质量成本案例分析报告
财务及质量成本分析报告(3篇)

第1篇一、报告概述随着市场竞争的加剧,企业对成本控制的重视程度日益提高。
财务成本和质量成本是企业成本控制的重要组成部分,对企业的经济效益和市场竞争力有着重要影响。
本报告旨在通过对某企业的财务及质量成本进行深入分析,揭示成本构成、成本控制策略以及成本优化措施,为企业提高经济效益和竞争力提供参考。
二、企业概况某企业是一家以生产电子产品为主的高新技术企业,拥有较强的研发能力和生产能力。
近年来,企业产品在国内市场占有率逐年提高,但成本控制方面仍存在一定问题。
为了提高企业经济效益,本报告对企业的财务及质量成本进行深入分析。
三、财务成本分析1. 成本构成(1)原材料成本:原材料成本是企业成本构成的主要部分,占到了总成本的60%以上。
原材料价格波动、采购策略不合理等因素都会对原材料成本产生影响。
(2)人工成本:人工成本包括工资、福利、社保等,占总成本的30%左右。
随着劳动力市场供求关系的变化,人工成本呈现上升趋势。
(3)制造费用:制造费用包括折旧、维修、能源消耗等,占总成本的10%左右。
制造费用的高低与设备先进程度、生产效率等因素密切相关。
2. 成本控制策略(1)优化采购策略:通过与供应商建立长期合作关系,降低原材料采购价格;采用集中采购、批量采购等方式降低采购成本。
(2)提高生产效率:通过技术改造、优化生产流程等方式提高生产效率,降低制造费用。
(3)加强人力资源管理:提高员工技能,降低人工成本。
3. 成本优化措施(1)加强原材料成本控制:密切关注原材料价格走势,合理制定采购计划;加强供应商管理,降低采购成本。
(2)降低人工成本:优化人力资源结构,提高员工素质;加强绩效考核,激发员工积极性。
(3)降低制造费用:加强设备维护,提高设备利用率;合理配置能源,降低能源消耗。
四、质量成本分析1. 成本构成(1)预防成本:预防成本包括质量策划、质量培训、质量审核等,占总成本的10%左右。
(2)鉴定成本:鉴定成本包括产品检验、质量检验等,占总成本的20%左右。
质量成本案例
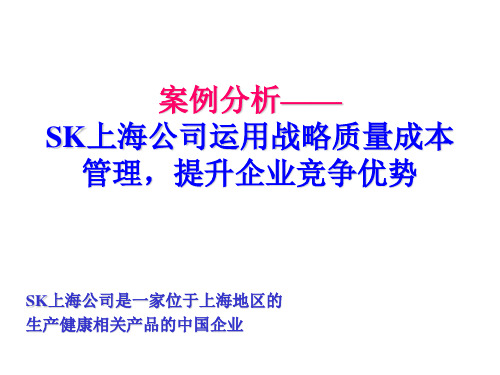
鉴定成本包括: 鉴定成本包括: 测试和检查成本。 检测设备和仪器。 质量审计。 实验室验收检测。 现场评估和测试。 信息费。
(3)内部失败成本
内部失败成本是由于商品在送达顾客之前通过鉴定发 现其质量低劣而发生的成本。这些成本是不增值的并且是 现其质量低劣而发生的成本。 完全不必要的。 完全不必要的。
¥202,300 ¥29,200 ¥14,400 ¥245,900 ¥12,800 ¥3,120 ¥27,000 ¥22,500 ¥180,000 ¥2,220 ¥11,000 ¥2,240 ¥36,000 ¥296,880 0.80% 0.66%
¥301,100 ¥48,600 ¥18,000 ¥367,700 ¥18,920 ¥5,070 ¥48,900 ¥55,800 ¥226,000 ¥4,380 ¥18,900 ¥40,050 ¥51,800 ¥469,820 0.84% 0.66%
3、帕累托图
帕累托图是促成质量问题的各种因素按照发生的频率 由高到低排列的直方图。 由高到低排列的直方图。
图表6-12 质量问题帕累托直方图19X9
累积
次 数 80
60 40 20
0
(1) (2) (3) (4) (5)(6)
质量问题 因素:(1)鸡蛋大小 (2)搅拌速度 (3)溶液
(4)搅拌时间 (5)巧克力质量 (6)不正确冷冻
第一年至第二年 第二年至第三年
上述研究数据说明,SK上海公司通过引入TQM和以稳定 产品质量为特征的战略质量成本控制,取得满意的结果: 客户抱怨减少 公司核心竞争力上升 产品美誉度上升 市场份额占有率提升
一、质量与战略成本管理
质量改进
降低退货率
降低制造成本
提高顾客认知价值
质量成本分析报告范本

质量成本分析报告范本一、引言质量成本分析作为一种管理工具,旨在帮助企业在提高产品质量的同时,有效控制和降低质量成本。
本报告旨在提供一个质量成本分析报告的范本,帮助企业进行质量成本分析,以实现更好的质量管理和成本控制。
二、背景质量成本分析是企业质量管理的重要组成部分,通过对质量管理活动产生的成本进行分析,帮助企业识别质量问题的根源,改进质量管理体系,降低质量成本,提高产品质量和客户满意度。
三、质量成本分类1.预防成本:包括质量规划、培训、设计验证、供应商评估等活动产生的成本。
2.评估成本:包括检验、测试、验证等活动产生的成本。
3.内部故障成本:包括不合格品处理、返工、报废等活动产生的成本。
4.外部故障成本:包括客户投诉处理、召回、赔偿等活动产生的成本。
四、质量成本分析方法1.质量成本比率分析:通过计算不同类型的质量成本在总成本中的占比,识别质量成本的重点领域。
2.趋势分析:通过对历史质量成本数据的分析,识别质量成本的变化趋势,发现潜在问题。
3.标准成本分析:通过制定质量成本的标准,对实际质量成本进行对比分析,找出偏差原因并采取相应措施。
4.效益分析:通过对改进措施的效果进行评估,分析质量投资的回报情况。
五、质量成本控制措施1.质量规划:制定全面的质量管理计划,明确质量目标和指标,并进行跟踪和评估。
2.培训提升:加强员工的质量意识和技能培训,确保所有岗位都能够按照标准进行工作。
3.供应商管理:建立健全的供应商评估体系,选择合格的供应商,并与其保持良好的合作关系。
4.流程优化:优化质量管理流程,缩短交付周期,降低出错率。
5.持续改进:建立持续改进机制,通过分析质量成本数据,寻找问题根源,并采取相应的改进措施。
六、结论通过质量成本分析,企业能够全面了解质量管理活动产生的成本,并找到质量成本的重点领域。
通过合理的质量成本控制措施,企业可以有效降低质量成本,提高产品质量和客户满意度。
质量成本分析报告范本提供了一个简单的框架,帮助企业进行质量成本分析,定制适合自己企业的质量管理措施。
财务部质量成本分析报告(3篇)
