高精度零件尺寸控制
精密注塑件尺寸精度的解决方案

精密注塑件尺寸精度的解决方案一、背景介绍精密注塑件是一种在制造业中广泛应用的零部件,其尺寸精度对产品的质量和性能有着重要影响。
然而,在注塑件生产过程中,由于材料、模具、注塑机等因素的影响,注塑件的尺寸精度可能存在一定的偏差。
因此,为了解决精密注塑件尺寸精度的问题,我们需要采取相应的解决方案。
二、解决方案1. 优化模具设计模具是注塑件生产过程中最关键的因素之一。
通过优化模具设计,可以提高注塑件的尺寸精度。
具体措施包括:- 选择高精度的模具材料,如优质钢材,以确保模具的稳定性和耐磨性。
- 设计合理的模具结构,避免尺寸变形和偏差的产生。
- 采用先进的模具加工技术,如数控加工,以提高模具的加工精度和表面质量。
2. 优化注塑工艺参数注塑工艺参数的选择和调整对注塑件的尺寸精度有着重要影响。
以下是一些优化注塑工艺参数的建议:- 控制注塑机的注射速度和压力,以确保注塑料充填均匀,避免尺寸不一致。
- 控制注塑机的冷却时间和温度,以确保注塑件的收缩率和尺寸稳定性。
- 选择合适的熔融温度和保压时间,以确保注塑料的流动性和成型质量。
3. 引入精密测量设备精密测量设备可以帮助我们准确测量注塑件的尺寸,及时发现和纠正尺寸偏差。
以下是一些常用的精密测量设备:- 三坐标测量机:可以实现对注塑件各个尺寸的精确测量和比对。
- 光学投影仪:可以对注塑件的平面尺寸和轮廓进行快速测量。
- 厚度测量仪:可以测量注塑件的厚度,判断是否符合要求。
4. 严格质量控制和检验在注塑件生产过程中,严格的质量控制和检验是确保尺寸精度的关键。
以下是一些常用的质量控制和检验措施:- 制定严格的质量标准和工艺规范,确保每个环节都符合要求。
- 进行过程监控和数据分析,及时发现和纠正质量问题。
- 进行全面的尺寸检验,包括外观检查、尺寸测量等,确保注塑件的质量和尺寸精度。
三、案例分析以汽车零部件为例,通过采取上述解决方案,成功解决了精密注塑件尺寸精度的问题。
经过优化模具设计,采用高精度的模具材料和先进的模具加工技术,注塑件的尺寸稳定性得到了显著提高。
高精度航空航天关键机械零部件 加工参数

高精度航空航天关键机械零部件加工参数1. 引言随着科学技术的不断发展,航空航天领域对于高精度机械零部件的需求越来越高。
这些机械零部件的加工过程需要严格控制各项参数,以确保其具备精确度、可靠性和稳定性。
本文将探讨高精度航空航天关键机械零部件的加工参数及其重要性。
2. 加工参数的定义在航空航天领域中,加工参数是指在加工过程中需要控制和调整的一系列关键参数,包括切削速度、进给速度、切削深度、切削力等。
这些参数的选择和控制直接影响着零部件的加工质量和性能。
2.1 切削速度切削速度是指刀具切削金属材料的速度。
在机械零部件的加工过程中,切削速度的选择应根据材料的种类、刀具的类型和工作环境等因素综合考虑。
切削速度过高会导致刀具磨损加剧,切削速度过低则会降低加工效率。
2.2 进给速度进给速度是指工件在刀具切削下的移动速度。
进给速度的选择应根据切削力和切削深度等参数来确定,以保证加工过程中的稳定性和精度。
进给速度过高会导致加工表面质量下降,进给速度过低则会影响加工效率。
2.3 切削深度切削深度是指切削刀具切入工件的深度。
切削深度的选择应根据工件的材料和几何形状来确定,以确保加工过程中的稳定性和切削力的控制。
切削深度过大容易导致刀具振动和加工表面质量下降,切削深度过小则会影响加工效率。
2.4 切削力切削力是刀具在切削过程中对工件的力作用。
切削力的大小直接影响加工过程的稳定性和零部件的加工质量。
合理控制切削力可以减小刀具磨损、降低加工振动和提高加工精度。
3. 加工参数的影响因素高精度航空航天关键机械零部件的加工参数受多个因素的影响,包括材料的性质、刀具的设计和加工设备的稳定性等。
3.1 材料的性质材料的硬度、韧性、热导率等性质会直接影响切削过程中的切削力和切削温度。
不同材料需要采用不同的加工参数才能保证零部件的性能和质量。
3.2 刀具的设计刀具的几何形状、材料和涂层等都会对加工参数的选择和控制产生影响。
优化设计的刀具能够提高切削效率、降低切削力和改善加工表面质量。
数控车床加工过程中尺寸精度的控制[权威资料]
![数控车床加工过程中尺寸精度的控制[权威资料]](https://img.taocdn.com/s3/m/1f6ac9b6b1717fd5360cba1aa8114431b90d8efd.png)
数控车床加工过程中尺寸精度的控制摘要:本文围绕、弹性变形、精加工及刀具等要素对加工产生的影响,论述了如何保证加工零件的尺寸精度的方法。
关键词:加工误差;弹性形变;弹性恢复;二次精加工尺寸精度是指加工后的工件尺寸和图纸尺寸要求相符合的程度。
两者不相符合的程度通常是用误差大小来衡量。
误差包括加工误差、安装误差和定位误差。
其中,后两种误差是与工件和刀具的定位、安装有关,和加工本身无关。
要提高加工精度减小加工误差,首先要选择高精度的机床,保证工件和刀具的安装定位精度,其次主要与数控车床加工工艺有关。
工艺系统中的各组成部分,包括机床、刀具、夹具的制造误差、安装误差、使用中的磨损都直接影响工件的加工精度。
也就是说,在加工过程中工艺系统会产生各种误差,从而改变刀具和工件在切削运动过程中的相互位置关系而影响零件的加工精度。
