ISO9001:2015质量手册-英文版
ISO 9001-2015 中英文对照

ISO 9001:20151 ScopeThis International Standard specifies requirements for a quality management system when an organization:a)needs to demonstrate its ability toconsistently provide product or servicethat meets customer and applicablestatutory and regulatory requirements,andb)aims to enhance customer satisfactionthrough the effective application of thesystem, including processes forimprovement of the system and theassurance of conformity to customer and applicable statutory and regulatoryrequirements.All requirements of this International Standard are generic and are intended to be applicable to all organizations, regardless of type, size and product and service provided.NOTE 1 In this International Standard, the terms “product” or “service” only apply to products and services intended for, or required by, a customer.NOTE 2 Statutory and regulatory requirements can be expressed as legal requirements. 1範圍本國際標準所訂的品質管理系統要求,當一個組織:a)必須展現其提供一致地符合顧客要求和符合適用法令和法規要求之產品或服務的能力。
ISO9001:2015全套文件英文版(含质量手册及全套程序文件)

Ningbo XXX Material TechnologyCo.,LtdISO9001:2015 Quality ManualRevision [A/0] - [2018/3/1](c) [Copyright Year Of 2018] [Ningbo XXX Material Technology Co.,Ltd]; all rights reserved. This document may contain proprietary information and may only be released to third parties with approval of management. Document is uncontrolled unless otherwise marked; uncontrolled documents are not subject to update notification.Revision [A/0] - [2018/3/1]Page 1 of 19TABLE OF CONTENTS0.0 Revision History and Approval ...................................................................................................................... 3 1.0 Welcome to Ningbo XXX Material Technology Co.,Ltd ................................................................................ 4 2.0 XXX Material: Who We Are ........................................................................................................................... 4 2.1 Determining Our Strategic Direction ......................................................................................................... 4 2.2 Scope of the Management System ........................................................................................................... 4 2.2.1 Scope Statement ............................................................................................................................... 4 2.2.2 Facilities Within the Scope ................................................................................................................ 4 2.2.3 Permissible Exclusions ..................................................................................................................... 5 2.2.4 Scope of the ISO9001:2015 Quality Manual ..................................................................................... 5 3.0 Quality Policy................................................................................................................................................. 5 4.0 Management System Structure and Controls ............................................................................................... 5 4.1 Process Approach .................................................................................................................................... 5 4.1.1 Process Identification ........................................................................................................................ 5 4.1.2 Process Controls & Objectives .......................................................................................................... 6 4.1.3 Outsourced Processes ...................................................................................................................... 7 4.2 Documentation & Records ....................................................................................................................... 7 4.2.1 General .............................................................................................................................................. 7 4.2.2 Control of Documents ....................................................................................................................... 7 4.2.3 Control of Records ............................................................................................................................ 7 4.3 Change Management ................................................................................................................................ 8 4.4 Risks and Opportunities ............................................................................................................................ 8 5.0 Management & Leadership ........................................................................................................................... 8 5.1 Management Leadership and Commitment .............................................................................................. 8 5.2 Customer Focus ........................................................................................................................................ 9 5.3 Quality Policy ............................................................................................................................................. 9 5.4 Organizational Roles Responsibilities & Authorities ................................................................................. 9 5.5 Internal Communication ............................................................................................................................ 9 5.6 Management Review .............................................................................................................................. 10 6.0 Resources ................................................................................................................................................... 10 6.1 Provision of Resources ........................................................................................................................... 10 6.2 Human Resources .................................................................................................................................. 10 6.3 Infrastructure ........................................................................................................................................... 11 6.4 Work Environment ................................................................................................................................... 11 6.5 Organizational Knowledge ...................................................................................................................... 11 7.0 Operation ..................................................................................................................................................... 11 7.1 Operational Planning and Control ........................................................................................................... 12 7.2 Customer-Related Activities .................................................................................................................... 12 7.2.1 Capture of Customer Requirements ............................................................................................... 12 7.2.2 Review of Customer Requirements ................................................................................................ 12 7.2.3 Customer Communication ............................................................................................................... 12 7.3 Design and Development ........................................................................................................................ 13 7.4 Purchasing .............................................................................................................................................. 13 7.5 Provision of [Production of adhesive tape] .............................................................................................. 13 7.5.1 Control of Provision of [Production of adhesive tape] ..................................................................... 13 7.5.2 Identification and Traceability .......................................................................................................... 14 7.5.3 Property Belonging to Third Parties ................................................................................................ 14 7.5.4 Preservation .................................................................................................................................... 14 7.5.5 Post-Delivery Activities .................................................................................................................... 14 7.5.6 Process Change Control ................................................................................................................. 15 7.5.7 Measurement and Release of [Production of adhesive tape] ......................................................... 15 7.5.8 Control of Nonconforming Outputs .. (15)Revision [A/0] - [2018/3/1]Page 2 of 198.0 Improvement ............................................................................................................................................... 15 8.1 General .................................................................................................................................................... 15 8.2 Customer Satisfaction ............................................................................................................................. 15 8.3 Internal Audit ........................................................................................................................................... 16 8.4 Corrective and Preventive Action ............................................................................................................ 16 Appendix A: Overall Process Sequence & Interaction ........................................................................................ 17 Appendix B: ISO 9001:2015 Cross Reference . (18)Revision [A/0] - [2018/3/1] 0.0 Revision History and ApprovalRev. Nature of changes Approval DateA/0 Original release. XXX 2018/3/1Page 3 of 19Revision [A/0] - [2018/3/1] 1.0 Welcome to Ningbo XXX Material Technology Co.,LtdNingbo XXX Material Technology Co., Ltd. Was established in 2000, with the UAE businessmen to build the joint venture company; 2004 Ming Shan founded Nissin special adhesive tape and adhesive tape company; 2008 due to the strategic adjustment of 3 company merger and reorganization, the establishment of Ningbo letter mountains adhesive products Manufacturing Co., Ltd..PVC insulation tape is one of China’s national standard drafting unit, the field of adhesive products governing unit of China, Ningbo, adhesives and related products Industry Association, honorary president of the unit.We produce more than 1000 varieties of products of 11 categories. The annual throughput more than 100,000,000 square of the adhesive and 10,000 ton of the adhesive.Our company located in Ningbo which the city of the east China sea, beside 500 kilometers of shanghai, 20 kilometers from Ningbo list airport and 50 kilograms of the Ningbo seaport. The transport is very convenient (Easy to ship to everywhere on the world).2.0 XXX Material: Who We Are2.1 Determining Our Strategic DirectionXXX Material has reviewed and analyzed key aspects of itself and its stakeholders to determine the strategic direction of the company. This involves:∙Understanding our core products and services, and scope of management system (see 2.2 below).∙Identifying “interested parties” (stakeholders) who receive our [Production of adhesive tape], or who may be impacted by them, or those parties who may otherwise have a significant interest in our company. These parties are identified in the document [Requirements and expectations list of interested parties].∙Understanding internal and external issues that are of concern to XXX Material and its interested parties; also identified in the document [Requirements and expectations list of interested parties]. Many such issues are identified through an analysis of risks facing either XXX Material or the interested parties. Such issues are monitored and updated as appropriate, and discussed as part of management reviews.This information is then used by senior management to determine the company’s strategic direction. This is defined in records of management review, and periodically updated as conditions and situations change.2.2 Scope of the Management System2.2.1 Scope StatementBased on an analysis of the above issues of concern, interests of stakeholders, and in consideration of its products and services, XXX Material has determined the scope of the management system as follows:Production of adhesive tapePage 4 of 19Revision [A/0] - [2018/3/1]Page 5 of 192.2.2 Facilities Within the ScopeThe quality system applies to all processes, activities and employees within the company. The facility is located at: Factory Add :XXX Tel :XXX Fax :XXX XXX XXX2.2.3 Permissible ExclusionsThe following clauses of ISO 9001 were determined to be not applicable to XXX Material.∙ 8.3 Design and development of products and services 2.2.4Scope of the ISO9001:2015 Quality ManualThis manual is prepared for the purpose of defining the company’s interpretations of the ISO 9001:2015 international standard, as well as to demonstrate how the company complies with that standard.This manual does not follow the numbering structure of ISO 9001. Instead, Appendix B presents a cross reference between the sections of this manual and the clauses of ISO 9001:2015.This manual presents “Notes” which are used to define how XXX Material has tailored its management system to suit its purposes. These are intended to clarify implementation approaches and interpretations for concepts which are not otherwise clearly defined in ISO 9001:2015. Notes appear in italics, with gray background.Where subordinate or supporting documentation is reference in this manual, these are indicated by bold italics .∙ Quality PolicyThe Quality Policy of XXX Material is as follows:Quality first, customer satisfaction;Scientific management, continuous improvement. ∙ Management SystemStructure and Controls 4.1Process Approach4.1.1 Process IdentificationXXX Material has adopted a process approach for its management system. By identifying thetop-level processes within the company, and then managing each of these discretely, this reduces the potential for nonconforming [Production of adhesive tape] discovered during final processes or after delivery. Instead, nonconformities and risks are identified in real time, by actions taken within each of the top-level processes.Note: not all activities are considered “processes” – the term “process” in this context indicates the activity has been elevated to a higher level of control and management oversight.The controls indicated herein are applicable only to the top-level processes identified.。
ISO9001质量手册-中英文版
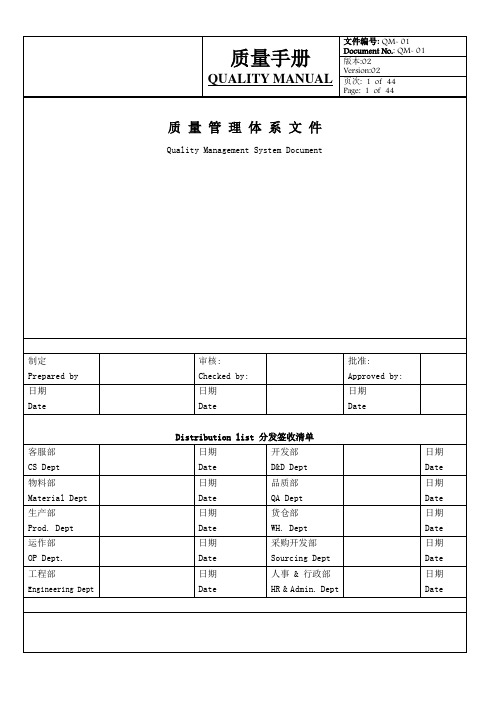
2. 引用标准………………………………………………………………………………….7 Normative reference
3. 术语和定义……………………………………………………………………………….7-8 Terms
4. 质量管理体系 Quality management system 4.1 总要求……………………………………………………………………………….8-9 General requirements 4.2 文件要求…………………………………………………………………………….9-11 Documentation requirements
开发部
Date
D&D Dept
日期
品质部
Date
QA Dept
日期
货仓部
Date
WH. Dept
日期
采购开发部
Date
Sourcing Dept
日期
人事 & 行政部
Date
HR & Admin. Dept
日期 Date 日期 Date 日期 Date 日期 Date 日期 Date
Revision History 修订记录
E. 主要产品 Main products: 手袋及其它缝纫制品。
Bags and other sewing products. F. 主要生产流程 Main production processes:
开料→贴合/热压/电压/烫画→车缝→包装 Cutting→Lamination/Thermoforming/High frequency/Transfer sticker→Sewing→Packing G. 主要生产设备 Main production equipment: 裁床、贴合机、热压机、电压机、针车等. Cutting machine, lamination machine, thermoforming machine, high frequency machine, sewing machine, etc. H. 主要测试仪器 Main measuring devices: 盐雾试验机、破裂强度测试仪、卡尺、硬度计、千分尺、拉力计、推拉力计、电子天平、验 布机及及其它布料测试设备等. Salt spray test machine, broken strength tester, caliper, hardness tester, microscope, pull gage, push-pull gage, electronic weight scale, fabric inspection machine and other fabric testing equipment.
