高速切削加工技术-黄冬平-142271336
高速切削技术概述

高速切削技术概述作者:同济大学职业技术教育学院唐立山一、高速切削技术概述1931年4月德国物理学家Carl.J.Saloman最早提出了高速切削(High Speed Cutting)的理论,并于同年申请了专利。
他指出:在常规切削速度范围内,切削温度随着切削速度的提高而升高,但切削速度提高到一定值之后,切削温度不但不会升高反而会降低,且该切削速度VC与工件材料的种类有关。
对于每一种工件材料都存在一个速度范围,在该速度范围内,由于切削温度过高,刀具材料无法承受,切削加工不可能进行。
要是能越过这个速度范围,高速切削将成为可能,从而大幅度地提高生产效率。
由于实验条件的限制,当时高速切削无法付诸实践,但这个思想给后人一个非常重要的启示。
高速加工技术经历了理论探索,应用探索,初步应用和较成熟应用等四个阶段,现已在生产中得到了一定的推广。
特别是20世纪80年代以来,航空工业和模具工业的需求大大推动了高速加工的应用。
飞机零件中有大量的薄壁零件,如翼肋、长桁、框等,它们有很薄的壁和筋,加工中金属切除率很高,容易产生切削变形,加工比较困难;另外,飞机制造厂方也迫切要求提高零件的加工效率,从而缩短飞机的交付时间。
在模具工业和汽车工业中,模具制造是一个关键,缩短模具交货周期,提高模具制造质量,也是人们长期努力的目标。
高速切削无疑是解决这些问题的一条重要途径。
自20世纪90年代起,高速加工逐步在制造业中推广应用。
目前,据统计,在美国和日本,大约有30%的公司已经使用高速加工,在德国,这个比例高于40%。
在飞机制造业中,高速切削已经普遍用于零件的加工。
目前高速切削已经有了一定的应用,但要给高速铣削下一个确切的定义还较困难,高速切削的切削速度范围较难给出。
高速切削是一个相对概念,它与加工材料、加工方式、刀具、切削参数等有很大的关系。
一般认为,高速切削的切削速度是常规切削速度的5~10倍。
对常用材料,一些资料给出了大致数据:铝合金1500~5500 m/min;铜合金900 ~5000 m/min;钛合金100~1000 m/min;铸铁750~4500 m/min;钢600~800 m/min。
中图分类号查询TG金属学与金属工艺
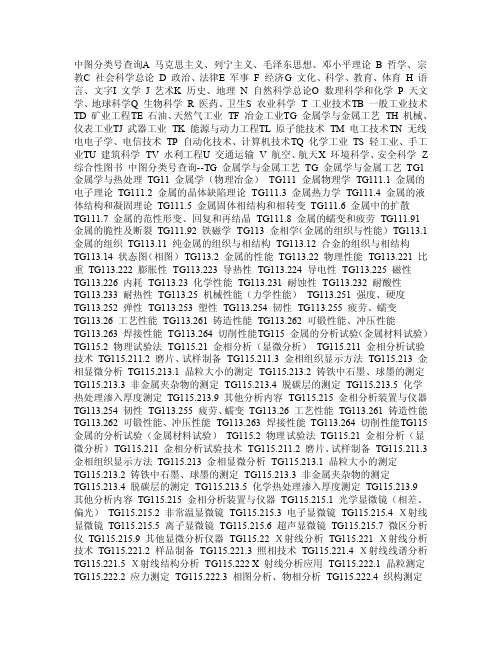
中图分类号查询A 马克思主义、列宁主义、毛泽东思想、邓小平理论B 哲学、宗教C 社会科学总论D 政治、法律E 军事 F 经济G 文化、科学、教育、体育H 语言、文字I 文学J 艺术K 历史、地理N 自然科学总论O 数理科学和化学P 天文学、地球科学Q 生物科学R 医药、卫生S 农业科学T 工业技术TB 一般工业技术TD 矿业工程TE 石油、天然气工业TF 冶金工业TG 金属学与金属工艺TH 机械、仪表工业TJ 武器工业TK 能源与动力工程TL 原子能技术TM 电工技术TN 无线电电子学、电信技术TP 自动化技术、计算机技术TQ 化学工业TS 轻工业、手工业TU 建筑科学TV 水利工程U 交通运输V 航空、航天X 环境科学、安全科学Z 综合性图书中图分类号查询--TG 金属学与金属工艺TG 金属学与金属工艺TG1 金属学与热处理TG11 金属学(物理冶金)TG111 金属物理学TG111.1 金属的电子理论TG111.2 金属的晶体缺陷理论TG111.3 金属热力学TG111.4 金属的液体结构和凝固理论TG111.5 金属固体相结构和相转变TG111.6 金属中的扩散TG111.7 金属的范性形变、回复和再结晶TG111.8 金属的蠕变和疲劳TG111.91 金属的脆性及断裂TG111.92 铁磁学TG113 金相学(金属的组织与性能)TG113.1 金属的组织TG113.11 纯金属的组织与相结构TG113.12 合金的组织与相结构TG113.14 状态图(相图)TG113.2 金属的性能TG113.22 物理性能TG113.221 比重TG113.222 膨胀性TG113.223 导热性TG113.224 导电性TG113.225 磁性TG113.226 内耗TG113.23 化学性能TG113.231 耐蚀性TG113.232 耐酸性TG113.233 耐热性TG113.25 机械性能(力学性能)TG113.251 强度、硬度TG113.252 弹性TG113.253 塑性TG113.254 韧性TG113.255 疲劳、蠕变TG113.26 工艺性能TG113.261 铸造性能TG113.262 可锻性能、冲压性能TG113.263 焊接性能TG113.264 切削性能TG115 金属的分析试验(金属材料试验)TG115.2 物理试验法TG115.21 金相分析(显微分析)TG115.211 金相分析试验技术TG115.211.2 磨片、试样制备TG115.211.3 金相组织显示方法TG115.213 金相显微分析TG115.213.1 晶粒大小的测定TG115.213.2 铸铁中石墨、球墨的测定TG115.213.3 非金属夹杂物的测定TG115.213.4 脱碳层的测定TG115.213.5 化学热处理渗入厚度测定TG115.213.9 其他分析内容TG115.215 金相分析装置与仪器TG113.254 韧性TG113.255 疲劳、蠕变TG113.26 工艺性能TG113.261 铸造性能TG113.262 可锻性能、冲压性能TG113.263 焊接性能TG113.264 切削性能TG115 金属的分析试验(金属材料试验)TG115.2 物理试验法TG115.21 金相分析(显微分析)TG115.211 金相分析试验技术TG115.211.2 磨片、试样制备TG115.211.3 金相组织显示方法TG115.213 金相显微分析TG115.213.1 晶粒大小的测定TG115.213.2 铸铁中石墨、球墨的测定TG115.213.3 非金属夹杂物的测定TG115.213.4 脱碳层的测定TG115.213.5 化学热处理渗入厚度测定TG115.213.9其他分析内容TG115.215 金相分析装置与仪器TG115.215.1 光学显微镜(相差、偏光)TG115.215.2 非常温显微镜TG115.215.3 电子显微镜TG115.215.4 X射线显微镜TG115.215.5 离子显微镜TG115.215.6 超声显微镜TG115.215.7 微区分析仪TG115.215.9 其他显微分析仪器TG115.22 X射线分析TG115.221 X射线分析技术TG115.221.2 样品制备TG115.221.3 照相技术TG115.221.4 X射线线谱分析TG115.221.5 X射线结构分析TG115.222 X 射线分析应用TG115.222.1 晶粒测定TG115.222.2 应力测定TG115.222.3 相图分析、物相分析TG115.222.4 织构测定TG115.223 漫散射TG115.225 X 射线分析设备与仪器TG115.225.1 X 射线自动记录仪TG115.225.2 X 射线发生、控制装置TG115.225.3 单色器TG115.225.4 细聚焦TG115.23 射线衍射分析TG115.24 内耗分析TG115.25 热分析TG115.26 电分析TG115.27 