VDA6.3新版过程FMEA六步法
FMEA要求六步分析法
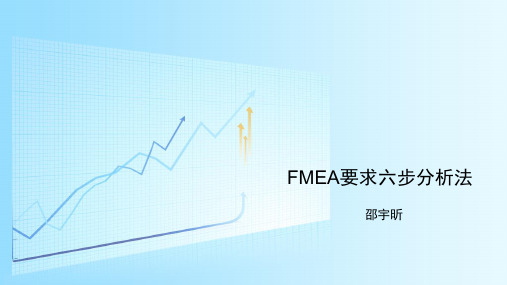
有的技术和材料,类似的应 但不足以确保不发生故障, 用随着周期/运行的条件变 分析能提供一些防止失效的
化,以前有测试或现场经验 原因
在预期使用寿命期间发生的 基于类似技术和材料的新设 标准、最佳实践和设计规则
7 可能性为较高
计,新的应用或改变工作周 适用于基准设计,但不适用 期/运行条件,以前未验证。 于创新,分析提供了有限的
标准不存在,最佳实践尚未 确定,分析不能预测实际性 能
• 从上表可以看出 • 新版 FMEA 的频度考虑了 • 设计成熟度(估计发生) • 产品成熟度(产品实践) • 和预防措施(预防控制) • • • • • 三个维度进行评分 • 增加了“公司或产品示例”栏
探测度(D) 是探测控制有效性的指标 以在产品发布、生产之前 可靠地探测失效原因或失效模式 探测度是指 在现行过程控制探测栏里的 最佳探测控制相关等级 探测度(D)打分表 (适用DFMEA)
第三步:功能分析
• 该步骤主要利用和接口矩阵等工具识别设计或过程的功能和要求并赋予给系统层 级和下一层级(产品、部件层级)如图所示
第四步:失效分析
• 该步骤是新版FMEA特色所在 • 将失效影响、失效模式和失效原因之间 • 的逻辑关系以“瀑布模型”的方式进行展示 • 上一层级的失效模式为下一层级的失效影响 • 下一层级的失效模式即为上一层级的失效原因
频度
估计发生
产品实践
预防控制
通过预防性控制和无故障 完成相同的成熟设计,相 设计经验符合标准、最佳
系列生产的历史,实际上 同的应用、工作周期和工 实践,考虑到经验教训,
1 可以消除故障的可能性 作条件,在可比较的操作 这有效的防止了条件失效
条件或成熟的设计下进行 的发生,分析能高信度的
新版VDA6.3-2016主要变化解读及过程审核培训教材25-12
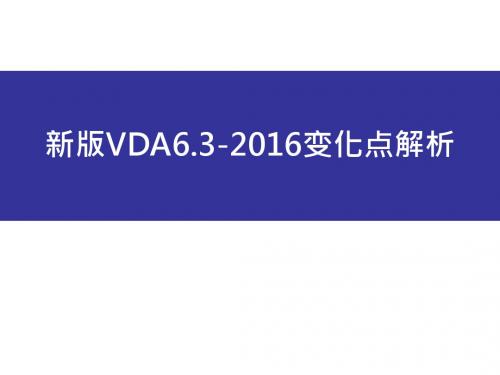
Key changes in new VDA6.3
主要变化点
• S/W issues added to questionary?提问表中加入 S/W 问题
• Audit result/ evaluation method weight of each questions same 每个问题对审核结果/评价方法的比 重一致
P5/P6/P7 audit (series)审核(量产): Number of questions 问题数量
P5/P6/P7 audit (series)审核(量产): Weighting of one question as % 每个问题的比重
Key changes in new VDA6.3
主要变化点
VDA6.3 new version 2016 (changes) VDA6.3新版 2016(变化)
Structure of VDA 6.3 same 结构和之前没有变化 Before 60 questions, now only 57 questions 之前60个问题,现在57个 All questions equal for final results 每个问题占相同的比重
Professional experience 工作经验:
At least 5 years of professional experience (from 3 years of professional experience, company training periods can be taken into account) preferably in producing companies from the automotive industry, of which at least 2 years quality management. 至少5年的工作经验(包括培训期),最好是汽车行业制造业领域,至少两年的质量管理 经验
vda6.3过程审核规程
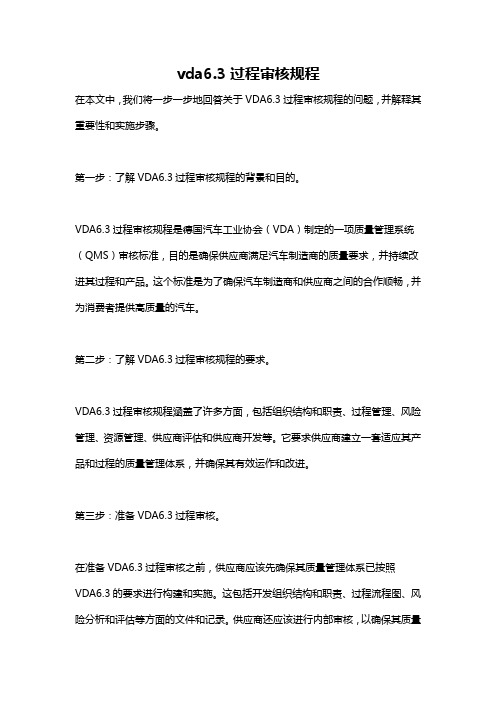
vda6.3过程审核规程在本文中,我们将一步一步地回答关于VDA6.3过程审核规程的问题,并解释其重要性和实施步骤。
第一步:了解VDA6.3过程审核规程的背景和目的。
VDA6.3过程审核规程是德国汽车工业协会(VDA)制定的一项质量管理系统(QMS)审核标准,目的是确保供应商满足汽车制造商的质量要求,并持续改进其过程和产品。
这个标准是为了确保汽车制造商和供应商之间的合作顺畅,并为消费者提供高质量的汽车。
第二步:了解VDA6.3过程审核规程的要求。
VDA6.3过程审核规程涵盖了许多方面,包括组织结构和职责、过程管理、风险管理、资源管理、供应商评估和供应商开发等。
它要求供应商建立一套适应其产品和过程的质量管理体系,并确保其有效运作和改进。
第三步:准备VDA6.3过程审核。
在准备VDA6.3过程审核之前,供应商应该先确保其质量管理体系已按照VDA6.3的要求进行构建和实施。
这包括开发组织结构和职责、过程流程图、风险分析和评估等方面的文件和记录。
供应商还应该进行内部审核,以确保其质量管理体系的有效性。
第四步:进行VDA6.3过程审核。
VDA6.3过程审核由经过培训和资格认证的审核员执行。
审核员将按照VDA6.3的要求进行审核,并与供应商的员工进行交流和访谈,以了解其质量管理体系的有效性和改进机会。