这些误差与工艺系统本身的结构状态和切削过程有关,产生加工误差的主要因素有:1 加工原理误差加工原理误差是由于采用了近似的加工运动方式或者近似的刀具轮廓而产生的误差,因在加工原理上存在误差,故称加工原理误差。
只要原理误差在允许范围内,这种加工方式仍是可行的。
2 机床的几何误差机床的制造误差、安装误差以及使用中的磨损,都直接影响工件的加工精度。
其中主要是机床主轴回转运动、机床导轨直线运动和机床传动链的误差。
3 刀具的制造误差及弹性变形我们很多人都有这样的经历,就是在前一刀车削了几毫米切深以后,发现离想要的尺寸还差几丝或者十几丝时,再按计划进行下一刀切削时,发现多切了很多,尺寸可能超差了。
那么这样的情况我们认真分析过其中的原因吗?有人说,这可能是因为机床间隙比较大所致,而在同一进刀方向上是不会受间隙影响的,其真正原因就是弹性形变和弹性恢复。
弹性形变表现在刀具、机床丝杠副、刀架、加工零件本身等对象的形变,使刀具相对工件出现后退,阻力减小时形变恢复又会出现过切,使工件报废。
产生形变的最终原因是这些对象的强度不足和切削力太大。
Kocks轧机高精度尺寸的控制
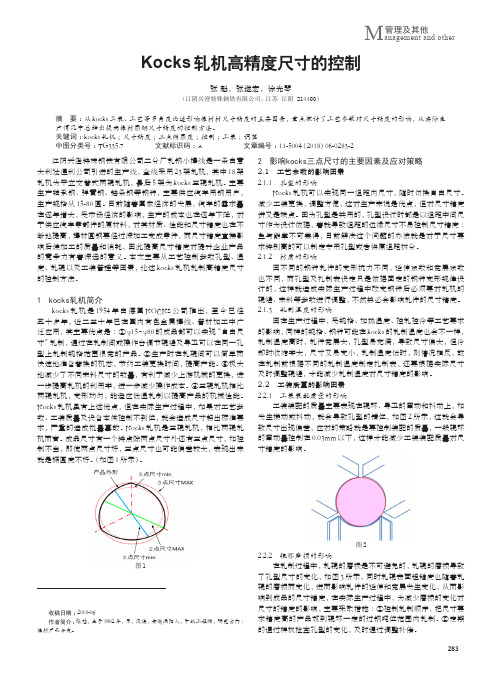
因 此 要 保 证 最 终 产 品 尺 寸 达 到 理 想 目 标,入 口 尺 寸 也 要 控 制 在 合 适 的 范 围,一 般 如 果 最 终 成 品 尺 寸 要 求 达 到 1/5~1/6DIN, 那么来料只要控制在 1/4DIN。
工装装配的质量主要表现在辊环、导卫的窜动和抖动上,如 发生攒动或抖动,就会导致孔型的错位,如图 2 所示,这就会导 致尺寸出现偏差,应对的策略就是要控制装配的质量,一般辊环 的窜动量控制在 0.03mm 以下,这样才能减少工装装配质量对尺 寸精度的影响。
图1
收稿日期 :2018-06 作者简介 :张魁,生于 1982 年,男,汉族,安徽涡阳人,中级工程师,研究方向 : 棒材产品开发。
关键词 :kocks 轧机 ;尺寸精度 ;三点椭圆度 ;控制 ;工装 ;调整
中图分类号 :TG335.7
文献标识码 :A
文章编号 :11-5004(2018)06-0283-2
江阴兴澄特殊钢铁有限公司二分厂轧钢小棒线是一条由意 大利达涅利公司引进的生产线,全线采用 23 架轧机,其中 18 架 轧机为平立交替式两辊轧机,最后 5 架为 kocks 三辊轧机。主要 生产轴承钢、弹簧钢、链条钢等钢种,主要供应汽车用钢用户, 生产规格从 15-80 圆。目前随着国家经济的发展,汽车的需求量 在逐年增大,受市场经济的影响,生产的成本也在逐年下降,对 于供应汽车零部件的原材料,对其材质、性能和尺寸精度也在不 断地提高,棒材圆钢要经过深加工变成零件,而尺寸精度直接影 响后续加工的质量和消耗,因此提高尺寸精度对提升企业产品 的竞争力有着深远的意义。本文主要从工艺控制参数孔型、温 度、轧辊以及工装管理等因素,论述 kocks 轧机轧制高精度尺寸 的控制方法。
极限量规的通规用来控制工件的什么作用尺寸

极限量规是一种用来控制工件尺寸的精密测量工具。
它可以通过对工件进行精确的测量和比较,确保工件的尺寸在设计要求的范围内,从而保证产品质量。
极限量规主要用于测量工件的外径、内径、长度和平行度等尺寸。
极限量规的通规是指用来对工件的直径、厚度和长度进行测量和控制的极限量规。
在工程制造过程中,保证工件的尺寸精度和一致性是非常重要的。
工件的尺寸不符合要求会导致产品质量不合格,甚至影响产品的功能和使用寿命。
使用极限量规的通规来控制工件尺寸是非常必要的。
极限量规的通规通过固定的测量标准,可以对工件的尺寸进行精确的测量和比较。
它可以帮助操作人员快速、准确地判断工件的尺寸是否符合要求,从而及时调整生产工艺,确保产品质量。
极限量规的通规通常由两个固定的测量标准和一个可调节的游标组成。
操作人员通过移动游标来对工件的尺寸进行测量,当游标与工件表面接触时,即可读取工件的尺寸。
通规的测量精度通常在0.01毫米以内,非常适合对精密工件进行测量和控制。
极限量规的通规在工业生产中被广泛应用,特别是在汽车、航空航天和机械制造等行业。
它不仅可以用来对成品进行质量检测,还可以用来对生产过程中的中间工件进行尺寸控制,确保整个生产过程的尺寸一致性。
在使用极限量规的通规时,操作人员需要注意以下几点:1. 定期校准通规,确保测量精度和稳定性。
2. 在测量前清洁工件表面和通规的测量标准,防止杂质影响测量结果。
3. 轻柔地操作通规,避免损坏测量标准和游标。
4. 保持通规的存放环境清洁干燥,避免受潮和污染。
5. 根据工件的形状和尺寸选择合适的通规进行测量,避免误差。
在工业制造领域,尺寸控制是非常重要的一环,而极限量规的通规作为一种精密的测量工具,为工件尺寸的控制提供了可靠的保障。
它的精准度和稳定性使其成为工业生产中不可或缺的工具,为产品质量的提升和工艺优化提供了有力支持。
通过正确使用和维护通规,可以延长其使用寿命,保证其持续的测量精度和可靠性。
在工程制造过程中,合理选择和使用极限量规的通规将对产品质量和生产效率产生积极的影响。
生产过程中的尺寸精度控制方法

生产过程中的尺寸精度控制方法尺寸精度控制是生产过程中非常重要的一环,它对产品的质量、性能以及使用寿命具有直接的影响。
在制造过程中,如何有效控制尺寸精度,保证产品达到预期设计要求,是每个制造企业都需要重视的问题。
本文将介绍几种常用的尺寸精度控制方法,以帮助企业实现更高的生产质量。
