DCS实验报告.pdf
DCS与工业组态软件实验报告

评分:DCS与工业组态软件实验报告学号:班别:姓名:实验一:硬件系统熟悉与操作一、实验目的:1、了解集散控制系统的组成和结构;2、熟悉系统规模、控制站规模;3、掌握控制站卡件型号、名称、性能及输入/输出点数;4、掌握控制站卡的地址设置。
二、实验内容:硬件简介:1、JX-300X DCS系统网结构如图1.1所示:图1.1 JX-300X DCS系统网结构示意图通讯网分为三层:信息管理、过程控制(SCnet II)和控制站内部I/O控制总线(SBUS)。
2、控制站卡件控制站卡件位于控制站卡件机笼里,主要由主控卡、数据转发卡和I/O卡组成。
卡件按一定的规则组合在一起,完成信号采集、信号处理、信号输出、控制、计算、通讯等功能。
控制站卡件一览表如表1.1所示:表1.1 控制站卡件一览表硬件选型:1、根据测点性质确定系统I/O卡件的类型及数量(适当留有余量),对于重要的信号点要考虑是否进行冗余配置;2、根据I/O卡件数量和工艺要求确定控制站和操作站的个数;3、根据上述设备的数量配置其它设备,如机柜、机笼、电源、操作台等;4、对于开关量,根据其数量和性质要考虑是否选配相应的端子板、转接端子和继电器。
Scnet II网络组件地址设置:对TCP/IP协议地址采用如表1.2所示的系统约定:表1.2系统约定的参数网络码128.128.1和128.128.2代表两个互为冗余的网络。
在控制站表现为两个互为冗余的通讯口,上为128.128.1,下为128.128.2。
在操作站表现为两块网卡,每块网卡所代表的网络号由IP地址设置决定。
三、实验条件:1、JX-300X集散控制系统一套2、DELL工控机计算机一台3、JX-300X DCS系统组态软件包一套四、实验练习:1、参考实验四的工程项目进行硬件配置。
2、TCP/IP协议地址的系统约定。
五、思考题:1、硬件选型时,I/O卡件选型的主要依据是什么?实验二:JX-300系统的组态设计一、实验目的:1、了解JX-300X系统组态软件包;2、掌握控制站、操作站等硬件设备在软件中的配置;3、掌握I/O设备、信号参数的设置。
XXXX电厂DCS考核试验报告
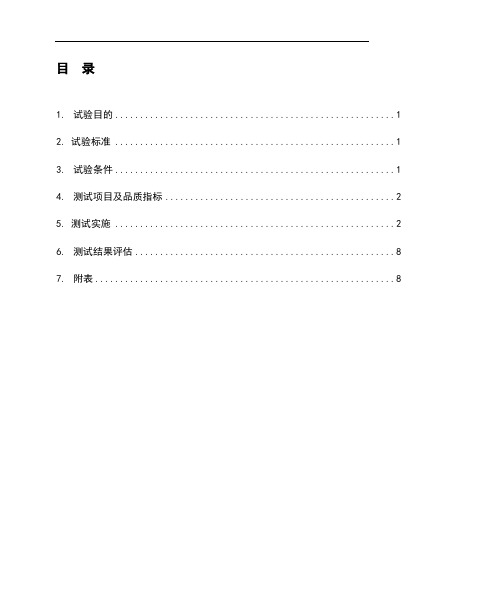
目录1.试验目的 (1)2. 试验标准 (1)3.试验条件 (1)4.测试项目及品质指标 (2)5. 测试实施 (2)6.测试结果评估 (8)7.附表 (8)1. 试验目的本试验通过对控制系统的在线测试,确认其有关功能、性能是否达到工程合同或电力行业标准要求,能否满足机组安全、经济运行的需要。
2. 试验标准试验参照标准为中华人民共和国电力行业标准DL/T 659-2006 《火力发电厂分散控制系统验收测试规程》(下称规程)。
3. 试验条件3.1 接入分散控制系统的全部现场设备,包括变送器、执行器、接线箱以及电缆等设备均应按照有关标准进行安装、调试、试运行并按DL/T 5190.5要求验收合格。
3.2 分散控制系统的硬件和软件应按照制造厂的说明书和有关标准完成安装和调试,并投入连续运行。
3.3 机组及辅机在试生产阶段中已经稳定运行,DCS随机组连续运行时间超过7天或累计60天。
3.4 DCS的运行环境符合DL/T774的规定,投入运行后的运行记录应完整。
DCS供电电源品质应符合制造厂技术条件。
3.5 DCS中央处理单元(CPU)负荷率、通信负利率的测试方法由DCS厂家提供。
如DCS厂家不能提供测试方法,由用户确定测试方法,作为考核标准。
3.6 DCS的接地应符合制造厂的技术条件和有关标准的规定。
屏蔽电缆的屏蔽层应单点接地。
若DCS采用独立接地网,若制造厂无特殊要求,则其接地极应与电厂电气接地网之间保持10m以上距离,且接地电阻不应大于2Ω。
若DCS与电厂电气系统共用一个接地网,控制系统接地网与电气接地网只允许有一个连接点,且接地电阻应小于0.5Ω。
3.7 试验用仪器仪表。
特稳携式校验仪(准确度:0.01%)秒表(精度:0.01s);数字万用表(精度:位);SOE分辨力测试仪(准确度:0.05ms);步话机(功率5W、频率400MHz~500MHz);上述仪器仪表均具备有效的合格证书。
4. 测试项目及品质指标4.1 功能测试●输入和输出功能检查●人机接口功能检查●显示功能检查●打印和制表功能检查●事故顺序记录和事故追忆功能检查●历史数据存储功能检查●全球定位系统(GPS)功能检查4.2 性能测试●系统容错(冗余)能力的测试●供电系统切换功能的测试●模件可维护性测试●系统储备容量测试●系统实时性测试●系统各部件的负荷测试4.3 抗干扰能力测试DCS控制系统抗干扰能力应符合行业标准的要求,其有关性能的品质指标参见第5节“测试实施”中的有关条款。
dcs实训报告2000字
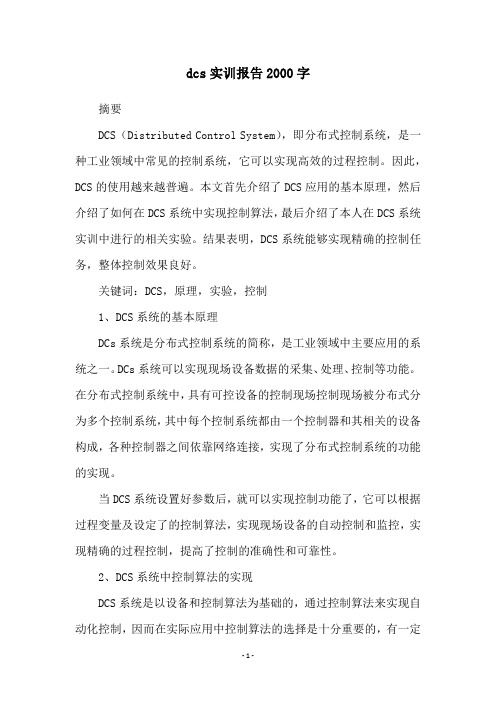
dcs实训报告2000字摘要DCS(Distributed Control System),即分布式控制系统,是一种工业领域中常见的控制系统,它可以实现高效的过程控制。
因此,DCS的使用越来越普遍。
本文首先介绍了DCS应用的基本原理,然后介绍了如何在DCS系统中实现控制算法,最后介绍了本人在DCS系统实训中进行的相关实验。
结果表明,DCS系统能够实现精确的控制任务,整体控制效果良好。
关键词:DCS,原理,实验,控制1、DCS系统的基本原理DCs系统是分布式控制系统的简称,是工业领域中主要应用的系统之一。
DCs系统可以实现现场设备数据的采集、处理、控制等功能。
在分布式控制系统中,具有可控设备的控制现场控制现场被分布式分为多个控制系统,其中每个控制系统都由一个控制器和其相关的设备构成,各种控制器之间依靠网络连接,实现了分布式控制系统的功能的实现。
当DCS系统设置好参数后,就可以实现控制功能了,它可以根据过程变量及设定了的控制算法,实现现场设备的自动控制和监控,实现精确的过程控制,提高了控制的准确性和可靠性。
2、DCS系统中控制算法的实现DCS系统是以设备和控制算法为基础的,通过控制算法来实现自动化控制,因而在实际应用中控制算法的选择是十分重要的,有一定的计算复杂度和计算负荷要求。
控制系统中可以使用常见的算法来实现控制,如PID(比例-积分-微分)控制和状态反馈控制,这些控制算法都能够实现更精确的控制,控制精度更高,且可以根据实际的需求进行修改。
3、DCS系统实训实验为了更好的了解DCS系统,本人在大学实习期间进行了DCS系统的实训实验。
实验中使用了瑞普特(Riptise)DCS系统,通过实验,可以有效地说明DCS系统的基本原理以及实现技术。
首先,根据实验要求,按照实验指导书的指示进行系统构建,实现过程控制系统的建立。
其次,在实验中,使用Riptise仿真工具,实现流程控制系统的仿真,并进行实验,以确定该系统的建立是否正确。
dcs实训总结

