蓄热式熔铝炉节能技术
蓄热式熔铝炉资料
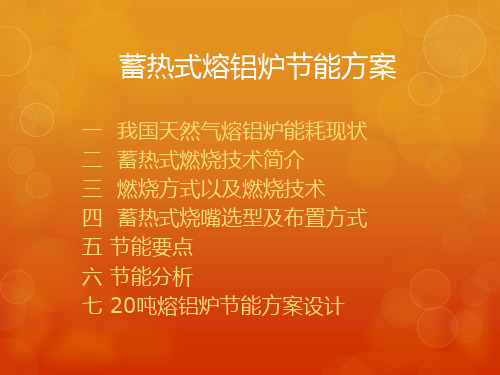
六 节能分析
我国天然气熔铝炉吨铝能耗75万大卡,折合天然气约88Nm3 , 过量空气系数1.17 需要空气量1030Nm3 产生烟气量1118Nm3 烟气温度1000℃ 烟气成分如图,1000℃烟气比热为1.51KJ/(m3℃) 空气平均温度22℃,比热为1.013KJ/(kg℃) 标况下空气密度1.293kg/m3 烟气带走热量约396680大卡
燃烧技术分类
二 燃气分级燃烧技术
没有定型的火焰,火焰无法控制,燃烧性能差, 燃气喷嘴易烧毁,辐射性能差,加热质量低。
二段式低NOx燃烧器
二段式低NOx燃烧器 该燃烧器的工作原理如图1所 示,是将燃烧用的空气分2次通 入燃烧区,从而使燃烧过程分两 个阶段完成,避免高温区过分集 中。二次空气是从还原区外围送 入的,在火焰尾部完成完全燃 烧。由于实行分段燃烧,避免了 高温区集中, 因而NOx的排放 浓度显著降低。
二 蓄热式燃烧技术简介
基本原理
烧嘴和蓄热体成对出现, 助燃空气通过其中一个烧嘴, 被加热后供燃烧用,另一个 烧嘴充当排烟的角色,同时 蓄热体被加热。当到达换向 时刻时,换向阀动作使系统 反向运行,烟气加热好的蓄 热体被用来加热空气,助燃 空气冷却的蓄热体又被离开 炉子的高温烟气加热,
技术形成
将高温空气喷射入炉 膛,维持低氧状态,同时将 燃料输送到气流中,产生燃 烧。空气温度预热到800℃ ~1000℃以上,燃烧区空气 含氧量在21%~2%,与传统燃 烧过程相比,高空气燃烧的 最大特点是节省燃料,减少 CO2和NOX的排放及降低燃烧 噪音,被誉为二十一世纪关 键技术之一。
蓄热式燃烧系统工作原理
三 燃烧方式分类
1扩散式燃烧 2部分预混式燃烧 3预混式燃烧
1扩散式燃烧
2部分预混式燃烧 3预混式燃烧
蓄热式熔铝炉节能技术
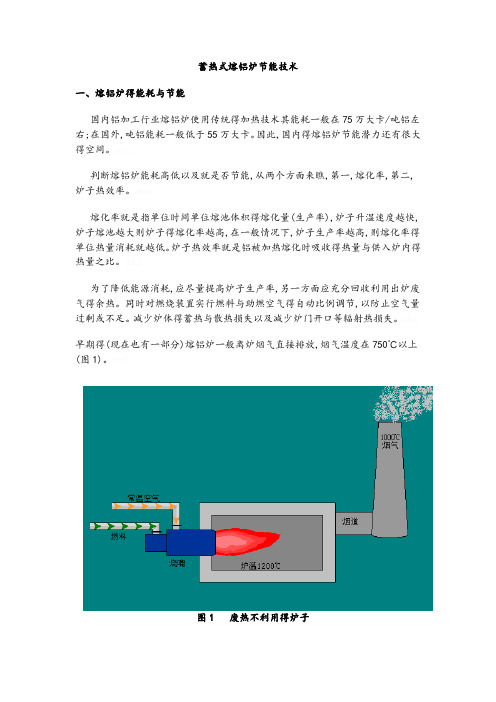
蓄热式熔铝炉节能技术一、熔铝炉得能耗与节能国内铝加工行业熔铝炉使用传统得加热技术其能耗一般在75万大卡/吨铝左右;在国外,吨铝能耗一般低于55万大卡。
因此,国内得熔铝炉节能潜力还有很大得空间。
判断熔铝炉能耗高低以及就是否节能,从两个方面来瞧,第一,熔化率,第二,炉子热效率。
熔化率就是指单位时间单位熔池体积得熔化量(生产率),炉子升温速度越快,炉子熔池越大则炉子得熔化率越高,在一般情况下,炉子生产率越高,则熔化率得单位热量消耗就越低。
炉子热效率就是铝被加热熔化时吸收得热量与供入炉内得热量之比。
为了降低能源消耗,应尽量提高炉子生产率,另一方面应充分回收利用出炉废气得余热。
同时对燃烧装置实行燃料与助燃空气得自动比例调节,以防止空气量过剩或不足。
减少炉体得蓄热与散热损失以及减少炉门开口等辐射热损失。
早期得(现在也有一部分)熔铝炉一般离炉烟气直接排放,烟气温度在750℃以上(图1)。
图1 废热不利用得炉子为减少烟气带走得热量损失,人们在排烟管道上安装了热量回收装置即空气换热器,将助燃空气预热到一定得温度(200℃左右)后参与燃料得燃烧,但换热器后得排放温度还在500℃以上(图2)。
图2 安装空气预热器得炉子采用蓄热式燃烧技术可以将烟气排放温度降低到150℃以下,助燃空气温度预热到700℃以上,这样就大大地减少了离炉烟气所带走得热量,使炉子热效率大幅度提高,燃料消耗大量减少,达到节能得目得(图3)。
图3 HTAC技术得工作原理图根据工业炉热工原理,助燃空气温度每升高100℃,能节省燃料约5%;或者烟气温度每降低100℃,能节省燃料约5、5%。
因此,采用蓄热式燃烧技术相对换热器回收装置可以节能25%以上。
二、熔炼炉概述:传统上有火焰炉、电阻炉、中频感应炉、反射炉以及坩埚炉等。
为了获得质量高又经济得铝合金溶液,各企业对熔炼设备得选择越来越重视,近几年来,火焰炉、电阻炉、中频感应炉、反射炉都有所改进。
熔炼炉结构得发展方向就是:操作自动化、应用更新化、原料节能化等。
熔炼炉节能

熔炼炉燃烧参数控制摘要:铝和铝合金的熔炼是铝加工企业生产中的第一道重要工序,而铝熔炼炉是铝熔炼的关键设备,也是工厂中主要耗能设备,在生产能耗中占有很大比例,一些企业铸轧板材生产中其燃料消耗达到总能耗的50%左右。
本文以铝及铝合金的熔炼炉燃烧控制参数——天然气流量、助燃风流量、天然气和助燃风比例、炉压、排烟温度等方面对能耗的影响及之间的相互影响和我厂在各参数控制方面的经验综合论述,望能够给同行参考。
关键词:熔铝炉蓄热式燃烧天然气流量助燃风流量天然气和助燃风比例炉压排烟温度ABSTRACT:Smelting aluminum and Avional is the first important procedure in fabricating factories. Moreover ,aluminum melting furnace is the key equipment in the smelting and the main energy consumption facilities. Aluminum smelting furnace occupies high proportion of energy consumption.For example ,the fuel consumed in a furnace is about 50% of general energy consumption in some enterprises who produce cast—rolling plate.This paper expatiated on the aluminum and aluminum alloy combustion control parameter— the gas flow, the combustion air flow, air-gas delivery ration, furnace pressure, exhaust temperature on the influence and the energy consumption of the interaction between various parameters and factory in controlling the comprehensive discussion, hope can experience for reference to Reference.KEYWORDS: Aluminum smelting furnace Regenerative burner Gas flow Combustion air flow Air-gas delivery ration Furnace pressure Exhaust temperature我厂熔炼炉是采用苏州博能窑炉科技有限公司2008年设计安装的,主要技术性能参数如下:1.