蓄热式熔铝炉
蓄热式熔铝炉资料
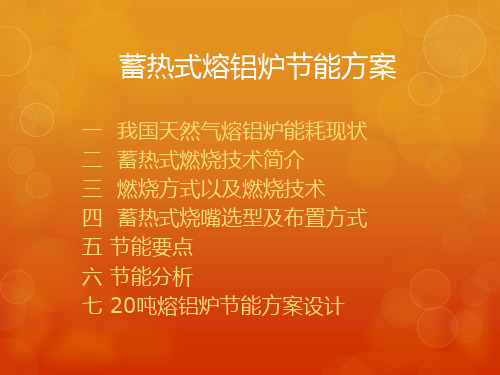
六 节能分析
我国天然气熔铝炉吨铝能耗75万大卡,折合天然气约88Nm3 , 过量空气系数1.17 需要空气量1030Nm3 产生烟气量1118Nm3 烟气温度1000℃ 烟气成分如图,1000℃烟气比热为1.51KJ/(m3℃) 空气平均温度22℃,比热为1.013KJ/(kg℃) 标况下空气密度1.293kg/m3 烟气带走热量约396680大卡
燃烧技术分类
二 燃气分级燃烧技术
没有定型的火焰,火焰无法控制,燃烧性能差, 燃气喷嘴易烧毁,辐射性能差,加热质量低。
二段式低NOx燃烧器
二段式低NOx燃烧器 该燃烧器的工作原理如图1所 示,是将燃烧用的空气分2次通 入燃烧区,从而使燃烧过程分两 个阶段完成,避免高温区过分集 中。二次空气是从还原区外围送 入的,在火焰尾部完成完全燃 烧。由于实行分段燃烧,避免了 高温区集中, 因而NOx的排放 浓度显著降低。
二 蓄热式燃烧技术简介
基本原理
烧嘴和蓄热体成对出现, 助燃空气通过其中一个烧嘴, 被加热后供燃烧用,另一个 烧嘴充当排烟的角色,同时 蓄热体被加热。当到达换向 时刻时,换向阀动作使系统 反向运行,烟气加热好的蓄 热体被用来加热空气,助燃 空气冷却的蓄热体又被离开 炉子的高温烟气加热,
技术形成
将高温空气喷射入炉 膛,维持低氧状态,同时将 燃料输送到气流中,产生燃 烧。空气温度预热到800℃ ~1000℃以上,燃烧区空气 含氧量在21%~2%,与传统燃 烧过程相比,高空气燃烧的 最大特点是节省燃料,减少 CO2和NOX的排放及降低燃烧 噪音,被誉为二十一世纪关 键技术之一。
蓄热式燃烧系统工作原理
三 燃烧方式分类
1扩散式燃烧 2部分预混式燃烧 3预混式燃烧
1扩散式燃烧
2部分预混式燃烧 3预混式燃烧
20吨蓄热式熔铝炉技术参数及设备报价
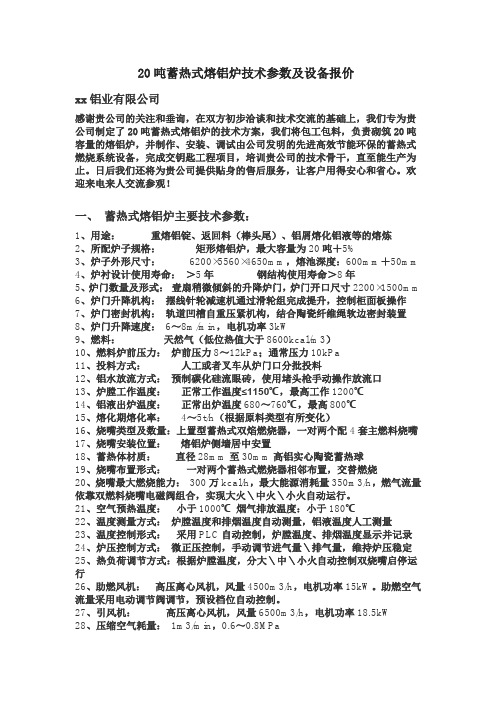
20吨蓄热式熔铝炉技术参数及设备报价xx铝业有限公司感谢贵公司的关注和垂询,在双方初步洽谈和技术交流的基础上,我们专为贵公司制定了20吨蓄热式熔铝炉的技术方案,我们将包工包料,负责砌筑20吨容量的熔铝炉,并制作、安装、调试由公司发明的先进高效节能环保的蓄热式燃烧系统设备,完成交钥匙工程项目,培训贵公司的技术骨干,直至能生产为止。
日后我们还将为贵公司提供贴身的售后服务,让客户用得安心和省心。
欢迎来电来人交流参观!一、蓄热式熔铝炉主要技术参数:1、用途:重熔铝锭、返回料(棒头尾)、铝屑熔化铝液等的熔炼2、所配炉子规格:矩形熔铝炉,最大容量为20吨+5%3、炉子外形尺寸:6200×5560×4650mm,熔池深度:600mm+50mm4、炉衬设计使用寿命:>5年钢结构使用寿命>8年5、炉门数量及形式:壹扇稍微倾斜的升降炉门,炉门开口尺寸2200×1500mm6、炉门升降机构:摆线针轮减速机通过滑轮组完成提升,控制柜面板操作7、炉门密封机构:轨道凹槽自重压紧机构,结合陶瓷纤维绳软边密封装置8、炉门升降速度:6~8m/min,电机功率3kW9、燃料:天然气(低位热值大于8600kcal/m3)10、燃料炉前压力:炉前压力8~12kPa;通常压力10kPa11、投料方式:人工或者叉车从炉门口分批投料12、铝水放流方式:预制碳化硅流眼砖,使用堵头枪手动操作放流口13、炉膛工作温度:正常工作温度≤1150℃,最高工作1200℃14、铝液出炉温度:正常出炉温度680~760℃,最高800℃15、熔化期熔化率:4~5t/h(根据原料类型有所变化)16、烧嘴类型及数量:上置型蓄热式双焰燃烧器,一对两个配4套主燃料烧嘴17、烧嘴安装位置:熔铝炉侧墙居中安置18、蓄热体材质:直径28mm至30mm高铝实心陶瓷蓄热球19、烧嘴布置形式:一对两个蓄热式燃烧器相邻布置,交替燃烧20、烧嘴最大燃烧能力:300万kcal/h,最大能源消耗量350m3/h,燃气流量依靠双燃料烧嘴电磁阀组合,实现大火\中火\小火自动运行。
蓄热式熔铝炉节能技术
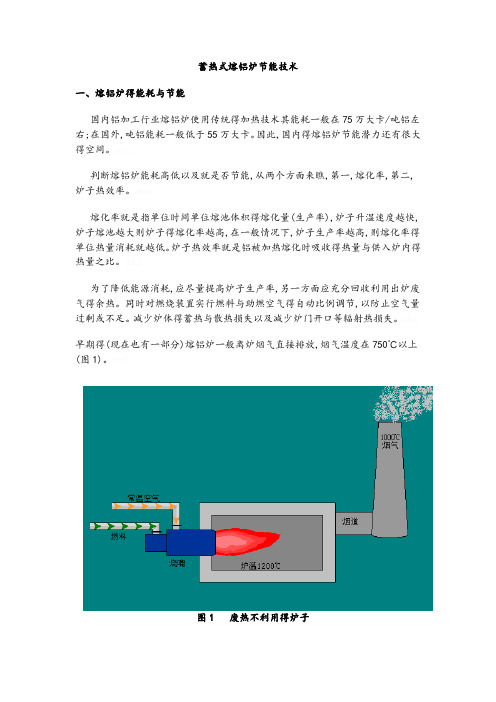