dcs实训总结DCS实训总结1. 前言在大学期间,我们不仅要学习理论知识,还需要掌握实践技能。
而DCS实训就是一种非常重要的实践活动。
在这次实训中,我深刻体会到了理论知识与实践技能的紧密联系,也收获了很多宝贵的经验和教训。
2. 实训内容本次DCS实训主要包括以下内容:(1)DCS基础知识:包括什么是DCS、DCS的组成部分、DCS系统的工作原理等。
(2)DCS软件:包括控制逻辑编写、控制策略设计、参数设置等。
(3)现场设备调试:包括现场设备安装调试、信号调整等。
(4)系统联调测试:包括系统联调测试、功能测试等。
3. 实训过程在实训过程中,我们首先学习了DCS基础知识。
通过老师的讲解和自己的学习,我们初步了解了什么是DCS以及它的组成部分。
接着,我们开始学习DCS软件。
老师详细介绍了控制逻辑编写、控制策略设计和参数设置等方面的知识,并通过实例演示了如何使用DCS软件进行控制逻辑编写和策略设计。
在这个阶段,我们也开始了自己的实践操作,通过模拟实验来掌握软件的使用方法。
在学习软件的过程中,我们还需要进行现场设备调试。
这一环节是非常重要的,因为只有将软件和硬件结合起来才能真正发挥DCS系统的作用。
在现场设备调试中,我们需要安装设备、调整信号等,以确保系统能够正常运行。
最后,我们进行了系统联调测试和功能测试。
这个阶段是整个实训过程中最重要的部分之一。
在测试过程中,我们需要测试DCS系统是否能够正常运行、控制策略是否正确、参数设置是否合理等方面的问题。
通过测试,我们可以发现问题并及时解决。
4. 实训收获通过这次DCS实训,我收获了很多宝贵的经验和教训。
首先,在学习软件方面,我深刻认识到理论知识与实践技能之间的联系是非常紧密的。
只有将理论知识应用到实践中去才能真正掌握它们。
其次,在现场设备调试方面,我也学到了很多。
在实践中,我们需要注意安全、细心认真地调试信号等,以确保系统能够正常运行。
最后,在测试方面,我也有了更深刻的认识。
DCS实习报告【范本模板】

计算机控制技术实习报告班级:电气1331班小组成员:罗欢、刘双、罗鸣指导教师:胡乃清、熊媛媛实习地点:实B301一、实习目的1熟悉集散控制系统(DCS)的组成2掌握Advan Trol Por组态软件的使用方法。
3培养灵活组态的能力。
4掌握系统组态与装置调试的技能。
二、实训内容以CS2000型实训装置为对象,按照实习任务书利用Advan Trol Por组态软件完成组态包括:1 数据库组态2 设备组态3控制器算法组态4 画面组态5 系统调试实习任务书如下:CS2000型实训装置DCS控制系统设计与调试任务书1.装置简述CS2000型实训装置是我院所购的微型装置,主要包括水槽、水箱、锅炉、换热器等对象。
它还集成了差压式流量计、涡轮流量计、液位计、热电阻等检测仪表,还集成了电动调节阀、变频泵、交流调压模块等执行器。
可配调节仪表或DCS实现常规仪表控制和DCS控制。
可实现的主要控制方案包括:液位单回路控制、流量单回路控制、流量—液位串级控制、液位—液位串级控制、前馈控制、温度单回路控制、流量比值控制.2.项目要求:要求按照DCS工程项目的设计、施工流程完成以下工作:(1)用户管理要求见表1表1 CS2000DCS系统用户管理要求表(2)按照表2所见的测点配置清单完成I/O组态表2 CS2000DCS系统测点配置清单(4)控制站及操作站配置✓项目由1个控制站、1个工程师站构成✓控制站地址根据网络确定(为02或04或06),工程师站地址设为本机地址. ✓要求主控卡、电源、数据转发卡、网络均冗余配置✓利用工程师站或操作员站可查看水箱和换热器的所有过程参数和画面(5)数据分为锅炉数据组和液位数据组, 炉数据组分为锅炉、换热器两个数据区;水箱操作小组设置液位数据组,液位数据组分为流量、液位数据区。
(6)工程师操作小组要求见表4表4 CS2000操作小组设置表A在工程师操作小组下绘制相关回路流程图B在分组画面第二页中显示累积量C添加液位的动画效果。
DCS实验报告刘金琳