用途:铝及铝合金的熔化2.炉子形式:固定式矩形炉、侧侧装电解铝液3.原料:电解铝液、铝锭、铝合金锭及废料4.炉子容量:25吨5.炉膛工作温度:1100-1200℃6.铝液出炉温度:720-760℃7.熔体温差:+5℃(精炼、搅拌终了)8.燃料:天然气/土煤气9.燃料最低发热值:4.18X8600/4.18X1200kJ/Nm310.熔化期最大熔化率:3吨/小时(纯冷料)11.燃料最大消耗量:350Nm3天然气/小时(1800土煤气/小时)12.熔化期吨铝消耗::≤65天然气/吨铝13.烧嘴形式:蓄热式燃烧器2个14.温度控制形式:PLC自动控制相关设备说明:熔炼炉燃烧系统图我厂熔炼炉采用蓄热式燃烧系统,配有2个蓄热式烧嘴,呈约15o向熔池倾斜,每个烧嘴都有自己一套点火和火焰检测装置。
24t熔铝炉蓄热式节能改造

维普资讯
第 5期
有色金属加工
2 1
据金属温度调节煤气 、 空气流量及空燃 比, 制两个 控 燃烧器的换 向燃烧 , 使炉料熔化升温 到 70~ 5 2 70℃; 熔体静置、 除渣后转入保温炉 , 每炉熔炼周期约 3 h左
右 。加 完料 后 , 当实 际温 度 低 于设 定 温度 2 0℃ 以上 时 , 制系 统将 煤 气 和 风 调 节 到 最 大值 , 烧 器 以最 控 燃
最大装炉容量 : ; 2 t 4
我们在本公司铝带坯铸轧机 的 2 熔铝炉节能改造 4t
中采用 了这项 先进 技术 。
熔化速率 : t ; 5/ h 燃 烧器数 : ; 2个
炉膛温度:5 — 0 90 110℃, 最高不超过 l 0 0℃ ; 2
温度波 动范 围 : 3o ± C; 炉膛压 力控 制范 围 : 0 P ; ±10. a 电气控 制 :0 1可编程 控制器 。 40
靳 秋 良 , 爱芝 乔
( 中铝洛阳铜业有 限公 司 , 河南洛阳 4 13 ) 70 9
摘
要 : 蓄热式高温空气 燃烧 技 术 ( T C 对 2 熔 铝 炉进行 了节 能改造 , 采用 H A ) 4t 降低 了产 品能耗 , 节约 了
能源 。
关键词 : 熔铝炉 ; T C; 能改造 HA 节
收 稿 日期 :0 861 2 0 -.9
3 电气 控制系统 的设计
3 1 工艺 对控 制 系统 的 要求 、 ・ 2 熔 铝 炉 正 常 生 产 时 , 般 每 次 投 料 装 入 4t 一 5- 铝 锭 , 料完 成 后 关 闭 炉 门 , 动控 制 系 统 ; 7t 投 启 根
维普资讯
第3 7卷
科技成果——低烧损和低氮氧化物排放的铝熔炼炉蓄热式贫氧燃烧技术
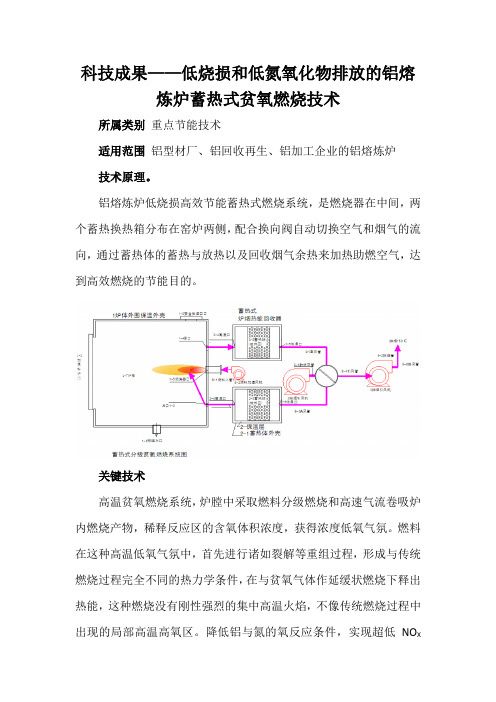
科技成果——低烧损和低氮氧化物排放的铝熔炼炉蓄热式贫氧燃烧技术所属类别重点节能技术适用范围铝型材厂、铝回收再生、铝加工企业的铝熔炼炉技术原理。
铝熔炼炉低烧损高效节能蓄热式燃烧系统,是燃烧器在中间,两个蓄热换热箱分布在窑炉两侧,配合换向阀自动切换空气和烟气的流向,通过蓄热体的蓄热与放热以及回收烟气余热来加热助燃空气,达到高效燃烧的节能目的。
关键技术高温贫氧燃烧系统,炉膛中采取燃料分级燃烧和高速气流卷吸炉内燃烧产物,稀释反应区的含氧体积浓度,获得浓度低氧气氛。
燃料在这种高温低氧气氛中,首先进行诸如裂解等重组过程,形成与传统燃烧过程完全不同的热力学条件,在与贫氧气体作延缓状燃烧下释出热能,这种燃烧没有刚性强烈的集中高温火焰,不像传统燃烧过程中出现的局部高温高氧区。
降低铝与氮的氧反应条件,实现超低NO X排放和高效节能,减小铝氧化损失目的。
初级小量的常温助燃风和燃料入口混合预燃烧,既可冷却燃料在喷咀的温度,防止燃料碳分解堵塞烧咀,又形成燃料富燃料烧,增加燃料喷射速度,这种高速气流卷吸炉内燃烧产物和高温助燃空气。
这种富燃料与分级燃烧的技术,气氛控制,使得燃料在高温低氧气氛中燃烧,以降低燃烧火焰中心区域的温度,并采用分级燃烧技术,动态燃烧反应,没有强烈的集中火焰,使炉膛温度分布更加均匀。
工艺流程燃烧系统设在炉墙上,具有A、B两组蓄热器、一套燃料喷咀,一台排烟引风机和一台助燃风机,一台助燃空气烟气切换阀,燃料喷咀在两组蓄热器中间,整个炉膛为燃烧区。
炉膛燃烧产生的高温烟气在引风机作用通过炉墙中的烟孔进入A蓄热器,与蓄热球换热,烟气降低到100度以下;助燃风机将助燃风送入蓄热体与蓄热球换热,助燃风被加热到700度以上,再送到炉膛与高温燃烧产物混合,形成低氧高温空气,燃料喷咀将燃料与小量的助燃空气混合,高速喷进炉膛燃烧。
形成加热室燃烧——加料室烟气余热利用——蓄热体热能回收——低温烟气排放——旋转蓄热体将助燃风加热——燃烧器高温助燃风与燃料混合——炉膛燃烧的循环。
211169313_铝熔炼炉蓄热式燃烧系统节能改造项目
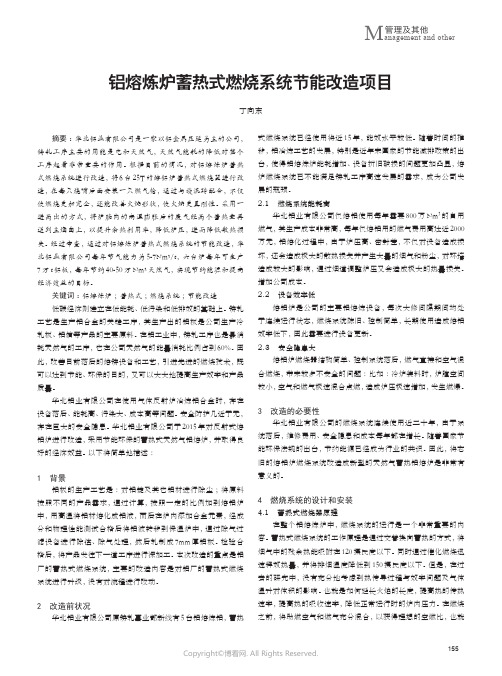
管理及其他M anagement and other 铝熔炼炉蓄热式燃烧系统节能改造项目丁向东摘要:华北铝业有限公司是一家以铝金属压延为主的公司,铸轧工序主要的用能是电和天然气,天然气能耗的降低对整个工序起着非常重要的作用。