蓄热式熔铝炉节能技术一、熔铝炉得能耗与节能国内铝加工行业熔铝炉使用传统得加热技术其能耗一般在75万大卡/吨铝左右;在国外,吨铝能耗一般低于55万大卡。
因此,国内得熔铝炉节能潜力还有很大得空间。
判断熔铝炉能耗高低以及就是否节能,从两个方面来瞧,第一,熔化率,第二,炉子热效率。
熔化率就是指单位时间单位熔池体积得熔化量(生产率),炉子升温速度越快,炉子熔池越大则炉子得熔化率越高,在一般情况下,炉子生产率越高,则熔化率得单位热量消耗就越低。
炉子热效率就是铝被加热熔化时吸收得热量与供入炉内得热量之比。
为了降低能源消耗,应尽量提高炉子生产率,另一方面应充分回收利用出炉废气得余热。
同时对燃烧装置实行燃料与助燃空气得自动比例调节,以防止空气量过剩或不足。
减少炉体得蓄热与散热损失以及减少炉门开口等辐射热损失。
早期得(现在也有一部分)熔铝炉一般离炉烟气直接排放,烟气温度在750℃以上(图1)。
图1 废热不利用得炉子为减少烟气带走得热量损失,人们在排烟管道上安装了热量回收装置即空气换热器,将助燃空气预热到一定得温度(200℃左右)后参与燃料得燃烧,但换热器后得排放温度还在500℃以上(图2)。
图2 安装空气预热器得炉子采用蓄热式燃烧技术可以将烟气排放温度降低到150℃以下,助燃空气温度预热到700℃以上,这样就大大地减少了离炉烟气所带走得热量,使炉子热效率大幅度提高,燃料消耗大量减少,达到节能得目得(图3)。
图3 HTAC技术得工作原理图根据工业炉热工原理,助燃空气温度每升高100℃,能节省燃料约5%;或者烟气温度每降低100℃,能节省燃料约5、5%。
因此,采用蓄热式燃烧技术相对换热器回收装置可以节能25%以上。
二、熔炼炉概述:传统上有火焰炉、电阻炉、中频感应炉、反射炉以及坩埚炉等。
为了获得质量高又经济得铝合金溶液,各企业对熔炼设备得选择越来越重视,近几年来,火焰炉、电阻炉、中频感应炉、反射炉都有所改进。
熔炼炉结构得发展方向就是:操作自动化、应用更新化、原料节能化等。
蓄热式熔铝炉节能技术
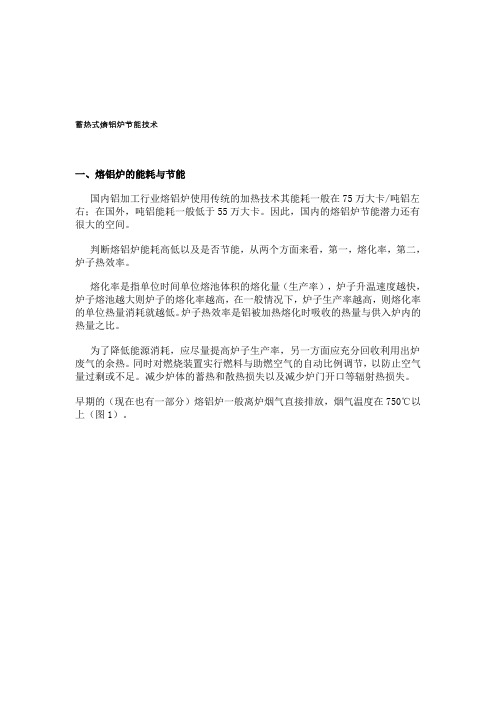
蓄热式熔铝炉节能技术一、熔铝炉的能耗与节能国内铝加工行业熔铝炉使用传统的加热技术其能耗一般在75万大卡/吨铝左右;在国外,吨铝能耗一般低于55万大卡。
因此,国内的熔铝炉节能潜力还有很大的空间。
判断熔铝炉能耗高低以及是否节能,从两个方面来看,第一,熔化率,第二,炉子热效率。
熔化率是指单位时间单位熔池体积的熔化量(生产率),炉子升温速度越快,炉子熔池越大则炉子的熔化率越高,在一般情况下,炉子生产率越高,则熔化率的单位热量消耗就越低。
炉子热效率是铝被加热熔化时吸收的热量与供入炉内的热量之比。
为了降低能源消耗,应尽量提高炉子生产率,另一方面应充分回收利用出炉废气的余热。
同时对燃烧装置实行燃料与助燃空气的自动比例调节,以防止空气量过剩或不足。
减少炉体的蓄热和散热损失以及减少炉门开口等辐射热损失。
早期的(现在也有一部分)熔铝炉一般离炉烟气直接排放,烟气温度在750℃以上(图1)。
图1 废热不利用的炉子为减少烟气带走的热量损失,人们在排烟管道上安装了热量回收装置即空气换热器,将助燃空气预热到一定的温度(200℃左右)后参与燃料的燃烧,但换热器后的排放温度还在500℃以上(图2)。
图2 安装空气预热器的炉子采用蓄热式燃烧技术可以将烟气排放温度降低到150℃以下,助燃空气温度预热到700℃以上,这样就大大地减少了离炉烟气所带走的热量,使炉子热效率大幅度提高,燃料消耗大量减少,达到节能的目的(图3)。
图3 HTAC技术的工作原理图根据工业炉热工原理,助燃空气温度每升高100℃,能节省燃料约5%;或者烟气温度每降低100℃,能节省燃料约5.5%。
因此,采用蓄热式燃烧技术相对换热器回收装置可以节能25%以上。
二.熔炼炉概述:传统上有火焰炉、电阻炉、中频感应炉、反射炉以及坩埚炉等。
为了获得质量高又经济的铝合金溶液,各企业对熔炼设备的选择越来越重视,近几年来,火焰炉、电阻炉、中频感应炉、反射炉都有所改进。
熔炼炉结构的发展方向是:操作自动化、应用更新化、原料节能化等。
蓄热式燃烧技术在熔铝炉上的应用
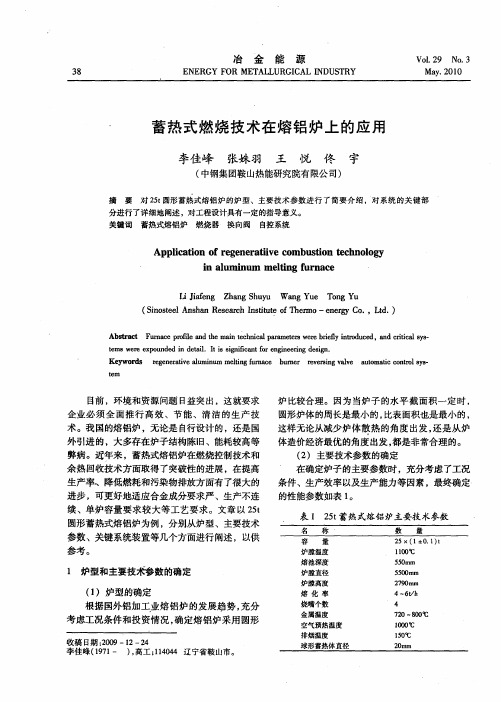