集散控制系统实验报告姓名刘金琳学号 10S030097 2011年4月实验一 分布式网络伺服控制系统实验目的:1. 熟悉TureTime 仿真软件的安装和基本使用操作;2. 熟悉网络控制系统的仿真;3. 分析网络流量和调度策略对分布式网络控制系统时延和控制性能的影响。
实验内容: 设直流伺服系统的连续时间传递函数为:)1(1000)(+=s s s G ,采用四个计算机节点来实现该系统,一个时间驱动的传感器节点周期性地对过程进行采样,并通过网络把采样结果送到控制器。
控制节点计算控制信号并把结果送到执行器节点,产生连续执行结果。
还有一个节点模拟网络中的额外流量,并在控制器节点运行高优先级的任务模拟网络节点的任务分配。
实验步骤:1. 安装TrueTime 仿真软件包,设置系统环境变量,运行Matlab 初始化命令;2. 根据$DIR/examples/simple_pid/matlab 中的直流伺服过程PID 控制的实例,熟悉Truetime 的仿真操作;3. 按照试验内容建立仿真系统,给出Simulink 仿真框图;4. 首先考察没有额外网络流量,而且控制器节点也没有额外任务的情况,观察系统运行的延迟时间和控制性能,给出相关结果;5. 打开额外网络流量,而且控制器节点也增加额外任务,采用两种不同的网络协议,和两种不同的调度策略,观察系统运行延迟时间和控制性能,给出相关结果并分析原因。
实验结果与分析:1分布式网络伺服控制系统仿真框图如下:2 仿真结果及分析:2.1 设额外网络流量为零(BWshare=0.0),且控制器节点也没有额外任务的情况下,选择网络协议为:CSMA/AMP(CAN),调度策略为‘prioFP’,其输入,输出曲线如下图所示: 延迟时间为0.03s,超调量为20%,上升时间约为0.05s,调整时间约为0.11s,控制性能好.2.2 设额外网络流量为0.1(BWshare=0.1),且控制器节点增加额外任务的情况下,选择网络协议为:CSMA/AMP(CAN),调度策略为‘prioFP’,其输入,输出曲线如下图所示: 延迟时间为0.03s,超调量为15%,上升时间约为0.05s,调整时间约为0.17s,控制性能较好.2.3 设额外网络流量为0.2(BWshare=0.2),且控制器节点增加额外任务的情况下,选择网络协议为:CSMA/AMP(CAN),调度策略为‘prioRM’,其输入,输出曲线如下图所示: 延迟时间为0.03s,超调量为20%,上升时间约为0.05s,调整时间约为0.15s,控制性能较好.2.4 设额外网络流量为0.2(BWshare=0.2),且控制器节点增加额外任务的情况下,选择网络协议为:Round Robin,调度策略为‘prioFP’,其输入,输出曲线如下图所示: 延迟时间为0.035s,超调量为50%,上升时间约为0.05s,调整时间约较长,控制性能差.2.5设额外网络流量为0.2(BWshare=0.2),且控制器节点增加额外任务的情况下,选择网络协议为:Round Robin,调度策略为‘prioRM’,其输入,输出曲线如下图所示: 延迟时间为0.035s,超调量大于50%,上升时间约为0.05s,调整时间较长,控制性能差.由以上四幅曲线图可以看出,图2.3和图2.4曲线的超调量和调整时间明显比图2.1和图2.2的数值大.因此当分布式网络伺服控制系统的网络协议选择CSMA/AMP(CAN)时,其控制性能明显比选择Round Robin网络协议的系统好.同时,比较图2.1和图2.2(或图2.3与图2.4)的曲线, 其曲线的分布相似.综上所述,可以得出以下结论网络协议的选择对系统控制性能起决定性作用,而且对于同一网络协议,选择不同的调度策略对系统的控制性能影响较小.实验二分布式无线网络控制系统实验目的:1.熟悉无线网络控制系统的仿真操作;2.熟悉电源模块的使用方法;3.分析不同网络协议和参数对分布式无线网络控制系统时延和控制性能的影响。
DCS实习报告

计算机控制技术实习报告班级:电气1331班小组成员:罗欢、刘双、罗鸣指导教师:胡乃清、熊媛媛实习地点:实B301一、实习目的1熟悉集散控制系统(DCS)的组成2掌握Advan Trol Por组态软件的使用方法。
3培养灵活组态的能力。
4掌握系统组态与装置调试的技能。
二、实训内容以CS2000型实训装置为对象,按照实习任务书利用Advan Trol Por组态软件完成组态包括:1 数据库组态2 设备组态3控制器算法组态4 画面组态5 系统调试实习任务书如下:CS2000型实训装置DCS控制系统设计与调试任务书1.装置简述CS2000型实训装置是我院所购的微型装置,主要包括水槽、水箱、锅炉、换热器等对象。
它还集成了差压式流量计、涡轮流量计、液位计、热电阻等检测仪表,还集成了电动调节阀、变频泵、交流调压模块等执行器。
可配调节仪表或DCS实现常规仪表控制和DCS控制。
可实现的主要控制方案包括:液位单回路控制、流量单回路控制、流量—液位串级控制、液位—液位串级控制、前馈控制、温度单回路控制、流量比值控制。
2.项目要求:要求按照DCS工程项目的设计、施工流程完成以下工作:(1)用户管理要求见表1表1 CS2000DCS系统用户管理要求表(2)按照表2所见的测点配置清单完成I/O组态表2 CS2000DCS系统测点配置清单(4)控制站及操作站配置✓项目由1个控制站、1个工程师站构成✓控制站地址根据网络确定(为02或04或06),工程师站地址设为本机地址。
✓要求主控卡、电源、数据转发卡、网络均冗余配置✓利用工程师站或操作员站可查看水箱和换热器的所有过程参数和画面(5)数据分为锅炉数据组和液位数据组, 炉数据组分为锅炉、换热器两个数据区;水箱操作小组设置液位数据组,液位数据组分为流量、液位数据区。
(6)工程师操作小组要求见表4表4 CS2000操作小组设置表A在工程师操作小组下绘制相关回路流程图B在分组画面第二页中显示累积量C添加液位的动画效果。
DCS实训报告

一、脱丙烷塔工艺简介
二、设计要求
1、控制方案
2、用户管理要求
3、监控画面要求
4、工程师小组要求(反应小组、冷凝回流小组);此处两个人写反应小组,两个人写冷凝回流小组;
三、集散控制系统
1、集散控制系统简介
2、浙大中控JX-300XP
四、硬件选择与安装
1、卡件选择(包含测点清单)
2、硬件安装
五、系统组态
1、工程设计
2、用户授权管理
3、系统总体组态
4、操作小组设置
5、数据组(区)设置
6、控制站I/O组态
7、控制站自定义变量组态
8、常规控制方案组态
9、自定义控制方案组态
10、二次计算组态
11、操作站标准画面组态
12、流程图制作
13、报表制作
14、系统组态保存与编译
15、系统组态传送与下载
16、系统监控调试
六、CS6000过程控制系统实验
1、CS6000过程控制系统介绍
2、金属管浮子流量控制
3、液位水箱自动控制实验
七、课程设计不足与改进
八、课程设计心得体会
九、附录
1、测点清单
2、卡件配置表
3、点数与卡件统计表
4、系统规模配置表
5、系统I/O卡件布置图
6、控制方案流程图。
DCS实训报告
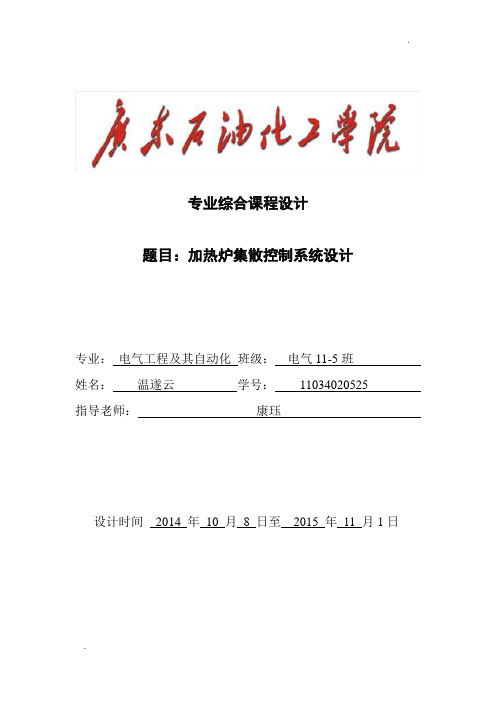
专业综合课程设计题目:加热炉集散控制系统设计专业:电气工程及其自动化班级:电气11-5班姓名:温遂云学号:11034020525指导老师:康珏设计时间2014 年10 月8 日至2015 年11 月1日.目录摘要 (2)关键词 (2)正文 (2)JX-300XP概述 (2)各操作站作用 (3)I/O卡件机笼包括卡件组成以及它们的功能 (4)JX-300X DCS系统的组态软件包各软件的作用 (5)JX-300X DCS系统通信网络的构成及其各个部分的基本特性 (5)项目的设计 (6)工艺简介 (6)加热炉控制流程图 (6)控制方案 (6)原料油罐液位控制 (6)原料加热炉烟气压力控制 (7)原料加热炉出口温度控制 (7)控制站及操作站配置 (7)系统组态 (8)新建一个组态 (8)I/O组态 (8)操作小组的组态 (11)常规控制方案的组态 (12)创建数据组(区) (14)位号的区域划分 (15)光字牌设置 (16)设置网络策略 (16)操作站标准画面组态 (16)流程图的制作 (18)报表的制作 (20)下载调试 (22)组态的编译和下载 (22)手操器检测系统工作是否正常 (22)图形化编程 (23)基本步骤 (23)常用的图形编程模块 (25)应用举例 (26)参考文献 (27)心得 (27)附录1-卡件的选择 (28)附录2-测点清单 (30)实验十(空气压力控制实验) (30)实验目的 (30)实验设备 (30)实验原理 (30)压力基本回路控制工段 (31)实验内容与步骤 (32)实验数据处理 (34)实验心得体会 (35)摘要集散控制系统是一个由过程控制级和过程监控级组成的以通信网络为纽带的多级计算机系统,综合了计算机,通信、显示和控制等4C技术,其基本思想是分散控制、集中操作、分级管理、配置灵活以及组态方便。
JX-300XP集散控制系统属于浙大中控SUPCON技术有限公司WebField系列,它是在JX-100、200、300、330的基础上开发出来的新一代集散控制系统。
DCS实验报告

