VSM 价值流分析
VSM价值流图分析步骤

VSM价值流图分析步骤
VSM价值流图分析包括的主要步骤是:
1、了解并记录顾客的要求。
2、了解并画出工厂内材料流图。
如图中下部的线框所示,也是工厂内的基本生产过程。
将能够连续进行的过程列入一个框内,无法连续的则在两框之间用库存三角分开。
3、收集并记录每个生产过程的数据(数据框)。
在每个过程线框下记录的主要数据包括生产节拍、换型时间、操作人数、有效工作时间、设备使用率、废品率等与过程改进有关的数据。
注意,这些数据应是现场收集的,而不是某些资料记载的。
4、了解库存情况。
小组应对所有库存(包括线上在制品库存)进行盘点,然后记载库存于三角下面。
注意,是点数而非查账!
5、原材料采购和交付的情况。
如图中左上角所示,了解主要供应商的供货情况。
6、信息传递,画出信息流。
了解、记录顾客订货、生产计划、原材料订货过程的信息传递途经及信息,画出信息流,如图上部所示,标示出顾客订单、材料订单和生产信息传递途径和方法。
7、画出生产时间线和计算相关数据。
将库存数量按照顾客需求节拍转化为时间,与生产过程时间数据一同画在时间线上,求出生产过程时间占整个时间的百分比。
如何绘制VSM-价值流分析图
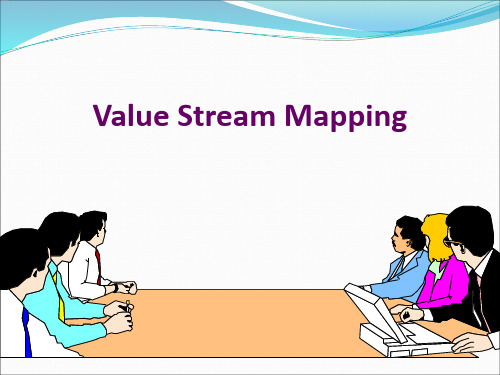
数据盒只记录实际需要的数据,不一定要记录 上面的全部信息
精益价值流的观念
➢ 第一个观念:遵循值流来重新架构组织
➢ 价值流的改造是一件大工程,它是各个职能的成 员组成的一个团队,并选出一个合适的Leader。 为了有效支持改造工作,管理方面的和实质的资 源必须步调一致,遵循价值流团队所设定的目标 ,各成员定期向负责人汇报进度。
TT = 60 sec.
Daily Ship Schedule
18,400 pcs/mo -12,000 “L” -6,400 “R” Tray = 20 pcs
2 Shifts
1x daily
I
Coils 5 days
Stamp 200 t
MCT = 1 second C/O = 1 hour REJ = 3% U/T = 85% 27,600 sec. avail. EPE = 2 weeks
精益价值流的观念
➢ 第六个观念:只对价值流中的一个制程发出生产 排程
➢ 价值流中的信息流(information flow)可以简化, 在精益价值流中接受生产排程命令的程序称为引 导程序(pacemaker process)。引导点必须排除值 流中其他程序的产能限制,来安排全部上游程序 的生产步调。选定引导程序是非常重要的。
27,600 sec. Avail.
I
1600 L 850 R
Sub-Assembly
1
OCT = 62 sec D/R = 62 sec C/O = 0 REJ = 6% U/T =100% 2 Shifts
500 ft coils
Tues & Thurs
6-week
1客. 户WfaFWx需eoerekhlc求yaastt时is 间Tak是MPCtRroT多Ponidmt少ureoc??ltion
VSM价值流分析PPT课件
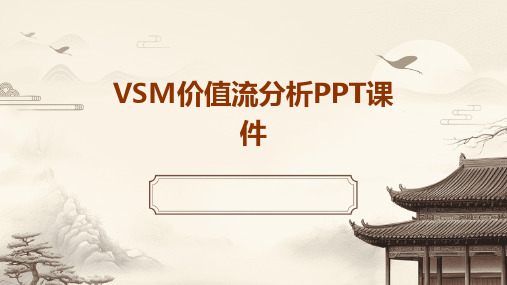
生产线平衡率计算
生产线平衡率 = 各工序时间总和 / ( 最长工序时间 * 工序数) * 100%。
提高设备利用率和员工工作效率,减 少在制品库存和等待时间,提高产品 质量和客户满意度。
生产线平衡方法
工序时间测定
通过秒表测时、预定时间标准等方法 ,准确测定各工序所需时间。
瓶颈工序识别
找出生产线上耗时最长的工序,即瓶 颈工序,进行重点改善。
02
收集数据
收集生产过程中的相关数据,如生产 周期、在制品数量、不良品率等。
01
03
绘制价值流图
使用标准的符号和工具绘制价值流图 ,包括流程图、数制定相应的改进计划, 包括优化生产布局、减少批量大小、 改进质量控制方法等。
05
04
分析浪费
在价值流图中标识出浪费的环节和原 因,如等待、运输、不良品等。