1. 设计合理的公差在产品设计阶段,制定合理的公差范围是尺寸精度控制的首要步骤。
合理的公差设计需要考虑产品的功能需求、材料特性以及生产设备的精度等因素。
公差的设定应符合设计标准,既不能过于苛刻导致生产成本过高,也不能过于宽松导致产品质量低下。
通过详细的尺寸公差设计,可明确制造过程中允许的尺寸变化范围,有利于生产过程的控制。
2. 选用合适的生产工艺不同的生产工艺对尺寸精度的控制能力有所差异。
在制造过程中,选择适合产品要求的生产工艺非常重要。
比如,在零件加工中,传统的机械加工方法相对于数控加工而言,可能存在较大的尺寸误差。
因此,对于对尺寸精度要求较高的产品,更适合采用数控加工等精密加工方法,以提高尺寸精度的控制能力。
3. 有效的装夹技术在加工过程中,装夹技术对尺寸精度控制的影响不可忽视。
合理的装夹方法可以减小零件加工过程中的变形和位移,从而提高尺寸控制的准确性。
因此,制造企业应注意选择适合的装夹工具和方法,确保零件在加工过程中的稳定性和精度。
4. 引进先进的测量设备尺寸精度控制离不开准确的测量。
随着科技的发展,现代制造业已经出现了许多先进的测量设备,如三坐标测量机、光学测量仪等。
这些设备具有高精度、高稳定性的特点,能够快速准确地测量零件的尺寸。
通过引进这些先进的测量设备,并对操作人员进行培训,有助于提高尺寸精度的控制能力。
5. 定期检验与调整尺寸精度控制是一个持续的过程,而不是一次性的工作。
定期检验和调整是确保尺寸精度控制持续有效的关键。
制造企业应制定合理的检验周期,对生产过程中的尺寸精度进行检查,并根据检查结果及时调整和改善生产工艺。
数控加工中的尺寸测量与精度要求

数控加工中的尺寸测量与精度要求在现代制造业中,数控加工已经成为一种重要的生产方式。
数控加工通过计算机控制机床进行加工,具有高效、精确、稳定等优势。
然而,在数控加工过程中,尺寸测量与精度要求是非常重要的环节。
尺寸测量是数控加工中的一项关键工作。
在加工过程中,需要对零件的尺寸进行测量,以确保其符合设计要求。
常用的尺寸测量方法有直接测量和间接测量两种。
直接测量是指通过使用测量工具,如卡尺、游标卡尺、百分表等,直接测量零件的尺寸。
而间接测量则是通过测量零件的其他尺寸参数,如直径、长度等,来推算出目标尺寸的方法。
无论是直接测量还是间接测量,都需要考虑精度要求。
精度是指测量结果与实际尺寸之间的偏差,也是衡量测量准确性的重要指标。
在数控加工中,精度要求通常是非常高的,尤其是对于一些精密零件的加工。
比如,航空航天领域中的发动机零件,精度要求可以达到几个微米甚至更小。
因此,在尺寸测量过程中,需要使用高精度的测量工具,并且严格控制测量环境,以保证测量结果的准确性。
除了测量工具和环境的要求外,数控加工中的尺寸测量还需要考虑到零件的形状和材料特性。
不同形状的零件可能需要采用不同的测量方法,以确保测量结果的准确性。
而不同材料的特性,如热膨胀系数、硬度等,也会对尺寸测量产生影响。
因此,在进行尺寸测量时,需要充分了解零件的形状和材料特性,并选择合适的测量方法和工具。
除了尺寸测量,精度要求也体现在数控加工的加工过程中。
数控加工通过计算机控制机床进行加工,具有高精度、高稳定性的特点。
在加工过程中,需要严格控制各项加工参数,如切削速度、进给速度、切削深度等,以确保加工结果的精度。
同时,还需要定期对机床进行维护和保养,以保证其精度和稳定性。
总之,数控加工中的尺寸测量与精度要求是非常重要的环节。
尺寸测量需要选择合适的测量方法和工具,并严格控制测量环境,以确保测量结果的准确性。
而精度要求则体现在加工过程中,需要严格控制各项加工参数,并定期对机床进行维护和保养。
机械加工质量控制标准

机械加工质量控制标准在机械制造领域中,机械零部件的质量是至关重要的。
为了确保机械零部件的加工质量,我们需要遵守一定的标准和规范。
本文将介绍机械加工质量控制标准。
一、加工质量要求机械零部件的加工质量要求包括尺寸精度、形位公差、表面质量等方面的要求。
在进行加工之前,需要明确零部件的加工质量要求,并在加工过程中严格控制,以保证最终产品的质量。
1. 尺寸精度尺寸精度是衡量机械零部件加工质量的重要指标之一。
尺寸精度一般分为公差等级,根据零部件的实际要求选择适当的公差等级。
加工过程中需采用合适的加工工艺和设备,保证尺寸精度的达到要求。
2. 形位公差形位公差是衡量机械零部件几何形状和位置精度的指标。
对于要求较高的零部件,需要在制定工艺方案和选择设备时考虑形位公差的控制。
在加工过程中,应严格按照设计要求进行加工,保证形位公差的控制。
3. 表面质量零部件的表面质量对于产品的整体外观和性能有较大的影响。
在机械加工过程中,应注重工艺操作的细节,控制好加工参数和刀具状况,保证零部件的表面光洁度和无明显缺陷。
二、加工工艺要求机械加工工艺是保证零部件加工质量的重要环节。
在加工过程中,应根据零部件的具体要求和材料特性,合理选择加工工艺和设备,并制定相应的操作规程。
1. 工艺路线在制定加工工艺时,需要明确每道工序的加工内容和顺序。
合理的工艺路线可以最大程度地减少加工扭曲和变形,提高零部件的加工精度。
2. 加工方法不同的零部件可能采用不同的加工方法,如车削、铣削、钻削、磨削等。
选择合适的加工方法需要考虑加工效率和加工质量的平衡,确保加工过程中的稳定性和准确性。
