Z向钢板加工工艺
Z向钢板与普通钢板工艺差别2011.11.11
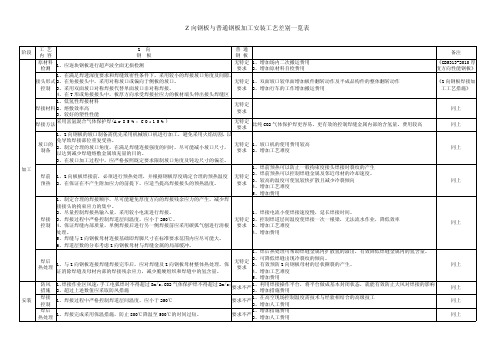
同上 比纯 CO2 气体保护焊更容易、更有效的控制焊缝金属内部的含氢量。费用较高 同上
1、坡口机的使用费用较高 2、增加工艺难度
同上
加工
1、焊前预热可以防止一般拘束度接头焊接时裂纹的产生 2、焊前预热可以控制焊缝金属及邻近母材的冷却速度。 无特定 3、较高的温度可使氢较快扩散且减少冷裂倾向 要求 4、增加工艺难度 5、增加费用
同上
焊接 控制
1、焊接电流小使焊接速度慢,延长焊接时间。 无特定 2、控制焊道层间温度使焊接一次一根梁,无法流水作业,降低效率 要求 3、增加工艺难度 4、增加费用
Z 向钢板与普通钢板加工安装工艺差别一览表
工 艺 Z 向 普 通 内 容 钢 板 钢 板 原材料 无特定 1、应逐块钢板进行超声波全面无损检测 检测 要求 1、在满足焊透深度要求和焊缝致密性条件下,采用较小的焊接坡口角度及间隙。 接头形式 2、在角接接头中,采用对称坡口或偏向于侧板的坡口。 无特定 控制 3、采用双面坡口对称焊接代替单面坡口非对称焊接。 要求 4、在 T 形或角接接头中,板厚方向承受焊接拉应力的板材端头伸出接头焊缝区 1、低氢性焊接材料 无特定 焊接材料 2、熔敷效率高 要求 3、较好的塑性性能 采用富氩混合气体保护焊(A r 8 5 % :C O 2 1 5 % ) 无特定 焊接方法 要求 1、Z 向钢板的坡口制备需优先采用机械坡口机进行加工,避免采用火焰切割, 以 免导致焊接部位重复受热。 坡口的 无特定 2、制定合理的坡口角度,在满足焊缝连接强度的同时,尽可能减小坡口尺寸, 制备 要求 以达到减少焊缝熔敷金属填充量的目的。 3、在坡口加工过程中,应严格按照既定要求限制坡口角度及钝边尺寸的偏差。 焊前 预热 1、Z 向板板焊接前,必须进行预热处理,并根据钢板厚度确定合理的预热温度 2、在保证在不产生附加应力的前提下,应适当提高焊接接头的预热温度。 1、制定合理的焊接顺序,尽可能避免厚度方向的焊接残余应力的产生,减少焊 接接头的拘束应力的集中。 2、尽量控制焊接热输入量,采用较小电流进行焊接。 3、焊接过程中严格控制焊道层间温度,应小于 250℃。 4、保证焊缝内部质量,单侧焊接后进行另一侧焊接前应采用碳弧气刨进行清根 处理。 5、焊缝与 Z 向钢板母材连接基础即焊脚尺寸在标准要求范围内应尽可能大。 6、焊道层数的分布考虑 Z 向钢板母材与焊缝金属的局部缓冲。
Z向钢板焊接加工工艺措施

Z向钢板焊接加工工艺措施1、概述厚板焊接目前已引起全国各塔厂的高度重视,一般不小于40 mm的厚钢板在焊接过程中较易产生层状撕裂,因为钢板越厚,非金属夹杂缺陷越多,且焊缝也越厚,焊接应力和变形就越大。