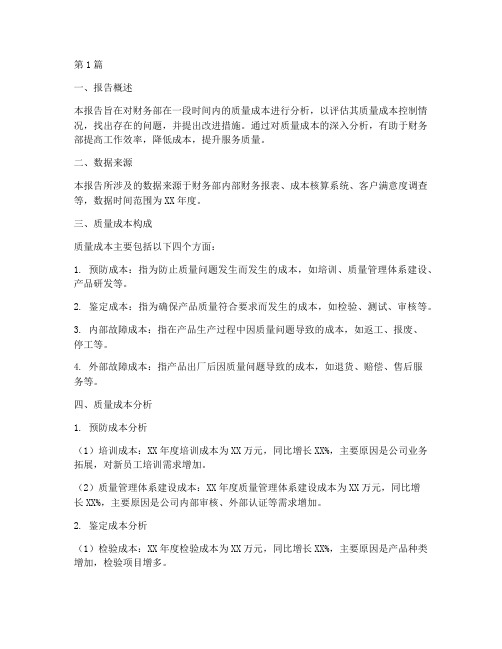
第1篇一、报告概述本报告旨在对财务部在一段时间内的质量成本进行分析,以评估其质量成本控制情况,找出存在的问题,并提出改进措施。
通过对质量成本的深入分析,有助于财务部提高工作效率,降低成本,提升服务质量。
二、数据来源本报告所涉及的数据来源于财务部内部财务报表、成本核算系统、客户满意度调查等,数据时间范围为XX年度。
三、质量成本构成质量成本主要包括以下四个方面:1. 预防成本:指为防止质量问题发生而发生的成本,如培训、质量管理体系建设、产品研发等。
2. 鉴定成本:指为确保产品质量符合要求而发生的成本,如检验、测试、审核等。
3. 内部故障成本:指在产品生产过程中因质量问题导致的成本,如返工、报废、停工等。
4. 外部故障成本:指产品出厂后因质量问题导致的成本,如退货、赔偿、售后服务等。
四、质量成本分析1. 预防成本分析(1)培训成本:XX年度培训成本为XX万元,同比增长XX%,主要原因是公司业务拓展,对新员工培训需求增加。
(2)质量管理体系建设成本:XX年度质量管理体系建设成本为XX万元,同比增长XX%,主要原因是公司内部审核、外部认证等需求增加。
2. 鉴定成本分析(1)检验成本:XX年度检验成本为XX万元,同比增长XX%,主要原因是产品种类增加,检验项目增多。
(2)测试成本:XX年度测试成本为XX万元,同比增长XX%,主要原因是新产品研发投入增加。
3. 内部故障成本分析(1)返工成本:XX年度返工成本为XX万元,同比增长XX%,主要原因是生产过程中存在质量问题。
(2)报废成本:XX年度报废成本为XX万元,同比增长XX%,主要原因是产品良品率较低。
4. 外部故障成本分析(1)退货成本:XX年度退货成本为XX万元,同比增长XX%,主要原因是产品存在质量问题。
(2)赔偿成本:XX年度赔偿成本为XX万元,同比增长XX%,主要原因是产品质量问题导致客户损失。
五、问题及改进措施1. 预防成本方面(1)加强培训管理,提高员工素质,降低培训成本。
体系质量成本统计与分析报告样本

4、原材料在投料前,质检员未对其进行检查;
5、原材料在投料前,质检员未对其进行检查;
纠
正
措
施
1、应对核心设备加以严格控制,设备操作者应通过培训上岗,并建立授权机制,非授权人员不得进行设备操作;
2、尽快制定质量意识培训筹划,召集所有生产一线员工进行全面质量意识培训,并进行关于考核,对培训效果进行评估;
0
3损失费
0
共计
不良质量成本项目记录分析图:
总结:
由图示,本月不良质量成本损失重要来源铝锭在工费和料费生产过程中产生报废,并由此导致返工、质量事故解决等损失,以上不良质量成本共计元,占本月销售额%。
2、因素分析:
因
果
图
分
析
材料污染
结
论
1、影响产品污染重要原由于:
2、未对核心设备加以严格控制,操作者未经培训或未经授权导致设备操作失误;
有限公司
200 /月度质量成本记录与分析报告
Q/YF.CW.M05-01-B04
一、成本记录
本月销售收入:万元不良质量成本额:元所占比例本年合计
金额
占%
金额
占%
内部成本
1、报废损失
2、返工损失
3、因质量问题导致停工损失
4、质量事故解决费
共计
外部成本
1质量惩罚
2质量事故解决费
3、完善质量管理制度,增长原材料投料前检查工序,防患于未然;
4、完善质量管理制度,增长原材料投料前检查工序,防患于未然;
编制
审核
批准
某企业质量成本报告

某企业质量成本报告质量成本是由于产品未能达到质量标准而发生的成本(包括机会成本),或者由于可能或存在的质量问题发生的成本。
从产品的生命周期可以将质量成本分为:预防成本、评价成本、内部失败成本、外部失败成本。
本案例是根据这一概念对某电气配件工厂质量成本分析后做出的质量报告,其中原始数据略有改动。
1.背景概述该工厂是厦门某合资低压电气公司配套供货商,XX年前后随着供货量增加,销售额增加,利润却无明显增加,而产品退货量大幅上升,并因质量问题给需方造成过重大损失,受到严重警告。
厂方意识到是质量管理出现问题,狠抓产品检验,增加售后服务人员,结果虽然退货明显减少,废品率却居高不下。
考虑到供需双方合作基础很好,企业求助需方帮助解决难题。
经过调研,需方为该厂制定了一套质量管理方案。
从XX年按该方案实施后,效果不错。
下面将XX、XX 和XX年实行质量管理方案前后的质量成本情况分析如下。
2.质量成本原始数据根据该厂生产特点,其质量成本包括:检测设备折旧、生产工艺、测试用料、产品检测、产品退货、统计过程控制、成品检验、返工成本、废品处理、废料成本、质量退换、成品维护和系统开发。
质量成本原始数据如下表:质量成本原始数据表项目金额(元)XXXXXX生产工艺53,00079,00086,000统计控制72,00076,000废料成本88,000127,00098,000成品维护442,000138,000 69,000检测设备折旧19,00031,00029,000返工成本148,000 218,000 178,000废品处理52,00074,00059,000系统开发66,000 112,000 121,000测试用料3,8005,8006,000产品检测68,000118,000129,000质量退换62,000176,0005,200成品检验86,000148,000168,000产品退货334,00079,00038,000合计1,421,8001,377,8001,062,2003.质量成本报告根据质量成本的概念将原始数据分类形成质量报告如质量成本报告项目金额(元)百分比(%) 金额(元)百分比(%) 金额(元)百分比(%) XXXXXX预防成本: 系统开发66,000 112,000 121,000生产工艺53,00079,00086,000统计控制72,00076,000小计119,000 263,000 283,000评价成本: 检测设备折旧19,00031,00029,000成品检验86,000 148,000 168,000产品检测68,000 118,000 129,000测试用料3,8005,8006,000小计176,800302,800332,000内部失败成本: 废品处理52,00074,00059,000废料成本88,000127,00098,000返工成本148,000218,000178,000小计288,000419,000335,000外部失败成本: 产品退货334,00079,00038,000产品维护442,000138,00069,000质量退换62,000176,0005,200小计838,000393,000112,200质量总成本1,421,8001,377,8001,062,200假定销售额: 10,000,000(元)4.成本分析上表说明,实行质量管理方案之前的XX年,质量总成本达到年度销售额的 %,通过质量管理到XX年已下降到 %。