ISO 9001质量手册英文版(ISO 9001 Quality Manual)

ISO 9001:2000 QUALITY MANUALWOLSTENHOLME INTERNATIONAL LIMITEDCONTENTS1.0 Scope of the Quality Management System at Wolstenholme International Limited 1。
1 Statement of Quality Policy2。
0 Quality Management System Documented Procedures2.1 Document Control2。
2 Control of Quality Records2.3 Internal Quality Audits2。
4 Control of Nonconforming Product2.5 Corrective Action2.6 Preventative Action3.0 Quality Management System Processes and Interrelations3。
1 Organisation Charts3.2 Responsibilities3.3 Interrelation of Processes3.4 Processes1。
0 Scope of the Quality Management System at Wolstenholme International LimitedWolstenholme International Limited is a Company with a long—standing successful history of supplying metal powders, pastes, pellets, varnish, offset ink, flexography ink and other related products for use in a large range of applications, on a worldwide basis. The scope of the Quality Management System encompasses all activities on the Darwen Site.The Metallic Powders Operation at Darwen is responsible for the manufacture and supply of metal powders and pigments mainly in aluminium, copper and brass (bronze) based alloys, for use in printing, inks, plastics and other industrial and engineering applications.The Ink Operation at Darwen is responsible for the manufacture of a wide range and type of printing ink, 'one—pack' gold ink, varnish and related printing products。
ISO9001:2015版质量手册(完整)
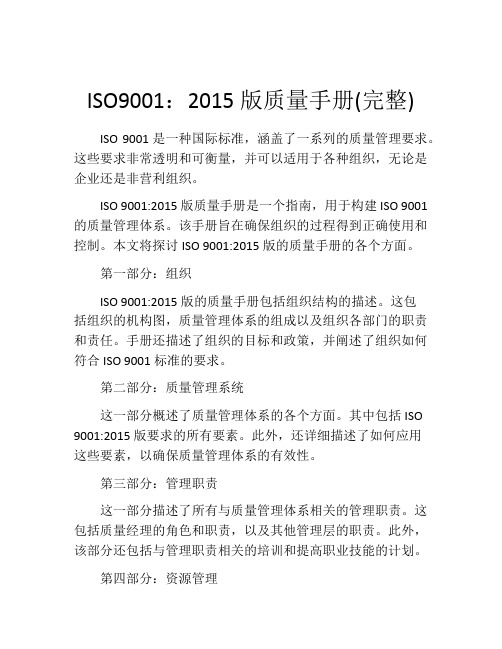
ISO9001:2015版质量手册(完整)ISO 9001是一种国际标准,涵盖了一系列的质量管理要求。
这些要求非常透明和可衡量,并可以适用于各种组织,无论是企业还是非营利组织。
ISO 9001:2015版质量手册是一个指南,用于构建ISO 9001的质量管理体系。
该手册旨在确保组织的过程得到正确使用和控制。
本文将探讨ISO 9001:2015版的质量手册的各个方面。
第一部分:组织ISO 9001:2015版的质量手册包括组织结构的描述。
这包括组织的机构图,质量管理体系的组成以及组织各部门的职责和责任。
手册还描述了组织的目标和政策,并阐述了组织如何符合ISO 9001标准的要求。
第二部分:质量管理系统这一部分概述了质量管理体系的各个方面。
其中包括ISO 9001:2015版要求的所有要素。
此外,还详细描述了如何应用这些要素,以确保质量管理体系的有效性。
第三部分:管理职责这一部分描述了所有与质量管理体系相关的管理职责。
这包括质量经理的角色和职责,以及其他管理层的职责。
此外,该部分还包括与管理职责相关的培训和提高职业技能的计划。
第四部分:资源管理ISO 9001:2015版的质量手册的这一部分强调了所有必要的资源,以确保质量管理体系的有效实施和运行。
这包括人员,物资,技术资源以及财务和时间资源的分配。
第五部分:产品/服务管理这一部分描述了如何通过质量管理体系的有效实施来管理产品和服务的生命周期。
包括计划,开发,生产/提供,交付以及售后服务的管理。
第六部分:监测与分析ISO 9001:2015版的质量手册的这一部分描述了如何实施监测和分析系统,以确保质量管理体系的有效性。
这包括如何收集数据,如何分析数据以及如何采取行动,以改进质量。
第七部分:行动计划这一部分描述了如何建立和实施行动计划,以改进质量管理体系的效率和有效性。
这包括如何确定和跟踪关键绩效指标(KPI),如何识别和纠正问题以及如何确保所采取的行动得到正确实施。
ISO9001:2015质量手册英文版(按标准条款)

ISO 9001:2015Quality ManualA quality manual is a document that states the company’s intentions for operating the processes within the quality management system. It can include policies for all areas of the business that affect your ability to make high-quality products and meet your customers’ and ISO’s requirements. These policies define how your department managers will implement procedures within the boundaries specified in the quality manual. The use of Quality Manual are as follows:1.To communicate management’s expectations to employees2.To demonstrate the company’s plan to conform to therequirements of ISO 9001:20153.To demonstrate the fulfilment of Clause 5.3, thatorganizational roles, responsibilities and authorities are assigned, communicated and understood4.To provide a starting point for auditors:1.Internal2.Customer3.ISO Certification BodyTo develop a quality manual, you might consider these steps: 1.List policies to be written (note any ISO requirements thatdo not apply).2.Draft policies based on applicable ISO requirements.3.List operating procedures or refer to them as appropriate.4.Determine the format and structure of the manual andmake the first draft.5.Circulate the draft manual for input from all departmentsand address inadequacies identified.6.Attain a formal approval and release.The contents of your quality manual are completely up to you. But, remember that everything you say you do, you must show evidence that you really do it! So be careful what you include and make sure the policies reflect actual practices. Here are some common topics included in quality manuals.the scope of QMSQuality policyExplanation of the company’s documentation structureOrganizational chartPolicy statements for each applicable ISO requirementReference to operating procedures1) The scope of the Quality Management System. This is in place to identify the limit of the system and is based on the scope agreed with the registrar to be placed on the ISO9001 certificate. This is the explanation of what your company does, be it “Design and Manufacture of the bevel Gear,” “Machining Services for Customers in the oil and service Industry,” or “Providing Fast Food for People in Kuwait city.” The second part of the scope requirement is to identify any exclusions from the standard. In many cases, the Quality Manual will identify none, but the most common exclusion is the requirement of the ISO 9001 standard for “Design & Development” for companies such as a machining shop, which works exclusively from customer drawings and does not design any products itself.2) The documented procedures established for the Quality Management System (or references): ‘Documentation’ means anything written down or captured in some form such as written procedures, policies, checklists, forms, or graphics, drawings, flowcharts, diagrams, IT systems. This is called ‘documentedinformation’ in the current version (2015) of ISO 9001. Confusingly, they have also decided to use the same term for what was formerly called ‘records’ – those things that showed what had been done, such as registers, logs, competed for forms, reports, meeting minutes and so on. ‘Documented information’ in 9001 terms means both the ‘written stuff’ that describe your quality system and say how it should operate (eg, flowcharts, procedures, policies, checklists) and the ‘written stuff’ that shows what was done. A system must be documented to achieve ISO 9001 certification because having certain documented information is required by the Standard. All the documents t needs to control how things are done, whether procedures, flowcharts, checklists, forms, IT systems or any other media or format that work in your business. But note that no mandatory procedures are prescribed. Nor a quality manual. What can confuse people is that actually, you can choose what your documents look like, what format and structure you use, and what to put in them. Provided you meet these requirements. You can use one or many formats, from checklists and flowcharts to intranets, wikis or workflow embedded into IT systems. You can use any media, hardcopy or soft, including intranet, online, internet or wiki. One often used way to do that was with a thingcalled a ‘quality manual’. And you can still do that if you choose. And it can be in hard copy (paper) or softcopy: online documents like web pages, help files or IT systems. And you can write your document in various ways, from easy and user-friendly to bureaucratic, verbose and very hard to follow. And such a manual may be the only document you have for your system, or it may be one of a number of documents. Or something in between.3) A description of the interaction of processes. This is most simply done with a flowchart that identifies all the processes in the organization with arrows showing how they connect. While an in-depth flowchart may help you to better understand the interactions between processes in your organization, a simple top-level flowchart is all that is needed for most people to understand the basics. Example of Quality Manual1.0 Company ProfileInclude your company profile1.1 The mission of the FirmOur mission is to enhance mobility through innovation, leadership and public service. Innovation by providing unparalleled value combined with flexibility and risk-taking ability, leadership by delivering exceptional performance in every domain and corporate responsibility through service to society.1.2 The vision of the FirmTo strive relentlessly with an aim to achieve excellence in all businesses that we venture into, with the objective of becoming an organization that all its employees and associates are proud of.2.0 Organization ScopeDesign, Development of Land, Construction Sales of Residential and Commercial Complexes2.1 Exclusions:NIL2.1 Quality PolicyXXX is committed to delivering quality construction work with promised amenities, in time possession, which meets and exceeds the needs & expectation of our customers. We promise our valued customer’s commitment to excellence in each activity by each employee in the organization by adopting innovative and best in class engineering and management practices with continual improvement in business and quality management system as a part of our efforts for enhancement in customer satisfaction while assuring 100% quality and quantity.2.2 Key ObjectivesTimely completion of projectsIncrease Customer satisfactionReduce Customer Complaint3.0 Glossary & Abbreviations4.0 Context of Organization4.1 Understanding the organization and its context: Shah Promoters and Developers determine external and internal issues that are relevant to its purpose and its strategic direction and that affect its ability to achieve the intended result(s) of its quality management system through PEST and SWOT. The external and internal issues identified throughPEST and SWOT are continuously being monitored and reviewed by CEO.PESTSWOT4.2- Understanding the needs and expectations of interested partiesxxx has determined the interested parties who are relevant to the xxx Quality management system and the requirement of the interested parties in order to prevent the potential effect on the organization’s ability to consistently provide products and services which meet the customer and applicable statutory