作业改善
通过作业分析、动作研究等方法,对 瓶颈工序进行作业改善,提高生产效 率。
生产线调整
根据改善后的工序时间,对生产线进 行调整,使各工序时间与节拍相等或 成整数倍关系。
改善措施制定
目标设定
原因分析
根据生产线平衡率和企业实际情况,设定 合理的改善目标。
针对生产线不平衡的原因进行深入分析, 找出根本原因。
收集生产过程中的相关 数据,通过统计分析识
别浪费现象。
员工参与法
鼓励员工积极参与,提 出生产过程中的浪费问
题和改进建议。
改善机会挖掘
01
02
03
04
消除浪费环节
针对识别出的浪费现象,制定 相应的改善措施,消除浪费环
节。
优化生产流程
通过改进生产工艺、调整设备 布局等方式,优化生产流程,
精益生产3VSM(价值流图及价值流分析

针对每个评估指标,制定相应的评估标准,明确达标的具体要求 和标准。
定期调整评估指标
随着企业生产和管理水平的提升,需要定期调整评估指标,以适 应新的发展需求。
绩效评估结果分析
数据收集与整理
收集与评估指标相关的数据,并进行整理、分类 和汇总。
结果分析
运用统计分析方法,对收集的数据进行分析,找 出存在的问题和不足之处。
降低成本
降低生产过程中的成本,包括原材料、 人力、设备等方面的成本。
缩短交货期
通过优化生产流程,缩短产品生产周期 和交货期,提高客户满意度。
流程优化方法
01
价值流分析
通过对生产流程中的价值流进 行分析,识别浪费和非增值活
动,并进行优化。
02
工艺流程再造
对现有的工艺流程进行重新设 计和优化,以提高生产效率和
现场观察
02
深入生产现场,仔细观察员工操作、设备运行、物料流动等实
际情况,发现浪费现象。
员工参与
03
鼓励员工积极参与浪费识别,利用他们对生产过程的了解,发
现潜在的浪费问题。
浪费消除策略
精益改善
通过精益工具和方法,对生产过程 进行持续改进,消除浪费,提高效
率。
自动化与智能化
引入自动化设备和智能化技术,减 少人工操作,降低浪费发生的可能
精益生产3VSM(价值流图及 价值流分析
目录
• 精益生产3VSM概述 • 价值流图绘制及分析 • 浪费识别与消除 • 流程优化与改善 • 绩效评估与持续改进 • 案例分析与应用实例
01
精益生产3VSM概述
精益生产3VSM定义
价值流图(Value Stream Mapping,VSM)是一种 可视化的工具,用于描述产品或服务从原材料到最终
VSM-价值流分析

绘制VSM 绘制未来图原则
1. 设计一个精益的价值流 a) 由绘制当前状态价值流图开始 b) 第一次绘制假定现有产品的设计、工艺技术与工厂位置不变 c) 未来状态必须持续的逐步发展成理想状态 d) 成为实施计划的基础--象一幅“蓝图” e) 总需要一个未来状态与一个实现此未来状态的计划
绘制VSM 绘制未来图步骤
降低MCT 降低DOH 提高FPY 提高生产率productivity
降低产成品库存 提高准时交付时间 降低发运时间 提高履行承诺比例
绘制VSM 项目列表
绘制VSM 绘制现状图
1
产品系列
2
绘制现状图
3
绘制未来状态图
4
实现未来状态
1.收集客户信息,产品数量 2. 沿着实物流走,构建过程框架 3.收集每个过程信息,填充数据盒 4. 描述货物是怎样送到客户手里的
5. 收集供货信息 6. 加上信息流
7. 画出过程之间的村料流图
8. 算出产品的Lead time and valueadded time.
绘制VSM 绘制现状图
1
产品系列
2
绘制现状图
3
绘制未来状态图
4
实现未来状况
绘制VSM 绘制现状图注意事项
1. 绘制注意事项 a) 如实描述现状是如何运作的 b) 包括物料流和信息流 c) 尽可能用图标绘制 d) 从“门到门”的价值流开始,从顾客开始倒着走 e) 必须从头到尾亲自走一遍流程并获得真实情况 f) 不依据想象的理想的状况 g) 用白板笔在大白纸上手工绘图 h) 随时记录有用的信息
Qty= 4/assy
Uptime= 85%
960 sec. avail.
