2020年(冶金行业)利用高温冶金性能试验指导高炉配矿研究
提高高炉炉料中球团矿配比,促进节能减排

提高高炉炉料中球团矿配比、促进节能减排(资料来源:冶金管理,王维兴)一、优化炼铁炉料结构的原则高炉炼铁炉料是由烧结矿、球团矿和块矿组成,各高炉要根据不同的生产条件,决定各种炉料的配比,实现优化炼铁生产和低成本。
世界各国、各钢铁企业没有一个标准的炼铁炉料结构,都要根据各企业的具体情况制定适宜的炉料结构,同时还要根据外界情况的变化,进行及时调整。
2017 年中钢协会员单位高炉的炉料中平均有13%左右的球团矿,78%烧结矿,9%块矿。
在高炉生产时,各企业要根据其具体生产条件下,实现科学高炉炼铁操作(满足炼铁学基本原理),完成环境友好、低成本生产的目的。
实现低成本炼铁的方法包括:优化配矿、优化高炉操作、设备维护完好、生产效率高。
而实现高产低耗就要高炉入炉矿含铁品位高,有优质的炉料,包括高质量烧结矿要实现高碱度(1.8-2.2倍)。
但炼铁炉渣碱度要求在1.0-1.1 倍,炉料就需要配低碱度的球团矿(或块矿)。
高炉生产实现低燃料比,要求原燃料质量要好(入炉铁品位要高、冶金性能好、低MgO 和Al2O3、低渣量、焦炭质量好、含有害杂质少等),成分稳定,粒度均匀等。
要实现资源的合理利用,就要合理回收利用企业内含铁尘泥等等资源。
建议将含有害杂质高的烧结机头灰、高炉布袋灰,加石灰混合,造球,干燥,给转炉生产用,切断炼铁系统有害杂质的循环富集。
此外,球团工艺相比烧结工艺具有一定的优越性:1)产品冶金性能一般来说,烧结矿综合冶金性能优于球团矿,因此,高炉炼铁炉料中以高碱度烧结矿(在1.8-2.2 倍)为主。
但是,炼铁炉渣碱度要求在1.0 左右,必须搭配一部分酸性球团矿,这样结构炉料的冶金性能才最优,使高炉生产正常进行。
球团矿的缺点是膨胀率高,易粉化。
目前,北美和欧洲一些高炉使用100%自熔性球团矿,冶金性能完全能满足高炉炼铁的要求,也取得了较好的高炉生产指标。
2)生产运行费用球团工序能耗是烧结的2/3,环保治理费用低,球团矿铁品位比烧结矿高5-9 个百分点(原料品位、碱度相同条件下),炼铁生产效益高10 元/t。
国家工信部批准的48项冶金行业标准(2020年1月1日起实施)(二)

2019年第3期新疆钢铁总151期6.YB/T 4143-2019《火花源原子发射光谱法测定固体金属均匀性检验方法》本标准适用于火花源原子发射光谱测量同批次下固体块状金属材料的均匀性。
本标准符合GB/T 15000.3标准样品定值的一般原则和统计方法。
主要是标准样品的应用开发,也可用于其它成批次(包括大批次和小批次,简称L/B )金属材料的均匀性测量,其结果是提供一个L/B 均匀性在室内或室间的综合性研究。
该试验的设计主要针对火花源原子发射光谱法金属L/B 中元素的均匀性检验,也可适用于其它仪器检测技术,如X 射线荧光光谱法(XRF )和原子吸收光谱法(AAS )代替标准:YB/T 4143-20067.YB/T 4144-2019《建立和控制原子发射光谱化学分析曲线规则》本标准规定了建立和控制原子发射光谱化学分析曲线的规则。
本标准适用于火花原子发射光谱,不适用于X-射线发射光谱。
尽管分析曲线的产生和日常控制运行关联,但是仍被看作是相互独立的。
因为计算机程序运行生成分析曲线的多元线性回归是责成的,村标准不再详细描述该过程,但是,还是给出了关于生成方程评估的一些推荐性规范。
代替标准:YB/T 4144-20068.YB/T4168-2019《焦炉用黏土砖及半硅砖》本标准规定了焦炉用黏土砖及半硅砖的分类及形状尺寸、技术要求、试验方法、质量评定程序、包装、标志、运输、储存和质量证明书。
本标准适用于焦炉用黏土砖、半硅砖,也可用于炭素炉、煤气发生炉和直立炉内衬用砖等。
代替标准:YB/T4168-20079.YB/T 4736-2019《锂电池用四氧化三锰》本标准规定了锂电池用四氧化三锰的术语和定义、技术要求、试验方法、检验规则、标志、包装、运输、贮存及质量证明书。
本标准适用于锂电池用四氧化三锰。
10.YB/T 4737-2019《炼钢铁素炉料(废钢铁)加工利用技术条件》本标准规定了炼钢铁素炉料(废钢铁)的术语和定义、分类、技术要求、交货条件、检验项目与检验方法、验收规则、运输和质量证明书等。
烧结配矿优化及高炉生产应对实践

M etallurgical smelting冶金冶炼烧结配矿优化及高炉生产应对实践张利波摘要:近些年,高炉炼铁一直是冶炼生铁过程中应用的最重要的技术,居于主导地位。
最近几年,全球的学者即使研究出许多高炉炼铁技术,不过在制作成本的经济性方面,依旧不能和以往的高炉制造技术进行比较。
国内,因为历史条件与制造成本的干预,非高炉炼铁技术的发展速度较慢,超过百分之九十五的生铁依旧借助高炉进行制作。
高炉生产期间,入炉原料重点是烧结矿、球团矿和块矿,而且烧结矿的比例高于百分之八十。
所以,烧结矿的品质高低在高炉生产过程中占据着主导作用,提升烧结矿品质对于缩减制作成本、保证高炉良好的运行具备着较高的作用。
关键词:烧结配矿优化;高炉生产;应对实践对策现如今使用的矿粉、矿石以及含铁工业物料等,使得烧结原料逐渐繁杂,如何通过原料的优化搭配实现品质最优、成本最优是钢铁生产重点关注的问题。
烧结矿是高炉的主要“口粮”,其质量的好坏直接影响高炉生产稳定和各项经济技术指标的完成。
为了确保烧结矿质量稳定,工作人员运用智能化手段,提升烧结配料精度,改善烧结矿质量,为高炉高效生产筑牢保障。
1 研究背景1.1 铁矿粉市场行情在我国环保政策高效实施的环境下,钢铁公司开始限制产量,铁矿石的需求数目逐渐下降。
不过在2017年~2018年鉴因为钢铁利润空间的变化,个别产能被释放,导致铁矿石的需求数目逐渐提升。
身为铁矿石的出产地澳大利亚与巴西境内铁矿石的出产量也随之增加,不过市场依然处于供需不平衡的状态,导致铁矿石的流通价格较高。
并且,因为持续的挖掘与应用优质资源,导致地球上的优质铁矿石数量逐步的减少,铁矿石供需框架的调节会是后期国际上需要一起面临与开展的工作。
我国铁矿石的存储数量位于世界前列,大约为整体存储量的百分之十二,整体的应用潜力较高。
由于铁矿的开采、加工工艺的提升,铁矿资源的整体应用会呈现出良好的经济性。
1.2 烧结配矿结构优化的理论基础低品矿粉为减少烧结资金投入最为重要的方式,不过品味下降可能导致非铁元素的高效提升,造成烧结矿品质降低,为后续高炉生产留下隐藏的危害,科学的应用铁矿粉高温特性展开烧结配矿,能够提升烧结配矿的效果。
18烧结矿冶金性能对其质量和高炉指标的影响

T10
1091 1092 1085
T40
1134 1247 1227
ΔT
43 155 142
Ts
1267 1435 1448
Td
1333 1450 1464
ΔT
66 15 16
ΔPm·9.8pa
S值(Kpa℃)
33.63 11.76 21.64
102 130 188
济钢
75.1
74.6
42.3
- - - 63.96 39.5
主要参考文献
序言:
烧结矿的冶金性能包括 900℃还原性(RI)、500℃低温还原粉化性 能( RDI )、荷重还原软化性能( TBS 、 TBE 、Δ TB )和熔融滴落性能 (Ts、Td、ΔT、ΔPm、S值)。这四项性能中900还原性是基本性能, 它不仅直接影响煤气利用率和燃料比,同时由于还原程度的不同,还 影响其还原强度(RDI)和软熔性能。500℃低温还原性能是反映烧结 矿在高炉上部还原强度的,它是高炉上部透气性的限制性环节。在高 炉冶炼进程中,高炉上部的阻力损失约占总阻力损失的 15%。烧结矿 的荷重还原软化性能是反映其在高炉炉身下部和炉腰部分软化带透气 性的,这部分的透气阻力约占高炉总阻力损失的25% 。熔融滴落性能 是烧结矿冶金性能最重要的部分,因为它约占高炉总阻力损失的60%, 是高炉下部透气性的限制性环节,要保持高炉长期顺行稳定,必须十 分重视含铁原料在熔融带的透气阻力。烧结矿在高炉的块状带、软化 带和熔融滴落带不同部位的性状和透气阻力的变化(详见示图)决定 着高炉内不同部位顺行和稳定,因此研究和分析清楚冶金性能对烧结 矿质量和高炉主要操作指标的影响是十分重要和必要的。
烧结矿的荷重还原软化性能是指其装入高炉后,随炉料下降,温度上升不断被 还原,到达炉身下部和炉腰部位,烧结矿表现出体积开始收缩即开始软化(TBS) 和 软 化 终 了 ( TBE ) 的 特 性 , 高 碱 度 烧 结 矿 的 TBS 应 ≥ 1100 ℃ , 软 化 温 度 区 间 (ΔTB= TBE -TBS)应≤150℃,烧结矿开始软化温度的高低取决于其矿物组成和 气孔结构强度〔1〕开始软化温度的变化往往是气孔结构强度起主导作用的结果, 这就是说,软化终了温度往往是矿物组成起主导作用。由高炉内各带透气阻力的 示图可知,软化带的阻力损失约占25%,是反映炉料在炉身下部和炉腰部位顺行状 况的,当烧结矿的开始软化温度低于950℃,软化温度区间>300℃时,高炉必须会 产生严重的悬料,因此为了保持高炉顺行稳定,烧结矿应具有良好的荷重还原软 化性能。关于荷重还原性能对高炉主要操作指标的影响 ,意大利的皮昂比诺 ( Piombimo )公司 4# 高炉曾于 1980 年做过统计,含铁原料的 TBS 由 1285 ℃提高到 1335℃,高炉的透气性ΔP由5.2kpa降低到4.75kpa(下降8.7%),产量提高了 16%, 日本神户公司的加古川厂和新日铁的广畑厂均通过改善酸性球团矿的软熔性能有 效地改善了高炉操作指标〔7〕。
湘钢高炉炉料结构优化试验研究

况
所 用含 铁 炉料 的冶 金 性 能 和 炉 料 结 构 进 行 了 试 验 研究 ,以寻求 最佳 的炉料 配 合 。 试 验 分两 部 分进 行 ,首 先 研 究 了单 一 含 铁
炉料 ( 7种 ,包括 4种块 矿 、2 球 团矿 和 1 种 种 烧 结 矿 )的冶 金 性 能 ;然 后 ,在 此 基 础 上 进 行 了炉料 结 构试 验 ,试 验 共 7组 ,均 按 炉 渣 碱 度
摘 要
对湘钢炼铁所用 炉料 的冶金性能进行 了试验 , 比较各种 炉料的还 原性 和熔滴性
能, 并对碱度符合要求 的几种 炉料结构 进行高 温性能 研究 和成本分 析 , 出 了比较合理 的炉 找 料结构 , 为高炉配矿提供 了理 论依据。
关键词 高炉炉料 优化 冶金性能 试验研究
概
置 于(内4 2 8的石 墨坩 埚 内 ,放 在 加 热炉 中加 热 , j 料柱荷 重9 8N e . /r 。加 热 程 序 :0 80℃,手 a 0
调快速 加 热 ( 3 C ri) 0 10 约 0 ̄/ n :80 0 0℃, 自 a
动升 温速率 4 ̄/ i;10 C rn 00℃恒 定 3 i,再 以 a 0rn a
的试样温度 为开 始熔 融 温 度 ( ,以压 差 开 始 T) 上 升至滴 下开始 的温度 区间 内压差 的积分 值为 透
2L mn / i  ̄原气体 ( O N =3/0 。用位移传 C / 2 07 )
感 器测定 料 面下降毫 米数 ,并用 压差变送 器测定 通 过料 柱 的压差 。将 料 面最终 下降毫米 数作为 收
维普资讯
20 年第 3 02 期
刘竹林等 湘钢高 炉炉料结构 优化述 堑塞
国外铁矿粉烧结基础特性及优化配矿研究
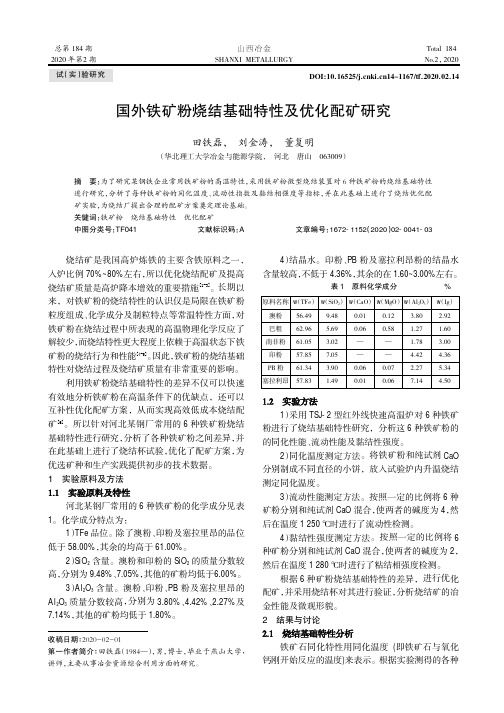
关键词:铁矿粉 烧结基础特性 优化配矿
中图分类号:TF041
文献标识码:A
文章编号:1672-1152(2020)02-0041-03