集散控制系统实验报告学院:电子信息与电气工程学院学生姓名:***学号:专业班级:合作者:崔俭俭朱雪扬指导教师:***时间:2015年10月27日蒸发器控制系统一、实训目的(1)熟悉集散控制系统(DCS)的组成;(2)学习、掌握集散控制系统硬件选型和系统配置方法;(3)掌握MACS组态软件的使用方法;(4)培养灵活组态的能力及DCS系统调试技能。
二、实训流程及内容利用实验室内的THSA-1型生产过程自动化技术综合实训装置,以及和利时的MACS系统进行组态实训,内容包括:(1)设备选型及系统配置(2)数据库组态、设备组态(3)算法组态(4)图形组态(5)系统调试三、实训设备和器材(1)THSA-1型生产过程自动化技术综合实训装置(2)和利时DCS现场控制站四、实训接线将过程连接电缆接到和利时DCS控制装置电缆接口。
五、实训步骤1、工程描述及工程分析以所给反应器工艺控制流程为工业背景,构建集散控制系统,实现图中所要求的功能。
要求:1)系统配置要求:一个现场控制站,二个操作员站,一台服务器,不冗余2)系统的硬件构成—型号及数量,给出配置原理图3)完成系统组态,并实现图中所示的控制功能工程分析:从所给工艺流程可知,共有13个温度测点、5个压力测点、3个流量测点,5个阀门。
压力和流量的测量在现场控制中由器件直接转化为标准电信号,可直接输入FM148A模块,该模块为8路高电平输入模块,由压力和流量输入点个数决定需要1个FM148A;温度不能直接传送信号,需使用热电阻输入模块FM143进行传送,该模块为8路,所以由温度指示点个数决定应使用2个;输出模块FM151则用于5个输出点。
因此该系统需要四个模块,其中二个FM143A和一个FM148A用于采集温度、压力、流量,一个FM151用于控制电动阀的开度。
系统构成框图如下所示:2、建立工程新建一工程,命名为reactor system,并编辑域组号为1。
3、设备组态为系统内的所有设备包括服务器、操作站、控制站、输入输出模块指定地址,从而建立他们之间的联系。
p3dcs实验报告

一、课程设计目的采用P3DCS系统设计完成水箱水位串级控制系统并进行参数整定和调试,包括数据库组态,SAMA图组态,流程图组态,操作器组态,设计手动和单回路自动控制,串级自动控制等控制方案,并实现手自动无扰切换和报警,设计相应的模拟量控制和逻辑控制方案并实现,进行仿真,参数整定与系统调试。
二、课程设计过程运行P3DCS软件,首先进行I/O配置:点击系统数据库图标,进行各参数的点名与说明。
由于本次设计要求是双容水箱串级控制系统,所以数值量有上水箱水位PV2、下水箱水位PV1、设定值SP、控制器输出AO等,逻辑量有控制器状态DO等。
保存后关闭窗口,进行SAMA图组态的制作。
如下图所示:点击SAMA图组态图标,打开SAMA图制作窗口。
SAMA图组态用于将系统内部定义的功能算法模块按照逻辑组合起来,编译下装到过程控制站中进行调用和执行。
由于本次课程设计是串级回路控制系统,所以我采用系统自带的2个PID功能块、1个M/A手操器功能块和若干线性功能块来构成SAMA图的基本框架。
PID1(左)用于控制下水箱水位,PID2(右)用于控制上水箱水位,M/A用于设定下水箱的目标值,线性功能块用于代表被控对象的特性。
根据串级回路的结构特点,绘制SAMA图如下所示:将各功能块的参数设为需要的值,并将其与数据库中的数据点一一对应,再用输入输出功能块引出,连接到显示界面。
TR为跟踪接口,用于实现控制器的手动/自动的无扰切换。
保存后关闭窗口,接着进行图形界面组态的运用。
用矩形、棒状图和折线绘制双容水箱、进出水管,阀门等,实时曲线绘制黑色表格。
将水箱与对应的数据点连接起来,PV1对应下水箱,PV2对应上水箱,并设定上下限与填充色。
实时曲线也同样与数据点对应,设置上下限与颜色。
其效果图如下:保存文件,接着绘制操作器显示界面。
同样用矩形和棒状图绘制操作器数值显示条,并将其与各模拟数据点一一对应,设置上下限并填充颜色。
指示灯用于指示控制器工作状态,6个按钮用于自动控制时增减设定值,手动控制时增减控制器输出。
集散控制系统实训报告
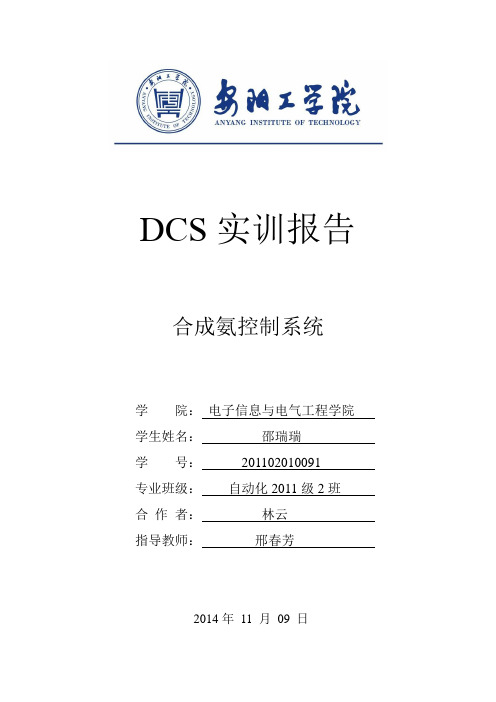
DCS实训报告合成氨控制系统学院:电子信息与电气工程学院学生姓名:邵瑞瑞学号:201102010091专业班级:自动化2011级2班合作者:林云指导教师:邢春芳2014年11 月09 日一、系统构成和利时公司的MACS集散系统,由4台操作员站兼工程师站、一台服务器、一台远程主控单元、和三个现场总线远程I/O模块,其中FM148为8路模拟量输入模块、FM143为8路热电阻输入模块、FM151为8路模拟量输出模块。
图1所示为MACSV系统结构图。
图1 DCS分布式系统框图二、实训目的(1)熟悉集散控制系统(DCS)的组成(2)学习、掌握集散控制系统硬件选型和系统配置方法(3)掌握MACSV组态软件的使用方法(4)培养灵活组态的能力及系统调试技能三、实训流程及内容以THSA-1型生产过程自动化技术综合实训装置为工业对象。
完成合成氨工艺控制流程系统的组态。
要求:设计合成氨工艺流程控制系统,并用MACS组态软件完成组态。
包括:(1)设备选型及系统配置:一个现场控制站,二,个操作员站,一台服务器,不冗余。
(2)数据库组态、设备组态。
(3)算法组态。
(4)画面组态。
(5)系统调试。
四、实训步骤1. 工程分析合成氨工艺流程控制系统需要7个流量测量输入信号,8个压强测量输入信号,7个温度测量输入信号,两个输出测量信号。
因此需要两个模拟量输入模块FM148、一个热电阻输入模块FM143和一个模拟量输出模块FM151,分别用来采集系统由一个主控单元FM801、一个D电源模块FM910和一台计算机(兼作服务器和操作员站)构成。
2.工程建立(1)打开:开始程序macsv组态软件数据库总控。
(2)选择工程/新建工程,新建工程并输入工程名:SR(3)点击“确定”按钮,然后在空白处选择“SR”工程。
显示当前域号为65535等信息。
(4)选择“编辑>域组号组态”,选择组号为1,将刚创建的工程“SR”从“未分组的域”移到右边“改组所包含的域”里,点击“确认”按钮。
DCS实验报告