I
2.5 EU
价值流程图-VSM

人员
VSM的图示 –其它
首先要选定你的产品,也就是研究的对象。为了操作的方便性,可以利用分组把产品分成产品家族。最佳的工具是使用产品家族矩阵。要建立产品家族矩阵之前,首先列出所有的产品在左编的栏位,并且在顶层列出加工流程步骤。找出共同的加工步骤,其中对应到不同的的产品可以分类成同一个家族。
产品
绘出现状图的7个步骤
使用铅笔、橡皮擦和便条纸绘制直接绘制在大白报纸上,避免使用电脑软体绘制可以使用下列颜色,使价值流图更容易阅读蓝色 –流程黄色 –存货或缓冲粉红色 – Master schedule / Production control主生产排成/生产控制单元绿色 –供应商及客户记得永远由客户开始绘制绘制完物流/流程步骤后,要留下空间画存货,图的下方还要留地方画各步骤的时间
价值图的改善
未来价值图
价值流图是一个团队改善活动,一个人绘制出来的价值流图通常是错的适合物料、讯息、生产的流程问题适合跨部门协调(多个部门之间的转接、协同合作有问题时)适合描述某一个具体的工作或办公区域,不适合描述复杂的工厂 ,如果太复杂,可以尝试切割流程,画在多张纸上不要尝试把所有东西都放在同一张纸上,记得80/20法则针对重点要解决的问题处理针对重要物料和办公管理过程绘制即可VSM不是万能的,但是VSM确实是一个能快速创造价值 的有力工具
加工流程
步骤一:辨识产品族
选定流程范围
跨公司
单个工厂(我们公司)
跨职能
过程层次
具体任务
通常由此开始
步骤二:绘出现状图
Customer
辨识产品及用户需求定义物料流定义物料处理流程及作业(从外部用户/客户内部供应商)第一次建议先画出从开始到结束的价值流加上资讯方块定义资讯流及作业,并加上资讯方块完成资料方块,并描述重要的活动状态定义库存点,并标注是(c)可控制或是(v)变动找出质量检核点及返修闭环,包括质量绩效、返修资源等给定前置作业时间,并了解时间变异的程度
2024版价值流程图VSM案例分析PPT课件

价值流程图VSM案例分析PPT课件目录•引言•案例分析:某制造企业生产流程优化•案例分析:某电商平台订单处理流程改进•案例分析:某医院患者就诊流程优化•总结与展望01引言提高生产效率降低成本提升产品质量目的和背景通过价值流程图VSM分析,识别生产过程中的浪费环节,优化生产流程,提高生产效率。
减少生产过程中的非增值活动,降低生产成本,提高企业竞争力。
通过价值流程图VSM分析,发现生产过程中的问题点,改进生产工艺,提升产品质量。
价值流程图VSM简介定义价值流程图VSM是一种可视化工具,用于描述产品或服务的整个价值流,包括从原材料到最终产品或服务的所有活动。
作用帮助企业识别生产过程中的浪费环节,优化生产流程,提高生产效率和质量。
适用范围适用于制造业、服务业等各个领域的企业。
02案例分析:某制造企业生产流程优化当前生产流程存在过多的环节和等待时间,导致生产效率低下。
生产流程繁琐资源浪费严重质量问题突出生产过程中的物料、人力和时间等资源未能得到充分利用,造成资源浪费。
产品质量不稳定,客户投诉率高,影响企业声誉和市场竞争力。
030201企业现状及问题分析深入企业生产现场,全面了解现有生产流程、设备、人员配置等情况。
流程调研收集生产过程中的关键数据,如生产周期、在制品数量、设备利用率等。
数据收集基于调研和收集的数据,绘制价值流程图VSM ,直观展示生产过程中的价值流动情况。
VSM 绘制价值流程图VSM 构建识别并消除生产过程中的浪费环节,如减少等待时间、降低库存等。
消除浪费优化生产流程,合并或取消不必要的环节,提高生产效率。
简化流程加强产品质量控制,采用先进的质量管理方法和技术手段,提高产品质量稳定性。
强化质量控制生产流程优化方案设计01020304生产效率提升资源利用率提高产品质量改善企业竞争力增强实施效果评估通过优化生产流程,提高生产效率,缩短生产周期。
充分利用物料、人力和时间等资源,降低生产成本。
通过生产流程优化,提高企业市场竞争力,实现可持续发展。
价值流分析2篇
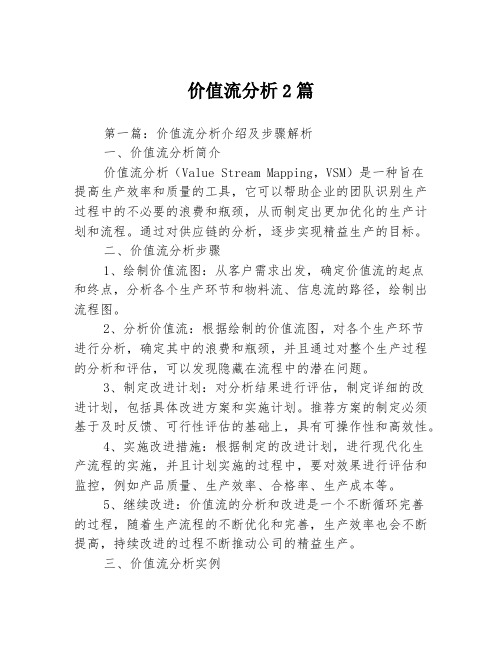
价值流分析2篇第一篇:价值流分析介绍及步骤解析一、价值流分析简介价值流分析(Value Stream Mapping,VSM)是一种旨在提高生产效率和质量的工具,它可以帮助企业的团队识别生产过程中的不必要的浪费和瓶颈,从而制定出更加优化的生产计划和流程。
通过对供应链的分析,逐步实现精益生产的目标。