and regulatory requirements.4.3 Determining the scope of the quality management systemThe organization had determined the scope of the Quality management system by considering external and internal issues, the requirement of relevant interested parties and Product & Service of the organization.The scope of Quality Management System isDesign, Development of Land, Construction Sales of Residential and Commercial ComplexesExclusions:NIL4.4 Quality management system and its processes4.4.1: xxx has determined the processes needed for the quality management system and their application throughout the organization in Process map & Interactions of processes.xxx has determined the inputs required and the outputs expected from each process in individual process map addressed in the documented information of each process.xxx has determined the sequence and interaction of the processes in Process map & Interactions of processes.xxx has determined and applied the criteria and methods (including monitoring, measurements and related performance indicators) needed to ensure the effective operation and control of these processes in the documented information of each process.xxx has determined the resources needed for these processes and ensure their availability in the documented information of Support process.xxx has assigned the responsibilities and authorities for each processxxx has addressed the risks and opportunitiesxxx has been evaluating these processes and implementing any changes needed to ensure that these processes achieve their intended results and improve the processes and the quality management systemImprove the processes and the quality management system4.4.2- xxx is also maintaining documented information to support the operation of its processes and retaining documented information to have confidence that the processes are being carried out as planned.5.0 Leadership5.1 Leadership and commitmentXxx Management has demonstrated leadership and commitment with respect to the quality management system through1.Taking accountability for the effectiveness of the qualitymanagement system by periodical review of qualitymanagement system through management review meeting, Quality objectives review and providing necessary resources.2.Management has established the quality policy andquality objectives for the quality management system and is compatible with the context and strategic direction of the organization.3.Management has determined the organizationalprocesses and integrated with the quality management system requirement through process map & Interaction this can be demonstrated.4.The established procedure for promoting the use of theprocess approach and risk-based thinking.5.Ensuring that the resources needed for the qualitymanagement system are available, this is being periodically reviewed through management review meeting.municating the importance of effective qualitymanagement and of conforming to the quality management system requirements7.Ensuring that the quality management system achievesits intended results8.Engaging, directing and supporting persons to contributeto the effectiveness of the quality management system by providing training, conducting awareness programs and 9.Promoting improvement by introducing the suggestionscheme, Kaizens and conducting meetings.10.Supporting other relevant management roles todemonstrate their leadership as it applies to their areas of responsibility.5.1.2 Customer focusXxx management has demonstrated leadership and commitment with respect to customer focus by ensuring that: 1.Customer and applicable statutory and regulatoryrequirements are determined, understood and consistently met.2.The risks and opportunities that can affect conformity ofproducts and services and the ability to enhance customer satisfaction are determined and addressedc) The focus on enhancing customer satisfaction is maintained and procedure for customer satisfaction is addressed5.2 QUALITY POLICYXXX is committed to delivering quality construction work with promised amenities, in time possession, which meets and exceeds the needs & expectation of our customers. We promise our valued customer’s commitment to excellence in each activity by each employee in the organization by adopting innovative and best in class engineering and management practices with continual improvement in business and quality management system as a part of our efforts for enhancement in customer satisfaction while assuring 100% quality and quantity. We are also committed to serving society as a whole by generating through clean development mechanism (CDM) project.5.2.1 Establishing the quality policyXxx management has established, implemented and maintained a quality policy that:1.is appropriate to the purpose and context of theorganization and supports its strategic direction.2.Provides a framework for setting quality objectives3.Includes a commitment to satisfy applicable requirements4.Includes a commitment to continual improvement of thequality management system5.2.2 Communicating the quality policyThe quality policy is1. Available and be maintained as documented informationmunicated, understood and applied within theorganization through display, Training and periodical review.3.Available to relevant interested parties, as appropriate. 5.3 Organizational roles, responsibilities and authoritiesXxx management has ensured that the responsibilities and authorities for relevant roles are assigned communicated and understood within the organization. While assigning roles, responsibility and authority, top management has considered and ensured that1.The quality management system conforms to therequirements of this International Standard2.The processes are delivering their intended outputs3.Reporting on the performance of the quality managementsystem and on opportunities for improvement, in particular, to top management4.The promotion of customer focus throughout theorganization5.The integrity of the quality management system ismaintained when changes to the quality management system are planned and implemented.Roles, responsibility and authorities assigned are available in process & as per Organization chart wiseDirectorsResponsibilityOverall Responsibility for formulating and communicating Quality Policy & Quality objectives.Formulation of Strategy for continuous up gradation of Business and Quality System.Ensure periodic assessment of the performance of Quality System.Approval of Quality System Manual.Budget Approval for the organization.Overall Responsibility for Business Development & all financial issues.Provision of resources as required.Strategic decisions on developments and technical setups. To provide the leadership for efficient implementations of the system.Authorities:Approval of customers orders, P.O. and Cheque.Sanctioning leaves of all Staff.Approval of funds for Training needs.All the authorities of downline personnel.Chairing Management review meetings.Project PlanningResponsibilities:Overall coordination between client, project managers and office department.Follow up for Schedules.The entire responsibility of Quality.Monitoring Client Satisfaction.Coordination with the consultants.Disciplinary actions against the staff.Prime responsibility for the safety at the siteProvision of a suitable working environmentEnsure the quality system is established, implemented and maintained.Authorities:Appointment of the staff, engineers and tech staff.Sanctioning the Leaves to Staff.All the authorities of downline personnel.Project ManagersResponsibilities:Responsibilities for the entire Project work, i.e. Quality, Quantity and Time.Coordination with consultants and contractors.Coordination with Consultants for drawings.Coordination with the Site engineers.Coordination with the client for the ongoing changes in drawings and projects.Monitoring site engineers work on a daily basis.Reporting to the GM Projects on the above issuesResponsibilities for safety at the site. (Good working environment).Authorities:Make or force a required decision at all levels to achieve project objectives.Initiate actions on the Contractors and consultants for Quality, Quantity and Timeframe issues related to project work.To stop and initiate corrective actions on non–confirming products/services.Site SupervisorResponsibilities:Coordinating with all staff for the Quality related issues of Construction.Daily Labour Handling for Civil Work.Monitoring of Work progress and daily reporting.Preparation of work progress report / Quality Documentation.Control of non – conformities on siteSafety at site / Construction work.Coordination with the Site Contractor for the daily work requirements.Coordination with external agencies for calibration of instruments and material testing.Authorities:Initiate actions on the staff for non-fulfillments of the documentation related qualityTo stop and initiate corrective actions on non–conforming products.Site engineerResponsibilities:Monitoring of site and labour contractors.Monitoring of work progress and daily reportingPreparation of work progress report.Control of non – conformities on site.Ensuring instruments are properly used and are with the status of calibration.Track Project progress & produce regular weekly status reports.Coordinate with all labour contractors to achieve continuous progress at the site as per schedule.Follow up with the Project manager for pending decisions/drawings/building specifications.Communicate management decisions and information to Site subordinate staff.Ensuring the worker’s safety at site and usage of safety equipment.Implementation and follow up and regular monitoring of implemented ISO 9001 