显示技术半导体制程
半导体中段制程-概述说明以及解释

半导体中段制程-概述说明以及解释1.引言1.1 概述概述半导体中段制程是半导体制造过程中的一个重要阶段。
在半导体制造过程中,通常将整个过程分为前段制程、中段制程和后段制程三个阶段。
中段制程是在前段制程完成后,将晶圆表面的介电层、金属层等进行加工和处理的阶段。
在中段制程中,主要涉及到的工艺包括光刻、沉积、刻蚀、清洗等步骤。
光刻是中段制程中的重要步骤之一。
它通过使用光刻胶和掩模光罩,将光刻胶涂覆在晶圆表面上,并通过紫外光照射,将掩模上的图形转移到光刻胶上。
然后,通过化学处理,将光刻胶上未曝光部分或曝光后进行过浸蚀、清洗等处理,最终形成所需的图案。
沉积是中段制程中另一个重要的步骤。
它主要是将金属、介电材料等沉积在晶圆表面,形成所需的层。
常用的沉积方法包括物理气相沉积(PVD)、化学气相沉积(CVD)等,根据不同的材料和需求,选择适合的沉积方法。
刻蚀是中段制程的一项关键步骤,它通过使用化学气相或物理方法,将不需要的材料层进行去除或定义。
刻蚀方法包括湿法刻蚀、干法刻蚀等,根据材料的不同选择不同的刻蚀方式。
清洗是中段制程中不可或缺的一步。
它的主要目的是去除杂质、残留物以及刻蚀产物,保证晶圆表面的纯净度和平整度。
清洗过程主要包括超声清洗、化学清洗等方法。
总之,半导体中段制程是半导体制造过程中至关重要的一步。
通过精确的加工和处理,可以实现对晶圆表面的图案形成和层之间的连接,为后续的工艺步骤打下坚实的基础。
在不断发展的半导体技术中,中段制程的优化和改进对于提高半导体器件的性能和可靠性具有重要意义。
1.2 文章结构文章结构部分的内容可以包括以下内容:在本篇长文中,我们将对半导体中段制程进行详细的探讨和分析。
文章分为引言、正文和结论三个部分。
引言部分首先对半导体中段制程进行概述,包括其定义、作用以及在半导体工业中的重要性。
接着,介绍文章的结构和目的,以及本文所要探讨的主要内容。
正文部分将分为两个要点来详细讨论半导体中段制程。
半导体纳米制程
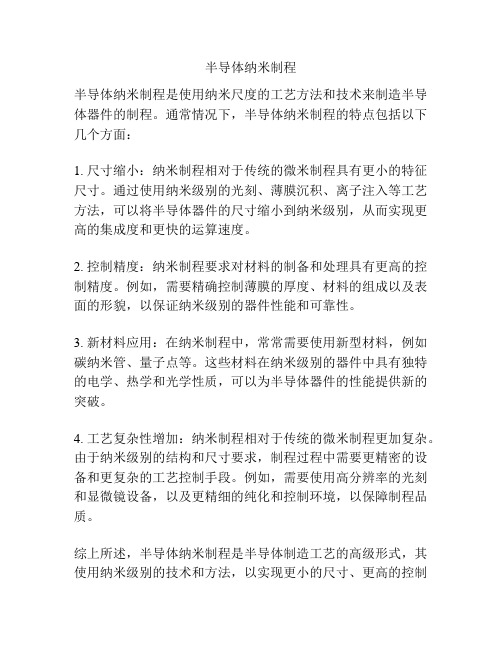
半导体纳米制程
半导体纳米制程是使用纳米尺度的工艺方法和技术来制造半导体器件的制程。
通常情况下,半导体纳米制程的特点包括以下几个方面:
1. 尺寸缩小:纳米制程相对于传统的微米制程具有更小的特征尺寸。
通过使用纳米级别的光刻、薄膜沉积、离子注入等工艺方法,可以将半导体器件的尺寸缩小到纳米级别,从而实现更高的集成度和更快的运算速度。
2. 控制精度:纳米制程要求对材料的制备和处理具有更高的控制精度。
例如,需要精确控制薄膜的厚度、材料的组成以及表面的形貌,以保证纳米级别的器件性能和可靠性。
3. 新材料应用:在纳米制程中,常常需要使用新型材料,例如碳纳米管、量子点等。
这些材料在纳米级别的器件中具有独特的电学、热学和光学性质,可以为半导体器件的性能提供新的突破。
4. 工艺复杂性增加:纳米制程相对于传统的微米制程更加复杂。
由于纳米级别的结构和尺寸要求,制程过程中需要更精密的设备和更复杂的工艺控制手段。
例如,需要使用高分辨率的光刻和显微镜设备,以及更精细的纯化和控制环境,以保障制程品质。
综上所述,半导体纳米制程是半导体制造工艺的高级形式,其使用纳米级别的技术和方法,以实现更小的尺寸、更高的控制
精度和更复杂的制程流程,从而实现半导体器件的更高性能和集成度。
制造工艺对显卡性能的影响

制造工艺对显卡性能的影响显卡作为计算机硬件中的重要组成部分,对图形处理与显示起着至关重要的作用。
而显卡的性能不仅与芯片设计及硬件配置有关,制造工艺也扮演着不可忽视的角色。
本文将探讨制造工艺对显卡性能的影响,并分析不同工艺对显卡性能的优劣。
一、工艺概述制造工艺是指显卡生产过程中使用的技术手段和方法。
目前主流显卡的制造工艺主要包括半导体制程和封装技术。
1. 半导体制程半导体制程是指芯片的制造过程,包括晶体管的形成、连线与互连、不同材料的堆叠等工艺步骤。
制程的发展直接影响到显卡性能的提升。
目前主流的半导体制程分为28纳米、14纳米、10纳米等等。
制程的缩进意味着制造工艺更加精密,能够在更小的面积内容纳更多的晶体管,从而提高显卡的计算性能和功耗控制。
2. 封装技术封装技术是指芯片封装为电子器件的过程,将芯片连接至外部电路,提供必要的防护与连接功能。
不同的封装技术将对显卡的散热性能、尺寸与整体性能产生重要影响。
目前常见的封装技术有传统的球栅阵列封装(BGA)和新兴的高级封装技术如三维堆叠封装(3D-IC),后者能够在更小的尺寸下实现更强大的性能。
二、制造工艺对显卡性能的影响1. 性能提升随着制造工艺的不断发展,比如从28纳米到10纳米的制程进步,显卡可以在更小的空间内集成更多的晶体管,提供更复杂的计算能力。
这意味着显卡的性能得到了巨大的增强,能够在游戏、图像处理和深度学习等任务中表现更出色。
2. 功耗控制制造工艺的进步也意味着显卡在相同的性能下能够实现更低的功耗。
采用更先进的制造工艺可以减少电流泄漏和功耗,从而提高计算效率和延长电池续航时间。
这对于依赖移动设备和笔记本电脑的用户尤为重要。
3. 散热与稳定性封装技术的不断创新不仅为显卡提供了更小巧的尺寸,还改善了散热性能。
采用新型封装技术,如3D-IC,可以在更小的空间内集成更多的散热组件,提高显卡的散热效果,从而避免因过热导致的性能损失和系统不稳定。
三、不同制造工艺的优劣虽然制造工艺的发展带来了显卡性能的提升,但不同的制造工艺也存在着各自的优劣。