我公司通过制定和实施厚板焊接加工防层状撕裂工艺措施,成功解决了厚板的层状撕裂问题。
2、层状撕裂产生原因层状撕裂产生的主要原因为钢中存在片状硫化物与层状硅酸盐或大量成片地密集于同一平面内的氧化铝夹杂物,可能导致Z向塑性降低,沿钢材轧制方向发生阶梯状的层状撕裂。
3、厚钢板焊接加工防层状撕裂工艺措施3.1 原材料控制GB/T 1591《低合金高强度结构钢》中要求Q345B钢中S含量≤0.04%、P含量≤0.04%。
在原材料进厂复验过程中,对钢板的S、P含量需进行严格的控制,S、P含量的实测值应低于标准要求的1/2。
厚板原材料进厂后应逐块进行无损检测,检测板内有无夹层。
对不符合要求的钢板必须要求退货处理。
3.2 焊接接头设计要点3.2.1 在满足焊透深度要求和焊缝致密性条件下,采用较小的焊接坡口角度及间隙。
3.2.2 在角接接头中,采用对称坡口或偏向于侧板的坡口。
3.2.3 采用双面坡口对称焊接代替单面坡口非对称焊接。
3.2.4 在T形或角接接头中,板厚方向承受焊接拉应力的板材端头伸出接头焊缝区。
3.3 焊接工艺控制3.3.1焊接材料的选择在满足接头强度要求的条件下,选用具有较好熔敷金属塑性性能的焊接材料,我公司采用的气保焊丝ER50-6是一种强度等级较低的低氢性焊接材料,焊丝的熔敷效率高且具有较好的塑性性能,也是一种公认的厚板焊接材料。
3.3.2 焊接方法的选择15%),在焊接厚板时,我公司采用了富氩混合气体保护焊(Ar85%:CO2气体保护焊更容易、更有效此种焊接方法为低氢焊接方法的一种,比纯CO2的控制焊缝金属内部的含氢量。
3.3.3 坡口的制备3.3.3.1 厚板的坡口制备需优先采用机械坡口机进行加工,避免采用火焰切割,以免导致焊接部位重复受热。
钢板成型加工工艺
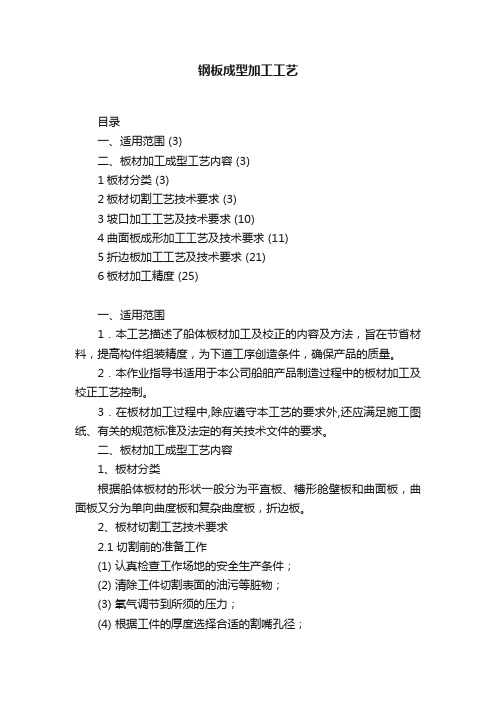
钢板成型加工工艺目录一、适用范围 (3)二、板材加工成型工艺内容 (3)1板材分类 (3)2板材切割工艺技术要求 (3)3坡口加工工艺及技术要求 (10)4曲面板成形加工工艺及技术要求 (11)5折边板加工工艺及技术要求 (21)6板材加工精度 (25)一、适用范围1.本工艺描述了船体板材加工及校正的内容及方法,旨在节省材料,提高构件组装精度,为下道工序创造条件,确保产品的质量。
2.本作业指导书适用于本公司船舶产品制造过程中的板材加工及校正工艺控制。
3.在板材加工过程中,除应遵守本工艺的要求外,还应满足施工图纸、有关的规范标准及法定的有关技术文件的要求。
二、板材加工成型工艺内容1、板材分类根据船体板材的形状一般分为平直板、槽形舱壁板和曲面板,曲面板又分为单向曲度板和复杂曲度板,折边板。