3. 刀具选择刀具是机械加工中不可或缺的工具,合适的刀具选择能够有效地提高加工质量。
在选择刀具时,需要考虑加工材料的硬度、表面光洁度等因素,并结合具体的加工操作进行选用。
三、设备要求机械加工设备对于加工质量的控制至关重要。
高精度、稳定性好的设备能够提供良好的加工基础,保证零部件加工质量的稳定性和可靠性。
零件技术要求
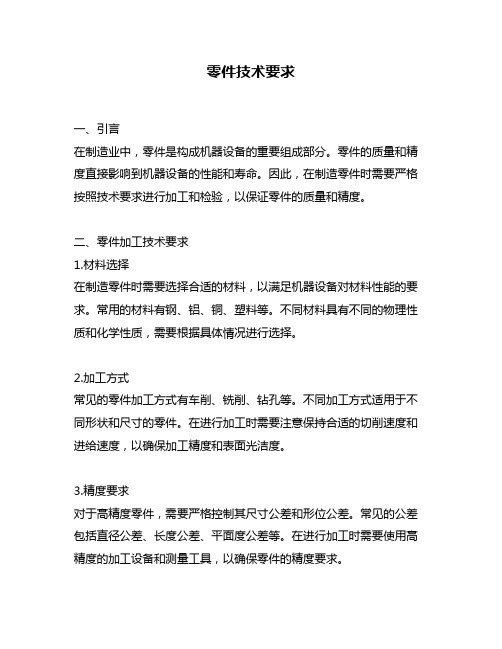
零件技术要求一、引言在制造业中,零件是构成机器设备的重要组成部分。
零件的质量和精度直接影响到机器设备的性能和寿命。
因此,在制造零件时需要严格按照技术要求进行加工和检验,以保证零件的质量和精度。
二、零件加工技术要求1.材料选择在制造零件时需要选择合适的材料,以满足机器设备对材料性能的要求。
常用的材料有钢、铝、铜、塑料等。
不同材料具有不同的物理性质和化学性质,需要根据具体情况进行选择。
2.加工方式常见的零件加工方式有车削、铣削、钻孔等。
不同加工方式适用于不同形状和尺寸的零件。
在进行加工时需要注意保持合适的切削速度和进给速度,以确保加工精度和表面光洁度。
3.精度要求对于高精度零件,需要严格控制其尺寸公差和形位公差。
常见的公差包括直径公差、长度公差、平面度公差等。
在进行加工时需要使用高精度的加工设备和测量工具,以确保零件的精度要求。
4.表面处理零件加工完成后需要进行表面处理,以提高其耐腐蚀性和美观度。
常见的表面处理方式有喷涂、电镀、氧化等。
在进行表面处理时需要注意控制处理时间和温度,以确保处理效果。
三、零件检验技术要求1.检验方法常见的零件检验方法包括三坐标测量、光学投影仪测量、影像测量等。
不同的检验方法适用于不同形状和尺寸的零件。
在进行检验时需要使用高精度的测量设备,以确保检验结果准确可靠。
2.检验标准对于不同类型的零件需要制定不同的检验标准。
常见的标准包括国家标准、行业标准和企业标准等。
在进行检验时需要按照相应标准进行操作,并记录下相关数据和结果。
3.质量控制在制造过程中需要对每个环节进行质量控制,以确保最终产品符合要求。
常见的质量控制方法包括过程控制、SPC(统计过程控制)、FMEA(失效模式与影响分析)等。
在进行质量控制时需要对每个环节进行详细记录,并及时纠正不良现象。
四、结论零件技术要求是制造高品质机器设备的关键环节。
在制造过程中需要注意材料选择、加工方式、精度要求和表面处理等方面的要求,同时也需要注重零件检验和质量控制,以确保最终产品符合要求。
热处理对汽车零件尺寸精度的影响及控制

热处理对汽车零件尺寸精度的影响及控制热处理是指通过对金属材料进行加热和冷却的过程,以改变其结构和性能的方法。
在汽车制造领域,热处理对零件的尺寸精度有着重要的影响。
本文将探讨热处理对汽车零件尺寸精度的影响以及如何进行有效的控制。
一、热处理对汽车零件尺寸精度的影响1. 热处理引起的尺寸变化热处理过程中,金属材料会发生体积的变化,这将直接影响零件的尺寸精度。
在加热过程中,尺寸会发生膨胀,而在冷却过程中又会发生收缩,这种变化是不可避免的。
不同材料的膨胀和收缩率各不相同,因此需要针对具体材料进行相应的调整和控制,以保证零件的精度。
2. 热处理引起的变形除了尺寸的变化,热处理还会引起金属零件的变形。
由于加热和冷却的过程中材料内部温度分布的不均匀性,会导致零件出现不同程度的变形现象。
这种变形会使得零件的尺寸和形状精度受到影响,进而影响整个汽车的性能和可靠性。
3. 热处理对材料组织的影响热处理对金属材料的结构和性能有直接的影响,进而也会影响零件的尺寸精度。
例如,热处理可以改变材料的晶体结构、晶粒大小和相对应的硬度等特性。
这些变化可能会导致材料内部应力的改变,从而进一步影响零件的形变和尺寸变化。
二、控制热处理对汽车零件尺寸精度的方法1. 优化热处理工艺为了减少热处理对汽车零件尺寸精度的影响,可以通过优化热处理工艺来控制尺寸的变化和变形。
首先,选择合适的加热温度和冷却速度,以降低尺寸变化和变形的程度。
其次,控制加热和冷却过程的均匀性,避免材料局部过热或过冷导致的不均匀收缩等问题。
最后,根据不同材料的性质和要求,选择合适的热处理方法,如正火、淬火等,以控制零件尺寸的精度。
2. 使用补偿工艺对于那些难以通过优化热处理工艺来控制尺寸精度的零件,可以考虑使用补偿工艺。
补偿工艺通常是在热处理后进行的,通过加工或其他调整手段来纠正零件的尺寸偏差,使其达到设计要求。
这种方法需要根据实际情况,结合零件的特点和要求来确定具体的补偿方案。
数控车床轴类零件加工的精确度控制

数控车床轴类零件加工的精确度控制数控车床是一种高效的机械加工设备,可用于高精度的零件加工。
在数控车床上加工轴类零件时,精确度控制是非常重要的。
该文档将探讨数控车床轴类零件加工的精确度控制。
本文将从以下方面进行介绍:1. 数控车床轴类零件加工的基本要求2. 数控车床中影响精确度的因素3. 如何控制数控车床轴类零件的精度1. 数控车床轴类零件加工的基本要求在数控车床上加工轴类零件需要符合一些基本的要求。
首先,加工出的轴应该具有高精度和高质量。
其次,加工出的轴应该符合所需的尺寸和形状。
最后,加工过程应该具有高效性和节省时间。
2. 数控车床中影响精确度的因素在数控车床上加工轴类零件时,有许多因素会影响精度。
其中包括以下几个重要方面:1. 材料:轴材料必须具有一定的强度和稳定性,这样才能保证加工时的精度。
另外,当材料硬度较高时,可能会影响加工的精度。