根据目前的情况,对铝熔炼炉蓄热式燃烧系统进行改造,将6台25T的熔铝炉蓄热式燃烧器进行改造,在每只烧嘴后面安装一只燃气枪,通过与旋流砖配合,不仅使燃烧更加完全,还能改善火焰形状,使火焰更具刚性。
采用一进两出的方式,将炉膛内的高温膨胀后的废气经两个蓄热室再送到主烟囱上,以提升余热利用率,降低炉压,进而降低散热损失。
经过审查,通过对铝熔炼炉蓄热式燃烧系统的节能改造,华北铝业有限公司每年节气能力为5-7Nm³/t,六台炉每年可生产7万t铝板,每年节约40-50万Nm³天然气,实现节约能源和提高经济效益的目标。
关键词:铝熔炼炉;蓄热式;燃烧系统;节能改造低碳经济则建立在低能耗、低污染和低排放的基础上。
铸轧工艺是生产铝合金的关键工序,其生产出的铝板是公司生产冷轧板、铝箔等产品的主要原料。
在铝工业中,铸轧工序也是最消耗天然气的工序,它在公司天然气的能量消耗比例占到60%。
因此,改善目前落后的熔铸设备和工艺,引进先进的燃烧技术,既可以达到节能、环保的目的,又可以大大地提高生产效率和产品质量。
华北铝业有限公司在使用气体反射炉冶炼铝合金时,存在设备落后、能耗高、污染大、成本高等问题。
安全防护几近于无,存在巨大的安全隐患。
华北铝业有限公司于2015年对反射式熔铝炉进行改造,采用节能环保的蓄热式天然气铝熔炉,并取得良好的经济效益。
以下将简单地描述:1 背景铝板的生产工艺是:对铝锭及其它铝材进行除尘;将原料按照不同的产品需求,通过计算,按照一定的比例加到熔铝炉中,用高温将铝材熔化成铝液,而后在炉内添加合金元素,经成分和物理性能测试合格后将铝液转移到保温炉中,通过除气过滤设备进行除渣、除气处理,然后轧制成7mm厚铝板。
蓄热燃烧技术的应用

蓄热燃烧技术的应用蓄热燃烧技术是基于蓄热室的概念回收废气的余热,实现余热极限回收和助燃空气的高温预热,达到节能效果。
蓄热室最早发明于1858年,主要用在玻璃熔炉、平炉、熔铝炉等工业路上。
自20世纪70年代能源危机后,节能降耗得到各个国家的重视,蓄热式燃烧技术由于能够最大限度地回收出炉烟气的热量,大幅度地节约燃料、降低成本,同时还能减少CO2和NO x的排放量。
因此,该技术在国际上被称为二十一世纪的关键技术之一。
1.蓄热式燃烧器九十年代至今, 美、日、英等国开发出蓄热式燃烧器,并不断加以发展完善,实现了高效节能与低污染排放,现已成功地应用于加热炉、热处理炉、锻造炉等工业炉上。
蓄热式燃烧器是一种集燃烧器、换热器、排烟功能为一体的新型燃烧器,主要通过蓄热体,利用烟气热量将空气预热至高温,很大地提高热能利用率;同时又采用了分级燃烧和烟气回流技术,减少了燃烧污染的排放量。
蓄热式燃烧器主要有陶瓷蓄热室、燃料喷口、高温空气喷口、绝热管道、换向阀等组成。
燃烧器喷口既是火焰入口又是烟气排出口。
蓄热室大多紧靠在燃烧器上,蓄热体材料的主要成分是氧化铝,一般采用直径为十几毫米的陶瓷球。
近来已发展采用蜂窝陶瓷体作为蓄热体,蜂窝陶瓷蓄热体比陶瓷球蓄热体具有更大的比表面,蓄热效率更高。
蓄热式燃烧器必须成对安装,两个为一组。
其中包括两个相同的燃烧器,两个蓄热器、一套换向阀门和配套控制系统。
如图1所示。
A烧嘴工作时,燃料和空气由A 烧嘴喷入,燃烧生成的火焰加热物料,高温烟气进入B烧嘴,并通过辐射、对流传热将热量传给蓄热体,烟气温度降低到200℃以下经过换向阀排出。
然后换向工作,冷空气通过B烧嘴的蓄热室后,已含热量的蓄热体再以对流换热为主的方式将空气预热至高温(一般空气预热温度与排烟入口温度仅差50~150 ℃),而使传热蓄热体被冷却。
换向阀一般以30~200s的频率进行切换,使两个蓄热体处于蓄热与放热交替工作状态,周而复始地运行。
蓄热式熔铝炉节能技术

蓄热式熔铝炉节能技术一、熔铝炉的能耗与节能国内铝加工行业熔铝炉使用传统的加热技术其能耗一般在75万大卡/吨铝左右;在国外,吨铝能耗一般低于55万大卡。
因此,国内的熔铝炉节能潜力还有很大的空间。
判断熔铝炉能耗高低以及是否节能,从两个方面来看,第一,熔化率,第二,炉子热效率。
熔化率是指单位时间单位熔池体积的熔化量(生产率),炉子升温速度越快,炉子熔池越大则炉子的熔化率越高,在一般情况下,炉子生产率越高,则熔化率的单位热量消耗就越低。
炉子热效率是铝被加热熔化时吸收的热量与供入炉内的热量之比。
为了降低能源消耗,应尽量提高炉子生产率,另一方面应充分回收利用出炉废气的余热。
同时对燃烧装置实行燃料与助燃空气的自动比例调节,以防止空气量过剩或不足。
减少炉体的蓄热和散热损失以及减少炉门开口等辐射热损失。
早期的(现在也有一部分)熔铝炉一般离炉烟气直接排放,烟气温度在750℃以上(图1)。
?图1 ?废热不利用的炉子为减少烟气带走的热量损失,人们在排烟管道上安装了热量回收装置即空气换热器,将助燃空气预热到一定的温度(200℃左右)后参与燃料的燃烧,但换热器后的排放温度还在500℃以上(图2)。
图2? 安装空气预热器的炉子采用蓄热式燃烧技术可以将烟气排放温度降低到150℃以下,助燃空气温度预热到700℃以上,这样就大大地减少了离炉烟气所带走的热量,使炉子热效率大幅度提高,燃料消耗大量减少,达到节能的目的(图3)。
图3 ?HTAC技术的工作原理图根据工业炉热工原理,助燃空气温度每升高100℃,能节省燃料约5%;或者烟气温度每降低100℃,能节省燃料约5.5%。
因此,采用蓄热式燃烧技术相对换热器回收装置可以节能25%以上。
二.熔炼炉概述:传统上有火焰炉、电阻炉、中频感应炉、反射炉以及坩埚炉等。
为了获得质量高又经济的铝合金溶液,各企业对熔炼设备的选择越来越重视,近几年来,火焰炉、电阻炉、中频感应炉、反射炉都有所改进。
熔炼炉结构的发展方向是:操作自动化、应用更新化、原料节能化等。
熔铝炉节能技术改造方案

熔铝炉节能技术改造方案广州好易燃能源科技有限公司1 概述铝及铝合金熔炼炉(简称熔铝炉)是铝加工熔铸行业最常用的设备,其熔炼过程也是铝加工行业能源及材料消耗最大的生产环节,熔化速率及吨铝能耗是熔铝炉两个最基本的能力指标,熔铝炉设计技术的实质就是要通过合理的结构设计,实现以最小的能源消耗获取最大的铝熔化速率,从而达到熔铝炉设备利用率、能源利用率、材料利用率最优化的目的。
