精益生产8WorldClassManufacturing-(世界级制造精益生产)PPT课件
精益生产名词解释
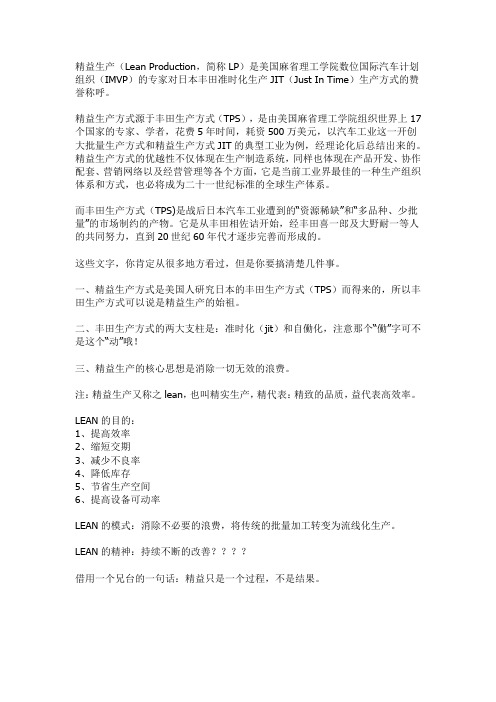
精益生产(Lean Production,简称LP)是美国麻省理工学院数位国际汽车计划组织(IMVP)的专家对日本丰田准时化生产JIT(Just In Time)生产方式的赞誉称呼。
精益生产方式源于丰田生产方式(TPS),是由美国麻省理工学院组织世界上17个国家的专家、学者,花费5年时间,耗资500万美元,以汽车工业这一开创大批量生产方式和精益生产方式JIT的典型工业为例,经理论化后总结出来的。
精益生产方式的优越性不仅体现在生产制造系统,同样也体现在产品开发、协作配套、营销网络以及经营管理等各个方面,它是当前工业界最佳的一种生产组织体系和方式,也必将成为二十一世纪标准的全球生产体系。
而丰田生产方式(TPS)是战后日本汽车工业遭到的“资源稀缺”和“多品种、少批量”的市场制约的产物。
它是从丰田相佐诘开始,经丰田喜一郎及大野耐一等人的共同努力,直到20世纪60年代才逐步完善而形成的。
这些文字,你肯定从很多地方看过,但是你要搞清楚几件事。
一、精益生产方式是美国人研究日本的丰田生产方式(TPS)而得来的,所以丰田生产方式可以说是精益生产的始祖。
二、丰田生产方式的两大支柱是:准时化(jit)和自働化,注意那个“働”字可不是这个“动”哦!三、精益生产的核心思想是消除一切无效的浪费。
注:精益生产又称之lean,也叫精实生产,精代表:精致的品质,益代表高效率。
LEAN的目的:1、提高效率2、缩短交期3、减少不良率4、降低库存5、节省生产空间6、提高设备可动率LEAN的模式:消除不必要的浪费,将传统的批量加工转变为流线化生产。
LEAN的精神:持续不断的改善????借用一个兄台的一句话:精益只是一个过程,不是结果。
附:丰田生产方式的起源:20世纪初,从美国福特汽车公司创立第一条汽车生产流水线以来,大规模的生产流水线一直是现代工业生产的主要特征。
大规模生产方式是以标准化、大批量生产来降低生产成本,提高生产效率的。
这种方式适应了美国当时的国情,汽车生产流水线的产生,一举把汽车从少数富翁的奢侈品变成了大众化的交通工具,美国汽车工业也由此迅速成长为美国的一大支柱产业,并带动和促进了包括钢铁、玻璃、橡胶、机电以至交通服务业等在内的一大批产业的发展。
世界级制造

20世纪70-80年代是美国经济受到日本的冲击处于的低潮时期,美国人突然发 现他工业“老大”的地位已经不复存在了。在日本企业竞争的压力下,处于危 机状态的美国人大量的研究日本制造技术。冷战结束,全球经济形成,更加剧 了企业间的竞争。这正是对传统反思、并发新思想火花的时期。于是从80年代 末开始,出现了一批新的、与美国传统大量生产模式的科学管理原则相对立的 新管理思想。如:
对全面质量管理的定义为: 一个组织以质量为中心,以 全员参与为基础,目的在于 通过让顾客满意和本组织所 有成员及社会受益而达到长 期成功的管理途径。
其特点:三全一多样,即: 全过程、全员、全企业、采 用多种方法进行质量管理活 动