system at the site.Coordination with the Quality Person for Quality related issues.Coordinating Material Accountability at siteAuthorities:Initiating the corrective and preventive actions as needed on contractors and consultants.Decision making on during any emergencies at the site.In-charge Marketing:Managing & motivating the sales force towards the achievement of target.Preparation of Sales plan.Annual sales forecast.Monthly sales forecast.Implementation of sales plan.Authorities:Approval of documents as per the Master list of Quality System Document.Authorized to decide corrective & preventive action.Authorized to obtain concessional acceptance for non – conforming product from the customer.InCharge – ADMIN + ACCOUNTResponsibilities:Responsible for tendering activity.Customer order review.Handling and coordinating customersIdentification of resources, as applicable.Document & Data control system pertaining to his department.Maintain all documents related to the quality system.Coordinator for Management reviews.Promoting awareness of customer requirements throughout the Organization.Compliance & effectiveness of the training system.Suitable working environment (cleanliness, ventilation, lighting, safety etc.).Record maintaining for Sales Register, Rent Register, Sale Files, Stationery and Office equipment.Archiving and record keeping of old files.Payroll Monthly: Salary –To release monthly salary of the employees as per policy finalized.Leave – To keep the record of leave as per policy finalized.Annual Allowance – To release annual allowances as per policy finalized.Employee Record – To update employee details as per organization Policy and QMS.To prepare an appointment letter, confirmation letter, experience letter & all employee-related matter as per policy finalized with the help of the Managing Director.Authorities:Approval of customer orders.Approval of documents as per the master list of Quality System Document.Authorized to decide corrective & preventive action.In charge Purchase:Responsibilities:Overall in charge of purchase activities.Identification of resources, as applicable.Purchasing system – Evaluation, selection, purchasing, monitoring.Document & Data control system pertaining to his department.Corrective / Preventive action system (subcontractor non-conformances, in particular.)Control of recordsAuthorities:Authorized to review & approve purchasing documents.Authorized to select & discontinue sub-contractor6.0 Planning6.1 Actions to address risks and opportunities6.1.1Xxx is addressed the issues, requirements the risks and opportunities1.give assurance that the quality management system canachieve its intended result(s)2.Enhance desirable effects3.Prevent, or reduce undesired effects4.achieve improvement6.1.21.actions to address these risks and opportunities2.How to1.integrate and implement the actions into its qualitymanagement system processes2.Evaluate the effectiveness of these actions6.2.2 Quality objectives and planning to achieve them 6.2.1Xxx establish quality objectives at relevant functions, levels and processes needed for the quality management system.The quality objectives shall1.Be consistent with the quality policy2.Be measurable3.Take into account applicable requirements4.Be relevant to the conformity of products and services andto the enhancement of customer satisfaction5.Be monitored6.Be Communicated7.Be updated as appropriate6.2.2 Xxx achieve its quality objectives,1.What will be done?2.What resources will be required?3.Who will be responsible?4.When it will be completed5.How the results will be evaluatedOur Quality Objectives are as below:Timely completion of projectsEnergy Generation Per YearIncrease Customer satisfactionReduce Customer Complaint6.3 Planning of changesXxx determines the need for changes to the quality management system, the changes are carried out in a planned manner1.the purpose of the changes and their potentialconsequences2.the integrity of the quality management system3.the availability of resources4.the allocation or reallocation of responsibilities andauthoritiesXxx has determined the processes needed for the quality management system and their application throughout the organization in Process map & Interactions of processes7 Support7.1 Resources7.1.1 GeneralXxx is determined and provide the resources needed for the establishment, implementation, maintenance and continual improvement of the quality management system. Xxx is consider1.the capabilities of, and constraints on, existing internalresources2.what needs to be obtained from external providersHR determine and provide the resources needed to implement and maintain the quality management system and continually improve its effectiveness and to enhance customer satisfaction by meeting customer requirement. The resources will be in the form ofHuman resources including qualified personnel for verification activities.Manufacturing machines, Test Equipment’s &infrastructure.Provide raw material & other inputs for the realization of the product.Providing funds.The Required resources are identified in the event of new Process Development / Business plan review, Mfg Process Flow, also based on the Organization performance review in MRM and monthly business reviews.7.1.2 PeopleXxx determine and provide the persons necessary for the effective implementation of its quality management system and for the operation and control of its processes. HR along with respective process IN CHARGE ensures that personnel performing work affecting product quality is competent and training to give on the basic operation and control of its processes.7.1.3 InfrastructureXxx is determined, provide and maintain the infrastructure necessary for the operation of its processes and to achieve conformity of products and services. Infrastructure can include1.buildings and associated utilities2.equipment, including hardware and software3.transportation resourcesrmation and communication technologyAt Xxx management determine, provide and maintain the infrastructure needed to achieve conformity to product requirements & in identifying the required resources the PARTNER play a key role based on their day to day interactions with respective IN CHARGE’s and employees 7.1.4 Environment for the operation of processesXxx is determined, provide and maintain the environment necessary for the operation of its processes and to achieve conformity of products and services. A suitable environment can be a combination of human and physical factors1.Social (e.g. non-discriminatory, calm,non-confrontational)2.Psychological (e.g. stress-reducing, burnout prevention,emotionally protective)3.Physical (e.g. temperature, heat, humidity, light, airflow,hygiene, noise).Project in coordination with respective IN CHARGE determines and manages the work environment needed to achieve conformity to product requirement and reviewed ongoing basis.7.1.5 Monitoring and measuring resources7.1.5.1 GeneralXxx is determined and provide the resources needed to ensure valid and reliable results when monitoring or measuring is used to verify the conformity of products and services to requirements. The organization shall ensure that the resources provided1.are suitable for the specific type of monitoring andmeasurement activities being undertaken2.are maintained to ensure their continuing fitness for theirpurposeXxx is retained appropriate documented information as evidence of fitness for purpose of the monitoring and measurement resources7.1.5.2 Measurement traceabilityXxx is measurement traceability is maintained requirement if applicable for the instruments or is considered by them to be an essential part of providing confidence in the validity of measurement results,1.calibrated or verified, or both, at specified intervals, orprior to use, against measurement standards traceable to international or national measurement standards; when no such standards exist, the basis used for calibration or verification shall be retained as documented information2.identified in order to determine their status3.safeguarded from adjustments, damage or deteriorationthat would invalidate the calibration status and subsequent measurement resultsXxx is determined the validity of previous measurement results has been adversely affected when measuring equipment is found to be unfit for its intended purpose, and shall take appropriate action as necessary.Control of Monitoring & Measuring Equipments. Measurement & Monitoring system is well equipped and the system has complete control over the monitoring andMeasuring Equipment. The measurement methods used are evaluated to ensure that they are appropriate and reliable. To ensure that the measuring equipment operates effectively and give reliable results, we have taken the following steps:Equipments are maintained properly and are calibrated & adjusted as and when needed. Necessary safeguards are in place to take care of adjustments that could lead to invalid results.Calibrations are carried out as per national standards (by NABL accredited laboratories only). Where no such standard exists, the basis used for calibration or verification is recorded. The calibration records include the last date of calibration, calibrating agency (for the external agency), calibration result, and frequency of calibration as per the process and/or instrument requirement and the next calibration date. The required accuracy is identified and compared to the measurement that meets expectations. Identification of appropriate equipment is accomplished by tagging, labelling, numbering or by including it in a calibration/maintenance database.。
ISO9001:2015一整套程序文件-英文版