半导体封装制程及其设备介绍详解演示文稿
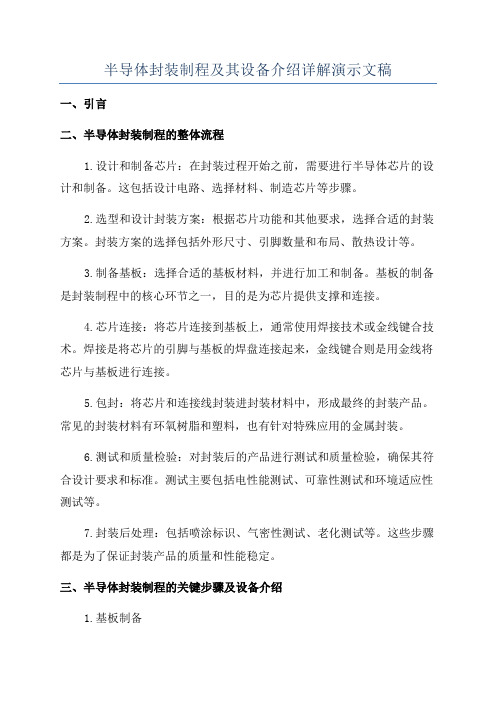
半导体封装制程及其设备介绍详解演示文稿一、引言二、半导体封装制程的整体流程1.设计和制备芯片:在封装过程开始之前,需要进行半导体芯片的设计和制备。
这包括设计电路、选择材料、制造芯片等步骤。
2.选型和设计封装方案:根据芯片功能和其他要求,选择合适的封装方案。
封装方案的选择包括外形尺寸、引脚数量和布局、散热设计等。
3.制备基板:选择合适的基板材料,并进行加工和制备。
基板的制备是封装制程中的核心环节之一,目的是为芯片提供支撑和连接。
4.芯片连接:将芯片连接到基板上,通常使用焊接技术或金线键合技术。
焊接是将芯片的引脚与基板的焊盘连接起来,金线键合则是用金线将芯片与基板进行连接。
5.包封:将芯片和连接线封装进封装材料中,形成最终的封装产品。
常见的封装材料有环氧树脂和塑料,也有针对特殊应用的金属封装。
6.测试和质量检验:对封装后的产品进行测试和质量检验,确保其符合设计要求和标准。
测试主要包括电性能测试、可靠性测试和环境适应性测试等。
7.封装后处理:包括喷涂标识、气密性测试、老化测试等。
这些步骤都是为了保证封装产品的质量和性能稳定。
三、半导体封装制程的关键步骤及设备介绍1.基板制备基板制备是封装制程中的核心步骤,主要包括以下设备:(1)切割机:用于将硅片切割成芯片,常见的切割机有钻石切割机和线切割机。
(2)干法清洗机:用于清洗芯片表面的杂质。
清洗机主要有氧气等离子体清洗机和干气流清洗机等。
(3)晶圆胶切割机:用于将芯片粘贴在基板上。
2.连接技术连接技术是将芯片与基板连接起来的关键步骤,常见的设备有:(1)焊接机:用于焊接芯片和基板之间的引脚和焊盘。
常见的焊接机有波峰焊机和回流焊机。
(2)金线键合机:用于将芯片与基板之间进行金线键合连接。
常见的金线键合机有球焊键合机和激光键合机等。
3.封装工艺封装工艺是将芯片和连接线封装进封装材料中的步骤,主要设备有:(1)半导体封装设备:用于将封装材料和连接线封装成最终产品。
半导体制程简介

半导体制程简介半导体制程是一种用于制造半导体器件的工艺过程,是现代电子工业不可或缺的关键部分。
半导体制程可以将硅等材料转化为半导体晶片,进而制造出各种集成电路、微处理器、存储芯片和其他电子器件。
在半导体制程中,首先需要选择合适的半导体材料,最常用的是硅。
硅具有优异的半导体特性和良好的物理特性,成为了制造半导体器件的首选材料。
其他半导体材料如化合物半导体和有机半导体也应用于特定的器件。
接下来是晶片的制备过程,主要包括晶体生长、切割和抛光。
晶体生长是通过高温熔炼和快速冷却,使单晶硅生长为大块晶体。
然后,晶体经过切割成薄片,再通过抛光和平整的过程使其表面光洁平整。
接着是半导体器件的制备过程。
这包括了沉积层、光刻、蚀刻、离子注入和金属化等步骤。
沉积层是通过物理气相沉积(PECVD)或热熔腐蚀(CVD)将薄膜材料沉积在晶片上。
光刻是将光敏胶覆盖在晶片上,然后用紫外线照射到其中的图案模板上,最后通过蚀刻去除未被曝光的区域。
离子注入是将离子通过加速器注入晶片中,改变材料的导电性和电阻率。
金属化是在晶片上涂覆金属,形成电线和电极,用于电子器件的连接。
最后是芯片封装和测试。
封装是将半导体器件连接到外部引脚和包装中,以保护器件并提供适当的电连接。
测试是对芯片进行电性能和可靠性的检查,以确保其正常工作并符合规格要求。
半导体制程是一项复杂而精细的工艺过程,需要严格的控制和高度的精确度。
不断的技术创新和工艺改进使得半导体器件的制造变得越来越高效和可靠。
半导体制程的进步不仅推动了电子技术的发展,还广泛应用于通信、计算机、汽车、医疗和工业等各个领域,为现代社会的科技进步和生活便利做出了巨大贡献。
在半导体制程中,制造芯片的关键技术之一是微影技术。
微影技术是一种将光刻或电子束曝光技术应用于半导体制程中的方法,用于将非常小的结构图案精确地转移到半导体表面,从而实现微小而密集的电子元件。
微影技术的进步极大地促进了半导体技术的发展,使得芯片的功能更加强大、体积更小。
半导体 nm制程
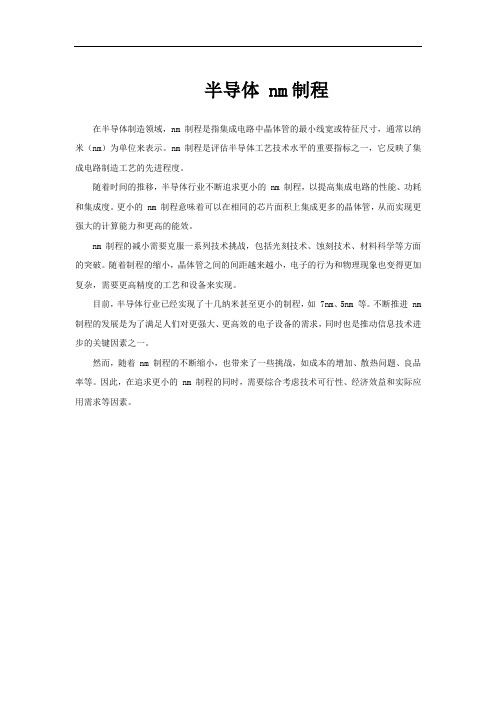
半导体 nm制程
在半导体制造领域,nm 制程是指集成电路中晶体管的最小线宽或特征尺寸,通常以纳米(nm)为单位来表示。
nm 制程是评估半导体工艺技术水平的重要指标之一,它反映了集成电路制造工艺的先进程度。
随着时间的推移,半导体行业不断追求更小的 nm 制程,以提高集成电路的性能、功耗和集成度。
更小的 nm 制程意味着可以在相同的芯片面积上集成更多的晶体管,从而实现更强大的计算能力和更高的能效。
nm 制程的减小需要克服一系列技术挑战,包括光刻技术、蚀刻技术、材料科学等方面的突破。
随着制程的缩小,晶体管之间的间距越来越小,电子的行为和物理现象也变得更加复杂,需要更高精度的工艺和设备来实现。
目前,半导体行业已经实现了十几纳米甚至更小的制程,如 7nm、5nm 等。
不断推进 nm 制程的发展是为了满足人们对更强大、更高效的电子设备的需求,同时也是推动信息技术进步的关键因素之一。
然而,随着 nm 制程的不断缩小,也带来了一些挑战,如成本的增加、散热问题、良品率等。
因此,在追求更小的 nm 制程的同时,需要综合考虑技术可行性、经济效益和实际应用需求等因素。
半导体制程简介
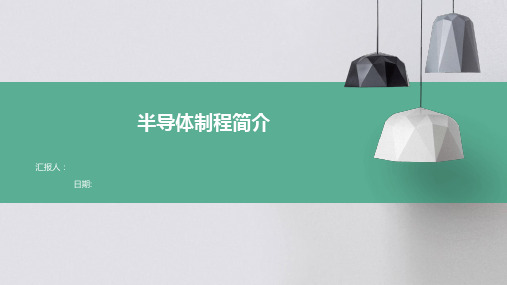