DCS实验报告dcS实验报告凝结水泵监控一、数据库总控工程建立1.打开-》开始》程序》macsv组态软件》数据库总控。
2.新建工程,输入工程名字。
3.选择“编辑>域组号组态”,选择编辑用的域组号。
4.在数据库总控组态中添加变量。
5.选择工具栏数据操作按钮,出现下面对话框,点击“确定”按钮。
6.选择需要的”ai””di””do”7.数据库编辑(如下图):()8.数据库编辑,注意:设置它的参数,根据实际情况,设置设备号(设备地址),通道号,量程上限下限,点名。
其他的可以不用设置。
(注意:点名不能重复使用)按照上面的步骤设置所有的变量,包括模拟量的输入和输出。
9.添加好变量后更新数据库。
二、设备组态步骤1.打开“设备组态工具”打开“开始》程序》macsv组态软件》设备组态工具”。
2.出现下图,选择“233”后点击“确定”按钮。
3.选择菜单栏编辑/系统设备。
设置上层的以太网网络。
点击“下一步”。
4.出现macS设备组态;5.选择菜单栏编辑/i/o设备。
设置下层的dP网络。
右健,添加设备,添加使用到的设备;三、服务器算法组态步骤1.打开服务器算法组态,在菜单栏中选择文件/新建工程,选择刚才新建的工程。
下页dcS实验报告2.点击新建站按钮,新建的站装目录下。
点击“保存”按钮。
3.对233站,与其下的服务器进行编译。
完成后如下图所示。
四、控制器算法组态步骤1.单击桌面上的“开始”》“程序”》“macV组态软件”》“控制器算法组态”,弹出工程选择窗口:3.选中控制站后点击“确定”按钮,控制器算法软件即被启动(注意此前一定要先进行目标安装,安装后在c盘根目录下会生成有TaRGET 文件夹)。
4.添加所需要的函数库。
5.在资源—全局变量中,如图所示声明变量。
注意:一条声明要写在一行中。
DCS实验报告

华北电力大学实验报告实验名称基于DCS实验平台实现的水箱液位控制系统综合设计课程名称计算机控制技术与系统专业班级:自动实 1101学生姓名:潘浩学号:201102030117成绩:指导教师:刘延泉实验日期:2014/6/29基于DCS实验平台实现的水箱液位控制系统综合设计一.实验目的通过使用LN2000分散控制系统对水箱水位进行控制,熟悉掌握DCS控制系统基本设计过程。
二.实验设备PCS过程控制实验装置;LN2000 DCS系统;上位机(操作员站)三.系统控制原理采用DCS控制,将上水箱液位控制在设定高度。
将液位信号输出给DCS,根据PID参数进行运算,输出信号给电动调节阀,由DDF电动阀来控制水泵的进水流量,从而达到控制设定液位基本恒定的目的。
系统控制框图如下:四.控制方案改进可考虑在现有控制方案基础上,将给水增压泵流量信号引入作为导前微分或控制器输出前馈补偿信号。
五.操作员站监控画面组态本设计要求设计关于上水箱水位的简单流程图画面(包含参数显示)、操作画面,并把有关的动态点同控制算法连接起来。
1.工艺流程画面组态在LN2000上设计简单形象的流程图,并在图中能够显示需要监视的数据。
要求:界面上显示所有的测点数值(共4个),例如水位、开度、流量等;执行机构运行时为红色,停止时为绿色;阀门手动时为绿色,自动时为红色。
2.操作器画面组态与SAMA图对应,需要设计的操作器包括增压泵及水箱水位控制DDF阀手操器:A.设备驱动器的组态过程:添加启动、停止、确认按钮(启动时为红色,停止和确认时为绿色)添加启停状态开关量显示(已启时为红色,已停时为绿色)B.M/A手操器的组态过程:PV(测量值)、SP(设定值)、OUT(输出值)的动态数据显示,标明单位,以上三个量的棒状图动态显示,设好最大填充值和最大值;手、自动按钮(手动时为1,显示绿色;自动时为0,显示红色),以及SP、OUT的增减按钮;SP(设定值)、OUT(输出值)的直接给值(用数字键盘)3.趋势画面组态趋势显示--新建实时趋势—添加三个观察数据点:上水箱水位、上水箱水位设定值和DDF电动阀开度电动阀投自动后设给定值SP,上水箱水位PV应逐渐逼近设定值SP对于趋势画面组态来说,我们可以看见图中有很多如“加长”“缩短”“放大”“缩小”等按钮,可以在我们需要的时候对我们所观察的图像曲线进行一定的加工,以期能够得到更好的观察结果。
dcs实验报告