2. 刀具:刀具是数控车床上非常重要的一个因素。
刀具类型、使用寿命等属性会影响加工的精度。
3. 机床参数:机床参数对加工精度也有很大影响。
例如,床身的刚性、主轴的精度、导轨的质量等等都会对整个加工精度产生影响。
4. 程序编程:数控车床需要通过程序实现精确的加工过程,因此程序编程的合理性对精度控制至关重要。
如果程序有错误,则可能导致加工不准确。
5. 环境因素:数控车床加工的环境因素,如温度和湿度,也会影响加工精度。
3. 如何控制数控车床轴类零件的精度为了控制数控车床轴类零件的精度,我们需要采取以下措施:1. 优化切削条件:切削参数包括刀具的选择、加工速度、进给率、切削深度等。
为了使加工达到最佳效果,应尽可能优化切削条件。
2. 优化加工技术:在加工过程中,应使用最先进的加工技术。
例如,应该尽可能使用工艺小切削,避免轴类零件受到过多的削除力。
3. 优化程序设计:程序设计应该尽可能合理化,尽可能减少加工中学习模式的重复。
4. 优化材料选择:在选择轴材料时,应尽量选择稳定性高的材料,以确保加工效果的一致性。
零件尺寸精度改进

零件尺寸精度改进零件尺寸精度改进步骤一:确定零件尺寸精度的重要性第一步是明确为什么零件尺寸精度对于制造过程的重要性。
零件尺寸精度是指零件的尺寸与设计要求之间的偏差。
精确的尺寸精度可以保证零件在装配和运作过程中的可靠性和稳定性。
此外,尺寸精度还直接影响产品的性能和质量。
因此,在制造过程中,确保零件尺寸精度的准确性至关重要。
步骤二:了解零件尺寸精度的测量和控制方法第二步是了解零件尺寸精度的测量和控制方法。
常见的测量方法包括使用测量工具(如千分尺、卡尺等)和精密测量设备(如光学投影仪、三坐标测量仪等)。
控制方法包括制定严格的制造工艺和质量控制标准,以确保零件尺寸的精确性和一致性。
步骤三:分析零件尺寸精度问题的根本原因第三步是分析导致零件尺寸精度问题的根本原因。
可能的原因包括材料选择不当、加工工艺不准确、设备磨损等。
通过仔细分析和排查,可以确定并解决这些问题,从而提高零件尺寸精度。
步骤四:优化制造过程以提高零件尺寸精度第四步是优化制造过程以提高零件尺寸精度。
这可以包括改进工艺参数、使用更精确的设备、优化材料选择等。
例如,使用先进的数控机床可以提高加工精度;采用高精度的模具可以减少材料浪费和误差;使用特殊的材料可以提高零件的稳定性等。
通过对制造过程进行全面的优化,可以显著改善零件尺寸精度。
步骤五:加强质量控制和检验第五步是加强质量控制和检验。
除了在制造过程中采取相应的措施,还应建立完善的质量控制体系和检验流程。
例如,建立合理的抽样检验规范,定期进行设备校准和检验,培训员工提高质量意识等。
通过加强质量控制和检验,可以及时发现和纠正零件尺寸精度问题,并确保产品质量的稳定性和一致性。
步骤六:持续改进和学习最后,持续改进和学习是提高零件尺寸精度的关键。
制造技术和设备都在不断发展和更新,因此,持续改进和学习是保持竞争力和提高尺寸精度的重要手段。
通过关注行业动态和技术趋势,参加培训和学习活动,不断改进制造过程和技术,可以不断提高零件尺寸精度,并推动企业的发展。
CNC机床加工中的加工精度控制方法

CNC机床加工中的加工精度控制方法在CNC机床加工中,加工精度的控制是至关重要的。
精确的加工能够确保零件尺寸的准确性和质量的稳定性。
本文将介绍几种常用的加工精度控制方法,帮助读者更好地理解和应用于实际生产中。
一、选用高精度CNC机床及工具在选择CNC机床时,应注重其加工精度和重复定位精度。
高精度的机床能够提供更好的工件精度和表面质量。
同时,使用质量优良的刀具、夹具以及其他加工工具也能够提高加工精度。
二、合理规划工艺参数在加工过程中,合理规划和控制工艺参数对于实现加工精度的控制至关重要。
例如,合理选择切削速度、进给速度和切削深度等参数,能够有效地控制切削力和温度,确保加工过程的稳定性和一致性。
三、控制机床刚度和热变形机床的刚度和热变形是影响加工精度的重要因素。
通过提高机床刚度,可以降低振动和变形,提高加工精度。
此外,控制机床的温度分布,采取散热和稳定温度的措施也能够减小热变形,提高加工精度。
四、准确测量和调整工件在CNC机床加工过程中,及时准确地测量工件尺寸是保证加工精度的重要环节。
通过使用高精度测量工具,如三坐标测量仪等,可以对加工过程进行实时监控和调整,确保工件尺寸的准确性。
五、合理选择刀具与切削液选择合适的刀具和切削液对于加工精度的控制同样至关重要。
高性能的刀具能够提供更好的切削质量和稳定性,而适当的切削液能够降低切削温度和摩擦,减少刀具磨损,提高加工精度。
六、制定严格的工艺控制和操作规程制定严格的工艺控制和操作规程对于实现加工精度的一致性和可控性非常重要。
在制定过程中,应明确各个环节的要求和标准,并加强对操作人员的培训和管理,确保每个环节的工艺参数得到准确执行,从而实现加工精度的控制。
七、不断改进和优化加工精度的控制是一个不断探索和改进的过程。
企业应当注重科研创新,引进新的加工技术和设备,改进工艺和工具,提升加工精度。
同时,加强与供应商和客户的沟通与合作,不断改进产品质量和精度要求,以满足市场需求。
机械零件尺寸精度控制方法
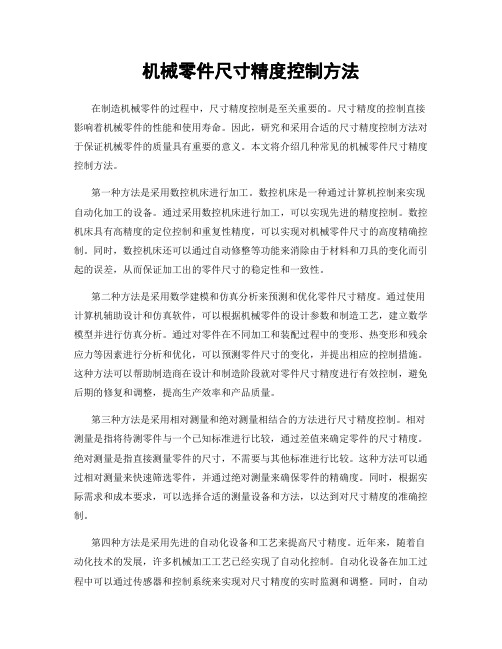
机械零件尺寸精度控制方法在制造机械零件的过程中,尺寸精度控制是至关重要的。