阐述图形化工艺的基本原理和方法,包括光刻、刻蚀、镀膜等步骤,以及这些步骤对半导体性能 的影响。
掺杂与退火
讲解掺杂剂的种类和作用,以及掺杂工艺的基本步骤和退火工艺对半导体性能的影响。
制程环境与设备
制程环境
介绍半导体制造所需的环境条件 ,如洁净度、温度、湿度等,以 及这些环境因素对半导体性能的 影响。
03
常见的半导体材料有硅、锗、砷化03
半导体材料具有高纯度、低缺陷等 特性。
硅是最常用的半导体材料,具有资 源丰富、制备工艺成熟等优势。
锗是一种具有高迁移率的半导体材 料,适用于高速电子器件。
半导体产业概述
01
半导体产业包括半导体制造、半导体设备、半 导体材料等领域。
案例三:纳米半导体器件制程
总结词
纳米半导体器件制程是一种制造纳米级尺寸 的半导体器件的制程,具有高频率、低功耗 、小尺寸等特点。
详细描述
纳米半导体器件制程采用先进的纳米制造技 术,如纳米压印、电子束光刻等,将半导体 材料加工成纳米级别的器件。该制程在微电 子、光电子、生物医学等领域具有广泛的应 用前景。
5G和物联网的驱动
5G和物联网技术的发展将推动半导体产业持续增长,对低功耗、 高性能半导体的需求不断增加。
中国市场的崛起
中国半导体市场已成为全球最大的市场之一,政府支持力度大,产 业发展迅速,国际合作与竞争日益激烈。
国际合作与竞争
国际合作
随着半导体产业的发展,国际合作成 为提高技术水平和竞争力的重要手段 ,各国纷纷建立合作机制,加强技术 交流和联合研发。
详细描述
半导体技术可以用于开发太阳能、风能等新能源发电设备中的半导体器件,提高能源利用效率;同时 也可以用于环保领域的半导体传感器、气体检测器等设备的开发,实现环境污染的监测与治理。
什么是半导体工艺制程,16nm、10nm都代表了什么

什么是半导体⼯艺制程,16nm、10nm都代表了什么什么是半导体⼯艺制程,16nm、10nm都代表了什么随着智能⼿机的发展,半导体⼯艺也急速提升,从28nm、16nm、10nm到7nm 这些半导体代⼯⼚们每天争相发布最新的⼯艺制程,让很多吃⽠群众⼀脸懵逼不知道有啥⽤。
半导体⾏业离我们似乎很遥远,FinFET是什么东西,EUV⼜是什么新技术,每次看到这种相关的新闻都让我们如同云⾥雾⾥,不知所谓。
其实它离我们很近,⽆论是FinFET还是EUV都是为了完善制程⼯艺所做的努⼒。
⽽⼀款处理器的性能表现、散热效率、功耗等等都和制程息息相关。
今天,我们来聊聊⼿机处理器的这些事。
●16nm、10nm,这些数字到底是啥?说起这个话题,我们要先搞清楚什么是制程。
那些20nm、16nm什么的到底代表了什么。
其实这些数值所代表的都是⼀个东西,那就是处理器的蚀刻尺⼨,简单的讲,就是我们能够把⼀个单位的电晶体刻在多⼤尺⼨的⼀块芯⽚上。
⼿机处理器不同于⼀般的电脑处理器,⼀部⼿机中能够给它留下的尺⼨是相当有限的。
蚀刻尺⼨越⼩,相同⼤⼩的处理器中拥有的计算单元也就越多,性能也就越强。
这也是为何⼚商会频繁强调处理器制程的原因。
同时,因为随着频率的提升,处理器所产⽣的热量也随之提⾼,⽽更先进的蚀刻技术另⼀个重要优点就是可以减⼩晶体管间电阻,让CPU所需的电压降低,从⽽使驱动它们所需要的功率也⼤幅度减⼩。
所以每⼀代的新产品不仅是性能⼤幅度提⾼,同时还有功耗和发热量的降低。
综合以上,可以发现处理器的制程对于⼿机⼗分重要,更⾼的性能带来更流畅的游戏体验,⽽⼀个保持正常温度的机⾝更是能保证⼤家拥有⼀个良好的使⽤体验。
⼀次制程的升级,带来了散热效果与计算性能的双重提升。
半导体全制程介绍

《晶圆处理制程介绍》基本晶圆处理步骤通常是晶圆先经过适当的清洗(Cleaning)之后,送到热炉管(Furnace)内,在含氧的环境中,以加热氧化(Oxidation)的方式在晶圆的表面形成一层厚约数百个的二氧化硅层,紧接着厚约1000到2000的氮化硅层将以化学气相沈积Chemical Vapor Deposition;CVP)的方式沈积(Deposition)在刚刚长成的二氧化硅上,然后整个晶圆将进行微影(Lithography)的制程,先在晶圆上上一层光阻(Photoresist),再将光罩上的图案移转到光阻上面。
接着利用蚀刻(Etching)技术,将部份未被光阻保护的氮化硅层加以除去,留下的就是所需要的线路图部份。
接着以磷为离子源(Ion Source),对整片晶圆进行磷原子的植入(Ion Implantation),然后再把光阻剂去除(Photoresist Scrip)。
制程进行至此,我们已将构成集成电路所需的晶体管及部份的字符线(Word Lines),依光罩所提供的设计图案,依次的在晶圆上建立完成,接着进行金属化制程(Metallization),制作金属导线,以便将各个晶体管与组件加以连接,而在每一道步骤加工完后都必须进行一些电性、或是物理特性量测,以检验加工结果是否在规格内(Inspection and Measurement);如此重复步骤制作第一层、第二层...的电路部份,以在硅晶圆上制造晶体管等其它电子组件;最后所加工完成的产品会被送到电性测试区作电性量测。
根据上述制程之需要,FAB厂内通常可分为四大区:1)黄光本区的作用在于利用照相显微缩小的技术,定义出每一层次所需要的电路图,因为采用感光剂易曝光,得在黄色灯光照明区域内工作,所以叫做「黄光区」。
2)蚀刻经过黄光定义出我们所需要的电路图,把不要的部份去除掉,此去除的步骤就> 称之为蚀刻,因为它好像雕刻,一刀一刀的削去不必要不必要的木屑,完成作品,期间又利用酸液来腐蚀的,所以叫做「蚀刻区」。
