.1根据热平衡确定换热量一回路进口焓值:'1i =1394.21 kj/kg (15.0MPa ,310℃);一回路出口焓值:''1i =1284.45 kj/kg (15.0MPa ,290℃);二回路给水焓:f i =944.38 kj/kg (5.0MPa ,220℃); 二回路饱和水温:s t =264 ℃ (5.0MPa );二回路饱和水焓:s i =1154.50kj/kg (5.0MPa ); 二回路饱和蒸汽焓值:''s i =2793.6 kj/kg (5.0MPa );二回路汽化潜热: r=''s i -s i =2793.6-1154.2=1639.73kj/kg (5.0MPa );排污量:0.01126 1.26/d s D C D kg s ==⨯=; 干度:x 0.01=;换热量:()()231278.98=++-=d s f Q Drx D D i i ; 一回路水流量: 1'''112128.40()η==-Qkg G si i ;η=0.99为蒸汽发生器的热效率。
2.2 管径的选取以及传热管数目的确定 选取传热管的外径为:430.8o t d mm ==;节距选取为:430.8o t d mm == ;则最小节圆半径为:min 261.6R t mm == ; 负公差修正系数:ϕ=1.102; 弯曲减薄系数:min1 1.0824oR d R ϕ=+=;一回路侧设计压:221,141.2515*1000000/9.8*10/191.3265/设-===P P kg cm kg cm 传热管壁厚:,111,11.34200[]0.8设设ϕφσ==+oR P d S mm P ,此处取1 1.5=S mm ;传热管内径:1219=-=i o d d S mm ;单管流通面积:222111928444ππ==⨯=i a d mm选取一回路侧水流速度为:1 5.0/u m s = 一回路水平均比容:310.001378/v m kg =(15.0MPa ,300℃,饱和水) 则一回路侧流通面积为:21110.5866m ==G v A uU 型管数目为:111/2128.40*0.001378/52069284====AG v u n a a 根据排管最后确定U 型管数目为:n=20862.3 换热面积的计算一回路侧水导热系数:10.5614/(℃)λ=⋅W m (15.0MPa ,300℃,饱和水) 一回路侧水普朗特数:Pr 0.8616=f (15.0MPa ,300℃,饱和水) 一回路侧水动力粘度:-518.83310kg/m s η=⨯ (15.0MPa ,300℃,饱和水) 一回路侧雷诺数:5111Re 7.810η==⨯if u d v 一回路侧换热系数:0.80.4110.023Re Pr 33128.72λα==f f id传热管导热系数:17.4/(℃)w W m λ=⋅ (给定) 传热管壁热阻:52ln 9.2710/2℃λ-==⨯⋅oow w id d R m W d污垢热阻:522.610/℃-=⨯⋅f R m W (按I-600选定) 传热温差: 'max 1''min 1max minln maxmin 31026446℃29026426℃462635℃46ln ln 26s s t t t t t t t t t t t ∆=-=-=∆=-=-=∆-∆-∆===∆∆121211q 5258假设一个值,进行迭代可以求得试取αα-⎛⎫=+++=⋅ ⎪⎝⎭ow f i d k R R W m K d 52ln 0.150.722 1.84610/0.55727357.7/()则此时的热负荷为:℃α=⋅∆=⨯==⋅s q k t W m p q W m 2ln 1252.80所需传热面积:==⋅∆QF m k t传热裕度系数:C=1.121378.08设设计传热面积:=⋅=F C F m2.4 管束结构的计算19939设总传热管总长:π==oF L m d传热管排列方式:按正方形排列 U 40.1232节最小型管节圆直径:==D t m 实际布管数:n=2086根D 2.34tb 管束直径:=mmax 1.17弯管段高为:=D mm 平均直径:0.5(0.1232 1.17)0.6466m =⨯+=D 弯管总长:0.54036.87弯π=⋅=L D n m 直管总长:199394036.8715902.13直总弯=-=-=L L L m 管束直段高: 3.82直直==L H m n管束弯段高:max 0.5 1.17弯==H D m管束总高: 4.98tb 直弯=+=H H H m2.5 强度计算12 2.38管束()衬筒内径:δ=+=wi t D D m 其中δt 是装配间隙,约10~20mm ,取20mm 。