尺寸精度的控制直接影响着机械零件的性能和使用寿命。
因此,研究和采用合适的尺寸精度控制方法对于保证机械零件的质量具有重要的意义。
本文将介绍几种常见的机械零件尺寸精度控制方法。
第一种方法是采用数控机床进行加工。
数控机床是一种通过计算机控制来实现自动化加工的设备。
通过采用数控机床进行加工,可以实现先进的精度控制。
数控机床具有高精度的定位控制和重复性精度,可以实现对机械零件尺寸的高度精确控制。
同时,数控机床还可以通过自动修整等功能来消除由于材料和刀具的变化而引起的误差,从而保证加工出的零件尺寸的稳定性和一致性。
第二种方法是采用数学建模和仿真分析来预测和优化零件尺寸精度。
通过使用计算机辅助设计和仿真软件,可以根据机械零件的设计参数和制造工艺,建立数学模型并进行仿真分析。
通过对零件在不同加工和装配过程中的变形、热变形和残余应力等因素进行分析和优化,可以预测零件尺寸的变化,并提出相应的控制措施。
这种方法可以帮助制造商在设计和制造阶段就对零件尺寸精度进行有效控制,避免后期的修复和调整,提高生产效率和产品质量。
第三种方法是采用相对测量和绝对测量相结合的方法进行尺寸精度控制。
相对测量是指将待测零件与一个已知标准进行比较,通过差值来确定零件的尺寸精度。
绝对测量是指直接测量零件的尺寸,不需要与其他标准进行比较。
这种方法可以通过相对测量来快速筛选零件,并通过绝对测量来确保零件的精确度。
同时,根据实际需求和成本要求,可以选择合适的测量设备和方法,以达到对尺寸精度的准确控制。
第四种方法是采用先进的自动化设备和工艺来提高尺寸精度。
近年来,随着自动化技术的发展,许多机械加工工艺已经实现了自动化控制。
自动化设备在加工过程中可以通过传感器和控制系统来实现对尺寸精度的实时监测和调整。
同时,自动化设备还可以通过智能化的算法和优化控制来最大程度地提高尺寸精度。
与传统的手工操作相比,自动化设备具有更高的精度和稳定性,可以大大提高机械零件的尺寸精度。
塑料制品的尺寸精度控制

塑料制品的尺寸精度控制在塑料工业中,制品的尺寸精度控制一直是至关重要的课题。
塑料制品的应用范围极其广泛,从日常生活的家用电器、玩具、包装材料,到工业领域的机械零件、汽车配件等,都对尺寸精度有着不同程度的要求。
尺寸精度直接影响着制品的质量、功能和外观,因此,研究并掌握塑料制品的尺寸精度控制技术,对提高我国塑料工业的整体水平具有重要意义。
1. 塑料加工过程对尺寸精度的影响塑料制品的尺寸精度主要受以下几个阶段的影响:1.1 树脂的特性树脂的种类、牌号及性质对制品的尺寸精度具有重要影响。
不同种类的树脂具有不同的结晶度、热膨胀系数和收缩率,这些因素都会直接影响制品的尺寸精度。
1.2 成型工艺成型工艺是影响塑料制品尺寸精度的重要环节。
包括注射成型、挤出成型、压制成型等多种方式。
不同成型工艺对制品尺寸精度的影响因素也不尽相同,如注射成型中模具温度、注射速度、保压时间等参数都会对制品尺寸精度产生影响。
1.3 模具设计及制造模具是塑料制品成型的关键工具,模具的设计和制造质量直接关系到制品的尺寸精度。
模具的型腔、型芯、滑块等部分的加工精度和表面质量都会对制品尺寸精度产生重要影响。
1.4 加工设备加工设备的性能也是影响塑料制品尺寸精度的重要因素。
设备的精度、稳定性及维护状况都会对制品尺寸精度产生直接影响。
2. 尺寸精度控制方法为了保证塑料制品的尺寸精度,可以采取以下几种方法进行控制:2.1 优化成型工艺参数通过合理设定模具温度、注射速度、保压时间等成型工艺参数,可以有效控制制品的尺寸精度。
例如,提高模具温度可以减小制品的收缩率,降低注射速度可以减小制品的应力变形等。
2.2 提高模具制造质量提高模具的加工精度和表面质量,可以有效减小制品的尺寸公差。
此外,合理设计模具结构,避免制品产生变形、翘曲等现象,也是提高制品尺寸精度的重要手段。
2.3 选用合适的树脂及助剂根据制品的用途和性能要求,选用合适的树脂及助剂,可以有效控制制品的尺寸精度。
钢球精度等级g10标准

钢球精度等级g10标准在现代工业中,精度要求越来越高。
钢球作为精密零件和传动元件,在许多领域中都发挥着重要的作用。
为了确保钢球的高精度和质量,国际上制定了一系列的精度等级标准,其中最为常见的就是G10标准。
G10标准是指钢球制造过程中所控制的尺寸偏差范围。
其中,G表示精度等级,数字10则表示尺寸偏差范围的千分之一。
按照G10标准制造的钢球,其直径尺寸偏差控制在0.015mm以内。
这意味着,无论是直径上的尺寸增加还是减小,都要在0.015mm的范围内。
换句话说,G10标准要求钢球的直径尺寸在0.03mm的范围内变化。
钢球的尺寸偏差不仅与生产工艺有关,还与材料的性质和制造设备的精度有关。
在制造过程中,需要采用高精度的设备和工艺来控制钢球的尺寸偏差。
通过机械加工、磨削和抛光等工艺,可以将钢球制造到满足G10标准的精度。
G10标准还要求钢球表面的光洁度和圆度满足要求。
光洁度是指钢球表面的平滑程度,圆度是指钢球表面的圆形度。
为了达到高精度的光洁度和圆度,制造过程中通常需要采用精密的磨削和抛光工艺。
根据G10标准,制造钢球的材料通常采用高强度、耐磨损的钢材,如碳钢、铬钢、不锈钢等。
这些钢材具有良好的机械性能和耐腐蚀性能,可以满足各种工业应用的需求。
G10标准的应用范围非常广泛。
在航空航天、汽车制造、机械设备、精密仪器等领域,都需要使用高精度的钢球。