广东省铝型材行业的熔铝炉大多是矩形炉,燃料种类大多是燃油和燃气,平均能耗在3200~4400MJ/吨铝,是型材行业的“煤老虎”。
我们对熔铝炉的使用状况进行了深入地了解和调研,组织技术人员进行攻关,对熔铝炉的工作运行方式和特点进行了准确的分析和论证,对炉型结构、炉衬材料及筑炉技术、燃烧器选型、生产过程全自动控制技术等都制定了自己独特的方案,对现在已经在用的熔铝炉的节能技术改造也确定了方案。
试图为新建企业的设备选型以及老企业的节能降耗做一份贡献。
2 熔铝炉运行特点与热工过程分析2.1 熔铝炉运行分析熔铝炉是典型的周期式高温熔炼设备,一般来说,从铝锭入炉到熔炼结束,大致可细分成以下几个阶段:装料期、熔化初期、熔化中期、熔化后期、升温期、精炼及保温期。
其相对应的炉温及能量分配模型见图1。
图1熔铝炉炉温及能量分配模型示意图2.2 熔铝炉内料堆熔化过程装料通常是在热炉下进行的,这时,烧嘴通常设在关闭或小火状态,随着冷炉料的加入,炉温下降很快,装料时间越长,炉温下降越多。
刚装入炉的铝锭在炉内呈料堆状态,随着温度上升,料堆表面的炉料开始熔化,熔融的铝液向下流动,当温度达到600℃左右时,支承料堆的强度消失,料堆下降并没入液面以下,炉内逐渐呈水平镜面。
图2为熔炼过程中炉料变化示意图。
图2熔炼过程中炉料变化示意图2.2.1 火焰冲击作用在料堆没入液面以前,火焰直接冲击到料堆上,由于强冲击作用,炉内对流传热效果占主导作用,热效率最高,炉料熔化最快,炉温上升缓慢。
蓄热式熔铝炉
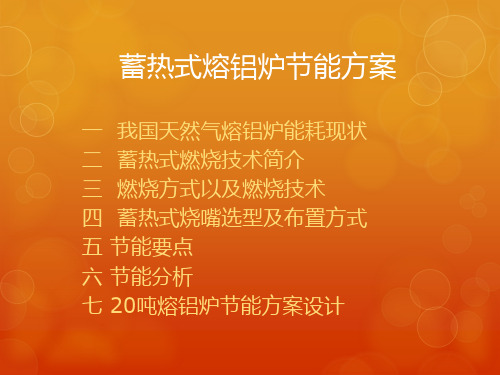
空气分级燃烧烧嘴结构示意图
一次空气系数α1
空气分级燃烧的一、二次空 气配比对燃烧室内NOx等污 染物排放有较大影响。从表 一可知,当一次空气占40% 左右时,燃烧室内可以更好 地形成很强的还原气氛,形 成低氧浓度区,并相应降低 了该燃烧区的温度,从而达 到抑制NOx生成的效果,此 时的NOx排放最少。
节能分析
利用烟气预热空气到900 ℃ 900 ℃空气比热为1.127KJ/(kg℃) 可以节省能量316065大卡,占可回收烟气热量约80%,采用蓄热技 术完全可行,
即节省折合约37m3天然气,
按80%效率可以节省约30m3天然气 即采用蓄热式烟气回收技术吨铝能耗可降至58m3
七 20吨熔铝炉节能设计方案
三对烧嘴,每对烧嘴80Nm3天然气,产生烟气量1016Nm3
每对烧嘴每分钟产生17Nm3烟气,约25670kj热量 即蓄热体需要蓄热量25670kj 蓄热陶瓷小球物性
比热容为1.1KJ/(kg℃)
密度2200kg/m3 价格约4元/kg 蓄热体温度200—950℃
需要蓄热陶瓷小球约31kg
体积约0.015m3 堆积体积约0.02m3 蓄热陶瓷小球
二 蓄热式燃烧技术简介
基本原理
技术形成
烧嘴和蓄热体成对出现, 助燃空气通过其中一个烧嘴, 被加热后供燃烧用,另一个 烧嘴充当排烟的角色,同时 蓄热体被加热。当到达换向 时刻时,换向阀动作使系统 反向运行,烟气加热好的蓄 热体被用来加热空气,助燃 空气冷却的蓄热体又被离开 炉子的高温烟气加热, 将高温空气喷射入炉 膛,维持低氧状态,同时将 燃料输送到气流中,产生燃 烧。空气温度预热到800℃ ~1000℃以上,燃烧区空气 含氧量在21%~2%,与传统燃 烧过程相比,高空气燃烧的 最大特点是节省燃料,减少 CO2和NOX的排放及降低燃烧 噪音,被誉为二十一世纪关 键技术之一。
熔铝炉的节能分析及烟气的余热利用

熔铝炉的节能分析及烟气的余热利用工业炉窑是我国工业耗能大户,对炉窑的节能掌握是国家关注的重点,也是企业降低成本的重要内容。
熔铝炉是主要工业炉窑之一,为了达到节能和减排的效果,近几年来蓄热式烧嘴系统成为熔铝炉常用配置,使熔炼炉节能技术向前迈进一步。
但我国熔铝炉熔炼过程中能耗与国外相比仍旧有较大差距,本文以23吨燃气熔铝炉为对象,通过对熔铝炉节能减排综合分析,初步探讨熔铝炉的节能减排措施;为使燃料燃烧热量充分利用,提出了一种中低温余热利用的装置和方法。
1、熔炼炉节能分析据统计,国内铝合金熔铸的综合能耗高于国外约8%~10%,产品的综合成品率却低约10%。
因此,提高铝合金熔炼过程的热效率,提高铸件质量和成品率,节省能源资源,已显得非常迫切和重要,这也是企业降本增效,增加企业竞争力的重要手段。
因此,有必要对铝合金熔炼炉的节能状况和节能途径进行分析,以查找节能方法和措施,提高熔炼炉的热效率。
下面,以XX公司23吨铝合金熔炼炉为例,分析影响铝合金熔炼炉节能效果的因素。
1.1烟气带走热量节能分析及措施熔铝炉的熔炼过程大致可分为4个阶段,即炉料装入到软化下榻;软化下榻至炉料化平;炉料化平到全部熔化;铝液温度持续上升。
对铝料的加热是通过烧嘴火焰的对流传热、火焰和炉墻的辐射传热以及铝料间的传导热来完成的。
整个过程中,三者之间比率不断变化,固态时铝的黑度小,导热力量强。
随着熔炼的进行,炉料进入半固态,导热力量下降,热力学性质发生了根本的变化。
液态铝的导热力量仅为固态铝的40%,熔池上部向底部的传导传热过程非常缓慢。
对于火焰反射炉来讲,在铝的熔化期,炉内温度一般掌握在1100℃-1200℃,此时的出炉烟气温度即为炉内气氛温度,经计算,烟气带走的热量约占炉子热负荷的60%左右,假如不充分利用这部分余热,将造成巨大的热能损失,同时带来四周环境的热污染和烟气污染。
因此,应充分利用热传导和烟气余热,削减排放烟气带走热量,实现熔铝炉的节能,详细措施可实行:1)采纳高速匀称化烧嘴,对炉料进行喷射加热,改善炉内空气循环,强化炉内传热;高速喷嘴使燃气获得充分燃烧,提高了燃烧值,削减了燃料的损失,提高了热效率。
蓄热式换热技术在熔铝炉上的应用

Ke wod rg n rt eh a x h n i tc n lg aunnu met g fra e a pi t n y r s ee eai ete c a gn eh oo y lriim v g li un c p l ai n c o
维普资讯
Vo .5 No 1 12 .