2、板材切割工艺技术要求2.1 切割前的准备工作(1) 认真检查工作场地的安全生产条件;(2) 清除工件切割表面的油污等脏物;(3) 氧气调节到所须的压力;(4) 根据工件的厚度选择合适的割嘴孔径;(5) 点火调节预热火焰(中性焰),然后打开切割氧气阀,检查切割气流(俗称风线)的形状和长度是否符合要求(呈细而直的射流喷出)。
2.2 切割操作技术要求(1)对手动切割和半自动切割工艺操作要求。
A 切割时应对准零件的号料线。
B 切割过程中,根据实际情况随时调整有关参数。
遇氧气压力不足或成份不纯而严重影响切割质量应立即停止切割。
C 为减少零件在切割时的变形应遵循下列程序:1) 大型零件的切割,应先从短边开始;2) 一张钢板上切割众多不同尺寸的零件时,应先割小件,后割大件;3) 同一张钢板上切割不同形状的零件时,应先割线型较复杂的零件,而后割较简单的零件;(2)对高精度方式自动切割机的操作技术要求。
A 切割前应检查切割机行走的情况(空车行走),导管状态,待正常后才能工作;随时检查导轨的垃圾或异物并及时清除;B 根据工件钢板的厚度选用合适的割嘴切割速度及氧气等的压力;C 根据工件的精度要求,调节割嘴与割嘴的间距;D 在切割过程中采用中性焰,风线要清晰,必须保持割嘴与钢板的垂直;E 切割过程中遇氧气压力不足或成份不纯而严重影响切割质量,应暂停切割,以待问题解决后再开始切割;F 切割过程中若切割机行走出现故障应停止切割,故障排除后,才可继续操作;G 切割多根板条时,始割端和终割端应以封闭状态形式,待稍冷后,再进行二端横缝切割;H 板条工件切割时,工件二侧应有留余边,并进行双矩并行切割;I 操作完毕后,将割矩装置升高及电源、氧气、燃气阀门关闭。
当设计对厚板有Z向性能要求时的焊接工艺措施

当设计对厚板有Z向性能要求时的焊接工艺措施
(1)选择合理的焊接节点连接形式:
应选择合理的节点连接形式,以减小局部区域由于焊缝收缩而引起的应力集中或尽量避
免钢板Z 向受拉。
1)在满足要求焊透深度的前提下,采用较小的焊接坡口角度及间隙。
2)在角接接头中,采用对称坡口或偏向侧板的坡口,减小板厚方向承受的收缩应力。
3)采用对称坡口,减小焊接收缩应力。
4)在T 形或角接接头中,不应在板厚方向受焊接拉应力的板材的端部设置焊缝,而应使
该板厚方向受拉的板材端部伸出接头焊缝区。
5)在T 形、十字形接头中采用过渡段,以对接接头取代T 形、十字形接头。
6)对大型连接节点,建议采用下图的构造设计来避免或减少厚度方向的应变。
(2)焊材及母材选择:
1)对有特殊要求的部位,可选用Z 向延性性能好的钢材。
2)在满足受力要求的前提下,尽可能选择屈服强度低的焊条。
(3)使用涂层和垫层:
采用软金属丝(一般为低强度的焊条)做垫层,使收缩变形发生在焊缝中或在节点焊缝处
涂焊一层低强高延性焊接金属,让焊缝收缩变形发生在涂焊金属中。
(4)防止层状撕裂的工艺措施:
1)T 形焊接时,在母材板面用低强度焊材先堆焊塑性过渡层。
