分享有关铝合金铸造模具的几点技术要求
压铸铝合金技术要求

压铸铝合金技术要求嘿,咱今儿就来聊聊压铸铝合金技术要求这档子事儿!你说这压铸铝合金啊,就像是一位需要精心呵护的宝贝。
首先呢,材料得选对咯!可不是啥铝合金都能拿来压铸的呀。
这就好比做饭,得挑好食材才能做出美味佳肴不是?对铝合金的成分那可得讲究,各种元素的比例得恰到好处。
要是比例不对,那压铸出来的东西可能就不结实,容易出问题。
就好像盖房子,根基不牢,那房子能稳当吗?压铸的过程呢,也得万分小心。
温度得控制好,高了不行,低了也不行。
这温度就像是炒菜时的火候,火候大了糊了,火候小了又不熟。
压力也得适中,不然压出来的东西不是这儿缺一块就是那儿多一块,那可就难看啦!模具也是关键啊!模具就像是一个模子,得做得精细,才能压铸出形状规整、漂亮的铝合金制品。
要是模具有瑕疵,那压铸出来的东西不就跟着有问题啦?这就跟刻印章似的,印章不好,印出来的字能好看吗?还有啊,压铸之后的处理也不能马虎。
表面得打磨光滑,不能有毛刺啥的。
这就跟人出门一样,得收拾得干干净净、利利索索的,不然多难看呀。
咱再说说这压铸铝合金的性能要求。
强度得够吧,不然怎么经得起使用呢?就像人的身体,得强壮才能干重活呀。
韧性也不能差,不然稍微碰一下就断了,那可不行。
而且啊,这压铸铝合金还得耐腐蚀。
你想想,要是容易被腐蚀了,那用不了多久不就坏了吗?这就好比一件好衣服,得耐穿才行,要是洗两次就破了,那多可惜呀。
在实际操作中,可得严格按照这些技术要求来。
不能偷工减料,不能马马虎虎。
每一个环节都得认真对待,就像呵护自己最心爱的东西一样。
总之呢,压铸铝合金技术要求可真是不少,但只要咱都做到位了,就能压铸出高质量的铝合金制品。
这不仅能让咱自己满意,也能让使用这些制品的人放心呀!这可不是开玩笑的事儿,大家可得重视起来哟!不然出了问题,那可就麻烦大啦!。
铝合金压铸技术要求
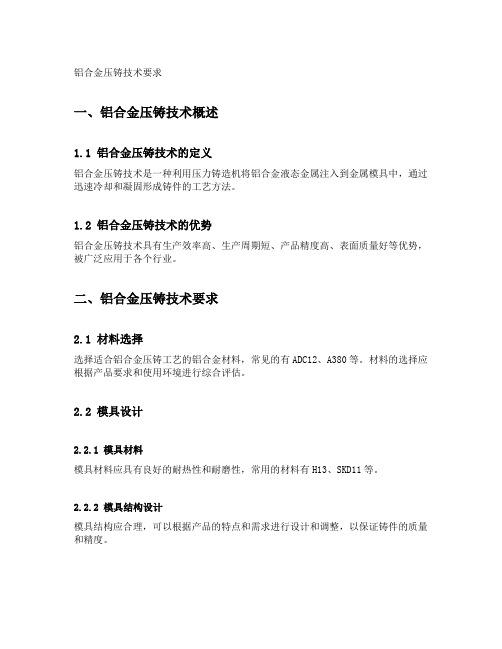
铝合金压铸技术要求一、铝合金压铸技术概述1.1 铝合金压铸技术的定义铝合金压铸技术是一种利用压力铸造机将铝合金液态金属注入到金属模具中,通过迅速冷却和凝固形成铸件的工艺方法。
1.2 铝合金压铸技术的优势铝合金压铸技术具有生产效率高、生产周期短、产品精度高、表面质量好等优势,被广泛应用于各个行业。
二、铝合金压铸技术要求2.1 材料选择选择适合铝合金压铸工艺的铝合金材料,常见的有ADC12、A380等。
材料的选择应根据产品要求和使用环境进行综合评估。
2.2 模具设计2.2.1 模具材料模具材料应具有良好的耐热性和耐磨性,常用的材料有H13、SKD11等。
2.2.2 模具结构设计模具结构应合理,可以根据产品的特点和需求进行设计和调整,以保证铸件的质量和精度。
2.3 注射设备2.3.1 压铸机选择根据产品的要求确定压铸机的型号和规格,包括锁力、注射压力等参数的选择。
2.3.2 注射系统注射系统包括注射缸、注射头、喷嘴等组成,其设计应合理,确保铝合金液态金属的注入和充填。
2.3.3 润滑系统润滑系统的设置对于铝合金压铸技术的稳定运行起着重要作用,应注意润滑剂的选择和使用。
2.4 工艺参数控制压铸工艺参数对于产品的质量和尺寸稳定性有很大的影响,应进行合理的控制和调整。
2.4.1 注射速度注射速度过快会导致铸件内部气孔、缺陷等问题,注射速度过慢会导致铝合金液态金属凝固不完全。
2.4.2 注射温度注射温度过高会导致铝合金液态金属粘度降低,流动性增强,但也会加快模具磨损。
注射温度过低则会导致液态金属凝固时间过长。
2.4.3 注射压力注射压力的控制对于铸件的密实性和表面质量有着重要影响,应根据产品要求进行精确控制。
2.4.4 注射时间注射时间应根据实际需要进行合理设置,以保证铝合金液态金属充填充实模腔。
2.5 热处理工艺铝合金压铸件在铸造成型后,经过热处理工艺可以改善其机械性能和物理性能,如固溶处理、时效处理等。
2.6 铸件表面处理铝合金压铸件的表面处理包括喷砂、喷涂、电镀等方法,以提高产品的外观质量和耐腐蚀性能。
锌合金、铜合金、铝合金压铸件技术条件

中华人民共和国第一机械工业部部标准锌合金、铝合金、铜合金压铸件技术条件JB 2702—80北京1981中华人民共和国第一机械工业部部标准JB 2702—80 锌合金、铝合金、铜合金压铸件技术条件本标准适用于机电、仪表、汽车、拖拉机等机械工业产品的锌合金、铝合金、铜合金压铸件(以下简称铸件)。
对有特殊要求的铸件,经商议后应在图样中注明。
一、铸件分类及级别1.铸件按使用要求分为两类,见表1。
2.铸件表面质量按使用范围分为三级,见表2。
3.铸件的类别和表面质量的级别应在图样中注明,表示方法如下:Ⅱ-∽铸件表面质量级别铸件分类类别铸件标准代号如有更高要求的部位应在图样中有关面处分别注明。
4.未注明铸件类别、级别和尺寸精度者,均按本标准相关的最低级别处理。
二、尺寸精度5.铸件线性尺寸公差才选用中华人民共和国第一机械工业部发布 1 9 8 1 年 1 月 1 日实施一机部沈阳铸造研究所提出上海电器压铸三、上海电表厂等起草共11页第2页 JB 2702—80⑴铸件的基本尺寸公差按表3选用。