审核员还会检查供应商的文件和记录,以确保其符合VDA6.3的要求。
第五步:发现和记录审核结果。
在执行VDA6.3过程审核的过程中,审核员可能会发现一些不符合VDA6.3要求的问题。
这些问题将被记录下来,并与供应商的管理层和员工进行沟通,以便他们能够采取措施纠正问题并改进其质量管理体系。
第六步:审核结果的评估和认证。
一旦审核完成,审核员将评估供应商对不符合项进行纠正和改进的措施。
如果供应商能够有效地解决问题,并满足VDA6.3的要求,他们将获得VDA6.3过程审核的认证,并被列为合格供应商。
第七步:监督和持续改进。
VDA6.3_过程审查
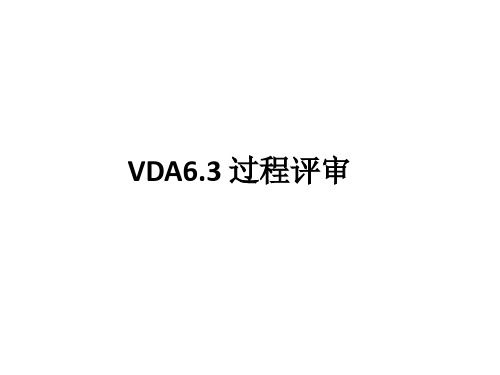
德国汽车工业联合会质量标准(VDA 6)
目的:1.开发以过程为导向的审核方法 2.作为产品生命周期的汽车标准
过程评审是实现过程监控的一种非常重要的工具。
VDA6.3过程审核
P1:潜力分析(新增内容) P2:项目管理(新增内容) P3:产品和过程开发的规划 P4:产品和过程开发的实现 P5:供应商管理 P6:过程分析/ 生产 P7:客户支持,客户满意度,服务 插图2:过程要素同产品生命周期之间的相互关联
KO (Communication CO) – 联络沟通 文件化、建立/保存记录(如:质量、问题)
RI (Risk-Oriented RI) --风险识别和导向 测量目标、监测过程有效性、数据分析、持续改进
VDA6.3过程审核
P3:产品和过程开发的策划:
提问概述 P3 产品和过程开发的策划
潜力
物流和
有形产品的过程
项目管理(P2)
EPM
产品和过程开发的策划(P3)
EPP
产品和过程开发的实现(P4)
EPR
供方管理(P5)
ELM
过程分析/生产(P6)
EPG
顾客支持/顾客满意/服务(P7)
Ek
定量评分定级方法:
VDA6.3过程审核
定级 A B C
符合率EG [%] EG >= 90
80 <= EG < 90 EG < 80
KPI? Effective & Efficiency
VDA6.3过程审核
VDA6.3过程审核
VDA6.3过程审核
过程导向式的审核—风险分析方法
Resources ? Equipments?
Input
新版DFMEA六步法
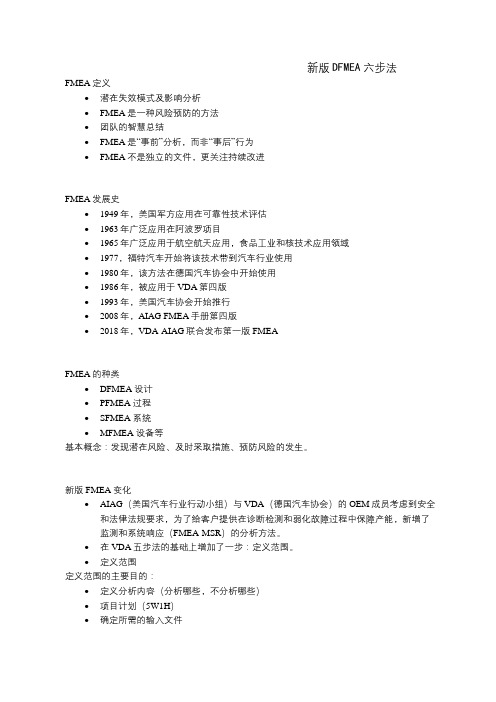
新版DFMEA六步法FMEA定义•潜在失效模式及影响分析•FMEA是一种风险预防的方法•团队的智慧总结•FMEA是“事前”分析,而非“事后”行为•FMEA不是独立的文件,更关注持续改进FMEA发展史•1949年,美国军方应用在可靠性技术评估•1963年广泛应用在阿波罗项目•1965年广泛应用于航空航天应用,食品工业和核技术应用领域•1977,福特汽车开始将该技术带到汽车行业使用•1980年,该方法在德国汽车协会中开始使用•1986年,被应用于VDA第四版•1993年,美国汽车协会开始推行•2008年,AIAG FMEA手册第四版•2018年,VDA-AIAG联合发布第一版FMEAFMEA的种类•DFMEA 设计•PFMEA 过程•SFMEA 系统•MFMEA 设备等基本概念:发现潜在风险、及时采取措施、预防风险的发生。
新版FMEA变化•AIAG(美国汽车行业行动小组)与VDA(德国汽车协会)的OEM成员考虑到安全和法律法规要求,为了给客户提供在诊断检测和弱化故障过程中保障产能,新增了监测和系统响应(FMEA-MSR)的分析方法。
•在VDA五步法的基础上增加了一步:定义范围。
•定义范围定义范围的主要目的:•定义分析内容(分析哪些,不分析哪些)•项目计划(5W1H)•确定所需的输入文件•定义团队指责定义范围输入:•法律法规•顾客要求(内部和外部)•框(边界)图•参数(P)图•原理图U物料清单(BOM)•QFD U可靠性分析在一规定时间内零件修理和更换的频率,以及长期可靠性/耐久性试验的结果。
常见可靠性测试:低温冲击、耐候性试验、盐雾试验、疲劳试验等•卡诺模型•以往质量问题等•结构分析③功能分析④失效分析⑤风险分析⑥优化全新的FMEA表格7大变化点。
VDA6.3-FMEA基础知识培训
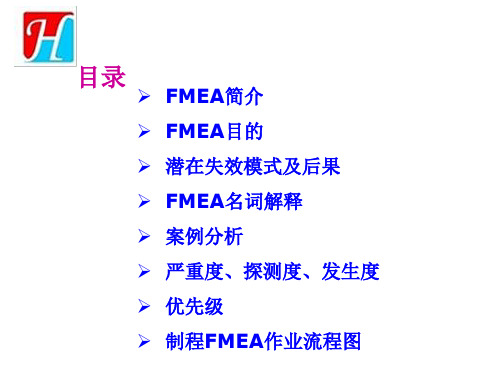
FMEA报告应至少每半年进行一次评审及更新。 然而,评审周期应增加到每月当:
任何重大的变更,如果会影响产品的质量和过程的稳定 客户对于质量及过程的投诉 识别了新的特殊特性 任何项目105
任何重大的变更如果会影响产品的质量和过程的稳定客户对于质量及过程的投诉任何项目105制程fmea作业流程认明每一操作之重要性决定通用之制程管制yes是否还yes有其他可能不良模式原因是否还有list所见特性项目并判定是否为不良模式指出其可能影响及发生决定不良模式之严重度发生度及难检度计分其他不良模式原因之组合存在求出rpn追踪确认依rpn研究改正措施持续改善记录改正措施并计算改正措施实施后之rpn改正措施之展开
Moderate 一般
2 per thousandBiblioteka / 1 in 5006
