热轧钢铁材料新一代TMCP技术
新一代控制轧制和控制冷却技术与创新的热轧过程

新一代控制轧制和控制冷却技术与创新的热轧过程王国栋作者单位:文摘:针对传统控制轧制控制冷却(TMCP)技术存在的问题,提出了以超快冷为核心的新一代的TMCP 技术,并详述了作为实现新一代TMCP 技术核心手段的超快冷技术的科学内涵和工业装备开发情况。
关键词:钢;热轧;新一代控制轧制和控制冷却;超快冷;强化东北大学王国栋摘要:针对传统控制轧制控制冷却(TMCP)技术存在的问题,提出了以超快冷为核心的新一代的TMCP 技术,并详述了作为实现新一代TMCP 技术核心手段的超快冷技术的科学内涵和工业装备开发情况。
关键词:钢;热轧;新一代控制轧制和控制冷却;超快冷;强化New generation TMCP and innovative hot rollingprocessWANG Guo-dong( Northeastern University )Abstract:A new-generation TMCP(thermo-mechanical control process) with ultra fast cooling as core technique was suggested instead of the conventional TMCP in which some problems are to be solved. Describes the ultra fast cooling technique theoretically and relevant equipment developed for commercial applications in detail.Key words:steel;hot rolling;new generation TMCP;ultra fast cooling;strengthening1 新一代NG-TMCP 的科学内涵1.1 传统TMCP控制轧制和控制冷却技术,即TMCP,是20 世纪钢铁业最伟大的成就之一。
热轧板带钢新一代TMCP装备及工艺技术
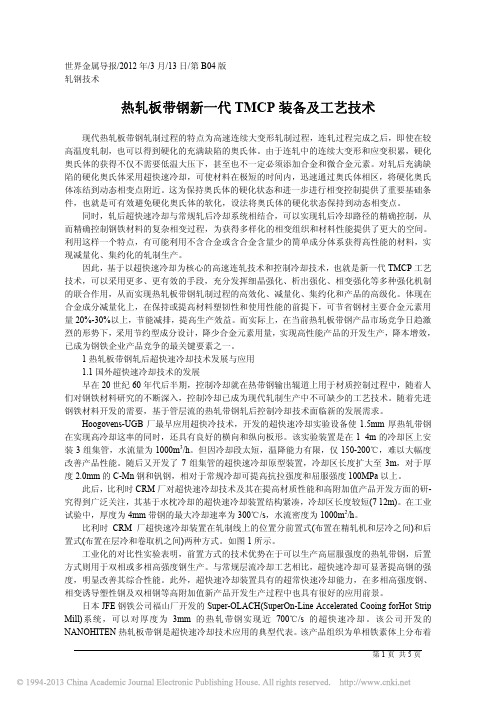
世界金属导报/2012年/3月/13日/第B04版轧钢技术热轧板带钢新一代TMCP装备及工艺技术现代热轧板带钢轧制过程的特点为高速连续大变形轧制过程,连轧过程完成之后,即使在较高温度轧制,也可以得到硬化的充满缺陷的奥氏体。
由于连轧中的连续大变形和应变积累,硬化奥氏体的获得不仅不需要低温大压下,甚至也不一定必须添加合金和微合金元素。
对轧后充满缺陷的硬化奥氏体采用超快速冷却,可使材料在极短的时间内,迅速通过奥氏体相区,将硬化奥氏体冻结到动态相变点附近。
这为保持奥氏体的硬化状态和进一步进行相变控制提供了重要基础条件,也就是可有效避免硬化奥氏体的软化,设法将奥氏体的硬化状态保持到动态相变点。
同时,轧后超快速冷却与常规轧后冷却系统相结合,可以实现轧后冷却路径的精确控制,从而精确控制钢铁材料的复杂相变过程,为获得多样化的相变组织和材料性能提供了更大的空间。
利用这样一个特点,有可能利用不含合金或含合金含量少的简单成分体系获得高性能的材料,实现减量化、集约化的轧制生产。
因此,基于以超快速冷却为核心的高速连轧技术和控制冷却技术,也就是新一代TMCP工艺技术,可以采用更多、更有效的手段,充分发挥细晶强化、析出强化、相变强化等多种强化机制的联合作用,从而实现热轧板带钢轧制过程的高效化、减量化、集约化和产品的高级化。
体现在合金成分减量化上,在保持或提高材料塑韧性和使用性能的前提下,可节省钢材主要合金元素用量20%-30%以上,节能减排,提高生产效益。
而实际上,在当前热轧板带钢产品市场竞争日趋激烈的形势下,采用节约型成分设计,降少合金元素用量,实现高性能产品的开发生产,降本增效,已成为钢铁企业产品竞争的最关键要素之一。
1热轧板带钢轧后超快速冷却技术发展与应用1.1国外超快速冷却技术的发展早在20世纪60年代后半期,控制冷却就在热带钢输出辊道上用于材质控制过程中,随着人们对钢铁材料研究的不断深入,控制冷却已成为现代轧制生产中不可缺少的工艺技术。
新一代TMCP技术控轧控冷

新一代TMCP技术
RAL.NEU
RAL
TMCP技术的发展和创新
• TMCP是20世纪最伟大的钢铁技术成果之一 • 开发引领未来社会发展和人类需求的新一代钢 铁材料 • 需要付出巨大的努力,充分利用新的科技成 果,站在巨人的肩膀上进行钢铁生产过程的脱 胎换骨的革命
RAL
TMCP技术的发展和创新
RAL
高速连轧的温度制度-“趁热打铁”
新一代的TMCP采用适宜的正常轧制温度 进行连续大变形,在轧制温度制度上不再坚持 “低温大压下”的原则。与“低温大压下”过程相 比,轧制负荷可大幅度降低,设备条件的限制 可放松。轧机建设不必追求高强化,大幅度降 低建设投资。
RAL
高速连轧的温度制度-“趁热打铁”
适宜的轧制温度,大大提高轧制的可操作 性,避免轧制工艺事故,例如卡钢、堆钢等, 同时也延长了轧辊、导卫等轧制工具的寿命。 提高产量、降低成本 对于一些原来需要在粗轧和精轧之间实施 待温的材料,可以直接轧制
RAL
“趁热打铁”及其优点