铸件受分型面或模具活动部位影响的尺寸应按表4、表5规定,在基本尺寸公差上再加附加公差。
铸件基本尺寸公差表3线性尺寸受分型面影响时的附加公差表4线性尺寸受模具活动部位影响时的附加公差表5注:一模多铸时,铸件分型面上的投影面积为各铸件投影面积之和附加公差应用示例:JB 2702—80 共11页第3页1 铝合金压铸件的尺寸A为3+0.12mm(基本公差按7级精度),模具活动部位由成形滑块构成,其投影面积为34cm2,由表5查得其附加公差为0.20mm,则A的尺寸公差应为0.12+0.20=0.32(mm) 。
2 在同一铸件上尺寸B为2.5+0.12mm(基本公差按7级精度),模具活动部位由滑块型芯构成,型芯直径为20mm,则其投影面积为3.14cm2,由表5查得其附加公差为0.15mm,则B处的尺寸公并为+0.12/-0.15。
⑵尺寸公差带的位置a.不加工的配合尺寸,孔取正(+),轴取负(-)。
铝压铸技术要求
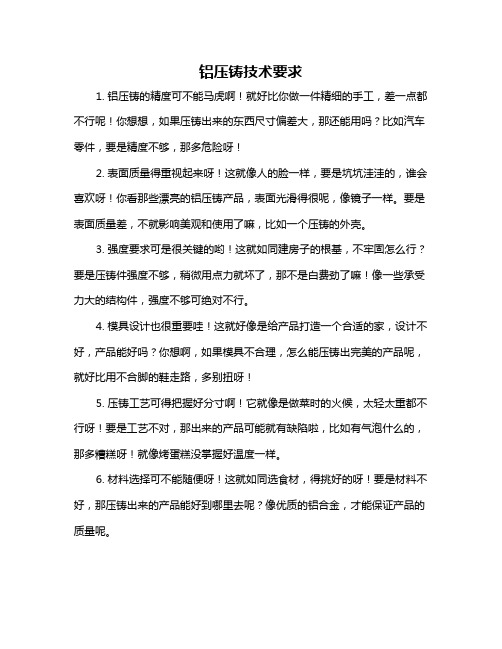
铝压铸技术要求
1. 铝压铸的精度可不能马虎啊!就好比你做一件精细的手工,差一点都不行呢!你想想,如果压铸出来的东西尺寸偏差大,那还能用吗?比如汽车零件,要是精度不够,那多危险呀!
2. 表面质量得重视起来呀!这就像人的脸一样,要是坑坑洼洼的,谁会喜欢呀!你看那些漂亮的铝压铸产品,表面光滑得很呢,像镜子一样。
要是表面质量差,不就影响美观和使用了嘛,比如一个压铸的外壳。
3. 强度要求可是很关键的哟!这就如同建房子的根基,不牢固怎么行?要是压铸件强度不够,稍微用点力就坏了,那不是白费劲了嘛!像一些承受力大的结构件,强度不够可绝对不行。
4. 模具设计也很重要哇!这就好像是给产品打造一个合适的家,设计不好,产品能好吗?你想啊,如果模具不合理,怎么能压铸出完美的产品呢,就好比用不合脚的鞋走路,多别扭呀!
5. 压铸工艺可得把握好分寸啊!它就像是做菜时的火候,太轻太重都不行呀!要是工艺不对,那出来的产品可能就有缺陷啦,比如有气泡什么的,那多糟糕呀!就像烤蛋糕没掌握好温度一样。
6. 材料选择可不能随便呀!这就如同选食材,得挑好的呀!要是材料不好,那压铸出来的产品能好到哪里去呢?像优质的铝合金,才能保证产品的质量呢。
7. 生产效率也很重要呢,你说是不是?这就好像比赛跑步,谁快谁就有优势呀!如果生产效率低,怎么跟别人竞争呀,尤其在量大的时候,不快怎么行呢!就好像打仗,速度可不能慢。
8. 质量检测绝对不能少哇!这就像是给产品做体检,有毛病就得赶紧治呀!不检测怎么知道产品合不合格呢,不管是小瑕疵还是大问题,都得检测出来呀!就像给病人看病一样仔细。
我的观点结论就是:铝压铸技术要求真的很多,每一项都非常重要,都需要我们认真对待,这样才能生产出高质量的铝压铸产品啊!。
铝合金铸造模具工艺设计参数手册
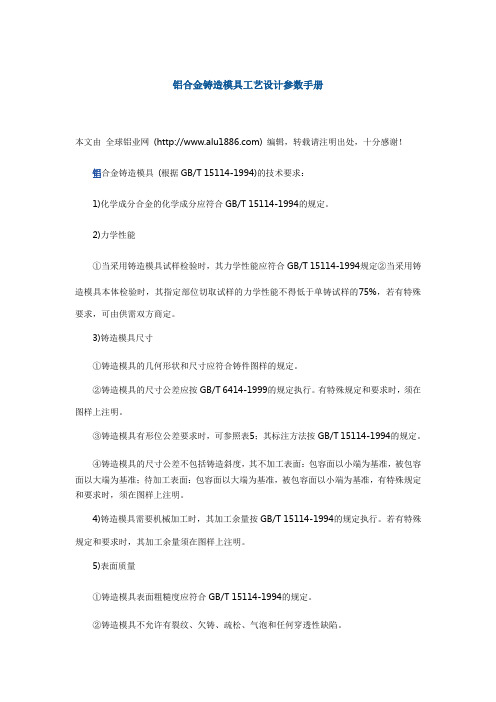
铝合金铸造模具工艺设计参数手册本文由全球铝业网 () 编辑,转载请注明出处,十分感谢!铝合金铸造模具 (根据GB/T 15114-1994)的技术要求:1)化学成分合金的化学成分应符合GB/T 15114-1994的规定。
2)力学性能①当采用铸造模具试样检验时,其力学性能应符合GB/T 15114-1994规定②当采用铸造模具本体检验时,其指定部位切取试样的力学性能不得低于单铸试样的75%,若有特殊要求,可由供需双方商定。
3)铸造模具尺寸①铸造模具的几何形状和尺寸应符合铸件图样的规定。
②铸造模具的尺寸公差应按GB/T 6414-1999的规定执行。
有特殊规定和要求时,须在图样上注明。
③铸造模具有形位公差要求时,可参照表5;其标注方法按GB/T 15114-1994的规定。
④铸造模具的尺寸公差不包括铸造斜度,其不加工表面:包容面以小端为基准,被包容面以大端为基准;待加工表面:包容面以大端为基准,被包容面以小端为基准,有特殊规定和要求时,须在图样上注明。
4)铸造模具需要机械加工时,其加工余量按GB/T 15114-1994的规定执行。
若有特殊规定和要求时,其加工余量须在图样上注明。
5)表面质量①铸造模具表面粗糙度应符合GB/T 15114-1994的规定。
②铸造模具不允许有裂纹、欠铸、疏松、气泡和任何穿透性缺陷。
③铸造模具允许有擦伤、凹陷、缺肉和网状毛刺等缺陷。
但其缺陷的程度和数量应该与供需双方同意的标准相一致。
④铸造模具的浇口、飞边、溢流口、隔皮、顶杆痕迹等应清理干净。
但允许留有痕迹。
⑤若图样无特别规定,有关压铸工艺部分的设置,如顶杆位置、分型线的位置、浇口和溢流口的位置等由生产厂自行规定,否则图样上应注明或由供需双方商定。
⑥铸造模具需要特殊加工的表面,如抛光、喷丸、镀铬、涂覆、阳极氧化、化学氧化等须在图样上注明或由供需双方商定。
铝合金压铸技术要求

1、范围本标准规定了铝合金压铸件的技术要求、试验方法、检验规则、交货条件等。
本标准适用于汽车发电机铝合金端盖压铸件。
