露天矿台阶中深孔爆破质量提高措施
浅谈改善露天爆破质量的有效方法
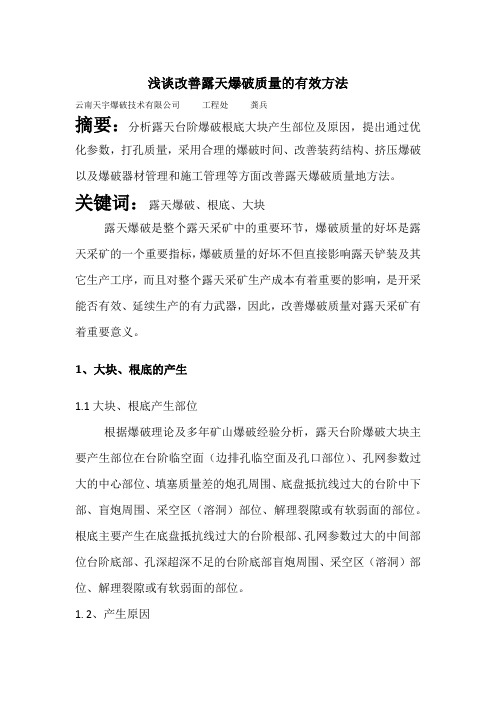
云南天宇爆破技术有限公司 工程处 龚兵
摘要:分析露天台阶爆破根底大块产生部位及原因,提出通过优
化参数,打孔质量,采用合理的爆破时间、改善装药结构、挤压爆破 以及爆破器材管理和施工管理等方面改善露天爆破质量地方法。
关键词:露天爆破、根底、大块
露天爆破是整个露天采矿中的重要环节,爆破质量的好坏是露 天采矿的一个重要指标, 爆破质量的好坏不但直接影响露天铲装及其 它生产工序,而且对整个露天采矿生产成本有着重要的影响,是开采 能否有效、延续生产的有力武器,因此,改善爆破质量对露天采矿有 着重要意义。 1、大块、根底的产生 1.1 大块、根底产生部位 根据爆破理论及多年矿山爆破经验分析,露天台阶爆破大块主 要产生部位在台阶临空面(边排孔临空面及孔口部位) 、孔网参数过 大的中心部位、填塞质量差的炮孔周围、底盘抵抗线过大的台阶中下 部、盲炮周围、采空区(溶洞)部位、解理裂隙或有软弱面的部位。 根底主要产生在底盘抵抗线过大的台阶根部、 孔网参数过大的中间部 位台阶底部、孔深超深不足的台阶底部盲炮周围、采空区(溶洞)部 位、解理裂隙或有软弱面的部位。 1. 2、产生原因
合理的微差时间是毫秒延时爆破的关键因素, 根据大量资料统计 分析,从起爆到岩石被破坏和发生位移的时间,大约是应力波传到自 由面所需的时间的 5~10 倍,即岩石破坏和移动时间与最小抵抗性 (地盘抵抗性)成正比,即:∆T = K × W 式中∆T-毫秒延时时间,MS。
K-与岩石性质,结构构造和爆破条件有关系数。在露天台阶爆
1.2.1 同一炮区孔底未打到同一标高平面,导致孔深不统一,孔 深过深,药柱高度偏低,孔口部分容易出大块,超深不足,造成底盘 抬高或根底。 1.2.2、孔网参数不均匀,由于受到穿孔质量、工作掌子面和地质 因素造成孔网参数不均匀,孔间距过大的中心部位容易产生大块,严 重的会出现根底或挡墙。 1.2.3、填塞质量差的炮孔周围容易产生大块,由于炸药能量从未 堵塞的炮孔中过早释放,造成废孔周围大块较多,填塞长度过大,孔 口部分岩石受到作用力过小,容易产生大块。 1.2.4、底盘抵抗线过大的台阶中下部,由于台阶坡面角过小、钻 机安全距离的限制或由于地质原因造成头排底盘抵抗线过大, 造成台 阶中下部大块较多,严重者出现根底。 1.2.5、软弱面对爆破质量的有着重要的影响;由于软弱带或软弱 面改变了应力波、应力和破裂抛掷方向以及造成能量过于集中、过早 释放造成软弱面周围大块根底较多。 1.2.6、节理裂隙发育部分容易产生大块根底,爆破岩石通常沿节 理裂隙方向破碎,尤其是临空面,容易产生大块。 1.2.7、盲炮周围容易产生大块根底,盲炮是产生大块根底的重要 因素。 1.2.8、采空区(溶洞)部位,由于受到采空区(溶洞)的影响, 穿孔不到位及炸药能量过早释放,容易产生大块根底。 1.2.9、爆破时间不合理,爆破时孔间时间过大时,先爆孔岩石推
论提高露天矿山爆破质量的方法
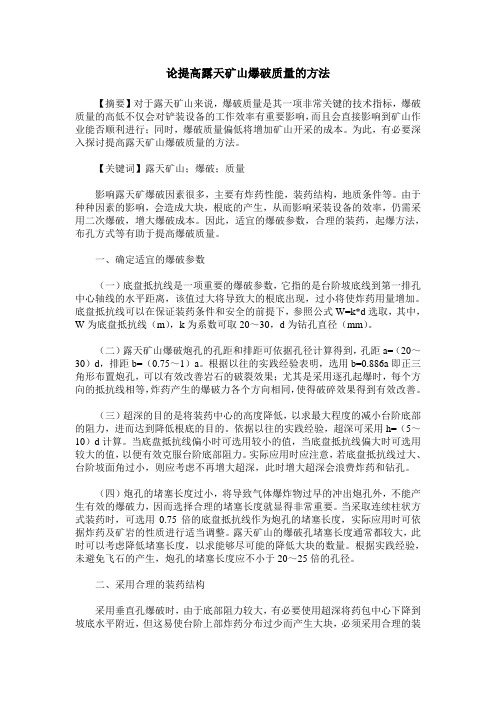
论提高露天矿山爆破质量的方法【摘要】对于露天矿山来说,爆破质量是其一项非常关键的技术指标,爆破质量的高低不仅会对铲装设备的工作效率有重要影响,而且会直接影响到矿山作业能否顺利进行;同时,爆破质量偏低将增加矿山开采的成本。
为此,有必要深入探讨提高露天矿山爆破质量的方法。
【关键词】露天矿山;爆破;质量影响露天矿爆破因素很多,主要有炸药性能,装药结构,地质条件等。
由于种种因素的影响,会造成大块,根底的产生,从而影响采装设备的效率,仍需采用二次爆破,增大爆破成本。
因此,适宜的爆破参数,合理的装药,起爆方法,布孔方式等有助于提高爆破质量。
一、确定适宜的爆破参数(一)底盘抵抗线是一项重要的爆破参数,它指的是台阶坡底线到第一排孔中心轴线的水平距离,该值过大将导致大的根底出现,过小将使炸药用量增加。
底盘抵抗线可以在保证装药条件和安全的前提下,参照公式W=k*d选取,其中,W为底盘抵抗线(m),k为系数可取20~30,d为钻孔直径(mm)。
(二)露天矿山爆破炮孔的孔距和排距可依据孔径计算得到,孔距a=(20~30)d,排距b=(0.75~1)a。
根据以往的实践经验表明,选用b=0.886a即正三角形布置炮孔,可以有效改善岩石的破裂效果;尤其是采用逐孔起爆时,每个方向的抵抗线相等,炸药产生的爆破力各个方向相同,使得破碎效果得到有效改善。
(三)超深的目的是将装药中心的高度降低,以求最大程度的减小台阶底部的阻力,进而达到降低根底的目的。
依据以往的实践经验,超深可采用h=(5~10)d计算。
当底盘抵抗线偏小时可选用较小的值,当底盘抵抗线偏大时可选用较大的值,以便有效克服台阶底部阻力。
实际应用时应注意,若底盘抵抗线过大、台阶坡面角过小,则应考虑不再增大超深,此时增大超深会浪费炸药和钻孔。
(四)炮孔的堵塞长度过小,将导致气体爆炸物过早的冲出炮孔外,不能产生有效的爆破力,因而选择合理的堵塞长度就显得非常重要。
当采取连续柱状方式装药时,可选用0.75倍的底盘抵抗线作为炮孔的堵塞长度,实际应用时可依据炸药及矿岩的性质进行适当调整。
提高露天矿爆破质量的方法

于克服台阶较大的底盘抵抗线,减少根底,这种方法 在南芬露天矿下盘也较常用,效果较好。 2.8爆前拉底 当露天矿台阶底盘抵抗线过大且台阶坡面清碴
时,在有条件的情况下进行爆前拉底也是可以使用 的方法。爆曲拉底足在正常采掘爆孔爆破之前,采用