例如,在航天器的导航系统中,钢球用于传递信号和驱动装置。
而在汽车发动机中,钢球则用于凸轮轴的滚动轴承。
为了确保钢球的质量和精度,通常需要进行严格的质量检测。
常见的检测方法包括光学投影仪、三坐标测量仪和显微硬度计等。
通过这些检测手段,可以对钢球的尺寸、圆度和光洁度进行全面的检测和评估。
总而言之,G10标准是制造高精度钢球的重要参考标准。
通过控制制造工艺和采用精密设备,可以确保钢球的尺寸偏差、光洁度和圆度满足要求。
随着工业技术的不断进步,对于钢球精度的要求也将不断提高,G10标准将继续发挥重要的作用。
零件的尺寸精度和配合的设计
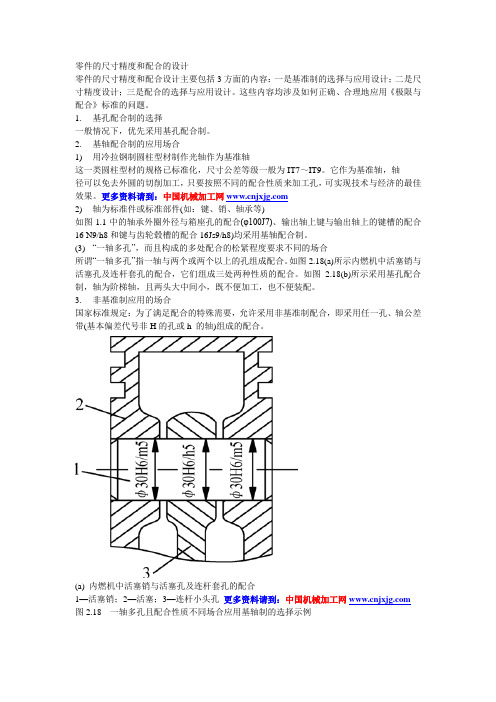
零件的尺寸精度和配合的设计零件的尺寸精度和配合设计主要包括3方面的内容:一是基准制的选择与应用设计;二是尺寸精度设计;三是配合的选择与应用设计。
这些内容均涉及如何正确、合理地应用《极限与配合》标准的问题。
1. 基孔配合制的选择一般情况下,优先采用基孔配合制。
2. 基轴配合制的应用场合1) 用冷拉钢制圆柱型材制作光轴作为基准轴这一类圆柱型材的规格已标准化,尺寸公差等级一般为IT7~IT9。
它作为基准轴,轴径可以免去外圆的切削加工,只要按照不同的配合性质来加工孔,可实现技术与经济的最佳效果。
更多资料请到:中国机械加工网2) 轴为标准件或标准部件(如:键、销、轴承等)如图1.1中的轴承外圈外径与箱座孔的配合(φ100J7)、输出轴上键与输出轴上的键槽的配合16 N9/h8和键与齿轮毂槽的配合16Js9/h8)均采用基轴配合制。
(3) “一轴多孔”,而且构成的多处配合的松紧程度要求不同的场合所谓“一轴多孔”指一轴与两个或两个以上的孔组成配合。
如图2.18(a)所示内燃机中活塞销与活塞孔及连杆套孔的配合,它们组成三处两种性质的配合。
如图 2.18(b)所示采用基孔配合制,轴为阶梯轴,且两头大中间小,既不便加工,也不便装配。
3. 非基准制应用的场合国家标准规定:为了满足配合的特殊需要,允许采用非基准制配合,即采用任一孔、轴公差带(基本偏差代号非H的孔或h 的轴)组成的配合。
(a) 内燃机中活塞销与活塞孔及连杆套孔的配合1—活塞销;2—活塞;3—连杆小头孔更多资料请到:中国机械加工网图2.18 一轴多孔且配合性质不同场合应用基轴制的选择示例(b) 基孔制配合的孔、轴公差带和孔、轴(c) 基轴制配合的孔、轴公差带和孔、轴图2.18 一轴多孔且配合性质不同场合应用基轴制的选择示例1. 公差等级的选择原则在满足使用性能的前提下,尽量选取较低的公差等级。
所谓“较低的公差等级”是指:假如IT7级以上(含IT7)的公差等级均能满足使用性能要求,那么,选择IT7级为宜。
机械加工中精度控制与误差补偿方法

机械加工中精度控制与误差补偿方法机械加工是一门关键的制造工艺,它对于高精度零件的制造至关重要。
然而,在机械加工过程中,由于多种因素的影响,零件的加工精度往往会受到一定程度的影响。
因此,精度控制与误差补偿成为了机械加工过程中不可或缺的一环。
一、精度控制的重要性在机械加工过程中,要求加工出来的零件能够满足特定的尺寸,形状和表面质量要求。
而这些要求可以通过加工设备和工艺的不断改进来实现。
精度控制的核心在于控制加工设备的运动轨迹和速度,并结合传感器或其他测量设备来实时监测零件的加工状况,并对加工结果进行反馈和调整。
通过这种方式,可以有效地确保零件的加工精度。
二、误差的来源在机械加工过程中,误差是无法避免的,它来自于多个方面。
主要的误差来源包括机械设备的刚性变形、加工工具的磨损、材料的性质以及工艺参数的变化等。
机械设备的刚性变形是机械加工中最主要的误差来源之一。
当机械设备在工作过程中受到外力的作用时,会导致其结构发生变形,从而影响零件的加工精度。
为了解决这个问题,可以通过选用高刚度的机械设备、加强机械设备的固定等方式来减小刚性变形。
加工工具的磨损也是机械加工中常见的误差来源之一。
随着加工次数的增加,加工工具会逐渐磨损,从而导致零件的尺寸精度下降。
为了解决这个问题,可以通过定期更换加工工具或者采用刀具补偿等方法来降低磨损对加工精度的影响。
材料的性质也会对机械加工的精度产生影响。
不同材料的导热性、热膨胀系数等参数不同,可能会导致加工过程中的温度变化和尺寸变化,从而降低加工精度。
为了解决这个问题,可以通过控制加工过程中的温度、选用适合的材料等方法来减小材料对加工精度的影响。
工艺参数的变化也是导致机械加工精度下降的重要原因之一。
例如,工件在加工过程中的切削速度、进给速度等参数的变化,可能会导致零件尺寸的误差。
为了解决这个问题,可以通过加强工艺参数的控制,选用更精确的加工参数等方式来提高加工精度。
三、误差补偿方法为了弥补机械加工过程中产生的误差,我们可以采用多种方法进行误差补偿。
探索硬质阳极化前后高精度尺寸的控制
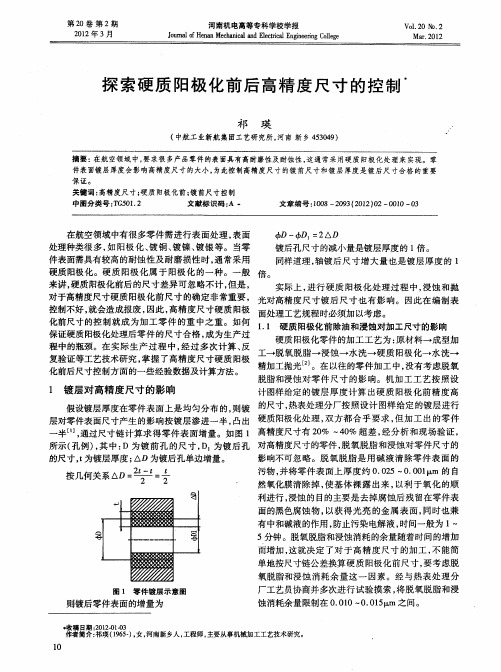
I
l 玟
面的黑 色腐蚀 物 , 以获 得 光 亮 的金 属 表 面 , 同时 也兼 有 中和 碱液 的作用 , 防止 污 染 电解 液 , 间一 般 为 1 时 —
l
●
&
季
5分钟 。脱 氧脱脂 和 浸蚀 消耗 的余 量随着 时 间的增 加 而增加 , 这就 决 定 了对 于 高 精 度 尺 寸 的加 工 , 能 简 不
・
・
2 3 考虑预处 理对 厚度 的影 响 .