2、引用标准GB6414 铸件尺寸公差GB6987.1-GB6987.16铝及铝合金化学分析方法GB288-87 金属拉力试验法GB/T13822-92 压铸有色合金试样GB6060.5 表面粗造度比较样块抛(喷)丸、喷吵加工表面3、技术要求3.1压铸铝合金的牌号压铸铝合金采用 UNS-A03800(美国A380.0,日本 ADC10 )可选用材料UNS-A03830 (美国383.0,日本 ADC12 )化学成份见表 1表 1牌号化学成份(重量百分比)标准号UNS 编号A380.0 Si 7.5-9.5,Cu 3.0-4.0 , Zn≤3.0 , Mg≤ 0.1, QQA-591E A13800 Mn ≤0.5, Ni ≤0.5, Sn≤0.35, Fe≤1.3 ,AI 余量ADC10 Si 7.5-9.5,Cu 2.0-4.0 , Zn≤1.0 , Mg≤ 0.3, JIS H5302 A13800 Mn ≤0.5, Ni ≤0.5, Sn≤0.3, Fe≤1.3 ,AI 余量383.0 Si 9.5-11.5,Cu 2.0-3.0, Zn≤3.0 , Mg≤ 0.1, QQ A-591E A03830 Mn ≤0.5, Ni ≤0.3, Sn ≤ 0.15,Fe≤1.3 ,AI 余量ADC12 Si 9.6-12,Cu 1.5-3.5 , Zn≤1.0 , Mg≤ 0.3, JIS H5302 A03830 Mn ≤0.5, Ni ≤0.5, Sn≤0.3, Fe≤1.3 ,AI 余量供应商可选择上述四种牌号的任何一种,如在生产过程中更换其它牌号,需重新进行样件鉴定。
3.1.1回炉料使用规定3.1.1.1回炉料分类一级回炉料:浇道、化学成份合格的废铸件,后加工次品等不含水分和油污。
铝合金压铸件一般技术要求
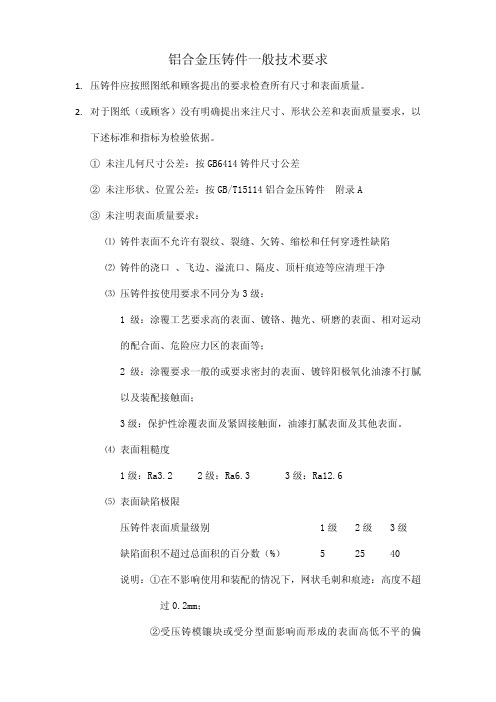
铝合金压铸件一般技术要求1.压铸件应按照图纸和顾客提出的要求检查所有尺寸和表面质量。
2.对于图纸(或顾客)没有明确提出来注尺寸、形状公差和表面质量要求,以下述标准和指标为检验依据。
①未注几何尺寸公差:按GB6414铸件尺寸公差②未注形状、位置公差:按GB/T15114铝合金压铸件 附录A③未注明表面质量要求:⑴铸件表面不允许有裂纹、裂缝、欠铸、缩松和任何穿透性缺陷⑵铸件的浇口 、飞边、溢流口、隔皮、顶杆痕迹等应清理干净⑶压铸件按使用要求不同分为3级:1级:涂覆工艺要求高的表面、镀铬、抛光、研磨的表面、相对运动的配合面、危险应力区的表面等;2级:涂覆要求一般的或要求密封的表面、镀锌阳极氧化油漆不打腻以及装配接触面;3级:保护性涂覆表面及紧固接触面,油漆打腻表面及其他表面。
⑷表面粗糙度1级:Ra3.2 2级:Ra6.3 3级:Ra12.6⑸表面缺陷极限压铸件表面质量级别 1级 2级 3级缺陷面积不超过总面积的百分数(%) 5 25 40说明:①在不影响使用和装配的情况下,网状毛刺和痕迹:高度不超过0.2mm;②受压铸模镶块或受分型面影响而形成的表面高低不平的偏差,不超过相关的公差尺寸;③推杆痕迹表面凸出或凹入铸件表面的深度,一般为±0.2mm;⑹表面质量要求(见附表)⑺挫痕:目视挫痕应均匀、一致,不允许有明显的凹凸。
经锉加工的表面和未经锉加工的表面允许有角度,但角度应在10°以内;⑻变形:压铸件成型后,如有变形应进行调整,经调整后的压铸件表面不允许有明显的打击痕迹。
调整部分的平面度:0.2mm;⑼对于顾客的特殊要求,要形成相应的工艺文件,规定其相关的工艺过程和检验方法。
附表: 缺陷名称 缺陷范围表面质量级别 备注1级2级 3级 流痕深度(mm )≤ 0.05 0.07 0.15面积不超过总面积的百分数515 30冷隔深度(mm )≤ 不允许1/5壁厚 1/4壁厚 1.在同一部分对应出不允许同时存在2.长度是指缺陷流向的展开长度长度不大于铸件的最大轮廓尺寸的(mm ) 1/101/5所在面上的不允许超过的数量 2处 2处 离铸件边缘距离(mm )≥ 4 4 两冷隔间距(mm )≥10 10 拉伤深度(mm )≤ 0.05 0.1 0.25 除一级表面外,浇道部位允许增加一倍面积不超过总面积的百分数35 10 凹陷 凹入深度(mm ) 0.10.3 0.5 粘附物痕迹整个铸件缺陷不允许超过 不允许1处 2处 占带缺陷的表面面积的百分比5 10气泡平均直径≤3mm1.每100cm 2缺陷个数不超过不允许 1 2 允许两种气泡同时存在,但大气泡不超过3个,总数不超过10个。
铝合金铸造件检验技术条件
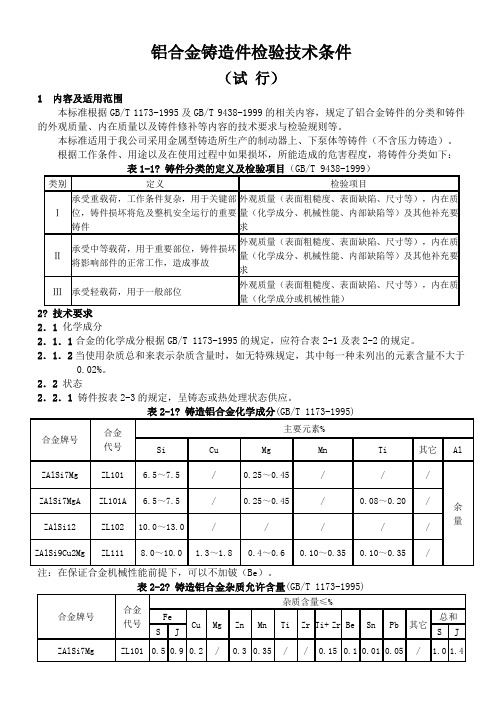
铝合金铸造件检验技术条件(试行)1 内容及适用范围本标准根据GB/T 1173-1995及GB/T 9438-1999的相关内容,规定了铝合金铸件的分类和铸件的外观质量、内在质量以及铸件修补等内容的技术要求与检验规则等。
本标准适用于我公司采用金属型铸造所生产的制动器上、下泵体等铸件(不含压力铸造)。