磁性分析TG115.271 热磁分析、磁各向异性TG115.272 磁分析设备与仪器TG115.28 无损探伤TG115.281 X 射线探伤TG115.282 Υ射线探伤TG115.283 荧光探伤TG115.284 磁探伤TG115.285 超声波探伤TG115.286 同位素探伤TG115.3 化学试验法TG115.31 化学分析TG115.312 定性分析TG115.313 定量分析TG115.314 微量分析、痕量分析TG115.32 比色分析TG115.33 光谱分析TG115.331 光源TG115.332 近似光谱分析法TG115.333 准确光谱分析法TG115.334 极谱分析TG115.335 分光光度分析TG115.336 放射化学分析TG115.337 质谱分析TG115.338 气体分析TG115.339 光谱分析仪器TG115.5 机械性能(力学性能)试验TG115.51 硬度试验TG115.52 拉伸试验TG115.53 压缩试验TG115.54 弯曲试验TG115.55 扭转试验TG115.56 冲击试验TG115.57 疲劳与蠕变试验、断裂韧性试验TG115.58 摩擦及磨损试验TG115.59 光弹试验TG115.6 工艺性能试验TG115.61 淬透性试验TG115.62 焊接性试验TG115.63 切削加工试验TG115.65 铸造性能试验TG115.66 可锻性试验TG115.9 其他分析实验TG13 合金学与各种性质合金TG131 合金学理论TG132 特种物理性质合金TG132.1 特种膨胀性质合金TG132.11 低膨胀性质合金TG132.12 不膨胀性质合金TG132.2 特种电磁性质合金TG132.21 低电阻合金TG132.22 高电阻合金TG132.23 恒电阻合金TG132.24 热电元件用?辖?TG132.25 电真空合金TG132.26 超导合金TG132.27 特种磁性质合金TG132.271 软磁合金TG132.272 硬磁合金TG132.3 特种热性质合金TG132.31 低熔点合金TG132.32 高熔点合金、难熔合金、高温合金TG132.33 耐热合金TG132.5 特种光学性质合金TG132.6 特种声学性质合金TG133 特种化学性质合金TG133.1 自然合金TG133.2 还原性质合金、产生氢的合金TG133.3 无火花合金TG133.4 耐蚀合金TG135 特种机械性质合金TG135.1 高强度合金TG135.2 弹性合金TG135.3 超塑性合金TG135.4 高韧性合金TG135.5 硬质合金TG135.6 耐磨合金TG135.7 高消震合金TG136 特种工艺性质合金TG136.1 铸造合金TG136.2 可锻合金TG136.3 焊接合金TG136.4 切削合金TG139 其他特种性质合金TG139.4 抗辐照合金TG139.5 假合金TG139.6 形状记忆合金TG139.7 储氢合金TG139.8 非晶态合金TG14 金属材料TG141 黑色金属材料TG142 钢TG142.1 钢的组织与性能TG142.11 钢的组织TG142.12 钢的性能TG142.13 钢中杂质元素及微量元素对钢性能的影响TG142.14 钢的工艺性能TG142.15 钢的分析试验TG142.2 各种钢材:按组织区分TG142.21 珠光体钢TG142.22 莱氏体钢(共晶体钢)TG142.23 铁素体钢(铁氧体钢)TG142.24 马氏体钢(马丁钢)TG142.25 奥氏体钢TG142.3 各种钢材:按化学成分区分TG142.31 碳钢TG142.33 合金钢TG142.4 各种钢材:按用途区分TG142.41 结构钢TG142.45 工具钢TG142.7 特种性能钢TG142.71 不锈钢、耐酸钢TG142.72 耐磨钢TG142.73 耐热钢TG142.74 耐辐射用钢TG142.75 特殊弹性钢TG142.76 特殊膨胀性能的合金钢TG142.77 磁钢TG142.78 高电阻合金钢TG142.79 低温钢(耐寒钢)TG143 铸铁TG143.1 白口铁TG143.2 灰口铁TG143.3 变质铸铁(孕育铸铁)TG143.4 韧性铸铁(可锻铸铁)TG143.49 蠕虫状石墨铸铁TG143.5 球墨铸铁TG143.6 激冷铸铁TG143.7 高合金铸铁TG143.8 高强度合金铸铁TG143.9 其他铸铁TG144 铬及其合金TG145 锰及其合金TG146 有色金属及其合金TG146.1 重有色金属及其合金TG146.11 铜TG146.12 铅TG146.13 锌TG146.14 锡TG146.15 镍TG146.16 钴TG146.17 铋TG146.18 锑TG146.191 汞(水银)TG146.192 镉TG146.2 轻有色金属及其合金TG146.21 铝TG146.22 镁TG146.23 钛TG146.24 铍TG146.26 碱金属TG146.261 钾TG146.262 钠TG146.263 锂TG146.264 铷TG146.265 铯TG146.27 碱土金属TG146.271 钙TG146.272 锶TG146.273 钡TG146.3 贵金属、铂族金属及其合金TG146.31 金TG146.32 银TG146.33 铂(白金)TG146.34 铱TG146.35 锇TG146.36 钯TG146.37 铑TG146.38 钌TG146.39 其他贵金属、铂族金属TG146.4 稀有金属及其合金TG146.41 难熔稀有金属(高温熔融金属)TG146.411 钨TG146.412 钼TG146.413 钒TG146.414 锆、铪TG146.416 钽、铌TG146.418 铼TG146.43 稀散元素TG146.431 镓、铟、铊TG146.435 硒、碲TG146.45 稀土金属TG146.451 钪TG146.452 钇TG146.453 重稀土TG146.454 轻稀土TG146.8 放射性金属及其合金TG148 金属瓷材料TG15 热处理TG151 基础理论TG151.1 加热时的转变TG151.2 冷却时的转变TG151.3 奥氏体转变曲线TG154 热处理用材料TG154.1 氰化介质、氮共渗介质TG154.2 氮化介质TG154.3 碳化介质(剂)TG154.31 固体渗碳剂TG154.32 液体渗碳剂TG154.33 气体技TG154.4 淬火剂TG154.5 镀材料TG155 热处理机械与设备TG155.1热处理炉TG155.11 电阻炉TG155.12 气体加热炉TG155.13 盐炉TG155.14 保护气体炉TG155.15 油炉TG155.16 真空热处理炉TG155.17 流态粒子炉TG155.2 加热装置TG155.21 感应加热装置TG155.22 接触电热加热装置TG155.23 电解液加热装置TG155.24 感应器TG155.25 火焰表面加热装置TG155.26 热处理联合机、自动机TG155.3 淬火装置TG155.31 淬火槽TG155.32 淬火压床、淬火机、淬火感应器TG155.33 淬火用附件TG155.34 冷处理设备TG155.4 辅助设备TG155.41 清洗设备TG155.42 酸洗设备TG155.43 