流态化还原炼铁技术
钢铁脱碳——氢基流态化粉矿还原(HYFOR)
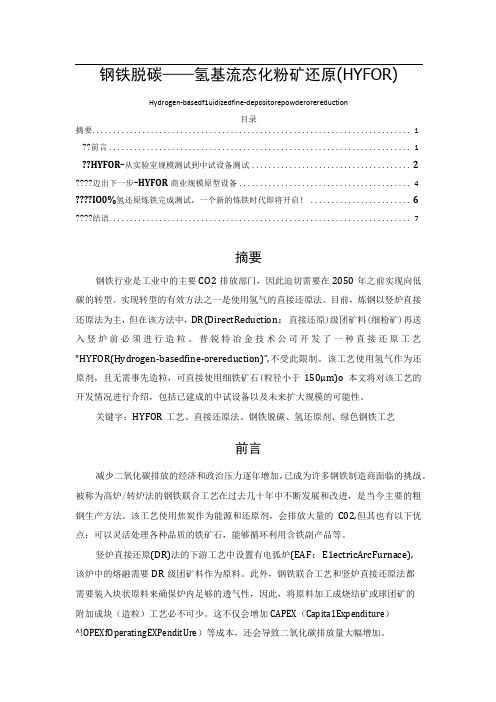
钢铁脱碳——氢基流态化粉矿还原(HYFOR)Hydrogen-basedf1uidizedfine-depositorepowderorereduction目录摘要 (1)前言 (1)HYFOR-从实验室规模测试到中试设备测试 (2)迈出下一步-HYFOR商业规模原型设备 (4)IO0%氢还原炼铁完成测试,一个新的炼铁时代即将开启! (6)结语 (7)摘要钢铁行业是工业中的主要CO2排放部门,因此迫切需要在2050年之前实现向低碳的转型。
实现转型的有效方法之一是使用氢气的直接还原法。
目前,炼钢以竖炉直接还原法为主,但在该方法中,DR(DirectReduction:直接还原)级团矿料(细粉矿)再送入竖炉前必须进行造粒。
普锐特冶金技术公司开发了一种直接还原工艺"HYFOR(Hydrogen-basedfine-orereduction)”,不受此限制。
该工艺使用氢气作为还原剂,且无需事先造粒,可直接使用细铁矿石(粒径小于150μm)o本文将对该工艺的开发情况进行介绍,包括已建成的中试设备以及未来扩大规模的可能性。
关键字:HYFOR工艺、直接还原法、钢铁脱碳、氢还原剂、绿色钢铁工艺前言减少二氧化碳排放的经济和政治压力逐年增加,已成为许多钢铁制造商面临的挑战。
被称为高炉/转炉法的钢铁联合工艺在过去几十年中不断发展和改进,是当今主要的粗钢生产方法。
该工艺使用焦炭作为能源和还原剂,会排放大量的C02,但其也有以下优点:可以灵活处理各种品质的铁矿石,能够循环利用含铁副产品等。
竖炉直接还原(DR)法的下游工艺中设置有电弧炉(EAF:E1ectricArcFurnace),该炉中的熔融需要DR级团矿料作为原料。
此外,钢铁联合工艺和竖炉直接还原法都需要装入块状原料来确保炉内足够的透气性,因此,将原料加工成烧结矿或球团矿的附加成块(造粒)工艺必不可少。
这不仅会增加CAPEX(Capita1Expenditure)^!OPEXfOperatingEXPenditUre)等成本,还会导致二氧化碳排放量大幅增加。
一种铁矿流态化悬浮预热预还原装置及方法[发明专利]
![一种铁矿流态化悬浮预热预还原装置及方法[发明专利]](https://img.taocdn.com/s3/m/52cd8bf6cc7931b764ce159e.png)
专利名称:一种铁矿流态化悬浮预热预还原装置及方法专利类型:发明专利
发明人:张宏建,刘刚,王兆平,王士军,李梦
申请号:CN201711159228.5
申请日:20171120
公开号:CN107630139A
公开日:
20180126
专利内容由知识产权出版社提供
摘要:一种铁矿悬浮预热预还原装置及方法,属于铁矿冶炼装置及方法。
铁矿悬浮预热预还原装置,包括:上料机、悬浮预热装置、焙烧炉、悬浮装置;上料机的输出端与悬浮预热装置的入料端连接,悬浮预热装置的出料端与焙烧炉的入料端连接,焙烧炉的出料端与悬浮装置的入料端连接。
铁矿粉状物料由上料机送入悬浮预热装置,逐级预热后,进入焙烧炉进行焙烧预还原,然后进入最后一级悬浮装置,出料后热料喷入熔融还原炉进行熔融冶炼。
悬浮预热装置采用平行气流,交叉料流的混连混流方式实现多次换热,焙烧炉排出热烟气经过悬浮预热装置与物料换热后,排出的废气经余热发电、物料烘干后净化排放。
本装置实现了悬浮预热、悬浮焙烧预还原、余热利用、节省原料、废气处理的技术。
申请人:徐州贝克福尔节能环保技术有限公司
地址:221116 江苏省徐州市徐州高新技术产业开发区长兴路16号泰和办公大楼
国籍:CN
更多信息请下载全文后查看。
富氢条件下铁矿粉流态化还原效果及粘结行为研究