2 次每 1000 个 / 1 次每 500 辆中 0.5 per thousand / 1 in 2,000 0.5 次每 1000 个 / 1 次每 2000 辆中 0.1 per thousand / 1 in 10,000 0.1 次每 1000 个 / 1 次每 10,000 辆中 Low 低 0.01 per thousand / 1 in 100,000 0.01 次每 1000 个 / 1 次每 100.000 辆中 ≤0.001 per thousand / 1 in 1,000,000 ≤0.001 次每 1000 个中 / 1 次每 1,000,000 Very Low 非常低 Failure is eliminated through preventive control 失效通过预防控制消除了 3 4 5
01.过程审核VDA6.3

b)
公司收入金额=月平均工资*节约人数 *50%= 5200* 63人*50%=16.38万
c)
员工激励金额=月平均工资*节约人数 *50%= 5200* 63人*50%=16.38万
三、第一阶段减人绩效激励(QC)
按公司50%+员工50%激励方式进行激 励,预 计每月 激励金 额为:
(94) 序号 1 人均值+523
二、品质部增效减人:编制优化状况 (QC人 员)
序号
部门
减少人员
比例
1
一厂品质部
10
ቤተ መጻሕፍቲ ባይዱ
2
二厂品质部
0
3
三厂品质部
28
4
四厂品质部
22
线体数量 减少
560 13% 600 0% 720 31% 550 26%
原编制
76 92 90 84
优化后编制
66 92 62 62
5
客服
16
15
1
6%
6
来料
8
6
2
25%
序号
部门
编制人数
6.4:质量体系审核-生产装备 提升总金额
1
一厂品质部
80
人均值+523
2
二厂品质部
103
3
三厂品质部
73
16.38万
4
四厂品质部
75
5
客服
15
6
来料
6
7
实验室
10
总计
313
备注:第二阶段激励根据生产计件效 果及品 质第二 阶段减 人情况 确定绩 效激励 方案。
拟制:
审核:
VDA6.3 讲解
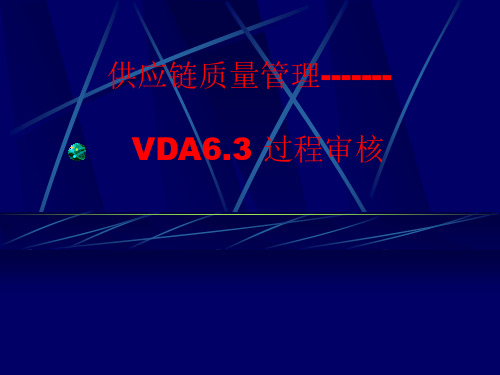
根据职业经验和素质选择合格的审核人员 安排审核任务。 按审核计划或根据发生的事件实施过程审核
3.4.3.2 审核员
与被审核组织/职能部门进行协商(确定要审核的过程、接 口等) 准备审核(研究资料,制订审核提问表,邀请专家参加或 利用专业诀窍等)
供应链质量管理------VDA6.3 过程审核
2 体系审核、过程审核及产品审 核之间的关系
体系审核、过程审核及产品审核是三种 审核方式。列举这三种审核方式并不说 明不存在其他审核方式。
2 体系审核、过程审核及产品审 核之间的关系
比较:
审核方式 体系审核 过程审核 产品审核 审核对象 质量管理体系 产品诞生过程/批量生产 服务过程/服务的实施 产品或服务 目的
3 关于过程审核的规定
实施审核 评分定级 末次会议和撰写报告 要求采取纠正措施 验证纠正措施的有效性 保密义务
保持应有的资格
熟悉最新的标准及文献 审核人员应具备的专业知识 过程知识
4 审核流程
审核总是按相同的系統方法进行:
准备 实施 报告和总结 纠正措施、跟踪、有效性验证。
审核开始前召开首次会议。根据不同情况确 定首次会议的时间和內容。 不同情况包括:
外部审核 內部审核 针对事件进行的审核 按计划进行的审核
6 实施审核
6.2 审核过程
按照事先已制订好的提问表进行审核。既可按照编码顺序也 可隨机提问。 提问的方式,例如:5W提问方式(为什么,何时,何人,如 何做等)以及其他的提问技巧是审核员培训的基本內容,在 此不再进一步闡述。 实践证明,多次用“为什么……”提问有利于对过程工艺进行 深入的分析。 在审核期间,可以提出新的提问并增加到提问表里。 通过提问把现场的人员也納入到审核过程中。建议隨时记录 发现的优点以及不足之处。 为了避免在末次会议上发生沖突,必须尽量在现场澄清不明 之处并达成一致意見。 在审核时若发现严重的缺陷,必须与过程負责人共同制订并 采取紧急措施。
【精品】VDA6.3过程审核标准解析(服务诞生过程.服务实施)PPT课件

审核方式 审核对象
目的
体系审核 过程审核 产品审核
质量管理体系
产 品 诞 生 过 程/批 量 生 产 服 务 诞 生 过 程/服 务 实 施
产品或服务
对基本要求的完 整性及有效性进
行评定 服 务 诞 生 /服 务 实 施过程的质量能
力进行评定 对产品的质量特
性进行评定
3
• 提问和过程要素的单项评分
分数 对符合程度要求的评定 10 完全符合 8 绝大部分符合,只有微小的偏差
6 部分符合有较大的偏差 4 小部分符合,有严重的偏差 0 完全不符合
• 审核结果的综合评分
序号
服务
代码
1
策划
EDE
2
外委服务/外购产品
EZ
3
各工序的平均值
EPG
4
服务/顾客满意程度 EK
E1+E2+---+EN
EPG= 被评定工序的数量 (%)
-在合适的平面上有充足的容量。 -在缺少运营工具时采取的紧急措施。
17
-地面要求的输送装备,运输工具,仓库设施,电子数据管理硬件,测量和检测工具 这 些必备装备的可使用性。
-针对气候和在运输,转运以及储存过程中受到的机械影响采取的零件保护措施。
-所用工具的情况以及维护保养。
-准备好测量以及检验工具。
2.纠正措施的执行必须要有上一级监督且要认可签字. D3.2.2.3纠正措施的落实状态随时都有可追溯性吗?
1.纠正措施的执行必须有计划. <<纠正措施落实情况追踪表>>可按计划的完 成的阶段点做追踪记录.