清理设备TG155.5 涂镀设备TG155.6 制造各种控制气体的设备TG155.7 化学热处理设备TG155.8 热处理检验设备TG155.91 热处理用仪表TG155.92 热处理自动化设备TG156 热处理工艺TG156.1 加热、保温与冷却TG156.2 退火TG156.21 控制金属组织转变的退火TG156.22 不同介质的退火TG156.23 消除应力退火TG156.24 轧制余热退火TG156.25 工件的退火TG156.26 退火的缺陷和防止TG156.27 退火质量检查TG156.3 淬火、表面淬火TG156.31 控制金属组织转变的淬火TG156.32 不同介质的淬火TG156.33 表面淬火TG156.34 工件的淬火TG156.35 淬火的缺陷和防止TG156.36 淬火质量检查TG156.4 正火TG156.5 回火TG156.6 调质、酸洗与精整TG156.7 电处理TG156.8 化学热处理TG156.81 渗碳TG156.82 渗氮、氰化、嫉采TG156.83 渗硅TG156.84 渗硫TG156.85 渗磷TG156.86 渗铝TG156.87 渗硼TG156.88 扩散渗铬TG156.9 特殊热处理TG156.91 冷处理TG156.92 时效处理TG156.93 形变热处理TG156.94 固溶处理、脱溶处理TG156.95 真空热处理TG156.96 超声波热处理TG156.97 磁场热处理TG156.98 氧化热处理TG156.99 其他热处理TG157 热处理质量检查、热处理缺陷及防止TG158 热处理车间TG161 钢的热处理TG162 钢件热处理TG162.1工具热处理TG162.2 刀具热处理TG162.21 提高耐用度方法TG162.22 车刀热处理TG162.23 钻头热处理TG162.24 铣刀热处理TG162.25 铰刀热处理TG162.26 丝锥热处理TG162.27 拉刀热处理TG162.28 圆板牙热处理TG162.29 其他刀具热处理TG162.4 模具热处理TG162.41 热锻压模具热处理TG162.42 冷锻压模具热处理TG162.43 冷冲模具热处理TG162.44 冷拉模具热处理TG162.5 量具热处理TG162.6 轧辊热处理TG162.7 机械零件热处理TG162.71 轴及轴承工件热处理TG162.73 齿轮热处理TG162.74 弹簧热处理TG162.75 杆件热处理TG162.79 其他零件热处理TG162.8 钢的成品及半成品热处理TG162.81 钢锭热处理TG162.82 钢轨热处理TG162.83 钢板热处理TG162.84 钢管热处理TG162.85 钢丝热处理TG162.86 带钢热处理TG162.9 铸钢热处理TG163 铸铁热处理TG164 各种铸铁热处理TG164.1 白口铸铁的可锻性热处理TG164.2 球墨铸铁热处理TG164.4 铁铸件的热处理TG166 有色金属及其合金的热处理TG166.2/.9 各种有色金属及其合金的热处理TG166.2 铜及其合金的热处理TG166.3 铝及其合金的热处理TG166.4 镁及其合金的热处理TG166.5 钛及其合金的热处理TG166.7 其他有色金属及其合金的热处理TG166.9 有色金属铸件的热处理TG17 金属腐蚀与保护、金属表面处理TG171 金属腐蚀理论TG172 各种类型的金属腐蚀TG172.1 辐射腐蚀TG172.2 接触腐蚀、缝隙腐蚀、摩擦腐蚀TG172.3 大气腐蚀、气体腐蚀TG172.31 工业大气腐蚀TG172.32 燃料气体腐蚀TG172.33 含硫气体腐蚀TG172.4 土壤腐蚀TG172.5 海水腐蚀、水腐蚀TG172.6 无机物腐蚀TG172.61 熔融金属腐蚀TG172.62 熔盐腐蚀TG172.63 酸、碱介质的腐蚀TG172.7 有机物腐蚀TG172.8 特殊状态的腐蚀TG172.81 高纯度水的腐蚀TG172.82 高温、高压下的腐蚀TG172.83 高压加氢的腐蚀TG172.84 杂散电流引起的腐蚀TG172.85 水中含砂的蚀损TG172.9 其他腐蚀TG174 腐蚀的控制与防护TG174.1 防蚀理论TG174.2 耐蚀材料TG174.21 材料的抗蚀性能TG174.22 金属耐蚀材料TG174.23 非金属耐蚀材料TG174.3 腐蚀试验及设备TG174.31 大气腐蚀试验及试验室腐蚀试验TG174.32 高度氧化腐蚀实验TG174.33 晶间腐蚀试验TG174.34 @透试验TG174.35 蠕变腐蚀试验TG174.36 电化学腐蚀试验TG174.37 腐蚀试验设备与仪器TG174.4 金属表面防护技术TG174.41 电化学保护TG174.42 金属防腐剂、缓蚀剂TG174.421 防锈切削液TG174.425 气相缓蚀剂TG174.426 油溶性缓蚀剂TG174.428 干燥剂TG174.43 水及蒸汽的防蚀处理方法TG174.44 金属复层保护TG174.441 电镀法TG174.442 喷镀法TG174.443 热浸法TG174.444 真空镀与气相镀法TG174.445 表面合金化(渗镀)TG174.446 色层、衬复TG174.45 无机物复层保护TG174.451 氧化法TG174.452 搪瓷复层TG174.453 陶瓷复层TG174.46 有机物复层保护TG174.461 涂漆TG174.462 硅漆TG174.463 橡胶复层TG174.464 塑料敷涂TG174.465 沥青绝缘层TG174.48 临时性封存保护材料TG174.481 油脂TG174.482 塑料TG174.483 充气TG174.484 内包装材料TG175 金属电抛光及化学抛光TG175.1 黑色金属及其合金TG175.3 有色金属及其合金TG176 金属表面精整TG177 金属着色TG178 各种金属及合金的腐蚀、防腐与表面处理TG179 各种工业的腐蚀及防腐新方法TG2 铸造TG21 铸造理论TG211 液态金属充型TG213 铸造应力、变形、裂纹及其防止TG214 金属液和铸型的相互作用TG22 铸造原材料及配制TG221 造型材料TG221.1 型(芯)砂主体材料及辅助材料TG221.2 型(芯)砂混合物TG222 砂箱、型芯、模型的材料TG223 熔化原料及添加物TG23 铸造机械设备TG231 造型材料制备机械TG231.1 起重运输设备TG231.2 型砂处理设备TG231.21 干燥设备TG231.22 辗式机TG231.23 松砂机TG231.3 破碎、磨碎设备TG231.4 分离设备TG231.5 旧砂再生设备TG231.6 造型、造芯设备TG231.61 手工造型机TG231.62 挤压造型(芯)机TG231.63 震击造型(芯)机TG231.64 抛砂机TG231.65 特殊造型机TG231.66 造芯机械TG231.7 落砂设备及出砂设备TG232 熔炼设备TG232.1 冲天炉TG232.2 转炉TG232.3 电炉TG232.4 反射炉TG232.5 坩埚炉TG232.6 真空炉TG232.7 附属设备TG233 铸造机械TG233.1 压力铸造机TG233.11 活塞式压铸机TG233.12 压缩空气式压铸机TG233.13 真空压铸机TG233.2 金属型铸造用机械TG233.3 离心铸造机TG233.4 壳型铸造机TG233.5 真空吸铸机TG233.6 连续、半连续铸造机TG233.7 熔模铸造用机械TG234 铸件落砂和清理设备TG234.1 去除浇口、冒口的设备TG234.2 去毛刺和校正用设备TG234.3 清理滚筒TG234.4 射丸.。