根据工作条件、用途以及在使用过程中如果损坏,所能造成的危害程度,将铸件分类如下:2?技术要求2.1 化学成分2.1.1合金的化学成分根据GB/T 1173-1995的规定,应符合表2-1及表2-2的规定。
2.1.2当使用杂质总和来表示杂质含量时,如无特殊规定,其中每一种未列出的元素含量不大于0.02%。
2.2 状态2.2.1铸件按表2-3的规定,呈铸态或热处理状态供应。
注:在保证合金机械性能前提下,可以不加铍(Be)。
2.3 机械性能2.3.1 每批铸件应按其类别检验机械性能。
2.3.2 合金及其铸件的机械性能应符合表2-3的规定。
2.4外观质量2.4.1铸件在进行表面粗糙度、表面缺陷、尺寸等外观质量检验之前,飞边、溢流口、隔皮等应清理干净、平整,但不可在非加工表面上留有明显的凿痕,且宽度不得超过2mm。
2.4.2铸件的表面粗糙度Ra为6.3μm以上。
2.4.3非加工表面的浇冒口,应清理到与铸件表面齐平;待加工表面的浇冒口残留量应不大于3mm。
2.4.4清除飞翅、夹砂等多肉类缺陷,铸件的内外表面由于型芯及顶杆的磨损所产生的飞边、毛刺应清除干净。
2.4.5根据顾客图样或技术文件的要求,铸件表面可进行喷砂处理。
2.4.6铸件上作为基准用的部位应平整,不允许存在任何凸起痕迹,装饰面上不允许有推杆痕迹(图样上注明)。
2.4.7非加工表面上,由于模具组合镶并或受分型面影响而形成的铸件表面高低不平差值不得超过0.3mm。
2.4. 8非加工表面上,不允许有超过表2-4(Ⅰ)级规定的花纹、麻面和有色斑点。
2.4.9铸件尺寸应符合图样的要求。
铝合金铸造件检验技术条件
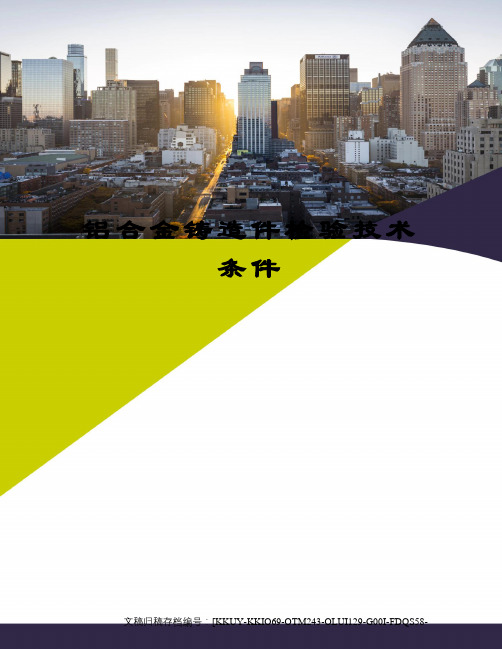
铝合金铸造件检验技术条件文稿归稿存档编号:[KKUY-KKIO69-OTM243-OLUI129-G00I-FDQS58-铝合金铸造件检验技术条件(试行)1 内容及适用范围本标准根据GB/T 1173-1995及GB/T 9438-1999的相关内容,规定了铝合金铸件的分类和铸件的外观质量、内在质量以及铸件修补等内容的技术要求与检验规则等。
本标准适用于我公司采用金属型铸造所生产的制动器上、下泵体等铸件(不含压力铸造)。
根据工作条件、用途以及在使用过程中如果损坏,所能造成的危害程度,将铸件分类如下:表1-1 铸件分类的定义及检验项目(GB/T 9438-1999)2技术要求2.1 化学成分2.1.1合金的化学成分根据GB/T 1173-1995的规定,应符合表2-1及表2-2的规定。
2.1.2当使用杂质总和来表示杂质含量时,如无特殊规定,其中每一种未列出的元素含量不大于0.02%。
2.2 状态2.2.1铸件按表2-3的规定,呈铸态或热处理状态供应。
表2-1 铸造铝合金化学成分(GB/T 1173-1995)注:在保证合金机械性能前提下,可以不加铍(Be)。
表2-2 铸造铝合金杂质允许含量(GB/T 1173-1995)表2-3 铸造铝合金机械性能(GB/T 1173-1995)2.3 机械性能2.3.1 每批铸件应按其类别检验机械性能。
2.3.2 合金及其铸件的机械性能应符合表2-3的规定。
2.4外观质量2.4.1铸件在进行表面粗糙度、表面缺陷、尺寸等外观质量检验之前,飞边、溢流口、隔皮等应清理干净、平整,但不可在非加工表面上留有明显的凿痕,且宽度不得超过2mm。
2.4.2铸件的表面粗糙度Ra为6.3μm以上。
2.4.3非加工表面的浇冒口,应清理到与铸件表面齐平;待加工表面的浇冒口残留量应不大于3mm。
2.4.4清除飞翅、夹砂等多肉类缺陷,铸件的内外表面由于型芯及顶杆的磨损所产生的飞边、毛刺应清除干净。
铝合金锻造工艺技术要求

铝合金锻造工艺技术要求铝合金锻造工艺技术要求铝合金锻造工艺是一种将铝合金材料加热至一定温度后在压力作用下使其发生塑性变形的工艺方法。
下面将介绍铝合金锻造工艺技术的要求。
一、温度控制:铝合金锻造过程中,材料的温度控制至关重要。
高温有利于材料的塑性变形,但温度过高会导致材料的烧损、氧化以及晶粒长大,降低材料的性能,因此需要控制加热温度,一般在材料的熔点以下适当加热。
而在锻造过程中,温度的控制也很重要,锻造温度过低会使材料难以塑性变形,而温度过高则易导致过度变形、裂纹等缺陷。
因此,需要根据材料的特性和实际情况,在适宜的温度范围内进行锻造。
二、锻造压力控制:铝合金的锻造过程中,锻造压力的大小直接影响到材料的塑性变形。
合理的锻造压力能够使材料得到良好的塑性变形,但过大的锻造压力会使得材料过度变形,甚至出现裂纹等缺陷。
因此,在锻造过程中需要合理控制锻造压力,根据材料的特性和锻造要求进行调整。
三、锻造速度控制:锻造速度是指在铝合金锻造过程中,锤击或压力的速度。
良好的锻造速度有利于材料的塑性变形,但过快的锻造速度则会使得材料塑性变形不充分,甚至出现裂纹等缺陷。
因此,在铝合金锻造过程中,需要合理控制锻造速度,使其保持在适宜范围内,以确保材料得到良好的塑性变形。
四、模具设计和加工精度:模具设计和加工精度直接影响到铝合金锻造件的尺寸和形状。
模具设计应合理,保证锻造件的尺寸和形状满足要求。