其基本思想为: ①顾客观点 ②以顾客为中心的职责 ③PDCA循环 ④以事实为依据(三现主义) ⑤确定管理或改进项目 ⑥过程的管理及改善 ⑦自律的日常管理 ⑧自发的方针管理 ⑨QC工具的应用
制造”概念迈出的第一步。
1986年,施恩伯发布了《世界级制造:简化应用经验》的著作。他根据100
家美国著名企业,实行日本生产方式成功经验的第一手资料,说明管理技 术在美国移植成功。施恩伯将当时的日本生产方式定位为“世界级制造 World Class Manufacturing”,成功实施日本简化技术的企业是世界级制 造企业。从而打造了“世界级制造”的术语和概念。
Perfect 完美
没有任何事物 是完美的 不断改进
Value 价值
站在客户 的立场上
Lean Manufacturing
精益生产
Value Stream 价值流
从接单到发货 过程的一切活动
精益生产WorldClassManufacturing世界级制造精益生产

生产方式 项目
产品特点
手工生产方式
完全按顾客要求
设备和工装
通用,灵活,便宜
大批量生产方 式
标准化品种单一
专用,高效,昂贵
精益生产方式
品种多样,系列化 柔性高,效率高
分工与作业内容 操作工人 库存水平 制造成本 产品品质 市场需求
粗略,丰富多彩
细致,简单,重复
懂设计制造,具有 高操作技艺
高
不需专门技能 高
• 领班:生产力改进;成本降低 • 主管:生产控制,作业标准,质量控制,
培 训,安全, • 经理:目标方针,资源配备,系统优化
高层管理 中层管理 基层管理 作业人员
1 Lean Manufacturing System Briefing 精益生产系统简介 ➢ 制造系统的要点
➢ 市场竞争及全球化
➢ 精益生产五项原则
• Ongoing efforts to improve Quality, Productivity, and Responsiveness
• Recognition of employee abilities
• 消除浪费 • 不断改进 • 员工参与
• Builds on synchronous manufacturing
• Capable plants linked to lean concepts
• 改善整个价值链 • 节点上连着精益工
厂
大批量生产方式的致命弱点
1. 库存量高 2. 生产周期长 3. 返修率高 4. 员工工作单调、积极性低 5. 制造系统缺乏弹性,反应速度慢 6. 阻碍知识和能力的发挥
三种生产方式的比较
1997 IWeek Survey of 2,900 manufacturers 1998 IWeek Survey of 2,100 additional manufacturers
精益生产(完美版)
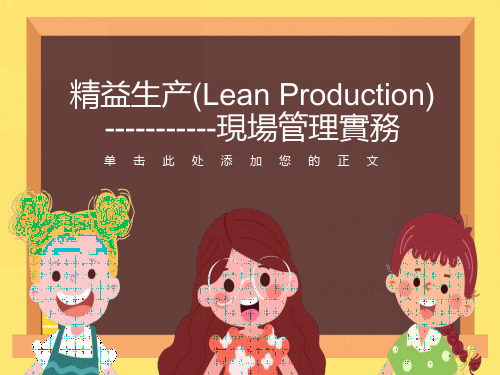
No.2 确定设计、采购和生产产品的整个价值流中的 步骤,找出不增加价值的浪费;
No.3 使那些创造价值的步骤流动起来,没有中断、 迂回、回流、等待和废品;
No.4 仅仅即时地按顾客的需求拉动价值流;
No.5 通过层层发现,由表及里地消除浪费,从而寻 求达到完美的境界。
1
☆ 作业顺序一致化 ☆ 逆时针方向操作 ☆ 进行适当的作业组合 ☆ 明确作业循环时间 ☆ 明确在制品数量
①.