高精度圆柱滚子倒角磨削工艺
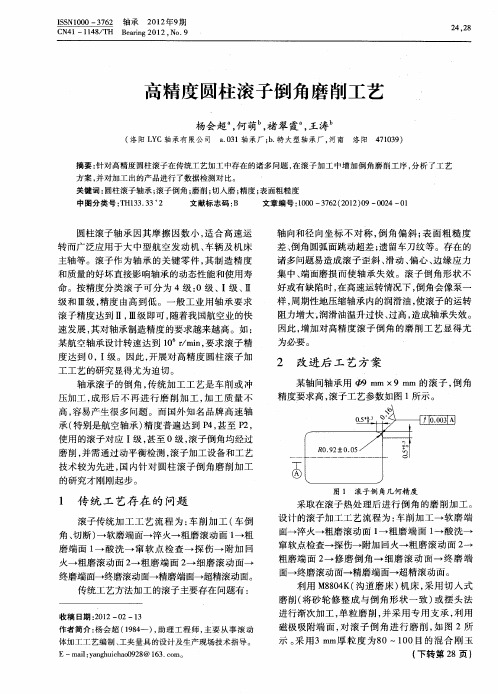
过修 改失稳 轴 承的侧 隙及 标 高 消 除 了油 膜振 荡 故
( 接第 2 上 4页 )
、
于圆弧倒 角 中心线 与水平 线成 4 0 角 的方 向 , 5夹 滚 子在压 轮带 动 下 匀 速 旋 转 一 周 , 千分 表 上 显 示 数
值 即为 倒角 圆弧对 基准 中心 圆跳 动 。 工 艺 改 进 前 、 检 测 数 据 对 比见 表 1 由 表 后 。
精度 要求 高 , 子工 艺参数 如 图 1所示 。 滚
轴承 滚子 的倒 角 , 统 加 工 工艺 是 车 削 或 冲 传
压加 工 , 形 后 不 再 进 行 磨 削 加 工 , 工 质 量 不 成 加
高, 容易 产生 很 多 问题 。而 国外 知 名 品牌 高 速 轴
承( 特别 是航 空轴 承 ) 度普 遍 达 到 P , 至 P 精 4甚 2,
滚 子传 统 加 工 工 艺 流 程 为 : 削 加 工 ( 倒 车 车
采 取在 滚子 热处 理 后 进 行倒 角 的磨 削 加 工 。
设 计 的滚子 加工 工艺 流 程 为 : 削 加工 一 软 磨 端 车
角 、 断 ) 软磨 端 面 淬 火一 粗磨 滚 动面 1 粗 切 一 一 磨 端 面 1 酸 洗 一 窜 软 点 检 查 一 探 伤一 附加 回 一 火 一 粗磨滚 动 面 2 粗磨 端 面 2 细磨 滚 动 面一 一 一 终 磨端面一 终磨滚动 面 精磨端面 超精 滚动面 。 传统工 艺 方法加 工 的滚子 主要存 在 问题有 :
示 。 用 3m 采 m厚 粒 度 为 8 0~1 0目的 混 合 刚 玉 0 94 ) 助理 工程 师 , 18 一 , 主要从 事 滚动 体加工 工艺编制 、 工夹量具 的设计及生产现场技术指导 。
高速切削加工技术
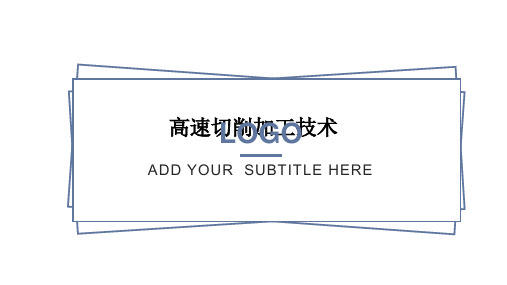
基本结构
进给机构 CNC控制 冷却系统
高速加工虽具有众多的优点,但由于技术复杂,且对于相关 技术要求较高,使其应用受到限制。
与高速加工密切相关的技术主要有:
○ 高速加工刀具与磨具制造技术; ○ 高速主轴单元制造技术; ○ 高速进给单元制造技术; ○ 高速加工在线检测与控制技术; ○ 其他:如高速加工毛坯制造技术,干切技术,高速加工的排屑技
术、安全防护技术等。
此外高速切削与磨削机理的研究,对于高速切削的发展也具 有重要意义。
高速切削 加工的关 键技术
高速主轴系统
高速主轴系统是高速切削技术最重要的关键技术之一。目前主 轴转速在15000-30000rpm的加工中心越来越普及,已经有转 速高达100000-150000rpm的加工中心。高速主轴由于转速 极高,主轴零件在离心力作用下产生振动和变形,高速运转摩 擦热和大功率内装电机产生的热会引起热变形和高温,所以必 须严格控制,为此对高速主轴提出如下性能要求:(1) 要求结 构紧凑、重量轻、惯性小、可避免振动和噪音和良好的起、停 性能;(2) 足够的刚性和高的回转精度;(3) 良好的热稳定性; (4) 大功率;(5) 先进的润滑和冷却系统;(6) 可靠的主轴监测 系统。
• 高速切削已成为当今制造业中一项快速发展的新技术,在工业发 达国家,高速切削正成为一种新的切削加工理念。
第 一 章 节 • 人们逐渐认识到高速切削是提高加工效率的关键技术。
高速切削的特点
随切削速度提高,单位时间内材料切除率增加,切削加工时间减 少,切削效率提高3~5倍。加工成本可降低20%-40%。
高速切削加工在国内的研究与应用
高速切削加工在国内的研究与 应用
20世纪90年代后,我们先后相继研究了模具高速切削加工技术与策 略、涂层刀具与PCBN刀具和陶瓷刀具等高速切削铸铁和钢的切削力、 刀具磨损寿命、加工表面粗糙度以及高速切削数据库技术等。
高速切削技术
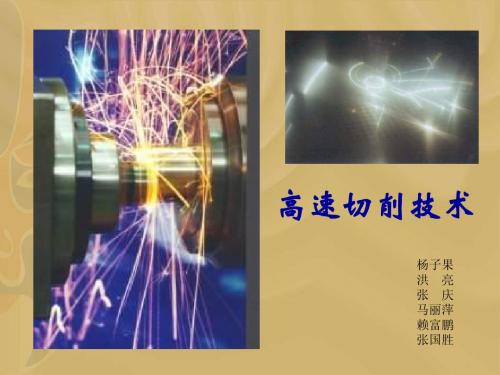
高速切削技术
目前研究内容
高速切削 刀具状态 监控及工 况监测技 术 加工误差 综合动态 补偿技术 研究。
高速切削机理研 究,尤其是模具 钢等难加工材料 高速切削机理研 究。
研究 内容
干式( 准干 式)切削技 术研究。
高速切削 工艺数据 库
高速切削 刀具系列 化、标准 化研究。
高速切削技术
存在差距因素
高速切削技术 高速切削的优势
可加工难加工材料 难加工材料如高锰钢、淬硬钢、奥氏体不锈钢、复合材 料和耐磨铸铁等切削加工切削效率低,刀具寿命短。高速切 削时,切削力小,切屑变形阻力小,刀具磨损小,故可加工 一些难加工材料。 高速干切削可以实现加工过程绿色制造 高速干切削就是切削加工过程中不使用任何切削液工艺 方法,是对传统切削方式一种技术创新。它相湿切削而言, 是一种从源头上控制污染绿色切削和清洁制造工艺,它消切 削液使用对外部系统造成负面影响。目前,能实现高速干切 削工件材料有铸铁、铝合金、滚动轴承钢等。
高速切削技术
高速切削发展现状 国外
德国Darm st adt工业大学PTW所以舒尔茨教授为核心的科研小 组和日本京都大学工学研究科以垣野教授为核心的课题组均已制 出商品化的高速切削机床,在德国和日本的企业界,都分别享有较 高的声誉。 舒尔茨教授在德国政府强有力的资助下,联合18家企业,共同攻 关,从1984年到1989年,完成高速切削机床各相关硬件与软件的开 发,研究水平超过了当时居领先地位的美国。1993年,直线电机的 出现拉开了高速进给的序幕, 从而也使高速切削技术走向成熟应 用阶段。目前,PTW所研制的高速机床已在德国许多企业里应用。 垣野教授联合9家企业,于1996年研制出日本第一台商品化卧式 高速切削加工中心,该加工中心主轴转速30000r/min,最大进给速 度80m/min,加速度为2g,重复定位精度±1Lm。目前,垣野研究室研 究成果在日本企业界甚至在国际上均产生重大影响。
《高速切削加工》课件

03 高速切削加工的关键技术
高速切削加工的刀具技术
刀具材料
01
高速切削加工需要使用高硬度、高耐磨性的刀具材料,如硬质
合金、陶瓷和金刚石等。
刀具涂层技术
02
涂层技术能够提高刀具表面的硬度和耐磨性,降低摩擦系数,
提高切削效率。
刀具几何形状
03
高速切削加工需要采用特殊的刀具几何形状,如小前角、大后
角和短刀刃等,以减小切削力、切削热和刀具磨损。
在高速切削加工中,降低能耗、减少废弃 物排放和提高资源利用效率成为重要的发 展趋势,符合可持续发展的要求。
高速切削加工面临的挑战与对策
高温与热变形
高速切削加工过程中产生的高温可能导致 刀具磨损、工件热变形等问题,需采用新 型刀具材料、强化冷却技术等手段解决。
振动与稳定性
高速切削加工过程中的振动可能影响加工 精度和表面质量,应优化机床结构、提高 刚性和阻尼性能。
模具型腔加工
高速切削加工技术在模具制造业 中广泛应用于模具型腔的加工, 如注塑模、压铸模等,能够快速 准确地完成复杂型面的加工。