半导体制程简介

半导体制程简介半导体制程是指制造半导体器件所需的一系列工艺步骤和设备。
它是将材料转换为具有特定功能的半导体器件的过程,多数情况下是芯片制造的关键部分。
半导体制程通常分为六个主要步骤:前道工艺、IC 设计、曝光与衬底处理、薄膜沉积、刻蚀与清洗、以及后道工艺。
前道工艺是半导体制程的起始阶段。
在这个阶段,制造商会选择适合的衬底材料(通常是硅),并使用一系列的物理和化学方法准备它,以便于后续的加工。
IC 设计是将半导体器件的功能、结构和电路设计成电子文件的过程。
这些文件将被用于后续的曝光与衬底处理。
曝光与衬底处理是半导体制程的关键步骤之一。
在这个步骤中,使用光刻机将设计好的电子文件投射到光敏材料上,形成模式。
然后,通过化学方法去除暴露的材料,从而得到衬底上的所需结构。
这些步骤会多次重复,以逐渐形成多层结构。
在薄膜沉积阶段,使用化学蒸气沉积(CVD)或物理蒸镀(PVD)等方法将薄膜材料沉积到衬底上。
这些膜层将用于实现器件的不同功能,如导电层、绝缘层和隔离层等。
刻蚀与清洗是将多余的材料从衬底上去除的过程。
使用化学或物理方法,将不需要的材料刻蚀掉,并进行清洗和检查,确保器件的质量和一致性。
后道工艺是半导体制程的最后阶段。
在这个阶段中,制造商会进行结构和线路的连接,以及器件的测试和封装等。
这些步骤将半导体器件转换为实际可用的芯片。
半导体制程是一个复杂而精细的过程。
通过精确的控制和不断的优化,制造商可以获得高质量、高性能的半导体器件。
这些器件在现代技术中发挥着重要的作用,包括计算机、通信设备、消费电子产品等。
因此,半导体制程在推动科技进步和社会发展中扮演着重要的角色。
半导体制程在现代科技领域扮演着极为重要的角色。
随着信息技术的发展和人们对高性能电子设备的需求不断增长,半导体制程成为了现代社会的基石之一。
在这方面,特别值得一提的是摩尔定律。
摩尔定律是一种经验规律,它指出在相同面积上可以容纳的晶体管数量每隔大约18-24个月将翻一番,同时造价也会下降50%。
半导体制程工艺
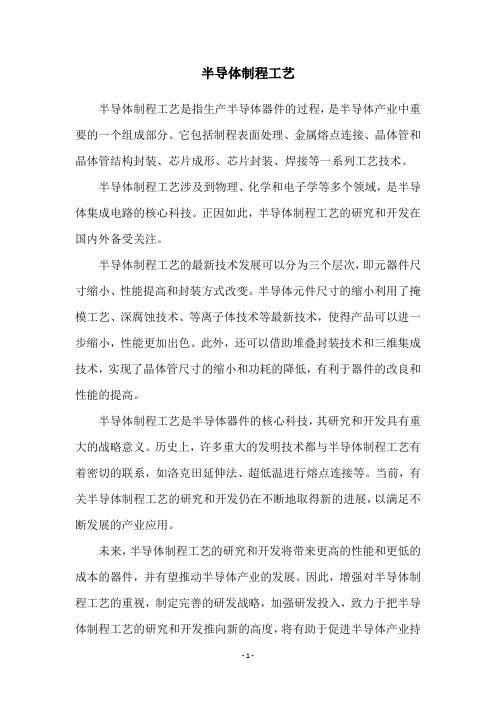
半导体制程工艺
半导体制程工艺是指生产半导体器件的过程,是半导体产业中重要的一个组成部分。
它包括制程表面处理、金属熔点连接、晶体管和晶体管结构封装、芯片成形、芯片封装、焊接等一系列工艺技术。
半导体制程工艺涉及到物理、化学和电子学等多个领域,是半导体集成电路的核心科技。
正因如此,半导体制程工艺的研究和开发在国内外备受关注。
半导体制程工艺的最新技术发展可以分为三个层次,即元器件尺寸缩小、性能提高和封装方式改变。
半导体元件尺寸的缩小利用了掩模工艺、深腐蚀技术、等离子体技术等最新技术,使得产品可以进一步缩小,性能更加出色。
此外,还可以借助堆叠封装技术和三维集成技术,实现了晶体管尺寸的缩小和功耗的降低,有利于器件的改良和性能的提高。
半导体制程工艺是半导体器件的核心科技,其研究和开发具有重大的战略意义。
历史上,许多重大的发明技术都与半导体制程工艺有着密切的联系,如洛克田延伸法、超低温进行熔点连接等。
当前,有关半导体制程工艺的研究和开发仍在不断地取得新的进展,以满足不断发展的产业应用。
未来,半导体制程工艺的研究和开发将带来更高的性能和更低的成本的器件,并有望推动半导体产业的发展。
因此,增强对半导体制程工艺的重视,制定完善的研发战略,加强研发投入,致力于把半导体制程工艺的研究和开发推向新的高度,将有助于促进半导体产业持
续健康发展。
总之,半导体制程工艺是半导体器件的核心科技,对于元器件尺寸缩小、性能提高和封装方式改变等技术具有重要意义,是现代半导体产业发展的重要基础。
因此,要加强对半导体制程工艺的重视,继续发挥其在半导体产业中的重要作用,促进半导体产业的健康发展。
半导体制程简介

半导体制程简介微机电制作技术,尤其是最大宗以硅半导体为基础的微细加工技术(silicon- based micromachining),原本就肇源于半导体组件的制程技术,所以必须先介绍清楚这类制程,以免沦于夏虫语冰的窘态。
一、洁净室一般的机械加工是不需要洁净室(clean room)的,因为加工分辨率在数十微米以上,远比日常环境的微尘颗粒为大。
但进入半导体组件或微细加工的世界,空间单位都是以微米计算,因此微尘颗粒沾附在制作半导体组件的晶圆上,便有可能影响到其上精密导线布局的样式,造成电性短路或断路的严重后果。
为此,所有半导体制程设备,都必须安置在隔绝粉尘进入的密闭空间中,这就是洁净室的来由。
洁净室的洁净等级,有一公认的标准,以class 10为例,意谓在单位立方英呎的洁净室空间内,平均只有粒径0.5微米以上的粉尘10粒。
所以class后头数字越小,洁净度越佳,当然其造价也越昂贵(参见图2-1)。
为营造洁净室的环境,有专业的建造厂家,及其相关的技术与使用管理办法如下:1、内部要保持大于一大气压的环境,以确保粉尘只出不进。
所以需要大型鼓风机,将经滤网的空气源源不绝地打入洁净室中。
2、为保持温度与湿度的恒定,大型空调设备须搭配于前述之鼓风加压系统中。
换言之,鼓风机加压多久,冷气空调也开多久。
3、所有气流方向均由上往下为主,尽量减少突兀之室内空间设计或机台摆放调配,使粉尘在洁净室内回旋停滞的机会与时间减至最低程度。
4、所有建材均以不易产生静电吸附的材质为主。
5、所有人事物进出,都必须经过空气吹浴(air shower) 的程序,将表面粉尘先行去除。