二、价值流分析步骤1、绘制价值流图:从客户需求出发,确定价值流的起点和终点,分析各个生产环节和物料流、信息流的路径,绘制出流程图。
2、分析价值流:根据绘制的价值流图,对各个生产环节进行分析,确定其中的浪费和瓶颈,并且通过对整个生产过程的分析和评估,可以发现隐藏在流程中的潜在问题。
3、制定改进计划:对分析结果进行评估,制定详细的改进计划,包括具体改进方案和实施计划。
推荐方案的制定必须基于及时反馈、可行性评估的基础上,具有可操作性和高效性。
4、实施改进措施:根据制定的改进计划,进行现代化生产流程的实施,并且计划实施的过程中,要对效果进行评估和监控,例如产品质量、生产效率、合格率、生产成本等。
5、继续改进:价值流的分析和改进是一个不断循环完善的过程,随着生产流程的不断优化和完善,生产效率也会不断提高,持续改进的过程不断推动公司的精益生产。
三、价值流分析实例这里举一个钣金加工厂的实例:1、画出价值流图:钣金加工厂从接到订单开始,涉及到下单、物资采购、报价、图纸设计、钣金加工、质检、包装和出货等环节,将这些环节汇总到一张流程图中。
2、分析价值流:每个环节隐含了许多浪费和瓶颈,例如需要多次审批,长时间等待询价结果,因设计不适当拖延生产周期等。
通过分析,可以找到各个环节的突出问题,从而进行改进。
3、制定改进计划:根据评估结果,针对各环节,提高审批效率、缩短询价时间、优化设计以及提高加工效率等,制定改进方案。
4、实施改进措施:方案得到批准,计划推进改进措施,逐步向可持续化的精益生产方向靠拢。
5、继续改进:随着改进方案的寻常推进,了解生产效率的变化和产品质量的变化,继续完善,不断优化价值流程。
VSM价值流分析
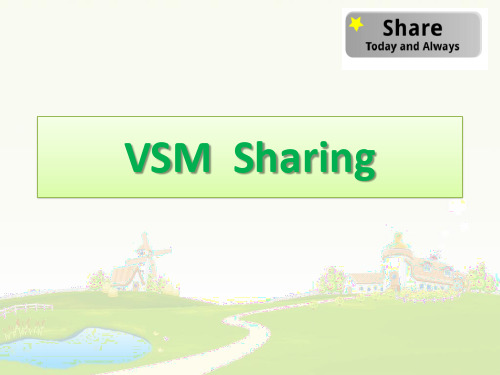
2.9 VAR
Value Added Ratio
Delivery time=VA time+NVA time (Total time for a whole process)
Example: Molding,welding,
assembling.
Essential,NVA
Have to be done in order to do the VA activities.
Example: Motions,handling.
Non-Value Added
Totally no use, must be eliminated.
PUSH Arrow
3.1 VSM icons
Information flow icon:
Manual Information
Flow
Electronic Information
Flow
Signal Kanban
Withdrawal Kanban
Production Kanban
General Icons:
Supermarket
Buffer or Safety Stock
300 pieces 1 Day
Inventory
Material Flow FG to Customer
max. 20 pieces
FIFO
First-In-First-Out Sequence Flow
Pull/Withdrawal
价值流分析-VSM

几项精益衡量尺度
L/T
C/T
周期时间(C/T) 增值时间(VAT)
生产周期(L/T)
价值流图的制图步骤
1
2
确定总装线体 及对应的产品 系列
绘制现状价值 流图、布局图、 山积图
3
绘制理想价值 流图、布局图、 山积图
4
工作计划并实 施(有优先次 序)
步骤1:选择总装线体及对应的产品系列 • W1、W2、W3…… • 110、190、260、350……
21.6H
C/T= 4 s 人数= 8
3s
5s
32s
2000
24H
日必要数=2000台
增值比=0.01%
L/T=122.4H VAT=40s
现状价值流图的第五视图
• 5. 绘制时间线
价值流增值比例
尽善 尽美
价值 浪费
Lean
价值 流图
拉动 生产
流动 生产
丰田汽车增值比例约为30%; 大多数企业增值比例不足2%; 我们不敢答应客户随时交货。
12000件/月左置
现状价值流图的第五视图
• 5. 绘制时间线
在图的最下方从左到右画出时间线,计算前置时间及周 期时间,其中: 上凸部分:表示前置时间,在库存图标正下方; 下凹部分:表示加工时间,在过程图标正下方。
前置时间 加工时间
前置时间 加工时间
前置时间(L/T)
增值时间 (VAT)
问题:前置时间和加工时间如何计算?