烧结矿是我国高炉炼铁的主要含铁原料之一, 入炉比例 70%~80%左右,所以优化烧结配矿及提高 烧结矿质量是高炉降本增效的重要措施[1-3]。长期以 来,对铁矿粉的烧结特性的认识仅是局限在铁矿粉 粒度组成、化学成分及制粒特点等常温特性方面,对 铁矿粉在烧结过程中所表现的高温物理化学反应了 解较少,而烧结特性更大程度上依赖于高温状态下铁 矿粉的烧结行为和性能[4-5]。因此,铁矿粉的烧结基础 特性对烧结过程及烧结矿质量有非常重要的影响。
根据 6 种矿粉烧结基础特性的差异,进行优化 配矿,并采用烧结杯对其进行验证,分析烧结矿的冶 金性能及微观形貌。 2 结果与讨论
收稿日期:2020-02-01 第一作者简介:田铁磊(1984—),男,博士,毕业于燕山大学, 讲师,主要从事冶金资源综合利用方面的研究。
铁矿石同化特性用同化温度 (即铁矿石与氧化 钙刚开始反应的温度)来表示。根据实验测得的各种
南非粉、澳粉、巴粗均为赤铁矿,而南非粉同化 能力最强,澳粉、巴粗同化温度相当,主要是因为南 非粉中 SiO2 比较适中,利于铁酸钙的生成,而澳粉 及巴粗中 SiO2 含量过高,将会使 SiO2 与 CaO·Fe2O3 中发生反应,把 Fe2O3 置换出来,生成高熔点硅酸二 钙,抑制铁酸钙的生成,从而使澳粉和巴粗同化性变 差。对于澳粉和巴粗而言,主要是因为巴粗铁矿粉中 MgO 含量较高,促进赤铁矿分解成磁铁矿,不利于铁 酸钙生成,从而相应地提高了同化温度。因此,南非 粉、澳粉、巴粗三种粉同化能力的高低为:南非粉跃澳 粉>巴粗。
007 利用高温冶金性能试验指导高炉配矿研究
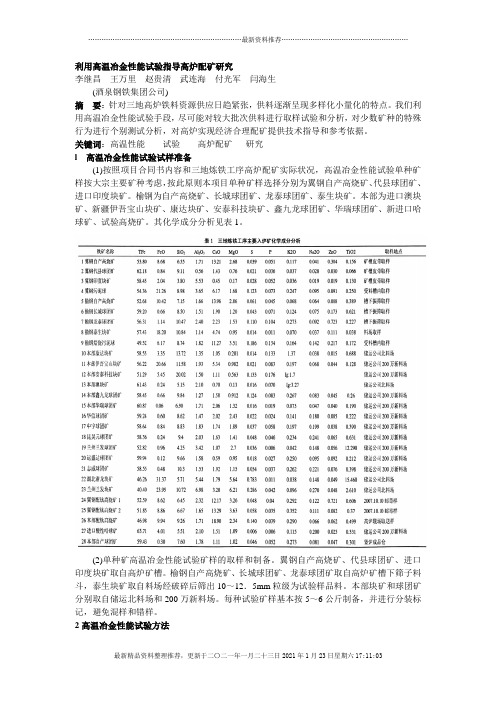
利用高温冶金性能试验指导高炉配矿研究李继昌王万里赵贵清武连海付光军闫海生(酒泉钢铁集团公司)摘要:针对三地高炉铁料资源供应日趋紧张,供料逐渐呈现多样化小量化的特点。
我们利用高温冶金性能试验手段,尽可能对较大批次供料进行取样试验和分析,对少数矿种的特殊行为进行个别测试分析,对高炉实现经济合理配矿提供技术指导和参考依据。
关键词:高温性能试验高炉配矿研究l 高温冶金性能试验试样准备(1)按照项目合同书内容和三地炼铁工序高炉配矿实际状况,高温冶金性能试验单种矿样按大宗主要矿种考虑,按此原则本项目单种矿样选择分别为翼钢自产高烧矿、代县球团矿、进口印度块矿。
榆钢为自产高烧矿、长城球团矿、龙泰球团矿、泰生块矿。
本部为进口澳块矿、新疆伊吾宝山块矿、康达块矿、安泰科技块矿、鑫九龙球团矿、华瑞球团矿、新进口哈球矿、试验高烧矿。
其化学成分分析见表1。
(2)单种矿高温冶金性能试验矿样的取样和制备。
翼钢自产高烧矿、代县球团矿、进口印度块矿取自高炉矿槽。
榆钢自产高烧矿、长城球团矿、龙泰球团矿取自高炉矿槽下筛子料斗,泰生块矿取自料场经破碎后筛出10~12.5mm粒级为试验样品料。
本部块矿和球团矿分别取自储运北料场和200万新料场。
每种试验矿样基本按5~6公斤制备,并进行分装标记,避免混样和错样。
2高温冶金性能试验方法本项目高温冶金性能试验方法有:铁矿石900℃还原性测定方法;铁矿石500℃低温还原粉化指数试验方法:铁矿石荷重软化性能测定方法;铁矿石熔融滴落试验方法。
试验全部在技术中心炼铁研究所试验室内进行。
2.1铁矿石900℃还原度实验方法900℃还原度试验采用GB/T 3241—91标准方法,试样在900℃温度下连续还原180分钟。
在试样升温阶段和还原度测试后的降温阶段,通入氮气进行保护,防止氧化。
还原度以“RJ”表示。
试验装置见照片1。
2.2 500℃低温还原粉化试验方法500℃低温还原粉化试验采用GB/T13242—9l标准方法,试样在500*C温度下连续还原60分钟,然后经转鼓实验后筛分称重得出结果。
高炉炉渣成分对炉料粘度的影响研究
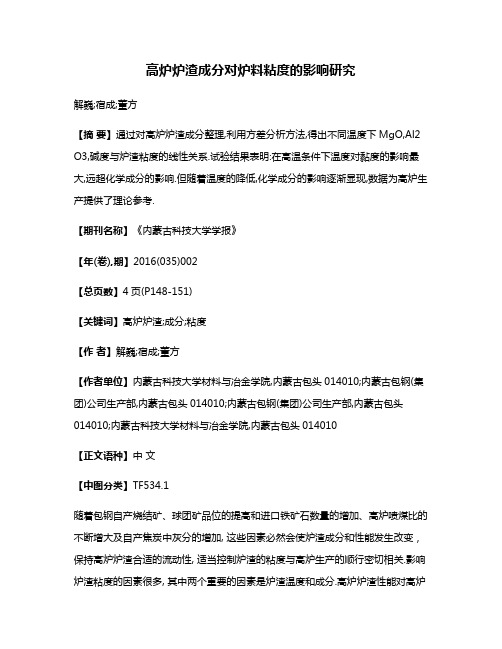
高炉炉渣成分对炉料粘度的影响研究解巍;宿成;董方【摘要】通过对高炉炉渣成分整理,利用方差分析方法,得出不同温度下MgO,Al2 O3,碱度与炉渣粘度的线性关系.试验结果表明:在高温条件下温度对黏度的影响最大,远超化学成分的影响.但随着温度的降低,化学成分的影响逐渐显现,数据为高炉生产提供了理论参考.【期刊名称】《内蒙古科技大学学报》【年(卷),期】2016(035)002【总页数】4页(P148-151)【关键词】高炉炉渣;成分;粘度【作者】解巍;宿成;董方【作者单位】内蒙古科技大学材料与冶金学院,内蒙古包头014010;内蒙古包钢(集团)公司生产部,内蒙古包头014010;内蒙古包钢(集团)公司生产部,内蒙古包头014010;内蒙古科技大学材料与冶金学院,内蒙古包头014010【正文语种】中文【中图分类】TF534.1随着包钢自产烧结矿、球团矿品位的提高和进口铁矿石数量的增加、高炉喷煤比的不断增大及自产焦炭中灰分的增加, 这些因素必然会使炉渣成分和性能发生改变,保持高炉炉渣合适的流动性, 适当控制炉渣的粘度与高炉生产的顺行密切相关.影响炉渣粘度的因素很多, 其中两个重要的因素是炉渣温度和成分.高炉炉渣性能对高炉操作、配矿成分和生铁成本产生重要影响.因此,系统研究目前炉渣粘度性能对高炉顺产意义重大.试验研究方案采用三因素四水平的正交试验设计,研究碱度,MgO,Al2O3含量对炉渣的粘度的影响.试验所用炉渣以包钢某高炉炉渣为基础,配加纯化学试剂来调整炉渣中的碱度,MgO,Al2O3含量.探寻不同碱度,MgO,Al2O3含量对高炉炉渣黏度的影响.测试采用东北大学研发的 RTW-10熔体物性测定仪(旋转法)进行[1],利用降温定点测定方法.首先,将炉渣试样的温度升至指定温度1 500 ℃下恒温 30 min,待熔渣的温度和化学成份均匀后测定该温度下的熔渣粘度;而后,开始降逐次测定各温度点下熔渣的粘度.采用某高炉炉渣成分,利用RTW-10熔体物性测定仪测定不同成分和不同试验温度条件下炉渣的粘度,试验结果见表1.从表1极差数据中可以看出,极差越大的因素,对炉渣黏度的影响越大.在1 480 ℃条件下,虽然MgO极差相比其它两者略高,但相差较小.而1 450 ℃时,Al2O3与碱度的极差增加,碱度增加的幅度较大,MgO极差略有下降.1 420 ℃到1360 ℃条件下,Al2O3的极差大大提高,远远大于其余二者.碱度极差在1 420 ℃几乎没有变化,而在1 360 ℃下降幅度较大.由此可见,在高温条件下温度对黏度的影响最大,远超化学成分的影响.随着温度的降低,化学成分的影响逐渐显现,尤其是Al2O3其对黏度的影响随温度的下降越来越大,成为主要影响因素,远超碱度和MgO对粘度的影响.利用Origin 7.5软件对数据进行方差分析,得到不同温度下,MgO,Al2O3碱度对粘度影响的线性关系.其中Y1 480,Y1 450,Y1 420,Y1 380,Y1 360为温度1 480 ℃,1 450 ℃,1 420 ℃,1 380 ℃,1 360 ℃时的黏度,X1,X2,X3分别为MgO,Al2O3含量和自由碱度.Y1 480=0.365 8-0.007 X1+0.01 X2-0.223 X3Y1 450=0.536 3-0.009 X1+0.015 X2-0.389 X3 (2)Y1 420=0.497 2-0.007 X1+0.024 X2-0.427 X3 (3)Y1 380=0.181 6-0.002 X1+0.046 X2-0.365 X3 (4)Y1 360=0.045 3-0.002 X1+0.059 X2-0.369 X3 (5)从回归方程可见,在实验室研究的高炉渣成分配比下,提高碱度,MgO含量,可以降低炉渣黏度;提高Al2O3含量则提高炉渣黏度.渣中MgO[2,3]含量可避免渣中出现高熔点的正硅酸钙(2CaO·SiO2),还可带入较多的O2-离子,减少Si-O,Al-O阴离子团的聚合度,破坏它们的网状结构,形成简单的单、双四面体结构,该结构的炉渣熔化温度较低,炉渣粘度低,流动性较好. 提高炉渣的二元碱度(CaO/SiO2),能使熔渣中 O2-活度增大,使硅氧复合阴离子解体,从而使熔渣粘度下降,流动性改善.但当碱度>1.20时[4],炉渣的粘度上升,炉渣的矿物结构发生了变化,炉渣中正硅酸钙(2CaO·SiO2)的数量增加,这部分高熔点矿物容易在炉渣中产生非均匀相,使炉渣熔化性温度急剧升高,流动性变差,短渣的性能逐渐增强,炉渣的稳定性也变差.随着Al2O3含量的增加,炉渣中Al2O3吸收氧离子构成 (AlO4)5-复合阴离子团的数量也随之增加,容易形成结晶能力很强的高熔点复杂化合物,如尖晶石(MgO·Al2O3,熔点为2 135 ℃),铝酸一钙(CaO·Al2O3,熔点为1 600 ℃)等;形成大量的非均匀相,很容易结晶出固体存在于炉渣熔体中, 造成炉渣的粘度越来越大, 流动性变差.(1)高温条件下温度对黏度的影响最大,远超化学成分的影响.随着温度的降低,化学成分的影响逐渐显现;(2)在实验炉渣成分配比内,MgO对炉渣粘度影响随炉温波动甚微;(3)在炉温较低的情况下,Al2O3与碱度的变化将对炉渣产生较大影响.【相关文献】[1] 邹祥宇,张伟,王再义,等. 碱度和Al2O3含量对高炉炉渣性能的影响[J]. 鞍钢技术,2008,(4):20-23.[2] 何环宇,王庆祥,曾小宁. MgO含量对高炉炉渣粘度的影响[J]. 钢铁研究学报,2006,(6):11-14.[3] 茅沈栋,杜屏. 降低MgO含量对高炉渣粘度和熔化性温度的影响[J]. 钢铁研究学报,2015,27(9):33-36.[4] 杨建炜. 高Al2O3高炉渣冶金性能的研究[D].保定:河北理工大学,2005.。
烧结过程中铁矿粉高温特性的原位观察研究
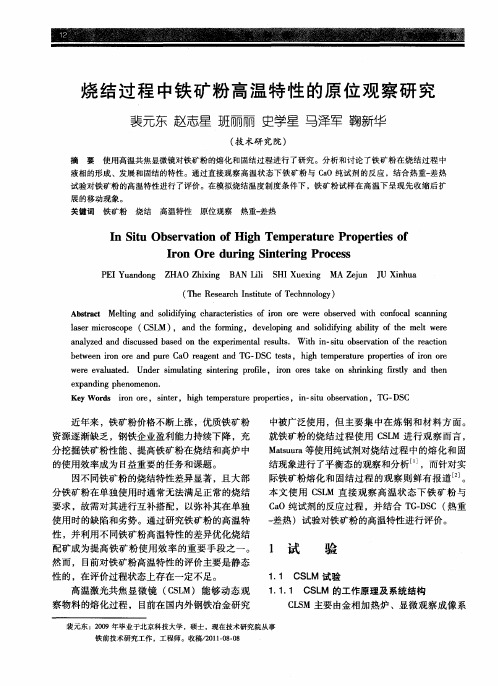
1 试
验
1 1 CS M 试 验 . L
1 1 1 CS M 的工作原 理及 系统 结构 . . L
C S 主要 由金相加热炉 、显微观察成像系 LM
we e e au td. Un e i ltn sn e i g p o l io r s a e o h nkn rty n t n r v l a e d r smu ai g it rn r f e, r n o e tk n s r ig f s a d he i i i l e p n i g p e o no x a d n h n me n. Ke o d io r sn e , hih tmp r t r o ri s i — i b e a in, TG- C y W r s r n o e, i tr g e e a u e prpete , n st o s r t u v o DS
近年 来 ,铁 矿 粉价格 不断 上涨 ,优质 铁矿 粉
中被广泛使用 ,但 主要集 中在炼钢和材料方 面。 就铁矿粉的烧结过程使用 C L 进行观察而言 , SM M t ua a ur 等使用纯试剂对烧结过程 中的熔化和固 s 结现 象进 行 了平 衡态 的观察 和分 析 … ,而针对 实 际铁 矿粉 熔化 和 固结 过 程 的 观察 则 鲜有 报 道 J 2。 本文使用 C L 直接观察高温状态下铁 矿粉与 SM C O 纯试剂 的反应 过 程 ,并结 合 T -S ( 重 a GD C 热
Ab ta t Met g a d s l i ig c a a t r t s o r n o e we e o s r e t o f c l s a n n s c r l n n o i f n h r c e si f i r r b e v d wi c n o a c n i g i d y i c o h
高炉使用含PMC矿炉料的配矿结构研究