由于新一代的TMCP避免了“低温大压下”,使得传统的“趁 热打铁”的思想得以贯彻实行,这对于减轻生产设备负荷、确 保轧制过程稳定、改善加工过程的可操作性、提高材料的可加 工性、降低轧制能耗等具有十分重要的意义。由于可以少加或 者不加微合金元素和合金元素,所以可以节省大量的资源和能 源,实现减量化的轧制,降低钢材生产成本,这对于钢铁工业 的可持续发展和协调发展具有重要的作用。
RAL
TMCP特征
• 低温大压下——轧制负荷、生产率、设备投 资、轧制稳定性 • 微合金化——提高成本、焊接性能恶化、冶炼连铸-轧制工艺复杂、轧制负荷增大 • 水是最廉价的合金元素——高冷却速率的开发 利用、冷却路径的利用、冷却的均匀性
日本JFE公司开发和应用的中厚板制造技术介绍

日本JFE钢铁公司开始开发采用水淬火的热机械控制工艺(TMCP),作为高强度、高韧性,具有优良焊接性能钢板生产技术的核心技术。
下面简单介绍由JFE钢铁公司开发和应用的中厚板制造技术,包括超级-OLAC技术,一种新的中厚板加速冷却技术以及HOP技术(热处理在线工艺),一种加速冷却后的在线热处理工艺。
同时,下面还介绍Easyfab钢板制造技术,即通过应用具有新功能的冷矫直机将中厚板中残余应力降至零。
一、新加速冷却技术——“超级-OLAC”技术的开发与控制轧制技术一起,加速冷却技术是TMCP工艺的核心技术。
JFE钢铁公司是世界上首家开发并成功在中厚板生产中应用在线加速冷却技术的钢铁企业。
在上世纪90年代初,采用加速冷却技术制造的TMCP钢实现了提高钢板强度、改进焊接性能的目的,从而有助于焊接结构建筑用钢使用的合理化和提高建筑的安全性,并开始用于造船业。
然而,最近几年对钢板质量的要求日趋严格,如减少强度下降等。
为了满足新的要求,基于一个全新的概念,JFE钢铁公司进行了大量研究以获得解决与传统冷却技术问题相关的方案,并开发出新一代加速冷却工艺,称之为超级-OLAC工艺,并应用于JFE钢铁公司西日本钢厂。
当中厚板进行水淬火时出现的热传递和沸腾现象可以大致分为两种方式,即核胞沸腾和薄膜沸腾。
在前一种沸腾中,冷却水直接与钢接触,热量通过产生的泡传递。
相比之下,后一种沸腾中在钢与冷却水间形成一个蒸汽薄膜,热量是通过蒸汽薄膜传递。
核胞沸腾的冷却能力比薄膜沸腾更高。
在中厚板冷却开始时,中厚板表面温度较高,薄膜沸腾起主导作用。
然而,随着中厚板表面温度的下降,蒸汽薄膜变得不稳定,冷却水开始局部上直接与中厚板接触,沸腾逐渐转向核胞沸腾。
此外,在瞬时沸腾状态下,当薄膜沸腾和核胞沸腾共存时,随着冷却的继续,冷却能力提高。
采用传统冷却方法,如喷淋冷却和层流冷却时,如果冷却水流量提高以强化冷却,冷却迅速地转换成瞬时沸腾,是核胞沸腾和薄膜沸腾的混合。
控轧控冷技术的发展及在钢管轧制中应用的设想

写 T P技 术是 随着钢铁 材料性 能的提 高 和新 钢 种 MC )
开发 的需要 而产 生 的 ,并 随之 得到 了持 续 的发 展 与
应 用 ,其 可在不 降低 韧性 的前 提下 获得更 高 的强度
王 国栋 ( 9 2 ) 14 一 ,男 ,教 授 ,博 士 生 导 师 ,中 国工 程 院 院士 ,中 国金 属 学 会 常 务理 事 ,中 国金 属 学 会 轧 钢 学
在 T P技 术 的发 展 历 程 中 ,人 们 首 先 认 识 MC 到 的是控 制轧 制 。控 制轧制 是 一种用 预定 的程序 来
控 制热 轧 钢 的变形 温度 、压 下量 、变 形道 次 、变 形
会副理事长 、轧制理论学术委 员会 主任 。长期从事钢铁 材料轧制理论 、工艺 、自动化等领域的应用基础和工程 技术研究。先后 主持 和完成多项 国家重点基础研究发展 计划 ( 7 ) 目、高技术 研究 发展计划 (6 ) 目、国 9 3项 8 3项
时间
( 例如 N ) b 是为了提高奥氏体 的再结晶温度 ,使奥 氏体在 比较 高 的温度下 还 处于未 再结 晶区 ,从 而增 大奥 氏体在 未再 结 晶区 的变形量 ,实现奥 氏体 的硬 化。 仅 通过控 制 轧制对 钢材 性能 的提 高有一 定 的局 限性 。比如 “ 温大 压 下 ” 长 久 以来 形成 的 “ 低 与 趁热 打铁” 的传统观念背道而驰 ,它必然受到设备能力 等 条件 的 限制 。操 作方 面 的 问题 也不 容 回避 。为 了 突破控 N ̄N 的限制 ,同时也是 为 了进一 步强 化钢 F L 材 的性 能 ,在控 制轧制 的基 础上 ,又 开发 了利用 轧 材余 热 进行 热处 理 的控 制冷 却技 术 。控制冷 却 的核
控轧控冷技术的发展与应用

控轧控冷技术的发展与应用作者:李聪来源:《中国科技博览》2013年第19期摘要:介绍了控轧控冷工艺的发展历史、工艺原理,介绍了NG-TMCP 技术目前在热轧带钢、中厚板、棒线材工业生产中的应用进展情况,说明了采用控轧控冷技术是生产高性能钢材的必然趋势。
关键词:控轧控冷微合金化热轧超快速冷却晶粒尺寸一、前言控轧控冷是一项具有丰富理论内容和较大实用价值的轧钢新技术。
其基本特点是把利用塑性变形得到钢材外部几何形状的热加工成形过程与控制改善钢材组织状态,提高钢材性能的物理冶金过程有机结合起来。
其突出的优点是:可大幅度提高低碳钢、低合金钢材的强韧性;同时可简化工序,节省能耗,节约合金,具有显著的经济效益和社会效益。
二、控轧控冷技术的现状与发展控轧控冷技术是适应高强度低合金钢的发展而产生和发展的。
早期的高强度低合金钢的化学成分是按强度设计的,而对焊接性能、成型性及抗脆性断裂性能没有给予重视。