质量成本统计分析报告
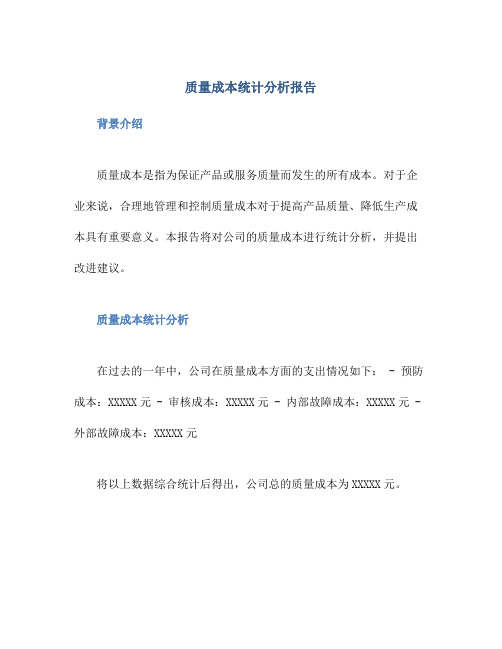
质量成本统计分析报告
背景介绍
质量成本是指为保证产品或服务质量而发生的所有成本。
对于企业来说,合理地管理和控制质量成本对于提高产品质量、降低生产成本具有重要意义。
本报告将对公司的质量成本进行统计分析,并提出改进建议。
质量成本统计分析
在过去的一年中,公司在质量成本方面的支出情况如下: - 预防成本:XXXXX元 - 审核成本:XXXXX元 - 内部故障成本:XXXXX元 - 外部故障成本:XXXXX元
将以上数据综合统计后得出,公司总的质量成本为XXXXX元。
质量成本分析
根据上述统计数据,可以得出以下分析结论: - 预防成本和审核
成本较高,说明公司在产品设计和生产过程中比较注重预防和审核工作,这有助于提前发现和避免质量问题。
- 内部故障成本和外部故障
成本不容忽视,说明公司在产品质量控制方面仍存在一定的问题,需
要加强质量管理措施。
改进建议
为了降低质量成本,提高产品质量,公司可以考虑以下改进建议:1. 强化质量意识,全员参与质量管理,提高产品质量意识。
2. 加强
过程控制,从源头上杜绝质量问题的发生。
3. 建立健全的质量管理
体系,确保质量控制各环节的有效执行。
结论
通过对质量成本的统计分析,公司可以清晰地了解各项成本支出
的情况,从而有针对性地进行质量管理和成本控制。
希望公司能够根
据本报告提出的改进建议,不断提升产品质量,降低质量成本,提高企业竞争力。
以上就是本次质量成本统计分析报告,希期能对公司的质量管理工作有所帮助。
以上报告仅为示例,具体数据和结论请根据实际情况进行调整。
中钞光华的质量成本实例分析
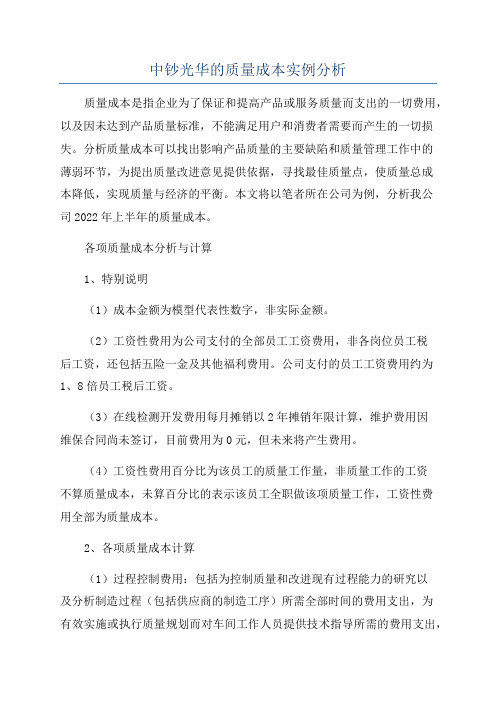
中钞光华的质量成本实例分析质量成本是指企业为了保证和提高产品或服务质量而支出的一切费用,以及因未达到产品质量标准,不能满足用户和消费者需要而产生的一切损失。
分析质量成本可以找出影响产品质量的主要缺陷和质量管理工作中的薄弱环节,为提出质量改进意见提供依据,寻找最佳质量点,使质量总成本降低,实现质量与经济的平衡。
本文将以笔者所在公司为例,分析我公司2022年上半年的质量成本。
各项质量成本分析与计算1、特别说明(1)成本金额为模型代表性数字,非实际金额。
(2)工资性费用为公司支付的全部员工工资费用,非各岗位员工税后工资,还包括五险一金及其他福利费用。
公司支付的员工工资费用约为1、8倍员工税后工资。
(3)在线检测开发费用每月摊销以2年摊销年限计算,维护费用因维保合同尚未签订,目前费用为0元,但未来将产生费用。
(4)工资性费用百分比为该员工的质量工作量,非质量工作的工资不算质量成本,未算百分比的表示该员工全职做该项质量工作,工资性费用全部为质量成本。
2、各项质量成本计算(1)过程控制费用:包括为控制质量和改进现有过程能力的研究以及分析制造过程(包括供应商的制造工序)所需全部时间的费用支出,为有效实施或执行质量规划而对车间工作人员提供技术指导所需的费用支出,在生产过程中自始至终进行质量控制所支出的费用,如表1所示(由于有些费用公司目前未支出,因此表中也未列出,以下各项费用也是如此)。
(2)质量体系管理及审核费用:包括质量体系设计和管理费用,质量体系内审、外审费用等,如表2所示。
(3)原材料检验费用:包括由专业部门所进行的为评价外购材料质量所支出的费用,有关管理人员及办公室人员可能用到的费用,以及检验人员到供货厂评价所购材料时支出的差旅费用,如表3所示。
(4)计量服务及检验费用:包括计量仪器及相关仪器购买、校准及维修费用,工序检测费用,如表4所示。
(5)核对工作费用:包括操作人员按照质量计划要求而检验自己的工作质量、在制造过程中按照要求检查产品和工序是否合格、挑出不符合质量要求而送回全部次废品、加工过程中产品质量评价所需时间的费用,如表5所示。
质量与成本案例分析(doc 9页)
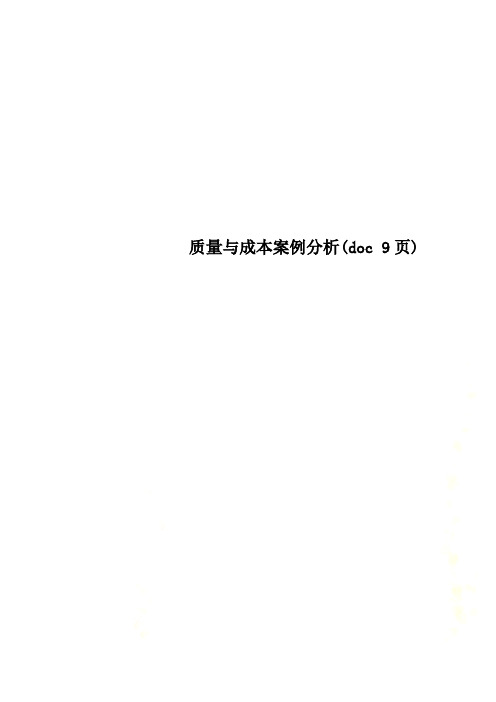
质量与成本案例分析(doc 9页)案例:质量与成本一、案例场景某行业省公司(A单位)信息应用系统工程项目(A项目)通过招标方式选择承建单位,希赛信息技术有限公司(CSAI)以1800万元的标底获得A项目工程合同。
A项目包含1000万元设备采购安装和800万元软件开发费用。
其中设备采购安装预计有150万元利润,CSAI渴望通过A项目的建设能够获得600万元纯利润。
为了能够最大限度地获取利润空间,CSAI在组建项目小组,制定工程费用预算的时候,尽力压缩工程费用预算。
CSAI安排刘工担任A项目的项目经理,刘工在对项目进行工作分解的基础上,制订了工程实施资源计划,编制了项目实施预算经费。
根据刘工的预算,项目实施经费预算(人员工资、差旅费、会议费、行政管理费等)为220万元,其中人员工资占了很大比例,为150万元,CSAI领导在审核经费预算的时候,认为人员工资所占份额太大,CSAI要求刘工将人员工资预算减少为120万元,并列入对刘工的绩效考核指标。
由于人员工资预算的减少,刘工面临两种选择,要么将招聘软件工程师的能力等级降低,要么减少项目组成员数量。