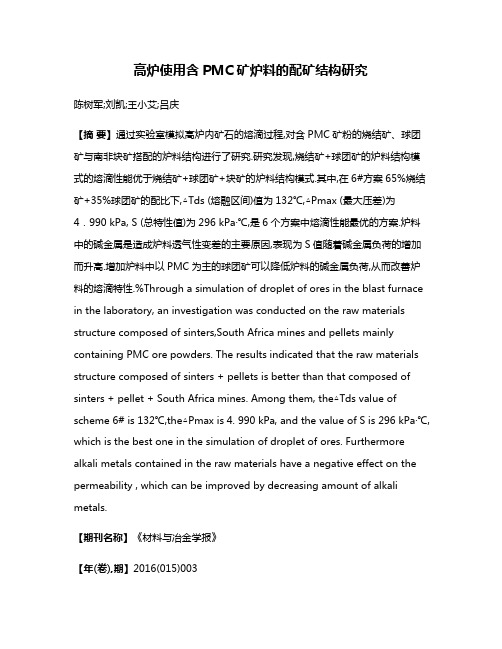
高炉使用含PMC矿炉料的配矿结构研究陈树军;刘凯;王小艾;吕庆【摘要】通过实验室模拟高炉内矿石的熔滴过程,对含PMC矿粉的烧结矿、球团矿与南非块矿搭配的炉料结构进行了研究.研究发现,烧结矿+球团矿的炉料结构模式的熔滴性能优于烧结矿+球团矿+块矿的炉料结构模式.其中,在6#方案65%烧结矿+35%球团矿的配比下,△Tds (熔融区间)值为132℃,△Pmax (最大压差)为4.990 kPa, S (总特性值)为296 kPa·℃,是6个方案中熔滴性能最优的方案.炉料中的碱金属是造成炉料透气性变差的主要原因,表现为S值随着碱金属负荷的增加而升高.增加炉料中以PMC为主的球团矿可以降低炉料的碱金属负荷,从而改善炉料的熔滴特性.%Through a simulation of droplet of ores in the blast furnace in the laboratory, an investigation was conducted on the raw materials structure composed of sinters,South Africa mines and pellets mainly containing PMC ore powders. The results indicated that the raw materials structure composed of sinters + pellets is better than that composed of sinters + pellet + South Africa mines. Among them, the△Tds val ue of scheme 6# is 132℃,the△Pmax is 4. 990 kPa, and the value of S is 296 kPa·℃, which is the best one in the simulation of droplet of ores. Furthermore alkali metals contained in the raw materials have a negative effect on the permeability , which can be improved by decreasing amount of alkali metals.【期刊名称】《材料与冶金学报》【年(卷),期】2016(015)003【总页数】8页(P159-165,170)【关键词】炉料结构;PMC磁铁矿;碱金属;碱度;熔滴性能【作者】陈树军;刘凯;王小艾;吕庆【作者单位】东北大学冶金学院,沈阳 110004; 河钢集团承钢分公司;华北理工大学冶金与能源学院,教育部现代冶金技术重点实验室,河北唐山 063009;河钢集团宣化分公司;华北理工大学冶金与能源学院,教育部现代冶金技术重点实验室,河北唐山 063009【正文语种】中文【中图分类】TF53在日益严峻的钢铁形势下,降低铁水成本,提高资源利用率,成为钢铁企业亟需解决的问题[1-3].因此,越来越多的企业提高了外矿的使用率.PMC精粉是一种含铁品位较高,同时含有较高钛、磷、铜、碱金属,且价格较低的铁矿粉.目前,使用PMC矿对高炉顺行的影响,尤其是对软熔滴落带影响的研究还较少.为了最大限度地使用PMC矿产资源,保证高炉冶炼顺行、高产,本文对PMC烧结矿、球团矿与南非块矿合理配比进行了研究.炉料结构没有统一固定的模式,高炉生产实践表明[4,5],对炉料进行合理组织都可能获得较理想的冶炼效果.炉料结构的软熔滴落性能是影响高炉透气性指标的重要因素[6],直接关系到高炉顺行.炉料结构的软熔滴落性能已经成为选择高炉冶炼合理炉料结构、判断和改变高炉软熔带形状的重要依据和手段.通过实验室模拟炉料在高炉冶炼状态下的还原过程,检测矿石的软化区间(ΔT1)、还原气的压力差(ΔPmax)、熔融区间(ΔTds)、总特性值(S)值等值,能够得到软熔带温度区间、高温区域透气性、焦炭高温反应性能、初渣流动性等重要参数,使熔滴试验结果与高炉的软熔带建立起联系,从而推定各种铁矿石在高炉内形成软化带、软熔带的相对部位,并预测它们对高炉料柱透气性及炉缸温度的影响,为高炉调整炉料结构提供理论基础[7-9].参考国内高炉实际生产的炉料结构[10],试验采用了烧结矿+球团矿+块矿和烧结矿+球团矿的炉料结构模式,对不同配矿的熔融滴落性能进行了研究.1.1 试验原料试验所用烧结矿、球团矿均为实验室条件下所制,原料的化学成分如表1~表3所示.试验用的原料化学成分如表3所示.1.2 试验步骤试验采用熔融滴落模拟高温炉,其结构如图1所示.用直径为60 mm,高215 mm的石墨坩埚作为反应容器,试样总质量为214 g,其中矿石为170 g,焦炭为44 g;焦炭分为上下两层装入,荷重 9.8 N/cm2.试验过程:从室温到1 300 ℃ 的升温速率为10 ℃/min,从1 300 ℃ 到1 550 ℃ 的升温速率为5 ℃/min,保温30 min,升温过程通N2保护;炉温200 ℃时装入炉料,500 ℃时切换成由一氧化碳和氮气组成的反应气体,体积比为CO∶N2=30∶70,炉料收缩量为10%前保持气体流量为0.9 m3/h,收缩10%后不再调节气体流量,直至矿石熔融滴落,保存完数据后切换成氮气,流量0.3m3/h.试验过程中各参数的意义:分别以收缩率到达10%和40%代表软化开始温度和软化终了温度,用T10%和T40%表示,以压差陡升温度和渣铁开始滴落的温度代表熔化开始温度和滴落开始温度,用Ts、Td表示.ΔT1=T40% -T10%为软化区间,ΔTds=Td-TS为熔化区间,熔化开始时的压差用ΔPs表示,最大压差用ΔPmax表示.S值为综合衡量炉料熔滴性能的指标,S值越小代表熔滴性能越好.1.3 试验方案以实验室制备的烧结矿、球团矿为原料,按照一定的炉料结构进行熔滴试验,具体的试验方案如表4所示,各试验方案的化学成分如表5所示.炉料熔滴性能试验结果如表6所示.2.1 不同炉料结构的ΔT1比较不同炉料结构的ΔT1如图2所示.高炉软熔带在高炉冶炼过程中起到煤气二次分配器的作用,合理的炉料结构应该有利于理想的软熔带形成.试验中ΔT1是T40%和T10%的差值,其值的大小表征着软化温度区间的宽窄,其值越小说明软化温度区间越窄,矿石的软化性能越好.由图2可知:ΔT1由高到低的顺序为4#、5#、6#、3#、2#、1#.其中,1#方案的ΔT1最低,为180 ℃,软化温度区间最窄,炉料透气性阻力最小,对于高炉内煤气运动比较有利.结合表6可知,4#方案的T40%最高,达到了1 423 ℃,6#方案的最低,为1 373 ℃,二者相仅仅相差50 ℃.因此,6个方案的T40%相差得并不大,并且整体都落在了一个比较高的温度范围,所以其软熔带位置都比较低,高炉的块状带都相对较宽,透气性比较好.由以上分析可知,6个方案软化温度区间都比较窄.其中,1#方案的软化温度区间最窄,在冶炼条件相同时矿石的软熔带最薄,料柱的透气性最好,有利于高炉内煤气的运动.2.2 不同炉料结构的ΔTds比较不同炉料结构的ΔTds如图3所示.由图3可知:ΔTds由高到低的顺序为4#、5#、3#、2#、1#、6#.ΔTds是Td和Ts的差值.熔滴性能优良的炉料结构应具有较低的ΔTds.其中,6#方案的△Tds值为132 ℃,在6个方案中最低,熔滴带的温度区间最窄.现代高炉炼铁一般要求△Tds<100 ℃,1#方案的△Tds值为133 ℃,与6#没有太大的差别.因此,就△Tds指标而言,1#、6#方案都比较好.由表5可知,1#、6#方案的TFe含量都比较高,渣量相对较少,炉料易滴落,炉料透气性好,所以△Tds值比较低.由于炉料在高温下快速熔化对高炉顺行意义重大,所以现代高炉炼铁一般要求铁矿石的滴落温度要高.由表6可知,6#方案的Td值最低,为1 391 ℃,其余五个方案均在1 400 ℃以上.因此,就Td指标来看各个方案都达到了比较好的水平.具有较好熔融滴落性能的高炉原料结构应具有较高的Ts、Td和较低的ΔTds.综合考虑Ts、Td和ΔTds,炉料的熔滴性能以6#方案为最优.2.3 不同炉料结构与ΔPmax、S值关系(1)不同炉料结构ΔPmax的比较不同炉料结构ΔPmax如图4所示.由图4可以看出,整体上1#、2#、3#方案的ΔPmax高于4#、5#、6#方案.其中,3#方案的ΔPmax最高与具有相同炉料结构的1#相比高出近 2 kPa;然而,同为烧结矿+球团矿结构的4#、5#、6# 方案的ΔPmax相差并不大.如前所述,各方案的软化温度区间都比较窄,所以使ΔPmax产生区别的主要原因并不是软熔区间的不同造成的,通过表5可以看到1#、2#、3#方案的碱金属含量都比较高,会使焦炭的气化反应提前并且加剧,使料柱软熔带气窗的透气性大大降低,导致ΔPmax升高.因此,仅从ΔPmax指标来看,选择碱金属含量较低的4#、5#、6#方案,对于改善透气性指标,降低碱金属入炉比较有利.(2)不同炉料结构S值比较不同炉料结构S值如图5所示.由图5可以看出,1#、2#、3#方案的S值整体上高于4#、5#、6#方案.由S值的计算式:式中:Ts为熔化开始温度,℃; Td为滴落开始温度,℃;ΔPs为熔化开始时的压差,kPa;ΔPmax 为最大压差,kPa.可以看到,ΔPmax是S值的一个重要影响因素,因此,很多情况下作为熔滴性能综合评定指标的S值与ΔPmax表现出的规律很相似.本试验中6#方案的ΔPmax最低,炉料的透气性好,所以6#炉料结构的S值最低,熔滴性能最好.(3)炉料二元碱度Rw(CaO)/w(SiO2)与ΔPmax的关系炉料二元碱度Rw(CaO)/w(SiO2)与ΔPmax的关系如图6所示.由图6可知,△Pmax随二元碱度Rw(CaO)/w(SiO2)的变化呈先下降后稍有升高的趋势.二元碱度Rw(CaO)/w(SiO2)在1.60~1.80之间时,△Pmax都比较低.其中,6#方案碱度下的△Pmax最低.整体上看,1#、2#、3#方案的碱度下的△Pma x高于4#、5#、6#方案.从炉料结构上分析,1#、2#、3#方案的炉料结构与4#、5#、6#相比,区别主要是1#、2#、3#配入了一定量的南非块矿,而4#、5#、6#方案提高了球团矿的配比.由表3可知南非块矿的Rw(CaO)/w(SiO2)仅为0.027,而球团矿的二元碱度Rw(CaO)/w(SiO2)为0.27,是南非块矿的10倍,所以在提高球团矿的配比时,炉料的二元碱度Rw(CaO)/w(SiO2)就会增加.从试验结果看,炉料的二元碱度Rw(CaO)/w(SiO2)控制在一定范围内时,对于改善△Pm ax非常有利,所以生产中可以考虑提高球团矿的使用.而且由表2可知,本次试验所用球团矿中的PMC矿配比高达68.60%,因此,可以通过提高球团矿的配比达到优化炉料性能、提高PMC矿使用率的目的.从二元碱度Rw(CaO)/w(SiO2)对炉料透气性能影响上分析,炉料二元碱度Rw(CaO)/w(SiO2)在一定范围内时,△Pmax会随着二元碱度Rw(CaO)/w(SiO2)增加而降低[12,13],当二元碱度Rw(CaO)/w(SiO2)超过一定值后,由于6个方案的炉料中均含有较高的TiO2,渣中的钙钛矿含量增加,使渣的黏度增大,导致△Pmax升高.而且,各方案的 Al2O3含量都比较高,高炉渣中Al2O3含量高会使炉渣黏度增加,影响料柱的透气性[14].综合以上分析,6#方案的碱度最有利于改善炉料的透气性.然而,高炉炼铁一般要求熔滴过程的△Pmax要低,最好△Pmax<1.764 kPa.