序号
生产区域
1 C/T
2 C/O时间及频率
3 操作人数
4 班数及每班时数
5 机器数量
6 可动率
7 OEE
8 直通率
9 L/B(平衡率)
VSM价值流图分析(常识)

VSM价值流图分析(常识)众所周知,VSM价值流图分析的用途十分广泛,它不仅是一种可以减少资源浪费的工具,还是一种沟通工具,也经常被用作战略工具和管理工具。
值得注意的是,在VSM价值流图分析的应用中,一些常识性问题,很多人都不知道。
如下:1. VSM价值流图分析只是辅助性工具,只有开展好基础性相关改善,价值流图才有意义这种基础性工作包括现场5S管理、消除浪费、快速换模、优化生产布局、TPM全员生产性维护等。
2. VSM价值流图分析的主要用途在于:摸不清当前状况的梳理;在现状图中找出改善机会;建立可对比的基准价值流图的优势在于全局性的统览。
当摸不清当前状况时,通过价值流图,可以从全局视角审视重点问题在哪里。
价值流图现状图中常常可以找出一定的改善机会进而开展改善。
价值流图现状图是某个时间切点的基准,新的时间切点的价值流图可与之前现状图进行对比,确认在全局场景下的进展或进步。
3. VSM价值流图分析主要阐明三类信息:①信息流;②物流;③时间数据信息流:客户、企业、供应商之间以及企业内部生产指令信息是如何交互的;物流:客户、企业、供应商以及企业内部的生产物流形式;时间数据:以时间为主体的各类信息,如切换时间、停滞时间、单件产品生产周期、人工数、可用生产时间等信息。
4. VSM价值流图分析明确倾向于单件流生产方式单件流生产方式确保了生产敏捷性与柔性化,这类生产方式对生产切换效率、生产线平衡率要求极高。
通常,单件流方式具有较好的响应度、敏捷性以及柔性化5. 没必要过多在意价值流图中的图标绘制现有的价值流图分析书籍规定了价值流图的图标,这些图标增加了价值流图绘制的复杂性,这些图标可以借鉴参考,但不是价值流图的重点。
通常,企业内部绘制价值流所用图标只要容易理解、不产生歧义即可。
价值流图分析
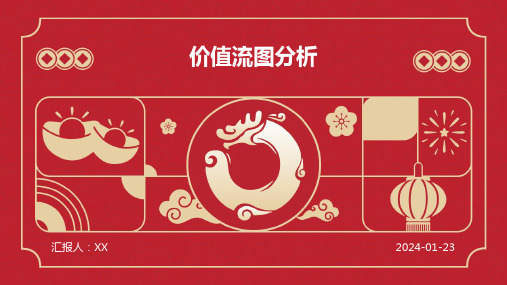
04 价值流图在流程优化中的应用
CHAPTER
识别浪费环节
识别非增值活动
通过价值流图分析,可以清晰地 识别出生产流程中的非增值活动 ,如等待、运输、库存等。
量化浪费程度
价值流图可以量化每个环节的浪 费程度,如时间、人力、物力等 资源的消耗,为后续优化提供依 据。
确定改进方向
通过对比行业最佳实践和内部标 杆,确定浪费环节的改进方向和 优先级。
02
在价值流图中标注出存在浪费的环节,如过多的库存、不必要
的运输、重复加工等。
对浪费环节进行深入分析,找出根本原因,为后续的优化提供
03
依据。
优化供应链流程
01
根据价值流图的分析结果,针 对浪费环节制定相应的优化措 施,如减少库存、优化运输路 线、提高生产效率等。
02
对供应链流程进行重新设计, 消除浪费环节,实现流程的优 化和再造。
价值流图分析
汇报人:XX
2024-01-23
目录
CONTENTS
• 价值流图概述 • 价值流图的核心概念 • 价值流图分析步骤 • 价值流图在流程优化中的应用 • 价值流图在供应链管理中的应用 • 价值流图在持续改进中的应用 • 总结与展望
01 价值流图概述
CHAPTER
定义与背景
价值流图(Value Stream Mapping ,VSM)是一种可视化的工具,用于 分析和优化产品或服务的整个价值流 。
促进跨部门协作
价值流图分析需要跨部门、跨职能的合作,有助于打破部门壁垒,加强内部沟通与合作 ,形成协同效应。
未来发展趋势和研究方向
数字化与智能化
随着信息技术的发展,未来价值流图分析将更加 注重数字化与智能化的应用,如利用大数据、人 工智能等技术提高分析的准确性和效率。
精益生产3.VSM价值流图及价值流分析课件
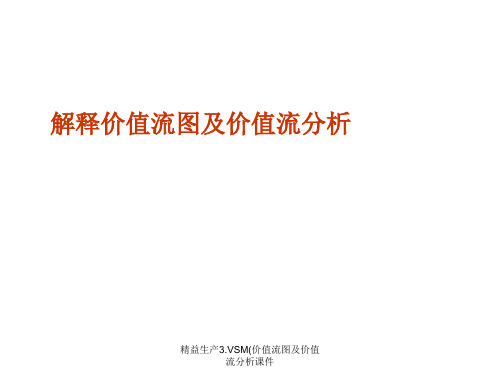
4天
统计数据
50秒 5分钟
LB=34天 T总=170秒
27600秒
99% 4天
50秒
二、什么是价值流分析
1、价值流分析的概念
价值流分析是建立在价值流图基础之上的有效分析 工具,它起源于丰田公司的材料及信息流图“,任何的 生产过程中均存在着材料流和信息流,价值流分析是从 为客户创造价值的视角,将我们的注意力倾注于建立流 动,消除非增值活动,快速增加价值的改进上去,并建 立起材料流和信息流的联系。借助价值流图的价值流分 析,是有效的”学会发现“的手段。
精益生产3.VSM(价值流图及价值 流分析课件
3、价值流图的目标
价值流图是一种强力的可视化工具,它的主要目 标是帮助我们确认运营流程中存在的潜在的,对客户 不增值的浪费活动,价值流图是任何企业展开流程分 析的有效工具,既可作为企业内部沟通的工具,也可 作为企业的战略规划工具,将企业流程所有相关的物 流,信息流和现金流以图示的方式加以表达,有利于 企业了解目标的经营现况和未来的经营现况。绘制一 副现有系统的
附
加
价 值
发布草案
产品X 产品A
月末结算 现金需求
销售报价
定单目录
返回材料需求
概念
原材料
产成品
现金
第0周
第52周
注:图中的APQP代表的含义是“质量先期计划”。
精益生产3.VSM(价值流图及价值 流分析课件
5、价值流图形的信息沟通
