钢烧结矿烧结指标及冶金性能的影响
210978870_烧结负压对烧结矿质量的影响

管理及其他M anagement and other烧结负压对烧结矿质量的影响王 彬1,汪世峰1,丁广伟1,杨爱民2,3,4,5,6,李 杰2,3,4,5,6摘要:中国钢铁行业存在烧结矿质量低下的问题,因此提高烧结矿质量对于钢铁行业发展起到重要作用。
烧结生产的工艺流程复杂,需要优化和调整的细节较多,如烧结负压、燃料配比、料层高度等因素均对烧结矿的质量产生较大影响。
为了进一步提高烧结矿的质量和成品率,本文展开了一系列相关研究。
研究结果表明,随着烧结负压的增加,烧结时间变快、废气温度降低、烧结矿成品率、<10mm粒级指标变差、烧结矿转鼓强度变差。
因此在实际生产中要合理控制烧结负压,从而得到理想指标的烧结矿,这对于改善烧结矿产质量和优化烧结工艺具有重要的指导作用。
关键词:烧结矿;烧结负压;烧结矿性能;烧结优化随着经济社会的发展,我国对于钢铁的需求迅速增加,钢铁的质量问题变得尤为重要,烧结矿作为钢铁主要原材料,如何提高烧结矿的质量成为了核心问题。
在烧结生产的过程中,主要的工艺参数为:料层高度、混合料水分、燃料配比、烧结负压,这些参数对烧结矿的质量产生直接影响。
印度金尔尔钢铁公司曾在烧结料层上开展了烧结负压在900mm~1700mm水柱范围内的烧结杯试验。
试验结果表明:在1300mm水柱负压下,烧结机的利用系数达到最大。
我国首钢、武钢和梅山等厂也曾对抽风机转子进行了改造,通过提高抽风负压,实验也取得了不同程度的效果。
Xinying Ren等利用转鼓指数的变化对烧结矿质量的影响进行了研究,利用机器学习相关算法预测了烧结转鼓强度,通过大量数据试验建立了有关转鼓指数的预测模型。
张兰泉在《烧结过程大风量高负压问题的探讨》中探讨了负压对烧结矿的厚度以及生产率的影响,指出风机负压提高,适宜的料层厚度会随之提高;料层的厚度增加生产率得到提高,但达到一定程度后生产率则会有所降低。
周江虹在《烧结过程风量合理分布实验研究》中通过烧结杯模拟,改变烧结负压,在最优的方案下提高了烧结成品率、利用系数以及垂直烧结速度。
不同碱度对烧结矿冶金性能的影响

不同碱度对烧结矿冶金性能的影响摘要:在龙钢公司3#配比基础上,保持FeO在9.5±0.5范围内,通过碱度的变化,对烧结矿低温粉化指数、高温还原指数等方面进行研究。
低温粉化率在2.1±0.05左右最佳,高温还原率在2.0±0.05最佳。
综合评定当FeO稳定在9.5±0.5,碱度在2.0±0.05时烧结矿冶金性能最好。
关键词:碱度低温粉化高温还原冶金性能1前言近年来随着内外的试验研究及现有的烧结规律研究表明,当碱度升高达到一定值时,其冶金性能达到最好状态,当碱度再次升高时,其冶金性能状态有所下滑。
近年来,随着烧结技术的提升,对生产质量的要求也越来越高,合适的碱度变化成为烧结研究的主要问题。
本文主要研究碱度含量对烧结矿冶金性能的影响,通过合理的控制碱度来降低成本,稳定烧结矿质量,进而保证高炉的顺利运行,从而为公司降本增产提供有利的指导性参考。
2实验原料主要原料包括超特、巴混、纽曼及生灰、返矿、固体燃料等。
实验原料均取自烧结原料现场,所有原料均科学随机取样并且一次性取够八次实验所需的样。
实验原料化学成分见表1。
3实验方法与方案3.1实验方法实验参数混合料水分为7.0±0.2%,烧结杯为Ø300X1000mm,混合料质量为110kg,混合时间为300s,烧结料层厚度为800mm,烧结点火温度为1200℃,点火时间为30s,烧结点火负压为12KPa,铺地料5kg。
实验将烧结废气开始下降定为烧结终点,采用人工布料,烧结过程用计算机控制。
3.2试验方案设计五组烧结杯试验,其中FeO均控制为9.5±0.5,碱度含量分别为2.1±0.05,2.0±0.05,1.9±0.05,1.8±0.05,1.7±0.05,分别对应方案1-5,对烧结矿冶金性能进行研究;表1 含铁原料化学成分/%名称烧损率TFeFeOSiO2CaOMgOAl2O3矿1956.45.88.08.083.2矿23.9662.6.724.62.02.061.58矿35.6154.4.489.25.09.13.6矿44.5462.454.19.09.162.32矿5505002A.499.6.11.03.09.87矿B 2.559.85.5.34.22.59矿C -1.0963.226.623.44.434.11.08矿D 1.661.68.65.61.14.761.1矿E 7.0559.7.434.49.02.052.4矿F-1.862.7255.26.873.87.75矿G-1.8463.124.311.07.55.341.64表2 烧结矿主要成分/% 表3低温还原粉化、还原度指数/%实验方TFe%FeO%SiO2%CaO%MgO%Al2O3%案方案155.019.045.3411.122.002.18方案255.699.485.2910.471.822.04方案355.139.285.4510.561.852.18方案455.809.725.369.501.772.08方案556.329.095.209.111.712.186.3mm% 3.15mm%5mm%I%方案144.172.037.6961.332.08方案237.9770.836.4675.901.98方案337.5668.338.4673.061.94方案429.1165.78.7174.061.77方案536.7166.875.4571.861.754 试验结果分析4.1 碱度与低温粉化指数的关系图1碱度与低温粉化指数的关系图2碱度与高温还原指数关系图由表3和图1可看知,以1.75为基准,碱度提高到1.77时RDI+3.15从66.87%降到 65.7%,降低了1.17%主要原因是由于碱度的增加,SiO2的含量相对较低,作为粘结相的硅酸盐的含量相对较低,妨碍了铁矿石内部间的连晶作用,致使烧结矿抗膨胀粉化能力减弱,进而使烧结矿低温粉化指数降低;当碱度增加到2.08时,低温粉化指数RDI+3.15增加到72.03%,主要是因为碱度的增加,使铁酸钙和硅酸盐都增加,铁酸钙和硅酸盐相结合抑制了低温还原过程中体积的膨胀,进而使粉化指数显著提高;当碱度在2.1左右出现最大值,烧结矿碱度与低温还原粉化指数在部分区域内呈明显的增长关系。
烧结质量指标
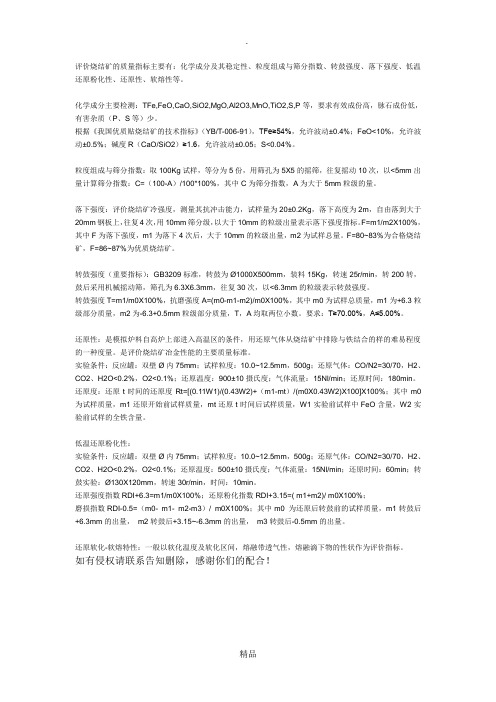
.评价烧结矿的质量指标主要有:化学成分及其稳定性、粒度组成与筛分指数、转鼓强度、落下强度、低温还原粉化性、还原性、软熔性等。
化学成分主要检测:TFe,FeO,CaO,SiO2,MgO,Al2O3,MnO,TiO2,S,P等,要求有效成份高,脉石成份低,有害杂质(P、S等)少。
根据《我国优质贴烧结矿的技术指标》(YB/T-006-91),TFe≥54%,允许波动±0.4%;FeO<10%,允许波动±0.5%;碱度R(CaO/SiO2)≥1.6,允许波动±0.05;S<0.04%。