刘工在权衡利弊后认为,项目组员工工资高,容易引起公司其他部门的忌妒,工作不好开展,于是,刘工只能采取降低项目组成员工资的方法。
为此刘工所组建的项目小组有8人没有达到刘工预期的技术资质等级。
A项目经过18个月(延期3个月)的建设周期,项目建设完成并交付用户使用。
CSAI也如愿以偿地获得了预期的利润,项目实施经费190万元,预提项目维护经费60万元(两年免费维护),商务费用50万元,超期3月赔偿A 单位15万元,CSAI认为实现的利润635万元,已经达到了计划的目标。
项目验收交付使用后,CSAI为项目维护配备2位工程师,每位工程师工资加管理成本共计10万元/人年,其他辅助设备购置10万元/年。
但是,A项目的运行维护并不像CSAI想像的那样好,由于A项目定制软件的质量存在很多隐患、缺陷,如软件代码质量差,导致系统运行效率低;技术文件缺乏或文件与实际情况不相符,或技术文件纵向及横向对相应内容的描述不一致;这些问题使得A项目的维护工作难以高质量地开展,经常给A单位的业务开展带来不良的影响。
质量不良成本分析报告

质量不良成本分析报告尊敬的领导:根据质量管理部门的要求,经过对本公司生产过程中的质量不良问题进行调研和数据分析,我编写了一份质量不良成本分析报告,内容如下:一、背景介绍本公司一直以来都非常重视质量管理,但近期发现了一些质量不良问题,且由于质量不良导致的后果严重影响了公司的形象和利润,因此有必要对质量不良成本进行分析。
二、质量不良成本分析1.原材料损失成本质量不良导致的原材料损失涉及到产品的报废、退货等问题,这些成本包括:购买的原材料费用、仓库存储费用、处理不良产品的费用等。
2.生产线停机成本当质量不良的产品被发现时,需要暂停生产线进行返工或修复,这样就会导致停机时间增加,进而影响公司的生产进度和交期。
停机时间所带来的成本包括:员工工资、设备折旧费用等。
3.质量检验成本为了防止质量不良问题发生,公司出资对产品进行检验,以确保产品质量符合标准。
这些检验所产生的成本包括:检测设备、检验人员薪资等。
4.售后服务成本质量不良会导致大量售后服务工作的产生,包括产品返修、更换、退货等。
这些成本包括:售后人员的薪资、维修费用以及对客户的赔偿等。
5.品牌形象成本质量不良会严重影响公司的品牌形象,进而影响销售额和市场份额。
这些成本包括:市场散布负面新闻的成本、品牌形象重塑的成本等。
三、质量不良成本案例分析根据数据统计,近期质量不良问题最为突出的是产品A,其不良品率为10%。
基于这一数据,我通过以下计算,对质量不良问题的成本进行了分析:(1)原材料损失成本:产品A年产量为1000件,不良品率为10%,则每年会有100件产品报废。
假设每件产品的成本为1000元,那么每年的原材料损失成本为100*1000= 100000元。
(2)生产线停机成本:停机时间为10天,每天需要支付员工工资1000元,设备折旧费用100元。
那么停机的总成本为(10*1000)+(10*100)= 11000元。
(3)质量检验成本:每件产品检验费用为10元,年产量1000件,则总的检验成本为1000*10 = 10000元。
企业质量成本管理案例分析
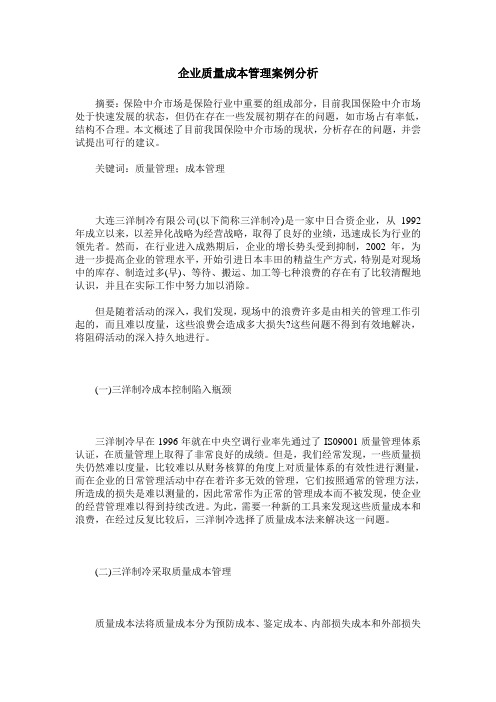
企业质量成本管理案例分析摘要:保险中介市场是保险行业中重要的组成部分,目前我国保险中介市场处于快速发展的状态,但仍在存在一些发展初期存在的问题,如市场占有率低,结构不合理。
本文概述了目前我国保险中介市场的现状,分析存在的问题,并尝试提出可行的建议。
关键词:质量管理;成本管理大连三洋制冷有限公司(以下简称三洋制冷)是一家中日合资企业,从1992年成立以来,以差异化战略为经营战略,取得了良好的业绩,迅速成长为行业的领先者。
然而,在行业进入成熟期后,企业的增长势头受到抑制,2002年,为进一步提高企业的管理水平,开始引进日本丰田的精益生产方式,特别是对现场中的库存、制造过多(早)、等待、搬运、加工等七种浪费的存在有了比较清醒地认识,并且在实际工作中努力加以消除。
但是随着活动的深入,我们发现,现场中的浪费许多是由相关的管理工作引起的,而且难以度量,这些浪费会造成多大损失?这些问题不得到有效地解决,将阻碍活动的深入持久地进行。
(一)三洋制冷成本控制陷入瓶颈三洋制冷早在1996年就在中央空调行业率先通过了IS09001质量管理体系认证,在质量管理上取得了非常良好的成绩。
但是,我们经常发现,一些质量损失仍然难以度量,比较难以从财务核算的角度上对质量体系的有效性进行测量,而在企业的日常管理活动中存在着许多无效的管理,它们按照通常的管理方法,所造成的损失是难以测量的,因此常常作为正常的管理成本而不被发现,使企业的经营管理难以得到持续改进。
为此,需要一种新的工具来发现这些质量成本和浪费,在经过反复比较后,三洋制冷选择了质量成本法来解决这一问题。
(二)三洋制冷采取质量成本管理质量成本法将质量成本分为预防成本、鉴定成本、内部损失成本和外部损失成本,这是一种最常用的质量成本管理法。
预防成本是指为了防止劣质产品或服务而开展的所有活动的成本。
例如进行新产品评审、质量教育和培训、质量改进班组会议、质量策划、供方能力调查和质量部门员工的工资等,可以由成本发生部门把成本汇总后提交给公司的财务部门,由财务部按照质量成本的管理要求重新进行科目分配。
质量成本分析报告范文

质量成本分析报告1. 引言在现代企业管理中,质量管理是一项至关重要的任务。
质量不仅直接关系到产品和服务的满意度,还对企业的声誉和竞争力产生深远影响。
因此,进行质量成本分析是必不可少的。
本报告旨在分析质量成本的不同方面,以帮助企业更好地理解质量成本的构成和影响,并提供相应的建议。
2. 质量成本的定义质量成本是指为了确保产品和服务的质量而发生的费用。
它包括三个主要方面:预防成本、评估成本和故障成本。
2.1 预防成本预防成本是为了防止质量问题在生产过程中出现而进行的投入。
这些成本主要包括培训员工、制定和执行质量标准、改进生产工艺等费用。