2)厚板焊接时,可采用低氢型、超低氢型焊条或气体保护焊施焊,并适当提高预热温度。
3)当板厚在80mm 以上时,对Ⅱ类或Ⅱ类以上钢材箱形柱角焊缝,板边火焰切割面宜用
机械方法去除淬硬层。
4)对大尺寸熔透焊,可采用窄焊道焊接技术,并选择合理的焊道次序,以控制收缩变形。
焊接过程中,应用锤击法来消除焊缝残余应力。
正火轧制Z向性能钢板Q355NCZ15试制开发

2020年第2期近年来,市场上对低合金钢板的使用越来越广泛,对其质量要求也越来越高,除了具备高强度、高韧性以及易加工性之外,还要求具备良好的抗层状撕裂性能(Z 向性能)。
而行车梁、承重柱等框架结构件,还会选用正火状态下使用性能优良的结构钢来制造。
正火轧制指钢板最终变形是在一定温度范围内的轧制过程中进行,使钢材达到一种正火后的状态,是模拟正火热处理状态的生产方式。
正火轧制在实际应用中可节约能源和时间,降低成本。
柳钢根据市场需求,采用Nb-Ti 复合强化方式,运用洁净钢生产技术以及合理的加热、轧制工艺,在2800mm 双机架四辊可逆中厚板轧机成功开发正火轧制Z 向性能钢板Q355NCZ15,本文对试制工作进行总结。
试制开发本试验轧制钢板使用细晶强化和沉淀强化的方式提高钢板强度,决定在板坯内加入Mn 、Nb 、Ti 、Al 进行强化。
连铸坯断面尺寸220mm ×1820mm ,主要生产工艺流程为:铁水脱硫预处理→150t 转炉冶炼→LF 精炼→RH 精炼→板坯连铸→推钢式加热炉加热→除鳞→粗轧→精轧→矫直→钢板检查→标记入库。
成分及性能要求试验钢为Q355NCZ15,其成分及性能满足GB/T 1591-2018《低合金高强度结构钢》、GB/T 5313-2010《厚度方向性能钢板》的规定,具体见表1、表2。
正火轧制向性能钢板试制开发陈盛淋(技术中心),张肄,韦仕朵(经销公司),何涛(中板厂)表1Q355NCZ15钢板力学性能要求屈服强度/MPa抗拉强度m /MPa 伸长率/%180°冷弯V 型冲击功(纵向)≤16mm >16~40mm >40~63mm≤63mm ≤16mm >16~100mm 温度/℃/J ≥355≥345≥335470~630≥22=2=320≥34成分设计考虑到钢板性能要求及合金成本,成分设计上采用Nb-Ti 复合强化工艺。
在C 、Mn 固溶强化的基础上,往钢中加入Nb 、Ti 微量合金元素,有强烈阻止奥氏体晶粒长大的作用,易于研发动态192020年第2期获得细晶粒组织。
z向钢焊接工艺
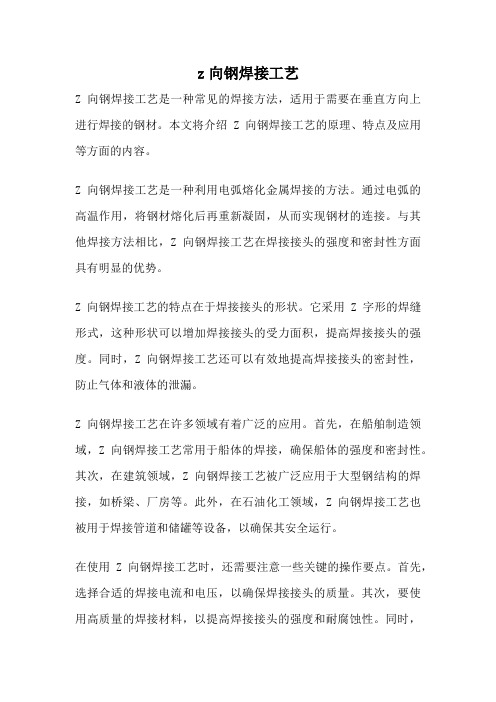
z向钢焊接工艺Z向钢焊接工艺是一种常见的焊接方法,适用于需要在垂直方向上进行焊接的钢材。
本文将介绍Z向钢焊接工艺的原理、特点及应用等方面的内容。
Z向钢焊接工艺是一种利用电弧熔化金属焊接的方法。
通过电弧的高温作用,将钢材熔化后再重新凝固,从而实现钢材的连接。