自从第二次世界大战中全焊接结构船发生脆断事故以来,战后对造船用钢及其他结构用钢,通常采取提高Mn/C比,用铝脱氧及进行常化处理等措施来获得较高的断口韧性。
但一些国家如比利时、瑞典等的钢铁厂当时没有热处理设备,故在工业生产上首次采用控制轧制来代替常化处理,解决了钢的脆断问题,这就确立了控轧控冷技术的原始基础。
到了20世纪60年代初期,在美国科研人员定性地解释了热轧后的钢材继续发生奥氏体再结晶动力学变化后,这才从理论上某种程度地解释了控制轧制技术。
70年代以来,控轧控冷技术越来越受到重视,并在生产中得到广泛应用,例如法国生产的中厚钢板控轧板约占60%。
80年代以来,控轧控冷技术又有新的进展,开发了一些新的控轧方法,如多胚交叉轧制法;SHT法,即住友公司高韧性生产法,其特点是双加热—双轧制,粗轧后水冷至Arl,再加热至常化温度轧制。
目前控轧控冷技术仍处在发展中。
三、控轧控冷技术的基本原理控轧控冷技术的基本原理就是控制热轧条件,经过相变过程在奥氏体的基体上,形成高密度的铁素体晶核,从而在相变后,达到细化钢材的组织结构。
钢铁的控轧控冷工艺(TMCP)介绍

4.控制轧制的效应
(1)使钢材的强度和低温韧性有较大幅度的改善
控制轧制对细化晶粒有明显的作用,按常规轧制工艺, 铁素体晶粒最好的情况为7~8级,晶粒直径>20m,而 按控制轧制工艺,铁素体晶粒可达12级,其直径可为 5m。仅从这方面就可使钢材的强韧性能得到明显的改 善。
(2)可以充分发挥微量合金元素的作用
5.控制冷却的介绍
➢ 控制冷却存在的主要问题是高冷却速率下材料冷 却不均而发生较大残余应力、甚至翘曲的问题。 例如,作为控制冷却的极限结果,直接淬火的作 用早已为人们所认识。但是,其潜在的能力一直 未得到发挥,原因在于直接淬火条件下冷却均匀 性的问题一直没有得到解决,板形控制一直因扰 着人们。
5.控制冷却的介绍
对于控制冷却,有两个通俗说法:
(1)水是最廉价的合金元素 (可以用水替代合金元素来改变钢材的性能)
控制冷却的理念可以归纳为“水是最廉价的合金元素” 这样一句话。
(2)中国的多数(中板)轧机是世界上最干旱的轧机 (目前我们还没有充分利用好水的作用) -川崎水岛:12000 m3/h,迪林根:14000 m3/h -宝钢2050:14000 m3/h,1580: 13000 m3/h
钢铁的控轧控冷 工艺介绍
知识求索人
目录
1. 何为控轧控冷工艺? 2. 控轧控冷工艺的优势和应用 3. 控制轧制的类型 4. 控制轧制的效应 5. 控制冷却介绍
1.何为控轧控冷工艺?
➢ 控轧控冷工艺,又称TMCP(Thermo Mechanical Control Process:热机械控制工艺),是将控制轧制和控制冷却 技术结合起来的工艺,该工艺能够进一步提高钢材的强 韧性和获得合理的综合性能,并能够降低合金元素含量 和碳含量,节约贵重的合金元素,降低生产成本。TMCP 是20世纪钢铁业最伟大的成就之一!
TMCP技术的新进展

TMCP技术的新进展———柔性化在线热处理技术装备近年来,在线热处理技术受到普遍重视,这是因为在线热处理利用轧制余热对钢材进行热处理,可以省去离线热处理的二次加热工序,因而达到节约能源、简化操作、缩短产品交货期的目的。
同时,在线热处理可以利用材料热轧过程中积累的应变硬化,在有些情况下可以得到比离线热处理更优的产品性能和质量。
传统的在线热处理包括加速冷却和直接淬火(DQ)。
传统的在线热处理工艺和装备有两方面的问题。
其一,轧后冷却过程是调整材料相变组织乃至性能的重要阶段。
为了得到需要的材料组织和性能,仅仅依靠冷却是不够的,有时候还需要加热。
其二,即使是冷却过程,出于冷却路径控制的需要,也不能仅靠简单的加速冷却。
人们希望可以在低速到直接淬火之间进行宽范围的冷却速度控制,还希望可以控制冷却的路径,甚至可以在线加热。
这样,就可以依据需要的材料组织和性能,在线控制材料的冷却路径,即实施柔性化的热处理过程。
通过轧后的热处理,可以得到多种多样的材料组织和性能,实施技术创新、提升材料性能的空间广阔。
在这种情况下,各种在线热处理的新设备、新工艺应运而生。
应当注意的是,除了加热和冷却设备之外,生产线上的其他设备,如热连轧的卷取机和各类钢材的精整设备也可能须进行适应性改造。
超快速冷却系统的发展Super-OLAC:1998年,JFE西日本制铁所福山地区厚板厂对原有的冷却系统进行改造,建设了Super-OLAC (超级在线加速冷却)新型加速冷却系统。
该系统的最大的特点是具有可达极限冷却的冷却速率和极高的冷却均匀性。
Super-OLAC系统既可以实现加速冷却,又可以实现在线直接淬火。
一套系统兼有直接淬火和加速冷却两种功能,是新一代控制冷却系统的重要特征。
CLC-μ:新日铁于1983年率先采用冷却前钢材矫直和约束冷却方式的冷却系统,称之为CLC(连续在线控制),并应用于生产焊接性优良的高强、高韧性钢等产品。
新日铁在CLC应用的基础上,开发了新一代控制冷却系统CLC-μ。
以超快速冷却为核心的新一代技术

以超快速冷却为核心的新一代技术The New Generation TMCP with rhe KeyTechnology of Uletra Fast Cooling王国栋摘要针对传统TMCP技术采用“低温大压下”和“微合金化”的问题,利用连续轧制的大变形和应变积累,提出以超快速冷却技术为核心的新一代控制轧制和控制冷却技术的大变形和应变积累,提出以超快速冷却技术为核心的新一代控制轧制和控制冷却技术(NG-TMCP),描述了它的技术特征和材料特点,指出这是一项节省资源和能源,有利于材料循环利用,促进社会可持续发展的新技术。