预防成本的目的是在生产过程中预防缺陷的发生,从而降低后期的修复成本。
2.2 评估成本评估成本是为了评估产品和服务的质量而产生的费用。
这些成本包括实验室测试、质量检查、质量控制设备和人力资源等费用。
评估成本的目的是确保产品和服务符合质量标准,以满足顾客的需求和期望。
2.3 故障成本故障成本是由于质量问题而产生的费用。
这些成本包括退货、维修、保修、客户投诉处理等费用。
故障成本是由于质量问题而导致的损失,不仅需要承担实际的修复费用,还可能伤害企业的声誉和顾客满意度。
3. 质量成本分析方法为了更好地理解质量成本的构成和影响,可以采用以下方法进行质量成本分析:3.1 质量成本测算质量成本测算是通过收集和分析相关数据来计算质量成本的方法。
可以通过以下步骤进行质量成本测算:1.收集质量成本相关数据,包括预防成本、评估成本和故障成本。
2.对数据进行分类和整理,以便于后续的分析和计算。
3.计算每个类别的质量成本,并将其总和作为总体质量成本。
3.2 质量成本影响因素分析质量成本的大小和构成受多种因素的影响。
对于一个企业来说,以下因素可能对质量成本产生影响:1.生产工艺:如果生产工艺不稳定或存在缺陷,将导致更多的故障成本。
2.供应链管理:供应链中的质量问题可能会导致更多的退货和维修成本。
3.员工培训:缺乏足够的培训可能导致质量问题增加,从而增加故障成本。
质量成本分析报告范文
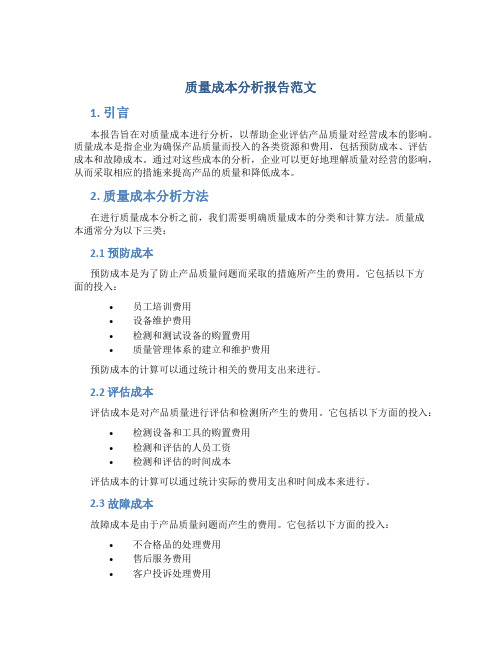
质量成本分析报告范文1. 引言本报告旨在对质量成本进行分析,以帮助企业评估产品质量对经营成本的影响。
质量成本是指企业为确保产品质量而投入的各类资源和费用,包括预防成本、评估成本和故障成本。
通过对这些成本的分析,企业可以更好地理解质量对经营的影响,从而采取相应的措施来提高产品的质量和降低成本。
2. 质量成本分析方法在进行质量成本分析之前,我们需要明确质量成本的分类和计算方法。
质量成本通常分为以下三类:2.1 预防成本预防成本是为了防止产品质量问题而采取的措施所产生的费用。
它包括以下方面的投入:•员工培训费用•设备维护费用•检测和测试设备的购置费用•质量管理体系的建立和维护费用预防成本的计算可以通过统计相关的费用支出来进行。
2.2 评估成本评估成本是对产品质量进行评估和检测所产生的费用。
它包括以下方面的投入:•检测设备和工具的购置费用•检测和评估的人员工资•检测和评估的时间成本评估成本的计算可以通过统计实际的费用支出和时间成本来进行。
2.3 故障成本故障成本是由于产品质量问题而产生的费用。
它包括以下方面的投入:•不合格品的处理费用•售后服务费用•客户投诉处理费用•产品修复和召回费用故障成本的计算可以通过统计实际的费用支出来进行。
3. 质量成本分析实例假设某企业生产的产品出现质量问题,需要进行质量成本分析以评估其对经营的影响。
下面是对该企业的质量成本进行分析的示例:3.1 预防成本该企业在过去一年中,为了预防质量问题,投入了以下费用:•员工培训费用:100,000元•设备维护费用:50,000元•检测和测试设备的购置费用:80,000元•质量管理体系的建立和维护费用:120,000元总预防成本为350,000元。
3.2 评估成本该企业在过去一年中,对产品质量进行评估和检测的费用为:•检测设备和工具的购置费用:60,000元•检测和评估的人员工资:200,000元•检测和评估的时间成本:100,000元总评估成本为360,000元。
质量成本控制案例
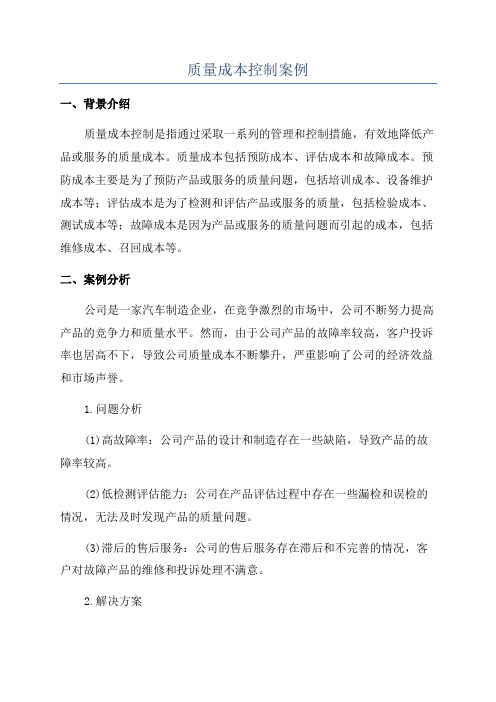
质量成本控制案例一、背景介绍质量成本控制是指通过采取一系列的管理和控制措施,有效地降低产品或服务的质量成本。
质量成本包括预防成本、评估成本和故障成本。
预防成本主要是为了预防产品或服务的质量问题,包括培训成本、设备维护成本等;评估成本是为了检测和评估产品或服务的质量,包括检验成本、测试成本等;故障成本是因为产品或服务的质量问题而引起的成本,包括维修成本、召回成本等。
二、案例分析公司是一家汽车制造企业,在竞争激烈的市场中,公司不断努力提高产品的竞争力和质量水平。
然而,由于公司产品的故障率较高,客户投诉率也居高不下,导致公司质量成本不断攀升,严重影响了公司的经济效益和市场声誉。
1.问题分析(1)高故障率:公司产品的设计和制造存在一些缺陷,导致产品的故障率较高。
(2)低检测评估能力:公司在产品评估过程中存在一些漏检和误检的情况,无法及时发现产品的质量问题。
(3)滞后的售后服务:公司的售后服务存在滞后和不完善的情况,客户对故障产品的维修和投诉处理不满意。
2.解决方案(1)改进设计和制造流程:公司需要加强对产品设计和制造流程的管理,引入先进的质量管理方法和技术,确保产品的质量。
(2)提高评估能力:公司应加强对产品的检测和评估,引入先进的测试设备和方法,提高产品的质量评估能力。
(3)完善售后服务:公司需要加强对售后服务的管理和培训,提高售后服务人员的专业素质和服务水平,改善客户的满意度。
3.实施效果(1)故障率降低:通过改进设计和制造流程,产品的故障率明显下降,提高了产品的可靠性和质量。
(2)检测评估能力提升:公司引入了先进的测试设备和方法,提高了产品的检测和评估能力,及时发现和解决产品的质量问题。
(3)客户满意度提高:公司加强了对售后服务的培训和管理,提高了售后服务人员的专业素质和服务水平,客户的满意度明显提高。
三、结论通过质量成本控制措施的实施,汽车制造企业成功降低了产品的质量成本,并改善了产品的质量和客户满意度。
质量成本分析案例(DOC 10页)复习过程

质量成本分析案例(D O C10页)专题报告公司某事业部质量损失分析报告一、文章概要目前公司某产品品质非常脆弱,品质问题已成为制约该事业部可持续发展的关键瓶颈之一。
本文希望从如下方面揭示问题:1、质量损失不仅包括显性损失,而且包含更大的隐性损失。