2.现场的具体情况要有状态标识. 必须考虑到,例如: -完成偏差报告(例如:来自以前的物流审核)。 -连续的Soll(额定)-IST(实际)-偏差和对偏差的控制。 -全过程的措施文件。
VDA 6_3过程审核
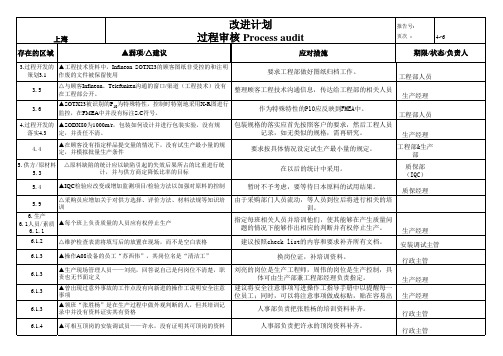
▲H-09设备能力Speed
,CMK=1.17,不能满足要求(1.67)
要求重做,由小沈验收。
生产经理
6.2.2
▲平板机vision system设定没规范化,且掌握此设定技术的人员太 建议vision system设定要规范化,并增加掌握此设定的
少
技术人员。
工程部
6.2.4
△SOTX23,P10为S.C,建议根据目前的经验制作表达“与制造参 数和制造工位之间的关系”(如:压带、气流量)
6.3.4
△生产现场的原料应采用一种固定的方法以让操作人员识别,是 什么材料
6.4缺陷分析/纠 正措施/持续改
进6.4.2
△应对过程中产生的不合格的纠正措施事项进行统计,提高过程 中频繁的不合格原因分析技术
同意。
质保部
建议用粘贴纸或印章的形式表明检验状态标识,由于目
前生产质量处在不稳定期间,这个过程必须完成。 质保部&仓库
同7.2。
投诉,至今才回复给顾客)
销售部 销售部 销售部
同意此建议,本星期开sales meeting.
△多次送样的原因应被记录,并告知QC,以提醒下次检验时进行 关注
多次送样原因的记录曾经被维持过一个月,但后来没有 继续下去,本星期开会将讨论sales如何做好送样跟踪情
况的问题。
△应统计目前纠正措施回复的时效性,以反映目前纠正措施的反
应速度有无改进的可能。(如Telefunken SODX80的在2004.4.16
整理顾客工程技术沟通信息,传达给工程部的相关人员
生产经理
3.6
▲SOTX23被识别的P10为特殊特性,控制时特别地采用X-R图进行 监控,在FMEA中并没有标注S.C符号。
VDA6.3及过程管理分解

第四章
VDA6.3/P6
P6.3 6.3.1 6.3.2* 6.3.3
所有生产过程是否受控?工艺流程 是否对员工委以监控产品和过程质量的职责和权限? 员工是否能从事被安排的工作,其资质是否始终有效? 是否有人员上岗计划?
零部件 处置
PV
ZI
KO
RI
X X X X
VDA6.3及过程管理
6.6.3
是否根据需要对产品/零部件进行适当仓储,所使用 的运输设备/包装方式是否与产品/零部件的特殊特性 相互适应?
是否进行了必要的记录和放行,并且进行了相应的 存档?
X
X
X
6.6.4
VDA6.3及过程管理
VDA6.3及过程管理
X X
X X X
6.5.4*
对过程和产品是否定期开展审核?
X
VDA6.3及过程管理
第四章
VDA6.3/P6
6.5.1关注要点: 定义并且记录了产品和过程衡量指标;在设定值和实际结果之间开展了对比; 明确了具体的过程目标,并且开展了监控以及联络沟通; 对不符合项加以分析,同时采取了适当的改进措施; 不断挖掘潜在的改进可能 6.5.2关注要点:
VDA6.3及过程管理
第四章
VDA6.3/P6
6.2.4关注要点: 在控制计划中定义了特殊产品和过程参数,并且加以系统的监控(SPC); 对于任何影响到产品特性的偏差,必须得到客户许可;对于特殊特性,具体明确了质量记录 要求。 6.2.5关注要点:
对于没有被放行的零部件、缺陷件以及带有缺陷特征的零部件,必须通过可靠地流程加以隔
发放以及使用均且加以了记录。
VDA6.3及过程管理
第四章
P6.5 6.5.1 6.5.2 6.5.3*
VDA6.3新版过程FMEA六步法

过程FMEA分六步进行这六个步骤为失效模式和后果分析提供了一种系统的分析方法,并作为过程风险分析的记录。
PFMEA分析六步如下:∙PFMEA第一步:定义范围及项目计划∙PFMEA第二步:结构分析∙PFMEA第三步:功能分析∙PFMEA第四步:失效分析∙PFMEA第五步:风险评估∙PFMEA第六步:优化PFMEA第一步:定义范围过程范围定义的目的是:∙项目识别-哪些过程/哪些过程的部分要进行分析?∙项目计划- 培养一些有发展潜力的团队人员、创建项目时间表等∙定义分析界限- 包括什么,不包括什么。
∙确定能够使用的相关经验教训和决策,例如:最佳实践、准则和标准、防错-防呆方法等等。
工厂可能影响产品质量的过程,以及考虑用于PFMEA分析的过程:∙接收过程、∙零件和材料存储、∙产品和材料交付、∙制造、∙组装、∙打包、∙贴标签、∙运输、∙存储、∙维护过程、∙检验过程∙返工和返修过程等。
图确定过程范围PFMEA第二步:结构分析过程结构分析的主要目标是:∙结构化产品或过程元素∙可视化分析范围∙确定工步∙作为功能分析步骤的基础流程图是结构分析的输入文件。
图过程流程图结构树按层次排列系统元素,并通过结构连接说明关联关系。
这个形象化的结构考虑了过程项目、工步和过程工作要素之间的关系。
图结构分析-结构树示例(电机组装线)工步是PFMEA分析的重点!图工步影响工步失效的潜在原因,其类别数量由4M、5M、6M等决定4M类别:机人材料(间接)环境(环境)其他类别但不限于:方法测量图结构分析扩展表格示例PFMEA第三步:功能分析过程工作要素功能通过实现工步来反应过程/产品的特性。
示例:用手从滑槽中取出烧结轴承示例:将磨损的轴承压入定子壳内功能和结构逻辑连接时,应该问以下这些问题:“发生了什么”?如何从左到右实现产品/过程要求-(过程项目- 工步- 过程工作元素)“为什么”?为什么从右到左实施产品过程的要求-(过程工作元素-工步- 过程项目)功能网可视化过程项目功能、工步功能和过程工作元素功能之间的交互通过链接来可视化:功能网、功能结构、功能树、功能矩阵或用PFMEA工具软件进行的功能分析。
VDA6.3过程审核教材

2021/6/21
22
7.3 审核具体落实
出现下列情况,评审小组可以决定中断审核: 1、在评审过程中必要的信息被拒绝提供。 2、明显触犯了法律法规。 3、评审人员受到蓄意干扰。 4、虽然事先进行了协商,但仍然被拒绝进入与平时有关区域。 5、被评审组织的评审准备工作严重不足。 6、提供了明显失实的信息
可制造性开展了评价? P3.3 是否为产品和过程开发编制了相关的计划资源调查 P3.4 针对产品和过程开发,是否考虑到了所需的资源 P3.5 针对采购对象,是否编制了相关的质量管理计划?