1 TMCP技术及其特征控制轧制和控制冷却技术,即TMCP,是20世纪钢铁业最伟大的成就之一。
正是因为有了TMCP技术,钢铁业才能源源不断地向社会提供越来越优良的钢铁材料,支撑着人类社会的发展和进步。
控制轧制和控制冷却技术的目标是实现晶粒细化和细晶强化。
在控制轧制和控制冷却技术的发展历程中,人们首先认识到的是控制轧制,其核心思想是对奥氏体硬化状态的控制,即通过变形的奥氏体中积累大量的能量,力图在轧制过程中获得处于硬化状态的奥氏体,为后续的相变过程中实现晶粒细化做准备。
控制轧制的基本手段是“低温大压下”和添加微合金元素。
所谓“低温”是在接近相变点的温度进行变形,由于变形温度低,可以抑制奥氏体的再结晶,保持其硬化状态,“大压下”是指施加超出常规的大压下量,这样可以增加奥氏体内部储存的变形能,提高硬化奥氏体程度。
增加微合金元素,例如Nb,是为了提高奥氏体的再结晶温度,使奥氏体在比较高的温度即处于未再结晶区,因而可以增大奥氏体在未结晶区的变形量,实现奥氏体的硬化。
图1图1控制轧制和控制冷却为了突破控制轧制的限制,同时也是为了进一步强化钢材的性能,在控制轧制的基础上,又开发了控制冷却技术,控制冷却的核心思想,是对处于硬化状态奥氏体相变过程进行控制,以进一步细化铁素体晶粒,甚至通过相变强化得到贝氏体等强化相,进一步改善材料的性能。
2009091701-TMCP和在线离线热处理-王国栋
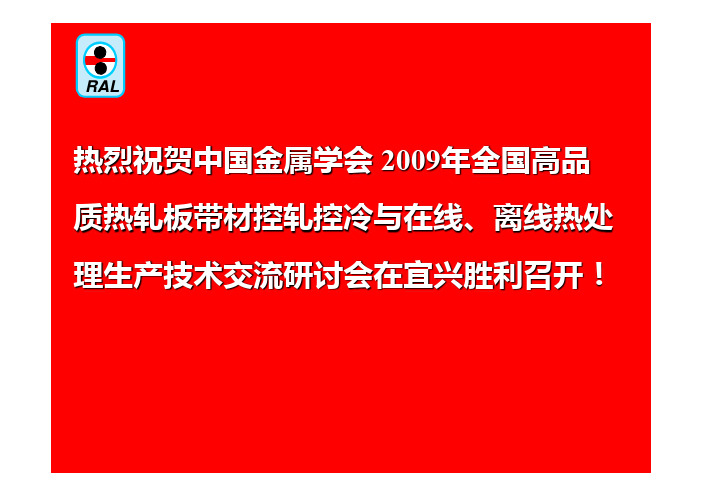
RAL2009RAL 王国栋东北大学轧制技术及连轧自动化国家重点实验室2009年9月17日, 江苏宜兴2009年全国高品质热轧板带材控轧控冷与在线、离线热处理生产技术交流研讨会RAL中国钢铁工业面临的问题炼铁炼钢轧钢可持续发展能源钢铁产品水原材料废弃物废气废水资源限制高效高服役性能长寿命低成本可循环绿色环境负荷自主创新重点跨越支撑发展引领未来RALPOSCO的发展战略打造具备全球竞争力的一流钢铁产业•钢铁生产规模达到6000万吨,保持全球前5位•以生产成本的大幅降低确保全球竞争力的增强•实现创新钢铁技术(例如FINEX)的商业化,引领全球钢铁技术发展趋势在原料竞争中确保优势•积极在海外投资开发矿产•实现废钢的自给自足引导未来需求的创新材料的开发•开发并普及高附加值产品生产技术•为确保全球竞争力不断开发新技术并实现商业化打造绿色科技(GreenTech)钢铁产业•环境友好型洁净技术开发和使用•促进CDM事业发展,积极应对气候变化落潮时的反思RAL巴菲特:只有在大海退潮的时候,才知道谁没有穿泳裤。
泳裤——核心竞争力三种基本的竞争战略RAL经济学家波特在对行业结构进行深入分析并在广泛研究不同的企业成败经验的基础上提出了三种基本的竞争战略。
第一是成本领先战略,它主要依靠追求规模经济、专有技术和优惠的原材料等因素,以尽可能低的成本(低于行业平均水平)提供产品和服务,来获得较高的利润和较大的市场份额。
第二是差异化战略,这种战略依赖于基础产品、销售交货体系、营销渠道等一系列因素,为顾客提供附加价值,以它的一种或多种特质在产业内独树一帜。
第三是目标集聚战略,这种战略着眼于产业内的一个狭小空间作出选择,即选择产业内一种或一组细分市场,并量体裁衣为其服务而不是为其他细分市场服务。
转变发展方式RAL•由产量扩张型的建设项目转向质量、效益提高型的改造项目和配套项目;•新引进“先进”轧机也有强烈的改造需求!•由引进、吸收、消化转向自主创新•由单一项目转向工艺、机电、产品一体化的整体集成和创新项目技术改造成为重点(李毅中)RAL•当前,技术改造不仅是拉动经济增长、应对国际金融危机的有效措施,也是调整产业结构、提高产品质量和增强企业竞争力的有效途径。
中厚钢板的生产中控轧控冷工艺

目前在中厚钢板的生产中控轧控冷(TMCP)工艺已普遍应用,并在管线钢、高强度结构钢、海洋平台用钢、造船板等的生产中发扬了积极作用,大大提高了钢板的综合性能,节约了贵重的合金元素。
然而,TMCP处理的钢板性能离散度较大,而且一些钢种要求特别苛刻的临界轧制。
因此,关于生产厚规格、高性能钢板,尤其是要求性能均匀性比立高的锅炉压力容器钢板、桥梁钢板、高层建筑钢板、Z向钢板等,传统的离线热处理方式仍然是难以替代的。
因此一个定位于生产高性能品种钢为主的中厚板厂,建设一条现代化的中厚板热处理生产线,是在设计之初就必须考虑的咨询题。
建设热处理工序应统筹考虑的咨询题1对炼钢、轧钢工序设备的要求中厚板轧后热处理炉是生产高技术含量、高附加值产品不可缺少的要紧设备,因此应定位在生产“双高〞产品,要求钢质纯洁、有害元素和夹杂物含量低,板坯厚度要满足一定的压缩比,配备有控轧控冷设施等。
这就要求前面的炼钢和轧钢工序具备生产“双高〞产品的条件,如炼钢工序要配备有铁水预处理设施、大吨位的顶底复吹转炉或高功率电炉、LF/VD/RH等炉外精炼设施、直弧形大板坯连铸机等,轧钢工序要配备有高刚度强力轧机、ACC(DQ)、强力矫直机等。
2对轧钢厂的场地要求在建设中厚板厂时,要考虑精整的能力足够大,也确实是根基后面剪切、冷床等的能力要大于前面轧钢能力,以便于充分发扬轧机的潜能。
同样要是一个中厚板厂定位于生产高技术含量、高附加值产品时,就要考虑厂房后部工序要留有充分的火焰切割、探伤、热处理生产线的场地。