冶
金
能
源
3 5
J n. 0 6 a 20
ENERGY DR Ⅳ匝 TAI . GI、 F .I I. 瓜 (AL NDUS I 汀R Y
蓄 热 式换 热 技 术 在 熔 铝 炉 上 的应 用
张学湛 余 强
tc o o y i l mi i m etn u n c e hn l g n a u n u m li g f r a e
Z agX ehn Y a g h n uz a uQi n
( hn hi ar ni n n S ag aC deE v omet& Si c dT cnl yC .t) r c nea ehoo o Ld e n g
波动 ,因此需要在开停工时注意调节制冷机用汽 负荷 ,并对加热蒸汽采用可 自动调节用汽负荷的 自动控制技术 。 ()蒸汽喷射式热泵系统所提供的低压回收 2
蒸汽用于工厂建筑取暖比蒸汽并网和直接作为其
它工业用汽容易实现 ,但在供暖运行 中要及时发 现和处理加热器出现泄露时取暖蒸汽中夹带被加 热物料的现象 ,同时为确保暖汽压力安全要求 , 在热泵出口管上须安装蒸汽超压放散安全阀。 ()蒸汽喷射式热泵技术是投资和运行成本 3 低 、节能效果较好的实用节能技术 ,国家环境保
蓄热式熔铝炉节能技术
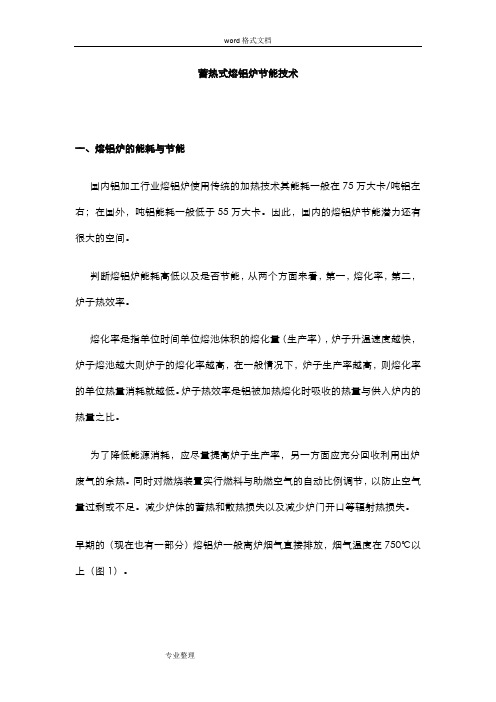
蓄热式熔铝炉节能技术一、熔铝炉的能耗与节能国内铝加工行业熔铝炉使用传统的加热技术其能耗一般在75万大卡/吨铝左右;在国外,吨铝能耗一般低于55万大卡。
因此,国内的熔铝炉节能潜力还有很大的空间。
判断熔铝炉能耗高低以及是否节能,从两个方面来看,第一,熔化率,第二,炉子热效率。
熔化率是指单位时间单位熔池体积的熔化量(生产率),炉子升温速度越快,炉子熔池越大则炉子的熔化率越高,在一般情况下,炉子生产率越高,则熔化率的单位热量消耗就越低。
炉子热效率是铝被加热熔化时吸收的热量与供入炉内的热量之比。
为了降低能源消耗,应尽量提高炉子生产率,另一方面应充分回收利用出炉废气的余热。
同时对燃烧装置实行燃料与助燃空气的自动比例调节,以防止空气量过剩或不足。
减少炉体的蓄热和散热损失以及减少炉门开口等辐射热损失。
早期的(现在也有一部分)熔铝炉一般离炉烟气直接排放,烟气温度在750℃以上(图1)。
图1 废热不利用的炉子为减少烟气带走的热量损失,人们在排烟管道上安装了热量回收装置即空气换热器,将助燃空气预热到一定的温度(200℃左右)后参与燃料的燃烧,但换热器后的排放温度还在500℃以上(图2)。
图2 安装空气预热器的炉子采用蓄热式燃烧技术可以将烟气排放温度降低到150℃以下,助燃空气温度预热到700℃以上,这样就大大地减少了离炉烟气所带走的热量,使炉子热效率大幅度提高,燃料消耗大量减少,达到节能的目的(图3)。
图3 HTAC技术的工作原理图根据工业炉热工原理,助燃空气温度每升高100℃,能节省燃料约5%;或者烟气温度每降低100℃,能节省燃料约5.5%。
因此,采用蓄热式燃烧技术相对换热器回收装置可以节能25%以上。
二.熔炼炉概述:传统上有火焰炉、电阻炉、中频感应炉、反射炉以及坩埚炉等。
为了获得质量高又经济的铝合金溶液,各企业对熔炼设备的选择越来越重视,近几年来,火焰炉、电阻炉、中频感应炉、反射炉都有所改进。
熔炼炉结构的发展方向是:操作自动化、应用更新化、原料节能化等。
铝熔炼炉蓄热式燃烧系统节能改造项目

电力(kWh) 193365 208950 210920 213540 213705 237765 287520 283770 256275 237360 162870 177390 2683430
时间 2016年6月 2016年7月 2016年8月 2016年9月 2016年10月 2016年11月 2016年12月
5.6
熔炉车间
4
5
打包机
SB-DBJ-01-02
/
熔炉车间
1
6
制氮机
SB-ZDJ-01
6.7
熔炉车间
1
7
回转炉
SB-HZL-01-02
11
炒灰车间
2
8
冷灰筒
SB-LHT-01
11
炒灰车间
1
9
直读光谱仪
ARL3460/OES
5.5
质检部
1
10 数显式液压万能试验机
WEW-100B
3
质检部
1
11
煤气炉
Φ3.2M
铝合金锭生产工艺的主要过程:将废铝料分选,进行 容量的反射炉改造为1台80t、2台40t、1台20t的反射炉,8台
冲洗除尘;根据不同的产品要求将各种不同成分的原材 20t容量的保温炉改造为1台40t、2台20t、1台10t的保温炉,
料经过计算按比例加入熔解炉中,经高温加热使其熔化 8台的HX-07(4t)的炒灰炉改造为4台HX-07(5t),将燃烧炉
为铝液,将熔解后的铝液转入合金炉,在合金炉中加入合 的高温尾气通过热交换器回用于助风机,提高了余热的利
金元素并对铝液进行除渣、除气处理,精炼后的铝液经成 用。改造前后的设备一览表如表2所示。
分、含渣、含气量及物理性能检测合格后,再浇铸为铝合金 锭。经检测合格后成品入库。
20吨蓄热式熔铝炉技术参数及设备报价
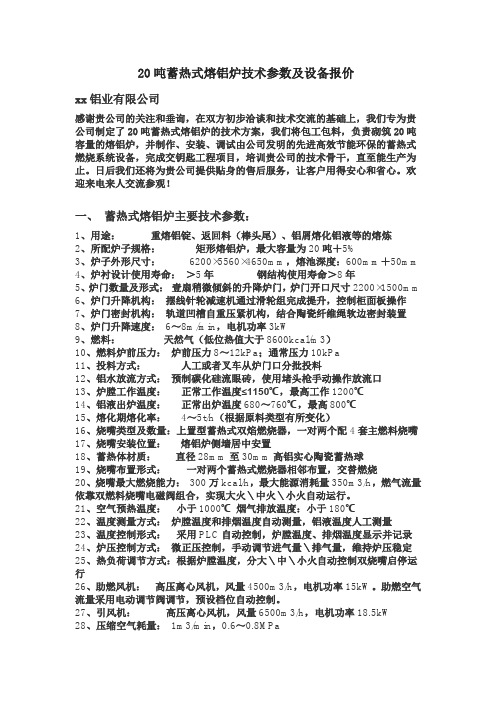
20吨蓄热式熔铝炉技术参数及设备报价xx铝业有限公司感谢贵公司的关注和垂询,在双方初步洽谈和技术交流的基础上,我们专为贵公司制定了20吨蓄热式熔铝炉的技术方案,我们将包工包料,负责砌筑20吨容量的熔铝炉,并制作、安装、调试由公司发明的先进高效节能环保的蓄热式燃烧系统设备,完成交钥匙工程项目,培训贵公司的技术骨干,直至能生产为止。
日后我们还将为贵公司提供贴身的售后服务,让客户用得安心和省心。