外引进 的,大多存在炉子结构陈旧、能耗较高等 弊病。近年来 ,蓄热式熔铝炉在燃烧控制技术和 余热回收技术方面取得了突破性的进展 ,在提高 生产率、降低燃耗和污染物排放方面有了很大的 进步 ,可更好地适应合金成分要求严、生产不连 续、单炉容量要求较大等工艺要求。文章 以 2t 5 圆形蓄 热式熔 铝炉 为例 ,分别从 炉型 、主要技术 参数、关键系统装置等几个方面进行阐述 ,以供 参考 。
余仍 以扩 散燃 烧 的方 式进人 炉 内反应放 热 ,也使 火焰 具有 足够 的长 度 ,满 足炉体 半径方 向对温 度 场均 匀性 的要 求 。 由于铝 的 黑 度 很 小 ,吸 收 辐 射 热 的 能 力较 低 ,所 以提高热 效率 降低 能耗 的主要途径 是改变
容
量
2 5×( 0 1 t 1± . )
I00 1 ℃
5 0mm 5 5 0o 5 mm
29 7 0mm
炉 膛温 度
1 炉型和主要技术参数的确定
( ) 炉型 的确定 1
熔 池深度 炉膛直径
炉膛高度 熔 化 率
4—6th , /
4
根据国外铝加工业熔铝炉的发展趋势 , 充分 考虑工况条件和投资情况 , 确定熔铝炉采用 圆形
冶
金
能
源
3 9
ENERGY OR F METALLURGI CAL I NDUS TRY
2 关 键 系统
可 以看 出 ,阻力损 失与蓄 热室 高度之 比,随 球径 的增加 而减小 ,与空 塔流 速成幂 函数关 系 。 综合热 交换 系数 是设计 蓄 热室 的另一重 要参 数 ,也 是 反 映蓄 热 室 中冷 热 气 体 之 间 ( 过 蓄 通
天然气蓄热式熔炼炉_高效节能的好炉子_黄向阳
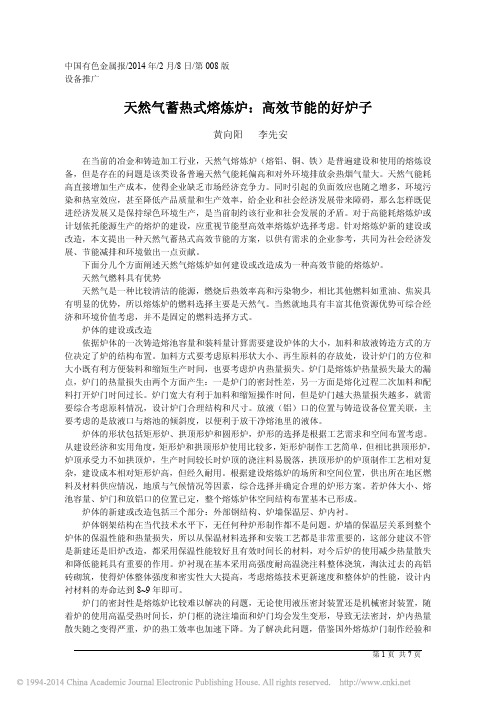
中国有色金属报/2014年/2月/8日/第008版设备推广天然气蓄热式熔炼炉:高效节能的好炉子黄向阳李先安在当前的冶金和铸造加工行业,天然气熔炼炉(熔铝、铜、铁)是普遍建设和使用的熔炼设备,但是存在的问题是该类设备普遍天然气能耗偏高和对外环境排放余热烟气量大。
天然气能耗高直接增加生产成本,使得企业缺乏市场经济竞争力。
同时引起的负面效应也随之增多,环境污染和热室效应,甚至降低产品质量和生产效率,给企业和社会经济发展带来障碍,那么怎样既促进经济发展又是保持绿色环境生产,是当前制约该行业和社会发展的矛盾。
对于高能耗熔炼炉或计划依托能源生产的熔炉的建设,应重视节能型高效率熔炼炉选择考虑。
针对熔炼炉新的建设或改造,本文提出一种天然气蓄热式高效节能的方案,以供有需求的企业参考,共同为社会经济发展、节能减排和环境做出一点贡献。
下面分几个方面阐述天然气熔炼炉如何建设或改造成为一种高效节能的熔炼炉。
天然气燃料具有优势天然气是一种比较清洁的能源,燃烧后热效率高和污染物少,相比其他燃料如重油、焦炭具有明显的优势,所以熔炼炉的燃料选择主要是天然气。
当然就地具有丰富其他资源优势可综合经济和环境价值考虑,并不是固定的燃料选择方式。
炉体的建设或改造依据炉体的一次铸造熔池容量和装料量计算需要建设炉体的大小,加料和放液铸造方式的方位决定了炉的结构布置。
加料方式要考虑原料形状大小、再生原料的存放处,设计炉门的方位和大小既有利方便装料和缩短生产时间,也要考虑炉内热量损失。
炉门是熔炼炉热量损失最大的漏点,炉门的热量损失由两个方面产生:一是炉门的密封性差,另一方面是熔化过程二次加料和配料打开炉门时间过长。
炉门宽大有利于加料和缩短操作时间,但是炉门越大热量损失越多,就需要综合考虑原料情况,设计炉门合理结构和尺寸。
放液(铝)口的位置与铸造设备位置关联,主要考虑的是放液口与熔池的倾斜度,以便利于放干净熔池里的液体。
炉体的形状包括矩形炉、拱顶形炉和圆形炉,炉形的选择是根据工艺需求和空间布置考虑。
蓄热式双室熔铝炉工作原理
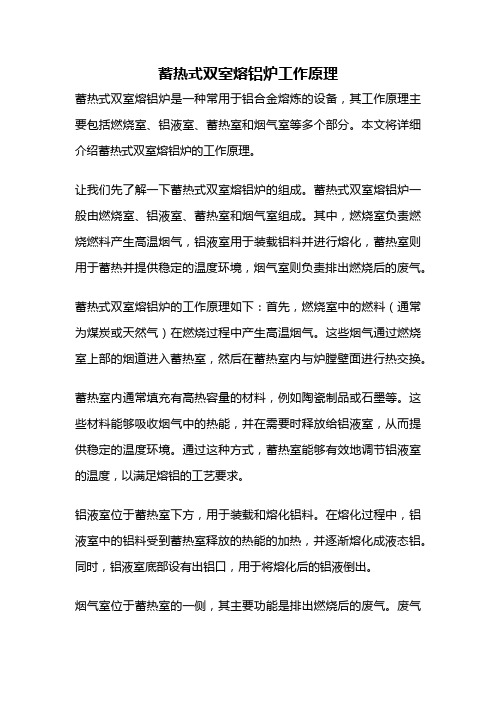
蓄热式双室熔铝炉工作原理蓄热式双室熔铝炉是一种常用于铝合金熔炼的设备,其工作原理主要包括燃烧室、铝液室、蓄热室和烟气室等多个部分。
本文将详细介绍蓄热式双室熔铝炉的工作原理。
让我们先了解一下蓄热式双室熔铝炉的组成。
蓄热式双室熔铝炉一般由燃烧室、铝液室、蓄热室和烟气室组成。