实践证明,上述内容是提商露天矿爆破质量的
・采矿工艺与技术・
提高露天矿爆破质量的方法
王辉
(本钢南芬露天铁矿辽宁本溪1 17014)
摘要:分析了露天矿爆破时大块和根底产生的部位和原因,提高爆破质量就是减少大块和根底。提出了优化 爆破参数、采用对角起爆的微差爆破、改善装药结构及采用挤压爆破等技术措施,并讨论了爆破器材的管理 和爆破施工注意事项。 关键词:露天矿爆破质量
4按设计要求进行穿孔和爆破施工作业
ms,通常用15—30 m8。南芬矿现场爆破,硬岩取
较小值,软岩取较大值,排间微差和挤压爆破都可取
稍长些,这样会取得较好的破碎质量。
2石采用嬲L爆破
从台阶深孔爆破效果看,斜孔优于垂直孔,因为 沿深孔全长上抵抗线相等,因而矿岩破碎均匀,大 块、根底少,还容易保持所需台阶坡面角,爆后坡面 平整,有利于下一循环的穿孔爆破工作,且因钻机至
表2单位炸药消耗置
I,l o暑一2JDl
3-4
5
6
8
10
12
14
16
20
药包的特殊装药结构。 2.4采用挤压爆破 挤压爆破是指在工作面残留有一定厚度的爆堆 的情况下的爆破,碴堆的存在为挤压创造了条件,不 仅控制爆堆宽度,避免矿岩飞散,而且能延长爆破的 有效作用时间,改善炸药能的利用和破碎效果,从而
减少大块的产生。
孔深的35%~40%和40%-45%为宜。
露天矿山台阶深孔爆破大块成因及解决措施探究

露天矿山台阶深孔爆破大块成因及解决措施探究发布时间:2021-06-23T17:07:07.100Z 来源:《基层建设》2021年第8期作者:彭婷[导读] 摘要:在露天煤矿生产过程中,台阶深孔爆破大块率一直是企业高度关注的问题,过高的大块率会增加成本、降低经济效益。
中国葛洲坝集团易普力股份有限公司重庆市 401121 摘要:在露天煤矿生产过程中,台阶深孔爆破大块率一直是企业高度关注的问题,过高的大块率会增加成本、降低经济效益。
本文就露天煤矿台阶深孔爆破大块成因进行了探讨分析,并相应地从加强施工管理、改进爆破技术、合理设置爆破参数等几个方面提出了解决措施,以期对煤矿企业降低大块率有所帮助。
关键词:露天矿山;台阶深孔爆破;大块率前言:随着爆破技术的进步、深孔钻井机的广泛使用,露天台阶深孔爆破技术也成为了露天煤矿最常使用的爆破技术。
从节约成本、保证安全的角度出发,企业也对爆破作业效果提出了一系列要求,比如爆渣粒度大小适当,爆堆形状和位移合理、台阶工作面要规整、对台阶坡度破坏小等。
1露天矿山台阶深孔爆破大块的问题概述在采矿过程中,经常会用爆破的手段来破坏岩石层,为后续铲装及运输提供大小合适的矿岩颗粒物料,爆破作业的好坏直接影响后续工作的效率和成本。
台阶深孔爆破是大型的露天矿山常常会用到的一种爆破工艺,台阶深孔爆破会受到岩石本身性质与构造、爆破装置与炸药性能、爆破参数、装药结构、施工管理等种种不确定因素的影响,而大块率是衡量爆破效果的重要指标。
大块率或根底率过高一方面会制约铲装车的运输效率,增加二次爆破工作量和炸药使用量,需要的额外时间制约各项工序的正常衔接;另一方面,大块岩石进入破碎机,还可能会导致破碎机卡锤而停止运转,降低煤矿生产效率,增加企业运营成本。
因此,如何有效爆破,降低大块率和根底率成为许多露天煤矿所面临的重要难题。
2露天矿山台阶深孔爆破大块的成因及解决措施 2.1露天矿山台阶深孔爆破大块的成因分析 2.1.1岩石结构的影响台阶深孔爆破实践发现,岩石的性质和非均质程度对岩石爆堆的松散程度、破碎位移都有很大影响。
露天矿山爆破质量优化措施

38
矿 业 工 程
M ining Engineering
第 1O卷 第 5期 2012年 1O月
露 天 矿 山爆 破 质 量 优 化 措 施
刘 亮 (洛 阳栾 川钼业 集 团有 限责任 公 司 ,河南 栾 川 471500)
摘 要 :介 绍 了 爆 破 过 程 中遇 到 的 问题 及 改 进措 施 。通 过 不 断 优 化 完 善 爆 破 施 工 规 范 ,有 效 地 保 证 了施 工 质 量 ,提 高 了 爆 破 效 果 。
— — 布孔 方 式 。多 排 布 孔 一 般 有 方 形 、矩 形 及 三 角 形 (即 梅 花 形 ) 3种 布 孔 方 式 ,从 能 量 均 匀 分 布 的 观 点 看 , 以 等边 三 角形 布 孔 最 理 想 。实 践 表 明 , 在 保 持 孔 网 面 积 不 变 的前 提下 ,通 过 减 少 排 距 ,增 大 孔 距 ,即 增 大 孔 的 密 集 系 数 ,可有 效 地 改变 破 碎 质 量 。所 以布 孑L方 式 采 用 大 孔 距 小 排距 三 角 形 布 孔 。 针对 前排 爆 破 后 大 块及 岩根 较 多 的 现 象 , 可 对 前 排 孔 进 行 了 适 当 得 加 密 。
爆 破设 计 是 对爆 破 施 工 的 详 细介 绍 和 要求 ,对 现 场 施 工 具 有指 导 作 用 。 内容 包 括爆 区地 理 位 置 、周 边 环 境 、穿 孔 施 工 情况 、孑L网参 数 、药 量计 算 、装 药 结 构 、起 爆 网络 、主 材 消 耗 、主要 技 术 经济 指 标 、爆 破 安 全 、劳 动施 工 组 织 、实 测 图与 网 络 图等 。
露天采场中深孔爆破技术的优化
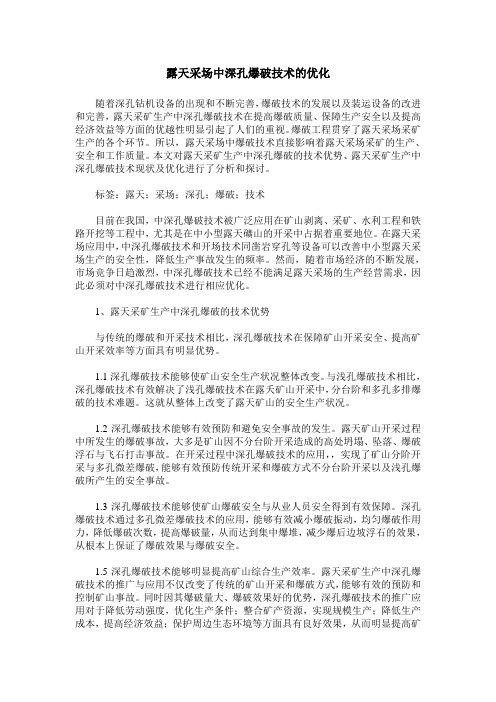
露天采场中深孔爆破技术的优化随着深孔钻机设备的出现和不断完善,爆破技术的发展以及装运设备的改进和完善,露天采矿生产中深孔爆破技术在提高爆破质量、保障生产安全以及提高经济效益等方面的优越性明显引起了人们的重视。