按照隐性损失ABC核算法保守估测,该产品03年隐性质量损失是显性损失的2倍左右,达亿元;加上显性损失亿,质量损失高达亿元;2、控制质量损失具有重要的战略与经营意义,如果按照实现353规划既定质量目标保守推算,事业部因提升品质平均每年可获得收益万元;3、品质问题的解决宜从电控着手,以建立大品质体系与成本品质均衡的决策机制为手段,逐步摆脱品质“监控残缺”的尴尬局面,进入“全局掌控-重点突破-系统创新-全面收益”的良性循环阶段。
二、质量损失的内涵1、质量损失的构成所谓质量损失,是指企业为确保或提高产品质量而发生的费用支出,以及由于未能达到质量标准而造成的价值损失。
它不仅包括为提高质量而实际支出的费用,而且还包括因品质缺陷导致的价值流失。
根据可识别性质量损失分为显性质量损失和隐性质量损失,按照产生流程分为预防成本、鉴定成本、损失成本(外部损失、内部损失)三部分(图1)。
图1:质量损失构成2、隐性质量损失的内涵由产品品质不良导致的价值链机会成本损失是隐性质量成本的本源,包括:顾客流失——老顾客流失和新顾客流失:老顾客流失——顾客因维修体验而在二次选购时放弃选择原品牌,导致企业损失原可获得的收益。
据麦肯锡对中国该产品市场的研究,未来几年老顾客比例呈迅速增长趋势,将由02年的%上升至08年的%。
新顾客流失——经口碑传播而建立某品牌不良品质形象的潜在选购者,当其中部分人作现实购买时放弃选择该品牌,导致该企业损失原可获得的收益。
科特勒曾指出,家电消费品是顾客购买决策受参照群体1影响最大的产品之一,一个有过维修体验的顾客会将痛苦体验传播给4—8个人。
1有过同类产品使用体验的同事、亲人、朋友。
质量成本分析报告(模板)

质量成本分析报告
从质量成本构成比例情况分析,预防成本比较高,主要是公司进行国军标认证费用和培训费用等共投入5万,公司领导重视预防成本的投入,这为公司质量体系的建立和产品质量控制打下了良好的基础,从总体质量成本的投入及废品损失情况看,质量成本构成比例较好,满足质量成本的运作要求。
二、质量成本占生产成本的比例
2017年1月至2017年9月公司的生产成本为40万,质量成本为13万元,质量成本占生产成本的32.5%,其中鉴定成本占19%,预防成本占38.5%,目前看质量成本是以预防成本和鉴定成本为主体,但内部故障成本也较高,主要是返工返修的零件较多,在生产过程中没有发生较大的质量问题,为用户提供的产品没有出现因质量问题造成批次性返修、退货现象,也没有出现过顾客投诉现象。
三、总结
根据质量成本统计、分析情况,公司应加强工序过程的控制,适当增加工序控制的费用,做好数控程序编制和确认审批工作,以提高生产过程的能力,减少废品及返工、返修现象,提高成品的合格率,为用户提供满足要求的产品,把不良品控制在生产过程中,减少浪费,提高公司的经济效益。
办公室
年月日
质量成本统计表
年月日
制表:审核:批准:。
月度质量成本分析报告

月度质量成本分析报告目录月度质量成本分析报告 (1)引言 (1)背景介绍 (1)目的和意义 (2)质量成本概述 (3)定义和分类 (3)质量成本的重要性 (4)质量成本的计算方法 (5)质量成本分析方法 (7)内部质量成本分析 (7)外部质量成本分析 (8)月度质量成本分析报告编制 (9)数据收集和整理 (9)质量成本指标计算 (10)报告撰写和呈现 (12)案例分析 (13)公司A的月度质量成本分析报告 (13)公司B的月度质量成本分析报告 (14)总结与展望 (15)主要发现和结论 (15)对质量成本管理的建议 (16)未来研究方向 (17)引言背景介绍随着全球经济的快速发展和市场竞争的日益激烈,企业对产品和服务的质量要求越来越高。
质量成本分析作为一种重要的管理工具,可以帮助企业评估和控制质量成本,提高产品和服务的质量水平,增强企业的竞争力。
质量成本是指为了确保产品和服务的质量而发生的各种成本,包括预防成本、评估成本、内部故障成本和外部故障成本。
预防成本是为了防止质量问题的发生而进行的各种活动和投入,如培训员工、制定和实施质量管理体系等。
评估成本是为了评估产品和服务的质量而进行的各种活动和投入,如检验、测试、审核等。
内部故障成本是由于质量问题而在企业内部产生的各种成本,如返工、报废、停产等。
外部故障成本是由于质量问题而在企业外部产生的各种成本,如退货、赔偿、维修等。
质量成本分析的目的是通过对各种质量成本的分析和评估,找出质量问题的根本原因,采取相应的措施进行改进,从而降低质量成本,提高产品和服务的质量水平。
质量成本分析可以帮助企业识别和解决质量问题,改进生产和服务过程,提高客户满意度,降低质量风险,增加企业的利润。
本月度质量成本分析报告旨在对我公司的质量成本进行详细分析和评估,为企业决策提供科学依据。
通过对质量成本的分析,我们可以了解到质量成本在企业总成本中的比重,找出质量成本的主要来源和影响因素,识别质量问题的根本原因,制定相应的改进措施,提高产品和服务的质量水平。
六西格玛改善质量成本的应用案例分析

六西格玛改善质量成本的应用案例分析一、案例背景S公司是中加合资企业.是通用汽车公司全球供应商,主要为上海通用、韩国通用大宇、北美通用供应自动变速箱中的传动阀,是汽车行业一级供应商。
在质量成本控制方面,S公司采用了六西格玛符合及非符合质量成本模型对质量成本进行监控。
设立预防成本、鉴定成本、内部失效成本及外部失效成本四大一级科目。
根据公司及所在汽车行业的具体情况,分别设立如下二级子科目。
X年3月,因韩国通用大宇投诉的碰伤质量问题导致当月质量成本率超过10%,出现了明显异常,大大超出了6%的目标,也导致了当年截至3月质量成本平均率超标。
二、改善过程从质量成本评估分析开始,细化、完善了数据统计系统。
设立了外部分拣损失等三级细分科目。
针对性的明细数据为指出质量成本超标的成因,提供了强大的数据支持。
从案例定义及测量阶段开始,从后续的分析及改进阶段提供了指导方向。
针对碰伤缺陷特性,结合汽车行业QSB中的适宜的分析工具,递进式地采用了4D过程要素检查法、鱼骨图多因素分析法、以及潜在失效模式的风险管理法识别出了引起碰伤的根本原因及其潜在风险。