其中,燃烧室负责燃烧燃料产生高温烟气,铝液室用于装载铝料并进行熔化,蓄热室则用于蓄热并提供稳定的温度环境,烟气室则负责排出燃烧后的废气。
蓄热式双室熔铝炉的工作原理如下:首先,燃烧室中的燃料(通常为煤炭或天然气)在燃烧过程中产生高温烟气。
这些烟气通过燃烧室上部的烟道进入蓄热室,然后在蓄热室内与炉膛壁面进行热交换。
蓄热室内通常填充有高热容量的材料,例如陶瓷制品或石墨等。
这些材料能够吸收烟气中的热能,并在需要时释放给铝液室,从而提供稳定的温度环境。
通过这种方式,蓄热室能够有效地调节铝液室的温度,以满足熔铝的工艺要求。
铝液室位于蓄热室下方,用于装载和熔化铝料。
在熔化过程中,铝液室中的铝料受到蓄热室释放的热能的加热,并逐渐熔化成液态铝。
同时,铝液室底部设有出铝口,用于将熔化后的铝液倒出。
烟气室位于蓄热室的一侧,其主要功能是排出燃烧后的废气。
废气中含有大量的烟尘和有害气体,因此需要通过烟气室中设立的烟囱或排气管道进行排放,以确保环境的清洁与安全。
蓄热式双室熔铝炉通过合理的热能传递和储存方式,实现了铝液室温度的稳定控制和烟气的净化处理。
其工作原理简单而高效,能够满足铝合金熔炼过程中对温度和环境的要求。
蓄热式双室熔铝炉通过燃烧室、铝液室、蓄热室和烟气室等部分的协同工作,实现了铝合金熔炼过程中的温度控制和废气处理。
其工作原理简洁而高效,为铝工业的发展提供了可靠的技术支持。
蓄热式熔铝炉节能技术
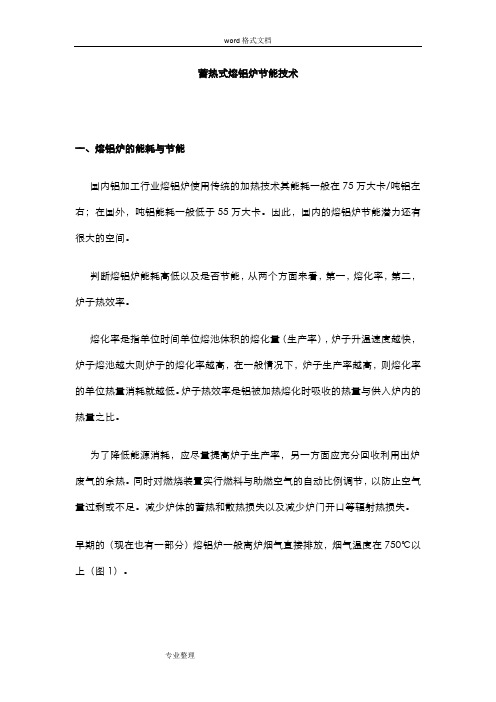
蓄热式熔铝炉节能技术一、熔铝炉的能耗与节能国内铝加工行业熔铝炉使用传统的加热技术其能耗一般在75万大卡/吨铝左右;在国外,吨铝能耗一般低于55万大卡。
因此,国内的熔铝炉节能潜力还有很大的空间。
判断熔铝炉能耗高低以及是否节能,从两个方面来看,第一,熔化率,第二,炉子热效率。
熔化率是指单位时间单位熔池体积的熔化量(生产率),炉子升温速度越快,炉子熔池越大则炉子的熔化率越高,在一般情况下,炉子生产率越高,则熔化率的单位热量消耗就越低。
炉子热效率是铝被加热熔化时吸收的热量与供入炉内的热量之比。
为了降低能源消耗,应尽量提高炉子生产率,另一方面应充分回收利用出炉废气的余热。
同时对燃烧装置实行燃料与助燃空气的自动比例调节,以防止空气量过剩或不足。
减少炉体的蓄热和散热损失以及减少炉门开口等辐射热损失。
早期的(现在也有一部分)熔铝炉一般离炉烟气直接排放,烟气温度在750℃以上(图1)。
图1 废热不利用的炉子为减少烟气带走的热量损失,人们在排烟管道上安装了热量回收装置即空气换热器,将助燃空气预热到一定的温度(200℃左右)后参与燃料的燃烧,但换热器后的排放温度还在500℃以上(图2)。
图2 安装空气预热器的炉子采用蓄热式燃烧技术可以将烟气排放温度降低到150℃以下,助燃空气温度预热到700℃以上,这样就大大地减少了离炉烟气所带走的热量,使炉子热效率大幅度提高,燃料消耗大量减少,达到节能的目的(图3)。
图3 HTAC技术的工作原理图根据工业炉热工原理,助燃空气温度每升高100℃,能节省燃料约5%;或者烟气温度每降低100℃,能节省燃料约5.5%。
因此,采用蓄热式燃烧技术相对换热器回收装置可以节能25%以上。
二.熔炼炉概述:传统上有火焰炉、电阻炉、中频感应炉、反射炉以及坩埚炉等。
为了获得质量高又经济的铝合金溶液,各企业对熔炼设备的选择越来越重视,近几年来,火焰炉、电阻炉、中频感应炉、反射炉都有所改进。
熔炼炉结构的发展方向是:操作自动化、应用更新化、原料节能化等。
20吨蓄热式熔铝炉技术参数及设备报价
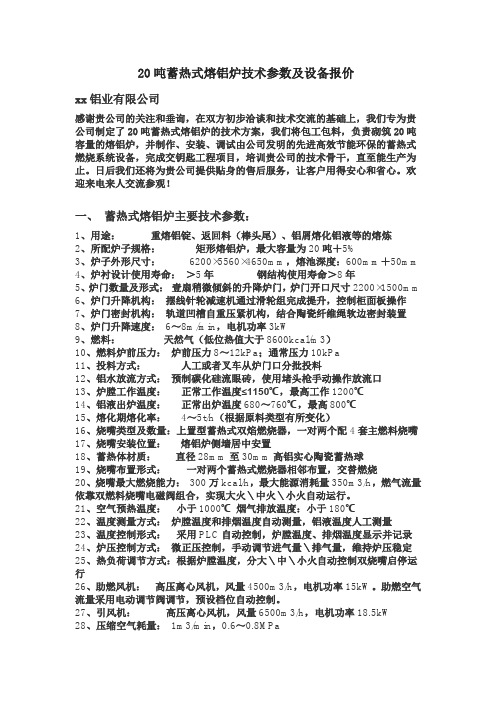
20吨蓄热式熔铝炉技术参数及设备报价xx铝业有限公司感谢贵公司的关注和垂询,在双方初步洽谈和技术交流的基础上,我们专为贵公司制定了20吨蓄热式熔铝炉的技术方案,我们将包工包料,负责砌筑20吨容量的熔铝炉,并制作、安装、调试由公司发明的先进高效节能环保的蓄热式燃烧系统设备,完成交钥匙工程项目,培训贵公司的技术骨干,直至能生产为止。
日后我们还将为贵公司提供贴身的售后服务,让客户用得安心和省心。