爆破工程贯穿了露天采场采矿生产的各个环节。
所以,露天采场中爆破技术直接影响着露天采场采矿的生产、安全和工作质量。
本文对露天采矿生产中深孔爆破的技术优势、露天采矿生产中深孔爆破技术现状及优化进行了分析和探讨。
标签:露天;采场;深孔;爆破;技术目前在我国,中深孔爆破技术被广泛应用在矿山剥离、采矿、水利工程和铁路开挖等工程中,尤其是在中小型露天礦山的开采中占据着重要地位。
在露天采场应用中,中深孔爆破技术和开场技术同凿岩穿孔等设备可以改善中小型露天采场生产的安全性,降低生产事故发生的频率。
然而,随着市场经济的不断发展,市场竞争日趋激烈,中深孔爆破技术已经不能满足露天采场的生产经营需求,因此必须对中深孔爆破技术进行相应优化。
1、露天采矿生产中深孔爆破的技术优势与传统的爆破和开采技术相比,深孔爆破技术在保障矿山开采安全、提高矿山开采效率等方面具有明显优势。
1.1深孔爆破技术能够使矿山安全生产状况整体改变。
与浅孔爆破技术相比,深孔爆破技术有效解决了浅孔爆破技术在露夭矿山开采中,分台阶和多孔多排爆破的技术难题。
这就从整体上改变了露天矿山的安全生产状况。
1.2深孔爆破技术能够有效预防和避免安全事故的发生。
露天矿山开采过程中所发生的爆破事故,大多是矿山因不分台阶开采造成的高处坍塌、坠落、爆破浮石与飞石打击事故。
在开采过程中深孔爆破技术的应用,,实现了矿山分阶开采与多孔微差爆破,能够有效预防传统开采和爆破方式不分台阶开采以及浅孔爆破所产生的安全事故。
1.3深孔爆破技术能够使矿山爆破安全与从业人员安全得到有效保障。
深孔爆破技术通过多孔微差爆破技术的应用,能够有效减小爆破振动,均匀爆破作用力,降低爆破次数,提高爆破量,从而达到集中爆堆,减少爆后边坡浮石的效果,从根本上保证了爆破效果与爆破安全。
关于改善矿山露天爆破质量的几点思考

关于改善矿山露天爆破质量的几点思考发布时间:2021-06-04T03:49:38.241Z 来源:《中国科技人才》2021年第9期作者:熊正超[导读] 在露天矿采掘台阶过程中,如果存在前排孔底板抵抗线过大、单次爆破排数过多、炮孔填塞高度超标、起爆方式不当、爆破参数不合理等问题时,容易出现引发爆破上翻、后冲、根底、大块等现象,在工作面后方的冲击力作用下,矿岩向最小抵抗线反方向出现翻起现象,导致工作面后方未起爆岩体结构中形成裂隙,或是部分矿岩上翻堆积至未爆台阶顶面部位,不但无法取得预期的爆破效果,还将对后续爆破作业的开展造成阻碍。
宏大爆破工程集团有限责任公司广东省广州市 510000摘要:露天爆破作为矿山开采项目中的一项关键技术,通过起爆炸药产生的爆破冲击波来破碎矿岩结构,高效完成台阶采剥与掘沟作业,技术应用情况与矿山开采效率密切相关。
然而,在实际生产期间,受到多方面因素影响,矿山露天爆破质量存在不确定性,存在爆破后冲、大块、根底等质量问题。
因此,本文对矿山露天爆破质量问题进行思考,提出主要质量问题解决措施与爆破质量控制措施,为从业人员提供参考。
关键词:露天矿;爆破质量;改善措施一、矿山露天爆破质量问题分析与防治处理1、爆破上翻与后冲在露天矿采掘台阶过程中,如果存在前排孔底板抵抗线过大、单次爆破排数过多、炮孔填塞高度超标、起爆方式不当、爆破参数不合理等问题时,容易出现引发爆破上翻、后冲、根底、大块等现象,在工作面后方的冲击力作用下,矿岩向最小抵抗线反方向出现翻起现象,导致工作面后方未起爆岩体结构中形成裂隙,或是部分矿岩上翻堆积至未爆台阶顶面部位,不但无法取得预期的爆破效果,还将对后续爆破作业的开展造成阻碍。
为预防爆破上翻与后冲质量问题的出现,需要从优化爆破技术方案与改进爆破工艺两方面共同着手。
一方面,根据现场情况对爆破技术方案进行优化调整,准确验算前排孔底板抵抗线、台阶高度、相邻炮孔间距、单次爆破排数、前后排孔装药量、起爆网络等参数是否合理,要求前排孔底板抵抗线禁止超过台阶高度且与炮孔直径有关,保证前排抵抗线在合理范围泥,在必要情况下调整台阶高度。
如何改善露天矿深孔爆破质量
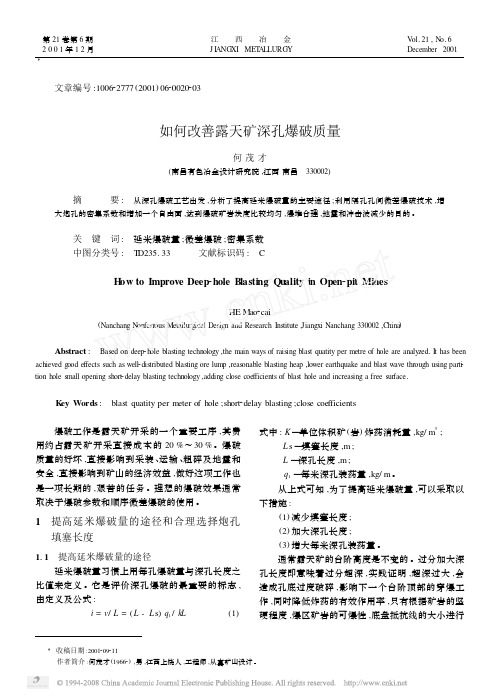
Key Words : blast quatity per meter of hole ;short2delay blasting ;close coefficients
爆破工作是露天矿开采的一个重要工序 ,其费 用约占露天矿开采直接成本的 20 %~30 %。爆破 质量的好坏 ,直接影响到采装 、运输 、粗碎及地震和 安全 ,直接影响到矿山的经济效益 ,做好这项工作也 是一项长期的 ,艰苦的任务 。理想的爆破效果通常 取决于爆破参数和顺序微差爆破的使用 。
Abstract : Based on deep2hole blasting technology ,the main ways of raising blast quatity per metre of hole are analyzed. It has been
achieved good effects such as well2distributed blasting ore lump ,reasonable blasting heap ,lower earthquake and blast wave through using parti2 tion hole small opening short2delay blasting technology ,adding close coefficients of blast hole and increasing a free surface.