规 定硬 质 阳极 化后 加 工尺寸 为 X 2~Y 2 硬质阳极化前需 采用预处理 即脱氧脱脂和浸蚀 由尺寸链 换算 可 求得 , 质 阳极化 前尺寸 公差 : 硬 Xl=X +A 一0. 02 等工艺, 应预留高精度 尺寸需要硬质 阳极 化的厚度 , 以保证 高精度 尺寸镀 后尺 寸在 图样要 求范 围 内。 y =Y+B一 .2 0 0 考 虑脱 氧脱 脂 、 】 0 0 (. 2是 浸蚀 和 实 际生产过 程 中有 两 种 较 为 常 见 的 方法 使 零 件 抛 光余 量 ) 表 面预 留出接近 于镀层 的尺 寸余 量 , 处 理 即脱 氧脱 预 硬 质 阳极化后 尺 寸公差 : X2= X1—0. 5一A =X +A 一0 02—0 01 一A = 01 . . 5 脂 和浸蚀 及 机械 加 工 过 程 中 预 留足 够 的镀 层 厚 度 尺 0o5 .o 寸 。 以解 决生 产 过程 中高 精 度 尺 寸 硬 质 阳极 化 的瓶 颈 为例 : y = 一 . 1 B = + B 一 . 2—0 0 5一B 2 0 0 5一 X 00 .1 y 0 05 考虑脱氧脱脂和浸蚀余量 005 .1) X X零 件孔 尺寸 为  ̄ 6 ( 009 硬 质 阳极 化 = 一 .0 ( X 3 H8 3 ) 硬质 阳极化后对孔进行抛光 , 把抛光余量限制在 层为 2 4 1 0~ 0. c m 0 0 5 m, 么精 加工 抛光 后 , .0  ̄ 那 就可 得到设计 要求 的尺 规定 图纸要 求镀 层 为 A— 寸 公差 , 证零 件 10 保 0 %合 格 。 规定设 计 图纸要 求最 后尺 寸公 差为 ~l , 3 2 硬质 阳极 化前 后轴 的尺 寸公 差控 制 . 规定 硬质 阳极化 前加 工尺 寸为 X 一y 1 规定图纸要求阳极化层为 口一 6 口 按尺 寸链 公 差计算 镀 前公差 : ) 规定设 计 图纸要 求最 后尺 寸公差 为 — Y X1=X +A =0 03 . 9+0. 2 0 0=0. 5 09 规 定硬 质 阳极化 前加 工尺寸 为 1 y 一1 y :Y+B =0 +0 0 0 =0 0 1 .4 .4 规定 硬质 阳极 化后 加 工尺寸 为 一y 2
浅谈在数控车床上如何控制零件总长
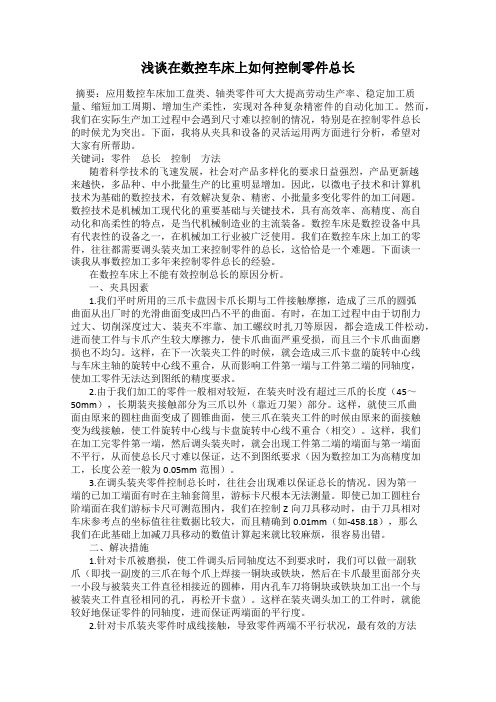
浅谈在数控车床上如何控制零件总长摘要:应用数控车床加工盘类、轴类零件可大大提高劳动生产率、稳定加工质量、缩短加工周期、增加生产柔性,实现对各种复杂精密件的自动化加工。
然而,我们在实际生产加工过程中会遇到尺寸难以控制的情况,特别是在控制零件总长的时候尤为突出。
下面,我将从夹具和设备的灵活运用两方面进行分析,希望对大家有所帮助。
关键词:零件总长控制方法随着科学技术的飞速发展,社会对产品多样化的要求日益强烈,产品更新越来越快,多品种、中小批量生产的比重明显增加。
因此,以微电子技术和计算机技术为基础的数控技术,有效解决复杂、精密、小批量多变化零件的加工问题。
数控技术是机械加工现代化的重要基础与关键技术,具有高效率、高精度、高自动化和高柔性的特点,是当代机械制造业的主流装备。
数控车床是数控设备中具有代表性的设备之一,在机械加工行业被广泛使用。
我们在数控车床上加工的零件,往往都需要调头装夹加工来控制零件的总长,这恰恰是一个难题。
下面谈一谈我从事数控加工多年来控制零件总长的经验。
在数控车床上不能有效控制总长的原因分析。
一、夹具因素1.我们平时所用的三爪卡盘因卡爪长期与工件接触摩擦,造成了三爪的圆弧曲面从出厂时的光滑曲面变成凹凸不平的曲面。
有时,在加工过程中由于切削力过大、切削深度过大、装夹不牢靠、加工螺纹时扎刀等原因,都会造成工件松动,进而使工件与卡爪产生较大摩擦力,使卡爪曲面严重受损,而且三个卡爪曲面磨损也不均匀。
这样,在下一次装夹工件的时候,就会造成三爪卡盘的旋转中心线与车床主轴的旋转中心线不重合,从而影响工件第一端与工件第二端的同轴度,使加工零件无法达到图纸的精度要求。
2.由于我们加工的零件一般相对较短,在装夹时没有超过三爪的长度(45~50mm),长期装夹接触部分为三爪以外(靠近刀架)部分。
这样,就使三爪曲面由原来的圆柱曲面变成了圆锥曲面,使三爪在装夹工件的时候由原来的面接触变为线接触,使工件旋转中心线与卡盘旋转中心线不重合(相交)。
- 1、下载文档前请自行甄别文档内容的完整性,平台不提供额外的编辑、内容补充、找答案等附加服务。
- 2、"仅部分预览"的文档,不可在线预览部分如存在完整性等问题,可反馈申请退款(可完整预览的文档不适用该条件!)。
- 3、如文档侵犯您的权益,请联系客服反馈,我们会尽快为您处理(人工客服工作时间:9:00-18:30)。
高精度零件尺寸
控制
高精度零件尺寸控制
高精度零件尺寸控制是制造业中非常重要的一个方面,它直接影响到产品的质量和性能。
在进行高精度零件尺寸控制时,下面是一些步骤和思考方法可以帮助我们进行有效的控制。
第一步是制定准确的尺寸控制目标。
在开始制造高精度零件之前,我们需要明确产品的设计要求和所需的精度。
这包括确定零件的尺寸范围、公差等要求。
只有明确了目标,我们才能有针对性地进行尺寸控制。
第二步是选择合适的测量工具和方法。
在进行高精度零件尺寸控制时,我们需要选择适当的测量工具来确保测量的准确性和精度。
这可能包括使用千分尺、量块、光学投影仪等高精度测量设备。
同时,我们还需要选择适当的测量方法,以确保所使用的测量工具能够准确地检测出尺寸的变化。
第三步是进行合适的材料选择和处理。
在制造高精度零件时,我们需要选择合适的材料来保证零件的稳定性和精度。
有些材料可能在加工过程中容易变形
或受到外部环境的影响,因此我们需要对材料进行合理的处理和控制,以确保零件尺寸的稳定性。
第四步是进行精确的加工和装配。
在制造高精度零件时,加工和装配过程的精度和准确性至关重要。
我们需要选择合适的加工工艺和设备,并严格按照设计要求进行加工和装配。
同时,我们还需要进行实时的尺寸检测和调整,以确保零件的尺寸符合要求。
第五步是进行严格的质量控制和检验。
在制造高精度零件后,我们需要进行严格的质量控制和检验,以确保产品的质量和性能。
这包括使用合适的检测设备对零件进行尺寸检测、形状检测以及材料成分分析等。
同时,我们还需要建立完善的质量控制体系,对生产过程进行监控和改进。
最后一步是持续改进和优化。
高精度零件尺寸控制是一个不断优化和改进的过程。
我们需要不断总结经验,找到并解决尺寸控制中的问题,不断改进和优化生产工艺和设备,以提高零件的质量和精度。
总之,高精度零件尺寸控制是制造业中非常重要的一个环节。
通过制定准确的尺寸控制目标,选择合适的测量工具和方法,进行合适的材料选择和处理,
进行精确的加工和装配,进行严格的质量控制和检验,以及持续改进和优化,我们可以有效地控制高精度零件的尺寸,提高产品的质量和性能。