粒度组成与筛分指数:取100Kg试样,等分为5份,用筛孔为5X5的摇筛,往复摇动10次,以<5mm出量计算筛分指数:C=(100-A)/100*100%,其中C为筛分指数,A为大于5mm粒级的量。
落下强度:评价烧结矿冷强度,测量其抗冲击能力,试样量为20±0.2Kg,落下高度为2m,自由落到大于20mm钢板上,往复4次,用10mm筛分级,以大于10mm的粒级出量表示落下强度指标。
F=m1/m2X100%,其中F为落下强度,m1为落下4次后,大于10mm的粒级出量,m2为试样总量。
F=80~83%为合格烧结矿,F=86~87%为优质烧结矿。
转鼓强度(重要指标):GB3209标准,转鼓为Ø1000X500mm,装料15Kg,转速25r/min,转200转,鼓后采用机械摇动筛,筛孔为6.3X6.3mm,往复30次,以<6.3mm的粒级表示转鼓强度。
转鼓强度T=m1/m0X100%,抗磨强度A=(m0-m1-m2)/m0X100%,其中m0为试样总质量,m1为+6.3粒级部分质量,m2为-6.3+0.5mm粒级部分质量,T,A均取两位小数。
要求:T≥70.00%,A≤5.00%。
还原性:是模拟炉料自高炉上部进入高温区的条件,用还原气体从烧结矿中排除与铁结合的样的难易程度的一种度量。
烧结矿质量及其对高炉冶炼主要操作指标的影响

高炉主要操作指标
利用系数
燃料比
1.228
813
1.998
559.4
2.412
535.0
2.153
496.7
2.28
478.0
0.788
793.2
0.463
878.0
1.519
556.9
1.719
547.6
2.147
538.0
0.472
986
1.234
610
2.04
601
2.20
550
近几年有不少钢铁企业采用低品位、大渣量的做法,主观愿望想降低成本,实际适得其反,造
2 烧结矿质量的内涵和价值
烧结矿的质量由化学成分、物理性能和冶金性能三部分组成,它们三者间的关系是:化学成分是基 础,物理性能是保证,冶金性能是关键。
2.1 烧结矿的主要化学成分及其价值
烧结矿的主要化学成分包括品位和SiO2、碱度、MgO、Al2O3和FeO,还有S、P、Ka2O、ZnO和Cl等有 害元素。 2.1.1 含铁品位对烧结矿质量的价值
900℃还原/% 80.75 80.10 77.12 85.51 81.56 79.12
烧结生产之所以要配MgO是为了满足高炉炼铁炉渣流动性、脱硫和脱碱(K2O+Na2O)的需 求。
2.1.6 FeO含量对烧结矿质量的价值 FeO含量也是烧结矿的一个重要内容,FeO含量的高低直接影响烧结矿的强度、粒度和冶金
烧结矿冶金性能的有关参数

烧结矿冶金性能的有关参数一、低温还原粉化性能(1)RDI-3.15=30%时RDI+6.3一般在41%左右这个范围的低温还原粉化性能有一定恶化,但仍处在可维护中、小高炉冶炼所允许的范围之内。
(2)RDI-3.15=20—25%时RDI+6.3一般在60—50%这个范围基本能满足较高冶强的顺行要求。
(3)RDI-3.15=17—19%时RDI+6.3一般在67—63%这个范围的低温还原粉化性能应该说非常好,非常有利于改善高炉块状带的透气性,但要注意对还原性能的检验,还原度不能低于75%。
(4)RD=I-0.5一般在6—7%范围一般烧结矿中磁铁矿和硅酸铁含量的增加,有利于改善低温粉化性能,同时随着FeO%含量的相应提高(从6%逐步提高到12%以下)也有利于低温还原粉化性能的改善。
二、烧结矿的还原性能还原度RI(900℃时)在75—80%左右时,应该是比较好的还原性能指标。
凡还原度的降低都不利于降低高炉冶炼燃料比,一般情况下,当采取减少低温粉化率措施的同时,还原度相应降低,它往往也与难还原的磁铁矿和硅酸铁含量的增加有关,FeO%>10%RG,还原度也会出现明显的降低趋势。
三、烧结矿荷重软化性能一般烧结矿碱度在1.85±0.1条件下,软化的开始温度在1200—1220℃,软化终了温度在1320—1330℃,软化温度区间在110—120℃,凡软化温度区间(T2—T1)变小,对降低高炉软熔带的透气性是有利的。
反之,如果软化开始温度↓软化温度区间自然变大,不利于软熔带透气性的改善,一般影响烧结矿荷重软化性能,主要有两个因素:一是烧结矿的还原性能:烧结矿还原性能的改善有利于烧结矿在升温过程中形成液相的温度升高,导致烧结矿的软化开始温度升高。
二是烧结矿中脉石的熔点,在烧结矿碱度基本不变的条件下,烧结矿中脉石的熔点不变,R2低熔点低,R2高熔点高。
烧结矿质量对高炉冶炼的影响 精品

吉林电子信息职业技术学院毕业论文烧结矿质量对高炉冶炼的影响摘要烧结矿是高炉炼铁生产的主要原料之一,烧结矿的性能和质量直接影响高炉冶炼的顺行、操作制度和技术经济指标。
本论文通过对烧结矿的还原,滴落实验,验证不同粒度的半焦、无烟煤代替焦粉作燃料的铁矿烧结技术的比较优势。
以及改变其粒度等方面对烧结进行分析、研究。
本项研究内容包括:原、燃料的物理化学性质、燃料的性能及反应性、烧结矿质量指标的评价;在不同原料配比条件下改变燃料粒度的烧结实验;烧结矿的物理化学性能和冶金性能等检测;对燃料种类和配比对烧结矿生产指标、烧结矿化学成分、矿物组成、还原性能、还原粉化性能、软熔滴落性能的影响进行评价,实验结果及其分析。
实验结果证明:半焦在>5mm粒级控制在15%的粒度下是很好的烧结燃料。
无烟煤相对做烧结燃料效果不好;<3mm粒级控制在70%左右为宜。
关键词:烧结矿,无烟煤,焦粉,半焦,矿物组成,烧结矿冶金性能,改变粒度I吉林电子信息职业技术学院毕业论文目录第一章绪论·············································································································· - 6 -1.1烧结生产的目的·············································································································- 6 -1.2烧结用原料条件·············································································································- 7 -1.3燃料的粒度 ······················································································································- 7 -1.4燃料的基本性质·············································································································- 