欢迎来电来人交流参观!一、蓄热式熔铝炉主要技术参数:1、用途:重熔铝锭、返回料(棒头尾)、铝屑熔化铝液等的熔炼2、所配炉子规格:矩形熔铝炉,最大容量为20吨+5%3、炉子外形尺寸:6200×5560×4650mm,熔池深度:600mm+50mm4、炉衬设计使用寿命:>5年钢结构使用寿命>8年5、炉门数量及形式:壹扇稍微倾斜的升降炉门,炉门开口尺寸2200×1500mm6、炉门升降机构:摆线针轮减速机通过滑轮组完成提升,控制柜面板操作7、炉门密封机构:轨道凹槽自重压紧机构,结合陶瓷纤维绳软边密封装置8、炉门升降速度:6~8m/min,电机功率3kW9、燃料:天然气(低位热值大于8600kcal/m3)10、燃料炉前压力:炉前压力8~12kPa;通常压力10kPa11、投料方式:人工或者叉车从炉门口分批投料12、铝水放流方式:预制碳化硅流眼砖,使用堵头枪手动操作放流口13、炉膛工作温度:正常工作温度≤1150℃,最高工作1200℃14、铝液出炉温度:正常出炉温度680~760℃,最高800℃15、熔化期熔化率:4~5t/h(根据原料类型有所变化)16、烧嘴类型及数量:上置型蓄热式双焰燃烧器,一对两个配4套主燃料烧嘴17、烧嘴安装位置:熔铝炉侧墙居中安置18、蓄热体材质:直径28mm至30mm高铝实心陶瓷蓄热球19、烧嘴布置形式:一对两个蓄热式燃烧器相邻布置,交替燃烧20、烧嘴最大燃烧能力:300万kcal/h,最大能源消耗量350m3/h,燃气流量依靠双燃料烧嘴电磁阀组合,实现大火\中火\小火自动运行。
20吨蓄热式熔铝炉技术参数及设备报价
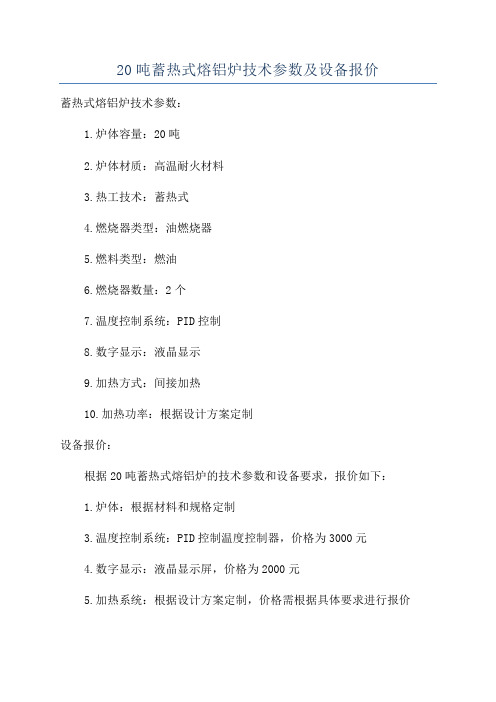
20吨蓄热式熔铝炉技术参数及设备报价
蓄热式熔铝炉技术参数:
1.炉体容量:20吨
2.炉体材质:高温耐火材料
3.热工技术:蓄热式
4.燃烧器类型:油燃烧器
5.燃料类型:燃油
6.燃烧器数量:2个
7.温度控制系统:PID控制
8.数字显示:液晶显示
9.加热方式:间接加热
10.加热功率:根据设计方案定制
设备报价:
根据20吨蓄热式熔铝炉的技术参数和设备要求,报价如下:
1.炉体:根据材料和规格定制
3.温度控制系统:PID控制温度控制器,价格为3000元
4.数字显示:液晶显示屏,价格为2000元
5.加热系统:根据设计方案定制,价格需根据具体要求进行报价。
蓄热式熔铝炉节能技术
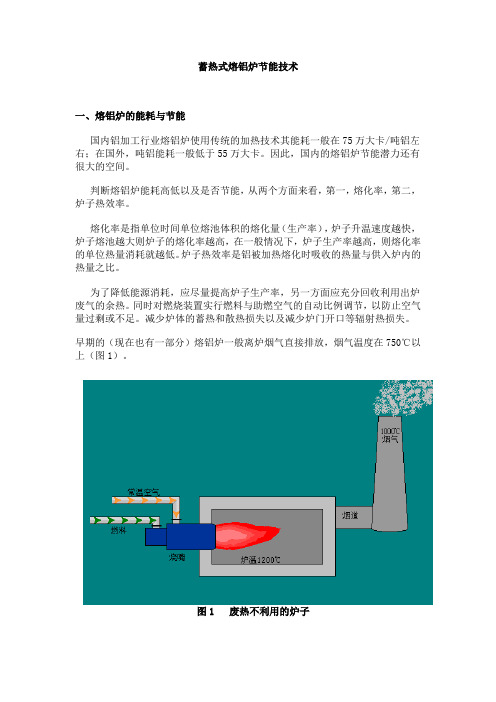
蓄热式熔铝炉节能技术一、熔铝炉的能耗与节能国内铝加工行业熔铝炉使用传统的加热技术其能耗一般在75万大卡/吨铝左右;在国外,吨铝能耗一般低于55万大卡。
因此,国内的熔铝炉节能潜力还有很大的空间。
判断熔铝炉能耗高低以及是否节能,从两个方面来看,第一,熔化率,第二,炉子热效率。
熔化率是指单位时间单位熔池体积的熔化量(生产率),炉子升温速度越快,炉子熔池越大则炉子的熔化率越高,在一般情况下,炉子生产率越高,则熔化率的单位热量消耗就越低。
炉子热效率是铝被加热熔化时吸收的热量与供入炉内的热量之比。
为了降低能源消耗,应尽量提高炉子生产率,另一方面应充分回收利用出炉废气的余热。
同时对燃烧装置实行燃料与助燃空气的自动比例调节,以防止空气量过剩或不足。
减少炉体的蓄热和散热损失以及减少炉门开口等辐射热损失。
早期的(现在也有一部分)熔铝炉一般离炉烟气直接排放,烟气温度在750℃以上(图1)。
图1 废热不利用的炉子为减少烟气带走的热量损失,人们在排烟管道上安装了热量回收装置即空气换热器,将助燃空气预热到一定的温度(200℃左右)后参与燃料的燃烧,但换热器后的排放温度还在500℃以上(图2)。
图2 安装空气预热器的炉子采用蓄热式燃烧技术可以将烟气排放温度降低到150℃以下,助燃空气温度预热到700℃以上,这样就大大地减少了离炉烟气所带走的热量,使炉子热效率大幅度提高,燃料消耗大量减少,达到节能的目的(图3)。
图3 HTAC技术的工作原理图根据工业炉热工原理,助燃空气温度每升高100℃,能节省燃料约5%;或者烟气温度每降低100℃,能节省燃料约5.5%。
因此,采用蓄热式燃烧技术相对换热器回收装置可以节能25%以上。
二.熔炼炉概述:传统上有火焰炉、电阻炉、中频感应炉、反射炉以及坩埚炉等。