按照QSB中对改进措施的要求,从预防、预测、保护方面,有层次地采取了系统性改进措施,以从根本上消除缺陷所引起的潜在风险。
在重中之重的控制阶段,首先,利用潜在失效模式中的改进措施工具验证及重新评估了改进措施完成后的相关风险系数,为验证措施效果提供了风险管理保障;其次,将经验证的控制措施更新入了标准化作业规程,将措施进行了常态化、制度化;最后,利用QSB中的分层审核,把对控制措施的检查纳入了公司管理层对现场的日常检查机制。
即巩固了改进效果的控制,也增强了管理层对改进方法和效果的理解,可谓实现了控制和质量意识宣传的双赢结果。
三、效果评价通过六西格玛方法的改善,不仅根本性地解决了质量问题。
也从质量成本方面显示了质量经济性的提高。
短期收益来看,解决了碰伤之具体的质量问题,降低了外部失效成本,从改善前的质量成本率10.73%,到改善后的2.69%,重新达到了质量成本目标。
- 1、下载文档前请自行甄别文档内容的完整性,平台不提供额外的编辑、内容补充、找答案等附加服务。
- 2、"仅部分预览"的文档,不可在线预览部分如存在完整性等问题,可反馈申请退款(可完整预览的文档不适用该条件!)。
- 3、如文档侵犯您的权益,请联系客服反馈,我们会尽快为您处理(人工客服工作时间:9:00-18:30)。
专题报告公司某事业部质量损失分析报告一、文章概要目前公司某产品品质非常脆弱,品质问题已成为制约该事业部可持续发展的关键瓶颈之一。
本文希望从如下方面揭示问题:1、质量损失不仅包括显性损失,而且包含更大的隐性损失。
按照隐性损失ABC核算法保守估测,该产品03年隐性质量损失是显性损失的2倍左右,达亿元;加上显性损失亿,质量损失高达亿元;2、控制质量损失具有重要的战略与经营意义,如果按照实现353规划既定质量目标保守推算,事业部因提升品质平均每年可获得收益万元;3、品质问题的解决宜从电控着手,以建立大品质体系与成本品质均衡的决策机制为手段,逐步摆脱品质“监控残缺”的尴尬局面,进入“全局掌控-重点突破-系统创新-全面收益”的良性循环阶段。
二、质量损失的内涵1、质量损失的构成所谓质量损失,是指企业为确保或提高产品质量而发生的费用支出,以及由于未能达到质量标准而造成的价值损失。
它不仅包括为提高质量而实际支出的费用,而且还包括因品质缺陷导致的价值流失。
根据可识别性质量损失分为显性质量损失和隐性质量损失,按照产生流程分为预防成本、鉴定成本、损失成本(外部损失、内部损失)三部分(图1)。
图1:质量损失构成2、隐性质量损失的内涵由产品品质不良导致的价值链机会成本损失是隐性质量成本的本源,包括:顾客流失——老顾客流失和新顾客流失:老顾客流失——顾客因维修体验而在二次选购时放弃选择原品牌,导致企业损失原可获得的收益。
据麦肯锡对中国该产品市场的研究,未来几年老顾客比例呈迅速增长趋势,将由02年的%上升至08年的%。
新顾客流失——经口碑传播而建立某品牌不良品质形象的潜在选购者,当其中部分人作现实购买时放弃选择该品牌,导致该企业损失原可获得的收益。
科特勒曾指出,家电消费品是顾客购买决策受参照群体1影响最大的产品之一,一个有过维修体验的顾客会将痛苦体验传播给4—8个人。
价格损失——中低价位的该产品,与主要竞争对手相比,产品品质差异因素带来的售价差异平均超过10%2。
生产率流失——将投入到不良品返修的劳动力和设备资源转化为生产合格品可获得的收益。
事实上,同等条件下返修生产往往低于正常生产效率,目前下属某工厂按照正常生产工时的2.5倍来核算返修工时。
供方成本转嫁——从系统性、长远性来看,供方的部分质量成本损失必然会通过后期成交价格、供货质量、议价能力变化等方式,以及采购方供应商转换成本,转嫁给购买者。
这部分转嫁的质量成本,主要体现为筛选不合格退货物料价值、物料在线下线导致的生产率流失。
三、该产品质量损失测算1、显性质量损失呈迅速攀升趋势——2002年,事业本部显性质量损失已达到万元3,比上年净增多万元。
平均单台质量成本元,其中质量损失达到元/台,见图2。
1有过同类产品使用体验的同事、亲人、朋友。
2内部访谈一致认为,产品品质是影响价格差异的关键因素之一,其影响力至少超过50%。
谨慎起见,本文取10%。
3据品质统括部2002年度质量分析报告分析,2000年、2001年质量成本数据存在严重低估失真。
外部损失是攀升过快的主要表现——外部损失呈现出较快的攀升速度,02年占到了显性质量损失的70%。
02年显性质量损失构成如图3。
2、隐性质量损失隐性损失是显性质量成本的2倍以上——根据隐性质量成本估算模型与估量公式(详见附件1)计算可知,03销售年度隐性质量损失合计达亿元,是显性质量成本的2倍以上,其中顾客流失所占比例最大。
按质量成本的来源分,隐性内部损失亿元,隐性外部损失亿元。
(见图4)。
(已删除)相对于品质的“冰山理论”(显性:隐性=1:9)而言,我们对该产品质量隐性损失的以上估算是非常保守的!综合以上分析,我们不难得到如下结论:① 03销售年度该事业部内销总体质量损失4高达 亿元(其中:显性损失为 亿元,隐性损失 亿元),占当年内销销售收入的 %以上。
由此可见,该产品品质收益弹性较大,即通过提高品质降低总体质量损失而增加经营效益的潜4因未作销售年度显性质量成本统计,实际测算03销售年度总质量成本时使用了02财年的数据。
因财年统计区间早于销售年度统计区间半年,实际数据前者会小于后者,故本文测算是谨慎和可信的。
——1个顾客的不满会传给2人,2人传给4人,4人传给16人,…。
——显性特征与隐性特征具有1:9的关系。
隐藏在海面以下的隐性损失(潜——发生1件报废品(1个顾客投诉),意味着29件同样品质问题存在(29冰山理论 海因里奇法则 2级数效应1:9 1:29:300 2n,n=1,2,3,…力巨大。
在竞争环境极度恶劣,该事业部探索规模与利润平衡增长的盈利模式背景下,提高品质以增加事业部总体收益具有更加重要的现实经营意义与长远战略意义;②居高不下的市场维修率与质量损失,不仅使公司在与竞争对手的相持中失去经营效益的比较优势,而且导致对顾客满意度、品牌、信誉等企业无形价值的损伤与蚕食。