6、人体及衣物的毛屑是一项主要粉尘来源,为此务必严格要求进出使用人员穿戴无尘衣,除了眼睛部位外,均需与外界隔绝接触(在次微米制程技术的工厂内,工作人员几乎穿戴得像航天员一样。
) 当然,化妆是在禁绝之内,铅笔等也禁止使用。
7、除了空气外,水的使用也只能限用去离子水(DI water, de-ionized water)。
半导体先进工艺制程

半导体先进工艺制程半导体先进工艺制程是指通过一系列的加工步骤对半导体材料进行精细加工,以制造出高性能、高稳定性的半导体器件。
随着科技的不断进步和需求的不断增长,半导体工艺制程也在不断演进和创新。
本文将介绍半导体先进工艺制程的基本原理、发展历程以及未来的发展趋势。
半导体先进工艺制程的基本原理是通过一系列的化学、物理及电子加工步骤来改变半导体材料的性质,从而制造出具有特定功能的半导体器件。
整个工艺制程通常包括晶圆制备、掩膜光刻、离子注入、薄膜沉积、金属化、退火等步骤。
这些步骤的顺序和参数的控制非常关键,能直接影响到器件的性能和可靠性。
随着半导体工艺制程的发展,先进工艺制程逐渐取代了传统的工艺技术。
在传统工艺中,器件的尺寸越大,性能越好,但是制程复杂度也越高。
而先进工艺制程则采用了更小的尺寸,通常在纳米级别,这使得器件具有更高的集成度和更低的功耗。
同时,先进工艺制程还采用了更多的创新材料和结构设计,以提高器件的性能和可靠性。
在半导体先进工艺制程的发展历程中,最重要的里程碑是CMOS技术的引入。
CMOS(互补金属-氧化物-半导体)技术是一种基于硅的半导体制造技术,它将N型和P型的MOSFET(金属-氧化物-半导体场效应晶体管)结合在一起,以实现更高的性能和更低的功耗。
CMOS技术的引入使得半导体工艺制程得以快速发展,从而推动了整个信息技术产业的进步。
当前,半导体先进工艺制程正朝着更加微小化和高性能的方向发展。
首先,尺寸的缩小是先进工艺制程的主要趋势之一。
随着技术的进步,晶圆上的晶体管数量越来越多,尺寸也越来越小,这使得芯片的集成度大幅度提高。
其次,新材料的引入也是先进工艺制程的重要方向。
例如,碳化硅(SiC)和氮化镓(GaN)等宽禁带半导体材料具有更高的导电性能和更好的热特性,可以应用于功率器件和光电器件等领域。
此外,三维集成和新型封装技术也是先进工艺制程的研究热点,可以进一步提高芯片的性能和可靠性。
未来,半导体先进工艺制程的发展还将面临一些挑战。
半导体 制程
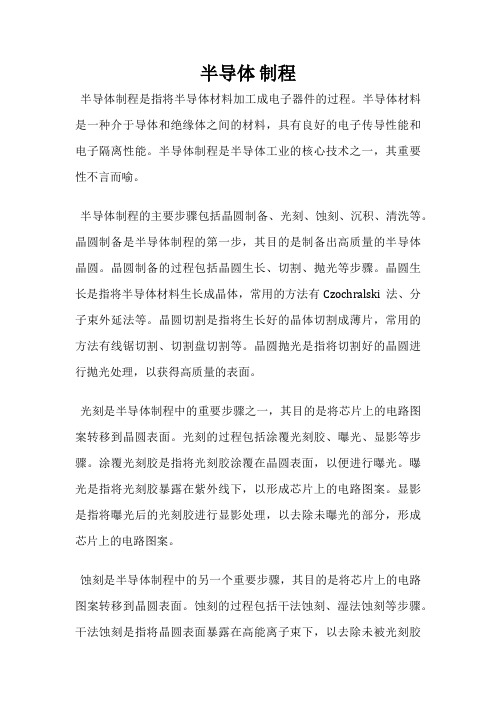
半导体制程半导体制程是指将半导体材料加工成电子器件的过程。
半导体材料是一种介于导体和绝缘体之间的材料,具有良好的电子传导性能和电子隔离性能。
半导体制程是半导体工业的核心技术之一,其重要性不言而喻。
半导体制程的主要步骤包括晶圆制备、光刻、蚀刻、沉积、清洗等。
晶圆制备是半导体制程的第一步,其目的是制备出高质量的半导体晶圆。
晶圆制备的过程包括晶圆生长、切割、抛光等步骤。
晶圆生长是指将半导体材料生长成晶体,常用的方法有Czochralski法、分子束外延法等。
晶圆切割是指将生长好的晶体切割成薄片,常用的方法有线锯切割、切割盘切割等。
晶圆抛光是指将切割好的晶圆进行抛光处理,以获得高质量的表面。
光刻是半导体制程中的重要步骤之一,其目的是将芯片上的电路图案转移到晶圆表面。
光刻的过程包括涂覆光刻胶、曝光、显影等步骤。
涂覆光刻胶是指将光刻胶涂覆在晶圆表面,以便进行曝光。
曝光是指将光刻胶暴露在紫外线下,以形成芯片上的电路图案。
显影是指将曝光后的光刻胶进行显影处理,以去除未曝光的部分,形成芯片上的电路图案。
蚀刻是半导体制程中的另一个重要步骤,其目的是将芯片上的电路图案转移到晶圆表面。
蚀刻的过程包括干法蚀刻、湿法蚀刻等步骤。
干法蚀刻是指将晶圆表面暴露在高能离子束下,以去除未被光刻胶保护的部分。
湿法蚀刻是指将晶圆表面暴露在化学溶液中,以去除未被光刻胶保护的部分。
沉积是半导体制程中的另一个重要步骤,其目的是在晶圆表面沉积一层薄膜,以形成芯片上的电路元件。
沉积的过程包括物理气相沉积、化学气相沉积、物理溅射沉积等步骤。
物理气相沉积是指将材料蒸发在真空中,以形成薄膜。
化学气相沉积是指将材料在化学反应中沉积在晶圆表面,以形成薄膜。
物理溅射沉积是指将材料溅射在晶圆表面,以形成薄膜。
清洗是半导体制程中的最后一步,其目的是去除晶圆表面的杂质和残留物,以保证芯片的质量。
清洗的过程包括化学清洗、超声波清洗等步骤。
化学清洗是指将晶圆浸泡在化学溶液中,以去除表面的杂质和残留物。
半导体cpm制程

半导体CPM制程简介半导体封装是将制造出来的芯片和外部世界连接起来的重要环节,CPM(Chip Package Module)制程是一种常用的半导体封装技术。
在CPM制程中,芯片被封装在一个外部保护壳内,以保护芯片的完整性和安全性,并提供与外部环境的接口。
本文将详细介绍半导体CPM制程的原理、流程和常见工艺。
原理CPM制程的原理是在一个封装基板上将半导体芯片、金属引脚和外部元器件(如电容和电阻)连接起来。
封装基板是一块由绝缘材料制成的板子,上面通过铜等导电材料制成的电路将芯片和其他元器件连接在一起。
这些连接被称为封装线路或封装线。
半导体芯片和封装基板之间的连接通常采用线缆或球连接(wire bonding or ball bonding)技术,其中通过焊接或压接形成金属线或球来实现芯片和基板之间的信号传输和电力供应。
这种连接方式既可靠又节省空间,同时兼顾了信号传输和散热需求。