欢迎来电来人交流参观!一、蓄热式熔铝炉主要技术参数:1、用途:重熔铝锭、返回料(棒头尾)、铝屑熔化铝液等的熔炼2、所配炉子规格:矩形熔铝炉,最大容量为20吨+5%3、炉子外形尺寸:6200×5560×4650mm,熔池深度:600mm+50mm4、炉衬设计使用寿命:>5年钢结构使用寿命>8年5、炉门数量及形式:壹扇稍微倾斜的升降炉门,炉门开口尺寸2200×1500mm6、炉门升降机构:摆线针轮减速机通过滑轮组完成提升,控制柜面板操作7、炉门密封机构:轨道凹槽自重压紧机构,结合陶瓷纤维绳软边密封装置8、炉门升降速度:6~8m/min,电机功率3kW9、燃料:天然气(低位热值大于8600kcal/m3)10、燃料炉前压力:炉前压力8~12kPa;通常压力10kPa11、投料方式:人工或者叉车从炉门口分批投料12、铝水放流方式:预制碳化硅流眼砖,使用堵头枪手动操作放流口13、炉膛工作温度:正常工作温度≤1150℃,最高工作1200℃14、铝液出炉温度:正常出炉温度680~760℃,最高800℃15、熔化期熔化率:4~5t/h(根据原料类型有所变化)16、烧嘴类型及数量:上置型蓄热式双焰燃烧器,一对两个配4套主燃料烧嘴17、烧嘴安装位置:熔铝炉侧墙居中安置18、蓄热体材质:直径28mm至30mm高铝实心陶瓷蓄热球19、烧嘴布置形式:一对两个蓄热式燃烧器相邻布置,交替燃烧20、烧嘴最大燃烧能力:300万kcal/h,最大能源消耗量350m3/h,燃气流量依靠双燃料烧嘴电磁阀组合,实现大火\中火\小火自动运行。
蓄热式熔铝炉节能技术
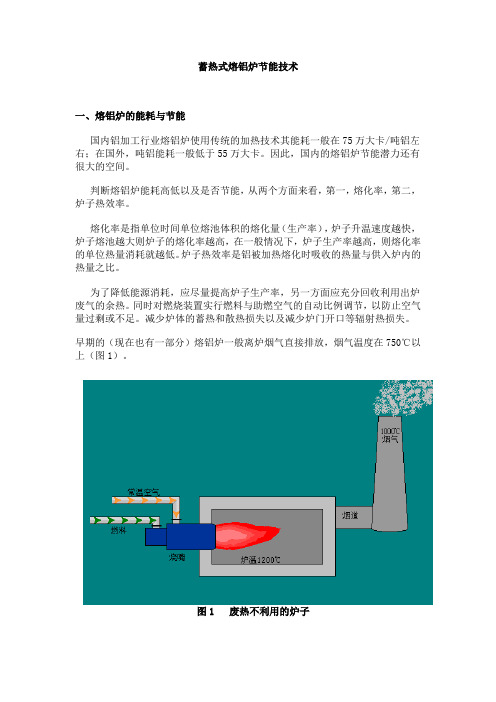
蓄热式熔铝炉节能技术一、熔铝炉的能耗与节能国内铝加工行业熔铝炉使用传统的加热技术其能耗一般在75万大卡/吨铝左右;在国外,吨铝能耗一般低于55万大卡。
因此,国内的熔铝炉节能潜力还有很大的空间。
判断熔铝炉能耗高低以及是否节能,从两个方面来看,第一,熔化率,第二,炉子热效率。
熔化率是指单位时间单位熔池体积的熔化量(生产率),炉子升温速度越快,炉子熔池越大则炉子的熔化率越高,在一般情况下,炉子生产率越高,则熔化率的单位热量消耗就越低。
炉子热效率是铝被加热熔化时吸收的热量与供入炉内的热量之比。
为了降低能源消耗,应尽量提高炉子生产率,另一方面应充分回收利用出炉废气的余热。
同时对燃烧装置实行燃料与助燃空气的自动比例调节,以防止空气量过剩或不足。
减少炉体的蓄热和散热损失以及减少炉门开口等辐射热损失。
早期的(现在也有一部分)熔铝炉一般离炉烟气直接排放,烟气温度在750℃以上(图1)。
图1 废热不利用的炉子为减少烟气带走的热量损失,人们在排烟管道上安装了热量回收装置即空气换热器,将助燃空气预热到一定的温度(200℃左右)后参与燃料的燃烧,但换热器后的排放温度还在500℃以上(图2)。
图2 安装空气预热器的炉子采用蓄热式燃烧技术可以将烟气排放温度降低到150℃以下,助燃空气温度预热到700℃以上,这样就大大地减少了离炉烟气所带走的热量,使炉子热效率大幅度提高,燃料消耗大量减少,达到节能的目的(图3)。
图3 HTAC技术的工作原理图根据工业炉热工原理,助燃空气温度每升高100℃,能节省燃料约5%;或者烟气温度每降低100℃,能节省燃料约5.5%。
因此,采用蓄热式燃烧技术相对换热器回收装置可以节能25%以上。
二.熔炼炉概述:传统上有火焰炉、电阻炉、中频感应炉、反射炉以及坩埚炉等。
为了获得质量高又经济的铝合金溶液,各企业对熔炼设备的选择越来越重视,近几年来,火焰炉、电阻炉、中频感应炉、反射炉都有所改进。
熔炼炉结构的发展方向是:操作自动化、应用更新化、原料节能化等。
蓄热式燃烧技术在熔铝炉使用过程中的优缺点
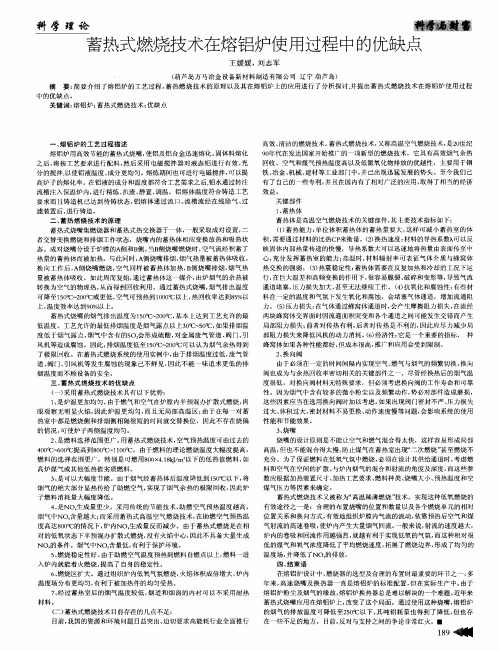
三、 蓄 热式燃烧技术 的优缺 点 ( 一) 采用蓄热式燃烧技术具有 以下优势: 1 、 是炉温 更加均匀 。 由于燃气 和空气在炉膛 内半预混办扩散式燃烧 , 肉 眼观察无 明显火焰 , 因此炉温更均 匀, 而且无局部高温 区; 由于在每 一对蓄 热室中部是燃烧侧和排烟侧相 隔很短 的时间就交替换位,因此不存在烧偏 的情况 , 可使炉子两侧温度均匀 。 2 、 是燃料选择范围更广 。 用蓄热式燃烧技术 , 空气预热温度可由过去的 4 0 0 q C - 6 0 0 R 2 提 高N8 o o  ̄ c  ̄ 1 1 0 0 K; 。由于燃料 的理论燃烧温度 大幅度提 高, 燃料 的选择 范 更J 、 ,特别 是可燃 用8 0 0 x 4 . 1 8 k J / m 以下的低热值燃料 , 如
效益。
之后 , 将按工艺要求进行配料 , 然 后 采 用 电 磁 搅 拌 器 对 液 态 铝进 行 有 效 、 充
分 的搅拌, 以使铝液温度 、 成分更均匀。熔炼期 间也可进行 电磁搅温度 都符合工艺需求之后, 铝水通过转注 流槽注入保温炉 内, 进 行精炼 、 扒渣、 静置、 调温 。铝熔体温度符合铸造工艺
低 温度 。 工 艺允 许 的最 低 排 烟 温 度 是 烟 气露 点 以上 3 0 q C  ̄ 5 0  ̄ G, 如 果 排 烟 温
关键部件 1 、 蓄 热 体 蓄热体是高温空气燃烧技术的关键 部件 , 其主要技术指标如下: ( 1 ) 蓄热能力: 单位体积蓄热体的蓄热量要大 , 这样 可减 小蓄热室的体 积, 需要通过材料的比热CP 来衡量。( 2 ) 换热速度 : 材料的导热系数 可以反 映固体 内部热量传递 的快慢 ,导热系数大可 以迅速地将热量 由表面传至 中 心, 充分发挥蓄热 室的能力 ; 高温 时, 材料辐射 率可表征气体介质与蜂窝体 热 交换 的强弱 。( 3 ) 热震稳定性: 蓄热 体需要在反复加热和冷 却的工况下运 行, 在 巨大温差和高频变换 的作用下, 很容 易脆裂、 破碎和变形等 , 导致气流 通道堵塞 , 压力损失加大, 甚至无法继续工作 。( 4 ) 抗氧化和腐蚀性 : 有些材 料在一 定的温度和气氛 F发生氧化和腐蚀,会堵塞气体通道,增加流通 阻 力。 ( 5 ) 压力损失: 在气体通过蜂窝体通道 时, 会产生摩擦阻力损 失, 在流经 两块蜂窝体交界面时因流通 面积突变和各个通道之 间可能发生交错而产 生 局部阻力损失; 前者对传 热有利, 后者对传 热是不利的 , 因此应尽力减少局 部阻力损 失来 降低风机的动 力消耗 。 ( 6 ) 经济性: 它是一个重要 的指标, 种 蜂窝体如果各种性能都好, 但成本很高, 推, 和应用会受到限制。
蓄热式燃烧技术在熔铝炉使用过程中的优缺点

蓄热式燃烧技术在熔铝炉使用过程中的优缺点作者:王媛媛刘志军来源:《科学与财富》2014年第01期摘要:简要介绍了熔铝炉的工艺过程,蓄热燃烧技术的原理以及其在熔铝炉上的应用进行了分析探讨,并提出蓄热式燃烧技术在熔铝炉使用过程中的优缺点。
关键词:熔铝炉;蓄热式燃烧技术;优缺点一、熔铝炉的工艺过程描述熔铝炉用高效节能的蓄热式烧嘴,使铝及铝合金迅速熔化。