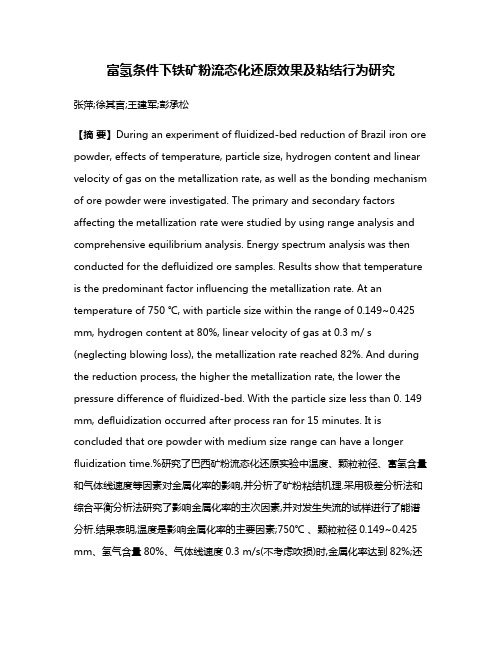
富氢条件下铁矿粉流态化还原效果及粘结行为研究张萍;徐其言;王建军;彭承松【摘要】During an experiment of fluidized-bed reduction of Brazil iron ore powder, effects of temperature, particle size, hydrogen content and linear velocity of gas on the metallization rate, as well as the bonding mechanism of ore powder were investigated. The primary and secondary factors affecting the metallization rate were studied by using range analysis and comprehensive equilibrium analysis. Energy spectrum analysis was then conducted for the defluidized ore samples. Results show that temperature is the predominant factor influencing the metallization rate. At an temperature of 750 ℃, with particle size within the range of 0.149~0.425 mm, hydrogen content at 80%, linear velocity of gas at 0.3 m/ s (neglecting blowing loss), the metallization rate reached 82%. And during the reduction process, the higher the metallization rate, the lower the pressure difference of fluidized-bed. With the particle size less than 0. 149 mm, defluidization occurred after process ran for 15 minutes. It is concluded that ore powder with medium size range can have a longer fluidization time.%研究了巴西矿粉流态化还原实验中温度、颗粒粒径、富氢含量和气体线速度等因素对金属化率的影响,并分析了矿粉粘结机理.采用极差分析法和综合平衡分析法研究了影响金属化率的主次因素,并对发生失流的试样进行了能谱分析.结果表明,温度是影响金属化率的主要因素;750℃ 、颗粒粒径0.149~0.425 mm、氢气含量80%、气体线速度0.3 m/s(不考虑吹损)时,金属化率达到82%;还原过程中,金属化率越高,床层压差越小.当粒度小于0.149 mm时,15 min开始出现失流,中等粒度的矿粉能保持较长的流化时间.【期刊名称】《矿冶工程》【年(卷),期】2017(037)001【总页数】5页(P103-107)【关键词】流态化还原;还原铁;金属化率;压差;粘结【作者】张萍;徐其言;王建军;彭承松【作者单位】安徽工业大学冶金工程学院,安徽马鞍山 243032;安徽工业大学冶金工程学院,安徽马鞍山 243032;安徽工业大学冶金工程学院,安徽马鞍山243032;安徽工业大学冶金工程学院,安徽马鞍山 243032【正文语种】中文【中图分类】TF111由于炼焦煤逐渐成为世界短缺资源,使得对冶金焦有强烈依赖的高炉炼铁成本越来越高。