Quality System Procedures(ISO 9001:2015)GENERAL INFORMATION Name of the Organisation:Address:E-Mail:Web:QUALITY SYSTEM STATUSQuality System:ISO 9001: 2015 Issue No.:01Issue Date: System Effective Date:December 2017 December 2017Copy No.:01LIST OF CONTENTSection-1 Control of DocumentSection-2Control of RecordsSection-3Management Review MeetingSection-4Resource ManagementSection-5Customer Related ProcessSection-6Purchase ProcessSection-7Supplier Evaluation and Selection Process Section-8Service ProcessSection-9Receipt Storage and Issue of Product Section-10Customer SatisfactionSection-11Internal AuditSection-12Control of Nonconforming Product Section-13Analysis of dataSection-14Continual ImprovementSection-15Corrective Action and Preventive ActionSection-1Control of Documents1.0Purpose1.1To establish a procedure to ensure that the documents required for Quality ManagementSystem are in controlled condition.1.2To ensure that pertinent versions of documents are available at the point of use.2.0Scope2.1Applicable to all documents and data generated for Quality Management System via theProcedures, Work Instructions, Documents, Lists, Formats and Registers etc.2.2This procedure also covers the external origin documents such as Standards and CustomerDocuments.3.0Responsibility3.1 Management Representative is responsible for controlling all the documents of Quality ManagementSystem being originated internally and the documents from External origin.3.2 It is the responsibility of Management Representative to ensure that pertinent documents are available atpoint of use.4.0Procedure4.1The numbering of all Quality Management System documents is done as per the Annexure.4.2Document Generation / Creation4.2.1 Management Representative issues the copies of the Quality System Manual / Procedures /Guidelines / Formats to all concerned personnel and records in Issue Control Register.4.2.3Any Departmental member, who perceives the need for a new quality system documentfor upgrading the system, prepares a draft procedure and forwards it to the ManagementRepresentative.4.2.3Management Representative studies the possibility of modifying any existing procedurein consultation with approving authority or accepts the draft procedures with or withoutmodifications and approves it before issue.4.3Document Change / Modification4.3.1Changes / Modification in document arises in any one of the following area;A.Change in Organization structureB.Any change in the departmental functioningC.Change in / addition / deletion of existing systemD.Change in International / National StandardsE.Findings of Internal Quality Audit4.3.2Departmental members prepares Document Change Request and forwards it toManagement Representative4.3.4 If the changes are acceptable, Management Representative makes necessary changes in thedocumentation and gets it signed by the concerned authority.4.3.5If the document is added or deleted, all linked procedures are updated in theAmendment Record Sheet.4.3.6While issuing the revised copies to all concerned, Management Representative ensures thatthe obsolete documents are retrieved back from all personnel and the same are destroyed.The respective Master copy is stamped as “OBSOLETE” and maintained for a period of oneyear from the date of next revision or till the next revision, which ever is later.4.3.7The Issue No. will be incremented when number of revisions in any section/page ofdocument exceeds 09 revisions. The Issue No. will be TBA…etc. and Revision No. of all thesection / pages shall be reset to 004.4Management Representative shall maintain and update the Master List of Documents.4.5The document status shall be maintained as follows:MASTER“MASTER COPY”(Seal affixed on rear side of each page of document)CONTROLLED“CONTROLLED COPY”(Seal affixed on front right hand side of the document)OBSOLETE“OBSOLETE COPY”(Seal affixed on front side of the document)4.6 The approval authority for various documents is as mentioned below:Document Type Description Approved by Apex ManualProceduresDocument Type Description Approved byGuidelines & Formats As per Master List of Documents4.7External Originated Documents (National / International Standards And Customer Drawings)4.7.1Documents of National / International Standards / any other Guidelines are procured, revisedand implemented by Management Representative.4.7.2 A List of External Origin Documents is maintained by Management Representative and willbe updated whenever necessary.4.7.3All the standards are stamped as “CONTROLLED COPY” on the cover page of the standardand issued to the concerned by making necessary entries in Issue Control Register.4.7.4Documents of customers / suppliers are maintained only after receiving concrete ordersfrom them. If the order does not mature, the documents are either destroyed or returned tothem as the case may warrant.5.0Reference5.1Issue Control Register5.2Document Change Request5.3Amendment Record Sheet5.4Master List of Documents5.5List of External Origin DocumentsAnnexureNumbering System shall be as follows1.Quality System ManualAAG/QSM-XX, whereAAG–refers to the company, AAG Land SurveyQSM–refers to Quality System ManualXX–refers to Section No.2.Quality System ProceduresAAG/QSP/YYAAG–refers to the company, AAG Land SurveyQSP–refers to type of proceduresQSP – Quality Management System ProceduresYY–refers to running Serial Number of procedures3.Documents & RecordsAAG-AXX:YYAAG–refers to the company, AAG Land Survey。
ISO9001质量手册英文版

ISO9001质量手册英文版WOLSTENHOLME INTERNATIONAL LIMITEDCONTENTS1.0 Scope of the Quality Management System at Wolstenholme Internatio nal Limited1.1 Statement of Quality Policy2.0 Quality Management System Documented Procedures2.1 Document Control2.2 Control of Quality Records2.3 Internal Quality Audits2.4 Control of Nonconforming Product2.5 Corrective Action2.6 Preventative Action3.0 Quality Management System Processes and Interrelations 3.1 Organisation Charts3.2 Responsibilities3.3 Interrelation of Processes3.4 Processes1.0 Scope of the Quality Management System at Wolstenholme International LimitedWolstenholme International Limited is a Company with a long-standing succe ssful history of supplying metal powders, pastes, pellets, varnish, offset ink, flexog raphy ink and other related products for use in a large range of applications, on a w orldwide basis. The scope of the Quality Management System encompasses all acti vities on the Darwen Site.The Metallic Powders Operation at Darwen is responsible for the manufacture and supply of metal powders and pigments mainly in aluminium, copper and brass (bronze) based alloys, for use in printing, inks, plastics and other industrial and eng ineering applications.The Ink Operation at Darwen is responsible for the manufacture of a wide ran ge and type of printing ink, 'one-pack' gold ink, varnish and related printing produc ts.All production processes at Darwen are validated before leaving the site and a s such sub-clause 7.5.2 is excluded.The overall operation at Darwen is controlled by the Ink & Print business unit and the Industrial business unit.Technical Service and Research and Development are vital to the future devel opment of the Company, together with understanding and developing new products and applications for our customers.The manufacturing, technical and administration functions of the Company ar e based in Darwen, Lancashire, England and employ some 210 staff at that locatio n.Through the application of Quality Management Systems and Company wide t raining programmes, Wolstenholme International Ltd. is committed to ensuring con tinuous improvements to both its processes and product technology.WOLSTENHOLME INTERNATIONAL LTD.QUALITY POLICYWolstenholme International Limited is committed to the provision of customer satisfaction. Quality in everything we do is the central ingredient in the above com mitment. Our commitment goes beyond maintaining a quality system which fully c omplies with the requirements of BS-EN-ISO 9001. We are committed to achievin g, maintaining and improving overall organisational performance and capabilities b y the application of the principles outlined in BS-EN-ISO 9004:2000We will maintain and continuously improve our quality management system b y the setting of measurable quality objectives throughout the organisation and vigo rous internal audits. We will review our performance at regular management review s. Additional inputs to these reviews will also include customer feedback, process p erformance and product conformance. The prime output of the review will be to ens ure continuing customer satisfaction and improvement of products.As part of this commitment we will identify and meet the training needs of our employees, so ensuring that the needs of our customers are met. This Policy will b e made available throughout our organisation to ensure that the commitment to our customers is clear and widely understood.Chris Ravenscroft Managing DirectorControl of Quality RecordsAll quality records will be maintained and controlled. The records will be legi ble and stored in such a manner as to protect them from damage, loss and deteriorat ion. Quality records will also be stored and clearly located in such a manner as to fa cilitate easy retrieval of information.REF: Control of Quality/ Environmental Records - WIQSP.22.3 Internal Quality AuditsInternal audits will be carried out in accordance with Company procedures and will be conducted for any of the following reasons:-(i) On a scheduled basis.