而模具的加工精度对于铝合金锻造件的质量也有重要影响,因此,需要严格按照设计要求进行模具的加工。
五、表面处理:铝合金锻造后的产品通常需要进行表面处理,以去除表面氧化层、油污等杂质,提高表面质量。
表面处理的方法可以包括酸洗、抛光等。
表面处理的质量直接影响到产品的外观和性能,因此,需要严格控制表面处理的质量。
综上所述,铝合金锻造工艺技术要求包括温度控制、锻造压力控制、锻造速度控制、模具设计和加工精度以及表面处理等多个方面。
只有通过合理控制这些要求,才能保证铝合金锻造过程中材料的塑性变形和锻造件的质量。
山东铝合金重力铸造设计标准
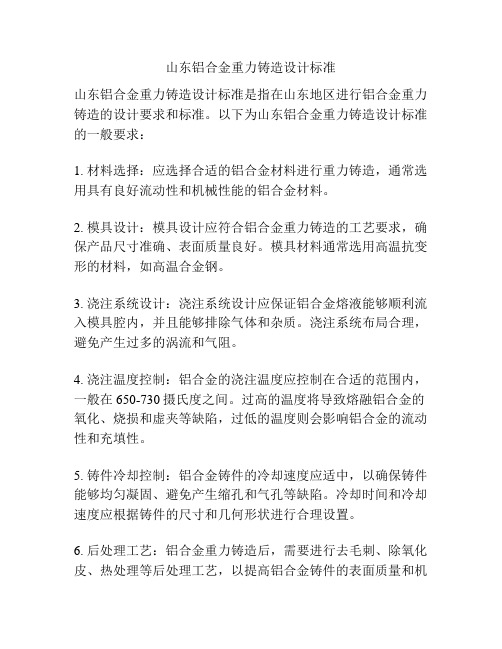
山东铝合金重力铸造设计标准
山东铝合金重力铸造设计标准是指在山东地区进行铝合金重力铸造的设计要求和标准。
以下为山东铝合金重力铸造设计标准的一般要求:
1. 材料选择:应选择合适的铝合金材料进行重力铸造,通常选用具有良好流动性和机械性能的铝合金材料。
2. 模具设计:模具设计应符合铝合金重力铸造的工艺要求,确保产品尺寸准确、表面质量良好。
模具材料通常选用高温抗变形的材料,如高温合金钢。
3. 浇注系统设计:浇注系统设计应保证铝合金熔液能够顺利流入模具腔内,并且能够排除气体和杂质。
浇注系统布局合理,避免产生过多的涡流和气阻。
4. 浇注温度控制:铝合金的浇注温度应控制在合适的范围内,一般在650-730摄氏度之间。
过高的温度将导致熔融铝合金的氧化、烧损和虚夹等缺陷,过低的温度则会影响铝合金的流动性和充填性。
5. 铸件冷却控制:铝合金铸件的冷却速度应适中,以确保铸件能够均匀凝固、避免产生缩孔和气孔等缺陷。
冷却时间和冷却速度应根据铸件的尺寸和几何形状进行合理设置。
6. 后处理工艺:铝合金重力铸造后,需要进行去毛刺、除氧化皮、热处理等后处理工艺,以提高铝合金铸件的表面质量和机
械性能。
7. 工艺参数记录:在铝合金重力铸造过程中,应记录浇注温度、冷却时间、铸造工艺参数等重要数据,以便进行工艺分析和质量控制。
山东铝合金重力铸造设计标准的目的是规范山东地区铝合金重力铸造过程,确保铸件的质量和性能符合设计要求,提高铝合金铸件的生产效率和市场竞争力。
铝合金压铸件一般技术要求

铝合金压铸件一般技术要求铝合金压铸件是利用铝合金熔体通过高压注射进入金属模具中,通过自身的凝固过程形成的零件。
它具有良好的综合性能,广泛应用于各个领域,如汽车、航空航天、电子等。
为了保证铝合金压铸件的质量和可靠性,有一系列一般技术要求需要遵守。
首先,铝合金压铸件的设计要合理。
合理的设计能保证零件的结构和尺寸满足使用要求,避免因结构设计不当而导致的铝合金压铸件质量问题。
设计时应考虑铝合金材料的特性和成型工艺,合理布置加强筋和放大壁厚等措施,确保压铸件有足够的强度和刚度。
其次,材料的选择要合适。
铝合金压铸件一般采用高强度、高导热性的铝合金材料,如ADC12、A380等。
材料的选择要符合使用环境的要求,具有良好的耐热、耐腐蚀、耐磨损和耐腐蚀性能。
材料的选择还需要考虑成本因素,以保证生产的经济性。
第三,模具的制造要精确。
模具的精度和质量对铝合金压铸件的成型质量起着重要的影响。
模具制造应严格按照设计要求进行,尺寸精度应达到零件的使用要求。
模具材料一般选用精密,耐磨耐热的材料,如合金钢、硬质合金等,以保证模具的耐用性和寿命。
第四,操作工艺要规范。
铝合金压铸件的压铸过程需要控制压铸机的参数,如注射速度、注射压力和注入时间等。
同时,还需要注意合金的热处理和退火工艺,以提高原材料的性能和细化晶粒。
此外,还需要对压铸件进行后处理,如除霜、抽调、清洗和表面处理等,以保证铝合金压铸件的表面质量和使用寿命。
最后,质量检查要全面。
对铝合金压铸件进行全面的质量检查是确保产品质量的重要手段之一、常用的检查方法有外观检查、尺寸检查、物理性能测试、金相组织分析等。
通过严格的质量检查,可以及时发现和纠正问题,保证产品的合格率和一致性。
综上所述,铝合金压铸件的一般技术要求涉及设计、材料、模具、操作工艺和质量检查等方面,通过科学的设计和精确的制造工艺,可以生产出质量可靠的铝合金压铸件,满足不同领域的使用需求。
铝合金压铸技术要求
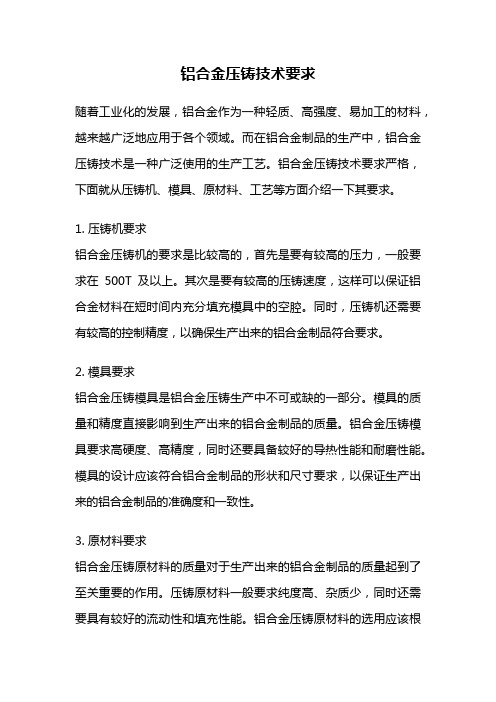
铝合金压铸技术要求随着工业化的发展,铝合金作为一种轻质、高强度、易加工的材料,越来越广泛地应用于各个领域。
而在铝合金制品的生产中,铝合金压铸技术是一种广泛使用的生产工艺。
铝合金压铸技术要求严格,下面就从压铸机、模具、原材料、工艺等方面介绍一下其要求。
1. 压铸机要求铝合金压铸机的要求是比较高的,首先是要有较高的压力,一般要求在500T及以上。
其次是要有较高的压铸速度,这样可以保证铝合金材料在短时间内充分填充模具中的空腔。
同时,压铸机还需要有较高的控制精度,以确保生产出来的铝合金制品符合要求。
2. 模具要求铝合金压铸模具是铝合金压铸生产中不可或缺的一部分。
模具的质量和精度直接影响到生产出来的铝合金制品的质量。