模具钢材料加工
高速切削加工技术能够高效地加 工各种模具钢材料,如H13、 SKD61等,提高加工效率,减少 热量的产生和材料的变形。
高速切削加工在航空航天制造业的应用
航空发动机制造
高速切削加工的工艺参数
1 2 3
切削速度
提高切削速度可以提高加工效率,但同时也需要 选择合适的刀具和材料,以避免刀具磨损和工件 热变形。
进给速度
进给速度的提高可以增加材料去除率,但过高的 进给速度可能导致刀具磨损和工件表面质量下降 。
切削深度
适当的切削深度可以提高加工效率,但过大的切 削深度可能导致刀具磨损和工件表面质量下降。
高速铣削切削力与温度的分析
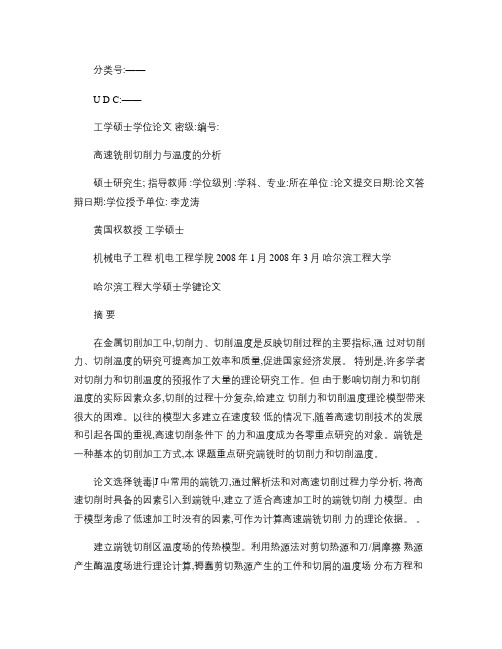
分类号:——U D C:——工学硕士学位论文密级:编号:高速铣削切削力与温度的分析硕士研究生; 指导教师 :学位级别 :学科、专业:所在单位 :论文提交日期:论文答辩日期:学位授予单位: 李龙涛黄国权教授工学硕士机械电子工程机电工程学院 2008年1月 2008年3月哈尔滨工程大学哈尔滨工程大学硕士学键论文摘要在金属切削加工中,切削力、切削温度是反映切削过程的主要指标,通过对切削力、切削温度的研究可提高加工效率和质量,促进国家经济发展。
特别是,许多学者对切削力和切削温度的预报作了大量的理论研究工作。
但由于影响切削力和切削温度的实际因素众多,切削的过程十分复杂,给建立切削力和切削温度理论模型带来很大的困难。
以往的模型大多建立在速度较低的情况下,随着高速切削技术的发展和引起各国的重视,高速切削条件下的力和温度成为各零重点研究的对象。
端铣是一种基本的切削加工方式,本课题重点研究端铣时的切削力和切削温度。
论文选择铣毒|J中常用的端铣刀,通过解析法和对高速切削过程力学分析, 将高速切削时具备的因素引入到端铣中,建立了适合高速加工时的端铣切削力模型。
由于模型考虑了低速加工时没有的因素,可作为计算高速端铣切削力的理论依据。
建立端铣切削区温度场的传热模型。
利用热源法对剪切热源和刀/屑摩擦熟源产生酶温度场进行理论计算,褥蠢剪切熟源产生的工件和切屑的温度场分布方程和刀/屑摩擦热源产生的刀具和切屑的温度场分布方程;并得出了二者共同作用下刀具和切属的温度场分布方程,进而将此方程弓l入到端铣中褥到端铣切削温度场模型。
由于热源法可得出最简单形式的解答,计算结果和实际结果比较接近,因此褥出的端铣切削温度场模型可作为计算端铣切削温度的理论依据。
应用弹塑性力学讨论了切削变形区的弹、塑性阶段的应力、应变状态和材料进入塑性状态的属服准则、强化准裂及应力与应变的关系。
为有限元分析做了充分准备。
采用有限元软俸ANSYS对金属切削过程进行了仿真,对应力、应交及前刀面摩擦状况等仿真结果进行了分析并将仿真结果与金属切削中的规律进行比较。
高速加工技术

21
3.7.2 高速加工机床与刀具
聚晶立方氮化硼(PCBN/Polycrystalline Cubic Boron Nitride) 1970年问世 ◆ PCBN切削性能 较高的硬度和耐磨性: CBN 晶体结构与金刚石相 似,化学键类型相同,晶 格常数相近。 CBN 粉末硬 度 HV8000 , PCBN 硬 度 3000-5000。切削耐磨材料 时,其耐磨性为硬质合金 刀具的 50 倍,涂层硬质合 金刀具的 30 倍,陶瓷刀具 的25倍。
陶瓷球轴承
陶瓷球轴承 冷却水出口
旋转变压器
冷却水入口 陶瓷轴承高速主轴
郭德伟
8
3.7.2 高速加工机床与刀具
磁浮轴承主轴结构
前径向轴承 电主轴 后径向轴承 双面轴向 推力轴承
前辅助轴承
后辅助轴承
前径向传感器
后径向传感器 轴向传感器 图3-48 磁浮轴承高速主轴
郭德伟
12
3.7.2 高速加工机床与刀具
最高 最高 高精度 Ra=0.1-0.05 IT5-6 硬质合金\铜\ 铝有色金属及 其合金\陶瓷 等高硬度材料
一般钢 材、铸 铁粗、 精加工
17
3.7.2 高速加工机床与刀具
碳原子 氮原子 硼原子
图3-36 金刚石(左)与CBN(右)原子结构 金刚石与 CBN 晶体结构相似,每一个原子都以理想四面体方式以 109°28′键角与邻近4个原子结合。金刚石中的每个C原子都以共价键 方式与邻近4个C原子结合。CBN中每个N原子与4个B原子结合,每个 B原子又与4个N原子结合,并存在少数离子键。
硬度/HV 5000 4000 3000 BN20 2000 1000 0 0 硬质合金 200 400 600 800 1000 温度/℃ 陶瓷
高速切削切屑形态及切削力研究
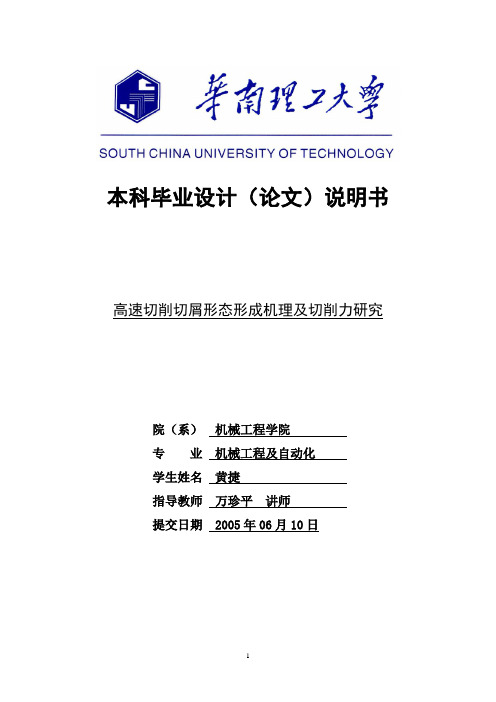
本科毕业设计(论文)说明书高速切削切屑形态形成机理及切削力研究院(系)机械工程学院专业机械工程及自动化学生姓名黄捷指导教师万珍平讲师提交日期 2005年06月10日华南理工大学毕业设计(论文)任务书兹发给01机械4 班学生黄捷毕业设计(论文)任务书,内容如下:1.毕业设计(论文)题目:高速切削切屑形成机理及切削力研究2.应完成的项目:(1)对高速切削切削力与切削速度关系进行研究(2)对切屑形态和切削热与切削速度关系进行研究(3)对切削力、切削温度和切屑形态的综合研究(4)对高速切削加工表面粗糙度进行研究3.参考资料以及说明:(1)艾兴等,高速切削加工技术,国防工业出版社,2003年10月第1版(2)曾志新等,机械制造技术基础,武汉理工大学出版社,2001年7月第1版(3)Serope Kalpakjian, Steven R. Schmid, Manufacturing Engineering andTechnology—Machining, 机械工业出版社,2004年3月第1版(4)(5)(6)4.本毕业设计(论文)任务书于2005年03月01日发出,应于2005年06月10日前完成,然后提交毕业考试委员会进行答辩。
专业教研组(系)、研究所负责人审核年月日指导教师签发年月日毕业设计(论文)评语:毕业设计(论文)总评成绩:毕业设计(论文)答辩负责人签字:年月日摘要高速切削是实现高效率制造的核心技术。
工序的集约化和设备的通用化使之具有很高的生产效率。
根据机加工实践所知,在不同的情况下,包括工件材料不同、刀具类型不同、刀具特性不同、机床特性不同、转速不同、进给量不同、切削深度不同等等,都会造成切屑形态的不同。
在高速切削加工过程中,切削速度、切削深度和进给量的不同都会造成切屑的形态有所不同。
本实验对①相同切削深度和相同进给量,②相同切削深度和不同进给量,③相同进给量和不同切削深度三种情况下,对切削力、切削温度和切屑形态随切削速度变化的规律作了不同的研究探讨,同时本实验也研究了各种情况下工件已加工表面粗糙度与切削速度之间的关系。
高速切削加工技术的现状和发展
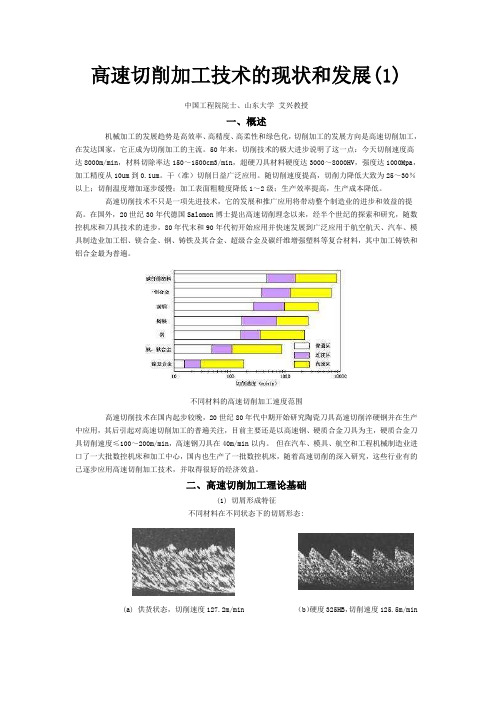
高速切削加工技术的现状和发展(1)中国工程院院士、山东大学艾兴教授一、概述机械加工的发展趋势是高效率、高精度、高柔性和绿色化,切削加工的发展方向是高速切削加工,在发达国家,它正成为切削加工的主流。
50年来,切削技术的极大进步说明了这一点:今天切削速度高达8000m/min,材料切除率达150~1500cm3/min,超硬刀具材料硬度达3000~8000HV,强度达1000Mpa,加工精度从10um到0.1um。