因为关于需要热处理的钢板来讲,一般40mm以上的厚规格钢板受剪切能力限制,需要火焰切割,而且热处理的钢种许多要求逐张探伤。
因此,在厂房设计时要留有足够的场地,否那么将严重制约生产能力的发扬。
探伤一般可安排在热处理之前,如此探伤不合可直截了当改判以节约热处理费用,但正火通过再结晶细化均匀组织,关于某些微小的探伤缺陷有改善作用,尤其是合金含量较高的钢种。
新一代TMCP技术的发展_王国栋
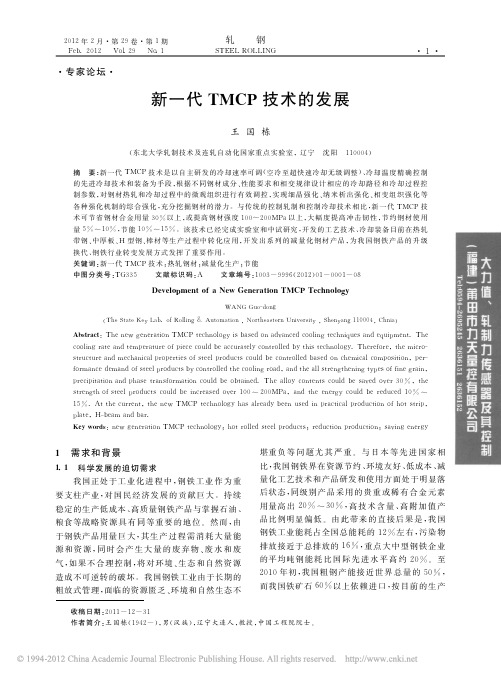
堪重负 等 问 题 尤 其 严 重 。 与 日 本 等 先 进 国 家 相 比, 我国钢铁界在资源节约 、 环境友好 、 低成本 、 减 量化工艺技术和产品研发和使用方面处于明显落 后状态 , 同级别产 品 采 用 的 贵 重 或 稀 有 合 金 元 素 用量高 出 2 高 技 术 含 量、 高附加值产 0% ~3 0% , 我国 品比例明显 偏 低 。 由 此 带 来 的 直 接 后 果 是 , 钢铁工业能耗占全国总 能 耗 的 1 污染物 2% 左 右 , 重点大中型钢铁企业 排放接近于总排放的 1 6% , 的平均吨 钢 能 耗 比 国 际 先 进 水 平 高 约 2 0% 。 至 我国 粗 钢 产 能 接 近 世 界 总 量 的 5 2 0 1 0 年初 , 0% , 而我国铁矿石 6 按目前的生产 0% 以上依 赖 进 口 ,
控制冷却工艺一般需要提高钢中微合金元素含量 或进一步提 高 轧 机 能 力 。 然 而 , 前者会造成钢材 成本的提升和资 源 的 消 耗 , 后者则因现代化轧机 能力已接近 极 限 而 无 法 轻 易 实 现 。 另 外 , 长期以 来, 国内外普遍追 求 通 过 低 温 大 压 下 来 实 现 钢 材 对于普碳钢材而言 , 晶 的细晶强化 。 但实践证明 , 粒尺寸小到 2 尽管钢材的强度可有效 m 以下时 , μ 但其屈强比接近 1, 已经 失 去 工 程 材 料 的 应 提升 , 用价值 。 追求超细晶的生产工艺不仅会降低热轧 生产效率 、 增加事故发生率 , 而且会把过多的负担 转移到轧制过程 , 忽视了轧后冷却对钢材性能的 调控作用 。 此外 , 传统 TMC P 技术在提高热轧钢 会因低温轧制产生残余应力而 板强韧性的同时 , 带来板形不良和 剪 裁 瓢 曲 等 问 题 ; 生产高强钢厚 板时 , 除非提高钢 中 合 金 元 素 含 量 或 进 行 轧 后 热 否 则 已 无 法 突 破 强 度 和 厚 度 规 格 的 极 限。 处 理, 热轧钢铁 材 料 的 相 变 主 要 在 轧 后 冷 却 过 程 中 完 它 是 调 控 组 织 结 构、 最终控制性能的主要手 成, 段 。 因此 , 为实现资源节约型高性能钢材的生产 , 必须对轧后冷却 技 术 进 行 创 新 , 通过冷却路径和 冷却速率的优化 控 制 , 实现钢材组织和性能的调 控, 使成分简单的 钢 铁 材 料 能 够 具 备 满 足 多 样 化 要求的性能指标 。 为弥补传统控 制 冷 却 技 术 的 不 足 , 在欧洲和 日本相继 开 发 出 了 热 轧 板 带 轧 后 超 快 速 冷 却 技 术 。 传统的层流冷却和新一代的超快速冷却具有 即需要使用冷却水 , 利用冷却水来调 共同的特点 , 。但 节热轧 钢 材 的 冷 却 过 程 ( 材 料 的 相 变 过 程) 是, 与传统层流冷却相比 , 超快速冷却可有效打破 汽膜 , 实现对热轧钢板进行高效率 、 高均匀性的冷 / 却( 对于 3 mm 厚 钢 板 冷 却 速 率 可 达 4 0 0 K s以 / 上; 5 0 mm 厚 中 厚 板 的 平 均 冷 却 速 率 超 过 5 0 K ) , 并可 避 免 因 冷 却 不 均 匀 而 产 生 的 残 余 应 力 。 s 轧后超快冷技术使热轧钢板的性能指标有了质的 飞跃 , 而材料成本 和 生 产 过 程 中 的 各 类 消 耗 则 大 幅度降低 。 目前 , 轧后超快冷技术已经成为热轧 板带材生产线改 造 的 重 要 方 向 , 已用于生产中厚 板、 热轧 带 钢 、 棒 线 材、 钢管等9 H 型 钢、 0% 以 上 的热轧钢材 。 与 常 规 冷 却 方 式 相 比 , 超快冷不仅 且与常规 A 可以提高 冷 却 速 率 , C C 配合可实现 与性能要求相适应的多种冷却路径优化控制 。 但 是, 与对传统轧制技术的研究深度和广度相比 , 关 于超快速冷却条件下的各种物理冶金学规律尚未
钢材控制轧制和控制冷却技术

钢材控制轧制和控制冷却技术材控14卢玉厚钢材的控制轧制和控制冷却技术卢玉厚材冶学院材料成型及控制工程 118【摘要】控制轧制和控制冷却技术,在提高钢材综合力学性能、开发新品种、简化生产工艺、节约能耗和改善生产条件等方面,取得了明显的经济效益和社会效益。
近三十年以来,控制轧制和控制冷却技术在国外得到了迅速的发展,各国先后开展了多方面的理论研究和应用技术研究,并在轧钢生产中加以利用,明显的改善和提高了钢材的强韧性和使用性能,为了节约能耗、简化生产工艺和开发钢材新品种创造了有力条件。
控制轧制是指在热轧过程中,通过对金属加热、轧制和冷却的合理控制,使范性形变与固态相变过程相结合,以获得良好的晶粒组织,使钢材具有优异的综合性能的轧制技术。
控制冷却是指热加工后对钢材进行的旨在控制相变组织和钢材性能的冷却技术。