与其他焊接方法相比,Z向钢焊接工艺在焊接接头的强度和密封性方面具有明显的优势。
Z向钢焊接工艺的特点在于焊接接头的形状。
它采用Z字形的焊缝形式,这种形状可以增加焊接接头的受力面积,提高焊接接头的强度。
同时,Z向钢焊接工艺还可以有效地提高焊接接头的密封性,防止气体和液体的泄漏。
Z向钢焊接工艺在许多领域有着广泛的应用。
首先,在船舶制造领域,Z向钢焊接工艺常用于船体的焊接,确保船体的强度和密封性。
其次,在建筑领域,Z向钢焊接工艺被广泛应用于大型钢结构的焊接,如桥梁、厂房等。
此外,在石油化工领域,Z向钢焊接工艺也被用于焊接管道和储罐等设备,以确保其安全运行。
在使用Z向钢焊接工艺时,还需要注意一些关键的操作要点。
首先,选择合适的焊接电流和电压,以确保焊接接头的质量。
其次,要使用高质量的焊接材料,以提高焊接接头的强度和耐腐蚀性。
同时,还要注意焊接过程中的保护措施,避免焊接接头受到氧化和污染。
总结起来,Z向钢焊接工艺是一种常见且重要的焊接方法,它通过Z 字形的焊缝形式提高了焊接接头的强度和密封性。
在船舶制造、建筑和石油化工等领域有着广泛的应用。
在使用该工艺时,需要注意选择合适的焊接参数和材料,并做好焊接过程中的保护工作。
只有在正确操作和应用的前提下,Z向钢焊接工艺才能发挥其优势,确保焊接接头的质量和可靠性。
Z钢结构的施工工艺流程

钢结构施工技术1.加工工艺本工程的钢结构主梁为大型工字钢,加工焊接工字钢显得尤其重要,工字钢的流水作业生产工艺流程如图1所示。
图1 工字钢流水作业生产的工艺流程1.1材料拼接钢板拼接必须在直条下料前完成,先采用埋弧自动焊进行钢板的焊接,焊后按规定要求进行无损探伤,20%X射线探伤,符合GB标准中的Ⅲ级为合格。
无损探伤合格后,钢板的调平采用滚板机进行。
钢板对接接头预放收缩量:板厚δ8~16 mm 时, 为1.5~2mm ; 板厚δ20~40 mm 时,为2.5~3mm 。
1.2下料直条下料采用多头切割机,将平直的钢板用行车吊至多头切割机工作台上,根据图纸要求调整好纵向割炬的间距,然后进行切割。
连接件、肋板等的下料采用仿形切割机切割,按制作好的样板先切割一件,检验合格后进行批量生产。
型钢下料采用机械切割。
下料应预留加工余量、焊接收缩量:所有机加工边的加工余量一般预留为5mm ;接口焊缝每一个接口为1.0mm ;纵长焊缝焊接收缩量每米0.1~0.5mm 。
1.3组对将翼缘板置于组对专用设备上,使之对中;然后把腹板立放对中,将翼缘板和腹板压紧点焊固定,组对成┻形;最后将另一块翼缘板组对点焊好成Ⅰ形。
定位焊时在两侧每隔200mm 点焊50mm 长、3~5mm 高的间断焊。
1.4焊接对组后的工字型钢运至焊接工作台上(如图2-a 所示),置于船形位置,采用埋弧自动焊进行平角位置的焊接,焊缝两端设置长100mm 的T 形引出板,引出板处焊缝长度不得少于50mm ,焊接顺序如图2-b 所示。