干(准)切削日益广泛应用。
随切削速度提高,切削力降低大致为25~30%以上;切削温度增加逐步缓慢;加工表面粗糙度降低1~2级;生产效率提高,生产成本降低。
高速切削技术不只是一项先进技术,它的发展和推广应用将带动整个制造业的进步和效益的提高。
在国外,20世纪30年代德国Salomon博士提出高速切削理念以来,经半个世纪的探索和研究,随数控机床和刀具技术的进步,80年代末和90年代初开始应用并快速发展到广泛应用于航空航天、汽车、模具制造业加工铝、镁合金、钢、铸铁及其合金、超级合金及碳纤维增强塑料等复合材料,其中加工铸铁和铝合金最为普遍。
不同材料的高速切削加工速度范围高速切削技术在国内起步较晚,20世纪80年代中期开始研究陶瓷刀具高速切削淬硬钢并在生产中应用,其后引起对高速切削加工的普遍关注,目前主要还是以高速钢、硬质合金刀具为主,硬质合金刀具切削速度≤100~200m/min,高速钢刀具在40m/min以内。
但在汽车、模具、航空和工程机械制造业进口了一大批数控机床和加工中心,国内也生产了一批数控机床,随着高速切削的深入研究,这些行业有的已逐步应用高速切削加工技术,并取得很好的经济效益。
二、高速切削加工理论基础(1) 切屑形成特征不同材料在不同状态下的切屑形态:(a) 供货状态,切削速度127.2m/min (b)硬度325HB,切削速度125.5m/min连续带状切屑(D.LEE)锯齿状切屑(c)硬度325HB,切削速度250m/min锯齿状切屑(d)硬度325HB,切削速度2600m/min即将分离的锯齿状切屑高速切削不同状态AISI4340钢(40CrNiMoA)时的切屑形态(纵截面微观照片)((b)、(c)、(d)从komarduri)切削渗碳淬硬20CrMnTi钢(HRC60~62)在100~110m/min时的切屑形貌工件材料及其性能和切削条件对切屑形态起主要作用,其中工件材料及其性能有决定性的影响。
精密与特种加工(第1讲)
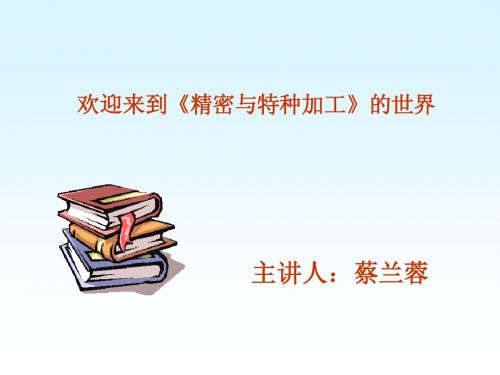
教学计划:
课堂授课:24学时 实验教学:8学时
教学大纲:
特种加工技术:30学时 精密切削磨削技术:2学时
请你认真思考以下产品的加工方法!
请你认真思考以下产品的加工方法!
请你认真思考以下产品的加工方法!
请你认真思考以下产品的加工方法!
请你认真思考以下产品的加工方法!
雕刻的水晶作品
请你认真思考以下产品的加工方法!
1-工件 2-脉冲电源 3-自动进给调节装置 4-工具 5-工作液 6-过滤器 7-工作液泵 8-被蚀除的材料
一、电火花加工的原理和设备组成
4.工作原理:
1)工具和工件与电源的两极相接,均浸在 有一定绝缘度的流体介质(通常用煤油或 矿物油)中。 2)脉冲电压加到两极之间,在工具电极向 工件电极运动中,将极间最近点的液体介 质击穿,形成火花放电。 3)由于放电通道截面积很小,通道中的瞬 时高温使材料熔化和气化。单个脉冲能使 工件表面形成微小凹坑,而无数个脉冲的 积累将工件上的高点逐渐熔蚀。 4)随着工具电极不断地向工件作进给运动, 工具电极的形状便被复制在工件上。 5)加工过程中所产生的金属微粒,则被流 动的工作液流带走。 6)总能量的一小部分也释放到工具电极上 形成一定的工具损耗。
第三节 特种加工对材料可加工性和结构性的影响
提高了材料的加工性
材料的加工性不再与硬度、强度 等成直接、比例关系。
第三节 特种加工对材料可加工性和结构性的影响
改变了零件的典型工艺路线
成形加工 淬 淬
火
火
成形加工
第三节 特种加工对材料可加工性和结构性的影响
对产品零件的结构设计带来很大影响
雕刻的水晶作品
高速切削加工技术
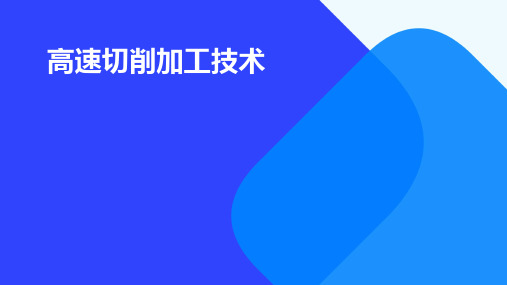
在通用机械制造业中,高速切 削加工技术广泛应用于机床、 泵阀、压缩机和液压传动装置 等产品的制造。
05
高速切削加工技术的发 展趋势与挑战
高效稳定的高速切削技术
高效稳定的高速切削技术是未来发展 的关键,需要不断提高切削速度和加 工效率,同时保持加工过程的稳定性 和可靠性。
高效稳定的切削技术还需要不断优化 切削参数和刀具设计,以适应不同材 料和加工需求的挑战。
高速切削工艺技术
切削参数选择
根据不同的加工材料和切削条件, 选择合适的切削速度、进给速度 和切削深度等参数,以实现高效
切削和高质量加工。
切削液使用
合理选用切削液,如乳化液、极 压切削油等,以提高切削效率和 工件表面质量,同时减少刀具磨
损和热量产生。
加工路径规划
采用合理的加工路径和顺序,以 减少空行程和换刀次数,提高加
高效稳定的切削技术需要解决切削过 程中的振动和热变形问题,提高加工 精度和表面质量。
高性能刀具材料的研发
高性能刀具材料是实现高速切削 的关键因素之一,需要具备高硬 度、高强度、高耐磨性和良好的
抗热震性等特点。
研发新型高性能刀具材料,如超 硬材料、陶瓷材料等,能够提高 切削速度和加工效率,同时减少
刀具磨损和破损。
改善加工质量
01
高速切削加工技术能够减少切削 力,降低切削热,从而减小了工 件的热变形和残余应力,提高了 加工精度和表面质量。
02
由于切削力减小,工件不易产生 振动,减少了振纹和表面粗糙度 ,进一步提高了加工质量。
降低加工成本
高速切削加工技术能够显著提高加工效率,缩短了加工周期,从而降低了单件成 本。
高速切削加工技术
目 录
• 高速切削加工技术概述 • 高速切削加工技术的优势 • 高速切削加工的关键技术 • 高速切削加工的实践应用 • 高速切削加工技术的发展趋势与挑战 • 高速切削加工技术的未来展望
旋转超声振动铣削Cr12MoV轴向切削力与表面粗糙度研究

Cr12MoV模具钢具有硬度高、耐磨性和淬透性 好等优点,在汽车制造、轮船制造、航空、机电产品 制造及家用电器等行业中占有重要地位叫常被用 于制造形状较大、承受较大工作负载的各种工具和 模具叫 然而,由于Cr12MoV模具钢切削加工困难,
收稿日期:2021-01-01 第一作者简介:安强,男,1997年生,硕士研究生。
减小,当切削宽度大于2 mm时,切削力增大,但仍 低于切削宽度为1-5 mm时的切削力。
表4轴向平均切削力极差分析结果&!/(r-min"1)
y/mm
Op/mm
o/mm
&1
10.3
16.436
13.14
16.01
&2
15.4
17.916
14.03
17.69
&3
20.45
17.332
16.394
20.05
表面粗糙度%#!m
0.659 0.471 0.478 1.366 1.495 0.552 0.472 1.13 1.297 0.491 0.466 0.687 0.453 0.461 0.547 0.62 0.538 0.544 0.787 0.338 0.433 0.452 0.417 0.586 0.471
《电加工与模具>2021年第3期
超声加工及其他特种加工
旋转超声振动铳削Crl2MoV轴向 切削力与表面粗糙度研究
安强1,靳伍银1,周志楷2
(1.兰州理工大学机电工程学院,甘肃兰州730050; 2.中国铁建重工集团股份有限公司,湖南长沙410100 )