在这一要求下,6个方案的最大压差均处在了较高的水平.所以,很有必要做进一步的研究.(4)炉料二元碱度Rw(CaO)/w(SiO2)与S值的关系炉料二元碱度Rw(CaO)/w(SiO2)与S值的关系如图7所示.由图7可知,总特性值S随着二元碱度Rw(CaO)/w(SiO2)的变化呈先减小后增大的趋势,其变化趋势与△Pmax随二元碱度Rw(CaO)/w(SiO2)的变化趋势一致.一般S值越小代表炉料的熔滴性能越好,6个方案中,6#方案的S值最低为 296 kPa·℃,是这几组方案中熔滴性能最好的方案.但是,与国际先进水平要求下的S<40 kPa·℃ 相比差距还是很大.如前所述,6#方案的△Pmax、ΔTd都是6个方案中最低的,所以6#方案的S值最低,熔滴性能最好.(5)炉料碱金属含量与ΔPmax的关系炉料碱金属含量与ΔPmax的关系如图8所示.由图8可知,随着炉料中碱金属负荷的增加,△Pmax呈增大的趋势.△Pmax增大,料柱透气性变差.由表3的原料成分可知,球团矿的钾钠含量是这三种矿中最低的,而南非块矿最高.碱金属是高炉中的有害元素,在高炉内会形成碱金属循环,积累到一定程度时会给高炉带来严重危害,而降低炉料的碱金属含量是控制碱金属危害的一个重要手段.所以在使用本试验中的炉料进行冶炼生产时,炉料的碱金属含量可以通过提高球团矿的配入量进行控制,同时也实现了提高PMC矿使用率的目的.由表5可以知道,1#、2#、3#方案的碱金属含量整体比4#、5#、6#方案高.碱金属对△Pmax的影响,主要是由于碱金属会加速炉料中焦碳的碳素溶损反应,使炭气化反应剧烈,焦炭气孔壁变薄,软熔带气窗的透气性降低,压差升高[15];此外,在熔滴试验的铁矿石还原过程中,由于碱金属对还原反应具有正催化作用,使矿石中金属铁晶体生长加快,在相界面上产生应力,当应力积累到一定程度时,便产生大量的裂纹,导致粉化率升高,粉化加剧导致料层透气性变差,△Pmax升高.6个试验方案中,6#方案的K、Na含量最低,其△Pmax最小,熔滴性能最好.(6)炉料碱金属含量与S值的关系炉料碱金属含量与S值的关系如图9.由图9可知随着炉料中碱金属负荷的增加,S值呈增大的趋势.炉料中碱金属含量的增加,破坏了焦炭的强度,恶化了料柱的透气性,使△Pmax升高,熔滴性能变差,反映到S值上就是S值变大.取6#、3#试验后的焦炭进行电镜扫描,对比不同K、Na含量对焦炭的腐蚀程度如图10所示.图10(a)是6#方案下反应后的焦炭形貌,图10(b)是3#方案下反应后的焦炭形貌.由图10可以看到,由于3#方案的碱金属含量高于6#方案,所以反应后的焦炭表面腐蚀严重,气孔变大,气孔壁变薄,焦炭强度下降,料柱透气性变差,总特性S值升高.(1)6个方案的软熔区间都比较窄.其中,4#配矿方案T10%与T40%指标都比较高,在高炉中的相应位置最低;1#方案的软化温度区间最窄,在冶炼条件相同时料柱的透气性最好,有利于高炉内煤气的运动.(2)6#方案的△Tds值在六个方案中最低,熔滴温度区间最窄;1#方案的△Tds值与6#没有太大的差别,因此,就△Tds而言1#、6#方案的指标都比较好.(3)△Pmax随二元碱度Rw(CaO)/w(SiO2)的变化呈先下降后升高的趋势.其中,6#方案的△Pmax最低;S值随着二元碱度Rw(CaO)/w(SiO2)的变化呈先减小后增大的趋势.6个方案中,6#方案的S值最低为296 kPa·℃,是这几组方案中熔滴性能最好的方案.但是,与国际先进水平要求下的S<40 kPa·℃ 相比差距还很大,仍然有必要进行更进一步的研究.(4)随着炉料中碱金属负荷的增加,△Pmax、S值均呈增大的趋势.碱金属对炉料熔滴性能的影响主要是通过对焦炭反应性的催化作用实现的,在实际生产中碱金属的危害应该引起足够的重视.(5)整体上烧结矿+球团矿的炉料结构模式的熔滴性能优于烧结矿+球团矿+块矿的炉料结构模式.因此,在冶炼含PMC矿的炉料时应首先考虑烧结矿+球团矿的炉料结构模式.【相关文献】[1]王明军, 张丙怀, 阳海斌, 等. 南钢新2号高炉炉料冶金性能的研究[J]. 钢铁, 2008, 43(4): 14-17. (Wang Mingjun , Zhang Binghuai , Yang Haibin, et al. Comprehensive evaluation of burden metallurgical properties for No. 2 blast furnace at nanjing steel[J]. Iron and Steel, 2008, 43(4): 14-17. )[2]王竹民, 王磊, 吕庆, 等. 邯钢高炉炉料结构优化研究[J]. 钢铁研究, 2009, 37(4): 4-7. (Wang Zhumin, Wang Lei, Lu Qing, et al. Study on optimization of burden design for blast furnaces at handan steel[J]. Research on Iron& Steel, 2009, 37(4): 4-7. )[3]姜汀. 承钢含钒钛烧结矿的熔滴试验[J]. 河北冶金, 2012(12): 13-16. (Jiang Ting. Droplet test of sinter bearing vanadium and titanium[J]. Hebei Metallurgy, 2012(12): 13-16. )[4]储满生, 陈立杰, 柳政根, 等. 高炉冶炼钒钛磁铁矿合理炉料结构的研究[J]. 河南冶金, 2013, 21(6): 1-5. (Chu Mansheng, Chen Lijie, Liu Zhenggen, et al. Study on raional burden structure of smelting vanadium-titanium magnetite in blast furnace[J]. Henan Metallurgy, 2013,21(6): 1-5. )[5]郭豪, 张建良, 钟树周, 等. 韶钢合理炉料结构的研究[J]. 钢铁, 2008, 43(1): 9-12. (Guo Hao Zhang Jianliang, Zhong Shuzhou, et al. Study on charge optimization on shaogang blast furnaces[J]. Iron and Steel, 2008, 43(1): 9-12. )[6]梁栋, 周小辉, 石红燕, 等. 莱钢高炉用含铁炉料熔滴性能试验及分析[J]. 山东冶金, 2013, 35(2): 25-34. (Liang Dong, Zhou Xiaohui, Shi Hongyan, et al. Blast furnace iron furnace charge drop performance test and analysis of laigang[J]. Shandong Metallugy, 2013, 35(2): 25-34.[7]Keiichi A, Takazo K, Yoshikazu N. Effect of test condition on de-crepitation index and test repeatability for lump iron ore[J]. ISIJ International, 2010, 50(10): 1 511-1 513.[8]Ritz V J, Kortmann H A, Koch K. Reduction, softening and melting properties of pellets, sinters, lumpy ore and mixed blast furnace burden[C]//2nd International Congress on the Science and Technology of Ironmaking and 57th Ironmaking Conference. Toronto,Canada, 1998: 1 635-1 640.[9]Tsunehisa N, Kenichi H, Masaaki N, et al. Evaluation of soften-ing, shrinking and melting reduction behavior of raw material for blast furnace[J]. ISIJ International, 2011, 51(8): 1 316-1 321.[10]吴胜利, 许海法, 汪国俊, 等. 现代高炉合理使用天然块矿的基础研究[J]. 北京科技大学学报, 2007, 29(3):320-324. (Wu Shengli, Xv Haifa, Wang Guojun, et al. Basical study on the rational use of natural ore in the blast furnace on modern tinmes[J]. Journal of University of Science and Technology Beijing, 2007, 29(3):320-324. )[11] 沐继尧. 高碱度烧结矿的软熔性能[J]. 烧结球团, 1986, 11(6): 17-23. (Mu Jiyao. Soft melting performance of high basicity sinter[J]. Sintering and Pelletizing, 1986, 11(6): 17-23. )[12]孙金铎. 合理烧结矿碱度的探讨[J]. 钢铁, 2001, 36(8): 1. (Sun Jinduo. Investigation on rational basicity of sinter[J]. Iron and Steel, 2001, 36(8): 1. )[13]王福佳, 吕庆, 陈树军, 等. 碱度对含钒钛高炉炉料熔滴性能的影响[J]. 钢铁钒钛, 2015, 36(5): 95-96. (Wang Fujia, Lü Qing, Chen Shujun, et al. Research on influence of basicity on dropping performance of vanadium-titanium burden [J]. Iron and Steel Vanadium Titanium, 2015, 36(5): 95-96. )[14]龙防. 富Al2O3矿对炼铁原料及冶炼过程的影响[D]. 武汉: 武汉科技大学, 2006. (Long Fang. The effection on ironmaking raw materials and metallurgical process by high content of Al2O3 iron ore[D]. Wuhan: Wuhan University of Science and Technology, 2006. )[15]吕青青, 杜屏, 周俊兰. 高炉块状带焦炭劣化机理[J]. 钢铁, 2016, 51(1):14-18. (Lu Qingqing, Du Ping, Zhou Junlan. Coke deterioration mechanism in lump zone of blast furnace [J]. Iron and Steel, 2016, 51(1):14-18. )。
“系统思维、过程管控、结果导向”提升球团矿质量生产实践