2021/6/21
30
过程要素P4
产品和过程开发的实 现
2021/6/21
31
过程要素P4:产品和过程开发的实现
注:如果中断审核,则必须说明原因,对于中断审核前的审核 记录应保留,应由负责评审组织决定是否重新评审。
2021/6/21
23
7.3 审核具体落实
过程要素P2
项目管理
2021/6/21
24
过程审核提问表
◦ 在过程审核时应优先从产品的角度来观察所审核的过程, 因为过程对产品的影响特别重要。
◦ 提问表分结构如下: ◦ P2项目管理 ◦ P3 产品和过程开发的规划 ◦ P 4产品和过程开发的落实 ◦ P 5供应商管理 ◦ P 6生产过程分析 ◦ P 7客户支持,满意度、服务
了控制?
2021/6/21
33
过程要素P5
供应商管理
2021/6/21
34
过程要素P5:供应商管理
*P5.1 是否只和获得批准且具备质量能力的供应商开 展合作?
2021/6/21
21
7.3 审核具体落实
新版FMEA标准改进以及新标准的特点:从六步法进阶到七步法
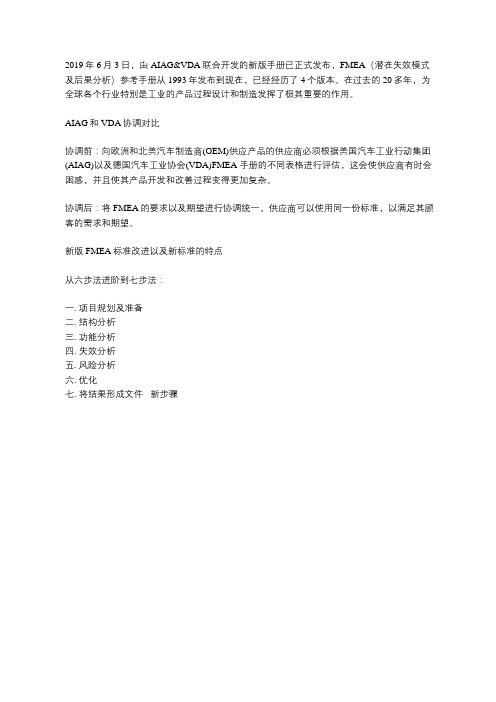
2019年6月3日,由AIAG&VDA联合开发的新版手册已正式发布,FMEA(潜在失效模式及后果分析)参考手册从1993年发布到现在,已经经历了4个版本。
在过去的20多年,为全球各个行业特别是工业的产品过程设计和制造发挥了极其重要的作用。
AIAG和VDA协调对比
协调前:向欧洲和北美汽车制造商(OEM)供应产品的供应商必须根据美国汽车工业行动集团(AIAG)以及德国汽车工业协会(VDA)FMEA 手册的不同表格进行评估,这会使供应商有时会困惑,并且使其产品开发和改善过程变得更加复杂。
协调后:将FMEA的要求以及期望进行协调统一,供应商可以使用同一份标准,以满足其顾客的需求和期望。
新版FMEA标准改进以及新标准的特点
从六步法进阶到七步法:
一. 项目规划及准备
二. 结构分析
三. 功能分析
四. 失效分析
五. 风险分析
六. 优化
七. 将结果形成文件 - 新步骤。
VDA63新版过程FMEA六步法
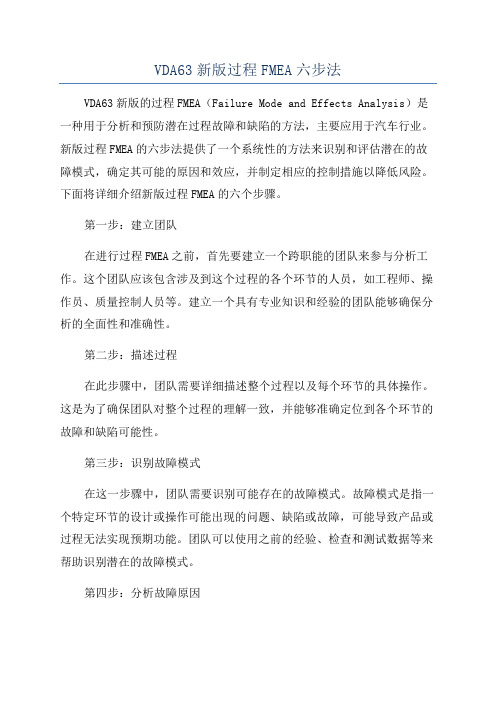
VDA63新版过程FMEA六步法VDA63新版的过程FMEA(Failure Mode and Effects Analysis)是一种用于分析和预防潜在过程故障和缺陷的方法,主要应用于汽车行业。
新版过程FMEA的六步法提供了一个系统性的方法来识别和评估潜在的故障模式,确定其可能的原因和效应,并制定相应的控制措施以降低风险。
下面将详细介绍新版过程FMEA的六个步骤。
第一步:建立团队在进行过程FMEA之前,首先要建立一个跨职能的团队来参与分析工作。
这个团队应该包含涉及到这个过程的各个环节的人员,如工程师、操作员、质量控制人员等。
建立一个具有专业知识和经验的团队能够确保分析的全面性和准确性。
第二步:描述过程在此步骤中,团队需要详细描述整个过程以及每个环节的具体操作。
这是为了确保团队对整个过程的理解一致,并能够准确定位到各个环节的故障和缺陷可能性。
第三步:识别故障模式在这一步骤中,团队需要识别可能存在的故障模式。
故障模式是指一个特定环节的设计或操作可能出现的问题、缺陷或故障,可能导致产品或过程无法实现预期功能。
团队可以使用之前的经验、检查和测试数据等来帮助识别潜在的故障模式。
第四步:分析故障原因一旦故障模式被识别出来,团队就需要分析可能导致这些故障模式发生的原因。
这可能涉及到设计或操作的不当、材料质量问题、设备故障等多个方面。
团队可以使用5W1H(What、When、Where、Who、Why、How)等方法来系统性地找出故障的根本原因。
第五步:确定故障效应识别和分析故障模式后,团队需要确定这些故障模式可能引发的效应,包括对产品质量、安全性和可靠性的影响等。
这有助于团队评估潜在故障的严重程度和发生概率,并制定相应的控制措施。
第六步:制定控制措施最后一步是根据分析结果制定控制措施来降低故障风险。
团队应该考虑采取的预防性措施来预防故障的发生,以及可能的发现和修正措施来控制故障的后果。
除了以上六个步骤,新版VDA63还强调了对经验数据的正确应用、对特殊过程和产品的特殊要求的特殊评估等方面的要求。
VDA6.3
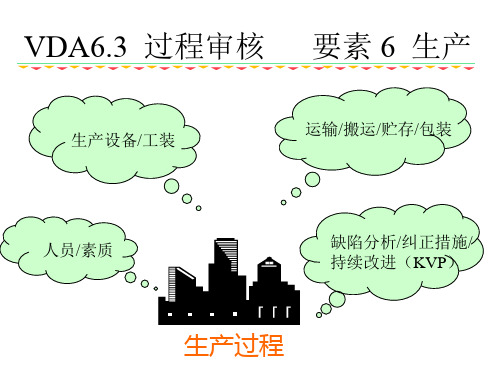
VDA6.3 过程审核
要素 6 生产
分要素 6.1:人员/素质 6.1.5 是否有效地使用了提高员工工作积极性的方法? 是否有效地使用了提高员工工作积极性的方法? 要求/说明 通过针对性的信息(宣传)促进员工的投入意识,并 以此来提高质量意识。 需考虑要点,例如: -质量信息(要求值/实际值) -志愿行动(培训、质量小组) -对质量改进的贡献 -改进建议 -低病假率 -自我评定
VDA6.3 过程审核
要素 6 生产
分要素 6.2:生产设备/工装 6.2.1 生产设备 工装模具是否能保证满足产品特定的质量 生产设备/工装模具是否能保证满足产品特定的质量 要求? 要求? 要求/说明 需考虑要点,例如: -对重要特性/过程特定的参数进行机器能力调查/过程能力 调查 -重要参数要强迫控制/调整 -在偏离额定值时报警(如:声光报警、自动断闸) -上/下料装置 -模具/设备/机器的保养维修状态(包括有计划的维修)
VDA6.3 过程审核
要素 6 生产
分要素 6.3:运输/搬运/贮存/包装 6.3.1 产品数量 生产批次的大小是否按需求而定? 产品数量/生产批次的大小是否按需求而定 生产批次的大小是否按需求而定? 是否有目的地运往下道工序? 是否有目的地运往下道工序? 要求/说明 需考虑要点,例如:
-足够、合适的运输器具 -最小库存/无中间库存 -准时化生产 -仓库管理 -向下道工序只供合格件 -信息流 -定置库位 -看板管理 -先进先出 -更改状态 -数量记录/统计
VDA6.3 过程审核