由于价值流图形直观地反映了某一产品系 列(价值流)的物资和信息的流动,因此,它 是对过程革新进行目视管理的一种必不可少的 工具。绘制一个过程的图形能够使你清楚地看 到阻碍流动的浪费现象。消除浪费现象能够使 生产的订货提前期缩短,这还会有助于你持续 不断地满足客户的需求。
VSM价值流图分析的作用
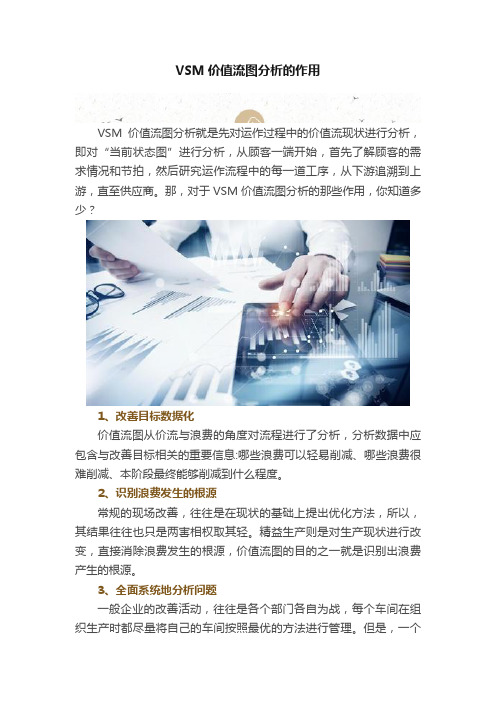
VSM价值流图分析的作用VSM价值流图分析就是先对运作过程中的价值流现状进行分析,即对“当前状态图”进行分析,从顾客一端开始,首先了解顾客的需求情况和节拍,然后研究运作流程中的每一道工序,从下游追溯到上游,直至供应商。
那,对于VSM价值流图分析的那些作用,你知道多少?1、改善目标数据化价值流图从价流与浪费的角度对流程进行了分析,分析数据中应包含与改善目标相关的重要信息:哪些浪费可以轻易削减、哪些浪费很难削减、本阶段最终能够削减到什么程度。
2、识别浪费发生的根源常规的现场改善,往往是在现状的基础上提出优化方法,所以,其结果往往也只是两害相权取其轻。
精益生产则是对生产现状进行改变,直接消除浪费发生的根源,价值流图的目的之一就是识别出浪费产生的根源。
3、全面系统地分析问题一般企业的改善活动,往往是各个部门各自为战,每个车间在组织生产时都尽量将自己的车间按照最优的方法进行管理。
但是,一个车间最优并不代表整体最优。
因此,就需要从整体角度对工人进行分析,提出整体最优的解决方案。
4、确定改善的优先次序价仇流图能够清晰地揭示出物料在哪些邵门,以及哪些工序停滞时间长、那些周期最长的部门就要优先改善,这样就可以避免员工只挑容易的部门进行改善的问题,从而明确改善的优先次序。
5、通过柔性计划生产降低库存精益生产的重要指标之一就是减少库存。
库存一般都是按照计划生产出来的,因此,要想减少库存,就必须要从生产计划入手。
6、建立广泛的沟通平台精益生产是一件跨部门的改善工程,需要各部门的配合。
价值流图要使用大家都能明白的符号,以揭示各个部门的情况以及彼此之间的关系,这样一来,各部门在进行跨部门之间的改善时就有了一个沟通的平台。
价值流程图(VSM)案例分析

第一章
价值流概念
价值流程图
价值流程图案例分析
主要内容
价值流是制造产品所需一切活动的总和,包含了增值活动和不增值活动。 使用价值流分析意味着对全过程进行研究,而不只是研究单个过程;改进全过程,而不是仅仅优化局部。 据统计,增值活动约占企业生产和经营活动的5%,不增值活动约占95%。因此,应在价值流中识别不增值活动,通过持续不断地开展价值流改进,消除各种浪费,降低成本。 价值流改进重点在于物流和信息流。
01
同时,可以考虑采用流水线生产和拉式生产相结合的生产和管理方式。因为这样不仅有利于减少在制品库存,缩短提前期,也非常有利于对装配工位需求的响应。此外,由于定拍工序粗车节拍为60s,采取拉式生产有利于为减少生产过多过早的浪费。
02
改进方案设想
未来价值流程图
需要注意的是,由于钻孔、精车抛光、检验三道工序是2个人在U形生产线中完成的,如采用逐兔式完成,因此每人115s完成三道工序的生产即115s共完成两个工件的加工,同时粗车工人120s完成两个毛坯加工,因此相当于U形生产线中57.5s完成一个零件的加工。因此,图3-2中后面三道工序的加工周期标注57.5s。
1
粗车
1
精车、抛光
1
物料流
有价值
无价值
VSM分析的对象
价值流程图分析以客户的观点分析现有价值流程图每一个活动的必要性,画出期待的价值流的未来状态图,并制定实施计划。 绘制出并简单显示出物流和信息流 揭示产生浪费的原因 创建一个改善的价值流 创建和协调一个跨部门团队方法
价值流程图分析特征
价值流程图分析的好处
01
同时,我可以看出,依照新的方案安排生产,生产提前期可减小到0.5天,比原来减少了66.67%((1.5-0.5)/1.5x100%)。同时可实现流水线下的拉式生产,在制品库存也可明显减少,对装配车间的需求响应将更加的迅速准确。此外生产线平衡率大大提高
VSM 价值流分析精品课件(一)

VSM 价值流分析精品课件(一)介绍VSM(Value Stream Mapping)被认为是现代精益生产的核心方法。
它是指一种精益工具,可以用来帮助企业识别并消除流程中的浪费。
对于企业来说,VSM有助于有效降低成本,提升生产效率,并增强市场竞争力。
而VSM 价值流分析精品课件,就是一种学习这一技术的重要工具。
一、课件的设计VSM 价值流分析精品课件是经过多年的实践基础上开发的。
这套课件通过完整系统的设计,帮助学员快速而全面地掌握VSM的理论、工具和技能。
VSM 价值流分析精品课件的设计理念是贯穿于整套课程之中的,为学员提供更加详尽的理论知识,同时又与实际案例密切结合,帮助学员能够快速掌握VSM工具的应用方法。
二、课程内容VSM 价值流分析精品课件的内容丰富,涵盖了诸多方面的知识点,其中包括了VSM概述、VSM分析工具、VSM流程图等重要内容,还介绍了如何有效地消除浪费,提升生产效率的方法等。
作为一个领域的专家,我们注重培养学员的实际操作能力,因而课程涵盖了实际应用的案例分析与模拟练习,更注重传授学员如何应用知识解决实际问题。
三、课程优势VSM 价值流分析精品课件具有多项优势:1.概念清晰,理论详细,内容全面。