摘要:为研究切削参数对切削效果的影响,将旋转超声振动铣削引入Cr12MoV模具钢铣削过 程中;通过正交试验设计开展切削试验,从轴向平均切削力和表面粗糙度两方面研究了旋转超声 振动铣削参数选择对Cr12MoV模具钢加工的影响#结果表明:在旋转超声振动辅助铣削Cr12MoV 模具钢的过程中,主轴转速和切削深度对轴向平均切削力和表面粗糙度影响最大;在主轴转速 2000 r/min%切削深度0.6 mm时,可获得较小的轴向平均切削力和较好的表面粗糙度;将旋转超声 振动应用到Cr12MoV模具钢铣削过程中,能获得较好的加工效果#
高速加工技术93.pptx

静压轴承工作原理
第47页/共99页
静压轴承对轴颈圆度误差的均化作用
第48页/共99页
静压轴系特点
轴承间隙内介质压强由外部供给,忽略主轴旋转时的动 压效应,承载能力不受主轴转速的影响,实现任何转速 下液/气体摩擦,具有设计所需的承载能力;适应性好, 寿命长
主轴浮起后是纯液/气体摩擦,起动摩擦阻力小,主轴 旋转后轴线偏移量比轴颈轴套的加工误差小得多
高速加工在汽车工业中的应用
1
2
3
4
钻孔 表面倒棱 内侧倒棱 铰孔 高速钻孔 表面和内侧倒棱
专用机床
高速加工中心
5轴×4工序 = 20轴(3万件/月)
1台1轴1工序(3万件/月)
刚性(零件、孔数、孔径、孔 型固定不变)
柔性(零件、孔数、孔径 、孔型可变)
汽车轮毂螺栓孔高第速24页加/共工99页实例(日产公司)
和工件受力均小。切削速度高,吃刀量很小, 剪切变形区窄,变形系数ξ减小,切削力降低 大概30%-90% • 刀具和工件受热影响小。切削产生的热量大部 分被高速流出的切屑所带走,故工件和刀具热 变形小,有效地提高了加工精度 • 刀具寿命长(高速切削刀具)。刀具受力小, 受热影响小,破损的机率很小,磨损慢
后径向传感器 轴向传感器 磁浮第轴53承页/高共9速9页主轴
磁悬浮轴承电主轴
高频电动机
磁悬浮轴承
松刀用液压装置
HSK-E刀柄
磁悬浮轴承
水套冷却
瑞士IBGA公司的磁悬浮电主轴
第54页/共99页
磁浮轴承电主轴特点
➢主轴由两个径向和两个轴向磁浮轴承支承,磁 浮轴承定子与转子间空隙约0.1mm。
第8页/共99页
德国 ROEDERS,42000rpm,适 合如手机模具加工
高速切削技术及其刀具
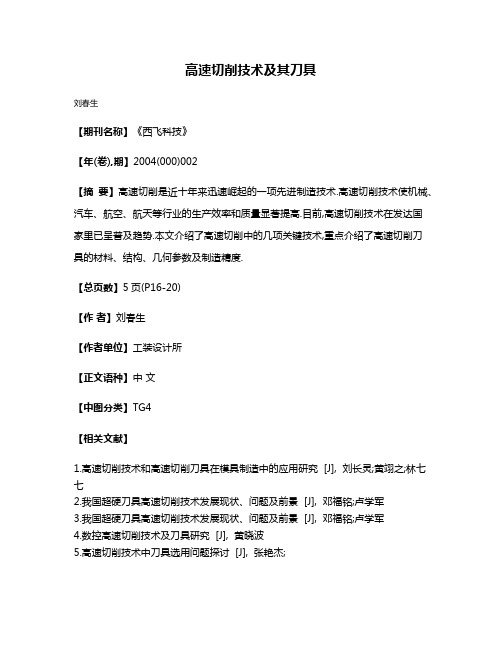
高速切削技术及其刀具
刘春生
【期刊名称】《西飞科技》
【年(卷),期】2004(000)002
【摘要】高速切削是近十年来迅速崛起的一项先进制造技术.高速切削技术使机械、汽车、航空、航天等行业的生产效率和质量显著提高.目前,高速切削技术在发达国
家里已呈普及趋势.本文介绍了高速切削中的几项关键技术,重点介绍了高速切削刀
具的材料、结构、几何参数及制造精度.
【总页数】5页(P16-20)
【作者】刘春生
【作者单位】工装设计所
【正文语种】中文
【中图分类】TG4
【相关文献】
1.高速切削技术和高速切削刀具在模具制造中的应用研究 [J], 刘长灵;黄翊之;林七七
2.我国超硬刀具高速切削技术发展现状、问题及前景 [J], 邓福铭;卢学军
3.我国超硬刀具高速切削技术发展现状、问题及前景 [J], 邓福铭;卢学军
4.数控高速切削技术及刀具研究 [J], 黄晓波
5.高速切削技术中刀具选用问题探讨 [J], 张艳杰;
因版权原因,仅展示原文概要,查看原文内容请购买。
- 1、下载文档前请自行甄别文档内容的完整性,平台不提供额外的编辑、内容补充、找答案等附加服务。
- 2、"仅部分预览"的文档,不可在线预览部分如存在完整性等问题,可反馈申请退款(可完整预览的文档不适用该条件!)。
- 3、如文档侵犯您的权益,请联系客服反馈,我们会尽快为您处理(人工客服工作时间:9:00-18:30)。
4
2
0
2
(3)
此即为麦钱特剪切角公式。但过去的麦钱特公式是在低的切削速度下按最小能量原理 推导的,而式(3)是根据能量平衡原理推导的,它适合于任何切削速度情况,式 (3)给出了剪切角Φ与摩擦角β 以及γ 0 的关系。 随着切削速度的提高,会使金属流动的速度大于塑性形变的速度,及形变区尚未形 成,切削过程已经完成。这意味着此时第一变形区后移,使剪切角增大。同时切削速 度 v 对刀具前刀面上的平均摩擦系数μ 也有影响,在高速区,v 增大切削温度提高,摩 擦系数减小,则摩擦角β (β =arctgμ )减小,由式(3)可见,剪切角Φ增大。所以切 削速度提高导致剪切角增大,有式(1)可见,剪切角增大会使剪切力降低。由式 (2)可知,剪切角增大会使切屑惯性力增加,切削速度本身也使惯性力增加,也就是 说,切削速度提高,会使剪切力降低,而使切屑惯性力增加,可见,切削速度对切削 力的影响复杂,是上述两种作用的综合结果。总过大量实验总结,剪切角Φ增大,导 致剪切力减小的幅度较大;由于切屑质量很小,虽然切削速度提高,导致切屑惯性力 增大,但其增加幅度比剪切力幅度小很多,故在高速切削范围内,切削速度的提高最 终导致切削力的降低。
R1
1 a 1 1.33 1 vac
(6)
式中,a1 为工件材料导热系数,ε 为剪应变。由式(6)知,随 v 与 ac 增大,R1 增 加,但 v 的变化范围比 ac 大,所以 v 对 R1 的影响更大,也就是说,随 v 提高,剪切 面上产生的热量流入切屑的比例 R1 增大,即切削速度越高,被切屑带走的热量越多, 切屑温度升高,而刀具温度升高少。 高速切削实验也表明,随切削速度的提高,开始切削温度升高很快,但达到一定速 度后,切削温度的身高逐渐缓慢,甚至很少升高。
0 引言
高速加工这一概念起源于二战前,但其真正开始发展是上世纪七十年代末。高速加 工技术的出现大大提高了机械加工的生产效率,并逐渐成为实现柔性制造,以满足人 们对产品多样化,个性化越来越高的要求。 由于高速加工特别适合于加工大切除率的薄壁件,所以它在航天航空等对零件轻量 化要求很高的领域有着十分重要的意义。以往上百个零件经焊接组成的部件,现在可 由毛坯一次加工成形,大大缩短了零件的生产周期[1]。 随着对刀具材料的突破,主轴转速的不断提升,高速加工技术仍有着广阔的发展潜 力,并逐渐取代传统加工。可以毫不夸张的说,在将来,高速加工技术将成为一个国 家制造业水平,甚至工业水平的一个重要指标。
1.2.2 切削速度对切削热的影响
高速切削时,总的切削功 W 消耗在以下几个方面: 1 形成以加工表面和切屑底面两个新生表面所需要的能量 Wn
其值等于物体该表面的表面能。切削单位体积材料的表面能 Wn 大致为 0.02N·cm。 与切削时消耗的总能量成正比,实际上是很小的,它成为工件和切屑增加的内能。 2 剪切区德剪切形变共 Ws 3 前、后刀面与切屑、工件的摩擦功 Wf 4 切削层材料经过剪切面时,由于动量改变而消耗的功 Wm 剪切变形功 Ws 和动量改变所消耗的功 Wm 大部分将变为剪切变形区(第一变形 区)的热量 Eq1,一小部分形成两个新生表面的表面能以内能形式储存于加工表面和 切屑中。前、后刀面的摩擦功 Wf 全部将变为第二、三形变区的热量 Eq2 和 Eq3。因 此,单位时间内产生的总热量 Eq 为:
图 2 萨洛蒙曲线
2.3 超高速加工技术的发展