dcs实验报告
DCS实验报告
实验目的:通过DCS(分布式控制系统)的实验,探索其在工业控制领域的应
用及性能表现。
实验设备:我们使用了一套由DCS控制器、传感器、执行器等组成的工业控制
系统,并搭建了一个简单的模拟工业生产线。
实验过程:在实验过程中,我们首先对DCS控制器进行了配置和编程,设置了
一些基本的控制逻辑和参数。
然后,我们将传感器和执行器连接到DCS控制器,并进行了调试和测试。
最后,我们模拟了一些常见的工业生产场景,如温度控制、液位控制等,通过DCS控制器对生产线进行了控制和监控。
实验结果:通过实验,我们发现DCS在工业控制领域具有以下优点:首先,DCS可以实现分布式控制,多个控制器可以相互通信和协作,提高了系统的灵
活性和可靠性;其次,DCS具有强大的数据采集和处理能力,可以实时监控和
分析生产过程中的数据,为生产过程的优化提供了有力支持;此外,DCS还具
有良好的扩展性和可维护性,可以方便地进行系统升级和维护。
结论:通过本次实验,我们认为DCS在工业控制领域具有广阔的应用前景,可
以为工业生产带来更高的效率和更好的控制性能。
我们将继续深入研究DCS在
实际生产中的应用,并不断优化和完善其性能,以更好地满足工业生产的需求。
dcs画面响应时间试验报告

dcs画面响应时间试验报告DCS画面响应时间试验报告随着工业自动化的发展,DCS(分布式控制系统)在工业生产中得到了广泛的应用。
DCS中的HMI(人机界面)是工厂操作员与控制系统之间的桥梁,可以通过它来实现对工厂的实时监控与控制。
在HMI中,画面响应时间是一个重要的性能指标。
本文通过对DCS 画面响应时间进行试验,来了解其对HMI性能的影响。
一、试验方案本次试验采用了台湾台达电子的DCS系统,其中HMI系统使用了iView SCADA软件。
我们对HMI系统中的画面响应时间进行了测试,测试方法如下:1. 选择一个具有代表性的画面作为测试对象,并记录该画面的元素数量和复杂度。
2. 在该画面中随机点击五个元素,并记录每个元素的响应时间。
3. 重复步骤2,共进行五次测试,并计算平均响应时间。
4. 改变HMI系统的配置,如增加元素数量、调整通信设置等,再次进行测试。
二、试验结果在本次试验中,我们进行了多组测试,并记录了各组测试的结果。
以下是其中一组测试结果:测试对象:生产线监控画面元素数量:30个响应时间(ms):125、140、130、135、132平均响应时间:132ms通过对不同画面的测试,我们得到了如下的结论:1. 画面中的元素数量和复杂度会影响响应时间。
当元素数量和复杂度增加时,响应时间也会相应增加。
2. 通信设置对响应时间也有影响。
当HMI系统与控制系统的通信速度变慢时,响应时间也会相应增加。
3. HMI软件的优化程度对响应时间也有影响。
优化程度较高的软件响应速度较快。
三、结论与建议通过本次试验,我们了解了DCS画面响应时间对HMI性能的影响。
为了提高HMI系统的响应速度,我们可以采取以下措施:1. 控制画面中元素的数量和复杂度,避免过多的元素导致系统负担过重。
2. 优化通信设置,尽量减少通信延迟。
3. 选择优化程度较高的HMI软件。
我们也应该注意到,HMI系统的响应速度不是唯一的性能指标。
在实际应用中,我们还需要考虑系统的稳定性、易用性、安全性等方面,综合考虑来选择最适合自己的HMI系统。
DCS系统综合实践过控报告

(封面)XXXXXXX学院DCS系统综合实践过控报告题目:院(系):专业班级:学生姓名:指导老师:时间:年月日综合实践过控报告实验目的1、熟悉A3000实验装置及过程控制实训装置的工艺流程。
2、熟悉使用浙大中控DCS系统,了解DCS系统的工作原理。
3、掌握使用DCS系统组态软件进行组态和设计控制系统基本过程。
4、在A3000实验装置或过程控制实训装置上完成对象特性测试及建模。
5、在A3000实验装置或过程控制实训装置上完成简单控制系统的设计与分析。
6、在A3000实验装置或过程控制实训装置上完成复杂控制系统的设计与分析。
7、深入理解控制器参数的调整原理。
实验内容1.熟悉工艺流程,绘制装置流程图。
(第1天)1.1工作内容(1)熟悉系统的工艺流程,了解装置上的检测点和执行机构并进行记录。
(2)了解装置上各个手动阀和泵的作用。
(3)了解电磁阀的作用和工作原理。
(4)了解变频泵的作用和工作原理(5)掌握如何开启、关闭系统。
(6)在前几步的基础上进行如下操作:a).使用工频支路给上水箱上水。
b).使用变频支路给上水箱上水。
c).使用工频支路给下水箱上水。
d).使用变频支路给下水箱上水。
(7)绘制整个工艺过程的工艺流程图1.2 思考题:如何控制上水箱的水位(给出设计方案)。
2.熟悉浙大中控DCS的设计环境及控制站组态、整合(第2-3天)2.1思考题:(1)什么是DCS?(2)控制站和操作站在整个系统中有何作用。
(3)“组态”的含义是什么?(4)主控卡的各种参数依据什么设定?(5)控制站组态的顺序?(6)I/O点的组态与DCS的硬件系统有何关系。
(7)流程图组态需要注意哪些事项。
(8)运行时流程图的动态效果是如何实现的。
(9)各种组态的作用。
(10)各种组态需要遵循的原则有哪些?(11)为何要进行系统整合?注意:在进行以上各项组态时,要理解各项组态的含义及作用,组态时要具有目的性。
答:(1)什么是DCSDCS是分布式控制系统的英文缩写(Distributed Control System),在国内自控行业又称之为集散控制系统。
DCS控制化工常减压精馏实训系统实习报告

DCS控制化工常减压精馏实训系统实习报告专业:应用化工与技术学生姓名:徐路实习目的将所学的理论知识与实践结合起来,培养勇于探索的创新精神、提高动手能力,加强社会活动能力,与严肃认真的学习态度,为以后专业实习和走上工作岗位打下坚实的基础。
通过两个月的实习使我们对生产乙酸乙酯有一定的感性和理性认识,打好日后进入工厂学习专业知识的基础。
同时实习使我们获得了对实际生产知识的认识和技能的提升。
培养了我们理论联系实际的能力,提高分析问题和解决问题的能力,增强了独立工作的能力。
最主要的是培养了我们与其他同学的团队合作、共同探讨、共同前进的精神。
具体如下:1、熟悉了生产乙酸乙酯的工艺流程、工艺设计、化工设备等。
2、了解了反应釜、精馏塔、等在实际生产的应用,作用等。
3、熟悉实习工厂的坏境,从而对工厂有一个更高的认识。
实习要求1.听从技术老师和企业工作人员的安排指导,有秩序,有礼貌,遵守实习工厂的相关规定。
2.认真听取技术老师的讲解介绍,并按照技术老师的规定和要求操作,掌握各种管道里的物质及输送方向。
有问题及时虚心提问,有意见建议要有礼貌地提出并做好相应的笔记。
3.认真学习乙酸乙酯的工艺流程,以其中双釜反应器相关知识,包括精馏塔的生产流程等。
实习内容、过程1、制备原理:乙酸乙酯的制取:先加乙醇,再加浓硫酸,最后加乙酸,然后加热。
乙酸的酯化反应制乙酸乙酯的方程式:CH3COOH+CH3CH2OH⇄CH3COOC2H5+H2O(可逆反应、加热、浓硫酸催化剂、吸水剂、)1:酯化反应是一个可逆反应。
为了提高酯的产量,必须尽量使反应向有利于生成酯的方向进行。
一般是使反应物酸和醇中的一种过量。
在工业生产中,究竟使哪种过量为好,一般视原料是否易得、价格是否便宜以及是否容易回收等具体情况而定。
2:制备乙酸乙酯时反应温度不宜过高,要保持在60 ℃~70 ℃左右,温度过高时会产生乙醚和亚硫酸等杂质。
2、实习内容a、掌握乙酸乙酯的工艺流程。
DCS实训报告