造粒超细三氧化二铁粉的流态化及直接还原实验的研究
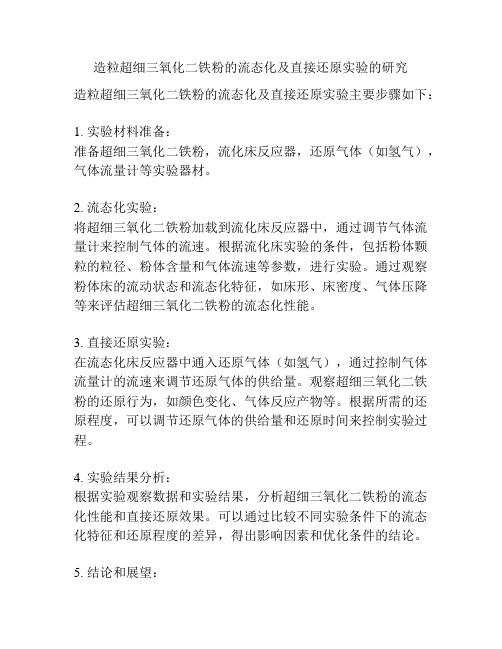
造粒超细三氧化二铁粉的流态化及直接还原实验的研究
造粒超细三氧化二铁粉的流态化及直接还原实验主要步骤如下:
1. 实验材料准备:
准备超细三氧化二铁粉,流化床反应器,还原气体(如氢气),气体流量计等实验器材。
2. 流态化实验:
将超细三氧化二铁粉加载到流化床反应器中,通过调节气体流量计来控制气体的流速。
根据流化床实验的条件,包括粉体颗粒的粒径、粉体含量和气体流速等参数,进行实验。
通过观察粉体床的流动状态和流态化特征,如床形、床密度、气体压降等来评估超细三氧化二铁粉的流态化性能。
3. 直接还原实验:
在流态化床反应器中通入还原气体(如氢气),通过控制气体流量计的流速来调节还原气体的供给量。
观察超细三氧化二铁粉的还原行为,如颜色变化、气体反应产物等。
根据所需的还原程度,可以调节还原气体的供给量和还原时间来控制实验过程。
4. 实验结果分析:
根据实验观察数据和实验结果,分析超细三氧化二铁粉的流态化性能和直接还原效果。
可以通过比较不同实验条件下的流态化特征和还原程度的差异,得出影响因素和优化条件的结论。
5. 结论和展望:
总结实验结果,得出造粒超细三氧化二铁粉的流态化和直接还原实验的研究结论。
展望未来的研究方向,如进一步优化流态化条件、改进还原方法等,提高超细三氧化二铁粉的流态化和还原性能。
项目名称低碳节能流态化还原炼铁关键技术基础

项目名称:低碳节能流态化还原炼铁关键技术基础提名单位: 北京科技大学完成单位: 北京科技大学, 中国科学院过程工程研究所主要完成人: 郭占成,王明涌,公旭中,宋学平,王志,邵剑华,唐惠庆项目简介:钢铁工业是国民经济建设的支柱产业,我国钢铁产量已达世界的50%以上。
近中期内,我国钢铁产量仍将保持高位水平。
由于传统钢铁生产存在能耗高、碳排放大的问题,因此,低碳节能钢铁生产新技术是钢铁工业可持续发展的重大需求。
从铁矿粉到金属铁,是钢铁生产最主要过程。
传统高炉炼铁,铁矿粉和粉煤分别经烧结和焦化造块,然后烧结矿与焦炭装入高炉并喷吹热风和煤粉实现碳热还原炼铁,这是一个能耗高、污染重、碳排放大的长流程过程,能耗和污染物及碳排放都占钢铁生产全流程的70%以上。
为解决这些问题,世界冶金科技工作者早在上世纪初就开始研究铁矿粉直接流态化还原炼铁技术,还原剂可为煤气化产生的中高温CO气,或天燃气重整产生的以H2为主的中高温CO-H2气。
由于CO还原Fe2O3是放热反应,而H2还原Fe2O3是强吸热反应,要维持高温过程,还原气体CO-H2的H2/CO要适当,理想组成与流态化还原工艺及技术参数控制有关。
因此,要实现铁矿粉流态化还原炼铁的低能耗和低碳排放,首先必须解决低成本低能耗且H2/CO 可调的高温还原气制备技术。
此外,铁矿粉流态化还原炼铁,虽然是一个节能减排的低碳炼铁技术,但是,几十年来,由于铁矿粉还原过程发生颗粒粘结失流,致使这一技术一直未能工程化应用。
由此可见,解决CO-H2还原气制备技术和铁矿粉还原过程的粘结失流技术,是铁矿粉流态化还原炼铁低碳节能的关键。
针对铁矿粉流态化还原炼铁的节能减碳还原气制备,在“863”项目的支持下,提出了能源互补、节能、低碳的煤与天然气共气化制备H2/CO可调高温还原气的新技术原理,揭示了共气化参数对产物气体H2/CO比例的可控调节规律,并完成了气体产量100 m3/h级技术验证;提出了粉煤负载Fe2O3催化煤气化新技术,解析了粉煤催化气化过程中煤焦结构演变规律及Fe2O3粒径对催化效果的影响规律,据此发明了催化剂负载方法,大幅度降低了Fe2O3用量并提高催化效果;在国家自然科学基金项目支持下,提出了超重力强化水电解制氢技术,阐明了超重力电解节能机理,解析了基于气泡快速分离的强化机制,形成节能高效易于大规模制氢的创新方法,可支撑流态化低碳冶金H2/CO比的动态调节。