8 -1.4.1燃料的工业分析、元素分析 ......................................................................... - 8 -1.4.2燃料的灰成分和灰熔点·······························································································- 10 -第二章烧结的作用·································································································- 11 -2.1烧结矿的作用 ···············································································································- 11 -2.2烧结机的作用 ···············································································································- 12 -2.3烧结矿中MgO 作用机理 ····························································································- 12 -第三章烧结生成工艺及生产的工艺流程·························································- 13 -3.1烧结生成工艺 ···············································································································- 13 -3.2烧结生产的工艺流程··································································································- 13 -3.2.1烧结原料的准备 ..................................................................................... - 14 -3.2.2配料与混合............................................................................................... - 14 -3.2.3烧结生产 ................................................................................................... - 15 -第四章烧结矿对高炉冶炼的影响·····································································- 18 -4.1烧结矿指标对高炉冶炼过程的影响·······································································- 18 -4.2烧结矿指标和冶金性能的影响因素·······································································- 20 -第五章结论·········································································································- 24 -参考文献·················································································································- 25 -致谢·································································································错误!未定义书签。
FeO对烧结矿产质量的影响
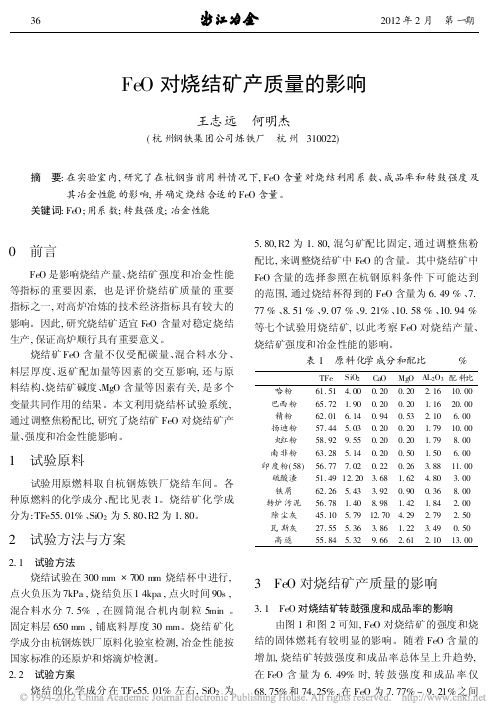
FeO 对烧结矿产质量的影响王志远 何明杰(杭州钢铁集团公司炼铁厂 杭州 310022)摘 要:在实验室内,研究了在杭钢当前用料情况下,FeO 含量对烧结利用系数、成品率和转鼓强度及其冶金性能的影响,并确定烧结合适的FeO 含量。
关键词:Fe O;用系数;转鼓强度;冶金性能0 前言FeO 是影响烧结产量、烧结矿强度和冶金性能等指标的重要因素,也是评价烧结矿质量的重要指标之一,对高炉冶炼的技术经济指标具有较大的影响。
因此,研究烧结矿适宜FeO 含量对稳定烧结生产,保证高炉顺行具有重要意义。
烧结矿FeO 含量不仅受配碳量、混合料水分、料层厚度、返矿配加量等因素的交互影响,还与原料结构、烧结矿碱度、MgO 含量等因素有关,是多个变量共同作用的结果。
本文利用烧结杯试验系统,通过调整焦粉配比,研究了烧结矿FeO 对烧结矿产量、强度和冶金性能影响。
1 试验原料试验用原燃料取自杭钢炼铁厂烧结车间。
各种原燃料的化学成分、配比见表1。
烧结矿化学成分为:TFe55.01%、SiO 2为5.80、R2为1.80。
2 试验方法与方案2.1 试验方法烧结试验在300mm @700m m 烧结杯中进行,点火负压为7kPa ,烧结负压14kpa ,点火时间90s ,混合料水分7.5%,在圆筒混合机内制粒5min 。
固定料层650mm ,铺底料厚度30mm 。
烧结矿化学成分由杭钢炼铁厂原料化验室检测,冶金性能按国家标准的还原炉和熔滴炉检测。
2.2 试验方案烧结的化学成分在TFe55.01%左右,SiO 2为5.80,R2为1.80,混匀矿配比固定,通过调整焦粉配比,来调整烧结矿中FeO 的含量。
其中烧结矿中FeO 含量的选择参照在杭钢原料条件下可能达到的范围,通过烧结杯得到的FeO 含量为6.49%、7.77%、8.51%、9.07%、9.21%、10.58%、10.94%等七个试验用烧结矿,以此考察FeO 对烧结产量、烧结矿强度和冶金性能的影响。
烧结知识问答
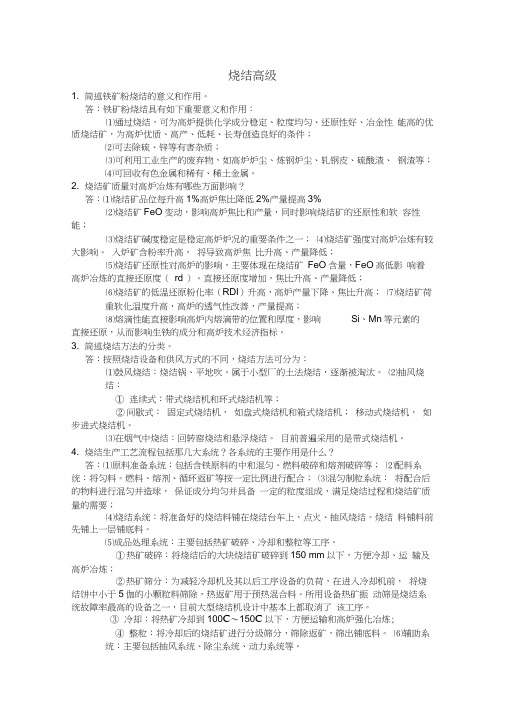
烧结高级1. 简述铁矿粉烧结的意义和作用。