【关键词】控制轧制技术控制冷却技术特点应用发展趋势Abstract:Controlled rolling and controlled cooling technology, to improve the comprehensive mechanics performance of steel, the development of new varieties, simplify the production process, save energy and improve production conditions, etc., have achieved obvious economic benefits and social benefits. For nearly 30 years, controlled rolling and controlled cooling technology obtained the rapid development in foreign countries, and countries successively carried out various theoretical research and applied technology research, and tries to use in the production of steel rolling, the obvious improve and enhance the tenacity of steel and the use of performance, in order to save energy consumption, simplify production process and development of new steel varieties created favourable conditions. Control is to point to in the hot rolling process of rolling, based on the reasonable control of the metal heating, rolling and cooling, and make the plastic deformation combined with solid phase change process, in order to obtain good grain organization, make steel has excellent comprehensive performance of the rolling technology. Controlled cooling means to control phase change of steel after hot working organization and performance of the steel cooling technology.Key Words:Control rolling technology;Characteristics of controlled cooling technology;application;development trend1.引言近代工业发展对热轧非调质钢板的性能要求越来越高,除了具有高强度外 ,还要有良好的韧性、焊接性能及低的冷脆性。
新型细晶强化Q460级宽厚板的TMCP工艺研究
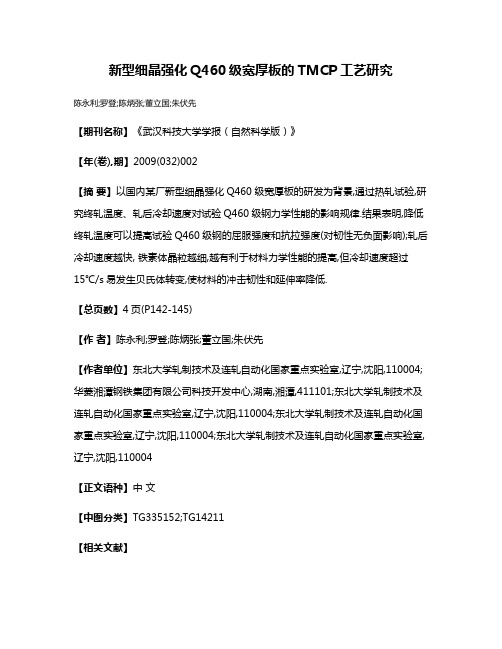
新型细晶强化Q460级宽厚板的TMCP工艺研究陈永利;罗登;陈炳张;董立国;朱伏先【期刊名称】《武汉科技大学学报(自然科学版)》【年(卷),期】2009(032)002【摘要】以国内某厂新型细晶强化Q460级宽厚板的研发为背景,通过热轧试验,研究终轧温度、轧后冷却速度对试验Q460级钢力学性能的影响规律.结果表明,降低终轧温度可以提高试验Q460级钢的屈服强度和抗拉强度(对韧性无负面影响);轧后冷却速度越快, 铁素体晶粒越细,越有利于材料力学性能的提高,但冷却速度超过15℃/s易发生贝氏体转变,使材料的冲击韧性和延伸率降低.【总页数】4页(P142-145)【作者】陈永利;罗登;陈炳张;董立国;朱伏先【作者单位】东北大学轧制技术及连轧自动化国家重点实验室,辽宁,沈阳,110004;华菱湘潭钢铁集团有限公司科技开发中心,湖南,湘潭,411101;东北大学轧制技术及连轧自动化国家重点实验室,辽宁,沈阳,110004;东北大学轧制技术及连轧自动化国家重点实验室,辽宁,沈阳,110004;东北大学轧制技术及连轧自动化国家重点实验室,辽宁,沈阳,110004【正文语种】中文【中图分类】TG335152;TG14211【相关文献】1.大厚度S460G2+M钢板TMCP工艺研究 [J], 刘印子;林明新;张萌;胡湘红2.TMCP型大厚度390 MPa级工程机械用钢板的开发及工艺研究 [J], 王晓书;李常牛3.新型低成本细晶强化Q460级中厚钢板-UP460的研制 [J], 刘彦春;朱伏先;任培东;孙智千;王谨4.TMCP型70kg级高强钢的生产工艺研究及应用 [J], 赵华5.新一代TMCP条件下钛微合金化Q460钢种开发 [J], 郭仁辉;韩毅;邓想涛因版权原因,仅展示原文概要,查看原文内容请购买。