为了获得质量高又经济的铝合金溶液,各企业对熔炼设备的选择越来越重视,近几年来,火焰炉、电阻炉、中频感应炉、反射炉都有所改进。
熔炼炉结构的发展方向是:操作自动化、应用更新化、原料节能化等。
蓄热式燃气熔铝炉安全规程
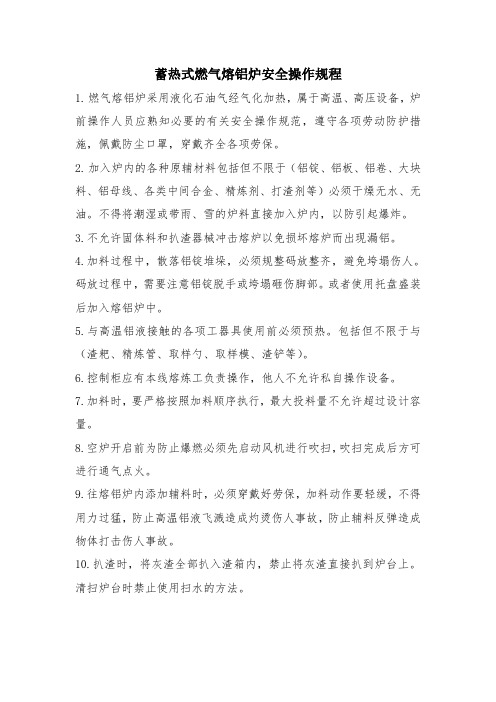
蓄热式燃气熔铝炉安全操作规程
1.燃气熔铝炉采用液化石油气经气化加热,属于高温、高压设备,炉前操作人员应熟知必要的有关安全操作规范,遵守各项劳动防护措施,佩戴防尘口罩,穿戴齐全各项劳保。
2.加入炉内的各种原辅材料包括但不限于(铝锭、铝板、铝卷、大块料、铝母线、各类中间合金、精炼剂、打渣剂等)必须干燥无水、无油。
不得将潮湿或带雨、雪的炉料直接加入炉内,以防引起爆炸。
3.不允许固体料和扒渣器械冲击熔炉以免损坏熔炉而出现漏铝。
4.加料过程中,散落铝锭堆垛,必须规整码放整齐,避免垮塌伤人。
码放过程中,需要注意铝锭脱手或垮塌砸伤脚部。
或者使用托盘盛装后加入熔铝炉中。
5.与高温铝液接触的各项工器具使用前必须预热。
包括但不限于与(渣耙、精炼管、取样勺、取样模、渣铲等)。
6.控制柜应有本线熔炼工负责操作,他人不允许私自操作设备。
7.加料时,要严格按照加料顺序执行,最大投料量不允许超过设计容量。
8.空炉开启前为防止爆燃必须先启动风机进行吹扫,吹扫完成后方可进行通气点火。
9.往熔铝炉内添加辅料时,必须穿戴好劳保,加料动作要轻缓,不得用力过猛,防止高温铝液飞溅造成灼烫伤人事故,防止辅料反弹造成物体打击伤人事故。
10.扒渣时,将灰渣全部扒入渣箱内,禁止将灰渣直接扒到炉台上。
清扫炉台时禁止使用扫水的方法。
蓄热式燃烧技术在熔铝炉使用过程中的优缺点

蓄热式燃烧技术在熔铝炉使用过程中的优缺点作者:王媛媛刘志军来源:《科学与财富》2014年第01期摘要:简要介绍了熔铝炉的工艺过程,蓄热燃烧技术的原理以及其在熔铝炉上的应用进行了分析探讨,并提出蓄热式燃烧技术在熔铝炉使用过程中的优缺点。
关键词:熔铝炉;蓄热式燃烧技术;优缺点一、熔铝炉的工艺过程描述熔铝炉用高效节能的蓄热式烧嘴,使铝及铝合金迅速熔化。
固体料熔化之后,将按工艺要求进行配料,然后采用电磁搅拌器对液态铝进行有效、充分的搅拌,以使铝液温度、成分更均匀。
熔炼期间也可进行电磁搅拌,可以提高炉子的熔化率。
在铝液的成分和温度都符合工艺需求之后,铝水通过转注流槽注入保温炉内,进行精炼、扒渣、静置、调温。
铝熔体温度符合铸造工艺要求而且铸造机已达到待铸状态,铝熔体通过流口、流槽流经在线除气、过滤装置后,进行铸造。
二、蓄热燃烧技术的原理蓄热式烧嘴集燃烧器和蓄热式热交换器于一体,一般采取成对设置,二者交替变换燃烧和排烟工作状态,烧嘴内的蓄热体相应变换放热和吸热状态。
成对烧嘴分设于炉膛的A侧和B 侧,当B侧烧嘴燃烧时,空气流经积蓄了热量的蓄热体而被加热。
与此同时,A侧烧嘴排烟,烟气热量被蓄热体吸收。
换向工作后,A侧烧嘴燃烧,空气同样被蓄热体加热,B侧烧嘴排烟,烟气热量被蓄热体吸收。
如此周而复始,通过蓄热体这一媒介,出炉烟气的余热被转换为空气的物理热,从而得到回收利用。
通过蓄热式烧嘴,烟气排出温度可降至150℃~200℃或更低,空气可预热到1000℃以上,热回收率达到85%以上,温度效率达到90%以上。
蓄热式烧嘴的烟气排出温度为150℃~200℃,基本上达到工艺允许的最低温度。
工艺允许的最低排烟温度是烟气露点以上30℃~50℃,如果排烟温度低于烟气露点,烟气中含有的SO2会形成硫酸,对金属废气管道、阀门、引风机等造成腐蚀。
因此,排烟温度低至150℃~200℃可以认为烟气余热得到了极限回收。
在蓄热式燃烧系统的使用实例中,由于排烟温度过低,废气管道、阀门、引风机等发生腐蚀的现象已不鲜见,因此不能一味追求更低的排烟温度而不顾设备的安全。
蓄热式熔铅炉简介及原理

蓄热式熔铅炉简介及原理
熔铅炉是炼铅工艺中的较为重要的设备。
相较电阻炉、感应炉和传统火焰炉,蓄热式熔铅炉采用上世纪九十年代以来国际燃料利用和燃烧技术研究领域开发成功的蓄热式燃烧技术,通过蓄热体这一媒介,将出炉烟气的余热被转换成空气的物理热从而得到回收利用,可以极大地降低能量消耗和生产成本。
同时,蓄热式熔铅炉一般采用天然气作为能源,其具有能量高,碳排低、燃效好等优良特性,取得了较好的实际效果和经济效益,应用前景广阔。