答:铁矿粉烧结具有如下重要意义和作用:⑴通过烧结,可为高炉提供化学成分稳定、粒度均匀、还原性好、冶金性能高的优质烧结矿,为高炉优质、高产、低耗、长寿创造良好的条件;⑵可去除硫、锌等有害杂质;⑶可利用工业生产的废弃物,如高炉炉尘、炼钢炉尘、轧钢皮、硫酸渣、钢渣等;⑷可回收有色金属和稀有、稀土金属。
2. 烧结矿质量对高炉冶炼有哪些方面影响?答:⑴烧结矿品位每升高1%高炉焦比降低2%产量提高3%⑵烧结矿FeO变动,影响高炉焦比和产量,同时影响烧结矿的还原性和软容性能;⑶烧结矿碱度稳定是稳定高炉炉况的重要条件之一;⑷烧结矿强度对高炉冶炼有较大影响。
入炉矿含粉率升高,将导致高炉焦比升高、产量降低;⑸烧结矿还原性对高炉的影响,主要体现在烧结矿FeO含量,FeO高低影响着高炉冶炼的直接还原度(rd )。
直接还原度增加,焦比升高、产量降低;⑹烧结矿的低温还原粉化率(RDI)升高,高炉产量下降、焦比升高;⑺烧结矿荷重软化温度升高,高炉的透气性改善,产量提高;⑻熔滴性能直接影响高炉内熔滴带的位置和厚度,影响Si、Mn等元素的直接还原,从而影响生铁的成分和高炉技术经济指标。
3. 简述烧结方法的分类。
答:按照烧结设备和供风方式的不同,烧结方法可分为:⑴鼓风烧结:烧结锅、平地吹。
属于小型厂的土法烧结,逐渐被淘汰。
⑵抽风烧结:①连续式:带式烧结机和环式烧结机等;②间歇式:固定式烧结机,如盘式烧结机和箱式烧结机;移动式烧结机,如步进式烧结机。
⑶在烟气中烧结:回转窑烧结和悬浮烧结。
目前普遍采用的是带式烧结机。
4. 烧结生产工艺流程包括那几大系统?各系统的主要作用是什么?答:⑴原料准备系统:包括含铁原料的中和混匀、燃料破碎和熔剂破碎等;⑵配料系统:将匀料。
燃料、熔剂、循环返矿等按一定比例进行配合;⑶混匀制粒系统:将配合后的物料进行混匀并造球,保证成分均匀并具备一定的粒度组成,满足烧结过程和烧结矿质量的需要;⑷烧结系统:将准备好的烧结料铺在烧结台车上,点火、抽风烧结。
18烧结矿冶金性能对其质量和高炉指标的影响

T10
1091 1092 1085
T40
1134 1247 1227
ΔT
43 155 142
Ts
1267 1435 1448
Td
1333 1450 1464
ΔT
66 15 16
ΔPm·9.8pa
S值(Kpa℃)
33.63 11.76 21.64
102 130 188
济钢
75.1
74.6
42.3
- - - 63.96 39.5
主要参考文献
序言:
烧结矿的冶金性能包括 900℃还原性(RI)、500℃低温还原粉化性 能( RDI )、荷重还原软化性能( TBS 、 TBE 、Δ TB )和熔融滴落性能 (Ts、Td、ΔT、ΔPm、S值)。这四项性能中900还原性是基本性能, 它不仅直接影响煤气利用率和燃料比,同时由于还原程度的不同,还 影响其还原强度(RDI)和软熔性能。500℃低温还原性能是反映烧结 矿在高炉上部还原强度的,它是高炉上部透气性的限制性环节。在高 炉冶炼进程中,高炉上部的阻力损失约占总阻力损失的 15%。烧结矿 的荷重还原软化性能是反映其在高炉炉身下部和炉腰部分软化带透气 性的,这部分的透气阻力约占高炉总阻力损失的25% 。熔融滴落性能 是烧结矿冶金性能最重要的部分,因为它约占高炉总阻力损失的60%, 是高炉下部透气性的限制性环节,要保持高炉长期顺行稳定,必须十 分重视含铁原料在熔融带的透气阻力。烧结矿在高炉的块状带、软化 带和熔融滴落带不同部位的性状和透气阻力的变化(详见示图)决定 着高炉内不同部位顺行和稳定,因此研究和分析清楚冶金性能对烧结 矿质量和高炉主要操作指标的影响是十分重要和必要的。
烧结矿的荷重还原软化性能是指其装入高炉后,随炉料下降,温度上升不断被 还原,到达炉身下部和炉腰部位,烧结矿表现出体积开始收缩即开始软化(TBS) 和 软 化 终 了 ( TBE ) 的 特 性 , 高 碱 度 烧 结 矿 的 TBS 应 ≥ 1100 ℃ , 软 化 温 度 区 间 (ΔTB= TBE -TBS)应≤150℃,烧结矿开始软化温度的高低取决于其矿物组成和 气孔结构强度〔1〕开始软化温度的变化往往是气孔结构强度起主导作用的结果, 这就是说,软化终了温度往往是矿物组成起主导作用。由高炉内各带透气阻力的 示图可知,软化带的阻力损失约占25%,是反映炉料在炉身下部和炉腰部位顺行状 况的,当烧结矿的开始软化温度低于950℃,软化温度区间>300℃时,高炉必须会 产生严重的悬料,因此为了保持高炉顺行稳定,烧结矿应具有良好的荷重还原软 化性能。关于荷重还原性能对高炉主要操作指标的影响 ,意大利的皮昂比诺 ( Piombimo )公司 4# 高炉曾于 1980 年做过统计,含铁原料的 TBS 由 1285 ℃提高到 1335℃,高炉的透气性ΔP由5.2kpa降低到4.75kpa(下降8.7%),产量提高了 16%, 日本神户公司的加古川厂和新日铁的广畑厂均通过改善酸性球团矿的软熔性能有 效地改善了高炉操作指标〔7〕。
《钢铁冶金》第二章铁矿烧结

四、燃料燃烧和传热
❖ 烧结料中固体碳的燃烧为形成粘结所必须的液相和进行 各种反应提供了必要的条件(温度、气氛)。烧结过程所需 要的热量的80~90%为燃料燃烧供给。然而燃料在烧结混 合料中所占比例很小,按重量计仅3~5%,按体积计约 10%。在碳量少,分布稀疏的条件下,要使燃料迅速而 充分地燃烧,必须供给过量的空气,空气过剩系数达 1.4~1.5或更高。
❖ 随着烧结过程的进行,燃烧层向下移动,烧结矿层增厚, 自动蓄热作用愈显著,愈到下层燃烧温度愈高。这就出现 上层温度不足(一般为1150℃左右),液相不多,强度较低, 返矿较多;而下部温度过高,液相多,过熔,强度虽高而 还原性差,即上下烧结矿质量不均的现象。为改善这种状 况,提出了具有不同配碳量的双层或多层烧结的方法。即 上层含碳量应高于平均含碳量,而下层应低于平均含碳量, 以保证上下层温度均匀,质量一致。而且节省燃料。苏联 采用分层烧结某矿粉,下部含碳量低1.2%,节省燃料10%, 联邦德国某厂使用双层烧结,节省燃料15%,日本用此法 节省燃料10%。
❖ 随着烧结料层的增厚,自动蓄热量增,有利于降低燃料 消耗,但随着料层厚度增加,蓄热量的增加逐渐减少,所 以燃耗降低幅度也减小。当烧结矿层形成一个稳定的蓄热 层后,则蓄热量将不再增加,燃耗也不再降低。因此,从 热量利用角度看,厚料层烧结是有利的,但不是愈厚愈好, 在一定的条件下,存在着一个界限料层高度。同时料层高 度的进一步增加还受到透气性的限制。
❖ 在某一层中可能同时进行几种反应,而一种反应又可能在几层中进行。 下面对各过程分别进行研究和讨论。
二、烧结料中水分的蒸发、分解和凝结
❖ 任何粉料在空气中总含有一定水分,烧结料也不例外。除 了各种原料本身带来和吸收大气水分外,在混合时为使矿 粉成球,提高料层透气性,常外加一定量的水,使混合料 中含水达7~8%。这种水叫游离水或吸附水。100℃即可 大量蒸发除去。如用褐铁矿烧结,则还含有较多结晶水 (化合水)。需要在200~300℃才开始分解放出,若含有粘 土 质 高 岭 土 矿 物 (Al2O3·2SiO2·H2O) 则 需 要 在 400~600℃ 才能分解,甚至900~1000℃才能去尽。