物流 顺畅
☆ 一头一尾存货, 中间均衡快速流动 ☆ 考虑线与线之间的 库存放置、搬运方法 和搬运路径 ☆ 前后生产线尽量靠拢
01
零切换浪费 零库存 零浪费 零不良 零故障 零停滞 零事故
02
7个“零”目标
7个“零”目标
零目标
目的
现 状
思考原则与方法
零 切换 浪费
多品种 对应
切换时间长, 切换后不稳定
· 经济批量 · 物流方式JIT · 生产计划标准化 · 作业管理 · 标准化作业
零 库存
单件流动
配置 作业人员
维持管理
样 板 制 作
12步迈向无人化
流线生产的布置要点
保证标准作业
避免物流浪费
考虑信息流动
便于设备维护
少人化生产
确保全数检查
确保作业安全
整体布置协调
标准 作业
保证标准作业—— 避免:制造过多的浪费 步行距离的浪费 手动作业的浪费
能力 提升
(2)个别效率与整体效率
项 目
工序1
工序2
工序3
工序4
能 力
100件/H
125件/H
80件/H
100件/H
达成率
精益生产
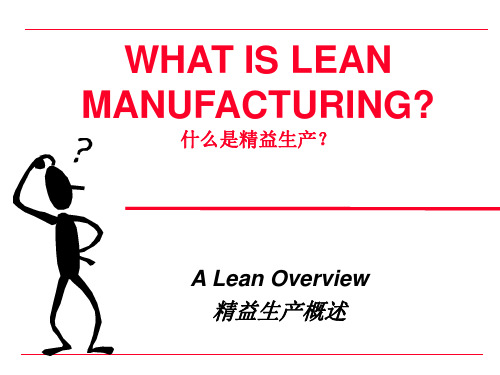
什么是精益生产?
A Lean Overview
精益生产概述
TOPICS 主题
• Lean History 精益历史 • Lean Defined & Key Concepts 精益定义及关键概念 • The Lean Techniques 精益技术 • The Leanest of the Lean 精益精髓 • Report Card of Lean in the U.S.A. 精益在美国的业绩
7
DEFINING LEAN 定义精益
“A systematic approach to identifying and eliminating waste (non-value-added activities) through continuous improvement by flowing the product at the pull of the customer in pursuit of perfection”
If NO 如果不是
Can it be eliminated?是否能消除? If not, can it be reduced? 如果不是,是否可减少
NOTES: Be sure to include all the wasteful activities that occur “occasionally.” 注意:确定包括了所有的” 偶而“发生的浪费行为“
精益生产=消除浪费
• Overproduction • 生产过剩 • Defects 缺点 • Non-value added • 无附加值 • Processing处理 • Waiting 等待 • Underutilized • 未充分使用 • People人员 • Excess motion过剩动作 • Transportation运输 • Excess inventory超额库存
精益生产知识介绍

精益生产知识介绍什么是精益生产?精益生产是一种管理方法,旨在通过最小化浪费和提高效率来改善生产过程。
它起源于日本汽车制造业,最早由丰田汽车公司引入并在世界范围内推广。
精益生产的目标是实现在不断变化的市场需求下提供高质量产品的同时,尽量降低成本和提高生产速度。
精益生产原则精益生产基于以下几个关键原则:1.价值:只有为客户创造价值的活动才是有意义的,其他无价值活动应尽量减少或消除。
2.价值流:识别生产活动中的价值流程,并尽量消除非价值流程。
3.拉动:按需生产并以客户需求为导向,避免过度生产和库存。
4.流程:通过优化生产流程,实现高效率和高质量的生产。
5.完美:不断追求完美,通过持续改进来实现精益生产的长期目标。
精益生产的关键工具和技术在实施精益生产方法时,有几个关键的工具和技术可以帮助企业实现改进和优化。
5S5S是精益生产中的一个基本方法,用于改善工作环境和提高效率。
它由以下五个步骤组成:1.整理 (Sort):清理工作区,只保留必要的工具和设备。
2.整顿 (Straighten):为工具和设备设定固定的位置,以便于查找和使用。
3.清扫 (Shine):保持工作区清洁整洁,减少污垢和垃圾的积累。