要素 6 生产
分要素 6.2:生产设备/工装 6.2.3 生产工位、检验工位是否符合要求? 生产工位、检验工位是否符合要求? 要求/说明 工作环境条件(包括返工/返修工位)必须符合于产品 及工作内容,以避免污染、损伤、混批混料/说明错误 。
IATF16949-2016VDA6.3过程审核及VDA6.5产品审核培训学习教材

Solution proposal 简易方案:
for every question (i.e. 1/3 calculation dropped).每个问题比重相等,如1/3比例下调 Note: In the case of several process stage, the questions from P6 are average across all process stages. 注:如果有几个过程步骤,P6的问题按所有过程步骤平均计算
Key changes in new VDA6.3
主要变化点
• S/W issues added to questionary?提问表中加入 S/W 问题 • Audit result/ evaluation method weight of each questions same 每个问题对审核结果/评价方法的比 重一致 • Matrix and remarks, reference for questions矩阵和 注释,问题参考 • Auditor qualification/审核员资质 • Questionary for Service provider /服务提供的提问 表
--企业是否识别了适用的清洁度要求并在内部文件中规定?是否识别了在企业内有哪些污 染物应予以控制? --对污染物控制要求的符合性会如何影响到最终产品? --若不能满足清洁度规范会在企业内部导致怎样的后果?
--当发现产品的清洁度未能达标时如何处置,是否形成文件流程规定?
--零部件的清洁度结果如何验证? --企业是否有对应批量生产的清洁度评审的计划(计划包括:评审范围、频次、容量、 等),以及对应的反应计划和控制流程?
VDA18卓越经营模式”引导企业成为世界上最优秀的公司
FMEA制造工艺质量的六步分析法

FMEA制造工艺质量的六步分析法关注AIAG-VDA FMEA要求用六步法分析如下图示其中第1-3步为系统分析是FMEA分析的先决条件第4-6步为失效分析和风险降低下面对各步详述该步骤主要利用边界图等工具确定FMEA分析的范围如下图示▼结构树分析等工具展示设计或过程之间的相互关系和作用新版FMEA要求分析3个层级即直接上一层级( Higher Level )> 聚焦分析层级( Focus Level ) > 直接下一层级( Lower Level )常用的分析工具为结构树如下图示▼该步骤主要利用使用 P图功能分析表和接口矩阵等工具识别设计或过程的功能和要求并赋予给系统层级和下一层级(产品、部件层级)如下图示▼常用的分析工具为功能分析表示例如下(离合器功能)▼该步骤是新版FMEA特色所在将失效影响、失效模式和失效原因之间的逻辑关系以“瀑布模型”的方式进行展示上一层级的失效模式为下一层级的失效影响下一层级的失效模式即为上一层级的失效原因如下图示▼在进行失效分析时需同时进行三个层级的分析并在FMEA表中体现出三个层级之间的逻辑关系如下图示▼该步骤的主要目的是对严重度频度和探测度进行打分并确定改进行动的优先级(AP)新版FMEA打分标准与AIAG第四版 FMEA手册有很大区别并取消了RPN以AP代替严重度(S)打分表(适用DFMEA)与AIAG第4版手册有4点变化(1)不论是否预警,影响到安全的严重度均为10(2)影响法规符合性的严重度为9(3)严重度在2-4之间取消了定量描述用“Haptics”(察觉,感官)表述(4)增加“公司或产品示例”栏需公司自行定义频度(O)是衡量预防控制有效性的指标是相对值而不是绝对值FMEA小组可决定评分标准但在公司内部必须使用一致的标准进行打分以确保连续性频度(O)打分表(适用DFMEA)▲从上表可以看出新版 FMEA 的频度考虑了设计成熟度(估计发生)产品成熟度(产品实践)和预防措施(预防控制)三个维度进行评分增加了“公司或产品示例”栏探测度(D)是探测控制有效性的指标以在产品发布、生产之前可靠地探测失效原因或失效模式探测度是指在现行过程控制探测栏里的最佳探测控制相关等级探测度(D)打分表(适用DFMEA)新版 FMEA 手册使用的行动优先级(AP)分为三种A高优先级(H)最高级别的改进优先级小组必须(shall)确定适当的行动以改进预防和/或探测控制如果没有改进措施应有文件化的理由说明B中优化级(M)中等级别的改进优先级小组应当(should)确定适当的行动以改进预防和/或探测控制如果小组结合公司实际情况不采取改进措施应有证据显示为什么控制是足够的C低优化级(L)最低级别的改进优先级小组可以(could)确定改进预防或探测控制的措施注如果暂时不采取改进措施至少应包括“不需要进一步行动”的声明我们推荐以探测度(D)为基础的AP表示例如下例1D为7-10,S为5,O为3由下表可知行动优先级为“M”例2D为5-6,S为5,O为3由下表可知行动优先级为“M”例3D为2-4,S为5,O为3由下表可知行动优先级为“L特例D=1时AP表中由部分区域行动优先级“未定义”我们相信新版FMEA正式发布时将揭开“未定义”的神秘面纱FMEA小组必须决定是否需要采取进一步的措施来降低所发现的任何风险由于资源、时间、技术和其他因素所限团队必须正确选择改进的优先级只有当所有的改进措施完成及验证后才能进行产品发布关注AIAG-VDA FMEA要求用六步法分析如下图示其中第1-3步为系统分析是FMEA分析的先决条件第4-6步为失效分析和风险降低下面对各步详述该步骤主要利用边界图等工具确定FMEA分析的范围如下图示▼结构树分析等工具展示设计或过程之间的相互关系和作用新版FMEA要求分析3个层级即直接上一层级( Higher