铝合金压铸模具要求高硬度、高精度,同时还要具备较好的导热性能和耐磨性能。
模具的设计应该符合铝合金制品的形状和尺寸要求,以保证生产出来的铝合金制品的准确度和一致性。
3. 原材料要求铝合金压铸原材料的质量对于生产出来的铝合金制品的质量起到了至关重要的作用。
压铸原材料一般要求纯度高、杂质少,同时还需要具有较好的流动性和填充性能。
铝合金压铸原材料的选用应该根据铝合金制品的要求和生产工艺来进行选择。
4. 工艺要求铝合金压铸技术的工艺要求主要包括模具温度、压铸温度、压铸速度等。
模具温度一般要求在200℃以上,以保证铝合金材料充分流动。
压铸温度要求控制在合适的范围内,过高会导致铝合金材料产生气孔,过低则会导致铝合金材料填充不充分。
压铸速度也要根据铝合金制品的要求和生产工艺来进行调整。
铝合金压铸技术要求严格,需要从多个方面考虑,才能生产出符合要求和标准的铝合金制品。
同时,压铸技术的不断创新和完善,也为铝合金制品的生产提供了更好的技术支持。
铝合金铸造技术要求

铝合金铸造技术要求铝合金铸造技术是一种常用的金属加工技术,广泛应用于航空航天、汽车、机械等领域。
在铝合金铸造过程中,需要满足一定的技术要求,以确保产品的质量和性能。
本文将介绍铝合金铸造技术的要求,包括合金选择、模具设计、熔炼与浇注、热处理和表面处理等方面。
一、合金选择选择合适的铝合金对于铝合金铸造至关重要。
铝合金的选择应根据产品的用途、性能要求和成本考虑。
常用的铝合金有铝硅合金、铝铜合金、铝镁合金等。
不同的合金具有不同的性能特点,如强度、耐蚀性、导热性等。
在选择合金时,需综合考虑产品的使用环境和要求,以及合金的可加工性。
二、模具设计模具设计是铝合金铸造中的关键环节。
合理的模具设计能够提高产品的质量和生产效率。
在模具设计中,需要考虑产品的结构形式、壁厚、收缩率等因素。
模具的结构应具有足够的强度和刚性,以承受铝液的冲击和热应力。
同时,模具的排气和冷却系统也需要合理设计,以避免缺陷的产生。
三、熔炼与浇注铝合金铸造的熔炼与浇注过程需要严格控制。
首先,需选择合适的熔炼设备和工艺。
熔炼设备应具备良好的加热和保温性能,以确保铝液达到适宜的浇注温度。
其次,需控制铝液的成分和温度,以确保合金的成分和性能符合要求。
在浇注过程中,应注意避免气体和杂质的混入,以减少缺陷的产生。
四、热处理热处理是提高铝合金铸造品质的重要手段。
常用的热处理方法有时效处理、固溶处理和淬火等。
热处理能够改善铝合金的强度、硬度和耐腐蚀性。
在热处理过程中,需控制加热温度、保温时间和冷却速率,以确保合金的组织和性能达到预期目标。
五、表面处理表面处理是铝合金铸造的最后一道工序,能够提高产品的外观和耐腐蚀性。
常用的表面处理方法有阳极氧化、电泳涂装和喷涂等。
表面处理能够形成保护膜,防止铝合金与外界环境的接触,延长产品的使用寿命。
铝合金铸造技术要求包括合金选择、模具设计、熔炼与浇注、热处理和表面处理等方面。
合理选择合金、设计模具、控制熔炼与浇注过程、进行合适的热处理和表面处理,能够确保铝合金铸造产品的质量和性能,满足用户的需求。
铝合金铸件的成形实验注意事项

铝合金铸件的成形实验注意事项一、实验前准备1.1 确定实验目的和要求,了解所需铝合金材料的性质和特点。
1.2 确定所需设备和工具,并检查其状态和完好度。
1.3 准备好所需材料,包括铝合金材料、模具、涂料等。
二、模具制备2.1 根据所需铝合金铸件的形状和尺寸,选择合适的模具,并进行加工和调试。
2.2 清洁模具表面,涂抹隔离剂以防止粘结。
2.3 根据实验要求,在模具内部加入冷却水管道或其他辅助装置。
三、铸造操作3.1 将准备好的铝合金材料放入熔炉中进行熔化,保持适宜温度并搅拌均匀。
3.2 将模具放入注型机中,将熔化后的铝合金倒入注射头中进行注射。
注意控制注射速度和压力,避免产生气泡或裂纹等缺陷。
3.3 在注射完成后,将模具放入冷却水中进行冷却。
注意控制冷却速度和时间,避免产生变形或裂纹等缺陷。
四、铝合金铸件的处理和检测4.1 将铝合金铸件从模具中取出,并进行去除余料、切割和修整等处理。
4.2 进行表面处理,包括喷砂、抛光、电镀等。
4.3 进行物理性能测试,如硬度、拉伸强度、冲击韧性等。
同时进行缺陷检测,如气孔、夹杂等。
五、实验注意事项5.1 操作人员必须经过专业培训,并严格遵守操作规程和安全操作要求。
5.2 熔炉和注射机等设备必须定期维护和保养,确保其正常运行状态。
5.3 模具必须严格按照设计要求制作,并进行加工和调试。
模具表面必须清洁干净并涂抹隔离剂。
5.4 铝合金材料必须符合国家标准或行业标准,并进行质量检测。
熔化后的铝合金液体必须保持适宜温度并搅拌均匀。
5.5 注射过程中必须控制注射速度和压力,避免产生气泡或裂纹等缺陷。
冷却过程中必须控制冷却速度和时间,避免产生变形或裂纹等缺陷。
5.6 铝合金铸件处理和检测过程中必须严格按照标准操作,并进行记录和统计分析。
5.7 实验结束后,必须对设备、工具、材料等进行清洁和归位,并做好实验记录和报告。
铝合金铸造模具标准

铝合金铸造模具标准