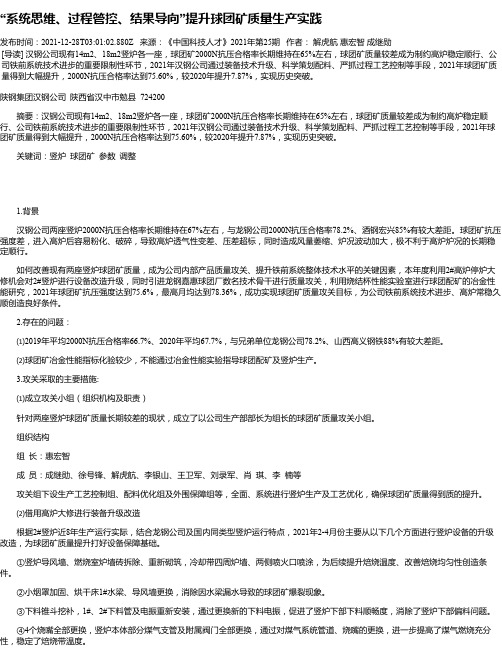
“系统思维、过程管控、结果导向”提升球团矿质量生产实践发布时间:2021-12-28T03:01:02.880Z 来源:《中国科技人才》2021年第25期作者:解虎航惠宏智成继勋[导读] 汉钢公司现有14m2、18m2竖炉各一座,球团矿2000N抗压合格率长期维持在65%左右,球团矿质量较差成为制约高炉稳定顺行、公司铁前系统技术进步的重要限制性环节,2021年汉钢公司通过装备技术升级、科学策划配料、严抓过程工艺控制等手段,2021年球团矿质量得到大幅提升,2000N抗压合格率达到75.60%,较2020年提升7.87%,实现历史突破。
陕钢集团汉钢公司陕西省汉中市勉县 724200摘要:汉钢公司现有14m2、18m2竖炉各一座,球团矿2000N抗压合格率长期维持在65%左右,球团矿质量较差成为制约高炉稳定顺行、公司铁前系统技术进步的重要限制性环节,2021年汉钢公司通过装备技术升级、科学策划配料、严抓过程工艺控制等手段,2021年球团矿质量得到大幅提升,2000N抗压合格率达到75.60%,较2020年提升7.87%,实现历史突破。
关键词:竖炉球团矿参数调整1.背景汉钢公司两座竖炉2000N抗压合格率长期维持在67%左右,与龙钢公司2000N抗压合格率78.2%、酒钢宏兴85%有较大差距。
球团矿抗压强度差,进入高炉后容易粉化、破碎,导致高炉透气性变差、压差超标,同时造成风量萎缩、炉况波动加大,极不利于高炉炉况的长期稳定顺行。
如何改善现有两座竖炉球团矿质量,成为公司内部产品质量攻关、提升铁前系统整体技术水平的关键因素,本年度利用2#高炉停炉大修机会对2#竖炉进行设备改造升级,同时引进龙钢嘉惠球团厂数名技术骨干进行质量攻关,利用烧结杯性能实验室进行球团配矿的冶金性能研究,2021年球团矿抗压强度达到75.6%,最高月均达到78.36%,成功实现球团矿质量攻关目标,为公司铁前系统技术进步、高炉常稳久顺创造良好条件。
高炉炼铁资源优化模型的研究与应用

高炉炼铁资源优化模型的研究与应用摘要:我国钢铁生产突飞猛进,高炉生产在各方面取得了显著进步,但在资源和能源利用率及环保等方面还有很大差距。
本文以成本最优为目标,提出了高炉优化配比模型,该模型可快速、准确计算出满足目标要求又兼顾降低资源消耗和减少环境污染的优化配比方案。
比较了应用高炉优化配矿模型前后的炼铁成本、矿石单耗和吨铁炉渣量等数据。
结果表明,高炉优化配比模型的应用,降低了吨铁生产成本,节约了资源,减少了排放,取得较好的经济效益和环境效益。
abstract: with the steel production developing by leaps and bounds in our country, blast furnace has achieved remarkable progress in various aspects, but it also has the very big gap in the utilization rat of resources and energy and environmental protection. in this article, it puts forward the optimization ratio model of blast furnace according the target of the optimal cost, and it can calculate the optimization ratio scheme of meeting the goal request and also considering reducing resource consumption and environmental pollution. it compares the data of the cost of pig iron, the consumption of ore and the quantity of blast furnace slag which is from before and after of applying the optimization ratio model of blast furnace. the results showthat it reduces the cost of tons pig iron, economizes resources, reduces the emissions, and obtains better economic benefits and environmental benefits because of applying the optimization ratio model of blast furnace.关键词:高炉炼铁;成本最优;优化配比key words: blast furnace;the optimal cost;the optimal ratio中图分类号:tf5 文献标识码:a 文章编号:1006-4311(2013)13-0047-03————————————作者简介:马光银(1991-),男,贵州瓮安人,本科生在读,研究方向为冶金设备管理。
高炉炼铁合理配矿研究

高炉炼铁合理配矿研究作者:俞廷来源:《城市建设理论研究》2013年第26期【摘要】节约能源降低成本,是提高企业经济增长的重要途径,也是企业竞争的必然要求。
面对原燃料市场的价格不断上涨,钢材市场在严峻的和多变的形势,在企业内部向规模要效益、向管理要效益、向指标要效益、向品种要效益的过程中,将钢铁企业中的炼铁工序,作为降耗增效最多的环节,从而进一步地加强管理和调控。
如何对高炉炼铁进行合理的配矿也是当代众多企业需要深入了解的一部分。
【关键词】高炉炼铁技术合理配矿现状研究炉料结构优化中图分类号: TF321 文献标识码: A一.引言烧结、高炉配矿结构的优化即针对国际、国内铁矿石市场的变化,对烧结、高炉所用主原料配比不断进行优化,以求达到成本最低、性能最佳,改善烧结过程、烧结矿品质、高炉顺行状态及冶炼技术经济指标等。
二.高炉炼铁的现状。
高炉炼铁技术,适合于那些工业化初步发展的国家,生产大路货、初级钢材,但在发达国家,高炉技术正面临淘汰。
电炉技术炼钢是当今世界趋势。
电炉炼铁可以提升钢材质量和特殊性能,减少原材料和电力等的浪费。
在订单经济时代,生产要根据市场需求变化,但高炉炼铁技术周期长,生产产品低级,且生产的产品还需要一道甚至更长的加工链条。
电炉炼钢则可缩短钢材冶炼周期,可根据订单安排生产,原材料和动力资源浪费少,不再如高炉炼铁那样存在大量的产品积压情况。
当今社会进入材料时代后,市场需要的钢材不再是传统的材料,高炉炼铁生存空间更大为缩小,且附加值很低,以中国钢铁业为例,全国钢铁产业利润还不如开采铁矿的赚钱,原因就是因为高炉炼铁技术低级落后,不能生产高附加值产品。
作为世界上第一钢铁生产大国,世界铁矿第一进口大国,世界钢铁业初级钢材第一出口大国,世界钢铁第一进口大国,世界钢铁产业人数最多的国家,世界钢铁厂最多的国家,中国必须认真思考中国钢铁业的下一步发展战略。
不能以推动就业为借口,把钢铁业的发展寄托在国家的巨型投资拉动钢铁业的繁荣,而要认真的思考减少污染,提高产品附加值和适应市场的实际需求,实现钢铁业的产业升级,效益升级。
冶金性能对高炉 的影响

还原软化-熔融特性
软化、熔融性能:炉料的荷重软化、熔融性能反映了炉料在高 炉下部的高温软化和熔化、滴落过程的特性。对高炉软熔带的 形成(位置、形状、厚度)和透气性起着决定性作用。 表征此特性的参数有炉料的软化开始温度、软化终了温度、熔 融温度、软化区间以及熔融区间。 高炉要求矿石具有合适的软化开始温度、熔化开始温度,窄的 软化和熔融温度区间,以使高炉软融带位置既为过高,也不过 低,处于适宜的位置,即能适当增加炉内块状带区域的高度, 利于改善上部透气性。 软熔带位置过低,熔融渣铁或炉墙周围熔化的粘结物易直接进 入炉缸,导致崩、滑料甚至炉凉。炉料的软化熔融温度区间较 宽,表明高炉软熔带较厚,煤气通过软熔带的阻力较大,高炉 透气性较差。
烧结矿冶金性能指标 影响因素及有关问题探讨
2013.11
内容
烧结矿的冶金性能指标 影响冶金性能指标的因素探讨 测定方法
高炉精料要求
入炉品位高,脉 石及杂质含量 低
提高入炉料强 度和粒度组成 合理
改善原燃料 高温冶金性能
烧结矿的冶金性能指标
900℃还原度 550℃低温还原粉化指数 荷重软化性能 软熔-滴落性能
影响因素: 1烧结矿化学成分 2 烧结矿矿相组成 3 工艺条件
再生赤铁矿形成 残余应力增大 区域结构弱化 原生褐铁矿大颗粒 后果: 产生粉末,恶化高炉 上部透气性
磁铁矿直接氧化生成
破坏性大
还原为磁铁矿体积膨胀25%
颗粒状次生赤铁矿 骸晶状赤铁矿
物铁 其 的纹 主 。酸 中 周和 要 钙 夹 围熔 分 和 杂 。蚀 布 磁着 状在 铁玻 残气 矿璃 存孔 等质 原、 矿、 矿裂
MgO含量对低温还原粉化的影响
高炉炼铁对炉料质量的要求及优化配矿技术

高炉炼铁对炉料质量(de)要求及优化配矿技术王维兴 中国金属学会一. 高炉炼铁炉料质量对生产有重要意义炼铁学基本理论和高炉生产实践均证明,优化高炉炼铁原燃料(de)质量和冶金性能既是高炉高效化、大型化、长寿化、节能减排(de)前提条件,也是提高喷煤比、降低焦比和燃料比(de)基础条件.所谓优化炉料质量即是提高炉料质量是入炉矿品位高,渣量少和改善原燃料性能等.大高炉做到入炉矿品位≥58%、炉料含低SiO 2、低Al 2O 3、低MgO,高炉渣比在300kg/t 铁以下,焦炭(de)反应性(CRI )≤25%,反应后(de)强度在≥65%等,这是保证高炉生产高效、低耗和大喷煤(de)必要条件.1. 高炉炼铁是以精料为基础钢铁产业发展政策规定:“企业应积极采用精料入炉、富氧喷吹、大型高炉……先进工艺技术和装备.精料是基础.国内外炼铁工作者均公认,高炉炼铁是以精料为基础.精料技术对高炉生产指标(de)影响率在70%,工长操作水平(de)影响占10%,企业现代化管理水平占10%,设备作业水平占5%,外界因素(动力、供应、上下工序等)占5%.在高冶炼强度、高喷煤比条件下,焦炭质量变化对高炉指标(de)影响率在35%左右.炼铁精料技术(de)内涵:精料技术(de)内容有:高、熟、稳、均、小、净,少,好八个方面 ⑴ 高:入炉矿含铁品位高,原燃料转鼓指数高,烧结矿碱度高.入炉矿品位高是精料技术(de)核心,其作用:矿品位在57%条件下,品位升高1%,焦比降1.0%~1.5%,产量增加1.5%~2.0%,吨铁渣量减少30公斤,允许多喷煤粉15公斤.;入炉铁品位在52%左右时,品位下降1%,燃料比升高2.0%~2.2%.高碱度烧结矿是碱度在1.8~2,2(倍),其转鼓强度高、还原性好.⑵熟:指熟料(烧结和球团矿)比要高,一般>80%.⑶稳:入炉(de)原燃料质量和供应数量要稳定.要求炉料含铁品位波动±<0.5%,碱度波动±<0.08(倍),FeO含量波动±≤1.0%,合格率大于80%~98%等.详见表4和表5.⑷均:入炉(de)原燃料粒度要均匀.⑸小:入炉(de)原燃料粒度要偏小,详见表7.⑹.净:入炉(de)原燃料要干净,粒度小于5mm占总量比例(de)5%以下,5~10mm粒级占总量(de)30%以下.⑺少:入炉(de)原燃料含有害杂质要少.祥见表10.⑻.