(a) 焊接位置(b) 焊接顺序 图2焊接材料选择如表:埋弧自动焊焊接工艺规范如表:1.5调校焊接后的H钢的翼缘板会产生菌状变形,而且翼缘板与腹板的垂直度也有偏差,必须采用工字钢矫正机进行矫正。
其原理如图3所示,导辊布置在图剖面的前后,以校正垂直,采用矫正辊两侧下压进行。
矫正时必须先试校一段(约500mm 长),检查合格后方可正常进行。
Z向性能钢板的技术要求及选用

处理。示例见表6。
4 防止层状撕裂工艺措施
在厚板焊接结构中,厚度方向焊接十字接头、
T形接头和斜接头,构件上始终承受因收缩产生的
焊接应力。母材内微小的层状偏折,在受垂直板面
的拉应力作用时,易产生层状撕裂。为避免构造不
当产生层状撕裂,设计人员在节点构造设计时,可
下式求得:
E
D
C
B
A
E
A
n
n
]
[
]
[
]
[
]
[
]
[
]
[
ψ
ψ
ψ
ψ
ψ
ψ
ψ
+
+
+
+
∑
=
=
=
各影响因素所需的断面收缩率[ψ]n的参数见
表5。表中列出的断面收缩率[ψ]n为参考值,当
[ψ]n为负值时表示该影响因素有利于抗层状撕
Pcm(%)=C+Si/30+Mn/20+Cu/20
+Ni/60+Cr/20+Mo/15 (2)
+V/10+5B
用于建造高层建筑结构和其他类似重要建筑
结构厚度≤100 mm钢板的化学成分和碳当量(Ceq)
或焊接裂纹敏感性指数 (Pcm)见表1、表2、表3。
近20年年来,我国高层建筑钢结构、海上采
油平台以及类似的重要建(构)筑物钢结构得到了
蓬勃的发展。在这类建(构)筑物中因结构承载力的
需要,常常采用厚板焊接结构,厚板结构在制造焊
接中,由于钢材质量和焊接构造等原因,厚板容易
z型钢成型方法
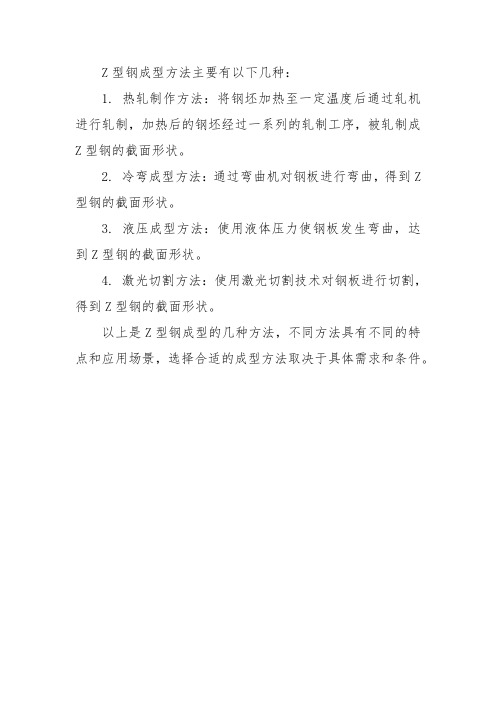
Z型钢成型方法主要有以下几种:
1. 热轧制作方法:将钢坯加热至一定温度后通过轧机进行轧制,加热后的钢坯经过一系列的轧制工序,被轧制成
Z型钢的截面形状。
2. 冷弯成型方法:通过弯曲机对钢板进行弯曲,得到Z 型钢的截面形状。
3. 液压成型方法:使用液体压力使钢板发生弯曲,达到Z型钢的截面形状。
4. 激光切割方法:使用激光切割技术对钢板进行切割,得到Z型钢的截面形状。
以上是Z型钢成型的几种方法,不同方法具有不同的特点和应用场景,选择合适的成型方法取决于具体需求和条件。
c型钢、z型钢加工工艺
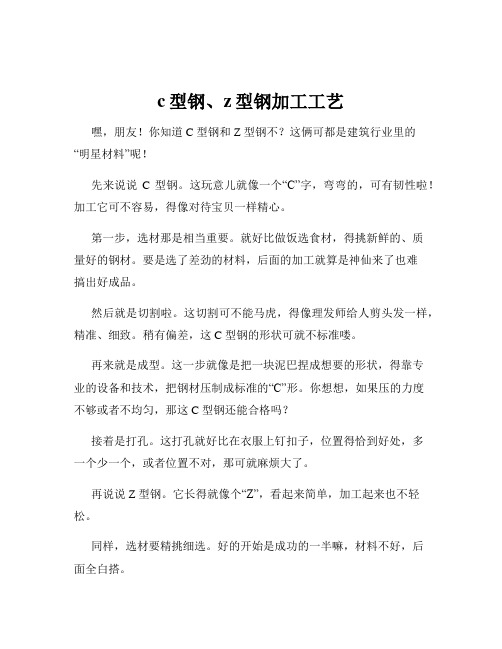
c型钢、z型钢加工工艺嘿,朋友!你知道 C 型钢和 Z 型钢不?这俩可都是建筑行业里的“明星材料”呢!先来说说C 型钢。
这玩意儿就像一个“C”字,弯弯的,可有韧性啦!加工它可不容易,得像对待宝贝一样精心。