DCS实训报告姓名:魏鑫宇学号:200702010024院系:电子信息与电气工程学院一.实训目的(1)熟悉集散控制系统(DCS)的组成(2)掌握MACS组态软件的使用方法。
(3)培养灵活组态的能力。
(4)掌握系统组态与装置调试的技能。
二.实训内容以双容水箱为对象,设计液位串级控制系统,并利用MACS组态软件完成组态包括:1 数据库组态2 设备组态3控制器算法组态4 画面组态5 系统调试三.实训工程分析双容水箱液位定值控制系统需要二个输入测量信号,一个输出控制信号。
因此需要一个模拟量输入模块FM148A和一个模拟量输出模块FM151。
采集上水箱液位信号(LT1),下水箱液位信号(LT2)和控制电动控制阀的开度的控制信号(P1)。
通过以上分析可得:AI:LT1 1~5V(信号范围)0~20cm(量程)LT2 1~5V(信号范围)0~20cm(量程)AO:P1 4~20mA(信号范围)0~100%(量程)硬件的选取:(1)I/O:FM148A(一块)FM151A(一块)(2)主控模块:FM801(一块)(3)操作员站(一台)(4)工程师站(一台)控制原理框图:四.实训步骤1. 工程建立及数据库组态1)打开:开始 程序 macs 组态软件 数据库总控 点击新建工程,输入工程名如下图:2)选择新建工程,选择编辑>域号组态,选择组号为1,将刚创建的工程从“未分组的域”移到右边“该组所包含的域”里,点“确认”按钮。
出现当前域号:0。
3) 在数据库总控中添加变量。
选择编辑→编辑数据库,弹出窗口,输入用户名和口令bjhc/3dlcz。
进入数据库组态编辑窗口。
4) 选择系统→数据操作,出现下面对话框,点击“确定”按钮。
5) “AI模拟量输入”选项出现下图。
6) 选择所需项名,并更改相应数据及说明,如下图:7) 点击更新数据库。
8) “AO模拟量输出”同上,如下图:9) 点击更新数据库。
10) 单击数据库编译→基本编译,若显示数据库编译成功,则数据库组态完毕。
- 1、下载文档前请自行甄别文档内容的完整性,平台不提供额外的编辑、内容补充、找答案等附加服务。
- 2、"仅部分预览"的文档,不可在线预览部分如存在完整性等问题,可反馈申请退款(可完整预览的文档不适用该条件!)。
- 3、如文档侵犯您的权益,请联系客服反馈,我们会尽快为您处理(人工客服工作时间:9:00-18:30)。
四.控制方案改进可考虑在现有控制方案基础上,将给水增压泵流量信号引入作为导前微分或控制器输出前馈补偿信号。
五.操作员站监控画面组态本设计要求设计关于上水箱水位的简单流程图画面(包含参数显示)、操作画面,并把有关的动态点同控制算法连接起来。
1.工艺流程画面组态在LN2000上设计简单形象的流程图,并在图中能够显示需要监视的数据。
要求:界面上显示所有的测点数值(共4个),例如水位、开度、流量等;执行机构运行时为红色,停止时为绿色;阀门手动时为绿色,自动时为红色。
2.操作器画面组态与SAMA图对应,需要设计的操作器包括增压泵及水箱水位控制DDF阀手操器:A.设备驱动器的组态过程:添加启动、停止、确认按钮(启动时为红色,停止和确认时为绿色)添加启停状态开关量显示(已启时为红色,已停时为绿色)B.M/A手操器的组态过程:PV(测量值)、SP(设定值)、OUT(输出值)的动态数据显示,标明单位,以上三个量的棒状图动态显示,设好最大填充值和最大值;手、自动按钮(手动时为1,显示绿色;自动时为0,显示红色),以及SP、OUT的增减按钮;SP(设定值)、OUT(输出值)的直接给值(用数字键盘)3.趋势画面组态趋势显示--新建实时趋势—添加三个观察数据点:上水箱水位、上水箱水位设定值和DDF电动阀开度电动阀投自动后设给定值SP,上水箱水位PV应逐渐逼近设定值SP对于趋势画面组态来说,我们可以看见图中有很多如“加长”“缩短”“放大”“缩小”等按钮,可以在我们需要的时候对我们所观察的图像曲线进行一定的加工,以期能够得到更好的观察结果。
4.SAMA图组态本图为本次实验的上水箱水位控制SAMA图组态模块介绍:主要是AI、DI、AO、DO、AM、DM、PID 控制器、M/A手操器、设备驱动器,RS触发器、比较器模块,包括模块实现的功能及其输入输出中间参数。
(详见算法手册说明)本实验需要组态的有:(1)设备驱动器:电动门、增压泵(2)M/A手操器:水箱水位控制DDF阀手操器SAMA图功能说明:实现手自动无扰切换(利用跟踪),偏差大的时候切手动,增压泵流量只有在DDF电动阀有一定开度的时候才允许启动。
在给水流量为零的时候跳闸。
SAMA图设计思路说明:首先对上水箱水位进行测量,然后通过滤波环节处理后输入到PID的PV(过程变量)口。
同时对上水箱水位进行报警监测,当上水箱水位高于20cm的时候进行高水位报警。
PID控制器的输出输入到M/A站。
M/A输出上水箱水位设定值,一是提供给PID控制器作为SP的输入,二是将此设定值与上水箱水位实际值进行比较,如果两者偏差的绝对值大于5,则进行强制切手动动作。
PID控制器的TR口对M/A站的输出进行跟踪,同时M/A 站的SPT口也对实际的上水箱水位值进行跟踪(为了满足无扰动切换的要求)。
在操作员站发出手自动切换指令的时候,M/A站的S输出口发出指令,发到PID控制器的STR口进行手自动切换的动作(在发出M/A站进行手动控制的指令时,S输出开关量1,PID控制器STR口收到指令后停止动作,满足手动操作的要求;在操作员发出自动操作的指令的时候,S=0,PID控制器此时进行自动调节动作,M/A停止手动动作)。
同时,通过M/A站的输出,电动调节阀只有在电动调节阀开度大于一定程度(5%)的时候,会启动电源;也会在电动调节阀开度为零的时候,关闭电动调节阀的电源。
对增压泵控制的系统来说,只有当电动调节阀开度大于一定程度(5%)的时候,对泵发出启动指令的时候,可以启动增压泵。
如果当增压泵流量为零的时候增压泵的DEVICE模块的TOTP口得到1的开关量输入,会发发出停止增压泵的指令(即增压泵流量为零时跳闸)。
5.系统数据库数据库的组态一般分为两部分:数据采集测点的配置组态和中间计算点的组态。
中间计算点是为了图形数据显示所形成的统计计算点。
I/O测点清单如下:六.组态逻辑下装步骤(2号站):过程站操作——选择需要下装的站——下装备站——执行操作——切换主备站——执行操作——从主站复制到备站——执行操作——关闭。
1号站直接下装主站-执行操作。