在空调行业策略转折点即将来临,无形资源竞争逐渐占据主导地位的形势下,公司的品质脆弱性会严重削弱公司可持续发展能力。
为此,必须下决心改变主打产品的品质现状。
四、提升品质水平(降低质量损失)的经营与战略意义㈠经营意义1、市场维修率与质量损失相关关系回归分析一般说来,市场维修率与质量损失两个要素之间具有如下正相关关系:c=f(r o)=Ar o+B,c——质量损失,r o——年度市场维修率,A、B——相关系数。
对01~03年度美的空调市场维修率、质量损失数据的归纳分析(详见附件2),剔除销售价格变化因素影响(折合到03年),该产品年度市场维修率与加权单台质量损失的相关关系为:c=281r o +71, 具体回归关系图如下:表中圆点表示事业本部01~03年实际经营所处的品质与质量损失发生点。
说明:质量损失因多变、复杂的经营背景不同而有所不同,由于市场竞争结构、客户结构的不断演变,必然引起以全精确。
2、2004-2008年该事业部质量损失预测品质统括部三五三质量规划提出的市场维修率控制目标如表1,到三五三战略阶段的最后一年,市场维修率将下降为 %,总降幅 %。
但与行业品质水准对比,这个指标仍然不及国际大品牌等企业目前品质水平(东芝市场维修率 %),也仅比03年国内竞争对手的品质水平强一点5。
因此树立更为积极、更富有挑战性的质量目标十分必要。
表1:2004—2008年质量规划目标5据内部访谈:主要竞争对手当年市场维修率仅为该事业部 %以下,年度市场维修率与当年市场维修率具有同幅趋同特性,故推测其年度维修率应为该事业部的 %。
图8: 01~03冷年空调市场维修率与质量成本关系50100150200ro=3%ro=9%ro=15%ro=21%市场维修率ro单台质量成本(元)根据以上质量规划目标中的具体数据及回归方程c=281ro+71,可得到2004-2008年该事业部质量损失曲线如下:由上图可见,降低质量损失将为企业带来巨大的节支收益,其增加幅度随着经营规模的扩大而不断扩大。
在三五三战略实施阶段,该产品质量水平如实现品质统括部规划的质量目标,相比参考状态,累计可节约质量损失4.4亿元,平均每年为8800万元;而更积极的质量目标状态将节支达7.8亿元,平均每年1.56亿元。
㈡战略意义1、三大品牌品质战略与实践对比战略95年实施精品战略84年开始树立优质观念01年提出“品质领导一切”执行“总经理12条”“砸冰箱”“作秀”落实不到位口碑(国内)行业最佳质量口碑服务口碑掩盖质量口碑中低档产品的质量口碑对品牌的拉动非常明显,成长迅速逐步弱化,优势渐失主要以价格拉动2、源自质量的竞争优劣势比较××:质量损失低于竞争对手一半——市场维修率的差异反应了质量成本的差异。
××市场维修率目前是公司的,借鉴公司品质与质量损失回归关系曲6这里指当年销售产品当年发生的市场维修比率,预测值来自品质统括部市场稽查的经验判断。
线可以推断,××具有低于主要竞争对手一半左右的质量损失控制能力,已形成其核心竞争优势并赢得了较好的消费者口碑;××:质量损失与公司相当——依靠产品工业设计、售后服务来粉饰品牌形象与口碑以维持产品的高价位。
公司:质量损失较高,售后服务没有特色,处于品质竞争的劣势——任何一个行业前三强的国际性品牌,都不是三流的品质能力所能支撑的。
目前我们的品质能力仅处于业界中下游水平,三五三战略需要将其提升到一个适合的水准,至少必须接近乃至超越××、××等国际二流质量水平,而目前差距还相当明显。
公司必须从自身质量损失形成的源头进行检讨梳理,明确战略方向与具体策略并迅速行动。
五、质量损失产生的根源剖析1、零部件质量问题2002年家用内销维修率前10名的零部件如下图:图4: 02年维修率前十名零部件结构示意图0%2%4%6%8%10%占维修量比例从上图可以看出:①电子件品质控制能力非常薄弱——近几年,电子件(电控部件、电子元器件)零部件始终占维修总量40%~60%,其中室内电控主板、遥控器等一直处在维修率最前列。
2002年内新进入维修前10名的4类零部件中有3类即是电子件。
管温传感器更是一路攀升,到今年9月不仅一举占据维修排行榜榜首,而且创下了单件零件超过总维修量10%的不良记录。
这充分表明了电子件品质控制能力是提升品质水平的关键瓶颈。
建议事业部对电子件采取“品质优先,兼顾成本”的长期制造开发战略;②关键零部件质量控制能力呈现维持甚至弱化迹象——一方面,一些长期性品质问题尚未得到有效扭转。
例如,自2000年以来室内电控主板、室内连接管等六类零部件始终位于维修率前10名之列;另一方面,以往免检的关键零部件维修率也在迅速上升,如压缩机已跃居维修率前10名,返修率高达2.83%。
2、质量管理问题检讨①品质问题未引起各单位的实质性重视——主要表现为“认识上不到位、思想上不关心、行动上不重视”。
部分单位的主要领导人没有从系统与全局的高度上认识到现阶段公司产品品质提升对降低整体成本、提高总体经营效益的事实,片面将品质与成本、市场反应速度对立起来,总是按照“非此即彼”的简单逻辑处理品质与成本的关系。
在竞争环境恶劣的情况下,往往从部门本位与短期利益出发,采取简单的“竭泽而渔”的方式追求成本最小化而牺牲品质;②品质决策与监控体系“残缺不全”,系统的“大品质体系”远未形成——在降成本的惯性压力下,影响品质的关键环节(如技术开发、供应链招标、工艺技术改进等)进行相关决策时,几乎听不到品质的声音,因此,成本品质的均衡决策与监控机制在关键环节缺失,造成品质工作的“缘木求鱼”;③责任缺位——事业部究竟谁对居高不下的品质损失负责?应该考核谁?如何考核?这些问题尚未落到实处;④涉及品质提升的某些关键问题(如电控)迟迟不能突破,影响了整体品质水平提升——电控开发与制造技术停留在凭感觉摸索的“手工作坊”时代,对行业技术规律与同行的对比分析认识不深,提不出创造性的改革突破方案;⑤事业部品质管理部门“长于技术、疏于管理”——对某些危及品质的严重现象(如产品开发设计的“删、减、换、省”)既缺乏约束机制与评价结论,也缺乏有效的管控制止手段。