Ξ 收稿日期 :2001209211 作者简介 :何茂才 (19662) ,男 ,江西上饶人 ,工程师 ,从事矿山设计 。
第 21 卷第 6 期 何茂才 :如何改善露天矿深孔爆破质量
·21 ·
选取才是合理的 。一个矿山的穿孔设备 、炸药种类 、 装药手段是基本不变的 ,要增大每米深孔装药量是 难以实现的 。因此 ,唯一比较现实的方法就是适当 减少填塞长度 。如果能够找到一个最小填塞长度 , 就能最大限度地提高延米爆破量 。 112 合理选择填塞长度[1]
谈提高露天矿爆破质量的主要措施 李发帅
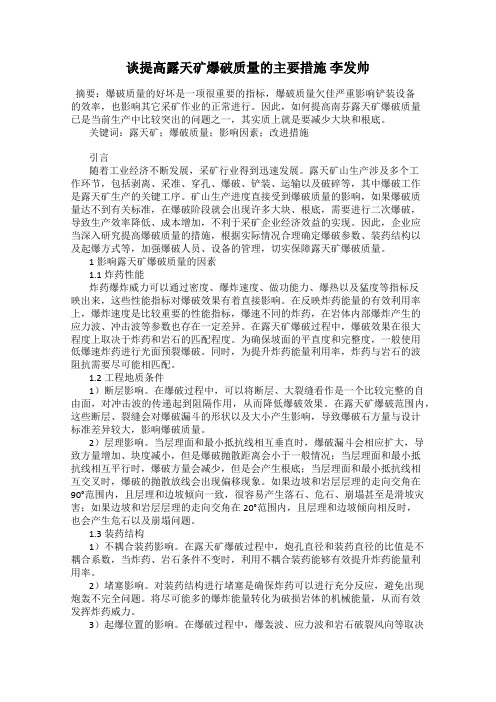
谈提高露天矿爆破质量的主要措施李发帅摘要:爆破质量的好坏是一项很重要的指标,爆破质量欠佳严重影响铲装设备的效率,也影响其它采矿作业的正常进行。
因此,如何提高南芬露天矿爆破质量已是当前生产中比较突出的问题之一,其实质上就是要减少大块和根底。
关键词:露天矿;爆破质量;影响因素;改进措施引言随着工业经济不断发展,采矿行业得到迅速发展。
露天矿山生产涉及多个工作环节,包括剥离、采准、穿孔、爆破、铲装、运输以及破碎等,其中爆破工作是露天矿生产的关键工序。
矿山生产进度直接受到爆破质量的影响,如果爆破质量达不到有关标准,在爆破阶段就会出现许多大块、根底,需要进行二次爆破,导致生产效率降低、成本增加,不利于采矿企业经济效益的实现。
因此,企业应当深入研究提高爆破质量的措施,根据实际情况合理确定爆破参数、装药结构以及起爆方式等,加强爆破人员、设备的管理,切实保障露天矿爆破质量。
1影响露天矿爆破质量的因素1.1炸药性能炸药爆炸威力可以通过密度、爆炸速度、做功能力、爆热以及猛度等指标反映出来,这些性能指标对爆破效果有着直接影响。
在反映炸药能量的有效利用率上,爆炸速度是比较重要的性能指标,爆速不同的炸药,在岩体内部爆炸产生的应力波、冲击波等参数也存在一定差异。
在露天矿爆破过程中,爆破效果在很大程度上取决于炸药和岩石的匹配程度。
为确保坡面的平直度和完整度,一般使用低爆速炸药进行光面预裂爆破。
同时,为提升炸药能量利用率,炸药与岩石的波阻抗需要尽可能相匹配。
1.2工程地质条件1)断层影响。
在爆破过程中,可以将断层、大裂缝看作是一个比较完整的自由面,对冲击波的传递起到阻隔作用,从而降低爆破效果。
在露天矿爆破范围内,这些断层、裂缝会对爆破漏斗的形状以及大小产生影响,导致爆破石方量与设计标准差异较大,影响爆破质量。
2)层理影响。
当层理面和最小抵抗线相互垂直时,爆破漏斗会相应扩大,导致方量增加、块度减小,但是爆破抛散距离会小于一般情况;当层理面和最小抵抗线相互平行时,爆破方量会减少,但是会产生根底;当层理面和最小抵抗线相互交叉时,爆破的抛散放线会出现偏移现象。
简述露天矿爆破因素及提高爆破质量方法

一
爆破
炸 药
引 言 影 响露 天 矿爆 破 因素很 多 ,主要 有 炸药 性能 ,装 药 结构 ,地 质 条
、
药 中心 的高 度 以便有 效 克服 台阶 底部 阻力 ,避 免减 少根 底 ,可根 据经 验公式 :
h = f O . 1 5 - 0 . 3 5 ) w
响 ,在光 面 预裂 爆破 中位 保 护坡 面 的完整 平 直 ,需 用低爆 速 炸药 。为 提 高炸 药能 量 的有效 利 用率 ,炸 药 的波 阻抗应 尽 可能 与所 爆岩 石 的波
阻抗 相匹 配 。
2 . 工程 地质 条件对 爆破 作用 的影响 2 . 1 断 层 的影响
.
断层 和大 裂缝 对 爆破 作用 相 当于 一个 完整 的 自由面 ,可 以阻断 冲 击波 的传 播 ,造 成爆 生气 体 的突 出 ,使爆 破效 果 恶化 ,在 药包 爆破 作 用范 围 内的断 层或 大 裂缝 影 响爆 破漏 斗 的大 小和 形状 ,从 而 减少或 增 加爆 破破石 方量 ,使爆破 不 能达到 预定 的抛掷效 果 。 2 . 2 层 理的影 响 最 小抵 抗 线与 层理 面 垂直 ,将 扩 大爆 破漏 斗 ,增加 方 量 ,块度 降 低 ,但爆 堆抛 散距 离 比一 般情 况 小 ;最小 抵抗 线 与层 理面 平行 时 ,将 减小 爆破 方量 ,但 容 易 留根底 ;最 小抵 抗 线与 层理 斜 交时 。爆 堆抛 散 方 向会发 生偏 移 。当层理 走 向与边 坡 走向 交角小 于 9 O 。 时 ,层 理倾 向 与边坡 相 同 ,可 能出现危 石 ,落石 ,崩塌 ,严重 时可 能 引起 顺 层滑坡 ; 当岩 层走 向与 边坡 走 向交 角小 于 2 0 。 ,岩 层倾 向与边 坡相 反 ,倾 角在 7 0 。~ 9 O 。时 ,易发 生危石 和崩塌 。 3 . 装药 结构对 爆破效 果影 响 3 . 1 不耦 合装 药影 响 炮孔 直 径 与装 药直 径之 比 为不 耦合 系数 ,在 一 定岩 石和 炸 药条 件 下 ,采用不 耦 合装 药 或空 气间 隔装 药可 以增加 炸药 用 于破 碎或 抛掷 岩 石 能 量的比例 ,提 高爆破 能量 的有效 利用率 。 3 . 2 堵塞 的影 响 堵 塞 的 目的是 保证 炸药 充 分反应 ,使 之 产 生最 大热 量 ,防止 炸 药 不 完全 爆轰 ,防止 高温 高 压爆 轰气 体过 早 从炮 眼 中逸 出 ,使 爆 炸产 生 的 能量 更 多地 转换 成破碎 岩体 的机械 功 ,提 高炸药 能量 利用率 。 3 . 3 起爆 位置 的影 响 起爆 药 包放 在什 么 位及 岩 石破裂 发展 方 向。
浅谈露天矿山深孔爆破质量控制措施

浅谈露天矿山深孔爆破质量控制措施在大型露天矿山开采过程中,深孔爆破是开采的主要工序之一,深孔爆破质量的好坏直接决定着铲装、运输、破碎等各个工艺环节的效率及经济效益。