第一步,选材那是相当重要。
就好比做饭选食材,得挑新鲜的、质量好的钢材。
要是选了差劲的材料,后面的加工就算是神仙来了也难搞出好成品。
然后就是切割啦。
这切割可不能马虎,得像理发师给人剪头发一样,精准、细致。
稍有偏差,这 C 型钢的形状可就不标准喽。
再来就是成型。
这一步就像是把一块泥巴捏成想要的形状,得靠专业的设备和技术,把钢材压制成标准的“C”形。
你想想,如果压的力度不够或者不均匀,那这 C 型钢还能合格吗?接着是打孔。
这打孔就好比在衣服上钉扣子,位置得恰到好处,多一个少一个,或者位置不对,那可就麻烦大了。
再说说 Z 型钢。
它长得就像个“Z”,看起来简单,加工起来也不轻松。
同样,选材要精挑细选。
好的开始是成功的一半嘛,材料不好,后面全白搭。
切割的时候更得小心,不能有毛刺,不然就像脸上长了痘痘,多难看呀。
成型环节那是关键中的关键。
要让它乖乖地变成“Z”形,设备得给力,操作的师傅也得有真功夫。
还有焊接,这焊接就像是给人缝伤口,得严丝合缝,不然强度不够,怎么能承受住压力呢?无论是 C 型钢还是 Z 型钢,加工过程中的每一个环节都像是一场精密的舞蹈,一步错步步错。
这就像搭积木,一块没放好,整个房子都可能垮掉。
所以啊,在加工 C 型钢和 Z 型钢的时候,一定要严格把关,每一个步骤都要做到极致。
只有这样,才能生产出高质量的型钢,让我们的建筑更加牢固、更加美观。
朋友,你说是不是这个理儿?。
- 1、下载文档前请自行甄别文档内容的完整性,平台不提供额外的编辑、内容补充、找答案等附加服务。
- 2、"仅部分预览"的文档,不可在线预览部分如存在完整性等问题,可反馈申请退款(可完整预览的文档不适用该条件!)。
- 3、如文档侵犯您的权益,请联系客服反馈,我们会尽快为您处理(人工客服工作时间:9:00-18:30)。
厚板加工工艺措施
1、概述
厚板焊接目前已引起全国各塔厂的高度重视,一般不小于40 mm的厚钢板在焊接过程中较易产生层状撕裂,因为钢板越厚,非金属夹杂缺陷越多,且焊缝也越厚,焊接应力和变形就越大。
我公司通过制定和实施厚板焊接加工防层状撕裂工艺措施,成功解决了厚板的层状撕裂问题。
2、层状撕裂产生原因
层状撕裂产生的主要原因为钢中存在片状硫化物与层状硅酸盐或大量成片地密集于同一平面内的氧化铝夹杂物,可能导致Z向塑性降低,沿钢材轧制方向发生阶梯状的层状撕裂。
3、厚钢板焊接加工防层状撕裂工艺措施
3.1 原材料控制
GB/T 1591《低合金高强度结构钢》中要求Q345B钢中S含量≤0.04%、P含量≤0.04%。
在原材料进厂复验过程中,对钢板的S、P含量需进行严格的控制,S、P含量的实测值应低于标准要求的1/2。
厚板原材料进厂后应逐块进行无损检测,检测板内有无夹层。
对不符合要求的钢板必须要求退货处理。
3.2 焊接接头设计要点