烧结实业部质量指标影响因素

烧结内部控制要求:
成分 TFe FeO MgO R2 Pb Zn Na2O+k2O 转鼓 粒度 要求 ≥55% 9%-11.5% 2.2%-2.5%
1.8%±0.1%
备注
原料稳定后考虑1.8%±0.08%
≤0.02% ≤0.02% ≤0.1 ≥77.33% 5-10≤23%
烧 结 品 质
凝 聚 成 才
好,但是流动性差,不易排出炉外,从而影响高炉顺行。相反,如果酸性氧化
物含量高,炉渣的流动性好,凝固后的固态炉渣呈现玻璃状,一般称为玻璃渣 或者长渣,这样的炉渣脱硫效果很差,但是流动性好。所以高炉操作者要调整 炉渣的成分,也就是炉渣的碱度,既保持优良的流动性,也能有很好的脱硫效 果,使生铁达到一类要求。
的之接还原;
烧 结 品 质
凝 聚 成 才
烧结分厂
烧结矿对高炉冶炼的影响及质量的要求 一般烧结矿碱度在1.85±0.1条件下,软化的开始温度在1200-1220, 软化终了温度在1320-1330,软化温度区间在110-120,凡软化温度区 间(T2-T1)变小,对降低高炉软熔带的区间是有利的。反之,如果软 化开始温度降低,软化温度区间自然变大,不利于软熔带透气性改善, 一般影响烧结矿荷重软化性能的主要因素有: 一是烧结矿的还原性能:烧结矿还原性能的改善有利于烧结矿在升温过 程中形成液相,温度升高,导致烧结矿的软化开始温度升高。 二是烧结矿中脉石的熔点:在烧结矿碱度基本不变的条件下,烧结矿中 脉石的熔点不变,碱度低熔点低,碱度高熔点高;
因为磷化物是催性物质,冷凝时聚集于钢的晶界周围,减弱晶粒间的结 合力,使钢材在冷却时产生很大的脆性,从而造成钢的冷脆现象。由于
磷早烧结和选矿过程中不易脱除,在高炉冶炼过程中几乎全部还原进入
钢铁生产过程中的烧结
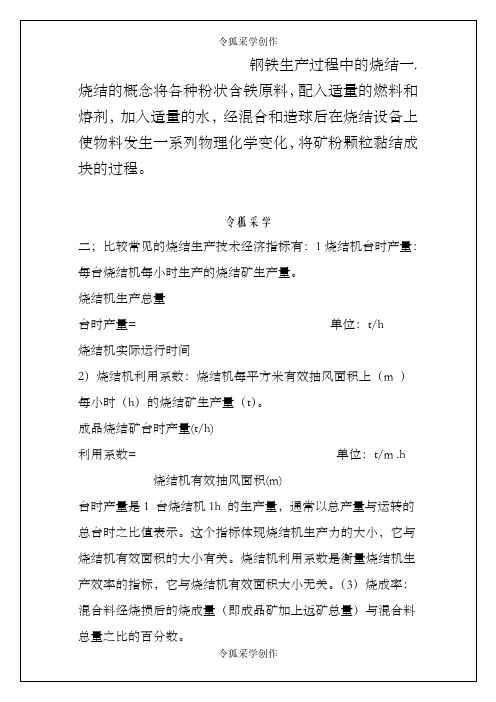
烧结配料是按烧结矿的质量指标要求和原料成分,将各种原料(含铁料、熔剂、燃料等)按一定的比例配合在一起的过程。它是整个烧结工艺中的一个重要环节,精心配料是获得优质烧结矿的前提。适宜的原料配比可以生产出数量足够的性能良好的液相,适宜的燃料用量可以获得强度高、还原性良好的烧结矿。从而保证高炉顺行,使高炉生产达到高产、优质、低耗。
六.改善烧结透气的方法加强烧结原料准备
加强原料、燃料、溶剂准备、减少烧结料层各带的气流阻力;改进烧结设备减少漏风和提高抽风机能力等是改善烧结料层透气性的主要措施。
1)、改进原料粒度和粒度组成。
随着矿石粒度的增加,透气性显著改善,而且这种改善随抽风能力增加而加强。因此,选用适当粗粒度矿石烧结,以增加物料间的孔隙率,是改善透气性的重要措施。
钢铁生产过程中的烧结一.烧结的概念将各种粉状含铁原料,配入适量的燃料和熔剂,加入适量的水,经混合和造球后在烧结设备上使物料发生一系列物理化学变化,将矿粉颗粒黏结成块的过程。
令狐采学
二;比较常见的烧结生产技术经济指标有:1烧结机台时产量:每台烧结机每小时生产的烧结矿生产量。
烧结机生产总量
台时产量= 单位:t/h
烧结机实际运行时间
2)烧结机利用系数:烧结机每平方米有效抽风面积上(m )每小时(h)的烧结矿生产量(t)。
成品烧结矿台时产量(t/h)
利用系数= 单位:t/m .h
烧结机有效抽风面积(m)
台时产量是1 台烧结机1h 的生产量,通常以总产量与运转的总台时之比值表示。这个指标体现烧结机生产力的大小,它与烧结机有效面积的大小有关。烧结机利用系数是衡量烧结机生产效率的指标,它与烧结机有效面积大小无关。(3)烧成率:混合料经烧损后的烧成量(即成品矿加上返矿总量)与混合料总量之比的百分数。
低碱度烧结矿的冶金性能分析

低碱度烧结矿的冶金性能分析摘要:低碱度烧结矿的冶金性能分析有助于更好的合理利用低品质铁矿石和矿粉资源,优化烧结质量指标,降低生产成本,为钢铁企业生产带来积极影响。
本次分析了低碱度烧结矿原料成分与特点分析以及冶金性能,证实其能够满足生产需求,有助于降低成本提升效益。
关键词:低碱度烧结矿冶金性能成分成本一直以来我国高炉炉料的选择都倾向于高碱度烧结矿,其冶金性能优良性价比较高,一直以来大受欢迎,但是由于近两年来生产成本上升,为顺应钢铁市场剧烈竞争,低碱度烧结矿开始在市场上占据重要比例,不少钢铁企业都积极寻求各种技术手段利用劣质低价矿粉生产低碱度烧结矿。
由于低碱度烧结矿使用时会对机型产生有害影响,导致生产成本增加等问题,所以加强对其冶金性能的分析有助于更好的合理利用低品质铁矿石和矿粉资源,优化烧结质量指标,降低生产成本,为钢铁企业生产带来积极影响。
下面我们结合国内某钢铁厂实际情况对低碱度烧结矿的冶金性能进行分析。
一、低碱度烧结矿原料成分与特点分析高炉炉料的成分较为复杂,一般主要包括FeO、MgO、TFe、Al2O3、K2O、Na2O、CaO、SiO2、TiO2等化学成分,这些成分的构成比决定了原料的化学成分和质量。
炉料的品味关系到其质量,直接影响到冶炼的焦比和产量。
烧结矿中MgO含量十分重要,在生产中有些企业将MgO生产配比提升至≥4%,结果烧结矿MgO达4%,同等白云石含量30%配入5%,烧结矿的品味降低3%,关于这个问题在生产实践中是必须予以重视的。
烧结矿中会有一定的MgO有利于抑制烧结矿的自然粉化和还原粉化,不利于烧结矿的强度和中温还原,但有利于高温还原和改善烧结矿的软熔性能。
SiO2的含量是烧结矿的主要成分,也是Al2O3/SiO2是形成复合铁酸钙的一个重要条件,其过高会导致冶炼问题,所以针对当前我国6%-8%的含量比要尽可能的降低比重,以提升冶炼质量和经济效益,这样才能够更好的控制烧结矿的碱度。
烧结矿质量指标

烧结矿质量指标
烧结矿的质量指标包括化学成分和物理机械性能两个方面,两方面所包含的各个指标都符合冶金部规定标准的产品,称为合格品。
烧结矿质量对高炉冶炼的影响。
从化学成分看,烧结矿的品位越
高越有利于提高生铁产量降低焦比,但烧结品位取决于所用的原料条件,烧
结生产中只能通过合理准确的配料,使之保持稳定,这对高炉冶炼至关重
要。
烧结矿的碱度应根据各企业的条件具体确定,合适的
碱度有利于改善高炉的还原和造渣过程,烧结矿碱度应保持稳定,这是稳
定造渣制度的重要条件,只有稳定的造渣制度,才有助于热制度和炉况的顺
行,并使炉渣具有良好的脱硫能力,改善生铁质量。
我厂所生产使用的烧结
矿为高碱度(R=1.5-2.5 )烧结矿,各项指标如下:
注:A:为烧结矿品位基数,根据所用原料条件调节;
R :为烧结矿碱度基数,根据高炉要求和烧结矿库存情况调
附:
烧结矿技术标准(YB/T421-92)。
Al2O3/SiO2对烧结矿冶金性能的影响
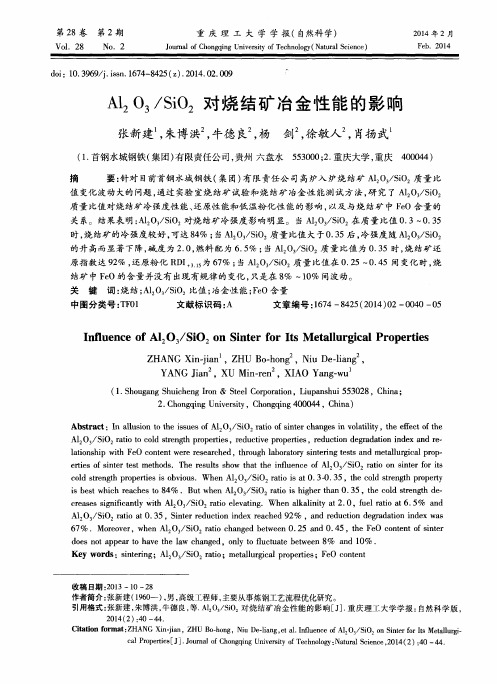