直接还原铁生产工艺及发展方向

直接还原铁(海绵铁)生产工艺及发展方向习惯上,我们把铁矿石在高炉中先还原冶炼成含碳高的生铁,而后在炼钢炉内氧化,降低含碳量并精炼成钢,这项传统工艺,称作间接炼钢方法;在低于矿石熔化温度下,通过固态还原,把铁矿石炼制成铁的工艺,称作直接炼铁(钢)法或者直接还原法,用这种方法生产出的铁也就称作直接还原铁(即DRI)。
由于这种铁保留了失氧时形成的大量微气孔,在显微镜下观察形似海绵,所以直接还原铁也称之为海绵铁。
一、直接还原铁(海绵铁)的用途直接还原铁是精铁粉在炉内经低温还原形式的低碳多孔状物质,其化学成分稳定,杂质含量少(碳、硅含量低),主要用作电炉炼钢的原料,也可作为转炉炼钢的冷却剂,如果经二次还原还可供粉末冶金用。
一次还原铁粉(海绵铁)的主要用途有:①作为粉末冶金制品的原料,耗用量约占铁粉总耗用量的60~80%;②作为电焊条的原料,在药皮中加入10~70%铁粉可改进焊条的焊接工艺并显著提高熔敷效率;③作为火焰切割的喷射剂,在切割钢制品时,向氧-乙炔焰中喷射铁粉,可改善切割性能,扩大切割钢种的范围,提高可切割厚度;④还可作为有机化学合成中的还原剂、复印机油墨载体等。
近年来由于钢铁产品朝小型轻量化、功能高级化、复合化方向发展,故钢材中非金属材料和有色金属使用比例增加,致使废钢质量不断下降。
废钢作为电炉钢原料,由于其来源不同,化学成分波动很大,而且很难掌握、控制,这给电炉炼钢作业带来了极大的困难。
如果用一定比例的直接还原铁(30~50%)作为稀释剂与废钢搭配不仅可增加钢材的均匀性,还可以改善和提高钢的物理性质,从而达到生产优质钢的目的。
因此,直接还原铁(海绵铁)不仅仅是优质废钢的替代物,还是生产优质钢材必不可少的高级原料(天津无缝钢管公司国外设计中就明确要求必须配50%的直接还原铁(海绵铁))。
根据国外报导,高功率电炉冶炼时,炉料搭配30~50%直接还原铁,生产率提高10~25%,作业率提高25~30%。
流化床竖式氢基还原铁
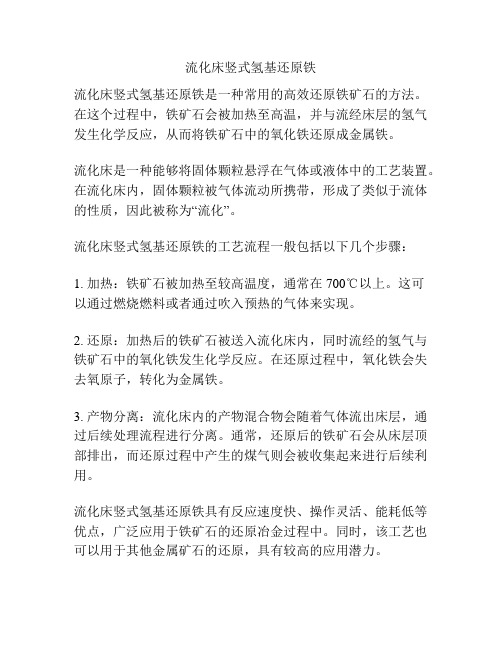
流化床竖式氢基还原铁
流化床竖式氢基还原铁是一种常用的高效还原铁矿石的方法。
在这个过程中,铁矿石会被加热至高温,并与流经床层的氢气发生化学反应,从而将铁矿石中的氧化铁还原成金属铁。
流化床是一种能够将固体颗粒悬浮在气体或液体中的工艺装置。
在流化床内,固体颗粒被气体流动所携带,形成了类似于流体的性质,因此被称为“流化”。
流化床竖式氢基还原铁的工艺流程一般包括以下几个步骤:
1. 加热:铁矿石被加热至较高温度,通常在700℃以上。
这可
以通过燃烧燃料或者通过吹入预热的气体来实现。
2. 还原:加热后的铁矿石被送入流化床内,同时流经的氢气与铁矿石中的氧化铁发生化学反应。
在还原过程中,氧化铁会失去氧原子,转化为金属铁。
3. 产物分离:流化床内的产物混合物会随着气体流出床层,通过后续处理流程进行分离。
通常,还原后的铁矿石会从床层顶部排出,而还原过程中产生的煤气则会被收集起来进行后续利用。
流化床竖式氢基还原铁具有反应速度快、操作灵活、能耗低等优点,广泛应用于铁矿石的还原冶金过程中。
同时,该工艺也可以用于其他金属矿石的还原,具有较高的应用潜力。
一种探究流态化还原铁矿粉反应机理的实验系统[实用新型专利]
![一种探究流态化还原铁矿粉反应机理的实验系统[实用新型专利]](https://img.taocdn.com/s3/m/045f5c3ec1c708a1294a4427.png)