- 1、下载文档前请自行甄别文档内容的完整性,平台不提供额外的编辑、内容补充、找答案等附加服务。
- 2、"仅部分预览"的文档,不可在线预览部分如存在完整性等问题,可反馈申请退款(可完整预览的文档不适用该条件!)。
- 3、如文档侵犯您的权益,请联系客服反馈,我们会尽快为您处理(人工客服工作时间:9:00-18:30)。
世界金属导报/2012年/1月/10日/第B04版轧钢技术热轧钢铁材料新一代TMCP技术TMCP(Thermo-MechanicalControlled Processing),即控制轧制和控制冷却技术,是20世纪钢铁业最伟大的成就之一,也是目前钢铁材料轧制及产品工艺开发领域应用最为普遍的技术之一。
正是因为有了TMCP技术,钢铁工业才能源源不断地向社会提供越来越有用的钢铁材料,支撑着人类社会的发展和进步。
1 TMCP工艺技术的发展及基本原理TMCP工艺的两个重要组成部分之一,控制轧制,在热轧钢铁材料领域很早就已根据经验予以实施,其核心思想是对奥氏体硬化状态的控制,即通过变形在奥氏体中积累大量的能量,力图在轧制过程中获得处于硬化状态的奥氏体,为后续的相变过程实现晶粒细化做准备。
在20世纪60年代至70年代,随着能源不断开发,对高性能管线钢的需求大幅增加。
为满足管线钢板的生产,控制轧制技术得到快速发展,并在当时的厚板轧制、船板生产等方面得到广泛应用。
为了突破控制轧制的限制,同时也是为了进一步强化钢材的性能,在控制轧制的基础上,又开发了控制冷却技术。
控制冷却的核心思想是对处于硬化状态的奥氏体相变过程进行控制,以进一步细化铁素体晶粒,甚至通过相变强化得到贝氏体等强化相。
相变组织比单纯控制轧制更加细微化,促使钢材获得更高的强度,同时又不降低其韧性,从而进一步改善材料的性能。
1980年,日本NKK福山制铁所首次为厚板生产线配置并使用了OLAC(On-Line Accelerated Cooling)系统。
此后基于对提高厚板性能及钢种开发的需要,重点发展了厚板的快速在线冷却技术,并相继开发出一系列快速冷却装置,投入厚板的开发生产及应用中。
控制冷却设备的普遍应用有力地推动了高强度板带材的开发和在提高材质性能方面技术的进步。
后来,人们将结合控制轧制和控制冷却的技术称为控轧控冷技术TMCP(Thermo-MechanicalControlled Processing)。
因此,热轧钢铁材料TMCP的基本冶金学原理是,在再结晶温度以下进行大压下量变形促进微合金元素的应变诱导析出并实现奥氏体晶粒的细化和加工硬化;轧后采用加速冷却,实现对处于加工硬化状态的奥氏体相变过程的控制,获得晶粒细小的最终组织。
为了提高再结晶温度和保持奥氏体的硬化状态,同时也为了对硬化状态下奥氏体的相变过程进行控制,控制轧制和控制冷却始终紧密联系在一起。
控制轧制的基本手段是“低温大压下”和添加微合金元素。
所谓“低温”是在接近相变点的温度进行变形,由于变形温度低,可以抑制奥氏体的再结晶,保持其硬化状态。
“大压下”是指施加超出常规的大压下量,这样可以增加奥氏体内部储存的变形能,提高硬化奥氏体程度。
微合金化是增加微合金元素,例如铌等微合金元素的加入,是为了提高奥氏体的再结晶温度,使奥氏体在比较高的温度即处于未再结晶区,因而可以增大奥氏体在未再结晶区的变形量,实现奥氏体的硬化。
控制冷却的理念可以归纳为“水是最廉价的合金元素”这样一句话。
通过冷却参数的控制与优化实现对热轧后钢板相变过程的控制,配合控制轧制工艺过程得到所需的组织和性能。
TMCP工艺实施所依托的装备条件除轧机外,主要是层流冷却系统,如图1为中厚板生产线轧后层流冷却设备。
国外钢铁技术发达国家如日本等,自控制冷却技术(含工艺及装备)工业化大批量应用开始为标志至今,TMCP工艺技术已历经30余年。
我国约从2000年开始,在国内相关科研单位如东北大学、北京科技大学等努力下,依托相关钢铁企业中厚板轧线建设及技术改造,自主研发出具有当时国际先进水平的自主知识产权的系列控冷设备。
此后,国内中厚板企业轧线设备或采用国产或通过成套引进,中厚板轧线相继都配备了冷却机理一致、但设备形式及功能有所差异的层流冷却设备,并在此设备基础上,开发出相关控制冷却工艺技术,在各类品种及工艺开发过程中发挥了巨大作用。
2 TMCP的创新发展:新一代TMCP技术的起源与基本原理20世纪90年代,国内外钢铁行业掀起了超级钢的工艺技术开发潮流。
1998年底,我国国家重点基础研究发展计划(973计划)“新一代钢铁材料的重大基础研究”项目启动,东北大学RAL 承担“轧制过程中实现晶粒细化的基础研究”子课题,其任务是通过细化晶粒,使现有200MPa 级别的普碳钢在成分基本不变的条件下屈服强度提高一倍,并具有良好的塑性和韧性。
在研究过程中,与当时国际上流行的最大限度细化晶粒的技术路线不同,RAL科技工作者创新性的提出采用晶粒适度细化的概念,开发出在现有工业条件下能够实现的超级钢生产工艺技术。
2005年我国生产超级钢热轧带钢、超级钢棒线材、超级钢中厚板等品种超级钢逾400万t。
RAL在热轧钢铁材料TMCP工艺技术开发领域取得的成就令人瞩目。
面对不断增长的超级钢工业化批量生产数据,超级钢的开发实践成绩令人鼓舞,超级钢开发课题在国内钢铁行业作出了令人瞩目的贡献。
但对于RAL科研学术团队来说,静心思考之余,总隐隐地感觉到传统TMCP这一技术理念存在一定的不足和缺憾:在热轧板带、中厚板生产应用过程中,低温大压下,轧制温度很低,导致轧机负荷都很大;同时,为满足组织转变要求,终冷温度通常较低,通常都低于500℃,有的钢种温度已低至350-450℃左右。