对整个矿山的生产及技术经济指标具有较大的影响、矿岩爆破大块率和根底率是衡量爆破质量的两项重要指标,露天矿爆破质量主要控制目的是减少爆破大块率和根底率。
本文通过对露天矿爆破中产生产生大块和根底的原因进行分析和总结,并针对产生根底大块的具体原因,提出了切实可行的解决方案。
通过生产实践论证,这些措施提高了爆破质量,降低了根底和大块率,为露天矿生产循环提供有利保障。
标签:露天矿山深孔爆破质量控制一、深孔爆破中大块、根底产生的部位和原因1、爆破中大块、根底产生的部位根据爆破理论知识和现场实际生产经验,根底与大块有一定的关系。
有根底的部位,必然有大块产生。
但是有大块的部位不一定存在根底。
大块主要出现的部位是:台阶上部的自由面及空口部位,孔网参数偏大的中心周围。
根底主要主要出现在底盘抵抗线偏大的台阶底部,孔网参数较大的中间部位的台阶底部,炮孔缠身不足的台阶底部及盲炮部位。
2、爆破中大块、根底的产生原因(1)在同一爆破区超深变化较大,个别炮孔超深偏大,使得在同一炮区台阶坡面部分抵抗线不等,在露天深孔爆破中,炮孔装药的药柱距台阶坡面的抵抗线自上俄日新逐渐增大,在台阶底部的抵抗最大,由于抵抗线不均匀,在爆破过程中,孔与孔之间很快被击穿,爆生气体泄露,导致台阶上部岩体产生较大的块。
如果超深偏小,台阶底部矿岩受到炸药能量作用不足,爆破后往往出现台阶底部抬高或者根底。
(2)孔网参数不合理,在爆破过程中,孔网参数应根据不同的岩性和段高随时进行调整,在孔网参数较大的中间部位,由于炸药破坏的作用较小,使得爆破后的大块增多,也有可能出现台阶抬高或者根底。
(3)爆破设计中单位耗药量不合理,爆破设计中原则上根据岩石的根底和可爆性设计炸药的单耗量,如果单耗不合理,孔内药柱较低,易在上部形成大块。
提高露天铁矿中深孔爆破质量的途径
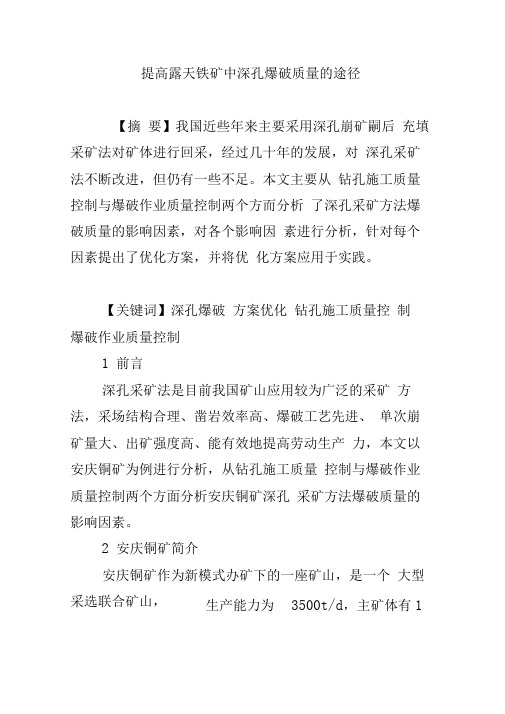
提高露天铁矿中深孔爆破质量的途径【摘要】我国近些年来主要采用深孔崩矿嗣后充填采矿法对矿体进行回采,经过几十年的发展,对深孔采矿法不断改进,但仍有一些不足。
本文主要从钻孔施工质量控制与爆破作业质量控制两个方而分析了深孔采矿方法爆破质量的影响因素,对各个影响因素进行分析,针对每个因素提出了优化方案,并将优化方案应用于实践。
【关键词】深孔爆破方案优化钻孔施工质量控制爆破作业质量控制1前言深孔采矿法是目前我国矿山应用较为广泛的采矿方法,采场结构合理、凿岩效率高、爆破工艺先进、单次崩矿量大、出矿强度高、能有效地提高劳动生产力,本文以安庆铜矿为例进行分析,从钻孔施工质量控制与爆破作业质量控制两个方面分析安庆铜矿深孔采矿方法爆破质量的影响因素。
2安庆铜矿简介安庆铜矿作为新模式办矿下的一座矿山,是一个大型采选联合矿山,生产能力为3500t/d,主矿体有1号矿体、 2 号矿体、马头山矿体,其中着大部分生产任务, 1 号矿体部分属急倾斜矿体,走 向长760m ,矿体平均厚度28m ,大多数为50 一 70m , 矿围岩均属稳固岩层,采场垂直矿体走向布置,宽度 为15m ,长度为矿体厚度,分段高度为60m ,分矿房、 矿柱二步骤回采,回采时实行分段凿岩,崩矿,集中 出矿。
钻机为 Simba-261 型潜孔钻机,大孔直径为 165mm ,出矿设备为ST1030铲运机,斗容3.8亩,采 场回采完毕后嗣后一次充填, 矿房采用尾砂胶结充填, 矿柱采用尾砂充填,正因为运用此种采矿方法,安庆 铜矿 骤采场的增多,矿石的损失率和贫化率也大大增加, 严重制约着矿山的发展。
在这种情况下,控制深孔采 矿工艺的爆破质量显得尤为重要。
3 钻孔施工质量控制 随着科学技术的发展,科研人员经过前期大量的 科研工作,己经优化出最佳的采场布孔参数,这些参 数大部分沿用至今,且在实际应用过程中取得了良好 的效果。
经过长期的实践发现,在保证最优的采场布 孔参数的前提下,炮孔施工质量的好坏对爆破效果的 影响极大。
谈提高露天矿爆破质量的主要措施
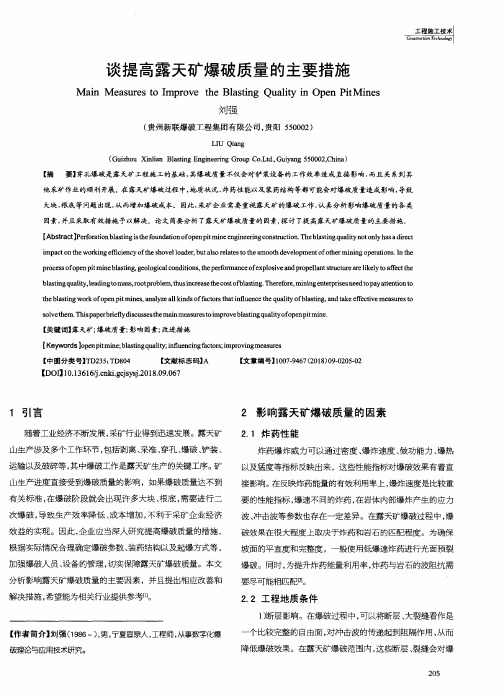
1 引言
2 影响露天矿 爆破质量 的因素
随着工业经济不断发展 ,采矿行业得到迅速发 展。露天矿 山生产涉 及多个工作环节 ,包括剥离 、采准 、穿孔 、爆破 、铲 装 、 运输 以及破碎等 ,其中爆破工作 是露 天矿 生产 的关键工序 。矿 山生产进度直接受到爆破质量 的影响 ,如 果爆破质量达不到 有关标 准 ,在爆破 阶段就会 出现许 多大块 、根底 ,需要进 行二 次爆 破 ,导致生产效 率降低 、成 本增加 ,不利 于采矿企 业经济 效益 的实现 。 因此 ,企业应当深人研究提高爆破质量 的措施 , 根据 实际 情况合理确定爆破参数 、装药结构以及起爆方式等 , 加强爆破 人员 、设 备的管 理 ,切实保障 露天 矿爆破 质量。本文 分析 影响露天矿爆破质量 的主要 因素 ,并且提 出相 应改 善和 解决措施 ,希望能为相关行业提供参考 [1]。
【关键词】露天矿 ;爆破 贡量;影响 因素;改进措施
【Keywords]openpitmine;blastingquality;influencingfactors;improvingmea sures
【中 图 分 类 号]TD235;TD804
【文献 标 志 码 IA
【DOI】10.13616/j.cnki.gcjsysj.2018.09.067
LIU Qiang (Guizhou Xinlian Blasting Engineering Group Co.Ltd.,Guiyang 550002,China)