专利名称:一种探究流态化还原铁矿粉反应机理的实验系统专利类型:实用新型专利
发明人:徐其言,任鑫,冉铭泽,毕枝胜
申请号:CN201720261816.9
申请日:20170317
公开号:CN206573509U
公开日:
20171020
专利内容由知识产权出版社提供
摘要:本实用新型的一种探究流态化还原铁矿粉反应机理的实验系统,属于冶金实验设备技术领域。
本实用新型包括双层管反应单元、加热单元和供气单元,外部套管固定于支撑平台的中部,反应内管套装于外部套管内部,且反应内管底部与外部套管底部相连通,该反应内管内设置有流化床筛板;所述的加热单元包括加热炉炉体,热炉炉体内设置有与外部套管相配合的加热炉炉膛,双层管反应单元与加热炉炉膛相配合;供气单元为流态化还原过程提供还原性气体。
本实用新型的供气单元可以模拟不同的还原气体成分,气体加热单元对还原性气体和铁矿粉进行加热,有效地模拟不同条件下的流态化还原铁矿粉的实验过程,为探究流态化还原铁矿粉的反应机理打下了基础。
申请人:安徽工业大学
地址:243002 安徽省马鞍山市花山区湖东路59号
国籍:CN
代理机构:南京知识律师事务所
更多信息请下载全文后查看。
流化床竖式氢基还原铁 -回复
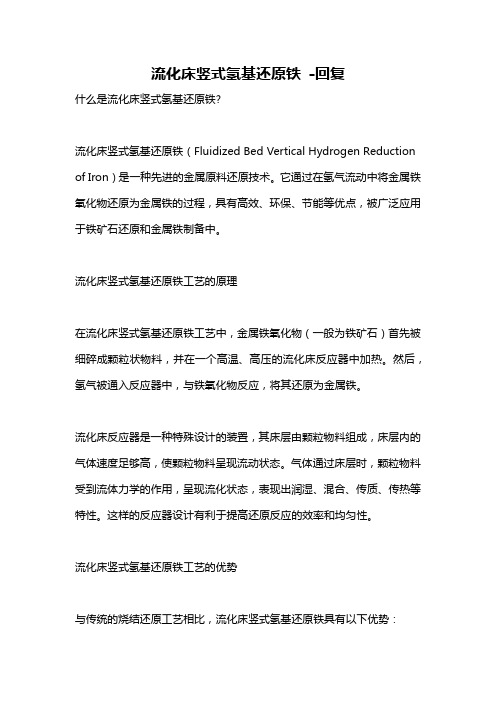
流化床竖式氢基还原铁-回复什么是流化床竖式氢基还原铁?流化床竖式氢基还原铁(Fluidized Bed Vertical Hydrogen Reduction of Iron)是一种先进的金属原料还原技术。
它通过在氢气流动中将金属铁氧化物还原为金属铁的过程,具有高效、环保、节能等优点,被广泛应用于铁矿石还原和金属铁制备中。
流化床竖式氢基还原铁工艺的原理在流化床竖式氢基还原铁工艺中,金属铁氧化物(一般为铁矿石)首先被细碎成颗粒状物料,并在一个高温、高压的流化床反应器中加热。
然后,氢气被通入反应器中,与铁氧化物反应,将其还原为金属铁。
流化床反应器是一种特殊设计的装置,其床层由颗粒物料组成,床层内的气体速度足够高,使颗粒物料呈现流动状态。
气体通过床层时,颗粒物料受到流体力学的作用,呈现流化状态,表现出润湿、混合、传质、传热等特性。
这样的反应器设计有利于提高还原反应的效率和均匀性。
流化床竖式氢基还原铁工艺的优势与传统的烧结还原工艺相比,流化床竖式氢基还原铁具有以下优势:1. 高效:流化床反应器内的颗粒物料呈现流动状态,与氢气充分接触,提高了反应效率。
同时,床层内的混合和传质作用也更加强化,进一步促进了还原反应的进行。
因此,流化床竖式氢基还原铁工艺的还原速度和还原率均较高。
2. 环保:流化床反应器内的气固分离相对完善,废气中的颗粒物料可以通过设备进行捕捉,减少了对环境的污染。
此外,流化床技术还可以实现二氧化硫和一氧化碳等有害气体的高效脱除,保护了环境和人员的健康。
3. 节能:流化床竖式氢基还原铁采用氢气作为还原剂,相较于传统的高炉工艺中使用的焦炭,氢气的燃烧能量更高,且燃烧产物纯净,不会对金属铁质量产生不良影响。
此外,流化床反应器利用床层内颗粒物料的加热即可达到高温要求,无需额外的能源消耗。
4. 可控性强:流化床竖式氢基还原铁工艺可以根据生产需要对反应温度、氢气流量等参数进行调控,实现对还原过程的精确控制。
高温流态化反应器中的钢铁冶炼仿真
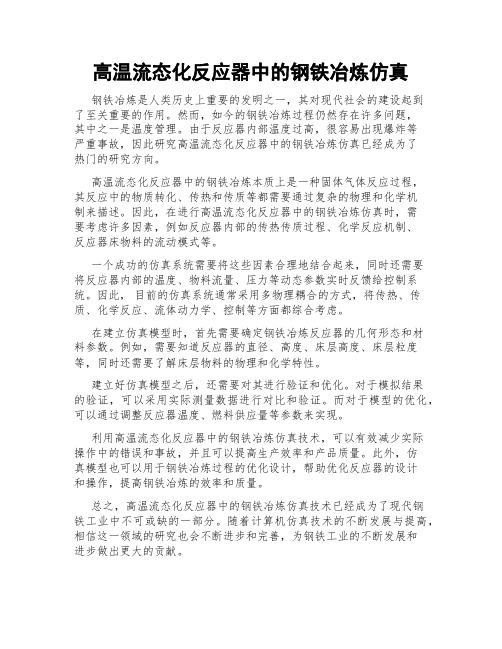
高温流态化反应器中的钢铁冶炼仿真钢铁冶炼是人类历史上重要的发明之一,其对现代社会的建设起到了至关重要的作用。
然而,如今的钢铁冶炼过程仍然存在许多问题,其中之一是温度管理。