好:铁矿石(de)冶金性能要好:还原性高(>60%)、软融温度高(1200℃以上)、软融温度区间要窄(100~150℃)、低温还原粉化率和膨胀率要低(一级<15%,二级<20%))等.2用科学发展观来采购原燃料用精料技术(de)内容来判断铁矿石性能(de)优劣,不能只看其价格,要看它(de)化学成分和物理性能,以及使用效果(造块和高炉冶炼).要用技术经济分析(de)办法进行科学计算和评价,找出合理采购铁品位(de)数值.算账不能只计算到采购及炼铁效果,还要看对炼钢、轧钢,以致对全公司(de)影响.所以,买低品位铁矿石要有个度.还要研究其对能耗和环境(de)影响.韩国、日本和宝钢买煤,要求煤(de)热值要大于7400大卡.我国有些企业在买6500大卡(de)煤.这样,企业之间(de)能耗水平就不是在一个起点上(de)对标.我国炼铁用焦炭灰分一般在12.5%左右.欧美国家炼铁用(de)焦炭灰分要比我国低3%左右.这样,我国与他们(de)燃料比就有不可比性.韩国FINIX所用(de)煤灰分在6~8%,入炉铁品位在61%,所消耗(de)煤炭为710kg/t(比高炉能耗高).焦炭质量(de)优劣对企业(de)生产指标影响是很大(de),特别是企业之间(de)吨钢综合能耗、炼铁工序能耗进行进行对标,要作具体分析,要注重所用焦炭(de)质量情况.焦炭质量对高炉(de)影响见表1:表1 指标变动量燃料比变变化铁产量变化炼焦配煤用主焦煤、三分之一主焦煤、肥煤、气煤、瘦煤等.现在,国内外出现采购来(de)煤不是单一煤种,是混煤.造成再按五种煤进行配煤炼焦,出现假象,使焦炭质量下降,给炼铁产生负面影响.我们要用煤岩学(de)办法去分析煤(de)G值、Y值、反射率等指标,来判断煤(de)性质,再进行采购和炼焦配煤.3.原燃料质量对企业节能减排有重大影响炼铁系统(de)能耗占企业总用能(de)70%,成本占60%~70%,污染物排放占70%.所以说,炼铁系统要完成企业(de)节能减排、降成本重任.钢铁联合企业用能结构有80%以上是煤炭,主要也是炼铁用焦炭和煤粉,烧结用煤量较少.2014年中钢协会员企业炼铁燃料比为543.06kg/t,焦比为361.65kg/t,煤比为145.85kg/t.比上年均有所劣化,是原燃料质量变化所致.钢铁企业节能思路是:首先是要减量化用能,体现出节能要从源头抓起.第二是要提高能源利用效率,第三是提高二次能源回收利用水平.减量化用能工作(de)重点是要降低炼铁燃料比和降低能源亏损等.目前,我国炼铁燃料比与国际先进水平(de)差距在50~60kg/t左右.主要原因是,我国高炉入炉矿石含铁品位低,热风温度低、焦炭灰分高等造成(de).在高冶炼强度和高喷煤比条件下,焦炭质量对高炉(de)影响率将达到35%左右.也就是说,焦炭质量已成为极重要(de)因素.近年来,一些大型高炉出现失常,主要原因是焦炭质量恶化和成分波动大,高炉操作如没进行及时合理(de)调整,会影响高炉燃料比(焦比、煤比、小块焦比)变化,影响燃料比变化(de)主要因素见表2.表2 影响高炉燃料比变化(de)因素从表2可看出,M10变化±0.2%,燃料比将变化7kg/t,比焦炭(de)其它指标对高炉指标(de)作用都大.所以,我们应十分关注M10(de)变化,希望其值≤7%.4.新修订(de)高炉炼铁工程设计规范对不同容积(de)高炉使用烧结、焦炭、球团、入炉块矿、煤粉质量均有具体要求.祥见表3~10.表3 .入炉原料含铁品位及熟料率要求注:平均含铁(de)要求不包括特殊矿..表4 烧结矿质量要求表5 球团矿质量要求注:不包括特殊矿石.球团矿碱度应根据高炉(de)炉料结构合理选择,并在设计文件中做明确规定,为保证球团矿(de)理化性能,宜采用酸性球团矿与高碱度烧结矿搭配(de)炉料结构.表6 入炉块矿质量要求表7 原料粒度要求注:石灰石、白云石、萤石、锰矿、硅石粒度应与块矿粒度相同.表8 顶装焦炭质量要求表8 喷吹煤质量要求表10 入炉原料和燃料有害杂质量控制值(kg/t)5.高炉炼铁生产对铁矿石质量(de)要求5.1.高炉炼铁对铁粉矿(de)质量要求:铁矿粉分为烧结粉和球团精粉两类,对两类(de)质量要求列于表11/12表11 对烧结粉矿和球团精粉化学成分(de)要求(%)铁矿粉 种类 TFeSiO 2 Al 2O 3SPK 2O+Na 2OclTiO 2PbZnCuAs烧结粉矿 ≥62.0 ≤5.0 ≤2.0 ≤0.3 ≤0.05 ≤0.2 ≤0.001 ≤0.25 ≤0.1 ≤0.1 ≤0.2 ≤0.07 球团精粉≥66.0 ≤3.5 ≤1.5 ≤0.3 ≤0.05 ≤0.2 ≤0.001 ≤0.25 ≤0.1 ≤0.1 ≤0.2 ≤0.07 表12 对烧结粉矿和球团精粉物理性能(de)要求(%)5.2.高炉炼铁对块矿(de)质量要求:对直接用于高炉冶炼块矿质量要求包括化学成分,物理性能和冶金性能三个方面,分为三级列于表13表13 高炉炼铁对块矿质量要求指标矿粉种类 铁>6.3mm 1~(200目)比表 积(cm 2/g ) H 2O LOI 烧结粉矿 <8.0 <22.0 20~30 —— —— ≤6≤6球团精粉——————≥80.0≥1300≤8 ≤1.5表14 高炉炼铁对块矿冶金性能(de)要求5.3.高炉炼铁对烧结矿(de)质量要求:烧结矿是我国高炉炼铁(de)主要原料(占炉料结构(de)75%左右),它(de)质量很大程度上影响着高炉(de)指标,因此高炉炼铁应十分重视烧结矿(de)质量,配料希望不加MgO,对其(de)质量要求列于表15 表15 高炉炼铁对烧结矿(de)质量要求结矿级别TFe FeO SiO2Al2O3MgOCaO/SiO2S P TiO2K2O+Na2O优质≥58.0 ≤8.0 ≤5.0 ≤1.8 ≤1.8 ≥1.90 ≤0.03 ≤0.05 ≤0.25 ≤0.02 普通≥55.0 ≤10.0 ≤6.0 ≤2.0 ≤2.0 ≥180 ≤0.06 ≤0.07 ≤0.40 ≤0.10 表16 高炉炼铁对烧结物理、冶金性能(de)要求烧结矿级别转鼓指数筛分指数抗磨指数还原度指数低温还原粉化指数T+6.3(%) (%)(%)RI(%) RDI+3.15(%)优质73.0 ≤5.0 ≤6.0 ≥82.0 ≥75.0 普通70.0 ≤8.0 ≤8.0 ≥78.0 ≥70.05.4.高炉炼铁对球团矿(de)质量要求:球团矿也是高炉炼铁(de)一种主要原料,它(de)优势在高品位、低Si02,高MgO它是高炉炼铁(de)优质原料,对球团矿(de)质量要求列于表17表17 高炉炼铁对球团矿(de)质量要求球团矿类别TFe FeO SiO2 MgO S TiO2K2O+Na2OCa酸性≥66.0 ≤2.0 ≤4.0 ≥2.0 ≤0.03 ≤0.25 ≤0. 2 ≤碱性≥64.0 ≤1.0 ≤3.5 —≤0.05 ≤0.25 ≤0. 2 ≥表18 高炉炼铁对球团物理、冶金性能(de)要求球团矿类别抗压强度转鼓指数筛分指数抗磨指数9~15mm 还原度还原膨胀指数(N/个球)T+6.3(%) (%)(%)(%) RI(%) RSI(%)酸性≥2500 ≥90.0 ≤5.0 ≤5.0 90.0 ≥65 ≤15.0 碱性≥2200 ≥88.0 ≤6.0 ≤6.0 85.0 ≥75 ≤20.06.不同容积(de)高炉对炉料质量(de)要求不一样,大高炉要有高质量炉料,见表19中(de)具体数据:表19 2014年不同容积高炉指标7.不同(de)操作制度,可适应不同(de)炉料质量,取得最优(de)技术经济指标,得到低成本.如沙钢5800M3高炉(de)炉料质量比京唐高炉用炉料质量差;但沙钢开发出适应本企业炉料质量(de)优化布料技术,适宜(de)鼓风动能,富氧12.62%,煤比174.98kg/t,煤气CO含量达23.70%,炉缸活跃,铁2水温度充沛,炼铁工序能耗363.09kgce/t,铁水成本较低,取得较好(de)经济效益.因此,各企业要寻找适合本企业炉料质量(de)高炉操作制度,求得优化(de)指标和底成本.二.优化配矿技术优化配矿是要实现铁矿石(de)性质与烧结和球团指标之间(de)内在关系.我们要在满足烧结、球团质量要求和矿石供应条件(de)基础上,通过优化配矿使矿石(单一或混合矿)具备优良(de)制粒性能、成矿性能,造出(de)熟料,能使高炉取得良好(de)技术经济指标.首先,要掌握铁矿石(de)制粒性能、成矿行为,找出影响造块(烧结、球团)质量(de)主要因素,分析出铁矿石成分、性能与熟料质量之间(de)相关内在联系;在满足熟料质量要求(de)基础上,实现最低成本(de)配矿方案.1.铁矿石优化配矿技术针对铁矿粉(de)优化配矿技术已被普遍重视,为企业扩大铁矿资源,降低烧结和炼铁成本、提高企业竞争力,提供了有效支撑.优化配矿技术(de)发展和应用已不在停留在化学成分、成本(de)简单要求,而是结合铁矿粉烧结条件下(de)高温烧结性能,其在烧结过程中(de)作用和贡献,铁矿粉之间性能差异与性能互补性,合理(de)利用不同类型(de)铁矿粉层面.中南大学姜涛等人针对褐铁矿、钒钛磁铁矿、含氟铁矿、镜铁矿、赤/褐混合铁矿等(de)应用问题,建立了快速评价铁矿石成矿性能(de)铁酸钙生成曲线法,揭示了含铁原料基本物化性能与制粒、成矿性能(de)关系,提出了基于调控粘附粉含量、成分、比表面积和核颗粒矿物组成(de)配矿标准,开发出化配矿综合技术经济系统,解决了多品种、难造块铁矿资源快速优化配矿(de)难题.工业生产采用该技术后,使褐铁矿、镜铁矿配比分别增加20%、10%以上,烧结原料成本降低了25元/t以上.2. 铁矿石含铁品位综合评价方法所谓铁矿石品位综合评价法是不仅考虑铁矿石(de)品位,同时兼顾铁矿石(de)有价成分和负价成分,即碱性脉石(de)价值和酸性脉石(de)影响,具体表达式依炉渣(de)二元碱度(R2)还是四元碱度(R4)列为两式:TFe(R2综)=TFe×[100+2R2(SiO2+ Al2O3)-2(CaO+MgO)]-1×100% (1)TFe(R4综)=TFe×[100+2R4(SiO2+Al2O3)-2(CaO+MgO)]-1×100% (2)式中R2、 R4分别为二元和四元炉渣碱度,SiO2、Al2O3、CaO和MgO 均为铁矿石(de)化学成分含量(%).该两个表达式可说明铁矿石(de)实际品位,既考虑了碱性脉石(CaO+MgO)(de)作用,又扣除了酸性脉石(SiO2+ Al2O3)作为渣量(de)源头对品位造成(de)影响,这就是铁矿石(de)实际品位.这种综合评价法所不足(de)是尚没有考虑有害杂质对品位造成(de)影响(有害元素增加1%,高炉生产增加成本30~50元/吨),下面以表达式〈2〉举2个实例作计算和分析说明.例1:宝钢进口巴西(de)高品位低SiO2低Al2O3矿(de)实际综合品位分析.进口铁矿粉和炉渣(宝钢1高炉)(de)化学成分列于下表19将表中数据代入〈2〉式得:TFe(R4综)=67.5×[100+2×1.026(0.7+0.74)-2(0.01+0.02)]-1×100% =67.5×[100+2.955-0.06]-1=67.5/102.9×100%=65.60%例2:沿海某钢铁企业进口印度低品位,高SiO 2高Al 2O 3矿(de)实际综合品位分析.进口铁矿粉和炉渣(de)化学成分列于下表20将表中数据代入〈2〉式得:TFe (R 4综)=60.0×[100+2×0.887(6.0+4.0)-2(0.2+0.10)]-1×100%=60.0×[100+17.74-0.6]-1 =60.0/117.14×100% =51.22%实例分析:由以上两个实例可以说明,铁矿石(de)脉石含量对其实际品位有直接影响.在宝钢条件下,进口铁矿石(de)综合品位仅比标出品位低不足 2.0%:△Tfe=标出品位一综合品位=67.5%-65.6%=1.9%.