流程半导体CPM制程是一个复杂的过程,通常包括以下几个主要步骤:1.设计封装方案:在制程开始之前,需要根据芯片的功能要求、尺寸和散热需求等因素,设计一个适合的封装方案。
这个方案将指导后续的制造过程。
2.制作封装基板:封装基板是半导体芯片的承载体,它必须具备一定的绝缘性、导电性和热导性能。
制作封装基板通常包括材料选型、板材加工和印制电路制作等步骤。
3.将芯片粘贴到基板:在封装基板上的适当位置,使用粘合剂将芯片固定在基板上。
这需要高精度的操作和设备,以确保芯片的正确定位和粘贴质量。
4.连接芯片和基板:根据设计方案,使用线缆或球连接技术将芯片和封装基板上的引脚连接起来。
这个过程需要精密的设备和技术,以确保连接的可靠性和稳定性。
5.封装封装基板:在将芯片连接到封装基板后,需要在基板上覆盖一个保护层,通常是一层塑料。
这个层保护芯片和连接,同时提供机械保护和防尘功能。
6.测试和质量控制:完成封装之后,需要对芯片和封装进行一系列的测试,以确保其性能和质量。
半导体封装制程与设备材料知识简介

半导体封装制程与设备材料知识简介半导体封装制程主要包括以下几个步骤:首先是对芯片进行划片,将大块的半导体晶圆切成小的芯片;接着是焊接引脚,将芯片的金属引脚焊接到封装件上;最后是封装成型,将芯片和引脚封装在一个保护性的封装件中。
在制程中需要使用到多种设备和材料。
其中,设备包括芯片切割机、焊接机、封装设备等;而材料则包括封装胶、引脚材料、封装盒材料等。
这些设备和材料的选择和使用对封装质量和成本都有着重要影响。
半导体封装制程和设备材料知识是半导体封装工程师和技术人员需要掌握的重要内容。
通过深入了解和学习,可以更好地理解半导体封装的工艺流程,提高封装质量,降低生产成本,推动半导体封装技术的发展。
半导体封装制程与设备材料知识是半导体领域中至关重要的一部分。
半导体封装是将半导体芯片连接到PCB(印刷电路板)上的过程,以便将芯片应用于各种电子设备中。
在半导体工业中,封装是半导体制造的最后一道工序,它对芯片的保护、连接、传导和散热起着重要作用。
这一制程既涉及到材料的选择,也需要各种设备的使用。
在制程中,半导体封装需要考虑诸多因素,包括封装材料的导热性能、电气特性、耐高温性以及成本效益和环保等方面。
在制程中需要用到的设备包括高精度的切割机、精密的焊接设备、封装设备以及检测设备等。
这些设备需要满足封装工艺的要求,以确保封装质量和生产效率。
此外,封装材料也是封装制程的重要组成部分。
例如,封装盒的选材需要考虑其对温度变化的稳定性和防尘、防潮性能;封装胶需要具备良好的导热性能和机械强度,以确保芯片在工作时不会受到机械应力和温度应力的影响。
而对于封装材料的选择,也需要考虑到生产成本和环保要求。
因此,一些新型的封装材料,如可降解材料、环保材料等,也逐渐被引入到半导体封装的制程中。
在半导体封装制程和设备材料知识的应用领域中,半导体工程师和技术人员需要具备系统地理解和掌握相关知识。
他们需要不断地关注封装技术的发展动态,研究新型封装材料和设备,以提高封装质量、降低生产成本,并推动半导体封装技术的不断进步。
半导体cpm制程

半导体cpm制程一、引言半导体制程是指将半导体材料转化为电子器件的过程,其中包括了从晶圆制备到最终器件封装的所有步骤。
CPM制程是一种新型的半导体制程,它采用了先进的光刻技术和化学机械抛光技术,具有高精度、高可控性和高产能等优点。
二、CPM制程的基本原理CPM制程是通过在硅片表面形成一层光致聚合物(photoresist)薄膜来实现图形转移的。
首先,在硅片表面涂覆一层光致聚合物,并利用光刻机将所需图形曝光在聚合物上;然后,通过化学反应将曝光区域和未曝光区域分别转化为亲水性和疏水性区域;最后,在疏水性区域进行蚀刻或沉积等工艺步骤,以实现对硅片表面的加工。
三、CPM制程的主要步骤1. 晶圆清洗:晶圆在进入CPM制程前需要经过多次清洗,以去除表面杂质和污染物。
2. 光刻胶涂覆:将光致聚合物涂覆在晶圆表面,形成一层薄膜。
3. 光刻胶曝光:使用光刻机将所需图形曝光在聚合物上,形成图案。
4. 光刻胶显影:使用化学药液将曝光区域和未曝光区域分别转化为亲水性和疏水性区域。
5. 蚀刻或沉积:在疏水性区域进行蚀刻或沉积等工艺步骤,以实现对硅片表面的加工。
6. 光刻胶去除:使用化学药液将剩余的光致聚合物去除,完成一次CPM制程。
四、CPM制程的优点1. 高精度:CPM制程采用了先进的光刻技术,可以实现微米级别的精度要求。
2. 高可控性:CPM制程中各个步骤都可以进行严格的控制和监测,保证了产品质量的稳定性和可靠性。
3. 高产能:由于CPM制程采用了自动化生产线和大批量生产技术,可以实现高效率、高产能的生产。
4. 环保节能:CPM制程采用了化学机械抛光技术,可以减少废料和废水的产生,达到环保节能的目的。
五、CPM制程的应用领域CPM制程广泛应用于半导体行业中,包括芯片制造、LED显示屏制造、太阳能电池板制造等领域。
随着半导体技术的不断发展和完善,CPM制程将会得到更广泛的应用和推广。
六、结论CPM制程是一种新型的半导体制程,具有高精度、高可控性和高产能等优点。
半导体nm制程对应的关键尺寸

半导体nm制程对应的关键尺寸半导体制程中的"nm"代表纳米(nanometer),是衡量制程技术尺寸的单位。
半导体制程的关键尺寸通常指的是不同工艺步骤中最小的特征尺寸。
以下是一些常见的半导体制程对应的关键尺寸:
1. 180 nm制程:该制程的最小特征尺寸约为180纳米。
2. 130 nm制程:该制程的最小特征尺寸约为130纳米。