Level )> 聚焦分析层级( Focus Level ) > 直接下一层级( Lower Level )常用的分析工具为结构树如下图示▼该步骤主要利用使用 P图功能分析表和接口矩阵等工具识别设计或过程的功能和要求并赋予给系统层级和下一层级(产品、部件层级)如下图示▼常用的分析工具为功能分析表示例如下(离合器功能)▼该步骤是新版FMEA特色所在将失效影响、失效模式和失效原因之间的逻辑关系以“瀑布模型”的方式进行展示上一层级的失效模式为下一层级的失效影响下一层级的失效模式即为上一层级的失效原因如下图示▼在进行失效分析时需同时进行三个层级的分析并在FMEA表中体现出三个层级之间的逻辑关系如下图示▼该步骤的主要目的是对严重度频度和探测度进行打分并确定改进行动的优先级(AP)新版FMEA打分标准与AIAG第四版 FMEA手册有很大区别并取消了RPN以AP代替严重度(S)打分表(适用DFMEA)与AIAG第4版手册有4点变化(1)不论是否预警,影响到安全的严重度均为10(2)影响法规符合性的严重度为9(3)严重度在2-4之间取消了定量描述用“Haptics”(察觉,感官)表述(4)增加“公司或产品示例”栏需公司自行定义频度(O)是衡量预防控制有效性的指标是相对值而不是绝对值FMEA小组可决定评分标准但在公司内部必须使用一致的标准进行打分以确保连续性频度(O)打分表(适用DFMEA)▲从上表可以看出新版 FMEA 的频度考虑了设计成熟度(估计发生)产品成熟度(产品实践)和预防措施(预防控制)三个维度进行评分增加了“公司或产品示例”栏探测度(D)是探测控制有效性的指标以在产品发布、生产之前可靠地探测失效原因或失效模式探测度是指在现行过程控制探测栏里的最佳探测控制相关等级探测度(D)打分表(适用DFMEA)新版 FMEA 手册使用的行动优先级(AP)分为三种A高优先级(H)最高级别的改进优先级小组必须(shall)确定适当的行动以改进预防和/或探测控制如果没有改进措施应有文件化的理由说明B中优化级(M)中等级别的改进优先级小组应当(should)确定适当的行动以改进预防和/或探测控制如果小组结合公司实际情况不采取改进措施应有证据显示为什么控制是足够的C低优化级(L)最低级别的改进优先级小组可以(could)确定改进预防或探测控制的措施注如果暂时不采取改进措施至少应包括“不需要进一步行动”的声明我们推荐以探测度(D)为基础的AP表示例如下例1D为7-10,S为5,O为3由下表可知行动优先级为“M”例2D为5-6,S为5,O为3由下表可知行动优先级为“M”例3D为2-4,S为5,O为3由下表可知行动优先级为“L特例D=1时AP表中由部分区域行动优先级“未定义”我们相信新版FMEA正式发布时将揭开“未定义”的神秘面纱FMEA小组必须决定是否需要采取进一步的措施来降低所发现的任何风险由于资源、时间、技术和其他因素所限团队必须正确选择改进的优先级只有当所有的改进措施完成及验证后才能进行产品发布。
vda6.3过程审核方法
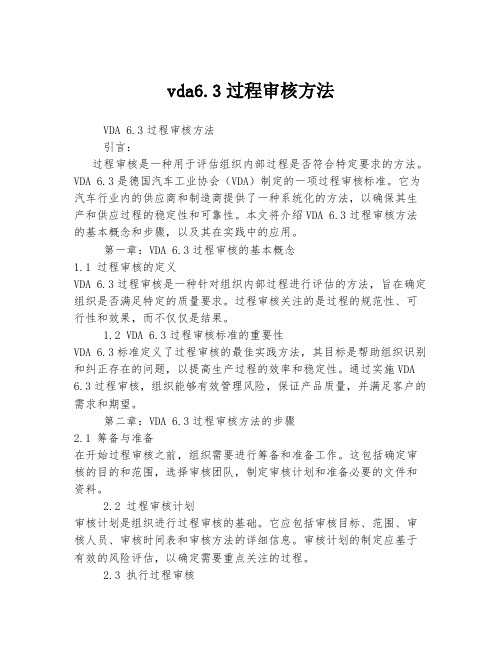
vda6.3过程审核方法VDA 6.3过程审核方法引言:过程审核是一种用于评估组织内部过程是否符合特定要求的方法。
VDA 6.3是德国汽车工业协会(VDA)制定的一项过程审核标准。
它为汽车行业内的供应商和制造商提供了一种系统化的方法,以确保其生产和供应过程的稳定性和可靠性。
本文将介绍VDA 6.3过程审核方法的基本概念和步骤,以及其在实践中的应用。
第一章:VDA 6.3过程审核的基本概念1.1 过程审核的定义VDA 6.3过程审核是一种针对组织内部过程进行评估的方法,旨在确定组织是否满足特定的质量要求。
过程审核关注的是过程的规范性、可行性和效果,而不仅仅是结果。
1.2 VDA 6.3过程审核标准的重要性VDA 6.3标准定义了过程审核的最佳实践方法,其目标是帮助组织识别和纠正存在的问题,以提高生产过程的效率和稳定性。
通过实施VDA 6.3过程审核,组织能够有效管理风险,保证产品质量,并满足客户的需求和期望。
第二章:VDA 6.3过程审核方法的步骤2.1 筹备与准备在开始过程审核之前,组织需要进行筹备和准备工作。
这包括确定审核的目的和范围,选择审核团队,制定审核计划和准备必要的文件和资料。
2.2 过程审核计划审核计划是组织进行过程审核的基础。
它应包括审核目标、范围、审核人员、审核时间表和审核方法的详细信息。
审核计划的制定应基于有效的风险评估,以确定需要重点关注的过程。
2.3 执行过程审核过程审核的执行包括收集和评估与过程相关的信息和数据。
审核人员需要与相关部门和人员进行交流,以了解过程的实施情况,并验证其是否符合VDA 6.3标准的要求。
此外,审核人员还需要对所收集的信息进行记录和分析,以确定是否存在违规或改进的机会。
2.4 发现与报告在过程审核的过程中,审核人员可能会发现存在不符合VDA 6.3标准要求的情况。
这些发现需要记录并向组织的管理层进行报告。
报告应包括违规情况的详细描述、可能的原因和建议的改进措施。
- 1、下载文档前请自行甄别文档内容的完整性,平台不提供额外的编辑、内容补充、找答案等附加服务。
- 2、"仅部分预览"的文档,不可在线预览部分如存在完整性等问题,可反馈申请退款(可完整预览的文档不适用该条件!)。
- 3、如文档侵犯您的权益,请联系客服反馈,我们会尽快为您处理(人工客服工作时间:9:00-18:30)。
过程FMEA分六步进行
这六个步骤为失效模式和后果分析提供了一种系统的分析方法,并作为过程风险分析的记录。
PFMEA分析六步如下:
•PFMEA第一步:定义范围及项目计划
•PFMEA第二步:结构分析
•PFMEA第三步:功能分析
•PFMEA第四步:失效分析
•PFMEA第五步:风险评估
•PFMEA第六步:优化
PFMEA第一步:定义范围
过程范围定义的目的是:
•项目识别-哪些过程/哪些过程的部分要进行分析?