铝合金铸造模具是用于铝合金铸造的工具,其质量和精度对铝合金铸件的质量
和精度有着重要的影响。
因此,铝合金铸造模具的标准化是非常重要的。
本文将从模具材料、设计、制造、使用等方面介绍铝合金铸造模具的标准。
首先,模具的材料选择是模具标准化的重要内容之一。
铝合金铸造模具的材料
应具有一定的强度、硬度和耐磨性,以确保模具在长时间使用过程中不会出现变形或损坏。
常用的模具材料有铝青铜、合金工具钢等,这些材料具有良好的机械性能和耐磨性,能够满足铝合金铸造模具的使用要求。
其次,在模具的设计方面,应遵循一定的标准和规范。
模具的结构设计应考虑
到铝合金铸件的形状和尺寸,以确保铸件的精度和表面质量。
此外,模具的冷却系统设计也是模具标准化的重要内容之一,良好的冷却系统设计能够有效地控制铸件的凝固过程,提高铸件的组织致密度和力学性能。
在模具的制造过程中,应严格遵循相关的工艺标准和操作规程。
模具的加工精
度和表面质量直接影响着铝合金铸件的质量和外观。
因此,模具的加工过程应严格控制,确保模具的尺寸精度和表面光洁度达到标准要求。
最后,在模具的使用过程中,应定期进行检查和维护,确保模具的性能和精度。
模具的使用环境应符合相关的安全标准,避免因操作不当或环境因素导致模具损坏或事故发生。
综上所述,铝合金铸造模具的标准化涉及模具材料、设计、制造、使用等多个
方面,只有严格遵循相关的标准和规范,才能保证铝合金铸造模具的质量和精度,最终提高铝合金铸件的质量和外观。
希望本文的介绍能够对铝合金铸造模具的标准化有所帮助。
压铸模具技术条件

1 目的:规范公司模具设计、制造的技术、质量标准,在顾客没有特殊要求的情况下,作为公司模具制造、验收的准则。
2 适用范围:适用于公司制造的铝、镁、锌压铸模具的设计、制造、验收、运输过程。
3 引用标准:GB/T8844-2003 压铸模具技术要求GB/T1804-2000 一般公差未注公差的线性和角度公差GB/T1184-1996 形状公差和位置公差未注公差值GB/T197-1981 普通螺纹公差与配合4 技术要求4.1压铸模材料、热处理技术要求压铸模零件选用的材料、热处理技术要求:应符合表1。
表1:压铸模零件常用材料及热处理要求4.2压铸模几何尺寸技术要求4.2.1 成型部位未注公差的极限偏差:应符合表2要求4.2.2 成型部位转接圆弧未注公差的极限偏差:应符合表3要求4.2.3成型部位未注角度和锥度公差:应符合表4要求(注:锥度公差按锥体母线长度决定,角度公差按角度短边长度决定)4.2.4非成型部位未注公差的极限偏差:应符合表5要求表5:非成型部位未注公差 mm4.2.5螺钉安装孔、推杆孔、复位杆孔等未注孔距公差的极限偏差:应符合表6要求表6:螺钉安装孔、推杆孔、复位杆孔等未注孔距公差mm4.2.6模具零件图中螺纹的基本尺寸:应符合表7要求表7:螺纹的基本尺寸mm4.2.7压铸模模具零件的配合类别和精度等级:应符合表8、表9要求表8:模具零件的配合类别和精度等级表9:极限公差表μm4.3.1成型部位未注脱模斜度时,形成铸件内侧壁的脱模斜度:应不大于表10的规定值(外侧壁的脱模斜度不大于表5规定值的1/2)表10:成型部位未注脱模斜度4.3.2圆模芯的脱模斜度:应不大于表11的规定值表11:圆模芯脱模斜度4.3.3文字符号的脱模斜度:10°-15°。
4.4 压铸模形位公差技术要求4.4.1模具结构零件和有配合关系结构的形位公差:应符合表12、表13、表14的要求表12:模具结构零件的形位公差表14:形位公差数值表4.4.2 模具零件图中未注形位公差:应符合表15要求压铸模零件表面粗糙度:应符合表16的要求表16:压铸模零件工作部位表面粗糙度4.6 压铸模其他技术要求4.6.1成型部位未注明圆角:R0.5,非工作部位棱边应倒角,型面与分型面或与型芯、推杆等相配合的交接边缘不允许倒角或倒圆。
铝合金铸造过程工艺参数

铝合金铸造是金属铸造领域的重要分支,广泛应用于航空、汽车、电子、建筑等各个行业。
一、浇注系统浇注系统是铝合金铸造过程中的重要组成部分,它包括浇口杯、直浇道、横浇道、内浇口等部分。
浇注系统的设计合理与否直接影响到金属液体的充型能力和充型速度。
在选择浇注系统时,需要根据铸件的结构和要求来选择合适的浇口杯形状、尺寸和位置,以及合理的直浇道和横浇道结构。
同时,还需要根据浇注速度和充型时间等因素来调整内浇口的尺寸和位置。
二、铝合金铸造的参数铝合金铸造的参数主要包括压铸压力、注射速度、模具温度和填充时间。
1. 压铸压力压铸压力也是影响铸件质量和性能的重要参数。
压铸过程中的压力由压力泵产生,作用在金属液体上的压力是获得结构致密、轮廓清晰的铸件的主要因素。
压铸压力的大小直接影响到金属液体的充型能力和压实程度。
过高的压铸压力可能导致金属液体过度流动,形成飞边等缺陷;而过低的压铸压力则可能导致金属液体无法充分填充型腔,形成缩孔等缺陷。
因此,选择合适的压铸压力可以保证金属液体的充型能力和压实程度,提高铸件的质量和性能。
2. 速度(1)压铸速度铝合金铸造的注射速度是指压铸过程中注射头的速度。
注射速度的设置应该根据具体的情况来决定。