4.标准化 (Standardize):制定标准化工作程序,并确保所有人遵守。
5.坚持 (Sustain):维持5S方法的持续改进,并培养良好的工作习惯。
持续改进持续改进是精益生产的核心原则之一。
通过定期的反思和分析,不断寻找优化生产过程的机会,并取得持续的增量改进。
常用的持续改进工具包括:•PDCA循环:计划(Plan)- 执行(Do)- 检查(Check)-行动(Act)的循环,用于系统性地实施和评估改进措施。
•Kaizen活动:指定特定的时间段,集中进行改进工作,并利用团队的智慧来解决问题和提出改进建议。
价值流映射价值流映射是一种从整体上分析和优化生产流程的方法。
通过绘制价值流图,可以识别出活动的流程和时间,并找出潜在的浪费。
世界级制造 造世界级产品

世界级制造造世界级产品作者:来源:《驾驶园》2016年第04期为向用户提供更高品质的重卡产品,50余年来,红岩汽车一直秉承着专注、专业、专一的“工匠精神”。
在新的发展进程中,自2012年开始,进一步引进了菲亚特全球WCM世界级制造管理体系。
全面提升了公司的综合制造水平,促进了生产系统性能的彻底改善,把高品质的重卡产品交付用户手中。
WCM——即World Class Manufacturing“世界级制造”,是菲亚特·克莱斯勒集团在全球各个工厂所制定的一种管理体系。
它是贯穿于产品设计、制造全过程的一套集成了众多精益管理工具的体系性方法。
包括人员管理、生产设备与流程,以及物流管理在内的顶级质量和技术,以实现零事故、零错误、零库存、零故障。
WCM也是菲亚特在全球所推广的包括人员培训、制造工艺、技术以及质量管理在内的一套制造方面的管理体系。
WCM管理体系当中有一个非常重要的工具,其对于工艺及质量稳定性的提升起着举足轻重的作用,它就是“4M1D”,即Man(人)、Machine(机)、Material(料),Methods (法)、Design(设计)。
·Man(人),标准操作,避免出错Man(人),即对于所有由人完成的生产操作,都要按工艺规范要求,细化至每个工位步骤及设备操作,编制相应的SOP(标准操作流程书),让操作者能够清晰、明确地按照标准指导完成操作,避免错装、漏装等现象。
·Machine(机),自主维护,提升设备综合效率Machine(机)。
关于设备机器,采用CILR及设备台账方式进行周期维护,CILR,即清洁(C1ean),检查(Inspect),润滑(Lubricate),紧固(Refasten),通过定点目视化。
帮助设备操作者高效有序地完成自主维护,提升设备基础条件。
另外专业维修团队结合现场设备台账,固定时间、固定频率地对设备进行点检,可有效预防设备故障,提升设备综合效率,保障生产。
顾问必须熟悉的ERP专业术语-中英及缩写对照

CAM (computer-aided manufacturing) 计算机辅助制造
CIMS (computer integrated manufacturing system) 计算机集成制造系统
critical ratio 紧迫系数
B字母
back scheduling 倒排计划
backflushing 反冲法
BOR (bill of resource) 资源清单
business plan 经营规划
batch process 批流程
bottleneck 瓶颈资源(工序)
back order 脱期定单
backlog 拖欠定单
美国生产与库存管理系统
agile manufacturing 敏捷制造
APICS Applied Manufacturing Education Series 实用制造管理系列培训教材
AMT (Advanced Manufacturing Technology) 先进制造技术
anticipation inventory 预期储备
planning BOM 计划物料单
proposed cost 建议成本
picking list 领料/提货单
parent item 母件
Pareto Principle 帕拉图原理
production cycle 生产周期
production activity control 生产作业控制
MRP (material requiremants planning) 物料需求计划