【摘 要】穿孔爆破是露天矿 工程施 工的基础 ,其爆破质量 不仅会对铲 装设备 的工作效率造成 直接 影响 ,而且 关 系到其 他采矿作业的顺利开展 。在 露天矿爆破过程 中,地质状况 、炸药性能以及装药结构等都可能会对爆破质量造成影响 ,导致 大块、根底 等问题 出现 ,从 而增加爆破成本 。因此 ,采矿企 业需要 重视露天矿的爆破工作 ,认真分析影 响爆破质 量的各类 因素 ,并且采取 有效措施 予以解 决。论 文简要分析 了露天矿爆破质量 的因素,探讨 了提 高露天矿爆破质 量的主要措施 。
凿岩爆破工程-露天深孔爆破质量控制
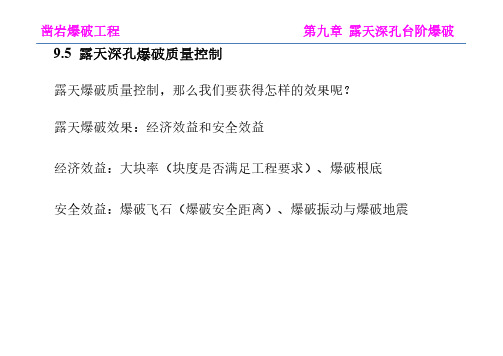
凿岩爆破工程
第九章 露天深孔台阶爆破
9.5 露天深孔爆破质量控制
作业区预处理
深孔爆破质量控制的措施
钻孔作业 爆破器材的准备
钻孔作业:
施爆作业
(1)布孔。孔位点与方位的误差必须控制在设计所要求的误差范围内
。
(2)质量控制方法、安全技术交底。由爆破技术负责人组织技术员、
钻工、爆破员、安全员进行质量控制标准、施工方法、安全技术措施、
凿岩爆破工程
9.5 露天深孔爆破质量控制
深孔爆破质量控制的措施
第九章 露天深孔台阶爆破
作业区预处理 钻孔作业 爆破器材的准备 施爆作业
作业区预处理:剥离土层,清除作业面浮土、浮渣,尽量使作 业面平整,禁止出现伞檐、根底和空洞,台阶工作平台宽一般 不应小于15米;对边坡进行修整预处理,使其坡面角尽量控制 在60°~75°范围内。完工后由工程技术负责人组织进行验收 ,合格后进入下一工序。
具并反复调整,使钻机满足钻孔要求。
第一、保证钻机方向控制的精度。孔距、排距用皮尺采用内插法进行确定比较好
,不应采用逐孔推移加密的方法,孔位用防水油漆标识、编号并进行保护。
第二、钻孔倾角的控制。钻孔倾角的确定原则上采用钻机上的量角器控制,特殊
情况下可考虑用罗盘辅助。
第三、钻孔方向控制。用线锤吊在钻杆的下缘正中,调整钻杆,使线锤的正投影
计划完成时间等事项进行交底。技术员就爆破设计内容、过程控制方法
向钻工作详细书面交底,同时交代清孔、验孔及炮孔的保护的具体标准
及方法。
(3)测量器具的检查与校验。钻孔前钻工必须对当班使用的测量器具
进行检查校验。罗盘、量角器的误差一般不应超过1°;钻杆采用1米钢
板尺和水平尺进行检查,检验合格后才能钻孔作业,对于精度达不到要
露天爆破大块产生及优化
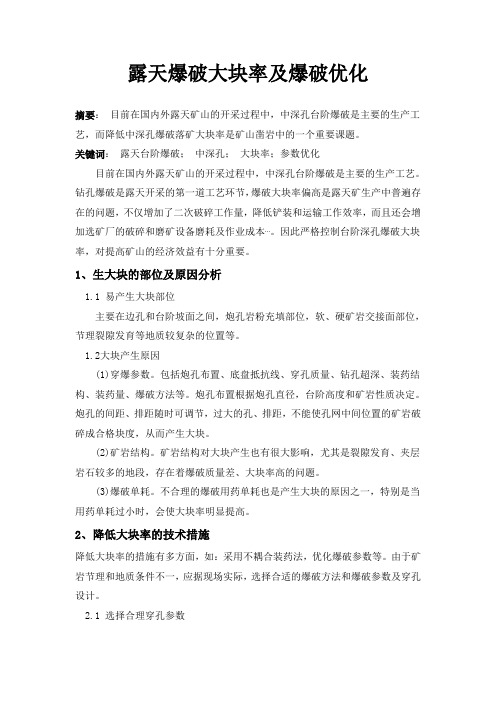
露天爆破大块率及爆破优化摘要:目前在国内外露天矿山的开采过程中,中深孔台阶爆破是主要的生产工艺,而降低中深孔爆破落矿大块率是矿山凿岩中的一个重要课题。
关键词:露天台阶爆破;中深孔;大块率;参数优化目前在国内外露天矿山的开采过程中,中深孔台阶爆破是主要的生产工艺。
钻孔爆破是露天开采的第一道工艺环节,爆破大块率偏高是露天矿生产中普遍存在的问题,不仅增加了二次破碎工作量,降低铲装和运输工作效率,而且还会增加选矿厂的破碎和磨矿设备磨耗及作业成本⋯。
因此严格控制台阶深孔爆破大块率,对提高矿山的经济效益有十分重要。
1、生大块的部位及原因分析1.1 易产生大块部位主要在边孔和台阶坡面之间,炮孔岩粉充填部位,软、硬矿岩交接面部位,节理裂隙发育等地质较复杂的位置等。
1.2大块产生原因(1)穿爆参数。
包括炮孔布置、底盘抵抗线、穿孔质量、钻孔超深、装药结构、装药量、爆破方法等。
炮孔布置根据炮孔直径,台阶高度和矿岩性质决定。
炮孔的间距、排距随时可调节,过大的孔、排距,不能使孔网中间位置的矿岩破碎成合格块度,从而产生大块。
(2)矿岩结构。
矿岩结构对大块产生也有很大影响,尤其是裂隙发育、夹层岩石较多的地段,存在着爆破质量差、大块率高的问题。
(3)爆破单耗。
不合理的爆破用药单耗也是产生大块的原因之一,特别是当用药单耗过小时,会使大块率明显提高。
2、降低大块率的技术措施降低大块率的措施有多方面,如:采用不耦合装药法,优化爆破参数等。
由于矿岩节理和地质条件不一,应据现场实际,选择合适的爆破方法和爆破参数及穿孔设计。
2.1 选择合理穿孔参数(1)布孔应根据台阶高度确定合理参数:如抵抗线、孔距、排距、炮孔超深等。
(2)抵抗线是影响爆破效果的一个重要参数,抵抗线过小,会造成飞炮,存在安全隐患;抵抗线过大,会产生过多大块及根底。
(3)孔、排距是影响爆破效果的第二重要参数,硬矿岩宜用小的孔、排距,软、碎、裂隙发育的矿岩可采用大的孔、排距。
露天矿山台阶深孔爆破大块成因及解决措施

露天矿山台阶深孔爆破大块成因及解决措施摘要:在现今社会,煤炭在各行各业需求中占的比重越来越重,呈现出了逐渐上涨的趋势,做好采矿工作就显得至关重要。
在我国科技水平的快速提高下,对于深孔爆破技术的应用范围不断扩大,因此,本文分析了露天矿山中深孔爆破根底以及大块率的成因,并提出一些切实可行的解决方法,通过生产实践的论证有效地解决这些问题,提高了矿山的生产率,保证了露天矿山的生产循环。
关键词:露天矿山;深孔爆破;大块成因;解决措施引言目前深孔台阶爆破是露天煤矿石方剥离爆破中普遍采取的爆破方法。
然而,深孔台阶爆破时又普遍存在大块率偏高等问题。
大块率是评价爆破效果的重要指标之一,大块率高直接影响铲装作业效率,增加挖掘机械设备磨损,同时增加二次破碎的工程量和爆破成本,影响矿山的生产和安全。
根底率也是评价爆破效果的重要指标之一,根底率偏高造成平台底面凸凹不平,不但影响本次爆破石方铲装,而且也会影响下一爆破循环正常进行。
因此,分析产生大块等原因,提出解决措施具有十分重要的意义。