能够全面而深入地讲解VSM的各种工具、方法及应用。
2.课程设置独特、内容生动,受众广泛。
适合任何想要了解VSM技术及工具优化的人群,无论是企业管理层还是从事生产制造的一线工作者均能从中受益。
3.课程重点突出,实战性强。
通过实际项目的案例分析、模拟实战,能够让学员更好地理解和掌握VSM分析工具的使用,增强实战能力。
4.课程售后服务完善。
售后服务方面能够及时回馈学员的疑问和解答问题,保障学员的学习效果。
结论VSM 价值流分析精品课件是一套有助于企业完成自我转型的重要培训课件,对于提高生产效率、降低成本具有非常重要的意义。
通过学习这套课程,企业管理层和员工都能够更好地掌握VSM工具和方法,更好地提升自身实际操作能力。
- 1、下载文档前请自行甄别文档内容的完整性,平台不提供额外的编辑、内容补充、找答案等附加服务。
- 2、"仅部分预览"的文档,不可在线预览部分如存在完整性等问题,可反馈申请退款(可完整预览的文档不适用该条件!)。
- 3、如文档侵犯您的权益,请联系客服反馈,我们会尽快为您处理(人工客服工作时间:9:00-18:30)。
James Tian 田文璋
Nov, 2007
精工咨询 James Tian 田文璋
Seven Components of the Lean产Enterprise 精益范围
VALUE STREAM MANAGEMENT 价值流管理
1000
4:6比率线 B组 3:7比率线 (70-95%) 2:8比率线
0
P25 P23
P1
P3
P5
精工咨询 James Tian 田文璋
P7
P9
P11
P15 P13
P17
P21 P19
P27
P29
P31
价值流管理: VSM 8步曲 (VSM:Value Stream Management)
– 指标的评估 – 设定未来目标
精工咨询 James Tian 田文璋
价值流管理: VSM 8步曲 (VSM:Value Stream Management)
• 第6步: 未来价值流图的绘制; 客户需求阶段 – 理解并必须满足客户需求:品质/交期/价格,具体精益工具为:
精工咨询 James Tian 田文璋
价值流管理: VSM 8步曲 (VSM:Value Stream Management)
• 第2步: 选择价值流 – 只选择一个产品或一个产品簇! – 选择价值流的标准:
• 客户需求(客户已经定义产品簇) • 共用的制程/过程 (产品路径分析法) • 高的价值或较大批量(PQ 分析法)
“Seeing the Whole Process – Order to Cash”
SUPPLY CHAIN EXECUTION 供应链管理
“Reliable Flow of Materials”
LEAN BUSINESS PROCESSES 精益商业过程
“Fast, Error-free Transaction Flow” 快速反应, 零误差交易流
DEMAND MANAGEMENT 需求管理
“Consistent Flow of Orders”
SIX SIGMA
“Eliminating / Managing Variation in Manufacturing and Business Processes” 消除 / 管理在制造过程中的误差
LEAN MANUFACTURING 精益制造
“Fast, Waste-Free Manufacturing Cycle Time” 快速反应,零浪费,缩短制造周期
FOUNDATION ELEMENTS 基本改善
5S+2, Employee Engagement, Problem Solving, Project Management 7S, 全员参与, 问题解决, 项目管理
Current State 当前状态
数据采集 -基准度量标准 -产品/工艺 -批量/混线生产 -流程图 -工作内容
Project Management and Execution 项目管理与执行
平衡生产线设计、培训 Action Plan 行动计划 拉式进度安排;看板 精益商业流程设计 其他工具和培训(如有需要) -品质改进 -预防性维护 -减少作业准备 -改善 -差错预防 -6&工具 Continual Improvement 持续改进
• 第3步: 学习Lean (The fundamentals of Lean: 精益基础) – 改善和计划前学习和正确理解和掌握Lean的相应知识! – 精益基础应具备以下内容/条件: • 合理制订并产生一个精益推行计划(每个组织可能都不同!) • 培训计划 (VSM项目成员在启动项目前掌握必要的精益概念和知识) • 降低成本的原理与方法 (客户成本的压力与VSM成本空间的识别) • 七大浪费的减少 • TPS的两大支柱: JIT 和 Jidoka (Autonomation,不完全等于Automation.三种功能:a.将人与机器的工作 分开; b.开发防呆装置 c.应用Jidoka来组装: 顺畅无不良flow) • 5S系统 • 应用的三大阶段(DemandFlowLeveling) 其通用的原理/目的是3S (Stabilize & Standardize your process / Simplify through Kaizen after 2S) • 目视管理 • 全员参与(No-blame/Team work/Vision/Communication/CI/Ownership)