精益生产的发展与变迁

BPS
Bosch Production System
TPS
Toyota Production System
WCM
GM-GMS
Global Manufacturing
System
FIAT
FIAT World Class Production System
MPS
Mercades Production System
支援体系:生产技术研究所、工程技术、物流部
制造生产线革新
• 内置化生产线构筑 • 进化的cell房 • Multi LCA适用
物流革新
• 根据SCM的库存管理 • 仓库运营方法 • 物流模拟试验
制造基本革新
• 浪费去除 • LOB提高 • 作业环境改善
一、世界级制造——工业4.0 & 工业互联网
计算能力、信息提取和交流系统所带来的改变,已经在制造业中“肆虐”。关于这样一个新时代的表述 不尽相同:德国称其“工业4.0”(Industry4.0),美国则更多地将之概况为颇为宏大的概念“工业 互联网”(Industrial Internet)。实际上,无论叫什么名字,本质上都是信息技术与工业技术的高 度融合,表述的是网络、计算机技术、信息技术、软件与自动化技术的深度交织所产生新的价值模型。
一、世界级制造——工业4.0 & 工业互联网
工业 4.0的基本特征
智能机器:用先进的传感器、控制和软件应用等新方式连接大量的机器、设备等; 先进的分析能力:基于物理的分析、预见性算法、自动化和材料科学的专业领域知识,
电力工程和其他重点学科,这些都有助于理解机器和系统的运作; 工作中的人:让工作中的人无论身处工厂、办公室、医院还是移动中,都可以高质量、
精选精益生产课件

计算如下: 60m / h 60s / h 21.2units / h 170s / unit 80units / h 3.8 21.2units / h
(取4个工作台,尚有生产能力剩余)
规划精益生产单元的布置。
实际设计生产精益生产单元时,可以考 虑设置两个铣、钻、磨加工区,每个加 工区由两个工作台组成,每个工作台配 备一个工人
生产指定产品每道工序的单位加工时间:
工序 加工时间(秒)工序 加工时间(秒)
铣(M) 80
装配线1 80
钻(D) 30
装配线2 180
磨(P) 60
包装 30
现对其进行精益化改造 经调查: 1.铣、钻、磨床尚有剩余生产能力,因
此在不影响其它生产条件下,可进行 适当调整 2.所有装配线和包装依靠手工完成,只 需提供工作台和工具
消除零件不必要的移动
生产布局合理是造成零件往返搬动的 根源,使得生产线长,生产周期长,占 用很多在制品库存,增加生产成本
按加工顺序安排设备,尽可能紧凑,消 除不必要的移动,节约生产时间
消灭库存 精益生产对库存的看法: 1、会掩盖许多生产问题 2、会滋长工人的惰性 3、占用大量的资金
因此,库存是最大的浪费,必须消灭
看待库存
是必要的
是万恶之源
业务观 严格分工和控制 相互协作,流程精简
质量观 次品是必然的
零缺陷
人
附属于岗位
强调能动性、协调
精益生产的实施方法
如何改进生产流程
消除检验和返工 把防错技术(POKA YOKE)的思想贯穿 到整个生产过程 从产品设计开始就把质量问题考虑进去, 保证每种产品只能严格地按照正确的方 式加工和安装,避免生产流程中可能发 生的错误
从精益生产到世界级制造

从精益生产到世界级制造一、精益生产的概念和原则精益生产(Lean Production)是一种通过消除浪费来实现高效、高质量生产的管理方法。
它起源于日本的丰田汽车公司,通过优化生产流程、提高效率和质量,最大限度地满足客户需求,同时降低成本。
精益生产的核心思想是不断改进和持续学习,以整体的观点来看待生产过程,使整个组织变得更加敏捷和灵活。
精益生产的原则包括:•价值流思维:从客户需求出发,明确产品的价值流,了解每个环节的价值和浪费,优化价值流程。
•一次做对:在生产过程中,确保一次就做对,避免因为不良品而造成重复工作和浪费。
•流程平衡:通过平衡各个生产环节的工作量,改善生产流程的连贯性和效率。
•持续改进:不断寻找改进的机会,并迅速采取行动,以提高效率和质量。
二、精益生产的实施步骤精益生产的实施通常包括以下几个步骤:1. 确定价值流首先,需要明确产品所承载的价值是什么,审视整个生产流程,找出每个环节的价值和浪费。