结矿中 F e O的含量并没有出现有规律的变化 , 只是在 8 %一 1 0 % 间波动。
关 键 词: 烧结; A 1 2 O / S i O 2比值 ; 冶金 性 能 ; F e O含 量
中图 分类 号 : T F 0 1
文献标 识码 : A
文 章编 号 : 1 6 7 4—8 4 2 5 ( 2 0 1 4 ) 0 2— 0 0 4 0— 0 5
I n l f u e n c e o f AI 2 03 / S i O2 o n S i n t e r f o r I t s Me t a l l u r g i c a l P r o p e r t i e s
Z H A N G X i n . j i a n , Z H U B o . h o n g ,N i u D e — l i a n g ,
2 0 1 4年 2月
F e b .2 0 1 4
d o i : 1 0 . 3 9 6 9 / j . i s s n . 1 6 7 4 - 8 4 2 5 ( z ) . 2 0 1 4 . 0 2 . 0 0 9
A 1 2 0 3 / S i O 2对 烧 结 矿 冶金 性能 的影 响
值 变化 波动 大的 问题 , 通过 实验 室烧 结矿 试 验 和烧 结矿 冶金 性 能 测试 方 法 , 研究了A l 0 / S i O
质 量 比值 对烧 结矿 冷 强度性 能 、 还 原性 能和低 温粉 化性 能 的影 响 , 以及 与 烧 结矿 中 F e O含 量 的 关 系。结果表 明 : A l 2 O / S i O 2 对 烧 结矿冷 强度 影响 明显 。 当 A 1 2 O , / S i O 2 在 质量 比值 0 . 3— 0 . 3 5
高碱度烧结矿矿物结构对其冶金性能的影响

高碱度烧结矿矿物结构对其冶金性能的影响摘要:采用光学显微镜及IPP软件对高碱度烧结矿显微结构及矿物组成进行了研究,并检测和分析了高碱度烧结矿的冶金性能。
研究结果表明:高碱度烧结矿主要由赤铁矿、磁铁矿、铁酸钙、硅酸二钙等矿物组成,不同碱度条件的烧结矿显微结构基本相似,主要为交织熔蚀结构;当碱度从1.5提高到2.0时,烧结矿中的赤铁矿质量分数增加了8%,磁铁矿质量分数降低了18%,铁酸钙质量分数增加了23%,磁铁矿与铁酸钙形成熔蚀结构;烧结矿的成品率从75.09%增加到82.78%之后稍有降低,转鼓指数从54%增加到69.33%,低温还原粉化性能和还原性均得到较大改善。
关键词:高碱度烧结矿;矿物组成;显微结构;冶金性能高碱度烧结矿有着优良的冶金性能,早在60年代,即引起人们的广泛注意。
近年来高碱度烧结矿已在国外一些大高炉上得到广泛应用;在国内不仅在一些中小厂得到了应用,而且在重点企业中,如重钢、包钢、攀钢、湘钢等都进行了工业试验和应用,取得了较好的结果。
我国贫矿多且人造富矿中烧结又占主要地位,推广高碱度烧结矿并对其进行深入研究,对于提高烧结矿质量,进一步提高炼铁生产水平,有着积极而现实的意义。
1.烧结生产烧结是铁原材料、燃料、溶剂、等,比例匹配在一起,混合造粒后,加水润湿后躺在烧结设备,从上到下点火烧结,点火烧结机的底部开始抽搐的同时,从上到下的燃油混合矿石燃烧的同时,将容易融化材料熔体润湿困难的材料,液体冷却将很难融化材料粘在一起,这个过程直到烧结炉篦结束。
得到的块状物体叫烧结矿,也叫人造富矿。
需用到的设备包括翻车机、行车、燃料溶剂破碎设备(锤式、四辊)等;配料系统设备如配料秤等;烧结机(分带式、步进式、环烧等,及配套的抽烟机等)圆通混料机、破碎(单辊)热筛;冷却设备:带冷机或环冷机、冷筛等。
另外最多的是皮带等转运设备。
2.原料处理2.1原燃料成分值管理原燃料质量的稳定性是烧结、高炉生产,工厂为了使原燃料质量相对稳定,进入院子里的原始燃料将严格实施价值管理,即通过商检,停车测试组件进入工厂,黑色材料根据不同,二氧化硅含量堆积在指定地址,禁止混合物质事故;同时在积累过程中堆积颗粒,以保证原料的粒度和均匀性。
烧结矿质量指标标准

烧结矿质量指标标准
烧结矿是一种铁矿石粉末,通常用于冶金工业中的烧结生产过程。
其质量指标标准通常由国家或行业标准确定,具体标准可能会因国家和地区的不同而有所差异。
下面是一些可能包括在烧结矿质量指标标准中的常见参数:
1. 化学成分:包括烧结矿的主要成分和杂质含量,比如铁(Fe)含量、硅(SiO2)含量、铝(Al2O3)含量、钙(CaO)含量、镁(MgO)含量等。
这些成分的比例对于烧结矿的质量和适用性至关重要。
2. 粒度分布:烧结矿的粒度分布对于烧结反应的进行和产出烧结块的质量具有重要影响。
通常包括最大粒径、平均粒径、细度以及特定粒度分数的要求。
3. 烧结特性指标:这包括耐磨指数、烧结指数、烧损指数等,这些指标反映了烧结矿在高温下的烧结性能。
4. 矿石热性能:主要涉及烧结矿的热膨胀性能和结块性能,也是评价烧结矿的重要指标。
5. 其他特殊要求:如含硫量、磷含量、水分含量、胶结指数、耐热强度等适用于特殊工艺和使用条件的指标。
以上仅是一些可能包括在烧结矿质量指标标准中的常见指标,具体的标准以及要求应当根据实际的国家标准、行业标准或企业标准进行制定和遵守。
冶金性能对高炉 的影响

还原软化-熔融特性
软化、熔融性能:炉料的荷重软化、熔融性能反映了炉料在高 炉下部的高温软化和熔化、滴落过程的特性。对高炉软熔带的 形成(位置、形状、厚度)和透气性起着决定性作用。 表征此特性的参数有炉料的软化开始温度、软化终了温度、熔 融温度、软化区间以及熔融区间。 高炉要求矿石具有合适的软化开始温度、熔化开始温度,窄的 软化和熔融温度区间,以使高炉软融带位置既为过高,也不过 低,处于适宜的位置,即能适当增加炉内块状带区域的高度, 利于改善上部透气性。 软熔带位置过低,熔融渣铁或炉墙周围熔化的粘结物易直接进 入炉缸,导致崩、滑料甚至炉凉。炉料的软化熔融温度区间较 宽,表明高炉软熔带较厚,煤气通过软熔带的阻力较大,高炉 透气性较差。
烧结矿冶金性能指标 影响因素及有关问题探讨
2013.11
内容
烧结矿的冶金性能指标 影响冶金性能指标的因素探讨 测定方法
高炉精料要求
入炉品位高,脉 石及杂质含量 低
提高入炉料强 度和粒度组成 合理
改善原燃料 高温冶金性能
烧结矿的冶金性能指标
900℃还原度 550℃低温还原粉化指数 荷重软化性能 软熔-滴落性能
影响因素: 1烧结矿化学成分 2 烧结矿矿相组成 3 工艺条件
再生赤铁矿形成 残余应力增大 区域结构弱化 原生褐铁矿大颗粒 后果: 产生粉末,恶化高炉 上部透气性
磁铁矿直接氧化生成
破坏性大
还原为磁铁矿体积膨胀25%
颗粒状次生赤铁矿 骸晶状赤铁矿
物铁 其 的纹 主 。酸 中 周和 要 钙 夹 围熔 分 和 杂 。蚀 布 磁着 状在 铁玻 残气 矿璃 存孔 等质 原、 矿、 矿裂
MgO含量对低温还原粉化的影响
厂烧结矿烧结指标及冶金性能的影响
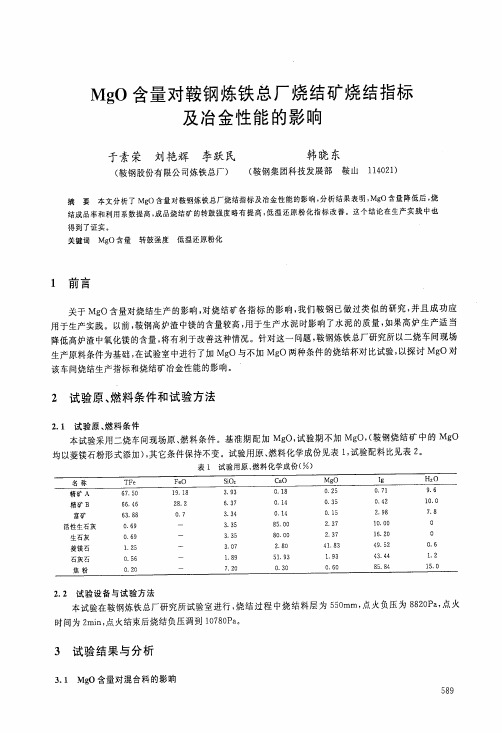