固体料熔化之后,将按工艺要求进行配料,然后采用电磁搅拌器对液态铝进行有效、充分的搅拌,以使铝液温度、成分更均匀。
熔炼期间也可进行电磁搅拌,可以提高炉子的熔化率。
在铝液的成分和温度都符合工艺需求之后,铝水通过转注流槽注入保温炉内,进行精炼、扒渣、静置、调温。
铝熔体温度符合铸造工艺要求而且铸造机已达到待铸状态,铝熔体通过流口、流槽流经在线除气、过滤装置后,进行铸造。
二、蓄热燃烧技术的原理蓄热式烧嘴集燃烧器和蓄热式热交换器于一体,一般采取成对设置,二者交替变换燃烧和排烟工作状态,烧嘴内的蓄热体相应变换放热和吸热状态。
成对烧嘴分设于炉膛的A侧和B 侧,当B侧烧嘴燃烧时,空气流经积蓄了热量的蓄热体而被加热。
与此同时,A侧烧嘴排烟,烟气热量被蓄热体吸收。
换向工作后,A侧烧嘴燃烧,空气同样被蓄热体加热,B侧烧嘴排烟,烟气热量被蓄热体吸收。
如此周而复始,通过蓄热体这一媒介,出炉烟气的余热被转换为空气的物理热,从而得到回收利用。
通过蓄热式烧嘴,烟气排出温度可降至150℃~200℃或更低,空气可预热到1000℃以上,热回收率达到85%以上,温度效率达到90%以上。
蓄热式烧嘴的烟气排出温度为150℃~200℃,基本上达到工艺允许的最低温度。
工艺允许的最低排烟温度是烟气露点以上30℃~50℃,如果排烟温度低于烟气露点,烟气中含有的SO2会形成硫酸,对金属废气管道、阀门、引风机等造成腐蚀。
因此,排烟温度低至150℃~200℃可以认为烟气余热得到了极限回收。
在蓄热式燃烧系统的使用实例中,由于排烟温度过低,废气管道、阀门、引风机等发生腐蚀的现象已不鲜见,因此不能一味追求更低的排烟温度而不顾设备的安全。
熔铝炉节能技术改造方案

熔铝炉节能技术改造方案广州好易燃能源科技有限公司1 概述铝及铝合金熔炼炉(简称熔铝炉)是铝加工熔铸行业最常用的设备,其熔炼过程也是铝加工行业能源及材料消耗最大的生产环节,熔化速率及吨铝能耗是熔铝炉两个最基本的能力指标,熔铝炉设计技术的实质就是要通过合理的结构设计,实现以最小的能源消耗获取最大的铝熔化速率,从而达到熔铝炉设备利用率、能源利用率、材料利用率最优化的目的。
广东省铝型材行业的熔铝炉大多是矩形炉,燃料种类大多是燃油和燃气,平均能耗在3200~4400MJ/吨铝,是型材行业的“煤老虎”。
我们对熔铝炉的使用状况进行了深入地了解和调研,组织技术人员进行攻关,对熔铝炉的工作运行方式和特点进行了准确的分析和论证,对炉型结构、炉衬材料及筑炉技术、燃烧器选型、生产过程全自动控制技术等都制定了自己独特的方案,对现在已经在用的熔铝炉的节能技术改造也确定了方案。
试图为新建企业的设备选型以及老企业的节能降耗做一份贡献。
2 熔铝炉运行特点与热工过程分析2.1 熔铝炉运行分析熔铝炉是典型的周期式高温熔炼设备,一般来说,从铝锭入炉到熔炼结束,大致可细分成以下几个阶段:装料期、熔化初期、熔化中期、熔化后期、升温期、精炼及保温期。
其相对应的炉温及能量分配模型见图1。
图1熔铝炉炉温及能量分配模型示意图2.2 熔铝炉内料堆熔化过程装料通常是在热炉下进行的,这时,烧嘴通常设在关闭或小火状态,随着冷炉料的加入,炉温下降很快,装料时间越长,炉温下降越多。
刚装入炉的铝锭在炉内呈料堆状态,随着温度上升,料堆表面的炉料开始熔化,熔融的铝液向下流动,当温度达到600℃左右时,支承料堆的强度消失,料堆下降并没入液面以下,炉内逐渐呈水平镜面。
图2为熔炼过程中炉料变化示意图。
图2熔炼过程中炉料变化示意图2.2.1 火焰冲击作用在料堆没入液面以前,火焰直接冲击到料堆上,由于强冲击作用,炉内对流传热效果占主导作用,热效率最高,炉料熔化最快,炉温上升缓慢。
- 1、下载文档前请自行甄别文档内容的完整性,平台不提供额外的编辑、内容补充、找答案等附加服务。
- 2、"仅部分预览"的文档,不可在线预览部分如存在完整性等问题,可反馈申请退款(可完整预览的文档不适用该条件!)。
- 3、如文档侵犯您的权益,请联系客服反馈,我们会尽快为您处理(人工客服工作时间:9:00-18:30)。
蓄热式熔铝炉节能技术
一、熔铝炉的能耗与节能
国内铝加工行业熔铝炉使用传统的加热技术其能耗一般在75万大卡/吨铝左右;在国外,吨铝能耗一般低于55万大卡。
因此,国内的熔铝炉节能潜力还有很大的空间。
判断熔铝炉能耗高低以及是否节能,从两个方面来看,第一,熔化率,第二,炉子热效率。
熔化率是指单位时间单位熔池体积的熔化量(生产率),炉子升温速度越快,炉子熔池越大则炉子的熔化率越高,在一般情况下,炉子生产率越高,则熔化率的单位热量消耗就越低。
炉子热效率是铝被加热熔化时吸收的热量与供入炉内的热量之比。
为了降低能源消耗,应尽量提高炉子生产率,另一方面应充分回收利用出炉废气的余热。
同时对燃烧装置实行燃料与助燃空气的自动比例调节,以防止空气量过剩或不足。
减少炉体的蓄热和散热损失以及减少炉门开口等辐射热损失。
早期的(现在也有一部分)熔铝炉一般离炉烟气直接排放,烟气温度在750℃以上(图1)。
图1 废热不利用的炉子
为减少烟气带走的热量损失,人们在排烟管道上安装了热量回收装置即空气换热器,将助燃空气预热到一定的温度(200℃左右)后参与燃料的燃烧,但换热器后的排放温度还在500℃以上(图2)。
图2 安装空气预热器的炉子
采用蓄热式燃烧技术可以将烟气排放温度降低到150℃以下,助燃空气温度预热到700℃以上,这样就大大地减少了离炉烟气所带走的热量,使炉子热效率大幅度提高,燃料消耗大量减少,达到节能的目的(图3)。
图3 HTAC技术的工作原理图
根据工业炉热工原理,助燃空气温度每升高100℃,能节省燃料约5%;或者烟气温度每降低100℃,能节省燃料约5.5%。
因此,采用蓄热式燃烧技术相对换热器回收装置可以节能25%以上。
二.熔炼炉概述:
传统上有火焰炉、电阻炉、中频感应炉、反射炉以及坩埚炉等。
为了获得质量高又经济的铝合金溶液,各企业对熔炼设备的选择越来越重视,近几年来,火焰炉、电阻炉、中频感应炉、反射炉都有所改进。
熔炼炉结构的发展方向是:操作自动化、应用更新化、原料节能化等。
新型加热材料、新型耐火材料和新溶剂得到新的应用。
1、采用蓄热式烟气余热回收装置,交替切换空气和烟气,使之流经蓄热体,能
够最大程度上回收高温烟气热量,将助燃空气预热800度-1000度以上,其余热回收率可达85%以上。