•项目计划- 培养一些有发展潜力的团队人员、创建项目时间表等
•定义分析界限- 包括什么,不包括什么。
•确定能够使用的相关经验教训和决策,例如:最佳实践、准则和标准、防错-防呆方法等等。
工厂可能影响产品质量的过程,以及考虑用于PFMEA分析的过程:
•接收过程、
•零件和材料存储、
•产品和材料交付、
•制造、
•组装、
•打包、
•贴标签、
•运输、
•存储、
•维护过程、
•检验过程
•返工和返修过程等。
图确定过程范围PFMEA第二步:结构分析
过程结构分析的主要目标是:
•结构化产品或过程元素
•可视化分析范围
•确定工步
•作为功能分析步骤的基础
流程图是结构分析的输入文件。
图过程流程图
结构树按层次排列系统元素,并通过结构连接说明关联关系。
这个形象化的结构考虑了过程项目、工步和过程工作要素之间的关系。
图结构分析-结构树示例(电机组装线)
工步是PFMEA分析的重点!
图工步
影响工步失效的潜在原因,其类别数量由4M、5M、6M等决定
4M类别:
机
人
材料(间接)
环境(环境)
其他类别但不限于:
方法
测量
图
结构分析扩展表格示例
PFMEA第三步:功能分析
过程工作要素功能通过实现工步来反应过程/产品的特性。
示例:用手从滑槽中取出烧结轴承
示例:将磨损的轴承压入定子壳内
功能和结构逻辑连接时,应该问以下这些问题:
“发生了什么”?
如何从左到右实现产品/过程要求-(过程项目- 工步- 过程工作元素)
“为什么”?
为什么从右到左实施产品过程的要求-(过程工作元素-工步- 过程项目)
功能网可视化
过程项目功能、工步功能和过程工作元素功能之间的交互通过链接来可视化:功能网、功能结构、功能树、功能矩阵或用PFMEA工具软件进行的功能分析。
图功能分析结构树示例
图功能分析表格示例PFMEA第四步:失效分析
工步的失效从产品特性和过程特性中推断出。
示例包括:
•不合格
•部分合格
•非预期的活动
•不必要的活动
失效链
几个系统元素的功能的交互必须是可展示的。
例如,用功能树/网或功能矩阵进行
在FMEA中分析失效有三个不同的方面:
•失效影响(FE)
•失效模式(FM)
•失效原因(FC))
图失效链理论模型
失效影响与过程项目(系统,子系统,部件元素或过程名称)的功能相关,失效影响应根据客户可能会注意或碰到的后果来描述。
可能影响安全或导致违反法规的失效需要在PFMEA 中明确标识。
客户可以是:
•内部客户(下一步操作/后续操作/操作指标)
•外部客户(下一层级/OEM /经销商)
•立法机构
•产品、产品最终用户/操作者
失效影响用严重度等级评价:
•工厂内:假设在工厂中检测到缺陷引起的失效模式的影响(工厂将采取什么行动,例如报废)•工厂转运:假设在运送到下一个工厂之前没有检测到缺陷引起的失效模式的影响(下一个工厂会采取什么行动?)
•车辆最终用户:过程项目影响的后果(车辆最终用户将注意到什么,感觉,听到,闻到什么,例如,窗户提升得太慢)
PFMEA第五步:风险评估
过程风险分析的主要目标是:
•预防控制措施的分配(现有和/或已计划的)
•探测控制措施的分配(现有和/或已计划的)
•评估每个失效链的严重度,发生度和探测度。
•客户和供应商之间的层连
有两个不同控制措施组:现行预防控制和现行探测控制。
现行探测措施示例:
•目视检查
•根据样件清单进行目检
•使用成相系统进行光学检查
•使用一定数量的样品进行光学测试
•使用XX设备属性测试
•用卡尺测量尺寸
•抽检
•扭矩监测
•负载检查
•终检等
图过程FMEA中的预防和探测
过程意图曲线
评估
评估每种失效模式,因果关系(失效链或失效网)以估计风险。
风险的评估标准:
严重度(S):代表失效影响的严重程度
发生度(O):表示失效原因发生度
探测度(D):表示探测失效原因/模式的探测度
S、O、D的评估等级分别分为1-10个等级,其中等级10的风险贡献最高。
通过分别检查S、O、D的评级和三者的组合,可以得到对风险因素采取降低风险行动的优先排序。
行动优先级(AP)
之前的FMEA手册建议使用RPN来确定动作优先级,然而并没有说明S. 0,D和RPN的所有组合的理性/逻辑的细节。
AP 表为FMEA团队提供了S. 0和D的所有1000种可能的逻辑组合,它基于逻辑描述每个行动优先级,根据每个S.O.D.值的个体评估对行动优先排序,根据组合的值确定可能需要降低的风险。
优先级高(H)
行动的最高优先级。
团队必须确定一个适用的改进探测和(或)/预防措施,或者证明/说明目前的措施是适当的。
优先级中等(M)
行动的中等优先权。
团队应该确定一个适用的改进预防和/或探测措施,或者由公司自行决定,证明/说明目前的措施是适当的。
优先级低(L)
行动的优先级低,团队可以确定要改进的预防或探测措施。
建议管理层至少审核潜在的严重程度等级9 - 10的失效影响与行动优先级高和中的措施,包括采取的所有建议措施。
6
PFMEA第六步:优化
过程优化的主要目标是:
•确定降低风险所需的措施
•确定责任和目标完成时间
•采取行动的实施和记录
•确认实施行动的有效性。
•采取措施后重新评估风险
•持续改进过程
•完善过程要求、预防和探测措施
如果团队决定不需要进一步的行动,在备注栏中写入“无”或“未计划”,以表示风险分析已完成。
PFMEA可以作为过程持续改进的基础
按以下顺序进行优化是最有效的:
•为了减少发生失效原因(FC)的可能性,修改过程。
•增加检测失效原因或失效模式的能力(FC或FM)。
•在进行过程修改的情况下,再次评估所有受影响的工步
行动的状态
悬而未决:
行动既没有被定义也没有讨论。
待确认(可选):
行动已经确定,但还没有决定。
决策文件正在创建。
待实施(可选):
该行动已经确定,但尚未执行。
已完成:
行动已确定并已经执行完成,其效果已经被证明和记录。
最后的评估已经完成。
放弃:
如果决定不执行某个措施,当与成本,实施时机或业务策略相关的风险大于技术风险时,可能会发生这种情况,则选择“放弃”状态。
图PFMEA优化及新风险评估报告。