由于反应器内部温度过高,很容易出现爆炸等严重事故,因此研究高温流态化反应器中的钢铁冶炼仿真已经成为了热门的研究方向。
高温流态化反应器中的钢铁冶炼本质上是一种固体气体反应过程,其反应中的物质转化、传热和传质等都需要通过复杂的物理和化学机制来描述。
因此,在进行高温流态化反应器中的钢铁冶炼仿真时,需要考虑许多因素,例如反应器内部的传热传质过程、化学反应机制、反应器床物料的流动模式等。
一个成功的仿真系统需要将这些因素合理地结合起来,同时还需要将反应器内部的温度、物料流量、压力等动态参数实时反馈给控制系统。
因此,目前的仿真系统通常采用多物理耦合的方式,将传热、传质、化学反应、流体动力学、控制等方面都综合考虑。
在建立仿真模型时,首先需要确定钢铁冶炼反应器的几何形态和材料参数。
例如,需要知道反应器的直径、高度、床层高度、床层粒度等,同时还需要了解床层物料的物理和化学特性。
建立好仿真模型之后,还需要对其进行验证和优化。
对于模拟结果的验证,可以采用实际测量数据进行对比和验证。
而对于模型的优化,可以通过调整反应器温度、燃料供应量等参数来实现。
利用高温流态化反应器中的钢铁冶炼仿真技术,可以有效减少实际操作中的错误和事故,并且可以提高生产效率和产品质量。
此外,仿真模型也可以用于钢铁冶炼过程的优化设计,帮助优化反应器的设计和操作,提高钢铁冶炼的效率和质量。
总之,高温流态化反应器中的钢铁冶炼仿真技术已经成为了现代钢铁工业中不可或缺的一部分。
随着计算机仿真技术的不断发展与提高,相信这一领域的研究也会不断进步和完善,为钢铁工业的不断发展和进步做出更大的贡献。
氢还原炼铁技术
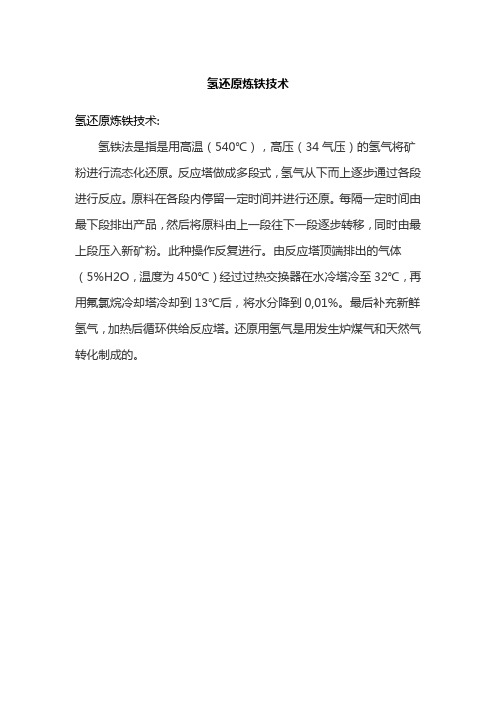
氢还原炼铁技术
氢还原炼铁技术:
氢铁法是指是用高温(540℃),高压(34气压)的氢气将矿粉进行流态化还原。
反应塔做成多段式,氢气从下而上逐步通过各段进行反应。
原料在各段内停留一定时间并进行还原。
每隔一定时间由最下段排出产品,然后将原料由上一段往下一段逐步转移,同时由最上段压入新矿粉。
此种操作反复进行。
由反应塔顶端排出的气体(5%H2O,温度为450℃)经过过热交换器在水冷塔冷至32℃,再用氟氯烷冷却塔冷却到13℃后,将水分降到0,01%。
最后补充新鲜氢气,加热后循环供给反应塔。
还原用氢气是用发生炉煤气和天然气转化制成的。
流态化技术在世界熔融还原工艺中的应用
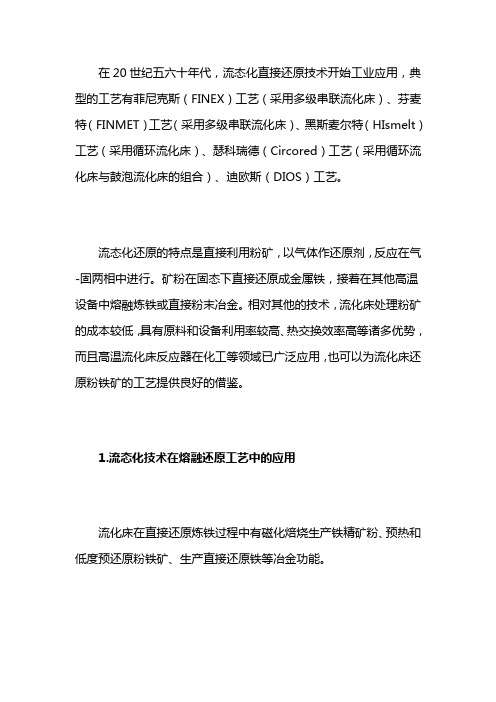
在20世纪五六十年代,流态化直接还原技术开始工业应用,典型的工艺有菲尼克斯(FINEX)工艺(采用多级串联流化床)、芬麦特(FINMET)工艺(采用多级串联流化床)、黑斯麦尔特(HIsmelt)工艺(采用循环流化床)、瑟科瑞德(Circored)工艺(采用循环流化床与鼓泡流化床的组合)、迪欧斯(DIOS)工艺。
流态化还原的特点是直接利用粉矿,以气体作还原剂,反应在气-固两相中进行。
矿粉在固态下直接还原成金属铁,接着在其他高温设备中熔融炼铁或直接粉末冶金。
相对其他的技术,流化床处理粉矿的成本较低,具有原料和设备利用率较高、热交换效率高等诸多优势,而且高温流化床反应器在化工等领域已广泛应用,也可以为流化床还原粉铁矿的工艺提供良好的借鉴。
1.流态化技术在熔融还原工艺中的应用流化床在直接还原炼铁过程中有磁化焙烧生产铁精矿粉、预热和低度预还原粉铁矿、生产直接还原铁等冶金功能。
1)磁化焙烧铁精矿粉磁化焙烧是将Fe2O3在还原气氛中焙烧得到磁化性的Fe3O4,经过磁选使Fe3O4与杂质分离,得到品位高的铁精矿。
1973年~1982年,为了开发攀枝花资源,我国进行了3次流态化还原综合回收钒钛铁的试验研究。
3次的试验结果表明,我国的流态化还原法在理论上是可靠的,工艺上是可行的,主体设备上是成功的,从而为向工业化过渡创造了条件。