(ii)2.5 Corrective Actiontomers have cause to complain or following in-progress/ final inspection. Correctiv e action requests may also be raised in an effort to improve current working practis es. Corrective actions and customer complaints will be reviewed at Management R eview Meetings.When non-conforming products or services are identified, the root cause of the problem will be investigated, corrective action taken and preventative measures ini tiated to preclude a recurrence.REF: Corrective Action - WIQSP.52.6 Preventative ActionCorrective action is taken as a result of Product or process nonconformity. It is hence a reactive measure and does not necessarily prevent further non conformancThe SARA Manager (MR) has the primary responsibility to structure the qual ity system which will involve all sections and also to ensure compliance with all qu ality system requirements.Specifically, the Management Representative is involved in areas such as:-- Drafting the policy on quality assurance of the Company along with th e Operations Director.- Setting the quality management objectives of the Company.- Reporting on the performance of the Quality System at Management Review Meetings.- Determining and reporting the principle causes of quality system non-c onformances.- Monitoring the quality system to determine where improvements are needed and monitoring the necessary corrective action.- Maintain contact with the external Registration Body on matters relating to t he operation of the Quality System.SARA Manager is responsible to the Operations Director for the upkeep and maintenance of all the ISO Systems and the Company Health and Safety Policy. Th e SARA Manager is also responsible for driving the E,H&S policies within the Co mpany.Technical DirectorsThe Technical Directors for pigments and inks are responsible to the Managin g Director .. and ink and print Director respectively for ensuring that processes and equipment are designed and developed such that product of the highest attainable q uality is produced consistently and efficiently.Human Resources and Administration ManagerThe Human Resources and Administration Manager reports to the Managing Director and is responsible for managing all aspects of the personnel function, whic h includes the facilitating, co-ordinating, recording personnel issues and training, w ithin Wolstenholme International Ltd.Ink Manufacturing ManagerThe Ink Manufacturing Manager is responsible to the Operations Director for t he control of stocks, manpower and the process necessary to produce products to th e correct specification within a given time.Sales DirectorsThe Sales Directors are responsible to the Managing Director for ensuring that customers' requirements for the sale of printing/ industrial powders, pastes, pellets, inks, varnishes and related Company products are taken, reviewed and dealt with e fficiently.UK Financial Controller and Purchasing Manager.The UK Financial Controller & Purchasing Manager is responsible to the Fina ncial Director for the effective control and reporting of manufacturing costs incurre d by the manufacturing facility at the Darwen site.There is also a responsibility to the Financial Director for the effective and eco nomic procurement of raw materials and consumables used in the business of the C ompany.Research and Development ManagersResearch and Development Managers are responsible to Technical Directors f or managing Research and Development projects, maintaining customer contact du ring the project development stages and the general running of research laboratorie s.Bronze Manufacturing Manager / Offset Ink R&D ManagerThe Bronze Manufacturing Manager and Offset Ink R&D Manager (ink operat ions) are responsible to the Technical Directors for the agreement of specifications with the customer, and ensuring that there is a facility to continuously monitor and i nspect the product to ensure that all such requirements are met.Customer Services ManagerThe Customer Services Manager is responsible to the Operations Director for t he operation of Customer Services together with a team of administrators.Production Supervision。
2015年正式版_质量手册(ISO9001-2015年)
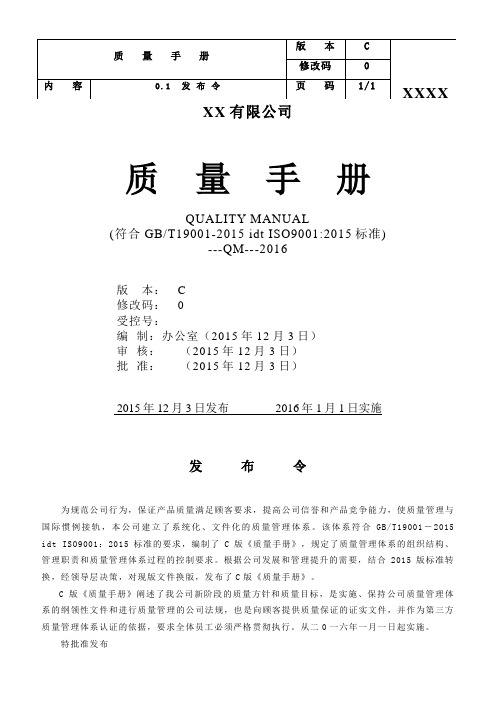
XX有限公司质量手册QUALITY MANUAL(符合GB/T19001-2015 idt ISO9001:2015标准)---QM---2016版本: C修改码: 0受控号:编制:办公室(2015年12月3日)审核:(2015年12月3日)批准:(2015年12月3日)2015年12月3日发布 2016年1月1日实施发布令为规范公司行为,保证产品质量满足顾客要求,提高公司信誉和产品竞争能力,使质量管理与国际惯例接轨,本公司建立了系统化、文件化的质量管理体系。
该体系符合GB/T19001-2015 idt ISO9001:2015标准的要求,编制了C版《质量手册》,规定了质量管理体系的组织结构、管理职责和质量管理体系过程的控制要求。
根据公司发展和管理提升的需要,结合2015版标准转换,经领导层决策,对现版文件换版,发布了C版《质量手册》。
C版《质量手册》阐述了我公司新阶段的质量方针和质量目标,是实施、保持公司质量管理体系的纲领性文件和进行质量管理的公司法规,也是向顾客提供质量保证的证实文件,并作为第三方质量管理体系认证的依据,要求全体员工必须严格贯彻执行。
从二0一六年一月一日起实施。
特批准发布2015年12月3日任命书为了贯彻执行GB/T19001-2015 idt ISO9001:2015标准的要求,加强对质量管理体系的管理,特任命同志为本组织的管理者代表。
管理者代表的职责是:a)确保质量管理体系符合标准的要求;b)确保各过程获得其预期输出;c)报告质量管理体系的绩效及其改进机会,特别向最高管理者报告;d)确保在整个组织推动以顾客为关注焦点;e)确保在策划和实施质量管理体系变更时保持其完整性。
总经理:2015年12月3日我公司为保证产品质量始终得到顾客的满意,经管理者代表组织员工按总经理对方针、目标的要求,进行了讨论,形成了公司的质量方针和目标,并经过了总经理批准。
现声明如下:1.质量方针:诚信为本以质量求生存科技创新追求行业领先水平在质量管理中,我公司认真按照GB/T19001-2015 idt ISO9001:2015《质量管理体系要求》进行质量管理,生产中严格按照顾客要求和产品标准进行生产,诚信为本,科技创新,生产出顾客满意的高附加值的机械产品。
ISO9001_2015_中英对照介绍
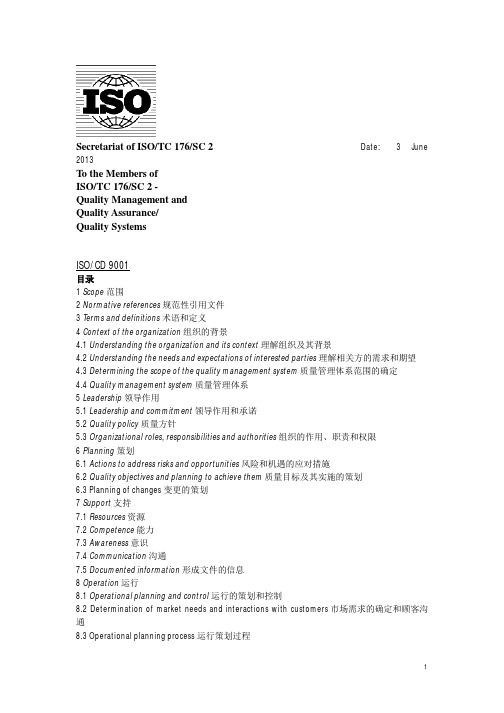
Secretariat of ISO/TC 176/SC 2Date: 3 June 2013To the Members ofISO/TC 176/SC 2 -Quality Management andQuality Assurance/Quality SystemsISO/CD 9001目录1 Scope范围2 Normative references规范性引用文件3 Terms and definitions术语和定义4 Context of the organization组织的背景4.1 Understanding the organization and its context理解组织及其背景4.2 Understanding the needs and expectations of interested parties理解相关方的需求和期望4.3 Determining the scope of the quality management system质量管理体系范围的确定4.4 Quality management system质量管理体系5 Leadership领导作用5.1 Leadership and commitment领导作用和承诺5.2 Quality policy质量方针5.3 Organizational roles, responsibilities and authorities组织的作用、职责和权限6 Planning策划6.1 Actions to address risks and opportunities风险和机遇的应对措施6.2 Quality objectives and planning to achieve them质量目标及其实施的策划6.3 Planning of changes变更的策划7 Support支持7.1 Resources资源7.2 Competence能力7.3 Awareness意识7.4 Communication沟通7.5 Documented information形成文件的信息8 Operation运行8.1 Operational planning and control运行的策划和控制8.2 Determination of market needs and interactions with customers市场需求的确定和顾客沟通8.3 Operational planning process运行策划过程8.4 Control of external provision of goods and services外部供应产品和服务的控制8.5 Development of goods and services产品和服务开发8.6 Production of goods and provision of services产品生产和服务提供8.7 Release of goods and services产品和服务放行8.8 Nonconforming goods and services不合格产品和服务9 Performance evaluation绩效评价9.1 Monitoring, measurement, analysis and evaluation监视、测量、分析和评价9.2 Internal Audit内部审核9.3 Management review管理评审10 Continual improvement持续改进10.1 Nonconformity and corrective action不符合和纠正措施10.2 Improvement改进附录A Annex A Quality management principles (Informative)质量管理原则文献1.Scope范围This International Standard specifies requirements for a quality management system where an organization本标准为有下列需求的组织规定了质量管理体系要求:a)needs to demonstrate its ability to consistently provide goods and services that meet customer and applicable statutory and regulatory requirements, and需要证实其具有稳定地提供满足顾客要求和适用法律法规要求的产品和服务的能力;b)aims to enhance customer satisfaction through the effective application of the system, including processes for continual improvement of the system and the assurance of conformity to customer and applicable statutory and regulatory requirements通过体系的的有效应用,包括体系持续改进的过程,以及保证符合顾客和适用的法律法规要求,旨在增强顾客满意。
ISO9001-2015-标准中英文
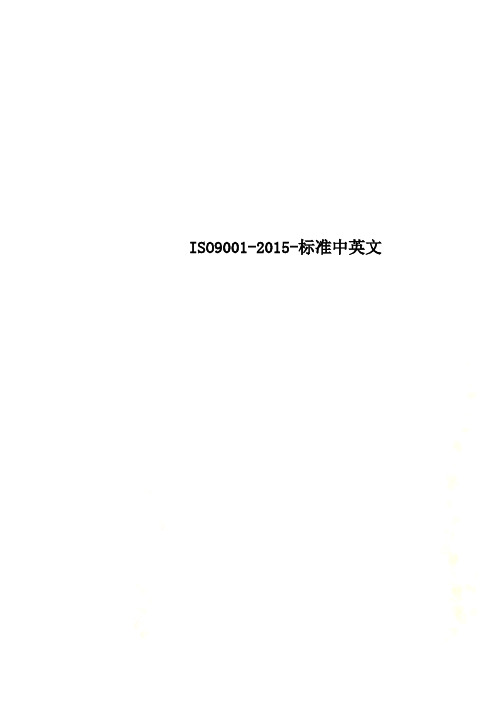
ISO9001-2015-标准中英文ISO 9001:2015Quality management systems —Requirements质量管理体系-要求Introduction引言0.1 General 总则The adoption of a quality management system is a strategic decision for an organization that can helpto improve its overall performance and provide a sound basis for sustainable development initiatives. The potential benefits to an organization of implementing a quality management system based on this International Standard are:a) the ability to consistently provide products and services that meet customer and applicable statutory and regulatory requirements;b) facilitating opportunities to enhance customer satisfaction;c) addressing risks and opportunities associated with its context and objectives;d) the ability to demonstrate conformity to specified quality management system requirements.This International Standard can be used by internal and external parties.It is not the intent of this International Standard to imply the need for:— uniformity in the structure of different quality management systems;— alignment of documentation to the clause structure of this International Standard;— the use of the specific terminology of this International Standard within the organization.The quality management system requirements specified in this International Standard are complementary to requirements for products and services.This International Standard employs the process approach, which incorporates the Plan-Do-Check-Act (PDCA) cycle and risk-based thinking.The process approach enables an organization to plan its processes and their interactions.The PDCA cycle enables an organization to ensure that its processes are adequately resourced and managed, and that opportunities for improvement are determined and acted on.Risk-based thinking enables an organization to determine the factors that could cause its processes and its quality management system to deviate from the planned results, to put in place preventive controls to minimize negative effects and to make maximum use of opportunities as they arise (see Clause A.4). Consistently meeting requirements and addressing future needs and expectations poses a challenge for organizations in an increasingly dynamic and complex environment. To achieve this objective, the organization might find it necessary to adopt various forms of improvement in addition to correction and continual improvement, such as breakthrough change, innovation and re-organization.In this International Standard, the following verbal forms are used:—“shall” indicates a req uirement;—“should” indicates a recommendation;—“may” indicates a permission;—“can” indicates a possibility or a capability.Information marked as “NOTE” is for guidance in understanding or clarifying the associated requirement.采用质量管理体系应该是组织的一项战略性决策,可以帮助组织改进其整体绩效,并为可持续发展计划提供良好的基础。