2、合理组织燃烧工况,使炉内形成与传统火焰迥然不同的新型火焰型,创造出
炉内均匀的温度场分布。
3、通过空气与燃料气流的合理组织,交替使用,是燃料在低氧环境中进行燃烧,
消除炉内局部高温区。
三、蓄热式燃烧系统工作原理
蓄热式烧嘴成对布置,相对的两个烧嘴为一组(A、B烧嘴)。
从鼓风机出来的常温空气由换向阀切换进蓄热式烧嘴A后,在流过蓄热式烧嘴A陶瓷小球蓄热体时被加热,常温空气被加热到接近炉膛温度(一般为炉膛温度的80%~90%)。
被加热后的高温空气进入炉膛后,卷吸周围炉内的烟气形成一股含氧量大大低于21%的稀薄贫氧高温气流,贫氧高温空气与注入的燃料混合,实现燃料在贫氧状态下燃烧;与此同时,炉膛内的热烟气经过蓄热式烧嘴B排出,高温热烟气通过蓄热式烧嘴B时将显热储存在蓄热式烧嘴B内的蓄热体内,然后以低于150℃的低温烟气经过换向阀排出。
当蓄热体储存的热量达到饱和时进行换向,蓄热式烧
排嘴A和B变换燃烧和蓄热工作状态,如此周而复始,从而达到节能和降低NO
X
放量等目的。
蓄热式燃烧技术改变了传统的燃烧方式,主要表现为燃料与空气以适当速度
含量被稀释,从不同的喷嘴通道进入炉内,并卷吸炉内的燃烧产物,空气中的O
2
燃料在炉膛中高温(1 000℃以上)低氧浓度场(5%~6.5%)工况下燃烧,此种燃烧方式带来了许多优点:
(1)节能效果显著,比传统熔化炉平均节能25%以上
由于蓄热体“极限回收”了烟气中大部分的余热,并由参与燃烧的介质带回炉内,大大降低了炉子的热支出,所以采用蓄热式燃烧技术的炉子比传统熔化炉节能。
(2)消除了局部高温区,炉温分布均匀
燃料在高温低氧浓度工况下燃烧,在炉内形成没有明显火焰的弥漫燃烧,消除了火焰产生的局部高温区,火焰边界几乎扩大到整个炉膛,使炉温更加均匀。
蓄热式烧嘴工作状态频繁交换,使燃烧热点的位置及炉气流动方向频繁改变,强化了炉气对流,减小炉内死角,也使炉温更加均匀。
(3)提高加热质量
均匀的炉温使铝锭加热更均匀,降低了局部高温以及富氧环境对铝液的挥发和氧化作用。
(4)延长炉子耐火材料使用寿命
炉温均匀和消除局部高温区使耐火材料受热均匀,并保证耐火材料始终工作在合理的使用温度范围内。
(5)减少温室效应气体CO
2排放量及NO
X
生量
燃料节省25%,相应的CO
2
排放量也减少25%。
由于局部高温区的消除,有效的
降低了NO
X
的生成量。
四、蓄热体材料
蓄热体是蓄热式燃烧技术关键部分,它要求蓄热体具有蓄热量大、换热速度好、高温强度好、阻力损失小、抗氧化抗渣性强,而且经济耐用。
陶瓷球的原理就是在蓄热室内填冲直径相同的许多陶瓷实心球,堆积呈固定床,球径一般在15-25mm之间。
陶瓷球蓄热体比表面积240m2/m3,众多的小球将气流分割成很小流股,气流在蓄热体中流过时,形成强烈紊流,有效地冲破了蓄热体表面的附面层,又由于球径很小,传热半径小,热阻小,密度高,导热性强,加之换向系统设计独特,故可实现频繁且快速的换向,固此,蓄热体可利用30次/H,高温烟气流经蓄热体床层后便可将烟气降至150℃排放。
常温空气流径蓄热体在相同路径内即可预热至反比烟气温度低50℃,温度效率高达95%以上。
另外,因为蓄热体体积十分小巧,加之小球床的流通能力强,即使积灰的阻力增加也不影响换热指标,陶瓷小球的更换,清洗非常方便,并可重复利用。
蓄热体材质陶瓷材料
形状球形
蓄热体体积 3m3
换向时间 120秒
空气预热温度 1000℃
高温烟气温度 1050℃
排烟温度≤150℃
材料比表面积(m2/m3) 240
球径 25mm
热回收率约70%-80%
五、应用案例
下面以燃油、燃气蓄热式熔铝炉为案例,对采用某公司单蓄热(空气)技术及专利设备(换向阀)等应用节能效果做比较和分析。
1.某铝厂熔化车间——新建项目
熔化材料:铝坯及再生铝材
炉子形式:矩形固定式
炉子容量:30T 炉膛工作温度:< 1 100℃
铝液温度:720℃~830℃熔体温差:≤±5℃
熔化期熔化率:5.2t/h
熔池面积:5.05×4.5=22.7m2
熔池深度:650mm
熔化期吨铝消耗:≤62 m3/吨铝
铝坯入炉温度:常温
燃料:天然气
发热值:8 500 kcal/Nm3
排烟温度:<150℃
蓄热材料:陶瓷小球
烧嘴型式:含点火及常明式蓄热式烧嘴
2.某铝业有限公司——改造项目
改造前:为常规的烧嘴技术,即采用机械式雾化油枪技术,熔化率为3.5吨,吨铝耗油76千克。
经过改造后的熔化率达到5吨,熔铝热耗53千克,平均节油率30%。
相关参数如下:
熔化材料:30%铝及铝合金锭、废料+70%电解铝液
炉子形式:矩形固定式、一扇组合大炉门、机械扒渣
炉子容量:25T
炉膛工作温度: < 1 100℃
铝液温度:730℃~860℃
熔化期熔化率:5t/h
熔池面积:5×4=20 m2
熔化期吨铝消耗:~53公斤/吨铝
熔料入炉温度:常温
燃料:0#轻柴油
发热值:10 200 kcal/kg
排烟温度:<150℃
六、总论:
从热平衡角度来说,采用蓄热式换热技术的熔化炉燃料节约率与炉子砌体的蓄热量、炉体的表面散热损失有关。
因为烧嘴是通过烟气回收余热的,炉体的蓄热量减小,表面散热损失越少,则排烟余热量越大,燃料节约率就越高。
同时,由于熔铝炉间歇性工作特点,在不同工作状态时炉温、蓄热体中空气流速、烟气出口温度有较大波动。
这样烧嘴换向时间也应随工作状态变化而变化,优化蓄热体的利用率,使余热回收达到更好的效果。
由于空气通过蓄热体后温度升高,带进炉内大量显热,使得燃料的理论燃烧温度显著提高。
在采用相同的炉型和燃料时,蓄热炉比常规炉有更高的综合加热温度和更快的加热速度。
采用蓄热式换热技术,带来的直接经济效益主要是节省燃料。
由于消除局部高温区,炉温分布均匀,使耐火材料使用寿命延长,同时提高了加热质量,减少了氧化烧损。
由这些因素带来的经济效益也是相当可观的。
从环境保护角度来说,燃料节省25%,烟气中CO
2
等温室气体总量也相应减少了
25%。
同时由于燃料在高温空气贫氧环境下,降低了NO
X
的产生。
总之,蓄热技
术应用到熔铝炉上,起到了很好的节能效果;也降低了CO
2和NO
X
的排放,减轻
环境污染。
同时,蓄热技术还有待进一步研究,达到更好的节能、环保效果。
蓄热式熔铝炉【节能技术】
河南鑫源铝业经销部。