而由此造成的轧制过程不稳定、冷却过程的板形不良等问题时刻考验着企业的操作及生产工艺过程,从企业接受程度来说,总是存在一定的难度。
对此,王国栋院士曾用“如鲠在喉”来形容企业对于该工艺生产技术的感受。
对于当时超级钢开发过程的另一个收获在于棒线材方面的开发工作。
棒线材生产过程由于轧速很高,低温轧制常导致堆钢等生产事故。
因此,采用在热轧板材推广应用过程中惯用的“低温大压下”路线在当时棒线材尤其是在线材超级钢工艺的开发过程中屡屡碰壁,推广应用难以展开。
“低温路线走不通,必须高温轧制,有没有新的工艺技术路线可以实现?”,当时这个问题时常萦绕在RAL轧钢工作者的心头。
最终RAL轧钢工作者创新性的提出采用高温终轧路线,通过大应变连续累积变形+水雾超快速冷却工艺,在适当的温度点停止冷却。
通过超快速冷却抑制奥氏体再结晶,保持硬化状态,并控制随后的相变过程,实现了强度从Q235级别升级到400MPa级别的棒线材稳定工业化批量生产,突破了常规低温控制轧制的观念。
问题是创新的源泉。
善于发现问题,是技术创新不竭的动力。
具体反思和认识TMCP技术本身,通过采用低温大压下和微合金化的技术路线,铌等微合金元素的加入虽然可以显著提高钢材的再结晶温度,扩大未再结晶区,大大强化轧制奥氏体的硬化状态,且以碳氮化物形式析出,实现沉淀强化,从而对提高材料强度作出贡献。
但是,微合金和合金元素加入,会提高材料的碳当量,这会恶化材料的焊接性能,同时还会造成钢材成本上升和合金资源的消耗。
至于进一步提高轧机能力,则因现代化轧机能力已接近极限而无法轻易实现。
另外,采用低温大压下易导致热轧钢板表面形成过多的红色氧化铁皮,对表面质量造成破坏,会增加后续加工过程中的加工成本,甚至损伤钢板的表面。
再者,传统TMCP在提高热轧钢板强韧性的同时,会因低温轧制产生残余应力而带来板形不良和剪裁瓢曲等问题。
最后,传统TMCP技术生产高强钢厚板时,除非提高钢中合金元素含量或进行轧后热处理,否则已无法突破强度和厚度规格极限。
因此,传统TMCP技术本身已有了其难以克服的局限性。
同时,随着社会的高速发展,使人类面临越来越严重的资源、能源短缺问题,承受着越来越大的环境压力。
人类必须解决这些问题,才能与自然和谐发展,保持人类社会的长治久安和子孙后代的幸福安康。
针对这样的问题,在制造业领域,提出了4R原则,即减量化、再循环、再利用、再制造。
具体到TMCP技术本身,传统TMCP工艺过程实现的两个要素“低温大压下”和“微合金化”,一方面导致轧制生产工艺过程与人们长久以来形成的“趁热打铁”的观念相违背,必然受到设备能力等方面限制,轧制生产过程操作方面的问题不容回避;另一方面导致钢铁材料产品生产过程中大量的资源和能源消耗。
长期以来,钢铁企业为此而大幅提升轧制设备能力,投入了大量资金、人力,同时消耗了大量的能源和资源。
如何克服传统TMCP工艺过程的缺点,即采用节约型的成分设计和减量化的生产工艺方法,获得高性能、高附加值、可循环的钢铁产品。
这一问题实实在在地摆在了轧钢工作者的面前,作为钢铁材料物理冶金重要手段的TMCP技术,需要建立新的发展思路和开发框架。
而与此同时,为弥补传统控制冷却技术的不足,在欧洲和日本相继开发出了热轧板带轧后超快速冷却技术。
传统的层流冷却和新一代超快速冷却的共同特点,是它们都需要使用水,利用水来调节热轧钢材的冷却过程,即调节材料的相变过程。
但是,与传统层流冷却相比,超快速冷却可有效打破汽膜,实现对热轧钢板进行高效率、高均匀性的冷却(对于3mm厚钢板冷却速度可达400K/s以上),冷却速率可达到传统层流冷却速率的2-5倍左右。
但当时人们对该技术的认识和应用更多的是实现热轧钢材的快速降温或用于后段强冷实现双相钢的开发生产等补充或辅助手段。
基于RAL在超级钢工艺上的开发实践和对钢铁材料TMCP工艺技术领域的研究与体会,以及对传统控制冷却(层流冷却)技术重新认识,王国栋院士敏锐地认识到,将超快速冷却技术应用于热轧钢铁材料轧制技术领域,与控制轧制相结合,必将为已发展30余年的TMCP技术带来革命性的变化,引领新的发展。
随后在RAL开展的系列实验室研究结果表明,超快速冷却使热轧钢板的性能指标与以往相比有了质的飞跃,而材料成本和生产过程中的各类消耗则大幅度降低。
这种技术在生产中的初步应用使人们认识到,使用水的冷却过程不仅仅可以丰富轧后冷却路径控制手段,而且会衍生出很多新的钢材强韧化机理。
在此基础上,2007年,以王国栋院士为代表的RAL轧钢科技工作者系统提出了以超快速冷却技术为核心的新一代TMCP技术。
目前,轧后超快速冷却技术已经成为热轧板带材生产线改造的重要方向。
中试结果和部分生产应用都表明,这种技术可以推广应用于包括中厚板、热连轧、棒线材、H型钢、钢管等90%以上的热轧钢材。
与常规冷却方式相比,不仅可以提高冷却速度,且与常规ACC相配合可实现与与性能要求相适应的多种冷却路径优化控制。
与传统TMCP技术采用“低温大压下”和“微合金化”不同,以超快速冷却技术为核心的新一代TMCP技术的中心思想是:①在奥氏体区,趁热打铁,在适于变形的温度区间完成连续大变形和应变积累,得到硬化的奥氏体;②轧后立即进行超快冷,使轧件迅速通过奥氏体相区,保持轧件奥氏体硬化状态;③在奥氏体向铁素体相变的动态相变点终止冷却;④后续依照材料组织和性能的需要进行冷却路径的控制。