蓄热式熔铅炉原理
蓄热式熔铅炉主要由熔铅炉体,两台带有蓄热体的烧嘴、烟气/空气四通换向阀空气鼓风机、烟气引风机等组成。
常温空气通过鼓风机引人高温的蓄热式烧嘴中,被加热至1 200 ℃左右后,与燃料混合点燃喷入熔铅炉体持续将铅液加热;燃烧后的热烟气从炉体另一侧排出至另外一台蓄热式烧嘴,烟气在经过蓄热体时将其加热,经过换向阀引风机排放至大气,此时冷烟气温度低于150 C。
之后循环切换换向阀通气方向,使常温空气始终通过高温蓄热体,热烟气始终通过低温蓄热体,使热烟气的能量持续得以回收利用。
- 1、下载文档前请自行甄别文档内容的完整性,平台不提供额外的编辑、内容补充、找答案等附加服务。
- 2、"仅部分预览"的文档,不可在线预览部分如存在完整性等问题,可反馈申请退款(可完整预览的文档不适用该条件!)。
- 3、如文档侵犯您的权益,请联系客服反馈,我们会尽快为您处理(人工客服工作时间:9:00-18:30)。
三对烧嘴,每对烧嘴80Nm3天然气,产生烟气量1016Nm3
每对烧嘴每分钟产生17Nm3烟气,约25670kj热量 即蓄热体需要蓄热量25670kj 蓄热陶瓷小球物性
比热容为1.1KJ/(kg℃)
密度2200kg/m3 价格约4元/kg 蓄热体温度200—950℃
需要蓄热陶瓷小球约31kg
体积约0.015m3 堆积体积约0.02m3 蓄热陶瓷小球
燃烧器品牌
目前进口燃烧器有:美国麦克森 、 德国威索、意大利利雅路、百 得、意高、英国力威、优尼瓦斯、瑞典百通、芬兰奥林等各种品 牌。 国产燃烧器有:北京神雾、岳阳颜氏燃烧器、浙江百特、欧瑞 特、上海凌云、华之邦、唐山金沙、无锡赛威特等
五 节能要点
(1)在加料期,应尽可能缩短加料时间。
(2)在熔化期,采用高速长火焰燃烧器,加强火焰对铝锭的冲击能力。
(3)在液面化平以后及固液转化期,采用必要的熔体搅拌手段。 (4)在固液转化期完成后,及时控制热负荷的供应量,避免过烧。 (5)精炼及保温期应精确控制热负荷大小,以最小的热供应量实现保温。
六 节能分析
我国天然气熔铝炉吨铝能耗75万大卡,折合天然气约88Nm3 ,
过量空气系数1.17
需要空气量1030Nm3 产生烟气量1118Nm3 烟气温度1000℃ 烟气成分如图,1000℃烟气比热为1.51KJ/(m3℃) 空气平均温度22℃,比热为1.013KJ/(kg℃) 标况下空气密度1.293kg/m3 烟气带走热量约396680大卡
采用半预混式燃烧方式结合空气分级燃烧方式,可以 达到最佳节能效果,并有效地降低了NOx的排放量。
空气分级燃烧烧嘴结构示意图
一次空气系数α1
空气分级燃烧的一、二次空 气配比对燃烧室内NOx等污 染物排放有较大影响。从表 一可知,当一次空气占40% 左右时,燃烧室内可以更好 地形成很强的还原气氛,形 成低氧浓度区,并相应降低 了该燃烧区的温度,从而达 到抑制NOx生成的效果,此 时的NOx排放最少。
二段式低NOx燃烧器
二段式低NOx燃烧器
该燃烧器的工作原理如图1所 示,是将燃烧用的空气分2次通 入燃烧区,从而使燃烧过程分两 个阶段完成,避免高温区过分集 中。二次空气是从还原区外围送 入的,在火焰尾部完成完全燃 烧。由于实行分段燃烧,避免了 高温区集中, 因而NOx的排放 浓度显著降低。
四 蓄热式烧嘴选型及布置方式
蓄热式燃烧系统工作原理
三 燃烧方式分类
1扩散式燃烧 2部分预混式燃烧 3预混式燃烧
2部分预混式燃烧
1扩散式燃烧 3预混式燃烧
几种燃烧方式对比
非预混式烧嘴特点:1结构简单、燃烧稳定不发生回火 2天然气与空气可预热到较高温度 3天然气与空气混合较差,火焰较长 4为使充分燃烧,必须提供较多的助燃空气。 半预混式烧嘴特点:1改变天然气和空气的配比可调节火焰长度 2基本上不存在回火现象 3可根据工艺要求控制气氛 。 全预混式烧嘴特点:1空气过剩系数小,燃烧强度高
蓄热体造价
每个蓄热体烧嘴蓄热陶瓷球约130元 三对烧嘴蓄热陶瓷球总价780元 每个蓄热体烧嘴体积约0.04m3 蓄热体效果好投资少占地面积也不大
节能效益