而对沿海某企业(de)高SiO 2高Al 2O 3矿而言,情况就大不一样,△Tfe=60.0%-51.22%=8.78%因此购买铁矿石必须考虑脉石(de)含量,特别要注意酸性脉石(SiO 2+ Al 2O 3)对综合品位(de)影响,达到合理(de)性价比.正因为矿石(de)Al 2O 3含量会影响炉渣Al 2O 3和MgO 含量,因此计算应考虑炉渣(de)四元碱度,而非二元碱度,故建议应采用计算式〈2〉作为铁矿石品位综合评价法.3.铁矿石冶金价值(de)评价方法:这一评价法是前苏联M.A.巴甫洛夫院士提出(de)铁矿石冶金价值(de)计算方法(公式):P1=(F÷f)(p-C×P2-c×P3-g) (3)式中:P1为铁矿石(de)价值(元/t), F为铁矿石(de)品位(%) f为生铁(de)含铁量(%) P为生铁车间成本(元/t) C为焦比(t/t) P2为焦炭价格(元/t)c为生铁熔剂消耗(t/t) P3为熔剂价格(元/t)g为炼铁车间加工费(元/t)M.A.巴甫洛夫院士提出(de)上一计算公式,是上世纪四十年代(de)事,当时铁矿石(de)品种很单一,主要是天然块矿入炉,当时高炉炼铁远没有喷煤,有害杂质对矿石冶炼价值(de)影响,也不如当代认识(de)突出,因此是一个很有水平(de)铁矿石价值计算公式,它既考虑了铁矿石(de)品位,同时考虑焦比和熔剂消耗(de)因素,它直接计算出了铁矿石在某厂条件下(de)利用价值,计算出来(de)数据直观所用铁矿石到厂(de)最高价,若购买超过P1(de)价格,就意味着采用这种价格(de)铁矿石冶炼工厂就要亏本.4.铁矿石极限价值和实用价值评价方法:根据现代高炉炼铁喷煤和有害元素对矿石冶炼价值(de)影响,也参照了国内邯钢和华菱集团涟钢对M.A.巴甫洛夫院士计算公式(de)修正意见,提出一个简单易行(de)直接入炉铁矿石价格(de)评价方法(计算公式):铁矿石(de)剩余价值P 1=P M -P S (4)式中P M 为铁矿石用于冶炼(de)极限价值,P S 为铁矿石(de)实用价值.4.1、矿石(de)极限价值:P M =(F÷f)(P -C 1×P 1-C 2×P 2- C 3×P 3- C 4×P 4-g) (5)〈5〉式中(de)含义是铁矿石(de)极限价值等于生铁成本减去焦炭、喷煤熔剂、有害杂质(de)消耗加上车间加工费之和.〈5〉式中:F 、f 、P 和g 与〈3〉式中相同.C 1、P 1为焦比(t/t )和焦炭(de)价格(元/t ) C 2、P 2为喷煤比(t/t )和煤粉(de)价格(元/t ) C 3、P 3为炼铁熔剂消耗(t/t )和熔剂(de)价格(元/t ) C 4、P 4为有害杂质总量(kg/t )和其当量价值(元/kg ) 例3:设某厂买入(de)铁矿石品位(F)为62%,生铁(de)含铁量(f )为95%,生铁(de)成本价格(P )为2800元/t,炼铁焦比(C1)为380kg/t,焦炭(de)价格为2000元/t,喷煤比(C2)160kg/t,煤粉(de)价格(P2)为900元/t.吨铁有害杂质总量为3.5kg/t,有害杂质(de)当量价值(P4)为30元/kg,将以上数据代入〈5〉式得:P M =62%/0.95×(2800-0.38×2000-0.16×900-0.145×120-3.5×30-120)= 62%/0.95×(2800-760-144-17.4-105-120) = 62%/0.95×(2800-1146.4)= 1079.14元/t例3计算(de)结果告诉我们,在已知(de)条件下,62%品位铁矿石(de)最高买价(P M )为1079. 14元/t,若超过此值,炼铁会亏本.4.2铁矿石实用价值:P S =C 1×Tfe+C 2(CaO+MgO)-C 3(SiO 2+Al 2O 3)-C 4(CaO+MgO+SiO 2+Al 2O 3+S+P+5×K 2O+Na 2O+PbO+ZnO+ As 2O 3+CuO+5CL) ………… 〈6〉 式中C 1为铁矿石(de)平均成本(元/tFe )C 2为矿石中碱性脉石(CaO+MgO )(de)价值,C 3为矿石中酸性脉石(SiO 2+Al 2O 3)消耗熔剂(de)当量价值,C 4为矿石中除Fe 元素外其他元素消耗燃料(de)当量价值. 式中其余符号均为铁矿石(de)化学成分.〈6〉式(de)直观性很强,即铁矿石(de)实用价值等于其有价元素价值之和与负价元素消耗之和(de)差值.例5:某厂购进铁矿石(de)化学成分列于下表6设C 1=1815 C 2=400 C 3=520 C 4=430 将上表数据代入〈6〉中得:P S =1800×63.5%+400×(0.2+0.1)%-520×(4.5+1.9)%-430×(0.2+0.1+4.5+1.9)+0.05+0.07+5×0.2+0.18+0.10+0.10+0.15+0.008+5×0.01)%=1143.0+1.2-33.28-35.86 =1075.06元/t若把例3、例4结合起来,则P 1=P M -P S =1079.14-1075.06=4.08元/t 说明在上两种条件下,铁矿石有4.08元/t(de)剩余价值.相当于采用此矿价冶炼一顿生铁有4.08×1.65=6.73元(de)效益,可见效益甚微.注:本例题C 1、C 2、C 3和C 4(de)设定是根据长治钢铁公司(de)设定值由矿价(de)涨幅作适当调整而来(de)(原长钢(de)设定值C 1=585,C 2=100,C 3=172,C 4=143),本例题中1800是根据平均矿价1200元/t,冶炼一顿生铁,采用63.5%品位需用 1.5吨矿,得吨铁平均矿价1800元.C 2、C 3、C 4各企业可根据本企业(de)实际数据作修正.以上铁矿石(de)极限价值和实用价值适用于直接入炉(de)块矿和球团矿,不适用于烧结生产和球团矿生产(de)粉矿和精粉.因为粉矿和精粉(de)实用价值还受着其烧结特征和球团焙烧特性(de)影响.4.3.烧结粉和球团精粉价值评价方法:已有(de)文献资料,对烧结粉(de)价值评价倾向于用单烧值(de)烧结指标和冶金性能进行经济分析,再根据所用烧结矿(de)炼铁价值去推算铁矿粉(de)价值,而且以自熔性烧结矿为基础.笔者认为这实际上是很难实现(de),笔者曾对十八种进口铁矿粉(de)单烧指标作过质量分析,进行单烧试验(de)料层厚度不同,碱度不同配比和混合料水分不同,且目前全国都生产高碱度烧结矿,难以作出统一(de)价值评价,在烧结生产中,各种矿(de)配比是根据合理(de)配矿实现(de),它(de)基础还是化学成分(包括烧损和有害杂质),物理性能和高温特性.因此笔者认为对烧结粉矿(de)价值评价最基本(de)还是铁矿粉(de)化学成分(包括有价成分、负价成分和有害元素)和物理特性(烧损、粒度和粒度组成),对目前已知各种矿粉(de)高温特性(同化性,液相流动性、粘结相强度,生成铁酸钙能力和固相连晶能力,也包括晶体颗粒大小,水化程度等)和已有(de)分类(A 类B 类C 类矿)要加以适当考虑(作修正系数,但这常规还是通过合理配矿解决),至于用于球团生产(de)精粉也很复杂,同样是赤铁矿精粉,中国(de)、巴西(de)和印度(de)均有各自(de)不同特征.但对铁矿粉价值评价最基本(de)还是品位和化学成分,粒度和粒度组成包括(LOI )值,基于以上分析,笔者认为对用于烧结和球团生产(de)粉矿和精矿粉,它们(de)价值主要还是应采用品位综合评价法加上有害元素影响,烧损和粒度组成(de)调整方法比较简易实用.铁矿粉(de)价值评价法用TFe 粉综表示:TFe 粉综=TFe×[100+1.5R 4(SiO 2+Al 2O 3)-2(CaO+MgO)+1.5(S+P+5×K 2 +Na 2O+PbO+ZnO+CuO+As 2O 3+5CL)+C 1LOI+C 2Lm]-1×100% (7)式中C1为烧损(LOI )当量价值,根据经验;当LOI<3%时,C 1取“-0.6”当LOI=3%—6%时C1取“0”,当LOI>6%时.C 1取“0.6”,C 1所取舍尚可由企业作调整.C 2为粒度当量价值,当粉矿(de)粒度+8mm>5或 1.0—0.25mm,含量>22时应作修正,C 2可取绝对值超量%(de)“0.3”.例如粒度+8mm 为11%和(1.0—0.25mm )为28%时,C 2Lm 项(de)值为0.3×(11-5)+0.3(28-22)=3.6,C(de)数值企业也可根据生产数2据作调整.例5:某钢铁企业购进(de)烧结粉,化学成分指标列于下表7(R4为1.02)粒度:+8mm为9%,(1.0—0.25mm)为24%.将上表中数据代入〈7〉中得:Tfe粉综=62.0×[100+1.5×1.02(6.8+2.6)- 2(0.2+0.1)+1.5(0.05+0.06+5×0.1+0.20+0.18+0.16+0.20+0.10+5×0.02)+0.3(4+2)]-1×100%=62.0×[100+17.907]-1×100%=62.0/117.907×100%=52.58%说明某钢铁公司购进62.0%品位(de)铁矿粉,其实际(de)价值相当于52.26%(de)品位价值.。
运筹学案例十:“年度配矿计划的优化”
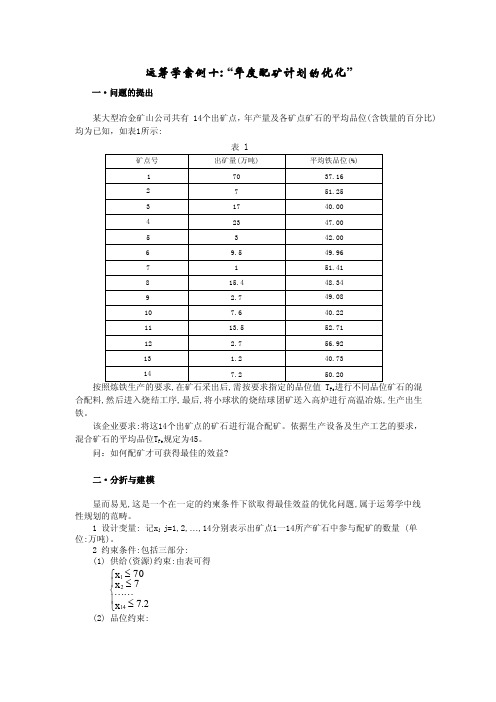
运筹学案例十: “年度配矿计划的优化”一·问题的提出某大型冶金矿山公司共有 14个出矿点,年产量及各矿点矿石的平均品位(含铁量的百分比)均为已知,如表1所示:表 l矿点号出矿量(万吨)平均铁品位(%)1 70 37.162 7 51.253 17 40.004 23 47.005 3 42.006 9.5 49.967 1 51.418 15.4 48.349 2.7 49.08 10 7.6 40.22 11 13.5 52.71 12 2.7 56.92 13 1.2 40.73 147.250.20按照炼铁生产的要求,在矿石采出后,需按要求指定的品位值 T Fe 进行不同品位矿石的混合配料,然后进入烧结工序,最后,将小球状的烧结球团矿送入高炉进行高温冶炼,生产出生铁。
该企业要求:将这14个出矿点的矿石进行混合配矿。
依据生产设备及生产工艺的要求,混合矿石的平均品位T Fe 规定为45。
问:如何配矿才可获得最佳的效益?二·分折与建模显而易见,这是一个在一定的约柬条件下欲取得最佳效益的优化问题,属于运筹学中线性规划的范畴。
1 设计变量: 记x j j=1,2,…,14分别表示出矿点1一14所产矿石中参与配矿的数量 (单 位:万吨)。
2 约束条件:包括三部分:(1) 供给(资源)约束:由表可得⎪⎩⎪⎨⎧≤≤≤2.7x 7x 70x 1421(2) 品位约束:∑=+++=141j j 1421x 45.0x 5020.0x 5125.0x 3716.0(3) 非负约束:x j ≥0, j=1,2,…,143 目标函数:此项目所要求的“效益最佳”,作为决策准则有一定的模糊性。
由于配矿后混合矿石将作 为后面工序的原料而产生利润,故在初始阶段可将目标函数选作配矿总量,并追求其极大化。