3.2.1 在满足焊透深度要求和焊缝致密性条件下,采用较小的焊接坡口角度及间隙。
3.2.2 在角接接头中,采用对称坡口或偏向于侧板的坡口。
3.2.3 采用双面坡口对称焊接代替单面坡口非对称焊接。
3.2.4 在T形或角接接头中,板厚方向承受焊接拉应力的板材端头伸出接头焊缝区。
3.3 焊接工艺控制
3.3.1焊接材料的选择
在满足接头强度要求的条件下,选用具有较好熔敷金属塑性性能的焊接材料,我公司采用的气保焊丝ER50-6是一种强度等级较低的低氢性焊接
材料,焊丝的熔敷效率高且具有较好的塑性性能,也是一种公认的厚板焊接材料。
3.3.2 焊接方法的选择
15%),在焊接厚板时,我公司采用了富氩混合气体保护焊(Ar85%:CO
2
气体保护焊更容易、更有效此种焊接方法为低氢焊接方法的一种,比纯CO
2
的控制焊缝金属内部的含氢量。
3.3.3 坡口的制备
3.3.3.1 厚板的坡口制备需优先采用机械坡口机进行加工,避免采用火焰切割,以免导致焊接部位重复受热。
3.3.3.2 制定合理的坡口角度,在满足焊缝连接强度的同时,尽可能减小坡口尺寸,以达到减少焊缝熔敷金属填充量的目的。
3.3.3.3 在坡口加工过程中,应严格按照既定要求限制坡口角度及钝边尺寸的偏差。
3.3.4 焊前预热
厚板焊接前,必须进行预热处理,并根据钢板厚度确定合理的预热温度,在保证在不产生附加应力的前提下,应适当提高焊接接头的预热温度。
焊前预热可以防止一般拘束度接头焊接时裂纹的产生,焊前预热可以控制焊缝金属及邻近母材的冷却速度。
较高的温度可使氢较快扩散且减少冷裂倾向。
Q345B材质预热温度为100~150℃。
3.3.5 焊接工艺控制
3.3.5.1 制定合理的焊接顺序,尽可能避免厚度方向的焊接残余应力的产生,减少焊接接头的拘束应力的集中。
3.3.5.2 焊接过程中严格执行焊接工艺卡参数,尽量控制焊接热输入量,采用较小电流进行焊接。
3.3.5.3 焊接过程中严格控制焊道层间温度,应小于250℃。
3.3.5.4 作用于收缩方向上的焊缝厚度应尽可能低。
3.3.5.5 保证焊缝内部质量,单侧焊接后进行另一侧焊接前应采用碳弧气刨进行清根处理。
3.3.5.6 焊缝与厚板母材连接基础即焊脚尺寸在标准要求范围内应尽可能大。
3.3.5.7 焊道层数的分布考虑厚板母材与焊缝金属的局部缓冲。
3.4 焊后热处理
3.4.1 焊后热处理可帮助焊缝金属内扩散氢的溢出,有效降低焊缝金属内的氢含量。
降低焊缝出现冷裂纹的倾向,同时也有效预防厚板母材的层状撕裂的产生。
3.4.2 与厚板连接焊缝焊接完毕后,应对焊缝及厚板母材整体热处理,保证消除焊缝及母材内部的焊接残余应力,减少脆硬组织和焊缝中的氢含量。
4、无损检测
待焊后热处理结束后,应对焊缝和母材分别进行超声波探伤,检验焊缝内部有无焊接缺陷,检验母材内部有无夹层及裂纹等缺陷。