于素荣 刘艳辉
李跃民
韩晓东
(鞍钢集团科技发展部鞍山
114021)
(鞍钢股份有限公司炼铁总厂)
摘要本文分析了M90含量对鞍钢炼铁总厂烧结指标及冶金性能的影响,分析结果表明,MgO含量降低后,烧
结成品率和利用系数提高,成品烧结矿的转鼓强度略有提高,低温还原粉化指标改善。这个结论在生产实践中也 得到了证实。
5
结论
试验室试验不加菱镁石粉,即烧结矿中MgO含量降低后:
5.1烧结混合料的指均粒径相差不多。 (下转第596页)
591
3.2积极发展节能减排技术 节能降耗是“十一五”期间我国各行业工作的重点,政府提出到2010年我国单位GDP产值能耗下降 20%,主要污染物排放要降低10%。钢铁行业作为高能耗、高污染行业,更应努力为节能减排作出贡献。烧 结节能主要方向应以降低固体燃料消耗和回收烧结废烟气余热为主。继续发展厚料层技术(包括小球烧结、 低温烧结、燃料分加技术等),料层厚度努力达到650~750ram(粉矿为主)或600~700mm(精矿为主); 烧结余热回收应重点关注余热发电,余热发电技术符合国家的产业政策,对优化烧结生产,降低工序能 耗,充分利用二次能源,改善生产环境具有重要意义,对推动循环经济发展起到积极的作用,具有良好的社会 效益和经济效益。济钢320m2烧结机余热发电设备和技术已经国产化,武钢也拟在四烧区域新建余热发电设 施。我国烧结工作者应多做研究开发,使烧结余热发电设备和技术早日国产化、普及化。大型烧结机应开发烟 气循环富集系统和余热综合利用技术,如莱钢265m2烧结机既回收了余热蒸汽,同时也采取了热风烧结技术。 “十一五”期间,减排SO:成为我国环境保护的重点,新的《钢铁工业大气污染物排放标准》将要颁布,征 求意见稿中对新建装备要求排放浓度SO。≤100mg/m3,NO。≤300mg/m3,PCDD≤0.5ng—TEQ/m3,按照 我国目前原燃料生产条件,即使全部采取进口矿生产也不能够达到上述要求,因此烧结工序的脱硫成为环境 治理首要任务。事实上,越来越多的企业将烧结烟气脱硫纳入“十一五”规划中来。宝钢不锈钢分厂和梅钢 烧结厂都在建脱硫设施,采取的工艺是石灰石一石膏法,其它如武钢、鞍钢、湘钢等都在积极论证方案中。虽 然我国烧结脱硫慢慢受到重视,但我国烧结脱硫的阻力依然非常大,缺乏成熟的技术,巨大的投资和高昂的 运行费用,以及脱硫建设场地和脱硫副产物的利用问题,造成企业大多还处于观望之中。开发适合我国国情 的生产工艺,主要设备国产化,降低投资和生产运行成本以及合理利用副产品是烧结烟气脱硫最迫切需要解 决的问题,需要依靠政府、企业和各科研院所一起努力,才能早日解决我国烧结脱硫的问题,才能完成“十一 五”节能减排的重任。活性焦吸附法既可以脱除SO。,还可以吸附NO。和PCDD类,在日本、韩国烧结机上 已得到广泛应用,应重点关注。
氧化镁对安钢400m~2烧结机烧结矿冶金性能的影响
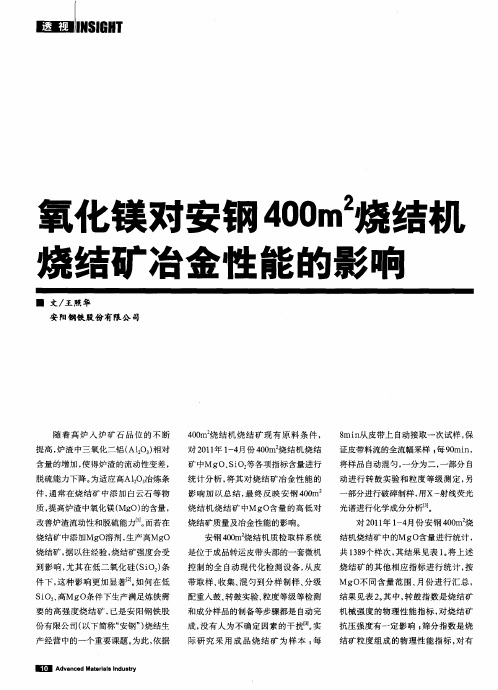
3. 0 S
3 A0
薯 | 《
罩 詈
鑫3 . 3 0
3。 O 2
31 .O
20 。0
22 0
24 .0
26 。O
蠢 79 80 .
辩
7 8 8. 0
7 7 8. O 7 .O 86
2. O O
2. O 2
2. 0 4
Hale Waihona Puke 2. 0 6 2. 0 8
Mg O范 围/ %
图1 烧结矿转鼓指数波动示意 图
l1ll ̄ N . 2 1 if l [ ! t m O 3 0 2蝴
圃
IH _T s l B
衄 A vne a rlI ut dacd t isn sy M ea d r
I
i 鬻 重圈 il l
烧结矿粉 末含量及 消 除大块有一定 的 作用 。 转股 指数和筛 分指数 的优劣 , 对 烧结矿投 入高炉生 产后料 柱的透气 性 及 冶炼顺 行有重要 的影 响。 从 上述 统 计数 据 来看 , 烧结 矿 中 Mg O的含量 发生 波动 时 , 鼓指数 和 转 筛 分 指数 均 发生 了明显 变化 。 了方 为
24 .%~3 0 .%的范围 内时 , 筛分 指数和
转 鼓强度 的变化趋 势 基本 相 同 , 表现 出平 稳 的趋 势 , 明烧结 矿 整体 强度 说 受Mg0的 影响 不 大 。 这说 明 , 烧结 矿
最好 , 明在Mg 说 O含量 此范 围 内烧 结
矿转 鼓指数 更有 利于生产 ; 由表 2 ② 、
光谱 进行化学 成分分析 。 】
对 2 1 年 1 月份 安 钢 4 0 烧 0 1 -4 0 m
- 1、下载文档前请自行甄别文档内容的完整性,平台不提供额外的编辑、内容补充、找答案等附加服务。
- 2、"仅部分预览"的文档,不可在线预览部分如存在完整性等问题,可反馈申请退款(可完整预览的文档不适用该条件!)。
- 3、如文档侵犯您的权益,请联系客服反馈,我们会尽快为您处理(人工客服工作时间:9:00-18:30)。
<0.5
2.21 1.87
降MgO前 降MgO后
25.89 26.42
由表10可见,降低MgO前、后,成品烧结矿的粒度组成没有明显变化。烧结矿的 低温还原粉化指标得到改善,其中>6.3mm部分由80.77%提高到89.07%,>3.15mm 部分由92.49%提高到95.47%,而<0.5mm部分则由2.21%降至1.87%。(注:烧结矿低 温粉化指标均为烧结矿喷洒CaCl2溶液后指标) 5结论 在试验室不加菱镁石,即烧结矿中MgO含量降低后: 5.1烧结混合料的指标稍有变差的趋势,具体为混合料中>3mm百分数稍有减少,平均 粒径相差不多。 5.2试验期烧结矿成品率增加了0.85%,利用系数略有提高,ISO转鼓指数变化不大, 略有提高。 5.3成品烧结矿品位提高0.86%。 5.4成品烧结矿低温粉化指标变好,其中>6.3mm部分增加了1.59%,>3.15mm部分增 加了O.86%,<0.5mm部分减少了0.72%。 而在生产实践中: 5.5降低菱镁石的配比后,成品烧结矿中的MgO由2.O%降至1.8%,烧结机的利用系 数有所增加,烧结矿的转鼓强度升高。 5.6烧结矿中的MgO含量降低后,烧结矿的低温还原粉化指标得到改善。
O.33%。
3.3
MgO含量对成品烧结矿粒度的影响 不同MgO含量的烧结矿粒度组成见表5。
表5 试验编号 加MgO 不加MgO
>40 5.65 3.28
不同条件成品烧结矿粒度组成(mm%)
40~25
22.25 25.29
25~16
30.53 31.3l
16~10
25.57 24.17
10"--5 20.20 15.96
表8
时间 降MgO前 降M90后
>3.15mm部分提
二烧车间降低烧结矿中MgO前、后的配料比
一次配料 大磁
32 30
二次配料 石灰石
5.5 6
鞍千
27 27
巴西
16 16
尘泥
5 7
生石灰
6 5.5
镁石
2.4 2.O
焦粉
1.6 1.7
生石灰
2.2 1.9
焦粉
1.6 1.6
表9
时间 降MgO前 降MgO后 利用系数t/m2h