1矿山地质与爆破概况矿山中主要以断裂构造为主,矿石的种类多种多样,不同的矿石的普氏硬度不同,奇爆破性也存在着很大的差异,矿石的普氏硬度比矿石较小,也存在于其独特的性质。
露天矿山的爆破运用高精度的雷管联线,进行逐孔起爆。
与此同时,在进行深孔爆破时,要安排好台阶的高度以及孔的深度,合理控制炸药的使用量,避免因用量过多或过少而影响到爆破的效果。
2露天矿山台阶深孔爆破大块产生原因分析2.1现场实际情况通过对采场布孔及爆堆效果的现场查看分析表明,大块主要产生于清渣爆破前排孔、炮孔填塞段、抵抗线和孔网参数较大以及岩土互层等区域。
2.2原因分析清渣爆破时,前排孔抵抗线较小,为防止炮孔正前方出现飞石,前排孔装药量集中于炮孔底部,使其沿炮孔轴线方向的炸药能量分布不均。
填塞段及孔口附近能量不足,岩石破坏不均匀。
岩土互层或同一爆区存在不同的岩性,炸药爆炸产生的应力波和爆轰气体从相邻的较软岩石层泄露,炸药能力在较硬岩石区域得不到充分利用,造成大块率增加。
露天深孔爆破出现的问题及解决方案
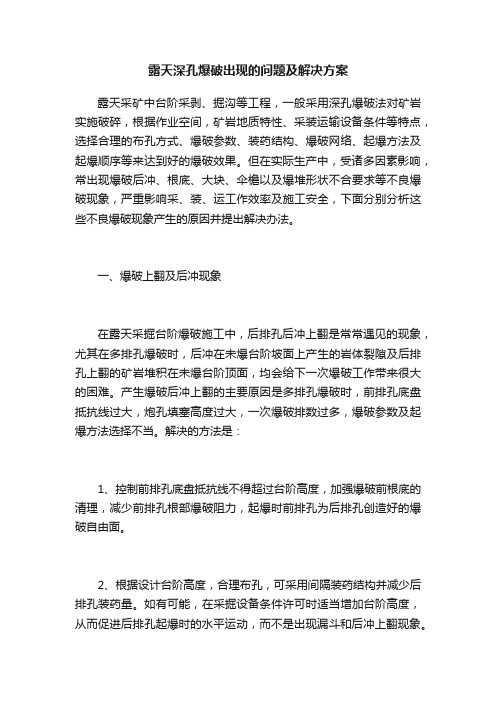
露天深孔爆破出现的问题及解决方案露天采矿中台阶采剥、掘沟等工程,一般采用深孔爆破法对矿岩实施破碎,根据作业空间,矿岩地质特性、采装运输设备条件等特点,选择合理的布孔方式、爆破参数、装药结构、爆破网络、起爆方法及起爆顺序等来达到好的爆破效果。
但在实际生产中,受诸多因素影响,常出现爆破后冲、根底、大块、伞檐以及爆堆形状不合要求等不良爆破现象,严重影响采、装、运工作效率及施工安全,下面分别分析这些不良爆破现象产生的原因并提出解决办法。
一、爆破上翻及后冲现象在露天采掘台阶爆破施工中,后排孔后冲上翻是常常遇见的现象,尤其在多排孔爆破时,后冲在未爆台阶坡面上产生的岩体裂隙及后排孔上翻的矿岩堆积在未爆台阶顶面,均会给下一次爆破工作带来很大的困难。
产生爆破后冲上翻的主要原因是多排孔爆破时,前排孔底盘抵抗线过大,炮孔填塞高度过大,一次爆破排数过多,爆破参数及起爆方法选择不当。
解决的方法是:1、控制前排孔底盘抵抗线不得超过台阶高度,加强爆破前根底的清理,减少前排孔根部爆破阻力,起爆时前排孔为后排孔创造好的爆破自由面。
2、根据设计台阶高度,合理布孔,可采用间隔装药结构并减少后排孔装药量。
如有可能,在采掘设备条件许可时适当增加台阶高度,从而促进后排孔起爆时的水平运动,而不是出现漏斗和后冲上翻现象。
3、采用多排孔微差爆破时,针对不同矿岩,选择最优的排间微差间隔。
对于大区间微差爆破,后排孔爆破条件显然与前排孔不同,其夹制作用较大,并且前排孔爆破应力波和爆生气体对后排孔的爆破影响也很大,如果排间微差间隔过短,前排孔不能在期望的时间内向台阶自由面移动,则后排孔会由于抵抗线过大出现后冲或上翻。
前后排孔的起爆间隔按抵抗线计算应在12-16ms/m较为合理,而后排孔应逐段增加时间间隔,一般为10%较为理想,需根据具体情况在爆破实验中探索,以取得良好的爆破效果。
一般来讲,台阶高度越短,台阶移动时间就越长,排间微差间隔的增加尤其必要。
4、采用倾斜深孔爆破方法,以减少后排孔底盘抵抗线。
- 1、下载文档前请自行甄别文档内容的完整性,平台不提供额外的编辑、内容补充、找答案等附加服务。
- 2、"仅部分预览"的文档,不可在线预览部分如存在完整性等问题,可反馈申请退款(可完整预览的文档不适用该条件!)。
- 3、如文档侵犯您的权益,请联系客服反馈,我们会尽快为您处理(人工客服工作时间:9:00-18:30)。
露天矿台阶中深孔爆破质量提高措施
摘要:本文简述了露天矿爆破时影响爆破效果的因素,提出了提高爆破质
量的一些常用方法。
其中采用合理的爆破参数,爆破方法等对于提高爆破质量具
有重要作用,进而提高其他采掘设备,运输设备的效率。
关键词:露天矿爆破质量
影响露天矿爆破质量因素很多,主要有炸药性能,装药结构,地质条件等。
由于种种因素的影响,会造成大块,根底的产生,从而影响采装设备的效率。
如
何提高露天矿爆破质量已是当前露天矿山生产任务中比较突出的问题之一。
提高
爆破质量实质上就是要减少大块和根底。
[1]
1大块产生的部位和原因分析:
1.1产生的部位
不合格的大块主要产自同一爆区的软硬岩的分界处;台阶上部和台阶的坡面,爆区的后部边界。
1.2产生原因
(1)爆区软硬岩分界部分,易于振落。
(2)炸药能量分布不均,孔口部分能量不足。
(3)台阶前部,岩石受前次爆破的破坏,甚至被切割成块体,爆破时“块体”易整体振落成大块。
(4)爆区后的后部与未爆岩石相交也会产生一些因爆破而振落的大块。
2影响爆破破碎因素及提高爆破质量的措施
2.1、影响爆破破碎的主要因素
(1)自由面条件和结构面的影响:岩块的破裂面大多数是沿着岩体内的结构面形成。
(2)岩性的影响:大块率随岩石的硬度提高而增加。
(3)爆破单位耗药量:随着单耗的增加,大块率降低,对不同岩石,存在一个最佳的爆破单耗。
(4)炸药在掩体中的分布:随着炮孔直径的增加,大块比例随之上升。
(5)炮孔布置与装药结构:大块经常出现在没有装药的部位和两侧拉裂的部位。
2.2提高爆破质量的措施
(1)选准前排孔抵抗线;
在倾斜钻孔时,最小抵抗线在炮孔上、下各部位是相等的,计算抵抗线时应加上钻孔偏差;在垂直钻孔时,最小抵抗线部位由于临空条件好,故采用夹制作用大处的底盘抵抗线作为参数进行。
根据钻机型号、性能和体型以及操作人员的作业水平,为了确保在台阶边缘钻孔时的施工安全所确定的第一排炮孔至台阶边缘的距离就是眉线距离,对于大型设备一般大于等于2.5~3米。
(2)保证填塞质量,控制最后排孔的装药高度;
填塞长度是控制个别飞石的主要参数,确定合理的填塞长度和保证良好的填塞质量对改善爆破效果和提高炸药能量利用率具有重要作用。
1.