精工咨询 James Tian 田文璋
价值流管理 (VSM:Value Stream Management)
• VSM不是:
– – – – 形成改善小组和等候结果 形成我行我素的工作小组和等候结果 仅仅计划你的物流和信息流 仅仅有负责的精益协调员来推行改善
记住:VSM不是告诉人们怎样做好他们工作的一种方法; 它是一种系统的路径,通过它使人们计划他们的工作 以更好的满足客户的需求
精工咨询 James Tian 田文璋
价值流管理: VSM 8步曲 (VSM:Value Stream Management)
• 第5步: 识别 Lean指标---目的:帮助推动持续改善和消除浪费 – 根据手中的当前VSM和必要信息制订当前的Lean指标
• • • • • • • • • 各阶段的WIP C/T L/T OTD OEE DPPM First pass yield Safety / Health ……
七大模块八大步
精工咨询 James Tian 田文璋
价值流管理 (VSM:Value Stream Management)
• 历史:在美国代表创新,是源自日本的一种计划方法。 • 定义:它是从TPS演变来的8步综合工具和技术方法,是一套完 整的计划系统。 • 作用:使你容易计划精益活动,以获得更大程度上的成功和 应用速度,是管理层(指标和报告)与执行层(精益工具应 用)的有机联接! • 关键点:
客户需求
连续流动 平衡(适物/时/量) 你的未来Lean历程!
精工咨询 James Tian 田文璋
价值流管理: VSM 8步曲 (VSM:Value Stream Management)
• 第1步: Lean的承诺----------------------管理层的角色 – 到现场去了解问题/需求… – 每一类产品簇指定一个VS价值流冠军/项目经理/组长 – 配置/提供必要的相应团队资源 – 使小组所有成员明确远景和目标 – 主导启动VSM项目(Kick off) – 评审所有的改善提案
精工咨询 James Tian 田文璋
两种VSM !
• 价值流管理(VSM:Value Stream Management)
• 价值流图(VSM:Value stream Mapping)
精工咨询 James Tian 田文璋
www.ue Stream Management):
精工咨询 James Tian 田文璋
价值流管理 (VSM:Value Stream Management)
七大模块
模块1: 启动 模块2: Lean的基础 模块3: 识别当前状态
VSM 8步曲
第1步: Lean的承诺 第2步: 选择价值流 第3步: 学习Lean 第4步: 当前价值流图绘制; 第5步: 识别 Lean指标
– 小组所有成员将针对选定的产品簇, 开展消除浪费和改进全 过程的物流和信息流活动
精工咨询 James Tian 田文璋
(P-Q)产品-数量分析图
产品P
2000 A组 (70%) 120% 100% 80% 60% 40% 500 C组 (95-99%)20%
1500
• Takt time / Pitch / Takt image / Buffer and safety inventories / FG supermarket
细节/备注
价值流管理的介绍 Lean的基础 当前状态
模块4: 未来状态的绘制; 客户需求阶段
模块5: 未来状态的绘制; 连续流动阶段 模块6: 未来状态的绘制; 平衡(适物/时/量)阶段 模块7: Kaizen改善计划
第6步: 未来价值流图的绘制; 客户需求阶段
第6步: 未来价值流图的绘制; 连续流动阶段 第6步: 未来价值流图的绘制; 平衡(适物/时/量)阶段 第7步: 定义Kaizen改善计划 第8 步: 执行Kaizen改善计划
精工咨询 James Tian 田文璋
目录
• 两种VSM! [区分价值流管理(VSM:Value Stream Management) 与价值流图(VSM:Value stream Mapping)] • 价值流管理(VSM:Value Stream Management) • 价值流图管理(VSM:Value stream Mapping) • 当前情况的分析(Analyzing the Current State)
Organizational Education 内部组织培训
ValueStream Mapping 价值流图
Future State(未来状态) Target Design 设计目标流程
• Employee Involvement Culture(全民参与的文化) Foundations(基础):• 7S - Workplace Organization(7s-整理工作场所) • Structured Problem Solving(系统化的解决问题方案)
– – – – – 将精益实施人、精益工具、指标、和报告要求连接在一起 保证精益推行的可持续性 每个人能够正确的理解精益! 过程能被有效控制 产生一套实际有效的推行计划