2)预热和低度预还原粉铁矿流化床预热和低度预还原粉铁矿工艺中的典型代表是HIsmelt 工艺和DIOS工艺。
HIsmelt工艺正处于工业化开发阶段。
矿粉经过整粒筛分除去大颗粒矿粉后经皮带输送到矿石预热器中进行预热和初级预还原。
整粒筛分后的粒度小于6mm,预热后的矿粉温度可达700℃~800℃,预还原度为10%~11%,处理后的热矿粉装入热矿仓等待喷吹。
为了缓解铁浴炉的压力,可提高预热粉铁矿的还原度,但是粉铁矿只经一级循环流化床预热还原,其还原度一般不超过25%。
DIOS工艺的预还原采用快速流化床与沸腾流化床组合的复合型流化床系统。
- 1、下载文档前请自行甄别文档内容的完整性,平台不提供额外的编辑、内容补充、找答案等附加服务。
- 2、"仅部分预览"的文档,不可在线预览部分如存在完整性等问题,可反馈申请退款(可完整预览的文档不适用该条件!)。
- 3、如文档侵犯您的权益,请联系客服反馈,我们会尽快为您处理(人工客服工作时间:9:00-18:30)。
流态化还原炼铁技术
流态化(fluidization)是一种由于流体向上流过固体颗粒堆积的床层而使得
固体颗粒具有一般流体性质的物理现象,是现代多相相际接触的工程技术。
使用流态化技术的流化床反应器因具有相际接触面积大,温度、浓度均匀,传热传质条件好,运行效率高等优点而应用于现代工业生产。
高炉炼铁技术在矿产资源受限和环保压力增大等形势下,将面临着前所未有的挑战。
铁矿石对外依存度过高、铁矿石粒度越来越小和焦炭资源枯竭等状况,迫使人们加快步伐探索改进或替代高炉工艺的非高炉型炼铁工艺。
以气固流态化还原技术为代表的非高炉炼铁工艺逐步受到重视。
新工艺的建立和发展需要理论研究作为支撑。
目前国内对于流态化还原炼铁
过程中的气固两相流规律的认识还不够深入,特别是对不同属性铁矿粉的流态化特性、不同操作条件下的流态化还原特性,以及反应器结构对流态化还原过程的影响等相关研究还不够充分,基于流态化还原技术的新工艺要成熟应用于大规模工业生产还有明显距离。
发展流态化技术须重视基础研究
流态化技术可以把固体散料悬浮于运动的流体之中,使颗粒与颗粒之间脱离接触,从而消除颗粒间的内摩擦现象,使固体颗粒具有一般流体的特性,以期得到良好的物理化学条件。
流态化技术很早就被引入冶金行业,成为非高炉炼铁技术气基还原流程中的一类重要工艺。
流态化技术在直接还原炼铁过程中主要有铁矿粉磁化焙烧、粉铁矿预热和低度预还原、生产直接还原铁的冶金功能。
我国从上世纪50年代后期开始流态化炼铁技术的研究。
1973年~1982年,为
了开发攀枝花资源,我国进行了3次流态化还原综合回收钒钛铁的试验研究。
中国科学院结合资源特点对贫铁矿、多金属共生矿的综合利用,开展了流态化还原过程和设备的研究;钢铁研究总院于2004年提出低温快速预还原炼铁方法(FROL TS),并
随后对工艺流程进行了探索,取得一定效果。
除此之外,还有针对铁矿及铁氧化物微粉的低温还原特性的研究,探索了小粒径矿粉进行流态化还原的技术特点。
使用流态化技术的代表性非高炉炼铁工艺的床层结构、还原气和物料特性见附表。
流态床的预还原反应器中的铁矿粉等物料与还原气体在流态化过程中相互作用,其动力学行为可促进两相之间的动量、热量和质量交换,为铁矿粉的还原反应创造良好的条件。
为有效发挥流化床反应器的还原效果,开展气固两相流的理论研究很有必要,基础性研究成果将促进流态化技术发展及工业应用。
气固两相流相关研究进展
在流态化过程中,固体颗粒在流动的气体或液体中呈现悬浮状态,具有流体的性质,其状态受流体属性、固体颗粒属性、床体结构、操作条件和相间作用的影响。
物料属性对流化状态的影响。