控制合理的超深;
超深指钻孔超出台阶底盘标高的那一段孔深,超深的作用在于降低装药中心位置,克服底盘岩石的夹制作用,使爆后少留或不留根底,以形成平整的底部平台。
当岩石松软时,取小值;岩石坚硬时,取大值。
(4)选取与岩石特性相匹配的炸药和装药结构,增强底部炸药的威力;
单耗的选取直接影响工程的炸药用量,在破碎爆破中,不同岩石都有一定范围的合理单耗值,低于合理值就会使爆破效果受到影响。
可以使用如下几种装药结构方式:
①连续装药结构:当孔深超过8m时,应布置两个起爆体。
②分段装药结构:将深孔种的药柱分为若干段,用空气间隔期隔开,可以提高装药高度,改善炮孔上部的破碎效果;躲开地质薄弱地段,可以节省炸药。
③混合装药结构:指孔底装高威力炸药,上部装普通炸药的一种装药结构,改善底部夹制作用大的部位的破碎效果,消除门坎,节省炸药。
[2](5)选取合理的毫秒微差延期间隔时间;
通常采用毫秒延时起爆网路,药包之间实施毫秒延时爆破是为了改善爆破效果和降低爆破震动。
基本思路是使每个炮孔都具备自由破碎的条件,孔间或排间要有一定的延迟时间,以保证后爆岩体具有侧向临空面。
从改善破碎效果着眼,前后段药包之间的延时时间应等于或接近可使用段药包承担的受爆体已经移动,后段药包的临空面已经形成的时间,使前段抛体达到最大抛速后,后段药包始起爆,后段抛体尽可能地尾随撞击前段抛体,减少能量渗漏,改善破碎效果,同时,先爆岩体能对后爆岩体起保护作用,可减少飞石产生。
目前国内采用孔内外延期爆破时多采用孔内高段位,孔外低段位雷管。
例如:孔内延期雷管为400ms,地表延期雷管延期时间25ms和42ms,排间延期雷管延期时间42ms,65ms,100ms。
1.
爆破有明显的结构面时,要根据岩体结构面的特征,决定起爆顺序;
首段雷管的位置直接控制爆堆的主体方向,同时其爆破效果对后续段别的钻孔爆破影响很大。
首段雷管应选择布置在台阶临空面条件比较好的部位,临空面
各部位的抵抗线大小应基本一致。
需要注意的是首段雷管钻孔处岩体的地质结构面,如断层、破碎带、节理面等的走向,以及环境条件,最小抵抗线方向应避开
建筑物,防止爆堆飞石对它们产生不利影响。
如果首段雷管部位临空面条件不好,可以布置首段雷管多排孔同时起爆,给后续段别创造较好的临空面。
网路设计尽可能整齐、规则、有利于检查,减少出错。
要使每个炮孔都具有
自由破碎的条件,在起爆网路布置就应尽量减少每个炮孔爆破时的夹制作用;如
果用导爆管雷管还需要考虑导爆管网路引爆后的3种状态,即①炮孔内雷管已爆
炸并引爆炸药产生爆轰;②地表接力雷管已被引爆,炮孔内雷管已点燃但延期体
仍在燃烧而未产生爆炸,炮孔内炸药尚未产生爆轰;③起爆信号尚未传播到,接
力雷管和网路种的导爆管雷管尚未被引爆。
要保证一定范围炮孔内雷管已点燃,
防止爆破应力波对网路破坏,或被爆介质错动而将网路切断或拉断,从而出现后
面炮孔的拒爆现象。
(7)在适宜的地点采取大孔距,小抵抗线和压渣爆破。
在保持炮孔负担面积s不变的前提下,加大孔距、减少抵抗线,即增大炮孔
密集系数m=a/b,(a-孔距,b-排距,s-孔担面积,m-炮孔密集系数)。
标准形式取m=1~1.25,宽孔距技术一般取m=3~4,个别情况可取m=6~8。
宽
孔距爆破头排孔和最后一排孔的抵抗线和孔间距需要按常规方法布孔,否则,过
小的抵抗线会增加飞石的危险,过宽的孔距会引起爆后破裂面的凹凸不平。
(8)严格的施工
主要指钻孔、装药和填塞三方面的作业,一定要按设计施工。
深孔台阶爆破
必须特别重视开挖台阶的形成。
台阶底板抵抗线多大,除爆破后形成根底,使机
械开挖无法顺利进行外,爆破时的底部夹制作用过大会严重影响爆破效果,并加
大后冲力。
底板抵抗线过大的地方,应视情况不同,分别采取加密炮孔,预拉底(即先
进行打眼放炮)、孔底扩壶或底部装密度大、威力高的炸药等方式来避免产生根
底。
炮孔布置要考虑每个炮孔都具备自由破碎的条件,一般后一排孔应比前一排孔两边各缩进半个孔间距。
为了控制爆破时的后冲,改善后排孔爆破效果,排数不宜过多,宜3~5排。
尽可能使炮孔在岩体中均匀分布;后排孔应布置在直线上以保证下一循环临空面的齐整。
(9)科学的管理
钻爆作业一体化,对施工作业人员和各工序环节做到分层管理,责任到人;严格执行质量管理体系和全方位监管。
严格遵守炮孔验收标准,保证孔深在允许误差范围内,发现不合格钻孔及时处理,未达到验收标准不得装药。
保证钻孔精度,在施工中精确逐孔放样,反馈设计与施工优化;通过爆破实时监控和科学管理,实现精细化的科学管理。
爆区台阶坡顶线、坡底线测量图应及时提供给爆破设计人员,以便调整装药量。
实践证明,通过以上技术措施可以达到提高爆破质量,保证爆破安全的目的。
参考文献
[1]陶颂霖.凿岩爆破[M].北京:煤炭工业出版社,1986.
[2]骆中洲.露天采矿学[M].徐州:中国矿业学院出版社,1986.。