表10
时间
>40
降MgO前、后烧结矿的成品粒度组成及低温还原粉化
成品粒度组成(%)
40~25
15.56 15.9l
低温还原粉化(%)
10~5
20.79 20.97
25~16
15.60 15.62
16~10
17.15 16.87
<5
4.46 4.35
>6.3 80.77 89.07
>3.15 92.49 95.47
MgO含量对鞍钢烧结矿烧结指标 及冶金性能的影响
于素荣刘艳辉李跃民
(鞍钢股份炼铁总厂)
摘要本文分析了MgO含量对烧结指标及冶金性能的影响,分析结果表明,MgO含量降低后, 烧结成品率和利用系数提高,成品烧结矿的转鼓强度略有提高,低温还原粉化指标改善。这个结论 在生产实践中也得到了证实。
关键词MgO
转鼓强度
由表9可见,降低MgO后烧结机的利用系数增加了O.103 t/m2.h,ISO转鼓指数升 高了0.64%,主要是因为MgO降低,减少了MgC03分解吸热,改变了烧结时液相的熔 化温度,使熔化温度降低,烧结矿化比较充分,颗粒之间黏结的强度较高,所以表现为 烧结矿的转鼓强度增加,烧结机的利用系数增加。而筛分指数随MgO含量的降低没有 明显的变化。 从理论上讲,降低MgO后,相对熔剂量减少,烧结矿的TFe品位应该升高。但是 由于后期生产中将2%高品位的大磁换成了低品位的尘泥,致使烧结矿的品位略有降低。
低温还原粉化
1
前言
由于以前鞍钢高炉渣中镁含量较高,用于生产水泥时影响了水泥质量,如果高炉适 当降低炉渣中氧化镁含量,将有利于改善这种情况。针对这一问题,鞍钢炼铁总厂研究 所以二烧车间现场生产原料条件为基础,在试验室中进行了加MgO与不加MgO两种 条件的烧结杯对比试验,以探讨MgO对该车间烧结生产指标和烧结矿冶金性能的影响。 2试验原、燃料条件和试验方法 2.1试验原、燃料条件 本试验采用二烧车间现场原、燃料条件。基准期配加MgO,试验期不加MgO,(鞍 钢烧结矿中的MgO均以菱镁石形式添加),其它条件保持不变。试验用原、燃料化学成 份见表1,试验配料比见表2。
垂烧速度
mm/min 19.32 19.54
一淤雯
表4
加MgO
试验条件\
不加MgO
烧成率
%
83.38 83.94
成品率
%
65.24 66.07
利用系数
t/m2.h 1.580 1.618
ISO转鼓,>6.3mm
%
64.67 65.00
燃耗
K卧
61.51 61.43
从表4数据可以看出,撤掉MgO后,垂直烧结速度变化不大,成品率稍有提高, 从基准期的65.24%提高到试验期的66.07%,提高了O.83%;利用系数略有提高,从 1.580Vmz.h提高到1.61 8ffm2.h,提高了O.038t/m2.h。ISO转鼓指数变化不大,提高了
MgO
O.57 O.25 0.35 O.15 2.37 2.37 41.83 1.93 O.60
Ig 0.84 0.7l 0.42 2.98 10.00 16.20 49.52 43.44 85.84
H20 9.8 9.6 10.0 7.8 0 O 0.6 1.2 15.0
表2
原料与配比 加MgO 不加MgO 齐大山
3.1
MgO含量对混合料的影响 不同试验条件下的烧结混合料指标见表3。
不同原料条件下混合料指标变化
>3 mm H20பைடு நூலகம்
i裳
表3
试验条件\
不加MgO 加MgO
平均粒径
mm 4.3l 4.27
静态料层阻力Pa
5m3/h 525 550 lOm3/h 1425 1450
%
59.57 57.05
%
7.3 7.4
57
表7
加MgO 不加MgO
不同条件成品烧结矿冶金性能指标,(%)
>6.3mm 51.77 53.36 >3.15mm 80.85 81.71 <O.5mm 5.28 4.56
从表7可以看出,混合料中撤掉菱镁石后,成品烧结矿的低温还原粉化强度提高, 其中>6.3mm部分从51.77%提高到53.36%,提高了1.59个百分点, 高了O.86个百分点;烧结矿的低温还原粉化率降低了0.72个百分点。 4生产实践 上世纪70年代,鞍钢成品烧结矿中MgO含量一直在2.3%~2.5%之间波动,为了 适应高炉生产的需要,2005年的4月份,二烧车间曾在保证烧结矿碱度和料层不变的 条件下,将MgO由原来的2.3%~2.5%降至2.1%,进而降至2.0%。 从2007年3月21日开始,二烧车间再次降低了烧结矿中MgO含量,即在保证其 他烧结条件不变的情况下,把镁石配比由2.4%降至2.O%,使烧结矿中的MgO含量由 原来的2.O%降至1.8%。生产具体配比见表8,烧结主要技术指标见表9,成品矿的粒 度组成及低温还原粉化见表10。
平均粒径
19.88 20.37
从表5看,撤掉MgO后,成品烧结矿粒度主要集中在中间三个粒级上。>40mm 粒级减少2.37个百分点,lO"..,5mm部分减少了4.24个百分点,平均粒径略有增大。
3.4
MgO含量对成品烧结矿化学成份的影响 不同原料条件下成品烧结矿化学成分见表6。
表6
TFe
不同条件成品烧结矿化学成份(计算值)
从表3可以看出,与基准期相比,在水分相近情况下,不加MgO(撤掉菱镁石) 混合料中大于3mm部分稍有减少,减少了2.52个百分点,混合料平均粒径变化不大, 仅减小了O.04mm,即减小了0.93%,混合料静态料层阻力变化不大。
3.2
MgO含量对烧结各项指标的影响 不同原料条件的烧结主要指标见表4。
不同原料条件下的烧结主要指标
32 32
不同原料条件的试验配料比
大磁
40 40
富矿
8 8
活性生石灰
2.5 2.5
生石灰
5.O 5.0
菱镁石
3.O O
石灰石
2.1 2.1
焦粉
4.2 4.2
返矿
18 18
2.2试验设备与试验方法
本试验在鞍钢炼铁总厂研究所试验室进行,烧结过程中烧结料层为550mm,点火 负压为8820Pa,点火时间为2min,点火结束后烧结负压调到10780Pa。 3试验结果与分析
表1
名称 弓浮 齐大山 大磁 富矿 活性生石灰 生石灰 菱镁石 石灰石 焦粉
TFe 68.70 67.50 66.46 63.88 0.69 0.69 1.25 0.56 0.20
试验用原、燃料化学成份(%)
FeO 27.18 19.18 28.2 O.7 Si02 3.80 3.93 6.37 3.34 3.35 3.35 3.07 1.89 7.20 CaO O.16 O.18 0.14 0.14 85.00 80.00 2.80 51.93 O.30
1.333 1.436
降MgO前、后的烧结主要技术经济指标
转鼓指数
%
80.70 81.34
筛分
%
4.39 4.35 TFe 57.87 57.41 Fe0 7.88 8.16 CaO 10.41 10.87
化学成分%
Si02 4.74 4.92 R 2.20 2.21
MgO
2.02 1.84
S 0.024 0.028
Si02 5.31 5.29 CaO lO.6l 10.57
%
MgO