- 1、下载文档前请自行甄别文档内容的完整性,平台不提供额外的编辑、内容补充、找答案等附加服务。
- 2、"仅部分预览"的文档,不可在线预览部分如存在完整性等问题,可反馈申请退款(可完整预览的文档不适用该条件!)。
- 3、如文档侵犯您的权益,请联系客服反馈,我们会尽快为您处理(人工客服工作时间:9:00-18:30)。
Quality Management System Policy ManualISO 9001:201511-8-17Date Printed: _______________1. Quality Management System ScopeCOMPANY NAME establishes this quality policy manual to implement and maintain a quality management system meeting the requirements of ISO 9001:2015, to ensure customer satisfaction in the manufacturing ofstamped, formed, machined and fabricated metal parts, weldments, subassemblies and painting ofmetal parts to customer and COMPANY NAME specifications1.1. Non-applicable Clauses of ISO 9001:1.1.1. 8.3 Product Design & Development of Products & Services – COMPANY NAME is acustommanufacturer and designs are provided by our customers.2. Quality Policy StatementCOMPANY NAME is committed to continually improving all products and services to achieve our customer’sexpectations.We do this by:1) Living our values,2) Providing opportunities for employee involvement, motivation and training,3) Developing, documenting and following processes.3. Quality ObjectivesCOMPANY NAME’s quality management system objectives are to enable COMPANY NAME to be our customers’ first choice by:1) Achieving satisfactory ratings on quality, delivery and other key metrics tracked and reportedby our customers through their formal supplier evaluation and performance systems,2) Achieving a level of 700 ppm as tracked through COMPANY NAME’s RA system for customers without aformal supplier evaluation system for quality,3) Achieving a 95% on-time delivery to the COMPANY NAME warehouse for customers without a formalsupplier evaluation system for delivery.Policy Manual Revisions LogDate 3/22/17 8/7/17Summary of RevisionsRewrite of Quality Policy Manual to meet ISO 9001:2015.1. Revised 4.2 to include “employees”, “owners” and“regulators”.Made ByJGVJGV2. Added Figure 2 to support to support the COMPANYNAME QMSProcess Flow11-8-17 Updated to clarify risk, inputs, out puts and KPI’s forSupport and Management Process in QMS ProcessReference page (page 6)JGVManagement ApprovalName: Title: Signature: Date: Paul Gintner President4. Context of the Organization4.1. Understanding the Organization & Its ContextTop Management determines the external and internal issues that are relevant to our qualitymanagement system and its strategic direction, and that affect our ability to achieve theintended results.COMPANY NAME is a contract manufacturer in a competitive market, therefore we must maintain on-time delivery, product quality, and good customer service. Our key internal issues are to maintainproduction capacities, including competent people, capable processes, and maintainedequipment.COMPANY NAME monitors and reviews information relevant to internal and external issues throughourmanagement review meetings.4.2. Understanding the Needs and Expectations of Interested PartiesDue to their potential effect on the organization’s ability to consistently provide products thatmeet customer requirements, Top Management determines:a) The interested parties that are relevant to the quality management system;b) The requirements of these interested parties that are relevant to the quality managementsystem.COMPANY NAME’s Top Management has determined that our customers, suppliers, employees, owners (Ottertail) and regulators (OSHA) are the interested parties that we need to be concerned withand will strive to meet their needs and expectations.Top Management monitors and reviews relevant measurements and information about theseinterested parties and their relevant requirements through management review meetings.4.3. Determining the Scope of the Quality Management SystemTop Management determines the boundaries and applicability of the quality managementsystem to establish its scope. (Ref. Section 1.)When determining this scope, Top Management has considered:a) The external and internal issues referred to in 4.1.b) The requirements of relevant interested parties.c) The products and services of the organization.We apply all the requirements of the standard that are applicable within the scope of the qualitymanagement system. With only one exclusion section 8.3 Product Design & Development ofProducts & Services - (Ref. Section 1.1.1)Top Management ensures the scope of the quality management system is available andmaintained, as documented in Section 1, including the types of products and services coveredby the quality management system, and justification for any requirements determined notapplicable to the scope of the quality management system.Top Management ensures conformity to the standard(s) referred to in Section 1, and that anyrequirements determined as not applicable do not affect our ability or responsibility to ensurethe conformity of our products and services and the enhancement of customer satisfaction.4.4. Quality Management System and Its Processes4.4.1. Top Management establishes, implements, maintains, and continually improves aquality management system, including the processes needed and their interaction, inaccordance with the requirements of the standard.Top Management determines the processes needed for the quality management systemand their application throughout the organization, and:a) Determines the inputs required and the outputs expected from these processes;b) Determines the sequence and interaction of these processes (Ref. Figure 1);c) Determines and applies the criteria and methods (including monitoring,measurements, and related performance indicators) needed to ensure the effectiveoperation and control of these processes;d) Determines the resources needed for these processes and ensures their availability;e) Assigns the responsibilities and authorities for these processes;f) Addresses the risks and opportunities as determined in accordance with Section6.1;g) Evaluates these processes and implements any changes needed to ensure thatthese processes achieve their intended results;h) Improves the processes and the quality management system.Figure 1 – Quality Management System ProcessesCOMPANY NAME QMS Process FlowCustomer Feedback Captured and Utilized for Continuous Improvement and FutureQuotesQuote Provided toCustomerOutputRiskMonitoringCustomer Places OrderCustomer RequirementsEDI/Forecast Inaccuracy andorder cancelationDaily forecast and orderconfirmationInputsRiskMonitoringOutputsInputsOrder Qty, Due date and ContainerJob CreatedChanging customer orders and WC capacity limitationsDaily exception reporting and weekly WC load meetings.RiskOutputsInputsMonitoringMaterial PurchasedMaterial needs, Due Date, Work Center AssignmentCommunication with Sales Team, Supplier Performance/Report CardsMaterial availability, SupplierOTDOutputsInputsRiskMonitoringDaily Exception Reporting, Communication withProduction and Daily Planners, Weekly Load Report MeetingJob PlannedProcess JobWC Capacity, BOM Item Availability, Man PowerMaterial Delivery DateOutputsInputsRiskMonitoringProductivity, MDI data, LPA program, Safety Audit, Delivery to the Warehouse, EQCP’s , Supplier Report CardsJob scheduled, Material Delivery, WC Load, ContainersMachine, Manpower, Tooling, Safety, Process Adherence, OSS OTD, Part QualityInputsOutputsInputsRiskMonitoringProduct Placed inInventoryDelivery to the Warehouse, Preservation of product, Inventory AccuracyLabeled Product and Inspection DataMDI Data, Random Inventory Audits, FIFO processes,OutputsInputsRiskMonitoringProduct Shipped to CustomerShort/Over shipments, late shipments, Understanding Customer Ship RequirementsPicking Verification Processes and Software, Customer Ship Notes, OTD to Customer, Shipping Errors Reported byCustomerLabeled Product and Inspection Data*See Figure 2 to reference specific processes that facilitate the COMPANY NAME QMS Process FlowCustomer Uses ProductFigure 2 – Quality Management System Reference ProcessesRev:11-08-17 Core Flow Processes Support Processes Management Processes Quote Provided to Customer * LAU2-001 Product Realization PRO2-002 Non-Conforming ProductSLS2-001 Quoting * LAU2-002 Part ManufacturingQualification PRO2-004 Production PartDeviationCHN2-005 Obsolete Part * LAU2-003 Proto Process* LAU2-010 New Customer LaunchProcess PRO2-005 Corrective Action*Launch (New Product) if applicable* LAU2-006 Customer Supplier GuideReview STD2-008STD2-003STD2-007STD2-004STD2-005COMPANY NAMEManagementReviewInternal AuditCustomer Places OrderSLS2-002 Process Customer OrdersSCH2-005 SCH2-001 SCH2-006 Supplier Assessment andSelectionEstablish New VendorLayered Process AuditJob CreatedMonitoring andMeasuring of ProcessesRisk Assessment MatrixOutsourcing In-HousePainted PartsMaterial PurchasedPRO2-008 Master Planning of DirectMaterialsHRE2-004 Onboarding EmployeesSHP2-002 Receive Material orService CHN2-001 ECN Engineering ChangeNotificationSCH2-004 Purchase IndirectMaterials or Services CHN2-003 Request for Operation orRate ChangeSee STD2-004 and STD2-005 forInputs/Outsputs/KPI's for all Supportand Management processesJob PlannedPRO2-007 Daily Production Planning STD2-002STD2-001BMS Document ControlBMS Document RevisionPRO2-009 Expedite CustomerOrdersSTD2-006 Records