注射速度分为慢速注射和快速注射,一般慢速为0.1~0.5M/S,快速一般为0.1~1.1M/S。
铸件壁厚越薄,注射速度越快,铸件形状越复杂,注射速度越快。
铸件的突出面越大,注射速度越快,铸球路径越长,注射速度越快。
(2)浇注速度浇注速度是影响铸件质量和性能的重要因素之一。
过快的浇注速度可能导致金属液体在充型过程中产生涡流和卷气等缺陷;而过慢的浇注速度则可能导致金属液体无法充分填充型腔,形成缩孔等缺陷。
因此,在铝合金铸造过程中,需要根据铸件的结构和要求来选择合适的浇注速度。
同时,还需要根据金属液体的流动性和充型能力等因素来调整内浇口的尺寸和位置。
3. 模具温度铝合金铸造的模具温度是影响铸件质量和性能的重要参数之一。
汽车用铝合金铸件技术条件-概述说明以及解释

汽车用铝合金铸件技术条件-概述说明以及解释1.引言1.1 概述概述汽车用铝合金铸件技术条件是指在汽车制造过程中,对于使用铝合金材料进行铸造的要求和标准。
随着车辆轻量化趋势的不断发展,汽车制造商越来越倾向于使用轻质材料来替代传统的钢铁材料。
铝合金作为一种重要的轻质材料,在汽车行业中得到了广泛的应用。
汽车用铝合金铸件技术条件的重要性不容忽视。
正确的技术条件可以保证铝合金铸件的质量和性能,同时也能提高生产效率和降低成本。
对于汽车制造商来说,汽车用铝合金铸件的质量和性能直接影响到车辆的安全性和可靠性。
因此,制定合适的技术条件对于保证汽车的品质至关重要。
本文将从以下几个方面对汽车用铝合金铸件技术条件进行详细的探讨。
首先,我们将介绍车辆轻量化趋势,解析为什么轻质材料在汽车制造中的应用越来越广泛。
其次,我们将深入探讨铝合金铸件在汽车行业中的应用,介绍铝合金材料在汽车制造中的优势和挑战。
最后,我们将重点关注汽车用铝合金铸件技术条件的重要性,分析如何制定合适的技术条件以保证铸件的质量和性能。
通过对这些内容的探讨和分析,我们将总结出汽车用铝合金铸件技术条件的关键要点,展望未来该技术的发展前景。
我们希望本文能够帮助读者更好地理解汽车用铝合金铸件技术条件的重要性,并为汽车制造商提供实用的指导和建议。
让我们一起深入研究这一重要的汽车制造技术,为推动汽车工业的发展做出贡献。
1.2 文章结构本篇文章主要分为引言、正文和结论三个部分。
在引言部分,首先概述了本文要讨论的内容——汽车用铝合金铸件技术条件。
接着介绍了文章的结构和目的,以让读者了解本文的整体安排和写作意图。
正文部分分为三个小节。
首先,讨论了当前车辆轻量化趋势,即汽车行业中越来越重视车辆的减重问题,并探讨了轻量化的重要性和影响。
接着,阐述了铝合金铸件在汽车行业中的应用情况,展示了铝合金铸件在解决车辆轻量化问题上的优势以及其在汽车制造中的广泛应用。
最后,重点讨论了汽车用铝合金铸件技术条件的重要性,介绍其对于铸件质量、性能、成本和可靠性的影响,以及对整个汽车制造工艺的重要作用。
- 1、下载文档前请自行甄别文档内容的完整性,平台不提供额外的编辑、内容补充、找答案等附加服务。
- 2、"仅部分预览"的文档,不可在线预览部分如存在完整性等问题,可反馈申请退款(可完整预览的文档不适用该条件!)。
- 3、如文档侵犯您的权益,请联系客服反馈,我们会尽快为您处理(人工客服工作时间:9:00-18:30)。
或由供需双方商定。 ⑥铸造模具需要特殊加工的表面,如抛光、喷 丸、镀铬、涂覆、阳极氧化、化学氧化等须在图 样上注明或由供需双方商定。
1)化学成分合金的化学成分应符合GB/T 151141994的规定。 2)力学性能 ①当采用铸造模具试样检验时,其力学性能应 符合GB/T
Байду номын сангаас
15114-1994规定②当采用铸造模具本体检验时, 其指定部位切取试样的力学性能不得低于单铸试 样的75%,若有特殊要求,可由供需双方商定。 3)铸造
模具尺寸 ①铸造模具的几何形状和尺寸应符合铸件图样 的规定。 ②铸造模具的尺寸公差应按GB/T 6414-1999 的规定执行。有特殊规定和要求
模具允许有擦伤、凹陷、缺肉和网状毛刺等缺陷。 但其缺陷的程度和数量应该与供需双方同意的标 准相一致。 ④铸造模具的浇口、飞边、溢流口、隔皮、顶 杆痕迹等应清
理干净。但允许留有痕迹。 ⑤若图样无特别规定,有关压铸工艺部分的设 置,如顶杆位置、分型线的位置、浇口和溢流口 的位置等由生产厂自行规定,否则图样上应注明
4)铸造模具需要时,其加工余量按GB/T 15114-1994的规定执行。若有特殊规定和要求 时,其加工余量须在图样上注明。 5)表面质量
模具设计教程网
①铸造模具表面粗糙度应符合GB/T 151141994的规定。 ②铸造模具不允许有裂纹、欠铸、疏松、气泡 和任何穿透性缺陷。 ③铸造
时,须在图样上注明。 ③铸造模具有形位公差要求时,可参照表5; 其标注方法按GB/T 15114-1994的规定。 ④铸造模具的尺寸公差不包括
铸造斜度,其不加工表面:包容面以小端为基准, 被包容面以大端为基准;待加工表面:包容面以 大端为基准,被包容面以小端为基准,有特殊规 定和要求时,须在图样上注明。