超高速加工技术的发展历史并不长,所以它仍是一门新兴的技术[5]。 1931 年,德国物理学家卡尔·萨洛蒙用大直径圆锯片进行了超高速切削模拟实验, 提出了超高速加工的概念。 1977 年,美国第一次在数控铣床上实现了超高速切削。当时进行了主轴转速为 18000r/min、30000r/min、100000r/min 三组超高速切削实验[6]。 自上世纪八十年代中后期以来,商品化的超高速切削机床不断出现,超高速机床从 单一的超高速铣床发展成为超高速车铣床、钻铣床乃至各种高速加工中心等。 目前,超高速加工在不断提速的同时,正和数控领域结合。我国目前研制的超高速 加工机床主轴最高转速仍处于 10000r/min,与国外先进水平存在较大差距。
关键词: 高速切削; 加工技术; 超高速加工
High Speed Machining Technology
Huang Dongping (University of Shanghai for Science and Technology Mechanical Engineering College Shanghai)
2.1 萨洛蒙超高速切削模拟实验
对于超高速加工的研究,起源于上世纪 30 年代,当时德国的切削物理学家卡尔·萨 洛蒙博士进行了一项研究。由于当时技术条件的限制,萨洛蒙采用加装了锯齿的大直 径圆锯片对铜等非铁金属进行了超高速切削的模拟实验,并提出了著名的萨洛蒙曲 线。在图中,实线是萨洛蒙真正做过的实验,另外的曲线是经过推测得出的。
Fs Ss Ac / sin
Fm Ac v 2 cos 0 / cos( 0 )
具前角,Φ是剪切角。
(1) (2)
式中:Ss 为工件材料动态剪切强度,Ac 为切削层截面积,ρ 是工件材料密度,γ 0 为刀 由式(1)与(2)可见,如果工件材料、切削面积 Ac 和刀具前角γ 0 一定,剪切力 Fs 和切屑惯性力 Fm 主要由剪切角Φ而定,而剪切角又受切削速度的影响。切削速度 低时,与剪切力 Fs 相比,切屑惯性力 Fm 很小,可视为零。 考虑切削速度的影响,按功率平衡原理,可以建立以下剪切角关系式:
1 高速切削加工
高速切削加工技术是指采用超硬材料的刃具,通过极大的提高切削速度和进给速度 来提升材料切除率,加工精度和加工质量的现代加工技术。 以切削速度和进给速度来界定:高速加工的切削速度和进给速度为普通切削的 5~10 倍[2]。 以主轴转速界定:高速加工的主轴转速大于等于 10000r/min。
EQ EQ1 EQ 2 EQ3
(4)
设单位时间内单位面积上在剪切面、前刀面和后刀面上产生的热量分别为 q1,q2 和 q3,而剪切面、前刀面——切屑、后刀面——工件接触面积分别为 A1,A2 和 A3。则:
EQ q1 A1 q2 A2 q3 A3
(5)
剪切面上产生的热量大部分传给切屑,一部分传入工件。设前一部分的比例为 R1, 于是单位时间传入切屑的热量为 R1q1acawcscΦ,单位时间传入工件的热量为(1-R1) q1acawcscΦ,其中 ac 为切削厚度,aw 为切削宽度。 剪切面上产生的热量流入切屑的比例 R1 为:
图 1 Salomon 切削模拟实验
2.2 萨洛蒙曲线
从萨洛蒙曲线中,我们可以看出: 1. 不同的材料,随着切削速度的提高,切削温度的变化不同。 2. 在常规切削速度范围内,切削温度随着切削速度的增加而增高,但当切削速度 到达某个峰值时,切削速度再提高,切削温度反而下降。 萨洛蒙曲线的意义在于,它预言了一个不可切削区的存在。当切削速度到达一定值 时,切削过程产生的热量将超过刀具的耐受极限,使切削无法继续。而将主轴转速 极大提升,又能使切削温度回到材料可加工的范围内。 由于当时实验条件的限制,无法论证萨洛蒙理论的正确性,所以萨洛蒙的发现在 当时并未受到人们的重视。之后,由于战争的缘故,当年的实验数据全部丢失,所 以也无法考证实验的正确性。另外,人们对于当年的测温技术也存在疑问,所以实 验数据的可信度也存在争议。直到 1977 年,美国第一次实现了超高速铣削,超高 速加工加工是相对于高速加工而言的,对此国内外学者没有一个统一的界定速度。 一般,国外学者认为:机床主轴转速 8000~12000r/min 为准高速切削, 15000~50000r/min 为高速切削,大于 50000r/min 就认为是超高速切削。而国内学者 认为:超高速加工是一种比常规切削速度高得多(10 倍左右)的速度对零件进行加工 的先进技术[4]。
高速切削加工技术
黄冬平 (上海理工大学机械工程学院 上海)
摘要
高速加工技术是近 30 年来急速发展的一门新兴技术,相对于普通加工,高速加工 有着高效率,高质量,生产周期短等一系列的优势。同时,主轴转速的提升改变了切 削的机理,所以高速加工能完成普通加工所不能实现的加工要求。因此,高速加工技 术对工业领域有着极其重要的意义。 本文将从高速加工的概念,原理,发展过程,应用领域及关键技术等方面介绍这一 加工技术。从中探讨高速加工与普通加工的区别,并说明高速加工技术在机械制造业 的价值和作用。
Abstract
High-speed machining technology is a new technology, which in recent 30 years of rapid developed. As opposed to ordinary processing, high-speed machining shows a series of advantages like high efficiency, high quality, short production cycle and so on. At the same time, with the enhancement of the spindle speed changes the cutting mechanism, so high-speed processing can complete the requirements, that ordinary machining processing can hardly achieve. Therefore, high-speed machining technology has an extremely important significance in industry. This article will introduce the high-speed machining in these aspects, the concept of this processing technology, principles, development, application areas and key technologies. In order to explore the difference between the high-speed machining and general machining, and explain the value and role of the high-speed processing technology in machinery manufacturing. Key Words: High-speed cutting; Machining technology; Ultra-rapid machining