通过价值流图的绘制,可以清晰地看到价值流程中的瓶颈和浪费,为后续的改进提供方向和依据。
2. 消除浪费在明确了价值流之后,重要的是要确定并降低各种类型的浪费。
典型的浪费包括等待、库存过多、过度生产和不必要的运输,它们都会增加成本并降低生产效率和质量。
通过改进流程、减少库存和优化运输方式等措施,可以逐步消除浪费。
3. 精细化生产流程精益生产要求生产流程的精细化和流程的平衡。
通过设立标准作业流程、优化工作站布局、合理分配工作量等方式,可以提高流程的连贯性和效率。
4. 培养团队和改善文化成功的精益生产实施需要培养一个团队合作的文化,激发团队成员的创造力和主动性。
定期的培训和改进活动,可以帮助员工不断学习和提高,形成持续改进的风气。
三、精益生产的优势和挑战精益生产具有以下几个优势:•提高生产效率:通过消除浪费和优化流程,精益生产可以显著提高生产效率,降低生产成本。
•提高产品质量:精益生产注重一次做对,通过精细化流程和标准化作业,可以减少产品缺陷,提高产品质量和可靠性。
世界级制造
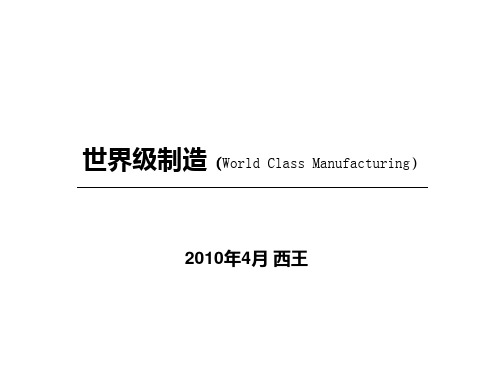
客户和持续改进是世界级制造的核心
持续改进的观点
“精益”和“世界级”的持续改进都是从日本的kaizen演变来 的。在精益思想中,持续改进既是基本方法,又是精益思想的基 础和总结。 在世界级制造:简化应用的经验(以后我们简称为世界级制造I) 这本书的第一章,施恩伯用了一个很怪的标题: “更快、更高、 更强”。世界级制造就是“持续地和及时的改进!”。“如果你 的企业以世界级制造为目标,你企业的座右铭就是“持续地和及 时的改进!”。所以世界级制造是组织和激励企业永不满足和不 断进步的概念。这是理解世界级制造概念的关键,世界级制造不 是某项“世界第一”的静止状态
Perfect 完美
站在客户 的立场上
Value Stream 价值流
没有任何事物 是完美的 不断改进
Lean Manufacturing 精益生产
从接单到发货 过程的一切活动
三、术语 1、拉动 2、生产均衡或平准 3、JIT 4、 标准作业 5、 自働化 6、KAIZEN 7、
Demand Pull 需本原则
8
LM - Lean Manufacturing精益生产
精益生产所追求的是对
衡量制造业绩效的各方 面项目的共同改善,是 通过贯穿在一系列行动 中的消除浪费的行动来 实现的;这些行动包括: 改变生产车间的工作组 织架构,将物流和生产 控制贯穿到供应链中, 以及将人力的方法应用 到生产和辅助工作中去 等等
BTR-按需求生产
象开发的河流 一样通畅流动
Flow 流动
VSM 8、七大浪费 9、Andon(安灯)系 统 10、看板 11、节拍 12、U型生产线 13 、 同 步 生 产 14 、 柔 性 制 造 15 、 SMED(快速切换) 16、PDCA 17、 多能工 18、VCS 19、5S 20、QC 21、一个流生产 22、小组活动……
精益生产的发展与变迁

世界级制造总准则: 准则1:依照客户或产品族成立团队,团队中包含客户代表 准则2:获得和运用有关客户、竞争力分析和最佳实践的信息资料 准则3:专注于在质量、快速反应、柔性、价值方面持续与快速的改善
准则4:一线员工参与到所有的变革和战略规划活动内以协助实现企业一致的目标
一、世界级制造
全世界中具有竞争力的制造业生产方式 和相关企业的经营者领导力,独特的文化 等相结合而形成的制造系统。 先进企业为了达成World Class Manufacturer,已经构筑了固有的生产方 式。 根据各国文化、技术积累、产业集群和民 族性格等特点,形成了各国的精益生产方 式。世界级制造和精益制造最终融合到了 一起,形成21世纪企业在竞争获胜的新的 强大武器——世界级制造将成为二十一世 纪优秀制造的新标准。
詹姆斯·沃麦克
二、精益生产的定义
2. 精益生产的演进史
1989,沃麦克教授出版 《改变世界的机器》一 书,在书中首次详细描 述和介绍了精益生产方 式,宣布精益生产方式 的原理同样可以用于全 世界每一种行业。 1996年,出版《精益 思想》,总结出精益 生产方式的5个基本原 则,将精益方式扩大 到制造业意外的所有 领域 沃麦克教授开始将精益思想 发展至消费者与供应链的问 题解决上——解决消费者和 供应商的问题,他将“精益 消费”和“精益供应”联结 为一体,塑造了一种全新的 强有力的竞争模式。