3. 90 nm制程:该制程的最小特征尺寸约为90纳米。
4. 65 nm制程:该制程的最小特征尺寸约为65纳米。
5. 45 nm制程:该制程的最小特征尺寸约为45纳米。
6. 32 nm制程:该制程的最小特征尺寸约为32纳米。
7. 22 nm制程:该制程的最小特征尺寸约为22纳米。
8. 14 nm制程:该制程的最小特征尺寸约为14纳米。
9. 10 nm制程:该制程的最小特征尺寸约为10纳米。
请注意,以上仅列举了一些常见的制程尺寸,随着技术的不断发展,制程尺寸可能会更小。
此外,不同的半导体制造厂商和工艺节点可能存在微小的差异。
1。
半导体先进工艺制程
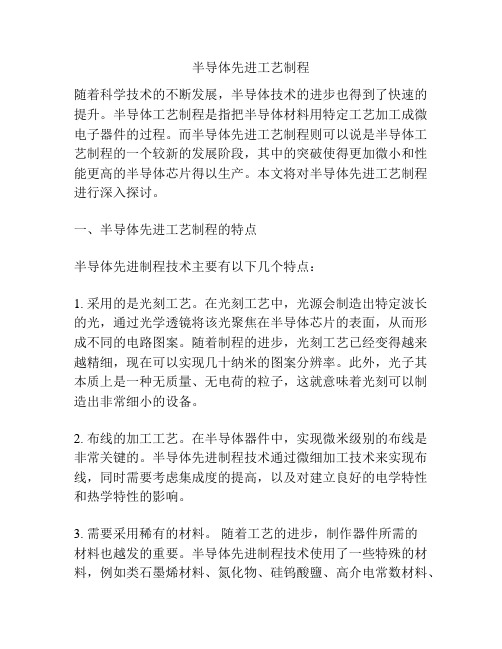
半导体先进工艺制程随着科学技术的不断发展,半导体技术的进步也得到了快速的提升。
半导体工艺制程是指把半导体材料用特定工艺加工成微电子器件的过程。
而半导体先进工艺制程则可以说是半导体工艺制程的一个较新的发展阶段,其中的突破使得更加微小和性能更高的半导体芯片得以生产。
本文将对半导体先进工艺制程进行深入探讨。
一、半导体先进工艺制程的特点半导体先进制程技术主要有以下几个特点:1. 采用的是光刻工艺。
在光刻工艺中,光源会制造出特定波长的光,通过光学透镜将该光聚焦在半导体芯片的表面,从而形成不同的电路图案。
随着制程的进步,光刻工艺已经变得越来越精细,现在可以实现几十纳米的图案分辨率。
此外,光子其本质上是一种无质量、无电荷的粒子,这就意味着光刻可以制造出非常细小的设备。
2. 布线的加工工艺。
在半导体器件中,实现微米级别的布线是非常关键的。
半导体先进制程技术通过微细加工技术来实现布线,同时需要考虑集成度的提高,以及对建立良好的电学特性和热学特性的影响。
3. 需要采用稀有的材料。
随着工艺的进步,制作器件所需的材料也越发的重要。
半导体先进制程技术使用了一些特殊的材料,例如类石墨烯材料、氮化物、硅钨酸鹽、高介电常数材料、导电高介电常数材料和其他多层结构等。
这些材料具有高处理温度、降低耗电、低带宽折射、保证信号传输等特点。
4. 采用了新的晶片技术。
制作芯片时需要使用新的晶片技术。
例如,压缩引入技术,可以实现更小的晶点和封装空间。
此外,半导体先进制程技术是在现代的工艺技术下采用预先设计的光子晶体创建出非常特殊的光子结构。
二、半导体先进工艺制程的应用半导体先进工艺制程主要应用于以下方面:1. 电子产品制造。
半导体芯片是电子产品的核心,半导体先进制程技术可以生产出高度集成的芯片,包括中央处理器、微控制器、存储芯片、图形处理器等。
2. 通讯技术。
随着信息技术的不断发展,通讯技术的应用也越来越普遍。
半导体先进制程技术可以生产出高端的通信设备,包括4G、5G网络设备等。
半导体制程简介

半導體製程簡介半导体制程是指用于制造半导体材料和器件的工艺流程。
半导体器件是现代电子技术的基础,几乎所有的电子产品都离不开半导体器件的应用。
半导体制程的发展对提升电子产品的性能和功能至关重要。
半导体制程包括前工艺和后工艺两个部分。
前工艺是指对硅片进行刻蚀、沉积、掺杂、光刻等工艺,用于形成各种晶体管、电容器和传感器等器件。
后工艺是指将切割得到的芯片进行封装、测试和贴片等工艺,以便进行成品制造和使用。
首先,前工艺的第一步是进行清洗和化学机械抛光,以去除表面的污染物和缺陷。
清洗后,需要进行氧化处理,形成一层薄的氧化硅层,用于保护硅片表面和形成绝缘层。
接下来是光刻工艺,利用光刻胶和掩膜模具进行曝光和显影,将所需器件的图案转移到硅片上。
通过光刻工艺,可以制造出微小的结构和线路。
光刻的精度与分辨率决定了芯片的性能和功能。
在光刻后,需要进行刻蚀和沉积工艺。
刻蚀是利用化学或物理手段去除不需要的材料或形成凹凸结构。
沉积是将一层薄的材料沉积在硅片表面,如金属、氧化物或多晶硅。
刻蚀和沉积工艺的选择和优化,可以控制器件的形状、性能和功能。
掺杂是半导体制程中的重要步骤。
通过掺入杂质原子,可以改变半导体材料的导电性质。
常用的掺杂元素有硼、磷和砷等。
掺杂后,需要进行退火处理,以激活和固定杂质原子。
完成了前工艺后,需要进行后工艺。
首先是切割芯片,将硅片切割成小的芯片单元,以便进行后续的封装。
然后是封装工艺,将芯片焊接到外部引脚和封装底座上,以便进行电路连接。
封装工艺的设计和调试,对产品的可靠性和稳定性有着重要影响。
最后是芯片测试和贴片工艺。
芯片测试是对芯片进行性能和功能的验证和测量。
贴片工艺是将芯片封装到电子产品中,如手机、笔记本电脑和汽车等。
贴片工艺要求精细和高效,以满足大规模生产的需求。
半导体制程的发展经历了多个技术革新和突破。
从最初的二极管、晶体管到现在的集成电路和纳米器件,半导体制程不断创新和进步,推动了电子技术的发展。
- 1、下载文档前请自行甄别文档内容的完整性,平台不提供额外的编辑、内容补充、找答案等附加服务。
- 2、"仅部分预览"的文档,不可在线预览部分如存在完整性等问题,可反馈申请退款(可完整预览的文档不适用该条件!)。
- 3、如文档侵犯您的权益,请联系客服反馈,我们会尽快为您处理(人工客服工作时间:9:00-18:30)。
TFT Array 製程關鍵性技術— 洗淨製程技術(2)
• 去除微塵顆粒的洗淨方法有
– 毛刷旋轉清洗基板表面的刮除洗淨(Scrub)
• 去除微小顆粒最有效的洗淨方式 • 尤其是強力附著於基板表面之微小顆粒的去除 • 僅限制用於可容許較大膜表面的情況
TFT Array 製程關鍵性技術— 洗淨製程技術(3)