研究颗粒及气体属性对流态化状态的影响具有重要意义,特别是对工业应用原料的制备和选取具有指导作用,从而使原料对流态化过程的不利影响降低到最小,并最大限度地服务于需要的流态化状态。
国外早在1947年就有研究人士用金刚砂研究了粒度和粒度分布对流化质量的影响,并作了定性的描述。
在针对不同平均粒径以及粒径分布对流化状态的影响研究中,得出的一般结论为:大粒子趋于增加流化的湍流强度,小粒子则趋于减弱流体的湍流强度,并且在粗粒床中加入细颗粒的作用是降低平均粒径从而改变与平均粒径有关的流化性质。
床体结构对流态化状态的影响。
在流态化反应器从实验室级试验到半工业试验直至工业生产规模试验的逐渐放大过程中,出现气泡的短路现象逐渐严重,气体反混逐渐加剧,致使反应选择性变差,转化率降低,不利于工业生产的进行。
而实践证明,通过合理的流化床反应器设计可以很好地改善这个问题。
流化床反应器的结构
形式很多,但一般由床层壳体、内部装置、换热装置、气固分离装置等组成,研究各个部分的工作特性,对控制床层内部状态和指导反应器设计具有重要意义。
为了适应工业生产需要,大型化、连续性、稳定性生产变得非常重要。
针对颗粒的还原度控制、还原气体的利用率提高、系统稳定经济高效的运行要求,流化床反应器趋向于循环流化床、多级流化床串联,鼓泡床、快速流化床、喷动床等多种流化床混合使用,各反应器相互独立又相互协作的方向发展,对流化床的设计和运行控制也提出了更高的要求。
流态化还原技术应用展望
随着适用于炼铁的优质铁矿资源不断减少、粒度越来越细,使用球团矿会增加生产成本,直接采用粉矿进行流态化还原成为炼铁技术发展中被考虑的一种重要途径。
该工艺可直接使用粉矿,省去传统的烧结、球团和炼焦流程,大大缩短铁前工序,有利于环境保护和资源综合利用,而且拥有高的换热、传质和输送效率,因其理论上的经济可行性与传统高炉工艺形成鲜明对比而备受关注。
目前开发成功并已工业化的FINEX工艺,采用了4级(或3级)串联的流化床预还原反应器,进行铁矿粉的预热和预还原,再进行压块或终还原。
无论是FINEX工艺,还是其他处于开发阶段、半工业化或小型工业化的流态化还原工艺,最常出现的问题包括:颗粒黏结,导致传输线堵塞和流态化效果损失;不能处理精矿大小的细颗粒;淘析损失和粉尘俘获效率低等。
此外,气体利用率低、气体循环消耗的能量高、产品的均匀度低等问题也有待解决。
于是,现有流化床反应器的流程(FINMET、FINEX、Circored)比气基竖炉(Midrex、HYL-III)更难控制和实现大型化工业应用。
因此,研究颗粒属性对流化特性的影响,对指导特定流化特性要求的生产工艺
的物料选择和制备具有重要意义。
而合理的床体结构和内部构件设计可以有效地改善流态化过程中气体的分布和气泡状态,是流化床反应器的放大及工业化应用的重要前提。
对于流态化还原的炼铁技术发展而言,须要进一步开展理论与实验研究,可借
助物理模型和数值模拟,研究不同粒径及分布、不同微观性质、不同成分与密度的铁矿粉的流化过程及性质,得出铁矿粉属性与流化性质的相互关系;研究针对铁矿粉流化的不同床体形状及尺寸和内部构件如分布板、气泡控制部件等对铁矿粉流化流态的影响,研究黏结失流产生的原因和条件,寻求适于铁矿粉流化的床体设计的变量和参数,以及改善内部流体力学条件的适宜的物理量及参数、多级流化床反应器或不同流型的流化床反应器的衔接参数等。
铁矿粉在流态化状态下表现出的动力学特性与传统铁矿粉还原的差异,以及不同还原条件(如温度、压力、气体成分组成等)对流态化还原过程的影响也同样值得进一步研究,以确定铁矿粉流态化还原的热力学和动力学适宜条件,避免黏结失流,并提高还原气体利用率和生产效率等。
还须研究反应器的放大问题,提出系
列有关流化床反应器的设计及运行优化的控制参数,以适应新工艺的发展要求,促进我国流态化还原炼铁新工艺的工业化应用。