高层
系统层次
中层
工具与技术层次
5S,看板,JIT,快速换模,目视化, • 利用精益工具和方法进行点滴改善 标准化,安灯,QCC,PDCA,QCD, 价值流图,PMC,TPM等
基层
3. 推进精益三个阶段
阶段一:准备阶段 创造精益变革环境
• 产生紧迫感。识别并 讨论挑战和危机、公 司现状及机会,创造 紧迫感,转变意识; • 建立领导联盟。建立 一个由一把手挂帅的、 来源广泛的领导联盟 来统领变革协同作战; • 打造愿景规划。建立 公司的愿景规划指导 精益变革,设计实施 这一愿景的战略规划。
TPM管理培训

「故障」 故障」
.灰尘、污垢、原料粘着 .磨耗、松动、松弛、漏 .腐蚀、变形、刮伤、龟裂 .过热、振动、噪音等
突发损失的来源
慢性损失的来源
上图所见是量变到质变的演化过程, 上图所见是量变到质变的演化过程,水面之下正是因为我们忽略 日常保养、防护细节所致的损失。 日常保养、防护细节所致的损失。
MP设计检讨书范例
设备 名称 编号 改善 处数 现状 改善目的 以往不适点 代号 內容 主因 直進下 料桶 過長 振動子 不适应 改善內容 缩短下料 桶长度 振动子改 善 标准化 检讨 标准化 简图
MP设计检讨书
主管
作者
1
下料桶料流 动性不好
A
直进下料桶在 整体中,流动 性不佳的场合 多
A:信赖性(可靠性) B:安全 C:作业、操作性
P:Productivity Q:Quality C:Cost S:Safety D:Delivery M:Morale
TPM的目标实现图 TPM的目标实现图
改善 人的体质
我是制造的人 你是维修的人
PQCDSM
改善 企业体质 比设备 强的人 创 造 充 满 活 力 工 厂
自己的设备自己来保全
保全 运转 部门 部门
一
TPM的定义 1 TPM的定义
TPM基本知识 TPM基本知识
TPM是源于日本现代设备管理维护制度,它是以达到最高的设备 综合效率为目标,确立以设备生命周期为对象的生产设备维护全系统, 涉及设备的计划、使用、维修等所有部门,从最高领导到第一线工人 全员参加,依靠开展小组自主活动来推行的生产维护。
建立对设备整个寿命周期的生产维护 设 备 综 合 效 率 最 高
定义
精益制造
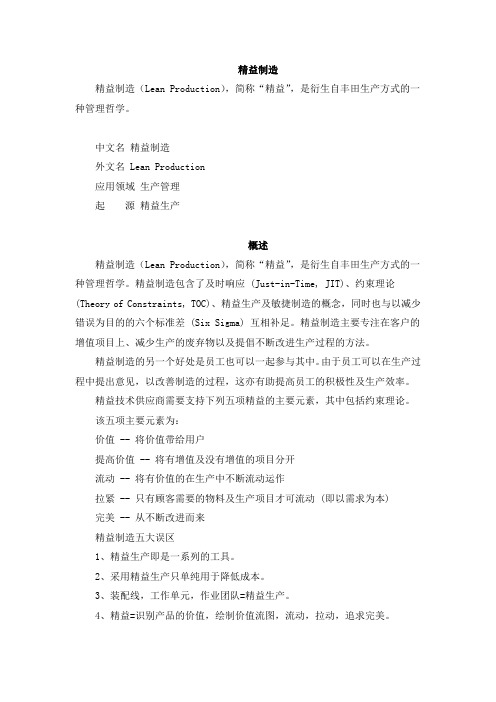
精益制造精益制造(Lean Production),简称“精益”,是衍生自丰田生产方式的一种管理哲学。
中文名精益制造外文名 Lean Production应用领域生产管理起源精益生产概述精益制造(Lean Production),简称“精益”,是衍生自丰田生产方式的一种管理哲学。
精益制造包含了及时响应 (Just-in-Time, JIT)、约束理论(Theory of Constraints, TOC)、精益生产及敏捷制造的概念,同时也与以减少错误为目的的六个标准差 (Six Sigma) 互相补足。
精益制造主要专注在客户的增值项目上、减少生产的废弃物以及提倡不断改进生产过程的方法。
精益制造的另一个好处是员工也可以一起参与其中。
由于员工可以在生产过程中提出意见,以改善制造的过程,这亦有助提高员工的积极性及生产效率。
精益技术供应商需要支持下列五项精益的主要元素,其中包括约束理论。
该五项主要元素为:价值 -- 将价值带给用户提高价值 -- 将有增值及没有增值的项目分开流动 -- 将有价值的在生产中不断流动运作拉紧 -- 只有顾客需要的物料及生产项目才可流动 (即以需求为本)完美 -- 从不断改进而来精益制造五大误区1、精益生产即是一系列的工具。
2、采用精益生产只单纯用于降低成本。
3、装配线,工作单元,作业团队=精益生产。
4、精益=识别产品的价值,绘制价值流图,流动,拉动,追求完美。
5、精益是最新的管理风尚。
精益制造的起源丰田公司在探索新的生产模式的过程中发现,小批量生产比大批量生产成本更低,而造成这种现象的原因有两个:第一,小批量生产不需要大批量生产那样大量的库存、设备和人员;第二,在装配前,只有少量的零件被生产,发现错误可以立即更正。