– 低頻(10~100kHz)、高頻(1MHz)超音波振盪 洗淨
• 超音波振盪洗淨是一種非接觸式,屬低損傷之微 小顆粒去除的洗淨方法
• 高頻超音波會產生空穴效應(Cavitation) ,使膜表 面的損傷程度變小
• 最常用於單片式隙縫沖洗(Slit Shower) ,具有去 除次微米級顆粒功能
显示技术半导体制程
前言
• TFT Array的製造流程基本上是TFT的製作過程 。
• α–Si TFT Array的製造流程有
– 洗淨技術 – 成膜技術如濺鍍法以及化學氣相沉積法(CVD) – 光微影技術如光阻劑塗佈 – 預先烘培、微影、顯影以及後續烘培等 – 蝕刻技術 – 光阻劑去除技術 – 電極蒸鍍技術等一連串反覆地操作過程
資料來源:顧鴻壽編著,“光電液晶平面顯示器—技術基礎及應用”
資料來源:顧鴻壽編著,“光電液晶平面顯示器—技術基礎及應用”
資料來源:顧鴻壽編著,“光電液晶平面顯示器—技術基礎及應用”
Step 1
• 將玻璃基板預先進行洗淨處理
– 目的:清除玻璃基板表面上可能殘留的納離 子類污染物
• 利用濺鍍法或電薄膜覆蓋 層
TFT Array 製程關鍵性技術— 成膜製程技術(6)
TFT Array 製程關鍵性技術— 成膜製程技術(7)
TFT Array 製程關鍵性技術— 成膜製程技術(8)
• 製程中的主要參數有
– 氣體流量 – 氣體流量比 – 基板溫度 – 反應室氣體總壓力 – 放電電力密度等
• 製程參數的改變將會影響到成膜的速度 和成膜的品質。
Step 4
• 運用物理式濺鍍法濺鍍透明導電電極膜--ITO (Indium Tin Oxide)薄膜
• 利用濕式蝕刻技術去除不需要的部分,形成畫 像素電極圖案(Pixel Pattern)
• 利用光阻劑塗佈、曝光微影、顯影等製程技術 將閘電極及接觸通道(Contact Hole)的圖案形成
• 再利用蝕刻技術將閘絕緣膜去除,僅形成接觸 通道
TFT Array 製程關鍵性技術— 洗淨製程技術(4)
• 紫外線洗淨及臭氧洗淨
– 去除有機物及控制基板表面狀態 – 方法有
• 有機溶劑處理法 • 臭氧處理法 • 紫外線照射處理法
TFT Array 製程關鍵性技術— 洗淨製程技術(5)
• 氟酸系藥劑處理法及Ar氣體的電漿處理 法或離子濺鍍處理法
• 利用濺鍍法將閘電極用或掃描配線材料 靶材濺鍍形成金屬薄膜
Step 2
• 將光阻劑剝離後,在閘電極的表面上形 成第一層陽極氧化膜作為閘極絕緣體
• 再利用(PCVD)連續地成長第二層SiNx閘 極絕緣膜、半導體活性層功能的α–Si :H 、通道保護膜SiNx等構成所謂的三層薄 膜結構
Step 3
Step 5
• 利用物理式濺鍍法濺鍍金屬薄膜 • 利用光阻劑塗佈、曝光微影、顯影等電路圖案
製作過程,形成所需TFT的源電極、汲電極及 信號線配線 • 利用(PCVD)成長氮化膜 • 再利用光阻劑塗佈、曝光微影、顯影等圖案製 作過程,,形成配線電極端子的接觸通道及顯示 電極開口部的圖案 • 將氮化膜利用蝕刻技術去除
資料來源:顧鴻壽編著,“光電液晶平面顯示器—技術基礎及應用”
TFT Array 製程關鍵性技術— 成膜製程技術(5)
• PCVD是應用於成長閘電極絕緣膜、α–Si :H膜、保護膜等。
• PCVD基本特性:
– 即使是玻璃基板,仍然可以於低溫成膜 – 可形成缺陷少的薄膜 – 製程的再現性較佳的 – 大面積均勻成膜
– 用於處理半導體薄膜、金屬層、摻雜層、歐 姆接觸等有損害之劣等自然氧化膜(長於半 導體膜表面)
TFT Array 製程關鍵性技術— 洗淨製程技術(6)
• 玻璃基板乾燥方法有
– 旋轉乾燥法 – 氮氣空氣刀乾燥法 – 乾燥空氣吹乾法 – 使用異丙醇的蒸氣乾燥法等
TFT Array 製程關鍵性技術— 成膜製程技術(1)
• 導電性的靶材是使用直流式濺鍍法
• 半導體、絕緣體的成膜則使用高頻的射 頻濺鍍法(Radio Frequency Sputtering , RF) 。
TFT Array 製程關鍵性技術— 成膜製程技術(3)
資料來源:顧鴻壽編著,“光電液晶平面顯示器—技術基礎及應用”
TFT Array 製程關鍵性技術— 成膜製程技術(4)
Step 6
• 成長保護膜SiNx ,將其週邊的電極接合 端部份顯露出來,完成TFT Array的製作
TFT Array 製程關鍵性技術— 洗淨製程技術(1)
• α–Si TFT Array 洗淨過程約佔整個製程的 30%
• 洗淨主要目的有三
– 為了得到良好的導電性、提升膜的密著性, 以改善、控制基板表面品質
TFT Array 製程關鍵性技術— 光微影製程技術(1)
• 化學方式的電漿化學氣相沉積法(Plasma Chemical Vapor deposition,PCVD)
– α–Si膜 – 絕緣膜等
• 物理方式的濺鍍法(Sputtering)
– 配線電極 – 透明顯示電極等導電薄膜
TFT Array 製程關鍵性技術— 成膜製程技術(2)
• 濺鍍法是應用於成長金屬薄膜,主要用 途包括閘電極、源電極、汲電極、掃描 線、儲存電容電極、信號線、畫像素線 等。
• 通道保護膜的配線圖案形成後,使其摻 有磷原子之n+型的α–Si形成薄膜
• 將n+型的α–Si及其下方的α–Si:H層同時進 行蝕刻處理,形成島狀結構配線圖案
• 利用光阻劑塗佈、曝光微影、顯影等製 程技術將TFT部份的α–Si圖案形成
• 利用乾式蝕刻技術將圖案部分以外的n+型 α–Si薄膜及α–Si薄膜去除