改造之前吨铝能耗88m3,采用蓄热式燃烧技术,吨铝能耗降到60m3 以下,节能量约为32% 天然气价格按4元/m3算,20吨熔铝炉,每天四炉,一年按300天运 行,每年可节省天然气672000m3,节约资金2688000元 本方案一次性投资约50万元,投资回收期约3个月。
国外蓄热式熔铝炉方案
主要结构为两部分:
1传统燃烧器,一次空气可以调节
2蓄热式预热二次空气直接通入炉膛
燃烧器结构
节能量计算
燃烧器一次空气为常温空气,空气量可以通过空气调节系统进行调 节,调节范围一次空气系数0.2到1.3 为达到最大节能效果一次空气系数调到0.2,二次空气系数0.97 二次空气预热到900℃ 每立方天然气需要二次空气9.7立方 900 ℃空气比热为1.127KJ/(kg℃) 预热空气热量12438kj,效率按80%算 每立方天然气可以节省9950kj热量
2天然气要保持较高的压力,以防回火
3天然气与空气预热温度不宜超过400℃
燃烧技术分类
一 空气分级燃烧
优点:非常好的火焰形状,火焰能够很好地进行 控制,火焰光亮,辐射性能好,加热效果好。
燃烧技术分类
二 燃气分级燃烧技术
没有定型的火焰,火焰无法控制,燃烧性能差, 燃气喷嘴易烧毁,辐射性能差,加热质量低。
节能分析
利用烟气预热空气到900 ℃ 900 ℃空气比热为1.127KJ/(kg℃) 可以节省能量316065大卡,占可回收烟气热量约80%,采用蓄热技 术完全可行,
即节省折合约37m3天然气,
按80%效率可以节省约30m3天然气 即采用蓄热式烟气回收技术吨铝能耗可降至58m3
七 20吨熔铝炉节能设计方案
二 蓄热式燃烧技术简介
基本原理
技术形成
烧嘴和蓄热体成对出现, 助燃空气通过其中一个烧嘴, 被加热后供燃烧用,另一个 烧嘴充当排烟的角色,同时 蓄热体被加热。当到达换向 时刻时,换向阀动作使系统 反向运行,烟气加热好的蓄 热体被用来加热空气,助燃 空气冷却的蓄热体又被离开 炉子的高温烟气加热, 将高温空气喷射入炉 膛,维持低氧状态,同时将 燃料输送到气流中,产生燃 烧。空气温度预热到800℃ ~1000℃以上,燃烧区空气 含氧量在21%~2%,与传统燃 烧过程相比,高空气燃烧的 最大特点是节省燃料,减少 CO2和NOX的排放及降低燃烧 噪音,被誉为二十一世纪关 键技术之一。
蓄热式熔铝炉节能方案
一 二 三 四 五 六 七 我国天然气熔铝炉能耗现状 蓄热式燃烧技术简介 燃烧方式以及燃烧技术 蓄热式烧嘴选型及布置方式 节能要点 节能分析 20吨熔铝炉节能方案设计
一 我国天然气熔铝炉能耗现状
国内外天然气熔铝炉吨铝能耗
万大卡
80
60
40 20 75
55
0 国内吨铝能耗 国外吨铝能耗
蓄热式天然气熔铝炉装料量20t 设计熔化速率:正常条件下4t/h,最大熔化速率5t/h
吨铝能耗60 m3/t
天然气热值8500大卡 选用型号为LX02DRQ060-1000的蓄热式烧嘴3对
烧嘴具体参数
蓄热式烧嘴
蓄热式烧嘴结构: 由耐高温的全陶瓷烧嘴和蓄 热式陶瓷换热器构成
蓄热式烧嘴
蓄热式烧嘴
烧嘴布置方式
蓄热式烧嘴最佳安装方式
为使蓄热式熔铝炉内温度分布均匀,蓄热式烧嘴的布置和对数很重要, 烧嘴的布置基本方式如下图所示,最少两对烧嘴交错布置,使炉内烟气 形成绕流,炉内温度分布均匀。烧嘴的对数选择与熔铝炉的外形尺寸和 总热负荷,单个烧嘴的最大出力有关。
烧嘴对数的选定
30 t熔铝炉 采用两组蓄热式烧嘴(单个烧嘴最大燃气能力200 Nm3/h),燃料为天然气(8500 kcal/Nm3)。 烧嘴的功率根据熔铝炉的总负荷来选择。一般4到7吨采用 一对烧嘴。考虑经济性因素,采用的蓄热式烧嘴对数不宜 过多。
相当于改造后每立方只需要0.72立方的天然气
节能量达到28%
节能效益
改造前吨铝能耗80立方,改造后吨铝能耗58立方 天然气价格按4元/m3算,20吨熔铝炉,每天四炉,一年按300天运 行,可以节省能耗费用2112000元 一次性投资利雅路燃烧器1500kw两台16万元,蓄热式换热器两对总 价20万,总投资36万
三对烧嘴等距对称布置
热量收支平衡
热量支出 热量收入
1吨铝熔化所需热量270000大卡 2出炉烟气带走热量275268大卡 3辐射及表面散热和其他热损失总计 约180卡
蓄热体材料及尺寸
熔铝4t/h,吨铝能耗60Nm3,每小时消耗240Nm3天然气