根据后一个原因,丰田得出结论,应该将产品的库存时间控制在两小时以内,这就是准时生产(jit)和零库存的雏形。
事实上后来jit生产还推广到与合作伙伴之间的合作,确定了这种模式下制造企业与合作伙伴之间亲密的依赖关系。
- 1、下载文档前请自行甄别文档内容的完整性,平台不提供额外的编辑、内容补充、找答案等附加服务。
- 2、"仅部分预览"的文档,不可在线预览部分如存在完整性等问题,可反馈申请退款(可完整预览的文档不适用该条件!)。
- 3、如文档侵犯您的权益,请联系客服反馈,我们会尽快为您处理(人工客服工作时间:9:00-18:30)。
培 训,安全, • 经理:目标方针,资源配备,系统优化
高层管理 中层管理 基层管理 作业人员
9
1 Lean Manufacturing System Briefing 精益生产系统简介 ➢ 制造系统的要点 ➢ 市场竞争及全球化 ➢ 精益生产五项原则 ➢ 最好的工厂?
3
Operational Management System 生产管理系统
投入
Input
Demand forecast Material Requirement Planning Inventory Control Purchasing plan Logistics etc...
Quality system Communication Quality control. etc...
Feed back
反馈
产出
Process
转换
Production schedule Production execution Equipment maintenance Process control Yield improvement Cost reduction Process improvement etc...
6
现代生产管理的主要方法
r 制造资源计划(MRP-II)
r 准时化生产(JIT)
r 企业流程再造(BPR)
接受价值
供应商
创造 价值
价值链
提供价值
用户
7
现代生产管理的任务
Quality 质量
Cost 成本
SQDC
Safety 安全、士气
Delivery 交货
8
现代生产管理者的职责
• 组长:质量及不合格品的注意;生产线 停线的责任
Henry Ford • Assembly line mass production • Produce in high volume with low variety • Single skill
福特首创的装配线是大规模低品种生产方式的代表, 工人被当成工作的机器
Toyota Production System (TPS) • Just-In-Time Production (produce only what is needed) • Pull System • High variety to meet customers wants
Output
Quality Assurance Customer satisfaction Sales/Marketing Customer service/support etc...
4
Operational Management – Milestones 生产管理 – 里程碑
1910s
1930s 1940s 1950s 1970s 1980s
1990s
Scientific management, time study Assembly line Economic Order Quantity (EOQ) Quality Management, Sampling plan, statistics Linear programming PERT, CPM Computer, MRP JIT, TQC, CIM, CAD/CAM, Automation TOC/Bottleneck Analysis TQC Re-engineering Supplier Chain Management, SAP
F.W. Taylor Frank F.W. Harris H. Dodge
IBM Toyota
Goldratt ASQC/ISO M. Hammer SAP, Oracle
5
现代生产管理的特征
r 以用户为中心 r 产品品种多样 r 柔性生产体系 r 制造技术先进 r 追求国际标准 r 运用智能设备
起源于20世纪50年代丰田汽车公司,而在80年代中
期被欧美企业纷纷采用。随着微利时代的来临, 精益生产模式成为企业竞争的有力武器
11
精益生产的来历
1. 丰田生产方式的形成及其推广 2. 美国工业的困惑 3. 美国对丰田生产方式的研究 4. 精益生产方式的兴起
12
Manufacturing Evolution 制造系统演化史
模拟演练 讨论, 现场
2
World Class Manufacturing 世界级制造
WCM = LM + TQM + TPM + SCM + EI
WCM - World Class Manufacturing 世界级制造 LM - Lean Manufacturing 精益生产 TQM - Total Quality Management 全员质量管理 TPM - Total Preventive Maintenance 全员设备维护 SCM - Supply Chain Management 供应链管理 EI - Employee Involvement 员工参与
丰田系统是建立在准时化观念上的拉动 式生产模式,以应付小订单多品种的挑战
13
Key Points for Manufacturing System 制造系统要点
10
Байду номын сангаас
Lean Thinking and Lean Manufacturing System 精益思维和精益生产系统
Starting with Toyota in the late 50’s and
catching on in the mid – 80’s in the reminder of the industrial world, Lean Manufacturing has become a key strategy for manufacturers
World Class Manufacturing
世界级制造
Manfred Zhang
Jan,2004
1
What Shall We Talk…? 内容安排
• 简介 • 精益生产系统 LM • 现场管理及5S • 柔性生产单元 • 看板拉动系统 • 全员质量管理 TQM • 全员设备维护 TPM • 供应链管理 SCM • 团队建设 / 员工参与 EI