七.系统运行调试实验系统调试实验主要包括以下内容:(1)观察过程参数显示是否正常、执行机构操作是否正常,是否按要求变化;(2)检查控制系统逻辑是否正确,并在适当时候投入自动运行;(3)系统扰动实验(水位给定值扰动、给水(上水/下水)阀门扰动);(4)增压泵流量信号:导前微分、前馈补偿扰动实验;(4)控制回路参数在线整定,PID参数可在线整定;(5)当系统存在较大问题时,如需进行控制结构修改、增加测点等,不能在线修改,应重新离线组态、编译、下装。
八.实际实验进程内容与所遇问题的解决办法及解释1.在对实际的水箱水位控制系统进行准确而仔细的分析后,先进行SAMA组态图的设计。
在设计SAMA图的过程中,需要对AI、DI、AO、DO、AM、DM、PID控制器、M/A手操器、设备驱动器,RS触发器、比较器模块,包括模块实现的功能及其输入输出中间参数有充分的理解和认识,并且在实验室中也通过对LN2000算法手册的阅读进行了相关的学习。
同时,本阶段需要完成的任务是对电动门,增压泵等设备驱动器环节和水箱水位控制DDF阀手操器的M/A环节进行组态。
在连线的过程中,一定要注意的是逻辑的合理性和连线的准确性。
逻辑的错误会导致控制效果的失败或错误。
而连线的时候需要对实线和虚线的连线给予充分的注意。
要对表示模拟量的实线和表示开关量的虚线拥有清晰的认知。
如AI模块的输出,AO模块的输入一定是实线(模拟量);DI模块的输出,DO模块的输入一定是虚线(开关量);比较器模块的输入一定是一个或者两个实线(模拟量),而其输出必然是能够表征其比较结果的开关量-虚线;同样的,针对PID控制器模块,M/A手操器模块和DEVICE 设备模块等输入输出口较多整体结构较为复杂的模块,更需要注意每个输入输出口是否正确的连接着对应的量,以及是否符合正确的逻辑。
只有这样,才能为接下来的实验打下坚实的基础。
2.对系统全局数据库组态进行研究认识(不要求手动配置)数据库的组态一般分为两部分:数据采集测点的配置组态和中间计算点的组态。
中间计算点是为了图形数据显示所形成的统计计算点。
诸如上水箱水位,下水箱水位和增压泵流量等模拟量输入数据便是数据采集测点能够得到并输入到数据库中的数据。
而上水箱水位设定值和上水箱水位控制手/自动信号即为中间计算点的中间变量,在之后的图形界面组态设计和趋势画面组态设计中相应曲线的实际数值来源。
正确认知哪些是模拟量,那些是开关量,那些是输入量,哪些是输出量,哪些是数值量,哪些是时间量,也有助于我们之后的设计中正确的关联相应的量,进行正确的操作。
3.对图形界面组态进行设计(工艺流程画面组态和操作器画面组态)本次的实验要求的是对单容水箱水位进行控制,即只对上水箱水位进行控制。
在本环节的设计过程中,遇到很多的问题,但经过细心的思考和老师的指导后,问题都得到了解决。
在工艺流程图设计中,一定正确的使用不同的模块来表示相应的实际器件,同时设置相应的颜色,关联相应的变量,然后正确使颜色随着量的不同值进行变化。
比如,在对多边形进行设计的时候,发现画完多边形之后无论使用什么办法都无法对多边形内的颜色进行填充。
后来,发现是由于软件缺陷,只能现在调色板内选好颜色,在进行多边形的设计,这样就可以得到期望颜色的多边形了。
还有,在使用棒图表征的上水箱中,关联了上水箱水位这个变量以后一定要对所关联量的上下限进行和理的设置,否则会在后面的运行中发现很低的上水箱水位便会导致工艺流程图中棒图表示的上水箱水位直接达到满值。
对于动态数据的关联也要注意准确性。
由于能够显示单位,我们在下装运行的时候也还是能够很清楚的看到动态数据的正确与否。
但是我们能够发现,在多次的下装运行之中,总会出现上水箱实际水位信号关联的动态数据会出现反应缓慢不灵敏,或者根本没有变化的情况。
后来经过老师的讲解,我认识到了这个是硬件和软件方面的缺陷,和主要逻辑与设计思路无关。
还有很多的很小但是也很重要的问题,都在经过思考后得到了有效的解决。
4.下装运行阶段(一号站)我所在组的一号站由于备用站无法使用,便能够直接进行下装运行操作。
由于我在当天上午便完成了主要的设计(先于同组其他的同学),便独自进行了多次的下装运行实验。
但是对于实验本身来说,一号站对应五个同学(五个操作员站/过程站),在同一段时期内,只能由一位操作员进行下装运行操作,其他的操作员不能进行相关操作,但是可以对系统数据以及相关的运行情况进行监控。
而对于二号站来说,正确的组态逻辑下装步骤是非常重要的:过程站操作——选择需要下装的站——下装备站——执行操作——切换主备站——执行操作——从主站复制到备站——执行操作——关闭。
在实验当天下午的时候,二号站的几位同学发现了二号站的五台操作员站只能有其中一个站可以之行下装运行操作。
后来经过同学们的讨论和老师的指导发现,二号站的操作员都必须正确的之行组态逻辑下装步骤,这样才能正常的之行下装运行才做。
而在同组别的操作员没有执行完操作之前,其余操作员是不允许进行下装运行操作的。
一旦进行,前一位操作员下装在站内的数据便会被当前操作员下装的数据覆盖。
同样的,也是由于软件方面的缺陷,对泵的启动与停止无法达到设计逻辑的要求。
而由于流量计的硬件缺陷,一号站的增压泵流量都会一直显示负值,这也是与控制逻辑不相符合的。
不过其余的逻辑都是满足要求的,偏差过大强制手动,以及泵的启动条件都是能够很好的实现。
在下装运行阶段,对SAMA图组态进行调试运行,对增压泵流量后的比较器模块进行强制输出为1(实际意义为此时的增压泵流量为零),增压泵即会停止下来,说明排除了软硬件方面的缺陷,本系统本身的设计逻辑是没有问题的。
5.对DCS系统的认识集散型控制系统(DCS)的实质是利用计算机技术对生产过程进行集中监视、操作、管理和现场前端分散控制相统一的新型控制技术。
它的出现是工业控制的一个里程碑。
工业过程控制的发展逐步从单机监控、直接数字控珠展到集散控制,也必将由集散控制进展到拥有更广阔应用前景的计算机集成制造,近几年的计算机集成制造(CIMS)技术的成就足以证明这一点。
DCS系统主要有现场控制站(I/O站)、数据通讯系统、人机接口单元(操作员站OPS、工程师站ENS)、机柜、电源等组成。
系统具备开放的体系结构,可以提供多层开放数据接口。
DCS的硬件系统在恶劣的工业现场具有高度的可靠性、维修方便、工艺先进。
底层汉化的软件平台具备强大的处理功能,并提供方便的组态复杂控制系统的能力与用户自主开发专用高级控制算法的支持能力;易于组态,易于使用。
支持多种现场总线标准以便适应未来的扩充需要。