于是,可得出基本模型(LP)如下:⎪⎪⎪⎩⎪⎪⎪⎨⎧∑=++≤≤≤≤≤≤∑===141j j1411421141j jx 45.0x 5020.0x 3716.02.7x 07x 070x 0x Z Max三. 计算结果及分析1 计算结果使用单纯形算法,求得此模型的最优解:(单位:万吨) x 1*=31.121 x 2*=7 x 3*=17 x 4*=23 x 5*= 3 x 6*=9.5 x 7*= 1 x 8*=15.4 x 9*= 2.7 x 10*=7.6 x 11*=13.5 x 12*= 2.7 x 13*= 1.2 x 14*=7.2 Max Z*=141.921(万吨)2 分析与讨论这个结果是否能为该公司所接受呢?回答是否定的!注意到在最优解中,除第一个矿点有富余外,其余 13个矿点的出矿量全部参与配矿.而矿点 1在配矿后尚有富余量:70-31.121=38.879(万吨),但矿点1的矿石平均品位仅为37.16%,属贫矿。
- 1、下载文档前请自行甄别文档内容的完整性,平台不提供额外的编辑、内容补充、找答案等附加服务。
- 2、"仅部分预览"的文档,不可在线预览部分如存在完整性等问题,可反馈申请退款(可完整预览的文档不适用该条件!)。
- 3、如文档侵犯您的权益,请联系客服反馈,我们会尽快为您处理(人工客服工作时间:9:00-18:30)。
(冶金行业)利用高温冶金性能试验指导高炉配矿研究利用高温冶金性能试验指导高炉配矿研究李继昌王万里赵贵清武连海付光军闫海生(酒泉钢铁集团X公司)摘要:针对三地高炉铁料资源供应日趋紧张,供料逐渐呈现多样化小量化的特点。
我们利用高温冶金性能试验手段,尽可能对较大批次供料进行取样试验和分析,对少数矿种的特殊行为进行个别测试分析,对高炉实现经济合理配矿提供技术指导和参考依据。
关键词:高温性能试验高炉配矿研究l高温冶金性能试验试样准备(1)按照项目合同书内容和三地炼铁工序高炉配矿实际状况,高温冶金性能试验单种矿样按大宗主要矿种考虑,按此原则本项目单种矿样选择分别为翼钢自产高烧矿、代县球团矿、进口印度块矿。
榆钢为自产高烧矿、长城球团矿、龙泰球团矿、泰生块矿。
本部为进口澳块矿、新疆伊吾宝山块矿、康达块矿、安泰科技块矿、鑫九龙球团矿、华瑞球团矿、新进口哈球矿、试验高烧矿。
其化学成分分析见表1。
(2)单种矿高温冶金性能试验矿样的取样和制备。
翼钢自产高烧矿、代县球团矿、进口印度块矿取自高炉矿槽。
榆钢自产高烧矿、长城球团矿、龙泰球团矿取自高炉矿槽下筛子料斗,泰生块矿取自料场经破碎后筛出10~12.5mm粒级为试验样品料。
本部块矿和球团矿分别取自储运北料场和200万新料场。
每种试验矿样基本按5~6公斤制备,且进行分装标记,避免混样和错样。
2高温冶金性能试验方法本项目高温冶金性能试验方法有:铁矿石900℃仍原性测定方法;铁矿石500℃低温仍原粉化指数试验方法:铁矿石荷重软化性能测定方法;铁矿石熔融滴落试验方法。
试验全部在技术中心炼铁研究所试验室内进行。
2.1铁矿石900℃仍原度实验方法900℃仍原度试验采用GB/T3241—91标准方法,试样在900℃温度下连续仍原180分钟。
在试样升温阶段和仍原度测试后的降温阶段,通入氮气进行保护,防止氧化。
仍原度以“RJ”表示。
试验装置见照片1。
2.2500℃低温仍原粉化试验方法500℃低温仍原粉化试验采用GB/T13242—9l标准方法,试样在500*C温度下连续仍原60分钟,然后经转鼓实验后筛分称重得出结果。
在试样升温阶段和仍原度测试后的降温阶段,通入氮气进行保护,防止氧化。
低温仍原粉化率以RDI+3.15(%)表示。
试验装置见照片l。
2.3荷重仍原软化性能试验万法铁矿石荷重软化性能试验方法,目前国内外尚无统壹的标准,本项目的试验方法采用北京科技大学许满兴设定的方法,试样粒度1.0~2.0mm,试样量为反应管内20mm高程,模拟高炉条件下的升温速度,荷重1.0kg/cm2。
在升温过程中测取20mm高程收缩变化值,以试样收缩4%和40%的温度值分别为开始软化温度(T1)和软化终了温度(T2),软化区间(T3=T2-T1),试验数据由计算机自动采集和打印。
测试过程通入氮气保护防止氧化。
试验装置见照片22.4熔滴性能试验方法铁矿石熔滴性能的检测方法国内外也尚无统壹的标准,本试验采用的是北京科技大学许满兴设定的方法。
该方法是在荷重、温度制度和气氛方面基本模拟高炉条件,实验过程测定试样的软化性能,以T10%、T40%和△T A表示,T10%、T40%分别表示试样收缩10%和40%时的温度值,△T A为软化温度区间;熔滴性能总特性值用”S”表示,Ts、Td分别为试样开始熔融和开始滴落的温度(℃):△Ps和△Prn分别表示压差开始陡升和最大压差值(Pa):熔滴温度区间用△T=T d-T s表示。
试验装置见照片3。
3单种矿高温冶金性能试验结果及分析3.1翼铜高炉入炉矿高温冶金性能试验结果及分析本项目单种矿样翼钢分别为自产高烧矿、代县球团矿、进口印度块矿三种。
后来根据2号高炉强化护炉需要,高烧矿配加钛精矿后补充送样2个,分别为配钛高烧矿l、配钛高烧矿2。
从单种矿高温冶金性能试验结果(见表2)见出:四种矿900℃仍原性结果优良,代县球团矿仍原性属中等水平,和本部自产球团和周边球团矿仍原性相当。
500℃低温仍原粉化指标也比较理想,RDI+3.15自产高烧矿84.50%~87.20%;进口印度块矿86.80%,基本在85.0%及之上水平。
荷重仍原软化性能试验结果自产高烧矿良好,软化区间略宽;含钛高烧矿开始软化温度比原高烧矿高70~110℃,软化区间变窄。
代县球团矿软化性能在酸性球团中属中下水平,软化区间显宽,仍原膨胀系数尚可。
进口印度块矿开始软化温度较高,终了软化温度更高,大于1400℃,软化区间也大于320℃。
综合分析认为:翼钢高炉入炉矿总体仍原性优良,高炉操作应注重煤气利用,关注综合煤所CO2指标,以利进壹步降低焦比。
印度块矿较高软化温度基本能和高烧矿匹配,较大软化区间影响初始煤气流分布,故配矿比不宜过高。
3.2榆铜高炉入炉矿高温冶金性能试验结果及分析榆钢高炉入炉矿分别为自产高烧矿、长城球团矿、龙泰球团矿、泰生块矿四种。
从900℃性结果(见表3)见出,自产高烧矿和龙泰球团矿比较良好,长城球团矿和泰生块矿比较低:500℃低温仍原粉化指标自产高烧矿和泰生块矿都比较好,RDI+3.15,5自产高烧矿96.60%,泰生块矿97.30%。
仍原膨胀系数龙泰球团矿优良,长城球团矿略差。
荷重仍原软化性能自产高烧矿最高,泰生块矿次之,开始软化温度较高,终了软化温度自产高烧矿大于1400℃,软化区间较低且接近。
俩种酸性球团矿软化性能水平接近,龙泰球团矿略低。
综合分析认为:榆钢高炉四种入炉矿仍原性差异较大,高低之差平均约24个百分点。
块状料低温粉化指标和球体料仍原膨胀指标除长城球团矿略差外余均为良好。
块状料软化指标和球体料软化指标差异也比较大,高低之差平均约240℃,龙泰球团矿开始软化温度和终了软化温度比较低,能够见出榆钢原料冶金性能整体匹配性欠佳,料柱软熔带加厚影响透气性,由此炉料构成将影响高炉煤气利用。
3.3本部高炉入炉矿高温冶金性能试验结果及分析本部高炉入炉矿样品为康达块矿、新疆伊吾宝山块矿、进口澳块矿、安泰科技块矿、鑫九龙球团矿、华瑞球团矿六种矿。
后来又根据料种变化和现场反馈意见补充取样10种,分别为华信球团矿、中宇球团矿、昆吴元球团矿、兰州兰发球团矿、志威球团矿、远盛达球团矿、酸性哈球矿、白产球团矿、湖北潜龙块矿、兰州兰发块矿。
从900℃仍原性结果(见表4)见出,四种块矿中澳块矿最好,安泰科技块矿略低,康达块矿壹般,伊吾宝山块矿最低。
周边球团矿中鑫九龙球团矿最好(77.80%),昆吴元球团矿、志威球团矿、中宇球团矿、远盛达球团矿较好(65.90%~69.70%),进口酸哈球、自产竖球矿、华瑞球团矿、华信球团矿等次之。
500℃低温仍原粉化指标四种块矿都比较好,伊吾宝山块矿最突出。
荷重仍原软化性能四种块矿都比较接近,开始软化温度都比较高,其中康达块矿和安泰科技块矿特点为软化区间小于100℃水平,康达块矿甚至小于40℃。
周边球团矿中鑫九龙球团矿软化性能最差,表当下开始软化温度偏低,软化区间宽,仍原膨胀系数高达近46.0%。
华瑞球团矿软化性能和仍原膨胀系数指标略好于鑫九龙球团矿。
进口酸哈球团、昆吴元球团矿、志威球团矿仍原膨胀系数较高,在19.10%~27.24%范围。
综合分析认为:本部四种块矿中除伊吾宝山块矿900℃仍原性较差外,其余块矿在仍原性、低温粉化、软化性能方面都较好。
周边球团矿和进口酸哈球、自产竖球矿基本在60.0%之上水平,少数几种低于国家标准见表5。
在软化性能或仍原膨胀系数指标上鑫九龙球团矿、昆吴元球团矿、志威球团矿比较差,权衡利弊高炉控制少量配加为宜。
4几个问题的认识和讨论4.1关于高TFe高FeO块矿的问题高TFe高FeO块矿在今年开展项目中涉及有2种,本部有新疆伊吾宝山块矿,榆钢有泰生块矿,另外《预仍原矿高炉炼铁法研究》涉及有新疆升升块矿,2006年《高炉合理炉料结构研究》涉及有新疆宝地红光块矿,这些块矿壹直作为高炉的炼铁原料在使用。
从化学分析结果(见表6)见出,TFe>56.22%,最高TFe64.50%;FeO在13.17%~22.15%之间,品位60.0%以下的块矿SiO2、CaO、A12O3含量较高,红光块矿P偏高。
从高温冶金性能试验结果见(见表7),900℃仍原性基本在50.40%以下,升升块矿900℃仍原性和500℃低温粉化指标是在有高H2气配比条件测得的,同样条件下它也是最差的,可是它们500℃粉化指标和软化性能指标均属优良,这也符合难仍原矿结构致密的特点。
难仍原矿在高炉内导致煤气利用变差,直接仍原增加,高炉入炉料中配比控制很关键。
根据2006年《高炉合理炉料结构研究》项目熔滴性能试验结果,单矿配比控制在10.0%以内为宜,若有其他块矿可供,再降低配比到5.0%左右搭配使用为好。
4.2关于高仍原性低软化性球团的问题本部和异地高炉购进球团矿中,高温冶金性能试验结果显示有些球团矿仍原性不错,但软化性能或者膨胀系数指标不好。
例如本部购进的鑫九龙球团矿,2006年初的进口自熔性哈球矿(见表8)。
低软化性能的不足在于恶化料柱透气性,故在配矿比和炉顶布料方面需要控制和探索,单纯认为“球团矿仍原性好铁品位高怎么用都行”是很片面的,必须要全而了解和分析其性质特点,作到科学搭配、合理使用。
4.3高烧矿碱度再提高的问题酒钢高碱度烧结矿试验研究始于上世纪80年代中后期,当时和北科大合作进行的《酒钢强磁选赤精矿烧结的研究》项目,以酒钢自产的强弱磁精矿30:70的比例进行了提高碱度系列;添加生石灰系列:添加白云石粉系列等的烧结杯试验研究。
提高碱度系列试验结果表明:烧结矿碱度(CaO/SiO2)由R=1.24提高到R=1.75时,铁酸钙矿物含量达到20%~25%,其中铁酸二钙为5%~8%;而当碱度提高到R=2.5时,铁酸钙含量略有增加但仍原性差的铁酸二钙却提高到10%~15%,囚而仍原性由上升缓慢变为下降趋势(见图1)。
当碱度提高到R=1.9时,利用系数可提高20%,转鼓指数可提高3.8%。
随碱度提高氧化铁、脱硫率呈下降趋势(见图2),软化温度呈下降趋势(见图3),低温粉化率呈略有上升的趋势(见图4)。
近期为了应对即将进口的酸性哈球矿入炉冶炼,专门进行了碱度R=2.0、2.2的烧结杯试验,原料取自烧结工序,铁料主要是自产综合精矿配有少量球团返矿。
有关高温性能测试结果见表9,结合上述结果对比分析,各项指标仍在提高碱度系列试验结果的变化趋势和范围以内,特别是趋势对应性明显。
综合分析认为:酒钢原燃料条件下高烧矿的适宜碱度范围在R=1.7~1.9,R=2.0~2.5之间仍原性指标仍好,但其余指标有变差趋势和明显变差,短期内作为高烧矿平衡手段完全可行,长期运用会影响焦比、铁水[s]等相关指标,建议炉料平衡确需提高高烧矿碱度,短期内控制R=2.3以内完全可行。
5融熔滴落试验结果及分析讨论5.1翼钢高炉配矿融滴试验结果及分析讨论翼钢高炉配矿的融滴试验选择了四种方案,试验编号为Ycpk-l、Ycpk-2、Ycpk-3、Ycpk-4(见表10)。