Control SCH2-003 Temporary OutsourcingProcess JobProduct Placed in Inventory PRO2-003 Part Production Color Key:Key ISO ProcessesCHN2-002 NSM Non-StandardManufacturingQMS Processes Flow Steps CHN2-004 QAD AdditionFAE2-007 LAU2-004 Work Center Transfer Container Designation ProcessPRO2-001 Monitoring andMeasuring of Product PRO2-006 Transfer of TemporaryWorkProduct Shipped to the Customer SHP2-001 Ship Customer Orders4.4.2. Top Management ensures the organization:a) Maintains documented information to support the operation of its processes;b) Retains documented information to have confidence that the processes are beingcarried out as planned.This documentation includes the “Quality Manual”, which consists of this Quality SystemPolicy Manual, as well as the quality system procedures, which are located andcontrolled as defined under documentation requirements per Section 7.5.5. Leadership5.1. Leadership & Commitment5.1.1. GeneralTop Management demonstrates leadership and commitment with respect to the qualitymanagement system by:a) Taking accountability for the effectiveness of the quality management system;b) Ensuring the quality policy statement and objectives are established for the qualitymanagement system and are compatible with the context and strategic direction ofthe organization;c) Ensuring the integration of the quality management system requirements into theorganization’s business p rocesses;d) Promoting the use of the process approach and risk-based thinking;e) Ensuring that the resources needed for the quality management system areavailable;f) Communicating the importance of effective quality management and of conformingto the quality management system requirements;g) Ensuring that the quality management system achieves its intended results;h) Engaging, directing, and supporting personnel to contribute to the effectiveness ofthe quality management system;i) j) Promoting improvement;Supporting other relevant management roles to demonstrate their leadership as it applies to their areas of responsibility.5.1.2. Customer FocusTop Management demonstrates leadership and commitment with respect to customerfocus by ensuring that:a) Customer and applicable statutory and regulatory requirements are determined,understood, and consistently met;b) The risks and opportunities that can affect conformity of products and services andthe ability to enhance customer satisfaction are determined and addressed;c) The focus on enhancing customer satisfaction is maintained.5.2. Policy5.2.1. Establishing the Quality PolicyTop Management establishes, implements, and maintains a quality policy statementthat:a) Is appropriate to the purpose and context of the organization and supports itsstrategic direction;b) Provides a framework for setting quality objectives;c) Includes a commitment to satisfy applicable requirements;d) Includes a commitment to continual improvement of the quality managementsystem.5.2.2. Communicating the Quality PolicyTop Management ensures the quality policy statement is:a) Available and maintained as documented information, ref. Section 2;b) Communicated, understood, and applied within the organization;c) Available to relevant interested parties, as appropriate.5.3. Organizational Roles, Responsibilities, & AuthoritiesTop Management ensures that the responsibilities and authorities for relevant roles areassigned, communicated, and understood within the organization.Top Management assigns responsibility and authority for:a) Ensuring that the quality management system conforms to the requirements of thestandard, per Section 1;b) Ensuring that the processes are delivering their intended outputs;c) Reporting on the performance of the quality management system and on opportunities forimprovement , in particular to top management;d) Ensuring the promotion of customer focus throughout the organization;e) Ensuring that the integrity of the quality management system is maintained when changesto the quality management system are planned and implemented.6. Planning6.1. Actions to Address Risks & Opportunities6.1.1. When planning for the quality management system, Top Management considers theissues referred to in 4.1 and the requirements referred to in 4.2, and determines therisks and opportunities that need to be addressed to:a) Give assurance that the quality management system can achieve its intendedresult(s);b) Enhance desirable effects;c) Prevent, or reduce, undesired effects;d) Achieve improvement.6.1.2. Top Management plans:a) Actions to address these risks and opportunities;b) How to:1) Integrate and implement the actions into its quality management systemprocesses;2) Evaluate the effectiveness of these actions.Top Management ensures actions taken to address risks and opportunities shall beproportionate to the potential impact on the conformity of products and services.Top Management has addressed risks and opportunities through the implementation ofthe quality management system, specifically through the procedures and processeswe’ve defined with the intention to prevent risks an d address opportunities.6.2. Quality Objectives & Planning to Achieve Them6.2.1. Top Management establishes quality objectives at relevant functions, levels, andprocesses needed for the quality management system.Top Management ensures the quality objectives:a) Are consistent with the quality policy statement;b) Are measureable;c) Take into account applicable requirements;d) Are relevant to conformity of products and services and to enhancement ofcustomer satisfaction;e) Are monitored;f) Are communicated;g) Are updated as appropriate.Top Management maintains documented information on the quality objectives.6.2.2. When planning how to achieve its quality objectives, Top Management determines:a) What will be done;b) What resources will be required;c) Who will be responsible;d) When it will be completed;e) How the results will be evaluated.Top Management plans to achieve objectives by defining our quality managementsystem procedures and processes. Top Management evaluates results andimprovement actions through the management review process, including document andtracking actions.6.3. Planning of ChangesWhen the need for changes to the quality management system are determined, TopManagement ensures the changes are carried out in a planned manner, considering:a) The purpose of the changes and their potential consequences;b) The integrity of the quality management system;c) The availability of resources;d) The allocation or reallocation of responsibilities and authorities.7. Support7.1. Resources7.1.1. GeneralTop Management determines and provides the resources needed for the establishment,implementation, maintenance, and continual improvement of the quality managementsystem, considering:a) The capabilities of, and constraints on, existing internal resources;b) What needs to be obtained from external providers.7.1.2. PeopleTop Management determines and provides the personnel resources necessary for theeffective implementation of its quality management system and for the operation andcontrol of its processes.7.1.3. InfrastructureTop Management determines, provides, and maintains the infrastructure necessary for the operation of its processes and to achieve conformity of products and services.7.1.4. Environment for the Operation of ProcessesTop Management determines, provides, and maintains the environment necessary forthe operation of its process and to achieve conformity of products and services.7.1.5. Monitoring & Measuring Resources7.1.5.1. GeneralTop Management determines and provides resources needed to ensure validand reliable results when monitoring or measuring is used to verify theconformity of products and services to requirements, ensuring the resourcesprovided:a) Are suitable for the specific type of monitoring and measurement activitiesbeing undertaken;b) Are maintained to ensure their continuing fitness for their purpose.Top Management ensures appropriate documented information is retained asevidence of fitness for purpose of the monitoring and measurement resources.7.1.5.2. Measurement TraceabilityWhen measurement traceability is a requirement, or is considered to be an essentialpart of providing confidence in the validity of measurement results, the QualityDepartment ensures measuring equipment is:a) Calibrated or verified, or both, at specified intervals, or prior to use, againstmeasurement standards traceable to international or national measurementstandards; when no such standards exist, the basis used for calibration orverification are retained as documented information;b) Identified in order to determine their status;c) Safeguarded from adjustments, damage, or deterioration that would invalidate thecalibration status and subsequent measurement results.Assigned personnel determine if the validity of previous measurement results havebeen adversely affected when measuring equipment is found to be unfit for itsintended purpose, and take appropriate action as necessary.7.1.6. Organizational KnowledgeTop Management determines the knowledge necessary for the operation of itsprocesses and to achieve conformity of products and services.Top Management ensures this knowledge is maintained and made available to theextent necessary.When addressing changing needs and trends, Top Management ensures currentknowledge is considered and determines how to acquire or access any necessaryadditional knowledge and required updates.Top Management has addressed this requirement through the documented processes and procedures of the quality management system, as well as through the retainedinformation supporting the quality management system processes.。